Safety summary
What happened
On 29 June 2021, a NSW Trains XPT was operating passenger service run ST24, between Albury and Sydney in NSW. At around 1325, ST24 passed through a worksite (504.500 km) at approximately 100 km/h. At the time the train passed through the worksite, ongoing repairs required that a speed limit of 40 km/h should have been in place.
No injuries or damage resulted from the incident.
What the ATSB found
During the process of preparing the track to allow ST24 to run through the worksite, the Australian Rail Track Corporation (ARTC) Protection Officer (PO) did not impose the required 40 km/h temporary speed restriction when fulfilling the Track Occupancy Authority (TOA) that had been in place to protect the worksite from trains entering the area. The speed restriction should have been applied using the Condition Affecting the Network (CAN) process.
When it came time to fulfil the TOA, the PO was away from the worksite where the repairs occurred. They were removing protection at the Wagga Wagga end of the TOA while also completing tasks associated with fulfilling the TOA. The PO was likely distracted by performing these competing tasks and did not inform the ARTC Network Controller (NC) of the need to place a temporary speed restriction on the track.
After the TOA was fulfilled and train ST24 was permitted to run at track speed, the PO realised the omission but was unable to successfully make contact with the NC in time to prevent the train passing through the worksite. As the train neared, the PO was still trying to contact the NC and did not use emergency stop handsignals.
The PO was using a new electronic form (eTAP) and system to fulfil the TOA. It was the first time they had used this system to fulfil a TOA when there was a CAN warning required for a temporary speed restriction. During the TOA fulfilment, the PO incorrectly answered one of the assurance questions about whether there was a CAN and consequently, the NC was not advised of the need for a temporary speed restriction to be applied. The NC acted on the electronic message from the PO and fulfilled the TOA and allowed ST24 to run unrestricted. The eTAP system, used at Track Occupancy Authority (TOA) fulfilment, does not include a key safeworking requirement contained in the ARTC Network Rules for confirming and repeating back safety critical information prior to acting on it.
The initial training for this new system was delivered to the PO while they were a PO1 level, meaning they did not possess the technical competency to implement a TOA. The PO may not have absorbed the content of the training because they did not possess the technical competency at the time of delivery. The ARTC training was delivered to a group of POs, irrespective of their competence level. There was no evidence of a competence assessment being applied to the PO after the training to confirm their ability to use the new system.
What has been done as a result
ARTC has separated the training modules for eTAP to ensure the content delivered is specific to the competency levels of the trainees. ARTC will undertake a review of the relevant Rules and Procedures applicable to TOA Fulfilment being ANWT 304 and ANPR 701, including ANGE 204.
Safety message
When introducing new technology, training regimes should include competency assessments, and content tailored for the workers and their required application of the technology. Training should include practical use of the technology under different scenarios, and include managing foreseeable errors, to promote familiarisation and understanding.
The occurrence
An ARTC civil workgroup from Wagga Wagga was assigned a task to straight rail the redundant Shepherds siding on the Main South rail line between Bomen and Harefield (figure 1) in the Riverina region of NSW. This task involved welding the rails to remove the redundant switches that serviced the old siding. The work group, consisting of six civil team members, left Wagga Wagga at approximately 0730 and arrived at the worksite around 0830.
Figure 1: Shepherds Siding
Source: Google images
The work was delayed by the absence of a team of signal electricians who were required to dismantle the disused points. The signal electricians arrived on site at approximately 1000 and the work then proceeded.
At approximately 1149 that day, NSW Trains XPT passenger service ST24, departed Albury for a scheduled service to Sydney. At approximately 1307, ST24 arrived at Wagga Wagga on time and departed at approximately 1309.
Shortly after leaving Wagga Wagga, ST24 stopped for a short period of time waiting for authorisation to continue its journey. The delay was required to allow workers to move off the track ahead, at the worksite in Shepherds Siding (504.500 km). At this point, the work was not yet complete, and the rail had not been welded together. The rail was held together with a device called a Robel clamp, which holds each end of the unwelded rail in place and allows for the passage of rail traffic until the weld is completed.
The worksite was being protected using a Track Occupancy Authority (TOA) which excluded trains for a specified period. At approximately 1320, once the track was clear, the Protection Officer (PO) fulfilled the TOA and handed the track back to the Network Controller (NC), who then authorised ST24 to proceed on its journey towards Sydney.
Just after they fulfilled the TOA, the PO realised they had forgotten to place a Condition Affecting the Network (CAN) 40 km/h speed limit warning on the section of track through the worksite. The PO unsuccessfully attempted to contact the NC on the regular phone line to inform them of the error.
