Executive summary
What happened
On the morning of 23 April 2023, a Saab 340A, registered VH-KDK and owned by Pel-Air Aviation, was being operated by Regional Express Airlines (Rex) for a non-revenue flight from Wagga Wagga, New South Wales, to Charleville, Queensland. While in cruise at 22,000 ft and passing to the east of Cobar, New South Wales, the flight crew received a cargo smoke indication on the central warning panel. As a precaution, the crew fitted their oxygen masks and smoke goggles. Shortly after, the cockpit filled with smoke.
The captain commenced a diversion to Cobar while the first officer made a PAN-PAN[1] call to Melbourne Centre. Thick smoke then filled the flight deck preventing the crew from effectively seeing external visual references or the aircraft’s flight instruments. While completing the emergency checklists, the crew received further warnings for avionics smoke, followed by a cabin depressurisation, and then a right engine fire detection fail indication. The crew landed at Cobar and elected to stop on the runway and evacuate the aircraft.
Shortly after landing, Fire and Rescue New South Wales personnel arrived from the Cobar station and located a heat source at the air cycle machine and in the associated wiring. After gaining access to the cabin underfloor area, the source of the heat was doused with water. An internal inspection of the aircraft found fire damage in the area around the right recirculating fan. The aircraft was substantially damaged, and the crew were not injured.
What the ATSB found
The ATSB found that a likely failure of the right recirculating fan electronic box sub-assembly resulted in an in-flight fire under the cabin floor. The fire filled the cabin with smoke, which then entered the flight deck due to a smoke barrier curtain not being fitted in place and the flight deck door being open.
When the crew fitted their oxygen masks, it was found that the first officer’s mask microphone was not working correctly, which delayed emergency checklists being actioned. The fire also caused substantial structural damage and led to a breach of the fuselage, resulting in a depressurisation of the aircraft.
It was also found that the Rex flight crew had not been trained or had knowledge of the differences in the cargo‑configured Saab 340 aircraft, leading to them having no familiarity with specific systems fitted. This prevented them from completing some of the required steps in the emergency checklists.
The flight crew did not receive training on the cargo‑configured aircraft differences prior to conducting freight operations. Further, the operator’s flight crew operating manuals did not reflect the differences in the cargo‑configured aircraft interior checklists, which may have alerted the flight crew to these differences during pre-flight preparation. Additionally, the manufacturer did not have any specific pre-flight check for correct fitment of the smoke barrier curtain for cargo‑configured aircraft preparation.
What has been done as a result
On 13 May 2023, Rex issued an Operations Notice to all pilots, highlighting the guidance on the cross-valve handle as outlined in the Saab Aircraft Operating Manual (AOM). Furthermore, this guidance has been incorporated into the Rex Flight Crew Operating Manual (FCOM).
On 13 November 2024, Rex amended the internal inspection checklist that is contained in their Saab 340 FCOM. The amendment now requires flight crews verify the position of the cross‑valve handle during the pre-flight checks.
Rex have also updated the training information delivered in their ground school to include the cross-valve system for the cargo‑configured Saab 340 aircraft into the training syllabus.
Rex indicated they are implementing a fleetwide inspection of the recirculating fan assemblies at the next aircraft heavy maintenance cycle, with a focus on the electronic sub-assembly module.
Pel-Air have included a revision to their flight crew operating manual with a caution that the smoke barrier curtain must be installed whenever combustible material is carried in the cargo compartment. Due to contract completion, Pel-Air have ceased conducting freight operations using the Saab 340 aircraft and have since sold the aircraft.
Saab has revised their preparatory and walk-around pre-flight checklists to include the fitting of the smoke barrier curtain when carrying cargo in the cargo‑configured aircraft.
Safety message
It is essential for operators to ensure that flight crew are conversant with differences in aircraft configurations when required to conduct operations on aircraft they may be unfamiliar with. It is important that information is readily available and accessible and be delivered in a manner to inform flight crews on the operational requirements of the aircraft.
Operator flight crew operating manuals need to be relevant for the aircraft configuration being utilised. Further, manufacturer checklists for pre-flight inspections are required to cover the modifications fitted, so that this is available to operators to enable them to write the appropriate documentation for their flight crews.
The occurrence
History of the flight
On the morning of 23 April 2023, a Pel-Air Aviation cargo‑configured Saab 340A, registered VH‑KDK and operated by Regional Express Airlines (Rex), was being prepared for the first stage of a non-revenue freight flight from Wagga Wagga, New South Wales, to Charleville, Queensland. The purpose of the flight was to pre‑position a Rex Saab 340 engine to Cairns, Queensland, utilising a Rex crew, consisting of a captain and first officer (FO), and operating under the Part 91 flight rules.
The crew had flown the aircraft from Cairns the previous day, and were tasked to fly the return leg, including a refuelling stop at Charleville. The flight crew arrived at the aircraft at about 0830 local time and conducted their pre-flight checks. The captain performed the interior checks while the exterior walk around checks were conducted by the FO. The aircraft departed Wagga Wagga at about 0949, tracking for Charleville, and cruising at FL 220.[1] The captain was the pilot flying (PF), and the FO was pilot monitoring (PM).[2]
In-flight fire and diversion
At about 1052, the crew was alerted by a cargo smoke detection warning[3] on the central warning panel. They began to manage the warning by identifying and cancelling the indication. The crew then donned their oxygen masks and smoke goggles. However, once fitted, the crew had difficulty communicating due to the FO’s mask microphone not functioning correctly and being very faint. A review of the cockpit voice recorder (CVR) recording showed it took another 57 seconds for the crew to establish effective communications with each other before they could commence the emergency checks.
At 1055 the crew received a right (engine) fire detection fail caution light, followed shortly after by an air conditioner caution light. This was due to the detection of a right distribution duct over temperature which automatically closed the right engine low pressure bleed valve. The crew initially detected no smoke or fumes, however within about 60 seconds, thick black smoke began filling the cockpit.
During the process of establishing the nature of the warnings, the flight crew discussed which airport would best suit their needs for the emergency, and opted to divert to Cobar, New South Wales (Figure 1). The captain had flown to this airport on several previous occasions and was familiar with it, and from their position, they could conduct a direct approach with minimal manoeuvring.
Figure 1: VH-KDK flight overview
Source: Google Earth and Flightradar24, annotated by the ATSB
At 1056, the FO gave a PAN PAN[4] radio call and advised air traffic control (ATC) that they were diverting to Cobar. ATC arranged for emergency services to meet the aircraft upon arrival into Cobar. Due to the radio coverage in the Cobar area, ATC utilised an overflying aircraft to relay communications as the diversion progressed.
While descending through FL 160, the crew received a cabin pressure failure warning, indicating that the aircraft had lost pressurisation. This occurred 4 minutes after the initial warning of the cabin smoke. The cabin depressurisation led to the crew increasing their rate of descent to get below FL 100.
At approximately 1058, they commenced the ‘cargo compartment smoke’ emergency checklist. The CVR indicated the crew completed the first checklist item, which called for the left bleed valve to be closed. The checklist then called for closing the cross-valve handle, however the crew was unable to locate it, with the CVR recording indicating the crew tried to find it for 61 seconds before resuming the checklist flow without actioning the cross-valve handle closure. The crew completed the cargo compartment smoke checklist as visibility on the flight deck reduced to less than 10 cm. The captain recalled sliding their seat forward to enable them to see the instrument panel through the thick smoke.
Five minutes after the PAN PAN call, the crew commenced the checklist for ‘avionic or electrical smoke or fire’.[5] The crew then conducted the ‘smoke removal’ checklist to clear the smoke from the flight deck.
One requirement of the smoke removal checklist called for aircraft speed reduction to below 160 kt, and to open a crew hatch to aid in smoke removal. Due to the unknown severity of the on‑board fire, the crew decided to maintain their speed and not complete all the checklist items as required, enabling them to expedite their landing.
As the crew continued their approach, the volume of smoke in the flight deck began to dissipate. This allowed them to navigate using external visual cues and conduct a visual approach for the landing. Because of the unknown source of the fire, upon arrival in Cobar, the crew elected to stop the aircraft on the runway and evacuate the aircraft.
As part of the emergency evacuation procedure, the crew activated the fire extinguisher system[6] on both engines after shutting down, and then exited the aircraft. The incident had taken 22 minutes from the first smoke warning to landing.
After evacuation, the crew noted smoke to be coming from the vicinity of the right air cycle machine at the right wing root. Shortly after landing, Fire and Rescue New South Wales personnel arrived from the Cobar station and assessed the aircraft. After gaining access to the cabin underfloor area, an electrical harness was initially found melted and smoking. Consequently, the area was doused with water.
