Investigation summary
What happened
On the morning of 9 April 2022, the fully laden capesize bulk carrier Hagen Oldendorff departed its berth in Port Hedland, Western Australia with a harbour pilot on board and 4 tugs assisting. The first of the tugs was cast off shortly after departure and the ship continued its passage of the port’s navigational channel. As the pilot navigated the ship through a turn in the channel, the 2 shoulder tugs were cast off and retained as passive escorts while the aft tug remained tethered as an active escort. Shortly after the turn was completed, the ship experienced a loss of electrical power supply to all the ship’s analogue rudder angle indicators and, a few minutes later, struck the western batter of the channel. The pilot manoeuvred the ship back into the centre of the channel and, with the assistance of additional tugs and a second pilot, resumed the outbound passage and conducted the ship to an anchorage outside port limits.
Subsequently, the ship was found to be taking on water in the number 1 and 2 port double‑bottom water ballast tanks. Surveys and inspections conducted over the following days identified substantial damage to the ship’s bottom shell plating including hull breaches of the shipside shell plating of the damaged tanks and the failure of the transverse bulkhead between the tanks. There were no reported injuries or pollution of the sea as a result of the grounding.
What the ATSB found
The ATSB investigation found that a short circuit in a bridge rudder angle indicator tripped the common circuit breaker for the ship’s rudder angle indicators resulting in a loss of electrical power and illumination to all the analogue indicators. Following the power supply failure to the indicators, the ship’s pilot initiated emergency procedures for a steering failure, with manoeuvring orders issued to maintain directional control of the ship resulting in an uncontrolled turn to port and the subsequent grounding.
The ATSB also identified that the pilot had cast off the ship’s port and starboard shoulder tugs, which limited their ability to reduce the ship’s speed or to arrest the turn to port. The pilot’s decision to cast off these tugs was found to be inconsistent with the recommended practices of the port’s implemented escort towage strategy. Furthermore, this best practice escort towage guidance was not integrated into the port user guidelines and procedures or into the pilotage provider’s safety management system.
Finally, the ATSB determined that neither the applicable international regulations, nor the responsible classification society’s rules, required that rudder angle indication systems be protected against a single point of failure in their electrical power supply, nor was there a requirement for audible or visual alarms to alert crew to such a failure.
What has been done as a result
Following this incident, the Pilbara Ports Authority (PPA) updated the port user guidelines and procedures to incorporate the tug retention and utilisation practices, and guidance recommended in the port’s escort towage strategy. The PPA also issued a marine notice requiring a suitably qualified and competent person be present in the steering gear room during ship transits of the Port Hedland channel.
Port Hedland Pilots (PHP) advised that, following the grounding, pilots keep the forward 2 tugs fast as recommended for the relevant channel zones unless prevented from doing so by weather or other factors. The PHP safety management system procedures for towage requirements were updated to reflect the tug retention and tug utilisation guidelines of the port's escort towage strategy including specific directions to pilots on where, and under what conditions, tugs were to be released.
Hagen Oldendorff’s ship managers, Wah Kwong Ship Management Hong Kong, advised the ATSB that an audible and visual alarm was fitted to the ship to alert crew if and when the ship’s rudder angle indicators lose electrical power. In addition, the ship managers installed closed circuit television cameras in the ship’s steering gear room to allow direct monitoring of the physical rudder angle from the bridge.
Lloyd’s Register advised that alternate design solutions may effectively address the risk associated with a single point of failure in electrical power supply for ship's rudder angle indicators and that the Machinery Panel of the International Association of Classification Societies (IACS) may consider a unified interpretation (UI) of SOLAS requirements.
The Liberia Maritime Authority (LiMA) advised the ATSB that the Liberian Administration was considering issuing a marine advisory and that it was addressing this safety issue with the ship's classification society, Lloyd's Register, and, if necessary, with the International Association of Classification Societies (IACS).
The Australian Maritime Safety Authority (AMSA) advised that it would consider any requests for support from the Liberian Administration should the Administration seek to take action to address this safety issue at the International Maritime Organization (IMO). However, due to the absence of detailed proposals and a timeframe to seek safety action aimed at the resolution of the safety issue, the ATSB has issued safety recommendations to Lloyd’s Register, AMSA and the LiMA. The ATSB will continue to monitor the safety issue while working to highlight and promote awareness of the issue.
Safety message
Pilotage and towage often serve as primary risk control measures in ensuring the safety of port operations. Where demonstrated techniques and practices have been identified that increase the effectiveness of towage in preventing incidents and in mitigating the consequences when they occur, it is imperative that they are appropriately documented, disseminated and implemented.
The occurrence
Overview
On the morning of 9 April 2022, the fully laden capesize bulk carrier Hagen Oldendorff departed its berth in Port Hedland, Western Australia with a harbour pilot on board and 4 tugs assisting. The first of the tugs was cast off shortly after departure and the ship continued its passage of the port’s navigational channel. As the pilot navigated the ship through a turn in the channel, the 2 shoulder tugs were cast off and retained as passive escorts while the aft tug remained tethered as an active escort. Shortly after the turn was completed, the ship experienced a loss of electrical power to all the ship’s analogue rudder angle indicators and, a few minutes later, struck the western batter of the channel. The pilot manoeuvred the ship back into the centre of the channel and, with the assistance of additional tugs and a second pilot, resumed the outbound passage and conducted the ship to an anchorage outside port limits.
Subsequently, the ship was found to be taking on water in the number 1 and 2 port double‑bottom water ballast tanks. Surveys and inspections conducted over the following days identified substantial damage to the ship’s bottom shell plating, including hull breaches of the shipside shell plating of the damaged tanks and the failure of the transverse bulkhead between the tanks. There were no reported injuries or pollution of the sea as a result of the grounding.
Pre-departure activity
On the morning of 7 April 2022, the 300 m Liberian-registered bulk carrier Hagen Oldendorff (Figure 1) arrived at Port Hedland, Western Australia, from Tianjin, China, to load a cargo of iron ore. By 0900 local time, the ship was all fast, port side alongside at Stanley Point berth number 2 (SP2), operated by Roy Hill Iron Ore. Shortly after, the ship commenced loading.
Figure 1: Hagen Oldendorff at anchor off Port Hedland

Source: Australian Maritime Safety Authority
By 1544 the following day, Hagen Oldendorff had completed loading 205,465 tonnes of iron ore and was drawing forward and aft draughts of 18.34 m and 18.42 m, respectively. The ship’s departure was planned for 0045 on 9 April.[1]
By 0001 on 9 April, Hagen Oldendorff had its main engine on standby for departure, having completed pre-departure checks, which included the testing of the steering gear, main engine, and other navigational equipment. At about 0018, a harbour pilot boarded the ship. Shortly after, the master-pilot information exchange was completed on the ship’s navigation bridge (bridge) and the pilot confirmed the master was satisfied departing with a minimum under keel clearance of 0.69 m. The steering gear checks and main engine ahead and astern movement were then repeated with the pilot observing. By 0031, 3 tugs were made fast in preparation for departure with a fourth to be made fast after unberthing.
At 0048, Hagen Oldendorff departed the berth and shortly after, the fourth tug was also made fast. Tugs RT Inspiration and RT Atlantis were fast on the port and starboard shoulders[2] respectively, RT Clerke through the centre lead aft, and RT Darwin on the starboard quarter.[3] The ship’s bridge team for the departure consisted of the master, third mate, helmsman and pilot, who was situated at the front of the bridge, separated from the rest of the bridge team by the bridge console. The engine room was manned by the chief engineer, second engineer and duty oiler.
The weather at the time was fine with south-westerly winds at force 3 (between 7 and 10 knots),[4] 1 m seas and good visibility.
The pilotage
At about 0118, when Hagen Oldendorff was about 3.5 cables[5] (648 m) south of Hunt Point (Figure 2), RT Darwin was cast off and dismissed. The ship proceeded north-east along the channel. The pilot then offered RT Clerke’s master a training opportunity in helping turn the ship into the Goldsworthy channel using ‘indirect towing’[6] (a routine practice in the port to train, and maintain the skills of, tug masters). RT Clerke’s tug master accepted the pilot’s offer.
At about 0126, the pilot commenced a turn to port using RT Clerke to provide steering forces (to pull the ship’s stern to starboard) and the ship’s rudder as necessary (port 10° and port 20°). At this time, the ship’s speed[7] was about 6.4 knots.[8]
At about 0133, the pilot ordered the release of the tug RT Atlantis on the starboard shoulder and by 0135, the crew of RT Atlantis had recovered the tug’s towline (Figure 2). RT Atlantis continued to maintain station off the ship’s starboard shoulder as a 'passive escort’.[9] Shortly after, the pilot ordered the release of the tug RT Inspiration on the port shoulder as Hagen Oldendorff approached beacons 36-37 in the Goldsworthy channel (Figure 2). Recorded data from the ship’s voyage data recorder (VDR)[10] showed that, at the time, the ship was turning to port at a rate of turn (RoT)[11] of about 9° per minute and its speed was 6.7 knots, with the main engine set to manoeuvring full ahead (51 RPM).
By 0137:22, the RoT had reduced, and the ship was largely steady on the Goldsworthy leading lights (leads) line (aligned 156°‑336°), slightly to the west of the channel centreline. The aft tug, RT Clerke, was now positioned off the ship’s port quarter, having assisted with steadying the ship as the turn to port was completed.
Figure 2: Section of navigational chart Aus 53 showing location of key events
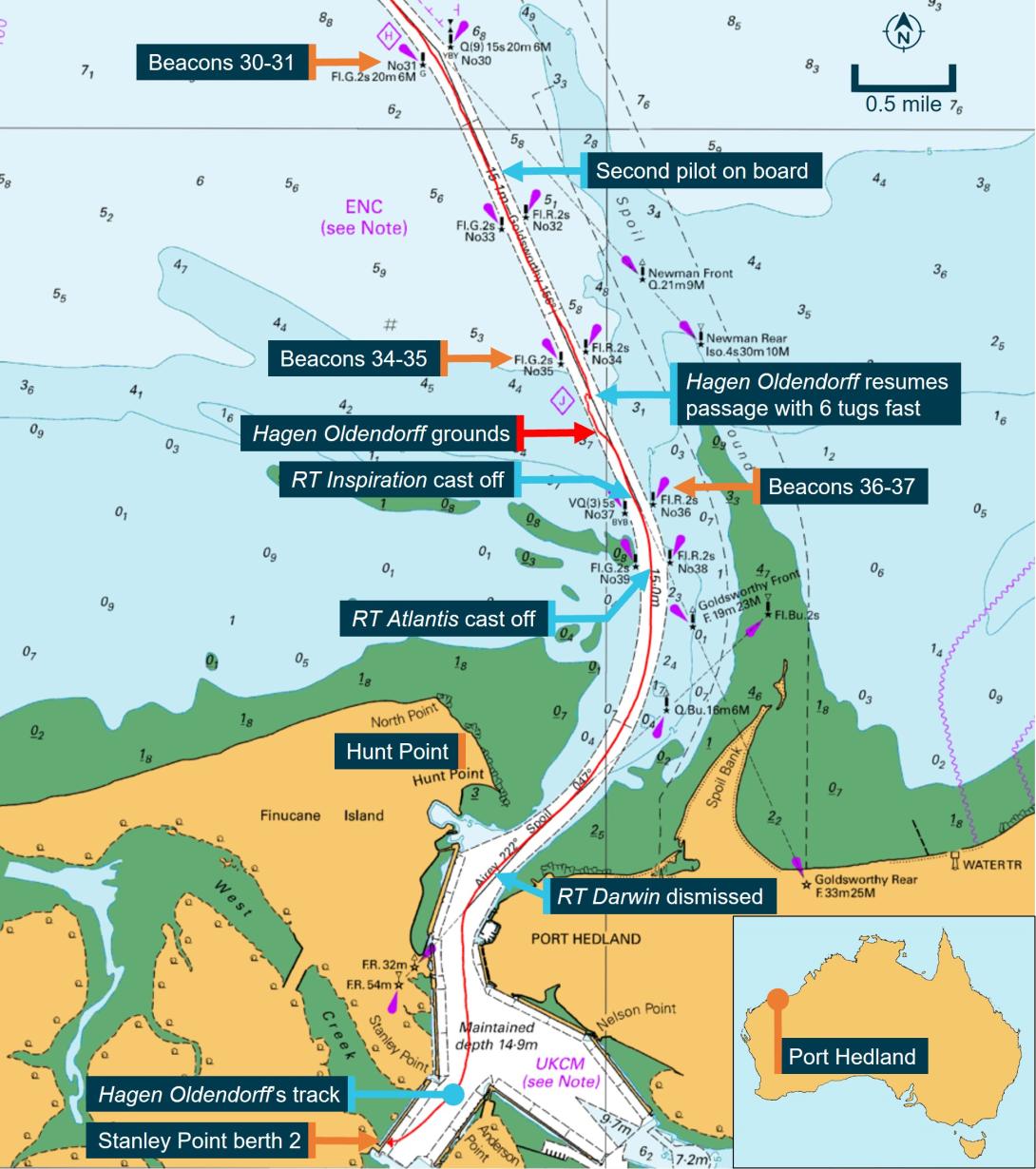
Source: Australian Hydrographic Office, annotated by the ATSB
At 0137:25, the ship was steady on a heading[12] of about 334° with a course over ground of 336°, when the pilot ordered starboard 10° of rudder, likely to regain the channel centreline. At about the same time, the pilot advised RT Clerke’s master of the completion of the indirect towage training. The tug master acknowledged the completion of the training and asked the pilot for feedback on their performance.
Meanwhile, the ship had started to turn slowly to starboard at a RoT of about 2° per minute, and the pilot ordered the rudder to midships, followed immediately by a heading order of 335° (for a tabular sequence of events, see Appendix A). By this time, RT Inspiration had been cast off and had assumed the role of a passive escort. The starboard RoT increased to about 3.6° per minute and at 0137:47, the pilot ordered port 10° of rudder.
The grounding
At 0137:49, the pilot and bridge team heard ‘clicking sounds’ (from the electrical cabinet on the bridge), followed by the loss of illumination of the rudder angle indicators (see the section titled Rudder angle indicators). The pilot recalled that before the rudder angle indicator went dark it was indicating that the rudder was amidships. However, by the time illumination of the indicators was lost, the helmsman had executed the pilot’s previous order of port 10° and VDR data showed the rudder was at port 10° while the starboard RoT had increased slightly to 3.7° per minute.
The pilot then ordered port 20° of rudder and also ordered the aft tug, RT Clerke, to pull the ship’s stern to starboard with a force of 40 tonnes[13] (to counteract the ship’s starboard RoT). The helmsman immediately executed the pilot’s order of port 20° and RT Clerke began to move from the ship’s port quarter to the starboard quarter.
Moments later, at 0138:08, the pilot ordered ‘non-follow-up, port 20°’ (see the section titled Steering gear) while the master and rest of the bridge team attempted to determine what had happened.
At 0138:10, the pilot informed RT Clerke’s master of a ‘rudder failure’ and ordered the tug to take the ship’s ‘stern to starboard, 60 tonnes’. This was followed by the pilot ordering RT Inspiration to make fast on the ship’s port shoulder. VDR data indicated that at 0138:21 non-follow-up (NFU)[14] mode was engaged. By this time, the starboard RoT had largely been eliminated and the ship was steady on a heading of 336° with the rudder at port 20°.
By 0138:28, the ship had started turning to port. Closed-circuit television (CCTV) footage from RT Clerke and RT Inspiration showed the aft tug, RT Clerke, crossing the ship’s stern as it transitioned to the starboard quarter to execute the pilot’s last order of ‘stern to starboard, 60 tonnes’. At 0138:30, the pilot rescinded their previous order to RT Clerke by ordering ‘Clerke, no weight, Clerke’, which RT Clerke’s master acknowledged. About 5 seconds later, at 0138:35, the helmsman applied port NFU helm input, and the rudder angle slowly increased to port 27°.
At 0138:36, on the pilot’s orders, the master started reducing the main engine telegraph setting from ‘full ahead’ to reduce the ship’s speed which was about 6.9 knots. A few seconds later, the pilot ordered RT Clerke ‘stern to port, 20 tonnes’ and then, shortly after, ‘stern to port, full’, in an attempt to counteract the increasing port RoT which was now about 7° per minute. At 0139:20, RT Inspiration was ordered to push with full power on the port bow.
At 0139:24, the pilot ordered ‘stop engines’ and the ship’s speed started to reduce. At 0139:28, the port RoT peaked at 13.6° per minute and then started decreasing. At 0139:30, RT Atlantis was tasked to push on the starboard quarter, after initially being instructed to make fast between cargo holds 2 and 3 on the starboard side. Meanwhile, the third mate and master had contacted the chief engineer (in the engine control room) and the second mate (manning the aft mooring stations) and directed them to the steering gear room to investigate.
At 0139:35, the pilot queried if the rudder was responding and then ordered ‘hard to port’. The helmsman complied by applying port NFU input and VDR data showed that the rudder moved from its initial position of about port 27° to hard over to port (35°). At this time, RT Clerke was using full power to bring the stern to port and the ship’s port RoT was 13.4° per minute and decreasing. The ship’s master queried the pilot’s order of ‘hard to port’ while the pilot reported to the Port Hedland vessel traffic service (VTS) that the ship had experienced a ‘rudder failure’ and declared a ‘Port Emergency’.[15] About 15 seconds after the pilot’s order of hard to port, the master queried the rudder order again. The pilot immediately ordered the rudder amidships followed by an order of hard to starboard. VDR data showed that by 0140:11, the rudder was hard over to starboard.
Shortly after 0140, on the pilot’s order, the master put the main engine astern. At 0140:21 the pilot asked if the rudder was hard to starboard, and the master confirmed that it was, indicating that the ship’s steering gear room was probably manned.
At 0140:30, Port Hedland VTS made a radio broadcast on the port’s very high frequency (VHF) working channel (channel 12) requesting available tugs to assist with Hagen Oldendorff’s emergency and notified the harbour master about the incident. Over the next 5 minutes, the masters of 5 tugs (FMG Dusky, Iron Ibis, IronWhistler, RT Darwin and Iron Kestrel)[16]confirmed they were responding.
From about 0140:34 onwards, there was a sharp reduction in both the ship’s speed and its RoT to port. VDR data confirmed that the ship had contacted the western channel batter (the steep side of the navigable channel), about 4 cables south-east of beacon 35 (Figure 3) at a speed of about 6.1 knots. The ship’s bow then swung away from the side of the channel to starboard.
Figure 3: Hagen Oldendorff at the time of the grounding
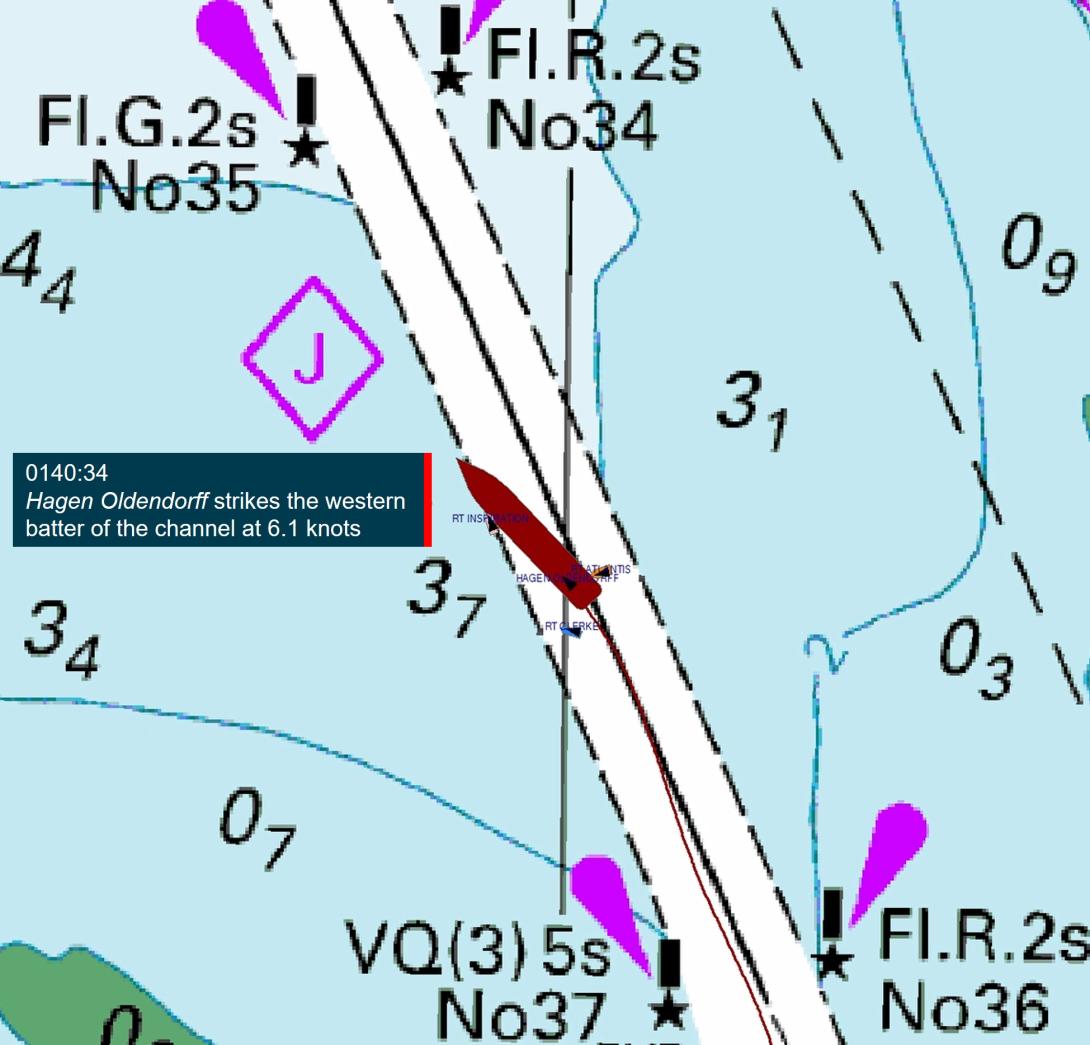
Source: Australian Hydrographic Office, annotated by the ATSB using VDR data
Response and recovery
At 0140:40, the pilot instructed RT Atlantis, which was pushing on the ship’s starboard quarter, to proceed to the starboard bow. The pilot also ordered RT Clerke to pull the stern to starboard using full power and instructed RT Inspiration, which was on the port bow, to stop pushing. RT Clerke’s master did not acknowledge the pilot’s order and continued pulling the stern to port while RT Atlantis proceeded forward. By about 0141, RT Inspiration was fast on the port shoulder and the pilot once again ordered RT Clerke to stop pulling, which the tug master then acknowledged. Meanwhile, the ship’s starboard RoT had increased to a maximum of about 19° per minute and then started reducing while the ship’s speed had decreased to about 4.3 knots.
Shortly after 0142, the pilot informed VTS that the ship may have grounded, that the engine was operational, that there was a rudder failure and the steering gear was not responding in any mode, including NFU. The pilot also asked VTS to call the duty pilot and the next pilot on the roster. At 0144, the pilot ordered RT Atlantis to make fast on the ship’s starboard shoulder.
