Executive summary
What happened
On 10 November 2022, a Link Airways (Link) Saab 340B, registered VH-VEQ, was being prepared for a commercial air transport flight. The aircraft was operating as VA633, scheduled from Canberra, Australian Capital Territory, to Sydney, New South Wales.
During the aircraft preparation process, the first officer (FO) did not attach the strap extension between the stairway and the left propeller. The strap extension was used by some operators to guide passengers onto the aircraft and would prevent the cabin door being closed without its removal. Once passengers had boarded and during the final inspection, the FO did not remove the propeller strap—used to prevent propeller windmilling—from the left engine.
The dispatch coordinator (dispatcher), who was employed and trained by the ground handling company Swissport, did not conduct another walk-around or follow the FO. Prior to engine startup the propeller strap was not noticed by the captain or the dispatcher. During the startup sequence there was a delay between the commencement of engine start and the propeller spinning due to the pins securing the strap to the engine cowling. Once these failed, the propeller began turning normally and the aircraft was cleared to depart with the strap still attached to the left propeller but not visible due to the propeller’s rotation.
At about the time the aircraft became airborne, the propeller strap was thrown free of the blade and into the fuselage. Passengers recalled hearing an extremely loud bang, and could see that an object had penetrated the cabin. The strap itself became embedded in the fuselage, but the failed cowling pins broke free of the strap and entered the cabin. One fragment struck the leg of a passenger, resulting in a minor injury (bruising).
From the flight deck, the flight crew did not see or hear the propeller strap penetrate the fuselage. The cabin manager (CM) realised what had happened, but waited until the aircraft was no longer in a critical phase of flight before contacting the flight crew. The CM stated that there was an emergency in the cabin, and that someone was hit, but did not elaborate beyond expressing a need to return to Canberra and that an ambulance would be required. The flight crew, believing the emergency to be only passenger-related, did not seek any additional information. The aircraft landed safely in Canberra and emergency services assessed the injured passenger.
What the ATSB found
The ATSB found several factors that may have contributed to the propeller strap not being noticed or removed by the FO, captain or dispatcher. Most importantly:
- The strap extension was not fitted. Because the cabin door could not be closed with the strap extension in place, its correct fitment would almost certainly have prevented the flight from proceeding with the propeller strap attached. A review of other departures out of Canberra found that some other flights were boarded without the strap extension being attached.
- The propeller strap did not have a visibility aid (streamer) fitted in accordance with the manufacturer’s design. Link conducted an inspection of its Saab 340B fleet and found the condition of propeller straps to be significantly variable.
- Guidance provided by Link Airways for training of Swissport dispatchers did not explain the appearance, function and importance of the propeller straps.
In addition, while not found to have contributed to this occurrence, Swissport did not ensure that the implemented dispatcher training and audits for operations involving the Link Airways Saab 340B dispatches incorporated all of the elements required for pre-departure walk-arounds in its own ground handling manual. This increased the overall risk to the flight.
Similarly, risk was increased by the flight crew not being informed of the fuselage penetration, although this did not contribute to the outcome of the occurrence.
What has been done as a result
Link advised that it had updated the flight crew and cabin crew operating manuals to include additional preflight checks for the presence of the propeller strap and strap extension. Additional clarity was provided to cabin crew regarding contacting the flight deck during emergencies. Propeller strap discrepancies were rectified within Link’s Saab 340B fleet, and regular inspections and maintenance were added to procedures.
Link amended training guidance to Swissport, including more details on the use of propeller straps and strap extensions, as well as the dispatcher’s role in checking for the strap. Link has planned audits of Swissport dispatches to ensure the procedures are correctly implemented.
Swissport informed all ramp staff (including dispatchers and trainers) that walk-arounds were required on Saab aircraft. It consulted with Link to better define dispatcher responsibilities and expectations, and planned refresher training on the walk-around described in Swissport’s procedures.
Safety message
For those directly involved in aircraft operations, this occurrence highlights the importance of vigilance. When there are multiple risk controls in place and multiple responsible parties, it is easy to become complacent from an expectation that earlier checks have been done correctly and that future checks elsewhere in the system will likely catch anything missed.
From an organisational perspective, the occurrence illustrates the importance of strong communication and harmonised procedures. The use of external ground handling services has become increasingly common in aviation. The relationship between carrier and ground handler can add complexity to ground handling operations. In this instance, differences in expectations and understanding of ground handler responsibilities led to a dispatch procedure that was not effective in confirming that the aircraft was clear for engine start-up. It is critical that all involved parties have a complete understanding of their roles and responsibilities, and how they fit together to create a safe and functional operating environment.
The occurrence
On the morning of 10 November 2022, a Saab 340B, registered VH-VEQ, was being prepared for a scheduled air transport flight from Canberra Airport, Australian Capital Territory to Sydney Airport, New South Wales. The flight was being operated by Link Airways (Link), with flight number VA633. The flight was to be conducted with 2 flight crew, a cabin manager (CM), and 29 passengers.
It was the first flight of the day for the aircraft and both members of the flight crew. Both propellers had been restrained overnight to prevent windmilling using propeller straps that secured a propeller blade to the engine cowling. At 0718, as part of the aircraft preparation process, the first officer (FO) began the external portion of the daily aircraft inspection[1] (see Use and stowage). As part of this inspection, the FO removed the right propeller strap and inspected the right engine in accordance with Link’s Flight crew operating manual (FCOM). The FO then ‘dressed’ the propeller, rotating it 45° from its restrained ‘T’ position to an ‘X’ position, as an indication that the propeller was free to spin.
After continuing the walk-around, the FO removed the left propeller strap to inspect the engine, then reattached the strap so that passengers could safely board without the propeller windmilling. The procedures required the attachment of a strap extension[2] from the left propeller strap to the airstairs[3] (see Propeller straps). The strap extension was designed to prevent passengers from walking under the aircraft, and its presence also prevented the cabin door from being closed without first removing it. The strap extension was in its normal stowage location in the flight deck behind the door but the FO did not remove the strap extension from the flight deck.
At 0754, after the passengers had boarded, the FO commenced a final external check of the aircraft, which involved a walk-around starting at the nose and moving clockwise around the aircraft confirming that the aircraft was generally prepared for flight, including that hatches were closed and ground service equipment had been removed. The FO closed the cargo bay door, and proceeded to board the aircraft via the airstairs, instructing the CM to close the cabin door. Prior to boarding the aircraft, the FO inadvertently did not remove the left propeller strap.
The dispatch coordinator (dispatcher)[4] tasked with dispatching the aircraft later reported that they observed the FO closing the cargo bay door and entering the aircraft, and this was supported by available closed-circuit television (CCTV) footage, which showed the dispatcher near the cargo bay door at the time. However, the dispatcher did not follow the FO during the entire walk-around (see Dispatcher training and procedures).
The dispatcher moved to the nose of the aircraft in accordance with procedures, so that the captain could be signalled when engines were clear to start. The dispatcher reported that they did not look for, or notice, the strap fitted to the left propeller. However, from the dispatcher’s perspective, the sun was behind and just above the aircraft, which reportedly reduced the aircraft’s visibility.
The captain signalled that the right engine would be started, and the dispatcher signalled all clear. The captain started the right engine, and then signalled that the left engine would be started. The dispatcher once again signalled all clear.
The captain commenced starting the engine, and CCTV showed the left propeller move slightly, then stop. Neither the captain or dispatcher noticed this brief movement, and neither noticed the propeller failing to rotate as it normally would.[5] Seated on the right side, the FO could not observe the left propeller.
The engine continued to build torque with the propeller restrained, and 33 seconds after the initial movement the propeller began to turn. Subsequent investigation established that the propeller torque caused the pins securing the strap to the engine cowling to fail with the strap remaining secured to one of the blades.
