What happened
On 4 November 2021, a Boeing B737-36E SF, registered ZK-FXK, was being operated on a scheduled freight flight from Darwin, Northern Territory, to Brisbane, Queensland. After take-off, the flight crew observed that the aircraft did not pressurise as expected and the indicated cabin altitude was climbing much quicker than normal.
As the cabin altitude kept increasing, the crew stopped the aircraft’s climb at 11,000 ft and soon after commenced descent to 10,000 ft. As the aircraft passed 10,300 ft on descent, a cabin altitude warning alert occurred. The crew completed the required checklist actions but were unable to establish control of the pressurisation. Subsequently, the equipment cooling fan failed, the electronic flight information system reverted to a monochrome display output, and the weather radar failed.
The crew decided to return to Darwin. On arrival they identified that the guarded cargo/depress switch was on. This switch was normally only used in the event of a main cargo deck smoke event, when it will depressurise the aircraft to assist smoke removal. Switching this off returned the aircraft to serviceability.
What the ATSB found
The ATSB found that the cargo/depress switch had been turned on by the engineer as a means to cool the flight deck during pre-flight preparation. However, the engineer had omitted to turn it off prior to completing their duties, which prevented the aircraft from pressurising. Using the cargo/depress switch in this manner was not authorised but it had become normalised by the operator’s staff in Darwin, who were not aware that this practice would not be effective on the B737-36E SF aircraft in their fleet.
Although the cargo conversion operations manual supplement required the switch to be checked, this information was not incorporated into the operator’s flight crew operating manual, nor was the supplement information otherwise available to the flight crew. As a result, the crew did not identify that the switch was on during pre-flight activities. The operator also did not provide sufficient training during the introduction of the B737-36E SF to its fleet to ensure its personnel understood the differences of these aircraft to the rest of their B737 fleet.
The flight crew were accustomed to checking pressurisation after take-off to ensure the aircraft was pressurising as expected. As a result, the flight crew identified the pressurisation problem early, which enabled prompt action and prevention of a more serious incident.
What has been done as a result
The operator issued communications to its staff to immediately cease the unauthorised practice and remind staff to only operate equipment in accordance with approved documentation. Additionally, they commenced a review of operational documentation and completed incorporating the requirements of the operations manual supplement.
The operator also commenced a review of its training and aircraft induction processes to ensure sufficient staff and documentation were available to conduct support these processes.
Safety message
This incident highlights the risks associated with undertaking unauthorised practices and using equipment in a manner other than for its intended purpose. Without formal assessment of its efficacy or its potential for unintended consequences, combined with no documentation or training, there is no assurance that an unauthorised practice would be carried out consistently or safely.
This incident also demonstrated how essential training and up-to-date documentation is in ensuring correct understanding and operation of an aircraft.
The occurrence
On 4 November 2021, a Boeing B737-36E SF, registered ZK-FXK and operated by Airwork Flight Operations, was scheduled for a freight flight from Darwin, Northern Territory, to Brisbane, Queensland. The aircraft was crewed by 2 pilots.
The engineer assigned to prepare the aircraft commenced their tasks at about 1615 local time. The flight crew arrived at about 1630. At this time, the engineer was inside the flight deck conducting their pre-flight procedures but vacated to allow the crew to commence their aircraft preparation. The first officer commenced pre-flight procedures inside the flight deck and the captain commenced the external inspection. No anomalies were identified with the aircraft or its systems.
The aircraft departed Darwin at about 1754. Following the after take-off checks, the flight crew identified that the aircraft was not pressurising as expected. They noted that the cabin pressure differential[1] was lower than normal and that the cabin altitude was increasing at a higher than expected rate of 2,000 ft/minute.
The crew monitored the pressurisation and, as the aircraft was nearing 10,000 ft, noted the cabin altitude was about 8,000 ft and increasing. (Above cabin altitudes of 10,000 ft, flight crew are required to use supplemental oxygen to avoid the possibility of hypoxia.)