At 0145:23, the master informed the pilot that the rudder indicator did not appear to be working. About a minute later, the master confirmed that the rudder indicator was not working, and that the ship’s crew had engaged the emergency local steering controls in the steering gear room. VDR data indicated that the changeover to emergency local steering control occurred at 0148:42.
In the meantime, the tugs FMG Dusky and Iron Ibis had arrived at the ship’s location. At 0147:20, the pilot informed VTS that the ship’s emergency steering system was available, and that they planned to take the ship to the anchorage.
By 0148, FMG Dusky and Iron Ibis were fast on the starboard quarter and centre lead forward, respectively. By this time, Hagen Oldendorff was stopped and had been recovered to the middle of the channel, south of beacon 35 (Figure 2). Shortly after, the tug Iron Whistler was made fast on the port quarter and RT Atlantis was fast on the starboard shoulder.
At about 0152, the ship began moving along the channel under its own power with 6 tugs fast. About a minute later, the pilot asked for the ship’s forward, port ballast tanks to be sounded (to check for water ingress). At 0157, Iron Kestrel arrived and was instructed to take up station amidships on the port side and follow the ship.
At 0158, VTS advised the pilot that the harbour master had been informed that the ship had engaged emergency steering, and it was cleared to proceed to the anchorage. At 0204, RT Darwin arrived and was directed to take up station amidships on the starboard side.
At about 0212, when the ship was past beacons 32-33, a second pilot boarded the ship by helicopter (Figure 2). The second pilot took charge of communications with external parties while the pilot maintained conduct of the ship. Shortly after, VTS advised the pilot that sufficient tidal window remained for the ship to proceed and exit the channel at the C1 beacon.
At 0239, after several inquiries by the pilot, the master advised that the forward ballast tanks had been sounded and that the soundings indicated no water ingress. The pilot asked for the tanks to be sounded again after 30 minutes.
At about 0303, the ship cleared beacons 15-16 (about 8.8 miles north-north-west of Hunt Point). Shortly after, FMG Dusky was cast off and dismissed and Iron Kestrel was made fast in its place on the starboard quarter.
At about 0327, the master reported that the latest tank soundings had confirmed no water ingress.
Shortly after 0430, the ship cleared the channel (at beacons C1-C2) and all tugs, except RT Clerke, were dismissed. By 0530 on 9 April, the ship had anchored outside the port limits in a position 24 miles north-north-west of Hunt Point (Figure 4). Soon after, RT Clerke was dismissed, and the pilots left the ship by helicopter.
Figure 4: Hagen Oldendorff's track overlaid on chart of Port Hedland
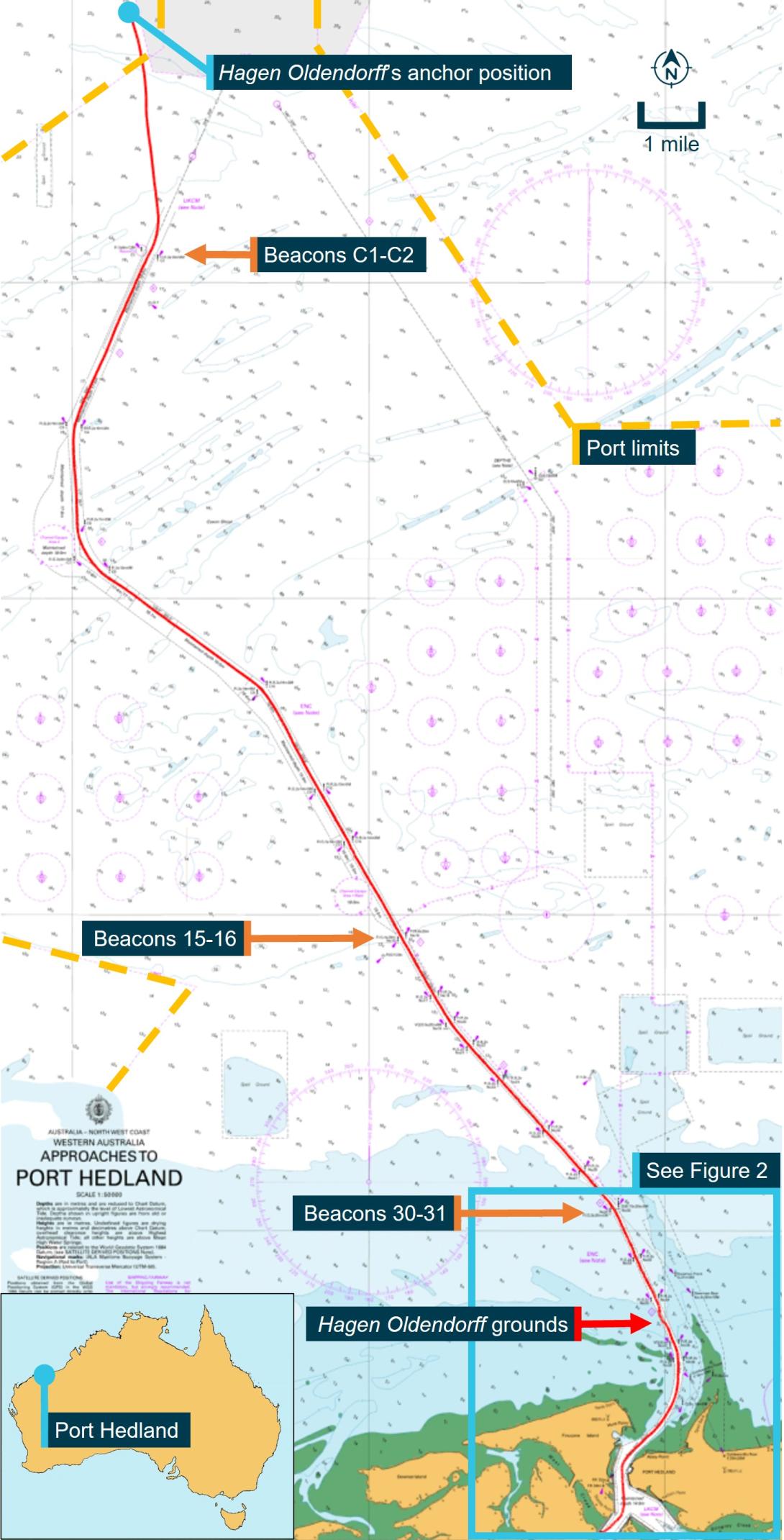
Source: Australian Hydrographic Office, annotated by the ATSB
Post-incident actions
At 0530 on 9 April, the harbour master notified the Australian Maritime Safety Authority (AMSA) of Hagen Oldendorff’s grounding and that the ship was at the anchorage. At 0600, AMSA issued the ship’s master with a detention order.[17]
At about 1000, the master notified Port Hedland VTS that the ship was taking on water in number 1 and 2 port double‑bottom water ballast tanks, had developed a trim by the head, and requested assistance. In response, the harbour master ordered 2 dive boats to the ship’s location and notified AMSA of the water ingress. Shortly after, the master reported that one ballast pump was coping with pumping out the water from the breached tanks. Later that day, the master advised that all other compartments (ballast and fuel tanks) were intact.
On 10 April, an AMSA surveyor, accompanied by a representative of the ship’s owners, boarded the ship at anchorage by helicopter. The surveyor conducted an inspection of the ship and an assessment of the ship’s steering system, seaworthiness condition and crew’s welfare.
On 11 April, an underwater hull inspection identified substantial damage to the ship’s port side bottom shell plating. The hull was breached in 2 locations – a 0.65 m by 0.95 m breach and a 0.3 m by 0.4 m breach about 10 m forward of the first breach. Additionally, the transverse bulkhead between the 2 tanks had failed, allowing flooding between them. Subsequent inspections also identified extensive impact damage with the most significant damage extending over a length of about 53 m along the forward, port side of the ship’s hull near the turn of the bilge (Figure 5). Several structural frames and internal strength members had also buckled or fractured.
Figure 5: Damage to Hagen Oldendorff's hull
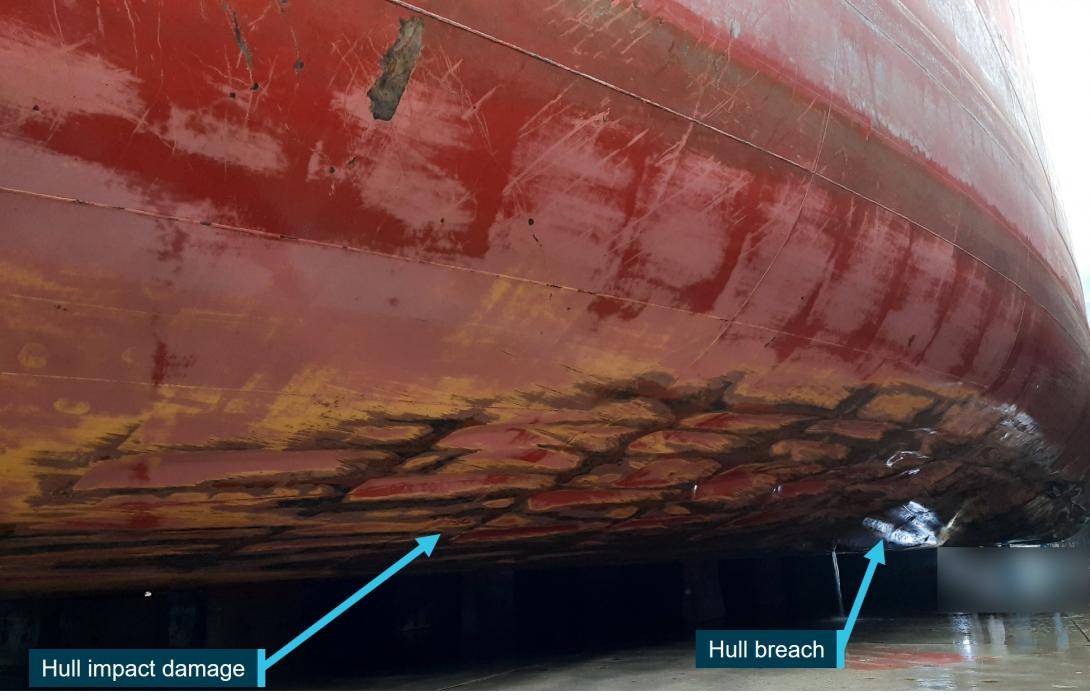
Source: Wah Kwong Ship Management HK, annotated and modified by the ATSB
On 18 May, following temporary repairs at the anchorage, the ship’s flag State (Liberia) approved the ship to undertake a direct voyage to its discharge port in China before proceeding to a shipyard for permanent repairs.
At 2000 on 19 May, AMSA released Hagen Oldendorff from its detention. At 2154, the ship departed for Lianyungang, China, to discharge its cargo. After discharging the cargo, the ship sailed to a shipyard in Zhoushan, China, where permanent repairs were carried out.
ATSB investigation
The ship’s initial incident alert and incident report notifications[18] submitted in April 2022 reported that Hagen Oldendorff had experienced an issue with its steering due to faulty rudder indicators during its outbound transit of the Port Hedland channel. An initial ATSB review of those notifications resulted in a decision not to investigate the occurrence.
Subsequently, reports from AMSA’s Port Hedland port marine surveyors indicated that the ship had grounded in the channel and sustained hull damage as a result. A few weeks later, in May 2022, BHP[19] also reported to the ATSB (via telephone) that the ship had grounded and sustained substantial damage. In late July, BHP presented the ATSB with additional information, including recorded data.
The ATSB reassessed the available information, obtained further information from the Pilbara Ports Authority (PPA) and Port Hedland Pilots (PHP), and commenced an investigation into this serious incident. Subsequently, ATSB investigators attended the offices of PPA, PHP and BHP in Port Hedland in October 2022 to interview relevant persons and collect available evidence. The ATSB also obtained VDR and other relevant digital and documentary evidence from the ship’s managers, PPA, PHP and BHP.
Context
Hagen Oldendorff
The ship
Hagen Oldendorff was a Liberian-registered, capesize[20] bulk carrier built in 2020 by Cosco Shipping Heavy Industry (Yangzhou, China). At the time of the grounding, the ship was owned by CL Marina, managed and operated by Wah Kwong Ship Management Hong Kong (HK) and classed with Lloyd’s Register (LR).
The ship was equipped with the necessary navigational and manoeuvring equipment required by the International Convention for the Safety of Life at Sea (SOLAS)[21] for a ship of its size. This included radar, electronic chart display and information system (ECDIS) and a Highlander HLD‑VDR600 voyage data recorder (VDR), from which information useful to the investigation was recovered, including bridge voice recordings.
The ship’s propulsion was provided by a 6-cylinder, MAN B&W G70ME-C9.2 engine developing 15,131 kW driving a single, 4-blade, fixed‑pitch, right-handed propeller.
Ship’s crew
At the time of the incident, Hagen Oldendorff was crewed by 20 Chinese nationals, including the master.
The master held a Chinese master’s certificate of competency and had about 28 years of seagoing experience, with about 11 years as master. This was the master’s first time working with Wah Kwong Ship Management HK and also their first time on board Hagen Oldendorff, having joined the ship about 5 months before the grounding.
The third mate held a Chinese third mate’s certificate of competency and had about 15 years of seagoing experience, with about 6 months as third mate. This was also their first time working with Wah Kwong Ship Management HK and their first time on board Hagen Oldendorff, having joined the ship about 5 months before the grounding.
The helmsman held a Chinese able-bodied seaman’s qualification and had about 9 years of seagoing experience. This was also their first time working with Wah Kwong Ship Management HK and their first time on board Hagen Oldendorff, having joined the ship about 5 months before the grounding.
Hagen Oldendorff had previously called at Port Hedland in November 2021 with the same master, third mate and helmsman on board.
There was no evidence to indicate that the master, third mate or helmsman were experiencing a level of fatigue known to have a demonstrated effect on performance.
Steering gear
Hagen Oldendorff was fitted with a Kawasaki FE21-288 electro-hydraulic 4-ram steering gear. The steering gear consisted of a single rudder and 2 identical hydraulic systems (systems number 1 and 2), each powered by an LV-180 hydraulic pump. The rudder could be put hard-over to a maximum rudder angle of 35° on either side.
The steering gear could be remotely operated from the bridge in 3 main control modes:
- autopilot steering mode
- manual steering mode (follow‑up mode/wheel control)
- non-follow‑up (NFU) steering mode.
In an emergency, the steering gear could also be operated locally from the steering gear room.
In autopilot mode, the autopilot compares the operator-selected heading against the ship’s heading and transmits rudder angle orders such that the ship remains on, or returns to, the selected heading. There were 2 rudder angle feedback units, which transmitted the rudder angle signal from the rudder to the bridge steering control stand unit. This rudder angle feedback signal was compared to the rudder angle orders issued by the autopilot with the deviation signal driving the torque motor and hydraulic pump to obtain or maintain the commanded rudder angle.
Similarly, in hand steering mode, when the helm (wheel) is moved manually (Figure 6) to port or starboard, a signal is transmitted to move the rudder. A follow-up or feedback signal is received at the bridge steering control stand and compared to the helm order to stop the rudder at the commanded angle.
In the NFU mode, when the spring-loaded lever (Figure 6) is operated in the port or starboard direction, the rudder moves in that direction until the lever is released or the mechanical rudder limit is reached. When operating in NFU mode, the helmsman depends upon the rudder angle indicator or other means of knowing what the rudder angle is so that the lever can be released when the desired rudder angle is reached.
The mode of steering operation was selected by means of push-button switches on the bridge console (Figure 6).
An examination of the ship’s planned maintenance system records for the steering gear identified no deficiencies and showed that the scheduled checks and maintenance had been performed.
Figure 6: Hagen Oldendorff's bridge console layout showing steering mode controls
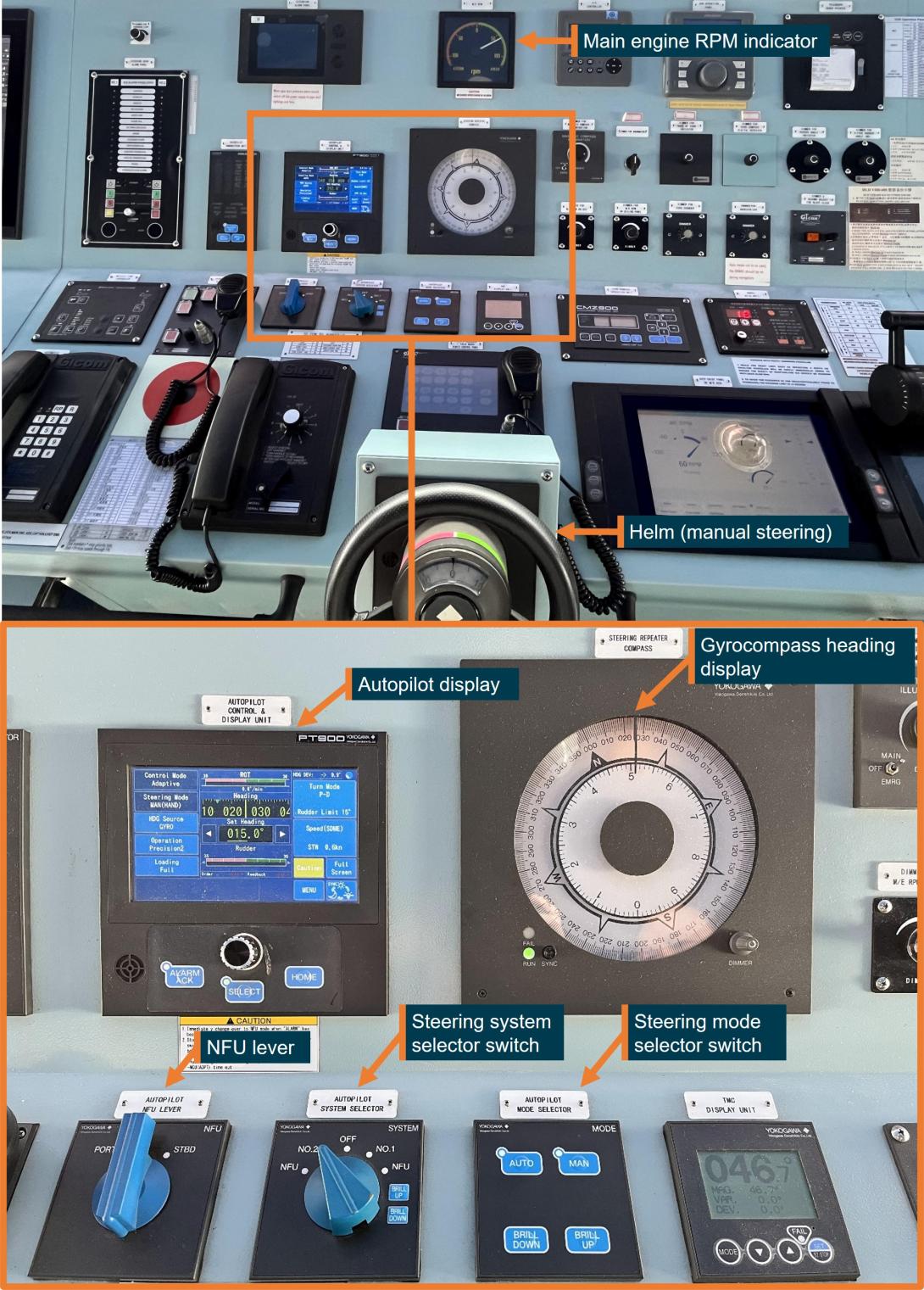
Source: Wah Kwong Ship Management HK, annotated and modified by the ATSB
Rudder angle indicators
The ship was fitted with a Yokogawa RAIS 100 rudder angle indicator system, which included a rudder angle transmitter (in the steering gear room), and 6 analogue rudder angle indicators located as follows:
- a 3-face (omnidirectional) rudder angle indicator mounted on the bridge deckhead (along the ship’s fore and aft centreline and above the bridge manoeuvring console) (Figure 7)
- a rudder angle indicator mounted on the bridge front instrument cluster (Figure 7)
- port bridge wing
- starboard bridge wing
- engine control room
- steering gear room.
The 6 rudder angle indicators had a common power supply protected by one circuit breaker located in a junction box in an electrical cabinet on the bridge.
There were no audible or visual alarms installed to alert crew to the tripping of this breaker or of the loss of electrical power supply to the rudder angle indicators.
Figure 7: Hagen Oldendorff's bridge rudder angle indicators
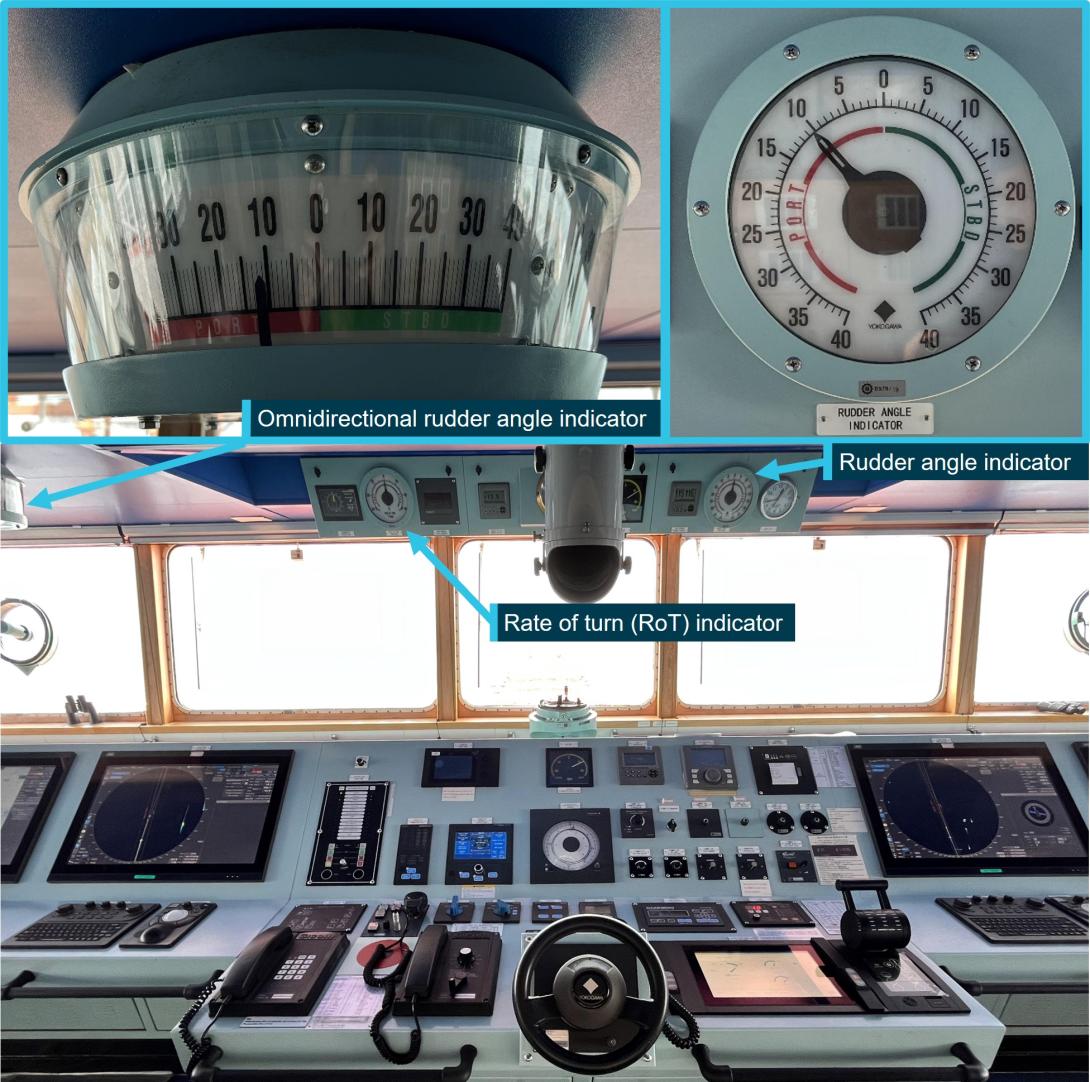
Source: Wah Kwong Ship Management HK, annotated and modified by the ATSB
Rate of turn indicator
Hagen Oldendorff was equipped a rate of turn (RoT) indicator as required by the regulations. The bridge RoT indicator was mounted on the bridge front instrument cluster (Figure 7). The RoT indicator remained operational throughout the incident.
