Executive summary
What happened
On 26 June 2024, a De Havilland Canada DHC-8-402 (Dash 8), was preparing to operate a QantasLink passenger flight from Horn Island to Cairns, Queensland. The flight crew identified that the take-off would be performance-limited due to the runway length at Horn Island and the high passenger and cargo weights. The crew determined that a flap setting of 15° and the bleed air system switched off was required for take-off.
During pre-flight preparation, the first officer (FO) was the pilot flying and inadvertently selected a flap setting of 5° instead of the required flap setting of 15°. The crew completed the after start checks and after start checklists in accordance with the standard operating procedures, however neither the first officer, nor the captain as pilot monitoring, detected the incorrect flap setting.
During the initial take-off run, the Dash 8 accelerated normally, however the crew noted that the aircraft’s rotation was slow and that the aircraft performance differed from their usual experience during take-off. The first officer’s application of continued back pressure to the controls during the take-off run resulted in the aircraft successfully becoming airborne slightly after the expected rotation speed. The first officer identified that the flaps were configured at a setting of 5° and immediately advised the captain. The captain instructed the first officer to continue to fly the aircraft. The first officer slightly lowered the nose of the aircraft to increase airspeed. The aircraft accelerated in response to this action and a positive rate of climb was maintained. The flight continued to Cairns without further incident.
What the ATSB found
During preparation for take-off from Horn Island, the FO inadvertently selected the flap lever to 5° instead of the required setting of 15°. This was likely due to habitual behaviour as the flap setting of 5° was the most common take-off flap setting for other sectors in the network and was the flap setting required on the 2 sectors flown prior to the incident. Standard pre‑flight checks and crosschecks were conducted, however the flight crew failed to identify the incorrect flap setting before take-off at Horn Island. This was likely due to automatic behaviour by the crew registering flap 5° to be the usual setting at take-off.
What has been done as a result
Following the occurrence, the operator implemented the following organisational and operational, changes:
- Review of standard operations procedures as necessary to reduce the likelihood of erroneous flap selection and misidentification.
- Review of relevant checklists to strengthen crosschecking in accordance with the computed take-off performance data.
- Training for crew focusing on standard operating procedures and compliance.
Safety message
The preparation, taxi and take-off phases of flight involve high workload and demand heightened attention to ensure correct settings are selected as unintentional slips can easily occur without. To minimise the risk of slips going unnoticed, flight crews must carefully verify and methodically complete checks and checklists. Maintaining focus and staying mindful of potential deviations to usual settings is essential during periods of high workload for safe operations.
The investigation
Decisions regarding the scope of an investigation are based on many factors, including the level of safety benefit likely to be obtained from an investigation and the associated resources required. For this occurrence, a limited-scope investigation was conducted in order to produce a short investigation report and allow for greater industry awareness of findings that affect safety and potential learning opportunities. |
The occurrence
On 26 June 2024, a De Havilland Canada DHC-8 402 (Dash 8) registered VH-QOI was being prepared to operate a QantasLink passenger flight from Horn Island, Queensland, following an arrival from Cairns. The aircraft arrived at Horn Island airport about 1015 local time and was scheduled to return to Cairns at 1055 with the same flight crew. The crew consisted of the first officer (FO), assigned as the pilot flying, the captain in the role of pilot monitoring and 2 cabin crew.
The flight crew followed standard pre-departure procedures in preparation for the flight. The FO loaded the flight plan into the flight management system (FMS)[1] and the captain confirmed the FMS was programmed in accordance with the flight plan. During the confirmation, the captain had to adjust performance data calculations that had previously been entered. This was prompted by a revised forecast for adverse weather conditions for arrival at Cairns and a full passenger load. The captain reported repeatedly checking the automatic weather information service due to changes in the prevailing wind and efforts to avoid offloading any passengers due to weight restrictions. The captain stated that they made several calls to load control and frequently checked the automated weather information service to calculate the headwind component for the final performance data which allowed for the uplift of all the passengers and their baggage.
The main runway length for runway 08 at Horn Island is considered performance limiting for Dash 8 operations at a length of 1,389 m, with higher terrain near the departure end presenting a potential obstacle. The captain was cognisant of the aircraft performance limitations as the aircraft was carrying a full load. The calculation of thrust requirements, and the corresponding FMS entries, were made prior to the engine start. The FO reported that each flight crew programmed their own Aerodata apps[2] on their iPads to calculate the airspeeds required for take-off, based on the weather information and the aircraft weight. The final weight of the aircraft was 27,800 kg and was close to the maximum regulated take‑off weight (RTOW). The Aerodata results produced a requirement to turn off the bleed air system to provide the increased thrust necessary for take-off with a flap[3] setting of 15°. The FO recorded this information on the take-off and landing distance card (TOLD)[4] card.