Further inspection of the aircraft found significant fire damage concentrated in the area around the right recirculating fan. The right recirculating fan was also significantly fire damaged. An assessment of the right engine found no evidence of a fire. The aircraft underfloor structure was substantially damaged, and the crew were not injured.
Context
Aircraft information
The Saab 340A[7] is a twin-engine turboprop aircraft designed and initially produced by Saab and Fairchild Aircraft. It is designed to seat 30–36 passengers in standard configuration and is powered by 2 General Electric CT7-5A2 turboprop engines.
VH-KDK was manufactured in Sweden in 1984 and first registered in Australia in February 1985. It was operated in passenger configuration by Regional Express Airlines (Rex), before being modified to cargo configuration in 2009. VH-KDK was then owned and operated by Pel‑Air Aviation.[8]
At the time of the accident,[9] VH-KDK had accrued a total time in service of 48,130.6 hours and 60,046 landings and had flown 13.5 hours since the last maintenance.
Flight crew information
Captain
The captain held an air transport pilot licence (ATPL) (Aeroplane), and a valid Class 1 aviation medical certificate. They reported a total flying time of 7,579 hours with about 5,070 of those being on the Saab 340. They had flown for the operator for about 10 years, and previously had flown for another regional airline and had operated into Cobar airport on numerous occasions.
The captain had previously flown the Saab 340A in a passenger configuration but had not flown either the Saab 340A or B variant in a cargo configuration.
First officer
The first officer (FO) held an ATPL (Aeroplane), and a valid Class 1 aviation medical certificate with a restriction for vision correction. They had reported a total flying time of about 18,297 hours, having flown about 1,480.9 in the Saab 340B. The FO had not previously flown any Saab 340 variants in a cargo configuration.
Meteorological conditions
Graphical area forecasts provided by the Bureau of Meteorology (BoM) stated that generally good weather conditions, with little cloud, and visibility greater than 10 km existed during the flight. The terminal area forecast for Cobar indicated light winds from the east at about 10 kt with the flight crew reporting CAVOK[10] conditions existing for the time of the diversion.
Cargo configuration
VH-KDK cargo conversion
The cargo conversion modification was carried out in accordance with Saab service bulletin (SB) 340-25-280. As an overview, the SB involved removal of the passenger fit‑out and replacing it with an interior cargo liner, blanked over windows, additional cargo barrier nets, and a floor roller system (Figure 2). In conjunction with this SB, other SBs were incorporated on the cargo version, which modified the air conditioning system. This was done by removing the left recirculating fan and introducing a cross-valve handle.
A removable smoke barrier curtain was added at the forward section of the cargo compartment. The fire extinguishing system for the passenger cargo area at the rear of the cabin (zones C1 and C2) was also removed, and additional smoke detectors were added to the cabin.
Figure 2: Cargo configuration modification
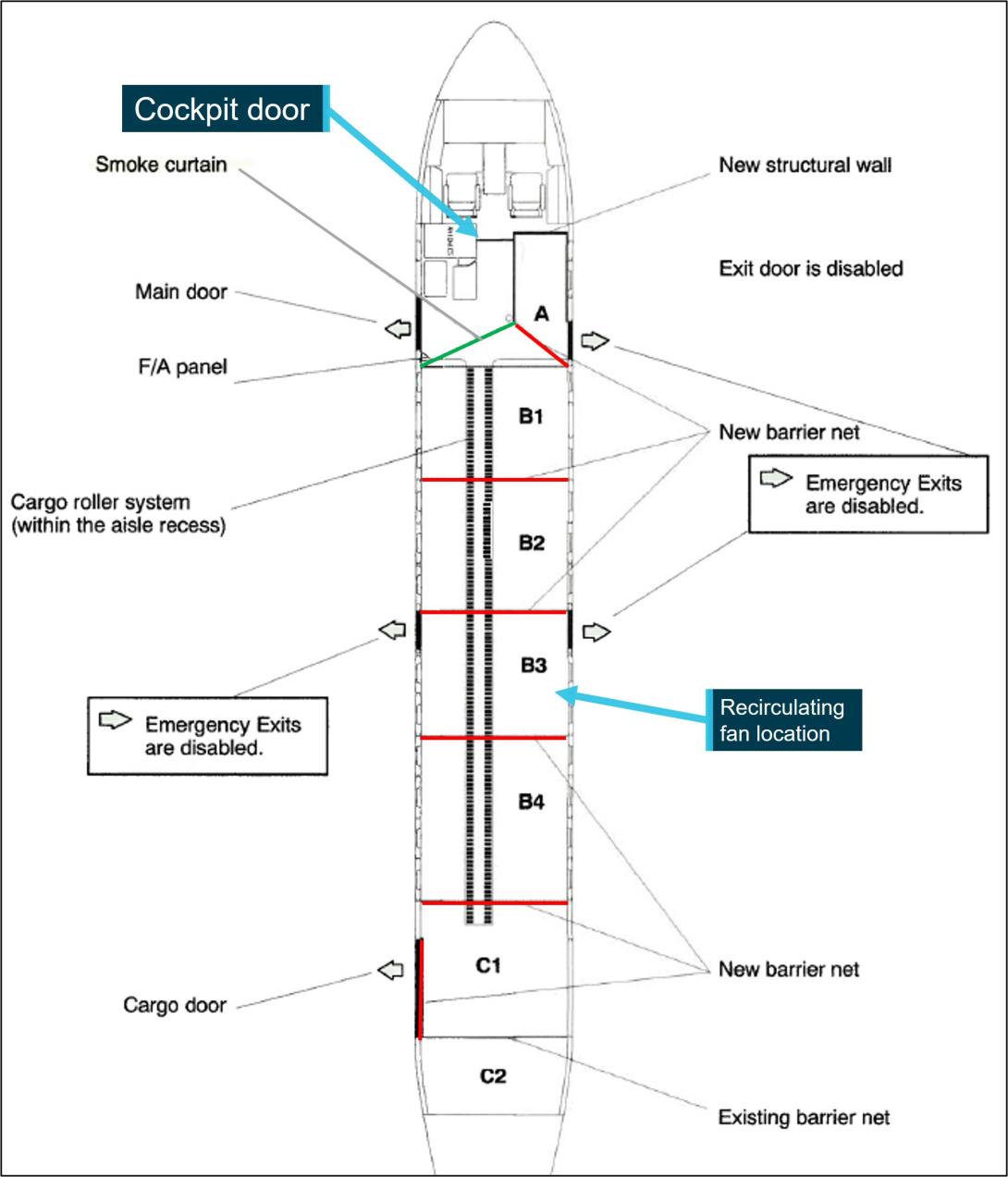
Source: Saab, annotated by the ATSB
Smoke curtain
A removable smoke barrier curtain was designed to be installed between compartment A and the front-left fuselage (Figure 2). The purpose of the curtain was to provide containment of smoke and fire within the cargo compartment in the event of an on-board fire and prevent smoke ingress to the flight deck (Figure 3). The aircraft carried a placard at the top of the entrance stairs which stated:
Smoke barrier must be installed for all cargo operation flights.
The smoke barrier was constructed of a fibreglass impregnated vinyl which was secured in place by a Velcro perimeter and metal press studs. The aircraft owner stated that the standard procedure was that it would be left attached by the left side attachment points and secured in place by the freight handlers after loading of cargo. It was then to be checked by the FO prior to flight.
During interview, the flight crew stated that they were not aware of the use of the smoke barrier, and that it had been located after the incident in compartment A of the cargo area, and that it was not in place on the left of the cabin. The ATSB did not determine why the engineers who loaded the engine into VH-KDK had not secured the smoke curtain.
Figure 3: Smoke barrier curtain location in exemplar aircraft
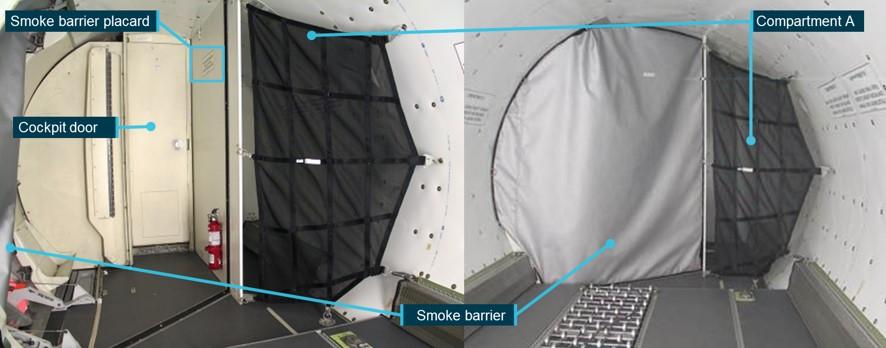
Source: Saab, annotated by the ATSB
Air conditioning system
In passenger configuration, the Saab 340 air conditioning system is comprised of a left and right air conditioning pack (ACP) which is supplied by bleed air from its respective engine. Each ACP is mounted externally under a fairing on the lower fuselage near the rear of each wing. The system has 2 recirculating fans under the adjacent cabin floor, ducting for the cabin and flight deck conditioned air supply and return, temperature sensors and controls, and cabin and flight deck air outlets.