Shipboard investigation
The post-incident shipboard investigation identified that the tracking motor of the omnidirectional rudder angle indicator (Figure 8, inset) had burnt out and caused a short circuit. This short circuit tripped the common circuit breaker in the bridge cabinet resulting in a loss of electrical power to all the ship’s analogue rudder angle indicators. Consequently, all 6 of the ship’s analogue rudder angle indicators and their associated illumination stopped functioning.
When the omnidirectional indicator was isolated post‑incident (when the ship was at anchor), all other rudder angle indicators were found to be functional.
Figure 8: Burnt out tracking motor of rudder angle indicator
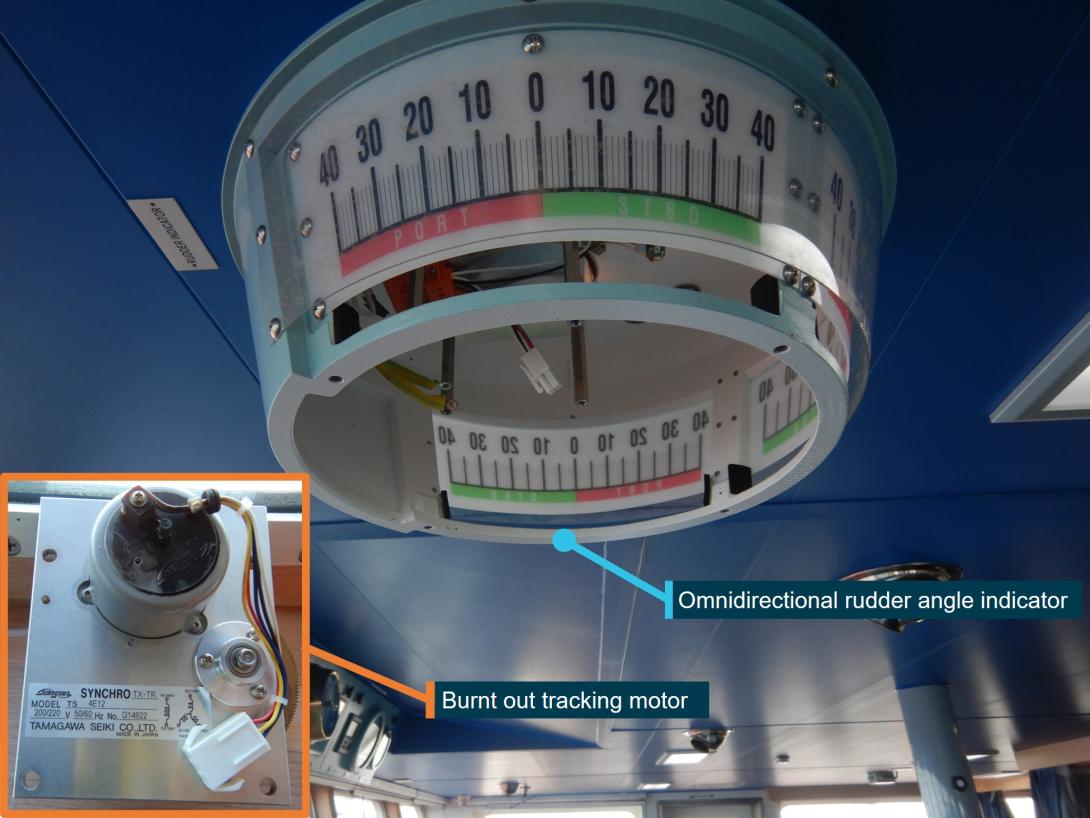
Source: Pilbara Ports Authority, modified and annotated by the ATSB
Following the incident, Wah Kwong Ship Management HK conducted a survey of the rudder angle indicator power supply arrangement on all the ships managed or operated by the company. The survey identified that almost all the ships (over 20 ships) had a similar rudder angle indicator circuit breaker arrangement to Hagen Oldendorff.
Autopilot system
In addition to the 6 analogue rudder angle indicators, the ship’s Yokogawa PT900 autopilot system display unit (Figure 9) also displayed rudder order and feedback (rudder angle). The autopilot system’s power supply and rudder angle feedback signal were independent of the analogue rudder angle indicators’ power supply and rudder angle signal transmitter. The autopilot rudder angle display remained operational throughout the course of the incident. However, neither the ship’s officers, nor the pilot were aware of this functionality.
Figure 9: Autopilot rudder angle display
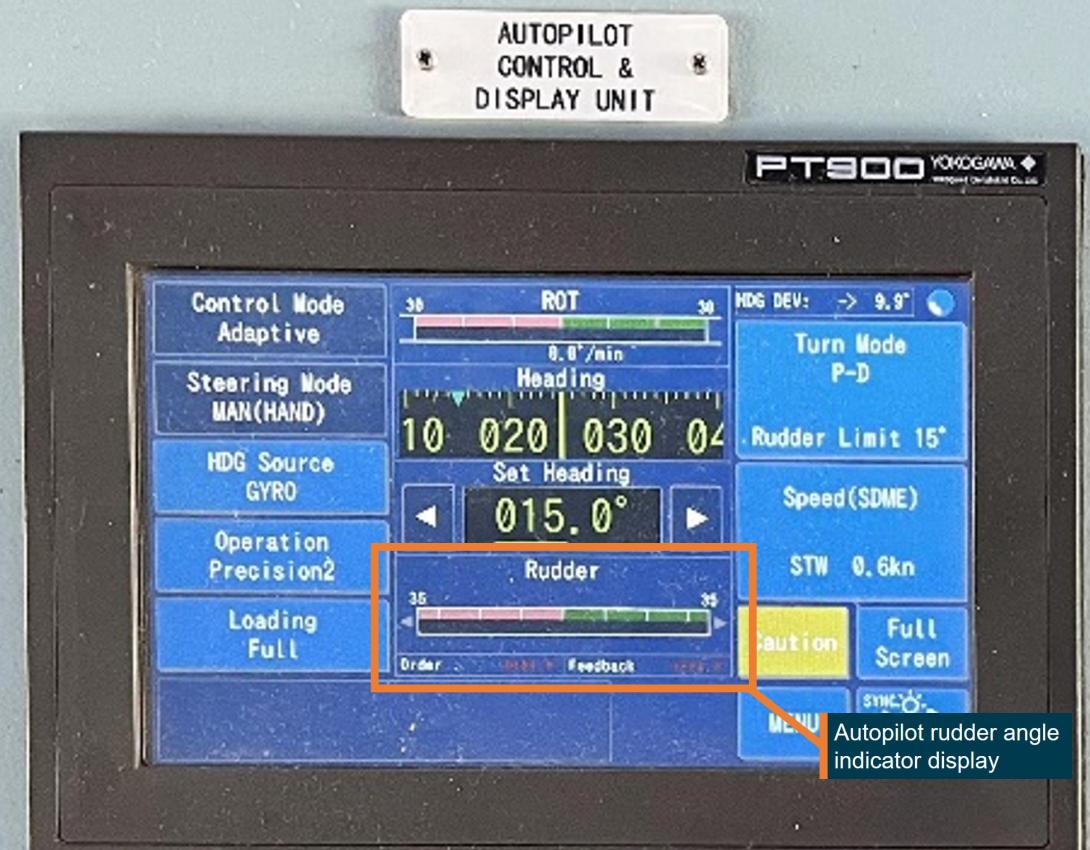
Source: Wah Kwong Ship Management HK, annotated and modified by the ATSB
Steering gear drills and tests
SOLAS regulations[22] required that the ship’s steering gear be checked and tested by the ship’s crew within 12 hours before the ship’s departure from port. The testing was to include, among other things, operation of the:
- steering gear and steering gear power unit failure alarms
- remote steering gear control systems and power failure alarms
- steering positions located on the bridge
- emergency power supply
- rudder angle indicators in relation to the actual position of the rudder.
The checks and tests were to include checking the movement of the rudder over its full range of movement, a visual inspection of the steering gear and the operations of the means of communications between the bridge and steering gear room. Hagen Oldendorff’s third mate conducted the ship’s pre-departure steering test with the assistance of a ship’s engineer (in the steering gear room) at about 2330 on 8 April, about an hour before the ship’s departure.
The steering gear tests were conducted using a steering gear test checklist and completion of the test was logged in the bridge and engine room pre-departure checklists. There were no steering gear deficiencies identified as part of the pre-departure steering tests. The steering, including NFU steering, was briefly tested once again in the presence of the pilot at about 0025 on 9 April with no issues noted.
The regulations also required crews to carry out emergency steering gear drills at least once every 3 months to practice direct control of steering gear from the steering gear compartment and the communications procedure with the bridge. Shipboard drill records showed that emergency steering gear drills were last carried out on 24 November 2021 and on 23 February 2022 (about 6 weeks before the grounding).
The drill record indicated that several crew, including the ship’s navigational ratings, practiced operating the local emergency steering and communicating with the bridge using the emergency telephone. Additionally, a review of shipboard training records showed that a training session on emergency steering was conducted on 21 March 2022 in preparation for the port call at Port Hedland.
Emergency steering procedure
The International Safety Management (ISM) Code[23] required shipping companies to develop, implement and maintain a safety management system (SMS), with instructions and procedures to ensure the safe operation of ships and to prepare for, and respond to, emergencies.
Hagen Oldendorff’s SMS included an emergency procedure manual, which contained procedures to be employed in various emergency scenarios, including for a steering failure and grounding. There was no specific emergency procedure for a rudder angle indicator failure.
The steering failure emergency procedure directed crew to carry out the ship-specific emergency steering procedure. It also directed crew to undertake other standard actions such as to inform the engine room and master, consider reducing speed and to make the appropriate broadcasts and communications. Hagen Oldendorff’s emergency steering procedure, posted on the ship’s bridge and in the steering gear room, provided a series of sequential actions and steps aimed at restoring steering control. At each step, crew were to check whether control had been restored and, if not, move to the next step.
The procedure stated that in the event of a loss of steering control:
- if in autopilot mode, change to manual steering mode
- change from system 1 to system 2 (or vice versa)
- check both hydraulic pumps are ON [both pumps were kept ON for departure and the pilotage]
- change to NFU steering
- public address system broadcast to crew to muster in the steering gear room
- change to local steering and steer using the pump control knob.
Following the loss of electrical power and illumination to the bridge omnidirectional rudder indicator and the bulkhead-mounted indicator, the ship’s bridge team assumed they had lost steering control of the ship. Subsequently, the pilot and master initiated actions consistent with a response to a steering failure, including ordering the steering gear room be manned and switching to NFU steering and then local steering.
The ship’s bridge team were unaware of the autopilot’s rudder angle indicator display and the pilot could not see the display from their location forward of the bridge console. Furthermore, following the loss of rudder angle indication, there was no attempt to check whether any of the other rudder angle indicators (on the bridge wings or on the autopilot display) were operational before initiating steering failure response procedures. Therefore, the possibility of a rudder angle indicator failure was probably not considered, and it is unlikely that knowledge of the autopilot indicator display would have significantly altered the sequence of events that led to the grounding.
Shipboard steering-related emergency procedures also do not typically distinguish between a steering/rudder failure and a rudder angle indicator failure, nor do steering failure procedures include a check to first rule out indicator failure before seeking to restore steering control. In emergency situations, where valuable time may be lost trying to first rule out a rudder angle indicator failure, initiating steering failure procedures and establishing a crew presence in the steering gear room is a reasonable response.
Shipboard working language
Hagen Oldendorff’s bridge logbook documented that the ship’s working languages were ‘English’ and ‘Chinese’.
SOLAS regulations[24] required that a working language be established and recorded in the ship’s logbook and that the crew be able to understand, give orders and instructions, and report back in that language. The regulations also required that English be used as the working language for bridge-to-bridge and bridge-to-shore communications as well as for communications between pilots and bridge watchkeeping personnel (unless they spoke another common language). This requirement was also reflected in the Bridge Procedures Guide,[25] an internationally recognised publication reflecting watchkeeping best practice.
The pilot stated that the master’s command of English was reasonable although the helmsman and third mate’s was less so. VDR audio recorded that the helmsman and third mate’s responses to the pilot’s rudder and main engine orders were intelligible and consistent with standard marine phraseology.
Following the rudder angle indicator failure, communication between the master, third mate and helmsman was predominantly in Mandarin. Furthermore, communications with other crew over hand-held radios and conversations with engineers over the telephone were similarly in Mandarin. Although the master continued to address the pilot and respond to their queries in English, the pilot was unable to understand the operational communications between the rest of the bridge team and between the bridge team and engineers.
SOLAS requirements impose an obligation on seafarers to learn and communicate in English when it may not be their native language. While most seafarers, in particular senior deck and engineering officers, can be expected to have a working knowledge of English, other crew such as ratings may not. During a shipboard emergency, quick, concise and clear communication is required when issuing orders to, or receiving reports from, crew. Under these circumstances, the master, and others in positions of authority, often resort to communicating with crew in the language they comprehend best. While this may optimise crew communications, it can leave the pilot out of the communication loop.
A review of recorded VDR audio did not identify any critical information communicated among the crew and engineers in Mandarin that would have significantly improved the pilot’s mental model of the situation in the limited time before the grounding. However, this does not preclude the possibility that there were other conversations, radio traffic or telephone communications in Mandarin not captured by the VDR that may have been useful to the pilot. While the crew’s use of Mandarin excluded the pilot from the communication loop, it probably did not contribute to the grounding.
Rules and regulations
SOLAS regulations
Regulations for steering gear
SOLAS regulations, specifically Chapter II-1,[26] set out the requirements for ships’ steering gear arrangements. The regulations required that every ship be provided with a main steering gear and an auxiliary steering gear, arranged so that the failure of one will not render the other inoperative. In most merchant ships, including Hagen Oldendorff, the steering gear comprised 2 or more identical power units to meet the requirements for main and auxiliary steering gear.
Steering gear control systems were required to be provided for the steering gear, both on the navigating bridge and in the steering gear compartment. Steering gear control systems were defined as the equipment by which orders were transmitted from the navigating bridge to the steering gear power units and included transmitters, receivers, hydraulic control pumps and their associated motors, motor controllers, piping and cables. Any steering gear control system operable from the navigating bridge had to be equipped with short circuit protection and with audible and visual alarms in the event of an electrical power failure.
SOLAS Chapter V[27] covered the carriage requirements for shipborne navigational systems and equipment. It required that ships of 500 gross tonnage and upwards be provided with rudder indicators or other means to determine and display rudder angle (to be readable from the conning position) and ships of 50,000 gross tonnage and above be provided with a RoT indicator.
The regulations stated that the angular position of the rudder was to be indicated on the navigating bridge and in the steering gear compartment. The regulations also stated that the rudder angle indication systems were to be independent of the steering gear control system.
Code on Alerts and Indicators
The International Maritime Organization (IMO) Code on Alerts and Indicators provided general design guidance to promote uniformity of type, location and priority for alerts and indicators required by SOLAS. The guidance in the Code stated that rudder angle indicators were to be powered from the main source of electrical power and should have an automatic changeover to the emergency source of electrical power in case of loss of normal power supply.
The Code did not require rudder angle indicating systems be fitted with alarms to alert crew to a loss of electrical power.
Classification society rules
Lloyd’s Register rules
SOLAS regulations also required that ships be designed, constructed and maintained in compliance with the structural, mechanical and electrical requirements of a classification society recognized by the Administration.
Lloyd’s Register (LR) rules and regulations for the classification of ships replicated SOLAS requirements for steering gear arrangement, control systems and rudder angle indicators.[28]
LR advised that, while the automatic power supply changeover arrangements outlined in the Code on alerts and indicators was not reflected in the minimum requirements of LR rules, there were optional notations available to shipowners that allowed for increased resilience in navigational systems (including rudder angle indicator systems).
For example, ships bearing the ‘NAV1’ notation were required to have an automatic changeover to an alternative main source of electrical power supply for navigational aids. Similarly, LR advised that the rules for the integrated bridge systems, ‘IBS’ notation could be interpreted to require ships bearing that notation to have each item of electrically operated navigational equipment be individually connected to its distribution panel and that failure of any power supply to the distribution panels were to initiate an audible and visual alarm.
Hagen Oldendorff did not hold the NAV1 or IBS notations, nor was it required to.
Other classification society rules
Different classification societies had different requirements for rudder angle indicator systems. For example, Det Norske Veritas (DNV) rules for some ships included a requirement that the rudder angle indicating system be arranged such that a single failure in power supply or anywhere in the indicating system did not cause loss of rudder angle indication on the bridge.
Summary
Hagen Oldendorff complied with the minimum requirements of the SOLAS regulations and LR classification society rules for rudder angle indicators.
The applicable rules and regulations did not require the ship’s rudder angle indicators be protected against a single point of failure, such as the tripping of the common circuit breaker, which resulted in a loss of electrical power supply to all the indicators. Additionally, they did not require installation of audible or visual alerts to notify the bridge team of a loss of power supply affecting the indicators.
Port Hedland
Introduction
Port Hedland, located in the Pilbara region of Western Australia (WA), is the world’s largest bulk export port, with more than 6,000 shipping movements (inbound and outbound) annually. The port predominantly serves the mining industry of the Pilbara and facilitates an annual throughput of more than 500 million tonnes of cargo.[29] While iron ore is the port’s dominant export trade, its trade base also includes salt, manganese, copper concentrates, livestock, lithium mineral and tourism (cruise ships).
Port Hedland has 19 operational berths. Of these, BHP[30] owns and operates 8 berths while Fortescue Metals Group (5 berths), Roy Hill Infrastructure (2 berths) and the Pilbara Ports Authority (4 berths) own and operate the remaining berths. Port Hedland is the sole export route for the Pilbara iron ore assets of BHP, Fortescue Metals Group (FMG) and Roy Hill Iron Ore.
Port Hedland Channel
The port is served by a 22-mile (40 km) dredged channel that allows a single ship to traverse it at any given time. The 10-mile section of the channel closest to the port is highly confined with insufficient depths immediately adjacent to the channel to allow vessels to exit during an emergency. The channel is also tidally restricted for most laden ships including capesize ships such as Hagen Oldendorff.
These characteristics make the risk associated with a channel blockage significant. Furthermore, given the time between consecutive ship departures, separation distances between ships and depending on where in the channel the ship experiences the failure and founders, there could be up to 3 other vessels committed to, or within the channel, that would also be at risk as the tide recedes.
The Port Hedland navigation channel was divided into 6 zones (Figure 10) based upon navigational or environmental characteristics that would impact the risk within that zone. These characteristics included location, channel alignment, bathymetry, channel slopes and sea conditions.
The channel was divided as follows:
- Zone 1 – the inner harbour and berths
- Zone 2 – the inner harbour and berths to the south-west of zone 1
- Zone 3 – from the outer limit of the inner harbour at Hunt Point to beacons 36-37
- Zone 4 – from beacons 36-37 to 30-31
- Zone 5 – from beacons 30-31 to beacons 15-16
- Zone 6 – from beacons 15-16 to the termination of the channel at beacons C1-C2.
Ships in zones 1 and 2 were generally manoeuvred at low speed, although subject to large tides and currents when manoeuvring or berthed. Depths in the inner harbour were reported to be maintained at about 14.9 m.
In zone 3, the channel is narrow with steep channel batters and the potential for strong currents. This zone features a turn requiring a 71° course alteration into the Goldsworthy section of the channel and water depths outside the channel can be less than 1 m deep at lowest astronomical tide (LAT).
The section of channel in zone 4 is straight but also narrow with steep batters and the water adjacent to the channel is generally less than 6 m deep at LAT. Inbound vessels in ballast generally enter the channel from seaward of beacons 30-31. The channel depth in zones 3 and 4 are reported to be maintained at about 15 m. The transition from zone 4 into zone 5 involves an 18° course alteration into the Newman section of the channel.
The section of channel in zone 5 is relatively straight with a 13° course alteration of course for outbound vessels. The channel batters become significantly shallower from zone 5 onwards and water depths outside the channel are predominantly greater than 10 m with scattered shoal patches.
In zone 6, water depths outside the channel are predominantly greater than 15 m and, in places, exceeds the maintained channel depths which vary between 16.2 m and 18 m. This zone has the added benefit of an emergency passing lane, along the western edge of the channel.
The channel has a minimum width of about 162 m in the Goldsworthy and Newman sections (zones 4 and 5). The batter slope along the channel margins are a significant factor influencing the risk of a ship grounding on the seabed, as opposed to the ship contacting the seabed and being deflected away from the channel batter. Zones 5 and 6 have shallower batter slopes compared to zones 3 and 4. As a result, if a ship grounds in zone 5, the contact area between the ship hull and seabed is larger, making the ship harder to re-float.
The wave conditions in the Port Hedland channel steadily increase from zone 3 through to the end of zone 5, which is generally where the most severe sea conditions are experienced. Wave conditions are generally most severe in December and January, and most mild in July and August.
Hagen Oldendorff grounded on the western side of the channel in zone 4, between beacons 37 and 35 (Figure 3).
