Executive summary
What happened
On 28 January 2022, shortly before noon, the bulk carrier Goliath collided with the moored tugs York Cove and Campbell Cove in Devonport, Tasmania. The tugs, which were unmanned at the time, sustained significant damage and subsequently sank. Authorities ashore initiated pollution control and oil spill recovery measures and the ensuing loss of fuel and other oils from the tugs were largely contained. Goliath sustained minor damage to its bow while the tugs were both subsequently declared a constructive total loss.
What the ATSB found
The ATSB found that, in the process of a transfer of manoeuvring controls from Goliath’s bridge to the bridge wing, the correct steering mode was not selected. Consequently, control of the ship’s rudders remained at the wheel, inside the ship’s wheelhouse, while the master attempted to manoeuvre the ship in the swing basin using the bridge wing VecTwin joystick panel. The master’s manoeuvring orders, issued in the belief that the ship was in joystick steering mode, had the effect of increasing the ship’s speed as it closed on the tugs before colliding with them.
The investigation found that neither the master nor the second mate had undertaken the required bridge resource management (BRM) training and that BRM on board was ineffective. The design of the ship’s joystick system was also identified as having increased the risk as it was misleading and did not provide a positive visual confirmation that the correct steering mode had been selected.
Finally, the ATSB observed that, while the TasPorts risk assessment for Devonport had considered the potential for collisions between ships manoeuvring in the swing basin and smaller vessels in the vicinity, the risk of injury to personnel on board those smaller vessels was not specifically considered. On this occasion, it was largely fortuitous that there were no personnel on board the tugs at the time of the collision.
What has been done as a result
CSL Australia arranged for all deck officers serving on board Goliath, to attend bridge resource management (BRM) training ashore. Additionally, the ship’s health safety environment and quality (HSEQ) manager and HSEQ superintendent also undertook the training, and a new dynamic navigation audit was instituted to allow for regular audits focused on implementation of BRM on board. The safety management system requirement for BRM training was also incorporated into crew training schedules across the CSL Australia fleet.
Goliath’s VecTwin joystick panels were modified to incorporate a positive visual indication that joystick steering mode was selected, and the transfer of control checklist modified accordingly. The company’s standing orders, bridge checklists and the ship’s procedures on navigation, watchkeeping and passage planning were amended to specify the conditions under which the relief of watchkeeping officers could take place during pilotages or during extended manoeuvres.
TasPorts’ investigation into the accident resulted in several recommendations for proposed safety action, including recommendations to prohibit Goliath using the swing basin to berth port side alongside if vessels are berthed at berth number Three West, to introduce changes to the Devonport pilot exemption conditions, training, assessment, and renewal processes and to clarify the applicability of tidal restrictions relevant to Goliath’s port calls.
Safety message
The various concepts, techniques, and attitudes that together comprise bridge resource management remain among the most effective measures available to identify and eliminate, or rectify, human error. Training in the various elements that comprise effective BRM provides a foundation upon which competency may be built through experience and practice. In addition, the design of bridge systems can also play a part in mitigating the risks of human error by incorporating intuitive and conspicuous indications of correct operation and conversely, of errors or incorrect settings.
The occurrence
Overview
On 28 January 2022, the 143 m Australian-registered, bulk cement carrier Goliath (Figure 1) collided with the moored tugs York Cove and Campbell Cove in Devonport, Tasmania. The tugs, which were not manned at the time, sustained significant damage and sank shortly after. Authorities ashore initiated pollution control and oil spill recovery measures with the ensuing loss of fuel and other oils from the tugs largely contained. Goliath sustained minor damage to its bow while the tugs were both subsequently declared a constructive total loss.[1]
Pre-arrival activity
On the morning of 28 January 2022, Goliath was on passage from Melbourne, Victoria to Devonport, Tasmania. The ship had departed Melbourne the previous evening and was bound for the bulk cement facility at Devonport’s berth number One West, where it usually berthed port side alongside.
Figure 1: Goliath, alongside at berth number One West, Devonport
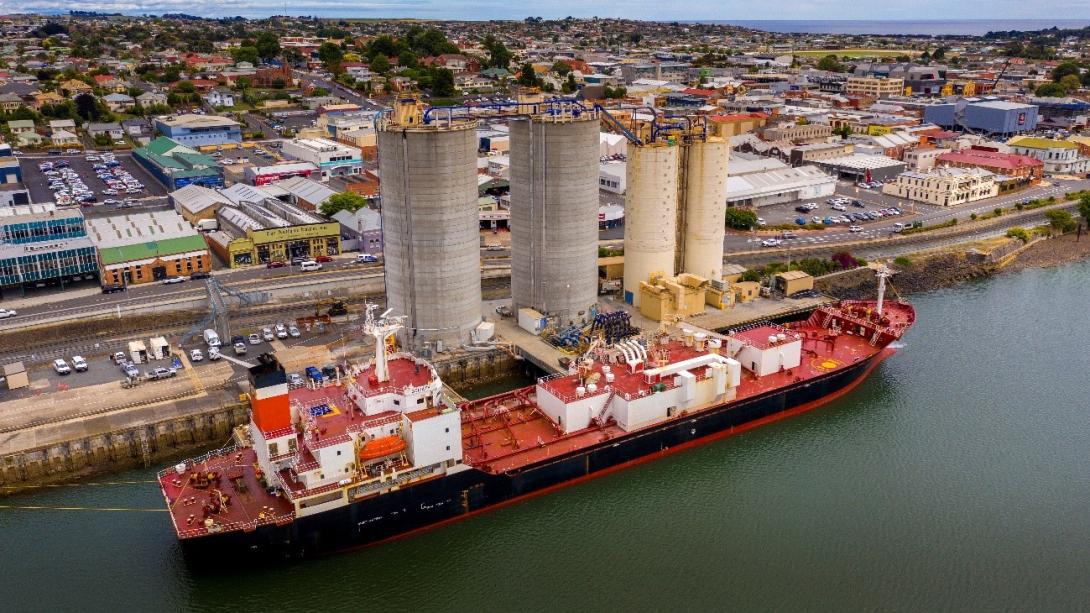
Source: TasPorts
Shortly after 1000 Eastern Daylight-saving Time,[2] the officer of the watch (third mate) began to complete the ship’s bridge arrival checklist in preparation for arrival at Devonport. This included checks of the bridge equipment and other machinery. By about 1020, most of the checks in the bridge arrival checklist had been completed, including checks of the ship’s steering gear,[3] whistle, and very high frequency (VHF) radios. By 1050, the deck crew reported that the ship’s anchors had been unsecured and made ready for use. Shortly after, the third mate began reducing the ship’s sea speed using the main engine slow down program. At about the same time, the master came to the bridge and, shortly after, took over the conduct of the ship. At about 1055, the master moved the main engine telegraph from ‘navigation ahead’ to manoeuvring ‘full ahead’.
At about 1106, as the ship approached Devonport port limits (Figure 2), the third mate tested the ship’s bow thruster and had the main engine put on stand-by for manoeuvring. Shortly after, the watchkeeping integrated rating (IR)[4] came to the bridge for helmsman duties. At about 1108, the master called Devonport vessel traffic service (VTS) on the port’s VHF radio working channel (VHF channel 14). The master reported the ship’s maximum draught of 6.6 m and pilotage exemption details to the VTS and requested permission to enter port limits and proceed inwards. The VTS granted permission and advised that there was no other traffic expected in the port.
The weather at the time was overcast with slight seas and a light north-easterly breeze. The tide was ebbing with low water at Devonport predicted at 1422 with a height of tide of 0.50 m.[5]
Figure 2: Section of chart Aus 164 showing Goliath’s track
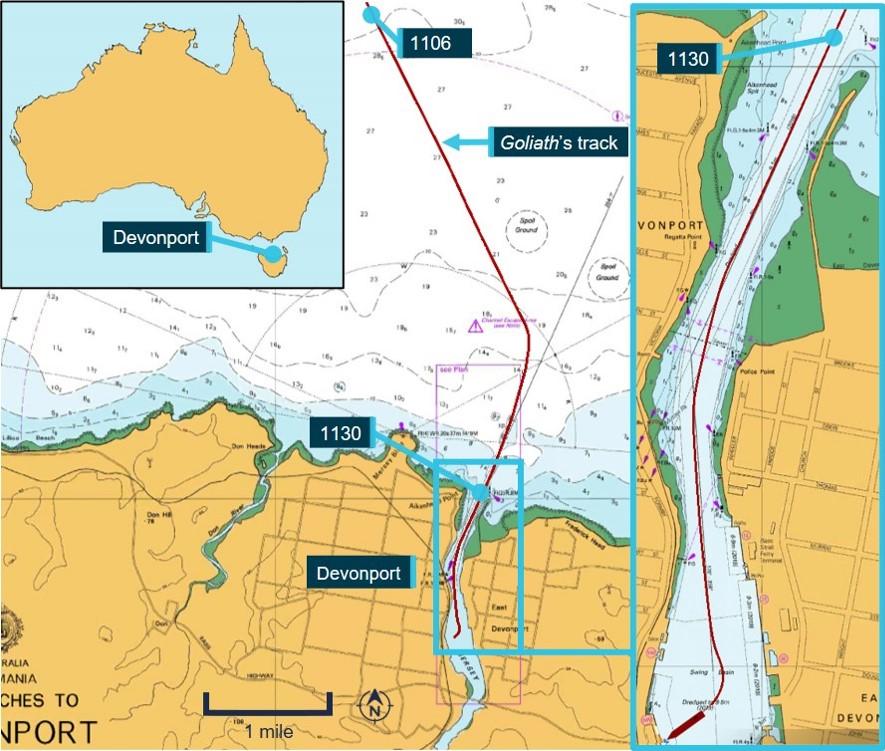
Source: Australian Hydrographic Office, annotated by the ATSB using electronically recorded data
At about 1110, the ship’s steering mode was switched from autopilot to manual steering using the steering mode selector switch located on the starboard side of the steering console (see the section titled Steering system), and the IR began steering. The master continued reducing the ship’s speed, moving the telegraph to ‘half ahead’ and by 1128, to ‘slow ahead’. Shortly before 1130, the chief mate came to the bridge and, after a brief hand over, relieved the third mate who proceeded to the aft mooring stations.
Navigation within port limits
At 1130, Goliath passed the breakwater inbound. At the time, the ship’s bridge team comprised the master, chief mate, helmsman, and the deck cadet.
At about 1140, the second mate came to the bridge with the intention of relieving the chief mate. The second mate and chief mate, situated to starboard of the steering console, began discussing the state of various ship’s machinery, personnel, and bridge equipment. The helmsman was steering, and the master was stationed to port of the steering console where the main engine telegraph, bow thruster controls and VecTwin steering control joystick were located (see the section titled Goliath’s manoeuvring system and Figure 3). By this time, the master had placed the telegraph on ‘dead slow ahead’ and shortly after, to ‘stop’.
Figure 3: Goliath's bridge layout showing the location of various controls and equipment
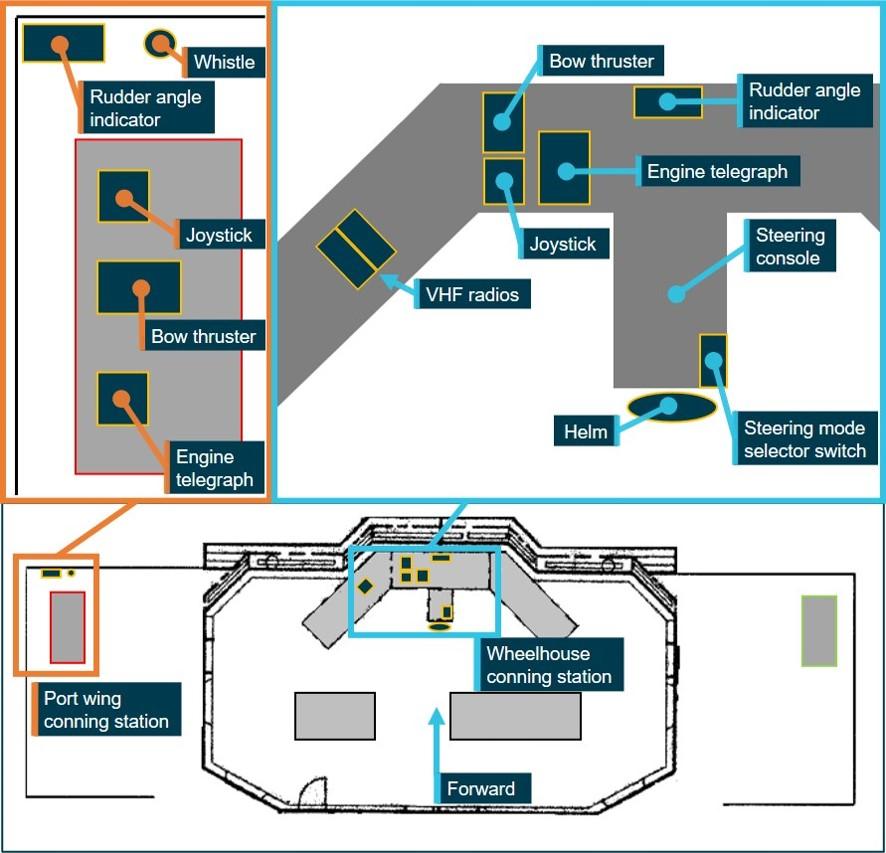
Source: CSL Australia, modified and annotated by the ATSB
At about 1142, crew on board the mooring lines boat Rubicon called Devonport VTS on VHF channel 14 advising that it was underway in preparation to assist with Goliath’s berthing. The call was acknowledged by VTS. Following this, at about 1143, Rubicon called Goliath on VHF channel 14, requesting a radio check. On board Goliath, the master asked the second mate to deal with the radio call as he was busy conducting the ship in the approach to the swing basin.
After a brief discussion with the master and chief mate about which radio to use, the second mate moved to the left of the master to use one of the 2 VHF radios located on the bridge-front console (Figure 4). One of those radios was generally used to maintain a listening watch on VHF channel 16[6] and the other to monitor working frequencies such as the port’s working channel (in this case, channel 14). A portable VHF radio was normally reserved for berthing communications (channel 6).[7] The second mate acknowledged Rubicon’s call on channel 14 and advised that the ship was standing by on channel 6.
