Executive summary
What happened
On 4 December 2021, the pilot of an Air Tractor AT-400 aircraft, registered VH-ACQ and operated by Aircair Aviation Operations Pty Ltd (Aircair), was conducting aerial spraying operations on a property 75 km west-south-west of Moree, New South Wales.
At 0632 Eastern Daylight-saving Time, the aircraft took off from the property’s airstrip with the first spray load. The pilot then completed 10 spray loads, each time returning to the airstrip where the loader mixed about 1,250 L of chemical into the aircraft’s hopper. During that period, the loader also refuelled the aircraft twice.
Prior to departing with the eleventh load, the loader again refuelled the aircraft to full and mixed chemical into the hopper. The aircraft then returned to the western side of the target block, where the pilot had been spraying in a racetrack pattern on the previous load. After descending to recommence spraying towards the south, the aircraft climbed and turned away to track north and overfly a flood-affected area. The pilot radioed the company operations manager expressing concern about the weather conditions and the potential for chemical to drift onto a neighbouring property. About 5 minutes later, the aircraft returned to the target block, this time on the eastern boundary.
The pilot then conducted 2 ‘smoker’ runs to assess the drift, followed by 5 back-to-back (parallel) spray runs. At the end of the fifth spray run, the aircraft was observed to climb then enter a right procedure turn. During the turn, the aircraft descended rapidly, collided with terrain, and was subsequently destroyed by fire. The pilot sustained fatal injuries.
What the ATSB found
The ATSB found that the aircraft was too close to the start of the spray run during the turn, which probably resulted in the pilot tightening the turn. This almost certainly resulted in an aerodynamic stall at a height too low to recover before colliding with the ground.
Mishandling the turn was probably a result of the combined effects of the pilot experiencing high workload and fatigue due to long flight and duty times, inexperience, the complexity of the task and the weather conditions. The combination of these factors would likely have identified an elevated flight risk, had an aerial application-specific flight risk assessment been conducted. However, it was not a requirement to conduct a flight risk assessment or to have a flight risk assessment tool.
The pilot was almost certainly wearing a helmet and 4-point restraint increasing their chances of survival in an accident. However, the aircraft’s fuel tanks ruptured during the accident sequence resulting in a fire and fatal thermal injuries to the pilot.
The aircraft was not fitted with a crash-resistant fuel system, nor was it required to be under the standards in place at the time of manufacture. The current standards also do not require it. The ATSB found that on average, post-impact fire in VH-registered certified aeroplanes results in one fatality every 2 years in Australia. As such, post-impact fire presents a significant risk of fire-related injuries and fatalities to occupants of general aviation aeroplanes.
What has been done as a result
As a result of this accident, Aircair has implemented additional fatigue management measures, which include an assessment of other factors that may contribute to fatigue and flight risk, within the regulatory fatigue requirements.
In August 2022, the operator’s pilot group completed training with an expert instructor in advanced stall and spin prevention, recognition and recovery. The operator is investigating ways to incorporate such training into its pilot induction program.
Safety message
An aerodynamic stall occurs when the aircraft’s wing exceeds the critical angle of attack. The angle of attack of the wing is caused by the angle of deflection of the elevator, independent of the airspeed, pitch attitude, angle of bank, weight and power. Therefore, pilots should remain aware that if they pull the control stick (or column) back too far and deflect the elevator too far, it will increase the angle of attack of the wing beyond the critical angle and stall it. The control stick position at which an aircraft will stall is therefore also independent of airspeed, pitch attitude, angle of bank, weight and power, but specific to the aircraft and may change with flap configuration. To un-stall the wing, the pilot has to move the control stick forward to a position corresponding to an angle of attack below the critical angle of attack.
Aircair pilots who completed the advanced stall/spin training (after the accident), found that discovering the stall stick position and its independence of other factors was very beneficial, particularly because they frequently operated at low level in a loaded aircraft, often towards the margins of the aircraft’s flight envelope. They also identified that the stall stick position in Air Tractor aircraft was forward of other aircraft types they had flown.
The US Federal Aviation Administration’s Airplane Flying Handbook (2021) stated that reducing the angle of attack is crucial for all stall recoveries. As aerial application pilots are usually operating at a height too low to recover from a stall, stall prevention by maintaining an awareness of elevator control input is key to preventing similar accidents.
The 2014 US National Transportation Safety Board Special investigation report on the safety of agricultural aircraft operations identified that risk management guidelines and best practices specific to aerial application operations were necessary to help operators and pilots mitigate their unique risks. These practices should include checklists for performing flight risk assessments to identify hazards specific to the task. Mitigation strategies should then be implemented to support pilot decision-making, particularly during high-risk activities.
Post-impact fire has been found to present a significant risk to aircraft occupants, including those conducting aerial application operations. Crash-resistant fuel systems have been proven effective in helicopters and in automotive applications. Implementing requirements for similar engineering countermeasures in existing, newly manufactured and newly certified FAR 23 aeroplanes, would reduce the incidence of fire-related serious injuries and fatalities in otherwise survivable accidents (TSB, 2006).
The occurrence
On 4 December 2021, the pilot of an Air Tractor AT-400 aircraft, registered VH-ACQ and operated by Aircair Aviation Operations (Aircair), was conducting aerial application (spraying) operations on a property 75 km west-south-west of Moree, New South Wales.
At 0604 Eastern Daylight-saving Time,[1] the aircraft departed Moree Airport and tracked to the property’s airstrip, 43 km south-west of Moree Airport. A loader was stationed at the property’s airstrip, whose role was to mix and load chemical into the aircraft’s hopper, and to refuel the aircraft.
A GPS tracker onboard the aircraft recorded data at 15-second intervals. The data showed that commencing at 0632, the aircraft took off from the property airstrip and sprayed 11 loads over the course of the morning.
For the first 8 loads, the aircraft remained within sight of the loader. Those loads were sprayed using a racetrack pattern (Figure 1). Each of the 8 loads took about 20 minutes, except the third load, which took 32 minutes as it included clean-up spray runs (across the direction of the pattern) and tracking to the next target area. Each time the aircraft landed at the airstrip, the loader mixed chemical and water totalling 1,250 L into the hopper. On 2 of those occasions, the loader refilled the aircraft fuel tanks.
Figure 1: Racetrack spray pattern
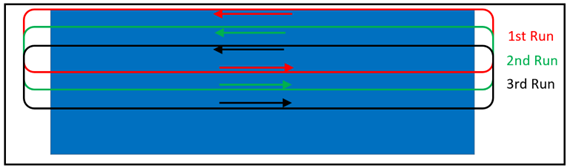
Source: ATSB
At 0914, while the pilot conducted the seventh load, the operations manager sent the pilot a text message advising that 4 of the target fields marked on the map were no longer to be sprayed (marked in orange in Figure 2). On the next (eighth) load, the pilot overflew an area marked on their map to be sprayed that day, which was adjacent to a river and under water due to flooding. As a result, the pilot radioed the operations manager to ask whether to spray the flood-affected area. The operations manager reported that they contacted the property owner but were subsequently unable to communicate with the pilot via radio to provide a response.
Figure 2: Operating area including target spray blocks, location of airstrip, property boundary and neighbouring house
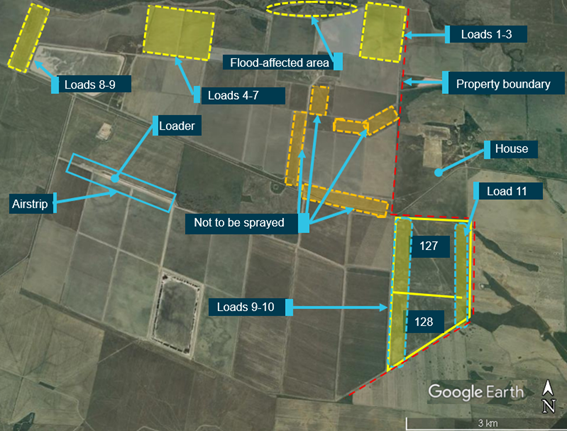
Source: Aircraft operator information overlaid on Google Earth, annotated by the ATSB
At 1053, the aircraft took off with the tenth load and continued to fly north-south racetrack patterns from the western side of blocks 127 and 128, followed by an inspection of the northern end of the target area, before returning to land at the airstrip again at 1120. The loader then filled the aircraft with fuel and loaded 1,250 L of chemical into the hopper. While the loader did those tasks, the pilot had a snack and a drink, and conducted a walk-around of the aircraft, which they had done consistently during refuelling breaks throughout the day.
At 1126:15, the aircraft departed on the eleventh load and tracked again towards blocks 127 and 128 to recommence spraying the next run from where they had left off (as can be seen in Figure 3), in the racetrack pattern. The pilot commenced a run to the south, but before reaching the target crop, the aircraft climbed and turned left. The aircraft then overflew the northern boundary of block 127, which was also the property boundary. The operations manager heard the pilot on the radio expressing concern about the potential for chemical spray to drift towards a house on the neighbouring property due to the wind. The aircraft then tracked north and again overflew the flood-affected area (top of Figure 2 and Figure 3), before returning to the north‑eastern end of block 127 (Figure 3).
Figure 3: GPS data showing the aircraft’s track on the accident load
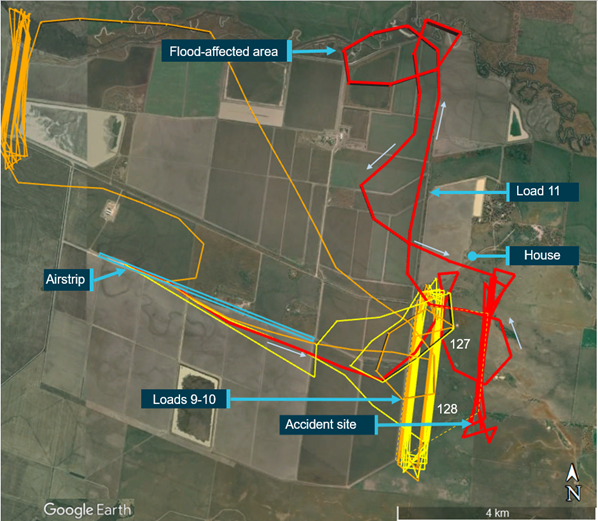
Source: Aircraft operator TracPlus data overlaid on Google Earth, annotated by the ATSB
A witness reported that on the first and second runs along the eastern boundary, which were towards the south and north respectively, the pilot used smoke to assess the drift from the wind, before commencing spraying on the next (third) run. Instead of a racetrack pattern, the pilot conducted back-to-back spray runs with a procedure turn at each end. In a procedure turn, the aircraft is initially turned away from the direction of the turn, usually about 45°, before reversing the direction and completing the turn to position the aircraft on the reciprocal heading for the next spray run (Figure 4).
Figure 4: Back-to-back patterns with procedure turns
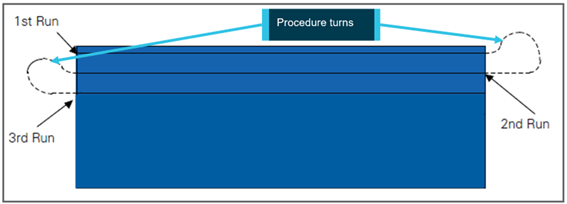
Source: Aerial Application Pilots Manual (Aerial Application Association of Australia, 2011), annotated by the ATSB
After the two ‘smoker’ runs, the aircraft sprayed 4 runs. At 1145, the aircraft commenced a spray run towards the south, at the end of which the aircraft climbed. The aircraft’s last recorded position was at 1145:30 about 170 m beyond the southern end of the field and 180 ft above the ground.
A witness (‘Witness 1’, Figure 5) located in the neighbouring paddock to the east, observed the aircraft turn slightly left then enter a right turn, consistent with a procedure turn. During the turn, the witness observed the aircraft’s nose pitch down and it descended rapidly, right‑wing low, then disappeared behind trees. The witness reported seeing a black plume of smoke rise almost immediately afterwards.
Figure 5: Aerial photo of target spray area taken 10 December 2021, showing accident site and witness location
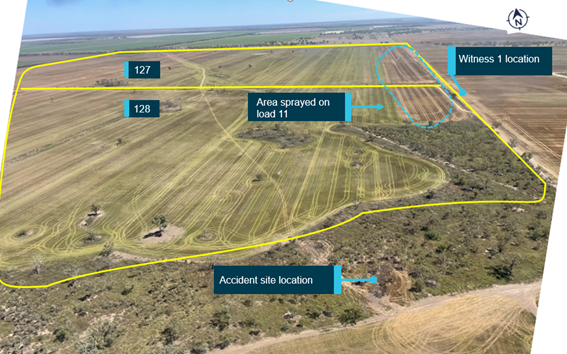
Note: The yellow lines represent the block boundaries.
Source: Aircraft operator, annotated by the ATSB
Another witness positioned about 1 km south of the accident site, observed the aircraft’s distinct yellow colouring as it descended among trees and impacted the ground. The witness estimated this was followed within about 2 seconds by flames and smoke. The pilot was fatally injured, and the aircraft was destroyed.
Context
Pilot information
Medical, licence and qualifications
The pilot held a valid Class 1 Aviation Medical Certificate issued on 15 October 2021 with no recorded medical issues and was reported to have been fit and healthy. The pilot’s Commercial Pilot Licence (Aeroplane) was issued on 30 March 2021.
The pilot also held ratings for:
- single-engine aeroplane
- low-level
- aerial application[2]
and endorsements for:
- tailwheel
- manual propeller pitch control
- gas turbine engine.
The pilot attained Spraysafe accreditation[3] through the Aerial Application Association of Australia (AAAA) on 2 July 2021 and had been issued a Pesticide Licence by the New South Wales Environment Protection Authority on 24 August 2021.
At the start of the accident day, the pilot had accumulated 372.5 flying hours, 203.3 of which were conducting aerial application operations (including training), 31.7 of which were in VH-ACQ.
Recent history
The pilot’s recent sleep-wake and work history was determined from a combination of interviews, text messages, logged flight times and recorded flight data.
The pilot lived about 30 km from their assigned base and about 70 km from the operator’s Moree base. In late November, the pilot’s commute was increased by about 1 hour as a road was inaccessible due to flooding.
On 2 December 2021 (2 days prior to the accident), the pilot left home at about 0600, returned at 2000 for dinner and was in bed by 2100. That day, the pilot recorded 13 hours of duty time and 8 hours of flight time. The pilot had described this as a huge day – the most spraying so far in one day – and was very tired at the end of the day.
The day prior to the accident, the pilot was awake by 0412 and left for work at 0530. That day, the pilot recorded 13 hours of duty time and 7.9 hours of flight time. At 1816, the pilot sent a text message to a friend stating that they were about to fall asleep in the aeroplane (but did not advise the operator), before ferrying the aircraft to Moree Airport for maintenance, arriving at about 1900. Rather than drive home, the night before the accident, the pilot stayed with another company pilot in Moree. The company pilot reported that the accident pilot was happy and was proud of having sprayed 1,100 hectares that day and 1,000 hectares the previous day. They went out for dinner at about 2100 and went to bed between 2200 and 2215. Others described the pilot that evening as a bit tired but nothing out of the ordinary.
The accident day was the pilot’s ninth consecutive day of duty. That morning, the pilot was awake by 0510 and picked up another company pilot at 0530. They purchased breakfast, snacks and lunch from a petrol station before heading to Moree Airport. The company pilot recalled that the pilot reported having had a good sleep, appeared fresh and not tired, and was very happy that morning. Other company pilots who had seen the pilot in the 24 hours prior to the accident reported that the pilot did not seem overwhelmed or stressed.
For the 3 days prior to the accident, the recorded flight times were the longest consecutive logged by the pilot (7.7, 8.0 and 7.9 hours) and the longest duty times (12, 13 and 13 hours).
Flight training
The pilot completed their commercial pilot licence flight test on 24 March 2021 with 166 hours total flying time. The pilot had completed an integrated training course, combining ground theory training with practical flight training for their private and commercial pilot licences. During this training, the pilot was described as a good student who was well-prepared, focused and dedicated. The pilot’s non-technical skills were assessed as being very good, and their aircraft handling skills were described as exceptional – including maintaining the aircraft well within the required tolerances in steep turns, practice forced landings and circuits.
Aerial application training
The pilot commenced training for aerial application and low-level ratings on 15 June 2021, and achieved those, along with a tailwheel endorsement, on 30 June 2021. At that time, the pilot had accrued 204.3 hours total flying time. This included the aerial application rating training, which consisted of 31.1 hours dual (including test) and 5.5 hours solo aerial application flight time, conducted in a Piper PA-25 two-seat dual-control aircraft.
