Executive summary
What happened
On the morning of 22 April 2023, World Diana departed from berth no 3 in Bunbury under the conduct of a harbour pilot with 2 tugs assisting. The ship had to be manoeuvred into the inner harbour turning basin and turned to port to exit the harbour entrance. The turn did not go as planned and the ship’s bow grounded on a shallow bank to the east of the entrance.
The ship was then manoeuvred clear of the bank and departed the port. Subsequent inspections and surveys indicated minor hull damage and the ship was cleared to continue trading.
What the ATSB found
The ATSB investigation found that World Diana's turn to port was started earlier than planned, which reduced the available sea room to complete the turn. During the turn, the ship’s speed was allowed to increase until there was no room to safely turn, and the ship grounded.
The ATSB also found that bridge resource management during the pilotage was ineffective. The pilot set up the portable pilot unit but did not use the unit to its full potential. The departure plan did not provide any specific information or limits for the turn to either the ship’s bridge team or the tug masters. Nevertheless, while the tug masters had previous experience with this manoeuvre and the ship’s bridge team had further resources available no concerns were raised with the pilot until it was too late to avoid the grounding.
Finally, the investigation identified that the port had not developed adequate procedures that included arrival and departure plans for larger ships required to berth starboard side alongside berth no 3.
What has been done as a result
Southern Port Authority has updated its marine pilotage standards and procedures for Bunbury with standard procedures for departing all berths, including no 3 when berthed starboard side alongside. A maximum rate of turn for turning ships in the harbour has also been specified.
Safety message
This grounding illustrates the important part that bridge resource management plays in safe pilotage. Effective use of available resources reduces the chance of single-person errors and minimises their impact.
In this instance, proper use of the portable pilot unit, effective communication and active involvement of the World Diana’s bridge team and the tug masters would have allowed the deviation from the plan to be detected in time to prevent the grounding.
The investigation
Decisions regarding the scope of an investigation are based on many factors, including the level of safety benefit likely to be obtained from an investigation and the associated resources required. For this occurrence, a limited-scope investigation was conducted in order to produce a short investigation report, and allow for greater industry awareness of findings that affect safety and potential learning opportunities. |
The occurrence
On the morning of 22 April 2023, the bulk carrier World Diana was scheduled to depart the Port of Bunbury, Western Australia under the conduct of a harbour pilot. The ship was berthed starboard side alongside at berth no 3 (head-in) and needed to be manoeuvred into the inner harbour turning basin and then turned to port towards the harbour entrance (Figure 1). The ship was nearly fully laden with a cargo of grain and had a draught of 11.65 m forward and 11.69 m aft (a deep draught for the port).
Figure 1: Overview of Bunbury inner harbour with World Diana at berth no 3
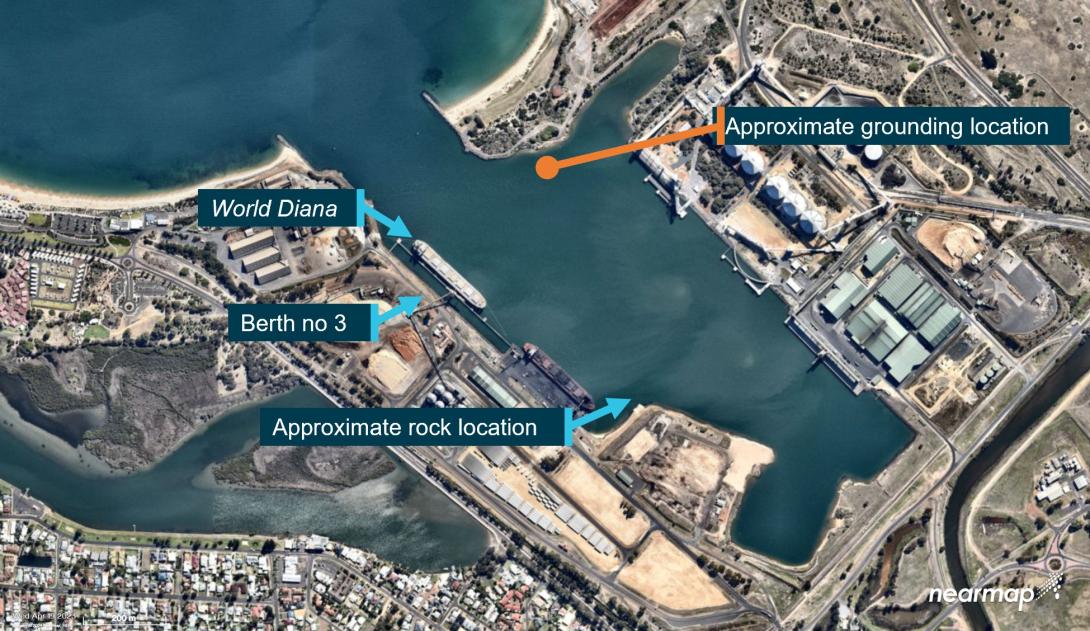
Image source: Nearmaps, annotated by ATSB
From about 0542 local time, the pilot conducted a master-pilot information exchange (see the section titled Bridge resource management) on the ship’s navigation bridge (bridge), including discussing the departure plan. The 2 tugs allocated for the departure were made fast forward and aft on the port side. At 0620, the mooring gang arrived and began casting off the ship’s mooring lines as directed by the pilot.
At 0632, when all the mooring lines had been cast off, the pilot instructed both tug masters to ‘lift off’[1] using quarter power and, shortly after, asked them to increase to half power. By 0636, the ship had developed slight headway (0.3 kt)[2], with its main engine running dead slow ahead.
Soon after, the pilot stopped the ship’s engines and commenced turning the ship to port by directing that the aft tug stop lifting off and push at half power. The forward tug was directed to continue lifting off. At 0640, the ship’s speed had increased to 1.5 kt and the engine was ordered half astern. The ship’s rate of turn was 25°/minute and the forward tug was directed to stop (no weight on the tow line) while the aft tug continued pushing on the port side aft at full power.