After the passengers were boarded, the flight crew conducted the before start procedure and then commenced taxiing to runway 08. The crew then conducted the after start checks and checklist, during which time the FO inadvertently selected flap 5° instead of 15°. The checklist is completed as a ‘challenge and response’ format. The FO calls the check which requires a verbal confirmation from the captain. One of the items on the list specifically called for is the flap setting. The FO called for ‘flaps’ and recalled that they checked that flap 5 was indicating for the flap lever and the digital indications. However, the captain did not recall the response given for this challenge during interview.
For the take-off run, the crew reported no issues with acceleration as the aircraft increased speed along the runway until the captain called for ‘V1’[5] and ‘rotate’. The FO described the rotation as slow but reported rationalising the heavy weight of the aircraft as the reason and continued to apply more pressure to the control column until the aircraft rotated about 5 kt after the planned rotation speed.
The flight crew noticed that aircraft performance was not what they would normally expect at the start of the climb. The captain checked the speeds and trim which were identified as being set correctly. At about the same time, the FO checked the flap setting and noticed that the flaps were configured to 5° and alerted the captain immediately.
By this time, the main landing gear was up and the captain instructed the FO to continue to fly the aircraft. The FO momentarily lowered the nose of the aircraft by a small amount to assist with increasing the airspeed. The aircraft accelerated and continued to Cairns without further incident.
Context
Aircraft information
VH-QOI was manufactured in Canada in 2008 and was powered by 2 Pratt & Whitney Canada PW150A (turboprop) engines.
Flight crew information
The captain held an air transport pilot licence (aeroplane) and had been flying for about 30 years with a total aeronautical time of about 8,450 hours, of which 5,800 hours were on the Dash 8.
The FO had been flying for 12 years and held a commercial pilot licence (aeroplane) with about 3,870 hours, of which 346 were on the Dash 8.
Both pilots had valid class one medical certificates.
Meteorological conditions
The meteorological aerodrome report provided the weather observations for Horn Island as warm and humid, with moderate south-east winds to 13 kt, good visibility and broken to overcast clouds. The valid terminal forecast for Cairns airport was issued at 0902 local time and identified a temporary forecast for showers of moderate rain and scattered cloud at 3,000 ft with periods of 30–60 minutes where showers of rain were forecast, potentially reducing visibility to 7,000 m.
Airport information
Horn Island airport is located at the northern end of Cape York Peninsula and is one of the primary airports for local transportation. The main runway orientation is 08/26 and is 1,389 m in length and has an elevation of approximately 13 m above mean sea level. Some higher terrain and trees are located at the of end of runway 08 and are a potential obstacle.
Recorded information
Flight data from the aircraft’s quick access recorder (QAR) was provided to the ATSB and contained about 70 seconds of data, recorded at one-second resolution, commencing at the beginning of the take-off on runway 08 at Horn Island (Figure 1). The data indicated that the Dash 8 had the flaps set to 5° prior to taxi and were retracted as the aircraft was flying through 1,406 ft above mean sea level.