The instructor who conducted the pilot’s aerial application rating and endorsement, noted in the second lesson (16 June) that the pilot had carried out stalls in all configurations at 1,000 ft above ground level. The pilot was reported to have handled these well for their total flying experience and achieved a good standard in recovery from stalls during climbing turns with left- and right-wing drops.
The lesson conducted on 20 June was conducted on a field similar to the accident field – with a diagonal boundary and trees – and included conducting back-to-back runs with procedure turns (Figure 6). On the training day, the wind was about 5 kt in the downwind direction at the diagonal boundary. The lesson notes indicated the pilot initially had difficulty lining the aircraft up on the spray run after the turn. The notes from the following day’s lesson (21 June) included ‘needs to back off on turns, pulling too tight…at times near stall’. A similar comment was made on 28 June. The instructor reported providing feedback to the operator of VH-ACQ (Aircair), to keep an eye on this aspect, but overall assessed that the pilot flew very well when taking into account the limited hours of experience at that time.
Figure 6: Diagonal boundary paddock example
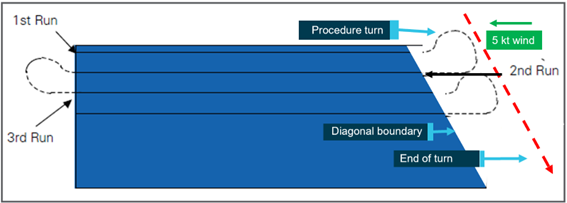
Source: ATSB
Employment at Aircair
The pilot was inducted into Aircair Aviation Operations (Aircair) in July 2021, and initially commenced working as ground crew – mixing and loading chemical. On 9 September, the pilot satisfactorily conducted an operational proficiency check flight with the chief pilot in a Cessna 185 aircraft. The pilot’s first aerial application job at Aircair was on 15 September 2021 in a Cessna 188B (C188B) aircraft – a conventional single-seat, piston-engine, strut-braced low-wing agricultural aircraft – having completed 2.4 hours of familiarisation in the aircraft in the previous 2 days. The pilot’s emergency dump training[4] in the C188B aircraft was assessed satisfactory on 21 October 2021, although recorded in the pilot’s logbook as 13 October.
The pilot then conducted aerial application in the C188B aircraft and on 22 November 2021, the chief pilot signed off that the pilot had completed the required 110 hours of aerial application under supervision. At that time, the pilot had accrued 321 hours of flying time.
The pilot was described as having a natural ability to pick things up quickly, flew very nicely and did everything they were asked to. The chief pilot and general manager of Aircair assessed that the pilot was then ready to progress to turbine-engine aircraft.
Gas turbine design feature endorsement
On 26 November 2021, the pilot commenced gas turbine engine endorsement training. The Civil Aviation Safety Regulations Part 61 Manual of Standards Schedule 2 detailed the skills and knowledge required to operate a gas turbine powered aircraft on the ground and in the air during normal and abnormal operations. The elements specified in the Schedule were starting, stopping and managing a gas turbine engine, and managing abnormal and emergency actions applicable to a gas turbine engine.
The endorsement required the pilot to complete ground (theory) components including studying the applicable flight manual, and then submit a written exam on the engine and aircraft to the examiner, which the pilot completed on 26 November 2021.
The pilot also received ground familiarisation of the engine and aircraft, followed by 7.5 hours of flight time in a two-seat dual-control turbine Air Tractor AT-504 aircraft. This included normal and abnormal situations, stalls and steep turns, and aerial application operations. The pilot’s stall training in the AT-504 aircraft consisted of climbing to a safe height, at which the supervising pilot demonstrated a straight and level stall, with the accident pilot following on the controls. The supervising pilot pointed out the stall buffet and the stall stick position, then demonstrated recovery from the impending stall, by reducing back pressure on the control stick. The supervising pilot commented that the AT-504 always tended to drop the right wing about 5° in the stall. The accident pilot then conducted two stalls. On the second of those, during the recovery, the aircraft nose lowered, and, assuming the aircraft had recovered from the stall, the pilot reapplied back pressure. However, as the wing was still stalled at the time, this action resulted in a secondary stall, from which the pilot performed a successful recovery.
Having demonstrated the ability to identify and recover from stalls, the pilot then conducted their first aerial spraying activity under supervision in the AT-504. The supervising pilot reported that the pilot had initially applied too much back pressure on the control stick (‘pulled too hard’) during the turn. This was due to trying to keep the aircraft too close to the paddock and led to a stall buffet during the turn. The supervising pilot reported that they reiterated the importance of the stall stick position, and the need to reduce back pressure on the control stick. The amount of force required on the control stick depended on the trim setting. If the aircraft was trimmed such that forward pressure was required during a spray run, the back pressure required to stall the aircraft was small.
The supervising pilot also reported advising the pilot to increase the amount of initial turn (‘fade’) away from the direction of the turn in the procedure turn, so the resulting turn was not as tight. They commented that the pilot subsequently flew the spray pattern ‘beautifully’.
The pilot received their gas turbine endorsement on 27 November 2021. The pilot had completed the requirements of the endorsement; however, it was noted that the theory examiner had signed off the endorsement although the flying component was conducted by a different pilot. At the time the theory component was conducted, a dual-seat aircraft was not available to conduct the in-flight competencies, and as a result, the examiner would have had to observe the pilot solo in a single seat aircraft from the ground. The operator assessed it would be more effective and safer to wait until the dual-seat aircraft was available. The theory examiner was not available when the dual-seat aircraft became available and the flying component was supervised by a pilot whose instructor rating was not current as it had not been renewed, primarily due to COVID restraints. They had however, previously conducted 5 gas turbine endorsements before their rating lapsed, and subsequently renewed their instructor rating in 2022.
Transition to the AT-400
On the morning of 28 November, the pilot conducted circuits in the AT-504 in preparation for transitioning to the single-seat AT-400 aircraft.
The operator reported that they had put many less-experienced pilots in VH‑ACQ over the last 40 years, primarily because it never lacked take-off performance, even when fully loaded. They assessed that the biggest differences the pilot would have found in transitioning from the C188B to the AT-400, were that the operating speed of VH-ACQ was about 20 kt faster, it was heavier and had more inertia. Due to its inertia, it would take longer to recover from an impending stall than the C188B. The operator noted that the cockpit layout of VH-ACQ was very similar to the C188B but more ergonomic. The main difference was the Satloc GPS display, which had a touchscreen in the C188B, but a keypad in the AT-400. The pilot had reportedly noted during their endorsement that this was something they would have to get used to.
Before the accident pilot’s first flight in the AT-400 (VH-ACQ), the Aircair general manager reported briefing the pilot about the aircraft. This included cautioning the pilot to keep the airspeed up in the turns because of the shorter wings, without Hoerner wing tips (Appendix A – Hoerner wingtips), and higher wing loading[5] than the AT-504. As a result, VH-ACQ tended to give less pre-stall buffet indication before stalling. However, the general manager advised the pilot that the stall characteristics were similar to the AT-504, in that the AT‑400 would likely drop a wing in a stall and stall recovery required the pilot to reduce back pressure on the control stick. This was consistent with descriptions by other pilots who had flown VH-ACQ. They described it as providing a stall buffet later in an impending stall than an AT-502. Additionally, that it tended to drop a wing when close to the stall, and that all Air Tractors can produce a significant wing drop when close to the stall in an unbalanced turn.
On 29 November, the pilot conducted familiarisation and circuits in VH-ACQ, before commencing revenue operations with a reduced hopper load (1,000 L), mentored from the ground by the chief pilot. The next day, the chief pilot approved an increase to 1,200 L hopper loads for 3 days, before assigning a maximum hopper load of 1,300 L on 3 December. That was still the pilot’s assigned limit on 4 December.
The chief pilot reported that the pilot appeared to be coping well with the transition to VH-ACQ. The pilot had described the transition to the AT-400 as ‘like learning to fly again’ and had remarked that they loved flying VH-ACQ. The pilot had reportedly commented that because of the air conditioner in VH-ACQ, they did not get as tired as when flying the C188B. The pilot and chief pilot had spoken each day that the pilot flew VH-ACQ, up to the accident day. The chief pilot reported that this included discussion of general management of the turbine engine, and that the pilot had not indicated any deficiency in operating the aircraft.
Ongoing supervision and mentoring
During the pilot's flights at Aircair, they were typically supervised either by the chief pilot or the general manager flying in the same area or observing from the ground. Regardless of having completed the mandatory supervised hours, the chief pilot advised that inexperienced pilots were typically ‘spoon fed’ up until 800–900 hours of agricultural flying.
The pilot had been conducting aerial spraying on the same property on the 2 days before the accident. The chief pilot had briefed the pilot at the end of the day prior to the accident, and discussed what blocks had been done, which to do next and the expected weather noting the wind direction and forecast high temperature. The chief pilot was absent on the accident morning and did not speak to the pilot.
The chief pilot reported that they would have been on the radio with the pilot if they had not been called away on leave that day. As a result of that leave, on the day of the accident, the pilot was unsupervised for the first time. However, the Aircair general manager radioed the pilot at 0645 to check how they were going, and the pilot responded that they were good and had a plan for the day’s operation.
Aircraft information
VH-ACQ
VH-ACQ was an Air Tractor Incorporated AT-400 single-seat low-wing tailwheel agricultural aircraft manufactured in the United States (US) in 1980. It was first registered in Australia – to Aircair – in November 1980 to operate in the Agricultural category, and was later operated in the Restricted category.[6] The Certification basis was US Federal Aviation Regulation (FAR) 21.25(a)(1) and the aircraft met the structural requirements of FAR 23, basis February 1, 1965, through Amendment 23-9. The flight criteria, propulsion, system and equipment items met the requirements of Appendix B, Civil Aeronautics Manual (CAM) 8, November 15, 1951, as amended through January 10, 1956.
The aircraft was powered by a Pratt & Whitney PT6A-15AG turboprop engine, which drove a Hartzell HC-B3TN-3D three-blade constant speed reversible pitch propeller.
The aircraft was fitted with two fuel tanks, located in the inboard section of each wing and an integral part of the wing structure. Both tanks gravity fed into a small header tank, located behind the hopper. Their combined total fuel capacity was 476 L, of which 454 L was usable. This equated to a maximum usable fuel weight of 363 kg (using a specific gravity of 0.8 for Jet A1 fuel). The aircraft was also fitted with dispersal equipment for spraying and spreading, and a system that allowed the hopper contents to be dumped if required. The hopper had a capacity of 1,514 L.
Maintenance history
The aircraft was maintained by a Civil Aviation Safety Authority (CASA)-authorised maintenance organisation in accordance with a CASA-authorised system-of-maintenance. A periodic inspection, including annual, 150 and 300-hourly, was completed on 28 September 2021, with the current maintenance release issued at that time. Scheduled and preventative maintenance conducted during this time included:
- engine overhaul and fitment of an overhauled propeller assembly
- replacement of lower spar caps (due life limit), with wing disassembly allowing for wing repairs and hopper refurbishment
- testing of the airspeed indicator, altimeter, compass and pitot/static system
- corrosion treatment and repainting.
At the time of the accident, the aircraft had accrued 18,869.2 hours total time in service. The aircraft had flown 4 hours 42 minutes since maintenance, having undergone a scheduled 75-hour inspection the evening prior, which included checking air and fuel filters, tyres, brakes and governor. The maintenance release had likely been destroyed in the post-impact fire and was not recovered from the accident site. However, there was no report of any aircraft defects prior to the accident. Furthermore, a general review of the maintenance records did not identify any anomalies.
Aircraft operating weight
The AT-400 type certificate data sheet[7] specified a maximum weight of 2,722 kg (6,000 lb). For VH-ACQ to operate above that weight, Air Tractor Service Letter 304 – Establishing and operating with a special purpose operating weight for Air Tractor aircraft, applied. The Service Letter referenced methods described in CAM 8 to enable operations up to a maximum recommended weight of 3,565 kg (31% overload). A placard affixed to the aircraft stated the maximum take-off weight as 3,565 kg. The Service Letter stated:
When operating at weights above the certificated maximum weight, please note that the stall speeds will increase from the published stall speed numbers in the Airplane Flight Manual. For example, when operating at a 31% overload weight, the stall speed will be approximately 15% higher than at the certificated maximum weight. During the required flight check, the new stall speeds should be determined.
On 23 October 2018 at 18,098.2 hours total time in service, the airframe logbook included an entry stating that the aircraft was flight checked on that day in accordance with CAM 8.10-3(e). It was found to be safely controllable and to operate satisfactorily with the hopper load of 1,356 kg and aircraft total weight of 3,565 kg.
Accident load weight and balance
The Airplane Flight Manual (AFM)[8] for VH-ACQ included a load data sheet to calculate the aircraft’s weight and balance. The sheet contained a table with entries for the weight, arm and moment of the aircraft with sprayer and spreader configurations, pilot, baggage, hopper and fuel. The table also provided forward and aft centre of gravity (CG) limits for weights up to 2,269 kg and for 2,722 kg, with a straight-line variation between those points.
For the accident load, VH-ACQ had been refuelled to full and the hopper loaded to about 1,250 L. Using a fuel consumption rate of 225 L/hr for spraying based on the company’s operations manual, the probable fuel remaining was approximately 387 L (310 kg). The pilot had completed 4 spray runs about 1,700 m long at an 18 m wide swath, using a chemical application rate of 18 L/ha, which left about 1,030 L in the hopper. The accident weight was therefore approximately 3,066 kg, below the demonstrated maximum gross weight of 3,565 kg, and the CG was about 534 mm aft of the datum. This was within extrapolated CG limits.
The hopper load calculation table for VH-ACQ stated that with full fuel, the maximum permissible hopper load was 1,348 kg.
Fuel tank certification and testing
For the aircraft’s certification, CAM 8.3052 Tank Tests required that all fuel tanks should be pressured tested to 3.5 PSI to provide an indication of the ability of the tank to resist distortion and leakage under vibratory, accelerating, and surging loads, which may be encountered in flight and landing conditions.
FAR 23.967 (e)(1) stated that the fuel tank must withstand 9 G ultimate fore and aft load from emergency landing conditions. Air Tractor simulated this in testing by converting the acceleration to an internal pressure. Air Tractor provided an extract of the engineering report covering the fuel tank testing. Their testing found that using 20 PSI, the fuel tanks were capable of withstanding 27 G before leaking.
These two requirements were for flight, landing and emergency landing conditions, but did not assess the tank for tolerance to direct impingement. There was no requirement in the design standards for normal category aeroplanes to be tested for fuel tank crashworthiness.
Installed GPS systems
Systems
The aircraft was fitted with a TracPlus surveillance system, which provided real-time tracking through a satellite or mobile phone network. It reported position, altitude, and speed at set time periods, in this case every 15 seconds. The ATSB obtained TracPlus data for the accident day and several previous flights.
A Satloc aerial guidance system provided the pilot with guidance commands to fly accurate spray patterns. It was set to record at 2-second intervals. The Satloc data from the accident flight was unrecoverable due to extensive fire damage to the Satloc unit. However, the ATSB obtained Satloc data for several of the pilot’s previous flights.
Satloc increase/decrease
The Aircair Air Tractor fleet all had the same control stick switch configuration. The Satloc stick switch (button) provided a ‘remote’ function to increase or decrease the run number, which could also be done on the Satloc keypad (Figure 7).
Figure 7: Satloc stick switch and keypad
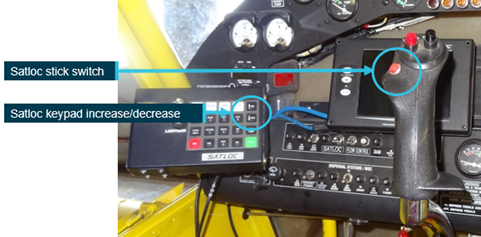
Source: ATSB
The Satloc keypad could be set to either increase or decrease the run numbers. When set to increase, pressing the stick switch (button) once, increased the run number by one, and when set to decrease, pressing the stick switch once decreased the run number by one. When a pilot had set up the Satloc GPS to spray a racetrack pattern, then changed to fly a back-to-back pattern, they would then be spraying every second run number (with the alternate numbers on the other side of the programmed racetrack pattern). Therefore, the next parallel spray run required the switch to be double-clicked at the end of each run to spray the adjacent, parallel run.
The stick switch could only make the run numbers go one way: up if increase was set or down if decrease was set. Therefore, if a pilot inadvertently clicked the button too many times and needed to go back, that would have to be done using the keypad.