As World Diana turned, its headway increased (1.6 kt) and, by 0641, the ship’s bow was closing on the shallow water on the eastern side of the harbour entrance at about 2.0 kt (Figure 5). At 0642, the forward tug master advised the pilot that the yellow buoys marking the shallow water were very close. In response, the pilot asked that the tug push with full power on the port bow to arrest the turn. At 0643, the same tug master advised the pilot that the tug could not remain in its position as it would ground, and suggested pulling back on the tow line to arrest the ship’s headway. The pilot then instructed both tugs to pull back on their lines at half power.
At 0643:30, World Diana’s bow grounded on the bank and its speed rapidly reduced to zero. The pilot then manoeuvred the ship astern using its propulsion and the tugs. Once the ship was established in the centre of the turning basin, the turn was completed. At the time of the incident, a pilot transfer vessel inspected the shallow area but did not identify any evidence of a grounding therefore it was believed to have been a near miss. Consequently, there was no inspection of the ship’s hull carried out prior to departing Australia. The pilot and ship’s master continued the departure and the pilot disembarked the ship outside the outer harbour.
Two days later, the pilot reported the incident as a near miss. A subsequent review of incident data indicated a grounding, and a survey of the seabed in the incident location was arranged. The survey identified an indentation in the soft seabed where World Diana’s bow had grounded (Figure 2).
Figure 2: Post incident survey imagery of shallow water (circled)
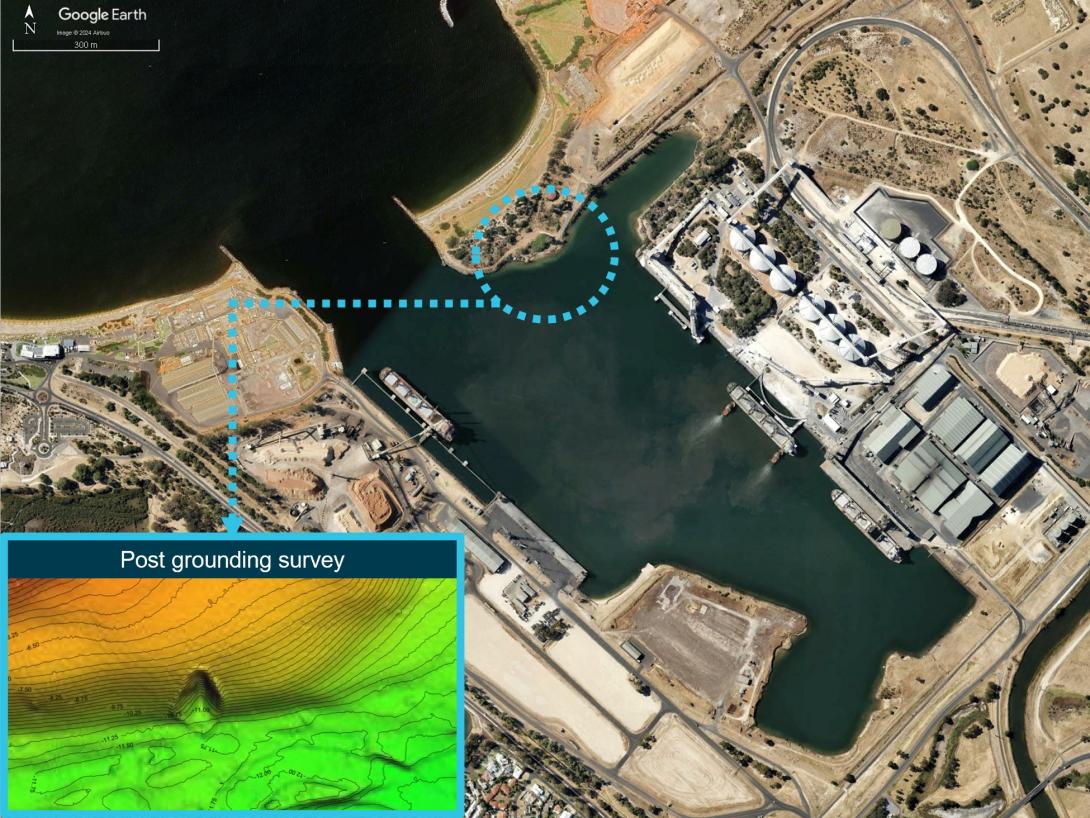
Image source: Survey by MNGsurvey overlay on Google Earth and annotated by the ATSB
Meanwhile, the ship was en route to its discharge port in Thailand via Singapore Strait. When the ship’s managers were made aware of the grounding, an underwater hull inspection was arranged to be done in Singapore. This inspection was conducted on 1 May and identified minor contact damage of the shell plating of the fore peak tank. The ship was cleared to continue trading with the damage to be attended at its next scheduled dry docking in 2025.
Context
World Diana
At the time of the incident, World Diana was registered in the Isle of Man, managed by OSM Maritime Group, Norway, and classed with Det Norske Veritas. It had been built by Oshima Shipbuilding, Japan, in 2020.
The ship was a Panamax[3] bulk carrier with an overall length of 229 m and breadth of 32.3 m. Propulsion was provided by a MITSUI‑MAN B&W 6S60E diesel engine driving a single, fixed‑pitch right‑hand turning propeller. The ship was fitted with a single, semi-spade conventional rudder.
World Diana’s navigation bridge was equipped with navigational equipment consistent with SOLAS[4] requirements, which included a voyage data recorder (VDR). However, data for the incident was not available to this investigation.
The ship had an appropriately qualified, multi‑national crew of 19.