The crew attempted contact with air traffic control in order to stop the aircraft’s climb at 10,000 ft, but they were unable to due to radio congestion. After contact was made, the controller cleared the crew to stop the climb at flight level (FL)[2] 110, and subsequently to descend to 10,000 ft. The cabin altitude was below 10,000 ft at this stage, but still climbing.
At about 1800, while passing 10,300 ft on descent, a cabin altitude warning occurred. The alert consisted of the master caution light and a warning horn, and indicated that the cabin altitude was above 10,000 ft. The crew commenced the required immediate actions in response to this warning, which included the use of supplemental oxygen. However, very soon after the aircraft reached 10,000 ft, at which time supplemental oxygen was no longer required.
The cabin altitude warning checklist required changing the pressurisation mode to manual and selecting the outflow valve to fully closed.[3] The crew recalled that the outflow valve was already closed and completing the checklist actions did not establish positive control of the pressurisation.
At about this time, the master caution alert on the overhead panel presented. Looking at the overhead panel, the crew identified the equipment cooling fan(s) had failed. The crew selected the alternate fans in accordance with the quick reference handbook (QRH) procedure, but this did not restore the operation of the equipment cooling fans. Subsequently, the electronic flight information system (EFIS) reverted to monochrome display output, which was a system design feature to reduce heat output.
A short time later the weather radar also failed. The crew stated that, although they were visual at the time, there were thunderstorms in the area, for which the weather radar was a required system. With numerous systems malfunctioning, the crew decided to return to Darwin. The crew conducted a normal approach and landed at 1915.
After shutting down the aircraft, the captain moved to the jump seat to complete the post-flight log. In the darker ambient conditions compared to departure, the captain noticed an unexpected amber light on the aft overhead panel. The light was from the guarded cargo/depress switch, indicating it was in the ON position. The flight crew realised that this was the reason why the aircraft did not pressurise, as the switch was normally only used in the event of smoke in the main cargo deck.[4]
The crew discussed the occurrence with the engineer, who advised that they had selected the cargo/depress switch to ON with the intention of cooling airflow into the flightdeck while the aircraft was on the ground. The engineer stated they had omitted to select the switch off prior to completing their duties, nor had they informed the crew of the switch selection.
After turning the switch off, the aircraft was considered serviceable, and it was operated on its freight service. The systems malfunctions did not occur again nor was there any further incident.
Context
Personnel information
Captain
The captain held an Air Transport Pilot Licence (Aeroplane) and Class 1 aviation medical certificate. They had flown for the operator for about 4 years and had previously flown the B737 for 2 other airlines. The captain had also flown a variety of aircraft with regular public transport, charter and general aviation operators. They had 12,150 flight hours in total, with 3,500 hours on B737 aircraft.
First officer
The first officer (FO) held an Air Transport Pilot Licence (Aeroplane) and a Class 1 aviation medical certificate. They had been at the operator for about 1 year on the B737 but had also flown the B737 for other operators in Australia and overseas. Their previous experience included various aircraft types in regular public transport and regional operations. The FO had 17,300 flight hours in total, with 13,000 hours on B737 aircraft.
Engineer
The engineer was a licensed aircraft maintenance engineer with over 30 years' experience maintaining B737 aircraft. The engineer stated that they had only maintained B737 aircraft but had also held a maintenance manager’s position prior to commencing at the operator about 4 months prior to the occurrence.
Aircraft information
General
ZK-FXK was a Boeing B737-36E Special Freighter (SF) aircraft. It was manufactured in 1991 as a passenger aircraft with serial number 25256. It was then modified for freight operations in 2004 by Israel Aircraft Industries Limited (IAI). The aircraft was acquired by the operator in 2019.
Cargo/depress switch
The cargo/depress switch was part of the main deck smoke detection system. It was on the main deck cargo smoke detector panel, which was located on the aft overhead panel of the flight deck (Figure 1, Figure 2). The panel was located behind the flight crew seats and was not within normal line of sight for a flight crew.