Figure 10: Port Hedland channel zones
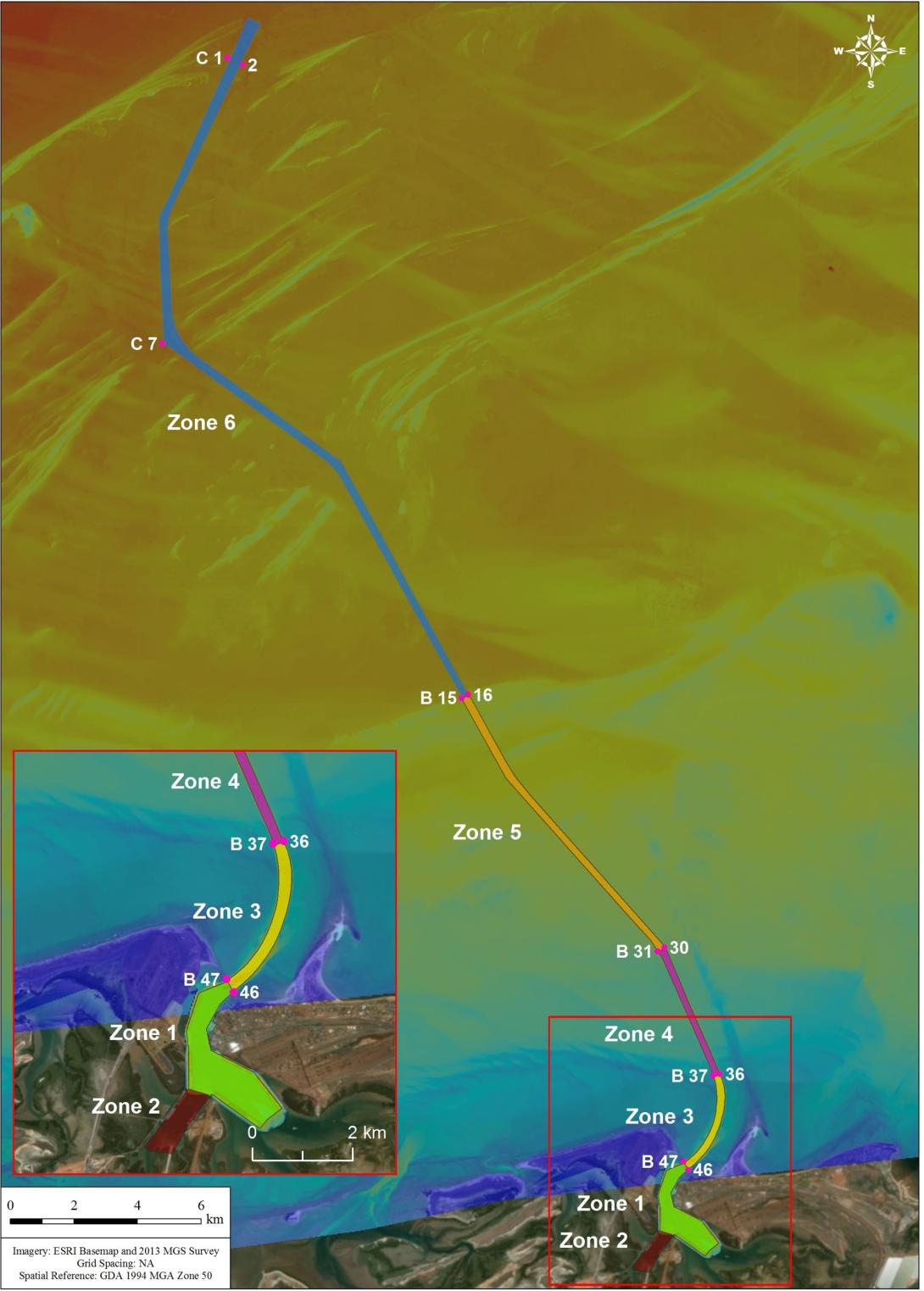
Source: Pilbara Ports Authority
Channel damage
On 11 April 2022, the Pilbara Ports Authority (PPA) commissioned a survey of the area of the channel between beacons 36-37 and beacons 34-35. The survey data identified that Hagen Oldendorff had impacted an area of the western batter about 500 m long (Figure 11) resulting in bank collapses extending between 7–21 m into the channel.
Figure 11: Survey data showing channel batter impact damage
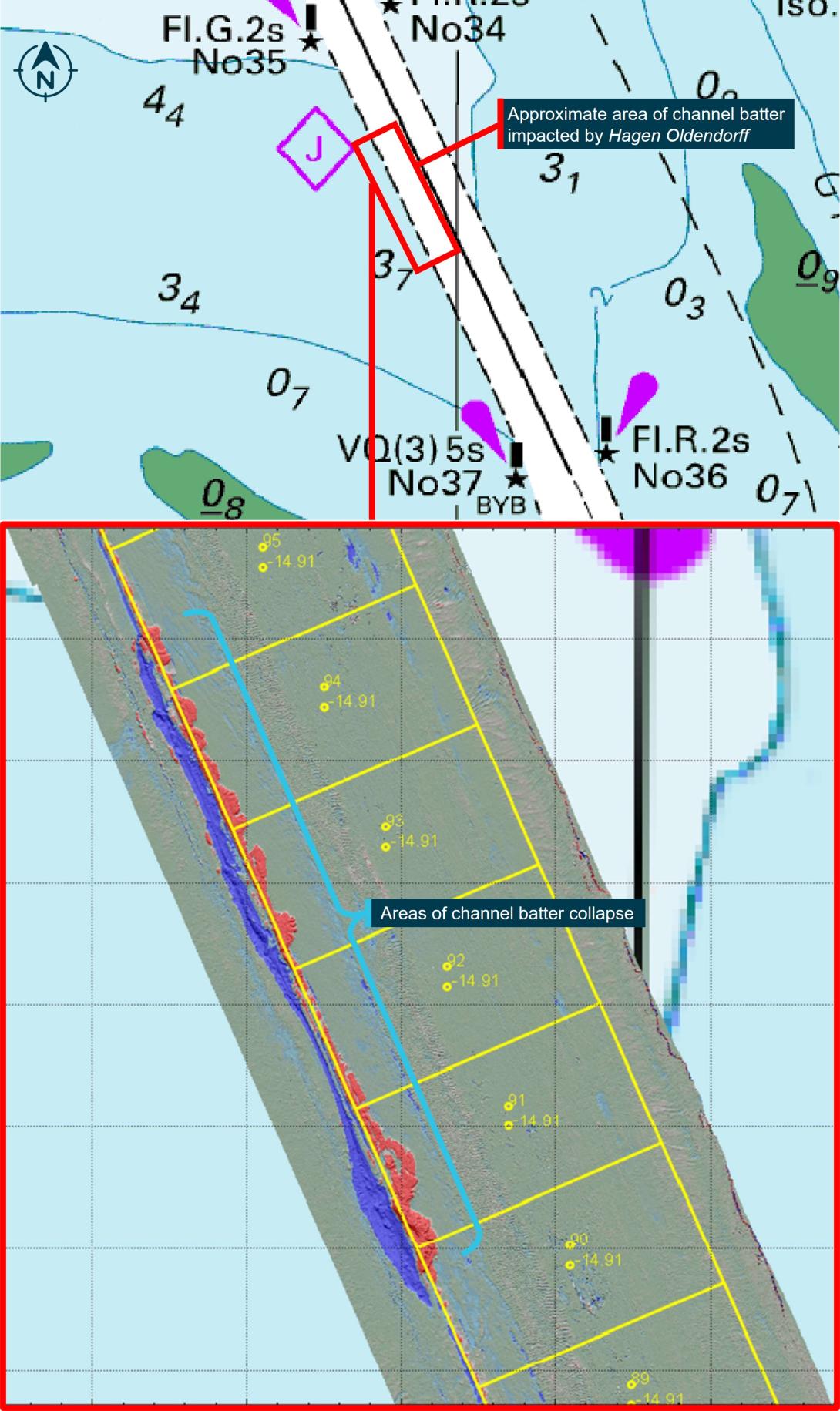
Source: Pilbara Ports Authority, modified and annotated by the ATSB
Management of channel risk
The Pilbara Ports Authority (PPA) (see the section titled Pilbara Ports Authority) maintained a risk management policy and a port strategic risk register (see the section titled Port strategic risk register) to identify and manage risks to the port, including the risk of a channel blockage. In order to effectively manage this risk, the PPA and other major stakeholders, including BHP, invested significant effort to define the drivers of incidents that could lead to a channel blockage and to identify preventative and mitigating controls.
The primary drivers of a marine incident that could contribute to a blockage of the Port Hedland channel were assessed to be main engine failures/slowdowns, steering incidents, mooring failures and hull/structural failures. Of these, incidents arising from main engine failures/slowdowns and steering incidents resulting in a loss of navigational control were assessed as being most likely to result in a channel blockage.
The port’s assessment of past incident and near-miss data showed that engine-related incidents were far more likely than steering incidents but that steering incidents were more likely to result in a channel blockage. A 2019 channel blockage mitigation study by BHP identified that the likelihood of steering incidents was about 0.024% per manoeuvring hour with past incident data indicating an incidence of about 1–2 steering incidents per year. However, the study also acknowledged that there was insufficient information to identify the root causes of these steering incidents and that they broadly included rudder failure, system fault and human error.
A review of the port’s risk register identified that the PPA had several risk controls in place to prevent incidents that could result in a loss of navigational control and to mitigate the risk of a ship grounding or stranding blocking the channel in the event such an incident occurred. These controls included:
- pre-arrival declarations by ships to confirm the operational status of all critical machinery
- testing of emergency engine and steering control systems (such as NFU steering)
- vessel traffic services
- the use of a dynamic under keel clearance system
- vessel quality assurance processes
- incident emergency response procedures
- emergency exercises to train pilots and tug masters
- pilotage
- towage.
Towage in Port Hedland
The tugs in Port Hedland were operated under towage licences granted by the PPA to BHP Towage Services (BHPTS) and Pilbara Marine (a subsidiary of FMG). Rivtow were contracted to operate the tugs under the BHPTS licence, while KOTUG operated tugs under the Pilbara Marine towage licence. Table 1 below outlines the composition of the Port Hedland tug fleet at the time of the grounding.
Table 1: Port Hedland tug fleet
Licensee | Type of tug | Bollard pull (tonnes) | Number of tugs |
BHPTS | Z-Tech | 63 t | 2 |
BHPTS | RT80-32 | 80 t | 5 |
BHPTS | ART80-32 | 80 t | 4 |
BHPTS | RAstar85 | 85 t | 6 |
Pilbara Marine | RT80-32 | 80 t | 1 |
Pilbara Marine | ART85-32W | 85 t | 8 |
The Z-Tech tugs were equipped with 2 azimuth thrusters[31] located aft, each driven by a 1,864 kW main engine in a z-drive configuration.[32] The tugs were designed with a relatively low forward sheer to allow the tugs to work in close proximity under the flare of ship’s bows.
The RT80-32 rotortug used a propulsion arrangement with 2 azimuth thrusters forward and a third azimuth thruster aft in place of the traditional skeg arrangement. Each azimuth thruster was driven by a 1,654 kW main engine in a z-drive configuration.
The ART80-32 advanced rotortug used a similar propulsion arrangement to the RT80-32 but with hybrid propulsion, enhanced manoeuvrability and greater redundancy. The ART80-32 tug’s azimuth thrusters were each driven by a 1,765 kW main engine in a z-drive configuration.
The ART85-32W evolved from the ART 80-32 design and offered a modified hull form for increased stability during escort duties, improved manoeuvrability and higher bollard pull.[33]
The RAstar85 tugs were azimuth stern drive tugs with 2 azimuth thrusters located aft, each driven by a 2,550 kW main engine in a z-drive configuration. These tugs were designed with improved winches and with an increased bollard pull similar to that of the ART85-32W tugs.
Environmental conditions
The prevailing environmental conditions at the time of the grounding were within normal operating parameters for ship movements at Port Hedland.
A PPA monitoring station at beacon 42 recorded conditions at the time of the incident as being south-south-westerly winds at about 6 knots, with a south-south-easterly near-surface current of about 0.45 knots and estimated wave heights of about 0.5 m. The monitoring station further north at beacon 31 recorded southerly winds at about 10 knots, gusting to 14 knots and a south‑south‑easterly near-surface current of about 0.4 knots with estimated wave heights of about 1 m.
Anemometer readings recorded on Hagen Oldendorff’s VDR showed that wind in the inner harbour at the time of the ship’s departure was south-south-westerly at about 6 knots while the wind at the time and location of the grounding was west-south-westerly between 10–12 knots.
Port Hedland escort towage strategy
Background
In 2008, following the grounding of the capesize bulk carrier Iron King in Port Hedland (see the section titled Similar occurrences), the port authority identified that in emergency situations under adverse operating parameters the benefit of the port’s then 65 tonne tugs was marginal, even when fast. With projected increases in ship size and numbers calling at Port Hedland, escort towage was identified as a viable mitigating strategy against channel blockage due to incidents such as Iron King’s grounding.
In 2013, BHP developed a detailed risk framework to quantify the channel blockage risk at Port Hedland and to recommend a mitigation strategy. The study identified adequate escort towage as the most effective strategy. BHP subsequently commissioned Baird Australia to review and assess the towage capacity requirements for Port Hedland. This project included extensive analyses and consultation to determine the size, type and number of tugs necessary to mitigate potential channel blockage incidents. The analyses included:
- physical modelling of vessel grounding at the Council for Scientific and Industrial Research (CSIR) in South Africa
- desktop and full-mission navigation simulations of emergency scenarios involving capesize ships at FORCE Technology in Denmark
- sea trials at Port Hedland.
The physical modelling assessed the outcomes of grounding and contact with the channel batter at various speeds and impact angles. The results indicated that at higher speeds and greater angles of impact, greater damage resulted, and a larger force was required to remove the vessel from the channel batter.
The results of the analyses identified that optimisation of the use and configuration of the port’s existing tug fleet could reduce the impacts of main engine or steering failures of capesize ships during departures. Additionally, data from sea trials indicated that tug towlines were experiencing shock loads of up to 40 t when towing in sea states over 1.5 m. Analysis of the safe working loads (SWL) of bitts[34] on capesize ships showed that the most common SWL was between 65–70 t and that the port’s tugs could generate tow forces well in excess of this value.
The project recommended that BHP invest in tugs with improved escort towage capability (RAstar85 tugs) to further mitigate the risk of channel blockage and, in the meantime, develop and implement an interim escort towing strategy. The port subsequently also mandated an increased SWL for bitts on ships calling at Port Hedland.[35]
Interim escort towing strategy (2013)
The interim escort towage strategy provided guidance to optimise the use of the port’s existing Z‑Tech and RT80-32 tugs while the RAstar85 tugs were built. The number of tugs and their configuration were based on the channel zone that the ship was navigating in. The tug arrangements recommended as part of the interim strategy for departing capesize ships in zone 3, zone 4 (where Hagen Oldendorff grounded) and zone 5 were:
Zone 3
An RT80-32 tug was to be tethered to the stern of the ship and a Z-tech or RT80-32 tug tethered to either shoulder of the vessel. All tugs were to remain tethered to the ship until beacons 36-37.
The escort tug utilisation procedures in the event of an emergency (such as a steering failure) in zone 3 called for the pilot to initially use the main engine and the 2 tethered shoulder tugs as a brake, to reduce the ship’s speed. The aft tug could then be used in the indirect towing mode to control the RoT and, once the ship was under control, to provide steering forces to conduct the ship to a safe location.
Zones 4 and 5
In zones 4 and 5, an RT80-32 tug was to be tethered to the stern of a departing ship until beacons 15‑16 with an untethered tug (a Z-Tech or RT80-32 tug), off either the port or starboard quarter.
The procedures in the event of a steering failure in zones 4 or 5 were largely dependent upon the prevailing sea state, specifically, the significant wave height (Hs).[36] The conventional (static brake) winches installed on board the Z-Tech and RT80-32 tugs generally resulted in a reduction in effective towline force as sea states increased. Additionally, actively operating tugs with such conventional winches in moderate sea states presented safety hazards for the tug and crew.
When wave heights were less than 1 m, the pilot was to use the tethered aft tug in indirect towing mode to control the ship’s heading and then slow the ship to allow the passive escort tug to make fast at the bow. In wave heights between 1 m and 1.5 m, the aft tug was to initially provide indirect braking forces only (to avoid shock loading of the towline) until the ship had been slowed sufficiently to apply direct steering forces.
Once the vessel’s heading was controlled and the ship’s speed was less than 6 knots, the passive escort tug could be tethered at the bow. In wave heights above 1.5 m, the aft tug was to provide whatever assistance was deemed possible by the tug master until the ship’s heading was controlled, and speed reduced to less than 6 knots, when the passive escort standby tug could be made fast at the bow.
Other measures and outcomes
Other key measures recommended as part of the interim strategy included:
- restricting ship speeds to 8 knots when tugs were made fast
- ensuring pilots and tug masters were aware of the SWL of the aft towing bitts
- implementing indirect towing training programmes for tug crews.
Following implementation, the effectiveness of the interim escort towing strategy was reviewed and evaluated. After further studies and simulations, the specifications for the proposed RAstar85 tugs were refined. In September 2014, further simulations were undertaken to assess various tug configurations using the anticipated RAstar85 tug in the active escort role tethered aft of the ship.
The simulations identified that a single escort tug tethered aft, and a tug tethered to each shoulder of the ship, was the preferred configuration in zones 3 and 4. A final design for the new tugs was submitted for construction tender in October 2014.
Escort towage strategy (2015)
Introduction
In June 2015, construction of the new tugs and a new tug harbour in Port Hedland was approved. As part of the tug and tug harbour project, BHP developed an escort towage strategy to ensure that the future RAstar85 tugs were operated in conjunction with the existing tugs in a manner that would most effectively mitigate the risk of channel blockage from capesize ships. Additionally, BHP added 4 new ART80-32 tugs to the Port Hedland fleet that same year. The ART80-32 tugs were equipped with an improved sea-keeping and rendering winch with the capability to provide effective towage in sea states up to 1.5 m.
The BHP escort towage strategy (2015), developed by Baird Australia, documented the procedures, guidelines and tug allocations developed as an outcome of the various studies, simulations, exercises and consultation conducted as part of tug and tug harbour project and channel blockage risk mitigation initiatives. The document noted that the guidelines were developed with input from the PPA and Port Hedland Pilots (PHP), among others, and that adopting these guidelines could materially reduce the risk of a ship grounding and blocking the channel at Port Hedland.
The strategy required that, while tugs were tethered to the ship, the ship’s speed should not exceed 8 knots, and the ship was to be maintained on a track as close to the centreline of the channel as possible.
The document noted that, in the event of an emergency scenario, such as a rudder or engine failure, minimising the time between the onset of the emergency and the recognition and initiation of procedures by the pilot (stopping the ship’s engine and issuing commands to the tugs) was of extreme importance. In particular, it emphasised that measures to quickly assert control over the RoT of the ship was key to a successful outcome.
The strategy defined the following specific tug allocation guidelines and escort towing procedures for outbound capesize ships in zones 3 and 4:
Zone 3
A RAstar85 tug was to be made fast aft with a Z-Tech, RT80-32 or ART80-32 tug fast on each shoulder.
During an emergency in zone 3, the vessel’s speed was to be reduced using the main engine astern and the shoulder tugs to pull back and provide a braking force. To control the RoT, the aft tug was to rapidly move into the required position and apply an indirect steering force. Once the RoT was controlled and the ship was aligned parallel to the channel batter, the aft tug could be used to provide further braking forces. Once the vessel was fully under control, and the speed less than 4 knots, the shoulder tugs could be used to manoeuvre the vessel towards the channel centreline, while the aft tug provided steering forces, as required.
Zone 4
The guidelines stated that a RAstar85 tug may remain tethered aft if required to provide steering forces. Additionally, providing sea conditions were suitable, the shoulder tugs were to remain tethered to the ship to provide braking forces or to tow a disabled ship to safety. The shoulder tugs could be cast off at the end of zone 4 (beacons 30-31) and one of the tugs dismissed with the other retained as a passive escort at the bow through zone 5.
In the event of a steering emergency in zone 4 in sea states less than 1.5 m, the aft tug was to rapidly move into the required position and apply an indirect steering force while the shoulder tugs were used as a brake. Once the vessel’s heading was controlled, the pilot could use the aft tug to further reduce the speed to less than 6 knots, allowing the shoulder tugs to move to a towing position.
The shoulder tugs could then tow the vessel to a suitable anchorage, or to the end of the channel, while the aft tug provided steering forces. The strategy document noted that the RAstar85 tugs should be able to effectively perform the same manoeuvres in sea states greater than 1.5 m, although the tug masters of the shoulder tugs would need to determine whether they could remain tethered during moderate sea conditions and the extent of the assistance possible.
Summary
The strategy recommended that, for all sea states up to 3 m, a RAstar85 tug remain tethered to the stern of departing capesize ships until beacons 15-16 (end of zone 5). Between Hunt Point and beacons 30-31 (zones 3 and 4), tugs were to be tethered to both shoulders and, under normal conditions, both these tugs could be cast off at beacons 30-31 (end of zone 4), with one dismissed and the other retained as a passive escort until beacons 15-16 (end of zone 5). At beacons 15-16, both the active escort tug aft and the passive escort tug could be dismissed. Ships were not generally escorted in zone 6, except in the case of an emergency or if the ship was deemed to require escort towage until clear of port limits.
Implementation of the escort towage strategy
In 2016, a risk review was undertaken to assess the potential to further reduce the risk of, and impacts associated with, a channel blockage at Port Hedland. The study identified several initiatives to be explored for further channel risk mitigation namely:
- engineering controls, such as channel modifications and the possibility of a bypass channel
- operational controls, such as further towage improvements and mitigation plans to restore partial channel capacity in the event of a channel blockage.
In 2017, the Port Hedland working group (PHWG) was established with representatives from the PPA, BHP (and their technical representative - Baird Australia), PHP and other stakeholders, to review channel blockage risk, identify new risk management options and evaluate ongoing controls. That same year, the new tug harbour at Hunt Point and new RAstar85 tugs became operational with the first 2 tugs delivered in April 2017. The RAstar85 tug was equipped with a render/recover winch,[37] designed to be capable of performing the necessary indirect towing manoeuvres in sea states up to 3 m.
Following the introduction of the RAstar85 tugs in 2017, the recommended guidelines in the escort towage strategy began to be trialled and implemented to various degrees.
By April 2018, the BHPTS tug fleet at Port Hedland comprised 6 RAstar85 tugs, 4 ART80-32 tugs, 7 RT80-32 tugs and 2 Z-Tech tugs.
On 23 September 2019, during a PPA forum titled ‘Safe Ships – Safe Ports’, a BHP presentation titled ‘Best Practice Towage Standards’ stated:
The Port continues to work in a collaborative way with Pilots and Towage to find operational improvements that can be implemented without significant cost or investment.
Trials for enhanced escort towage include:
- Shoulder tugs being kept fast to B30/31 (where possible)
Similarly, on 18 November 2019, at a quarterly strategic review meeting of the BHP towage license, covering the quarter from August to October 2019, under the heading Continuous improvement – Channel risk reduction trials’, the meeting minutes recorded the following:
Shoulder tugs remaining fast to B30/31
- No concerns have been raised during the quarter and this is being achieved where conditions are favourable.
Updated escort towage strategy (2020)
Introduction
In July 2020, BHP consolidated and updated the escort towage strategy into a stand-alone document titled ‘Escort Towage Strategy – Port Hedland Working Group’. The document’s stated intent was to present information and guidelines related to escort towage at Port Hedland and to assist the PPA, pilots, tug masters, towage operators and other stakeholders to understand the rationale for escort towage and provide guidelines to support effective escort towage operations.
The document noted that the strategy had been updated to reflect current and potential future escort towage practices as a result of a number of enhancements in the port’s towage capabilities, including:
- completion of BHP’s tug and tug harbour project and commencement of operation of the RAstar85 tugs
- commencement of Pilbara Marine’s towage under the FMG towage licence, including the use of the ART85-32W tugs
- improvements in tug master training and competency assessment
- incremental enhancement to escort towage practices led by the PPA, pilots, tug masters and towage operators
- increased knowledge, escort towage performance information and development of improved escort towage guidelines through the work completed to date by the PHWG on channel blockage risk.