Figure 4: Goliath's bridge showing location of various controls and equipment
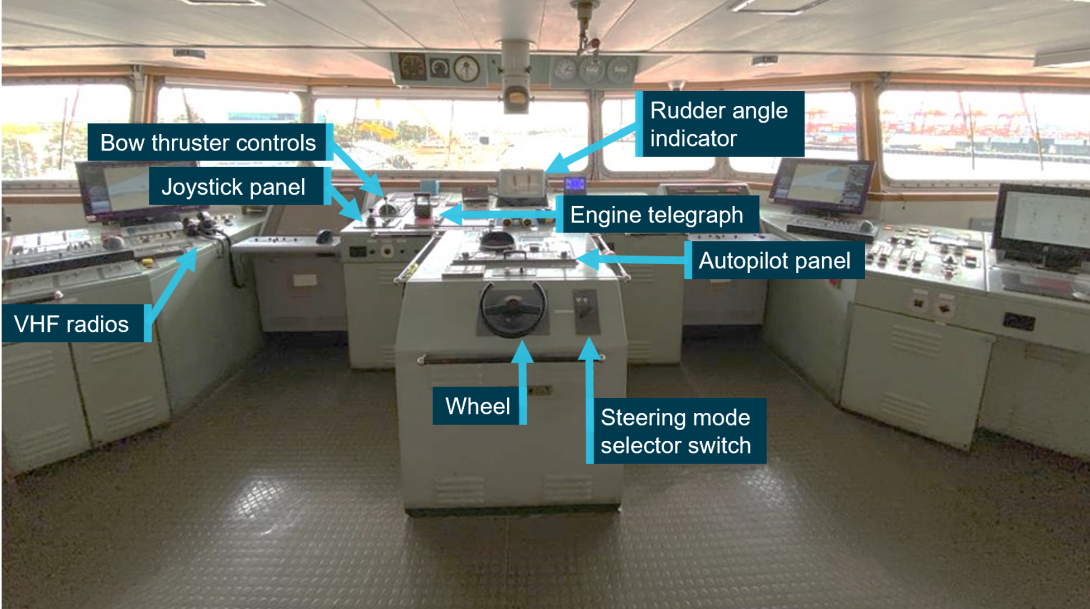
Source: CSL Australia, modified and annotated by the ATSB
By this time, the engine had been placed on ‘dead slow astern’ and the master used the main engine and bow thruster to commence slowly turning the ship to starboard in preparation to swing it to a northerly heading for approaching the berth. Shortly after, the engine telegraph was placed on ‘slow astern’ and, a few seconds later, the helmsman advised the master that the ship was no longer steering (that is, it was no longer responding to the rudder due to the ship’s decreasing speed). The master advised the helmsman that he was finished with the wheel and the helmsman promptly left the bridge for the aft mooring stations.
At about 1144, Rubicon’s crew again called the ship, requesting a radio check, this time on VHF channel 6. Recorded audio from Goliath’s voyage data recorder (VDR)[8] indicates that the call from Rubicon was almost certainly received on one of the 2 VHF radios on Goliath’s bridge-front console, indicating that one of the radios was set on channel 6. Following a brief period of confusion over which radio to use to respond, the second mate responded to the call using one of the bridge-front console radios. The second mate then remained beside those radios, to the left of the master, while the chief mate went to locate the portable VHF mooring radio. At about this time, a further brief VHF radio transmission between VTS and another vessel also resulted in the officers on the bridge voicing some confusion.
The collision
At about 1145, as the ship continued turning slowly to starboard, the master stopped the engine in readiness to transfer controls to the port bridge wing conning station.
As was normal practice on board, the master then called out to the chief mate that he was ready to ‘change over’ (that is, for controls of the ship’s steering and propulsion to be transferred to the port bridge wing conning station for the master to move outside, complete the swing and berth the ship). The second mate (who was closer to the port bridge wing door) verbally acknowledged the master’s order and recalled going out on to the bridge wing and taking control of the main engine, bow thruster and VecTwin steering system (joystick) on their respective panels on the port bridge wing console.
Once the second mate confirmed that the wing console was ready, the master walked out and took the con at the port bridge wing conning station (Figure 5). The chief mate, who had walked to the bridge wing door and observed the second mate taking control of the propulsion and steering at the wing console, then left the bridge and went down to the mess room.
Figure 5: Goliath's port bridge wing conning station (looking forward)
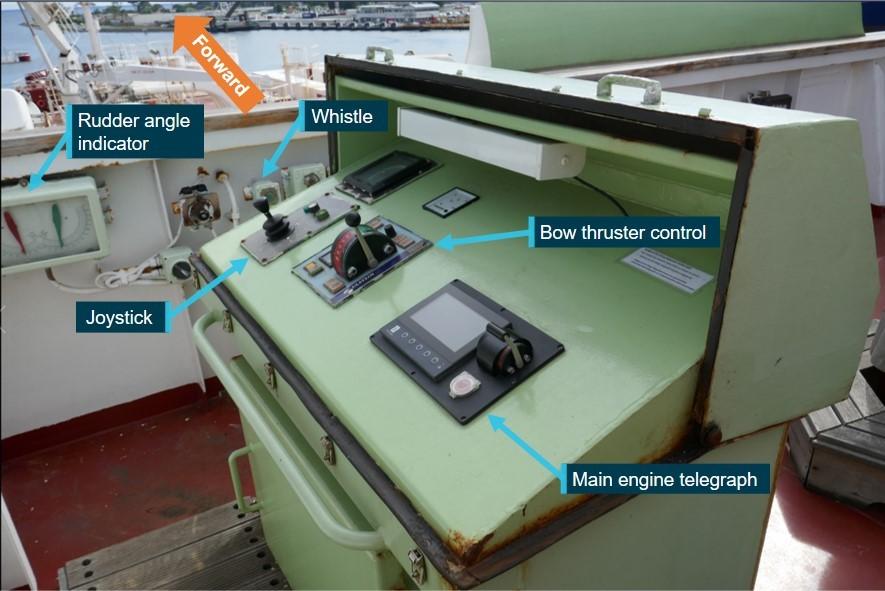
Source: ATSB
By this time, Goliath was turning slowly to starboard in the swing basin and its speed was about 1.2 knots. The third mate reported clearances to the shore from the ship’s port quarter while the bosun stationed on the foc’sle reported clearances ahead of the ship. At 1145:52, the master announced to the second mate that he was placing the bridge wing engine telegraph on ‘slow ahead’ (Figure 6). As was standard practice on board, the second mate went back inside the bridge and confirmed that the wheelhouse telegraph was appropriately replicating the master’s engine telegraph orders. The master set the VecTwin joystick to the ‘astern to port’ setting[9] and continued to use the bow thruster to swing to starboard. The second mate positioned himself just outside the wheelhouse door to monitor the ship’s swing and assist the master as required.
Figure 6: Section of chart Aus 164 showing Goliath's track and sequence of collision
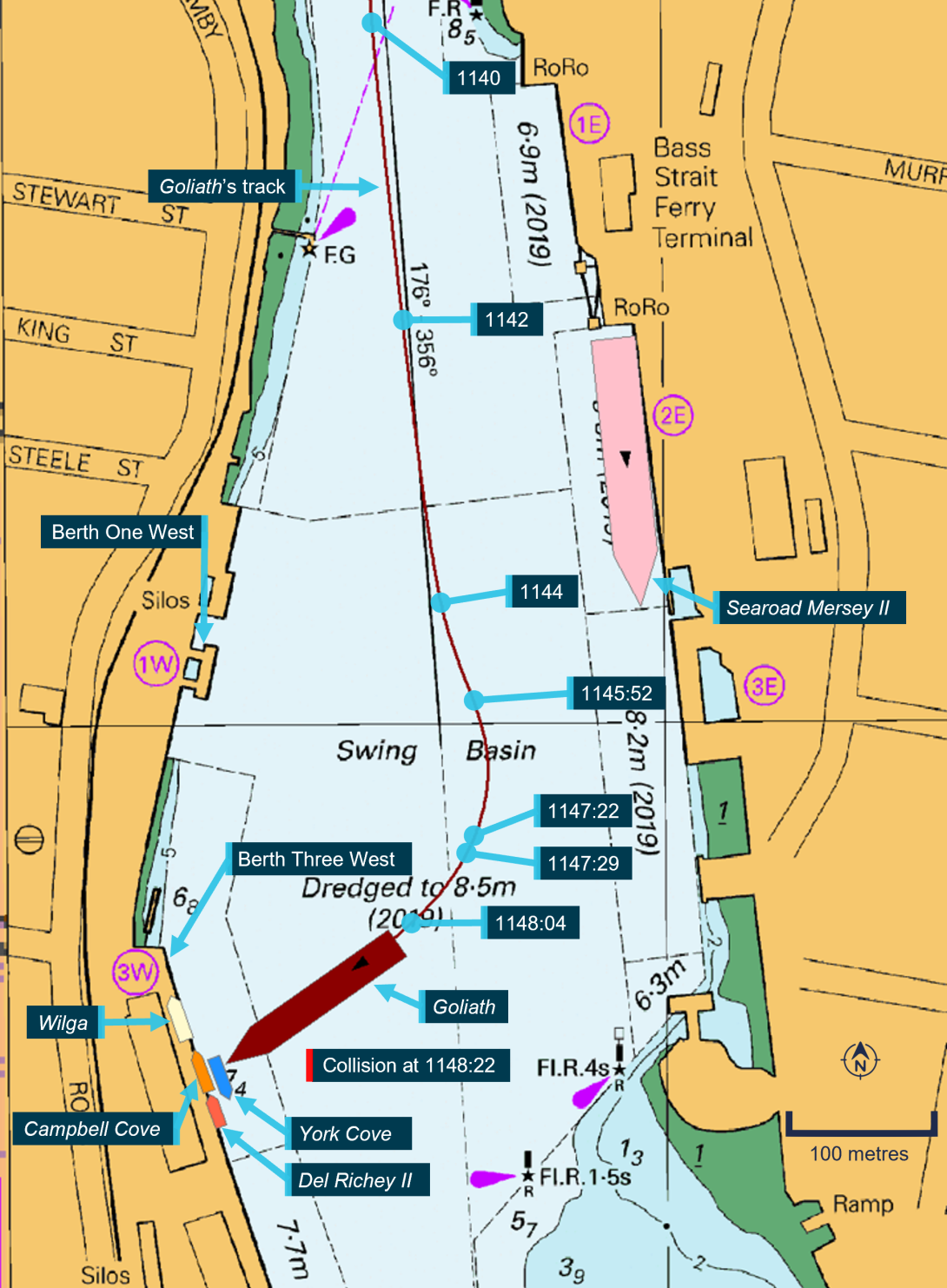
Source: Australian Hydrographic Office, annotated by the ATSB using electronically recorded data
As the manoeuvre progressed, the master felt that the ship was not swinging as expected and was closing with 2 tugs, which were moored at berth number Three West ahead. In an effort to arrest the ship’s headway, the master set the VecTwin joystick to the ‘astern’ setting[10] and, at 1147:22, placed the main engine at ‘half ahead’. A few seconds later, at 1147:29, the master used ‘full ahead’, but the ship’s headway continued to increase, with the speed now about 2.9 knots. Meanwhile, the bosun had begun reporting rapidly decreasing clearances to the tugs ahead. The bridge engine telegraph data logger shows that at 1147:41, the telegraph was placed at ‘half ahead’ before quickly being returned to ‘full ahead’. At 1148:04, the master placed the telegraph at ‘navigation ahead’ (that is, the maximum ahead engine telegraph setting). The ship’s speed had increased to 4 knots.
With the ship’s speed still increasing, the master checked the rudder angle indicator located in front of the port wing console and then observed that both rudders were still amidships and not at the angles corresponding to the VecTwin joystick setting as expected. The master called out to the second mate that the steering was not in VecTwin steering mode and immediately brought the engine telegraph to ‘slow ahead’ and then to ‘stop’.
At about the same time (1148:22), Goliath collided with the two tugs ahead. (Figure 7). The ship’s speed was 4.7 knots as it struck the port midships area of the tug York Cove, which was moored outboard, and alongside, of the tug Campbell Cove.[11] Both the tugs were severely damaged and began taking on water almost immediately. The tug Wilga and the fishing vessel Del Richey II, berthed to the north and south of the two damaged tugs respectively, were not impacted.
Figure 7: Goliath, immediately before the collision with the tugs
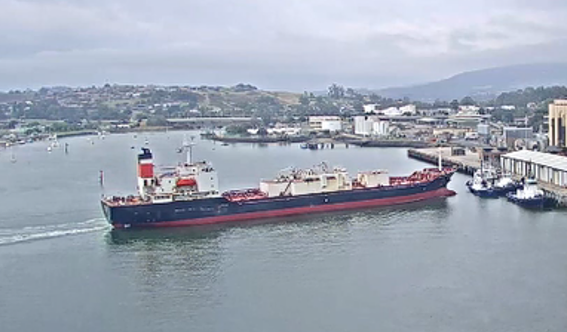
Source: TasPorts
On board Goliath, the second mate had run into the wheelhouse, checked the steering mode selector switch on the steering console and realised that it was still in manual steering mode. The second mate immediately switched it over to VecTwin (joystick) steering mode while the master placed the engine at ‘half astern’ followed by ‘full astern’ and, by 1148:31, at ‘emergency astern’.
At about 1149, crew on board the lines boat Rubicon called Devonport VTS on VHF channel 14 and reported that Goliath had collided with York Cove. Meanwhile, the fishing vessel Del Richey II, which was manned, began preparing to get underway and render assistance.
Shortly after, at about 1150, the second mate called Devonport VTS on VHF channel 14 and reported the collision. By this time, Goliath had started moving astern and the master decided to focus on getting clear of the tugs and berthing the ship. The chief mate, who had been resting in the mess room had felt the impact of the collision and come up to the bridge.
Subsequently, as the master manoeuvred the ship towards its berth, crew on deck began sounding the forepeak tank to check for possible hull damage. Meanwhile, the chief mate and second mate monitored the tank levels on the bridge’s ballast control screen.
Emergency response
At about 1154, two other vessels in the port (Searoad Mersey II and Torquay Ferry) called VTS on VHF channel 14 and advised that they were standing by to render assistance if required. Meanwhile, VTS notified key Tasmanian Ports Corporation (TasPorts)[12] personnel of the incident including the harbour master and deputy harbour master.[13]
On receiving advice of the collision, the TasPorts state operations centre[14] activated the port’s crisis management and incident management teams while port personnel began to organise oil spill response equipment and oil containment booms.
On board Goliath, its berthing now proceeded normally with the master using the engine, bow thruster and VecTwin steering joystick to bring the ship alongside. By 1159, the first mooring line had been passed ashore. At 1204, the master called VTS on the telephone about the collision and was informed that no one had been on board the damaged tugs. The master subsequently reported the collision to the ship’s manager (CSL Australia) and to the Australian Maritime Safety Authority (AMSA). There were no reported injuries on board Goliath and, by 1218, the ship was all fast, port side alongside, at berth number One West.
