Executive summary
What happened
On 22 December 2021, at around midday, a student pilot departed Muchea/Greenside ALA, Western Australia, on a training area solo flight in the Jabiru J170-C aircraft registered 24-7496. On return, during the downwind leg of the circuit, the pilot commenced configuring the aircraft for landing, at which point a vibration from the engine was felt. The engine gauges read as normal and the vibration reduced with throttle reduction.
Shortly after, while on final approach, the pilot observed emus crossing the runway around the normal touchdown point and conducted a go-around. While on climb at around 800 feet, there was a loud ‘bang’ and the pilot observed that the propeller had separated from the aircraft. The pilot subsequently landed in a paddock, approximately 2.5 km from the end of the runway. The aircraft suffered minor damage and the pilot was uninjured. The propeller was not recovered.
What the ATSB found
The propeller separated as a result of fracture of the propeller bolts that was likely related to a loss of bolt tension. However, the factors contributing to any loss of tension were not able to be determined.
The student pilot had recently undertaken several hours’ worth of flight emergency training, which positively influenced the pilot’s actions and contributed to the safe outcome.
Safety message
Pilots should remain vigilant to transient or persistent changes to the normal operation of their aircraft. Such changes may be indicative of an impending failure of a critical component or system. As such, a prudent course of action would be to land as soon as practicable and have the aircraft inspected. Even so, in-flight emergencies will continue to occur, and when faced with such an event, emergency training practice and recurrence will increase the likelihood of pilots achieving a safe outcome.
The investigation
Decisions regarding whether to conduct an investigation, and the scope of an investigation, are based on many factors, including the level of safety benefit likely to be obtained from an investigation. For this occurrence, a limited-scope investigation was conducted in order to produce a short investigation report, and allow for greater industry awareness of findings that affect safety and potential learning opportunities. |
The occurrence
On 22 December 2021, at around midday, a student pilot departed Muchea/Greenside aeroplane landing area (ALA), Western Australia, on a training area solo flight in the Jabiru J170-C aircraft registered 24-7496. The pilot flew for approximately 70 minutes before returning to land at Greenside ALA. During this time, the pilot did not observe anything unusual with the aircraft’s performance.
The pilot joined the downwind leg of the circuit (heading west) and around this time, observed a burning pine smell, which was significant enough for the pilot to look around the cabin and outside for a source. The smell dissipated and was not observed for the remainder of the flight. Shortly after observing the smell, the pilot commenced configuring the aircraft for landing, at which point a significant vibration from the engine was felt. The pilot immediately checked the engine gauges and noted everything was normal. The vibration lessened significantly upon reduction of the throttle. As a result, the pilot re-checked the gauges, which were still normal, and focused on continuing the circuit.
While on final approach, the pilot observed emus crossing the runway around the normal touchdown point, which prompted the pilot to conduct a go-around. The pilot then flew down the remainder of the runway, cleared the hangars and then the highway at the eastern end of the airstrip, climbing through approximately 500-600 feet. No abnormal vibration was observed at any point during the go-around.
Between 5 and 10 seconds after clearing the highway, at an altitude of around 800 feet, there was a loud ‘bang’ which was heard by witnesses back at the hangars. At the same time, the pilot noted that the propeller had separated from the aircraft.
After securing the engine, the pilot elected to land ahead and configured the aircraft for a glide to reach some cleared paddocks. The pilot then made a MAYDAY[1] call that was received nearby at Pearce RAAF base, who contacted the chief flying instructor at Muchea. The pilot subsequently conducted an uneventful landing in a paddock, approximately 2.5 km from the end of the runway. The aircraft suffered minor damage to the nose cowl (Figure 1) and right, main landing gear. The pilot was uninjured.
Figure 1: Propeller flange and nose cowl damage
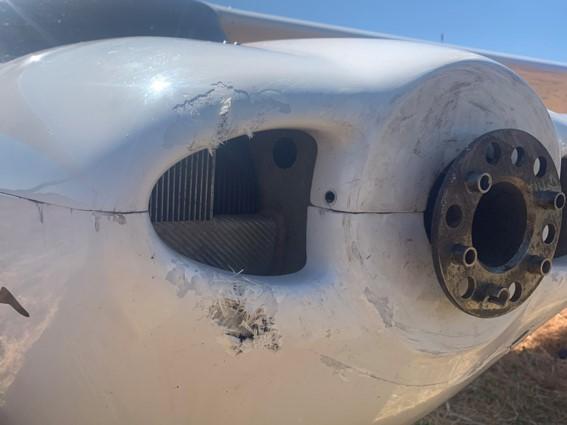
Source: Aircraft operator
Context
Pilot information
The student pilot had approximately 70 hours flying experience, all of which was on the Jabiru J170. The pilot had recently undertaken an area training flight with an instructor and had 3 hours of emergency procedures training, including engine failure, over the previous 5 weeks. The pilot commented that the training positively influenced their actions, helped them remain calm and contributed to the safe outcome.
