Executive summary
What happened
On 6 February 2023 at about 1532 local time, a Coulson Aviation Boeing 737-3H4 large air tanker (LAT), callsign Bomber 139 and registered N619SW, departed from Busselton Airport, Western Australia (WA) on a firefighting task to Fitzgerald River National Park, WA. There were 2 pilots on board, the aircraft captain in the left seat as the pilot flying and a co‑pilot in the right seat as the pilot monitoring. At about 1614, during the go-around from a second partial retardant drop, the aircraft impacted a ridgeline at an elevation of about 222 ft. The pilots suffered minor injuries and the aircraft was destroyed.
What the ATSB found
The ATSB found that the accident drop was conducted at a low height and airspeed downhill, which required the use of idle thrust and a high descent rate. The delay in the engines reaching go-around thrust at the end of the drop resulted in the aircraft’s height and airspeed (energy state) decaying as it approached rising terrain, which was not expected or detected by the pilot flying. Consequently, the aircraft’s airspeed and thrust were insufficient to climb above a ridgeline in the exit path, which resulted in a controlled flight into terrain. The operator’s practice of recalculating, and lowering, their target drop speed after a partial load drop also contributed to the low energy state of the aircraft leading up to the collision with terrain.
The ATSB also found that the operator and tasking agency had not published a minimum drop height, which resulted in the co-pilot, who did not believe there was a minimum drop height, not making any announcements about the low energy state prior to the collision. The ATSB found the operator’s pilot monitoring duties were reactive to the development of a low energy state and did not include call-outs either before or at the minimum target parameters to reduce the risk of a low energy state developing.
The ATSB benchmarked the WA, New South Wales and National Aerial Firefighting Centre standards against the United States Forest Service and United States National Wildfire Coordinating Group standards and found inconsistencies between the Australian agencies’ standards but not among the United States agencies’ standards. This was likely a result of each Australian state participating in the LAT program independently producing their own standards.
What has been done as a result
As a result of this accident, the operator developed a master corrective action plan to address the following topics:
- minimum drop speed and height
- recalibration of airspeed during partial load drops
- pre-drop planning and familiarisation
- pilot situational awareness
- flight training exercises
- exit flight path
- communication and coordination with Birddog
- adherence to standard operating procedures
- crew resource management
- human factors
- continuous training and proficiency assessment.
The Birddog operator reported that as part of their continuous improvement they removed their Lead Plane procedures from an annex in their Company Operations Manual and introduced a Lead Plane Standard Operating Procedures manual with expanded procedures in October 2023.
In November 2023, the WA Department of Fire and Emergency Services, and Department of Biodiversity, Conservation and Attractions released the Western Australian Aerial Fire Suppression Procedures 2023-2024. The draft version of this document was reviewed by their contracted operators and included a chapter for Large Air Tanker (LAT) Operating Procedures. The document included standard drop heights for all the aircraft types employed, procedures for task rejection, standdown and reinstatement of aviation resources after a safety incident, and a section on tactical flight profiles with the addition of the Lead and Chase-Position profiles.
In response to the draft report, the WA Department of Biodiversity, Conservation and Attractions reported they would review the 2024–25 published drop heights with the intent of prescribing a ‘minimum’ safe drop height, noting the actual drop height to safely achieve the objective is the pilot-in-command’s decision.
In response to the draft report, the Australasian Fire and Emergency Services Authorities Council committed to develop a national standard for LAT Operating Procedures. This was delegated to the Aviation Safety Group through the National Aerial Firefighting Centre Strategic Committee within the purview of the Consistent Doctrine working group.
Finally, the ATSB has issued a safety recommendation to Coulson Aviation to take safety action to address their crew resource management procedures for retardant drops to reduce the risk of the aircraft entering an unrecoverable state before the pilot monitoring alerts the pilot flying.
Safety message
The history of aerial firefighting includes collisions with terrain accidents during the descent, retardant (or water) drop and go-around that have primarily manifested as controlled flight into terrain and loss of control accidents. The history of accidents needs to be understood within the context of the effect of drop height and speed on the firefighting effort, and the environmental conditions at the fireground, which may lead to an elevated level of risk tolerance.
The lessons from this accident indicate that standard operating procedures and crew resource management should be implemented with the intent to prevent an unsafe situation from developing. While they should also include recovery actions, there may be insufficient safety margin available for a successful recovery and therefore the safety standards should not be solely dependent on the performance of the pilot flying and recovery call-outs.
At a large fireground, it is likely there will be personnel and assets from multiple organisations and jurisdictions interacting. In this scenario, non-standard procedures and practices may result in unforeseen risks emerging. It is therefore important for tasking agencies to take the lead, with the support of stakeholders, in developing the quality and safety standards they require for the firefighting effort to mitigate operational risks.
The occurrence
On 6 February 2023 at about 1532 local time, a Coulson Aviation Boeing 737-3H4 large air tanker (LAT), callsign Bomber 139 and registered N619SW, departed from Busselton Airport, Western Australia (WA) on a firefighting task to Fitzgerald River National Park, WA (Figure 1). There were 2 pilots on board, the aircraft captain in the left seat as the pilot flying and a co‑pilot in the right seat as the pilot monitoring.[1]
Figure 1: Bomber 139 flightpath from Busselton to Fitzgerald River National Park
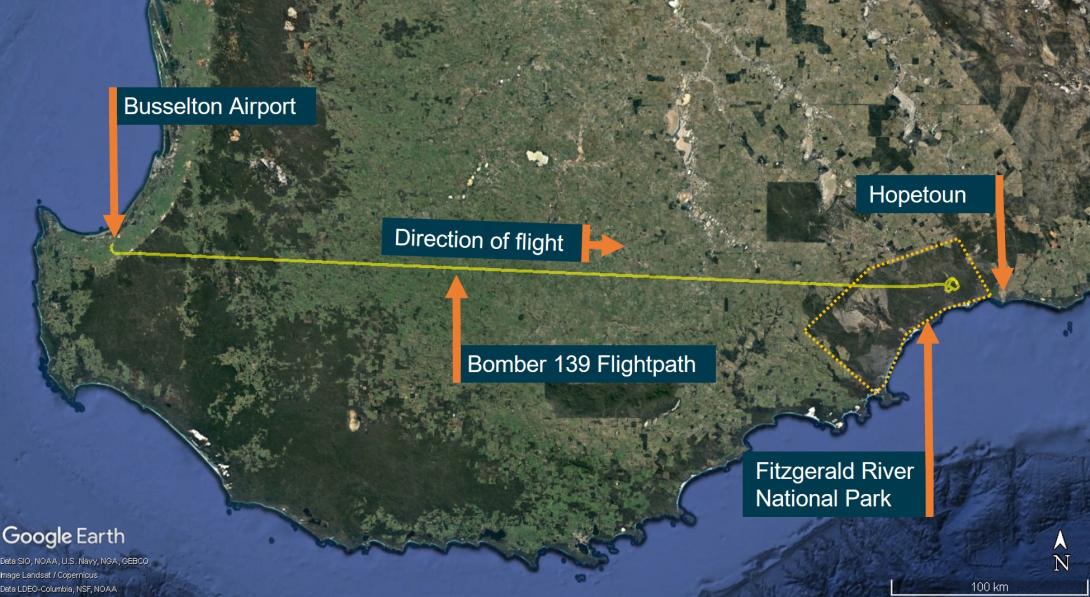
Source: FlightAware, annotated by ATSB
Earlier in the day, at 1015, and then again at 1215 and 1310, the WA Department of Biodiversity, Conservation and Attractions (DBCA) submitted aerial fire suppression requests to the State Operations Air Desk (SOAD). The request was for fixed-wing assets to the location of a fire 24 km west-north‑west of Hopetoun, WA under the criteria of ‘known high fuel loads and likelihood of excessive ROS [rate of spread] and/or extreme fire danger’. In response, the SOAD:
- identified the aerial assets available
- established a fire common traffic advisory frequency (F-CTAF)
- spoke to the pilots
- sent tasking messages at 1012, 1127, 1407 and 1505.
Bomber 139 was included in the 1127, 1407 and 1505 taskings. The SOAD LAT SARWATCH log[2] recorded that Bomber 139 departed from Busselton on these taskings at 1208 and 1330 and returned to Busselton each time before departing on the accident flight at 1530.
At 1519 the Birddog[3] (BD) responsibility for the LATs at the fireground transferred from Birddog 125 (BD125) to Birddog 123 (BD123) due to BD125 refuel requirements, with Birddog 682 (BD682) stationed above as the primary air attack aircraft.[4] Before BD125’s departure, a familiarisation flight of the fire zone was conducted in company with BD123 to discuss the layout of the fire, tactics, retardant drops, and objectives for the drops. The pilot of BD123 reported that no hazards were discussed. Bomber 139’s captain contacted BD123’s crew when they were 15 minutes from the fireground, and the Birddog pilot acknowledged their call and advised an altimeter QNH[5] setting of 1003 hPa. The captain acknowledged the altimeter setting and informed BD123’s pilot they would contact BD682 when they were 5 minutes from the fireground.
The pilot of BD682 subsequently cleared Bomber 139 to enter the F-CTAF not above an altitude of 2,500 ft and the captain notified BD682 they would be working with BD123 on an altimeter setting of 1003. The crew of BD123 queried BD682 if the line was clear and were advised that no ground personnel had been sighted and that they were not expected for about another hour. At this stage, Bomber 139’s co-pilot advised the captain of their drop speeds, which included a target drop speed (VDROP) of 133 kt (1.25 Vs[6]).[7] When the captain reported BD123 in sight, the Birddog pilot asked Bomber 139 if they wanted a Show-Me[8] run or to follow BD123 straight to the drop, which would be a Lead profile.[9] The captain responded that they would follow BD123 straight to the drop. BD123’s pilot then obtained confirmation from the captain that right-hand circuits would be acceptable to avoid reduced visibility in smoke.
BD123’s pilot briefed Bomber 139 that the plan was to use a road (Figure 2) as the start point and tag and extend the existing line of retardant, while keeping the smoke off to the left side, and that the line for the drop was clear of ground personnel. Bomber 139’s captain subsequently reported to BD123 that they were in position and the captain called for the co-pilot to complete the pre-drop checklist, which included:
- confirming coverage level[10] 3 was set
- disconnecting the autothrottles
- arming the retardant aerial delivery system.
The captain notified BD123 that their target speed would be 135 kt for final and then set the flaps to flap-40 (full flap). BD123’s crew then briefed Bomber 139 on the drop, which included advice of:
- a straight exit
- no hazards
- a downhill approach
- target altitude initially of 500 ft descending to 400 ft.
Bomber 139’s co-pilot subsequently reported to the captain that the checklist was complete. The captain then queried the co-pilot about the flightpath BD123 was leading them on to the target and commented that their approach appeared to be high.
BD123’s pilot reported turning onto final for the drop, which was on a heading of 155º, and that visibility would be good after they cleared the smoke. About 15 seconds later, the captain queried the co-pilot where the road was for the start of the drop and the co-pilot responded that it was just ahead of them. BD123’s pilot then briefed Bomber 139 to ’start at the road and keep all smoke to the left, 3, 2, 1, start, your target altitude is 500 descending to 400’. The captain then confirmed sighting the road.
Bomber 139 descended to a minimum height[11] of 78 ft and completed a 9-second partial drop[12] of three-quarters of their tank at about 70% N1[13] with a minimum computed airspeed[14] of 124 kt before the captain stopped the drop because their retardant line was starting to enter area that was already burnt. The captain reported the partial drop to BD123, and another Lead profile was set up to tag and extend the first drop with the remaining retardant, with the captain remarking to the crew of BD123 ‘…and head down off the hill’.
The captain instructed the co-pilot to conduct the pre-drop checklist for the second drop and the co‑pilot recalculated and reported that 118 kt would be their revised drop speed. On the second circuit the captain again queried the co-pilot about the flightpath they were taking to the final approach. The captain requested BD123 slow to 120 kt for the next drop, which was acknowledged. The Birddog pilot then briefed Bomber 139 to ‘tag and extend all existing retardant, it is start at the hill as it pushes down, target altitude 500 descending 400’.
The co-pilot reported that flap-40 was set, and the pre-drop checklist was completed. The captain again reported uncertainty to the co-pilot about the approach path BD123 was taking. The Birddog pilot then provided the following commentary, ‘this is final, fully retardant drop out here in a second, standby, [pause], retardant’s right at our 12 o’clock, [pause], 3, 2, 1, tag and extend existing retardant’. The captain reported at interview that the second approach was conducted through drift smoke from the fire, and they were unable to identify the target until they exited from the smoke, which was at the start of the drop. The co-pilot reported not being able to see the target on final until BD123 deployed smoke over the location.
During the second drop, Bomber 139 descended to a minimum height of 57 ft at 110 kt and about 30% N1 (engines at high idle)[15] as the retardant line was extended downhill. The aircraft recovered to a height of 81 ft at 107 kt at the end of the drop at which stage the captain had started to advance the thrust levers as the rate of descent peaked at about 1,800 ft/min. The co‑pilot had their hand on the flap lever in anticipation of the flap retract call from the captain as soon as they started to climb for the go-around.
The engines did not immediately respond to the movement of the thrust levers and the captain started to pitch the nose up, which resulted in a reversal of the rate of descent and a decay of the airspeed. The captain then announced ’fly airplane’ followed immediately, at about 1614,[16] by the activation of the stick shaker[17] and an abrupt vertical acceleration associated with the aircraft impacting a ridgeline at an elevation of about 222 ft at 104 kt with the engines at 85–89% N1.
The co-pilot did not announce any deviations during the drop and accident sequence and later reported their focus of attention was likely on the airspeed indicator and radio altimeter, monitoring for any adverse trends. After the impact with the ridgeline, the aircraft cleared a small line of foliage before impacting the ground a second time and then sliding to rest (Figure 2). In response to the collision, BD123’s pilot broadcast an all-stations MAYDAY[18] call.
Figure 2: Bomber 139 retardant drops and accident site
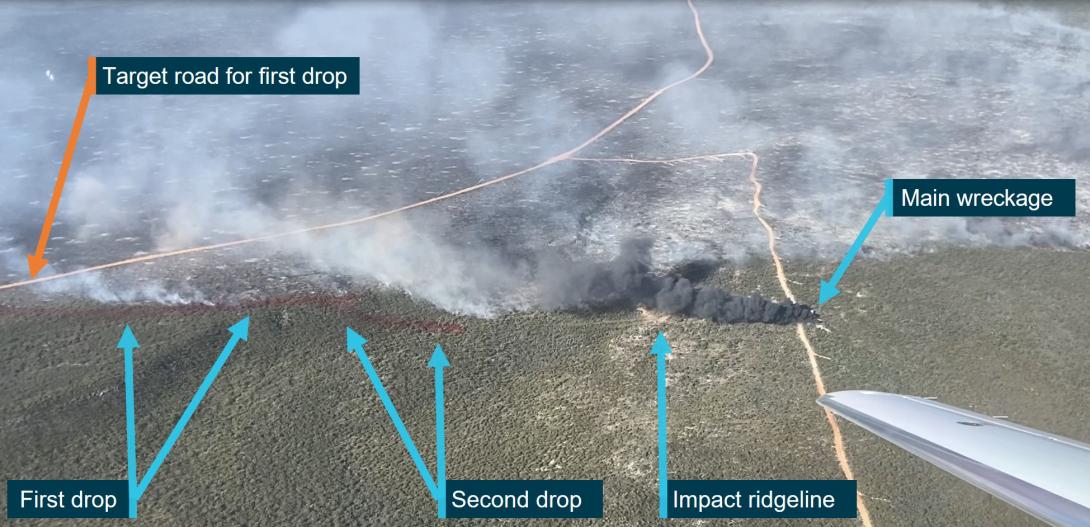
Source: Department of Fire and Emergency Services, annotated by ATSB
After motion had ceased, the co-pilot started the evacuation checklist. Both pilots were unable to open the cabin door as it had buckled and the co-pilot was unable to open the right-side window. The captain observed out of the left side window that a post‑impact fire had started and managed to open that window on their second attempt. Both pilots then exited out of the left window and moved clear of the wreckage and fire. They were subsequently rescued by a helicopter involved in the fire control activities after 2 single-engine air tankers had dropped water with foam on the aircraft fire, believing the crew were still inside. The crew suffered minor injuries and the aircraft was destroyed. Figure 3 depicts Bomber 139’s recorded accident flightpath.
Figure 3: Bomber 139 recorded accident flightpath at Fitzgerald River National Park
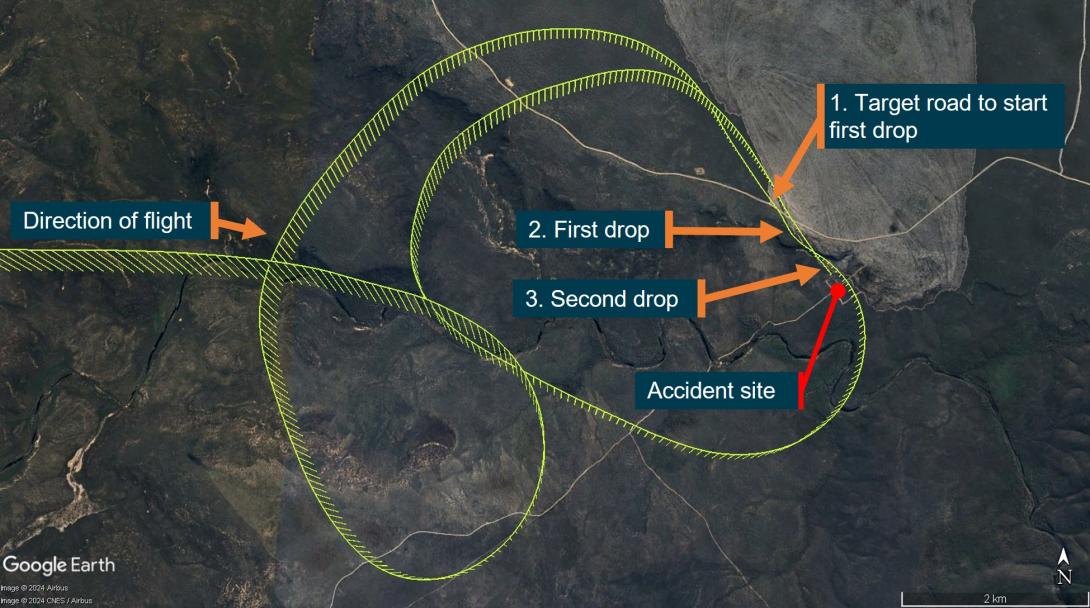
Source: Google Earth, annotated by ATSB
Context
Personnel information
Aircraft captain
The aircraft captain joined the operator, Coulson Aviation, in 2016 with a United States Department of Agriculture Forest Service (USFS) Air Tanker Training Pilot qualification. The captain became their director of fixed-wing operations in 2017, having flown several multi-engine airtanker types over about 20 years. The captain held an airline transport pilot certificate, reissued by the US Federal Aviation Administration (FAA) on 6 October 2020 with a rating for Boeing 737 (B737) and a current first class medical certificate with no limitations. The captain had accumulated 8,233 hours of flying experience, which included 1,399 hours on the B737 and about 5,500 hours aerial firefighting experience. In the previous 90 days the captain had accumulated 84 hours, all on the B737.