Figure 1: Main deck cargo smoke detector panel
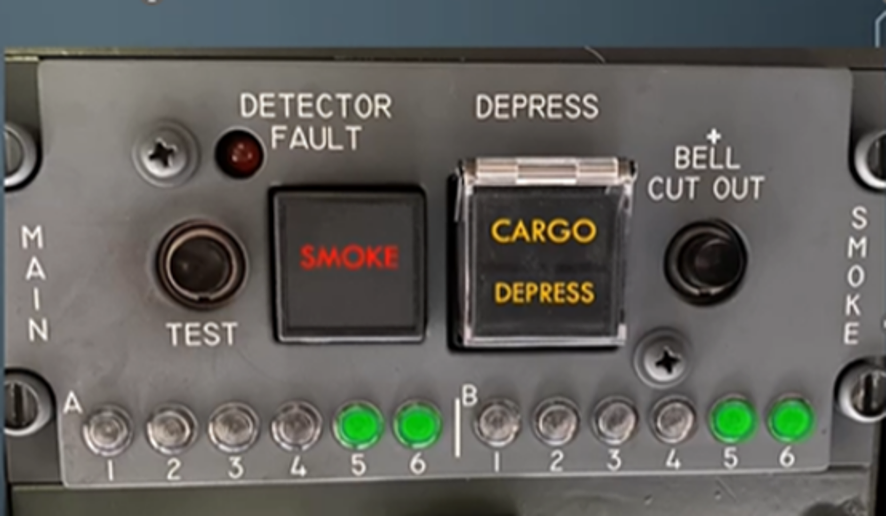
Source: Airwork
The cargo/depress switch was a push-button type switch that illuminated when selected ON. It was guarded by a clear, flat plastic cover. The switch could be on or off with the guard in place (Figure 2). This was in contrast to other guarded switches on the aircraft, where the guard had to remain raised to allow the toggle type switch to be on. The only indication that the switch had been selected ON was the illumination of the switch itself.
Figure 2: Main deck cargo smoke detector panel (view from left seat)
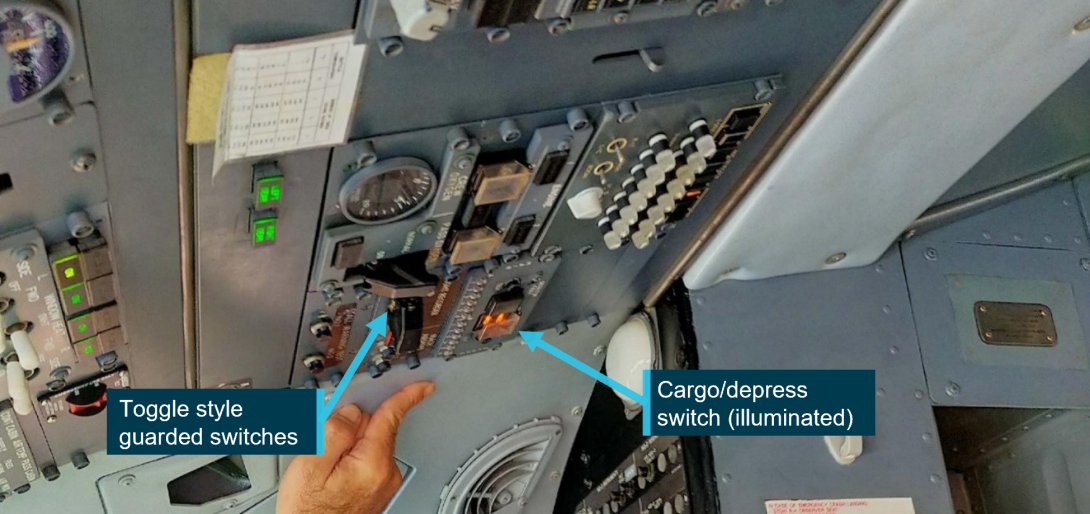
Source: Captain of ZK-FXK, modified by the ATSB
The only situation for which the switch was to be used was if smoke was detected within the main cargo deck. The flight crew operating manual (FCOM) stated that when the switch was:
Depressed:
Will depressurize aircraft and provide limited ventilation to flight deck.