By about 1220, both damaged tugs had developed a list to starboard as they took on more water and oil began to escape (Figure 8). By this time, the fishing vessel Del Richey II had cast off from its berth and taken up station nearby to assist. The tug Wilga remained alongside the berth.
Figure 8: York Cove and Campbell Cove about 20 minutes after the collision

Source: TasPorts
At about 1300, the TasPorts crisis management team met and appointed an incident controller to lead the incident management team and manage the incident response. Shortly after, AMSA placed a detention order on Goliath.[15] Meanwhile, Devonport’s mooring lines boats Rubicon and Dasher were engaged in setting up available oil containment booms around the damaged tugs. By about 1331, the booms were secured in place around the two foundering tugs and the undamaged tug Wilga.
TasPorts also notified the Environment Protection Authority (EPA) Tasmania[16] and Marine and Safety Tasmania (MAST)[17] of the incident and engaged a salvage company to undertake oil recovery operations from the sunken tugs. At 1436, MAST issued a navigation warning advising mariners of the incident and to avoid navigating in the area. By 1500, an EPA incident management team had been put in place by the State Marine Pollution Controller with the initial goal of protecting sensitive areas and collecting spilled oil as quickly as possible.[18]
By about 1700, both tugs had sunk in about 7 m of water off their berth (Figure 9). It was estimated that there had been 54,000 litres of diesel and other oil on board Campbell Cove and 15,000 litres on board York Cove, of which an unknown quantity had escaped the booms into the wider Mersey River estuary. By 1800, specialised oil containment booms and an EPA oil skimmer had been deployed.
On 29 January, while skimming and other spill response operations continued, aerial surveillance operations confirmed the escape of oils from the containment area.
Figure 9: The submerged York Cove and Campbell Cove
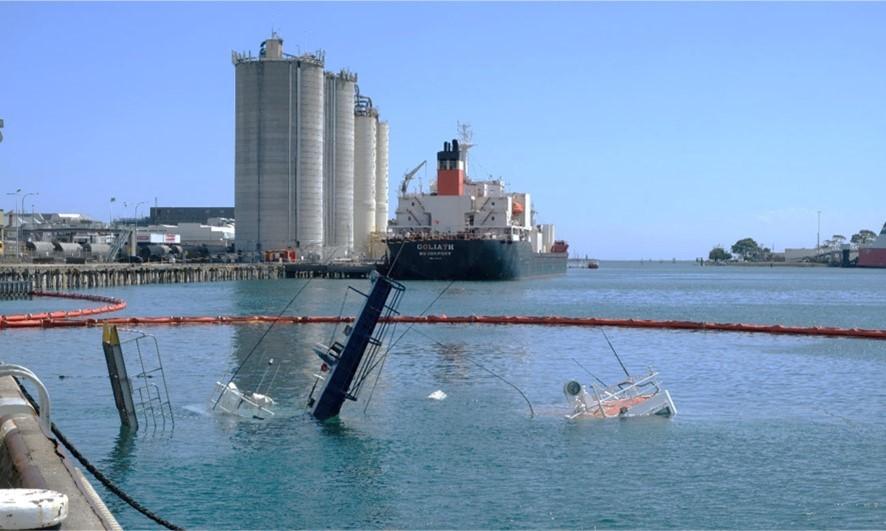
Source: ATSB
On 30 January, the EPA declared a ‘level 2 marine pollution incident’[19] in accordance with the Tasmanian Marine Oil and Chemical Spill Contingency Plan (TasPlan) and its agreement with TasPorts and MAST. The EPA assumed responsibility for oversight of the response and for the control and management of environmental aspects related to the incident. TasPorts was tasked with control of containment and oil recovery operations within the containment area. In addition, personnel from the Department of Natural Resources and Environment Tasmania, supported by EPA staff, monitored shorelines over the following days for signs of pollution and affected wildlife.
On 31 January, the tug Wilga was extracted from within the containment area, a larger skimmer from the AMSA’s National Plan stockpile was deployed and MAST declared a prohibited area due to the ongoing oil spill response activity. The next day, the EPA detained[20] Goliath and EPA inspections of the shoreline and surrounding areas identified small quantities of oil and several bird mortalities.
On 3 February, following temporary repairs, AMSA issued consent for Goliath to undertake a single voyage to Melbourne for further repairs. On 4 February, the EPA released Goliath from its detention, and the ship sailed.
By 11 February, salvage teams had recovered more than 18,000 litres of diesel, lubricating oil, and hydraulic oil from the sunken tugs. An estimated 10,000 litres of fuel and oil remained unaccounted for and probably had not escaped from the tugs’ hulls.
On 15 February, the EPA State Marine Pollution Controller formally advised TasPorts that the level 2 marine pollution incident response had been completed, and responsibility for ongoing aspects of the response were transferred to TasPorts.
Damage and recovery
The collision resulted in the destruction of the wharf’s fendering system, which was subsequently repaired. Further assessment of the damage to the concrete wharf face was required to be undertaken.
Damage sustained by Goliath was limited to deformation of its bulbous bow shell plating and internal structural members and, a non‑penetrating crack in the starboard bow’s shell plating. Following the repairs in Melbourne and after meeting other regulatory requirements, AMSA released Goliath from detention on 10 February and the ship returned to service.
Both York Cove and Campbell Cove were declared constructive total losses. On 11 March 2022, United Salvage were awarded the tender for removal of the wrecks of the sunken tugs. In July 2022, the heavy-lift ship AAL Melbourne was engaged to lift and remove the tugs’ wrecks. The ship arrived in Devonport on 7 August and recovered York Cove’s wreck (Figure 10). Campbell Cove’s wreck was also recovered by 12 August. During the recovery operation, an unknown quantity of oil escaped the containment area although EPA surveys of the shoreline and water did not detect any affected wildlife. AAL Melbourne departed Devonport on 16 August for Brisbane, Queensland where the tugs were to be scrapped (recycled).
Figure 10: York Cove being recovered
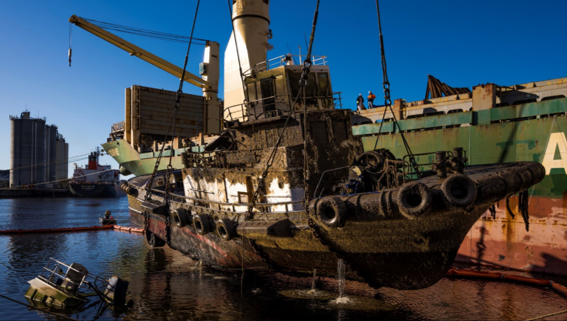
Source: TasPorts (Courtesy of Rob Burnett Images)
Context
Goliath
Ship details and history
Goliath is an Australian‑registered, self-unloading, bulk cement carrier built in 1993 by Hanjin Heavy Industries in Ulsan, Republic of Korea. At the time of the collision, the ship was classed with Lloyd’s Register and owned by CSL Australia. It was managed and operated by CSL Australia and engaged almost exclusively in the carriage of cement from Devonport, Tasmania to Melbourne, Victoria.
The ship was originally owned by Cement Australia until it was purchased by CSL Australia in 2007. Following the change of ownership, the ship was managed by Inco Ships until 2015 when management was taken over by CSL Australia.
Goliath was equipped with the necessary navigational, and other equipment, machinery and systems required by SOLAS[21] for a ship of its size. This included radar, automatic identification system (AIS), gyrocompass and electronic chart display and information system (ECDIS), which was the ship’s primary, and back-up means of navigation. Goliath was also equipped with a Japan Radio Company JCY 1850 voyage data recorder (VDR) from which data and information useful to the investigation was recovered, including audio recordings from the bridge.
Goliath’s main propulsion was provided by a Sulzer 5RTA 52 engine developing 6,080 kW driving a single, fixed pitch, right-handed propeller. The ship was also equipped with an Ulstein 883 kW bow thruster.
Ship’s crew
Goliath had a predominantly Australian crew of 17, including the master, 3 deck watchkeeping officers, chief engineer and 3 engineers, 2 cadets, 6 integrated ratings (IRs), including a trainee, and a cook. The ship was operated on a 6-week crew roster with many of the crew regularly assigned to the ship over several years.
The master had about 46 years of seagoing experience, with over 20 years in the rank of master with CSL Australia and, previously, another company. The master held a United Kingdom master’s certificate of competency, the equivalent Australian certificate of recognition and pilotage exemption certificates for Melbourne and Devonport. The master began working on board Goliath in 2002 as a third mate and was promoted to master after CSL Australia became its owners in 2008 and had continued in that rank since. The master had re-joined the ship about a week before the accident.
The chief mate had about 28 years of seagoing experience and had been a chief mate for about 8 months. The chief mate held an Australian chief mate’s certificate of competency and had worked on board Goliath since 2008. The chief mate had re-joined the ship 2 days before the accident.
The second mate had about 15 years of seagoing experience and had been second mate for about 8 months. The second mate held an Australian second mate’s certificate of competency and had also worked on board Goliath since 2008. The second mate had re-joined the ship about 3 weeks before the accident.
Hours of work and rest
Goliath’s deck officers maintained a traditional 4-on 8-off watchkeeping schedule at sea. Hence, the three watchkeeping officers kept a 4-hour navigation watch followed by 8 hours of rest opportunity or time to carry out non-watchkeeping duties. The master did not stand a navigational watch at sea.
The ship had departed Melbourne for Devonport at 1612 on 27 January (the day before the accident) and the night was spent underway at sea in good weather. This provided all the deck officers an opportunity for a full 8 hours of uninterrupted rest or sleep.
The master reported going to bed by about 2200 on 27 February and sleeping well until waking at 0600 on the morning of the accident. The master recalled being well rested and alert in the time leading up to the accident.
The chief mate had joined the ship during the port call at Melbourne after spending 2 nights in a hotel due to a delay with the ship’s berthing. The chief mate recalled sleeping reasonably well the night before the accident although still adjusting to the sleep environment on board and being at sea. The chief mate kept the usual navigational watch between 0400 and 0800, followed by breakfast and some paperwork, until about 1130, before relieving the third mate on the bridge. The chief mate reported being reasonably well rested and alert in the time leading up to the accident (although it was nearing the usual time for the rest period).
The second mate kept the 0001-0400 watch and then went to bed by about 0500 before waking at about 1100. The second mate then had lunch before going up to the bridge to relieve the chief mate. The second mate reported being well rested and alert in the time leading up to the accident.
Analysis of the master, chief mate and second mate’s recorded hours of work and rest found that they were compliant with the minimum hours of rest as required by the relevant international conventions[22] and the Australian Maritime Safety Authority’s (AMSA) Marine Order.[23]
Goliath’s manoeuvring system
Steering system
Goliath was fitted with a Hamworthy Industramar VecTwin steering system comprising 2 highlift, Schilling rudders installed symmetrically behind the propeller. Each rudder was independently driven by a Frydenbø-Mjølner HS 120 rotary vane steering gear unit, each fitted with 2 steering motors.
The steering gear could be remotely operated from the bridge in 4 main control modes:
- autopilot steering
- manual steering (wheel control)
- non-follow-up (NFU) steering
- VecTwin steering (joystick control).
Additionally, and similar to other ships, the steering could be operated locally from the steering gear room in case of an emergency involving the failure of the remote operating systems.
When steering in autopilot or manual steering modes, the 2 rudders operate in unison based on rudder angle commands respectively from the autopilot or the manual steering wheel. In non‑follow-up (NFU) mode, the rudders could be operated either independently with separate levers (tillers) or by a single lever.[24] In VecTwin steering mode, a joystick was used to control the rudders.
The steering could be operated in any mode when conning from inside the wheelhouse. When conning the ship exclusively from the bridge wing conning stations, joystick steering was the only available means of rudder control.
The mode of steering operation was selected by means of a manually operated selector switch on the bridge steering console (Figure 11). The selected steering mode was indicated by the illumination of the respective symbol on the steering selector switch panel, and on the autopilot panel on top of the steering console.
Rudder angle indicators were fitted in the wheelhouse, on each bridge wing (port and starboard), and in the steering gear room.
Figure 11: Goliath's wheelhouse, steering console, and steering mode selector switch
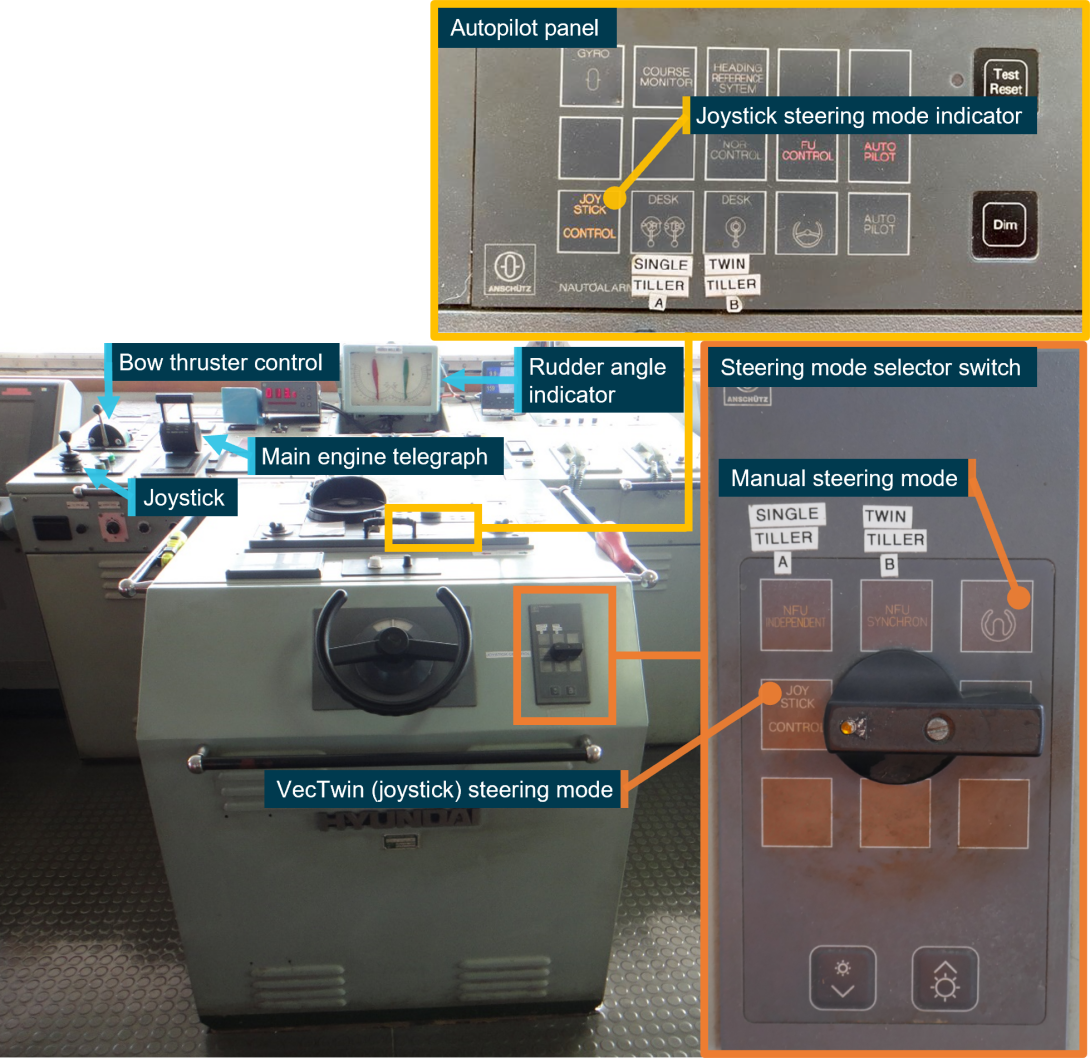
Source: ATSB
VecTwin steering mode
In VecTwin (joystick) steering mode, a joystick was used to select various pre-set combinations of rudder angles which, with ahead inputs on the ship’s main engine, allowed for the generation of thrust in different directions and for enhanced manoeuvrability, particularly at slow speeds. The system coordinated the 2 rudders independently with rudder angle settings ranging from 105° outboard to 25° inboard depending on the joystick setting selected (Figure 12). On board Goliath, VecTwin steering mode was generally only used at speeds under 2 knots, which generally limited its use to low-speed manoeuvring in port.