In a subsequent interview, the dispatcher reported that while the delay between the signal for ‘all clear’ and the propeller’s rotation was unusual, sometimes pilots would complete other tasks between signalling an engine start and commencing it. The dispatcher therefore did not believe it needed to be brought to the attention of the captain.
The rest of the aircraft dispatch process was completed without incident. At 0803 the flight crew taxied the aircraft to the runway and took off.
During the take-off, about the time the aircraft became airborne (according to the CM’s recollection), the propeller strap was thrown free of the blade and into the fuselage (Figure 1). The strap itself became embedded in the fuselage, but the two failed cowling pins that were attached to the strap broke free and entered the cabin. One fragment struck the leg of the passenger in seat 2A, resulting in a minor injury (bruising).
Figure 1: Part of the left propeller strap that entered the fuselage adjacent to seat 2A
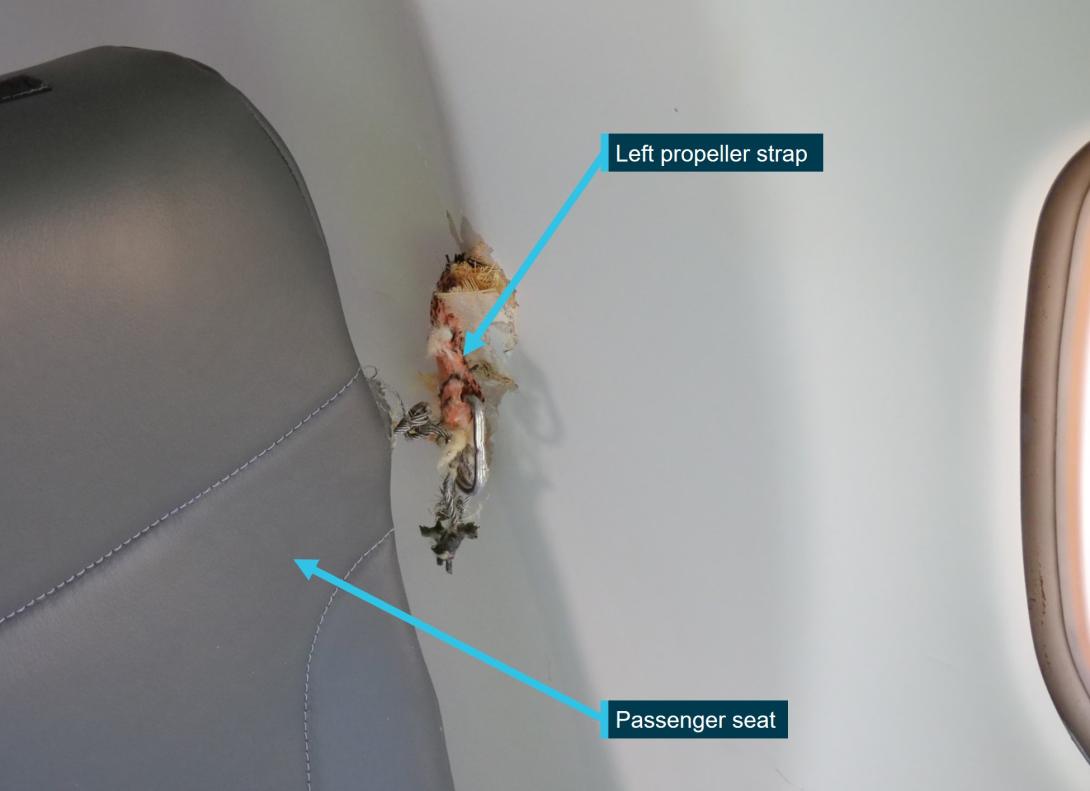
Source: ATSB
Passengers recalled hearing an extremely loud bang, and were able to see immediately that an object had penetrated the cabin. From the flight deck, the flight crew did not see or hear the strap penetrate the fuselage. The CM recalled that they recognised the propeller strap and realised what had occurred, but did not immediately contact the flight crew. In a subsequent interview, the CM stated that this was due to sterile cockpit procedures (see Cabin procedures).[6]
Approximately 25 seconds after take-off, the CM signalled to the flight crew using the emergency call button, which activated an aural and visual indication on the flight deck. When the flight crew contacted the CM, the response that was recorded was the CM stating ‘Emergency. Somebody… we need to get back to the airport.’ The flight crew then informed Canberra tower and prepared to return the aircraft to Canberra.
After 2.5 minutes, the flight crew contacted the CM again to ask if emergency services were required. The CM replied ‘Yes… a passenger was hit.’ Further communication between the CM and flight crew related to taxi procedures and provision of emergency services. There was no further communication about the nature of the emergency. The flight crew continued the flight under the impression that the emergency was only related to a medical condition of a passenger.
The aircraft landed at 0816 without further incident and the passengers were disembarked. The injured passenger was assessed by the emergency services in attendance.