The captain’s last pilot-in-command proficiency check on the B737 (in accordance with the FAA regulations) was on 30 November 2022, with a satisfactory result. The captain conducted 2 company check flights on 11 May 2022, which were simulated initial attack mission training flights for a new co-pilot. These flights were part of the operator’s annual northern hemisphere spring season training program. Both reports indicated no assistance was required and no deficiencies were recorded.
Co-pilot
The co-pilot joined Coulson Aviation on 18 April 2022 with prior aerial firefighting experience flying the air tactical group supervisor, but no previous low flying or large air tanker (LAT) experience. The co-pilot attended the operator’s 2022 spring season ground training and occupied the jump seat as an observer in the B737 for the flying training. Between 1–7 June 2022, the co-pilot completed a B737 type rating course with a satisfactory result recorded for the check on 7 June 2022. The co-pilot was issued with their USFS qualification on completion of their B737 type rating, which was an administrative process for co-pilots and did not require an evaluation flight.
The co-pilot held an airline transport pilot certificate, reissued by the FAA on 7 June 2022, with a rating for B737 and a current first class medical certificate with no limitations. On 12 September 2022, the co-pilot participated in an initial attack evaluation flight as the co-pilot on the B737. The co-pilot had accumulated 5,852 hours of flying experience, which included 128 hours on the B737, about 500 hours aerial firefighting experience and 36.9 hours on the B737 in the previous 90 days.
Crew work-rest history
The captain reported they had 6 and 14 hours sleep in the previous 24 and 48 hours respectively. They self‑assessed that their level of mental fatigue at the time of occurrence was 2 - Very lively. Responsive, but not at peak.[19] The co-pilot reported they had 8 and 18 hours sleep in the previous 24 and 48 hours respectively and a self‑assessed mental fatigue level at the time of occurrence of 2 - Very lively. Responsive, but not at peak.
The crew’s tour of duty started on 20 January 2023. They had flown 7.3 hours and conducted 13 drops (including partial drops) on the current tour prior to the day of the accident. The accident occurred on their third flight and fourth retardant drop of the last day of their tour after flying about 3.3 hours that day. The pilots’ self-assessments and work-rest history did not indicate that mental and physical fatigue were likely to have been contributing factors to the accident.
Aircraft information
General information
The aircraft was a Boeing 737-3H4, serial number 28035, registration N619SW, issued with a certificate of airworthiness in the transport category[20] by the FAA on 9 November 1995 and fitted with 2 CFM56-3 turbofan engines. It entered service with a US airline on 12 November 1995 and accumulated 69,016 hours before transfer of ownership to Coulson Aviation on 8 August 2017. The latest certificate of registration was issued on 14 November 2017 and was valid until 30 November 2023.
Tanker modification
On 10 November 2018, Coulson Aviation were issued with a supplemental type certificate (ST04050NY) by the FAA for the installation of the Coulson Aerial Firefighter Tanker Modification (retardant aerial delivery system – RADS) to Boeing model 737-300 series aircraft, which limited passengers to persons related to firefighting mission‑essential activities. The RADS modification was completed on 30 May 2022. At the time of the accident, the airframe had accumulated 69,187.6 hours.
The RADS incorporated 2 tanks on either side of the centre fuel tank with a total capacity of 36,000 pounds (lb).[21] The cockpit had a primary and secondary user interface installed and push button drop switches on both the pilot and co-pilot controls. According to the flight manual supplement:
When the flight crew activates either switch, the primary user interface software will produce a door position command based on the predefined Coverage Level (CL) requirement, drop quantity, tank levels, ground speed and aircraft height above the ground.
The RADS design included an emergency dump switch that provided full system hydraulic pressure to dump the full load in less than 2 seconds. To avoid nuisance audio alerts during a retardant drop, the RADS modification incorporated an audio inhibit switch, which inhibited the landing gear configuration, ground proximity warning system and traffic collision avoidance system for 5 minutes.
Flight instruments
The captain and co-pilot instrument panels were fitted with radio altimeter indicators to display the aircraft height above terrain when below 2,500 ft above ground level. A decision height (DH) could be set on each of the radio altimeters, which activated a DH light on the respective attitude indicator when that height was reached, but did not include an audio alert.
The altimeters and airspeed indicators incorporated bugs that could be set to reference altitudes and airspeeds. The operator reported that the orange airspeed bug was used for the target drop speed. The altimeter bug was not used because the retardant drop was conducted at a height above terrain and not at an altitude. Figure 4 illustrates the co-pilot’s instrument panel with the radio altimeter DH set at 50 ft.
Figure 4: Co-pilot’s partial instrument panel
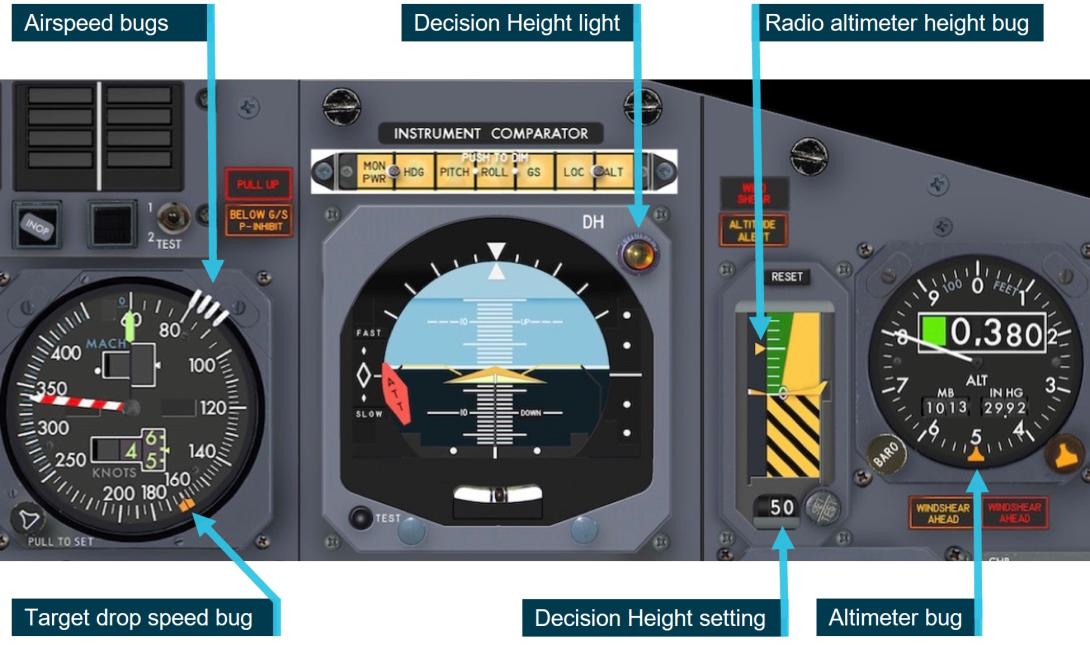
Source: Operator, annotated by ATSB.
Head-up guidance system
Under previous ownership, the aircraft was fitted with a Rockwell Collins flight dynamics model 2300 head-up guidance system (HGS) for the left seat pilot (captain’s seat), which was approved for use as a supplemental display. The HGS permitted the flying pilot to scan the airspeed and radio height, while maintaining an external visual scan of the environment during the retardant drop. Consequently, the captain reported that they considered the DH light on the instrument panel to be of no benefit while flying the retardant drop with the HGS.
The HGS had 4 modes of operation. All 4 modes could provide an airspeed error symbol, to indicate the difference between the aircraft’s actual airspeed and the reference airspeed set by the pilot on the mode control panel. A DH annunciation was also available in the mode used by the captain. The captain set the target drop speed on the mode control panel to provide a reference airspeed during the retardant drop but did not use the DH setting.
Boeing 737-300 engine acceleration requirements
According to the engine manufacturer, CFM (GE and Safran partnership):
An acceleration check is defined in Boeing 737-300/400/500 AMM Task 71-00-00-715-015-C00. This demonstration test requires the engine to accelerate from high idle to the fan speed corresponding to approximately 95% of static take-off thrust within 7.4 seconds.[22] The target fan speed is corrected for pressure altitude and outside air temperature. However, there are multiple factors that can impact the expected engine acceleration time during flight, including but not limited to:
- The 7.4-second requirement is for a rapid throttle movement (1 second or less) from idle to take-off power. Slower throttle movements may result in a longer acceleration time.
- The 7.4-second requirement is with engine bleeds and electrical loads OFF. Engine bleeds ON can extend the acceleration time.
- Mach number can impact the acceleration time, but an airspeed of 110 kts at low altitude would likely have an insignificant impact.
Meteorological information
On the day of the accident there was a low-pressure trough crossing southern WA, resulting in thunderstorms and wind direction changes from the north-east to the south-east to the south-west. The graphical area forecast for the accident site included moderate turbulence from the surface to 10,000 ft with thermals. A SIGMET[23] was issued at 1400 for frequent thunderstorms associated with the trough (Appendix A – SIGMET thunderstorm activity). While the north-western boundary of the SIGMET was close to the accident site, satellite and radar imagery indicated there were no thunderstorms in the vicinity of the accident site at the time of occurrence.
The Hopetoun North weather station, located about 24 km east‑north‑east of the site, did not record any rainfall and the 10-minute weather data from the station is provided in Table 1. With reference to Figure 2, the smoke from the fire and accident site indicated the retardant drops were conducted into wind, which the Bomber 139 captain reported was about 10–15 kt.
Table 1: Hopetoun North weather station recordings
Time (local) | Air temperature (ºC) | Dew point temperature (ºC) | Average 10-minute wind speed (kt) | Highest 10-minute wind speed (kt) | Average 10-minute wind direction | Rainfall in last 10 minutes (mm) |
1550 | 23.4 | 18.7 | 14.8 | 20.4 | ESE | 0 |
1600 | 23.2 | 18.7 | 14.0 | 19.6 | SE | 0 |
1610 | 23.1 | 18.6 | 11.6 | 17.1 | SE | 0 |
1620 | 23.4 | 18.7 | 11.4 | 15.0 | ESE | 0 |
1630 | 23.1 | 18.8 | 11.5 | 14.4 | SE | 0 |
1640 | 23.1 | 19.0 | 9.9 | 15.0 | SE | 0 |
Pre-flight risk assessment
The aircraft captain completed the operator’s flight risk assessment tool (FRAT) at 1015. The FRAT score was 14, which was an acceptable level of risk with no mitigation or escalation required. If the FRAT had been reviewed between each flight, the SIGMET issued at 1400 would have added 8 points, resulting in a FRAT score of 22 for the accident flight that departed from Busselton at about 1530.
A score greater than 21 required mitigation or escalation, noting the operator’s procedures prohibited an elevated FRAT from being approved by the aircraft captain. While the weather conditions, including the thunderstorm activity advised in the SIGMET, were not considered to be a factor in this accident, this has been included in the report to raise awareness of how a risk management process could miss a developing flight hazard.
Wreckage and impact information
The aircraft’s approach to the ridgeline left 2 distinct jet-blast lines, evidenced by trees broken in the opposite direction of travel (Figure 5). Closer to the ridgeline, trees were broken in the direction of travel, likely from contact with the aircraft’s engines and airframe with evidence of retardant transfer from the airframe to the foliage just below the ridgeline. The length of the jet‑blast lines were about 74 m and 62 m respectively for the left and right engines. After contacting the ridgeline, the aircraft became airborne for about 69 m, shedding engine, wing, and fuselage debris before impacting a second time in a slight nose down attitude on a heading of about 140º.
Figure 5: Jet-blast corridors and ridgeline impact
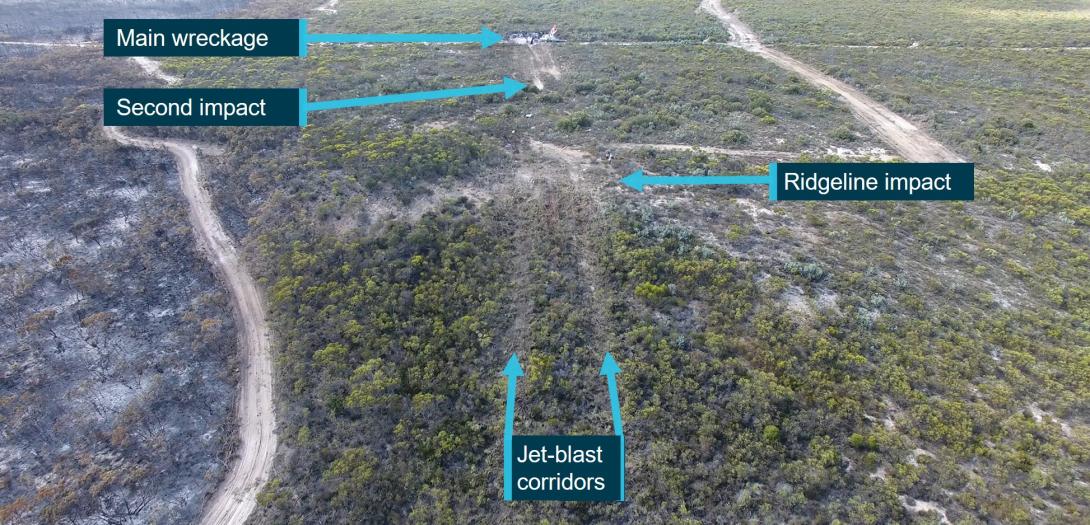
Bulldozer fire tracks constructed after the accident.
Source: ATSB
The aircraft came to rest about 176 m from the ridgeline and yawed left to the direction of travel onto a heading of about 080º. The fuselage had a main fracture near the tail and the left engine had separated from the left pylon and was resting adjacent to the forward fuselage (Figure 6). The left engine pylon exhibited a 70º upward bend, which was likely from the impact with the ridgeline, noting the left engine debris field started from the ridgeline and there was no evidence of left engine drag marks. The aircraft was consumed by fire, but there was no evidence of:
- fire trail[24] or fuel spill before the aircraft came to rest
- any debris separating from the aircraft before it impacted the ridgeline.
Figure 6: Second impact and main wreckage
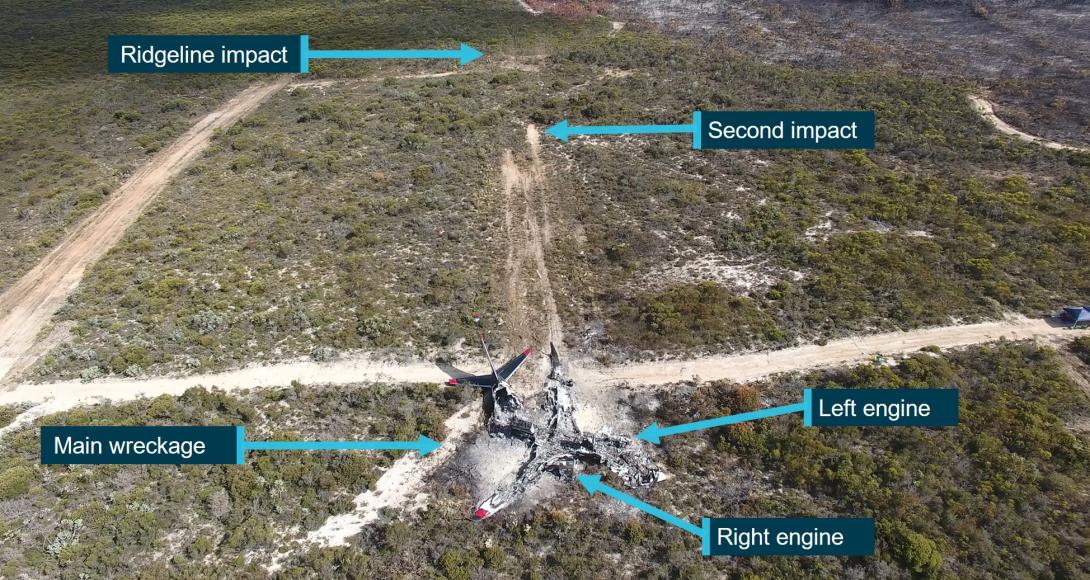
Bulldozer fire tracks constructed after the accident.
Source: ATSB
The flight data recorder (FDR) and cockpit voice recorder (CVR) were recovered on the first day of the site and wreckage inspection and retained by the ATSB for examination and download. Due to the extensive fire damage, only a limited inspection of the aircraft was achievable. This included establishing the positions of the leading-edge flaps, trailing-edge flaps, and horizontal stabiliser, with no anomalies found. The trailing-edge flap ballscrews were in the fully extended position, consistent with a flap-40 setting.
The left main landing gear was found adjacent to the aircraft and part of its support structure was in the debris field indicating it was torn from the aircraft prior to it coming to rest. The nose and right main landing gear were retracted in place. The extent of the fire damage precluded an inspection of the cockpit and flight instruments. Figure 7 depicts the horizontal distances and elevations (measured with a differential global positioning system), and the angles presented by the foliage damage associated with the accident sequence.
Figure 7: Accident sequence distances and elevations
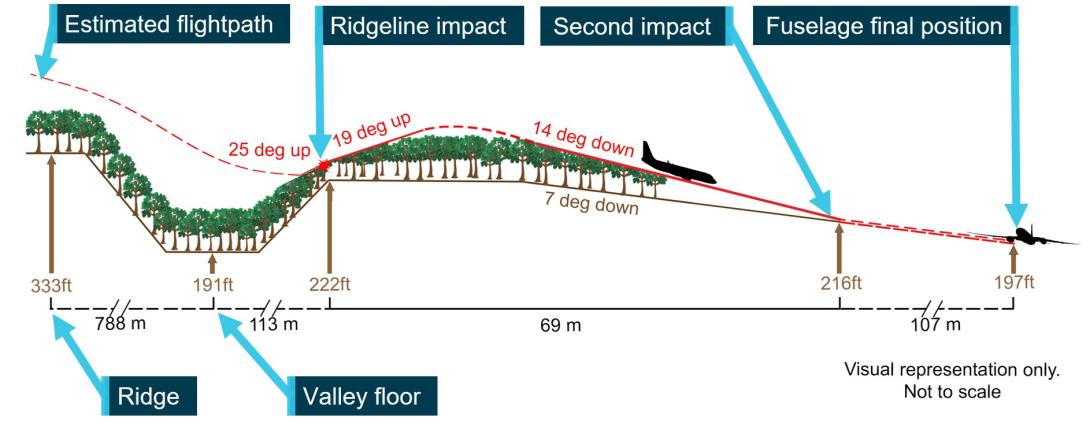
Source: ATSB
Recorded information
The CVR (Honeywell SSCVR P/N 980-6022-001) and FDR (Honeywell SSFDR P/N 980‑4700‑001) were transported by a recorders specialist from the accident site to the ATSB’s Canberra technical facility. The condition of the CVR prior to disassembly is depicted in Figure 8. The condition of the FDR prior to disassembly is depicted in Figure 9.