When using the VecTwin steering mode, ahead inputs on the main engine could be used to generate astern thrust, transverse thrust or even to ‘hover’, all with the propeller kept rotating in the ahead direction. For example, with the ‘astern’ joystick setting selected, each rudder was set to 105° outboard, with ahead inputs on the main engine generating astern thrust to slow/stop the ship or move the ship in the astern direction. This meant that the ship could be slowed, stopped, or moved astern without the need to stop the engine and engage astern propulsion, as usually required for conventional ship manoeuvring.
Figure 12: VecTwin steering joystick showing settings and corresponding rudder angles

Note that the direction of ship motion shown for various VecTwin joystick rudder angle settings is the direction of the resultant ship motion when ahead main engine movements are used in combination with the respective joystick setting.
Source: ATSB
Joystick design
There were 3 VecTwin joystick control panels, one in the wheelhouse and one on each bridge wing conning station.[25] Control could be taken at any one of the joystick panels by pushing the ‘joystick call up’ push button and the joystick selected for command was indicated by the illumination of a ‘joystick on’ indicator light on the respective panel.
During the ATSB’s on site investigation, investigators’ testing of the system determined that the illumination of the ‘joystick on’ light was independent of, and unrelated to, the steering mode selected. The illumination of the ‘joystick on’ light only indicated which joystick panel was selected and that control was possible from that panel.
This meant that the ‘joystick on’ light remained illuminated at whichever joystick panel had been selected (or last selected) even when the chosen steering mode was a mode other than ‘joystick control’ (such as ‘autopilot’ or ‘manual’ steering modes).
This was contrary to the understanding of the master and other deck officers who believed that the illumination of the ‘joystick on’ light was also indicative of the steering being in the correct VecTwin joystick steering mode. That is, the officers believed that the illumination of the ‘joystick on’ light was only possible if the steering mode selector switch had been turned to the right setting to select joystick steering mode.
Interview accounts also indicate that, in practice, there was no consistency among the involved officers regarding the use of the ‘joystick on’ light as an indicator of a successful transfer of control. At interview, the master stated that they often checked for the illumination of the ‘joystick on’ light to assure themselves that transfer had been successfully executed and that steering was in joystick mode. However, the chief mate and second mate both reported that they largely ignored the light and did not assign any significance to it either as an indicator of transfer or otherwise. It was also reported that the bridge joystick panel ‘joystick on’ light was usually left obscured by covering it with an opaque plastic bottle cap.
Following the accident, CSL Australia arranged for modification of the joystick control panels to provide affirmative visual confirmation that the correct steering mode had been selected and that the panel was selected for command (Figure 13). The modification was completed in April 2022.
Figure 13: Joystick panel at the time of the accident (left) and after modifications (right)
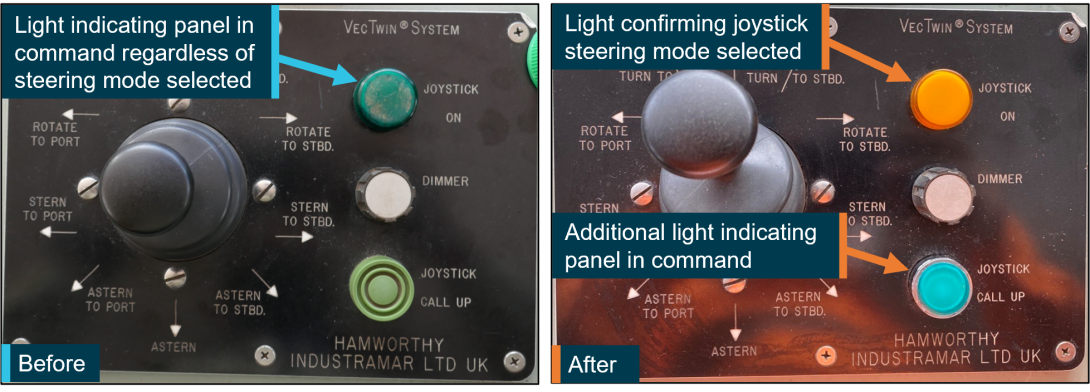
Source: CSL Australia, modified and annotated by the ATSB
Previous VecTwin steering incidents
As part of this investigation, the ATSB sought records of past incidents involving Goliath and its VecTwin joystick steering system. TasPorts records showed 2 relevant incidents involving Goliath (described below). At the time of those incidents, Goliath was owned by CSL Australia and managed by Inco Ships. As such, there was no record of those incidents or of the implementation of the resulting proposed corrective action within the CSL Australia incident management database. Neither of the 2 earlier incidents involved officers on board at the time of this accident
Devonport, 2007
On 10 December 2007, while manoeuvring Goliath in the Devonport swing basin, the master selected the ‘astern’ joystick setting on the port bridge wing joystick panel and ordered ahead inputs on the main engine telegraph to slow the ship for the final approach to the berth. However, the master observed that instead of slowing down, the speed was increasing. The master checked the rudder angle indicators and realised the rudders were amidships. Despite the master then ordering ‘full astern’, the bow made contact with the shore, resulting in some minor paint damage to the bulbous bow. There was no damage to shore infrastructure or pollution.
Following the incident, the steering mode selector switch was reset to manual steering before joystick mode was selected again. The joystick steering system then operated as normal and the ship berthed without further incident. The shipboard investigation found that joystick steering mode had been correctly selected, and control correctly transferred to the port bridge wing conning station. Subsequently, it was found that there were several loose connections and wiring with poor terminations in the steering mode selector switch mechanism, which resulted in the steering mode remaining in manual steering.
The incident resulted in a proposal to amend the ship’s procedures to include a requirement for a functional test of the steering following a change in the selected steering mode.
Devonport, 2009
On 15 May 2009, while manoeuvring Goliath in the swing basin, the master selected the ‘astern to starboard’ joystick setting on the port bridge wing joystick panel and ordered ‘slow ahead’ on the main engine telegraph. However, the master found that the ship was not swinging as expected, so ordered ‘half ahead’. At about that time, the master realised that the rudders were still amidships and that joystick control had not been accepted on the port bridge wing joystick panel. The master immediately pushed the ‘joystick call up’ push button, selected the ‘astern’ joystick setting and ordered ‘full ahead’ to slow down the ship. The master subsequently ordered ‘full astern’ and used the bow thruster to avoid colliding with the wharf ahead. Goliath narrowly avoided colliding with Campbell Cove, which was moored at berth 3W, but it did collide with an aluminium walkway for the small craft mooring pontoon north of the berth. There was only minor paint damage to the ship’s bow but substantial damage to the walkway and mooring pontoon. The moorings of 2 pilot launches at the pontoon also parted.
The shipboard investigation found that the master did not take control of the VecTwin joystick on the wing joystick panel and there was no verbal confirmation between the master and chief mate to confirm the transfer of control had been successfully completed. The investigation also identified that although there was a general practice for the transfer of controls, this was not documented and was not followed on the day. Importantly, the investigation identified that the design of the joystick panel did not incorporate an unambiguous indicator that control had been successfully transferred.
The incident resulted in a proposal to identify and document the indications of a successful transfer of controls and to identify locations where the transfer could occur safely in advance of committing to a critical manoeuvre. The corrective action also recommended that the improved process be captured in the ship’s passage plan and the ship’s officers be familiarised with the procedure and provided refresher training on aspects of good ‘bridge resource management’.
Safety management system
The International Safety Management (ISM) Code[26] has as its objective the prevention of human injury or loss of life and the avoidance of damage to the environment and to property. Among other things, it requires companies to provide for safe practices in ship operations, to assess all identified risks to ships, personnel and the environment and, to establish appropriate safeguards against these risks. The Code aims to achieve this by requiring companies to develop, implement and maintain a safety management system (SMS), with instructions and procedures to ensure the safe operation of ships, to prepare for and respond to emergencies and to conduct regular audits and reviews of the system.
Goliath’s SMS consisted of general procedures and instructions broadly grouped under sections such as fleet operations, company operations and safety and environmental procedures. The section on fleet operations covered navigation including procedures for passage planning, watchkeeping, and bridge resource management while the safety and environmental procedures covered risk assessment and risk management. These generic procedures applied to ships across the fleet and were augmented by the company’s standing orders. Additionally, each ship was required to develop master’s standing orders and ship-specific checklists taking into account the particular ship’s operations, circumstances, and equipment.
Passage planning
CSL Australia’s procedures for passage planning were largely aligned with the requirements of the relevant international conventions and best practice. Goliath’s passages were planned from berth‑to‑berth and generally required little change between voyages. The passage plan included guidance notes relevant to specific waypoints. For example, for the waypoint in the swing basin, the plan advised the master to monitor transit points during the swing and to take care not to develop unwanted headway towards the berth. The plan did not include any guidance on safe locations for the transfer of controls.
The exempt master briefing card for Devonport documented information such as tidal restrictions applicable to berthing, relevant port rules including courses and speeds within port limits and the dimensions of the swing basin. The briefing card included a short checklist with reminders to monitor the ship’s course and speed, helm orders and that the ship was proceeding according to the agreed passage plan. The card also included a check titled ‘Bridge Control transfer procedure confirmed’ but did not include guidance or information on safe locations where the transfer of controls could or should take place before the ship was committed to a manoeuvre. The briefing card for Goliath’s arrival in Devonport on the day of the accident was initialled by the master and all 3 deck officers and the bridge control transfer procedure check was marked completed.
Watchkeeping
Goliath’s SMS procedures relating to navigational watchkeeping were largely aligned with the requirements of the STCW Code[27] and other internationally recognised publications reflecting best practice on the subject, such as the Bridge Procedures Guide.[28]
The ship’s schedule of working arrangements described a traditional watchkeeping roster with one officer of the watch (OOW) on duty at any given time. In addition, the ship’s procedures called for a deck officer to assist with mooring and unmooring during port calls. While the role of the additional deck officer was usually allocated based on whether the mooring/unmooring operation occurred in the first or second half of the 4-hour watch, the roles of the additional officer and OOW were often allocated by agreement among the officers, or by their own initiative.
More importantly, the company’s standing orders also specified that the OOW was not to be changed over during a navigational manoeuvre. However, the definition of what constituted a ‘navigational manoeuvre’ was not specified.
Critical operations checklist
Goliath’s SMS defined critical tasks and operations as those with an initial risk rating of significant, high, or very high and that were performed more than 3 times a year. Every critical operation or task was to be supported by a checklist and other tools such as work permits, if required.
The risk assessment for the transfer of bridge controls between the wheelhouse and wing assessed the risk of an incorrect transfer of joystick steering to be ‘very low’. The risk of a similar incorrect transfer for the main engine was also assessed as ‘very low’ while the risk of an incorrect transfer of the bow thruster controls was assessed as ‘medium’. Nevertheless, a critical operations checklist was developed to provide a documented procedure for the transfer of bridge controls from the wheelhouse to the bridge wing conning station and vice versa.
Goliath’s documented procedure for the transfer of bridge controls to the wing described a sequential series of 5 steps and checks to ensure a safe and successful transfer of steering control, summarised as follows:
- Bridge wing and wheelhouse joysticks to be set to the ‘ahead’ position.
- Change the steering mode selector switch from ‘manual steering’ to ‘joystick steering’.
- Confirm that the indicator light on the steering console indicates ‘Joystick control’.
- To take joystick control at the bridge or bridge wing joystick panels, press the green button.
- Test VecTwin joystick function to confirm rudder movement.
A laminated copy of the transfer procedure was kept in a folder on the bridge along with other critical operations checklists (Appendix A).
On the day of the accident, 4 out of the 5 steps and checks in the transfer of control were either not carried out or were overlooked. The joysticks were not set to the ahead position and the steering mode selector switch was not switched over to joystick steering. The 2 checks that may have been able to identify that the steering was not in the correct mode: the check of steering console ‘joystick control’ light and the test of the joystick to move the rudders, were not carried out by either the master or the second mate.
Bridge resource management
Bridge resource management (BRM) can be defined as the effective management and utilisation of all resources, human and technical, available to the bridge team to ensure the safe completion of the vessel’s voyage.[29] BRM provides a method of organising the best use of these resources to reduce the level of operational risk. Its key safety aspect is to put in place defences against ‘single-person errors’, with the aim of avoiding serious incidents.
Published AMSA guidance stated that BRM techniques were integral to responsible navigation practices and that well executed BRM techniques enhanced safety and reduced the risk of single person errors.[30] An AMSA marine notice[31] on the subject also noted that effective BRM should include the following considerations, among others:
- Navigational and operational tasks and responsibilities should be clearly defined and delegated.
- Navigational, operational, and general safety priorities should be set and consistently reviewed in the context of the prevailing circumstances and conditions.
- Masters and officers in charge of a navigational watch, who regularly undertake the same voyage/route, should be mindful of the risks associated with human performance limitations (such as the effects of fatigue and workload on vigilance and monitoring tasks) and familiarity, to retain resilience.