The aircraft was quarantined in Canberra pending the ATSB’s attendance. A remnant of the propeller strap was recovered from the fuselage (Figure 1) where it had caught on a stringer.[7] The cowling pins were no longer attached to the strap. Sections of both cowling pins were still secured in the engine cowling following the occurrence (Figure 2). Other parts breached the fuselage and were recovered from the cabin floor (Figure 3). A small section of one cowling pin was not located. The strap extension was still stowed on the flight deck.
Figure 2: Cowling pin sections that remained secured in the engine cowling, and the damaged propeller strap shown in the normal fitment location after being recovered from the fuselage
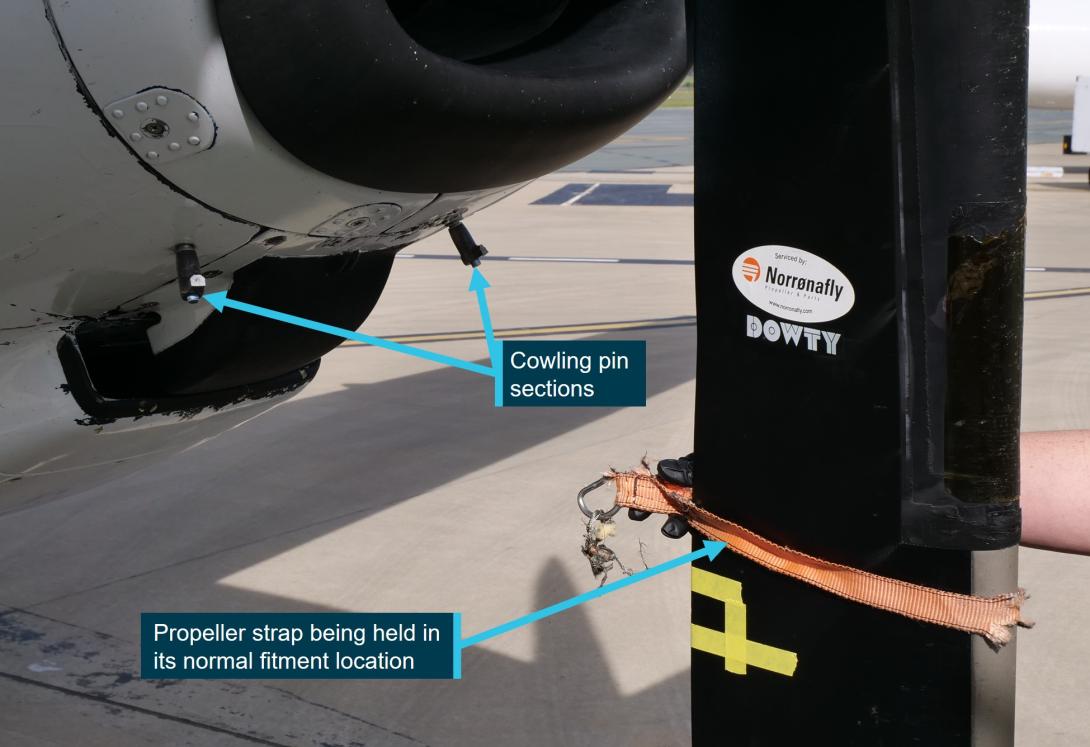
Source: ATSB
Figure 3: Parts of the cowling pins recovered from the cabin floor and the engine cowling
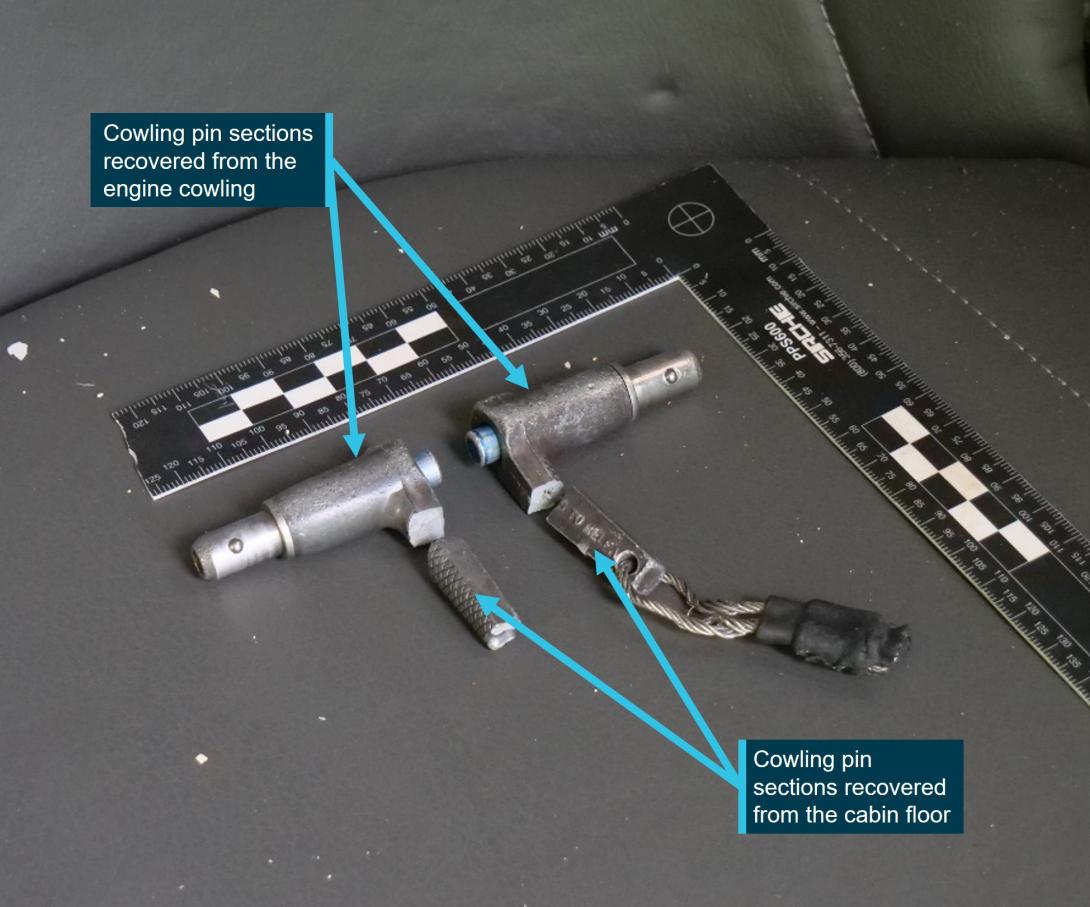
Source: ATSB
Context
Personnel information
The captain held an Air Transport Pilot Licence (Aeroplane) and a multi-engine command instrument rating. The captain held a Class 1 aviation medical certificate and had a total flying time of 4,836.2 flying hours with 1,423.3 hours on the Saab 340.
The first officer (FO) held an Air Transport Pilot Licence (Aeroplane) and a multi-engine command instrument rating. The FO held a Class 1 aviation medical certificate and had a total flying time of 834 flying hours with 436 hours on the Saab 340.
Both flight crew members were within duty limits as prescribed by Civil Aviation Order 48.1 Appendix 3. In a subsequent interview, the FO noted feeling fatigued on the morning of the occurrence due to flight duties and home life.
The cabin manager (CM) had 18 years of cabin crew experience and began working on Saab 340B aircraft in early 2022.
Propeller straps
Function and design
The propeller strap assembly, also referred to as the ‘propeller restraining bridle’ by Saab, was intended for use in preventing propeller movement when the aircraft was parked. The strap assembly provided by Saab consisted of a loop to slide over the propeller blade, two cables with pip pins for securing to the engine cowling, and a streamer to aid visibility (Figure 4).
Figure 4: Propeller strap assembly as issued by Saab
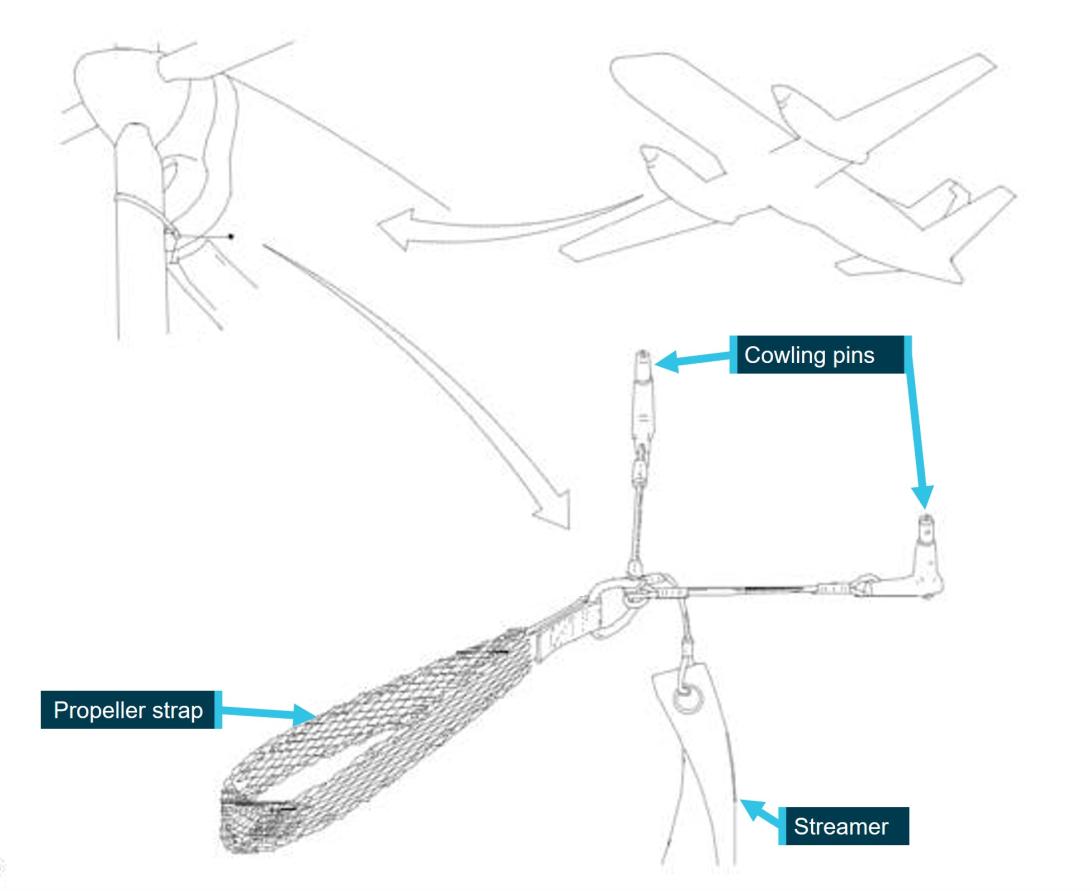
Source: Saab, annotated by the ATSB
The propeller strap could only be fitted with the propeller in the ‘T’ position, with 2 blades vertical and 2 horizontal. Without the strap, the propeller can be rotated.[8]
The propeller strap involved in the occurrence had bright orange webbing. Closed-circuit television (CCTV) footage showed that there was no ‘remove before flight’ streamer attached to it.