The left and right ACPs supply conditioned air to the cabin, and a portion of the right ACP conditioned air is supplied to the flight deck. The left recirculating fan returns the air to the left ACP from the aircraft cabin, while the right fan extracted air from the flight deck. The avionics fan draws air for cooling the avionics from the cabin conditioned air supply. The air is then expelled under floor.
As part of the modification from passenger to cargo configuration, the left recirculating fan and ducting were removed. This resulted in limited extraction and recirculation of any contaminated air from the cabin interior, while the right recirculating fan would extract and recirculate air solely from the flight deck.
Cross-valve handle
In the cargo configuration, a cross-valve and handle were added to the air conditioning system ducting between the left and right ACP (Figure 4), with the manual operating handle being located at floor level, next to the FO seat. Closing of the left bleed valve and cross-valve in accordance with the emergency checklist would isolate the supply of air to the cabin in the event of cargo smoke or fire, and the right ACP would supply only to the flight deck. As part of the emergency checklist for ‘cargo compartment smoke’, the left ACP would also be isolated from supplying the cabin.
Figure 4: Schematic of modified air conditioning system
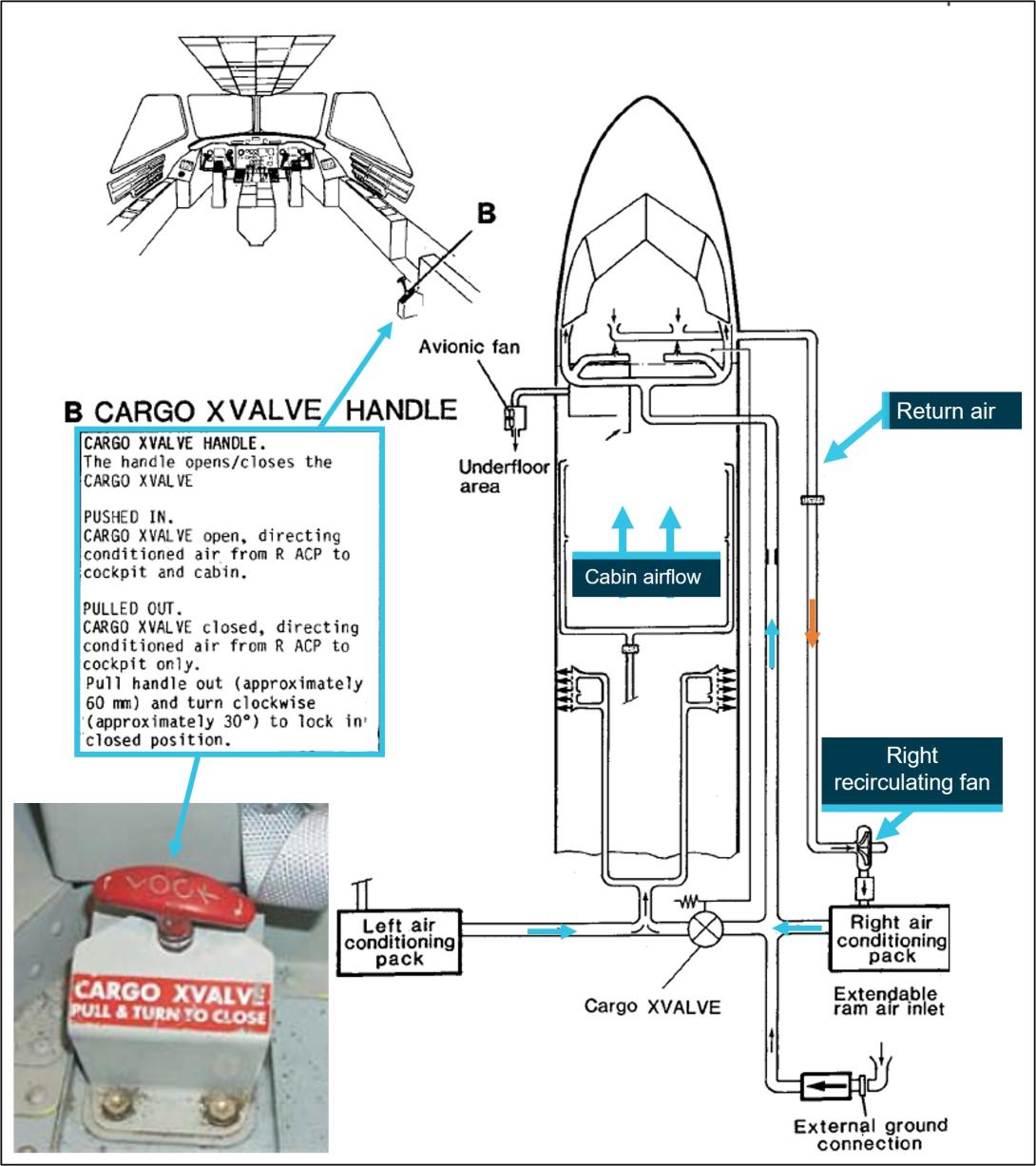
Source: Saab, annotated by the ATSB
Recirculating fan
The right recirculating fan was a centrifugal impeller type fan and was driven by an AC motor. The fan had an in‑built inverter, supplied by 28-volt DC. The majority of the electronics for the fan unit were contained in the box sub-assembly. This included the inverter, an electromagnetic interference (EMI) filter unit and the electronic card sub-assembly. The box sub-assembly controlled the fan operation, including the thermal control. Each electric motor was equipped with:
- a thermal switch[11] located in the cooler which guarded against an abnormal temperature increase. This switch would cut off the power if the motor temperature exceeded 110°C +/− 5° (230°F +/− 41°). The fan would start again when the temperature decreased to 65°C +/− 5° (149°F +/− 41°)
- a speed sensor which guarded against an abnormal decrease of nominal speed. If the speed fell below 80% of nominal speed for more than 17 seconds, the fan would be stopped.
In 1987, Saab released a service bulletin which gave operators the option to install an upgraded recirculating fan. The original fan was a brush type motor which required regular maintenance, including brush replacement when they had worn from use. Saab had received reports of smoke and burning smells which were attributed to brushes that were incorrectly installed. The brushless fans were introduced to help eliminate this issue and also required less maintenance.
The fan installed in VH-KDK was the new brushless fan, manufactured in 1990 and fitted in April 1996. The fan history prior to installation was unknown by the operator. The fan accrued 27,585 hours while fitted to VH-KDK.
Recirculating fan examination
Fire damage was found in the area around the right recirculating fan and on the fan itself (Figure 5). There were no other components in the vicinity of the fan with significant fire damage. As such, it is likely the right recirculating fan was the source of the fire.
Figure 5: Damaged recirculating fan
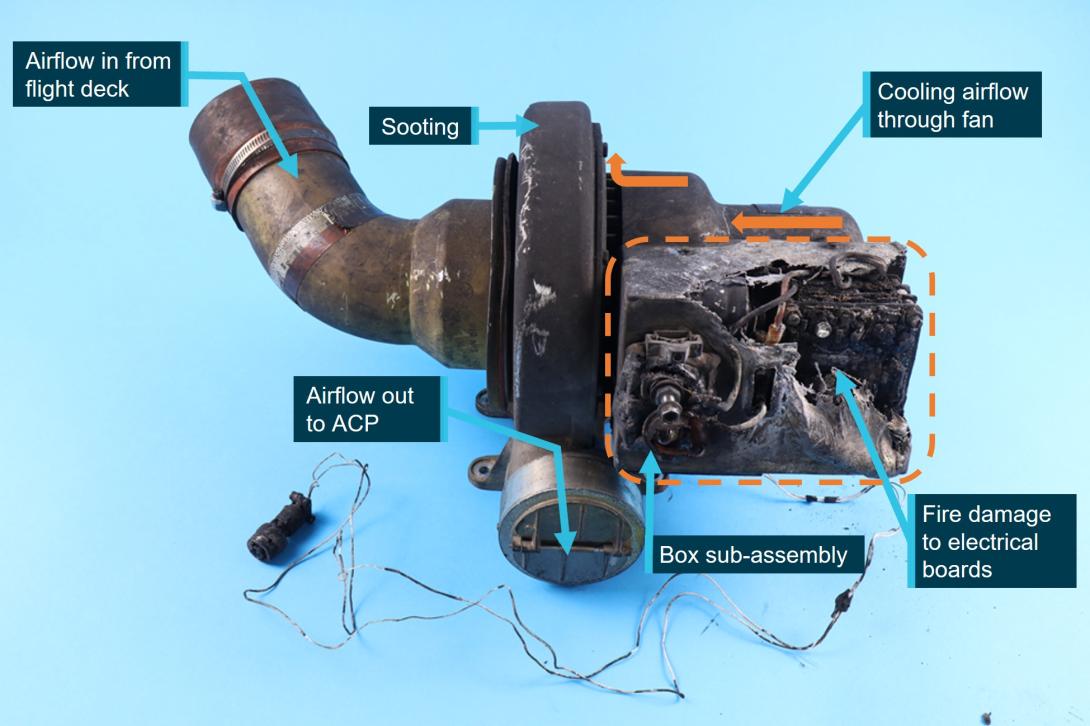
Source: ATSB
An examination of the recirculating fan was conducted at the ATSB’s technical facilities in Canberra. The examination found that the fire damage was most significant at the external box sub‑assembly which housed the EMI filter, the resistor support plates and electronic card sub‑assembly. The aluminium cover of the box sub-assembly had melted, the electrical wiring was damaged, and some terminals had disconnected as a result of the fire damage. There was heavy soot and melting of solder in the cooler assembly.