When the Satloc was set to decrease, this swapped the direction function of the keypad buttons: the up arrow on the keypad (labelled ABC) would then decrease the run number and the down arrow on the keypad (labelled DECR) would increase the run number. Reportedly, this frequently resulted in pilots pressing the incorrect (for example, up arrow) button first, then having to press the correct one (for example, down arrow) multiple times. This would require ‘head in cockpit’ time and the potential for distraction from controlling the aircraft. The US Federal Aviation Administration (FAA) Advisory Circular 137-1A stated that pilots should ‘use extreme caution when using GPS swath-marking equipment to prevent diverting attention away from the task of flying the aircraft safely’.
Meteorological information
Bureau of Meteorology
Between 0600 and 1145 on the accident day, the pilot was operating within the NSW - West subdivision of the Bureau of Meteorology Graphical Area Forecast.[9]. The forecast for NSW - West issued at 0323 on 4 December and valid 0400–1000 was for visibility greater than 10 km and no cloud. The graphical area forecast issued at 0325 and valid 1000–1600 included scattered high cloud above 10,000 ft and, from 1100, isolated cumulonimbus clouds with visibility reducing to 2,000 m in isolated thunderstorms and rain. Moderate turbulence below 10,000 ft was forecast in thermals and dust devils[10] from 1200.
The nearest Bureau of Meteorology weather station was at Moree Airport, 80 km east-north-east of the property airstrip. The aerodrome forecast[11] for Moree Airport issued at 0424 and valid from 0600–1900 included wind from 360° at 8 kt, changing from 1100 to 240° at 14 kt and CAVOK.[12] Between 1100 and 1500, there was a 30% probability of variable winds at 20 kt gusting to 40 kt with visibility reducing to 2,000 m in thunderstorms with rain and associated scattered cloud at 800 ft above aerodrome elevation. The maximum temperature was forecast to reach 34 °C.
Oz Forecast
For more accurate local weather information (temperature and wind speed/direction), company pilots usually referenced the closest Oz Forecast weather station. The wind was measured 2 m above ground level and recorded in km/h and degrees true (°T). The nearest Oz Forecast weather station was located 11 km west of the property airstrip. Data from that weather station recorded at 15-minute intervals and converted to kt, is shown in Table 1.
Table 1: Weather recorded at 15-minute intervals from 0600–1200 EDT
Time | Temperature | Wind direction (°T) | Wind speed (kt) | Wind gust (kt) |
---|---|---|---|---|
0600 | 21.6 | 250 | 0.5 | 1.6 |
0615 | 21.5 | 227 | 2.4 | 5.4 |
0630 | 22 | 230 | 4.0 | 5.9 |
0645 | 22.8 | 227 | 4.1 | 5.9 |
0700 | 23.9 | 225 | 4.2 | 5.9 |
0715 | 24.8 | 219 | 4.6 | 7.0 |
0730 | 25.6 | 217 | 4.3 | 7.0 |
0745 | 26.3 | 196 | 4.5 | 5.9 |
0800 | 27.1 | 194 | 4.4 | 7.0 |
0815 | 27.5 | 195 | 5.1 | 7.6 |
0830 | 28.1 | 191 | 5.8 | 10.3 |
0845 | 28.4 | 192 | 6.6 | 11.3 |
0900 | 29.2 | 198 | 7.1 | 12.4 |
0915 | 29.6 | 190 | 7.6 | 11.3 |
0930 | 30 | 209 | 6.0 | 10.3 |
0945 | 30.3 | 192 | 5.3 | 9.7 |
1000 | 30.9 | 221 | 5.4 | 11.3 |
1015 | 31.3 | 221 | 5.4 | 10.3 |
1030 | 31.8 | 220 | 5.7 | 11.3 |
1045 | 32.2 | 228 | 8.2 | 14.0 |
1100 | 32.5 | 215 | 9.6 | 17.3 |
1115 | 32.3 | 230 | 10.6 | 17.3 |
1130 | 32.5 | 213 | 9.4 | 16.7 |
1145 | 32.6 | 225 | 10.2 | 18.4 |
1200 | 32.5 | 221 | 10.3 | 18.9 |
Source: Oz Forecast
At the time of the accident (1145), the wind was from the south-west at 10 kt gusting to 18 kt and the temperature was 32.6 °C. On the last spray run, as the aircraft had been tracking south, the wind was primarily a headwind. As the aircraft started to turn, it initially encountered more of a crosswind. The accident occurred as the wind became a quartering tailwind, but before completion of the turn to the north.
Other observations
A witness described the wind at about the time of the accident as ‘chopping and changing directions, was more stop and start again…gusts on and off’. The loader also described the weather as ‘windy’ and reported that the wind had become stronger throughout the morning.
At the time of the accident, the Aircair general manager was flying near Moree Airport, where the temperature was about 32 °C. They described the flying conditions as starting to get ‘bumpy and uncomfortable’ and about 30 minutes after the accident, as ‘quite windy and rough’. They reported that on the accident day, the wind had started from the north-east and went around to the north-west during the morning, in the usual summer pattern, but that it was stronger than normal, and increased around the time of the accident.
Another company pilot operating in the area that day recalled that it was the first hot, rough day of the season.
The chief pilot reported that on the evening before the accident flight, during their briefing with the pilot, they discussed the forecast 35 °C temperature. This included discussion of the associated increased thermal activity, which may lead the pilots to cease spraying operations.
At the time of the accident, the sun was not in a position to affect the pilot’s visibility.
Operational information
Work orders
The pilot had operated at the same property on 2–4 December. The blocks allocated to the pilot to be sprayed were depicted on multiple work orders for the property, one of which is depicted in Figure 8. Of the blocks depicted in Figure 8, on 4 December the pilot sprayed blocks M10, M11, M24, M25, M118, before commencing blocks 127 and 128. Block 117 was the wet area along the river and 123, 124 and 125 were not to be sprayed (although as they had powerlines in them, the pilot had been told not to spray them anyway).
Figure 8: Work order map depicting areas to be sprayed and location of the accident site
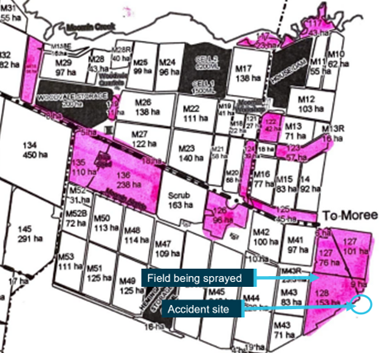
Source: Aircraft operator, annotated by the ATSB
Field selection
The operator reported that they selected blocks for spraying appropriate to a pilot’s experience and ability – including the block shape and whether there were powerlines in or near the target area. The accident pilot had not yet sprayed a block with a powerline in it, but had sprayed blocks with a powerline along one edge in the previous two weeks. Although not documented, it was reported that when any new aspects of the spraying task were introduced, the chief pilot or general manager would be there to mentor the pilots – either on the ground or flying next to them. The gradual progression to more complex blocks continued with the pilot’s transition to a more powerful, faster, heavier aircraft.
The field the pilot was spraying at the time of the accident (127 and 128 – Figure 8) was selected by the chief pilot because it was considered suitable for the pilot’s level of experience, with no powerlines or difficult obstacles. The blocks sprayed by the pilot the previous day were irrigated blocks – squarer and more defined. The accident field was a dry-land block with a few small trees. The field was near rectangular, but it had a diagonal border at the southern end, and the eastern and western fence lines were not quite parallel. The diagonal border angled down toward the western side, which would have made the back-to-back spray runs with a procedure turn at each end slightly more difficult for the pilot when incrementing runs from east to west. This is because with a diagonal end, each subsequent time the pilot pulled the aircraft up to make the procedure turn, the aircraft had to be further beyond the boundary to allow enough distance to line up for the next run (Figure 6).
Back-to-back pattern
According to the AAAA Aerial Application Pilot’s Manual (2011), the back-to-back pattern was the most common pattern flown prior to the availability of on-board GPS systems. It was usually the first pattern pilots learnt in their initial aerial application rating training. Flying back-to-back patterns was the preferred pattern when working around a hazard, such as a powerline, tree, susceptible crop, or house. This was because in a back-to-back pattern, the aircraft would be gradually moving towards a hazard. In contrast, when flying a racetrack pattern, the aircraft moves away from the hazard, which could be more easily forgotten on the next run. In a back-to-back pattern, during the procedure turn at the end of each run, the aircraft is turned through 180°. During the turn, ‘most of the speed is squandered and you arrive back on the same [reverse] heading at which you started the turn, with time and speed both going in the wrong direction’ (AAAA, 2011).
The operator reported that during a procedure turn, pilots judge how far to turn away (fade) by using the GPS light bar for guidance, counting (for example, for 3 seconds) in their head, or by feel, before banking the opposite way around the turn. If they do not get it right, it can be difficult to line up on the next run. In that case a pilot would normally skip that run and write the missed run number on their hand. They would then either return to spray it later or leave it and advise the operations manager at the end of the day, so that it would get done another day. The chief pilot reported having previously seen the pilot with missed run numbers written on their hand.
In a procedure turn, after the fade, as a pilot banked to turn the aircraft in the opposite direction, they would extend some flap during the turn, usually up to about 15° in the Air Tractor aircraft. They would then retract the flap as the aircraft lined up for the next spray run. The chief pilot reported that the key instrument referenced by a pilot during the turn was the airspeed indicator, while also cross-referencing the GPS light bar, and using the turn and balance indicator (ball) to ensure a balanced turn. The target airspeed they were referencing on the airspeed indicator depended on the aircraft weight.
Flight and duty review
Aircair flight and duty time limitations were in accordance with Civil Aviation Safety Regulations Part 137.Q. The key limitations were:
- maximum flight time of 170 hours in 28 days and 1,200 hours in 365 days
- daily tour of duty limit of 14 hours including a rest period of at least 8 hours after a duty of 10 hours or less, or 10 hours after a duty of more than 10 hours
- following a tour of duty of more than 10 hours, a pilot was permitted to recommence after 9 hours off duty, if they believed they were mentally and physically fit to do so and would not breach any other regulation in the subpart
- at least 36 hours continuous off duty in any 14 days
- 44 hours cumulative duty time limit in 3 days (72 hours) and 98 hours in 7 days (168 hours).
The Aircair Administration and Policy Manual stated that for aerial application operations, duty time was calculated from 30 minutes prior to the flight to 15 minutes after the flight. The regulations defined flight time as commencing when ‘the aircraft first moves under its own power for the purpose of taking off’.
On the accident morning, the aircraft engine started at 0553, take-off roll commenced at 0559 and it took off at 0600. According to Aircair’s procedures, recorded duty time would commence no later than 0529, although the pilot arrived at the airport at about 0550. According to the operator’s flight and duty records, the pilot had been on duty for 13 hours the previous day, having commenced duty at 0700 and ended at 2000. Recorded data showed the aircraft was shut down at 1919 that evening and duty time should therefore finish no earlier than 1934.
As the previous day’s duty time exceeded 10 hours, the pilot was required to have a rest period of 10 hours, but could recommence duty after 9 provided the pilot assessed themselves ‘mentally and physically fit to do so’. The pilot’s start time was close to the 10-hour rest period, accounting for imprecision of the recorded duty times. It could not be determined whether the pilot made this assessment, however, regulations required pilots to ensure they were fit for duty prior every flight. Civil Aviation Safety Regulation 137.300 described that a pilot was not fit for duty if they had not had adequate rest, food or drink; or was adversely affected by a medical condition or a psychoactive substance.
The pilot commenced flying for Aircair on 9 September 2021 and flew 15.5 hours total for the month. In October, the pilot flew 54.8 hours in the C188B aircraft, over 18 days, with the longest flight time 7.3 hours on 6 October followed by 6.3 hours on 7 October. From 1 to 24 November, the pilot conducted 50.4 hours in the C188B. In that period, the longest flight time was 6.6 hours on 16 November which was also the longest duty day of 10.5 hours. The previous longest flight time recorded was on 6 October (7.3 hours). Both those days had been preceded by significantly shorter flight times.
The pilot’s most recent day off work prior to the accident was 25 November. After their day off, on 26 November the pilot commenced the transition to turbine-engine aircraft. Figure 9 and Table 2 show the pilot’s flight and duty records from 26 November to 3 December. The first time (ever) that the pilot flew VH-ACQ, was 5 days before the accident on 29 November. On that day, the pilot was awake at 0454 and home at 2126, having logged 5.6 hours of flight time in VH-ACQ.
Figure 9: Recorded flight and duty times from 26 November to 3 December 2021
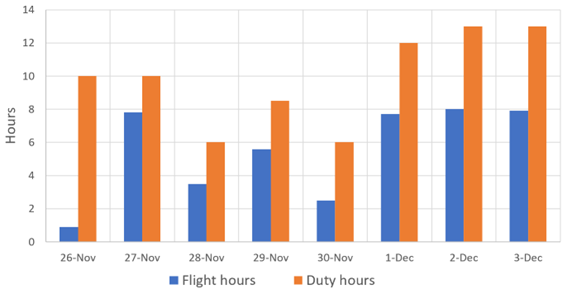
Source: Aircraft operator data analysed by the ATSB
Table 2: Flight and duty records from 26 November to 3 December 2021
Date | Aircraft | Flying hours | Activity | Duty hours (and times) |
26 Nov | AT-504 | 0.9 | Dual training | 10 (0800–1800) |
27 Nov |
AT-504 CA188B |
6.1 (dual) 1.7 |
2.6 training plus 3.5 spraying Spraying |
10 (0700–1700) |
28 Nov |
AT-504 CA188B |
0.5 3.0 |
6 circuits ICUS Spraying |
6 (0800–1400) |
29 Nov | VH-ACQ (AT-400) | 5.6 | 5 circuits (Tracplus shows 4 circuits at Moree) plus spraying 1,000 L load limit | 8.5 (0800–1630) |
30 Nov | VH-ACQ | 2.5 | Spraying 1,200 L load limit | 6 (0930–1530) |
1 Dec | VH-ACQ | 7.7 | Spraying 1,200 L load limit | 12 (0730–1930) |
2 Dec | VH-ACQ | 8.0 | Spraying 1,200 L load limit | 13 (0700–2000) |
3 Dec | VH-ACQ | 7.9 | Spraying 1,300 L load limit | 13 (0700–2000) |
In the 8-day period since the pilot’s last rest day, there were some discrepancies between the logged flight and duty times and the recorded GPS data for the aircraft. On 3 December, the aircraft was rolling at 0647, 13 minutes prior to the recorded duty commencement. On 29 November, the aircraft landed at 1841 and on 26 November, the aircraft landed at 1932, both times after the recorded end of duty period. It was the pilot’s responsibility to enter the flight and duty times and it could not be determined how the inconsistencies occurred. The chief pilot reported that they checked the entered data occasionally.
Operational tempo
A review of text messages the pilot sent to a friend (but not to the operator) showed that since October and throughout November, the pilot had often mentioned that they felt tired, and had frequently been awake at or before 0500, and getting to bed after 2100.
The accident pilot had flown more than 30 hours in VH-ACQ in the 4 days prior to the accident. The chief pilot commented that the company pilots had been doing a lot of flying and were approaching the flight and duty limits every day. Other company pilots reported that they had been working long, but not excessive, days. Further, that although they had early starts, they were not finishing very late.
On the day before the accident, the chief pilot had reported being worried about the company pilots with the workload ahead. The chief pilot sent a text message to check they were all managing the workload and reminding them to work together with each other and the ground crew, stick to the routine and keep it simple. Later that day, a company aircraft struck a powerline, which resulted in minor damage and no injuries to the pilot.
In response, on the morning of the accident flight, the chief pilot sent a message to all company pilots, reminding them, among other things, to be aware of the effects of successive early starts and late finishes. The message advised pilots to manage their time and rest when they could, consider load sizes particularly following refuelling, maintain wire awareness, and to be safe, have fun and keep it simple.
Communications
The UHF radio in VH-ACQ had malfunctioned on the day prior to the accident and been fixed that evening. The UHF radio was used to communicate with the operations manager, other company pilots in the area and normally, with the loader. However, the loader did not have a radio that day as they were not driving a (company) vehicle fitted with one. Normal procedure involved the pilot communicating with the loader via radio so the loader could prepare the next chemical load prior to landing. The operator also had a procedure for loaders to operate with an unserviceable UHF, which required the loader to either mix load by load only, or to continue mixing until further notice, and to have a mobile phone. The loader had a mobile phone.
During refuelling prior to the accident load, the pilot sent a text message to the operations manager and received an immediate response. After departing with the accident load at about 1130, a company pilot operating in the area heard the accident pilot on the radio to the operations manager advising of their concern about drift onto neighbouring property and that the wind was picking up. That company pilot later reported that they thought the pilot sounded nervous. The operations manager reportedly responded suggesting they could spray a different area or cease operating.