Figure 1: QAR derived flight data depicting aircraft position and flap setting
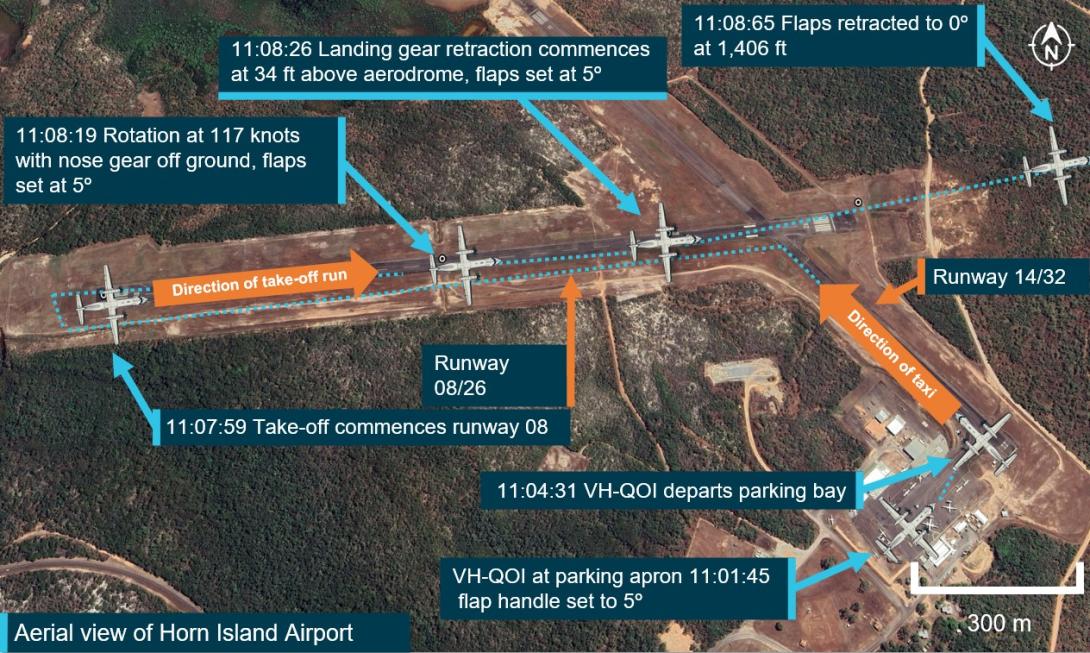
Source: QAR data and Google Earth, annotated by the ATSB (all heights indicated as above mean sea level)
Note: Dash 8 figures not to scale
Take-off distance
In the event of an engine failure during take-off, pilots must actively monitor several key speed parameters in order to ensure the aircraft can either continue or reject the take-off and stop on the runway if necessary. These are collectively referred to as ‘V speeds’.
- Should an engine failure occur before V1 the aircraft should be able to stop within the distance of the remaining runway.
- V2 is the speed that ensures that the aircraft can continue climbing safely with one inoperative engine in an emergency.
- Vr is the speed at which the rotation of the aircraft is initiated to take-off attitude. This speed cannot be less than V1
The QAR data determined that the mismatch in actual versus intended take-off flap configuration meant that the calculated take-off reference speeds and aircraft performance differed. The Dash 8 aircraft scheduled speeds for flap settings are stipulated in the operator’s aircraft performance manual (APM) (Figure 2).
Flap settings for take‑off
Pilots use different flap settings to increase or decrease performance during take-off and landings. The flap setting deployed for the take-off phase contributes to the performance of the aircraft on the take-off roll and the initial airborne segment. The Dash 8 flap setting requirements for take-off are stated in the APM and are based on the performance data, such as the prevailing weather conditions and aircraft take-off weight.
The crew advised that the performance calculations for the Dash 8 at Horn Island on the day required a flap setting of 15° for take-off to account for the lift required due to the limiting factor of the short runway. This setting was unusual for the crew as they stated that the last two sectors flown, the flap setting of 5° had been used and that, in their experience, flaps of 5° was the normal setting for take-off at most of the airports in the airlines network.
Figure 2: APM specified take-off performance for flap settings 5 and 15 degrees
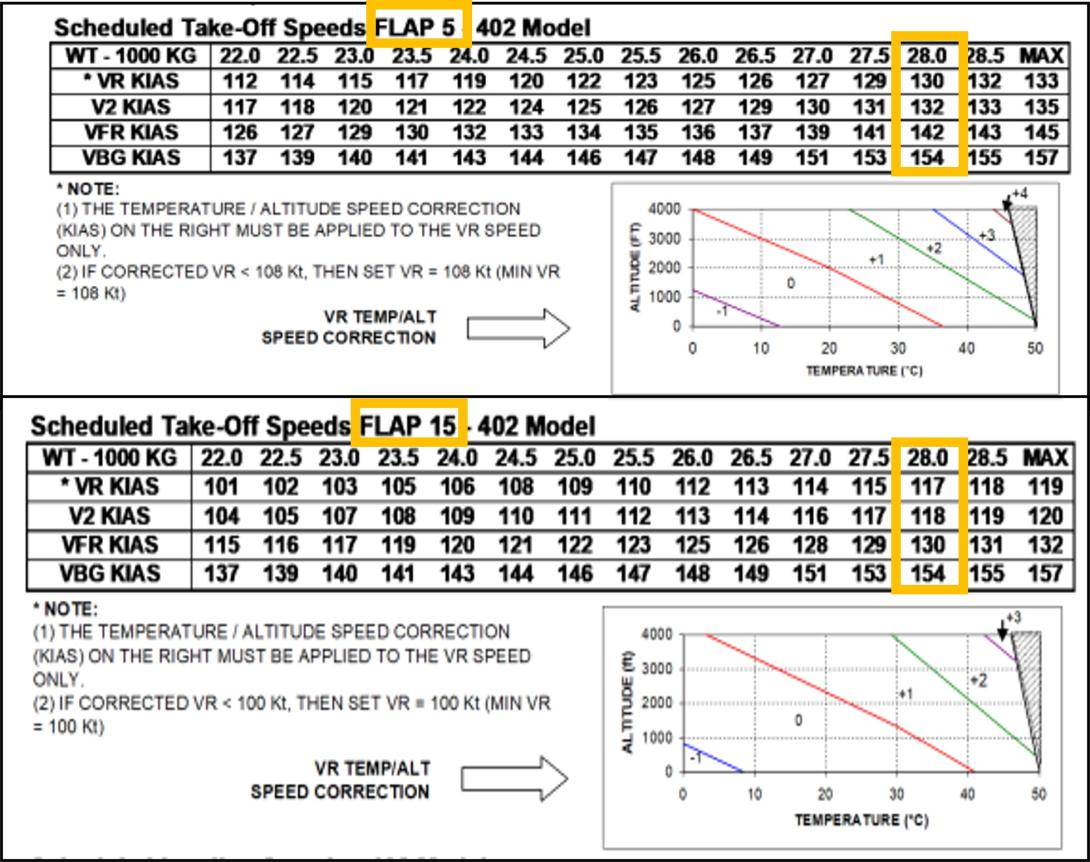
Source: APM provided by operator, annotated by the ATSB
Bleed air system
The bleed air system plays a role in multiple aircraft functions and operates through a network of ducts, valves, and regulators using high pressure air bled from the compressor section of the engine and auxiliary power unit. Turning off the bleed air system provides extra engine performance and maximises take-off power, which is beneficial for optimal performance on short runways with a high payload. The requirement to turn off the bleed air was not a routine occurrence, the FO reported they were very conscious of remembering ‘bleeds off’ for the take-off and so had written themselves a reminder note.