Objectives
The strategy document’s listed primary objectives, among others, were to:
- provide a summary of the drivers behind escort towage at Port Hedland, which is to assist an escorted ship to maintain manoeuvrability and navigate within water of sufficient depth to prevent a ship grounding, and the potential consequential impact of channel blockage
- document escort towage procedures that have been identified as effective at preventing a ship grounding and potential channel blockage through research, simulation and on-water trials.
The document noted that escort towage was a critical mitigative control to prevent a ship grounding in Port Hedland and that steering- or main engine-related incidents resulting in loss of navigational control were the likely causes for a grounding incident leading to channel blockage.
Escort tug fleet
The updated towage strategy stated that the primary escort-capable tugs at Port Hedland were the RAstar85 tugs (6) and ART80-32 tugs (4) operated by Rivtow, and the ART85-32W (8) tugs operated by KOTUG. It also noted that, of these tugs, the RAstar85 tugs and the ART85-32W tugs were the primary aft active escort tugs for laden capesize ships.
Tug allocation guidelines
The escort towage strategy document stated that the most up-to-date information on tug allocations were those in the Port of Port Hedland - Port User Guidelines and Procedures available on the port’s website (see the section titled Pilbara Ports Authority).
The strategy largely replicated the tug allocations outlined in the 2015 escort towage strategy.
Zone 3
It stated that, in zone 3, laden outbound ships would typically require 3 tugs and that the primary escort tug aft was to be the most capable tug asset available for the ship movement. It stated that the other 2 tugs should have their towlines tethered on the port and starboard shoulders of the ship prior to, and throughout zone 3, except where weather or other conditions made it unsafe to do so (Figure 12).
The strategy document noted that, in the event of a steering incident, navigation simulations had consistently demonstrated that pilots should initially instruct the aft escort tug to provide steering forces to counteract the rudder and control the heading before considering using the aft tug to provide braking forces to reduce speed. The shoulder tugs were to initially be used to provide braking forces and as ship’s speed reduced to less than 4 knots, the shoulder tugs could be used to control the ship’s bow.
The escort strategy emphasised that the shoulder tugs should maintain their towlines tethered as long as they could safely do so depending on the prevailing sea state. It also stated that, in all emergency scenarios in zone 3, having the shoulder tugs with their lines tethered was preferable so the tugs could immediately provide braking forces and assist with controlling the ship’s bow.
Zone 4
The towage strategy stated that the tug allocation in zone 4 was the same as zone 3 (Figure 12). Similarly, the escort towage procedure in the event of a steering incident in zone 4 was largely identical to that in zone 3, although the strategy noted that the channel was straight but narrower in zone 4 with ships generally making way at a higher speed (7–8 knots).
Importantly, the escort strategy stated that:
The shoulder tugs should maintain their towlines tethered as long as they can safely do so depending on their exposure to the prevailing sea state and interaction with the ship.
It also stated:
In all emergency scenarios in Zone 4, having the shoulder tugs with their lines tethered is preferable so that they can immediately provide braking forces and also be positioned to assist with controlling the position of the ship’s bow when the speed of the ship reduces.
Figure 12: Recommended tug configuration for capesize ships in zones 3 and 4
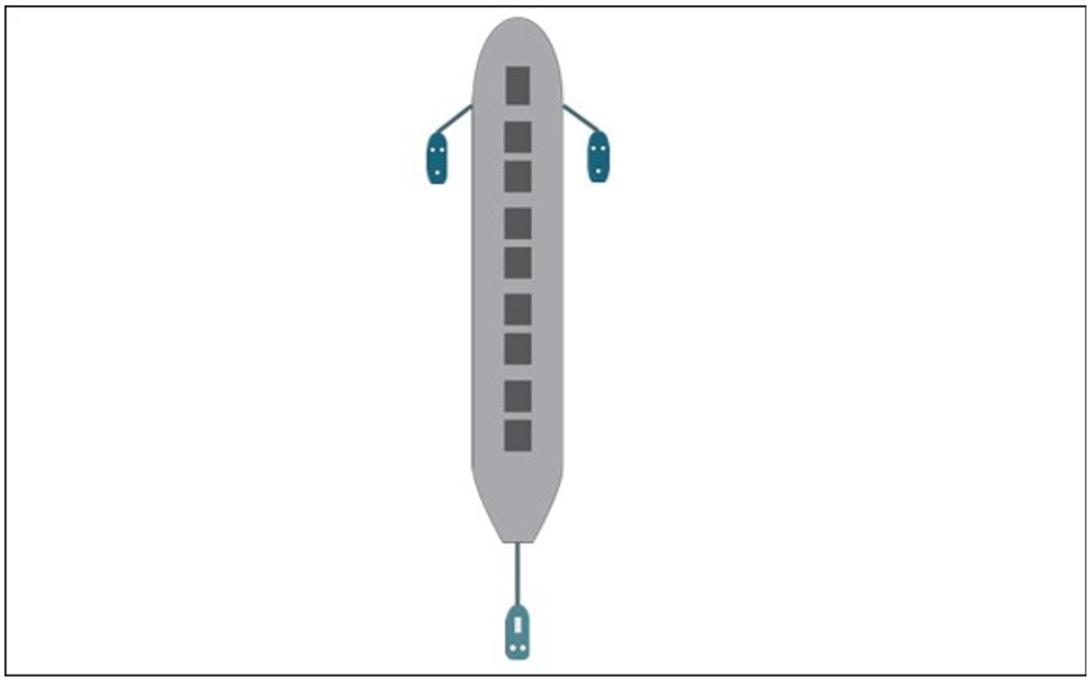
Source: BHP, modified and annotated by the ATSB
Stakeholder actions
The escort towage strategy directed the following actions, among others, be implemented by the key stakeholders involved in executing the strategy:
- Pilots to adopt the recommended escort tug configuration as presented in the strategy and use the escort tugs appropriately during emergencies
- Tug masters to seek towage practice opportunities and continually improve towing techniques
- Pilots and tug masters to conduct regular emergency training simulator sessions
- PPA to monitor pilot and towage operator competency and performance and conduct ongoing reviews of operating procedures and guidelines to support best practice pilotage and towage operations.
BHP subsequently submitted the escort towage strategy document to the PPA for review and official endorsement (see the section titled Pilbara Ports Authority).
BHP towage scheduling guidance
The BHP towage scheduling guidelines directed that the ideal tug allocation for an outbound ship was to assign an RAstar85 tug as the active escort tug aft and ART80-32 tugs for the shoulder tugs. However, the guidelines also acknowledged there would be exceptions and circumstances when the ideal allocation could not be achieved (for example, assignment to other ships, unplanned maintenance or tug crew training and availability). Under those circumstances, ART80‑32 tugs could be used as active escort tugs and RT80-32 tugs could be used as passive escorts.
Hagen Oldendorff’s aft active escort tug, RT Clerke, was an ART80-32 tug. At interview, the ship’s pilot advised that while it was unusual not to be assigned a RAstar85 tug for the aft active escort role, they were satisfied that the assigned tugs were adequate for the pilotage.
Table 2 below details the specifications of the 4 tugs assigned to Hagen Oldendorff on the morning of the grounding:
Table 2: Hagen Oldendorff's tugs
RT Clerke |
RT Atlantis |
RT Inspiration |
RT Darwin |
|
Type of tug |
ART80-32 |
ART80-32 |
RT80-32 |
RT80-32 |
Bollard pull (t) |
80 |
80 |
80 |
80 |
Position deployed |
Stern |
Starboard shoulder |
Port shoulder |
Starboard quarter |
BHP stated that RAstar85 tugs and ART80-32 tugs were both routinely deployed as the aft active escort tug for capesize ship movements. BHP advised that the capabilities of both tug types were largely similar in the relatively moderate sea conditions prevailing on the night and that the improved escort performance of the RAstar85 tugs was only significant on those days when sea and wave conditions in the channel were particularly adverse.
BHP also advised that both tug types were certified for open water escort with on-water escort performance notations (EPN) issued by Lloyd’s Register (see Appendix B) and that all 4 assigned tugs and their crews were appropriate, capable and experienced. Furthermore, during the indirect towage training, when RT Clerke was being used to assist Hagen Oldendorff’s turn in the channel, the tug master reported generating tow forces of up to 81 tonnes. This was not significantly different to the maximum bollard pull of the RAstar85 tugs and therefore, it is unlikely that the allocation of a RAstar85 tug for the aft active escort role would have resulted in a significantly different outcome on the night.
Escort towage performance
RT Clerke
Following the rudder indicator power failure, the pilot ordered RT Clerke to apply indirect steering force to pull the stern to starboard. RT Clerke’s master acknowledged the order and set about manoeuvring the tug to the starboard quarter. About 30 seconds later, the tug passed astern of the ship to starboard and although not in its optimal towing position probably started applying some tow force. The tug’s approximately 30-second transition time from the port quarter across the ship’s stern to the starboard side was reasonable, within the observed response times in BHP and the port’s towage studies’ sea trials.
Similarly, when the pilot ordered RT Clerke to take the stern to port, the time for the tug’s transition from the starboard quarter until it crossed the ship’s stern to the port side and began applying tow force was about 38 seconds. The tug was in its optimal towing position and likely applying full indirect steering forces on the port quarter about 20 seconds later.
Following the ship’s impact with the channel batter, the pilot ordered RT Clerke to pull the stern to starboard. However, RT Clerke’s master did not immediately acknowledge the pilot’s order and continued pulling the stern to port possibly because they did not hear the VHF transmission, or because they were focused on the task at hand. About a minute later, the pilot ordered RT Clerke to stop applying any force, which the tug master then acknowledged. The ship was recovered to the centre of the channel and stabilised shortly after and therefore, it is unlikely that the brief period when RT Clerke continued to pull the stern to port unduly increased risk.
RT Inspiration
About 30 seconds after the power supply to the rudder angle indicators failed, the pilot ordered RT Inspiration’s master to make fast again. As the tug master and ship’s crew worked to reconnect the tug, the pilot ordered RT Inspiration to ‘push full’ on the ship’s port bow. The tug master acknowledged the order and immediately began pushing. RT Inspiration continued pushing on the ship’s port side until about 20 seconds after the ship struck the channel batter when the pilot ordered the tug to stop. Hagen Oldendorff’s master informed the pilot that RT Inspiration was made fast at 0141, just over 2.5 minutes after the pilot’s order to make fast. This was a reasonable response time and less than then the average time to make fast (3 m 52 s) observed in BHP and the port’s towage studies’ sea trials.
RT Atlantis
About a minute after the indicator failure, the pilot ordered RT Atlantis to make fast on the starboard bow. However, before the tug could be made fast, the pilot ordered RT Atlantis to move to the starboard quarter and push. About 40 seconds later, as RT Atlantis was getting into position, the pilot ordered the tug to ‘push full’ on the starboard quarter. About 10 seconds later, the tug was in position and pushing. The tug continued to push until ordered by the pilot to stop and make fast on the starboard bow shortly after the ship struck the batter. The time taken by the tug to transition from the starboard bow to get into its optimal position to push on the starboard quarter was just under 1 minute.
Pilbara Ports Authority
The port of Port Hedland is managed by the Pilbara Ports Authority (PPA),[38] which has overarching responsibility for safety and efficiency of port operations and the environment under the Western Australia state legislation. The jurisdictional responsibilities of the PPA are exercised through the designated port harbour masters.
Port Hedland operated a vessel traffic service (VTS) delivering information, advice and instructions to vessels, including scheduling, berthing and pilot transfer information. The port also operated a dynamic under keel clearance (DUKC) system to optimise cargo loading and determine sailing windows.
The PPA published several documents providing information and guidance on port operations and shipping movements. These included:
- Port of Port Hedland – Port User Guidelines and Procedures
- Port of Port Hedland – Vessel Movement Protocols
- Port Handbook.
The latter 2 documents both directed port users to the port user guidelines and procedures as the authoritative document regarding shipping movements and towage requirements.
Port user guidelines and procedures
The port user guidelines and procedures document was intended for use by all personnel and organisations engaged in shipping and provided guidelines governing the movement of vessels at the Port of Port Hedland. The PPA had the statutory authority to give effect to these guidelines and procedures within port limits.
The document included a section on tug allocation and towage strategy. The document advised that vessels departing the Stanley Point berths (where Hagen Oldendorff departed from) required a minimum of 4 tugs. The procedures stated that a dedicated active escort tug was to be positioned and secured aft for all departing deep-draught capesize vessels from the berth to beacons 15-16 (end of zone 5). It also stated that a dedicated passive escort tug may be positioned forward for all departing deep-draught capesize vessels from the berth to beacons 15‑16.
The port procedures provided no further detail on the disposition, retention or use of the escort tugs.
Port strategic risk register
The port strategic risk register was formally reviewed on an approximately biannual basis by the port strategic risk review committee, which included representatives from the PPA, BHP, FMG, PHP and the towage providers. Channel blockage was an identified risk in the register with several associated risk controls documented including the escort towage strategy.
The risk register documented that a business continuity plan (BCP) for channel blockage was first added as a proposed risk control in May 2018. In June 2019, a risk treatment action plan was added to the register relating to the channel blockage aspect of business continuity and in November 2019, the register noted that the PPA harbour master had presented the BCP to the committee.
A review of records of minutes of the port strategic risk review committee from 2020, 2021 and 2022 showed that the channel blockage risk and associated risk controls, including the BCP, were a common subject of discussion.
Business continuity plan (2020)
In May 2020, the PPA issued a document titled ‘Port of Port Hedland Business Continuity Plan for Channel Blockage.’ The business continuity plan (BCP) outlined the port’s risk management approach for channel blockage. It was intended as a summary document that provided information, options and recommendations to maintain continuity of operations in the event of a channel blockage and to guide ongoing preparedness for such an incident. The BCP noted that, in addition to a large array of information prepared by the PHWG, the BCP also utilised technical information from the various studies, simulations and trials conducted by BHP as part of the tug and tug harbour project and the development of the escort towage strategy.
The BCP reiterated risk assessment evaluations from previous studies, which confirmed that main engine slowdowns/failures and steering incidents that result in a loss of navigation control were the most likely incidents that could result in a channel blockage. It also stated that historical incident data and simulations indicated that the time available to respond to a steering incident and prevent a ship grounding was typically 60–90 seconds, if the escort towage risk controls were not implemented.
The BCP noted that there were 2 primary mitigating risk controls in the event of a ship control failure in the channel – shipboard emergency response procedures (initiated by the pilot and ship’s crews) and the tug fleet at Port Hedland.
The BCP also stated that work completed by the PPA and the PHWG had identified a number of opportunities to further reduce the risk of channel blockage. Among these measures, the BCP identified improvements in towage procedures and stated the following as a ‘recently implemented towage practice’:
In Zone 4, improvement in towage for inbound and outbound ship movements has been implemented. For outbound ship movements, tugs are tethered to each shoulder of the ship with their towlines remaining attached thru to B30/31, whenever possible. In so doing, simulations have indicated that the effectiveness of the deployed tug fleet improves, and Pilots have more options to manage ship control failures, including engine and rudder failures. In some moderate sea state conditions, certain tugs within the fleet may not be able to maintain their towlines on the windward side of the ship; however, for the majority of ship movements, shoulder tugs should be able to maintain their towlines to B30/31.
In the event of a channel blockage, the BCP stated that the PHWG had identified 2 options to provide partial business continuity – the development of a shallow water bypass channel and a slow speed passing of a grounded ship. The BCP documented considerations of the feasibility of the 2 options and identified further actions and recommendations to support the development and future implementation of these options.
Draft escort towage strategy (2020)
Following BHP’s submission of the escort towage strategy to the PPA in July 2020, the entire contents of the document was transferred to a PPA document template. This ‘draft’ PPA escort towage strategy document did not progress further and remained in draft format at the time of the Hagen Oldendorff grounding.
During the ATSB investigation, the Port Hedland harbour master acknowledged receipt of the BHP escort towage strategy but advised that it remained a draft PPA document. The harbour master stated that towage allocation and strategy was to be conducted as directed by the port user guidelines and procedures and the BCP. The harbour master advised that, while pilots retained operational discretion, the contents of the BCP required that the shoulder tugs be kept fast until beacons 30-31 unless prevented from doing so due to environmental conditions.
Port Hedland Pilots
Provision of pilotage services
Port Hedland Pilots (PHP) was established in 1995 and were contracted by the PPA to provide pilotage services in Port Hedland. The individual pilots were employed by PHP and licensed by the PPA. The PHP contract with the PPA provided for 14 permanent pilot posts, with 2 pilots employed to fill each post, for a total strength of 28 pilots. PPA consideration and approval for additional pilot posts was contractually linked to projected shipping movements and the PHP fatigue risk management plan.
PHP typically maintained 14 pilots in Port Hedland at any given time to provide pilotage services, although the actual number available for duty could be less due to pilots being away for training or due to delays in filling posts of pilots who had retired or resigned or due to other circumstances.
Pilots typically worked a 4‑week duty period in Port Hedland followed by 4 weeks off and most pilots, including the incident pilot, operated on a fly-in-fly-out basis.
The pilot
The pilot on board Hagen Oldendorff had about 14 years’ sea going experience prior to taking up the role of a pilot in 2004. They had worked as a pilot in several ports around Australia, before joining PHP in 2015 and obtaining their unrestricted pilots license in 2018. At the time of the occurrence, the pilot held an Australian master’s certificate of competency, an unrestricted pilot’s licence for Port Hedland and had conducted over 1,700 ship movements in the port.
The pilot had commenced a 4-week duty period in Port Hedland on 28 March 2022, 10 days before the Hagen Oldendorff grounding.
Fatigue
As outlined in Appendix C, the ATSB conducted a detailed analysis of the potential for pilot fatigue to have contributed to this serious incident. In summary, while there were factors that potentially reduced the pilot’s ability to obtain sufficient, restful sleep of the required quality, there was insufficient evidence to establish that the pilot’s sleep quantity and quality was impaired to the point where they were likely experiencing a level of fatigue known to have an effect on performance.
Safety management system
PHP operated under an SMS as a condition of the pilotage services contract with the PPA.[39] The SMS comprised various policies, procedures and forms relevant to PHP operations including procedures related to passage planning, conduct of towage and emergency procedures.
Passage planning procedure
The SMS procedure on passage planning was aimed at ensuring that all pilots met a minimum standard for pilotage passage planning. The procedure covered considerations for planning the ship movement, the content of the master-pilot information exchange and procedures for the pilotage transit, which stressed the importance of bridge resource management and communications.
The passage planning procedure did not include any specific guidance or direction on the disposition, retention or use of towage assets. It directed pilots to refer to the port’s towage requirements, PPA guidelines and relevant marine notices on pilotage in Australia.[40]
Towage procedures
The SMS included several procedures on the subject of towage including the following (with the procedure’s approval date in brackets):
- Towage requirements (28 December 2016)
- Making tugs fast (1 July 2019)
- Tug escort towage requirements (1 July 2019)
- Indirect towage procedure (1 July 2019).
The SMS procedure titled Towage requirements stated that the harbour master advised tug requirements for different vessel categories and directed pilots to the PPA’s port user guidelines and procedures. It also stated that pilots should:
Maintain tugs in the position where they are most likely to be of greatest effect in the event of likely emergency situations.
Similarly, the procedure titled Making tugs fast directed pilots to:
Keep tugs fast for as long as it is safe for the tug to do so depending on environmental conditions, speed, and the particulars of the vessel. For capesize vessels the port’s recognised escort towage strategy should be adhered to.
The procedure titled Tug escort towage requirements covered the general procedures relating to escort towage. On the subject of capesize ship departures, the procedure stated that a RAstar85 tug (or an ART80-32 tug if a RAstar85 tug was unavailable) should be made fast aft and used in the active escort role until beacons 15-16. The procedure also stated:
One tug to be made fast on either shoulder in a position that is suitable for laying back alongside, i.e. two tugs fast forward. The shoulder tugs are to be kept fast until at least beacon 36/37 weather/sea conditions permitting.
The procedure also directed pilots to maintain the ship’s speed below 7 knots when the shoulder tugs were fast and less than 8 knots when the aft active escort tug was fast.
The Indirect towage procedure acknowledged the importance of pilots and tug masters practicing indirect towage during ship arrivals and departures to maintain competence. The procedure covered the circumstances under which indirect towage practice could take place and communication procedures for use during the practice. It stated that indirect towage practice could take place during the transit from the inner harbour to beacons 30-31 and between beacons 23-24 and beacons 15-16. It also required pilots to advise ship masters of the intention to conduct indirect towage practice, and to provide masters with an indirect towage notice form. The form identified the environmental parameters under which towage practice could occur, confirmed that the SWL for bitts and leads was adequate and directed the master to advise the pilot if there were any concerns.
There was no evidence that the pilot issued the indirect towage notice form to Hagen Oldendorff’s master. However, it is almost certain that the master was aware that indirect towage practice was taking place and did not object to it. Furthermore, Hagen Oldendorff’s aft bitts complied with the port’s SWL requirement of 120 t. Therefore, it is unlikely that the pilot’s oversight in not issuing the indirect towage practice notice to the ship’s master unduly increased risk.
Emergency procedures
The SMS included emergency procedures for various scenarios including groundings and steering failures.
The emergency procedure for a steering failure directed pilots to:
- inform VTS
- notify tugs in attendance and direct them as required
- call for additional tugs
- consider stopping the main engine and consider indirect towage
- check that crew were standing-by at anchors and following their emergency steering procedures
- look for a suitable anchorage or berth to avoid blocking the channel.
The emergency procedure for a ship grounding directed pilots to:
- inform VTS and any other affected vessels
- notify tugs in attendance, make fast and direct them as required
- call for additional tugs
- check that crew were standing-by at anchors and sounding spaces to determine damage
- have a tug or other vessel check for external damage and report ship’s drafts
- confirm which navigation and propulsion equipment was still functioning
- look for a suitable anchorage or berth to avoid blocking the channel (if the ship was still afloat or could be refloated).
About 2 minutes after the indicator failure, the pilot made a broadcast on the port’s working channel (VHF channel 12), which stated, ‘Port emergency. Rudder failure. Not looking good’. The pilot’s declaration of a port emergency did not specify the ship’s name, which prompted the duty vessel traffic services operator (VTSO) to issue a query, addressed using the pilot’s initials, to verify the origin of the broadcast. In response to the VTSO’s query, the pilot on board KN Amethyst,[41] an outbound ship ahead of Hagen Oldendorff, confirmed that it was Hagen Oldendorff’s pilot who had declared the port emergency. The VTSO subsequently broadcast a call directed to all ships advising that the pilot required assistance near beacon 35 and directed any available tugs to respond. At about the same time, Hagen Oldendorff struck the channel batter.
The pilot’s actions following the loss of rudder angle indication was broadly consistent with the emergency response procedures in the SMS for a steering failure (see the section titled Response to the rudder angle indicator failure). There was no specific emergency procedure for a rudder indicator failure. Similarly, the pilot’s actions following the grounding were largely consistent with the associated procedure in the SMS.