Following the occurrence, Link Airways (Link) conducted a fleet-wide review of its propeller straps and found significant variation in serviceability. Link found that:
…several prop straps fitted to the fleet did not have a hi vis [high visibility] streamer attached, or if they were attached were discoloured with age and not effective.
Link also found that the orange webbing of the propeller straps was dull or faded with age in some instances.
Link also used a strap extension, made with fluorescent webbing and connecting between the handrail on the airstairs and the left propeller strap. The strap extension was not designed or supplied by the aircraft manufacturer, but a similar product was used by other Saab 340B operators. According to the Link Flight crew operating manual (FCOM), it was intended to ‘provide a visual indication of a restricted area around the propeller’ and a ‘safety mechanism restricting the passenger door stairs from being closed without removing the extension and prop strap.’ An example of the fitment of a strap extension in accordance with the FCOM is shown in Figure 5.
Figure 5: Exemplar strap extension fitted between airstairs and propeller strap
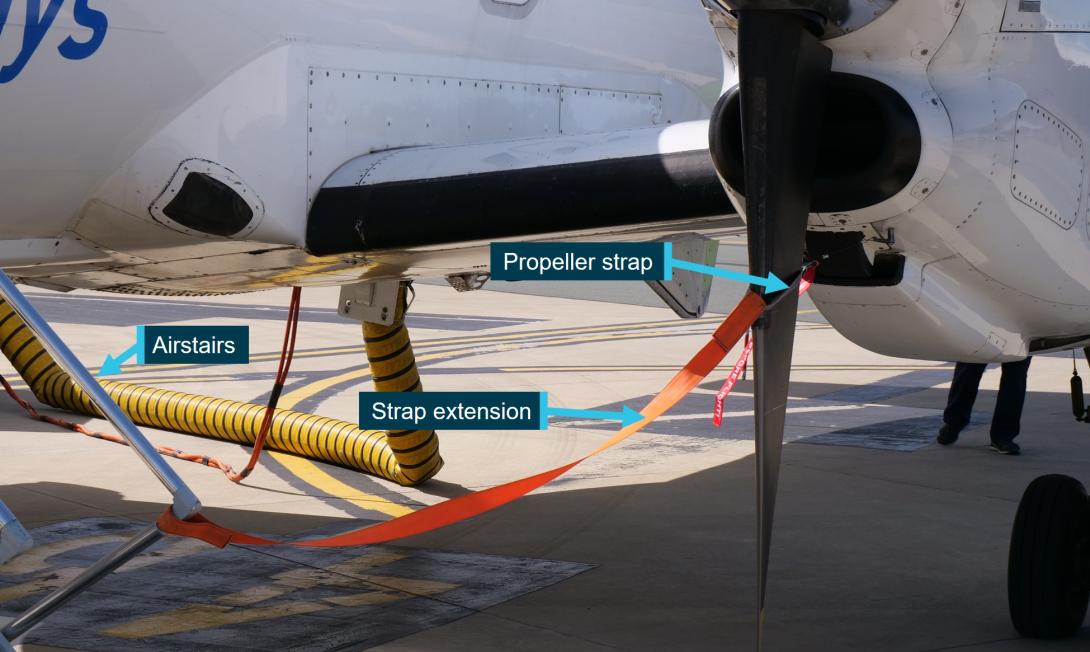
Source: ATSB
Use and stowage
During aircraft departures, procedures for the propeller straps and strap extension differed slightly depending on whether the aircraft was being prepared for the first flight of the day, or if it was following a previous flight.
Prior to a first flight, Link’s FCOM required a line check, known as a ‘Line Check 1’ or ‘LC1’, to be performed by one of the pilots. Both propeller straps would already be fitted (from the night before), with the strap extension stowed in the flight deck. As part of the line check, FCOM procedures required the pilot to remove the propeller straps in order to properly inspect both engines. The responsible pilot was then required to replace the left propeller strap and fit the strap extension. Prior to the occurrence flight, which was the first flight of the day, the FO removed both straps and replaced the left propeller strap during the inspection, but did not fit the strap extension.
For aircraft preparations following a previous flight, the right propeller strap was not to be fitted. The left propeller strap and strap extension should already be in place, because prior to passenger disembarkation, procedures required the flight crew to fit the connected propeller strap and strap extension to the propeller blade and airstairs, respectively.
For all departures, once passengers boarded, the FCOM required a ‘final external check’ by the flight crew. This list included the following items:
- Remove right Prop Strap and dress the propeller to 45°.
- Remove left Prop Strap and extension and dress the propeller to 45°.
Pilots did not generally separate the strap extension from the propeller strap when they were removed from the engine. They would remove the cowling pins and slide the propeller strap, along with the strap extension, off the blade. The other end of the extension would then be disconnected from the airstairs.
Prior to the occurrence flight during the final external check, the FO did not remove the left propeller strap, and therefore could not ‘dress’ the propeller (moving it from the ‘T’ to the ‘X’ position). The right propeller strap had been removed and the right propeller was dressed as part of the previous inspection. In a subsequent interview, the FO did not recall seeing the propeller strap, their actions after closing the cargo bay door, nor whether any distractions might have affected the walk-around. Available CCTV footage did not reveal any observable distractions, although the FO might have spoken with the CM waiting at the top of the airstairs at the point when the propeller strap would normally be removed.
At the end of the final external check, upon entering the flight deck, the pilot was required to stow the propeller strap and strap extension behind the flight deck door, and confirm with the other pilot using the following phrase as an example:
Pogo[9] stowed, Cargo Door closed, Prop Strap stowed, waiting for confirmation of 22 PAX
A review of cockpit voice recordings found that the FO did not advise the captain of door closure and equipment stowage.
Start-up procedures
Following the final external check, the Link FCOM required the flight crew to complete the engine start checklist and stated:
- Before starting any engine, the LP [left seat pilot, usually the captain] shall check propeller area is clear, the prop tie has been removed and fuel cap is on, then call ‘Clear left’.
- The RP [right seat pilot, usually the first officer] shall check propeller area is clear, the prop tie has been removed, the fuel cap is on and the fuel door is closed, then call ‘Clear right’.
Once the checklist was completed, the start procedure could be commenced. The captain was to signal to the dispatch coordinator (dispatcher) which engine was to be started using hand signals. After receiving the dispatcher’s signal that the specified engine was clear of obstructions and safe to be started, the pilot could start the engine. The FCOM required the captain to monitor the engine instruments, including checking for propeller rotation, during the start process. Although the propeller begins to rotate within a few seconds of the start, the rotation speed is not shown on the instruments until the captain cuts the starter, about 40 seconds after the start is commenced.
In a subsequent interview, the captain recalled checking the left engine area for obstructions before start-up. Seeing that nobody was near the propellers, the captain determined the engine was safe to start, but did not notice the propeller strap or the position of the propeller in the ‘T’ position rather than the ‘X’ position (see Use and stowage).