Procedures for pre-departure checks
At each critical phase of aircraft operation, pilots refer to checklists to guide them through specific items to configure the aircraft for the next planned phase of the flight. These enhance safety by providing an opportunity to confirm that the safety‑critical aspects of the aircraft configuration are correctly set. Consequently, any omissions or mistakes are more likely to be identified and rectified by the flight crew. Checklist deviations occur relatively frequently, compared to other forms of procedural deviation. A common form of checklist deviation includes responding without checking (Dismukes and others, 2010).
The company flight crew operating manual[6] (FCOM) states that many checklists are preceded by ‘checks’ which are memory items completed prior to actioning the checklist. For example, in the case of the after start checks, the captain will ask for the after start checks and the crew conduct their check flows, then the FO reads the after start checklist and the captain responds to the checklist. The standard operating procedures (SOPs) are outlined in the FCOM which documents 4 procedures that could potentially identify an incorrect flap setting:
- departure briefing
- take-off data crosscheck
- after start checks
- after start checklist.
Departure briefing
Crew departure briefings are intended to bring awareness of operational information and conditions that are not covered in the SOPs. The flap setting of 15° is an uncommon flap setting on the network and although there was no mandatory requirement to brief the take‑off flap setting, it did provide an opportunity to acknowledge the flap setting of 15° as an operational consideration or as a threat. Neither the FO nor the captain recalled if the flap setting was included as a threat in the content of the briefing. Calling out the flap setting as a threat would have provided a prompt to the crew which may have made the incorrect flap setting easier to detect. The crew stated that as they had previously flown out of Horn Island, the take-off flap setting of 15° was not considered abnormal unless a pilot had not previously flown from the aerodrome. The crew recalled that the ‘bleeds off’ procedure was briefed.
Take-off data crosscheck
The take-off data crosscheck required the captain to verify the take-off weight, runway distance intersection, and the flap setting from their Aerodata app while the FO was required to confirm the aircraft weight using the load sheet. The captain then ensured the correct take-off speeds were displayed on their primary flight display (PFD), which the FO cross referenced with their own PFD. The captain and the FO reported completing this step. Following this, the captain read the take-off speeds from the Aerodata and their PFD and the FO was required to verbally reiterate the speeds read from their own PFD.