The electronic card sub-assembly was made up 3 circuit boards, mounted to the resistor support plate. The function of the circuit boards was for motor speed detection, timer control, and a logic card. The damage exhibited on the circuit boards showed significant burning, consistent with the other components within the aluminium cover.
The electromagnetic interference (EMI) filter sub-assembly had considerable damage to the filter itself and to the mounting plate with signs of melting and heat tinting of the steel plate structure, indicating a significant heat source. The heat tint was indicative of temperatures of approximately 310° to 330°C.
Of note, the fire did not appear to be associated with the motor and there was no indication of damage to the internal components of the fan and was able to rotate freely. There was carbon and soot observed on the external surface on the motor. The crew stated that there had been no circuit breakers tripped that would be associated with the failure of the electronic card sub‑assembly.
The ATSB examination of the recirculating fan could not determine the cause of the failure of the electronic components attached to the assembly.
Pressurisation system
The Saab 340 cabin is pressurised by the 2 air conditioning packs. The pressurisation system uses bleed air drawn from each engine and was either automatically controlled by a pressurisation controller, or manually controlled by a control valve operated by the flight crew from the flight deck.
Pressure is able to be regulated by the opening and closing of 2 outflow valves, located in the empennage. The primary outflow valve is electro-pneumatically operated by the pressurisation controller, while the secondary outflow valve is pneumatically controlled from the cockpit and used as a manual standby system.
When emergency pressure relief is required, the primary outflow valve is able to be opened with the emergency pressure dump switch. When the crew of VH-KDK experienced the smoke in the cabin and flight deck, dumping cabin pressure as stated in the ‘smoke removal’ emergency checklist was the method used to assist in rapid removal of the smoke.
Aircraft depressurisation
The severity of the fire resulted in significant damage to the surrounding underfloor furnishings, ducting and airframe structure. The damage was then sufficient to rupture the skin (Figure 6) and caused a subsequent depressurisation of the aircraft.
Figure 6: Underfloor fire damage showing fuselage hole
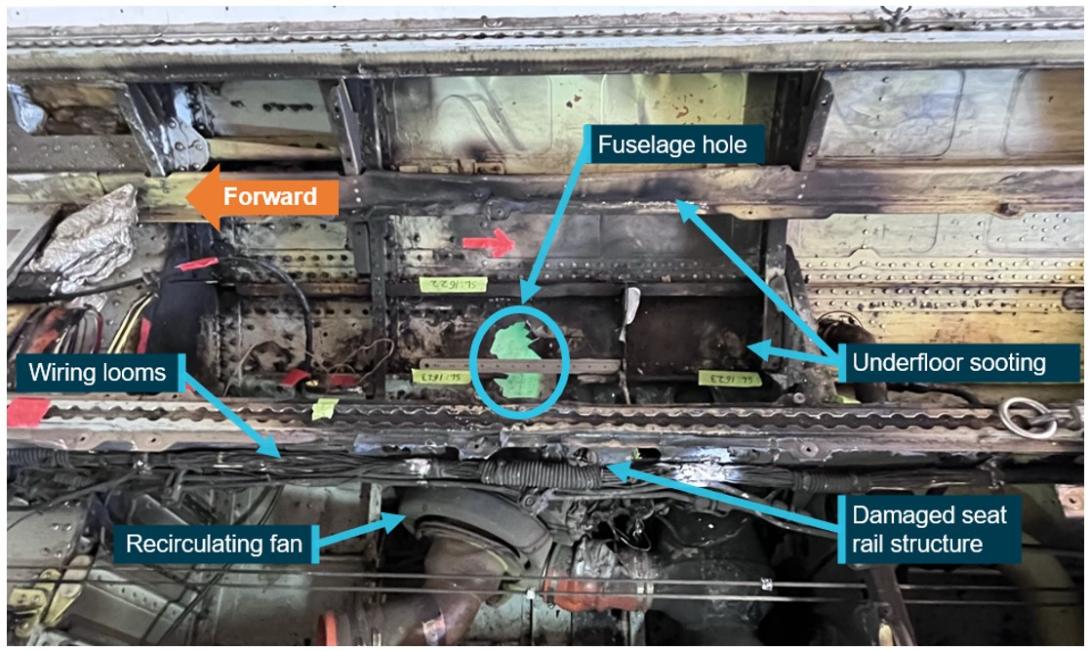
Source: Operator, annotated by the ATSB
Checklists
The pre-flight procedures for the Saab 340A aircraft, including cargo configuration aircraft, were covered by the Aircraft Operations Manual (AOM) normal procedures, produced by the aircraft manufacturer. The AOM pre-flight normal checklist contained a check of the cross-valve handle position prior to flight but did not include a specific check for correct fitment of the smoke barrier curtain.
A flight crew operating manual (FCOM) was carried on board VH-KDK which was developed by Pel-Air, based on the aircraft manufacturer’s AOM. Unlike the aircraft manufacturer's AOM, the pre-flight checks in the operator's FCOM did not contain any reference to the cross-valve handle. Consistent with the aircraft manufacturer’s AOM, the operator’s FCOM also did not include a specific pre-flight check for correct fitment of the smoke barrier curtain. The weight and balance chapter of the FCOM did show a diagram of the smoke curtain fitted but did not include a requirement to ensure the smoke curtain was in place.
The manufacturer had an airplane flight manual supplement in place, implemented as part of the cargo configuration SB, which included fitting the smoke barrier as a limitation (Figure 7 left). There were no identified interior checks in this supplement, which included the checking of the cross-valve handle prior to flight.
The aircraft manufacturer did have emergency checklists specific to cargo‑configured aircraft. These were compiled into the quick reference handbook (QRH) which was available to flight crew in the aircraft (Figure 7 right).
Figure 7: Flight manual supplement (left) highlighting smoke curtain use and QRH checklist (right) highlighting cargo cross-valve handle and cockpit door
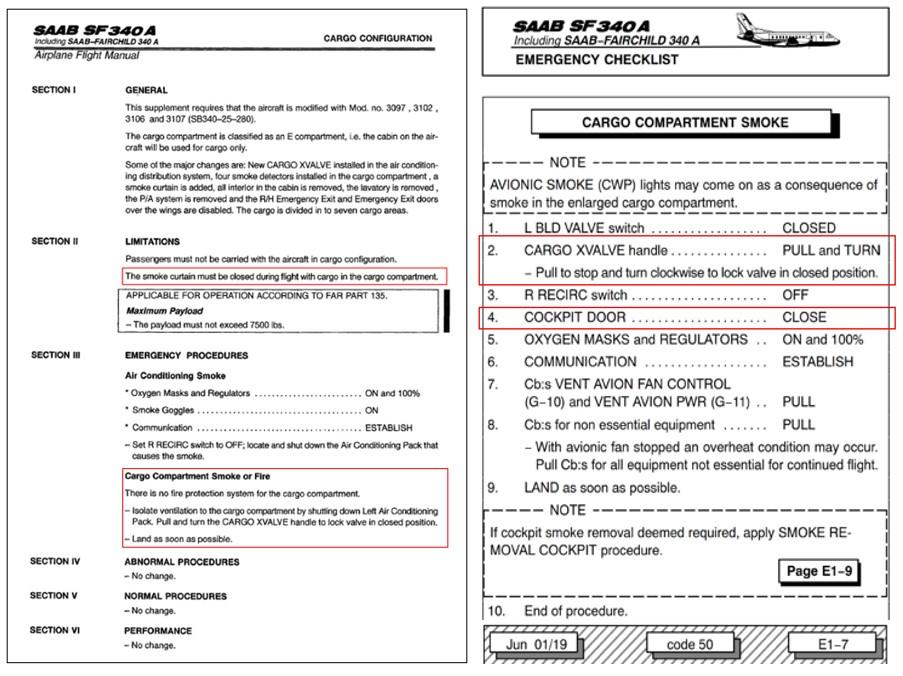
Source: Saab, annotated by the ATSB
Flight deck door
The Pel-Air FCOM stated in the Operating Limitations section that during flight, the flight deck door must be kept closed and locked at all times. It is further listed in the engine start checklist that all doors are closed before engine start.
