Executive summary
What happened
On the morning of 27 April 2022, a Boeing 737-800 registered VH-YFZ and operated by Virgin Australia Airlines departed from Gold Coast Airport, Queensland. Immediately after take-off, the pilot noticed the aircraft tended to roll to the right, and trimmed the rudder to keep wings level. The aircraft no longer required trim when the flaps were retracted for cruise, but the issue returned when the flaps were extended for landing. There were no warnings of flap skew or asymmetry provided to the flight crew.
A walk-around inspection following the flight revealed that left outboard aft flap had not completely retracted. A subsequent engineering inspection found several components in the aft flap actuation system had failed.
What the ATSB found
The ATSB determined that a pre-existing fatigue crack progressed through the aft flap’s inboard programming roller cartridge resulting in component failure. This cartridge held a roller that guided the aft flap during extension and retraction. The failed cartridge affected aft flap performance when flaps were deployed, and resulted in the aircraft’s tendency to roll to the right. While it could not be determined precisely when the cartridge failed, it likely occurred at some point following touchdown during the previous flight, but before take-off on the incident flight.
Boeing specified a general visual inspection of the left outboard flap. On VH-YFZ, this inspection last occurred in October 2020, with no defects found. It could not be determined whether the fatigue crack was present at the inspection. Ten other instances of cracking and/or failure at the programming roller were reported to Boeing between 2017 and 2022. At least 6 of these were old enough to have been inspected several times prior to failure. Significantly, the area in which the fatigue cracks developed was not included in a detailed inspection that Boeing specified for the flap actuation system.
What has been done as a result
While it was identified that failure of this component would not significantly affect the controllability of the aircraft, the ATSB issued a safety recommendation to The Boeing Company that it take safety action to increase the detection of fatigue cracks in the roller cartridges of 737‑800 prior to failure.
Safety message
While modern aircraft provide pilots with detailed system information, certain malfunctions can still occur without detection, such as in this occurrence. While the flight crew were not able to determine the root cause of the roll tendency during flight, they maintained continual awareness of the issue, reacting quickly and appropriately to maintain control of the aircraft.
The occurrence
At 0706 local time on 27 April 2022, a Virgin Australia Airlines Boeing 737-800 registered VH-YFZ departed from Gold Coast Airport en route to Sydney. It was the first flight of the day for both the aircraft and flight crew. As per normal operating procedures, the aircraft took off with flaps partially deployed. Shortly after take-off, the pilot flying noticed that the aircraft had a tendency to roll to the right and added 1.5° of left rudder trim[1] to keep the wings level. When the flaps were retracted during climb, the rudder was trimmed back to 0°.
As the aircraft climbed through 10,000 feet, the cabin manager mentioned to the flight crew that a ‘muffled rumble’ could be heard coming from the left side of the aircraft. In the cockpit, the captain could perceive a sound, but thought it to be more of a ‘whine’. The flight crew discussed potential sources for the noise, and attributed it to some slight damage on one of the engine fan blades that had been previously identified and logged for maintenance.
The autopilot was engaged for most of the flight, including during flap deployment for the first portion of the approach into Sydney Airport. As the aircraft intercepted the localiser[2] track and the wings levelled out, the pilot flying noticed that the control column was substantially laterally displaced. The pilot disengaged the autopilot and immediately felt the aircraft rolling to the right. The pilot used the aileron to keep wings level as the rudder was trimmed back to 1.5° to the left. The flight crew landed the aircraft without further incident.
Once the passengers had disembarked, one of the flight crew conducted a walk-around inspection of the aircraft and noticed that part of the left outboard aft flap had not completely retracted after landing, resulting in a skew (Figure 1). The flight crew received no flap asymmetry or flap skew warnings throughout the flight. A subsequent engineering inspection identified component failures in the left outboard aft flap actuation system.