Ground handling
Ground handling arrangements
The occurrence flight was being operated by Link on behalf of Virgin Australia (Virgin); part of an arrangement that commenced in January 2022. Ground handling services for all Virgin flights at Canberra Airport, including those operated by Link, were handled by Swissport through a Standard ground handling agreement (SGHA). These services included ramp support, equipment, towing/pushback of aircraft, and coordinating dispatches.
The use of third-party ground handling services has become increasingly common in Australia as well as globally. Many of these arrangements, as with the one between Virgin and Swissport, implement a variation on the SGHA that is controlled and distributed by the International Air Transport Association.
Article 5 of the SGHA applying to this arrangement outlined the standard of work to be performed by the handling company (Swissport). It stated:
The Handling Company shall carry out all technical and flight operations services as well as other services having a safety aspect, for example, load control, loading of aircraft and handling of dangerous goods, in accordance with the Carrier’s instructions…
Among the services agreed to be provided was the following ‘safety measure’:
Perform visual external safety/ground damage inspection of
(a) doors and panels and immediate surroundings
(b) other inspection items as specified in Carrier's Manuals
…immediately prior departure
This SGHA subsequently stated:
In the case of absence of instructions by the Carrier, the Handling Company shall apply its own standard practices and procedures…
Dispatcher training and procedures
Information provided by Link to Swissport
Prior to Swissport commencing ground handling duties for Link flights, Link provided Swissport with various documents including its Scheduled air transport ground handling manual (SATGHM), so that Swissport trainers could train its own employees on dispatching Link’s Saab 340B aircraft. The SATGHM included a basic familiarisation of the aircraft and associated hazards, procedures for loading baggage into the aircraft, and procedures for aircraft marshalling.
Within the aircraft familiarisation information, the propeller strap was noted as an item that the flight crew fitted prior to passenger disembarkation. No further information was provided to Swissport about propeller straps. There was also no information about the dressing of propellers. A Swissport trainer reported that they were told by Link staff that walk-arounds were the duty of the flight crew and not dispatchers.
However, Link also provided a practical training checklist for aircraft ramping and dispatch duties. This included a list item requiring the trainee to ‘complete [a] visual check of aircraft in final walk around’. The associated procedure stated:
Confirm by visual and/or touch that all doors and other opening are closed flush with the fuselage
Link provided no additional information to Swissport regarding dispatcher walkaround procedures for Saab 340B dispatches.
Swissport procedures
Swissport’s Ground operations manual (GOM) provided all dispatchers and ground crew with general instructions for tasks such as aircraft dispatches. These were designed to cover a wide variety of aircraft types and did not contain information specific to Saab 340B dispatches or any specific operators. The manual stated:
The purpose of this manual is to provide clear direction to all airport staff and staff contracted to Swissport Pacific on their responsibilities and work procedures relating to airport activities, wherever a client does not have specific procedures relating to the tasks being carried out.
This manual included a requirement for a walk-around for ‘all dispatches’, stating (original emphasis):
SAFETY NON-NEGOTIABLE: The walk-around is extremely important, it is the last physical and visual check of the aircraft prior to departure and is critical to ensuring the safety of passengers and crew. It must always be completed in full, with all due care and attention and without deviation. This is a safety non-negotiable.
This walk-around was to be performed by the dispatcher once all other dispatch preparation had been completed, such as loading and boarding. The GOM instructed dispatchers to walk clockwise from the nose around the aircraft’s perimeter, and provided a 10-point list of check items such as:
- open or protruding doors and panels
- signs of leaks and damage
- ‘remove before flight’ streamers on the landing gear or flight data sensors
- remaining ground support equipment or foreign object debris on the apron.
There was no specific instruction to look for a propeller strap or objects secured to the propellers/engine cowling.
The manual included a second, 15-point list of specific items to check during the dispatcher walk‑around. Dispatchers were to confirm ‘no signs of visible damage or fluid leaks on the tarmac’ around the engine area, and ‘no signs of “remove before flight” streamers … around the door and panel areas on the fuselage.’ None of the list items related to the propellers or propeller straps.
Following the occurrence, a Swissport internal investigation report stated that because Link had not provided a standard operating procedure for a dispatcher walk-around, it was the flight crew’s responsibility to complete a final walk-around, not the dispatcher.
Swissport training
All dispatchers and other ground crew completed training modules provided by Swissport for general employment procedures, such as work health and safety. The specific training provided by Swissport for Link’s Saab 340B dispatches used a combination of information provided by Link and Swissport’s procedures. This took the form of in-person presentations by the trainer, as well as practical training and assessment. The training did not refer to Swissport’s GOM, or instruct dispatchers to refer to it. Dispatchers seeking additional information were instead directed to Link’s SATGHM.
The ATSB sought interviews with several trainers and dispatchers of Saab 340B aircraft. Both a trainer and a dispatcher confirmed that dispatchers were taught that the final walk-around was the flight crew’s responsibility. Dispatchers were not trained to complete a full walk-around, but were trained to follow the pilot from the cargo bay door to the airstairs during the final external check. Dispatchers were trained to ensure that doors and hatches were flush with the fuselage, and that the pogo stick was stowed. Once the pilot conducting the final walk-around was aboard and the cabin door closed, dispatchers were trained to move to the nose of the aircraft to assist the captain with the engine start procedure (see Start-up procedures).
One dispatcher stated that previous Swissport training for other operators had also not required a walk-around. It was reported that, at the time of the occurrence, some dispatchers were not aware of the requirement in Swissport’s GOM that walk-arounds were be conducted for all dispatches.
It was reported by a trainer and a dispatcher that the training did not provide any information on the use of propeller straps, and did not require dispatchers to look for propeller straps or strap extensions during the aircraft dispatch. Similarly, the training did not discuss the significance of a propeller in the ‘T’ position or the ‘X’ position.
One trainer reported that while they knew that the Saab 340B had some form of propeller restraint, the trainer assumed that the propeller strap and strap extension were inseparable, and therefore that the cabin door could not be closed while the propeller strap was in place. The trainer therefore did not consider the strap an item that should be checked by dispatchers.
Audits on aircraft dispatches
Swissport conducted routine audits of some aircraft dispatches across all of its associated carriers. In March 2022, Swissport agreed to dispatch Link’s Saab 340B aircraft as part of an existing arrangement between Swissport and Virgin. Between March and the occurrence in November 2022, 4 audits on dispatches of Link aircraft were conducted. These audits were conducted by the same people who trained staff on Saab 340B dispatches. There were no adverse findings for 3 of the 4 audits, while the other audit had one finding relating to correct operation of the ground power unit.
Cabin procedures
Link’s Cabin crew operating manual (CCOM) provided cabin crew with a list of tasks to be completed prior to departure. At the time of the occurrence, the cabin crew had no responsibilities relating to the propeller strap or strap extension.
The CCOM contained procedures for various potential emergency scenarios, but there was no guidance specific to an object penetrating the fuselage. The CCOM section describing cabin crew responsibilities in the event of an emergency stated the following:
Reporting of any event or circumstance which may affect the safety or security of passengers, crew members or aircraft to the PIC [pilot in command] must be considered an immediate priority and shall be accomplished through the most expedient means available, even if to do so requires the interruption of the PIC in his duties.
The manual also described sterile flight deck procedures, stating that a sterile flight deck was in place during take-off until the seatbelt sign was turned off. Sterile flight deck (also known as sterile cockpit) procedures are a requirement of the Civil Aviation Safety Regulations and, among other things, limit the timing and reasons for cabin crew communications with the flight crew during certain critical periods of flight, including take-off. Regarding emergencies during the sterile flight deck phase, the CCOM stated:
For an emergency or abnormal situation during the sterile flight deck phase, and no contact period, Cabin Crew may make a call to Flight Crew by pressing EMERG CALL button at any time. Flight Crew will receive aural and visual indications on the Flight Deck.