At approximately 1325, ST24 passed through the worksite at Shepherds Siding travelling at 100 km/h. The PO managed to contact the NC on the emergency phone line just as ST24 entered the worksite and requested the verbal CAN warning, reducing speed to 40 km/h, for all subsequent rail traffic. The PO was then stood down and transported to Wagga Wagga ARTC provisioning centre for mandatory drug and alcohol testing, returning negative results.
Context
Location and rail network information
Shepherds Siding was an intermediate siding attached to the single main line between the crossing loops of Bomen and Harefield, located between 504.234 km and 504.940 km (figure 2). The siding was being removed as it was no longer operational. The rail network at this location is a single line, bi-directional system, which allows trains to run in either direction under the authority of the engineered signal control system.
Figure 2: Incident location
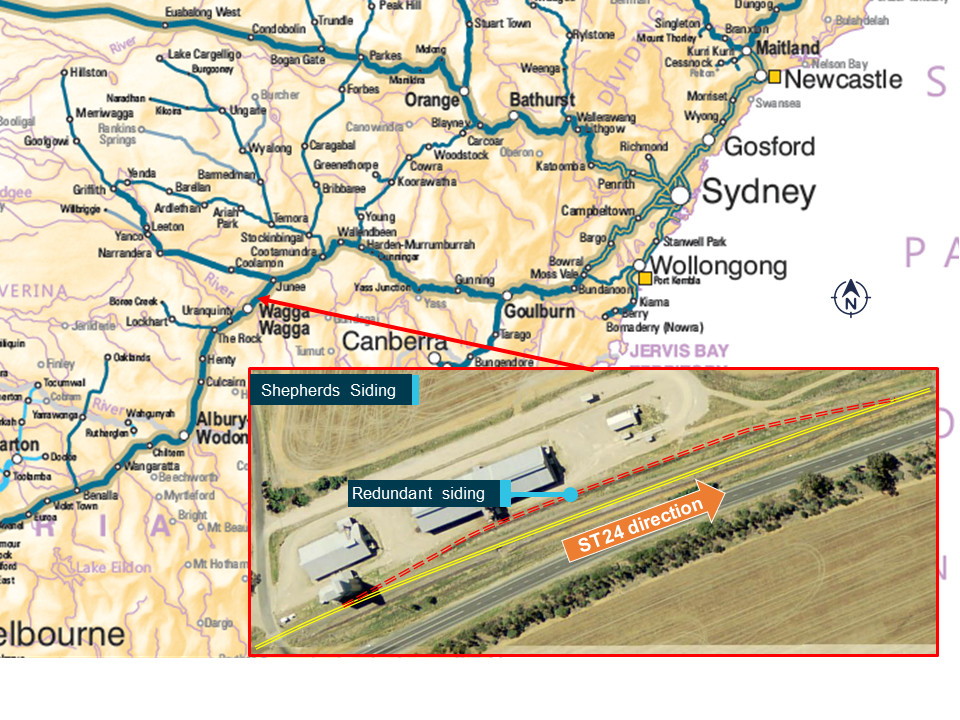
Source: Geoscience, annotated by OTSI
Environment
The Bureau of Meteorology showed the weather as recorded at Wagga Wagga (approximately 16 km from Shepherds Siding) was a minimum temperature of 4.7° C, and a maximum of 15.7° C. No rainfall was recorded in the 24-hour reporting period. Weather and environmental conditions were not considered a factor in this incident.
Parties Involved
NSW Trains
ST24 and the rest of the XPT fleet at the time of the incident were operated by NSW Trains, under the operating name of NSW TrainLink. NSW Trains was an agency of Transport for NSW[1].
Australian Rail Track Corporation (ARTC)
ARTC was a statutory corporation fully owned by the Government of Australia. ARTC was the Rail Infrastructure Manager (RIM) that manages the Main South rail line from Macarthur on the outskirts of Sydney to Melbourne. ARTC was an accredited operator and since September 2004 has held a 60-year lease of the interstate and Hunter Valley rail lines of NSW.
Trains were managed and controlled by ARTC Network Controllers at the Junee Control Centre, NSW.
eTAP
eTAP was a mobile device application designed as a tool for use by POs and Network Controllers to communicate safety critical information in the ARTC NSW Network. It was used to establish, monitor, and fulfill TOA, Look Out Working and Working in Corridor requests. The eTAP application replaced, to a large extent, the verbal exchange between the NC and the PO when applying for, authorising, and ending work on track.
The eTAP solution did not replace the need for verbal communication between the PO and NC when reporting or managing emergency conditions or CANs.