Figure 1:The skewed left outboard aft flap of VH-YFZ after landing in Sydney
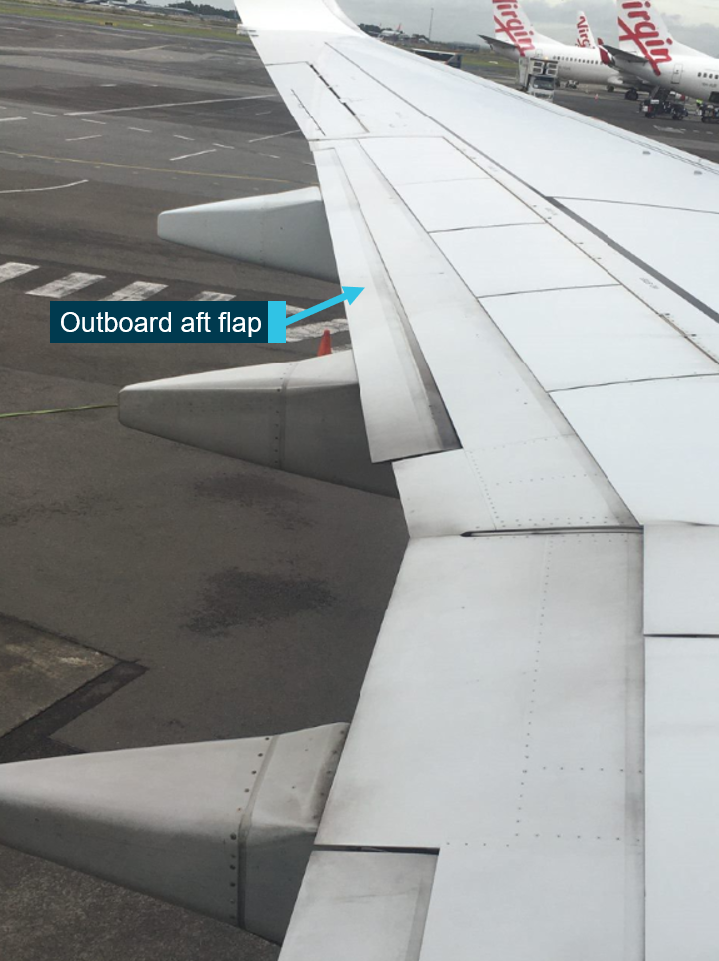
Source: Flight crew, annotated by the ATSB
Context
Flap actuation system and damage description
The aircraft’s trailing edge flap system contains an outboard aft flap nested within a larger main flap when fully retracted. Upon extension, a ball screw and gimbal transmit forces into pushrods rods to deploy the aft flap. The aft flap is guided by several rollers along tracks connected to the main flap. The roller on the inboard edge of the flap is known as the inboard programming track roller. In this occurrence, a component known as a ‘cartridge’ securing this roller to the aft flap failed (Figure 2).
Figure 2: The failed cartridge (left) and example cartridge highlighted in blue (right)
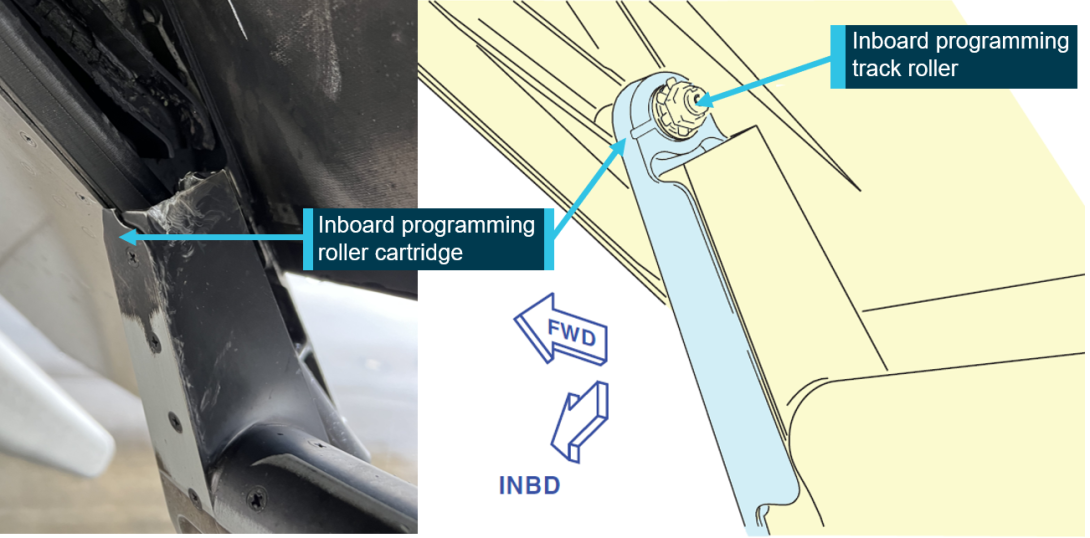
Source: Virgin Australia, copyright © Boeing. Used with permission, modified by the ATSB
When the damaged programming roller cartridge was found, the section still attached to the aft flap had caught on the underside of the main flap, damaging the skin (Figure 3, left). This contact with the main flap prevented the aft flap from retracting correctly. The other section of the cartridge, including the roller, detached from the aircraft and was not recovered. In addition to the damaged programming roller cartridge, one of the pushrods in the flap actuation system was also found to have failed (Figure 3, right).