Analysis of recorded data
The TracPlus data for 4 December 2021 indicated that the pilot had not flown a hazard check of any block before commencing spraying or conducting clean-up runs. This meant the pilot had not overflown the south-eastern area of the block (127 and 128) where the accident occurred.
For the accident load, several data points were recorded at the northern and southern ends during the turns. Analysis of these points indicated the maximum height reached during the turn at each end of the field was about 250 ft above the ground.
Analysis of Satloc data from the pilot’s flight the day prior to the accident, showed that in more than 75% of procedure turns, the peak angle of bank was 50–70° and peak acceleration was between 1.5 and 1.9 G. The angle of bank exceeded 80° three times and the peak G on average occurred at about the same time as the peak angle of bank. In the turn technique described in the AAAA’s Aerial Application Pilot’s Manual (AAAA, 2011), the peak G would be reached before the peak angle of bank:
A key pilot technique in aerial application is to unload the aircraft from excessive G before applying aileron to initiate a turn. This is most likely to be relevant during a pull out of a paddock at the end of a run. Pull back to get out of the paddock and establish the aircraft in a climb, unload the G, and then initiate the turn.
The Satloc data from the day prior to the accident also showed that during back-to-back spray runs with procedure turns, the aircraft was usually lined up (within half a swath width) on the next spray run about 200 m prior to the crop boundary.
Aerodynamic stall
A wing generates lift when the airflow around the upper and lower surfaces results in a pressure difference between those surfaces. At a certain angle of attack (the relative angle between the chord line of the wing and the approaching airflow), which is a characteristic of the wing design, the flow over the upper surface of the wing separates from the surface. This condition is known as an aerodynamic stall (or simply a stall) and results in a rapid reduction in the lift generated and an increase in drag. Due to the sudden reduction in lift from the wing and rearward movement of the centre of lift, an uncommanded nose-down pitch ensues.
A wing drop occurs when one wing stalls before the other, which can be exacerbated by uncoordinated (or ‘unbalanced’) flight. A cross-control stall occurs when the critical angle of attack is exceeded while aileron is applied in one direction and rudder in the opposite direction.
As a loss of altitude also occurs during recovery from a stall, it is possible to stall with insufficient height above the ground to recover. The AFM for VH-ACQ stated the altitude loss from a wings-level stall was 220 ft at 2,722 kg gross weight. The main indications of an impending stall in the AT-400 are airframe buffeting (vibration) and an aural stall warning (horn).
Aerofoils of the type used on aircraft such as the AT-400, typically stall at angles of attack of around 16°. This critical angle of attack can be exceeded at any airspeed, any (pitch) attitude and any power setting. As most small aircraft do not have an instrument that indicates the aircraft’s angle of attack, the angle of attack at which the stall occurs may be referenced to an airspeed. The AFM for VH-ACQ provided stall speeds at 2,722 kg gross weight, power off, wings level (0° angle of bank), in a balanced level turn at selected angles of bank, and with the flaps up (retracted) and flaps down (fully extended) (Table 3).
Table 3: Angle of bank and stall speed at 2,722 kg, power off (adapted from AFM)
Angle of bank | 0° | 15° | 30° | 45° | 60° |
Stall speed (kt) – flaps up | 66 | 67 | 71 | 78 | 93 |
Stall speed (kt) – flaps down | 59 | 60 | 63 | 70 | 83 |
However, the airspeed at which a stall will occur is not fixed to a single value, and varies with weight, centre of gravity, load factor,[13] and power setting. Tight turns and rapid pull-ups increase the load factor and therefore increase the stall speed. A stall that occurs at a stall speed greater than the +1 G stall speed, such as when turning or pulling up, is termed an accelerated stall. Increasing an aircraft’s weight by 25% will result in the stall speed being about 12% faster.
At the probable aircraft weight at the time of the accident (3,066 kg), the stall reference speeds in the AFM (Table 3) would increase by a factor of 1.06. For the referenced angle of bank stall speeds, if the pilot did not move the control stick aft to maintain level flight, and the aircraft descended while turning, (at the same radius), the G would be less, therefore the stall speed would be lower than when maintaining a level turn.
The primary control for angle of attack is the aircraft’s elevator. Pulling back on the control stick will increase the angle of attack and pushing forward will decrease the angle of attack. If a pilot pulls the stick too far back and deflects the elevator too far, it will increase the angle of attack of the wing to the critical angle and stall it. The elevator control stick (or column) position at which the critical angle of attack is reached is independent of factors including airspeed, angle of bank, power, and pitch attitude. Recovery from a stall requires reducing the angle of attack by moving the control stick forward, which normally means lowering the aircraft nose (pitching down). A secondary stall can result following a stall if, during the recovery, the pilot again pulls the stick past the position at which the critical angle of attack is reached in an effort to regain horizontal or climbing flight too quickly.
As VH-ACQ was the ‘first of type’ AT-400 registered in Australia, flight tests were conducted at Ballarat airfield, Victoria, on 31 October and 2 November 1980. At the flight-tested weight of 3,042 kg, the report concluded that the handling characteristics were acceptable. It found the airframe (pre-stall) buffet was felt at 76 kt indicated airspeed (IAS) with the flaps up (fully retracted) and was ‘not violent’. There was a ‘clear and distinctive’ stall warning onset at 80 kt IAS with flaps up (fully retracted) and at 68 kt with flaps down (fully extended). The stall characteristics were described as ‘satisfactory’.
Human performance considerations
Workload
Workload is defined as the sum of task demands placed on an individual’s cognitive resources that are used for attention, perception, decision making and action (Skybrary, 2010). Humans are limited in the amount of new information the brain can process at once. Once the limit of cognitive resources has been reached, performance starts to decline with increased error rates and/or delayed responses. Factors that can increase workload include excessive task demands, time pressures, a lack of operator skills and knowledge, or environmental conditions (NASA, 2010).
Task complexity and an individual’s level of experience and knowledge can have a significant impact on their workload (Li and others, 2021). Less experienced pilots typically have a higher cognitive workload compared to those that are more experienced due to their continual learning and development of skills. A more experienced and knowledgeable individual can rapidly interpret a situation based on past experiences and knowledge, and subconsciously pattern-match. This frees up cognitive capacity for a pilot to maintain vigilance and monitor performance, and, if they choose, reflect on their actions, whereas a less experienced individual may not (Byrne and others, 2013).
Green and others (1996) described the effect of practice on motor skills such as flying an aeroplane. With experience, skill acquisition progresses from the cognitive phase, in which the learner has to think consciously about the action, through the associative phase and on to become automatic, and the skill can then be executed without conscious control. Until this occurs, central processing capacity is needed to perform the task. Thus, a pilot with fewer hours in an aeroplane type would be expected to experience a higher workload than a more experienced one for the same task.
The instructor who conducted the pilot’s aerial application rating described the increase in workload for a pilot progressing from the C188B to the AT-400 as: ‘The workload is just so high for [the AT-400 aircraft] – they’re fast, nippy in the turn. If you are going to fly it on the edge, things are going to happen. It has more than double the weight and inertia’ of the C188B. They further reported that aerial application work is ‘not mundane’, that the pilot would be concentrating all the time, and has to consider other factors such as drift and temperature, in addition to flying. To conduct effective aerial application, while manoeuvring the aircraft at low altitude, a pilot must visually scan external cues and monitor internal resources (NTSB, 2014).
High workload is associated with increased error rates and reduced safety margins (Harris, 2011). It also leads to a degradation in performance and at extremely high levels of workload, important information may be missed due to the narrowing or focussing of attention onto only one aspect of the task (Green and others, 1996).
Fatigue
Overview
The Civil Aviation Safety Regulations define fatigue for a flight crew member (FCM) as:
a physiological state of reduced alertness or capability to perform mental or physical tasks, which:
- may impair the ability of the FCM to safely operate an aircraft
- is caused by 1 or more of the following:
- the FCM’s lack of sleep;
- the FCM’s extended wakefulness;
- the FCM’s circadian phase at any relevant time;
- the FCM’s workload of mental activities, or physical activities, or mental and physical activities at any relevant time.’
The International Civil Aviation Organization (ICAO) (2020) defines fatigue as:
… a physiological state of reduced mental or physical performance capability resulting from sleep loss or extended wakefulness, circadian phase, or workload (mental and/or physical activity) that can impair a person’s alertness and ability to perform safety-related operational duties.
Factors that can cause fatigue include (CASA, 2012):
- emotional strain
- mental workload
- strenuous or sustained physical exertion
- inadequate food and fluid intake
- adverse environmental conditions, such as extremes of temperature, low light levels, vibration and confined spaces
- disrupted and lost sleep.
Mental fatigue results from long periods of cognitive activity. Its effects can include reduced concentration and manual dexterity, increased reaction time, performance monitoring, error management and decision making (Boksem and others, 2005; Bafna & Hansen, 2021, CASA, 2012; Heywood 1999).
Self-assessment of fatigue
Although there are some known limitations of self-rated fatigue, research on airline flight crew has shown correlation between self-rated fatigue and performance in vigilance tasks, for example using the Samn-Perelli 7-point fatigue scale[14] (Garwon, 2016, Petrilli, 2007 and Roach, 2012). There was no regulatory or operator requirement for pilots to determine (or provide) a standardised fatigue estimation prior to, or during, operations.
Sleep and time of day
Inadequate quantity and quality of sleep is a contributor to fatigue. Most people generally require 7–8 hours of sleep to achieve a maximum amount of alertness and performance. Sleep debt can be cumulative and can result in degraded performance and uncontrolled sleep episodes (Orlady & Orlady, 1999; Hawkins, 1993). The pilot’s 72-hour history indicated they had adequate sleep opportunities in the preceding nights and the pilot was reported to have no sleeping issues.
Circadian rhythms are the body’s internal clock that regulates the sleep-wake cycle and repeats roughly every 24 hours. According to the International Civil Aviation Organization (2016) there are two times of peak sleepiness within a 24-hour cycle. The main peak is in the early morning between 0300–0500 known as the window of circadian low, another smaller peak around 1500–1700 is known as the afternoon nap window. For each individual these times can vary. The period between when the pilot arrived at Moree Airport and the accident was outside these peak sleepiness times.
Effect of multiple long days
The instructor who conducted the pilot’s aerial application rating, when asked what the effect of the previous long days would be, reported that it was not just the last couple of days; the season had effectively continued since July without a break. Research has found self-ratings of fatigue (Rithemeister and others 2021) and risks of successive incidents both increase for each consecutive day worked (Folkard and Akerstedt 2004).
As documented by ICAO (2020) biomathematical modelling is ‘a computer programme designed to predict aspects of a schedule that might generate an increased fatigue risk for the average person, based on scientific understanding of the factors contributing to fatigue…All bio-mathematical models have limitations that need to be understood for their appropriate use.’ Biomathematical models can only forecast the effects of sleep and circadian rhythms[15] on performance and cannot account for other factors known to impact performance such as training, experience, stress and illness. Additionally, the models were not designed for aerial agricultural operations and did not consider the pilot’s cognitive workload.
The ATSB used two software programs, Sleep Activity Fatigue Task Effectiveness-Fatigue Avoidance Scheduling Tool (SAFTE-FAST) and Fatigue Assessment Tool by InterDynamics (FAID) Quantum, which are biomathematical models to assess fatigue based on the pilot’s duty hours and sleep opportunity in the days leading up to the accident. Each model has specific applications and limitations.
SAFTE-FAST predicts future performance based on the recent sleep history of the projected population or individuals. The output is a performance score indicating a percentage of cognitive effectiveness at a point in time. The lower the performance score, the higher the effect of fatigue. The model is based on biological determinants of fatigue such as: hours of sleep, hours of wakefulness, current sleep debt, the circadian process and sleep fragmentation (awakenings during a period of sleep) that reduce quality (Hursh and others 2004). SAFTE-FAST indicated that the pilot’s performance was not affected by sleep history and circadian processes.
FAID uses work hours as its input to predict the effect on fatigue and performance of different duty periods or work schedules. The FAID output is a score indicating different levels of fatigue exposure for different work hours. The higher the FAID score, the higher the fatigue exposure. The FAID score is based on the following biological determinants of fatigue: time of day of work and breaks, duration of work and breaks, work history in the preceding 7 days, and biological limits on recovery sleep (InterDynamics n.d). FAID indicated a high fatigue exposure risk for the pilot on the accident day, but lower (although still high) at the time of the accident than the start of the day.
The outputs of the two models were inconsistent. The differences in results can be explained by the underlying parameters in each model.
Time on task
Agricultural operations are known to place high demands on the pilot’s attention for sustained work periods, which can result in a degradation of performance, even if the pilot has obtained adequate sleep. This is due to the continuous, repetitive, low altitude flying associated with this type of operation, while also managing the spray application (NTSB, 2014).
Rosa and others (2020) found that during a simulated 11-hour flight mission, participants' self-ratings of fatigue increased over time and their response time was slower after 7 hours. This demonstrates that sustained attention and vigilance were adversely affected by time on task.
Having started the aircraft’s engine at 0553, the pilot had been operating for nearly 6 hours when the accident occurred at 1145. Consistent with previous days and normal operations, the pilot took short breaks while the loader was refuelling, to get out of the aircraft, eat and drink. These breaks occurred approximately every hour and would last about 10 minutes. One fatigue countermeasure is activity breaks. These can reduce the impact of accumulating workload and alertness and performance will improve briefly due to providing a mental break from a continuous task (Caldwell 2008; Mallis and others 2022). Therefore, breaks can be temporarily beneficial in reducing the effects of fatigue.
Combined effects of workload and fatigue
Fatigue and workload can have similar effects on vigilance, perception and reaction/response times. A study of workload and fatigue in rail workers (Fan & Smith, 2017) found that both high workload and fatigue were associated with performance impairments. High workload was also found to increase fatigue, which then leads to a reduction in performance. The United Kingdom Civil Aviation Authority Flight-crew human factors handbook – CAP 737 (2016) described symptoms of increasing workload, including attentional and task focusing, task shedding, increased fatigue, and chance of error. It stated that:
Sustained workload contributes to fatigue. Very high workload (particularly fast onset) and feelings of not coping with the workload can cause high arousal or stress. All these things make error more likely.
The handbook lists effects of fatigue, similar to those associated with mental fatigue described earlier, including reduced awareness, easy distraction and increased slips and mistakes.
Accident site and aircraft damage
Accident site and impact
The wreckage was located at the southern end of a stand of trees and had been subject to a significant post-impact fuel-fed fire. There were no powerlines in the area and there was no evidence the aircraft struck a tree or bird prior to the collision with terrain.
On-site examination of the wreckage and surrounding ground marks indicated that the aircraft impacted terrain upright, in a nose-down attitude of about 40°, with the right wing down about 10°. The propeller, main wheels and wing leading edge impacted the ground first (Figure 10), during which the fuselage right bottom longeron[16] fractured and punctured the right wing main spar (Figure 11). Two propeller blades were located at the engine point of impact.
Figure 10: Initial impact points – right wing, main landing gear and propeller
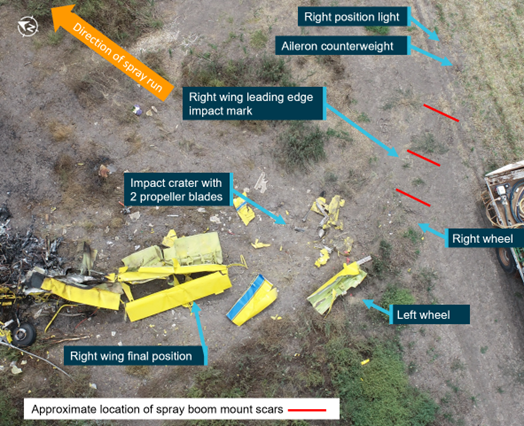
Source: ATSB
Figure 11: Fuselage frame longeron fracture and associated impact damage with main spar damage to right wing
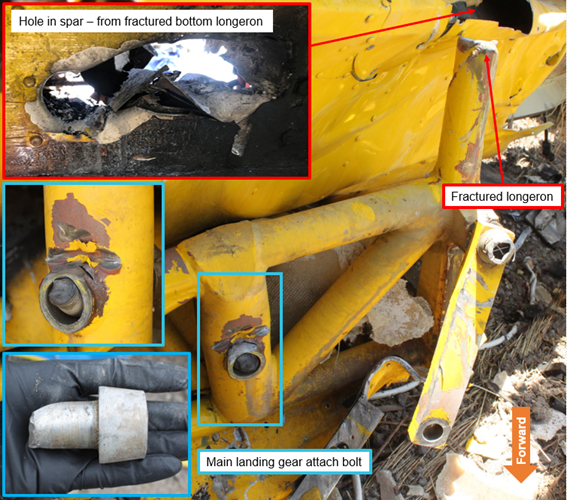
Source: ATSB
Forward momentum then collapsed the forward section of the fuselage and resulted in the main spar rotating about 120° and separating from the fuselage. The aircraft then continued a short distance rotating to the right, consistent with a right turn/spin, and came to rest facing approximately east.