- closes right and left main deck airflow shutoff valves
- right pack valve closes
- left pack valve closes to low flow (15-18% of normal output)
- R/H flow control valve will be closed
- forward outflow valve opens
The main deck cargo smoke, fire or fumes checklist further explained that:
Selecting this switch will depressurize the airplane and provides restricted heat and ventilation for exclusion of fumes and smoke from the cockpit.
As the aircraft departed with the cargo/depress switch on, ZK-FXK was prevented from pressurising.
No problems were identified with the weather radar or electronic flight information system (EFIS). Changes to the status of these systems during the flight was consistent with them being exposed to increased heat due to the cooling fan failure. The quick reference handbook explains that a cooling fan failure may be an indicator of a cabin pressurisation problem.
Operational manual supplement
An operational manual supplement (OMS) was produced by IAI to reflect all changes to the configuration and operation of the aircraft following its conversion from a passenger aircraft to a freighter. The OMS included a requirement that some of its pages must be inserted into the FCOM adjacent to their respective pages. This was to ensure the FCOM was fully amended with the latest information and procedures.
The operational manual supplement stated:
Depressing this switch will depressurize the aircraft to minimize airflow to the main cabin. The following valves will be activated.
- both left and right air condition shutoff valves will close
- right pack control flow valve will close
- left pack control flow valve will drive to low flow
- forward outflow valve will drive to open
In the preliminary flight deck preparation section of the normal procedures, the OMS required the main deck cargo smoke detector control panel to be checked as follows:
Main deck cargo smoke detector control panel – check
Check detector lights (12) – extinguished
Check detector fault light – extinguished
Check smoke light – extinguished
Main smoke no flow light – extinguished
Check depress switch, normal extinguished position, plastic cover stowed.
Both pilots stated that, after identifying the incorrect switch position on return to Darwin, they reviewed the FCOM and noted that it did not include any reference to pre-flight check requirements for the panel. During interview, the FO stated they were not aware of the OMS requirement and therefore they did not check the panel or switch during their pre-flight checks.
The ATSB reviewed the FCOM and confirmed that it had not been amended with the changes to the pre-flight procedures for checking the cargo/depress switch, as required by the OMS.
Flight crew pre-flight procedures
The FO conducted the flight deck preparation at the same time as the captain conducted the external inspection. The FO recalled that, while they were seated in the jump seat, they had looked at the overhead panel. However, rather than looking vertically up at where the cargo/depress switch was located, they looked across the panel at eye level, paying specific attention to various switches for correct positions. They described Boeing switches as being toggle types, all operating in the same direction to easily identify if they were on or off.
The FO stated that during this scan, in the bright ambient conditions, they did not notice that the cargo/depress switch was illuminated. As the clear plastic guard was able to be closed when the switch was on, and as this was different to the guard on the toggle type switches, the ability to visually determine its state was reduced. The FO recalled that at no stage was the main deck cargo smoke detector panel specifically checked. Following this activity, the FO continued the next section of pre-flight scans from their FO seat on the right side of the flight deck. From this seat, the cargo/depress switch was now behind their head and out of view.
When returning to the flight deck after the external inspection, the captain did not notice that the cargo/depress switch was on, nor were they required to check that panel. Both pilots mentioned conducting the light test to determine if lights were functional on the front, lower console and overhead panels. This test illuminated all lights but was not able to assist the pilots in visually identifying that the cargo/depress switch was on.
Prior to taxiing, the crew conducted the recall check of the master caution system annunciator panel during the before taxi checklist.[5] They also conducted this check again while attempting to establish the reason for the aircraft not pressurising. They received no alerts at those times. The crew and operator later identified that the cargo/depress switch was not connected to this system. This was not the crew’s expectation, given what systems the cargo/depress switch would affect and that it was outside of their normal line of sight.
The captain stated that the only training they received on ZK-FXK’s differences to the operator’s other B737 aircraft was related to operation of the main deck cargo door.