Figure 3: The programming roller cartridge obstructed by the main flap (left) and the failed pushrod (right)
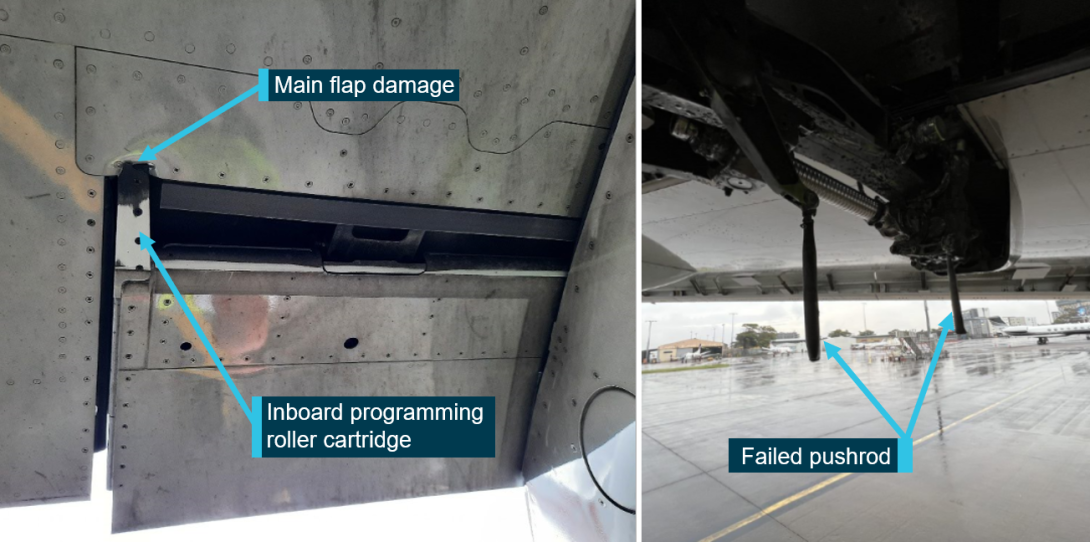
Source: Virgin Australia, annotated by the ATSB
The flap skew sensor—responsible for detecting asymmetry or skew in the flaps—tracked the position of the gimbal as the flaps extended and retracted. However, the failed cartridge and pushrod had no effect on the gimbal, so asymmetry or skew in the aft flap could not be detected.
Component examination
The failed inboard programming roller cartridge and pushrod were sent to the ATSB for detailed technical examination. Two regions of fatigue cracking were identified in the cartridge (Figure 4). These were separated by deformation resulting from contact with the main flap. Outside of these two regions, the fracture surfaces appeared to be consistent with overstress, with no evident fatigue cracking.