The pilot
The pilot started working in the Port of Bunbury in 2007 and had completed about 4,000 pilotage movements there, including about 35 vessels of over 200 m. At the time of the incident, the pilot held a license for the movement of ships of any size permitted in the port. They were qualified to ‘assess competency as a marine check pilot’ and during the past 5 years had mostly trained new pilots.
The pilot also held an unrestricted certificate of competency as a ship’s master and had completed bridge resource management training in 2021. They had attended the Port Ash (Australia) manned model ship-handling training centre in 2022 and completed the ‘manoeuvre and handle a ship in all conditions’ training course.
In 2022, the pilot completed the Southern Port Authority manoeuvring and emergency training for the Port of Bunbury, which included a simulator exercise for ships departing berth no 3 after berthing starboard side alongside. Before the incident, the pilot had undertaken the same manoeuvre as the second pilot on one occasion and subsequently a solo pilotage of a ship of similar size to the World Diana.
The pilot had accepted the World Diana departure pilotage on the previous day and reported having had plenty of time to prepare for the pilotage and feeling well rested before the incident.
Port of Bunbury
The entrance to the inner harbour of the Port of Bunbury is about 150 m wide (Figure 3). The inner harbour has 5 berths, and a submerged rock is located within the 9 m charted depths off berth no 5 (Figure 6).
Berth no 3 is located on the western side, closest to the entrance. It is a specialised grain and woodchip loading berth, which started being used to load Panamax bulk carriers in September 2022. This larger size of ship had to be berthed starboard side alongside the berth to allow the cargo loaders to access all the ship’s cargo holds. World Diana was the 10th ship exceeding 210 m that had berthed starboard side alongside at the berth.
Pilotage is compulsory for ships with an overall length greater than 35 m. The port does not provide a vessel traffic service but can be contacted by VHF radio at all times.
Figure 3: Bunbury harbour berth layout
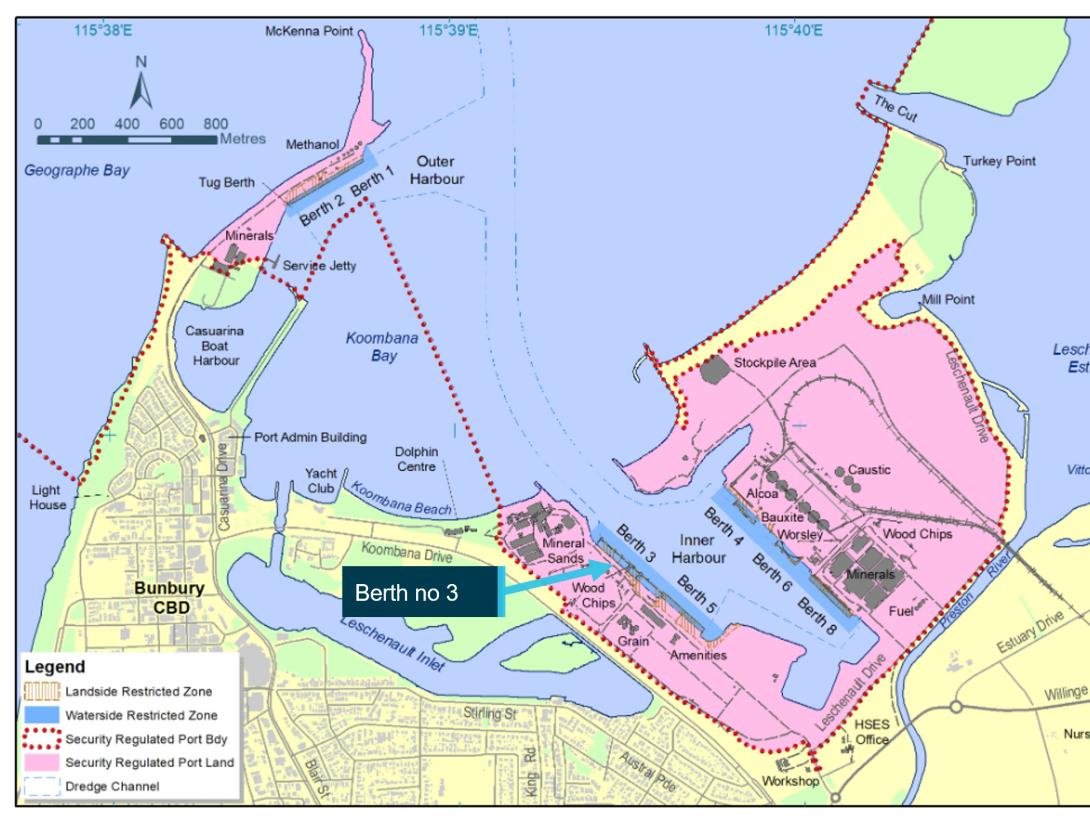
Image source: Southern Port Authority, annotated by the ATSB
Bridge resource management
Bridge resource management (BRM)[5] for World Diana’s pilotage started with a master‑pilot information exchange during which the pilot presented the departure plan (Figure 4). A hand‑drawn line on the plan indicated the approximate direction of travel, including the turn to port and the locations where the tugs would be cast off. It included the calculated static under keel clearance (1.82 m), but did not include any specific information such as ship’s speed, rate of turn and clearing distances or associated limits. There was no bridge audio data available, therefore there was no record of what was discussed during the exchange.