Cooling the flight deck
The engineer arrived at the aircraft about 1.5 hours prior to the scheduled departure time of 1745 to prepare the aircraft. They noted it was a very hot day and the aircraft interior had also become quite hot as a result. After turning the air conditioning on, the engineer then selected the cargo/depress switch to ON. The aircraft operator did not supply ground support equipment (GSE) capable of providing external air-conditioning.
At that time, the engineer believed that selecting the cargo/depress switch to ON would shut off airflow to the main deck and increase airflow to the flight deck to accelerate cooling there. The engineer stated that using the cargo/depress switch on the ground for cooling was not a documented procedure. They had learned to do this practice in Darwin from other engineers but had also seen some pilots do it. The engineer explained that they had not received any formal training on the differences between the operator’s 737 aircraft when they commenced employment with the operator.
The engineer explained that they would normally select this switch to ON, complete their aircraft preparation duties, then turn the switch to OFF prior to leaving the aircraft. On this occasion, the engineer felt that they needed to vacate the flight deck when the flight crew arrived earlier than expected. In doing so, they forgot to turn the switch off.
The operator identified that the same practice of cooling the flightdeck was used on all of their B737 aircraft by the engineers at Darwin.
Operator’s other 737 aircraft
The operator had 14 B737 freighter aircraft:
- 12 aircraft that had been modified by Aeronautical Engineers, Inc (AEI)
- 2 aircraft that had been modified by IAI (including ZK-FXK).
The AEI-modified aircraft were also fitted with a smoke detection system for the main cargo deck, however that system operated differently from that on the IAI-modified aircraft like ZK-FXK. On the AEI-modified aircraft, there was a cabin air shut-off switch that, when selected on, worked like the system on ZK-FXK to shut off air to the main deck, but it differed from ZK-FXK in that this system did not restrict air flow to the flight deck. Instead, all airflow was redirected to the flight deck to exclude smoke from the flight deck via positive pressure. This switch to control this system was the guarded toggle type and in the same position on the aft overhead panel as the cargo/depress switch on ZK-FXK.
Both pilots stated that the FCOM for the AEI-modified aircraft included a pre-flight operational check of the cabin air shut-off switch. The FO explained that the check required the guard to be lifted and the switch turned on to check the system operation. They explained there would be a very noticeable increase in air flow into the flight deck. The switch was then turned off and the guard closed.
The captain noted that the flow of air into the flight deck of the AEI-modified aircraft was significant to the point of distracting, and they would switch the system off if it was on. They did not notice any such air flow in ZK-FXK.
Pressurisation monitoring
The FCOM did not require that the aircraft pressurisation (cabin altitude and cabin pressure differential) be checked during flight. However, the FO stated they were in the habit of doing so due to experiences with B737 simulator instructors at a previous airline who would fail a student if they had not detected a pressurisation problem before the aircraft’s cabin altitude warning presented. The captain had a similar mindset with regard to checking the aircraft pressurisation.
It is likely that the cabin altitude warning would have presented while the aircraft was still climbing, however this did not occur because the flight crew had identified the pressurisation problem, monitored the cabin altitude, and then took action to avoid the cabin altitude rising above 10,000 ft.
Operator comments
The operator’s investigation report noted that the OMS for the IAI-modified aircraft was received by its maintenance control department when the aircraft was acquired. However, this manual was not provided to the engineering, flight operations or training departments prior to the aircraft entering service.
The report also identified that the training provided to flight crew was limited and focused on the operation of the main cargo door and escape slides. Engineers were not provided any formal training on the aircraft to identify the differences from other B737 aircraft in its fleet.
In summary, the operator identified that there were insufficient procedures as part of its aircraft induction process to ensure that all operational documentation was correctly distributed and that staffing deficiencies within the training department had impacted the oversight and delivery of training.
Safety analysis
Introduction
During pre-flight preparation, the engineer turned on the cargo/depress switch in an attempt to cool the flightdeck of ZK-FXK. The engineer omitted to turn the switch off prior to completing their duties and this was not identified by the flight crew. This prevented the aircraft from pressurising as expected and the cabin altitude subsequently rose above 10,000 ft.