Figure 4: The fracture surface of the cartridge, with the entire component inset
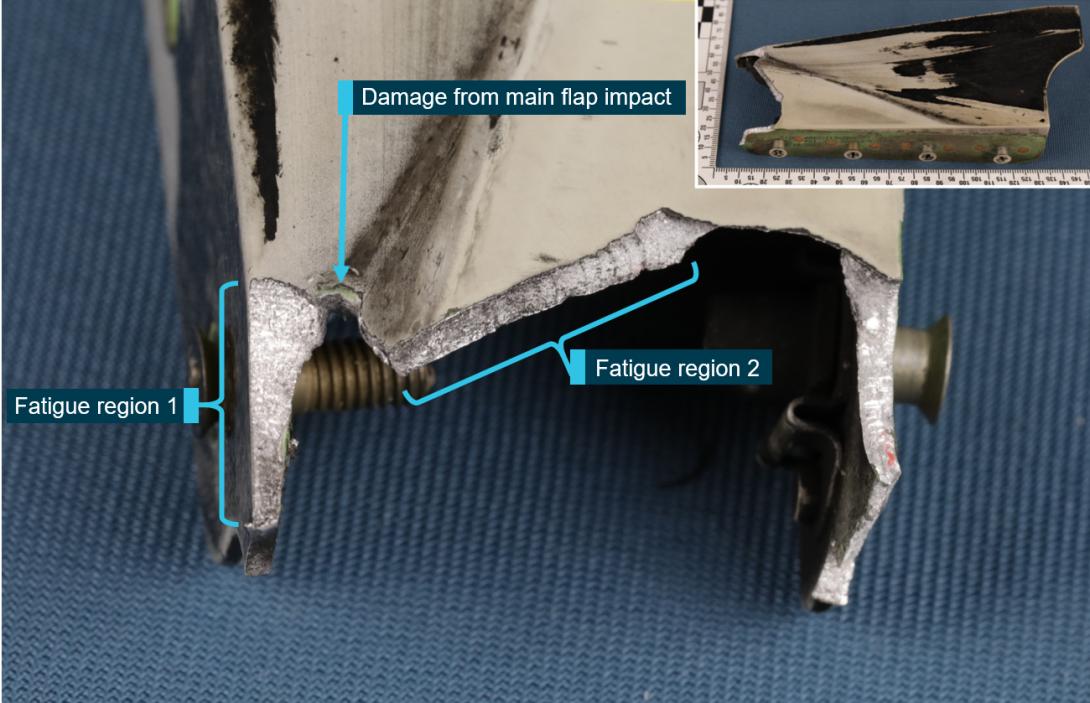
Source: ATSB
The two fatigue regions were examined using optical microscopy (Figure 5). Red arrows indicate the most obvious beachmarks—evidence of crack progression. The orientation of the beachmarks suggest the crack propagated in the direction indicated by the orange arrows. The crack origin was likely near the bottom of fatigue region 1. It was either obscured by smearing of the metal, or was on the section of cartridge that was not recovered. Blackening and corrosion pitting on the lower half of fatigue region 1 indicate that this portion of the crack had been present for some time.
Figure 5: Fatigue regions 1 (left) and 2 (right) on the failed programming roller cartridge
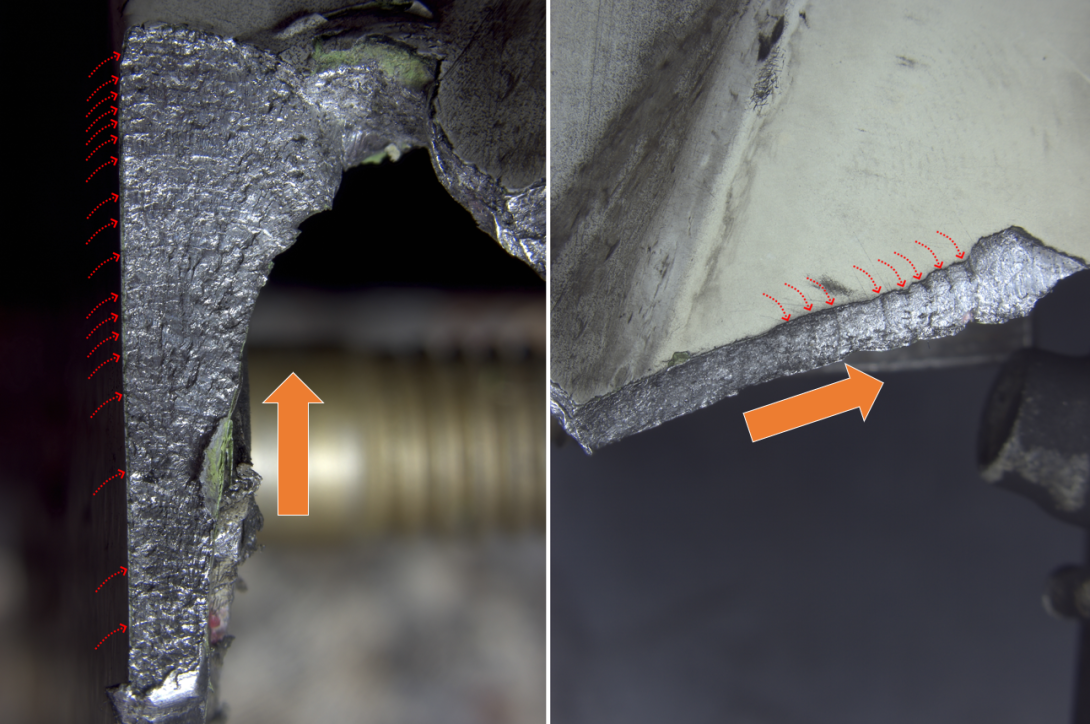
Red arrows point to observed beachmarks. Orange arrows indicate the direction of crack propagation.