The engine fractured in half around the flange ‘C’ area (ring of bolts joining the exhaust casing to the gas generator casing), with the gas generator module remaining near the fuselage. The propeller hub, with propeller blade, the engine power section module, including power turbine wheel, was recovered about 27 m from the impact point, in the direction of the target crop (north). The liberated compressor turbine disc was found a further 30 m beyond the hub in a similar direction (north-east), and at the edge of the fire zone (Figure 12).
The flame front and debris trail were in the direction of the wind (towards the north-east) and towards the target crop (north). The propeller hub displacement and fire zone were consistent with the aircraft’s trajectory prior to the loss of control, and with ignition at the final resting place. There was no evidence of fire at the initial impact point.
Figure 12: Overview of accident site and fire zone
Source: ATSB
Wreckage examination
Although the throttle position could not be determined from the wreckage, examination of the damage to the engine and propeller blades was consistent with the engine producing power at impact. Seat frame distortion was consistent with a nose-down attitude at impact. Although impact and fire/heat damage precluded inspection of some control tubes and cables, flight control continuity was established via examination of connections, for example steel rod ends securely attached to bellcranks.
Aircraft configuration
Flap actuator measurement and corresponding flap setting indicated the flaps were extended about 18°. Due to impact damage, the position of the dump lever and of the hopper door could not be determined.
Fuel testing
A fuel sample was collected from the operator’s fuel tank at the property. The fuel was tested for the presence of water with none identified. A visual inspection did not identify any particulate matter in the fuel. There were also no reports of fuel quality concerns with the operator’s other aircraft using the same fuel source.
Survivability
Post-mortem and toxicology results
An autopsy report was prepared for the NSW Coroner. The report provided to the ATSB included the results of a post-mortem examination conducted by a forensic pathologist and toxicology testing.
The post-mortem examination found one minor fracture and multiple heat-related injuries, with no (life-threatening) traumatic injuries identified. No natural disease pathology was identified and no substances likely to have contributed to the accident were found in the toxicology results. The cause of death was found to be the effects of fire.
Restraint and helmet
The pilot’s seat was fitted with a 4-point harness, the webbing of which was destroyed by the fire. Despite this level of damage, the left and right lap belt attach points were found secured and the lap belt and shoulder harness steel buckle was secured. Additionally, the lap belt and shoulder harness webbing had been replaced in January 2020, and therefore would be very unlikely to have failed due to deterioration.
The pilot was always known to wear a helmet and was almost certainly wearing it at the time of the accident.
Impact force analysis
The ATSB analysed deformation of the pilot’s seat frame to determine peak impact deceleration. The pilot’s seat frame was bent at the two seat attachment locations, but the seat pan was undeformed. This indicated that the angle of deceleration was mostly forward rather than vertical. It was assessed that the seat rail was at the lowest height adjustment. The 4-point restraint was being worn at impact.
In conducting a dynamic loads analysis, a conservative evaluation of the peak deceleration for the pilot seat was 75 G. Based on a stall speed with flaps retracted of 60 kt, this equates to a square wave deceleration pulse[17] duration of 42 milliseconds.
The Aircraft crash survival design guide Volume 2 – Impact conditions and human tolerance (Coltman and others, 1989) placed this forward deceleration in the ‘area of severe injury’. Severe injury included life-threatening injuries such as major haemorrhages, spinal, abdominal and thoracic injuries, multiple fractures, concussion and long-time unconsciousness (Eiband, 1959). This was based on experiments of whole-body impact tolerance conducted on human volunteers to (mostly) subcritical levels, and test animals. Whole-body tolerance criteria were assessed with subjects seated in the upright posture and wearing full-torso restraints (and in some cases head restraint). The tolerable magnitude of accelerative force is a function of the duration; higher G were tolerated for a shorter pulse duration.
Post-impact fire safety
Post-impact fire and survivability
A potentially survivable accident is one in which the impact forces are within the limits of occupant tolerance, the aircraft structure preserves the required survival space, and the occupant restraint is adequate. As detailed below, for aircraft (including fixed and rotary wing) with a maximum certified take-off weight of 5,700 kg or less, post-impact fire (PIF) has been shown to contribute significantly to injuries and fatalities in accidents that are otherwise potentially survivable (TSB, 2006).
Aircraft certification requirements
Aircraft certification is found primarily in three regulatory structures: the US Federal Aviation Regulations (FARs), the Canadian Aviation Regulations, and the European Aviation Safety Agency requirements. These requirements are harmonised such that light aircraft manufactured in the US, Canada and Europe all meet basically the same standards.
Part 23 of the FARs prescribes the airworthiness standards for aeroplanes in the normal, utility, aerobatic, and commuter categories. There are only three FAR 23 fuel system certification requirements designed to reduce the risk of PIF. These specifically apply to aircraft with retractable landing gear in the event of a wheels-up landing.
The AT-400 aircraft was certificated under FAR 21 in the restricted category. It met the structural requirements of FAR 23, and the flight criteria, propulsion, systems and equipment items of CAM 8, Appendix B (FAA TCDS A9SW).
Fuel tanks in accident impacts
In an accident impact, metal fuel tanks are prone to rupturing, allowing fuel to spill. The rupture of the tank causes the fuel to escape at high pressure and velocity which in turn causes the fuel to form a fine mist, which can be ignited by a source such as a hot engine or electrical arcing, and produces a very intense fire.[18]
The rupturing of the tanks results from high fluid pressures caused by inertial accelerations during the impact. The pressure distorts the tank walls and rupture will occur when the strain[19] of the distortion reaches the rupture strain (also known as the ‘ultimate’ or ‘fracture’ strain) of the tank wall material.
To improve crashworthiness, fuel bladders and cells have been constructed of materials that are less prone to rupturing, that is, they have a higher rupture strain. These are able to withstand more deformation and a puncture is less likely to expand or tear and form a larger opening from which fuel can escape.
The rupture strain for airframe aluminium (2024-T3 alclad sheet) is about 18%. Elastomers[20] tolerate severe deformation without rupturing – for a typical elastomer, the rupture strain is about 300% – significantly higher than metals. Additionally, even if elastomeric walls are punctured, the probability of fuel misting is very low because the flow rate for the puncture is much less than through a split tank wall. As an example, Robinson R44 helicopter bladder tanks are elastomer.
The resistance of elastomers to rupture and puncture can be substantially increased by incorporating high-strength fibres, such as Kevlar, into the material. For ultimate post-crash fire resistance (as in motor racing), fuel tanks (or cells) use double elastomeric walls with material such as Kevlar in the outer layer. This substantially reduces the probability of tank wall rupture, puncture and of fuel misting.
Prevention of post-impact fires
The US National Transportation Safety Board (NTSB) special study report General Aviation Accidents: Postcrash Fires and How to Prevent or Control Them (NTSB, 1980), found that PIF occurred in about 8% of the 22,002 general aviation accidents in the US during 1974–1978. Fatalities resulted from about 59% of the accidents involving PIF and 13.3% of the accidents without fire. The study tested the hypothesis that PIF occur more often in severe accidents. Severe accidents included collisions with the ground or objects such as trees/poles, stall/spin accidents, and some following engine failure/malfunction. These made up almost 80% of fatal accidents. In severe accidents, fatalities occurred in 18% of the accidents without PIF, but in more than 60% with PIF. For non-severe accidents, less than 1% involved fatalities without PIF and 19% involved fatalities with PIF. The report summarised that fire, rather than impact, was the major contributor to fatalities in general aviation accidents involving PIF.
The study found that PIF was occurring in survivable accidents. It noted that in contrast to civil aviation, the US Army had used fuel containment technology to dramatically reduce fire injuries and deaths. A crash resistant fuel system is designed to absorb energy in controlled failures of sacrificial structures to minimise impact loads on the fuel tank and eliminate the escape of flammable fluid in a crash. The intent was that the aircraft occupants would then have sufficient time to escape or be rescued without the threat of fire.
The report identified that technology for crash-resistant fuel systems existed (in 1980) suitable for general aviation aircraft. The 1980 NTSB special study report stated that ‘the concept of fuel containment is both feasible and achievable now’. The report Tests of Crash-Resistant Fuel System for General Aviation Aircraft (Perrella, 1978) concluded that lightweight, flexible, crash-resistant fuel cells used in combination with self-sealing break-away fuel-line couplings can effectively reduce PIF in general aviation aircraft equipped with wing tanks. Safety fuel cells were developed in the 1960s to prevent post-crash fuel-fed fires in race cars to improve survivability.
However, aircraft design and certification regulations did not reflect the technologies available. In response, the US NTSB issued 6 recommendations to the US Federal Aviation Administration (FAA) to implement regulations aimed at addressing the issue of post-crash fires – A-80-90 to A-80-95.
On 17 September 1985, the FAA issued an advance notice of proposed rulemaking that informed the public of the FAA’s intent to formulate rules to improve the crash-resistance of small airplanes' fuel systems and requested economic and technical information to assist in economic analysis and technical decisions for future rulemaking.
After several years of studies and discussions, on 20 May 1988, the FAA advised the NTSB that they had drafted a notice of proposed rulemaking (NPRM). On 14 February 1990, the FAA issued an NPRM proposing changes to the airworthiness standards to improve the crash resistance of fuel system on normal, utility acrobatic, and commuter category airplanes. These proposed design changes were to limit fuel spillage near ignition sources and would provide additional time for survivors of an accident to evacuate the aeroplane.
After some changes and review of the NPRM, in 1995, the FAA concluded that the recommendations could not be justified on a benefit-to-cost basis and therefore planned to take no action on these recommendations.
In 1996, the NTSB assessed that no tangible action had occurred in the 16 years since the issuance of these recommendations, and classified recommendations A-80-90 to -92 as closed with unacceptable safety action.
Since that time, crash-resistant fuel bladders/tanks have been introduced in rotorcraft. Crash-resistant fuel system technologies have also advanced significantly, particularly in motor sports.
Regulation of helicopter fuel systems
In 1994, US helicopter standards FAR 27.952 and FAR 29.952 introduced fuel system crash resistance tests and features for new design certification. These were introduced because it was estimated at the time that 5% of occupants in survivable rotorcraft accidents were killed or injured by PIF. There were no equivalent test requirements for fixed wing aircraft.
Research for ATSB investigation AO-2013-055, found that in Australia from 1993 to 2013, PIF occurred in 7 of 47 impact-related accidents (with usable fuel remaining) involving Robinson R44 helicopters not fitted with bladder tanks. Six of those accidents resulted in fatalities. The investigation found that PIF occurred in a significantly higher proportion of accidents involving R44 helicopters without bladder-type tanks than in other similar helicopter types. In response to ATSB safety recommendation AO-2013-055-SI-01, in April 2013, CASA issued an airworthiness directive requiring Australian operators of R44 helicopters to comply with the manufacturer’s service bulletin to replace all-aluminium fuel tanks with bladder-type tanks on R44 helicopters. Since then, there have been 68 R44 and R44 II accidents in Australia, 4 of which had PIF. There were no recorded fatalities as a result of PIF in R44 helicopters in that period.
Transportation Safety Board of Canada safety issues investigation
The Transportation Safety Board of Canada (TSB) conducted a safety issues investigation – Post‑impact fires resulting from small-aircraft accidents. The investigation examined TSB data for the 13,806 accidents involving aircraft weighing 5,700 kg or less, that occurred between 1976 and 2002. The TSB determined that PIF had occurred in 521 (3.8%) of those accidents, resulting in 728 (22%) of the 3,311 total fatalities. Of the 728 fatalities, 205 were assessed as due to fire as were 80 of the 231 total serious injuries. The aircraft included 382 production aeroplanes, 94 production helicopters, 27 amateur-built aeroplanes, 2 amateur-built helicopters, 1 gyroplane and 17 ultralights. Two of the accidents were mid-air collisions between 2 aeroplanes.
The investigation found that PIF presented a significant risk of fire-related injuries and fatalities to the aircraft occupants following a collision because of:
- the proximity of fuel to the occupants
- limited escape time
- limited energy-absorption characteristics of the airframes in crash conditions
- high propensity for immobilising injuries
- inability of firefighters to suppress PIFs in time to prevent fire-related injuries and fatalities.
The investigation concluded that there should be improvements to prevent PIF and reduce fire-related injuries in otherwise survivable accidents. It found that ‘the most effective defence against post-impact fire is to prevent the fire from occurring at impact, either by containing fuel or preventing ignition, or both’.
The investigation also reviewed the history of post-impact fire safety action and identified that previous attempts to amend certification requirements for small aircraft had been unsuccessful. The report stated that post-impact fire-resistant fuel system technology had been demonstrated to be effective in race car and automotive applications, and in certified civilian helicopters. However, there was no requirement to incorporate these engineering countermeasures into new or existing small aeroplanes (or helicopters certified before November 1994).
While acknowledging the difficulty of implementing design improvements in new and existing (FAR 23 and equivalent) aircraft, the investigation found that doing so would reduce the incidence of fire-related injuries and significantly increase the rate of occupant survival.
ATSB post-impact fire occurrences
Post-impact fire data
As not all accidents were likely to have a post-impact fire risk, ATSB identified a subset of accidents, which were impact-related and therefore expected to be more likely to result in fire. The ATSB occurrence database held records of 316 collision with terrain or controlled flight into terrain (CFIT) accidents involving VH-registered (fixed-wing) aeroplanes between 2012 and 2021.
PIFs occurred in 34 (11%) of these accidents. Of the 316 accidents, 81 resulted in fatal injuries, 24 of which had PIF, in 36 the highest injury level was serious, 5 of which had PIF, and 199 resulted in only minor or nil injuries, 5 of which had PIF. As a proportion of PIF accidents, 71% were fatal, 15% were serious injury accidents and 15% resulted in minor or nil injuries. By comparison, 20% on non-PIF accidents were fatal, 11% resulted in serious injuries and 69% in minor or nil injuries.
Figure 13: Proportion of accidents with and without PIF
The 316 accidents resulted in a total of 137 fatalities and 61 serious injuries. The 34 PIF accidents accounted for 35 of the fatalities (26%) (similar to the TSB issues investigation which found 22%), and 10 (16%) of the serious injuries (Table 4).
Table 4: Number of fatal and serious injuries in PIF vs all aeroplane accidents 2012-2021
All collision accidents (316 total) | ||
Injury category | Number | Rates per accident |
Fatalities | 137 | 0.43 |
Serious injuries | 61 | 0.19 |
All accidents resulting in PIF (34 total) | ||
Injury category | Number | Rates per accident |
Total fatalities | 35 | 1.03 |
Total serious injuries | 10 | 0.29 |
Fatalities due to fire | 5 | 0.15 |
Serious injuries due to fire | 4 | 0.12 |
Survivability analysis
The ATSB analysed available information from the 34 PIF accidents to determine which fatalities and serious injuries were due to fire or impact. Information sources included post-mortem reports, coroners’ reports and published ATSB investigation reports. Post-mortem reports were not available for all the fatal accidents and were generally only of flight crew (not passengers). Further, for non-fatal injuries, recorded details of the injuries were limited. For this analysis, the severity was assessed as having been increased due to fire only where burns or smoke inhalation were specifically mentioned. Where information was unavailable, these were not counted as fire-related injuries/fatalities. As the NTSB found, fire rather than impact was the major contributor to fatalities in general aviation accidents involving PIF.
There were 2 accidents in which the cause of death was a combination of multiple injuries and fire, and where the injuries included head/skull injuries. These were assessed as probably not survivable because head injuries and skull fractures were significantly associated with mortality in studies of falls from heights and motor vehicle accidents (Liu and others, 2009, Papadimitriou-Olivgeris and others, 2020).
In 5 of the 34 PIF accidents (15%), a total of 5 fatalities were assessed as a result of fire following survivable injuries received in the impact. This was about 4% of all the VH-registered aeroplane impact-related accident fatalities. Two additional accidents resulted in a total of 4 serious injuries due to fire. Detail of the analysis is in Appendix B. In summary, analysis of the 34 PIF accidents found:
- 5 were considered survivable without the post-impact fire, where occupants were fatally injured
- 18 in which the accident impact was not considered survivable or were probably not survivable
- 2 resulted in serious fire-related injuries
- 9 in which occupants egressed and survived without further injury.