The use of the cargo/depress switch in this manner was not authorised but had become normalised by the operator’s staff in Darwin.
The analysis will examine the issues related to unauthorised procedures and how documentation and training are essential for correct aircraft operations.
Normalised, unauthorised procedure
‘Normalisation of deviance’ was a process defined by Dianne Vaughan (1996) during the Space Shuttle Challenger investigation whereby unacceptable practices become accepted as the norm. The unacceptable practice is repeated without catastrophic results, reinforcing its normalisation.
Although the occurrence involving ZK-FXK did not have the same potential for a catastrophic outcome, it was an example of normalised deviance. The operator’s staff were using an aircraft system in a manner for which it was not designed (that is, using the cargo/depress switch on the ground). This practice was not authorised but had become accepted because of the perceived benefit of cooling the flight deck of its B737 aircraft in Darwin while working on the aircraft.
The engineer believed that in doing so they would be forcing air into flight deck but did not realise that this would not occur on ZK-FXK. It was identified that limited training on the B737-36E SF aircraft’s differences with the operator’s other type meant that operator’s staff were not aware that the desired result would not be achieved.
There was no evidence to suggest that anyone conducting this practice had undertaken a formal assessment of its efficacy or its potential for unintended consequences. The absence of formal documentation, procedures or training meant there was no assurance that the practice would be carried out consistently or safely. This was demonstrated by the engineer forgetting to deselect the switch, which is likely to have been a result of their normal routine being interrupted by the earlier than expected arrival of the flight crew. Lapses are common when interruptions occur and the absence of controls such as a documented procedure meant that the lapse was not recognised.
The absence of ground support equipment to provide external cooling appears to have instigated the unauthorised practice and it is likely that the practice may have continued given the frequently hot conditions in Darwin.
Aircraft documentation
Although the cargo conversion had taken place prior to the operator acquiring the aircraft, the operator did not ensure that all the aircraft documentation was adequately reviewed prior to entry into service. As a result, the flight crew operating manual (FCOM) had not been amended to include all changes detailed in the operational manual supplement (OMS), notably the requirement to check the main deck cargo smoke detector panel. The pilots were not aware of this requirement, thus removing a defence against the unauthorised use or incorrect position of the cargo/depress switch. Not checking the system also increased the risk of not detecting potential issues in the system.
The B737 is a very common aircraft but can be operated in various configurations which may differ between numerous operators. It is essential that aircraft documentation adequately reflect the correct aircraft configuration and procedures to prevent the aircraft being operated incorrectly.
Training on aircraft differences
Although the pilots had some training on the newly introduced aircraft, it was focused on the cargo door itself and not on all of the new procedures or systems following the cargo conversion. The engineer did not receive any formal training on the differences between the operator’s B737 aircraft. As such, the pilots and engineer were not provided with the opportunity to become fully aware of the aircraft they were required to operate.
In this occurrence, the limited training on aircraft differences reinforced the unauthorised use of the cargo/depress switch. Had the correct system knowledge been provided, it may have discouraged its use if it was known it would not work in the desired manner (at least on the B737-36E SF aircraft). The absence of training on required procedures also removed a defence against departure with an incorrect configuration.
Pilot vigilance
The pressurisation problem was identified early, enabled by the flight crew having developed the habit of monitoring pressurisation during their previous B737 experience. As the FCOM did not require a specific check of pressurisation during the after-take-off checks or climb phase, the pressurisation problem would still have triggered the cabin altitude warning albeit later in the climb. The crew’s heightened vigilance of pressurisation allowed them to identify and monitor the situation, take appropriate action promptly and thus avoid a more serious pressurisation incident.