Source: ATSB
A visual examination of the pushrod revealed no evidence of pre-existing damage. Localised deformation at the fractured ends was indicative of buckling/bending failure (Figure 6). This was consistent with the compressive forces it would have experienced as the aft flap become stuck during retraction.
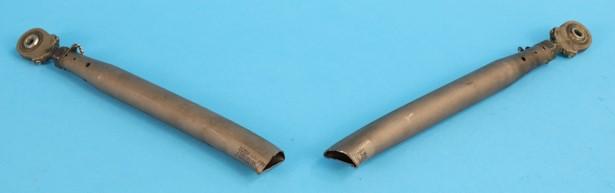
Source: ATSB
Maintenance history
The programming roller cartridge, pushrod and associated aft flap actuation system were the original parts installed when VH-YFZ was manufactured in 2017. They had acquired 6,377 flight cycles since their installation. Inspection of the roller cartridge was conducted as part of a general visual inspection of the left flap. This was scheduled every 6,000 flight cycles or every 36 months. Guidance from Boeing described this type of inspection as:
A visual examination of an interior or exterior area, installation or assembly to detect obvious damage, failure or irregularity. This level of inspection is made from within touching distance, unless otherwise specified. A mirror may be necessary to enhance visual access to all exposed surfaces in the inspection area.
This inspection was performed on-wing with flaps deployed, and last occurred on VH-YFZ in October 2020, with no defects identified.
A more detailed on-wing inspection was specified for the flap actuation system, which Boeing recommended every 12,000 flight cycles. In the associated task card, the engineer was required to perform ‘a detailed visual inspection of… inboard and outboard programming rollers’, and a diagram was provided (Figure 7). The roller cartridge was not an intended part of the inspection. This inspection had not been carried out on VH-YZF as it was not was not yet due.
Figure 7: Reference diagram for inspection of the inboard programming roller
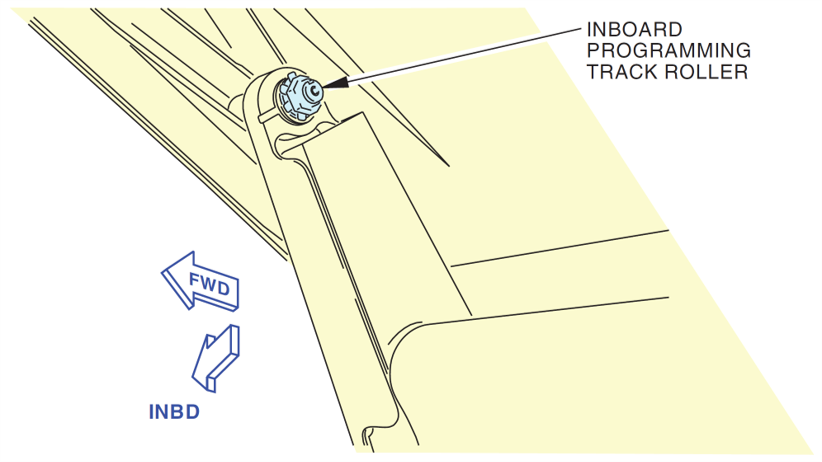
Source: Copyright © Boeing. Used with permission
Prior to the occurrence flight, there were no reports of aircraft handling issues related to VH-YFZ, and recorded data from the previous flight showed no significant rudder input required to keep the wings level. Walk-arounds were conducted by the captain and an engineer before the flight and no abnormalities with the flaps were reported.