Figure 8: CVR prior to disassembly
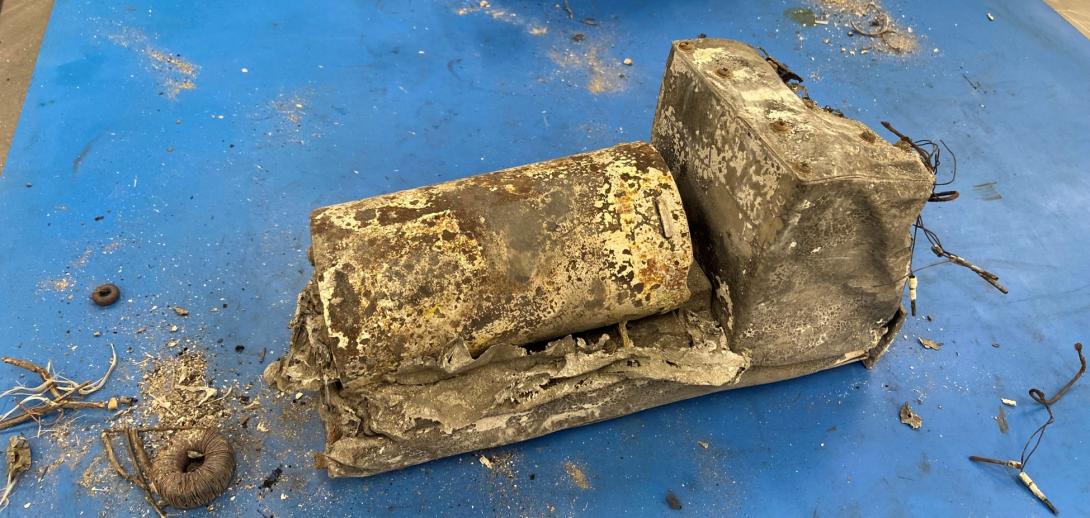
Source: ATSB
Figure 9: FDR prior to disassembly
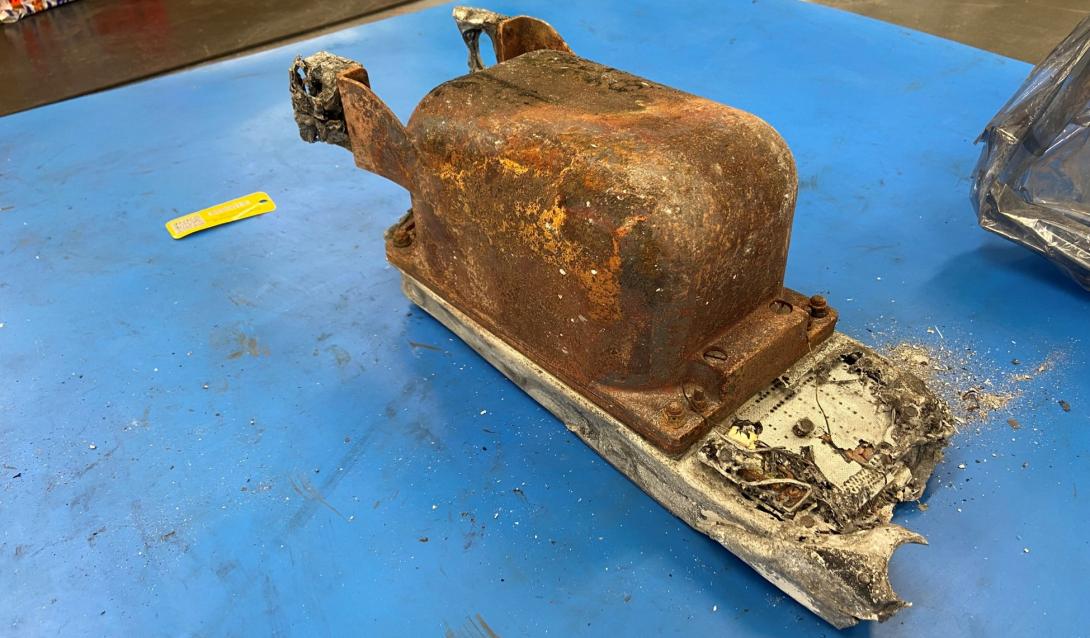
Source: ATSB
As a result of fire damage to the recorders the data recovery process required disassembly, inspection, and repair of the memory boards inside the crash survivable memory unit. The FDR memory board exhibited discoloration, melting and flow of the conformal coating with multiple controller pins desoldered. The CVR exhibited discoloration of the heat indicator, several controller pins had separated from the memory board and multiple short-circuits were identified.
Following repairs to both memory boards, successful downloads of data were achieved. The FDR provided 25.5 hours of flight data and the CVR 30 minutes of audio on 4 channels (pilot, co-pilot, public address, and cockpit area microphone). The FDR plot of the final 30 seconds before the impact with the ridgeline, with the approximate position of the accident retardant drop inserted, is shown at Figure 10. The time parameter in the figure (UTC)[25] is an approximate calculation based on the aircraft’s auxiliary telemetry unit global positioning system recording of the retardant drops. Appendix B contains the FDR plot of the last 5 minutes of flight with the 2 drops conducted on the accident flight.
During the final low-level retardant drop the thrust levers were positioned at high idle (0°) while at a radio height above the ground of less than 100 ft. As the engine N1 speed decreased to about 30%, the rate of descent increased to 1,800 ft/min before the thrust levers were advanced while the aircraft continued to descend. About 2 seconds prior to impact, at a radio altitude of about 28 ft with the flaps at 40°, an increasing aircraft nose-up pitch attitude resulted in both angle of attack vanes exceeding 20° (maximum 23.6°), which triggered the stick shaker. The aircraft attained a positive rate of climb just before impact with terrain.
Boeing provided the ATSB with a copy of their preliminary flight data analysis report of the accident, which was used to validate ATSB flight data output. Noting the aircraft attained a positive rate of climb with high engine N1 speed just prior to impact, Boeing reported in their preliminary findings that ‘Had there been sufficient altitude remaining, the airplane would have likely climbed away without impacting the ground.’
Figure 10: FDR plot of final 30 seconds of accident drop
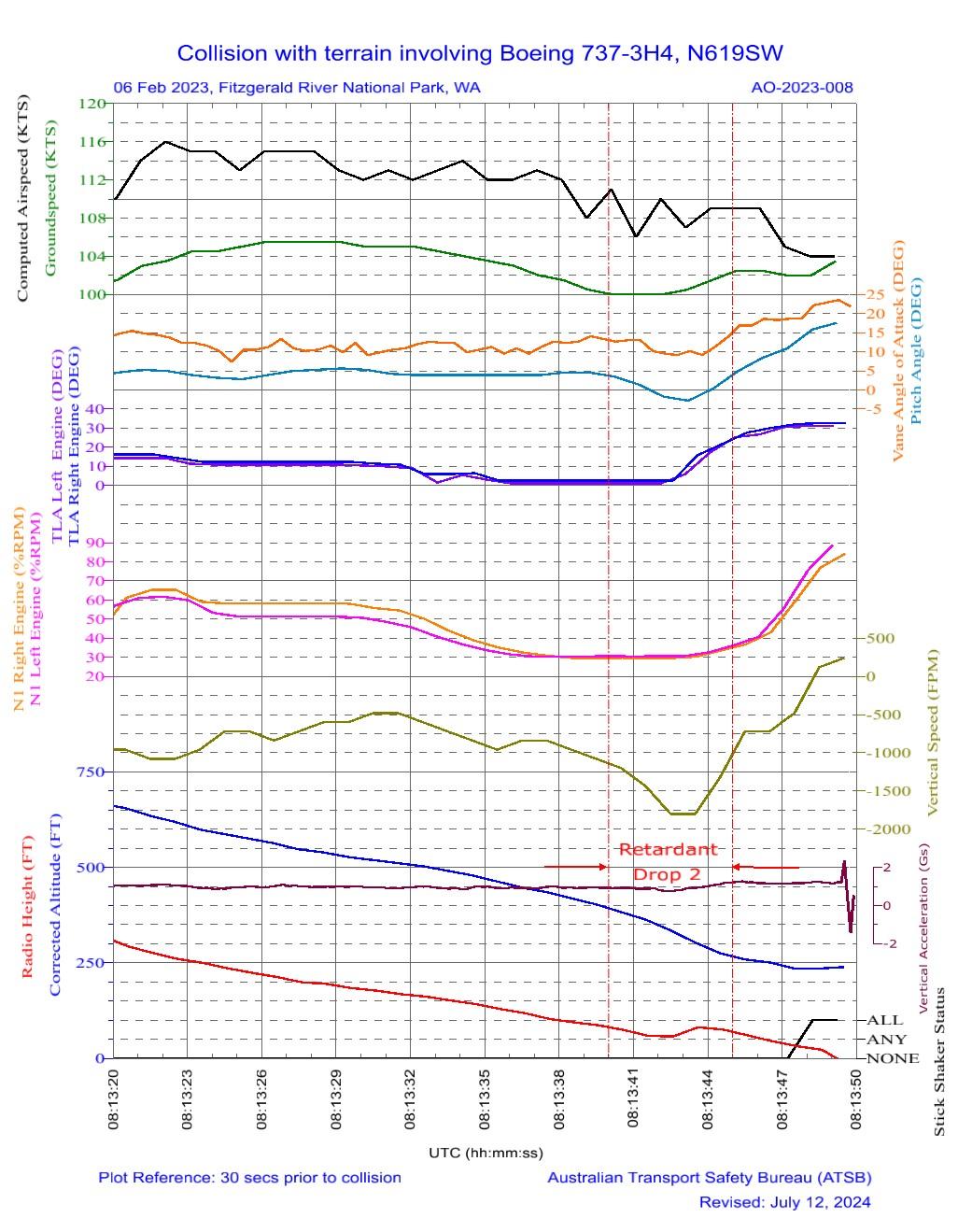
Final 30 seconds of flight data showing corrected altitude, radio height, pitch angle, angle of attack (same scale), thrust lever angle, engine N1 speed, computed airspeed, groundspeed, vertical speed, stick shaker and approximate position of the retardant drop. The vertical acceleration spike indicates the initial impact.
Source: ATSB
Engine acceleration performance and drop times
According to the FDR data, the captain started to advance the thrust levers about 7 seconds before the collision and took about 5 seconds to advance them from 0° to 30° thrust lever angle. The engines started to accelerate from 30% N1 (high-idle) about 1 second after the captain started advancing the thrust levers and reached about 85–89% N1 in a 6-second acceleration period that coincided with the first impact. The acceleration performance depicted by the recorded data was consistent with the Boeing 737-300 engine acceleration check requirements, discussed previously.
According to the operator’s flight crew operations manual (FCOM) take-off procedure, after the pilot flying has aligned the aircraft with the runway, the thrust levers are initially advanced to 40% N1 and the engines allowed to stabilise, then TO/GA [take-off / go-around] is selected and thrust levers advanced to take-off N1. The accident FDR plots depicted a distinct change in the engine acceleration curve from about 40% N1 (at 0813:46 in Figure 10). The engines took about 4 seconds to accelerate to 41–43% N1 and another 3 seconds to accelerate to 85–89% N1.
Noting the FCOM take-off procedure and the distinct engine acceleration profile, the ATSB asked the operator if the take-off procedure was related to engine acceleration time and how this was managed during a retardant drop. The operator clarified that the FCOM take-off procedure to allow the engines to momentarily stabilise at 40% N1 before advancing to take-off thrust was in accordance with the Boeing 737 flight crew training manual, which provided the following explanation:
Allowing the engines to stabilize provides uniform engine acceleration to take-off thrust and minimizes directional control problems. This is particularly important if crosswinds exist or the runway surface is slippery. The exact initial setting is not as important as setting symmetrical thrust.
For the management of engine acceleration during retardant drops, the operator reported that if the terrain at a drop site was level, then the engines would likely be set at 60–65% N1 and they would quickly accelerate to the go-around thrust at the end of the drop. However, to control the airspeed during a downhill drop, they could not prescribe a minimum N1 setting, and the pilot flying may need to use flight idle thrust to control the drop speed.
In this situation pilots were trained to advance the thrust levers about halfway through the drop so that the engines could quickly accelerate to go-around thrust at the end of the drop. The operator acknowledged that if the pilot was late advancing the thrust levers from idle, it would result in a delay of about 3 seconds before the engines could be accelerated up to the go-around thrust setting.
On the accident drop, the FDR recorded that the captain advanced the thrust levers about halfway through the drop. However, the accident drop was a quarter load, which took 5 seconds to release. In comparison, the first partial drop of three-quarters of the load took 9 seconds to release. The 2 previous drops on the day of the accident were both full loads at coverage level 3 and took 12 and 15 seconds, respectively. Two days earlier, 7 full or partial drops were conducted at coverage levels 6 and 8. The full drops at coverage level 6 were released in 6–7 seconds and the full drops at coverage level 8 were released in 5 seconds. This indicated that, given the typical engine spool‑up time, either a partial drop or a drop at a high coverage level with the engines at idle could result in a post-drop delay in engine acceleration to go-around thrust.
Tactical flight profile
First and second flight taskings
The first retardant drop of the day for Bomber 139 at the fire ground was with BD125 and started with a left-hand circuit Show-Me profile about 500 ft above the subsequent drop height in a northerly direction on the western flank of the fire. The overfly of the target was followed by a close left-hand circuit with BD125 in the Chase-Position profile[26] and a full load release at coverage level 3 over 12 seconds.
On the second drop, on the eastern flank of the fire, another Chase-Position profile left-hand circuit was flown with a tag and extend full load release in a southerly direction at coverage level 3 over 15 seconds but without a Show-Me profile. Figure 11 depicts the flight profiles and Figure 12 shows imagery of the first drop, which started at the same road as the accident flight, and the second drop tag and extend an existing line of retardant.
Figure 11: First and second drop flight profiles on 6 February 2023
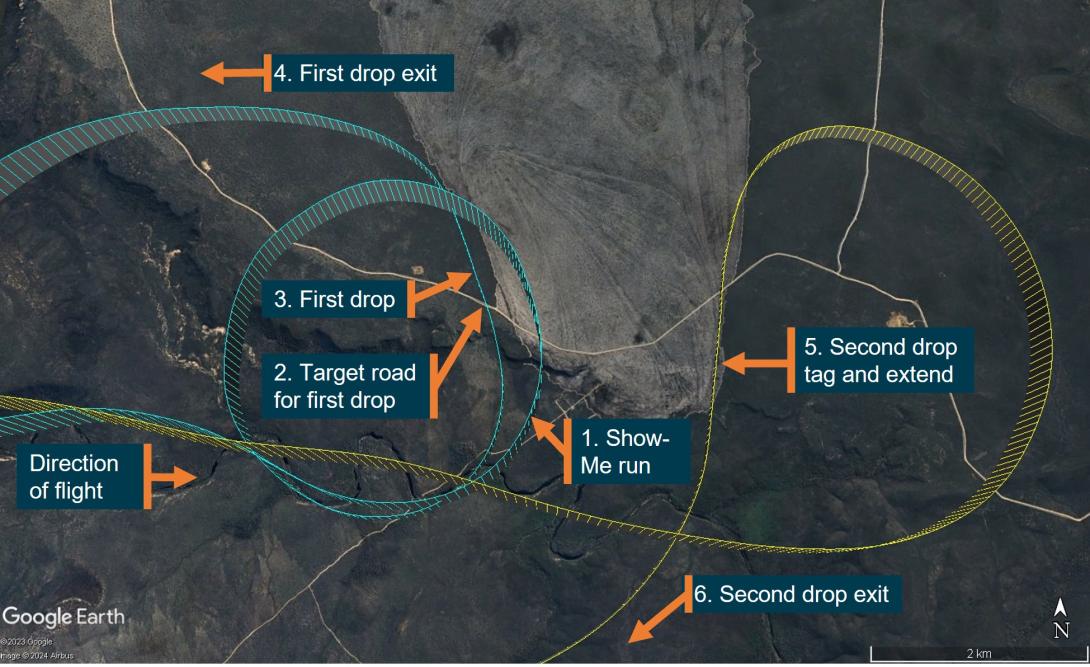
Source: Google Earth, annotated by ATSB
Figure 12: First drop (left) starting at road and second drop (right) tag and extend

Source: Department of Fire and Emergency Services, annotated by ATSB
Accident flight tasking
When Bomber 139 returned to the fire ground for the third drop of the day, BD123 had replaced BD125. The BD123 pilot reported having prior experience working in terrain with more extensive vertical relief in Canada and considered the accident flight target and exit to be relatively flat. They further advised being aware of a 40–50 ft change in the elevation and, as a matter of practice, would not conduct uphill drops.
The Birddog pilot assessed the altitudes for the drop were about 450 ft at the start and 400 ft at the end, which they estimated would provide 100–150 ft height above terrain. However, the pilot provided the altitudes in hundreds of feet and therefore briefed 500 ft as the start altitude. At follow-up, the pilot confirmed they briefed a safe altitude(s) for Bomber 139 to transit through the run and that they levelled their aircraft at their briefed altitude over the target as a visual reference for Bomber 139’s captain.
The Birddog pilot reported that it was not uncommon for the Show-Me profile not to be flown if the LAT had conducted previous drops in the area. A right-hand circuit was not their preferred option but they did not consider it would be a problem because they were providing a Lead profile to the target. However, they reported a ‘slightly longer final’ was conducted to ensure that they could line up on their visual cues and see the target.
After the first partial drop, BD123 conducted a sharp right turn to assess the drop while Bomber 139 conducted the go-around. When Bomber 139’s captain reported the need for a second drop the Birddog pilot offered the captain the choice of either another Lead or Chase-Position profile. The captain had no preference and the Birddog pilot elected to conduct another Lead profile, which required Bomber 139 extend their circuit until BD123 could regain the Lead position. The Birddog pilot reported that this resulted in another ‘slightly longer final’.
The Coulson Aviation fixed-wing flight operations manual did not include detail of the setup and conduct of retardant drops and the Bomber 139 captain referred the ATSB to the US National Wildfire Coordinating Group (NWCG) aerial supervision standards for how they expected a Lead Plane (Birddog) would conduct operations in the US. The Birddog operator’s standard operating procedures (SOPs) for Lead Plane Operations (2009 and 2023) provided the same tactical flight profiles and descriptions as those published by the NWCG.[27] Their SOPs also stated that drops ‘should be downhill’, that they were to provide ‘the final heading for the run and the altitude for the drop start point’, the drop height ‘minimum is 150 ft above the top of the vegetation for heavy tankers’ and that ‘The airtanker pilot is responsible for maintaining safe drop heights.’
Bomber 139’s captain’s preference for the circuit, and what they reported teaching, was to fly a close circuit that kept the target in sight. To achieve this, the captain would initiate a descending base turn abeam the drop start point and maintain visual contact with the target through the first half of the base turn. About halfway through the base turn, the captain would extend their visual scan from the target to include the exit and on roll-out to wings level, the aircraft would be positioned on short final close to the start of the drop.
On the first drop of the accident flight the captain reported the large circuit was due to the manoeuvring required to join up with BD123. The captain recalled that this resulted in a very wide base but final was flown clear of the smoke on the right side of the fire-line and at a normal angle of approach (Figure 13).
However, in the low ground of the depression the fire-line had extended further west, which resulted in a climbing right turn away from the fire before the downhill section of the drop and the captain did not see the exit before starting the second circuit. Subsequently, BD123 led them further east into the drift smoke for the next approach to turn the line in a more westerly direction. This resulted in Bomber 139 approaching the target through the smoke and the captain did not identify the target until they were at the start of the drop and had not seen the exit.