Findings
ATSB investigation report findings focus on safety factors (that is, events and conditions that increase risk). Safety factors include ‘contributing factors’ and ‘other factors that increased risk’ (that is, factors that did not meet the definition of a contributing factor for this occurrence but were still considered important to include in the report for the purpose of increasing awareness and enhancing safety). In addition, ‘other findings’ may be included to provide important information about topics other than safety factors. Safety issues are highlighted in bold to emphasise their importance. A safety issue is a safety factor that (a) can reasonably be regarded as having the potential to adversely affect the safety of future operations, and (b) is a characteristic of an organisation or a system, rather than a characteristic of a specific individual, or characteristic of an operating environment at a specific point in time. These findings should not be read as apportioning blame or liability to any particular organisation or individual. |
From the evidence available, the following findings are made with respect to the incorrect configuration and cabin pressurisation issue involving the Boeing B737-36E SF, registered ZK-FXK, near Darwin Airport, Northern Territory, on 4 November 2021.
Contributing factors
- While preparing the aircraft for flight, the engineer selected the aircraft’s cargo/depress switch to ON then omitted to switch it off prior to leaving the aircraft.
- During their pre-flight activities, neither of the flight crew identified that the cargo/depress switch had been selected ON. Although the aircraft operational manual supplement required this switch to be checked, neither pilot was aware of this requirement.
- During the aircraft’s climb, the cargo/depress switch was in the ON position. This prevented the aircraft from pressurising as expected and the cabin altitude subsequently rose above 10,000 ft, triggering the cabin altitude warning.
- The aircraft system to be used in the event of a main deck cargo smoke event on the operator’s B737 fleet was being routinely used by the operator’s engineering personnel in Darwin as a means to cool the flight deck. This practice had become normalised as a result of the perceived benefit of doing so, but there were insufficient risk controls in place to ensure that the aircraft would be returned to the correct configuration prior to departure. (Safety issue)
- The operator did not provide sufficient training during the introduction of the B737-36E SF to its fleet to ensure its personnel understood the differences between these aircraft and the rest of its B737 fleet.
- The operator’s flight crew operating manual for the B737-36E SF aircraft had not been fully amended to incorporate all revisions as detailed in the cargo conversion operational manual supplement.
Other findings
- The flight crew were accustomed to checking cabin pressurisation during climb to ensure the aircraft was pressurising as expected. As a result, the flight crew identified the pressurisation problem involving ZK-FXK early, which enabled prompt action and prevention of a more serious incident.
Safety issues and actions
Depending on the level of risk of a safety issue, the extent of corrective action taken by the relevant organisation(s), or the desirability of directing a broad safety message to the aviation industry, the ATSB may issue a formal safety recommendation or safety advisory notice as part of the final report. All of the directly involved parties were provided with a draft report and invited to provide submissions. As part of that process, each organisation was asked to communicate what safety actions, if any, they had carried out or were planning to carry out in relation to each safety issue relevant to their organisation. Descriptions of each safety issue, and any associated safety recommendations, are detailed below. Click the link to read the full safety issue description, including the issue status and any safety action/s taken. Safety issues and actions are updated on this website when safety issue owners provide further information concerning the implementation of safety action. |
Normalised, unauthorised procedure
Safety issue number: AO-2021-047-SI-01
Safety issue description: The aircraft system to be used in the event of a main deck cargo smoke event on the operator’s B737 fleet was being routinely used by the operator’s engineering personnel in Darwin as a means to cool the flight deck. This practice had become normalised as a result of the perceived benefit of doing so, but there were insufficient risk controls in place to ensure that the aircraft would be returned to the correct configuration prior to departure.
Safety action not associated with an identified safety issue
Whether or not the ATSB identifies safety issues in the course of an investigation, relevant organisations may proactively initiate safety action in order to reduce their safety risk. All of the directly involved parties are invited to provide submissions to this draft report. As part of that process, each organisation is asked to communicate what safety actions, if any, they have carried out to reduce the risk associated with this type of occurrences in the future. The ATSB has so far been advised of the following proactive safety action in response to this occurrence. |
Additional safety action by Airwork Flight Operations Limited
Airwork advised that:
- A review of the B737-36E SF flight crew operations manual and quick reference handbook was completed to ensure full compliance with the operations manual supplement. Work was in progress to implement an application in conjunction with the flight crew’s electronic flight bag to allow aircraft specific tail number data to be provided immediately to crew.