Evidence from the accident flight, however, shows that before the fire, the crew were operating with the cockpit door open. During interview, the flight crew indicated they closed the door, whilst performing the cargo compartment smoke checklist. This was further supported by the CVR review, where the crew were heard to state the door was to be closed as per the checklist steps, which was followed by the sound of the door shutting.
Flight crew training
Rex conducted a ground school, including simulator training, for their new Saab 340 flight crew. Under a commercial agreement, Pel-Air flight crews were also trained by Rex. The ground school covered the 340 variants of A, B and B WT. The aim of the ground school was to provide pilots from both operators with the necessary knowledge to gain a Saab 340 type rating. The type rating covered all Saab 340 aircraft and did not distinguish between any variant or configuration of the aircraft.
Following the Rex ground school, Pel-Air then conducted further training through its line training program for its flight crews allocated to freight operations. Delivery of this training was in a practical environment, with pilots learning the systems and differences of the cargo‑configured Saab 340. This included the use of the smoke barrier and the operation of the cross-valve handle.
The ATSB asked what the process was for Rex pilots to receive this training and knowledge. Pel‑Air advised that a pilot employed by Rex would only receive this if they were to transition to freight operations with Pel-Air in a permanent role.
Crew familiarity of cargo aircraft
The flight crew operating VH-KDK were both Rex pilots, who were normally rostered for passenger operations. The night before the flight to Wagga Wagga, they were rostered to fly the cargo‑configured 340A. The captain recalled asking the scheduler if they needed a briefing for flying the cargo 340A, and was told that they did not, but it could be arranged if needed.
The captain decided to speak to a Rex colleague who had flown the cargo‑configured 340A several times previously. They were told there were no differences other than the removal of the seats and a freight interior being fitted and that there were no special procedures to be aware of.
Both Rex and Pel-Air advised that their respective operations could roster a crew to fly either operator’s aircraft if it was available. Crewing arrangements were such that there was never any mixing of crew, that is that the flight crew would consist of either 2 Rex or 2 Pel-Air flight crew on any flight.
Oxygen mask
The flight crew fitted their oxygen masks and smoke goggles shortly after receiving the cargo smoke warning and smelling the smoke. The FO conducted the functional tests after fitment and found their microphone was barely readable by the captain. The cockpit voice recorder (CVR) indicated that, although muffled, the speech from the FO was recorded and they were also able to be heard by air traffic control (ATC) throughout the emergency.
The pre-flight checks relating to the crew oxygen system were conducted as part of the interior checklist. The FCOM detailed the checks as:
RIGHT OXYGEN MASK .................................................................................CHECKED
Check flight crew oxygen mask and microphone in accordance with the following:
• …,
• set audio panel BOOM - MASK switch to MASK,
• increase INT/SPKR volume and knock on mask,
• speaker noise indicates proper microphone function,
• set BOOM - MASK switch back to the BOOM position, ….
The check on the left oxygen mask was to be performed in the same manner. Although not detected on the CVR, the captain advised the masks were both tested prior to departure.
Aircraft damage
The damage caused by the underfloor fire was substantial. The fire had damaged underfloor air conditioning ducting and electrical wiring (Figure 8).
Figure 8: Underfloor fire damage
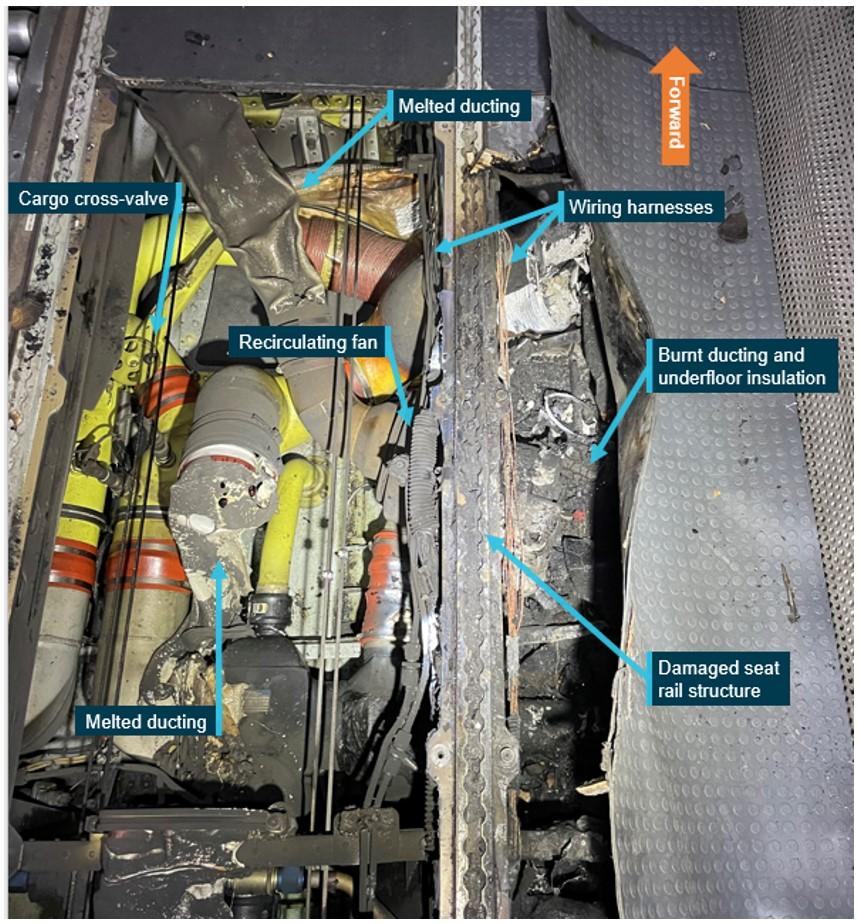
Source: Operator, annotated by the ATSB
Structural components in the surrounding area had been distorted by the extreme heat, including the floor panels, which had collapsed when fire crews entered the aircraft and inadvertently walked over the affected area. The seat track support structure had distorted, and the fuselage was weakened by the fire which breached the outer skin, preventing the aircraft from remaining pressurised (Figure 9).
Figure 9: Fuselage skin breach
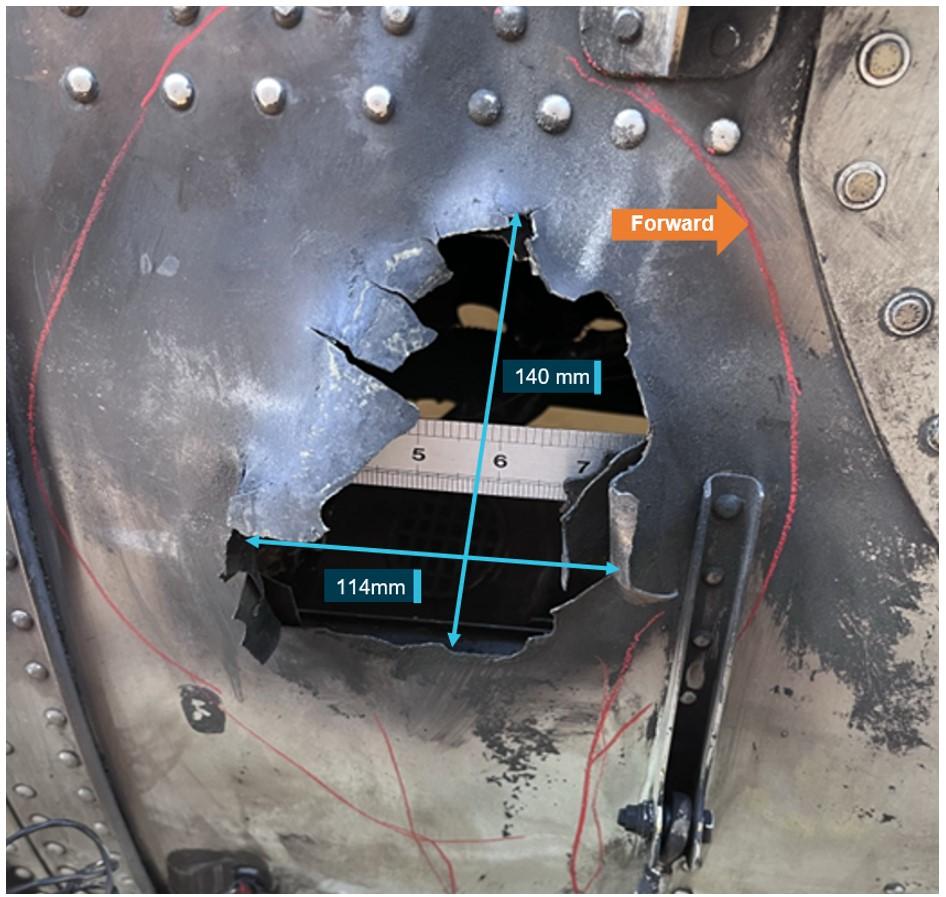
Source: Operator, annotated by the ATSB
The fuselage in the immediate area above and below the cabin floor was buckled and delaminated. The heat from the fire most likely travelled between the interior panels and freight lining, leading to the damage observed (Figure 10). Following an engineering inspection of the fire damage, the aircraft was withdrawn from service and not repaired.