Figure 13: Accident flight first and second drops
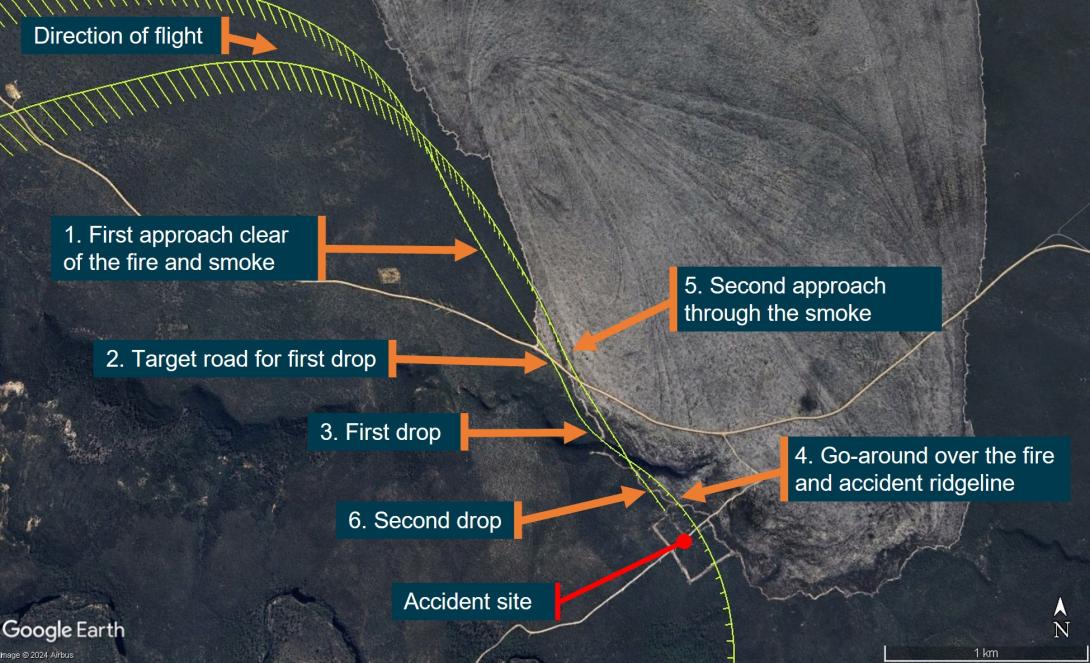
Source: Google Earth, annotated by ATSB
Energy management
United States Federal Aviation Administration handbook
The FAA provided a description of aircraft energy management in their Airplane Flying Handbook (FAA-H-8083-3C) Chapter 4: Energy Management: Mastering Altitude and Energy Control. The introduction to the chapter described it as ‘about managing the airplane’s altitude and airspeed using an energy-centered approach.’ While this chapter was not written for a LAT rapid inflight weight reduction, it included 4 concepts of relevance to the accident. They were: Irreversible Deceleration and/or Sink Rate, Total Mechanical Energy, Energy Height or Total Specific Energy and Specific Excess Power, which were described as follows:
Irreversible Deceleration and/or Sink Rate
Unrecoverable depletion of mechanical energy as a result of continuous loss of airspeed and/or altitude coupled with insufficient excess power available under a given flight condition. Failure to recover above a certain critical AGL [above ground level] altitude results in the airplane hitting the ground regardless of what the pilot does.
Total Mechanical Energy
Sum of the energy in altitude (potential energy) and the energy in airspeed (kinetic energy).
Energy Height or Total Specific Energy
Measured in units of height (e.g., feet), it represents the airplane’s total energy per unit weight. It is found by dividing the sum of potential energy and kinetic energy by the airplane’s weight. It also represents the maximum height that an airplane would reach from its current altitude, if it were to trade all its speed for altitude.
Specific Excess Power
Measured in feet per minute or feet per second, it represents rate of energy change—the ability of an airplane to climb or accelerate from a given flight condition. Available specific excess power is found by dividing the difference between power available and power required by the airplane’s weight.
The FAA’s equation for specific excess power was Ps = (T-D) * V / W, where Ps = specific excess power, T = engine thrust, D = total drag, V = airspeed, and W = aircraft weight.
Flight data review
The ATSB reviewed the 4 retardant drops conducted by Bomber 139 on the day of the accident (including the third partial drop followed by the fourth accident drop), and analysed the height, vertical speed, airspeed, angle of attack and N1 parameters. The 2 states compared for each run were at the minimum drop height and at the go-around thrust lever setting on completion of each drop (based on the thrust levers reaching a stable setting after being advanced at the end of each drop). The data for the 4 drops was as follows:
- On the first drop, Bomber 139 reached a minimum height of 46 ft with 120 ft/min rate of descent at 113 kt and 61–66% N1. Minimum airspeed was 109 kt at 50 ft and maximum angle of attack was 19.7° at 64 ft.[28] On reaching the go-around thrust lever setting, the height was 64 ft with 360 ft/min rate of climb at 128 kt and 77–86% N1. Idle thrust was employed intermittently near the start of the drop, which resulted in a V-shaped airspeed trace during the drop (Figure 14) and in BD125 closing on Bomber 139 during the drop (Figure 15).
- On the second drop, Bomber 139 reached a minimum height of 69 ft with 120 ft/min rate of descent at 132 kt and 67–70% N1. Minimum airspeed was 129 kt at 77 ft. On reaching the go‑around thrust lever setting, the height was 140 ft with 480 ft/min rate of climb at 136 kt and 85–88% N1.
- On the third drop, Bomber 139 reached a minimum height of 78 ft with 600 ft/min rate of descent at 126 kt and 70–71% N1. Minimum airspeed was 124 kt at 82 ft. On reaching the go‑around thrust lever setting, the height was 153 ft with zero vertical speed at 129 kt and 87–88% N1.
- On the accident drop, Bomber 139 reached a minimum height (before initiating the go‑around) of 57 ft with 1,800 ft/min rate of descent at 110 kt and 30–31% N1. Minimum airspeed was 106 kt at 59 ft. On reaching the go-around thrust lever setting, the height was about 30 ft with 480 ft/min rate of descent at 105 kt and 55–60% N1.
Figure 14: FDR plot of first drop with minimum airspeed reference
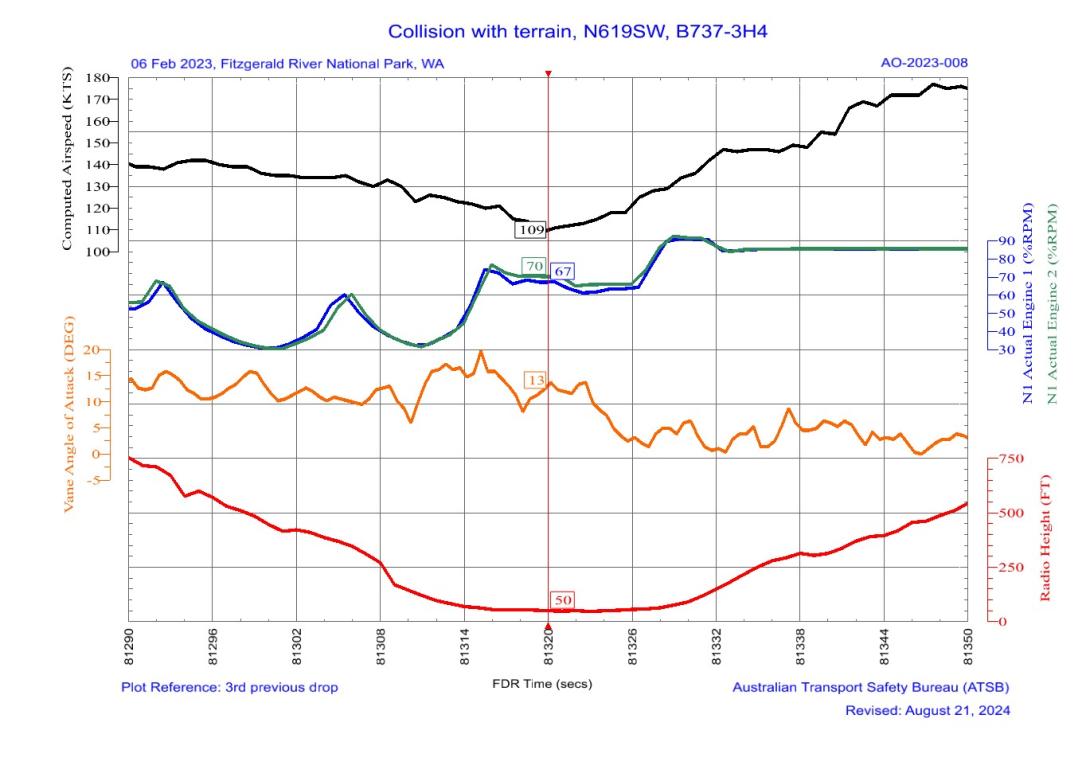
Source: ATSB
Figure 15: Aspect change of Bomber 139 from start of first drop (left) to go-around (right)

Birddog 125 closing on Bomber 139 during the first drop.
Source: Department of Fire and Emergency Services, annotated by ATSB
The effects of the FAA‑specific excess power equation were evident in the 4 retardant drops on the day of the accident. The high engine thrust (N1) and large weight reduction on the first 3 drops resulted in a positive reversal of the vertical speed and airspeed at the end of those drops. However, the idle thrust and smaller weight reduction on the accident drop resulted in the airspeed and height decaying at the end of the drop as the captain arrested the aircraft’s significantly higher rate of descent.
This was consistent with a negative specific excess power (drag greater than thrust) and the FAA’s description of an Irreversible Deceleration and/or Sink Rate. Table 2 summarises the parameters from the flight data review of the 4 drops.
Table 2: Summary of parameters
Drop |
Minimum drop height parameters (height; vertical speed; airspeed; N1) |
Go-around parameters (height; vertical speed; airspeed; N1) |
1 | 46 ft; -120 ft/min; 113 kt; 61–66% | 64 ft; +360 ft/min; 128 kt; 77–86% |
2 | 69 ft; -120 ft/min; 132 kt; 67–70% | 140 ft; +480 ft/min; 136 kt; 85–88% |
3 | 78 ft; -600 ft/min; 126 kt; 70–71% | 153 ft; 0 ft/min; 129 kt; 87–88% |
4 (accident) | 57 ft; -1,800 ft/min; 110 kt; 30–31% | 30 ft; -480 ft/min; 105 kt; 55–60% |
After the accident, the operator informed the ATSB that they had increased their minimum drop height from 150 ft to 200 ft and their target drop speed to 1.3 Vs for downhill drops with flaps-40 and 1.35 Vs for flat terrain drops with flaps-30. They later reported to the ATSB that they believed the recalculation and lowering of drop speeds between partial drops was a ‘significant contributing factor to the accident.’
The Bomber 139 captain reported that reducing the target drop speed (1.25 Vs) following a partial drop provided them with the same stall speed safety margin at the start of each drop as the stall speed also reduced following a partial drop.
If a performance problem occurred in the go-around from the first drop of a split load, the crew could jettison the remaining load to gain an airspeed safety margin equivalent to the loss of the full load. However, if a performance problem occurred on the final drop of a split load, then the additional safety margin was reduced as it was limited to the weight of the remaining partial load.
The release of the entire load on the first drop of the accident flight would have reduced the aircraft weight by about 28% (124,640 lb to 89,440 lb), whereas jettisoning the second drop reduced the aircraft weight by about 9% (97,850 lb to 89,440 lb).[29] In consideration of the implications of recalculating the drop speed between partial drops for a LAT, the ATSB used the FAA’s mechanical energy formulas to assess the potential gain in energy-height from higher drop speeds.
The drop speed at the end of the accident drop was used as the datum and compared with the target drop speed lower deviation limit (refer Figure 17), target drop speed, the previous end of drop speed, which was also the minimum airspeed during that drop, and previous target drop speed. The results are presented in the following table.
Table 3: Drop speed energy-height differences
Description | Drop speed | Energy-height difference |
Accident end of drop speed | 109 kt | datum |
Accident target drop speed lower deviation limit (-5 kt) | 113 kt | +39 ft |
Accident target drop speed | 118 kt | +90 ft |
Previous end of drop speed | 124 kt | +155 ft |
Previous target drop speed | 133 kt | +257 ft |
From Table 3, the actual airspeed at the end of the accident drop resulted in a loss of about 90 ft in energy-height compared to the target drop speed. However, the recalculation of the target drop speed resulted in a loss of about 167 ft in energy-height from the full load target drop speed. Therefore, a comparison between the full load target drop speed and the accident drop speed found that about 65% of the energy-height loss was from recalculating and lowering the drop speed and about 35% of the energy-height loss was from flying slower than the target drop airspeed.
The divergence in the go-around performance of Bomber 139 between the end of the third drop and the final drop is presented in the following FDR plot (Figure 16), in which the parameters are aligned with the end of each drop. The ATSB noted the following from the plot:
- the third drop (RETARDANT DROP 1) exits with a higher N1, airspeed, vertical speed, and lower angle of attack (AOA) than the final drop (RETARDANT DROP 2)
- the pitch attitudes and radio heights diverge at the exit, noting the third drop overflew the depression
- the airspeeds diverge as the vertical speeds and N1 converge.
Figure 16: FDR plot of the third (left labels) and final (right labels) drops
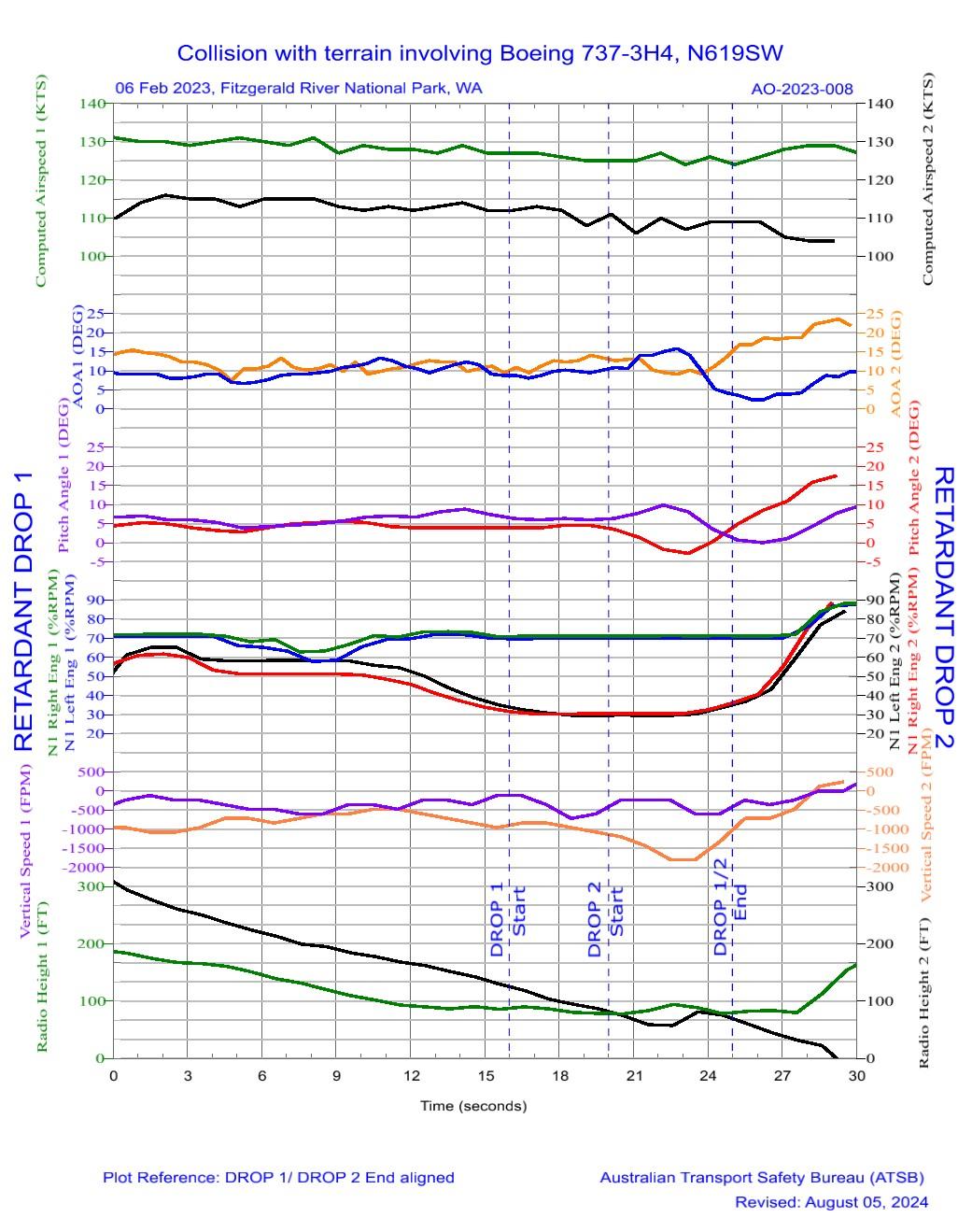
Source: ATSB
Crew resource management
Introduction
Crew resource management (CRM) and controlled flight into terrain (CFIT) prevention training were LAT contract requirements in Australia and the US. It was the responsibility of the contractor and not the contracting agency to deliver the training and provide evidence of completion. The operator, Coulson Aviation, delivered these training programs to their personnel during their northern hemisphere spring training in April 2022. The relationship between CRM and SOPs was described in FAA advisory circular AC 120‑71B (2017): Standard Operating Procedures and Pilot Monitoring Duties for Flight Deck Crewmembers, as follows:
Effective crew coordination and crew performance depend on the crew’s having a shared mental model of each task. That mental model, in turn, is founded on SOPs.
Monitoring performance can be significantly improved by: (1) developing and implementing effective SOPs to support monitoring and cross-checking functions, and appropriate interventions, (2) by training crews on monitoring strategies, and (3) by pilots following those SOPs and strategies.
Coulson Aviation standard operating procedures
Target drop height
The Coulson Aviation B737 flight crew operations manual (FCOM Volume 1, July 2019) RADS flight pre-drop checklist, included a step to ‘Set the DH REF [decision height reference]/radio altimeter minimums to target drop height.’ However, their B737 Fireliner quick reference handbook normal checklist (QRH - FCOM Volume 3, August 2019) abbreviated this checklist item to ‘Altimeters set’, as per the FAA approved flight manual supplement for the Fireliner modification. The CVR revealed several instances of the pilots cross-checking their altimeter pressure settings with each other and other aircraft, and confirming their drop speeds to bug, as per their QRH pre‑drop checklist. However, there was no reference to a target drop height or decision height setting.
The aircraft captain confirmed that the decision height setting on the radio altimeter was not used because it did not provide an aural alert and because the pilot flying is predominantly ‘eyes-out’ during the drop and therefore not monitoring the decision height light on the attitude indicator. The co-pilot did not use the decision height on the radio altimeter and did not believe it was a SOP to use it because it could cycle on-and-off during a retardant drop over undulating terrain.
The operator confirmed that, despite the documented FCOM requirement, the decision height setting was not used. They further stated that it could be a distraction if it activated intermittently during a retardant drop.
According to the aircraft captain, 150 ft was the standard target drop height, with the caveat that ‘drifting down’ to lower drop heights was not uncommon at lighter coverage levels. The operator confirmed that while they used the USFS LAT minimum drop height of 150 ft as their standard target drop height at coverage level 3 (accident drop setting), it was not published in their fixed‑wing flight operations manual or their B737 and C-130 FCOMs. The operator also reported that pilots may be tempted to drop below the standard target drop height at light coverage levels as the retardant will be subjected to less wind interference and this will improve the accuracy of the drop.
At their initial interview, the co-pilot stated they did not believe there was a minimum drop height, but also reported having limited industry knowledge.