The pilot also had a debrief with the operator after the event and made the following comments to the ATSB:
- They had not experienced anything like the vibration previously. Despite this, everything appeared to be safe to fly the aircraft in the short term because the vibration had reduced rapidly with throttle reduction and the engine gauges read as normal. Nevertheless, after landing, the pilot had planned to discuss with the chief pilot what was experienced.
- In hindsight, recognising the vibration as an indicator of impending failure, there was an opportunity to cut the circuit short and land as soon as possible. Alternatively, there was an opportunity to land long, past the emus. However, the pilot was also concerned about the possibility of more emus further down the runway, which had been encountered previously.
Aircraft information
The Jabiru J170-C is a 2-seat, light sport aircraft with a high-wing and fixed undercarriage. The subject aircraft was manufactured and first registered in 2010. It was powered by a Jabiru 2200B 4-cylinder engine, with a Jabiru C000242-series, 2-blade, fixed-pitch propeller, constructed of hoop pine, sheathed in fibreglass.
The occurrence propeller, serial number 3050, was manufactured in January 2009. The operator estimated that it had 1,500-1,600 hours in service. The propeller was overhauled by the manufacturer in February 2021. The leading-edge urethane wear strip started to disbond after about 50 hours post-overhaul and was returned to the manufacturer for repair. After the repair, the operator visually inspected the propeller, checked the balance, and re-fitted it to the aircraft. The propeller subsequently accumulated 7.9 hours up to the occurrence.
Operator information
The operator held RAAus Level 2 maintenance authority and had owned and maintained Jabiru aircraft since 2009. The operator advised that
- Propellers are fitted and inspected in accordance with the Jabiru maintenance manual, including a check of the propeller bolt torques after the first flight following fitment.
- Prior to the occurrence flight, the chief pilot conducted a thorough pre-flight inspection, as a demonstration to a new student pilot. The propeller was inspected for damage and security, including a check for any play or movement of the propeller on the end of the crankshaft. There were no anomalies noted.
- There were no reported unusual engine or propeller vibrations in the flights since the most recent propeller fitment.
- The propeller attachment hardware was periodically replaced when displaying any significant wear.
Physical evidence examination
Propeller assembly and maintenance
The Jabiru C000242-series wooden propeller was attached to the propeller flange by 6 propeller bolts (Figure 2). The propeller bolts were specified as either AN4-37 or AN4-40, meaning they were approximately 4 inches (10 cm) in length. They were installed with the bolt heads facing rearwards. The gap between the rear of the flange and the front of the engine cowl did not allow for the bolts to be installed or removed with the cowl in place.
The bolts were installed through stainless steel guide bushes, inserted into the flange. The bushes are a close fit (no free-play) in the rear of the propeller hub. A woven fibreglass composite backing plate sits between the flange and propeller hub and provides for attachment of the spinner.
In this installation, the bolts were assembled with Belleville washers,[2] which was a recommended alternate propeller mounting system, introduced by Jabiru in 2005. The purpose was to allow the assembly to better account for seasonal changes in the wooden hub dimensions and as such, reduce the frequency of inspections of propeller bolt tension. Jabiru maintenance manual JPM3L1-4 indicated that the propeller bolts must be checked after the first flight following installation and then recommended every 100 hours and/or annually thereafter. Jabiru Service Bulletin JSB014-1 indicated that a loss of bolt tension can cause the propeller to move and fret[3] on the mounting flange.