Similar occurrences
At the time of writing, Boeing had received 10 reports of similar occurrences in which a skewed flap resulted from similar cracks and/or failures at the aft flap programming roller during flight operations. All of these reports were received between 2017 and 2022. In the reports where the failure mechanism was provided, some described cracking through the roller cartridge, while others reported failure of the roller itself. Six of these reports included flight cycles and, in every instance, the number of flight cycles prior to failure was between 14,000 and 29,000.
As a result of these reports, Boeing performed a safety analysis of this condition to determine whether the event presented a potential safety issue to the affected 737 fleet. As part of the study, Boeing performed an aerodynamic review of worst-case-scenario events involving the loss of different sections of trailing edge flaps, and the effect those losses would have on the pilot’s ability to control the aircraft in the roll axis. For each of the studied events involving skews or losses of the outboard aft flap, Boeing found that the aircraft remained well within the bounds of controllability by pilots, and the issue was evaluated to result in a slight increase in workload for the pilot in the worst possible case. Based on prior occurrences, Boeing determined that fleet experience aligned with that severity study, and that the rate of occurrence was less than that required by the United States Federal Aviation Administration for the level of hazard presented.
Safety analysis
Flap component failure
Detailed technical examination identified that a fatigue crack propagated through the inboard programming roller cartridge on the left outboard aft flap, eventually resulting in failure of the cartridge. It is not clear exactly when this failure occurred, although the absence of any handling issues in the previous flight suggests that the failure was likely at some point after the previous flight’s touchdown at Gold Coast Airport.
It is also likely that the aft flap was fully and properly retracted following the previous flight. As, if it had not retracted properly—due to a failed cartridge caught on the main flap—the resulting skew would probably have been detected on at least 1 of the 2 walk-around inspections conducted prior to the occurrence flight. Additionally, any degree of cartridge damage that still permitted full flap retraction would likely have been obscured by the flap mechanism and therefore not identifiable during a walk‑around. Finally, the right-rolling tendency observed while the flaps were deployed indicates that the roller cartridge failed prior to take-off, noting that no parts of the roller cartridge were found at the airport.
The failure changed the position of the aft flap, resulting in the described asymmetric performance. When the flaps were retracted for cruise, it is possible the failed cartridge caught on the main flap, preventing compete retraction. This would explain the noise heard by the cabin manager; however, the aircraft handled normally, suggesting either the flap retracted correctly or retracted sufficiently to not affect handling.
Scheduled component inspection
Blackening and pitting of the roller cartridge fracture surface suggests that the crack might have been present for some time, but it could not be determined whether any cracking was present at the last general inspection of the left outboard flap in October 2020. The cracking observed was predominantly on the side of the cartridge that abutted the roller track. It would therefore have been very difficult to observe on-wing. There have been 10 similar occurrences involving cracking and/or failure at the aft flap programming roller during flight operations. Of the 6 occurrences where the component age was reported, the aft flap actuation system was old enough to have been inspected for fatigue cracks several times prior to failure, as part of the general visual flap inspection.
The more detailed inspection for the flap actuation system was not due on VH-YFZ for another 5,600 cycles; however, on each of the 6 aircraft mentioned above the programming rollers would have been inspected at least once prior to failure. As with the general visual inspection, this detailed inspection was performed on-wing, restricting observation of the cartridge. Additionally, while the task card specified an examination of the programming rollers, the cartridges that housed them were not included.
Findings
ATSB investigation report findings focus on safety factors (that is, events and conditions that increase risk). Safety factors include ‘contributing factors’ and ‘other factors that increased risk’ (that is, factors that did not meet the definition of a contributing factor for this occurrence but were still considered important to include in the report for the purpose of increasing awareness and enhancing safety). In addition ‘other findings’ may be included to provide important information about topics other than safety factors. Safety issues are highlighted in bold to emphasise their importance. A safety issue is a safety factor that (a) can reasonably be regarded as having the potential to adversely affect the safety of future operations, and (b) is a characteristic of an organisation or a system, rather than a characteristic of a specific individual, or characteristic of an operating environment at a specific point in time. These findings should not be read as apportioning blame or liability to any particular organisation or individual. |
From the evidence available, the following findings are made with respect to the flight control event involving Boeing 737-800, registered VH-YFZ at Gold Coast Airport, Queensland on 27 April 2022.