Goliath’s SMS highlighted the need for effective BRM. The SMS stated that the primary goal of BRM was the elimination of single-person errors and the procedures expanded on several elements of good BRM.
Bridge resource management is a broad topic covering many inter-related subjects. Key principles of effective BRM include situational awareness and shared mental models, closed loop communications, briefing and debriefing, challenge and response, delegation, and short-term strategies. The implementation of these principles on any ship’s bridge is the responsibility of all bridge team members.
Situation awareness and distraction
The concept of situation awareness is closely associated with the concept of a shared mental model. Situation awareness can be defined as ‘using cognitive processes to develop and maintain a mental model upon which decisions are made’ or more simply as knowing what is going on around you. In relation to a ship’s passage, situation awareness is dependent on working memory and is, therefore, affected by distraction, interruption, and stimulus overload.
Distractions during the completion of a task increase the likelihood of error. Distractions can be related to the task or from some external, unrelated source or event. An individual, or team, can also become completely occupied (fixated) with one event or task and therefore distracted from the overall objective. Minimising possible distractions is important for effective BRM.
Goliath’s SMS emphasised the need for officers to avoid distractions particularly during navigation in port or in restricted waters. In particular, the SMS advised that bridge team members should avoid getting engrossed in unimportant VHF radio communications.
At interview, Goliath’s master, chief mate and second mate, all reported being distracted by the VHF radio calls from the mooring lines boat. The evidence indicates that the relatively unimportant activity associated with responding to the radio calls and locating the mooring radio clearly occupied the officers’ attention and distracted them during the ship’s approach to the swing basin.
The process of transferring manoeuvring controls to the bridge wing was a highly regimented, often repeated activity for the second mate. The routine practice was to stand by the steering console and await the master’s order to transfer controls. Whenever the order was given, the second mate’s usual practice was to immediately reach out and use the steering mode selector switch to select joystick mode before proceeding to the wing to complete the transfer process.
The handover and distraction from the radio calls before the incident resulted in the second mate moving away from the usual station near the steering mode selector switch, disrupting the routine process for transferring controls. The second mate also recalled the master’s order on the day was unexpected (usually the second mate was ready and waiting for the order).
Roles and responsibilities
A key element of effective BRM requires that all bridge team members involved are aware of their roles and responsibilities. Duties should be clearly and unambiguously assigned to specific individuals, who should confirm that they understand their responsibilities and tasks should be performed according to a clear order of priority. A mutual understanding of individual roles and responsibilities in executing the agreed plan makes it more likely that single-person errors are detected early.
On the morning of the accident, the chief mate took over as OOW from the third mate at about 1130. About 10 minutes later, the second mate came up to the bridge intending to relieve the chief mate. This occurred at what was a high workload phase of the passage. The ship was passing the narrowest section of the passage into port (known as ‘the cut’) and approaching an area where large ships, such as the Searoad Mersey II, were moored. This section of the passage also included the approach to the swing basin where several critical steps had to be taken, such as the initiation of the swing and the transfer of controls to the wing. During this time, radio calls from the mooring lines boat distracted Goliath’s officers. When the master ordered the transfer of controls, it was directed at the chief mate, but it was the second mate who acknowledged the order and moved to carry it out.
The second mate could not recall whether the watch was formally handed over, but in responding to the master’s order to transfer control, assumed that it had and that the chief mate was no longer required on the bridge. The chief mate also shared the same understanding of the handover.
The master and second mate also had a different understanding about who was responsible for testing the operation of the bridge wing joystick following the transfer of controls. The master believed that the checklist required the OOW transferring the controls to test the function of the joystick. However, the second mate was of the understanding that function tests of the propulsion and steering were to be left to the master. The master stated that the joystick was usually tested and its operation confirmed using the rudder angle indicators but, on the day of the collision, it was not.
Error management
The detection and management of errors is key to avoiding serious incidents. Error management seeks to detect errors and control their effects to minimise negative outcomes. It generally comprises measures designed to limit the occurrence of errors and their adverse consequences.
Goliath’s master and second mate both knew that the manoeuvre in the Devonport swing basin allowed little room for error due to factors such as the dimensions of the basin and environmental conditions. While the tide and weather at the time of the accident were relatively benign, once committed to the manoeuvre, it required the master’s sustained attention, and unrestricted use of all the ship’s manoeuvring aids and equipment.
The procedure for the transfer of controls provided a sequential series of steps and checks which, if carried out, offered the safest method for the transfer. For example, the procedure required that the autopilot panel be checked to ensure the ‘joystick control’ sign was illuminated, and that the joystick function was tested (by checking that the rudder angle indicators moved to match the joystick setting selected). These checks provided opportunities to identify errors and, if any were identified, for these to be quickly rectified as part of the transfer process.
Past incidents on board Goliath (see the section titled Previous VecTwin steering incidents) had demonstrated the value of having pre-planned locations where the steps and checks associated with the transfer of controls could be safely carried out and identified issues rectified before committing the ship to a manoeuvre. At the time of the incident, no such planned locations were identified or documented in the ship’s passage plans.
Complacency
Goliath’s master had worked on board the ship since 2002 and had been its regular master since 2008. In that time, the master estimated having successfully conducted over 1,000 port arrivals and departures using the VecTwin joystick system, in various states of weather, tide and light. A significant proportion of these manoeuvres were at Devonport. Similarly, the chief mate and second mate had also worked on board the ship for over a decade. In the second mate’s case, the entirety of their career as a deck officer had been spent on board Goliath, largely operating between the ports of Melbourne and Devonport.
Schager (2008)[32] states:
… it may be wise to avoid exaggerated emphasis on time only. Parallel with length of time or quantity of experience, we should also emphasise the content or quality of experience.
We seldom refer to the actual content of experience. It is possible that a person, even with long experience, hasn’t met many situations from which he/she could benefit professionally, nor faced many critical or hazardous situations. Most work on board a ship involves routine and repetitiveness in such a way that another year in the same position does not necessarily add much to anybody’s competence.
Some repetitive experience can also be detrimental as it induces a sense of routine, safety, and normality in an otherwise risky environment. Over time, an officer’s respect for what he or she is doing might decrease while the skills and quantity of experience increase.
This sense of extended experience in the task or role can build up and, over time, result in a false sense of security or an illusionary feeling sometimes called complacency.
According to Schager (2008), complacency may be defined as:
being a state of mind. It is an unconcerned attitude, e.g. in connection with the presence of danger and risk, where individuals behave and think in a routine-like mode, anticipating an uneventful and ordinary development of the present situation.
Schager also stated that:
Complacency is a passive state, not an active one, and no one chooses to be complacent. It creeps into one’s mind imperceptibly. Individuals are therefore unaware of being complacent and would, if asked, reassuringly deny it. Instead, individuals would probably justify their state of mind as rational, realistic, reasonable and in line with situational requirements, as well as a sign of experience.
Complacency can lead to such things as disbelief when something unexpected happens. It can lead to a false sense of security as well as a false sense that the situation is under control when it isn’t. It can furthermore lead to deficient risk assessment or to repress risks and not paying proper attention to what one is engaged in.
Table 1 below sets out the times and sequence of manoeuvring orders and other associated events in the lead up to the collision (based on engine telegraph and VDR data).
Table 1: Sequence of manoeuvring orders and events
Time | Speed (knots) | Event |
1144:30 | 1.92 | Last radio broadcast from Rubicon to Goliath on VHF channel 6. |
1145:08 | 1.27 | Master orders transfer of manoeuvring controls to port bridge wing. |
1145:29 | 1.21 | Second mate confirms transfer completed and master moves to bridge wing. |
1145:52 | 1.19 | Joystick set to ‘astern to port’ and engine telegraph set to ‘slow ahead’. |
1147:22 | 2.78 | Telegraph set to ‘half ahead’ and joystick set to ‘astern’ at about same time. |
1147:29 | 2.91 | Telegraph set to ‘full ahead’. |
1148:04 | 3.96 | Telegraph set to ‘navigation ahead’. |
1148:21 | 4.68 |
Master realises that ship was not in joystick steering mode. Telegraph setting reduced to ‘slow ahead’. |
1148:22 | 4.72 | Goliath collides with York Cove and Campbell Cove. |
Following the initial order of slow ahead and joystick setting of ‘astern to port’, the master found that the ship was not swinging as expected. In response to the ship’s increasing speed, the master set the joystick to ‘astern’ and increased engine rpm to ‘half ahead’, then ‘full ahead’ and ‘navigation ahead’, which further increased the speed.
In that time, it would have become increasingly obvious that there was something abnormal and a collision was becoming unavoidable. However, the master did not check the rudder angle indicators until 2.5 minutes after the first order of ‘slow ahead’ likely indicating that they were not unduly concerned with the progress of the manoeuvre.
The risk of complacency in Goliath’s bridge team due to the frequent, repetitive nature of the team members was highlighted by a placard on the bridge that paraphrased Schager’s findings on the detrimental nature of repetitive tasks.
Emergency response
Goliath’s SMS included emergency contingency plans for collision. While the drills schedule did not specifically include a requirement to conduct drills for responding to a collision, there was evidence of several past oil spill drills which incorporated a collision in the drill scenario.
As the collision became imminent, no attempt was made to warn the tugs ahead or personnel in the vicinity (either by sounding the ship’s whistle or using the VHF radio). Following the collision, the master manoeuvred the ship away from the tugs, notified VTS and berthed the ship.
Post-collision activity on board was timely and appropriate and included the sounding of tanks, damage assessments and reporting. The general emergency alarm was not sounded however all the ship’s personnel were awake and alerted to the collision by other means.
Bridge resource management training
The importance of BRM and usefulness of BRM training is recognised internationally. The STCW Code (1995, as amended) required companies to develop and issue watchkeeping guidance to masters and officers based on bridge resource management principles.[33]
In 2010, the Manila amendments to the STCW Convention and Code introduced mandatory requirements for masters and deck officers to demonstrate knowledge of bridge resource management as part of their respective competency requirements.[34] While the Code allowed for competence to be demonstrated in various ways including through training or experience, companies were responsible for providing training in areas where seafarers did not have appropriate training or required refresher training.
Goliath’s SMS reflected this need for BRM training and required that all deck officers undertake formal BRM training (including simulator training) organised by the company or at a recognised shore establishment. The SMS also required that BRM refresher training be carried out at intervals not exceeding 3 years.
At the time of the collision, the master and second mate had not completed any formal BRM training. The chief mate had last undertaken BRM training about 13 years prior, in 2009.
Audits
On 18 November 2021, an annual internal audit was conducted on board Goliath to verify the ship’s compliance with the requirements of the ISM Code and Maritime Labour Convention,[35] among others. While there were no non-conformities identified, the audit resulted in one observation recommending that the ship’s master and chief mate attend BRM training as required in the ship’s SMS.[36] The observation also recommended that the company review the relevant sections of the SMS and include the requirement for regular BRM refresher training in the company’s training matrix.
TasPorts
Port of Devonport
The port of Devonport, located on Tasmania’s north coast, is a key entry point into Tasmania for passengers and cargo. The port accommodates berths for ro-ro vessels, tankers, ferries, and bulk carriers and serves as the Tasmanian port of call for the TT Line ferries between Melbourne, Victoria and Devonport, Tasmania. Each year between 3 and 4 million tonnes of cargo transit through the port. This includes the export of wheat, grain and cement and the import of fertilisers, fuel, and consumables.
The port of Devonport was managed and operated by the Tasmanian Ports Corporation (TasPorts); a Tasmanian State-owned company responsible for 11 Tasmanian ports including Devonport, and the Devonport airport. Among other things, TasPorts was responsible for the provision and maintenance of port infrastructure and navigational aids and the delivery of pilotage, towage, and vessel traffic services (see the section titled TasPorts).
Berth activity
Berth number Three West (berth 3W) was a general use berth used by Devonport’s tugs, other small commercial craft, and fishing vessels. These small vessels were often manned when alongside the berth.
On the day of the accident, there had been up to 4 persons scheduled to carry out maintenance and other routines on board the 2 tugs berthed together (Campbell Cove and York Cove). Shortly before the collision, coincidentally, all of them left the tugs for lunch or work elsewhere. Incidentally, at the time there were 3 persons on board Del Richey II, berthed immediately south of the tugs. Wilga, berthed just north of the 2 tugs, however, was not manned at the time.
Swing basin
A swing basin or turning basin is a designated body of water generally located in a port or shipping channel to allow ships to turn or reverse their direction of travel. Swing basins are a common feature of ports across Australia and the world. Devonport’s swing basin was used by all large ships that called at the port. The ships that used it most often were those that called regularly at Devonport including Goliath, the TT Line ferries and Searoad ships. As these ships called at the port regularly, they were generally also exempt from taking a pilot or tugs. Almost all ships turning in the swing basin, including Goliath, turned to the west (towards berth 3W).
TasPorts’ vessels
TasPorts owned, managed, and operated several vessels for the provision of harbour towage, pilotage, and mooring operations. At the time of the collision, Devonport was serviced by the tugs Wilga, Campbell Cove and York Cove, the mooring lines boats Dasher and Rubicon and the pilot launch Tamar.
York Cove (Figure 14) was an Australian-registered tug built in 1990 by Ryochu Kairiku Unyu, Japan. The tug operated under other names in Japan and the Republic of Korea until it arrived in Australia in 1998 and was re-named York Cove.
Figure 14: York Cove
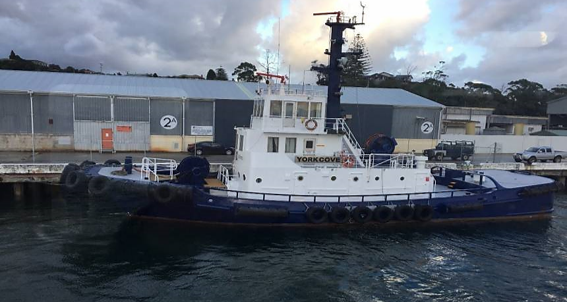
Source: TasPorts
Campbell Cove (Figure 15) was an Australian-registered tug built in 1976 by Carrington Slipways in Newcastle, New South Wales. The tug initially operated at the port of Newcastle until about 1998 when it relocated to Devonport.
At the time of the collision, both tugs were classed with Lloyd’s Register.