The manual subsequently stated that ‘Cabin Crew must, as soon as practical, ensure Flight Crew are made aware of what emergency or abnormal situation is happening in the cabin.’
Review of previous flights
CCTV footage was retrieved from Canberra Airport, capturing 8 separate flight preparations and dispatches involving Link Saab 340B aircraft from the day of the occurrence and the days prior. The propeller strap was used on all 8 occasions. Due to the position and quality of the footage, the condition of the individual propeller straps could not be determined. The strap extension was not attached between the propeller strap and airstairs during boarding for 2 out of the 8 observed departures, both of which were the first flight of the day.
Various Swissport staff were observed dispatching aircraft in the recordings. In each recorded departure, the duty dispatcher did not conduct a walk-around around the aircraft’s entire perimeter as prescribed in Swissport’s GOM. While the pilots walked from the cargo bay door to the airstairs, the actions of the dispatchers varied between departures. Some dispatchers were already at the nose of the aircraft, or walking towards it at the time. Others were driving the tug away from the aircraft after loading luggage. One dispatcher out of the 8 appeared to be walking around to the front of the aircraft, observing the pilot between cargo bay door and airstairs, but the dispatcher did not follow the pilot directly.
Safety analysis
Introduction
The aircraft was released for flight with the propeller strap still attached to the left propeller. Rotational torque during the engine start broke the 2 pins securing the strap to the engine cowling, leaving the strap webbing (with broken fragments of the pins still connected) attached to the propeller blade. The partial strap assembly was flung off the propeller during the take-off, penetrating the fuselage and injuring one passenger.
There were several opportunities for the first officer (FO), captain and dispatch coordinator (dispatcher) to recognise that the propeller strap was still attached prior to departure, but the strap’s presence on the left engine was not noticed. In the following sections, this analysis discusses the various factors associated with:
- pre-flight and engine start procedures
- ground handling and aircraft dispatching
- the use of strap extensions
- fleetwide propeller strap serviceability
- dispatcher training facilitated by Link Airways (Link) and Swissport
- interactions between the flight crew and cabin manager.
Pre-flight procedures
The Link Flight crew operating manual (FCOM) required the right seat pilot—the FO in this case—to conduct a final external check (walk-around) of the aircraft before departure. As part of the check, the FCOM required the FO to ‘remove left prop strap and extension and dress the propeller to 45° (the ‘X’ position). In this occurrence, the FO did not see and remove the propeller strap during the final external check, and did not notice that the strap extension was not present at the time. It is likely that the absence of the strap extension contributed to the FO not seeing and removing the propeller strap, since this larger and more obvious strap would serve as a reminder that the propeller strap was still present. Further, the propeller strap streamer was missing, which is specifically designed to attract attention and therefore reduce the chance that someone could miss the presence of the propeller strap (with or without the extension). There was insufficient evidence to determine whether distraction contributed to the FO not seeing or removing the strap.
There was also an opportunity for the flight crew to notice the fact that the propeller strap had not been brought into the flight deck. The FCOM specified that the FO should tell the captain that the propeller strap had been stowed, but it was not done in this instance. If the FO had remembered to confirm strap stowage with the captain, one of the crew members might have noticed its absence. While the FO noted feeling fatigued on the morning of the occurrence, there was insufficient evidence to establish if the pilot was likely experiencing a level of fatigue known to affect performance at the time of the occurrence.
Engine start
During the engine start sequence, there was an opportunity for the captain to notice the propeller strap was still attached prior to start-up. The FCOM required the captain to check the propeller was clear and that the ‘prop tie’ (propeller strap) had been removed. In an interview, the captain recalled checking the left engine area prior to start, but did not notice the strap.
The captain would not have been expecting the strap to still be present, and was probably focusing on ensuring that no people or obstructions were near the propeller rather than the condition of the propeller itself. As discussed in Propeller strap condition, if the propeller strap streamer was present, it would have increased the chance of the captain noticing the strap was still in place.
The captain was not required to check (and did not notice) whether the propeller was in the ‘X’ position or the ‘T’ position, which was used to indicate the presence of the propeller strap. However, sufficiently high winds can rotate an unrestrained propeller to a different orientation prior to engine start, so the propeller orientation would not necessarily alert a pilot to a potential issue.
As part of the engine start, the FCOM required pilots to monitor the instruments for propeller rotation along with other engine instruments. In this occurrence, there was 33 seconds between the propeller moving slightly (indicating engine start) and the cowling pins failing, allowing the propeller to rotate freely. By the time the propeller rotation could be monitored using the instruments (approximately 40 seconds after the start had commenced), the propeller would have been rotating normally. Given that the captain’s attention would have been on the instruments, it is likely that this aspect of the start sequence was not noticeably unusual to the flight crew.
Once the engine start was complete the propeller was likely spinning too fast to see that the propeller strap was still attached to the propeller.
Ground handling and dispatch
The dispatcher did not notice that the propeller strap was still attached to the aircraft during the FO’s final walk-around. The dispatcher was positioned near the cargo bay door during the walkaround, and reported observing the FO moving from the cargo bay door to the airstairs. The dispatcher did not follow the FO during this process, despite it being part of the practical training. Following the FO or performing a full walk-around in accordance with Swissport procedures (see Swissport dispatcher procedures and training) would have provided a better opportunity for the dispatcher to look for the kind of hazards described in the Ground operations manual (GOM), such as open panels, ‘remove before flight’ streamers and ground service equipment. It should be noted that dispatchers were not trained to look for propeller straps (seeDispatchers not familiar with propeller straps or propeller dressing).
While at the nose of the aircraft for the engine start procedure, the dispatcher did not see the strap when checking the engine was clear. The dispatcher also did not notice the slight movement of the propeller at the beginning of the engine start sequence. In addition to the strap visibility and lack of instruction regarding the strap, the position of the sun behind the aircraft could have limited the dispatcher’s view.
Use of strap extensions
The strap extension was to be fitted between the propeller strap and airstairs, and served to indicate the restricted area around the propeller during boarding. Since it was much larger than the propeller strap, it also served as an additional visual indication that the propeller strap was still fitted. Most critically, the strap extension prevented the cabin door being closed without first removing it from the airstairs.
In this occurrence, being the first flight of the day, the strap extension was not already attached from a previous flight. When leaving the flight deck to begin the line check, the FO did not take the strap extension from behind the flight deck door and attach it between the propeller strap and airstairs following the left engine inspection, as required by the FCOM. If the strap extension had been fitted, the cabin manager (CM) would have been unable to close the cabin door after boarding and the flight would have almost certainly not proceeded without removal of the propeller strap.
An examination of closed-circuit television (CCTV) footage at Canberra Airport showed other Link flights where the strap extension was not fitted prior to departure. Out of 8 observed departures, in addition to the occurrence flight, the strap extension was not fitted twice, including one that was the first flight of the day. It is likely that the differences in aircraft preparation for a first flight of the day compared to a turnaround increased the likelihood of the strap extension not being fitted for departure. As 3 of the 9 Link departures (occurrence flight and 8 previous departures) showed the extension strap not being used during boarding, it is evident that its non-use for the occurrence flight was not an isolated event by a single pilot.
Propeller strap condition
The propeller straps designed and supplied by the aircraft manufacturer included a streamer to aid visibility. However, the propeller strap that was provided for the occurrence aircraft did not have a streamer attached. The presence of a ‘remove before flight’ streamer would have increased the likelihood of the FO, captain and dispatcher noticing the propeller strap prior to departure.