After start checks
Among other items, the after start checks required the FO to set the flaps for take-off and that to complete this task, the Aerodata or TOLD card should be referenced to set and confirm the flap setting. The FO reported setting the flaps to 5° but could not remember referring to the Aerodata or the TOLD card to do this and recalled they may have had the load sheet or something else displayed on their iPad.
After start checklists
Directly following the after start checks, the after start checklist was a ‘challenge and response’ format which prompted for verification of the take-off data and flap settings among several other items. The captain and the FO reported they had no recollection of the response provided for the flap-setting challenge. On completion of this checklist, the captain and the FO had not detected that the flap setting was 5° which contrasted with the Aerodata display that showed a required flap setting of 15°.
Operator’s report
The findings from the operator’s internal safety investigation report stated that the flap setting of 5° increased the risk for tailstrike and reduced the margin for obstacle clearance. The aircraft would have been 2,112 kg overweight for take-off configured with a flap setting of 5° (Figure 3). The report determined that the required take-off distance with flap setting of 5° was 1,680 m which was greater than the available runway distance. However, the report concluded that as the aircraft was configured with flap 15° speeds set for take-off, the decision to reject the take-off would have been made with reference to the bugged[7] V1 speed of 116 kt and the accelerated stop distance required (ASDR)[8] would have been adequate. Therefore, the operator calculated that in the event of a rejected take-off, at or below the V1 that was set, the aircraft would have had sufficient deceleration to come to a stop before the runway threshold.
Figure 3: Aerodata performance calculations for VH-QOI for a flap settings of 15° and 5°
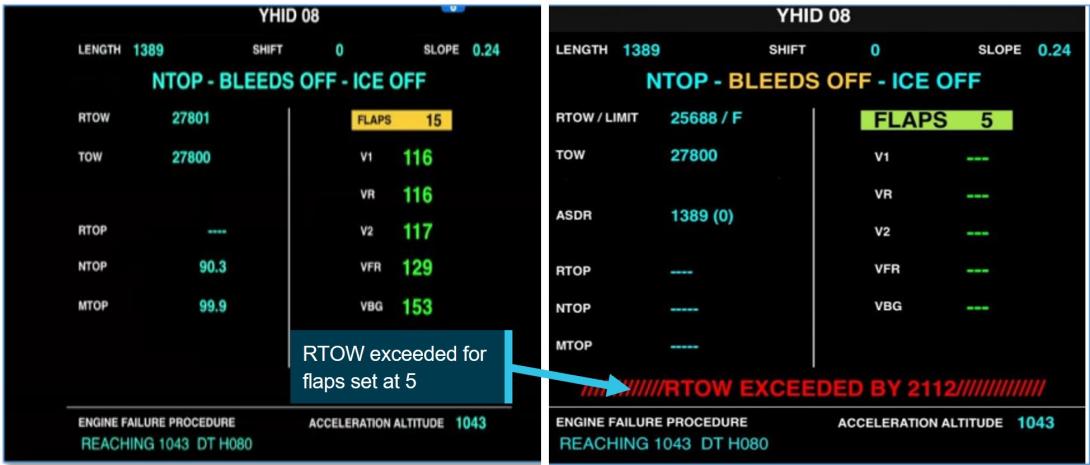
Source: Reproduction provided by operator, annotated by the ATSB
Fatigue
Fatigue is defined as a decrease in performance as a function of time on task (Salas and others, 2010). Fatigue can have a range of adverse influences on human performance and can lead to slips or lapses associated with attention, problem-solving, memory, vigilance and decision‑making. ATSB has identified that people experiencing fatigue are not able to accurately evaluate their own fatigue level or their ability to perform tasks, rather they tend to overestimate their abilities (ATSB, 2019). As such, fatigue is considered an important safety concern and an ATSB SafetyWatch priority.
The flight crew’s previous 72-hour roster allowed for regulated sleep opportunities. The flight crew commenced duty from Townsville at 0600 where they had stayed overnight. Their duty roster included three sectors for the day:
- Townville–Cairns
- Cairns–Horn Island
- Horn Island–Cairns.