Contributing factors
- Failure of the inboard programming roller cartridge was due to undetected fatigue cracking that occurred in an area that was not included in the detailed flap actuation system inspection. (Safety Issue)
- The failed roller cartridge affected aft flap performance when flaps were deployed, resulting in a tendency for the aircraft to roll to the right.
Safety issues and actions
Central to the ATSB’s investigation of transport safety matters is the early identification of safety issues. The ATSB expects relevant organisations will address all safety issues an investigation identifies. Depending on the level of risk of a safety issue, the extent of corrective action taken by the relevant organisation(s), or the desirability of directing a broad safety message to the aviation industry, the ATSB may issue a formal safety recommendation or safety advisory notice as part of the final report. All of the directly involved parties were provided with a draft report and invited to provide submissions. As part of that process, each organisation was asked to communicate what safety actions, if any, they had carried out or were planning to carry out in relation to each safety issue relevant to their organisation. Descriptions of each safety issue, and any associated safety recommendations, are detailed below. Click the link to read the full safety issue description, including the issue status and any safety action/s taken. Safety issues and actions are updated on this website when safety issue owners provide further information concerning the implementation of safety action. |
Undetected cracking resulted in failure
Safety issue number: AO-2022-029-SI-01
Safety issue description: Failure of the inboard programming roller cartridge was due to undetected fatigue cracking that occurred in an area that was not included in the detailed flap actuation system inspection.
Sources and submissions
Sources of information
The sources of information during the investigation included:
- the flight crew
- Virgin Australia Airways
- The Boeing Company.
Submissions
Under section 26 of the Transport Safety Investigation Act 2003, the ATSB may provide a draft report, on a confidential basis, to any person whom the ATSB considers appropriate. That section allows a person receiving a draft report to make submissions to the ATSB about the draft report.
A draft of this report was provided to the following directly involved parties:
- the flight crew
- Virgin Australia Airways
- The Boeing Company
- the Civil Aviation Safety Authority
- the United States National Transportation Safety Board.
Submissions were received from:
- Virgin Australia Airways
- The Boeing Company.
The submissions were reviewed and, where considered appropriate, the text of the report was amended accordingly.
Purpose of safety investigationsThe objective of a safety investigation is to enhance transport safety. This is done through:
It is not a function of the ATSB to apportion blame or provide a means for determining liability. At the same time, an investigation report must include factual material of sufficient weight to support the analysis and findings. At all times the ATSB endeavours to balance the use of material that could imply adverse comment with the need to properly explain what happened, and why, in a fair and unbiased manner. The ATSB does not investigate for the purpose of taking administrative, regulatory or criminal action. TerminologyAn explanation of terminology used in ATSB investigation reports is available here. This includes terms such as occurrence, contributing factor, other factor that increased risk, and safety issue. Publishing informationReleased in accordance with section 25 of the Transport Safety Investigation Act 2003 Published by: Australian Transport Safety Bureau © Commonwealth of Australia 2022 Ownership of intellectual property rights in this publication Unless otherwise noted, copyright (and any other intellectual property rights, if any) in this report publication is owned by the Commonwealth of Australia. Creative Commons licence With the exception of the Coat of Arms, ATSB logo, and photos and graphics in which a third party holds copyright, this publication is licensed under a Creative Commons Attribution 3.0 Australia licence. Creative Commons Attribution 3.0 Australia Licence is a standard form licence agreement that allows you to copy, distribute, transmit and adapt this publication provided that you attribute the work. The ATSB’s preference is that you attribute this publication (and any material sourced from it) using the following wording: Source: Australian Transport Safety Bureau Copyright in material obtained from other agencies, private individuals or organisations, belongs to those agencies, individuals or organisations. Where you wish to use their material, you will need to contact them directly. |
[1] In a 737-800, rudder trim makes a small change to the rudder position in order to maintain coordinated flight without constant pilot input.
[2] The localiser is part of the Instrument Landing System and provides lateral position necessary to align with the runway centreline.