ARTC investigated engineering solutions to mitigate some of the error-inducing factors resulting from applying work on track rules and decided to trial the 4Tel / John Holland Rail Electronic Track Work (ETW) System to determine its suitability for roll out across the ARTC network.
The ETW application was originally designed by John Holland Rail (JHR) & 4Tel to assist Rail Safety Workers in their daily roles and ultimately, create safer outcomes on the NSW Country Regional Network (CRN).
The initial ARTC trial was undertaken between May and July 2018 on the section between Wolseley and Mile End in South Australia on the interstate rail corridor. This trial only focused on use for the application of TOAs.
Based on the success of the initial trial, the scope of the trial was extended to include the ARTC Hunter Valley network in August 2018. A risk assessment workshop was conducted in March 2019 to assess and validate the performance of the application.
The workshop had 23 participants, of which one was an active worker from an infrastructure team, a work group leader from Coffs Harbour. Other participants included four network controllers, and staff from various business areas including safety, IT and management.
Network rules and procedures
The relevant ARTC Network Rules and Procedures applicable to this incident are:
- ANWT 300 – Planning work in the rail corridor. This rule sets out the requirements for planning work in the rail corridor and assessing it for the necessary safety requirements.
- ANWT 304 – Track Occupancy Authority. This rule describes the requirements for authorising, issuing, managing and ending occupation of the track for a specified period to allow work to occur.
- ANPR 701 – Using a Track Occupancy Authority. This procedure describes the steps to take to authorise, issue, manage and end occupation of the track for a specified period in order allow work to occur.
- ANGE 206 – Condition Affecting the Network. This rule describes the requirements for reporting and responding to unsafe conditions on the rail network.
- ANGE 204 – Network Communication. This rule describes the universal requirements for spoken and written communication in the ARTC Network.
Robel clamp
A Robel rail clamp was a device used to link rail ends in a safe and secure manner until permanent connection by welding is complete (figure 3). The clamp was used by the civil workgroup at Shepherds Siding to temporarily secure the rail for the low speed, up to 80 km/hr, passage of rollingstock, prior to completion of permanent joining works.
Figure 3: Robel clamp
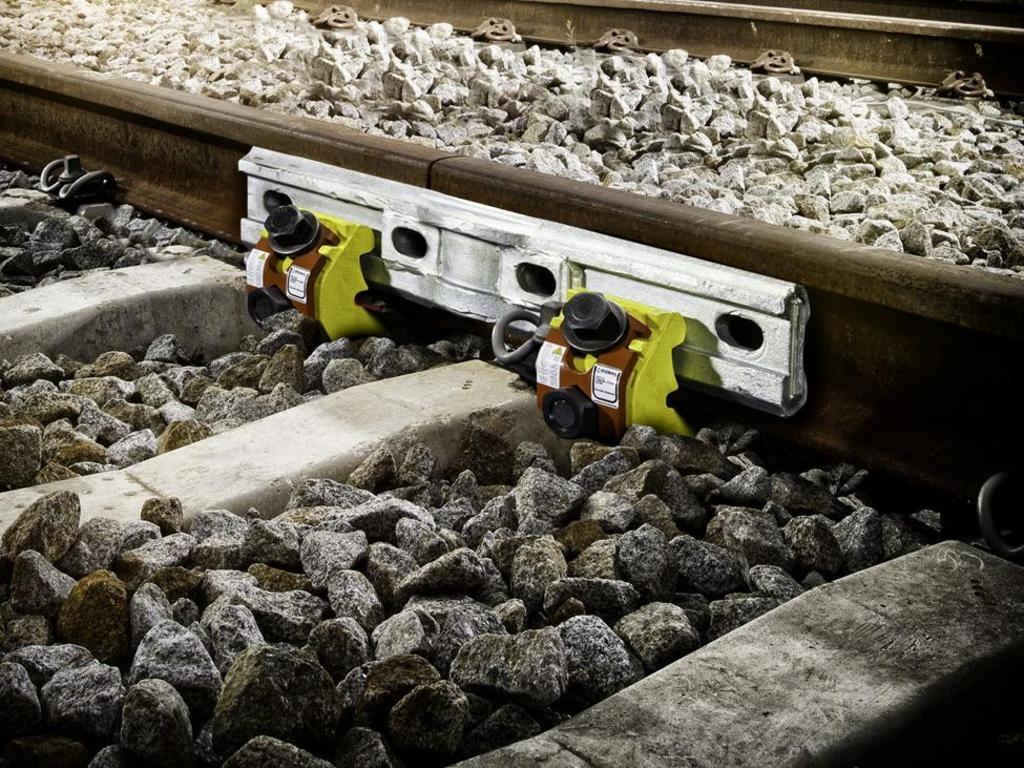
Source: Robel.com
Protection Officer
A PO1 is the base level of Protection Officer certification in a group of four certification levels from PO1 to PO4. As a PO moves through the grades, they are able to implement more complex methods of protection.