Figure 2: Propeller assembly
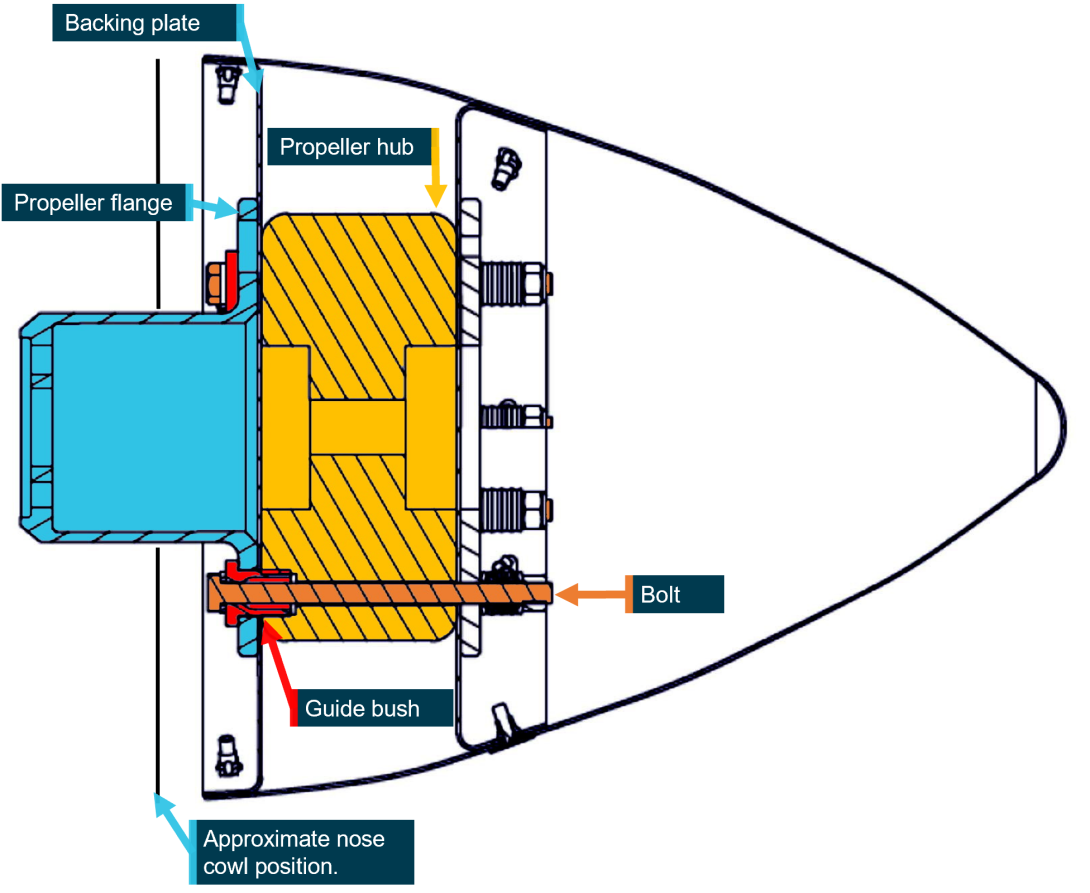
Source: Jabiru (annotated by ATSB)
Examination
In an effort to locate the separated propeller, the operator conducted an extensive aerial photographic survey (approximately 89 hectares), covering the flightpath and surrounding area to the east of the airstrip. Despite this, the separated propeller assembly was not recovered. As a result, component examination by the ATSB was limited to the propeller flange and 5 (of 6) remaining guide bushes (Figure 3).
Figure 3: Propeller flange detail
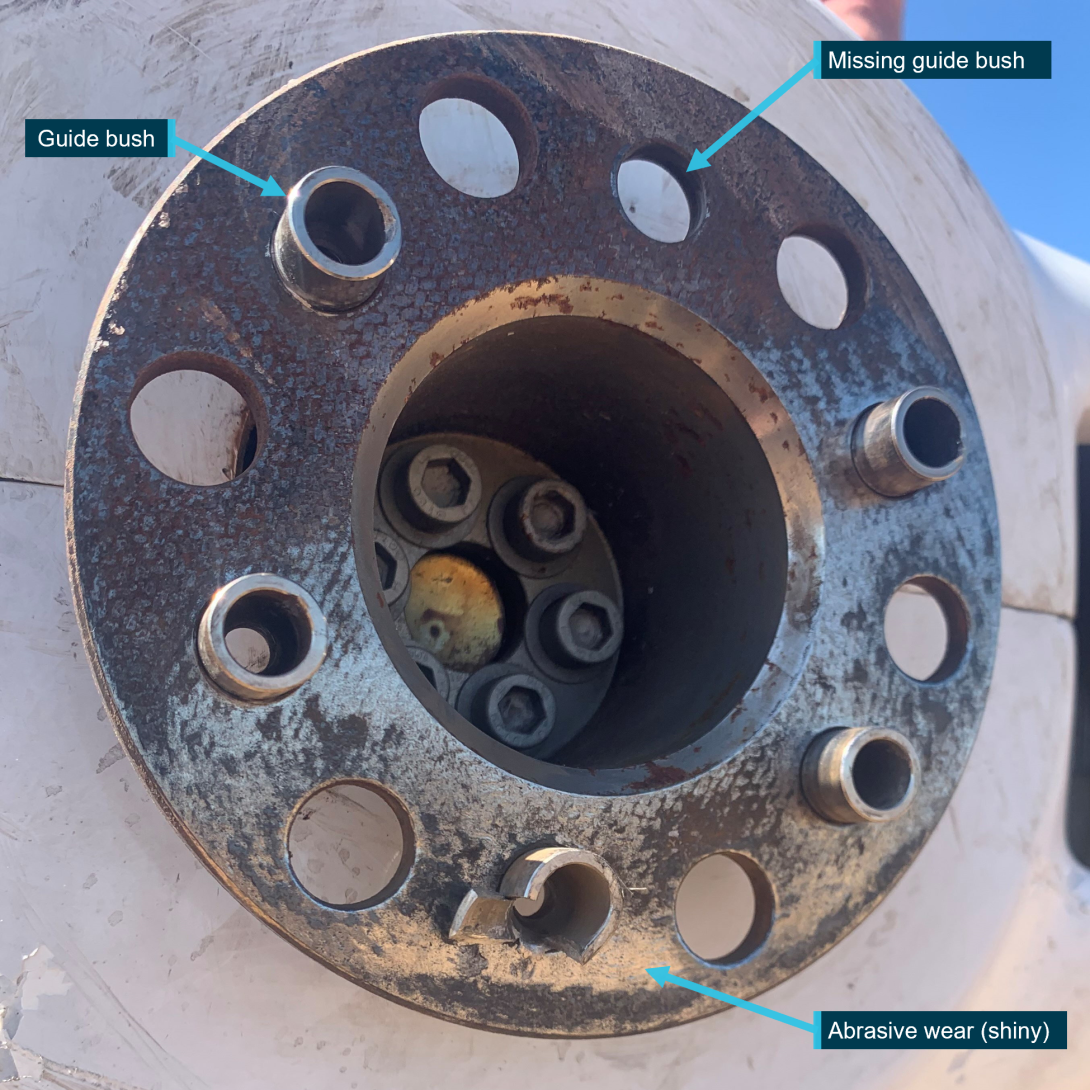
Source: Aircraft operator, modified by the ATSB
The examination found that:
- The flange forward face exhibited abrasive wear patterning consistent with the fibreglass weave of the backing plate, on one-half of the forward face of the flange. The wear had removed the surface contamination from the flange and microscopic grooves were worn into the surface in some areas. The presentation of the wear indicated that it likely predated the first indications of vibration observed by the pilot.
- Localised fretting wear was present between the guide bush and the rear face of the flange (Figure 4). The greatest amount of wear was associated with those bushes on the opposite half of the flange from the wear on the forward face. Surface contamination from the flange had also transferred to the bushes. This was most notable on those holes with the most wear indications.
- One of the bushes had a section of the wall fractured laterally and the remaining bushes had small amount of deformation on the inside rim of the forward face. This was a result of contact with the bolt shank at the point of the propeller separation.
- There were no indications of how the missing bush separated from the flange, however wear around the associated hole indicated that it was in situ in the time leading up to the occurrence.