At a follow-up interview, the co-pilot confirmed that none of the captains had briefed a target drop height and that they had flown with all the operator’s B737 captains. The co-pilot reported understanding that 150 ft was the standard drop height figure, but also stated that ‘150 ft is the highest you want to be for that coverage level [3] depending on wind drift.’ The co‑pilot also reported that the altitudes briefed by BD123 were for terrain clearance on the approach and exit and indicated it would be a downhill drop, and that they were not target drop heights. Finally, the co‑pilot advised that they felt confident about speaking up if something felt unsafe and, on that day, ‘there was nothing that seemed unsafe’.
Monitoring duties
The aircraft captain reported the co-pilot’s duty was to scan inside and out and call deviations, such as airspeed, if different from what was briefed, and confirmed the 150 ft drop height published by the USFS was a minimum height. The CVR indicated that the target drop speed was the only parameter briefed and the last announcement from the co-pilot was about 70 seconds before impact to inform the captain that the pre-drop checklist was complete. The co-pilot reported their focus of attention was inside on the airspeed, which they recalled was on their target drop speed of 118 kt, and on the radio altimeter, which they could not recollect but believed ‘would have been about 100 ft’. The co-pilot was listening to the engine noise but was not monitoring engine thrust and couldn’t recall the thrust lever settings.
A colleague of the co-pilot confirmed the operator’s CRM philosophy was not to overcommunicate – ‘brief first, then only communicate if there is a deviation from the brief’. Figure 17 depicts the operator’s B737 Fireliner FCOM Volume 1 Retardant drop procedure. With reference to the tolerances in Figure 17, the FDR data indicated that the aircraft descended below their standard target drop height deviation limit of -25 ft about 13 seconds before impact, and remained below it until impact. The airspeed was below their target speed deviation limit for about 11 seconds before impact and 4–5 seconds before the captain started to advance the thrust levers.
Figure 17: Retardant drop procedure
Source: Coulson Aviation
Crew resource management training
The operator’s CRM training package, delivered in April 2022, included material on the following topics:
- training objectives
- introduction to CRM
- current SOPs
- discussion
- roles and responsibilities.
The training objectives topic highlighted one of the challenges in their industry as follows:
Given the dynamic nature of fire, SOPs allow a relatively wide range of individual preferences among captains, this can and does lead to a level of confusion within the cockpit, especially among new/inexperienced crew members…
The introduction to CRM topic indicated that human error is a contributing factor to most accidents, and highlighted the following factors:
Problems are associated with poor group decision making, ineffective communication, inadequate leadership and poor task or resource management.
The ‘current SOPs’ topic within the CRM training package included detail of the FCOM Volume 1 Retardant drop procedure (Figure 17) and the QRH Pre-drop checklist. The FCOM Volume 1 Pre‑drop checklist procedure, which included setting the radio altimeter decision height to the target drop height was not included.
The ‘discussion’ topic listed the following items:
- callouts
- calling a go-around
- when and how to communicate discomfort
- identifying hazards
- when should FO/FE [first officer/flight engineer] hit the button [emergency dump]?
The ‘roles and responsibilities’ topic included, but was not limited to, the following:
- captain – Position aircraft on Show-Me to observe line and start/stop point
- co-pilot – Backup captain on configuration/altitude/airspeed/checklist/drop/escape.
Controlled flight into terrain prevention training
The operator’s CFIT prevention training package, also delivered in April 2022, included material on the following topics:
- What is CFIT?
- Why does it happen?
- How can I avoid CFIT?
- What are some of the contributing factors to CFIT?
- CFIT accident reviews [which included a general aviation accident, an airliner accident and 3 airtanker accidents].
The first 3 topics were based on material from the FAA’s general aviation joint steering committee (GAJSC) that defined CFIT as follows:
CFIT is defined as an unintentional collision with terrain (the ground, a mountain, a body of water, or an obstacle) while an aircraft is under positive control.
The operator had highlighted several sections of the FAA’s material, which included the following:
…the General Aviation Joint Steering Committee (GAJSC) observed that a clear majority of the CFIT accidents in a typical year occur in daylight, and with visual conditions.
Other top causes of CFIT are…unrealistic aircraft performance expectations (e.g., high density altitude, tailwinds on approach).
While the operator’s accident case studies included multi-crew operations, their introductory material from the GAJSC was directed at single-pilot general aviation operations. Consequently, the avoidance strategies focused on assisting single-pilot operations, such as a FRAT and technological devices such as moving maps with terrain overlays. The slides in their CFIT training package did not include CRM and SOPs as prevention strategies in the retardant drop.
The role of multi-crew CRM to prevent CFIT was described in FAA advisory circular AC 120-51E (2004): Crew resource management training, as follows:
Effective monitoring and cross-checking can be the last line of defense that prevents an accident because detecting an error or unsafe situation may break the chain of events leading to an accident. This monitoring function is always essential, and particularly so during approach and landing when controlled flight into terrain (CFIT) accidents are most common.
The FAA advisory circulars (AC 120-51E and AC 120-71B) were directed towards the commercial transport sectors to assist operators with the development and implementation of their CRM training, SOPs, and pilot monitoring duties. Consequently, they addressed the multi-crew environment and followed recommendations from a 1994 US National Transportation Safety Board safety study (NTSB/SS‑94/01): A review of flightcrew-involved, major accidents of U.S. air carriers, 1978 through 1990. The NTSB’s review found that 23% of the contributing errors were monitoring and/or challenging errors, which occurred in 84% of the accident sequences. They reported that ‘Most of the errors that were not monitored or challenged played very important roles in the accidents.’
Tasking agency standard operating procedures
National Aerial Firefighting Centre
The National Aerial Firefighting Centre (NAFC) was formed by the Australasian Fire and Emergency Services Authorities Council (AFAC) in 2003 through a partnership between the federal and state/territory governments to deliver cooperative national arrangements for the provision of aerial firefighting resources. The states and territories recognised that if they had one contract for operators to follow then they could easily be moved around the country as necessary to facilitate the sharing of the resource and associated cost. To support this process, the NAFC produced Operational Standards, which provided the minimum standards for a NAFC contract. These were procurement standards, with the respective state/territory emergency services having responsibility for operational policies and procedures.
The NAFC contracted about 150 firefighting aircraft, including LATs, for use by state and territory emergency service and land management agencies across Australia. At the time of the accident, the NAFC Members participating in the LAT program were New South Wales (NSW), WA, Victoria, and Queensland.
The NAFC-contracted aircraft were assigned a nominated operational base where they were tasked by the NAFC Member’s emergency services. Each of the NAFC Members participating in the LAT program confirmed to the ATSB that they had developed their own SOPs for aerial firefighting, which included LAT SOPs.[30] A LAT service provider (such as Coulson Aviation) therefore operated under a NAFC contract, which required them to comply with the NAFC Standards and the Member state’s SOPs associated with their base.[31] However, their base could change throughout the season in response to the fire threat, which was acknowledged in the National Aerial Firefighting Strategy 2021–26 section on risk management and resource sharing, as follows:
During any single fire season, it is highly likely that risk factors will lead to Commissioners and Chief Officers wanting to redeploy assets within jurisdictions and potentially redeploy assets across jurisdictional borders. Aerial assets offer the greatest flexibility to redeploy both within and across jurisdictions. LATs and strategic mapping aircraft can operate in more than one jurisdiction on the same day.
To date all aircraft have been assigned to a state or territory in line with the co-contribution commitment which has been part of the NAFC Resource Management Agreement since its inception. The 2020 Royal Commission into National Natural Disaster Arrangements introduced the notion that national assets, particularly LATs and Type 1 Rotary Wing, be tasked according to ‘greatest need’ and their deployment and application would be considered on a national rather than jurisdictional basis.
The NSW Rural Fire Service (RFS), which had their own LAT and could have multiple additional LATs on contract in any season, reported that if one of their LATs was re-deployed to a non‑participating Member state or territory, then it would be operated in accordance with the NSW RFS LAT SOPs, but not inconsistent with local requirements. However, the RFS acknowledged that the non-participating Member state or territory would need to brief the LAT and Birddog operators on any differences, which would require that Member to be familiar with the NSW LAT SOPs.
The federal government contributed funding to the NAFC national fleet of firefighting aircraft but the primary responsibility for aerial firefighting remained with the states and territories and therefore, Member states produced their own SOPs. However, AFAC stated that their Member states and territories would be undertaking greater resource sharing in the future. Therefore, they concluded that the industry should develop national standards and that the NAFC business unit, under the AFAC banner, is a mechanism for this as they had existing areas of Member collaboration in contracts and innovation for aerial firefighting.
Following the C-130 LAT accident in NSW on 23 January 2020 (AO-2020-007), a statement of intent for aviation safety by the NAFC led to the formation of the Aviation Safety Group (ASG). The ASG was supported by the NAFC and had Members from agencies in all jurisdictions, including New Zealand and a representative from the Civil Aviation Safety Authority. During the B737 LAT accident investigation, the NAFC advised the ATSB that the ASG had developed a list of priorities that included:
- airspace management, including cross-border operations
- human factors and CRM training – for agency personnel, especially those who interface with aviation
- consistent doctrine – review and national standardisation (where practical) of standards and operational procedures
- safety information framework – reporting and sharing of safety information and messaging
- common cross-border radio operations, including hardware innovations and frequency management
- a national LAT Lead Plane pilot training standard.
At the time of writing, the ASG had not identified a national LAT SOP as a priority item.
United States Forest Service standards
The USFS has managed wildland fires on national forests and grasslands for over 100 years, working with federal, state, tribal and local partners. In 1976 the National Wildfire Coordinating Group (NWCG) was established to provide national leadership for these partners. The NWCG had an Executive Board comprised of 12 member entities and their role was described as follows:
The Executive Board works in a collective, collaborative and consensus-seeking manner to accomplish the NWCG mission. NWCG develops the interagency standards that are core to implementing its mission, which the member agencies then choose to implement through their own directive systems.
The USFS reported that federally‑owned lands made up most of the western US and some states had adopted the USFS SOPs as their de facto standard where they had a small area of state responsibility. Local requirements were addressed with a briefing package at each airtanker base. In illustrating the multi‑jurisdictional nature of aerial firefighting, the USFS provided an example operational scenario where a LAT could be employed on a fire in Montana in the morning, in Southern California in the afternoon and end the day in Washington state on another fire.
They reported that these movements across geographical boundaries required national standards to be in place, and that most of the aviation standards were lessons learned from accidents. The national standards were accepted as a better way of operating and they considered the first 30 days after an operator moved between jurisdictions to be a high-risk period due to the change in rules. Therefore, given the movement of aerial firefighting aircraft and operating personnel between the US and Australia, they considered that closer harmonisation of standards would likely bring safety benefits across the industry.
Benchmarking of tasking agency standards and procedures
Following the C-130 LAT accident in 2020, the ATSB obtained a copy of the NSW RFS LAT SOPs (Operating guidelines for air tankers operations 2018) for review. That review included benchmarking the NSW SOPs against the USFS SOPs, noting the accident aircraft was a US registered LAT and the operator was also contracted by the USFS during their fire season.
The ATSB found several procedures in the USFS SOPs, relevant to the C-130 accident, which were omitted from the NSW SOPs. They were a task rejection policy and procedure, known as a ‘turn down’ in the USFS SOPs under their policy of ‘Risk Refusal’, and procedures for deploying a LAT without aerial supervision. These omissions were raised as safety issues by the ATSB in August 2022 and directed to the NSW RFS for action. The safety issues were closed on 2 May 2023 as adequately addressed.
Following the B737 LAT accident, the ATSB reviewed the WA LAT SOPs (Large air tankers operational procedures 2021-22 version 3.3), current at the time of the accident. This was a joint publication between the WA Department of Fire and Emergency Services and the WA Department of Biodiversity, Conservation and Attractions. The ATSB compared procedures relevant to the C‑130 and B737 accidents from the WA SOPs with the 2018 NSW RFS LAT SOPs and the USFS airtanker SOPs (Standards for airtanker operations 2019) and NWCG aerial supervision SOPs (Interagency aerial supervision guide 2017).[32],[33] While the USFS airtanker and NWCG aerial supervision SOPs were separate documents, the WA and NSW LAT SOPs also incorporated the LAT aerial supervision procedures.
The WA SOPs included 3 target identification techniques (tactical flight profiles), but they did not include the Lead or Chase-Position profiles, which were employed on the day of the accident. They also did not include a drop height and there was no task rejection policy or procedure. However, they did include the following requirements:
The BRDG [Birddog] AAS [air attack supervisor] is to confirm the drop zone clear with the Primary AAS or Ground Controller prior to the LAT commencing the final drop run.
The LAT must not drop until DROP ZONE CLEAR has been confirmed.
The NSW SOPs included the same target identification techniques as the WA SOPs and therefore they also did not include the Lead or Chase-Position profiles. However, the NSW SOPs did include reference to a LAT drop height and stated the following:
The Birddog aircraft will assess the Air Tanker for drop height to ensure a height of approximately 150 feet above the canopy or bare ground is attained. Low drop heights should be avoided to minimise the risk during low level flight operations and ground crews in the vicinity of the drop.
The NWCG SOP tactical flight profiles consisted of the Show-Me profile, Chase-Position profile, and Lead profile. All 3 of these profiles were flown on the day of the accident. The USFS and NWCG SOPs both stated the drop height for a LAT was a ‘minimum’ of 150 ft above the top of the vegetation. Below the minimum drop height reference in the NWCG SOPs were the following notes:
It is important for the retardant to “rain” vertically with little or no forward movement. The airtanker pilot is responsible for maintaining safe drop heights.
The preference for downhill drops was captured in the NWCG and WA SOPs. The NWCG SOPs stated that the approach should be ‘downhill, down canyon, down sun’. The WA SOPs stated, ‘implement where possible that all exits are downhill’. The NSW SOPs did not include an explicit statement to this effect but their flight safety considerations included ‘Terrain may limit firebombing run directions and the availability of exits.’
While not a factor in either the C-130 or B737 accidents, the NWCG SOPs included emergency overrun procedures (as did the Birddog operator). In the Lead profile (accident flight profile), the Birddog pilot cannot see the LAT and therefore there is a risk of the LAT overrunning the Birddog. The WA and NSW SOPs did not include procedures for how to mitigate the risks associated with an overrun, which include wake turbulence-induced loss of control for the smaller aircraft, mid-air collision and terrain collision associated with an avoidance manoeuvre.
Development of the target drop height and speed
Background
The NAFC contract for the operator’s multi-engine airtankers required their aircraft to have US Interagency Airtanker Board (IAB)[34] approval in addition to any local NAFC Member approval requirements. Multi-engine airtankers were approved for use in the US by the IAB, which was a contract requirement of US government agencies at the federal, state, and local level. The current Interagency Airtanker Board procedures and criteria for evaluating aircraft and dispensing systems used in aerial firefighting were published in 2013. According to the USFS, the theory of aerial application of retardant was as follows:
For proper aerial application of retardant to the fuel (vegetation), all forward momentum of the retardant cloud should stop, and the liquid should rain down vertically. This allows an even coating and better vertical penetration into the tree or brush canopy.
Section 7 (B) of the IAB procedures on tank system criteria, described the retardant coverage levels as the gallons per 100 square feet (gpc) and that the flow rate from an aerial delivery system is ‘the most significant controllable factor’ in determining the level of coverage obtained. The USFS considered drop tests to be the most accurate means of measuring ground pattern performance. The IAB procedures defined a drop test as a ‘dynamic flying test of the aircraft retardant delivery system over a cup/grid matrix, which is used to determine the coverage level production of the system for each drop type.’ According to the USFS:
A balance of factors is required for airtankers to meet the coverage level requirements. This balance is established during the IAB testing and is done in a controlled environment with little to no wind on flat terrain. Multiple passes are made over a test grid at different tank controller settings, airspeeds, and heights. This establishes the flight profile and tank controller settings that produce acceptable ground pattern performance under test conditions.
Section 3 (H) of the IAB procedures on multi-engine airtanker requirements included a descent profile requirement as follows:
Aircraft shall be capable of descending at Board-approved maximum operating weight along a 13 percent (7.4°) slope for 30 seconds to 5,000 ft pressure altitude in the drop configuration without exceeding maximum drop speed. At the 25 second mark, a full load of water shall be dispensed at coverage level 6 and again at coverage level 8 and demonstrate no more than 7% difference in average flow rate from grid results.
Drop height requirements
Section 3 of the IAB procedures on multi-engine airtanker requirements did not include a minimum drop height. However, section 7 (B) of the IAB procedures on tank system criteria stated that the requirement was that drops ‘shall be made at a 200-foot drop height or the minimum safe drop height if greater than 200 feet.’ The operator had conducted IAB drop testing with their B737 Fireliner and described the process as follows:
The IAB grid test evaluates the performance of the drop tank in negligible wind conditions at various coverage levels, aircraft configurations, ground speeds, and drop heights. As part of that process, high speed video was evaluated to determine the optimal drop height which is the lowest height that allows the forward trajectory of the retardant to cease, thus minimizing shadowing effect so that the fuels are evenly coated.
As part of the grid test evaluation, the IAB provided the operator with a table of the recommended minimum grid test drop heights under the heading of ‘minimum altitude above the height of the fuel to eliminate the forward momentum, i.e. eliminate shadowing[35] (feet).’ Each drop height corresponded with a controller setting for the coverage level to be achieved. For the operator’s B737 Fireliner, the minimum drop heights were over the range of 150–200 ft for the controller settings 1–8 (150–185 ft for the C-130). For all the LATs listed in the table, the recommended minimum grid test drop height was 150 ft for controller settings 1–3 (setting 3 was used on the day of the accident). The operator reported that they adopted the heights in the table as their standard target drop heights for training and operations.
The USFS clarified that the table drop heights were for determining ground pattern performance during testing only and were not operational requirements. The operational drop heights were identified in the contracts, which may reference interagency operational handbooks. They reported that environmental variables, such as wind, terrain, fire behaviour and suppression tactics may require a drop height higher than was demonstrated during testing.
The USFS Airtanker Services contract standards[36] stated a minimum drop height of 150 ft, which was consistent with their airtanker SOPs and the NWCG aerial supervision SOPs. Their contract standards also stated that ‘Retardant shall be dropped as accurately as possible on the designated target areas of the fire.’ The USFS confirmed that if an operator conducted drops below 150 ft, they would be non-compliant with the contract. However, they acknowledged that operators have dropped lower to improve their accuracy or with the assumption that it will assist the ground firefighters by providing a thicker line of retardant.
In March 2000, the USFS published the results of a research project into safe drop heights for fixed-wing airtankers (Lovellette). The purpose of the project was to examine the cessation of the forward momentum of the retardant cloud, which served 2 purposes:
- prevent shadowing of the fuel (as discussed above)
- reduce the risk to ground personnel from flying debris struck by the retardant cloud.
Video analysis of drop tests from the project led to the development of a relationship between safe drop height, load size, and the peak flow rate (Lovellette, 2000). The danger to ground firefighters was minimised if the retardant lost its forward momentum and fell vertically (Lovellette, 2000). This provided a safe drop height that increased with higher controller settings that use a higher flow rate to achieve the required coverage level.
Another review of drop patterns by the USFS found that lower coverage level patterns showed distortion under higher wind speeds while the higher coverage levels were relatively unaffected (Suter, 2005). Suter (2005) noted that higher drops increased the retardant cloud susceptibility to wind erosion and the maximum coverage levels tended to decrease as the drop height increased. While the analysis of drop patterns showed disadvantages to increasing drop height, Suter (2005) also noted that increasing drop height is ‘safer for flight crew and ground personnel.’