Figure 10: Right side delamination on fuselage
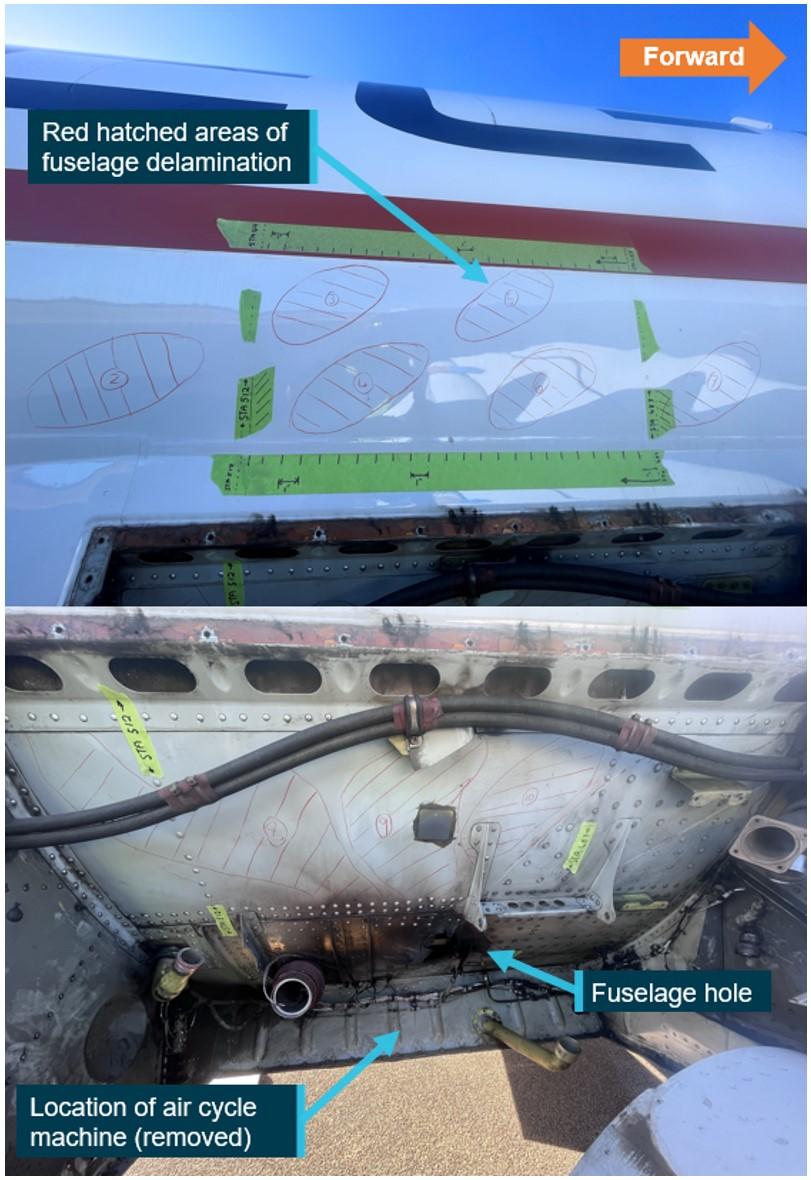
Source: Operator, annotated by the ATSB
Recorded data
The ATSB was supplied raw data by the operator from the flight data recorder (FDR). This data was analysed and was found to include the previous 4 flights.
The recorded data from the occurrence flight showed that at about 59 minutes after becoming airborne at Wagga Wagga, the FDR stopped recording. The recording stopped at about the same time as the initial smoke indication. This was most likely due to fire damage to the electrical wiring which controlled the FDR.
Flight track information was also obtained from FlightRadar24, which showed the entire flight, including the diversion and landing at Cobar (Figure 11).
Figure 11: VH-KDK flight track and diversion
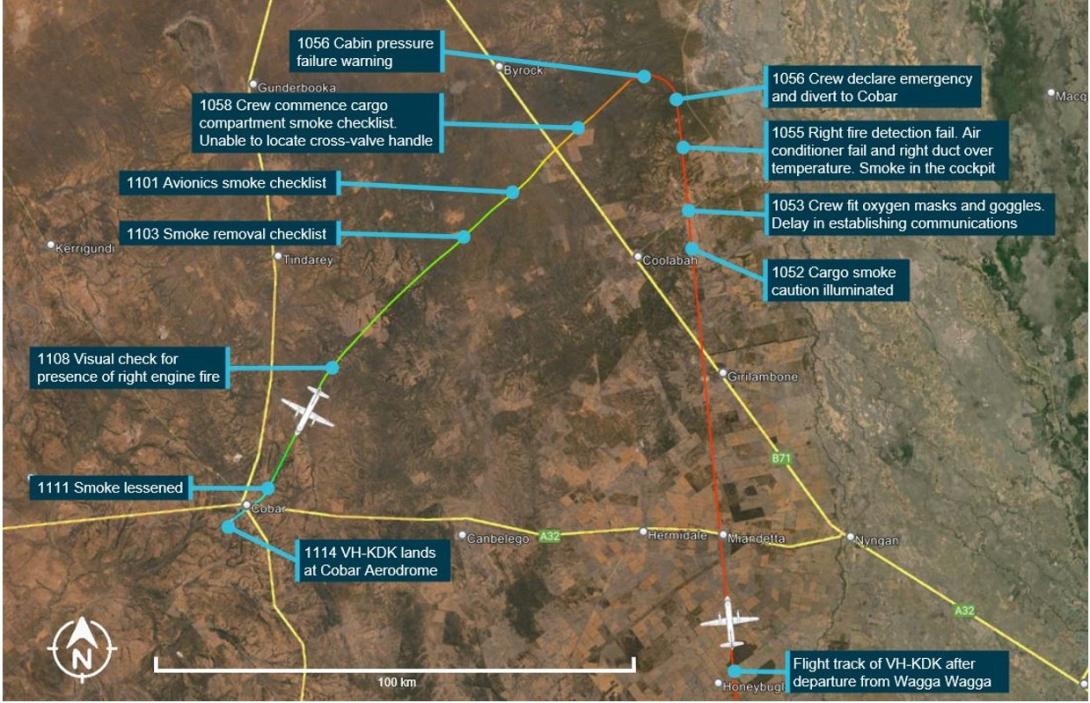
Source: Google Earth and Flightradar24, annotated by the ATSB based on CVR recordings
The CVR was removed and sent to the ATSB technical facilities in Canberra. The CVR data was downloaded, with the recovery of 4 channels of audio data of about 120 minutes duration which included the in-flight fire event. Reviewing the recorded CVR data also revealed that coincidentally, just prior to the indication of the cargo smoke caution, the flight crew had been discussing alternate airports in the area, and which one they would select if they had a need to divert.
The recording contained information from the end of the previous flight, and from the day of incident. It included the:
- flight crew’s initial reaction to the caution warning for the smoke in the cabin
- conduct of the emergency checklists
- additional warnings as they occurred
- crew intercom and communications with Melbourne Centre
- landing at Cobar and subsequent exiting of the aircraft.
The recording also revealed that while conducting the emergency checklist for ‘cargo compartment smoke’ the crew closed the cockpit door as a loud bang was heard, indicating it was open during the flight.
Safety analysis
Introduction
On 23 April 2023, the Regional Express (Rex) Airlines flight crew operating a Pel-Air Aviation Saab 340A, registered VH-KDK were conducting an internal revenue cargo flight from Wagga Wagga, New South Wales, to Charleville, Queensland. About 1 hour into the flight, the crew experienced an in-flight fire and diverted to Cobar, New South Wales. After experiencing thick smoke on the flight deck and then a cabin depressurisation, the crew performed a safe landing at Cobar. The aircraft was substantially damaged, and the flight crew were not injured.