Figure 4: Wear from drive bush on propeller flange
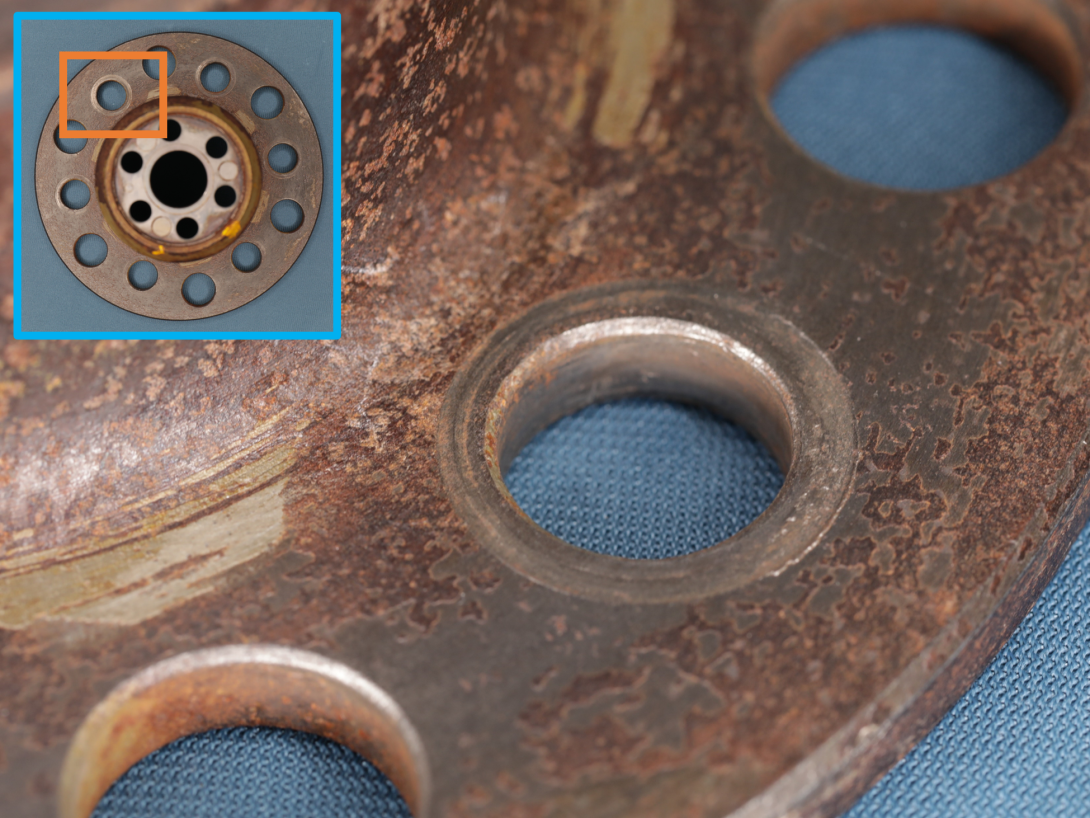
Source: ATSB
Previous occurrences
Review of the ATSB aviation occurrence database found five other instances of in-flight propeller separation, involving Jabiru aircraft:
- The ATSB investigated a March 2013 occurrence (AO-2013-046), involving a propeller separation as a result of fatigue fracture of the bolts securing the propeller flange to the engine crankshaft, and therefore a different point of fracture to the subject occurrence. In response to that occurrence and safety issues identified, Jabiru took several safety actions to reduce the likelihood of reoccurrence.
- Another 2013 event, a wooden propeller separated from a J200B aircraft while in the cruise phase of flight. Four of the bolts had fractured at the heads and two remained in situ, having torn through the hub. It was a reported as probable maintenance issue, related to over‑tensioning the propeller bolts.
- In 2021, the flight crew of a J230 aircraft experienced noticeable, but not severe vibration that did not respond to a reduction in throttle. The engine operation was normal. The pilots continued the flight and because of the continued vibration, they assessed alternative landing options. Approximately 20 minutes after the vibration onset, the propeller departed the aircraft. The pilots subsequently identified a suitable landing area and conducted a forced landing on a track through a paddock.
- Also in 2021, the pilot of a J160 aircraft reported a very rough running engine and after 30 seconds, the engine stopped. The pilot conducted a forced landing into a clearing and, upon exiting the aircraft, observed that the propeller had separated from the aircraft and that the propeller mounting bolts had fractured.
- In January 2022, a propeller separated as a result of broken propeller bolts after a reported bird-strike. That incident is the subject of ATSB investigation AO-2022-013.
No injuries were sustained in any of the above occurrences.
Safety analysis
Propeller separation
The operator indicated that the propeller bolts were installed in the correct orientation, and as such, there was insufficient clearance between the propeller flange and nose cowl for the bolts to back out of the flange. Therefore, the absence of propeller bolts retained in the flange indicted that the propeller ultimately separated from the aircraft due to fracture of the bolts.
Without the bolts available for examination, the reason for the propeller bolt fractures was not conclusively determined. However, the evidence of movement and fretting on the flange was consistent with a loss of clamping force or low bolt tension. The pilot-observed vibration and smell of burnt pine in the minutes prior to the separation was also evidence of relative movement between the wooden propeller and the mounting hardware. Vibration in a normally rigid system will introduce abnormal loading conditions, subjecting components to stresses beyond design considerations. Additionally, fretting wear can significantly reduce the fatigue limit and hence, the working life of components in the assembly.