The USFS confirmed that Lovellette’s (2000) safe drop height project was for the safety of ground personnel and not the airtankers. The focus on the safety of ground personnel was reinforced with their interagency aviation safety alert in 2019 (IASA 19-02)[37] on the subject: Retardant Safe Drop Height, area of concern: Safety of Ground Personnel. From the safety alert:
The force of the retardant dropped from too low of an altitude can topple trees up to 90 feet in height and a trunk a foot in diameter.
Pilots must remember that lower is not always better. Drops that are too low fail to provide retardant in an efficient manner with the desired coverage level. This is not only dangerous but fails to provide the support ground crews require.
Drop speed requirements
Section 3 (E*)[38] of the IAB procedures on multi-engine airtanker requirements included the following points about the effect on flight conditions from the release of retardant:
Release of retardant in all normal drop configurations and at all normal drop speeds does not result in dangerous or seriously objectionable flight conditions.
- The minimum drop speed is not less than the Vmc (minimum control speed), nor 1.25 Vs (stall speed), both speeds being evaluated in the drop configuration.
- The maximum drop speed does not exceed Va (design maneuvering speed).
According to the USFS, environmental variables may require an increase in the drop speed of 10–20 kt, but excessive drop speeds could adversely affect the firefighting effort as per the following description:
At higher airspeeds, the retardant can shear at the tank opening and not drop in a column, thus reducing coverage levels. If the retardant cloud has too much forward momentum the retardant will coat only one side and create a shadowing effect, allowing fire spread. Forward momentum creates a hazard to ground crews if they are inadvertently in the path of the drop. Too slow of a release speed is a safety of flight issue.
The USFS reported the drop test airspeed requirements dated back to 1976 and the rationale for the prescribed parameters could not be found. However, they reported that the speed is not limited to the maximum load the applicant is seeking approval for and the relevant condition was ‘Release of retardant in all normal drop configurations and at all normal drop speeds does not result in a dangerous or seriously objectionable flight condition.’ They further stated that:
Release can be one drop of the entire volume or split drops up to 4 drops so all normal drop configurations could be between the full volume down to a quarter volume. To produce the desired coverage level the speed may change but not go below the minimum drop Vmc nor 1.25Vs or above the maximum of Va.
The operator incorporated tables for weights and speeds in their B737 Fireliner QRH normal checklist. The weights column was based on 5,000 lb increments in the aircraft operating weight from 85,000 lb to 135,000 lb. There were 4 columns for airspeeds, which included a column for 1.25 Vs that was also annotated as V-drop (target drop speed). This table provided a quick reference for the crew to update their drop speed between partial drops and was consistent with the IAB minimum drop speed requirements for evaluating multi-engine airtankers.
Emergency dump
Section 7 of the IAB procedures on tank system criteria required ‘features that enhance safety in the event of an in-flight emergency.’ These features included an independently‑controlled emergency dump system. The operator’s flight manual supplement for the B737 RADS indicated the emergency dump system could jettison a full load in 2 seconds.
Previous controlled flight into terrain accidents
The ATSB reviewed several LAT and multi-engine water-bomber CFIT accidents during the investigation. The following 3 LAT accidents from Canada and the US were discussed with various personnel during the investigation.
Canada
Cranbrook, British Columbia – 2003
On 16 July 2003, a Lockheed L-188 Electra (Tanker 86) collided with terrain, fatally injuring the 2 crewmembers, during the go-around from a first partial retardant drop (A03P0194). In the final seconds before impact there were 2 separate retardant drops into the trees and ground witnesses heard the engine noise level increase significantly. The Transport Safety Board (TSB) of Canada noted that the ‘ridge that the aircraft struck blended into the rising terrain and was not obviously separate from its surroundings.’ The TSB published the following findings as to causes and contributing factors:
For undetermined reasons, the Electra did not climb sufficiently to avoid striking the rising terrain.
Given the flight path and the rate of climb chosen, a collision with the terrain was unavoidable.
The characteristics of the terrain were deceptive, making it difficult for the pilots to perceive their proximity and rate of closure to the rising ground in sufficient time to avoid it.
Lytton, British Columbia – 2010
On 31 July 2010, a Convair 580 (Tanker 448) collided with terrain, fatally injuring the 2 crewmembers, while crossing the edge of a ravine in the side of the Fraser River canyon before descending on the fire located in the ravine (A10P0244). The TSB findings as to causes and contributing factors included the following:
Visual illusion may have precluded recognition, or an accurate assessment, of the flight path profile in sufficient time to avoid the trees on rising terrain.
Visual illusion may have contributed to the development of a low energy condition which impaired the aircraft performance when overshoot action was initiated.
United States
Modena, Utah – 2012
On 3 June 2012, a Lockheed P2V-7 (Tanker 11) collided with terrain while following the Lead Plane onto final for its second retardant drop of the day at the same location (WPR12GA243), fatally injuring the 2 crewmembers. From their analysis of the 2 drops using the flight recorders, the NTSB made the following observation:
The most significant difference between the first drop approach and the accident drop approach was that Tanker 11's first approach into the drop zone was initiated from a higher altitude, about 1,000 feet above the ridge line surrounding the west side of the fire, and had a relatively steady rate of descent on to the final drop course. In comparison, the accident flight approached the final drop course from a lower altitude that approximated the elevation of the ridge lines surrounding the west side of the drop zone in level flight while it turned onto the final drop course.
The CVR revealed an ‘airspeed’ call from the first officer about 2 seconds before impact but no altitude or height calls. The NTSB determined the probable cause(s) of the accident to be:
The flight crew’s misjudgement of terrain clearance while maneuvering for an aerial application run, which resulted in controlled flight into terrain. Contributing to the accident was the flight crew’s failure to follow the lead airplane’s track and to effectively compensate for the tailwind condition while maneuvering.
The hidden hill visual illusion
The ATSB discussed previous LAT CFIT accidents and the topic of visual illusions in the low-level environment with the Bomber 139 captain. The TSB of Canada explored the problem of visual illusions during low-level flight in their reports of CFIT LAT accidents at Cranbrook, British Columbia (2003) and Lytton, British Columbia (2010). The Cranbrook accident was during the go‑around from a partial drop and the Lytton accident was during the approach to the drop zone. They concluded that visual illusion may have contributed to the accidents by delaying the crew’s recognition of the terrain.
The Bomber 139 captain presented lessons learned from the NTSB’s report into the LAT accident at Modena, Utah (2012) at the US National Aerial Firefighting Academy for a period of 3–4 years. During this period, the captain developed a belief that the crew of Tanker 11 experienced the ‘hidden hill’ illusion, which occurs when the terrain in the foreground blends into the terrain in the background, consistent with the TSB reports. The captain reported that ‘hidden hill’ was a common industry term they used in their annual CFIT prevention training and the ATSB noted the Tanker 11 accident was one of the case studies in the operator’s CFIT prevention training package.
While the ATSB was at the B737 LAT accident site in WA, the Bomber 139 captain visited the site with senior management personnel from the operator. At the start of the visit, the ATSB escorted them to the location of the start of the accident drop, which provided them with a view of the accident site from across the depression. The captain later reported the following observation:
If you looked away from where the airplane hit to where the vegetation still existed. It was hard to see any depth or any descent throughout that at all or the fact that there was a rise on the other side.
Safety analysis
Introduction
Bomber 139 conducted 3 flights on that day, which was the last day of the flight crew’s tour of duty. The first 2 flights each comprised a single full load drop at the fire ground with a return to Busselton. On the third flight, following an initial partial drop, the crew conducted a second drop, which released all the remaining retardant. The aircraft collided with terrain during the go-around from the second drop. The wreckage and site examination, meteorological information, flight data recorder (FDR), cockpit voice recorder (CVR) and flight crew interviews found no technical fault with the aircraft, evidence of flight crew fatigue or hazardous weather condition that contributed to the accident.
This analysis will discuss the operational and human factors at the fire ground that influenced the accident, in addition to the operator and tasking agency standard operating procedures (SOPs). It will also discuss the need for national LAT SOPs following this accident and a previous collision with terrain of a Lockheed C-130 LAT during the go-around from a partial load drop in New South Wales on 23 January 2020 (ATSB investigation AO-2020-007).
Accident sequence
On Bomber 139’s arrival at the fire ground on the first flight of the day, Birddog 125 (BD125) provided a Show-Me profile for Bomber 139 before Bomber 139 conducted a close left-hand circuit to the target with BD125 in the Chase-Position. The fire was burning on the right side of the drop line, which kept the circuit clear of smoke.
On arrival for the second drop, BD125 once again set Bomber 139 up with a left-hand circuit to the target for a drop flown by BD125 in the Chase‑Position, but this time without a Show-Me profile. The left-hand patterns clear of the smoke provided Bomber 139’s captain with a clear view of the drop zone and exit during the approach to the target.
When Bomber 139 arrived at the fire ground on the third (accident) flight, BD123 had replaced BD125. In preparation for the drop, BD123 briefed Bomber 139 that the drop zone was clear of ground crew, there were no hazards, and that it was a downhill drop. The captain declined BD123’s offer of a Show-Me profile, consistent with the second flight. However, the captain accepted a Lead profile right-hand circuit, which was inconsistent with the earlier flights.
The right‑hand pattern was chosen to keep them clear of smoke, as the plan was to tag and extend an existing line of retardant downhill into a depression towards the south with the fire burning to the east of the line. It also meant that the captain, in the left seat, was sitting on the outside of the circuit, which made it more difficult to view the drop zone on the downwind and base legs.
Bomber 139 then followed BD123 on a ‘wide’ right-hand circuit pattern with a final approach and descent to the target down the right side of the smoke. The captain, who preferred a closer circuit pattern to maintain visual contact with the drop zone and exit during the approach, had trouble identifying the start of the drop (a road crossing) on the first approach. The captain’s difficulty identifying the road was likely due to the wide right-hand circuit pattern and resulted in the captain’s attention becoming focussed on sighting it for the start of the drop.
During the drop the captain detected that they were not on the correct line to keep the retardant drop clear of the burnt area. Therefore, they stopped the drop and conducted a go-around from the high ground with the fire in the depression burning across their path. The elevation of the terrain beneath at the time of that go-around was higher than the elevation of the terrain at the accident site, which was on the far side of the depression. Therefore, the accident ridgeline remained below the horizon for the crew on the first drop, potentially obscured by smoke from the fire in the depression and likely indistinguishable from the surrounding terrain due to the relatively consistent vegetation coverage.
The captain’s decline of the Show-Me profile, wide right-hand circuit, Birddog brief of a downhill drop and subsequent go-around from the high ground, meant that the captain did not expect, or detect, rising terrain in the exit path prior to attempting the second drop.
The operator had adopted 150 ft as their standard target drop height. However, a low drop height and speed would improve the accuracy of a drop at a low coverage level. The crew was using a low coverage level [3] throughout the day and on the 2 previous flights that day, Bomber 139 recorded minimum drop height parameters of 46 ft and 69 ft with the engines at 60–70% N1. When the thrust levers were advanced at the end of each drop, there was an immediate positive response in N1, airspeed and vertical speed. The minimum parameters on the first (partial) drop of the accident flight were 78 ft and 124 kt at about 70% N1. Following the partial drop, when the captain advanced the thrust levers for the go-around there was once again an immediate positive response in N1, airspeed and vertical speed.
The captain was aware of the need to advance the thrust levers before the end of a drop if idle thrust was used. However, the accident drop was a partial load that only took 5 seconds and encompassed a downhill section with rising terrain in the exit that the captain was not aware of. Consequently, when the captain advanced the thrust levers about mid-way through the drop, there was a delay in the engines accelerating to go-around thrust which resulted in a low and decreasing aircraft energy state at the end of the drop and the collision with rising terrain in the exit path.
Energy management
A comparison of the drops conducted by Bomber 139 on the day of the accident indicated that N1 was a key parameter for a successful go-around and no performance problems were evident when N1 was in the region of 60–70% at the end of the drop. Variation in the N1 acceleration profile data at about 40% on the accident drop indicated that a slower engine acceleration occurred below this point, which was consistent with an idle thrust setting. However, the industry preference was for drops to be conducted downhill and consequently, the operator reported it was not practical to prescribe a minimum N1. Instead, they trained their pilots to advance the thrust levers during the drop if idle thrust was required at the start of the drop.
During the accident drop, Bomber 139’s captain advanced the thrust levers about mid-way through the drop, which provided insufficient time for the engines to respond. The ATSB found this would likely be the case for partial drops and drops conducted at higher coverage levels, due to the shorter drop time. If idle thrust was used in these scenarios, a safe go-around would depend on the LAT having sufficient energy, in terms of height and airspeed, to maintain terrain clearance until the engines accelerated to go-around thrust.
When considering the drop height parameter, the ATSB found that the US Interagency Airtanker Board (IAB) had investigated and determined that 150 ft was a LAT minimum safe drop height for their airtanker evaluation process. This was the reference drop height in the US airtanker and aerial supervision standards for a LAT.
Minimum drop heights were developed to reduce the forward momentum of the retardant cloud such that it would rain down vertically over the vegetation to prevent shadowing and minimise the hazard to ground personnel from falling debris. However, the retardant cloud can be subject to wind‑induced drift during the drop, which makes higher drop heights unsuitable due to the loss in coverage and incentivised lower drop heights over light fuel loads to improve accuracy.
Given the above factors, and noting that Bomber 139 was conducting drops significantly below 150 ft, there was no evident justification for changing the use of 150 ft as a LAT minimum drop height standard. Nevertheless, any increase in drop height would improve the aircraft energy state and therefore the safety of the flight crew.
The operator used a drop speed of 1.25 Vs for their drop configuration, which was based on the IAB minimum drop speed for their testing. The drop configuration was based on the flap setting and weight of the aircraft at the start of each drop. If a series of partial drops were conducted, then the flight crew would lower the target drop speed between each drop in accordance with the table of aircraft weights and speeds on their checklist.
While the IAB drop testing permitted drop speeds between 1.25 Vs and Va, the US Forest Service (USFS) explained that higher drop speeds can shear the retardant column at the tank opening and reduce the coverage level. Therefore, while an increase in the drop speed would improve the energy state of the aircraft, it would also require testing to ensure the required coverage level for effective fire suppression was maintained.
While the target drop speed was 1.25 Vs and the operator had published a lower deviation limit of ‑5 kt, the recorded data from the 4 drops on the day of the accident revealed that it was only on the second drop that Bomber 139 maintained the target drop speed within the tolerance. During the first drop, the airspeed decayed about 25 kt below the estimated target drop speed before recovering to within the tolerance at the end of the drop. On the third and fourth drops, the airspeed decayed about 9 kt below the target drop speed during the drops.
The retardant drop is a manually flown contour flight manoeuvre in potentially rough air and over undulating terrain across a drop zone that has not been formally surveyed for obstacle clearance and gradient. Therefore, airspeed and height deviations could be expected. If a performance problem developed before the entire load was released, then the crew had the option to conduct an emergency dump to reduce the weight and increase the airspeed safety margin. However, if the drop speed was recalculated and lowered between partial drops, the safety margin for the go‑around was also reduced.
During the investigation, the operator reported to the ATSB that they believed the recalculation and lowering of the target drop speed was a ‘significant contributing factor to the accident.’ It was also noted by Boeing, from their analysis of the recorded data, that had Bomber 139 avoided the ridgeline, there was nothing to preclude the aircraft climbing away from the ground.
The ATSB’s analysis of energy-height revealed Bomber 139 would have gained about 39–90 ft if the recalculated target drop speed lower tolerance of 113–118 kt was maintained during the final run. As such, even considering the low operating height of the final drop, if the aircraft had been flown at or above the lower deviation limit (113 kt) of the reduced target speed of 118 kt, the ground collision would probably have been avoided.
The energy analysis also identified that when the accident end-of-drop speed was compared with the previous drop, the recalculation of the drop speed was a greater proportion of the energy‑height loss (65%) than flying slower than the recalculated target speed (35%). The full load target drop speed would have provided them with +167 ft of energy-height to their target accident drop speed and +257 ft of energy height to their accident drop speed. Therefore, while the ATSB concluded that lowering of target drop speed between partial drops was not a contributing factor to the accident, it significantly reduced the terrain clearance energy‑height safety margin.
Crew resource management
Analysis of the cockpit voice recorder (CVR) for the accident flight revealed the Bomber 139 captain and co-pilot were working cooperatively with a division of duties during the set-up for the first drop. Between the first and second drop, they were again working cooperatively to track the position of BD123, update their checks and set their aircraft up for the second drop. However, the CVR also revealed that the co-pilot was silent in the cockpit for about the last 70 seconds of the flight, during which Bomber 139 was flown below the operator’s standard target drop height and speed deviation limits published in their flight crew operations manual (FCOM) Retardant drop procedure and with the engines at idle. In accordance with the FCOM procedure, deviating outside of the limits of either of these parameters required a ‘call-out’ from the pilot monitoring, which was the co-pilot.
The co-pilot had been employed by the operator for less than a year and was aware of the 150 ft standard for drop heights, although they also expressed a belief that the accident drop height was about 100 ft. The co-pilot also believed there was no minimum drop height and indicated that they had interpreted the 150 ft standard as a maximum drop height to mitigate the potential adverse effects of the wind on the fall of the retardant. On the day of the accident, all 4 drops were conducted significantly below 150 ft, which likely reinforced the co‑pilot’s interpretation of 150 ft as a maximum height and was consistent with the idea that the wind could reduce the accuracy and coverage level at higher drop heights.
The operator’s FCOM pre-drop checklist included setting the radio altimeter decision height bug to the target drop height. The 150 ft drop height was assumed knowledge in the operator’s organisation as they had adopted the IAB recommended minimum drop heights, which complied with their USFS contract requirements. However, the setting of the decision height bug to the drop height was not included in their quick reference handbook normal checklist and was not practiced by them.
Despite the published FCOM requirement, the operator believed that setting the decision height bug at their target drop height would result in a distraction if the decision height light cycled on and off over undulating terrain. Therefore, as the captain had not briefed a target drop height and the co-pilot had interpreted the 150 ft as a maximum drop height, the co-pilot did not have a minimum reference drop height to monitor against the deviation limits in the FCOM. This probably led to the co‑pilot’s silence about the low height during the accident drop.
The co-pilot reported the airspeed indicator was one of their primary flight instruments they were scanning during the drop, and that they believed it was indicating their target drop speed of 118 kt throughout the run. Recorded data indicated the airspeed went below, and remained below, the lower deviation limit about 2 seconds before the start of the drop after fluctuating intermittently above and below the lower limit during the approach. However, the co-pilot did not detect and announce the low and decreasing airspeed.
The second approach was flown through the smoke and the CVR indicated the captain was having trouble identifying the start of the drop. As the co-pilot was also looking for the target and observed BD123 deploy smoke over the target, they were potentially distracted from the airspeed indicator during the approach.
Within 2–3 seconds of the start of the drop, the captain started to advance the thrust levers at which stage the co-pilot was anticipating the flap retract call for the go-around. The ATSB was unable to determine why the co-pilot did not recognise the low and decaying airspeed. However, it is possible that the short duration of the drop might have resulted in the co-pilot shifting their attention to the vertical speed indicator, altimeter and flap lever in preparation for the go-around once the captain started to advance the thrust levers.