Implementation of the escort towage strategy
The pilot ordered both Hagen Oldendorff’s shoulder tugs to cast off their towlines before the ship had passed beacons 36-37. Table 4 below sets out the time when the tugs were ordered to cast off, when their towlines were recovered and the respective locations of the ship at the time.
Table 4: Hagen Oldendorff tug release times and locations
Time |
Event |
0133:30 | Pilot orders RT Atlantis to cast off towline (Ship’s bow abeam of beacons 38-39) |
0135:00 | Ship’s stern clear of beacons 38-39 |
0135:41 | RT Atlantis master confirms towline recovered (Ship about midway between beacons 38-39 and 36-37) |
0135:45 | Pilot orders RT Inspiration to cast off towline (Ship’s bow approaching abeam of beacons 36-37) |
0137:32 | Ship’s stern clear of beacons 36-37 |
0137:42 | CCTV footage from RT Inspiration shows towline cast off and being recovered on board the tug |
0137:49 | Rudder angle indicator circuit breaker trips and rudder angle indication lost |
0138:18 | RT Inspiration master confirms towline recovered |
0140:34 | Ship grounds about 4 cables south-east of beacon 35 |
At interview, the pilot stated that the decision on where to cast off the shoulder tugs depended on several factors but was essentially at the discretion of each individual pilot. The pilot advised that their standard practice on outbound ships was developed over time and entailed having the shoulder tugs fast until about (or just before) beacons 36‑37. Both shoulder tugs would then be retained as a passive escort until beacons 30-31 when one would be dismissed and the other retained until beacons 15-16 when both remaining tugs (the passive escort tug forward and the aft active escort tug) would be dismissed.
Interviews with other pilots indicated a general consensus that decisions on tug retention and utilisation were largely at their discretion, with pilots variously casting off the shoulder tugs between beacons 38-39 and 30-31. While several of the interviewed pilots, including the incident pilot, expressed a general awareness the escort towage strategy and its recommended practices, they did not believe there was an obligation to comply with it. There was only a limited awareness of the BCP or of its contents among the interviewed pilots.
Check pilotage
The PPA undertook annual audits of pilots which took the form of a check pilotage and involved a PPA representative (usually the harbour master or a deputy harbour master) accompanying and observing the pilot’s conduct of a pilotage task. The pilot’s performance was assessed against several criteria and documented in a marine pilot audit form. The performance criteria included application of bridge resource management, clarity of conning orders and the management of tugs, among others.
A review of Hagen Oldendorff’s pilot’s check pilotage forms for 2020, 2021 and 2022 showed that they consistently performed satisfactorily with respect to the relevant performance criteria. The 2020 check pilotage involved an outbound ship movement while the 2021 pilotage involved an inbound ship. The 2022 check pilotage was conducted after the Hagen Oldendorff grounding, in June 2022.
Simulation training
PHP pilots were required to undertake simulator training every 2 years. The training involved the pilot undertaking several exercises conducting various ship types in and out of Port Hedland with various pre-briefed emergency scenarios evolving during the exercise. The number and nature of the scenarios exercised were determined by an agreed training procedure with the scenarios drawn for a database of standard exercises. The training was typically conducted jointly with tug masters from Port Hedland towage providers and with a PPA representative present.
A review of the pilot’s simulator training report from their most recent simulator training session in July 2021 showed that the emergency scenarios exercised included main engine failures, steering failures (rudder lock at various rudder angles) and electrical blackouts. A rudder angle indicator failure was not among the exercised scenarios, nor was it part of the database of exercise scenarios.
Pilot equipment
The pilot was equipped with a Navicom Dynamics portable pilotage unit (PPU).[42] The pilot’s PPU was set up to comply with the requirements of a Class-A PPU. It provided very high accuracy, independent position, heading, speed and RoT data[43] while automatic identification system (AIS)[44] data was sourced from the ship by connecting the PPU to the ship’s pilot plug.
The pilot’s PPU was set up to display RoT as a numerical value with positive values indicating a RoT to starboard and negative values indicating a RoT to port. The PPU also displayed the ship’s track and a ‘predictor’ to indicate where the ship would be 1 minute and 2 minutes into the future based on the vessel’s current course, speed and RoT. The pilot reported that their PPU was fully functional and was their preferred source of navigational data, both generally and during the Hagen Oldendorff pilotage. A review of the PPU replay of the pilotage and grounding determined that the data displayed by the PPU was accurate and consistent with that displayed on the ship’s equipment.
Similar occurrences
Iron King
On 31 July 2008, the fully laden, capesize, Isle of Man-registered bulk carrier Iron King, departed from its berth in Port Hedland with a pilot on board. As the ship made its way through the harbour, the towlines of the 4 assisting tugs were cast off. Shortly after, the rudder failed to respond to the pilot’s helm commands and the ship grounded to the east of Hunt Point, near beacon 44. The ship remained aground for about 12 hours until the next high tide when it was refloated, recovered to the centre of the channel and conducted to the outer anchorage. An underwater survey of the ship’s hull identified damage to the ship’s bow shell plating but no hull breaches or pollution of the sea.
The ATSB transport safety investigation report MO‑2008‑008 found that, on 2 occasions shortly before the ship grounded, Iron King’s rudder failed to respond to helm orders because the steering system hydraulic pressure was limited by a leaking actuator relief valve whenever the rudder moved to port. The investigation also found that it was normal practice for assisting tugs to be released before departing ships reached Hunt Point and that the pilot had not been provided with training in the implementation of a suite of ‘risk analysed’ responses to reasonably foreseeable emergency scenarios in a simulated environment.
Additionally, the investigation identified that Iron King’s SMS did not include procedures that adequately ensured that the ship’s master and crew were aware of, and drilled in, the emergency steering system change over procedure to be followed in the event of a loss of steering control.
Dumun
On 29 April 2011, the Panama-registered bulk carrier Dumun grounded while departing the port of Gladstone, Queensland with a pilot on board. After the ship departed the berth, the pilot released the 2 assisting tugs and dismissed them. About 30 minutes later, the ship’s steering appeared to stop responding to bridge commands. The bridge team assumed that the steering had failed, and the pilot ordered the main engine stopped and then started astern. However, these actions were not enough to prevent the ship from departing the Auckland Channel and grounding. There was no structural damage sustained by the ship, but the hull coating was scored and abraded with exposed metal in some areas.
The ATSB transport safety investigation report MO‑2011‑004 found that the ship's steering appeared to stop responding to bridge commands because the linkage between the tiller and rudder angle transmitter had become detached. The steering gear remained operational and continued to respond to helm orders, but the rudder angle transmitter lost its input signal and, as a result, the bridge mounted rudder angle indicator stopped working.
The ATSB determined that the ship's builders did not identify that the rudder angle indicator transmitter and tiller linkage were not installed correctly. The ATSB also found that the analysis of shipping operations in Gladstone, carried out by the relevant authorities, had not appropriately considered all that could be done to prevent the grounding of a ship as a result of steering gear or main engine failure. Additionally, a comprehensive SMS, with the aim of identifying, evaluating and controlling pilotage related risk, had not been implemented in the port.
Safety analysis
Introduction
On the morning of 9 April 2022, the fully laden capesize bulk carrier Hagen Oldendorff departed its berth in Port Hedland, Western Australia with a harbour pilot on board and 4 tugs assisting. The first of the tugs was cast off shortly after departure and the ship continued its passage of the port’s navigational channel. As the pilot navigated the ship through a turn in the channel, the 2 shoulder tugs were cast off and retained as passive escorts while the aft tug remained tethered as an active escort. Shortly after the turn was completed, the ship experienced a loss of electrical power supply to all the ship’s analogue rudder angle indicators and, a few minutes later, struck the western batter of the channel. The pilot manoeuvred the ship back into the centre of the channel and, with the assistance of additional tugs and a second pilot, resumed the outbound passage and conducted the ship to an anchorage outside port limits.
Subsequently, the ship was found to be taking on water in the number 1 and 2 port double‑bottom water ballast tanks. Surveys and inspections conducted over the following days identified substantial damage to the ship’s bottom shell plating including hull breaches of the shipside shell plating of the damaged tanks and the failure of the transverse bulkhead between the tanks. There were no reported injuries or pollution of the sea as a result of the grounding.
This analysis will consider the triggering event for the grounding – the loss of rudder angle indication – and the resilience of the system protections in place to mitigate such an event. The analysis will also cover the manoeuvring of the ship leading up to the grounding, the pilot’s use of the available tugs and, the port authority and pilotage organisation’s procedures and guidance for the effective use of those tugs. Finally, the effect of fatigue on the pilot’s performance was examined in detail however there was insufficient evidence to establish that the pilot was experiencing a level of fatigue known to have an effect on performance.
Events leading up to the grounding
Loss of rudder angle indication
As part of pre-departure checks, Hagen Oldendorff’s steering had been successfully tested in manual and non-follow-up (NFU) steering modes including under the observation of the pilot. After departure from the berth the ship’s passage through the inner harbour was uneventful, with all systems operating normally. However, following a turn to port, conducted with the assistance of the aft active escort tug (as part of routine training), the bridge rudder angle indicators stopped working and experienced a loss of illumination. While the autopilot rudder angle indicator display remained operational, neither the ship’s crew, nor the pilot were aware of it. Consequently, the bridge team, including the pilot, had no way of knowing the position of the rudder or if the steering gear was operational.
In the moments leading up to the loss of rudder angle indication, the pilot was in the process of correcting a slight but developing turn to starboard using port helm. At the time of the power failure, the rudder (and rudder angle indicator) was at about midships. Subsequently, when the pilot’s helm order of port 10° was executed by the helmsman, the rudder indication remained amidships. The pilot, who remained concerned about the starboard rate of turn (RoT), increased their helm order to port 20°. Although unknown to the crew, the steering remained operational, and the rudder moved to port 20° while the indicator remained amidships. In the absence of any audible or visual alarms alerting the crew to an indicator failure, the bridge team reasonably perceived that there was a steering failure and acted accordingly. The loss of the rudder angle indication triggered the subsequent sequence of events which resulted in a turn to port and subsequent grounding.
A shipboard investigation carried out over the following days identified that the tracking motor of the ship’s bridge-mounted omnidirectional rudder angle indicator had burnt out and failed. The motor failure resulted in a short circuit, which tripped the common protective circuit breaker in the bridge electrical cabinet. That in turn, resulted in a loss of electrical power supply to all 6 of the ship’s analogue rudder angle indicators without any associated audible or visual alerts.
Contributing factor During an outbound pilotage, the tracking motor of Hagen Oldendorff's bridge-mounted omnidirectional rudder angle indicator failed resulting in a short circuit which tripped the common circuit breaker for all the ship's analogue rudder angle indicators, with an associated loss of power to these rudder indicators. Consequently, the bridge team assumed that the ship’s steering had failed and implemented steering failure emergency procedures. |
Response to the rudder angle indicator failure
The pilot and master’s response to the perceived steering failure included switching to NFU mode, applying port NFU input and ordering the steering gear room be manned. The helmsman’s port NFU input resulted in the rudder moving further to port, to about port 27°. However, in the absence of a working analogue rudder angle indicator and, being unaware of the autopilot indicator display, neither the pilot or the helmsman was able to determine what the rudder angle was or if steering control had been restored. The apparent ineffectiveness of the NFU input likely further convinced the bridge team that there was a steering failure. While the ship and pilot’s RoT indicators remained operational, it was probably challenging to infer that the steering remained operational based on the ship’s developing RoT alone.
The pilot also issued orders to the aft active escort tug, RT Clerke, to take the stern to starboard, that is, to apply indirect steering forces at the stern to eliminate the starboard RoT. As the port rudder took effect, and the ship started turning to port, the pilot rescinded the tug’s order and instructed the tug to return to the port quarter and apply indirect steering forces to arrest the port turn. However, the pilot did not issue orders to return the helm to amidships. This may have been because the pilot believed issuing helm orders was futile or because they were now occupied with directing the available passive escort tugs, RT Inspiration and RT Atlantis.
The pilot also did not begin reducing the ship’s main engine setting until about 47 seconds after the rudder indicator failure. Nevertheless, once the main engine was stopped and the efforts of the 3 tugs began to take effect, the ship’s port RoT peaked at about 13.6° and then started decreasing. The initial order to RT Clerke to take the stern to starboard probably did not contribute to the ship’s port turn as the order was rescinded before the tug could get into optimal position for indirect towage on the starboard quarter. However, valuable time was lost as the tug moved from the port to the starboard quarter and then back again, which likely limited the pilot’s ability to arrest the port turn.
The port RoT continued to decrease slowly despite a subsequent order by the pilot, which resulted in the rudder being put hard over to port for about 20 seconds. This order was an error on the part of the pilot likely due to the combined effects of acute stress and high workload and was corrected shortly after upon being challenged by the master. However, by this time, the grounding was unavoidable, and the ship struck the batter shortly after at a speed of about 6.1 knots.
Contributing factor Following the initiation of emergency procedures for a steering failure, the pilot's manoeuvring orders, aimed at maintaining directional control of the ship, resulted in an uncontrolled turn to port. Despite attempts to arrest this turn, Hagen Oldendorff's port bow collided with the western side of the channel, at a speed of about 6.1 knots. |
Escort towage strategy
Use of tugs
Following the introduction of tugs with improved escort towage capability in Port Hedland in 2017, a documented escort towage strategy was implemented to best utilise these tugs to mitigate the risk of channel blockage. For capesize ships, the towage strategy recommended pilots maintain the shoulder tugs fast on the port and starboard shoulders prior to, and throughout zone 3 and zone 4. The strategy acknowledged that, while weather or other conditions may render it unsafe to keep these tugs fast, it emphasised that the shoulder tugs should maintain their towlines tethered as long as they could safely do so. The weather on the morning of the grounding was relatively benign with winds at force 3–4 and 1 m seas and the conditions did not preclude the tugs being kept fast until beacons 30-31, as recommended by the strategy.
The pilot had ordered Hagen Oldendorff’s shoulder tugs cast off well before beacons 30-31 (near beacons 36-37) as this was their preferred practice. While the pilot was aware of the escort towage strategy, they believed that adherence to its recommendations remained at their discretion. This view was also shared by other pilots with tugs being released at various locations between beacons 36-37 and 30-31 based on individual preferences.
The escort towage strategy noted that, in the event of a steering incident, simulations had consistently demonstrated that initially, the aft escort tug should be used to provide steering forces to counteract the rudder and control the heading while the shoulder tugs were used to provide braking forces to slow the ship. However, when the rudder indicator failed, shortly after the ship passed beacons 36-37, both shoulder tugs, RT Inspiration and RT Atlantis, had been cast off and were passive escorts. Had these tugs been fast at the time, the pilot would have had more options at their disposal, including using both tugs to provide braking forces to slow the ship.
Based on the ship’s speed and forward momentum, the shoulder tugs would likely have been of limited effectiveness in influencing the ship’s heading and it is also likely that using RT Atlantis to push on the starboard quarter was a more effective technique to reduce the port RoT than pulling on the starboard bow. Nevertheless, the ship’s port turn could not be arrested and the ship grounded, with consequent breaches of the hull and flooding.
Hagen Oldendorff’s tug masters largely complied with the pilot’s orders effectively and within acceptable timeframes given the circumstances. It is reasonable to conclude that had the shoulder tugs remained fast and been used to provide braking forces as recommended in the escort towage strategy, that the ship may have struck the channel batter at a lower speed. Although difficult to quantify, even minor reductions in impact speed would likely have resulted in reductions in the impact energy thereby reducing damage to the ship.
Contributing factor The pilot’s decision to cast off the port and starboard escort tugs before the ship passed beacons 30 and 31 was inconsistent with the port’s identified and implemented best practice escort towage strategy. Consequently, when the rudder angle indicator failed, the pilot was unable to make the fullest possible use of these tugs to either reduce the ship’s speed or arrest the turn to port. |
Port escort towage documentation
The blockage of the Port Hedland navigation channel was identified as a strategic risk to the port’s operations. Port Hedland is a key export port in the supply chains of several major Australian seaborne iron ore exporters and the economic consequences of a ship grounding and blocking the channel had the potential to be severe and far-reaching. Consequently, significant effort was invested into identifying and implementing measures to prevent, and to mitigate the effects of, a channel blockage. While these efforts identified several channel improvements and risk mitigation measures, the primary risk controls took the form of pilotage and escort towage for ships.
As part of the procurement and introduction of escort-capable tugs at Port Hedland, BHP (one of the primary stakeholders with an interest in maintaining navigability of the channel), conducted various studies, simulations and trials aimed at identifying the most effective means of utilising these tugs. These studies, simulations and trials involved the assistance and participation of the Pilbara Ports Authority (PPA), Port Hedland Pilots (PHP), tug masters and other stakeholders. This core group of stakeholders evolved into the Port Hedland Working Group (PHWG), which oversaw the review, development and assessment of several channel blockage risk control measures including the escort towage strategy.
In 2013, an initiative was launched to procure tugs with improved escort towage capability and an interim escort towage strategy was developed to optimise the use of the port’s existing tugs. The interim strategy recommended that the shoulder tugs be kept fast until beacons 36-37 (end of zone 3). In 2015, an escort towage strategy was developed to supersede the interim strategy. The escort towage strategy identified that the most effective use of the escort tugs involved using an active escort tug fast aft until beacons 15-16 (end of zone 5) and 2 escort tugs tethered on the port and starboard shoulders until beacons 30-31 (end of zone 4) unless prevented from doing so by adverse environmental conditions. By 2017, a number of the improved escort towage tugs had been introduced and the measures in the escort towage strategy began to be implemented with evidence of shoulder tugs being kept fast by pilots until beacons 30-31 where conditions were favourable.
In 2020, BHP submitted an updated version of the escort towage strategy to the PPA for official endorsement as an operational port document. The strategy remained largely unchanged with respect to the use of tugs for capesize ships and recommended that tugs should have their towlines tethered on the port and starboard shoulders throughout zones 3 and 4, except where conditions made it unsafe to do so. However, the document remained in draft format with the PPA. The PPA directed port users to a public document, the port user guidelines and procedures, as the authoritative source of information on port operations including towage. However, the port user guidelines and procedures document did not include detail of the escort towage strategy’s recommended tug allocation and towage procedures or of the port’s expectations with regard to their implementation.
In 2018, a port business continuity plan (BCP) for channel blockage was introduced as a proposed risk control measure. Records of the port’s strategic risk review committee meetings, which were attended by PHP representatives, showed that the harbour master first presented a BCP to the committee in 2019 and in 2020, an updated version of the document was published. The BCP reiterated risk evaluations for channel blockage from previous studies and summarised elements of the escort towage strategy. It stated that the strategy had been implemented in the port and that in zone 4 tugs were tethered to each shoulder of outbound capesize ships with towlines attached through to beacons 30-31, whenever possible. It further stated that, in doing so, simulations indicated that the effectiveness of the deployed tug fleet was improved, and that pilots had more options to manage engine and rudder failures. The BCP was not a public document, and interviewed pilots expressed only limited awareness of its existence and of its contents.
The PHP safety management system (SMS) included several procedures on the subject of towage. The procedures primarily directed pilots to the Port Hedland port user guidelines and procedures document for information on tug requirements. In general, the SMS directed pilots to maintain tugs where they would be of greatest effect in the event of an emergency and to keep tugs fast as long as it was safe to do so depending on factors such as weather, speed and the ship’s characteristics.
The SMS also stated that, for capesize ships (such as Hagen Oldendorff), pilots were to adhere to the port’s recognised escort towage strategy and the PHP SMS procedure on escort tug towage requirements stated that tugs were to be kept fast until at least beacons 36-37. However, this reflected the practices in interim escort towage strategy and not the updated escort towage strategy implemented after the introduction of the improved escort tugs in 2017, which directed pilots to keep the shoulder tugs fast until beacons 30-31.
Neither the port user guidelines and procedures or the PHP SMS included clear directives or reference to the tug retention and usage recommendations of the escort towage strategy. Consequently, there was no consistent understanding or application by the pilots of the demonstrated, effective towage practices identified in the escort towage strategy.
Contributing factor Pilbara Ports Authority's port user guidelines and procedures did not reflect the best practice escort towage guidance detailed in the port's draft escort towage strategy and business continuity plan. The detail of these improved towage practices, designed to reduce the risk of channel blockages, were also not integrated into the Port Hedland Pilots' safety management system and were consequently, inconsistently applied by pilots. (Safety issue) |
Regulations and standards
The International Convention for the Safety of Life at Sea (SOLAS) specified minimum standards for the construction, equipment and operation of ships to ensure an adequate level of safety. Flag States are responsible for ensuring that ships under their flag comply with the requirements of SOLAS. In practice, this is achieved by designing, constructing and maintaining ships in compliance with the requirements of a classification society recognized by the flag State and Hagen Oldendorff was classed with Lloyd’s Register (LR).
SOLAS regulations and class rules for steering gear required that steering gear control systems be equipped with short circuit protection and, audible and visual alarms to alert crew to an electrical power failure in the system. However, rudder angle indication systems were not considered a component of steering gear control systems and were required to be independent of control systems.
Hagen Oldendorff was appropriately equipped with 6 rudder angle indicators spread across various locations on the ship. However, all 6 indicators were protected by a single circuit breaker located in the bridge electrical cabinet. Consequently, when the omnidirectional indicator on the bridge experienced a short circuit, it tripped the circuit breaker which removed power to all the ship’s rudder angle indicators. The protection of the ship’s mounted, analogue rudder angle indicators with a common circuit breaker constituted a single point of failure, which rendered the power supply to all the ship’s analogue indicators vulnerable to a fault in any one of them.
Some classification societies, such as Det Norske Veritas (DNV), required that rudder angle indicating systems on some ships be arranged such that a single failure in power supply or anywhere in the indicating system did not cause a loss of rudder angle indication on the bridge. However, neither the minimum SOLAS regulations, nor the standard LR rules for ships, required such protection from single points of failure in rudder angle indication systems.
Instead, LR offered optional notations, such as the ‘IBS’ notation, which could offer improved resilience by requiring each item of electrically operated navigation equipment be individually connected to its distribution panel. For example, had only the omnidirectional indicator failed, and the bridge front instrument cluster indicator remained operational, it is almost certain that the bridge team would have maintained awareness of the rudder angle and that the pilotage would have continued with only limited disruption. However, Hagen Oldendorff was not required to hold this notation and, in any event, the application of the requirement for individual connection to a distribution board to rudder angle indicators would rely on a favourable interpretation of the rules.
Furthermore, in the absence of protections against single points of failure, the rules and regulations also did not require audible or visual alarms to alert crew to a failure of power supply or to other failures in the rudder angle indication system. Hagen Oldendorff’s autopilot display offered a redundant source of rudder angle information, which remained operational after the electrical power to the analogue indicators had failed. However, this system was not required by either SOLAS or LR and neither the pilot, nor the ship’s crew were aware of this capability. While certainly a valuable resource had the pilot and crew utilised it, the ship’s bridge team assumed a steering failure and responded accordingly.
An audible/visual alarm that alerted crew specifically to a power failure of the rudder angle indicators would have provided the bridge team with assurance that the failure was limited to the indicators and that the steering gear remained operational. This would likely have inhibited the development of the sequence of events that culminated in the grounding.