Figure 15: Campbell Cove
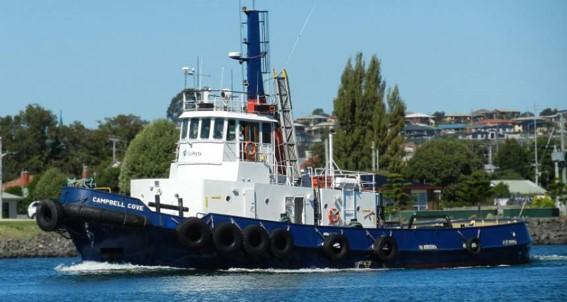
Source: TasPorts
Port procedures manual
Tasmanian Ports Corporation (TasPorts) was engaged by Marine and Safety Tasmania (MAST) and the Environment Protection Authority Tasmania (EPA) to undertake specified marine safety functions. This was achieved through a deed of agreement between the 3 organisations and supported by delegations and authorisations under the relevant legislation to TasPorts and its employees. Under the deed, TasPorts was engaged to perform and deliver the following functions, among others:
- provision of port communication services
- maintenance of navigation aids
- provision of pilotage services
- preparation of a pilotage code
- training of pilots
- administration of pilotage exemption certificate requirements
- regulation enforcement in pilotage areas
- provision of emergency response services including oil spill response functions.
In carrying out the above functions, TasPorts developed relevant manuals and plans, including a ports procedures manual, marine pilotage code, crisis management manual, incident management plan and oil spill contingency plan.
The TasPorts port procedures manual provided information on pilotage, operating parameters in applicable ports, incident reporting, vessel traffic services (VTS) and emergency response. The manual and its procedures applied to the 5 Tasmanian primary ports (including Devonport) and 6 secondary ports.[37]
Vessel traffic service
TasPorts operated an authorised vessel traffic service (VTS), providing advisory information to vessels. The VTS also served as the primary communications centre for contact with vessels and was tasked with monitoring pilot exempt master requirements. TasPorts procedures required any vessel intending to enter, depart or move within the port to report to VTS. While there was no documented requirement in the port’s procedures for a radio check between the lines boat and ships, such checks are generally consistent with good practice.
On the day of the accident, Goliath reported to VTS as required before entering port limits. Shortly after, the mooring lines boat Rubicon reported to VTS when departing the wharf in preparation for Goliath’s berthing. Following this, Rubicon conducted a radio check with Goliath, first on VHF channel 14 and then on channel 6. Goliath’s deck officers reported that these radio calls were highly unusual. The master, chief mate and second mate also stated that they were unexpected and contributed to them being distracted during the approach to the swing basin.
Radio communications during previous port calls
The ATSB analysed recorded VTS radio traffic from 3 of Goliath’s previous arrivals at Devonport in January 2022 to determine whether a radio check between the ship and assigned mooring lines boat was standard practice.
During a port call on 22 January, there was no radio check conducted between Goliath and the assigned mooring lines boat Dasher. Similarly, on 18 January, there was no evidence of a radio check being conducted between the ship and Dasher.
During a port call on 9 January, there was a radio check conducted between Goliath and Dasher although, on this occasion, the radio check was initiated by Goliath’s master.[38] This radio check was probably prompted by a planned lifeboat drill on board the ship, which would require the assistance of the mooring lines boat.
In summary, there is some evidence to support Goliath’s officers’ accounts that the radio check from the mooring lines boat Rubicon was unusual and out of the ordinary. However, in submission, TasPorts stated that such radios checks were not an unusual occurrence.
Incident reporting
TasPorts procedures required that all maritime incidents in pilotage areas be reported to MAST and VTS. If required, incidents would be investigated, and recommendations made to reduce the likelihood of a similar occurrence. Incident reports were also entered into the TasPorts incident management system and reviewed during 3-yearly risk assessments where they were used to inform improvements to the port procedures and pilotage manual. TasPorts was also required to retain accident and incident reports and records of other risk events for review by MAST during the annual port audit process.
During this investigation, TasPorts located, retrieved, and provided the ATSB with information on two previous incidents involving Goliath in Devonport (see the section titled Previous VecTwin steering incidents).
Risk assessment
As part of this investigation, the ATSB sought to assess whether the 2007 and 2009 Goliath incidents had any influence on the subsequent risk management in Devonport. In both the earlier incidents, Goliath narrowly avoided colliding with berth 3W and, in the 2009 incident, with Campbell Cove, which was moored alongside at berth 3W.
The ATSB sought the most recent TasPorts risk assessment as well as the last five 3-yearly risk assessments. The ATSB was provided with a pilotage and port risk assessment from 2019 and a safety review of Devonport pilotage services from 2008. There were no port or pilotage risk assessments completed between 2008 and 2019 and, there was no record available of risk assessments conducted prior to 2008.
2008 safety review
The 2008 safety review of pilotage services at Devonport and the associated workshop considered hazards associated with the provision of pilotage services to various berths and at various points of the pilotage. The review noted that berth number One West (Goliath’s berth) was the most exposed to the effects of tide and that there was potential for an incident if the ship’s exempt master were unfamiliar with the manoeuvring system. Control measures included the port’s pilotage exemption requirements and pilotage training.
The review identified that the physical constraints of the port made a number of berthing manoeuvres difficult. It recommended that smaller commercial vessels be relocated from berth number 3W to ease access to berth number Four West (used by larger bulk carriers) thereby improving safety and operability for the port. The review also suggested implementing a ‘large vessel approaching’ alert to warn small vessels operating near the mouth of the Mersey River of bow waves from passing large vessels.
2019 pilotage and port risk assessment
The 2019 risk assessment was aimed at reviewing the core hazard in several Tasmanian ports with the aim of ensuring that all reasonable precautions were in place. The core hazard for Devonport was assessed to be a grounding in the channel or swing basin. The assessment considered the potential threats that could lead to such a scenario as well as the control measures in place noting that these were different for piloted vessels and pilot exempt vessels.
The assessment concluded with a recommendation that all piloted vessels over 95 m in length use a tug for arrival and departure. There were no recommendations made regarding pilot exempt vessels and no consideration of any other scenarios.
VTS risk assessment
In addition to the 2008 and 2019 risk assessments, TasPorts also provided the ATSB with a risk assessment conducted in 2020 as part of TasPorts’ VTS accreditation process. As such, the assessment was focused on risks and risk controls related to aids to navigation rather than more general risks. The assessment included a consideration of past incidents and near misses however there was no evidence that Goliath’s 2007 and 2009 incidents were among those considered.
The assessment identified a scenario involving an ‘allision’[39] between a vessel manoeuvring in the swing basin and a wharf. The potential consequences identified included damage to the ship, infrastructure and environment, closure of the port and, notably, also collision with other vessels. Loss of life of personnel on board the vessels, however, was not among the consequences considered. Existing risk control measures included port and vessel procedures, VTS monitoring, navaids, pilot training and experience, and vessel audits. Nevertheless, the residual risk associated with this scenario was assessed as being ‘High’.[40]
The risk assessment also proposed further control measures which, if implemented, had the potential to further reduce the risk. These proposed further measures included the development of new procedures between VTS, pilots and pilot exempt masters, upgrades of VTS technology, continuous BRM training and VTS training. While TasPorts was subsequently authorised as a VTS provider, it is not known if any of the other additional proposed control measures were implemented or if the identified risk was re-assessed and found to have reduced.
Pilotage in Devonport
The TasPorts port procedures manual laid out the operating parameters for ships calling at Devonport including pilotage and towage requirements, tidal restrictions, and exemptions.
Pilotage exemption
Generally, TasPorts rules required all vessels over 35 m in length to engage a pilot unless the vessel’s master held a valid pilotage exemption certificate (PEC). The TasPorts marine pilotage code set out the required standards for obtaining and renewing pilot licences and pilotage exemption certificates while MAST was the responsible authority for the issue of the licences and exemptions. TasPorts’ marine pilotage code acknowledged the importance of BRM and human factors in pilotage operations. The code required pilots to undertake BRM training prior to the issue of a pilot’s licence, but this requirement did not extend to the issue of pilot exemption certificates.
Goliath’s master held a valid pilotage exemption certificate for Devonport that was first obtained in 2008 and been regularly renewed. The initial application for the pilotage exemption required the master to complete 15 trips[41] with a pilot on board and to pass a local knowledge test for the port in addition to other requirements such as medical fitness and holding an approved seagoing qualification. PECs were valid for a period of 12 months and could be renewed for a further 12 months by completing at least one voyage in the pilotage area. Additionally, vessels over 75 m in length were required to undertake an audit of the ship’s port and pilotage related bridge documentation.
In June 2021, the harbour master instituted an additional requirement for masters seeking to renew a PEC. Exempt masters at several ports in Tasmania, including Devonport, were now required to undertake a check pilotage in addition to the bridge documentation audit. On 21 July 2021, Goliath’s master undertook a check pilotage for Devonport with a licenced check pilot. The check pilotage occurred during arrival at the port and included a bridge documentation audit.
The check pilot’s report noted that the ship’s passage plan and waypoints were consistent with the TasPorts approved plan, that closed loop communications and challenge and response mechanisms were used to effect on the bridge and that communications with VTS were as required. Overall, the report concluded that the master’s conduct of the pilotage was good and conducted in compliance with all relevant port regulations. Goliath’s master’s PEC was subsequently renewed for a further year based on having satisfactorily completed the check pilotage and bridge documentation audit.
Towage and tidal restrictions
TasPorts procedures required ships of Goliath’s size to engage at least 2 tugs for all arrivals and departures at Devonport although this requirement could be reduced if the ship had a bow thruster and/or a stern thruster. The procedures included a specific exemption for Goliath which could arrive or depart without towage (as it was equipped with a bow thruster and VecTwin steering) provided the ship’s under keel clearance was adequate. Nevertheless, Goliath’s master advised that the tug exemption did not prevent them from engaging tug assistance when conditions warranted it and that they had done so several times in the past without issue.
The procedures also stated that, when Goliath was under pilotage, the ‘middle 2 hours of the ebb tide’[42] were to be avoided and that the ship was not to berth ‘in the 'middle of the ebb tide’.[43] TasPorts advised that the tidal restriction on berthing was originally introduced in 2011. The restriction was only strictly applicable when the ship had a pilot on board and not when being piloted by an exempt master for whom it was only recommended guidance. Similarly, while Goliath’s passage plan and exempt master pilotage briefing card also documented the tidal restriction, the master indicated that it was only recommended guidance.
TasPorts advised that the origin and underpinning reasoning for these tidal restrictions could not be conclusively established, although it was probably associated with managing any difficulties encountered in berthing Goliath at berth number One West during an ebb tide.
Similar occurrences
Over the years, flag administrations and safety investigation agencies in Australia and overseas have investigated several incidents involving ships colliding with infrastructure and/or other vessels while manoeuvring in port. Common themes identified in these investigations include the effectiveness of BRM and the management of risk in ports.
Wahei Maru
On 7 November 2018, the Japanese-registered bulk carrier Wahei Maru collided with the wharf in the port of Kobe, Japan. The ship was equipped with a VecTwin steering system similar to Goliath’s. The incident resulted in damage to the ship’s bow and to the wharf.
The Japan Transport Safety Board’s (JTSB) investigation found that, on the approach to the wharf, the ship’s master had not changed the steering selector switch over to the VecTwin steering mode. As the ship closed on the wharf, the master used the joystick to select the ‘astern’ setting on the VecTwin rudders and gave increasing engine movements ahead in effort to slow the ship.
The master did not notice that the rudder indicators showed that both rudders were still in the ‘hover’ (neutral) position. The ship subsequently collided with the wharf at a speed of about 4.3 knots. The JTSB report noted that corrective action taken by the ship’s owner included the creation of a procedure for the changeover which was posted on the steering console and the installation of an audible alert which sounded briefly when the steering selector switch was set to VecTwin steering.
Grand Rodosi
On 8 October 2010, the Liberian-registered bulk carrier Grand Rodosi, collided with the Australian fishing vessel Apollo S in Port Lincoln, South Australia. As a result of the collision, Apollo S, which was not manned at the time, was crushed against the wharf and sank shortly afterwards. Grand Rodosi sustained several relatively small holes in its bow shell plating.
The ATSB transport safety investigation report MO-2010-008 found that the collision occurred during the final turn to approach the berth because the ship’s main engine continued to run ahead despite astern engine telegraph orders by the pilot on the bridge. The main engine, which was being operated from the engine control room, was not allowed sufficient time for starting air to stop the ahead running engine. Consequently, when fuel was introduced into the engine, it continued to run ahead, despite the astern telegraph orders. The investigation also found that the incorrect operation of the engine was not identified by anyone on the ship’s bridge or in the engine room control room until after the collision and that BRM principles could have been better applied during the passage to the berth. Finally, the investigation found that while the port operator had identified several hazards and risk relevant to pilotage in Port Lincoln, the risk of a ship colliding with a wharf or another ship on an adjacent berth, while the berthing manoeuvre was being attempted, had not been identified.
Amarantos
On 10 April 2000, the Maltese-registered bulk carrier Amarantos collided with the wharf in Wallaroo, South Australia. The collision resulted in substantial damage to the wharf, piles, and the grain loader and its supporting superstructure on the wharf. The ship sustained minor non‑structural damage.
The ATSB transport safety investigation report 157 found that the ship’s speed of approach was misjudged by the ship’s pilot on the final approach to the berth. The investigation found that the tugs assisting the ship lacked the power and manoeuvrability to arrest the ship’s momentum and that the angle of approach to the wharf left little room for error. The investigation also found that there was a lack of proper BRM on board and that there was no formal risk assessment completed for the berthing and unberthing of ships of Amarantos’ size in the port of Wallaroo.
Safety analysis
Introduction
On 28 January 2022, shortly before noon, the bulk carrier Goliath collided with the moored tugs York Cove and Campbell Cove in Devonport, Tasmania. The tugs, which were not manned at the time, sustained substantial damage, and subsequently sank. Authorities ashore initiated pollution control and oil spill recovery measures and the ensuing loss of fuel and other oils from the tugs were largely contained. Goliath sustained minor damage to its bow while the tugs were both subsequently declared a constructive total loss.
There were no technical failures or other mechanical issues which could have affected the operation of Goliath’s propulsion and steering systems. It was also considered unlikely that the ship’s officers were experiencing a level of fatigue known to affect performance. Therefore, the following analysis examines the events, actions and conditions leading up to the collision, including the management of bridge resources on board Goliath and the factors that influenced the behaviour of the personnel involved. The analysis also considers the management of risks associated with ships manoeuvring in swing basins in the context of operations at Devonport.
Goliath
The collision
Goliath’s approach to its berth in Devonport involved turning the ship to starboard in the swing basin before it was brought alongside and moored. The practice on board was for the master to manoeuvre the ship through the swing and the subsequent berthing from the conning station on the port bridge wing. This required the transfer of propulsion and steering controls to the port bridge wing. As joystick control was the only available means of rudder control on the bridge wing, joystick steering mode needed to be selected before transferring steering control to the bridge wing.