The ATSB considered several possible reasons for the loss of bolt tension, including an error in the installation, worn or defective hardware, or an undiagnosed issue with the propeller itself. However, in the absence of further physical evidence or any indication of assembly or maintenance issues, the factors contributing to the loss of bolt tension were not able to be conclusively determined.
Decision-making
The engine vibrations and burning timber smell alerted the pilot to the abnormal situation from the powerplant. However, the pilot’s decision-making in relation to the developing situation was influenced by a combination of their experience (having had no similar encounters) and the information presented to them, indicating that the engine had returned to normal. Therefore, when faced with wildlife crossing the runway, the pilot applied the otherwise appropriate adage ‘if it’s not right – go-around’. As a result, the pilot was faced with an emergency off-field landing when the propeller subsequently separated. Despite this, the pilot executed the landing calmly and safely, which they attributed to their recent emergency training.
Findings
ATSB investigation report findings focus on safety factors (that is, events and conditions that increase risk). Safety factors include ‘contributing factors’ and ‘other factors that increased risk’ (that is, factors that did not meet the definition of a contributing factor for this occurrence but were still considered important to include in the report for the purpose of increasing awareness and enhancing safety). In addition ‘other findings’ may be included to provide important information about topics other than safety factors. These findings should not be read as apportioning blame or liability to any particular organisation or individual. |
From the evidence available, the following findings are made with respect to the In-flight propeller loss involving Jabiru J170, registration 24-7496, 2.6 km north-east of Muchea, Western Australia on 22 December 2021.
Contributing factors
- The propeller separated as a result of fracture of the propeller bolts that was likely related to a loss of bolt tension. The mechanism for the loss of bolt tension was not determined.
Other findings
- The student pilot had recently undertaken several hours’ worth of flight emergency training, which positively influenced the pilot’s actions and contributed to the safe outcome.
Sources and submissions
Sources of information
The sources of information during the investigation included the:
- Pilot of the accident flight
- Topfun Aviation
- Jabiru Aircraft Pty Ltd
Submissions
Under section 26 of the Transport Safety Investigation Act 2003, the ATSB may provide a draft report, on a confidential basis, to any person whom the ATSB considers appropriate. That section allows a person receiving a draft report to make submissions to the ATSB about the draft report.
A draft of this report was provided to the following directly involved parties:
- The pilot of the accident flight
- Topfun Aviation
- Jabiru Aircraft Pty Ltd
Any submissions from those parties will be reviewed and, where considered appropriate, the text of the draft report will be amended accordingly.
Purpose of safety investigationsThe objective of a safety investigation is to enhance transport safety. This is done through:
It is not a function of the ATSB to apportion blame or provide a means for determining liability. At the same time, an investigation report must include factual material of sufficient weight to support the analysis and findings. At all times the ATSB endeavours to balance the use of material that could imply adverse comment with the need to properly explain what happened, and why, in a fair and unbiased manner. The ATSB does not investigate for the purpose of taking administrative, regulatory or criminal action. TerminologyAn explanation of terminology used in ATSB investigation reports is available here. This includes terms such as occurrence, contributing factor, other factor that increased risk, and safety issue. Publishing informationReleased in accordance with section 25 of the Transport Safety Investigation Act 2003 Published by: Australian Transport Safety Bureau © Commonwealth of Australia 2022 Ownership of intellectual property rights in this publication Unless otherwise noted, copyright (and any other intellectual property rights, if any) in this report publication is owned by the Commonwealth of Australia. Creative Commons licence With the exception of the Coat of Arms, ATSB logo, and photos and graphics in which a third party holds copyright, this publication is licensed under a Creative Commons Attribution 3.0 Australia licence. Creative Commons Attribution 3.0 Australia Licence is a standard form licence agreement that allows you to copy, distribute, transmit and adapt this publication provided that you attribute the work. The ATSB’s preference is that you attribute this publication (and any material sourced from it) using the following wording: Source: Australian Transport Safety Bureau Copyright in material obtained from other agencies, private individuals or organisations, belongs to those agencies, individuals or organisations. Where you wish to use their material, you will need to contact them directly. |
[1] MAYDAY: an internationally recognised radio call announcing a distress condition where an aircraft or its occupants are being threatened by serious and/or imminent danger and the flight crew require immediate assistance.
[2] Conical disc spring washers.
[3] Fretting refers to wear involving small amplitude relative movement or vibration between contact surfaces.