Contributing factor Although Hagen Oldendorff’s steering and rudder angle indicator systems complied with the applicable rules and regulations, neither the SOLAS regulations, nor the rules of the ship’s responsible classification society, Lloyd’s Register, mandated protection of the ship's rudder angle indication systems against a single point of failure in electrical power supply, nor did they require installation of audible or visual alerts to notify the bridge team of a power failure affecting the indicators. (Safety issue) |
Findings
ATSB investigation report findings focus on safety factors (that is, events and conditions that increase risk). Safety factors include ‘contributing factors’ and ‘other factors that increased risk’ (that is, factors that did not meet the definition of a contributing factor for this occurrence but were still considered important to include in the report for the purpose of increasing awareness and enhancing safety). In addition, ‘other findings’ may be included to provide important information about topics other than safety factors. Safety issues are highlighted in bold to emphasise their importance. A safety issue is a safety factor that (a) can reasonably be regarded as having the potential to adversely affect the safety of future operations, and (b) is a characteristic of an organisation or a system, rather than a characteristic of a specific individual, or characteristic of an operating environment at a specific point in time. These findings should not be read as apportioning blame or liability to any particular organisation or individual. |
From the evidence available, the following findings are made with respect to the grounding of Hagen Oldendorff in Port Hedland, Western Australia on 9 April 2022.
Contributing factors
- During an outbound pilotage, the tracking motor of Hagen Oldendorff's bridge-mounted omnidirectional rudder angle indicator failed, resulting in a short circuit which tripped the common circuit breaker for all the ship's analogue rudder angle indicators with an associated loss of power to these rudder indicators. Consequently, the bridge team assumed that the ship’s steering had failed and implemented steering failure emergency procedures.
- Following the initiation of emergency procedures for a steering failure, the pilot's manoeuvring orders, aimed at maintaining directional control of the ship, resulted in an uncontrolled turn to port. Despite attempts to arrest this turn, Hagen Oldendorff's port bow collided with the western side of the channel, at a speed of about 6.1 knots.
- The pilot’s decision to cast off the port and starboard escort tugs before the ship passed beacons 30 and 31 was inconsistent with the port’s identified and implemented best practice escort towage strategy. Consequently, when the rudder angle indicator failed, the pilot was unable to make the fullest possible use of these tugs to either reduce the ship’s speed or arrest the turn to port.
- The Pilbara Ports Authority's port user guidelines and procedures did not reflect the best practice escort towage guidance detailed in the port's draft escort towage strategy and business continuity plan. The detail of these improved towage practices, designed to reduce the risk of channel blockages, were also not integrated into the Port Hedland Pilots' safety management system and were consequently, inconsistently applied by pilots. (Safety issue)
- Although Hagen Oldendorff’s steering and rudder angle indicator systems complied with the applicable rules and regulations, neither the SOLAS regulations, nor the rules of the ship’s responsible classification society, Lloyd’s Register, mandated protection of the ship's rudder angle indication systems against a single point of failure in electrical power supply, nor did they require installation of audible or visual alerts to notify the bridge team of a power failure affecting the indicators. (Safety issue)
Safety issues and actions
Central to the ATSB’s investigation of transport safety matters is the early identification of safety issues. The ATSB expects relevant organisations will address all safety issues an investigation identifies. Depending on the level of risk of a safety issue, the extent of corrective action taken by the relevant organisation(s), or the desirability of directing a broad safety message to the marine industry, the ATSB may issue a formal safety recommendation or safety advisory notice as part of the final report. All of the directly involved parties are invited to provide submissions to this draft report. As part of that process, each organisation is asked to communicate what safety actions, if any, they have carried out or are planning to carry out in relation to each safety issue relevant to their organisation. Descriptions of each safety issue, and any associated safety recommendations, are detailed below. Click the link to read the full safety issue description, including the issue status and any safety action/s taken. Safety issues and actions are updated on this website when safety issue owners provide further information concerning the implementation of safety action. |
Escort towage strategy
Safety issue number: MO-2022-007-SI-01
Safety issue description: The Pilbara Ports Authority's port user guidelines and procedures did not reflect the best practice escort towage guidance detailed in the port's draft escort towage strategy and business continuity plan. The detail of these improved towage practices, designed to reduce the risk of channel blockages, were also not integrated into the Port Hedland Pilots' safety management system and were consequently, inconsistently applied by pilots.
Escort towage strategy
Safety issue number: MO-2022-007-SI-02
Safety issue description: The Pilbara Ports Authority's port user guidelines and procedures did not reflect the best practice escort towage guidance detailed in the port's draft escort towage strategy and business continuity plan. The details of these improved towage practices, designed to reduce the risk of channel blockages, were also not integrated into the Port Hedland Pilots' safety management system and were, consequently, inconsistently applied by pilots.
Rules and regulations for rudder angle indicator systems
Safety issue number: MO-2022-007-SI-03
Safety issue description: Although Hagen Oldendorff’s steering and rudder angle indicator systems complied with the applicable rules and regulations, neither the SOLAS regulations, nor the rules of the ship’s responsible classification society, Lloyd’s Register, mandated protection of the ship's rudder angle indication systems against a single point of failure in power supply, nor did they require installation of audible or visual alerts to notify the bridge team of a power failure affecting the indicators.
Safety recommendation description: The Australian Transport Safety Bureau recommends that Lloyd’s Register takes steps to approach the International Association of Classification Societies and seek safety action to address the risk associated with a single point of failure in electrical power supply for ship's rudder angle indicators.
Rules and regulations for rudder angle indicator systems
Safety issue number: MO-2022-007-SI-04
Safety issue description: Although Hagen Oldendorff’s steering and rudder angle indicator systems complied with the applicable rules and regulations, neither the SOLAS regulations, nor the rules of the ship’s responsible classification society, Lloyd’s Register, mandated protection of the ship's rudder angle indication systems against a single point of failure in power supply, nor did they require installation of audible or visual alerts to notify the bridge team of a power failure affecting the indicators.
Safety recommendation description: The Australian Transport Safety Bureau recommends that the Australian Maritime Safety Authority provides the necessary support and assistance to the Liberia Maritime Authority in its efforts to seek safety action at the International Maritime Organization aimed at addressing the risk associated with a single point of failure in electrical power supply for ship's rudder angle indicators.
Rules and regulations for rudder angle indicator systems
Safety issue number: MO-2022-007-SI-05
Safety issue description: Although Hagen Oldendorff’s steering and rudder angle indicator systems complied with the applicable rules and regulations, neither the SOLAS regulations, nor the rules of the ship’s responsible classification society, Lloyd’s Register, mandated protection of the ship's rudder angle indication systems against a single point of failure in power supply, nor did they require installation of audible or visual alerts to notify the bridge team of a power failure affecting the indicators.
Safety recommendation description: The Australian Transport Safety Bureau recommends that the Liberia Maritime Authority takes steps to formally raise this safety issue with the International Maritime Organization to seek safety action aimed at addressing the risk associated with a single point of failure in electrical power supply for ship's rudder angle indicators.
Safety action not associated with an identified safety issue
Whether or not the ATSB identifies safety issues in the course of an investigation, relevant organisations may proactively initiate safety action in order to reduce their safety risk. The ATSB has been advised of the following proactive safety action in response to this occurrence. |
Additional safety action by Pilbara Ports Authority
On 29 October 2024, the Pilbara Ports Authority issued a local marine notice requiring all ships calling at Port Hedland to have a suitably qualified and competent person on stand-by in the steering gear room when the ship was navigating in the channel. The marine notice stated that the person on stand-by in the steering gear room was to be:
- trained and proficient in emergency steering procedures including switching to local steering and maintaining a direct means of communication to the ship's bridge
- able to identify and communicate the actual position of the rudder (rudder angle) to the bridge when requested
- able to steer the ship as directed from the ship's bridge
- dismissed from steering gear room only after consultation with the pilot.
The marine notice also recommended that ships calling at Port Hedland conduct an emergency steering test before arrival.
On 30 May 2024, the PPA issued a local marine notice requiring all capesize ships be equipped with a closed circuit television (CCTV) camera in the steering gear room with a monitor on the bridge to provide CCTV camera footage of the rudder angle for the bridge team.
On 18 June 2024, the PPA issued a further local marine notice clarifying reporting requirements for machinery events, equipment malfunctions and safety issues for ships calling at Port Hedland.
Additional safety action by Wah Kwong Ship Management Hong Kong
On 28 June 2024, Hagen Oldendorff's managers, Wah Kwong Ship Management Hong Kong, advised the ATSB that, in March 2023, an audible and visual alarm was installed on board the ship to alert crew in the event the rudder angle indicators' circuit breaker tripped resulting in a loss of power supply to the indicators. In addition, closed circuit television cameras were installed in the ship's steering gear room to allow direct monitoring of the physical rudder angle from the bridge.
Additional safety action by Port Hedland Pilots
Following the grounding and the Port Hedland Pilots (PHP) internal investigation, PHP advised that pilots keep the forward 2 tugs fast as recommended for the relevant channel zones unless prevented from doing so by weather or other factors.
On 29 July 2024, Port Hedland Pilots advised that in October 2023, the organisation's fatigue risk management procedure was updated to mandate additional risk fatigue risk controls including:
- a maximum FAID score of 75 for pilots who were more than 14 days into their 4-week duty period
- a maximum FAID score of 70 for the duty pilot
- a requirement that pilots obtain a minimum of 13 hours sleep in the 48-hour period before a pilotage
- a maximum of 3 consecutive nights of pilotage work before a mandated rest period from 1900 to 0800 hours
- self-declared sleepiness score of 6 to trigger an overnight rest period from 1900 to 0800 hours
- self-declared sleepiness score of 7 to trigger an extended overnight rest period acknowledging elevated fatigue risk.
Glossary
AIS | Automatic identification system |
AMSA | Australian Maritime Safety Authority |
BCP | Business continuity plan |
BHPTS | BHP Towage Services |
CCTV | Closed circuit television |
CSIR | Council for Scientific and Industrial Research |
DNV | Det Norske Veritas |
DUKC | Dynamic under keel clearance system |
ECDIS | Electronic chart display and information system |
EPN | Escort performance notation |
FAID | Fatigue Audit InterDyne |
FMG | Fortescue Metals Group |
FRMP | Fatigue risk management procedure |
Hs | Significant wave height |
IACS | International Association of Classification Societies |
IBS | Integrated bridge systems |
IMO | International Maritime Organization |
ISM | International Management Code for the Safe Operation of Ships and for Pollution Prevention, 1995, as amended |
LAT | Lowest astronomical tide |
LiMA | Liberia Maritime Authority |
LR | Lloyd’s Register |
NFU | Non-follow-up steering |
PHP | Port Hedland Pilots |
PHWG | Port Hedland Working Group |
PPA | Pilbara Ports Authority |
PPU | Portable pilotage unit |
PSWM | Prior sleep wake model |
RoT | Rate of turn |
RPM | Revolutions per minute |
SMS | Safety management system |
SOLAS | The International Convention for the Safety of Life at Sea, 1974, as amended |
SP2 | Stanley Point berth number 2 |
SWL | Safe working load |
UI | Unified interpretation |
VDR | Voyage data recorder |
VHF | Very high frequency |
VTS | Vessel traffic service |
WA | Western Australia |
WOCL | Window of circadian low |
Sources and submissions
Sources of information
The sources of information during the investigation included:
- Australian Maritime Safety Authority
- BHP
- directly involved officers and crew of Hagen Oldendorff
- directly involved tug masters
- documents, drawings, manuals, logbooks and photographs from Hagen Oldendorff
- Hagen Oldendorff’s pilot
- Lloyd’s Register
- Pilbara Ports Authority
- Port Hedland Pilots
- recorded information from Hagen Oldendorff’s voyage data recorder (VDR)
- Wah Kwong Ship Management, Hong Kong.
References
Akerstedt, T., & Wright, K. P. (2009). Sleep loss and fatigue in shift work and shift work disorder. Sleep medicine clinics, 4(2), 257-271.
Australian Transport Safety Bureau, Report No. MO-2008-008, Independent investigation into the grounding of the Isle of Man- registered bulk carrier Iron King, Port Hedland, Western Australia, 31 July 2008, ATSB, 2009. Available at www.atsb.gov.au
Australian Transport Safety Bureau, Report No. MO-2011-004, Grounding of the Panama‑registered bulk carrier Dumun, Gladstone, Queensland, 29 April 2011, ATSB, 2012. Available at www.atsb.gov.au
Chambers, T. P., & Main, L. C. (2015). Symptoms of fatigue and coping strategies in maritime pilotage. International maritime health, 66(1), 43-48.
Costa G (1996) ‘Effects on Health and Well-Being’, In: Colquhoun WP, Costa G, Folkard S and Knauth P Shiftwork Problems and Solutions, Peter Lang, Germany.
Dismukes R, Goldsmith TE, and Kochan JA (2015) Effects of acute stress on aircrew performance: literature review and analysis of operational aspects, NASA/TM—2015–218930, NASA Ames Research Center, Moffett Field, California.
Folkard S and Tucker P (2003) ‘Shift work, Safety and Productivity’, Occupational Medicine, 53(2): 95-101.
Gregory, K., Hobbs, A., Parke, B., Bathurst, N., Pradhan, S., & Flynn-Evans, E. (2020). An evaluation of fatigue factors in maritime pilot work scheduling. Chronobiology International, 37(9‑10), 1495-1501.
International Chamber of Shipping 2016, Bridge Procedures Guide, Marisec Publications, London.
International Maritime Organization (IMO) 1995, International Management Code for the Safe Operation of Ships and for Pollution Prevention (ISM Code) as amended, IMO, London. Available at www.imo.org
International Maritime Organization (IMO) 2014, The International Convention for the Safety of Life at Sea (SOLAS) 1974 as amended, IMO, London. Available at www.imo.org
International Maritime Organization (IMO), 2009, Resolution A.1021(26) Code on Alerts and Indicators, IMO, London. Available at www.imo.org
International Maritime Organization, 2019, MSC.1/Circ.1598 Guidelines on Fatigue, London, United Kingdom. Available at www.imo.org
Lloyd’s Register, 2019, Rules and Regulations for the Classification of Ships, London, United Kingdom.
Pilbara Ports Authority, 2020, Port handbook, Port Hedland, Australia.
Pilbara Ports Authority, 2021, Port user guidelines and procedures, Port Hedland, Australia.
Reale C, Salwei ME, Militello LG, Weinger MB, Burden A, Sushereba C, Torsher LC, Andreae MH, Gaba DM, McIvor WR, Banerjee A, Slagle J and Anders S (2023) ‘Decision-Making During High-Risk Events: A Systematic Literature Review’, Journal of Cognitive Engineering and Decision Making, 17(2): 188-212.
Riethmeister V, Matthews RW, Dawson D, de Boer MR, Brouwer S, and Bültmann U (2019) ‘Time-of-day and days-on-shift predict increased fatigue over two-week offshore day-shifts’, Applied Ergonomics, 78: 157-163.
Rosekind MR, Gander PH, Gregory KB, Smith RM, Miller DL, Oyung R, Webbon LL and Johnson JM (1996) ‘Managing Fatigue in Operational Settings 1: Physiological Considerations and Countermeasures’, Behavioural Medicine, 21: 157-165.
Tait, J. L., Chambers, T. P., Tait, R. S., & Main, L. C. (2021). Impact of shift work on sleep and fatigue in Maritime pilots. Ergonomics, 64(7), 856-868.
Van Dongen HP, Maislin G, Mullington JM and Dinges DF (2003) ‘The cumulative cost of additional wakefulness: dose-response effects on neurobehavioral functions and sleep physiology from chronic sleep restriction and total sleep deprivation’, Sleep, 26: 117-26.
Weaver, M. D., Sletten, T. L., Foster, R. G., Gozal, D., Klerman, E. B., Rajaratnam, S. M., ... & Czeisler, C. A. (2021). Adverse impact of polyphasic sleep patterns in humans: Report of the National Sleep Foundation sleep timing and variability consensus panel. Sleep health, 7(3), 293‑302.
Wickens CD, Hutchins SD, Laux L, and Sebok A (2015) ‘The Impact of Sleep Disruption on Complex Cognitive Tasks: A Meta-Analysis’, Human Factors, 57(6): 930-946.
Williamson A and Friswell R (2011) ‘Investigating the relative effects of sleep deprivation and time of day on fatigue and performance’, Accident Analysis & Prevention, 43(3): 690-697.
Submissions
Under section 26 of the Transport Safety Investigation Act 2003, the ATSB may provide a draft report, on a confidential basis, to any person whom the ATSB considers appropriate. That section allows a person receiving a draft report to make submissions to the ATSB about the draft report.
A draft of this report was provided to the following directly involved parties:
- Australian Maritime Safety Authority
- BHP
- directly involved tug masters
- Hagen Oldendorff’s pilot
- Lloyd’s Register
- Pilbara Ports Authority
- Port Hedland Pilots
- the ship’s flag State administration, Liberia
- Wah Kwong Ship Management, Hong Kong.
Submissions were received from:
- Australian Maritime Safety Authority
- BHP
- Hagen Oldendorff’s pilot
- Lloyd’s Register
- Pilbara Ports Authority
- Port Hedland Pilots
- the ship’s flag State administration, Liberia.
The submissions were reviewed and, where considered appropriate, the text of the report was amended accordingly.
Appendices
Appendix A – Key orders and events leading up to the grounding
Time | Rudder angle (deg) | RoT (deg/min) | Heading (True) | SOG (knots) | Events, orders and decisions on 9 April 2022 |
0048:00 | Midships (0°) | 0 | 034 | 0.0 | Hagen Oldendorff departed SP2 berth |
0117:45 | 11° S | 1.6° S | 042 | 4.3 | RT Darwin cast off and dismissed |
0135:41 | 0° | 8.9° P | 344 | 6.6 | RT Atlantis cast off |
0137:25 | 0° | 1° S | 334 | 6.8 | Pilot orders starboard 10° |
0137:30 | 7° S | 1.3° S | 334 | 6.8 | Indirect towage training completed |
0137:41 | 8° S | 3° S | 335 | 6.8 | Pilot orders a heading of 335° |
0137:42 | 9° S | 3.2° S | 335 | 6.8 | RT Inspiration cast off |
0137:47 | 0° | 3.6° S | 335 | 6.8 | Pilot orders port 10° |
0137:49 | 1° P | 3.8° S | 335 | 6.8 | Power supply failure to rudder angle indicators |
0137:53 | 10° P | 3.6° S | 335 | 6.8 | Rudder at port 10° |
0137:56 | 10° P | 3.7° S | 335 | 6.9 | Pilot orders port 20° |
0137:59 | 16° P | 3.7° S | 336 | 6.9 | Pilot orders RT Clerke ‘stern to starboard, 40 t’ |
0138:00 | 19° P | 3.5° S | 336 | 6.9 | RT Clerke moving from port to starboard quarter |
0138:01 | 20° P | 3.3° S | 336 | 6.9 | Rudder at port 20° and starboard RoT decreasing |
0138:08 | 20° P | 2.4° S | 336 | 6.9 | Pilot orders non-follow-up (NFU) port 20° |
0138:10 | 20° P | 2.1° S | 336 | 6.9 | Pilot orders RT Clerke ‘stern to starboard, 60 t’ |
0138:18 | 20° P | 0.7° S | 336 | 6.9 | Pilot orders RT Inspiration to make fast |
0138:21 | 20° P | 0 | 336 | 6.9 | Helmsman applies port NFU input |
0138:29 | 20° P | 1.3° P | 336 | 6.9 | RT Clerke passing astern of Hagen Oldendorff |
0138:30 | 20° P | 1.6° P | 336 | 6.9 | Pilot orders RT Clerke ‘no weight’ |
0138:36 | 24° P | 3° P | 336 | 6.9 | Pilot orders main engine ‘half ahead’ |
0138:38 | 27° P | 4° P | 336 | 6.9 | Helmsman ceases port NFU input |
0138:39 | 28° P | 4.4° P | 336 | 6.9 | Pilot orders RT Clerke ‘stern to port, 20 t’ |
0138:44 | 28° P | 6.1° P | 335 | 6.9 | Pilot orders RT Atlantis to make fast |
0138:47 | 28° P | 6.9° P | 335 | 6.9 | RT Clerke moving from starboard to port quarter |
0138:53 | 27° P | 8.5° P | 334 | 6.9 | Pilot orders main engine ‘slow ahead’ |
0138:55 | 27° P | 8.9° P | 334 | 6.9 | Pilot orders RT Clerke ‘stern to port, full’ |
0139:12 | 27° P | 12.2° P | 331 | 6.9 | Pilot orders main engine ‘dead slow ahead’ |
0139:19 | 27° P | 12.9° P | 329 | 6.9 | RT Clerke on port quarter starting to apply tow force |
0139:20 | 27° P | 12.9° P | 329 | 6.9 | Pilot orders RT Inspiration ‘push full’ |
0139:24 | 27° P | 13.4° P | 328 | 6.8 | Pilot orders ‘stop engines’ |
0139:28 | 26° P | 13.6° P | 327 | 6.8 | RoT peaks at 13.6° to port |
0139:30 | 26° P | 13.5° P | 326 | 6.8 | Pilot orders RT Atlantis ‘push on [starboard] quarter’ |
0139:35 | 26° P | 13.4° P | 325 | 6.7 | Pilot orders rudder hard to port/ Master queries order |
0139:38 | 28° P | 13.3° P | 325 | 6.7 | Helmsman applies port NFU input |
0139:40 | 35° P | 13.4° P | 324 | 6.7 | Rudder hard to port |
0139:44 | 35° P | 13.3° P | 323 | 6.7 | Pilot to VTS, ‘Port emergency. Rudder failure.’ |
0139:50 | 35° P | 12.8° P | 322 | 6.6 | Master queries pilot’s order of hard to port again |
0139:54 | 35° P | 12.7° P | 321 | 6.6 | Pilot orders rudder hard to starboard |
0139:55 | 35° P | 12.7° P | 321 | 6.6 | Helmsman applies starboard NFU input |
0140:01 | 11° P | 12° P | 320 | 6.6 | RT Inspiration confirms pushing full on port bow |
0140:05 | 8° S | 11.3° P | 319 | 6.5 | Pilot orders ‘dead slow astern’ |
0140:10 | 30° S | 10° P | 318 | 6.5 | Pilot orders RT Atlantis ‘push full’ on quarter |
0140:11 | 35° S | 10 °P | 318 | 6.4 | Rudder hard to starboard |
0140:30 | 35° S | 3° P | 316 | 6.2 | VTS broadcasts request for towage assistance |
0140:34 | 35° S | 3° P | 317 | 6.1 | Hagen Oldendorff grounds |
Appendix B – Escort Performance Notation
For escort tugs, Lloyd’s Register offers the specific notation EPN (F,B,V,C) to denote the escort performance numeral of the vessel obtained by full scale testing of the vessels. The EPN is made up of a series of values (F,B,V,C), defined as follows:
- F: Maximum steering force, in tonnes
- B: Maximum braking force, in tonnes
- V: Speed, in knots, at which F and B are determined
- C: Time, in seconds, required for the escort tug in manoeuvring from maintained oblique position of the tug giving it a maximum steering force on one side of the assisted vessel to a mirror position on the other side.