Figure 4: Departure plan diagram
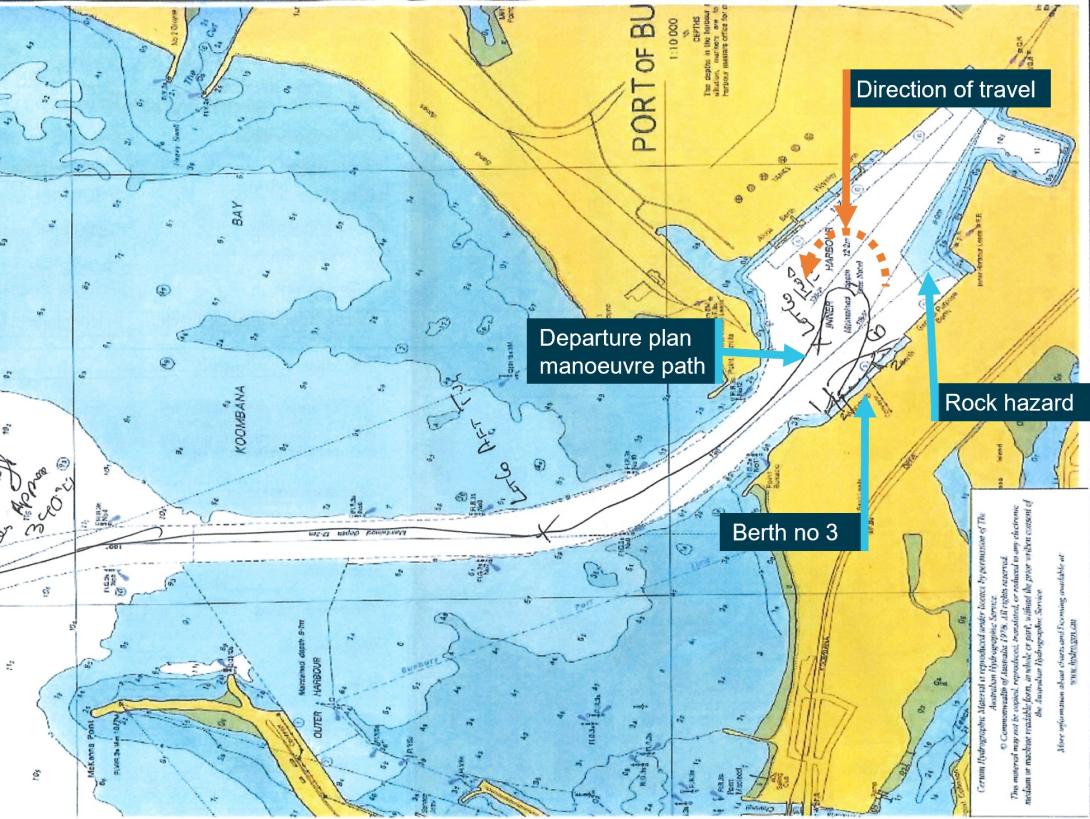
Image source: Southern Port Authority, annotated by the ATSB
The pilot reported having asked the ship master and bridge team to voice any concerns they had about the planned manoeuvre. They also stated that as the ship master was unfamiliar with the port, it was unlikely that deviations from the plan would be recognised.
The plan included using 2 tugs, each with a bollard pull of 80 tonnes. The pilot reported briefing both tug masters while waiting for the mooring gang and that both had previously participated in the planned manoeuvre.
Portable pilot unit
Before departing the berth, the pilot set up the port-supplied portable pilot unit (PPU) – an iPad application with a GPS receiver (Safe Pilot by Trelleborg). The ATSB obtained recorded PPU data, the only data available of the incident (as noted earlier, the ship’s VDR data was not saved). The PPU provided dynamic data together with a real-time display of the ship’s position, including a prediction of its trajectory.[6]
The involved pilot advised that they preferred to conduct pilotages largely by sight, using visual cues based on local knowledge and experience, and used the PPU mostly to check ship speed and rate of turn. A review of the recorded data by the ATSB identified that the PPU was showing the ship’s trajectory throughout the manoeuvring and had predicted that it was going to ground in the minutes before it occurred (Figure 5). It also showed the ship speed was 1.9 kt just prior to grounding.
Figure 5: Portable pilot unit display at 0641
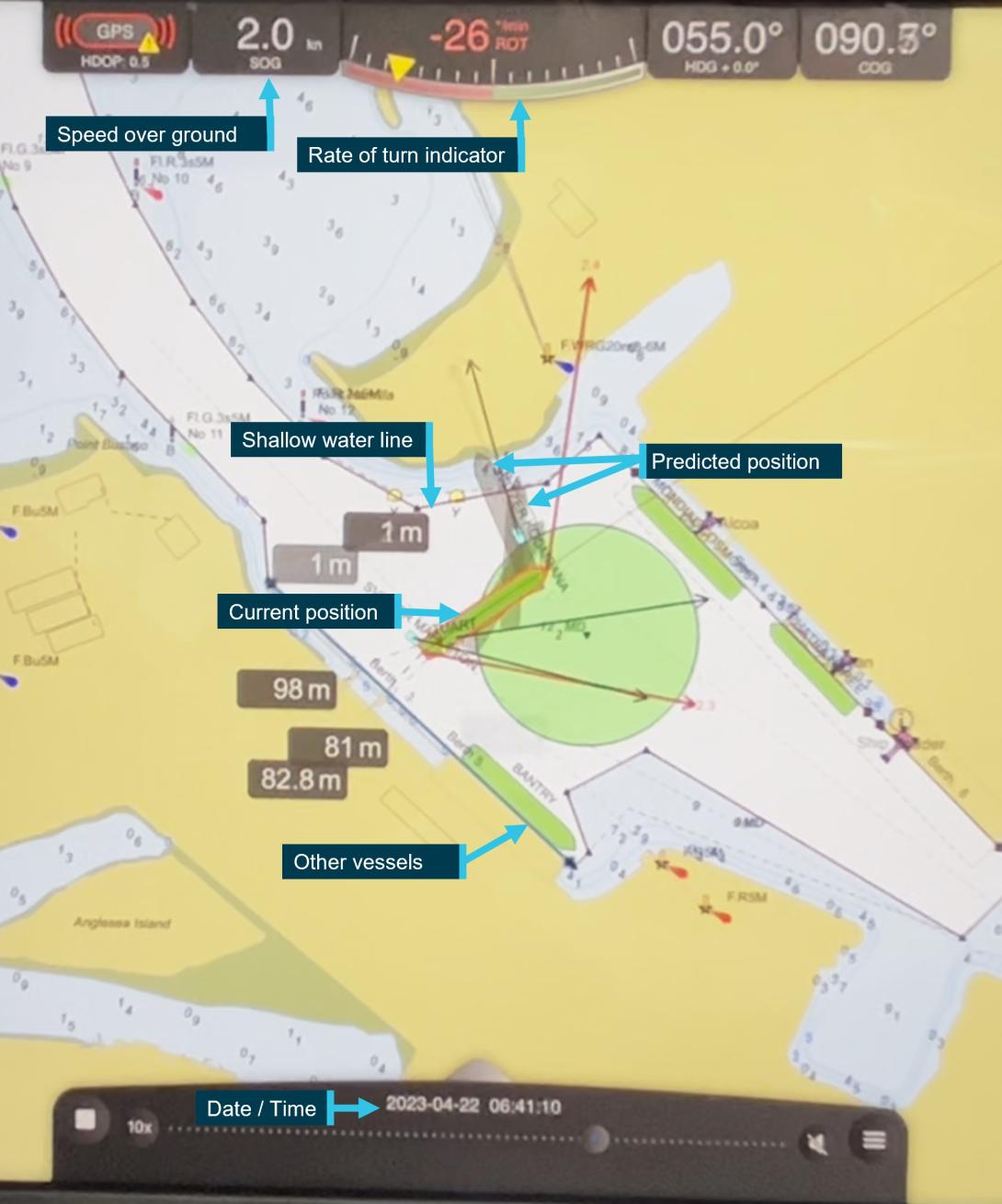
Image source: Southern Port Authority, annotated by the ATSB