This analysis will explore:
- origin of the in-flight fire
- aircraft preparation for the flight
- oxygen mask use and technical problem of the microphone
- cabin depressurisation
- flight crew knowledge of aircraft systems
- flight crew operating with the cockpit door open
- Pel-Air and Rex flight crew operating manual information deficiencies
- training of Rex flight crews
- Saab pre-flight inspection checklists
- Rex crew familiarity of cargo aircraft.
Origin of the in-flight fire
The source of the in-flight fire was traced to the right recirculating fan assembly. Although the fan was not damaged internally, the fire damage was most significant at the box sub-assembly, which was mounted external to the fan and housed the electrical control circuit boards. It is likely that an electrical component or components within the box sub-assembly failed, resulting in the underfloor fire. The fire damaged underfloor insulation and plastic air conditioning ducting components, which led to thick smoke filling the cabin and cockpit and aircraft structural damage.
The avionics warning received by the crew during the diversion was most likely associated with the avionics cooling air that was being drawn from the now smoke-filled cabin. This was also stated in the ‘cargo compartment smoke’ checklist.
The ATSB examination of the recirculating fan could not determine a cause for the failure in the electronic control cards which led to the fire.
When the crew received the air conditioning system right duct over temperature caution light, it was most likely due to the distribution duct over temperature being affected by the fire and the melting which occurred as a result. When the over temperature was sensed, the right bleed valve closed automatically as a function of system logic for over temperature protection.
Smoke barrier curtain
Cargo operations can have a greater fire risk than passenger operations due to the carriage of cargo that could be the source of a fire and the lack of cabin crew available to fight a fire. As such, additional protection was available to minimise flight crew exposure to cabin smoke in the form of additional smoke detectors and a smoke curtain.
However, the smoke curtain was not installed into position by anyone involved in the flight preparation. The flight crew, who normally operated the same aircraft type but in a passenger configuration, did not notice there was a placard at the aircraft entrance stating the smoke curtain was to be fitted for all cargo flights. The flight crew remained unaware of the smoke barrier curtain and its use for cargo operations. Further, the engine being transported was positioned in the cargo area of VH-KDK, on both occasions, by Rex engineers. As the curtain was usually installed by freight handlers during normal cargo operations, it is possible the Rex engineers were also unaware of its requirement to be fitted.
In this accident, the source of the fire was an aircraft component rather than the cargo being carried. If a similar fire occurs in a passenger‑configured Saab 340 aircraft, then the smoke curtain would not be in place. However, the smoke curtain was available and was required for use for this flight, so its non-use increased risk for this event.
The flight deck door was not closed during flight as prescribed in the operator’s FCOM operating limitations and checklists. Having the door closed would have likely prevented the smoke being able to flow into the flight deck.
The result of not having the smoke barrier fitted and the flight deck door closed as part of the aircraft pre-flight preparation was that smoke from the fire was not contained to the cabin area and was able to move forwards toward the flight deck.
Oxygen mask fault
The flight crew fitted their oxygen masks and smoke goggles when alerted of the presence of smoke by the central warning panel. This decision may have prevented the crew from being overcome by smoke and fumes in the cockpit in the next several minutes. However, once fitted, the crew had difficulty communicating with each other, as a result of the mask microphone being very faint and difficult for the captain to hear the first officer (FO). This appeared to be an internal fault only, as the cockpit voice recording (CVR) showed that the FO was able to be adequately heard by ATC.
This breakdown of communication delayed the crew by 57 seconds, in which emergency checks were not initiated due to the breakdown of communication. It created confusion and distraction between the crew while trying to execute the emergency checklist.
A review of the CVR captured prior to flight could not positively determine if the pre-flight check action in relation to the oxygen mask was performed. This is an important check of the emergency communication system whilst on oxygen and was designated as a mandatory check item for a daily inspection as required by the Rex and Pel-Air FCOM.
Cross-valve handle
While the flight crew were conducting the emergency checklist items for cargo compartment smoke, they were unable to locate the cross-valve handle. This was due to the combination of the thick smoke obscuring their vision and their lack of knowledge of the differences in the cargo‑configured aircraft.
Had the location and function of the cross-valve handle been known by the flight crew, the time taken to identify it during completion of the emergency checklist would have been minimised, which would have limited the delay of smoke removal from the flight deck.
In this case, the subsequent depressurisation resulted in the smoke dissipating even in the absence of the cross-valve.
Cabin depressurisation
The weakening of the fuselage structure due to the underfloor fire resulted in a breach of the fuselage skin, which led to a subsequent depressurisation of the aircraft during the descent. Although adding to another caution alert indication for the flight crew and subsequent checklist to be conducted, it also benefited in the removal of smoke from the cabin and flight deck.
At the time of the depressurisation, VH-KDK was at FL 160 and descending. The crew, when alerted to the depressurisation, increased the rate of descent to below 10,000 ft. The cabin depressurisation occurred 4 minutes after the initial smoke warning occurred.
Due to the size of the hole created, the smoke removal most likely occurred at a greater rate than using the aircraft pressurisation outflow valves alone. The resulting fortuitous reduction in the amount of smoke in the flight deck improved visibility and allowed the crew to carry out a safe landing into Cobar.
Crew familiarity of cargo‑configured aircraft
The flight crew had not flown or had any prior training on the cargo‑configured Saab 340 and were not familiar with the differences of the passenger configuration. The captain chose to liaise with a colleague to gain information on the cargo‑configured aircraft instead of accepting the company offer for a briefing.
This non-formal approach to understanding the differences between the 2 aircraft types ultimately did not pass on the required operational differences and potential safety aspects of the change of aircraft configuration.
Rex and Pel-Air manuals
Both operators (Rex and Pel-Air) manuals, which were designed to provide essential information to flight crews, did not include the required information to enable the pre-flight checks to be conducted adequately. While the weight and balance chapter of the FCOM showed the smoke barrier curtain location, there was no information on its importance to cargo operations, and as the crew had not been informed of any differences, they would not have been expecting that this section contained this information. The smoke barrier curtain installation information that was contained in the Saab service bulletin and flight manual supplement was not included in the pre‑flight checklists. As a result, the flight crew did not have awareness of its use.
The operators' manuals also did not have a check to verify the position of the cross-valve handle. As discussed above, when the checklist called for the crew to use this handle when the aircraft was already filling with smoke, the crew could not locate it.
Flight crew training
The Rex ground school provided type rating training on the Saab 340 series aircraft to both Rex and Pel-Air pilots. This training was based on the passenger‑configured aircraft. Pel-Air pilots undertook further training which gave them the knowledge and skills for the cargo‑configured aircraft.
In scheduling their flight crews to operate the cargo‑configured Saab 340, Rex did not have a process to ensure that the additional training or knowledge sharing for their crews in the differences applicable to aircraft operated by Pel-Air was delivered.
Saab pre-flight checklists
As discussed above, both operators’ manuals had no inclusion of a pre-flight interior check for the smoke barrier curtain or the cross-valve handle. Likewise, there was no pre-flight interior check for these items in the manufacturer’s documentation. Saab confirmed that there were no checks in the pre-flight checklist for the crew to specifically verify that the smoke barrier curtain was correctly fitted.
The result of the manufacturer’s pre-flight and interior checklists not detailing information for the smoke curtain was that the operator did not detail these in their own FCOM. This information was not available for the flight crew who, even without prior knowledge of the cargo‑configured variant, would have been alerted to these changes while conducting these pre-flight checks in accordance with the FCOM.
Findings
ATSB investigation report findings focus on safety factors (that is, events and conditions that increase risk). Safety factors include ‘contributing factors’ and ‘other factors that increased risk’ (that is, factors that did not meet the definition of a contributing factor for this occurrence but were still considered important to include in the report for the purpose of increasing awareness and enhancing safety). In addition, ‘other findings’ may be included to provide important information about topics other than safety factors. Safety issues are highlighted in bold to emphasise their importance. A safety issue is a safety factor that (a) can reasonably be regarded as having the potential to adversely affect the safety of future operations, and (b) is a characteristic of an organisation or a system, rather than a characteristic of a specific individual, or characteristic of an operating environment at a specific point in time. These findings should not be read as apportioning blame or liability to any particular organisation or individual. |
From the evidence available, the following findings are made with respect to the in-flight fire and cabin smoke involving a Saab 340A, VH‑KDK, 114 km east-north-east of Cobar, New South Wales, on 23 April 2023.
Contributing factors
- It was likely that an electrical component of a control circuit board on the recirculating fan failed, resulting in an in‑flight fire under the cabin floor.
- The smoke curtain was not fitted as required for the cargo configuration, and the flight deck door was open, which allowed smoke from the in‑flight fire to enter the flight deck.
- The underfloor fire caused weakening of the fuselage structure, which led to a subsequent depressurisation of the aircraft during the descent. However, the depressurisation aided in the removal of enough smoke from the flight deck on approach to allow an unhindered visual approach at Cobar.