However, on the day on the accident, when controls were transferred to the bridge wing, the steering mode selector switch was not switched over from manual steering to joystick steering. Consequently, the ship’s steering remained in manual steering mode, controlled by the wheel on the steering console inside the wheelhouse. The master though believed that the transfer of manoeuvring controls to the bridge wing had been successful, and therefore began to manoeuvre the ship using the bridge wing controls.
However, the master’s manoeuvring input did not have the desired effect because control of the rudders remained inside the wheelhouse. When the master realised that the turn was not progressing as expected and that the ship was moving ahead towards the berth, the master selected the ‘astern’ joystick setting and increased the engine setting to ‘half ahead’ in an attempt to slow the ship. This decision was consistent with the master’s belief that the ship was in joystick steering mode, although a glance at the rudder angle indicators would have made it apparent that the rudders were still amidships.
As Goliath advanced on the berth and the moored tugs at an increasing speed, the master continued to issue increasing engine telegraph orders ahead. The engine’s rpm was increased from ‘half ahead’ to ‘full ahead’ and finally to ‘navigation ahead’ to slow the ship. However, the ship’s speed kept increasing. Seconds before the collision, the master checked the rudder angle indicators and realised that they were still amidships. By this time, the collision was unavoidable.
Critical operations checklist
Goliath’s safety management system (SMS) required that a checklist be developed for operations which were conducted frequently, and which were considered to present a significant risk. The transfer of manoeuvring controls from the wheelhouse to the wing was one such operation for which a checklist had been developed.
The procedure for the transfer of steering controls involved a sequence of 5 actions and checks which, if carried out, would have ensured that control had been safely and effectively transferred to the wing. However, a critical step in the sequence—the switching of the steering selector switch to joystick steering mode—was not carried out. Two further checks, which could have alerted the officers to this oversight—a check of the autopilot panel and a function test of the VecTwin joystick, were also not carried out.
Bridge resource management training
However, at the time of the accident, Goliath’s master and second mate had never undertaken BRM training. Although the chief mate had completed this training, it had been about 13 years prior. BRM training would have provided the officers with the techniques and tools to support effective BRM. That in turn would probably have resulted in the single person‑errors that contributed to this accident being detected and the collision prevented.
Events and conditions on Goliath’s bridge
In the 20 minutes leading up to the collision, there were 2 changes of the officer of the watch (OOW). During the handover from the chief mate to the second mate, radio calls from the mooring lines boat distracted both officers and the master from what was otherwise a well-practiced manoeuvre that had been safely executed many times before. Less than a minute had passed after the last radio call before the master ordered the transfer of controls to the bridge wing.
The second mate was taken by surprise when the order was given, probably due to a loss of situation awareness with regard to the ship’s progress on the approach to the swing basin. The second mate immediately moved to respond to the master’s order but in doing so, overlooked the selection of the correct steering mode. This error probably occurred because, when they heard the order, they were not standing where they otherwise would have been (next to the steering console) had they not been distracted by their need to deal with the radio traffic.
The need to change the OOW during a pilotage is a foreseeable risk. The change involves potential disruption to the bridge team and distraction of personnel. There is also the risk of loss of information during the handover, a loss of the shared mental model and loss of situation awareness. The company’s standing order that changes to the OOW were not to occur during a manoeuvre primarily sought to mitigate that risk. However, the definition of what constituted a manoeuvre was open to interpretation, and consequently this order was not effectively implemented on board.
Following the (incomplete) transfer of manoeuvring controls, the master began manoeuvring the ship in the belief that all controls had been transferred successfully. The master and second mate had conflicting understandings of who was responsible for the function test of the joystick that was required by the transfer of bridge controls checklist. Consequently, checks in the wheelhouse and on the bridge wing that could have identified the error were not carried out by either officer.
Good practice dictated that the master visually check any rudder angle order issued against the rudder angle indicator. However, this did not occur until collision was imminent, despite the mounting evidence that their manoeuvring inputs were not having the desired effect. A check of the rudder indicators at any time after the transfer of controls would have immediately alerted the officers to the situation. This would have allowed time to either select the correct steering mode, operate the main engine astern conventionally or take other action to minimise damage and to alert other port users to the situation.
It is also possible that the master’s long association with the ship, calls at the same ports, experience in the role, and repetitive use of the VecTwin joystick system without incident, influenced their perception of the risk involved with the manoeuvre. The master’s use of increasing engine orders ahead to slow the ship, the failure to check the rudder angle indicators, to use conventional astern propulsion or to sound the ship’s whistle indicate that they probably believed that the situation was under control almost until the collision. This points to a confidence in the conduct of the manoeuvre and a false sense of security in the unerring operation of the VecTwin system that was at odds with the actual risks involved.
Past incidents
Goliath had previously been involved in 2 incidents involving the VecTwin joystick steering system and its use. On both occasions, there were several circumstances that were similar to this accident. Both earlier incidents occurred during arrival at Devonport, while the ship was manoeuvring in the swing basin, and involved an ineffective transfer of steering control to the bridge wing joystick. Both incidents resulted in the ship making contact with the shore or the wharf in the vicinity of berth number Three West, with the ship narrowly avoided colliding with Campbell Cove in one instance.
While acknowledging that Goliath’s current managers were not the ship’s managers at the time, these earlier incidents, and the potential lessons learned, offered valuable opportunities to prevent future incidents due to similar contributing factors. They also offered opportunities to identify other factors and improvements that could contribute to the safety of future operations and a reduction of risk.
Safety action that resulted from these earlier incidents included the drafting of a procedure for the transfer of controls and for function testing of the bridge wing joystick. However, other proposed safety action such as amending passage plans to identify and document safe locations for the transfer of controls or for providing refresher bridge resource management training were not implemented. The incidents also offered an opportunity to assess the design of the joystick and its indicator lights from a human centric point of view.
Joystick design
Goliath’s master and other deck officers had an incorrect understanding of the significance of the joystick panel indicator lights. The master believed that the illumination of the green ‘joystick on’ light signified that the joystick could be used to operate the ship’s rudders. They also understood that this must have meant that the ship was in joystick steering mode, that is, the illumination of the ‘joystick on’ light was confirmation that joystick steering mode had been selected on the steering console.
However, the design of the system was such that the illumination of the ‘joystick on’ light bore no relation to the steering mode selected and therefore provided no positive indication that the correct steering mode had been selected.
TasPorts
An analysis of risk assessments from TasPorts show that elements of the risks associated with vessels in the swing basin were identified, albeit in the context of risks to the provision of port services. However, specific risks to personnel on board vessels alongside at berth 3W did not appear to have been considered. The potential for incidents involving vessels manoeuvring in the swing basin and the risks they posed to vessels alongside at berth number 3W was not unforeseeable. Records show at least 2 previous incidents involving Goliath, where the ship narrowly avoided colliding with berth 3W (including one instance with Campbell Cove alongside).
In Devonport, pilot- and tug-exempt ships such as Goliath, the TT Line ferries and Searoad ships regularly utilise the swing basin to manoeuvre in the port. The risk control measures in place at Devonport to manage the risks associated with ships manoeuvring in the port generally relied on pilotage services, the port’s pilotage exemption requirements (in the case of pilot exempt masters), VTS monitoring, effective BRM and port procedures. However, the fact that the collision between Goliath and the tugs did not result in injury to personnel who may have been on board the tugs or adjacent vessels is largely attributable to good fortune rather than effective risk management.
The existence and use of swing basins as well as the associated risks to vessels in the vicinity and to personnel on board are not unique to Devonport. However, the defined scope of this investigation precluded a more comprehensive analysis of incidents, risks, and risk controls associated with vessels manoeuvring in swing basins in Devonport and more widely in ports across Australia.
Findings
ATSB investigation report findings focus on safety factors (that is, events and conditions that increase risk). Safety factors include ‘contributing factors’ and ‘other factors that increased risk’ (that is, factors that did not meet the definition of a contributing factor for this occurrence but were still considered important to include in the report for the purpose of increasing awareness and enhancing safety). In addition ‘other findings’ may be included to provide important information about topics other than safety factors. Safety issues are highlighted in bold to emphasise their importance. A safety issue is a safety factor that (a) can reasonably be regarded as having the potential to adversely affect the safety of future operations, and (b) is a characteristic of an organisation or a system, rather than a characteristic of a specific individual, or characteristic of an operating environment at a specific point in time. These findings should not be read as apportioning blame or liability to any particular organisation or individual. |
From the evidence available, the following findings are made with respect to the collision involving the bulk carrier Goliath and tugs York Cove and Campbell Cove, in Devonport, Tasmania on 28 January 2022.
Contributing factors
- During the transfer of steering and propulsion controls from Goliath’s wheelhouse to the port bridge wing conning station, the steering mode selector switch was not changed from manual steering to joystick steering mode. Consequently, control of the rudders remained at the wheel inside the wheelhouse.
- On transferring to the bridge wing, Goliath's master manoeuvred the ship in the belief that the ship’s steering was in joystick steering mode (which allowed for the use of ahead inputs on the main engine to generate astern thrust). Consequently, as the ship closed on the tugs and wharf, the master’s efforts to slow the ship and avoid collision by using ahead inputs on the main engine had the opposite effect of increasing the ship’s speed, resulting in the collision with the tugs.
- Actions and checks for the effective transfer of steering controls from one conning station to another, documented in the safety management system’s critical operations checklist for transfer of bridge controls, were not fully complied with. Had the actions and checks described in the checklist been carried out, it is likely that the failure to select the correct steering mode would not have occurred or been identified in time to be rectified.
- Bridge resource management was ineffective because:
- The chief mate and second mate were engaged in watch hand over activity in the lead up to a critical phase of the passage
- all the officers on the bridge were distracted by the unexpected and relatively unimportant radio traffic with the mooring line boat
- at the time the master issued the order to transfer controls to the bridge wing, there was no consistent understanding of whether the watch hand over had been completed and which of the mates was assisting the master
- neither the master nor the second mate identified that the correct steering mode had not been selected, that steering control remained at the wheel or that the master’s joystick rudder angle and main engine telegraph orders were not having the desired effect until it was too late to avoid the collision
- the master’s perception of the risk involved with the manoeuvre and the transfer of controls had probably diminished over time due to complacency resulting from extended service on board.
- Neither the master nor the second mate had undertaken required bridge resource management training. This probably contributed to the ineffective implementation of bridge resource management on board, which resulted in the single person errors that contributed to this accident not being detected. (Safety issue)
Other factors that increased risk
- Corrective action, proposed as a result of a previous incident involving factors related to the use of the joystick steering system in 2009 (and while under the ship’s previous management), were not reflected in Goliath's safety management system and had not been fully implemented on board. This lost opportunity to learn and implement corrective action increased the risk of future similar incidents.
- The illumination of the joystick steering panel’s ‘joystick on’ light indicated which panel was selected (or last selected) for use and bore no relation to the steering mode selected. This increased risk as it was misleading and contrary to the understanding of the ship’s officers who believed that the illumination of the light was only possible when the joystick steering mode was selected. (Safety issue)
- TasPorts’ risk assessments for Devonport included consideration of a potential collision between ships manoeuvring in the swing basin and vessels moored in the vicinity, however, the risks to personnel on board those moored vessels and possible risk control measures were not considered.
Safety issues and actions
Depending on the level of risk of a safety issue, the extent of corrective action taken by the relevant organisation(s), or the desirability of directing a broad safety message to the marine industry, the ATSB may issue a formal safety recommendation or safety advisory notice as part of the final report. All of the directly involved parties are invited to provide submissions to this draft report. As part of that process, each organisation is asked to communicate what safety actions, if any, they have carried out or are planning to carry out in relation to each safety issue relevant to their organisation. Descriptions of each safety issue, and any associated safety recommendations, are detailed below. Click the link to read the full safety issue description, including the issue status and any safety action/s taken. Safety issues and actions are updated on this website when safety issue owners provide further information concerning the implementation of safety action. |
Bridge resource management training
Safety issue number: MO-2022-002-SI-01
Safety issue description: Neither the master nor the second mate had undertaken required bridge resource management training. This probably contributed to the ineffective implementation of bridge resource management on board, which resulted in the single person errors that contributed to this accident not being detected.
Design of joystick indicator light
Safety issue number: MO-2022-002-SI-02
Safety issue description: The illumination of the joystick steering panel’s ‘joystick on’ light indicated which panel was selected (or last selected) for use and bore no relation to the steering mode selected. This increased risk as it was misleading and contrary to the understanding of the ship’s officers who believed that the illumination of the light was only possible when the joystick steering mode was selected.
Safety action not associated with an identified safety issue
Whether or not the ATSB identifies safety issues in the course of an investigation, relevant organisations may proactively initiate safety action in order to reduce their safety risk. The ATSB has been advised of the following proactive safety action in response to this occurrence. |
Additional safety action by CSL Australia
On 3 June 2022, CSL Australia advised the ATSB of amendments made to Goliath’s safety management system procedures for navigation, passage planning, watchkeeping, master/pilot exchange and the bridge arrival and departure checklists. The amendments included a requirement for watch handovers during pilotage to be planned and agreed upon by the master in advance and for safe areas to be identified for such handovers to take place.
Additional safety action by TasPorts
On 12 December 2022, TasPorts advised the ATSB that the port’s investigation into the accident resulted in several recommendations for proposed safety action. These included recommendations to:
- amend the port procedures manual to require that Goliath engage a tug and to prohibit the use of the ship’s VecTwin steering system when berthing in Devonport
- amend the port procedures manual and other port rules to prohibit Goliath from swinging on arrival if vessels are alongside at berth number Three West
- review the risk assessment for the port of Devonport with a view to identifying additional mitigation measures
- review Pilotage code to include emergency training for pilotage exemptions
- review and update the port procedures manual to clarify the requirements for Goliath’s entry, pilotage, manoeuvring and berthing in the port including clarifying the applicability of any tidal restrictions.
Glossary
AIS Automatic Identification System
AMSA Australian Maritime Safety Authority
BRM Bridge resource management
CSL Canada Steamship Lines
ECDIS Electronic chart display and information system
EPA Environment Protection Authority
HSEQ Health safety environment and quality
IR Integrated Rating. Integrated ratings are qualified to perform the duties of both an able seaman and an engine rating.