The manoeuvre
The pilot portable unit data was used to recreate the ship’s path (Figure 6).
Figure 6: Actual manoeuvre path
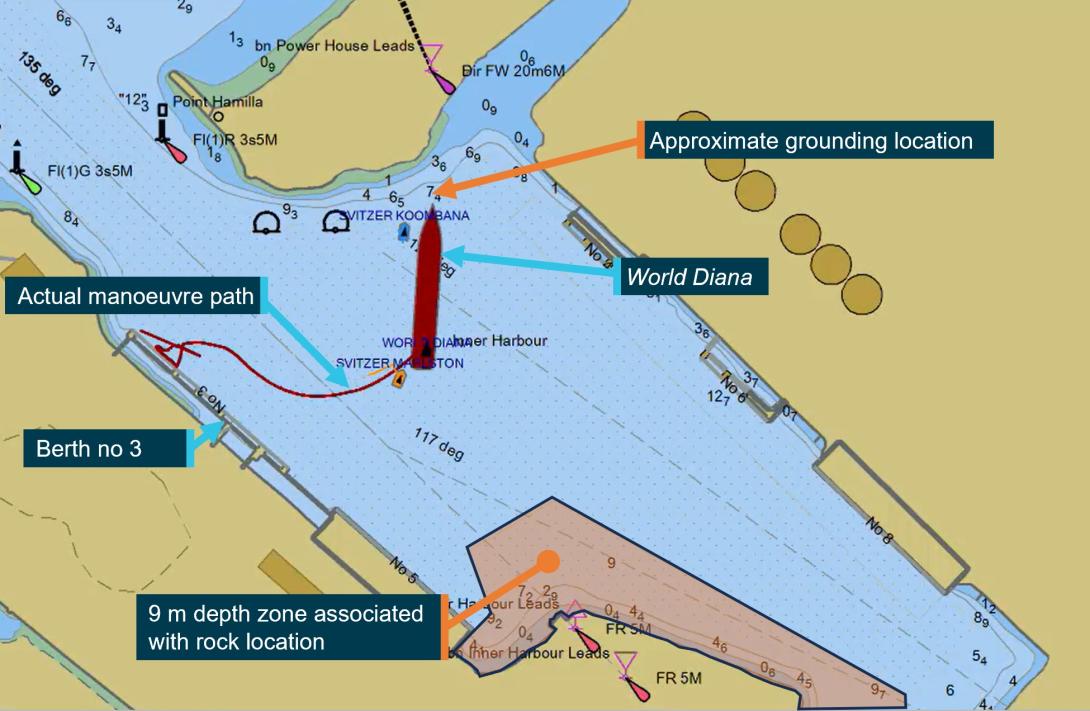
Image source: Southern Port Authority provided PPU data overlay on harbour nautical chart and annotated by the ATSB
According to the pilot, the turn was started early to keep clear of the submerged rock near berth no 5. The pilot stated that the plan was to have the aft tug push and then pull the ship back into position, but the ship's speed unexpectedly increased. The pilot attributed this to the aft tug pushing at full power at a slight angle, increasing the ship’s headway. The pilot attempted counteracting this by running the ship’s engine half astern and reported that as the rate of turn was 22˚/minute and increasing, the propeller was ineffective in arresting the headway. The pilot then resorted to using the forward tug to push at full power, but the tug had run out of sea room. Subsequently, the pilot instructed the tugs to pull back on the tow lines in an unsuccessful attempt to prevent the grounding.
The pilot further advised that the grounding could have been due to either of the following ship manoeuvring effects:
- Shallow water rudder effectiveness[7] – as the vessel swing was assisted by a fore and aft tug, it was determined that any degradation of rudder effectiveness due to low clearance with the harbour floor would have been overcome with the assistance of the tugs.
- Coanda effect[8] – this was not considered a contributing factor because the ship was pulled toward the bank by the tug and there was open water on the opposite side of the ship.