Five of those 34 accidents with a post-impact fire occurred during aerial application operations:
- 2 were probably not survivable as the occupants sustained multiple injuries including skull fractures
- 1 in which the occupant survived and exited the aircraft before it was destroyed by post-impact fire
- 1 in which the pilot died from the effects of fire
- 1 in which the pilot died from the effects of fire and sustained injuries that would probably have prevented the pilot extricating themselves from the wreckage.
Fuel tank type
Three types of fuel tanks were used in the accident aircraft – integral, rigid and bladder tanks:
- Integral fuel tanks are part of the aircraft structure. They are manufactured by assembling parts of the aircraft structure with sealant to form a fuel-tight compartment, most commonly in the wings.
- A rigid tank can be made of various materials including aluminium alloy, steel or composites. They are usually removable and mounted into the airframe structure.
- A bladder type fuel tank is a rubber/elastomer cell dependent on the structure of the cavity it sits in to support the weight of the fuel within it. Bladder (or ‘bag’) tanks have historically been installed in the wing in lieu of sealing the structural components but not made of crash-resistant materials. Crash-resistant materials are capable of providing impact and puncture resistant fuel bladders and cells such as those used in helicopters and racing cars.
For the aircraft involved in the 34 PIF accidents:
- Non-crash-resistant bladder tanks were fitted in 2 aircraft involving 6 fatalities. No serious injuries were recorded for those aircraft and neither accident was survivable.
- Rigid tanks were fitted in 9 of the aircraft involving 7 fatalities, none of which were survivable. Two resulted in serious injuries that were not fire related.
- Integral tanks were fitted in 23 of the aircraft involving 22 fatalities, 5 occupants of which would have survived without for the fire. In those aircraft, 8 serious injuries occurred, 4 of which were attributable to fire.
Organisational information
Aircair overview
Aircair was founded in 1980 and was one of the largest aerial application operators in Australia. The CASA-issued Air Operator’s Certificate current at the time of the accident was re-issued to Aircair on 11 June 2021, valid until 30 June 2024. Under the certificate, Aircair was authorised to conduct aerial application and aerial work operations. At the time of the accident, Aircair had a fleet of 13 aircraft conducting application operations and engaged 12 pilots. As well as VH-ACQ, the aircraft fleet included a radial-engine Air Tractor AT-301, turbine-engine AT-502, AT-504 and AT-802 type aircraft, and a piston-engine Cessna 188B, which the company had purchased specifically for the accident pilot to operate during their initial supervised hours of aerial application operations.
Safety management
At the time of the accident, although Aircair was not required to have a safety management system, they had implemented the AAAA’s Aerial Improvement Management System (AIMS). AIMS was designed to meet the safety management and quality assurance requirements of the multiple regulators that an aerial application employer is bound by, including CASA. AIMS incorporated safety management of all facets of the business, including aviation, and was designed to integrate with the company’s Operations Manual.
The AIMS section associated with planning and conducting an application detailed that the operations manager or general manager could select a particular pilot for a given application based on their experience. The section also included a detailed drift risk assessment, which was to be followed by a plan to manage the application risks, including identifying if a forecast temperature would result in a decision to cease spraying. There was no requirement for the risk assessment to be documented or retained. The chief pilot reported having discussed the application plan and forecast with the pilot the evening prior to the accident, and the pilot had confirmed the temperature spray limit with the operations manager while the aircraft was being refuelled shortly before the accident.
The AIMS section also required the pilot to complete a hazard check on arrival to the treatment area.
Similar occurrences
Loss of control in flight
The CASA Advisory Circular 61-16 – Spin avoidance and stall recovery training (CASA, 2020), stated that stall-spin accidents accounted for about a quarter of all general aviation accidents worldwide. Further, that other than those which occurred during dual flight instruction, most of those losses of control occurred at a height too low for recovery.
The ATSB occurrence database recorded 269 accidents that occurred due to a loss of control between 2010 and 2020 involving (fixed-wing) aeroplanes. Of those accidents, 32 occurred while manoeuvring or conducting airwork, 17 of which resulted in fatal injuries. Of the 32 accidents that occurred during manoeuvring/airwork, 14 were conducting aerial application or mustering operations.
The following is a sample of ATSB investigations into fatal accidents that resulted from an aerodynamic stall at a height too low to recover before the aircraft impacted terrain.
AO-2008-069
The pilot of a Piper Aircraft PA36-375 Pawnee Brave was conducting aerial baiting operations in the Pilton Valley, Queensland when the aircraft collided with terrain. The aircraft was seriously damaged by impact forces and a post–impact, fuel- and magnesium-fed fire. The pilot was fatally injured.
The investigation found that the topography of the area and the strong gusty wind conditions at the time, probably resulted in turbulence that increased the hazardous nature of the low-level application task. It is likely that the pilot lost control of the aircraft as a result of that turbulence, at a height from which recovery was not possible before the aircraft struck the ground.
AO-2009-070
The pilot of a Cessna A188B aircraft was fatally injured when the aircraft impacted terrain during spraying operations. The investigation determined that the aircraft stalled at an altitude from which the pilot was unable to recover before the aircraft impacted terrain.
AO-2011-082
A PZL-Mielec M18A Turbine Dromader aircraft impacted terrain on a cotton station near Dirranbandi, Queensland while conducting aerial spraying. The pilot was fatally injured, and the aircraft was destroyed by impact forces.
The ATSB found that, for reasons that could not be determined with certainty, the aircraft departed from controlled flight during a turn at low height and the pilot was unable to recover before impacting the ground.
AO-2012-059
The owner-pilot of a Cessna 150 aircraft was aerial stock mustering on a cattle station about 55 km north-east of Bourke, New South Wales. The aircraft was observed circling over an area (where cattle were not moving,) then entered a steep descent followed by the sound of an impact. The aircraft was seriously damaged, and the pilot sustained fatal injuries.
The ATSB found that, while manoeuvring at low level, the pilot inadvertently allowed the aircraft to aerodynamically stall, resulting in a high rate of descent and collision with terrain. There was insufficient information about pilot control inputs to establish the factors that precipitated the stall.
AO-2014-192
On 29 December 2014, a Cessna 172S aircraft departed Cambridge Airport, Tasmania to photograph yachts participating in the 2014 Sydney Hobart race. On board the aircraft were the pilot and a photographer.
At about 1815, the aircraft commenced low-level photographic runs on yachts. Shortly after completing a run on one yacht at a height of about 50 ft, the aircraft entered a steep climbing turn. The aircraft had almost completed a 180° turn when the upper (right) wing dropped sharply while the aircraft’s nose pitched down to almost vertical. The aircraft impacted the water’s surface in an almost vertical nose down attitude with wings about level. Both aircraft occupants were fatally injured, and the aircraft was substantially damaged.
As a result of the steep climbing turn, the aircraft’s upper wing aerodynamically stalled, resulting in a rapid rotation out of the turn. The steep pitch attitude indicated that, because of the stalled upper wing, the aircraft entered a spin. There was insufficient height for the pilot to recover the aircraft.
Addressing loss of control in flight occurrences
The US FAA Airplane Flying Handbook (2021) chapter 5 Maintaining aircraft control: upset prevention and recovery training, stated that a loss of control in flight (LOC-I) is the leading cause of fatal general aviation accidents in the US and commercial aviation worldwide. The text listed situations that increase the risk of loss of control, including uncoordinated flight, distraction, turbulence and poor risk management. It further stated that in situations where a LOC-I can occur, pilots must recognise when the aircraft is approaching a stall or has stalled and execute the correct procedure to recover the aircraft. This requires training that includes slow flight, stalls, spins, and unusual attitudes.
US FAA Advisory Circular 120-109 – Stall prevention and recovery training was aimed at reducing LOC-I accidents and incidents. The circular stated that a ‘recurring causal factor in LOC-I accidents and incidents is the pilot’s inappropriate reaction to impending stalls and full stalls’. Further, the circular advised that reducing the angle of attack was the most important pilot action to recover from an impending or full stall and therefore this should be emphasised in stall training.
Safety analysis
Introduction
On the morning of 4 December 2021, after completing the fifth spray run of the eleventh chemical load on a property near Moree, New South Wales, VH-ACQ was observed to climb, enter a right procedure turn, then descend rapidly and impact terrain, followed almost immediately by an intense fuel-fed fire.
The investigation found no evidence of a bird or tree strike, or anything likely to have jammed the flight controls affecting controllability. Continuity of the flight controls was established, the main wing spar was intact, and the engine was making power and driving the propeller when the aircraft impacted the ground. At the time of the accident, the aircraft was below the maximum take-off weight approved for aerial application operations and the centre of gravity was within the extrapolated limits.
This analysis will discuss development of the accident sequence and the effect of the environmental conditions. The pilot’s experience and how this contributed to workload and fatigue will also be examined. Further, it will consider the management of flight risk and factors affecting survivability.
Loss of control
Witness observations of the aircraft turning and descending rapidly were consistent with an aerodynamic stall and loss of control in flight. These observations were consistent with the accident site, in which the aircraft wreckage was confined in a small area, with evidence of a high vertical impact and low forward speed.
The last recorded GPS position left of the last spray run and about 180 ft above the ground, was consistent with the pilot conducting a right procedure turn – a shallower turn about 45° to the left, followed by a steeper right turn – at the end of the spray run. That last recorded height was very likely not the maximum reached, as the data from previous turns showed the aircraft generally climbed to about 250 ft above the ground.
The loss of control in flight was consistent with a rapid entry to the stall. That stall was a result of the angle of attack being too high from moving the elevator control stick position too far aft while increasing the bank angle during the turn. The stick force experienced by the pilot on the elevator control depended on the trim position, which could not be determined. Regardless of the stick force, the stick position that a pilot needs to set to recover from a stall will be the same. Stall prevention requires monitoring the position of the elevator control stick, awareness of its position at which the aircraft will stall, and to maintain the control stick forward of that position. Stall warning or buffet should alert the pilot to move the stick forward, but the pilot may have had very little warning. The pilot reportedly had the stall stick position demonstrated, and although they had on occasion pulled the stick back too far in a turn during training, this was a common training error, which the pilot had been observed to have rectified. Analysis of recorded GPS data from the pilot’s flights prior to the accident, showed the pilot generally employed sound technique in the turns.
The Airplane Flight Manual stated that the aircraft would lose 220 ft in recovering from a straight and level stall at the published maximum weight, based on flight testing. Recovery height would be increased by an accelerated stall and uncoordinated turn. Accident site analysis showed the aircraft impacted the ground nose-down and wings almost level, which suggested the pilot had acted to recover from the stall but had insufficient height to complete the recovery.
Effect of field shape
As evidenced by the recorded GPS data, the pilot had not flown hazard checks on the accident day. The operator assessed that as the pilot had overflown the accident block several times in the previous days, they were probably familiar with it. However, it could not be determined whether the pilot had identified the uneven southern boundary and shape of crop to be sprayed before commencing the accident turn.
Due to the shape of the target block, the pilot needed to turn the aircraft further beyond the southern boundary or wider than the previous turns, to line up on the next spray run at a suitable height to commence spraying. Consideration of additional turn radius was also required due to the 10–18 kt gusty south-westerly wind becoming a tailwind during the turn, thereby pushing the aircraft closer to the crop.
The recorded GPS data from the pilot’s flights on the day prior to the accident showed that the aircraft was usually lined up on the next spray run about 200 m prior to the crop boundary. The location of the accident and the position where the loss of control occurred was about 110 m south of the target crop. At that point, the aircraft was too high and too close to the southern boundary to manoeuvre safely to commence spraying the crop at the start of the next spray run. From this position, the pilot likely attempted to tighten the turn rather than miss the additional crop (and skip that spray run).
Experience, workload, and fatigue
Experience
The pilot had commenced aerial application training immediately after attaining a commercial pilot licence in the minimum timeframe. On achieving their aerial application and low-level ratings, the pilot commenced aerial application operations as an employee of the aircraft operator, in September 2021. The pilot then conducted the required supervised aerial application flight time in a piston-engine aircraft. One week before the accident, the operator assessed that the pilot was ready to transition to turbine-engine Air Tractor aircraft.
Although the pilot had demonstrated competence in the aircraft and aerial application to a high level of skill for their experience, at the time of the accident, they were still relatively inexperienced in overall flight time, aerial application, and particularly in the AT-400 aircraft. This inexperience likely affected many facets of the operation, including aircraft handling, workload and fatigue.
Workload
Agricultural pilots operating at low altitudes must visually scan external cues to control the aircraft and avoid obstacles, while also monitoring inside the cockpit including instruments, spray systems and property maps. Due to the close proximity to obstacles, terrain and the airspeeds at which the aircraft are flown, agricultural pilots have less time to respond to abnormal situations. As a result, any lapse in concentration or imprecision in control input could lead to catastrophic consequences (NTSB, 2014).
During the morning, the increased temperature, change in wind direction and increase in wind strength and gust speed, made the flying conditions increasingly turbulent. The conditions half an hour after the accident were described as quite windy and rough. Turbulence has been found to increase physical and mental workload, which can lead to degradation in the pilot’s ability to safely and effectively operate the aircraft. This is due to human perceptual systems breaking down, as a result performance can diminish, leading to fatigue, motion sickness and reduced mental performance. (Dodd and others, 2014). These conditions increased the pilot’s workload through additional physical aircraft handling and discomfort.
The pilot’s text message regarding the temperature, radio call regarding drift, and the aircraft’s track on the accident load, were indicative of the pilot making decisions in response to the changing conditions. While such decision-making is a usual part of spraying operations, it requires cognitive resources, thereby increasing workload. The pilot’s radio call about 20 minutes before the accident, suggested the pilot was experiencing stress and high workload. During the morning, the pilot had been in radio contact with the operations manager and other company pilots including the Aircair general manager. However, resources usually available to assist in managing the pilot’s workload and aid in decision‑making, were diminished on the accident day as the loader had no radio and it was the first day that the chief pilot was not supervising the pilot.
Without these resources to assist, the pilot was possibly assessing whether to cease flying due to the conditions, further adding to their cognitive load. Making such a decision may also have been more difficult while other company pilots were continuing to operate.
The pilot’s concern about drift precipitated a change of plan, whereby the pilot elected to move from the western to the eastern boundary, abandon the incomplete racetrack pattern and resume spraying in a back-to-back pattern. The change in spray pattern briefly required the pilot’s focus inside the cockpit to change GPS settings, introducing the potential for distraction and increasing workload. However, there was no evidence to demonstrate this distraction occurred at the time of the accident.
Due to a combination of inexperience, the environmental conditions, decision-making, and absence of supervision, the pilot’s workload was likely at a level known to increase error rates, reduce performance and lead to important information being missed (Green and others, 1996).
Fatigue
The pilot had several early starts and long days in the month prior to the accident, consistently reporting to a friend (but not to the operator) being very tired at the end of each day. As the accident day was the pilot’s ninth day of duty, there was an increased risk of cumulative fatigue. In the 3 days prior to the accident, the pilot had recorded their longest consecutive flight and duty times since commencing aerial application operations. Additionally, the pilot’s commute by car to and from the base was extended due to recent flooding, which reduced the opportunity for recovery between flight duties.
All the pilot’s recent flight time was cognitively demanding low-level aerial application with short breaks during refuelling. Additionally, the cognitive demands would have been higher than for a more experienced pilot, particularly the pilot’s very limited flight time in the turbine-engine aircraft. At the time of the accident, the pilot had been operating for approaching 6 hours, with several short (10-minute) breaks during refuelling, including one about 15 minutes prior to the accident. Research on sustained attention during a task has shown that decreases in performance and self-rating experiences of fatigue increase over time (Rosa and others, 2020). However, work breaks can be temporarily beneficial in reducing the effects of fatigue (Caldwell 2008; Mallis and others 2022).
The pilot’s sleep history and the accident time of day were unlikely to have affected the pilot’s performance. However, the consecutive long flight and duty times in the days leading up to the accident, in what would have been a high cognitive workload environment for the pilot, likely resulted in the pilot experiencing fatigue at a level known to affect performance.
Effects of workload and fatigue
Several factors increased the pilot’s workload at the time of the accident, including the conditions and inexperience. Those same factors and the high workload itself, combined with long flight and duty times in the preceding days, also likely contributed to the pilot experiencing fatigue.