Both flight crew members had presented for duty that morning stating they were fit to fly, although both reported to the ATSB that the environmental conditions at their accommodation in Townsville were not conducive for sleep. The captain noted that their sleep was broken due to noise and air‑conditioning issues and self-reported being a little tired at the commencement of duty as their previous night’s sleep prior to the incident was poor. The FO described their alertness at the beginning of duty as very lively and their sleep quality as good but also reported sleep disruption due to unreliable air-conditioning in the room. The ATSB concluded that it was very unlikely that either crew were experiencing fatigue to a level that could influence performance.
Safety analysis
Introduction
During a scheduled sector from Horn Island to Cairns, a reduced aircraft performance during take‑off and the initial climb did not align with the flight crew’s expectations. The first officer (FO), as the pilot flying, discovered that the flap setting was incorrectly configured at 5° instead of 15° and advised the captain. The aircraft was established in a positive climb and continued the flight without further incident.
This analysis will discuss factors that contributed to the incorrect aircraft configuration and lack of detection during the pre-flight crosschecks.
Crew actions
The inadvertent selection of the flaps to 5° instead of 15° by the FO was likely influenced by habitual behaviour driven by prior experience. A flap setting of 5° had been used for the previous two sectors flown by the flight crew and was, in their experience, the most common setting for take-off at most of the airports in the operator’s network. It is likely therefore, that the FO developed an unconscious habit for a flap setting of 5°, and the setting of 5° was a result of a slip. A slip is a form of human error defined to be the performance of an action that was not intended (Reason, 1990). Slips often occur during the largely automatic performance of routine tasks, usually in familiar surroundings, and characteristically involve an incorrect implementation of an intention (Mylopoulos, 2022). If other factors are also present, such as distraction, then the chance of such errors occurring increases. This type of slip cannot be eliminated by training alone, however, improvements in system design can reduce the likelihood of occurrence and provide a more error tolerant environment, which is why checks of the flap setting are built into the pre-flight processes (the after start checklist).
The flight crew reported adhering to the procedures for the pre-departure checks which provided 4 occasions to potentially identify or rectify the incorrect flap setting. Flight crews are particularly vulnerable to checklist errors during the pre-flight sequence in the time‑compressed phase of pre‑departure (Loukopoulos, and others, 2001). Under normal pre‑flight procedures workload is usually at a high level and for this flight the extra calculations for weight, weather and performance limitations elevated the crew workload. When workload is high, automaticity can be amplified as the mind seeks to conserve energy by relying on well learned routines (Bermúdez and others, 2021). This can be detrimental when a situation requires mindful engagement. The flight crew likely conducted the after start checklist with a high degree of automaticity, rather than consciously verifying the flap setting against the Aerodata or TOLD card. In this case there was a breakdown of this normal layer of defence, which emphasises how safety measures can be degraded if crews are not consciously focused on the task. It was possible that the crew had diminished sensitivity for error detection due to completing the checklist without carefully ensuring the confirmation of each of the steps.
As a result, the crew performed the take‑off with the flaps inadvertently at 5° instead of 15°. The incorrect configuration reduced the intended performance envelope of the aircraft. The FO’s continued back pressure to the controls during the take-off run resulted in the aircraft successfully becoming airborne slightly after the expected rotation speed. The FO’s actions to reduce pitch during the take‑off increased the airspeed and the aircraft maintained a positive climb.
Findings
ATSB investigation report findings focus on safety factors (that is, events and conditions that increase risk). Safety factors include ‘contributing factors’ and ‘other factors that increased risk’ (that is, factors that did not meet the definition of a contributing factor for this occurrence but were still considered important to include in the report for the purpose of increasing awareness and enhancing safety). In addition ‘other findings’ may be included to provide important information about topics other than safety factors. These findings should not be read as apportioning blame or liability to any particular organisation or individual. |
From the evidence available, the following findings are made with respect to the incorrect configuration involving Bombardier DHC-8, VH-QOI, at Horn Island Airport, Queensland on 26 June 2024.
Contributing factors
- The FO mistakenly set flaps to 5° for take-off at Horn Island when pre-flight planning identified flaps 15° should have been set.
- Standard pre-flight checks and crosschecks were conducted, however the flight crew failed to identify the incorrect flap setting before take-off at Horn Island. This was likely due to automatic behaviour by the crew registering flap 5° to be the usual setting at take-off.
- The incorrect configuration of the aircraft reduced the climb performance and potential obstacle clearance on departure from Horn Island.