Tug master report
The ATSB reviewed the incident reports for the grounding, including one submitted by the tug master of the forward tug. In it they advised that there was a trainee manoeuvring the tug at the time. The tug master advised they thought that the turn may have been started early however, they did not advise the pilot. They instructed the trainee to be prepared to go alongside the ship to pull back. When they realised that the turn was not going to plan and the tug was running out of sea room, they took over from the trainee. As the tug closed on the yellow marker, the master advised the pilot they were unable to continue pushing and suggested they could pull straight‑back, to which the pilot agreed.
The tug master provided details of a debrief with the pilot several days after the occurrence. They advised that good communication and speaking up if the crew see any issues arising, were both raised as key learnings from this incident.
Previous manoeuvres
Pilots in Bunbury had regularly conducted ships of similar size to World Diana, with lengths up to 238 m accepted at some berths. As noted earlier, World Diana was the 10th large ship (more than 210 m) to depart berth no 3 via a turning manoeuvre to port. The first 2 departures were conducted successfully by a pilot and a safety pilot (that is, 2 pilots on the bridge). It was then decided that one pilot would conduct these pilotages.
The ATSB compared ship track PPU data from 4 of the previous departures from berth no 3 with World Diana’s track. This showed that the ship’s turn was started earlier than the others and that it was later manoeuvred further to the east of the turning basin (Figure 7). The maximum rate of turn achieved during these departures did not indicate wide variations, with World Diana’s rate of turn similar to the incident-free departures (Table 1).
Figure 7: Ship departure tracks from berth no 3
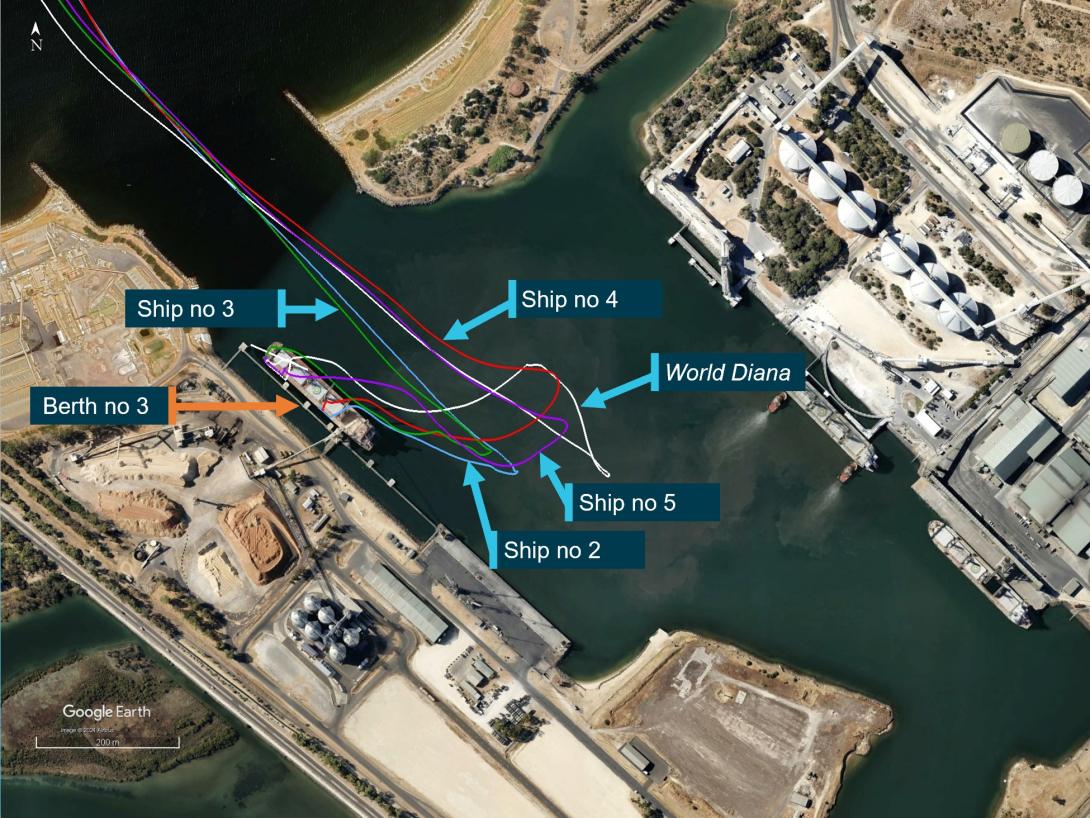
Ships referenced in image all have an approximate length of 229 m and show a different starting position due to their movement along berth no 3 used to load different hatches. The PPU data point is taken from a single position at the bridge of the ship. Labels also used as reference for Table 1.
Image source: Southern Port Authority provided PPU data overlay on Google Earth, annotated by the ATSB
Table 1: Maximum rate of turn recorded
Ship | Size (m) | Maximum rate of turn recorded by PPU |
World Diana | 229 | 29°/min |
Ship 2 | 229 | 20°/min |
Ship 3 | 229 | 25°/min |
Ship 4 | 229 | 27°/min |
Ship 5 | 229 | 28°/min |
Pilotage procedures
The Port of Bunbury marine pilotage standards and procedures manual stated that the PPU provided to pilots was to be used for the movements of ships with draughts exceeding 11 m. The manual stated that the PPU was 'an aid to navigation and should not be relied upon solely for the passage of the vessel’. Pilots were required to follow BRM principles, and the manual included the following instructions:
SPA [Southern Port Authority] fully endorses the principles of BRM. Pilots must:
- Make it to the bridge giving ample time for the proper exchange of information between the Master and Pilot before entering the channel.
- During the Master/Pilot exchange of information, present and discuss the intended passage plan and manoeuvre with the Master and bridge team. Information to be exchanged with the Master must include tug arrangements, prevailing weather and tidal conditions, mooring arrangements and vessel positioning. Information to be given to the Pilot should include: the vessels manoeuvring characteristics, arrival draft and the operational status of equipment and machinery. Master needs to sign the passage plan confirming the understanding of its intent.