The pilot had probably encountered similar environmental conditions while flying a piston-engine Cessna 188B aircraft in the previous weeks, but had more experience in that aircraft. That aircraft also had more docile stall characteristics and gave more warning of an impending stall. After commencing flying VH-ACQ 5 days before the accident, the pilot had demonstrated competence in that aircraft and operated it effectively, including spraying over 1,000 hectares in the previous 2 days. However, on the accident day, the pilot mishandled the aircraft during the turn. This handling error was likely a result of fixating on making the crop, and not monitoring the aircraft state or allowing adequate margin for the conditions. These errors and impaired awareness were consistent with the effects of both overload and fatigue.
Flight risk management
Management of fatigue is a shared responsibility between the aircraft operator and the pilot. Although the pilot had self-assessed as being tired on many occasions in the previous weeks, including the evening prior to the accident, there was no evidence this had been reported to the operator. Additionally, this tiredness had been noted in the evenings, following which there was a sleep opportunity for the pilot to recover (to some extent) before commencing the next morning.
Based on the regulatory duty time limitations, had the pilot been off duty for between 9 and 10 hours when they commenced on the morning of the accident, they were within a discretionary period that required a self-assessment of being mentally and physically fit to fly. The pilot commenced on the accident day close to the 10-hour rest period and it was unknown whether the pilot conducted this self-assessment. However, pilots were required to ensure they were fit to fly prior to every flight. There was also no evidence that the operator was aware the pilot had commenced duty on the accident day within or approaching the discretionary duty time window.
The aircraft operator’s operations manual stipulated that fatigue be managed in accordance with Civil Aviation Safety Regulations, which provided maximum flight and duty times (and minimum rest periods) for aerial application operations. However, there was no consideration of environmental conditions or experience – total aeronautical experience, aerial application flight hours, or hours in an aircraft model – nor how this may affect fatigue. Given inexperience and environmental conditions can increase fatigue, these factors in combination should be considered as part of fatigue risk.
Furthermore, fatigue risk is just one component of overall flight risk. A flight risk assessment provides a comprehensive assessment of factors that increase risk and the effect of combination of these factors. Although it was not required by regulations at the time, the aircraft operator had a safety management system. However, it did not include a flight risk assessment tool, which is a key component of a safety management system (FAA, 2016).
The 2014 US National Transportation Safety Board Special investigation report on the safety of agricultural aircraft operations outlined that risk management guidelines and best practices specific to agricultural aircraft operations were necessary to help operators and pilots mitigate their unique risks. These practices should include information and checklists for performing pre-flight risk assessments and identifying mitigation strategies.
A flight risk assessment tool specific for aerial application operations should include consideration of pilot (experience, recency, supervision, fitness to fly), aircraft (including role equipment), environment (weather, task, chemical, hazards) and operational pressures. Use of a flight risk assessment tool before commencing a flight also acts as a prompt for a pilot to reassess the risk when the considered factors change. Although the operator was attempting to manage the risk associated with inexperience, having a formal process may have integrated all the hazards present on the accident day. Had a flight risk assessment tool been available to the pilot on the accident morning, the combination of the weather conditions, inexperience, complexity of the task, absence of supervision, and probable fatigue, would have been expected to generate an elevated risk rating that would have required mitigation and/or approval for the pilot to conduct or continue the flight.
Survivability
The post-mortem examination identified that the pilot succumbed to the effects of fire. The fire was likely a hot, flash-over fire resulting from the rupture of the fuel tanks and misting of the fuel. Local workers who witnessed the accident were on site within minutes of the accident, however, the fire erupted within seconds of impact.
The tolerance of the human body to accident impact is a function of many variables, including individual characteristics, such as age, sex and general health. The restraint system significantly contributes to the overall probability of survival in an accident (Coltman and others, 1989). Contact injuries are reduced by 4-point (and 5-point) restraints and aviation-standard helmets. Restraints, energy-absorbing structure and seats reduce acceleration injuries. If these injuries do occur, they can contribute to fire-related fatalities and more serious injuries, by preventing self-extrication from an aircraft in the event of a post-impact fire.
An estimate of the impact forces, based on the bending of the pilot seat frame, indicated the accident would have likely resulted in severe injury. However, the pilot did not sustain impact-related injuries likely to have contributed to mortality. The pilot was almost certainly wearing a helmet and a 4-point restraint, and the cockpit maintained survivable space around the pilot’s torso. The crushing of the hopper and forward section of the aircraft likely absorbed a significant amount of the of the forward impact, aiding in reducing acceleration injuries.
Crash-resistant fuel systems
Air Tractor aircraft, like many others, use the aircraft wing structure as an integral fuel tank. The AT-400 fuel tank met or exceeded the certification requirements. In an impact with the ground, traditional aircraft wing structures are comparatively rigid and will rupture, allowing their fuel contents to escape. Due to the high fluid pressures generated inside the fuel tank in ground impacts, fuel forced through these ruptures tends to mist into a large cloud, which increases the risk of ignition and conflagrates quickly into a large encompassing fire.
An aircraft fuel tank lined with a crash-resistant bladder can be more resistant to spilling or leaking due to its ability to retain its contents if distorted. Being flexible, the bladder can withstand changes to its shape without rupturing or splitting. The bladder is also more tolerant of penetrating objects being able to deform around the intruding body to some extent. There have been no fatal or serious injuries to occupants as a result of post-impact fire in Robinson R44 helicopters in Australia since fitment of bladder tanks was mandated after a fatal accident in 2013. Prior to that time, accidents involving Robinson R44 helicopters without bladder tanks resulted in a significant proportion of post-impact fires. Of the (fixed-wing) aeroplanes involved in fatal accidents with post-impact fire in Australia between 2010 and 2022, 2 were fitted with fuel bladders. However, these were not made of crash-resistant materials.
Bladder tanks are one technology designed to improve crashworthiness of fuel systems. Crash‑resistant fuel systems reduce the risk of post-impact fire and provide occupants with more time to escape or be rescued. VH-ACQ was not fitted with crash-resistant fuel tanks or systems. The certification standards at the time the aircraft was manufactured did not require it, nor did the fixed-wing aircraft standards at the time of the accident. This differed from the requirements for rotary-wing aircraft.
The US National Transportation Safety Board and the Transportation Safety Board of Canada found a significant risk associated with post-impact fires in general aviation aircraft. As a result, they made recommendations to the US Federal Aviation Administration aimed at addressing the crashworthiness of fuel systems in these aircraft. A review of VH-registered aeroplane accidents in the ATSB occurrence database from 2010–2022 found a significant risk for post-impact fire fatalities, consistent with that previously identified in the US and Canada. Nearly 4% of the fatalities (5 fatalities in 10 years) in general aviation accidents in Australia were solely the result of the post impact fire. A fatality percentage of 5% was used by the Federal Aviation Administration to justify fuel system crash resistance tests and features for new helicopter designs.
The design principles and technologies for crash-resistant fuel systems exist and have been proven effective in helicopters and the automotive industry. Incorporating these in aeroplane design would reduce the risk of impact-induced fire in otherwise survivable accidents.
Findings
ATSB investigation report findings focus on safety factors (that is, events and conditions that increase risk). Safety factors include ‘contributing factors’ and ‘other factors that increased risk’ (that is, factors that did not meet the definition of a contributing factor for this occurrence but were still considered important to include in the report for the purpose of increasing awareness and enhancing safety). In addition, ‘other findings’ may be included to provide important information about topics other than safety factors. Safety issues are highlighted in bold to emphasise their importance. A safety issue is a safety factor that (a) can reasonably be regarded as having the potential to adversely affect the safety of future operations, and (b) is a characteristic of an organisation or a system, rather than a characteristic of a specific individual, or characteristic of an operating environment at a specific point in time. These findings should not be read as apportioning blame or liability to any particular organisation or individual. |
From the evidence available, the following findings are made with respect to the loss of control and collision with terrain involving Air Tractor AT-400, VH-ACQ, 75 km west-south-west of Moree, New South Wales, on 4 December 2021.
Contributing factors
- The aircraft was too close to the start of the spray run during the turn, which probably resulted in the pilot tightening the turn. This almost certainly resulted in an aerodynamic stall at a height too low to recover before colliding with the ground.
- The pilot was likely experiencing high workload and fatigue due to long flight and duty times, inexperience, the complexity of the task and the weather conditions. The combined effects of these factors probably resulted in the pilot mishandling the turn.
- The aircraft’s integral fuel tanks ruptured during the accident sequence. This resulted in a fire which led to the pilot’s fatal injuries.
Other factors that increased risk
- The aircraft was not fitted nor required to be fitted with a crash-resistant fuel system under the current standards or those in place at the time of manufacture. As a result, post-impact fire presents a significant risk of fire-related injuries and fatalities to aircraft occupants. (Safety issue)
Other findings
- A flight risk assessment tool is used in some aerial work operations, however for aerial application operations it is not a requirement and generally not used. A flight risk assessment tool tailored to aerial application would likely have identified an elevated risk on the day of the accident, due to the combination of the pilot’s inexperience, weather conditions, complexity of the task, absence of supervision and probable fatigue.
- The pilot was almost certainly wearing a helmet and 4-point restraint increasing their chances of survival in an accident.
Safety issues and actions
Depending on the level of risk of a safety issue, the extent of corrective action taken by the relevant organisation(s), or the desirability of directing a broad safety message to the aviation industry, the ATSB may issue a formal safety recommendation or safety advisory notice as part of the final report. The directly involved parties were provided with a draft report and invited to provide submissions. As part of that process, each organisation was asked to communicate what safety actions, if any, they had carried out or were planning to carry out in relation to each safety issue relevant to their organisation. Descriptions of each safety issue, and any associated safety recommendations, are detailed below. Click the link to read the full safety issue description, including the issue status and any safety action/s taken. Safety issues and actions are updated on this website when safety issue owners provide further information concerning the implementation of safety action. |
Crash-resistant fuel system
Safety issue number: AO-2021-052-SI-01
Safety issue description: The aircraft was not fitted nor required to be fitted with a crash-resistant fuel system under the current standards or those in place at the time of manufacture. As a result, post-impact fire presents a significant risk of fire-related injuries and fatalities to aircraft occupants.
Safety recommendation description: The ATSB recommends that the United States Federal Aviation Administration take action to address certification requirements for crash-resistant fuel systems for fixed wing aircraft to reduce the risk of post-impact fire.
Safety action not associated with an identified safety issue
Whether or not the ATSB identifies safety issues in the course of an investigation, relevant organisations may proactively initiate safety action in order to reduce their safety risk. All of the directly involved parties are invited to provide submissions to this draft report. As part of that process, each organisation is asked to communicate what safety actions, if any, they have carried out to reduce the risk associated with this type of occurrences in the future. The ATSB has so far been advised of the following proactive safety action in response to this occurrence. |
Additional safety action by Aircair Aviation Operations Pty Ltd (Aircair)
Aircair has considered whether there could be a risk associated with fatigue that does not necessarily correlate to flight and duty hours worked. As such, they are investigating if other means of measuring fatigue risk can be developed, such as a point score system that includes any other contributory factors such as conditions, experience, overall wellbeing and difficulty of the task. Further, they intend to explore technology available in modern cars and machinery that measures operator fatigue.
In August 2022, Aircair’s pilot group underwent advanced stall and spin prevention, recognition and recovery training with an experienced aerobatic instructor. Due to its success, Aircair is investigating ways of incorporating such training into its new pilot induction program.
Aircair recommended that the risks associated with mobile phone use in the cockpit (as referenced in the Aircair Operations Manual) are reiterated to pilots on a regular basis by way of pilot meetings and safety notices.
Aircair intends to ensure that pilots are regularly reminded of the possibility of becoming distracted by guidance systems and the impact this may have on safe operations. As part of this process, pilots should be reminded to only attend to GPS related issues when at a safe height above the ground.
Pre-application field inspections form a critical component for a safe application operation (particularly for unfamiliar fields). The requirement to conduct such inspections is set out in the Aircair Operations Manual and is tested during Aircair Operator Proficiency Checks (OPC). The importance of pre‑application field inspections will be reinforced to pilots on a regular basis by way of pilot meetings and safety notices.
Glossary
AAAA Aerial Application Association of Australia
AFM Airplane Flight Manual
AIMS Aerial Improvement Management System
CAM Civil Aeronautics Manual
CAR Canadian Aviation Regulation
CAS Calibrated airspeed
CASA Civil Aviation Safety Authority
CASR Civil Aviation Safety Regulations
CG Centre of gravity
EDT Eastern Daylight-saving Time
FAA Federal Aviation Administration
FAR Federal Aviation Regulation
FCM Flight crew member
IAS Indicated airspeed
ICAO International Civil Aviation Organization
LOC-I Loss of control in-flight
NASA National Aeronautics and Space Administration
NPRM Notice of proposed rule making
NTSB National Transportation Safety Board
PSI Pounds per square inch
SMS Safety management system. A systematic approach to organisational safety encompassing safety policy and objectives, risk management, safety assurance, safety promotion, third party interfaces, internal investigation and SMS implementation.
TSB Transportation Safety Board (of Canada)
UTC Coordinated Universal Time
Sources and submissions
Sources of information
The sources of information during the investigation included the:
- aircraft operator and chief pilot
- other company pilots
- Civil Aviation Safety Authority
- New South Wales Police Force
- aircraft manufacturer
- aircraft maintainer
- accident witnesses
- recorded data from the aircraft’s GPS units
- Bureau of Meteorology and Oz Forecast.
References
Australian Transport Safety Bureau (2017). ATSB Safety Investigation. Canberra, Australia: ATSB.
Bafna, T. & Hansen, J. P. (2021). Mental fatigue measurement using eye metrics: A systematic literature review. Psychophysiology, 58(6), 13828-n/a. doi: 10.1111/psyp.13828
Beilock, S. L., Carr, T. H., MacMahon, C., & Starkes, J. L. (2002). When paying attention becomes counterproductive: Impact of divided versus skill-focused attention on novice and experienced performance of sensorimotor skills. Journal of Experimental Psychology: Applied, 8, 6-16.
Boksem, M. A. S., Meijman, T. F., & Lorist, M. M. (2005). Effects of mental fatigue on attention: An ERP study. Brain research. Cognitive brain research, 25(1), 107-116. doi: 10.1016/j.cogbrainres.2005.04.011
Byrne, A. J., Murphy, A., McIntyre, O., & Tweed, N. (2013). The relationship between experience and mental workload in anaesthetic practice: an observational study. Anaesthesia, 68(12), 1266-1272. doi: 10.1111/anae.12455
Caldwell, J. A., Caldwell, J. L., & Schmidt, R. M. (2008). Alertness management strategies for operational contexts. Sleep medicine reviews, 12(4), 257-273. doi: doi:10.1016/j.smrv.2008.01.002
Civil Aviation Safety Authority (2012). Fatigue Management Strategies for Aviation Workers: A Training & Development Workbook.
Civil Aviation Safety Authority (2020). Advisory Circular AC 61-16 v1.0: Spin avoidance and stall recovery training.
Coltman, J. W., Van Ingen, C., Johnson, N. B. & Zimmerman, R. E. (1989). Aircraft crash survival design guide: Volume II – Aircraft design crash impact conditions and human tolerance. US: United States Army Aviation Applied Technology Directorate.
Dawson, D., & Reid, K. (1997). Fatigue, alcohol and performance impairment. Nature, July 1997, 388:235.
Dodd, S., Lancaster, J., Miranda, A., Grothe, S., DeMers, B., & Rogers, B. (2014). Touch Screens on the Flight Deck: The Impact of Touch Target Size, Spacing, Touch Technology and Turbulence on Pilot Performance. Proceedings of the Human Factors and Ergonomics Society 58th Annual Meeting, 58(1), 6-10. https://doi.org/10.1177/1541931214581002
Eiband, A. M., Human tolerance to rapidly applied accelerations: A summary of the literature, NASA Memorandum 5-19-59E, National Aeronautics and Space Administration, Washington, D.C., June 1959.
Faber, L. G., Maurits, N. M., Lorist, M. M., & de Lange, F. P. (2012). Mental Fatigue Affects Visual Selective Attention. PloS one, 7(10), e48073-e48073. doi: 10.1371/journal.pone.0048073
Fan, J., & Smith, A.P. (2017). The impact of workload and fatigue on performance. Conference Paper in Communications in Computer and Information Science, June 2017. doi: 10.1007/978-3-319-61061-0_6
Federal Aviation Administration (2021). Airplane Flying Handbook, FAA-H-8083-3C. US: FAA. Retrieved from: Airplane Flying Handbook | Federal Aviation Administration (faa.gov)
Fletcher, A., Lamond, N., van den Heuvel, C., & Dawson, D. (2003). Prediction of performance during sleep deprivation and alcohol intoxication by a quantitative model of work-related fatigue. Sleep Research Online, 5(2), 67-75.