Safety actions
Whether or not the ATSB identifies safety issues in the course of an investigation, relevant organisations may proactively initiate safety action in order to reduce their safety risk. All of the directly involved parties are invited to provide submissions to this draft report. As part of that process, each organisation is asked to communicate what safety actions, if any, they have carried out to reduce the risk associated with this type of occurrences in the future. The ATSB has so far been advised of the following proactive safety action in response to this occurrence. |
Safety action by QantasLink
In response to this occurrence the ATSB was advised by QantasLink that the following actions had been undertaken:
- Review of standard operating procedures to strengthen procedures as necessary to reduce the likelihood of erroneous flap selection and misidentification.
- Review of relevant checklists to strengthen crosschecking in accordance with the computed take-off performance data.
- Training for crew focusing on standard operating procedures and compliance.
Sources and submissions
Sources of information
The sources of information during the investigation included:
- interviews with the captain and first officer
- QantasLink internal safety report
- recorded data from the aircraft QAR.
References
ATSB (2019) Fatigue experiences and culture in Australian commercial air transport
Bermúdez, J. P., & Felletti, F. (2021). Introduction: Habitual Action, Automaticity, and Control. Topoi, 40(3), 587-595.
Dismukes, R., & Berman, B. (2010). Checklists and monitoring in the cockpit: Why crucial defenses sometimes fail (No. ARC-E-DAA-TN1902).
Reason, J. (1990). Human error. Cambridge University Press.
Salas, E., & Maurino, D. (Eds.). (2010). Human factors in aviation. Academic Press.
Submissions
Under section 26 of the Transport Safety Investigation Act 2003, the ATSB may provide a draft report, on a confidential basis, to any person whom the ATSB considers appropriate. That section allows a person receiving a draft report to make submissions to the ATSB about the draft report.
A draft of this report was provided to the following directly involved parties:
- flight crew consisting of captain and first officer
- QantasLink
- CASA
Submissions were received from:
- QantasLink
- flight crew – captain and first officer
- CASA
The submissions were reviewed and, where considered appropriate, the text of the report was amended accordingly.
Purpose of safety investigationsThe objective of a safety investigation is to enhance transport safety. This is done through:
It is not a function of the ATSB to apportion blame or provide a means for determining liability. At the same time, an investigation report must include factual material of sufficient weight to support the analysis and findings. At all times the ATSB endeavours to balance the use of material that could imply adverse comment with the need to properly explain what happened, and why, in a fair and unbiased manner. The ATSB does not investigate for the purpose of taking administrative, regulatory or criminal action. TerminologyAn explanation of terminology used in ATSB investigation reports is available here. This includes terms such as occurrence, contributing factor, other factor that increased risk, and safety issue. Publishing informationReleased in accordance with section 25 of the Transport Safety Investigation Act 2003 Published by: Australian Transport Safety Bureau © Commonwealth of Australia 2025
Ownership of intellectual property rights in this publication Unless otherwise noted, copyright (and any other intellectual property rights, if any) in this report publication is owned by the Commonwealth of Australia. Creative Commons licence With the exception of the Commonwealth Coat of Arms, ATSB logo, and photos and graphics in which a third party holds copyright, this report is licensed under a Creative Commons Attribution 4.0 International licence. The CC BY 4.0 licence enables you to distribute, remix, adapt, and build upon our material in any medium or format, so long as attribution is given to the Australian Transport Safety Bureau. Copyright in material obtained from other agencies, private individuals or organisations, belongs to those agencies, individuals or organisations. Where you wish to use their material, you will need to contact them directly. |
[1] FMS is an avionics system. It supports navigation, flight plans, positioning, guidance and other flight-related tasks.
[2] Aerodata software is QantasLink’s primary method for calculating take-off data.
[3] Flaps are hinged inboard trailing edge surfaces on an aircraft’s wings that can be extended down or retracted upwards.
[4] Take-off and Landing Distance card – a quick reference guide for data fields pertaining to take-off and landing.
[5] V1 is the maximum speed at which a rejected take-off can be initiated in the event of an emergency. V1 is also the minimum speed at which a pilot can continue take-off following an engine failure.
[6] The Flight Crew Operating Manual (FCOM 4.42, March 2024) is issued by the manufacturer as a guideline for operators to develop their own standard operating procedures (SOPs) in accordance with applicable requirements.
[7] Speed bugs are small pointers on the airspeed indicator, usually referred to as bugs. Pilots use the bugs as references for important take-off speeds.
[8] ASDR is the distance required to accelerate from brake release to V1, experience an engine failure at V1 and decelerate to a stop.