ISM International Management Code for the Safe Operation of Ships and for Pollution Prevention, 1995, as amended
MAST Marine and Safety Tasmania
NFU Non-follow-up steering
PEC Pilotage exemption certificate
RPM Revolutions per minute
SMS Safety management system
SOLAS The International Convention for the Safety of Life at Sea, 1974, as amended
STCW Standards of Training, Certification and Watchkeeping for Seafarers, 1995, as amended
TasPlan Tasmanian Marine Oil and Chemical Spill Contingency Plan
TasPorts Tasmanian Ports Corporation
VDR Voyage data recorder
VHF Very high frequency (radio)
VTS Vessel Traffic Service
Sources and submissions
Sources of information
The sources of information during the investigation included the:
- Australian Maritime Safety Authority
- Bureau of Meteorology
- CSL Australia
- directly involved officers and crew of Goliath
- Environment Protection Authority Tasmania
- investigation reports from the Japan Transport Safety Board
- Marine and Safety Tasmania
- recorded information from Goliath’s voyage data recorder (VDR)
- records, documents, manuals, and logbooks from Goliath
- Tasmanian Ports Corporation
- the master of the fishing vessel Del Richey II.
References
Australian Maritime Safety Authority, 2021, Marine Notice 07/2021 Responsible navigational practices, Canberra, Australia.
Australian Transport Safety Bureau, Report No. 157, Contact between the Maltese flag bulk cargo vessel Amarantos, Wallaroo, SA, 10 April 2000, ATSB, 2000.
Australian Transport Safety Bureau, Report No. MO-2010-008, Collision between the Liberian registered bulk carrier Grand Rodosi and the Australian registered fishing vessel Apollo S in Port Lincoln, SA, 8 October 2010, ATSB, 2012.
Cannon-Bowers, JA, Salas, E, Converse, S A (1993). Shared mental models in expert team decision making. In Mathieu, J, Heffner, T, Goodwin, G, Salas, E, Cannon-Bowers, J. The influence of Shared Mental Models on Team Process and Performance. Journal of Applied Psychology 2000, Vol 85, No. 2, pp. 273-283. American Psychological Association Inc, 2000.
Focus on Bridge Resource Management. Washington State Department of Ecology, 2007.
International Chamber of Shipping 2016, Bridge Procedures Guide, Marisec Publications, London.
International Maritime Organisation (IMO), Standards of Training, Certification and Watchkeeping for Seafarers (STCW) Code, 1995, as amended, IMO, London.
International Maritime Organization (IMO) 1995, International Management Code for the Safe Operation of Ships and for Pollution Prevention (ISM Code) as amended, IMO, London.
International Maritime Organization (IMO) 2014, The International Convention for the Safety of Life at Sea (SOLAS) 1974 as amended, IMO, London.
International Transport Workers’ Federation, STCW A guide for seafarers, ITF, London.
Schager, B. Human Error in the Maritime Industry – How to understand, detect and cope. Marine Profile, Sweden, 2008.
Submissions
Under section 26 of the Transport Safety Investigation Act 2003, the ATSB may provide a draft report, on a confidential basis, to any person whom the ATSB considers appropriate. That section allows a person receiving a draft report to make submissions to the ATSB about the draft report.
A draft of this report was provided to the following directly involved parties:
- directly involved officers and crew of Goliath
- CSL Australia
- Australian Maritime Safety Authority
- Environment Protection Authority Tasmania
- Tasmanian Ports Corporation
- Marine and Safety Tasmania.
Submissions were received from:
- Goliath’s master and second mate
- CSL Australia
- Australian Maritime Safety Authority
- Environment Protection Authority Tasmania
- Tasmanian Ports Corporation
- Marine and Safety Tasmania.
The submissions were reviewed and, where considered appropriate, the text of the report was amended accordingly.
Appendices
Appendix A
Critical operations checklist – Bridge controls changeover procedure
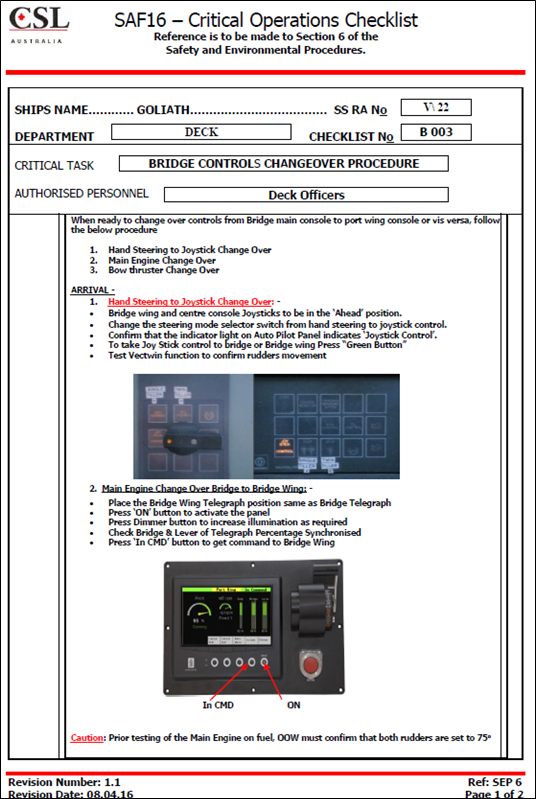
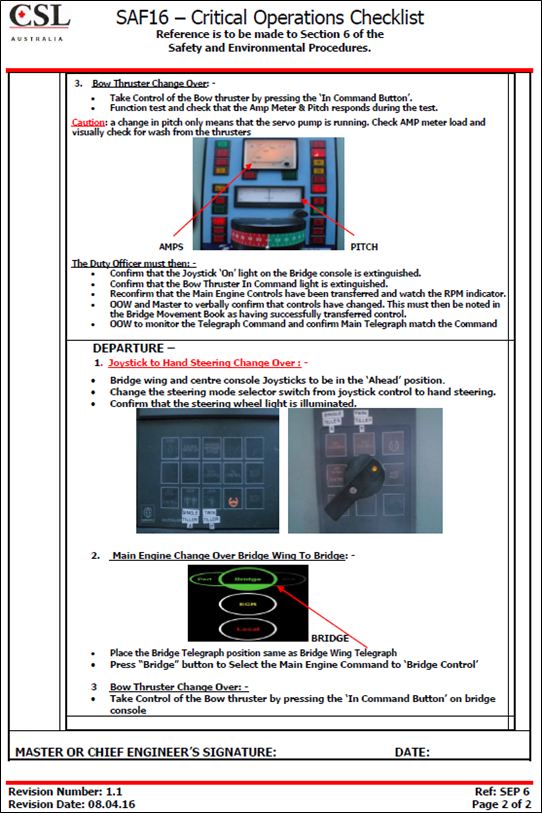
Purpose of safety investigationsThe objective of a safety investigation is to enhance transport safety. This is done through:
It is not a function of the ATSB to apportion blame or provide a means for determining liability. At the same time, an investigation report must include factual material of sufficient weight to support the analysis and findings. At all times the ATSB endeavours to balance the use of material that could imply adverse comment with the need to properly explain what happened, and why, in a fair and unbiased manner. The ATSB does not investigate for the purpose of taking administrative, regulatory or criminal action. TerminologyAn explanation of terminology used in ATSB investigation reports is available here. This includes terms such as occurrence, contributing factor, other factor that increased risk, and safety issue. Publishing informationReleased in accordance with section 25 of the Transport Safety Investigation Act 2003 Published by: Australian Transport Safety Bureau © Commonwealth of Australia 2023 Ownership of intellectual property rights in this publication Unless otherwise noted, copyright (and any other intellectual property rights, if any) in this report publication is owned by the Commonwealth of Australia. Creative Commons licence With the exception of the Coat of Arms, ATSB logo, and photos and graphics in which a third party holds copyright, this publication is licensed under a Creative Commons Attribution 3.0 Australia licence. Creative Commons Attribution 3.0 Australia Licence is a standard form licence agreement that allows you to copy, distribute, transmit and adapt this publication provided that you attribute the work. The ATSB’s preference is that you attribute this publication (and any material sourced from it) using the following wording: Source: Australian Transport Safety Bureau Copyright in material obtained from other agencies, private individuals or organisations, belongs to those agencies, individuals or organisations. Where you wish to use their material, you will need to contact them directly. |
[1] A constructive total loss, in the case of damage to a ship, occurs when the cost of repairing the damage under its insurance terms would exceed the value of the ship when repaired.
[2] Eastern Daylight-saving Time (EDT): Coordinated Universal Time (UTC) + 11 hours.
[3] The testing of the steering gear was done with the steering in manual mode and with all four steering motors running. The test involved the officer of the watch (third mate) on the bridge applying up to 20° of helm to either side, on both rudders, and the deck cadet physically verifying the rudder movements in the steering gear room.
[4] Integrated ratings are qualified to perform the duties of both an able seaman and an engine rating.
[5] Predicted high water was at 0741 with a height of tide of 3.42 m above chart datum.
[6] VHF channel 16 (156.800 MHz) is the international distress, safety and calling frequency. All VHF-equipped vessels are required to maintain a continuous listening watch on this frequency at sea.
[7] VHF channel 6 was the Devonport VHF working channel used for pilotage, towage, and berthing communications.
[8] A voyage data recorder is designed to collect and store data from various shipboard systems in compliance with SOLAS requirements.
[9] In VecTwin steering (joystick) mode, the ‘astern to port’ joystick setting sets the port rudder to a rudder angle of 105° to port and the starboard rudder to a rudder angle of 75° to starboard. In this setting, ahead movements of the ship’s main engine could be used to generate astern thrust and swing its stern to port.
[10] In VecTwin steering (joystick) mode, the ‘astern’ joystick setting sets the port rudder to a rudder angle of 105° to port and the starboard rudder to a rudder angle of 105° to starboard. In this setting, ahead movements of the ship’s main engine could be used to generate astern thrust
[11] Campbell Cove was moored with its head to the north while York Cove was moored outboard of Campbell Cove with its head to the south.
[12] The Tasmanian Ports Corporation (TasPorts) is Tasmania’s State-owned company responsible for the operation and management of eleven Tasmanian ports (including Devonport).
[13] The harbour master and deputy harbour master are responsible for overseeing navigational safety and ensuring compliance with regulatory and statutory requirements for the 11 Tasmanian ports operated by TasPorts.
[14] The TasPorts state operations centre (TSOC) was the main control hub for all port security functions including monitoring of CCTV, alarms, and other functions.
[15] A detention is an intervention action taken by the port State to ensure that the ship will not sail until it can proceed to sea without presenting a danger to the ship or persons on board, or without presenting an unreasonable threat of harm to the marine environment, regardless of whether such action affects the scheduled departure of the ship.
[16] The Environment Protection Authority (EPA) is Tasmania's independent statutory environmental regulator.
[17] Marine and Safety Tasmania (MAST) is a statutory authority established to ensure the safe operation of vessels, provide, and manage marine facilities, and manage environmental issues relating to vessels in Tasmania.
[18] The person with the overall responsibility for ensuring that a response to a tier 2/3 incident is managed and coordinated appropriately and with the authority to direct response and clean-up arrangements at a management level.
[19] According to the Tasmanian Marine Oil and Chemical Spill Contingency Plan (TasPlan) and the National Plan for Maritime Environmental Emergencies (National Plan), level 2 Incidents are more complex in size, duration, resource management and risk and may require deployment of jurisdiction resources beyond the initial response.
[20] Pursuant to section 51(1) of Tasmania’s Marine-related Incidents (MARPOL Implementation) Act 2020.
[21] International Maritime Organization, 2014, The International Convention for the Safety of Life at Sea (SOLAS) 1974 as amended, IMO, London.
[22] International Maritime Organisation, The International Convention on Standards of Training, Certification and Watchkeeping for Seafarers 1978, as amended, IMO, London.
[23] Marine Orders, also described as regulatory instruments or legislative regulations, are legal instruments made by AMSA pursuant to powers under Commonwealth legislation.
[24] In non-follow-up (NFU) mode, the movement of rudder to port or starboard is controlled using a lever. The lever is released when the rudder reaches the required angle.
[25] At the time of the collision, the starboard bridge wing joystick control station was not in commission.
[26] International Maritime Organization, 2018, International Management Code for the Safe Operation of ships and for Pollution Prevention (ISM Code) as amended, IMO, London.
[27] International Maritime Organisation, Standards of Training, Certification and Watchkeeping for Seafarers (STCW) Code, 1995, as amended, IMO, London.
[28] International Chamber of Shipping 2016, Bridge Procedures Guide, Marisec Publications, London.
[29] Focus on Bridge Resource Management. Washington State Department of Ecology, 2007.
[30] Australian Maritime Safety Authority, 2020, Pilot advisory note, Bridge resource management and the reduction of single person errors—advisory note, Canberra, Australia.
[31] Australian Maritime Safety Authority, 2021, Marine Notice 07/2021 Responsible navigational practices, Canberra, Australia.
[32] Schager, B. Human Error in the Maritime Industry – How to understand, detect and cope. Marine Profile, Sweden, 2008.
[33] STCW Code (1995, as amended), Section B, Chapter VIII/2, Part 3-1 – Guidance on keeping a navigational watch, Bridge resource management.
[34] The STCW Convention prescribes minimum standards relating to training, certification and watchkeeping for seafarers which countries are obliged to meet or exceed. The STCW Code supports, explains, and expands on the basic requirements contained in the Convention’s regulations. Part A of the Code is mandatory while Part B of the Code contains recommended guidance intended to help implement the Convention.
[35] The Maritime Labour Convention was established in 2006 under the International Labour Organization to consolidate all up-to-date standards of existing international maritime labour conventions and recommendations and introduced modern standards for the working and living conditions of seafarers. The convention came into force in 2013.
[36] With respect to the ISM Code, a ‘non-conformity’ means an observed situation where objective evidence indicates the non-fulfillment of a specified requirement and an ‘observation’ means a statement of fact made during a safety management audit and substantiated by objective evidence.
[37] The applicable ports were defined in the Marine and Safety (Pilotage and Navigation) Regulations 2017 (TAS).
[38] The master at the time was a different officer and not the person who was master on the day of the accident.
[39] An ‘allision’ is a term used to describe a collision between a vessel and a fixed object or structure or with another stationary vessel.
[40] High risk was defined as a level of risk for which substantial and urgent efforts must be made to reduce it to ‘ALARP’ [As low as reasonably practicable] levels within a defined time period. Significant funding was likely to be required and services may need to be suspended or restricted until risk control options had been actioned.
[41] A ‘trip’ meant a single voyage into or out of a port or marine pilotage area.
[42] For example, on the day of the accident, when high water was at 0741 and low water was at 1422, TasPorts identified the middle 2 hours of the ebb tide as being between 1001 and 1201.
[43] The procedures defined the middle of the ebb tide to be the period beginning 1.5 hours after high water and ending 2.5 hours before low water. For example, on the day of the accident, Goliath arrived on an ebb tide with the ‘middle of the tide’ lasting from 0911 to 1152.