The EPN values of the Rivtow (BHP towage service) tug fleet at Port Hedland is detailed in Figure 13 below. In the table, the value of ‘F’ (maximum steering force) is denoted by ‘Fs’ and the value of B (maximum braking force) is denoted by ‘Fb’. The values of Fs and Fb are provided for a ‘V’ of 6 knots, 8 knots and 10 knots.
The value of ‘C’ (transition time from port to starboard or vice versa while providing maximum steering forces) for the RAstar85 tugs at 6 knots and 8 knots was 45 seconds.
Figure 13: Tug escort performance notations
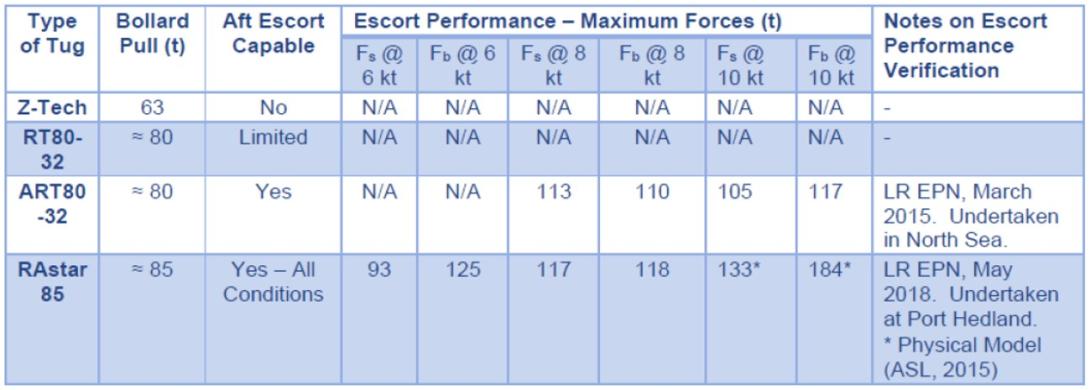
Source: BHP
Appendix C – Pilot fatigue analysis
Fatigue
The International Maritime Organization (2019)[45] defined fatigue as:
A state of physical and/or mental impairment resulting from factors such as inadequate sleep, extended wakefulness, work/rest requirements out of sync with circadian rhythms and physical, mental or emotional exertion that can impair alertness and the ability to safely operate a ship or perform safety-related duties.
Fatigue is a hazard because it affects everyone regardless of skill, knowledge and training and its effects can be particularly dangerous in the transportation sector, including the aviation and maritime industry.
Fatigue can be caused by any one or more of a range of factors including:
- lack of sleep (or inadequate restorative sleep)
- poor quality of sleep and rest
- circadian effects
- stress
- excessive workload.
Fatigue can have a range of effects on human performance, including:
- decreased short-term memory
- slowed reaction time
- decreased work efficiency
- reduced motivational drive
- increased errors of omission
- lapses in attention
- increased distractibility
- reduced vigilance and reaction time.
Inadequate quantity and quality of sleep is a primary contributor to fatigue. Most people generally require 7–8 hours of sleep to achieve a maximum amount of alertness and performance.
Pilot rostering
The PHP pilot rostering system involved the rotational allocation of pilots to ships in an ‘endless belt’ rotation where a pilot was allocated a pilotage task, then dropped to the bottom of the list, moving up as pilots further up the list were allocated pilotage tasks sequentially. The pilotage schedule and individual pilotage assignments were usually finalised between 1600–1800 every evening. Hagen Oldendorff’s pilot preferred to be awake at this time to ascertain when their next pilotage task was so they could plan their sleep accordingly.
Fatigue risk management system
Introduction
PHP operated a fatigue risk management system as part of the organisation’s contractual obligations to the PPA. The PHP fatigue risk management procedure (FRMP) formed part of the pilots’ SMS and compliance with the procedure was regularly audited. The procedure acknowledged that a channel blockage was a critical risk to the port, that pilot performance was a key mitigating risk control, and that fatigue-related impairment was a credible risk to pilot performance. The procedure identified that the most effective means to manage the effects of fatigue was to have restorative sleep and that the pilot’s work schedule was the primary means of managing pilot work and rest hours.
The FRMP provided a general overview of several methods, tools and criteria used in fatigue assessment. Of these, the procedure primarily applied the following 3 methods in assessing pilot fatigue and suitability for work:
- a biomathematical model fatigue assessment (FAID)
- a prior sleep wake model (PSWM)
- a fatigue self-assessment declaration.
The outcomes of these 3 elements of the PHP fatigue assessment determined whether a pilot could be assigned a given pilotage task. In the event a pilot breached any of these criteria, other options were considered, with the most common measure being to rotate that pilot out of the roster to a task at a more appropriate time, with the next pilot in line being assigned the ship movement.
Biomathematical fatigue model
Biomathematical models are tools for predicting fatigue levels based on a scientific understanding of the factors that contribute to fatigue. PHP utilised a software tool called Fatigue Audit InterDyne (FAID). The FAID bio-mathematical model of fatigue assessed the predicted level of fatigue based on the pilots’ rostered hours of work. Pilots logged the start and finish times of their pilotage tasks, and the FAID tool generated a predicted score for the expected completion time of the pilot’s following task.
A FAID score of 75 was considered the upper threshold for ‘normal’ pilotage jobs[46] although pilots with FAID scores of up to 80 could be rostered under certain circumstances with additional controls and approvals.
The incident pilot’s predicted FAID score at the completion of the Hagen Oldendorff pilotage was 73. That score was based on the time of day and duration of the pilot’s pilotage tasks over the previous 7 days, subsequent rest opportunities and, time of day and expected duration of Hagen Oldendorff’s outbound pilotage. The ATSB’s biomathematical analysis of the pilot’s roster using FAID produced similar results to the PHP score.
Prior sleep wake model
The prior sleep wake model (PSWM) was designed to account for actual sleep obtained and used 3 simple criteria to estimate when fatigue became an unacceptable risk in the workplace. The PHP PSWM proposed that:
- pilots should obtain a minimum of:
- 5 hours sleep in the previous 24-hour period
- 12 hours sleep in the previous 48-hour period
- time awake (the period from the pilot waking up to the end of their pilotage task) should not exceed the total sleep in the previous 48-hour period.
An automatic phone calling system notified pilots of their scheduled pilotage tasks 90 minutes prior to the planned pilot-on-board time. The pilot’s ‘time awake’ parameter for each shift was therefore calculated from 90 minutes prior to pilot-on-board time. The incident pilot usually set an alarm an additional 15 minutes before the time of the expected automated call.
A review of the pilot’s roster over the 72 hours before they woke to prepare for Hagen Oldendorff’s pilotage identified that the pilot had sufficient opportunity to obtain adequate, restful sleep.
Table 3 below details the pilot’s sleep opportunity over the preceding 3 days. The rest opportunity was calculated from one hour after the completion of a pilotage (to allow for travel back to accommodation) to 105 minutes before the next pilot-on-board time (the 90 minute automatic callout plus the pilot’s 15 minute allowance). The pilot estimated they woke at about 2230 on 8 April and boarded Hagen Oldendorff at 0018 on 9 April.
Table 3: Pilot rest opportunity leading up to the Hagen Oldendorff pilotage
Date | Rest opportunity (From/To) | Total rest opportunity |
8 April | 0610 on 8 April to 2230 on 8 April | 16 h 20 m |
7 April | 1500 on 7 April to 2351 on 7 April | 8 h 51 m |
6/7 April | 1645 on 6 April to 0833 on 7 April | 15 h 48 m |
Based on the pilot’s recollection and the PHP investigation report, the pilot estimated they obtained at least 8 hours of sleep in the 24 hours preceding the grounding. About 3–4 hours was reportedly obtained immediately before waking up for the pilotage with the rest obtained earlier during the day. Similarly, the pilot estimated they had obtained at least 8 hours of sleep every 24 hours over the preceding 2 days. While the sleep opportunity identified in Table 3 above demonstrates that it was possible for the pilot to have obtained the reported sleep, the pilot could not recall the exact hours of sleep obtained.
Fatigue self-assessment
The final element in the PHP fatigue assessment involved a subjective pilot self-assessment of their fatigue levels. The self-assessment was made using the Samn-Perelli fatigue scale – a scale from 1 to 7 – where 1 is ‘fully alert and wide awake’ and 7 is ‘completely exhausted, not able to function’.
The pilot self-assessed a fatigue score of 5 (Moderately tired, let down) at the commencement of the Hagen Oldendorff pilotage. However, the pilot also self-assessed the same score of 5 at the conclusion of the pilotage, indicating that the fatigue self-assessment was likely an unreliable risk control for fatigue.
Sleep quality
During their 4-week duty periods in Port Hedland, pilots generally resided in suitable accommodation that was quiet, temperature-controlled and conducive to restful sleep. Nevertheless, the nature of pilotage work meant that the sleep obtained was often not of optimal quality. Marine pilotage is typically characterised by irregular and unpredictable work periods (shifts) around the clock. This is particularly the case for pilotage in Port Hedland where most laden capesize ships can only be sailed out on the high tide.[47]
Research demonstrates that working these types of shifts results in sleep that is significantly shorter and of inferior recuperative value, even though many shifts are not excessive in length (Gregory et al, 2020; Chambers and Main, 2015). Sleep under these circumstances is also fragmented and more difficult to initiate (Weaver et al, 2021: 300). A study of 40 Australian marine pilots found that sleep quality following a night shift, where pilots are attempting to sleep in the early morning or day time, was significantly worse compared to sleep that occurred before working a day shift (Tait et al, 2021).
The pilot’s reported 8 hours of sleep was likely segmented, and the pilot reported that it was often difficult to get to sleep when assigned pilotage tasks in the early hours of the morning. The pilot also acknowledged that their sleep that day was ‘broken’ and ‘not good’. Analysis of the pilot’s mobile phone activity during the day showed that their reported 8 hours of sleep was probably broken into periods of between 2–5 hours’ sleep at a time. Sleep during the circadian peak for alertness (daytime hours), when we are least likely to fall asleep, generally results in a significantly reduced amount of recovery sleep (Akerstedt and Wright, 2009).
Effects of circadian rhythm
The grounding occurred at about 0140, during the nighttime circadian rhythm trough, and just outside the window of circadian low (WOCL, 0200 – 0600). Circadian effects on alertness and performance are well documented. Performance during the circadian trough is associated with lower alertness, slower reaction time, reduced cognitive performance and poorer accuracy compared to during the circadian peak (daytime hours) (Van Dongen and Dinges, 2005; Folkard and Tucker, 2003). However, the pilot’s rest opportunity/sleep over the preceding 72 hours included a period over the nighttime circadian trough (from 1645 on 6 April to 0833 on 7 April). Additionally, the presence of circadian effects in an occurrence is not sufficient on its own to establish the existence of fatigue (Riethmeister et al, 2019:158; Williamson and Friswell, 2011). Nevertheless, the pilot’s ability to manage the increased workload arising from managing the response to the incident was likely affected by the circadian effects of operating in the early hours of morning, just outside the WOCL.
Workload, stress and decision-making
Following the rudder angle indicator failure and the development of the turn to port, the pilot’s workload in managing the emergency naturally increased. Effective decision-making during an emergency is inherently challenging due to the time pressure, uncertainty, novelty, and the dynamic decisional environment (Reale et al, 2023). Research has shown decision-making under stress becomes less systematic and more hurried; fewer alternative choices are considered; and communication is reduced and of poorer quality, disrupting effective team performance (Dismukes, Goldsmith and Kochan, 2015).
For example, shortly after the ship started turning to port towards the side of the channel, the pilot ordered the rudder hard over to port. However, this order conflicted with the orders previously issued to the 3 escort tugs aimed at arresting the turn to port. The pilot’s rudder order of hard to port was an error on the part of the pilot who almost certainly intended to say, ‘hard to starboard’ and not ‘hard to port’. While documented effects of fatigue include increased incident of human error (Wickens et al, 2015), and decrements in vigilance, reaction time, information processing, and decision making (Rosekind et al, 1996:158), these behaviours are also characteristic of the effects of acute stress on decision-making under uncertainty.
Summary
The pilot’s FAID score of 73, PSWM hours of sleep and self-assessed fatigue score of ‘5’ was within the allowable limits of the PHP fatigue management procedure. Although, the pilot’s sleep history leading up to the grounding could not be definitively established, the pilot estimated obtaining at least 8 hours sleep in the preceding 24 hours and a similar amount of sleep each day over the previous 2 days. While the sleep in the 24 hours before the grounding was likely not of optimal quality, the 72-hour period before the grounding included an overnight rest opportunity when good quality sleep was most likely to be obtained.
Therefore, while there were factors that potentially reduced the pilot’s ability to obtain sufficient, restful sleep of the required quality, there was insufficient evidence to establish that the pilot’s sleep quantity and quality was impaired to the point where they were likely experiencing a level of fatigue known to have an effect on performance.
PHP fatigue trends
A PHP assessment of fatigue and roster data over a 3-year period from 2018–2020 identified that the number of alterations of the pilot roster sequence[48] due to unacceptable FAID and PSWM scores was increasingly trending upwards with an average of 21 changes per quarter.
The assessment acknowledged that while the FAID program considered sufficient sleep opportunity, it did not account for actual amount of sleep or sleep quality. Furthermore, it only considered the cumulative effects of a 7-day work history, rather than the entire 4-week duty period. The assessment also noted that the PSWM score did not differentiate between longer, better quality sleep and a series of shorter, lower quality sleep periods, which were often the case.
Purpose of safety investigationsThe objective of a safety investigation is to enhance transport safety. This is done through:
It is not a function of the ATSB to apportion blame or provide a means for determining liability. At the same time, an investigation report must include factual material of sufficient weight to support the analysis and findings. At all times the ATSB endeavours to balance the use of material that could imply adverse comment with the need to properly explain what happened, and why, in a fair and unbiased manner. The ATSB does not investigate for the purpose of taking administrative, regulatory or criminal action. TerminologyAn explanation of terminology used in ATSB investigation reports is available here. This includes terms such as occurrence, contributing factor, other factor that increased risk, and safety issue. Publishing informationReleased in accordance with section 25 of the Transport Safety Investigation Act 2003 Published by: Australian Transport Safety Bureau © Commonwealth of Australia 2024 ![]() Ownership of intellectual property rights in this publication Unless otherwise noted, copyright (and any other intellectual property rights, if any) in this report publication is owned by the Commonwealth of Australia. Creative Commons licence With the exception of the Commonwealth Coat of Arms, ATSB logo, and photos and graphics in which a third party holds copyright, this report is licensed under a Creative Commons Attribution 4.0 International licence. The CC BY 4.0 licence enables you to distribute, remix, adapt, and build upon our material in any medium or format, so long as attribution is given to the Australian Transport Safety Bureau. Copyright in material obtained from other agencies, private individuals or organisations, belongs to those agencies, individuals or organisations. Where you wish to use their material, you will need to contact them directly. |
[1] Based on the port’s dynamic under keel clearance (DUKC) system, the tidal window for the ship’s departure was between 0016 and 0156 on 9 April 2022. High water was at 0236 with a tide height of 5.25 m.
[2] The part of the ship where the curve of the bow meets the middle parallel body.
[3] Surface of the of the ship’s hull aft of midship and forward of the stern on either side.
[4] The Beaufort scale of wind force, developed in 1805 by Admiral Sir Francis Beaufort, enables sailors to estimate wind speeds through visual observations of sea states.
[5] One cable equals one tenth of a nautical mile or 185.2 m.
[6] In indirect towing, the tug uses its thrust to maintain a sheered position relative to the ship’s heading and generates towing forces (indirectly) by using a combination of the tug’s weight and drag on the tug’s hull and transmitted via the towline. When working at the stern of a ship, this method can generate substantially higher bollard pull at speeds through the water greater than 6 knots.
[7] All speeds referred to in this report are ‘made good/over the ground’.
[8] One knot, or one nautical mile per hour equals 1.852 kilometres per hour.
[9] A tug that follows a ship closely but is not connected via a towline.
[10] A voyage data recorder is designed to collect and store data from various shipboard systems in compliance with SOLAS requirements.
[11] Rate of turn is the instantaneous rate of change of the ship’s heading, expressed in degrees per minute.
[12] Direction of the bow of a vessel expressed in degrees, either true or magnetic. All ship’s headings in this report are in degrees by gyro compass with negligible error.
[13] The tugs providing indirect towage were equipped with a calibrated towline tension meter to monitor the towline tension and thereby the tow force being generated by the tug.
[14] Non-follow‑up (NFU) is a backup method for steering the ship. In the NFU mode, the rudder turns while the lever is held to port or starboard and remains at this angle when the lever is released.
[15] An event that poses significant risk to the safe or continued operation of the port by affecting safety of personnel in the port area, shipping channel, port assets or infrastructure
[16] FMG Dusky was returning after escorting the outbound ship Ocean Hong Kong and had just passed Hagen Oldendorff. Iron Ibis and Iron Whistler were returning after being dismissed from escorting another outbound ship, KN Amethyst, and were just ahead of Hagen Oldendorff. RT Darwin and Iron Kestrel were in the Hunt Point tug pens with RT Darwin having been earlier dismissed from Hagen Oldendorff, while Iron Kestrel was preparing for the departure of another ship.
[17] A detention is an intervention action taken by the port state when the condition of the ship or its crew does not correspond substantially with the applicable conventions. The action is taken to ensure that the ship will not sail until it can proceed to sea without presenting a danger to the ship or persons onboard, or without presenting an unreasonable threat of harm to the marine environment, whether or not such action will affect the scheduled departure of the ship.
[18] Incident report alert form 18 and incident report form 19, available at www.amsa.gov.au
[19] BHP own and operate 8 berths at Port Hedland for the export of iron ore.
[20] Capesize ships generally have dimensions larger than that allowable for transit of Panama and Suez Canals and therefore have to sail around Cape Horn and the Cape of Good Hope.
[21] International Maritime Organization, 2014, The International Convention for the Safety of Life at Sea (SOLAS) 1974 as amended, IMO, London.
[22] SOLAS Ch V/Reg 26
[23] International Maritime Organization, 2018, International Management Code for the Safe Operation of ships and for Pollution Prevention (ISM Code) as amended, IMO, London.
[24] SOLAS Ch V/Reg 14
[25] International Chamber of Shipping 2016, Bridge Procedures Guide, Marisec Publications, London.
[26] SOLAS Ch II-1/Reg 29
[27] SOLAS Ch V/Reg 19
[28] Lloyd’s Register, 2019, Rules and Regulations for the Classification of Ships, Part 5 Main and Auxiliary Machinery, Chapter 19 Steering Systems, Section 4 Steering control systems.
[29] The port’s annual throughput for the year 2021-2022 was 561 million tons from 3,289 vessel visits and with iron ore exports making up 93.4% of the port’s export commodities.
[30] In 2001, BHP Limited merged with Billiton Plc to form BHP Billiton. In 2018, ‘Billiton’ was dropped from the organisation’s name, and it is now known as BHP.
[31] An azimuth thruster is a type of marine propulsion unit where a propeller is integrated into a pod which can be rotated 360° thereby integrating the propulsion and steering functions into a single unit.
[32] A ‘Z-drive’ is a transmission configuration used to connect the mechanically‑supplied driving energy to the azimuth thruster device, such that the rotary motion has to make 2 right angle turns (thus resembling the letter ‘Z’).
[33] ‘Bollard pull’ is the most commonly used measure of a tug’s performance. It can be described as the maximum thrust developed by the tug’s propulsion systems when it is stationary in the water. When the tug is making way, the towing force generally decreases due to external factors such as weather and the underwater resistance of the tug’s hull.
[34] A pair of upright cylindrical steel posts projecting above the deck of a ship used for securing lines, in this case, for towing.
[35] In September 2017, the PPA notified ship operators that cape size ships calling at Port Hedland were required to have a set of towing bitts and a Panama lead rated to a minimum SWL of 120 t on the vessel’s aft deck. These requirements came into force on 1 February 2021.
[36] Significant wave height (Hs) is traditionally defined as the average height of the highest one-third of the waves experienced over time and generally corresponds to the wave height visually estimated by a skilled observer such as an experienced mariner.
[37] A render/recover winch is a dynamic, constant-tension winch control system that was capable of automatically hauling in and paying out the towline as required to maintain a constant tension on the line.
[38] The Pilbara Ports Authority (PPA) was established on 1 July 2014, as a result of the Ports Legislation Amendment Act 2014 which consolidated 7 of Western Australia’s 8 port authorities into 4 new regional port authorities. The PPA was formed by the amalgamation of the former port authorities of Dampier and Port Hedland and also encompassed the ports of Ashburton and Varanus Island.
[39] Port Hedland Pilots were required to comply with the relevant requirements of the International Standard for Maritime Pilot Organizations (ISPO) – an international standard of best practice for pilotage organisations with certification carried out by recognised classification societies. ISPO accreditation was maintained through regular audits of PHP operations and the SMS.
[40] Marine notices are published by the Australian Maritime Safety Authority (AMSA) and provide important safety‑related information, general guidance and details about upcoming changes to legislation to the shipping and maritime community.
[41] KN Amethyst and Ocean Hong Kong were the 2 outbound ships ahead of Hagen Oldendorff. KN Amethyst departed Finucane Island berth ‘B’ about an hour before Hagen Oldendorff departed, while Ocean Hong Kong departed Anderson Point berth 1 about 30 minutes before Hagen Oldendorff.
[42] A PPU is a specialised navigation aid used by pilots and typically consists of a tablet or laptop device loaded with electronic chart software, with associated position reference systems and sensors to provide position, heading and automatic identification system (AIS) data. The PPU may have its own independent sources for this data, or it may rely upon connection to the ship’s pilot plug to source this data from the ship’s navigational equipment.
[43] Australasian Marine Pilots Institute, 2020, AMPI PPU Code of Good Practice – For the implementation and use of Portable Piloting Units, 2nd edition, AMPI, Wollongong, New South Wales.
[44] The automatic identification system (AIS) is a maritime communications system that uses the very high frequency (VHF) radio band to transfer data such as a vessel’s course, speed and other dynamic and static data. The system enables AIS-equipped vessels and shore-based AIS stations to send and/or receive identification information that, in addition to the AIS unit, can be displayed on an electronic chart system, compatible radar or PPU.
[45] International Maritime Organization, 2019, MSC.1/Circ.1598 Guidelines on Fatigue, London, United Kingdom.
[46] The FAID score threshold was reduced to 70 in the event of an ‘abnormal’ pilotage task. An ‘abnormal’ pilotage task was one that involved factors that were likely to increase pilot workload, for example, strong winds, large tidal ranges, reduced visibility or a vessel with poor handling characteristics.
[47] Port Hedland predominantly experiences semi-diurnal tides with 2 high tides (high water) and 2 low tides (low water) every lunar day (24 hours and 50 minutes). Further, the deepest draught ships that call at Port Hedland can often only be sailed out on the spring tides which occur twice every lunar month (approximately 29.5 days). Ships that miss this sailing window may then have to remain in port for the duration of the neap tides until the next spring tide.
[48] An alteration of the pilot roster sequence usually occurred when a pilot in the belt roster had to be skipped and moved further down the sequence due to an exceedance of one of the 3 fatigue criteria (unacceptable FAID/PSWM score or adverse fatigue self-assessment).