Fletcher, A. (1999). Measurement and management of work-related fatigue: Development and preliminary validations of a predictive model. Ph.D. Thesis, 1999, The University of South Australia.
Folkard, S., & Åkerstedt, T. (2004). Trends in the risk of accidents and injuries and their implications for models of fatigue and performance. Aviation, space, and environmental medicine, 75(3), A161-A167.
Gawron, V. J. (2016). Overview of self-reported measures of fatigue. The International Journal of Aviation Psychology, 26:3-4, 120-131. doi: 10.1080/10508414.2017.1329627
Goode, J. H. (2003). Are pilots at risk of accidents due to fatigue?. Journal of safety research, 34(3), 309-313. doi: 10.1016/s0022-4375(03)00033-1
Green, R. G., Muir, H., James, M., Gradwell, D., & Green, R. L. (1996). Human Factors For Pilots (2nd ed.), Ashgate, England.
Harris, D. (2011). Human Performance on the Flight Deck. Ashgate, England.
Hawkins, F.H. (1993). Fatigue, Body Rhythms and Sleep. In H.W. Orlady (Eds.), Human Factors in Flight (2nd ed., pp. 56-83). Ashgate.
Heywood, B. (1999). Pilot Fatigue and the Limits of Endurance, Flight Safety Australia (1999, April). Retrieved from: https://skybrary.aero/sites/default/files/bookshelf/1080.pdf.
Hursh, S. R., Balkin, T. J., Miller, J. C., & Eddy, D. R. (2004). The fatigue avoidance scheduling tool: Modeling to minimize the effects of fatigue on cognitive performance. SAE transactions, 111-119.
InterDynamics (n.d.). FAID® Quantum Version 1.1 User Guide.
International Civil Aviation Organization (2020). Manual for the Oversight of Fatigue Management Approaches (Doc 9966).
Li, P. C., Wang, Y. X., Chen, J. H., Luo, Z. H., Dai, L. C. (2021). An experimental study on the effects of task complexity and knowledge and experience level on SA, TSA and workload. Nuclear engineering and design, 376, 111112. doi: 10.1016/j.nucengdes.2021.111112
Liu, C-C., Wang, C-Y., Shih, H-C., Wu, J. J-K., Huang, C-I., Hsu, H-S., Huang, M-H., Huang, M-H., Huang, M-S. (2009). Prognostic factors for mortality following falls from height. Injury, International Journal of the Care of the Injured, 40 (2009) 595–597.
Mallis, M., Banks, S., Dorrian, J., & Dinges, D. F. (2022). Aircrew fatigue, sleep need, and circadian rhythmicity. In Keebler, J.R., Wilson, K.A., Lazzara, K.H., & Blickensderfer, E.L. (eds) Human Factors in Aviation and Aerospace (pp. 309-339). Academic Press.
National Aeronautics and Space Administration (2010). Human Integration Design Handbook (HIDH). Retrieved from: https://www.nasa.gov/sites/default/files/atoms/files/human_integration_design_handbook_revision_1.pdf
National Transportation Safety Board (1980). General Aviation Accidents: Postcrash Fires and How to Prevent or Control Them (NTSB-AAS-80-02).
National Transportation Safety Board (2014). Special Investigation Report on the Safety of Agricultural Aircraft Operations (NTSB/SIR-14/01). Retrieved from: https://www.ntsb.gov/safety/safety-studies/Documents/SIR1401.pdf
Orlady, H.W., & Orlady, L.M. (1999). Human Factors in Multi-Crew Flight Operations. Ashgate, England.
Papadimitriou-Olivgeris, M., Panteli, E., Koutsileou, K., Boulovana, M., Zotou, A., Marangos, M., Fligou, F. (2021). Predictors of mortality of trauma patients admitted to the ICU: a retrospective observational study. Brazilian Journal of Anesthesiology, 71 (2021) 23-30.
Perrella, W.M. Jr. (1978), Tests of Crash-Resistant Fuel System for General Aviation Aircraft, (FAA-RD-78-28), interim report prepared for the US Department of Transportation, Federal Aviation Administration.
Petrilli, R.M.A., Roach, G.D., Dawson, D., & Lamond, N. (2007). The sleep, subjective fatigue, and sustained attention of commercial airline pilots during an international pattern. Chronobiology International, 23(6): 1347–1362. doi: 10.1080/07420520601085925
Riethmeister, V., Matthews, R. W., Dawson, D., de Boer, M. R., Brouwer, S., & Bültmann, U. (2019). Time-of-day and days-on-shift predict increased fatigue over two-week offshore day-shifts. Applied ergonomics, 78, 157-163. doi: 10.1016/j.apergo.2019.02.010
Roach, G.D., Petrilli, R.M.A., Dawson, D., & Lamond, N. (2012). Impact of layover length on sleep, subjective fatigue levels, and sustained attention of long-haul airline pilots. Chronobiology International, 29(5): 580–586. doi: 10.3109/07420528.2012.675022
Rosa, E., Eiken, O., Grönkvist, M., Kölegård, R., Dahlström, N., Knez, I., ... & Willander, J. (2020). Effects of fatigue on cognitive performance in long-duration simulated flight missions. Aviation Psychology and Applied Human Factors, 10(2), 82. doi: 10.1027/2192-0923/a000191
Skybrary (2010). Workload (OGHFA BN). Skybrary. Retrieved from: https://www.skybrary.aero/index.php/Workload_(OGHFA_BN)
Tran, Y., Craig, A., Craig, R., Chai, R., & Nguyen, H. (2020). Psychophysiology 57(5), e13554-n/a. doi: 10.1111/psyp.13554
Transportation Safety Board of Canada (2006). Post-impact fires resulting from small-aircraft accidents, (SII A05-01).
Tucker, A. (2015). JHC Commanders’ Guide to Fatigue Management. Retrieved from: https://www.aviation.govt.nz/assets/licensing-and-certification/medical/jhc-commanders-guide-to-fatigue-management.pdf
Submissions
Under section 26 of the Transport Safety Investigation Act 2003, the ATSB may provide a draft report, on a confidential basis, to any person whom the ATSB considers appropriate. That section allows a person receiving a draft report to make submissions to the ATSB about the draft report.
A draft of this report was provided to the following directly involved parties:
- the aircraft operator
- the aircraft maintainer
- Civil Aviation Safety Authority
- US National Transportation Safety Board
- Transportation Safety Board of Canada
- Pratt & Whitney Canada
- US Federal Aviation Administration
- Air Tractor Incorporated
- Satloc.
Submissions were received from;
- the aircraft operator
- the aircraft maintainer
- Civil Aviation Safety Authority
- US National Transportation Safety Board
- US Federal Aviation Administration
- Pratt & Whitney Canada
- Transportation Safety Board of Canada
- Air Tractor Incorporated
- Satloc.
The submissions were reviewed and, where considered appropriate, the text of the report was amended accordingly.
Appendix A – Hoerner wingtips
Hoerner wing tips Hoerner wing tips were designed to increase wing efficiency, by increasing the effective wing span beyond the actual length of the wing. Effects of this include reduced stalling speed and improved take-off performance. Hoerner wing tips were not an option for AT-400 aircraft, however, in subsequent Air Tractor models, they were either factory-fitted or offered as a post-factory modification. From Air Tractor regarding the AT-402B: ‘We designed a long, high-aspect ratio wing with Hoerner wing tips to increase wing efficiency, reduce drag and to lower stick and rudder forces so the controls are light and responsive, greatly reducing pilot fatigue.’ |
Appendix B – Post-impact fire mortality
Survivable w/out fire | Impact or Fire fatality | Reference | Injury Level | Aerial Application | Injury/death due to fire | Fatalities | Serious Injuries | Minor Injuries | Fuel Tank type |
Yes | Nil injury. Self–extricated | OA2012-00151 | Nil | 0 | 0 | 0 | Rigid | ||
No | Impact then fire | OA2012-00374 | Fatal | 2 | 0 | 0 | Rigid | ||
No | Impact | OA2012-02789 | Fatal | 1 | 0 | 0 | Integral | ||
No | Impact. Restraint compromised | OA2012-03602 | Fatal | Y | 1 | 0 | 0 | Rigid | |
No | Impact | OA2012-04925 | Fatal | 1 | 0 | 0 | Rigid | ||
No | Probably impact | OA2012-05096 | Fatal | 1 | 0 | 0 | Integral | ||
Yes | Impact and fire. 1 not wearing full restraint | OA2012-10258 | Fatal | 1 | 1 | 1 | Rigid | ||
No | Impact | OA2012-10597 | Fatal |
|
2 | 0 | 0 | Integral | |
Yes | Unknown cause of injury | OA2012-12080 | Serious | 0 | 1 | 0 | Rigid | ||
Probably not | Unknown, probably not survivable | OA2012-12087 | Fatal | 1 | 0 | 0 | Bladder | ||
Yes | Fire | OA2013-08649 | 1 | 1 | 0 | 0 | Integral | ||
No | Impact and fire. Skull fractures | OA2013-08772 | Fatal | * | 1 | 0 | 0 | Integral | |
No | Impact then bushfire | OA2013-09598 | Fatal | 1 | 0 | 0 | Integral | ||
No | Impact then fire | OA2013-09679 | 2 | 0 | 0 | Integral | |||
Yes – increased severity | Fire | OA2013-11507 | 2 fire-related serious injuries | 0 | 2 | 0 | Integral | ||
No | Impact then fire | OA2014-00990 | 1 | 0 | 0 | Integral | |||
Yes | Fire (pilot), 4 parachutists inadequately restrained – impact | OA2014-01533 | Fatal | 1 | 5 | 0 | 0 | Integral | |
Yes – increased severity | Fire increased severity | OA2014-01743 | Serious | 2 increased severity | 0 | 2 | 0 | Integral | |
Yes | Fire | OA2014-04896 | Fatal | 1 | 1 | 1 | 1 | Integral | |
No | Impact |
OA2014-07632
|
Fatal | 1 | 0 | 0 | Integral | ||
Probably not | Impact (including skull fractures) and fire | OA2015-01029 | Fatal | Y | * | 1 | 0 | 0 | Rigid |
Probably not | Impact then fire | OA2015-03021 | Fatal | 1 | 0 | 0 | Rigid | ||
No | Impact | OA2015-04887 | Fatal | 1 | 0 | 0 | Integral | ||
Yes | Nil. Evacuated. | OA2016-02270 | Nil | Y | 0 | 0 | 0 | Integral | |
Yes | Fire. Injuries would have prevented extraction | OA2016-04006 | Fatal | Y | 1 | 1 | 0 | 0 | Integral |
No | Unknown. Impact unlikely to be survivable | OA2016-04457 | Fatal | Y | 1 | 0 | 0 | Integral | |
No | Impact | OA2017-00686 | Fatal | 5 | 0 | 0 | Bladder | ||
Yes | Evacuated before fire | OA2017-04954 | Minor | 0 | 0 | 1 | Rigid | ||
Yes | Unknown. Evacuated | OA2018-01892 | Minor | 0 | 0 | 1 | Integral | ||
Yes | Unknown. Pilot extracted self and instructor | OA2018-02254 | Serious | 0 | 2 | 0 | Integral | ||
No | Impact then fire | OA2018-02773 | Fatal | 1 | 0 | 0 | Integral | ||
Yes | Nil | OA2020-03747 | Nil | 0 | 0 | 0 | Integral | ||
Yes | Impact – pilot ejected | OA2020-05449 | Serious | 0 | 1 | 0 | Integral | ||
Yes | Fire | OA2021-05331 | Fatal | Y | 1 | 1 | 0 | 0 | Integral |
34 | 6 | *Head injuries increase mortality | 35 | 10 | 4 |
Purpose of safety investigationsThe objective of a safety investigation is to enhance transport safety. This is done through:
It is not a function of the ATSB to apportion blame or provide a means for determining liability. At the same time, an investigation report must include factual material of sufficient weight to support the analysis and findings. At all times the ATSB endeavours to balance the use of material that could imply adverse comment with the need to properly explain what happened, and why, in a fair and unbiased manner. The ATSB does not investigate for the purpose of taking administrative, regulatory or criminal action. TerminologyAn explanation of terminology used in ATSB investigation reports is available here. This includes terms such as occurrence, contributing factor, other factor that increased risk, and safety issue. Publishing informationReleased in accordance with section 25 of the Transport Safety Investigation Act 2003 Published by: Australian Transport Safety Bureau © Commonwealth of Australia 2023 Ownership of intellectual property rights in this publication Unless otherwise noted, copyright (and any other intellectual property rights, if any) in this report publication is owned by the Commonwealth of Australia. Creative Commons licence With the exception of the Coat of Arms, ATSB logo, and photos and graphics in which a third party holds copyright, this publication is licensed under a Creative Commons Attribution 3.0 Australia licence. Creative Commons Attribution 3.0 Australia Licence is a standard form licence agreement that allows you to copy, distribute, transmit and adapt this publication provided that you attribute the work. The ATSB’s preference is that you attribute this publication (and any material sourced from it) using the following wording: Source: Australian Transport Safety Bureau Copyright in material obtained from other agencies, private individuals or organisations, belongs to those agencies, individuals or organisations. Where you wish to use their material, you will need to contact them directly. |
[1] Eastern Daylight-saving Time (EDT): Coordinated Universal Time (UTC) + 11 hours.
[2] Aerial spraying is one type of aerial application operation.
[3] Accepted by NSW Environment Protection Authority, this accreditation for pilots requires demonstrated knowledge of the ‘Spraysafe Manual’, prepared by the University of Queensland’s Centre for Pesticide Application and Safety.
[4] Emergency dump or jettison is an essential part of emergency procedures for aircraft operating with a hopper load. The procedure releases the entire hopper contents from the aircraft within a few seconds.
[5] Wing loading is the aircraft weight divided by the wing area. The take-off weight of the AT-400 divided by the wing area is greater than that of the AT-502.
[6] The Civil Aviation Orders that permitted foreign aeroplanes certified in the Agricultural Category were repealed in 1998 and those aircraft were then operated in the Restricted Category. Restricted category aircraft are limited to operate and carry personnel only for specified purpose/s.
[7] The Type Certificate Data Sheet includes general information about the design (dimensions, wing loading, limiting airspeeds), required placards and markings, control surface travel, engine installations and, where applicable, approved engine/propeller combinations. (Source: Skybrary)
[8] A Flight Manual is a manual, associated with the Certificate of Airworthiness, containing limitations within which the aircraft is to be considered airworthy, and instructions and information necessary to the flight crew members for the safe operation of the aircraft. (Source: Skybrary)
[9] Information about Graphical Area Forecasts is available on the Bureau of Meteorology website.
[10] The Bureau of Meteorology described a dust devil as: a localised dust filled vortex similar in shape to a tornado but of much less strength…They form due to intense heating at the surface causing a rapid upward movement of parcel of air. This displacement of the surface air causes an inward movement of surrounding air, creating the common spiral shape of the dust devil. Dust devils are generally small in size compared with tornadoes, being about 3-100 m in diameter and up to 300 m high. Wind speeds inside the vortex reach a maximum of 100km/hr.
[11] Information about aerodrome forecasts is available on the Bureau of Meteorology website.
[12] CAVOK: visibility of 10 km or more, no cloud below 5,000 ft, no cumulonimbus or towering cumulus and no significant weather.
[13] Load factor or G (force) is conventionally defined as the lift divided by the weight. Pilot control inputs and external factors particularly wind gusts (turbulence) affect the load factor.
[14] The Samn-Perelli 7-point scale asks people to rate their fatigue right now: 1 = fully alert, wide awake; 2 = very lively, responsive, but not at peak; 3 = okay, somewhat fresh; 4 = a little tired, less than fresh; 5 = moderately tired, let down; 6 = extremely tired, very difficult to concentrate; 7 = completely exhausted, unable to function effectively.
[15] 24-hour internal clock in our brain that regulates cycles of alertness and sleepiness by responding to light changes in our environment.
[16] Longeron: a longitudinal structural component of an aircraft's fuselage.
[17] The dynamic loading applied to a person or object in an accident is complex, unknown and varies for different locations throughout the aircraft. For analysis purposes, simplified assumptions are made about the shape of the deceleration pulse over the entire impact (acceleration versus time). Typical assumptions are triangular, trapezoidal, sinusoidal or square.
[18] A mist is very small liquid droplets in a gas. When the droplets are very small, the droplet surface area to volume ratio is very large. The intensity of the fire is dependent on the surface area of fuel. Therefore, for fine mists, the rate of combustion is very high, and produces a very intense fire.
[19] Strain: change in length per unit length
[20] Elastomer: a natural or synthetic polymer with elastic properties.