The procedures manual provided arrival plans for all berths, including guidance for entering the harbour. These plans indicated berthing the ship head-out (that is, bow facing harbour entrance) by turning the ship either to port or starboard as shown below for berth no 3 (Figure 8). Specific ship-handling guidance such as rate of turn or speed was not provided. The manual did not include a plan to berth a ship starboard side alongside berth no 3. No departure procedure or plan was provided for any berth. In their departure plans, pilots used a copy of the chart to hand‑draw a plan, such as in this case (Figure 4).
Figure 8: Arrival procedures for berth no 3
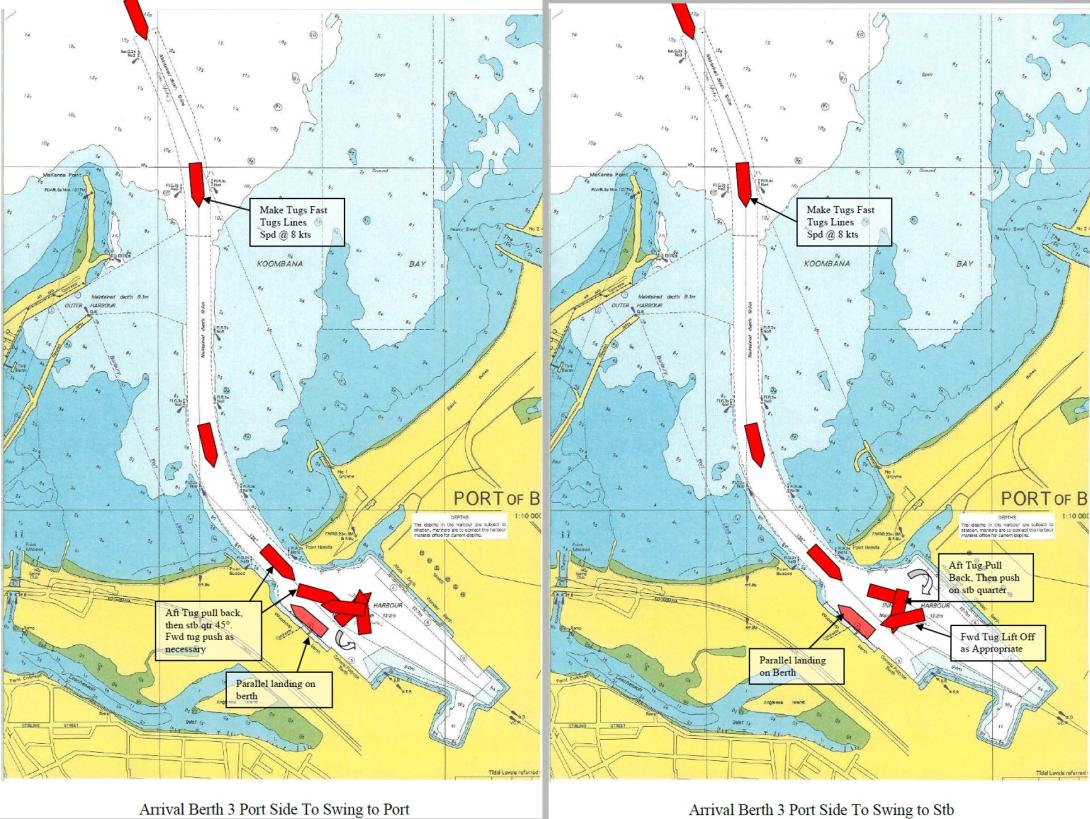
Image source: Southern Port Authority
Safety analysis
As World Diana was starboard side alongside berth no 3, its departure required the ship to be manoeuvred into the inner harbour turning basin and turned to port to exit the harbour entrance. During the master pilot information exchange on the morning of 22 April, the pilot provided a diagram of the departure plan, indicating the turn and the locations of the 2 assisting tugs. No specific information such as ship’s speed, rate of turn, clearing distances or associated limits was shown on the plan and no evidence was provided that these items were discussed.
At approximately 0632, shortly after the ship had left the berth, the pilot began turning the ship to port earlier than planned using both tugs, the ship’s main engine and steering. According to the pilot, the turn was started early to keep clear of the submerged rock near berth no 5. However, the rock was located off the farthest end of berth no 5, over a ship length ahead of the ship’s bow. Significantly, starting the turn early also reduced the sea room available to turn.
By 0636, use of the ship’s main engine had resulted in developing slight headway (0.3 kt). Four minutes later, the speed had increased to 1.5 kt and the ship was turning rapidly towards the shallow waters to the east of harbour entrance. In response to the developing situation, the pilot reversed the main engine (half astern) and instructed the aft tug to push at full power on the port side to turn the ship in the limited sea room. After a couple of minutes, the pilot realised that the turn could not be made in time to avoid the shoals and attempted to arrest the turn followed by an attempt to arrest the headway by using the tugs. These measures were unsuccessful, and shortly after 0643, the ship’s bow grounded.
The pilot’s portable pilot unit (PPU) was accurately displaying the ship’s position and progress in real time and indicating useful data, such as speed and rate of turn, to safely complete the turn. At 0641, the PPU predicted that the ship would ground. However, neither the pilot nor others on the bridge were using the PPU or paying attention to its display. Additionally, the forward tug's master identified that the ship was turned early but raised no concern with the pilot until the shallow water was extremely close, a minute before the grounding.
Overall, bridge resource management (BRM) was ineffective, most likely as specific information and limits for the departure plan were only known to the pilot, which made it difficult for the bridge team to raise concerns with the pilot. Nevertheless, had the ship’s master, being a ship-handler familiar with the ship’s manoeuvring characteristics, been actively monitoring the pilotage, the early turn and ship’s increasing headway, should have become evident on the ship’s monitors as well as the PPU. The PPU was displaying information to help avoid the grounding but this was not detected. Neither the bridge team nor the forward tug master raised any concerns with the pilot about the ship-handling errors until the grounding was imminent. In addition, when the pilot became aware of the imminent grounding, they did not make full use of the ship’s main engine, which remained at half astern (not full or emergency full astern) nor were the anchors dropped.