The operator reported their crew resource management (CRM) philosophy was to brief first and then only announce deviations as this minimised distractions during the retardant drop. However, this practice did not employ all the resources at their disposal to mitigate the risk of a low energy state developing. While they considered the decision height bug to be a distraction if it was set at the target drop height, they had not considered setting the bug at the lower deviation limit to assist the pilot monitoring duties. They also did not brief a target drop height if the captain planned to vary the drop height from their 150 ft standard, which resulted in the co-pilot being left ‘out‑of‑the‑loop’ in terms of their responsibility to monitor the target drop height.
The pilot monitoring call-outs in the operator’s retardant drop procedure were reactive to exceeding the target drop height or drop speed deviation limits. They did not include proactive ‘approaching target height/speed’ or ‘on height/speed’ call-outs. Proactive announcements confirm to other crewmembers that the pilot monitoring is conducting their duties and alerts the pilot flying to the flight path and energy state of the aircraft.
The operator’s expectations of pilot monitoring duties were presented in their CRM training but their controlled flight into terrain prevention training package did not present their CRM and SOPs as prevention strategies. Retardant drops are conducted to unsurveyed areas, which may result in lower safety margins than an approach to, or departure from, an airport. Hence the application of CRM and SOPs to managing the energy state of the aircraft should be as important for a retardant drop as for a departure or an arrival.
According to the US Federal Aviation Administration’s (FAA) advisory circular on standard operating procedures and pilot monitoring duties for flightdeck crewmembers, effective CRM is founded on SOPs. Therefore, while the operator’s pilot monitoring announcements were reactive to a low energy state, the ATSB could not conclude that this CRM-related aspect contributed to the accident due to the conflict between the operator’s procedures and actual practice. However, the ATSB concluded that the reactive nature of the pilot monitoring duties in their retardant drop procedure increased the risk of their aircraft entering an unrecoverable energy state and therefore have assessed it as a safety issue for Coulson Aviation.
Standard operating procedures
During the ATSB’s 2020 C-130 LAT accident investigation, it was apparent that the crew had developed an elevated level of risk tolerance for hazardous weather conditions. While the loss of the crews’ lives and lack of CVR data limited the ATSB’s ability to explore their pre-flight and tactical decision-making, the ATSB did note that there were no ‘circuit-breakers’ in the system to mitigate the crews’ acceptance of a task in the prevailing conditions. The operator had not imposed weather limits or a pre-flight risk assessment and the tasking agency did not have a policy and procedure to manage the task rejections that unfolded throughout the day.
Following the Bomber 139 accident, the co-pilot reported to the ATSB that they did not believe there was a minimum drop height. The ATSB subsequently found that neither the operator nor the tasking agency had published a drop height. While the operator had adopted their USFS contract standard of 150 ft as their standard target drop height, this was assumed knowledge within the organisation and was not published as a SOP. Consequently, captains could exercise their own judgement to improve accuracy if there was no contractual limit imposed. Their contract for services with the National Aerial Firefighting Centre (NAFC) did not impose a minimum drop height but required the operator to comply with the Member SOPs for their nominated operational base. The WA LAT SOPs did not impose a drop height limit and therefore the Bomber 139 crew could conduct their drops below 150 ft without breaching their contract or published SOPs.
The history of the development of airtanker drop heights revealed the primary aims were to minimise the risk to ground personnel from falling debris and prevent shadowing of the vegetation. The drop height safety requirement for ground personnel was published by the USFS in 2000 (Lovellette) and was later reiterated with a safety alert in 2019 following the fatal injury of a ground firefighter from a retardant drop in 2018. The WA LAT SOPs managed the safety risk to ground personnel by prohibiting drops before the drop zone was confirmed clear. This confirmation was communicated between the Birddog aircraft and Bomber 139 on the accident flight, which meant that the ground personnel safety requirement was not applicable to the drop height on this occasion.
The history of drop tests also revealed that wind speed and drop height affected the drop pattern and consequently the effectiveness of the drop. Greater wind speeds distorted the drop pattern at the lower coverage levels (Suter, 2005). When released from a sufficient height to stop the forward momentum of the retardant, Suter (2005) noted that the cloud was susceptible to wind erosion. Therefore, lower drop heights improve the drop pattern at low coverage levels. This knowledge may incentivise pilots to conduct lower drops, and operators and tasking agencies to accept this practice.
In this accident, the ATSB found that a low drop height was a contributory factor to the low energy state and collision with terrain during the exit from the drop. According to the FAA’s AC 120-71B (2017) Standard Operating Procedures and Pilot Monitoring Duties for Flight Deck Crewmembers, crew performance is founded on SOPs and pilot monitoring performance can be improved with the development of effective SOPs. Without a published SOP, the Bomber 139 captain could exercise drop height discretion and the co-pilot did not have a deviation parameter to monitor and call-out. Therefore, the ATSB has assessed the lack of a minimum drop height SOP as a safety issue for Coulson Aviation.
Furthermore, the fireground is an area of operations where multiple operators are required to interact. This introduces the problem of non-standard procedures between operators and the potential for unforeseen risks to emerge. In this accident, the Birddog operator had published a minimum drop height SOP. However, neither the LAT operator, nor the relevant WA government tasking agencies— the WA Department of Fire and Emergency Services and Department of Biodiversity, Conservation and Attractions—had published a minimum drop height.
The tasking agency SOPs provide a mechanism for the integration and standardisation of their aerial firefighting operation and for them to take the lead on setting the quality and safety criteria they require from the aerial firefighting effort. Therefore, the lack of a minimum drop height SOP is considered to be a safety issue for the WA Department of Fire and Emergency Services and Department of Biodiversity, Conservation and Attractions.
National large air tanker standard operating procedures
Aviation is a federally regulated activity but there is no federal authority with the operational responsibility for aerial firefighting. In 2003, the National Aerial Firefighting Centre (NAFC) was formed by the Australasian Fire and Emergency Services Authorities Council with the support of federal, state and territory governments. Their state and territory Members agreed that a single contract for each operator would facilitate the movement of assets between jurisdictions. However, the operating procedures that applied in each jurisdiction remained each Member’s responsibility.
While this may not increase risk for aerial firefighting assets that remain within a single jurisdiction throughout the season, LATs have been identified as having the capability to operate in more than one jurisdiction on the same day. Furthermore, the 2020 Royal Commission into National Natural Disaster Arrangements identified LATs as assets that should be tasked according to ‘greatest need’ on a national rather than jurisdictional basis.
The LATs and their aerial supervision do not operate in isolation and must be integrated into each jurisdiction where they operate. Therefore, any inconsistencies or omissions between tasking agencies’ SOPs will increase the complexity of risk management activities as it will be more difficult to assess and manage the associated risks. On the day of the Bomber 139 accident, the LAT and Birddog aircraft were conducting tactical flight profiles at the fireground, which were consistent with the Birddog operator and US National Wildfire Coordinating Group SOPs, but were not reflected in the WA LAT SOPs. Bomber 139 was also conducting drops without a prescribed minimum safe drop height or emergency overrun procedures under their contract for services.
The WA LAT target identification procedures (tactical flight profiles) were consistent with the 2018 NSW LAT procedures published at the time of the C-130 accident. However, NSW had published a LAT drop height of 150 ft but WA had not published a drop height, and where WA had prescribed the drop exits should be downhill, NSW had not made this explicit. Consequently, a different standard or no standard existed in each agencies’ document, which indicated an inconsistent approach to the development and implementation of LAT SOPs.
In contrast, the US standards for LAT and aerial supervision operations reviewed by the ATSB consistently reported a 'minimum drop height of 150 ft’ for LATs. The USFS reported that the move in 1976 towards the development of national standards was accepted as a better way of operating. They captured the lessons learned from accidents and facilitated the movement of airtankers across state borders to operate at multiple firegrounds on the same day.
The ATSB noted that the US aerial firefighting standards were a collaborative effort with multiple signatories on each document. One of the challenges in compiling a standard is understanding what should, and should not, be included. The current process of each NAFC Member developing their own standards hampers an inter-agency collaborative process with stakeholder consultation to develop a set of best-practice SOPs.
The differences in the NAFC Members’ LAT SOPs, noted by the ATSB, were not based upon a complete review, only the circumstances surrounding the C-130 and B737 accidents. A comprehensive review of all Member LAT SOPs, while beyond the scope of this ATSB investigation, would likely find further inconsistencies and omissions. This work is best conducted by the key stakeholders, who are the NAFC Members, with input from the LAT operators, aerial supervision operators and air attack supervisors.
At the time of the C-130 and B737 accidents, there was no agency responsible for producing national aerial firefighting SOPs. Following the Royal Commission into the 2019/2020 bushfire season, a national Aviation Safety Group (ASG) was formed from the NAFC Members and a priority list developed, which included standardised doctrine. However, the ASG’s list of priorities did not explicitly identify LAT SOPs, despite the 2 recent LAT accidents and the intent for them to be deployed on a national ‘greatest need’ basis.
The ATSB considers the absence of national LAT SOPs a safety issue and considers the Australasian Fire and Emergency Services Authorities Council collaboration model through the NAFC Strategic Committee the most appropriate pathway to address this deficiency. The safety issue has been raised with the understanding that the LAT SOPs will either incorporate the LAT aerial supervision procedures or that the LAT aerial supervision procedures will be developed and implemented concurrently, noting the ASG has already prioritised a national LAT Lead Plane pilot training standard.
Findings
ATSB investigation report findings focus on safety factors (that is, events and conditions that increase risk). Safety factors include ‘contributing factors’ and ‘other factors that increased risk’ (that is, factors that did not meet the definition of a contributing factor for this occurrence but were still considered important to include in the report for the purpose of increasing awareness and enhancing safety). In addition, ‘other findings’ may be included to provide important information about topics other than safety factors. Safety issues are highlighted in bold to emphasise their importance. A safety issue is a safety factor that (a) can reasonably be regarded as having the potential to adversely affect the safety of future operations, and (b) is a characteristic of an organisation or a system, rather than a characteristic of a specific individual, or characteristic of an operating environment at a specific point in time. These findings should not be read as apportioning blame or liability to any particular organisation or individual. |
From the evidence available, the following findings are made with respect to the controlled flight into terrain involving Coulson Aviation Boeing 737-3H4, registered N619SW, at Fitzgerald River National Park, Western Australia on 6 February 2023.
Contributing factors
- During the retardant drop downhill, the aircraft descended significantly below the operator’s standard target drop height and airspeed and entered a high rate of descent with the engines at idle. While the engines were starting to accelerate at completion of the drop, the airspeed and thrust were insufficient to climb above a ridgeline in the exit path, which resulted in the collision with terrain.
- Prior to the retardant drop, the aircraft captain (pilot flying) did not detect there was rising terrain in the exit from the drop, which likely contributed to the captain allowing the aircraft to enter a low energy state during the drop.
- After arrival at the fireground, the aircraft captain (pilot flying) declined a ‘Show-Me’ run and was briefed by the Birddog pilot that it would be a downhill drop. Bomber 139 then conducted a go-around from the high ground after the first drop and was led to the target through the smoke on the second drop. These factors likely contributed to the captain not expecting or detecting the rising terrain in the exit path.
- The co-pilot (pilot monitoring) did not identify and announce any deviations during the retardant drop, which could have alerted the aircraft captain (pilot flying) to the low-energy state of the aircraft when it descended below the target drop height with the engines at idle.
- The flight crew did not brief a target retardant drop height and, contrary to published standard operating procedures, did not set it as a decision height reference on the radio altimeter. Subsequently, the co-pilot (pilot monitoring), who did not believe there was a minimum drop height, did not alert the aircraft captain (pilot flying) to the low-energy state of the aircraft.
- Coulson Aviation and the relevant Western Australian Government Departments had not published a minimum retardant drop height in their respective operating procedures for large air tankers. Consequently, the co-pilot (pilot monitoring), who did not believe there was a minimum drop height, did not alert the aircraft captain (pilot flying) to a drop height deviation prior to the collision. (Safety issue)
Other factors that increased risk
- The Coulson Aviation practice of recalculating the target retardant drop speed after a partial drop reduced the post-drop stall speed and energy‑height safety margins. (Safety issue)
- The Coulson Aviation crew resource management practice of limiting the pilot monitoring (PM) announcements to deviations outside the target retardant drop parameter tolerances increased the risk of the aircraft entering an unrecoverable state before the PM would alert the pilot flying. (Safety issue)
- Australian states and territories that engage in Large Air Tanker (LAT) operations have developed their own separate standard operating procedures (SOPs) for LATs and aerial supervision assets. This can result in safety requirements being omitted or misunderstood by the different tasking agencies, such as a minimum drop height, resulting in inconsistencies in the development and application of LAT SOPs. (Safety issue)
Safety issues and actions
Central to the ATSB’s investigation of transport safety matters is the early identification of safety issues. The ATSB expects relevant organisations will address all safety issues an investigation identifies. Depending on the level of risk of a safety issue, the extent of corrective action taken by the relevant organisation(s), or the desirability of directing a broad safety message to the aviation industry, the ATSB may issue a formal safety recommendation or safety advisory notice as part of the final report. All of the directly involved parties were provided with a draft report and invited to provide submissions. As part of that process, each organisation was asked to communicate what safety actions, if any, they had carried out or were planning to carry out in relation to each safety issue relevant to their organisation. Descriptions of each safety issue, and any associated safety recommendations, are detailed below. Click the link to read the full safety issue description, including the issue status and any safety action/s taken. Safety issues and actions are updated on this website when safety issue owners provide further information concerning the implementation of safety action. |
Drop speed recalculation
Safety issue number: AO-2023-008-SI-01
Safety issue description: The Coulson Aviation practice of recalculating the target retardant drop airspeed after a partial drop reduced the post-drop stall speed and energy‑height safety margins.
Inadequate procedural requirements
Safety issue number: AO-2023-008-SI-02
Safety issue description: Coulson Aviation and the relevant Western Australian Government Departments had not published a minimum retardant drop height in their respective operating procedures for large airtankers. Consequently, the co-pilot (pilot monitoring), who did not believe there was a minimum drop height, did not alert the aircraft captain (pilot flying) to a drop height deviation prior to the collision.
Inadequate procedural requirements
Safety issue number: AO-2023-008-SI-03
Safety issue description: Coulson Aviation and the relevant Western Australian Government Departments had not published a minimum retardant drop height in their respective operating procedures for large airtankers. Consequently, the co-pilot (pilot monitoring), who did not believe there was a minimum drop height, did not alert the aircraft captain (pilot flying) to a drop height deviation prior to the collision.
Crew resource management practice
Safety issue number: AO-2023-008-SI-04
Safety issue description: The Coulson Aviation crew resource management practice of limiting the pilot monitoring (PM) announcements to deviations outside the target retardant drop parameter tolerances increased the risk of the aircraft entering an unrecoverable state before the PM would alert the pilot flying.
Safety recommendation description: The Australian Transport Safety Bureau recommends that Coulson Aviation takes safety action to address their crew resource management procedures for retardant drops to reduce the risk of the aircraft entering an unrecoverable state before the pilot monitoring alerts the pilot flying.
National Large Air Tanker standard operating procedures
Safety issue number: AO-2023-008-SI-05
Safety issue description: Australian states and territories that engage in Large Air Tanker (LAT) operations have developed their own separate standard operating procedures (SOPs) for LATs and aerial supervision assets. This can result in safety requirements being omitted or misunderstood by the different tasking agencies, such as a minimum drop height, resulting in inconsistencies in the development and application of LAT SOPs.
Safety action not associated with an identified safety issue
Whether or not the ATSB identifies safety issues in the course of an investigation, relevant organisations may proactively initiate safety action in order to reduce their safety risk. The ATSB has been advised of the following proactive safety action in response to this occurrence. |
Additional safety action by Coulson Aviation
3 May 2023
Coulson Aviation increased the safety margins for large air tanker drops in Australia from 150 ft and 1.25 stall speed to 200 ft and 1.35 stall speed. This was promulgated on Operations Bulletin 2023-01 on 8 February 2023 and their B737 Fireliner normal checklist was amended accordingly.
October 2023
In October 2023, Coulson Aviation provided the ATSB with a copy of their master corrective action plan (CAP) document, which they had developed in response to the Bomber 139 accident. This comprised flight activities, ground activities, Operations Bulletins and Flight Operations Manual amendments under the following topics:
CAP 1: raise minimum drop speed and height
CAP 2: recalibration of airspeed during partial load drops
CAP 3: pre-drop planning and familiarization
CAP 4: pilot situational awareness
CAP 5: flight training exercises
CAP 6: exit flight path
CAP 7: communication and coordination with Birddog
CAP 8: adherence to standard operating procedures
CAP 9: crew resource management
CAP 10: human factors
CAP 11: continuous training and proficiency assessment.
Additional safety action by the Birddog operator
The Birddog operator reported that as part of their continuous improvement they removed their Lead Plane procedures from an annex in their Company Operations Manual and introduced a Lead Plane Standard Operating Procedures manual with expanded procedures in October 2023.
Additional safety action by the Western Australian Department of Fire and Emergency Services and Department of Biodiversity, Conservation and Attractions
In November 2023, the Department of Fire and Emergency Services, and the Department of Biodiversity, Conservation and Attractions released the Western Australian Aerial Fire Suppression Procedures 2023–2024. The draft version of this document was reviewed by their contracted operators and included a chapter for Large Air Tanker (LAT) Operating Procedures. The document included standard drop heights for all the aircraft types employed, procedures for task rejection, standdown and reinstatement of aviation resources after a safety incident, and a section on tactical flight profiles with the addition of the Lead and Chase-Position profiles.
Additional safety action by the Western Australian Department of Biodiversity, Conservation and Attractions
The Western Australian Department of Biodiversity, Conservation and Attractions advised that published drop heights for 2024–25 will be reviewed with the intent of prescribing a ‘minimum’ safe drop height, noting the actual drop height to safely achieve the objective is the pilot‑in‑command’s decision.
Glossary
AC | Advisory circular |
AFAC | Australasian Fire and Emergency Services Authorities Council |
AGL | Above ground level |
ASG | Aviation Safety Group |
BD | Birddog |
CFIT | Controlled flight into terrain |
CRM | Crew resource management |
CVR | Cockpit voice recorder |
DBCA | Department of Biodiversity, Conservation and Attractions (WA) |
DFES | Department of Fire and Emergency Services (WA) |
DH | Decision height |
FAA | Federal Aviation Administration (US) |
FCOM | Flight crew operations manual |
FDR | Flight data recorder |
FRAT | Flight risk assessment tool |
IAB | Interagency Airtanker Board (US) |
LAT | Large air tanker |
NAFC | National Aerial Firefighting Centre |
NSW | New South Wales |
NTSB | National Transportation Safety Board (US) |
NWCG | National Wildfire Coordinating Group (US) |
PF | Pilot flying |
PM | Pilot monitoring |
QRH | Quick reference handbook (FCOM Volume 3) |
RADS | Retardant aerial delivery system |
SOAD | State operations air desk |
SOP | Standard operating procedure |
US | United States |
USDA | United States Department of Agriculture |
USFS | United States Forest Service |
WA | Western Australia |
Sources and submissions
Sources of information
The sources of information during the investigation included:
- Australasian Fire and Emergency Service Authorities Council
- Birddog 123 pilot
- Bomber 139 captain and co-pilot
- Coulson Aviation
- General Electric Aerospace
- National Aerial Firefighting Centre
- New South Wales Rural Fire Service
- Queensland Fire and Emergency Services
- The Boeing Company
- United States Forest Service
- United States National Transportation Safety Board
- Victorian Department of Energy, Environment and Climate Action
- Western Australian Department of Fire and Emergency Services.