- Crew were not familiar with the cargo configuration and were unaware of the smoke curtain requirements and location of the cross-valve handle.
- The Pel-Air and Rex Saab 340 flight crew operating manuals did not include reference to the location and operation of the cross-valve handle or the operation and use of the smoke curtain. (Safety issue)
- Rex did not ensure its flight crews received training in the differences between passenger and freight‑configured Saab 340 aircraft, prior to being scheduled to fly freight operations. (Safety issue)
- Saab did not include the smoke curtain fitment in pre-flight documentation for the cargo‑configured Saab 340 aircraft to inform flight crew of this difference from the passenger-configured version. (Safety issue)
Other factors that increased risk
- When the flight crew donned their oxygen masks, the first officer's oxygen mask microphone did not function correctly. This led to difficulty in communication between the flight crew and a delay in responding to the emergency.
- Due to the combination of the smoke density and lack of prior knowledge, the flight crew were unable to locate the cross-valve handle during the emergency, therefore delaying the removal of smoke from the flight deck.
Safety issues and actions
Central to the ATSB’s investigation of transport safety matters is the early identification of safety issues. The ATSB expects relevant organisations will address all safety issues an investigation identifies. Depending on the level of risk of a safety issue, the extent of corrective action taken by the relevant organisation(s), or the desirability of directing a broad safety message to the aviation industry, the ATSB may issue a formal safety recommendation or safety advisory notice as part of the final report. All of the directly involved parties were provided with a draft report and invited to provide submissions. As part of that process, each organisation was asked to communicate what safety actions, if any, they had carried out or were planning to carry out in relation to each safety issue relevant to their organisation. Descriptions of each safety issue, and any associated safety recommendations, are detailed below. Click the link to read the full safety issue description, including the issue status and any safety action/s taken. Safety issues and actions are updated on this website when safety issue owners provide further information concerning the implementation of safety action. |
Saab documentation for cargo configured aircraft
Safety issue number: AO-2023-020-SI-01
Safety issue description: Saab did not include the smoke curtain fitment in pre-flight documentation for the cargo‑configured Saab 340 aircraft to inform flight crew of this difference from the passenger‑configured version.
Operator documentation and crew familiarity
Safety issue number: AO-2023-020-SI-02
Safety issue description: The Pel-Air and Rex Saab 340 flight crew operating manuals did not include reference to the location and operation of the cross-valve handle or smoke curtain.
No formal company training
Safety issue number: AO-2023-020-SI-03
Safety issue description: Rex did not ensure its flight crews received training in the differences between passenger and freight‑configured Saab 340 aircraft, prior to being scheduled to fly freight operations.
Safety action not associated with an identified safety issue
Whether or not the ATSB identifies safety issues in the course of an investigation, relevant organisations may proactively initiate safety action in order to reduce their safety risk. The ATSB has been advised of the following proactive safety action in response to this occurrence. |
Additional safety action by Regional Express
Rex advised that it is implementing a fleet‑wide inspection of the flight deck and passenger compartment recirculation fans at the next aircraft heavy maintenance visit. The inspection will be focused on the electronic sub-assembly module of the recirculation fan due to this component being identified to have the most significant fire damage on the fan assembly removed from VH‑KDK.
Glossary
AC | Alternating current |
ACP | Air conditioning pack |
AOM | Aircraft operating manual |
ATC | Air traffic control |
ATPL | Air transport pilot licence |
BoM | Bureau of Meteorology |
CASA | Civil Aviation Safety Authority |
CVR | Cockpit voice recorder |
DC | Direct current |
FCOM | Flight crew operating manual |
FDR | Flight data recorder |
FL | Flight level |
FO | First officer |
INT/SPKR | Intercom/Speaker |
PF | Pilot flying |
PM | Pilot monitoring |
QRH | Quick reference handbook |
SB | Service bulletin |
Sources and submissions
Sources of information
The sources of information during the investigation included:
- the crew of VH-KDK
- Regional Express Airlines
- the chief pilot of Pel-Air Aviation
- the manager training and checking and head of operations for Regional Express Airlines
- Civil Aviation Safety Authority
- Bureau of Meteorology
- Fire and Rescue New South Wales
- Saab
- Airservices Australia
- the cockpit voice recorder and flight data recorder
- recorded data from Flightradar24.
References
Australian Government 2023, Part 91 (General Operating and Flight Rules) Manual of Standards 2020, Civil Aviation Safety Authority, Canberra, ACT, viewed 30 April 2024, <Federal Register of Legislation - Part 91 (General Operating and Flight Rules) Manual of Standards 2020>
Submissions
Under section 26 of the Transport Safety Investigation Act 2003, the ATSB may provide a draft report, on a confidential basis, to any person whom the ATSB considers appropriate. That section allows a person receiving a draft report to make submissions to the ATSB about the draft report.
A draft of this report was provided to the following directly involved parties:
- Civil Aviation Safety Authority
- Airservices Australia
- Crew of VH-KDK
- Regional Express Aviation
- Pel-Air Aviation
- Swedish Accident Investigation Authority (SHK)
- Bureau of Enquiry and Analysis for Civil Aviation Safety (BEA).
Submissions were received from:
- the captain of the crew
- Regional Express Aviation
- Pel-Air Aviation
- Swedish Accident Investigation Authority (SHK)
- Bureau of Enquiry and Analysis for Civil Aviation Safety (BEA).
The submissions were reviewed and, where considered appropriate, the text of the report was amended accordingly.
Purpose of safety investigationsThe objective of a safety investigation is to enhance transport safety. This is done through:
It is not a function of the ATSB to apportion blame or provide a means for determining liability. At the same time, an investigation report must include factual material of sufficient weight to support the analysis and findings. At all times the ATSB endeavours to balance the use of material that could imply adverse comment with the need to properly explain what happened, and why, in a fair and unbiased manner. The ATSB does not investigate for the purpose of taking administrative, regulatory or criminal action. TerminologyAn explanation of terminology used in ATSB investigation reports is available here. This includes terms such as occurrence, contributing factor, other factor that increased risk, and safety issue. Publishing informationReleased in accordance with section 25 of the Transport Safety Investigation Act 2003 Published by: Australian Transport Safety Bureau © Commonwealth of Australia 2024
Ownership of intellectual property rights in this publication Unless otherwise noted, copyright (and any other intellectual property rights, if any) in this report publication is owned by the Commonwealth of Australia. Creative Commons licence With the exception of the Commonwealth Coat of Arms, ATSB logo, and photos and graphics in which a third party holds copyright, this report is licensed under a Creative Commons Attribution 4.0 International licence. The CC BY 4.0 licence enables you to distribute, remix, adapt, and build upon our material in any medium or format, so long as attribution is given to the Australian Transport Safety Bureau. Copyright in material obtained from other agencies, private individuals or organisations, belongs to those agencies, individuals or organisations. Where you wish to use their material, you will need to contact them directly. |
[1] PAN PAN: an internationally recognised radio call announcing an urgency condition which concerns the safety of an aircraft or its occupants but where the flight crew does not require immediate assistance.
[2] Flight level: at altitudes above 10,000 ft in Australia, an aircraft’s height above mean sea level is referred to as a flight level (FL). FL 220 equates to 22,000 ft.
[3] Pilot flying (PF) and pilot monitoring (PM): procedurally assigned roles with specifically assigned duties at specific stages of a flight. The PF does most of the flying, except in defined circumstances, such as planning for descent, approach, and landing. The PM carries out support duties and monitors the PF’s actions and the aircraft’s flight path.
[4] Warnings and cautions: give pilots aural and visual alerts for abnormal conditions. Warnings are highest priority which require immediate action. Cautions are the second priority and give advisory information to pilots.
[5] PAN PAN: an internationally recognised radio call announcing an urgency condition which concerns the safety of an aircraft or its occupants but where the flight crew does not require immediate assistance.
[6] The avionics smoke indication was a result of the avionic bay drawing in smoke from the cargo area.
[7] Activating the fire extinguisher system also closes the fuel shut‑off valves, which removes all supply of fuel to the engines. The fire bottles are then operated, extinguishing fire within the engine cowlings.
[8] Saab manufactured the 340 in A, B and B WT variants.
[9] Both Rex Airlines and Pel-Air were wholly owned subsidiaries of Regional Express Holdings Limited (REX).
[10] Although VH-KDK landed safely, the extent of the damage from the fire is classified by ICAO Annex 13 as an accident due to the nature of major repair work required to the airframe.
[11] CAVOK: Conditions and visibility good, nil significant cloud and excess of 10 kilometres visibility
[12] The thermal switch is designed to detect an overheat of the cooler only. It is not configured or located where it would detect the overheating of the electronic card sub-assembly.
[13] Quick change aircraft are designed so that they can be operated in a passenger configuration and then quickly changed to then operate in a freighter configuration, depending on operator requirements.