The investigation identified that no procedures had been developed that included arrival and departure plans for larger ships that were required to berth starboard side alongside berth no 3. This reduced the information available to pilots for these ship movements and to share with bridge teams and tug masters to ensure a common understanding of how manoeuvring would be conducted.
Findings
ATSB investigation report findings focus on safety factors (that is, events and conditions that increase risk). Safety factors include ‘contributing factors’ and ‘other factors that increased risk’ (that is, factors that did not meet the definition of a contributing factor for this occurrence but were still considered important to include in the report for the purpose of increasing awareness and enhancing safety). In addition ‘other findings’ may be included to provide important information about topics other than safety factors. These findings should not be read as apportioning blame or liability to any particular organisation or individual. |
From the evidence available, the following findings are made with respect to the grounding of World Diana when departing berth no 3 in Bunbury, Western Australia on 22 April 2023.
Contributing factors
|
Other factor that increased risk
- The Port of Bunbury had not developed adequate procedures that included arrival and departure plans for larger ships that were berthed starboard side alongside berth no 3.
Safety actions
Whether or not the ATSB identifies safety issues in the course of an investigation, relevant organisations may proactively initiate safety action in order to reduce their safety risk. The ATSB has been advised of the following proactive safety action in response to this occurrence. |
Safety action by Southern Port Authority
The Southern Port Authority has updated its Marine Pilotage Standards and Procedures Manual to include:
- standard procedures for departing all berths, including berth no 3 after berthing starboard side alongside.
- a maximum rate of turn for turning ships in the harbour of 20° per minute.
Sources and submissions
Sources of information
The sources of information during the investigation included the:
- manager of World Diana at time of incident
- pilot
- forward tug master
- Southern Port Authority
- survey completed by MCMULLEN NOLAN GROUP PTY LTD
References
Sanders, D.J. and Plumridge, M.J. (1990) The Nautical Institute on pilotage and Shiphandling. London: Nautical Institute.
Port Ash (Version 3.7 Sept 2012) Course in General Shiphandling. Australia: Port Ash
Submissions
Under section 26 of the Transport Safety Investigation Act 2003, the ATSB may provide a draft report, on a confidential basis, to any person whom the ATSB considers appropriate. That section allows a person receiving a draft report to make submissions to the ATSB about the draft report.
A draft of this report was provided to the following directly involved parties:
- Australian Maritime Safety Authority
- the pilot, tug masters and ship manager
- Southern Port Authority
Submissions were received from the:
- tug operator
- ship manager
- Southern Port Authority
The submissions were reviewed and, where considered appropriate, the text of the report was amended accordingly.
Purpose of safety investigationsThe objective of a safety investigation is to enhance transport safety. This is done through:
It is not a function of the ATSB to apportion blame or provide a means for determining liability. At the same time, an investigation report must include factual material of sufficient weight to support the analysis and findings. At all times the ATSB endeavours to balance the use of material that could imply adverse comment with the need to properly explain what happened, and why, in a fair and unbiased manner. The ATSB does not investigate for the purpose of taking administrative, regulatory or criminal action. TerminologyAn explanation of terminology used in ATSB investigation reports is available here. This includes terms such as occurrence, contributing factor, other factor that increased risk, and safety issue. Publishing informationReleased in accordance with section 25 of the Transport Safety Investigation Act 2003 Published by: Australian Transport Safety Bureau © Commonwealth of Australia 2024 Ownership of intellectual property rights in this publication Unless otherwise noted, copyright (and any other intellectual property rights, if any) in this report publication is owned by the Commonwealth of Australia. Creative Commons licence With the exception of the Coat of Arms, ATSB logo, and photos and graphics in which a third party holds copyright, this publication is licensed under a Creative Commons Attribution 3.0 Australia licence. Creative Commons Attribution 3.0 Australia Licence is a standard form licence agreement that allows you to copy, distribute, transmit and adapt this publication provided that you attribute the work. The ATSB’s preference is that you attribute this publication (and any material sourced from it) using the following wording: Source: Australian Transport Safety Bureau Copyright in material obtained from other agencies, private individuals or organisations, belongs to those agencies, individuals or organisations. Where you wish to use their material, you will need to contact them directly. |
[1] Lift off: pulling back on the tug’s tow line from any direction, except alongside the ship.
[2] One kt, or one nautical mile per hour, equals 1.852 kilometres per hour.
[3] A ship that is limited in size to the dimensions of the original Panama Canal locks.
[4] The International Convention for the Safety of Life at Sea, 1974, as amended.
[5] Bridge resource management can be defined as the effective management and use of all appropriate resources, including personnel and equipment, by a ship’s bridge team to complete its voyage safely and efficiently.
[6] The ship prediction is a simple iterative projection of ship’s position and heading based on its current position, course over ground, speed over ground, and rate of turn. The course and speed values are ‘smoothed’ by using a 3-second average to calculate the prediction.
[7] In shallow water the under-keel clearance affects ship turning behaviour. The hydrodynamic actions are complex, but the overall result is that in shallow water the changes in water flow round the hull have the result that a given rudder angle produces a smaller yaw angle than in deep water.
[8] The Course in General Ship Handling course notes created by Port Ash version 3.7 Sept 2012, describe the Coanda effect as an area of low pressure created between the ship and wharf which occurs when a tug is pulling a ship’s bow away from a wharf. A low-pressure area is created if part of a tug’s wash moves around the ship’s bow. The low‑pressure area attracts the ship’s bow reducing or negating the tug’s pull.