References
Australian Transport Safety Bureau (2022), Collision with terrain involving Lockheed EC130Q, N134CG, 50 km north-east of Cooma-Snowy Mountains Airport (near Peak View), New South Wales, on 23 January 2020 (AO-2020-007). Retrieved from https://www.atsb.gov.au
Federal Aviation Administration (2004), Crew Resource Management Training (AC 120-51E). Retrieved from https://www.faa.gov
Federal Aviation Administration (2017), Standard Operating Procedures and Pilot Monitoring Duties for Flight Deck Crewmembers (AC 120-71B). Retrieved from https://www.faa.gov
Federal Aviation Administration (2018), Flight Test Guide for Certification of Transport Category Airplanes (AC 25-7D). Retrieved from https://www.faa.gov
Federal Aviation Administration (2021), Airplane Flying Handbook Chapter 4: Energy Management: Mastering Altitude and Airspeed Control (FAA-H-8083-3C). Retrieved from https://www.faa.gov
Interagency Airtanker Board (2013), Procedures and Criteria for the Interagency Airtanker Board (IAB). Retrieved from https://www.nwcg.gov
Lovellette G (2000), Safe Drop Height for Fixed-Wing Airtankers. Retrieved from https://www.fs.usda.gov
National Aerial Firefighting Centre (2021), National aerial firefighting strategy 2021-26. Retrieved from https://www.nafc.org.au
National Transportation Safety Board (1994), Safety study: A review of flightcrew-involved, major accidents of U.S. air carriers, 1978 through 1990 (NTSB/SS-94/01). Retrieved from https://www.ntsb.gov
National Transportation Safety Board (2014), Low altitude operation/event involving Lockheed P2V-7, N14447, Modena, Utah, 3 June 2012 (WPR12GA243). Retrieved from https://www.ntsb.gov
National Wildfire Coordinating Group (2017), Interagency Aerial Supervision Guide (PMS 505). Retrieved from https://gacc.nifc.gov
New South Wales Rural Fire Service (2018), Operating guidelines for air tankers operations. RFS, Sydney.
Suter A (2005), Aerial Delivery Systems User Information: Wind speed and drop height. Retrieved from https://www.fs.usda.gov
Transportation Safety Board of Canada (2004), Collision with Terrain, Air Spray (1967) Ltd., Lockheed L-188 Electra C-GFQA, Cranbrook, British Columbia 2.5 nm south, 16 July 2003 (A03P0194). Retrieved from https://www.tsb.gc.ca
Transportation Safety Board of Canada (2004), Collision with Terrain, Conair Group Inc., Convair 580 C–FKFY, Lytton, British Columbia, 9 nm SE, 31 July 2010 (A10P0244). Retrieved from https://www.tsb.gc.ca
United States Department of Agriculture Forest Service (2019), Standards for Airtanker Operations. Retrieved from https://www.fs.usda.gov
United States Department of Agriculture Forest Service (2019), Interagency aviation safety alert: Retardant safe drop height (IASA 19-02). Retrieved from https://www.fs.usda.gov
Western Australian Department of Fire and Emergency Services and Department of Biodiversity, Conservation and Attractions (n.d.), Large air tankers operational procedures 2021-22, v3.3.
Submissions
Under section 26 of the Transport Safety Investigation Act 2003, the ATSB may provide a draft report, on a confidential basis, to any person whom the ATSB considers appropriate. That section allows a person receiving a draft report to make submissions to the ATSB about the draft report.
A draft of this report was provided to the following directly involved parties:
- Australasian Fire and Emergency Service Authorities Council
- Birddog 123 pilot
- Bomber 139 captain and co-pilot
- Civil Aviation Safety Authority
- Coulson Aviation
- National Aerial Firefighting Centre
- New South Wales Rural Fire Service
- United States National Transportation Safety Board
- Western Australian Department of Fire and Emergency Services
- Western Australian Department of Biodiversity, Conservation and Attractions.
Submissions were received from:
- Australasian Fire and Emergency Services Authorities Council
- Birddog 123 pilot
- National Aerial Firefighting Centre
- Western Australian Department of Biodiversity, Conservation and Attractions.
The submissions were reviewed and, where considered appropriate, the text of the report was amended accordingly.
Appendices
Appendix A – SIGMET thunderstorm activity
Figure 18: Lightning strikes (red) at 1600
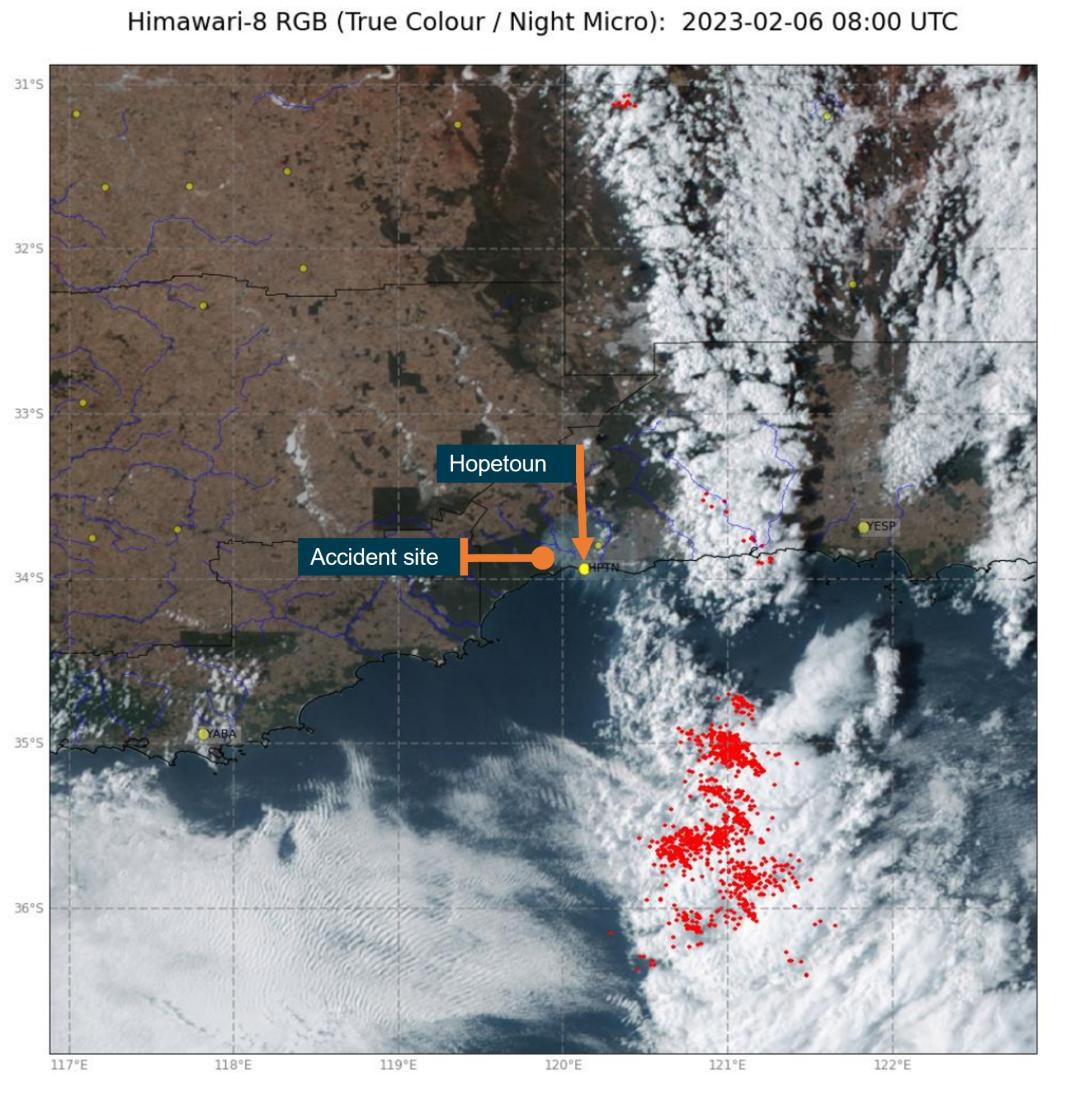
Appendix B – Flight data recorder plot
Figure 19: FDR plot of last 5 minutes of the accident flight with the last 2 drops
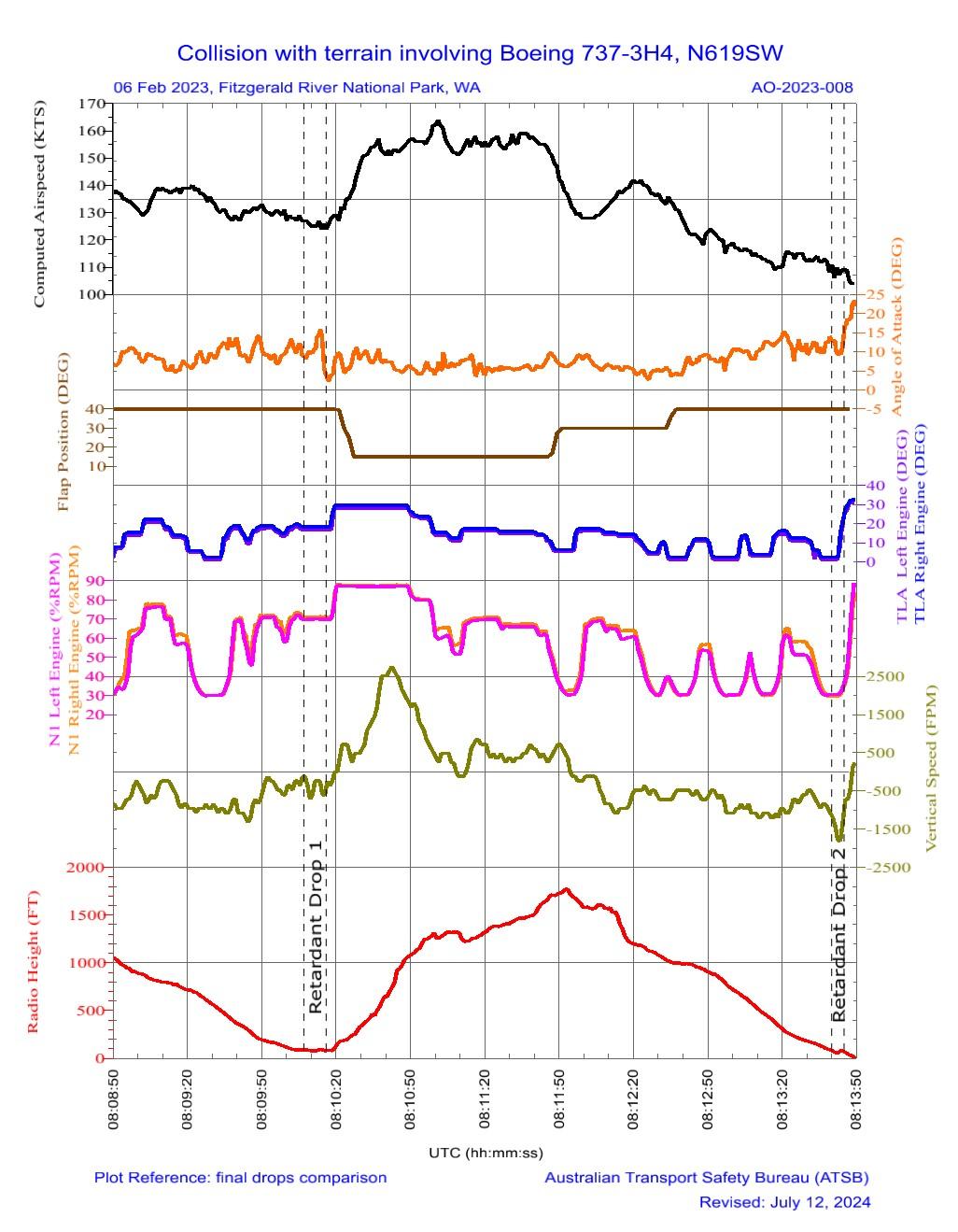
Purpose of safety investigationsThe objective of a safety investigation is to enhance transport safety. This is done through:
It is not a function of the ATSB to apportion blame or provide a means for determining liability. At the same time, an investigation report must include factual material of sufficient weight to support the analysis and findings. At all times the ATSB endeavours to balance the use of material that could imply adverse comment with the need to properly explain what happened, and why, in a fair and unbiased manner. The ATSB does not investigate for the purpose of taking administrative, regulatory or criminal action. TerminologyAn explanation of terminology used in ATSB investigation reports is available here. This includes terms such as occurrence, contributing factor, other factor that increased risk, and safety issue. Publishing informationReleased in accordance with section 25 of the Transport Safety Investigation Act 2003 Published by: Australian Transport Safety Bureau © Commonwealth of Australia 2024
Ownership of intellectual property rights in this publication Unless otherwise noted, copyright (and any other intellectual property rights, if any) in this report publication is owned by the Commonwealth of Australia. Creative Commons licence With the exception of the Commonwealth Coat of Arms, ATSB logo, and photos and graphics in which a third party holds copyright, this report is licensed under a Creative Commons Attribution 4.0 International licence. The CC BY 4.0 licence enables you to distribute, remix, adapt, and build upon our material in any medium or format, so long as attribution is given to the Australian Transport Safety Bureau. Copyright in material obtained from other agencies, private individuals or organisations, belongs to those agencies, individuals or organisations. Where you wish to use their material, you will need to contact them directly. |
[1] Pilot Flying (PF) and Pilot Monitoring (PM): procedurally assigned roles with specifically assigned duties at specific stages of a flight. The PF does most of the flying, except in defined circumstances, such as planning for descent, approach and landing. The PM carries out support duties and monitors the PF’s actions and the aircraft’s flight path.
[2] SARWATCH log: record of movement times for managing aircraft search and rescue times.
[3] The birddog is an intelligence-gathering aircraft, used to assess the fireground, determine the best flightpath and then lead the air tankers across the fireground and show them where to drop with a smoke generator. It is crewed by a birddog pilot and air attack supervisor.
[4] The primary air attack aircraft maintains a strategic overview of the situation, which includes communications with ground personnel, objectives for the air tanker operation and aircraft separation protocols.
[5] QNH: the altimeter barometric pressure subscale setting used to indicate the height above mean sea level.
[6] Vs: The stall airspeed or the minimum steady flight airspeed for the aircraft configuration.
[7] Prior to the first drop, the recorded flight management computer gross weight was 124,640 lb before being re-entered and reduced to 89,440 lb. The difference of 35,200 lb was equivalent to the aircraft’s retardant payload.
[8] A Show-Me run or Show-Me profile is a low-level pass made over the target using the physical location of the aircraft to demonstrate the line and start point of the retardant drop.
[9] The Lead profile is a low-level (below 500 feet AGL) airtanker drop pattern, made with the lead plane [Birddog] approximately 0.25 miles ahead of the airtanker.
[10] Coverage Level: The amount of retardant covering the ground or foliage expressed in gallons per 100 square feet.
[11] Minimum heights are in reference to the recorded radio altimeter height.
[12] All report references to drop times are based on the aircraft’s auxiliary telemetry unit data.
[13] N1: the rotational speed of the low-pressure compressor in a turbine engine.
[14] Computed airspeed is the airspeed recorded from the airplane air data inertial reference unit, which is the airspeed source for the flight crew (analog synchro) and Flight Data Recorder (digital databus).
[15] HIGH IDLE: The high idle speed is set at a level above the low idle setting to assure rapid engine acceleration during go-around and to assure adequate anti-ice performance. In flight, only high idle speed is allowed.
[16] The clock input to the flight data recorder was the captain’s clock, which was about 11.5 minutes ahead of actual time.
[17] The flap-40 stick shaker activation threshold was 20° angle of attack.
[18] MAYDAY: an internationally recognised radio call announcing a distress condition where an aircraft or its occupants are being threatened by serious and/or imminent danger and the flight crew require immediate assistance.
[19] The score is based on the Samn-Perelli 7-point fatigue scale, where 1 indicates fully alert and 7 indicates completely exhausted.
[20] Transport category: an airworthiness categorisation that applies to multi-engine aircraft primarily intended for regular public transport and/or cargo for hire or reward.
[21] The aircraft and retardant weights were published in pounds (lb), where 1 lb is approximately 0.4536 kg.
[22] The acceleration check time was consistent with the FAA Flight Test Guide for Certification of Transport Category Airplanes (AC 25-7D), in which the go-around thrust is the thrust available 8 seconds after starting to advance the thrust levers from flight idle to the go-around setting.
[23] Significant meteorological information (SIGMET): a weather advisory service that provides the location, extent, expected movement and change in intensity of potentially hazardous (significant) or extreme meteorological conditions that are dangerous to most aircraft, such as thunderstorms or severe turbulence.
[24] Isolated burnt patches were evident in the wreckage trail where engine parts had separated.
[25] Coordinated Universal Time (UTC): the time zone used for aviation. Local time zones around the world are expressed as positive or negative offsets from UTC.
[26] The Chase-Position profile is an observation position in trail of, and above the airtanker, at a position of 5 to 7 o'clock. It is used to verbally confirm or adjust the position of the airtanker when on final, and to evaluate the drop.
[27] The Birddog operator started to develop their SOPs in 2009 with input from the US National Interagency Fire Center. The NWCG is one of the National Interagency Fire Center programs.
[28] Using similar weights to the accident flight of 125,000 lb at the start of the drop and 90,000 lb at the end of the drop, Vs would have reduced from 107 kt at the start of a drop to 88 kt at the end of the drop. There was no stick shaker activation recorded during this drop as neither of the angle of attack sensors reached 20°.
[29] The fuel burn between drops was disregarded.
[30] Queensland Fire and Emergency Services clarified their document was a guide, which was developed for the use of their contracted LAT provider (not the accident operator) as well as any others that come into the state. They developed it in conjunction with their contracted LAT pilots and LAT-endorsed Air Attack Supervisors.
[31] NAFC reported that there were 2 LAT providers in Australia with one aligned to the USFS model and the other closer to the Canadian model.
[32] The preface for this document stated, ‘The Interagency Aerial Supervision Guide standardizes federal agencies, state agencies and local agencies in the accomplishment of aerial supervision positions as defined by the Incident Command System (ICS).’ It was subsequently renamed NWCG Standards for Aerial Supervision in February 2020.
[33] The NSW, USFS and NWCG documents were the versions current at the time of the C-130 LAT accident and have since been amended.
[34] The Interagency Airtanker Board (IAB) promotes standardization and cooperation among NWCG member agencies and airtanker-related industries in all aspects of aerial delivery systems utilisation. The IAB evaluates airtankers against established performance criteria and recommends their approval for use.
[35] Shadowing: where a combination of the forward velocity of the retardant and the height of the fuel/vegetation results in only one side of the fuel/vegetation being covered.
[36] The USFS provided example copies of 2010 and 2023 contracts to the ATSB during the C-130 and B737 LAT accident investigations.
[37] Safety alert IASA 19-02 followed the death of 1 and injury to 3 ground firefighters from a retardant drop that uprooted a tree and fell branches at California’s Mendocino Complex Fire in August 2018.
[38] Paragraphs bearing an asterisk (*) were subject to FAA certification testing.