- Training packages for both flight crew and engineering staff were developed, and a training manager/coordinator will be introduced to oversee flight operations and maintenance training.
- The aircraft induction process was reviewed, and an improved induction checklist was created to ensure data is transferred between engineering and flight operations.
Glossary
AEI Aeronautical Engineers, Incorporated
ATC Air traffic control
EFIS Electronic flight information system
FCOM Flight crew operations manual
FDR Flight data recorder
FL Flight level
FO First officer
GSE Ground support equipment
IAI Israel Aircraft Industries Limited
OMS Operations manual supplement
QRH Quick reference handbook
SF Special freighter
Sources and submissions
Sources of information
The sources of information during the investigation included the:
- the flight crew of ZK-FXK
- the engineer
- Airwork Flight Operations Limited (the operator).
References
Submissions
Under section 26 of the Transport Safety Investigation Act 2003, the ATSB may provide a draft report, on a confidential basis, to any person whom the ATSB considers appropriate. That section allows a person receiving a draft report to make submissions to the ATSB about the draft report.
A draft of this report was provided to the following directly involved parties:
- the flight crew of ZK-FXK
- the engineer
- Airwork Flight Operations Limited (the operator)
- the Civil Aviation Safety Authority
- the Civil Aviation Authority of New Zealand
- the Transport Accident Investigation Commission (New Zealand)
- the National Transportation Safety Board (United States of America).
Submissions were received from:
- the captain of ZK-FXK
- the engineer
- Airwork Flight Operations Limited.
The submissions were reviewed and, where considered appropriate, the text of the report was amended accordingly.
Purpose of safety investigationsThe objective of a safety investigation is to enhance transport safety. This is done through:
It is not a function of the ATSB to apportion blame or provide a means for determining liability. At the same time, an investigation report must include factual material of sufficient weight to support the analysis and findings. At all times the ATSB endeavours to balance the use of material that could imply adverse comment with the need to properly explain what happened, and why, in a fair and unbiased manner. The ATSB does not investigate for the purpose of taking administrative, regulatory or criminal action. TerminologyAn explanation of terminology used in ATSB investigation reports is available here. This includes terms such as occurrence, contributing factor, other factor that increased risk, and safety issue. Publishing informationReleased in accordance with section 25 of the Transport Safety Investigation Act 2003 Published by: Australian Transport Safety Bureau © Commonwealth of Australia 2023 Ownership of intellectual property rights in this publication Unless otherwise noted, copyright (and any other intellectual property rights, if any) in this report publication is owned by the Commonwealth of Australia. Creative Commons licence With the exception of the Coat of Arms, ATSB logo, and photos and graphics in which a third party holds copyright, this publication is licensed under a Creative Commons Attribution 3.0 Australia licence. Creative Commons Attribution 3.0 Australia Licence is a standard form licence agreement that allows you to copy, distribute, transmit and adapt this publication provided that you attribute the work. The ATSB’s preference is that you attribute this publication (and any material sourced from it) using the following wording: Source: Australian Transport Safety Bureau Copyright in material obtained from other agencies, private individuals or organisations, belongs to those agencies, individuals or organisations. Where you wish to use their material, you will need to contact them directly. |
[1] Cabin pressure differential was the difference between cabin pressure and atmospheric pressure.
[2] Flight level: at altitudes above 10,000 ft in Australia, an aircraft’s height above mean sea level is referred to as a flight level (FL). FL 110 equates to 11,000 ft.
[3] The normal mode for pressurisation is AUTO, whereby the system will automatically adjust the position of the outflow valve in order to modulate cabin pressure. Manual mode will give full control of the system to the flight crew.
[4] The passenger area of ZK-FXK’s cabin had been converted to a cargo compartment and was known as the main cargo deck.
[5] The recall check is used to verify if a master caution condition exists. Pushing the system annunciator panel will illuminate the appropriate system annunciator and master caution light. These systems will have their control/display panels out of the flight crew’s normal line of sight. If this occurs, the flight crew will be required to take further action to verify correct system operation.