Link’s subsequent investigation found variations in the condition of propeller straps within the Saab 340B fleet. The missing, discoloured or damaged streamers that were still in service would have reduced the likelihood of flight crew and dispatchers seeing and removing these propeller straps. Similarly, the straps with faded or discoloured webbing would have been more difficult to see against black propeller blades. This evidence indicates that the condition of propeller straps within Link’s Saab 340B fleet was not effectively managed, increasing the risk to associated flights.
Dispatchers not familiar with propeller straps or propeller dressing
The training material that Link provided to Swissport for dispatcher training did not include any specific requirements for dispatchers to check for propeller straps or the strap extension. Link’s ground handling manual only noted ‘prop straps’ as an item the flight crew fitted to the cabin door prior to disembarkation. The material did not include any further description of the propeller strap or its function and usage by Link. There was also no information regarding Link’s use of a strap extension, which was used by some operators for Saab 340B aircraft. Consequently, the Swissport trainers (and therefore the dispatchers that were trained) would not necessarily have been familiar with flight crew procedures regarding the propeller strap and strap extension. This would have reduced the effectiveness of dispatchers to notice departures from procedure such as a propeller strap not being removed, or a strap extension not being fitted before boarding.
A trainer thought that the strap extension was permanently connected to the propeller strap. Since the cabin door would not be closeable while the strap extension was connected, it would be reasonable for dispatchers to believe that there was no need for them to look for a propeller strap, since the attached strap extension would prevent the flight from proceeding. Beyond guidance on looking for broad problems like ‘remove before flight’ streamers on the landing gear or flight data sensors, dispatchers would not know to look for attached propeller straps during the dispatch process.
Training material from Link did not mention propeller dressing, or the significance of a propeller in the ‘T’ position (indicating the strap was attached) versus one in the ‘X’ position (free to spin). Training dispatchers to ensure propellers were in the correct orientation would provide an additional, albeit indirect, method of checking for the presence of a propeller strap.
Swissport dispatcher procedures and training
Under the ground handling agreement in place between Swissport and Virgin, and by extension between Swissport and Link, dispatches of Link aircraft were to be carried out in accordance with Link’s instructions. In the absence of such instructions, the agreement stated that Swissport was to ‘apply its own standard practices and procedures.’ Similarly, Swissport’s GOM stated that it applied ‘wherever a client does not have specific procedures relating to the tasks being carried out.’
Link provided Swissport with information for the training of dispatchers to provide ground handling services for Link Saab 340B aircraft. Regarding walk-arounds, there was no detailed procedure provided for dispatchers, although a training checklist provided by Link included the need for a ‘final walk-around’ to ‘confirm … that all doors and other opening[s] are closed flush.’ A Swissport trainer reported they were told by Link staff that walk-arounds were the duty of the flight crew, not the dispatcher. However, the training material provided by Link was for aircraft ramping and dispatch duties, not flight crew duties. The training information provided by Link did not provide any detail relating to propeller straps or their use.
In its investigation report into the occurrence, Swissport stated that a dispatcher walk-around was not required since no standard operating procedure for a dispatcher walk-around had been provided by Link. However, both the Standard ground handling agreement (SGHA) and Swissport’s GOM stated that Swissport’s procedures should be applied in the absence of ‘instructions’ or a ‘specific procedure’ from Link.
If this were to be the case, Swissport’s GOM stated that a walk-around was required for all aircraft dispatches, which was to be a check around the entire aircraft perimeter immediately prior to departure. On the other hand, if Link’s instructions had clearly specified that Swissport staff were not to conduct a walkaround, then complying with this would be consistent with the GOM.
Regardless of obligations under the SGHA, Swissport’s GOM strongly emphasised the need for a dispatcher walk-around, and the walk-around prescribed had more detail than in the training material Link provided. In contrast to Swissport GOM procedures, the training actually given to Swissport ground staff did not require a full-perimeter walkaround, and only required them to observe flight crew moving from the cargo bay door into the cabin, to ensure that doors and hatches were flush with the fuselage, and to ensure that the pogo stick was stowed. CCTV footage from Canberra Airport confirmed that a full-perimeter walk-around was not generally done. Including a complete dispatcher walk-around in the dispatch process would provide a second check that nothing critical has been missed before departure.
It is important to note that in this occurrence, since the GOM did not mention propeller straps, it is not certain that the dispatcher would have noticed the strap if Swissport’s full-walkaround had been implemented.
Audits can be an effective method to detect non-compliance with standard procedures and training. In this case, dispatch audits were conducted by the same Swissport personnel that conducted the dispatcher training. These audits might have been sufficient to prevent dispatchers deviating from the training, but it is not likely that they would detect when the training (and dispatcher actions) deviated from Swissport’s GOM or, more importantly, from the operator’s specific requirements.
Flight crew not informed of fuselage penetration
After realising that an object had penetrated the fuselage, the CM did not inform the flight crew immediately, because this would disrupt the sterile flight deck. Link’s Cabin crew operating manual (CCOM) required cabin crew members to inform flight crew of cabin emergencies as an immediate priority, even with sterile flight deck procedures in place. However, the time between the occurrence (at around the time the aircraft became airborne) and the CM contacting the flight deck (25 seconds after take-off) was not unreasonable, given the unexpected nature of the occurrence, and there being no apparent critical danger requiring an immediate response.
After this, however, the CM spoke to the flight crew several times but did not communicate the nature of the emergency (primarily being an object that had penetrated the fuselage) and this type of information was not sought by the flight crew. This left the flight crew under the impression that the emergency related only to the medical condition of a passenger, rather than the state of the aircraft. In accordance with the CCOM, cabin crew were required to ensure flight crew were made aware of the nature of an emergency or abnormal situation as soon as was practical.
Based on the understanding that a passenger was injured, the flight crew responded quickly and appropriately, returning the aircraft to Canberra Airport. In this case, the flight crew would likely not have done anything differently if they had known more about the nature of the emergency. However, the CM had no way of knowing whether there was unidentified damage to the propeller or engine, which could be anticipated if the debris is recognised as being from a propeller strap. The CM also would not have been able to identify damage to other systems, which is a reasonable possibility when any object penetrates the fuselage. If unidentified damage had occurred, the flight crew’s response to any consequential events would have been affected by their assumption that the emergency was not related to the aircraft itself.
Findings
ATSB investigation report findings focus on safety factors (that is, events and conditions that increase risk). Safety factors include ‘contributing factors’ and ‘other factors that increased risk’ (that is, factors that did not meet the definition of a contributing factor for this occurrence but were still considered important to include in the report for the purpose of increasing awareness and enhancing safety). In addition ‘other findings’ may be included to provide important information about topics other than safety factors. Safety issues are highlighted in bold to emphasise their importance. A safety issue is a safety factor that (a) can reasonably be regarded as having the potential to adversely affect the safety of future operations, and (b) is a characteristic of an organisation or a system, rather than a characteristic of a specific individual, or characteristic of an operating environment at a specific point in time. These findings should not be read as apportioning blame or liability to any particular organisation or individual. |
From the evidence available, the following findings are made with respect to the aircraft preparation and foreign object damage event involving Saab 340B VH-VEQ at Canberra Airport, Australian Capital Territory, on 10 November 2022.
Contributing factors
- The aircraft was released for flight with the propeller strap still attached to the left propeller. Parts of the strap assembly subsequently penetrated the fuselage during take-off, injuring one passenger.
- The first officer did not remove the propeller strap as part of the final external check (walk‑around) of the aircraft.
- The captain did not notice the propeller strap or the incorrect propeller position prior to engine start.
- The dispatch coordinator did not notice the propeller strap or, during the engine start, the unusual propeller motion.
- On one-third of the Link Airways Saab 340B flights for which video surveillance was examined, including the occurrence flight, the flight crews did not fit the strap extension between the propeller strap and the airstairs. As the cabin door could not be closed with the strap extension in place, its correct fitment would almost certainly prevent a flight from proceeding with a propeller strap fitted. (Safety issue)
- The propeller strap did not have a high-visibility streamer attached, and Link Airways did not effectively manage the condition of propeller straps for its Saab 340B fleet. This affected the visibility of the straps during ground operations. (Safety issue)
- Guidance provided by Link Airways for training of Swissport dispatch coordinators did not explain the appearance, function and importance of the propeller straps. (Safety issue)
Other factors that increased risk
- Swissport did not ensure that the implemented training and audits for Link Airways Saab 340B dispatches incorporated all of the elements required in its Ground operations manual for pre-departure walk-arounds. (Safety issue)
- The cabin manager did not tell the flight crew that an object had penetrated the fuselage. While this had no bearing on the outcome, it limited the information available to the flight crew if aircraft systems had been damaged.
Safety issues and actions
Depending on the level of risk of a safety issue, the extent of corrective action taken by the relevant organisation(s), or the desirability of directing a broad safety message to the aviation industry, the ATSB may issue a formal safety recommendation or safety advisory notice as part of the final report. All of the directly involved parties were provided with a draft report and invited to provide submissions. As part of that process, each organisation was asked to communicate what safety actions, if any, they had carried out or were planning to carry out in relation to each safety issue relevant to their organisation. Descriptions of each safety issue, and any associated safety recommendations, are detailed below. Click the link to read the full safety issue description, including the issue status and any safety action/s taken. Safety issues and actions are updated on this website when safety issue owners provide further information concerning the implementation of safety action. |
Strap extension not always fitted
Safety issue number: AO-2022-055-SI-01
Safety issue description: On one-third of the Link Airways Saab 340B flights for which video surveillance was examined, including the occurrence flight, the flight crews did not fit the strap extension between the propeller strap and the airstairs. As the cabin door could not be closed with the strap extension in place, its correct fitment would almost certainly prevent a flight from proceeding with a propeller strap fitted.
Propeller strap deterioration
Safety issue number: AO-2022-055-SI-02
Safety issue description: The propeller strap did not have a high-visibility streamer attached, and Link Airways did not effectively manage the condition of propeller straps for its Saab 340B fleet. This affected the visibility of the straps during ground operations.
Link training guidance lacked details regarding propeller straps
Safety issue number: AO-2022-055-SI-03
Safety issue description: Guidance provided by Link Airways for training of Swissport dispatch coordinators did not explain the appearance, function and importance of the propeller straps.
Swissport training and audits
Safety issue number: AO-2022-055-SI-04
Safety issue description: Swissport did not ensure that the implemented training and audits for Link Airways Saab 340B dispatches incorporated all of the elements required in its Ground operations manual for pre‑departure walk-arounds.
Safety action not associated with an identified safety issue
Whether or not the ATSB identifies safety issues in the course of an investigation, relevant organisations may proactively initiate safety action in order to reduce their safety risk. All of the directly involved parties are invited to provide submissions to this draft report. As part of that process, each organisation is asked to communicate what safety actions, if any, they have carried out to reduce the risk associated with this type of occurrences in the future. |
Additional safety action by Link Airways
In addition to the safety action described above, Link Airways took the following safety action:
- The Cabin crew operating manual was amended to provide additional clarity regarding the need for the cabin manager to contact the flight crew in the event of an emergency.
- A risk assessment was conducted for the potential adoption of an intercom system between pilot and dispatcher, in order to improve communication (on the basis of this risk assessment, such a system was not implemented).
Additional safety action by Swissport
In addition to the safety action described above, Swissport planned to review its Ground operations manual regarding positioning of the dispatcher.
Glossary
CCTV | Closed-circuit television |
CCOM | Cabin crew operating manual |
CM | Cabin manager |
FCOM | Flight crew operating manual |
FO | First officer |
GOM | Ground operations manual |
SATGHM | Scheduled air transport ground handling manual |
SGHA | Standard ground handling agreement |
Sources and submissions
Sources of information
The sources of information during the investigation included:
- the flight crew, cabin manager, dispatcher, and dispatch trainers
- Link Airways
- Virgin Australia
- Swissport
- Saab
- Canberra Airport
- the Civil Aviation Safety Authority
- aircraft cockpit voice recorder and flight data recorder.
Submissions
Under section 26 of the Transport Safety Investigation Act 2003, the ATSB may provide a draft report, on a confidential basis, to any person whom the ATSB considers appropriate. That section allows a person receiving a draft report to make submissions to the ATSB about the draft report.
A draft of this report was provided to the following directly involved parties:
- captain, first officer, cabin manager, and dispatcher
- dispatch trainers
- Link Airways
- Virgin Australia
- Swissport
- Civil Aviation Safety Authority
- Saab
- Swedish Accident Investigation Authority.
Submissions were received from Link Airways and Swissport.
The submissions were reviewed and, where considered appropriate, the text of the report was amended accordingly.
Purpose of safety investigationsThe objective of a safety investigation is to enhance transport safety. This is done through:
It is not a function of the ATSB to apportion blame or provide a means for determining liability. At the same time, an investigation report must include factual material of sufficient weight to support the analysis and findings. At all times the ATSB endeavours to balance the use of material that could imply adverse comment with the need to properly explain what happened, and why, in a fair and unbiased manner. The ATSB does not investigate for the purpose of taking administrative, regulatory or criminal action. TerminologyAn explanation of terminology used in ATSB investigation reports is available here. This includes terms such as occurrence, contributing factor, other factor that increased risk, and safety issue. Publishing informationReleased in accordance with section 25 of the Transport Safety Investigation Act 2003 Published by: Australian Transport Safety Bureau © Commonwealth of Australia 2024 Ownership of intellectual property rights in this publication Unless otherwise noted, copyright (and any other intellectual property rights, if any) in this report publication is owned by the Commonwealth of Australia. Creative Commons licence With the exception of the Coat of Arms, ATSB logo, and photos and graphics in which a third party holds copyright, this publication is licensed under a Creative Commons Attribution 3.0 Australia licence. Creative Commons Attribution 3.0 Australia Licence is a standard form licence agreement that allows you to copy, distribute, transmit and adapt this publication provided that you attribute the work. The ATSB’s preference is that you attribute this publication (and any material sourced from it) using the following wording: Source: Australian Transport Safety Bureau Copyright in material obtained from other agencies, private individuals or organisations, belongs to those agencies, individuals or organisations. Where you wish to use their material, you will need to contact them directly. |
[1] This inspection was a ‘Line Check 1’ (or LC1) daily inspection.
[2] Also referred to as a prop (propeller) strap extension.
[3] Airstairs are a passenger and crew stairway that form an integral part of the aircraft and, after use, are hinged up and stowed on board.
[4] A ground handling person who coordinates and performs various activities during dispatch. In this case, the role did not have any direct regulatory or airworthiness responsibilities.
[5] The core engine speed can differ from the propeller speed, as the two are not mechanically linked. When the engine is running, the exhaust flow exerts a rotational force on the propeller via a turbine.
[6] Sterile cockpit procedures are part of the Civil Aviation Safety Regulations and require pilots to only perform duties essential to the aircraft’s safety during certain critical phases of flight, including take-off.
[7] Stringers are structural components that run the length of an aircraft fuselage.
[8] After the prop straps are removed, the propeller is to be moved to the ‘X’ position with the blades at a 45° angle. See Use and stowage.
[9] The tail strut, or ‘pogo stick’ supports the tail of the aircraft during loading/unloading and refuelling. It is stowed in the cargo bay of Saab 340B aircraft.