The PO involved in this incident had approximately two years of experience in that role. They had worked for 12 months as a PO1, followed by completing four months of supervised training before qualifying as a PO2. The PO had carried out a variety of protection work in this time.
The PO attended a briefing on the eTAP system in February 2020 that included the requirements for requesting, managing and fulfilling a TOA, but as a PO1 they were not authorised to implement this method of protection at the time. The PO received no further instruction on the application and learned its use on the job when promoted to a PO2.
The PO was removing protection for the southern end of the TOA at the time of fulfilling the TOA due to the make-up of the work group. The workers in the team were needed at the site for the task being performed, so the PO was absent from the worksite when the TOA was fulfilled.
Network Controller
The NC at the Junee Control Centre had been in the rail industry since November 2020, when they commenced as a trainee NC, progressing through the traineeship in April 2021. The NC had been operating as an authorised NC in the Junee Control Centre for approximately four months.
Safety analysis
The work being undertaken
The workgroup was in the process of installing and welding a closure rail in a section of track after removing a redundant switch to a disused siding. This entailed cutting the track to disconnect the disused infrastructure and joining the main line rails to form a continuous rail. Once the track was cut, it was plated together using bolts and clamps, and the join would then be welded together.
The workgroup encountered some delays in performing this task due to the late arrival of the signal electricians at the worksite, who were delayed by a meeting in the Wagga Wagga depot that ran overtime. The signal electricians arrived approximately 90 minutes late to the worksite. The signal electrician’s role was to disconnect the points to allow the civil team to cut the track and weld it back together.
Just prior to the incident, the work had not yet progressed to the point where welding had commenced. The join was secured using a Robel clamp until the welding could occur. By this time, the worksite protection arrangement being used for this work, a TOA, was due to end because a passenger train, the Sydney bound XPT service ST24, was scheduled to arrive at Bomen and travel through the section.
Fulfilling the Track Occupancy Authority (TOA)
The rules of ending, or fulfilling, the TOA meant the below activities had to be undertaken in the following order:
- Removal of people, tools, and equipment from the track
- Removal of trackside protection including railway track signals and red flags or lights
- Informing the NC of these activities and confirming the track is fit for service, or alternatively, of any conditions or restrictions that need to apply.
The NC then removes blocks on the protecting signals for the TOA and trains are allowed to run, subject to any conditions or restrictions.
As the expiry time for the TOA was approaching, the PO was advised that the work was not complete because the welding had been delayed by the late arrival of the signal electricians. As the rail was held in place by a clamp a temporary speed restriction would be necessary. The track certifier in the work group spoke with the PO and advised that a 40 km/h speed restriction was required.
Removal of Track Occupancy Authority (TOA) protection
Due to the makeup of the team, the PO needed to go to the Wagga Wagga end of the TOA to remove the protection, as there were no other available workers to perform this task. The protection was approximately 500 m away from the worksite. Another team member went to the northern end of the TOA to remove the protection there. The remaining team members were required at the worksite to complete the work activity in order to make the track safe for train running.
Ten minutes prior to leaving the worksite, the PO had a conversation with the track certifier about the need to impose a temporary 40 km/h speed restriction. However, at the time of fulfilling the TOA, the PO was likely focused on removing the protection and associated tasks with fulfilling the TOA so overlooked the application of the speed restriction.
The ARTC Network Rule ANWT 300 Planning work in the rail corridor states:
Protection Officer
A worksite must have a Protection Officer (PO).
A Protection Officer’s primary duty is to keep the worksite and workers safe.
The Protection Officer must be satisfied other work will not interfere with protection duties.
In this case the PO was performing another task, being the Qualified Worker removing the protection for the TOA which is permitted under the ARTC Network Rules. It meant that the PO was absent from the worksite, and their attention was on both removing the protection and fulfilling the TOA in order to allow the passage of a high-priority passenger service.
Temporary speed restriction and fulfilling the TOA via eTAP
A temporary speed restriction is applied through Network Rule ANGE 206 Condition Affecting the Network (CAN), it states:
Warning Rail Traffic
The Network Control Officer must give written warning using a CAN form to rail traffic crews if:
• temporary speed restrictions have been reported and no signs erected.
While at the Wagga Wagga end of the TOA, the PO attempted to gain an extension of time for the TOA but was refused by the NC as the northbound XPT was due to run, then the southbound XPT needed to run after that. These were two high-priority, long-haul passenger trains, and effort is always made to avoid delays to these services.
The unsuccessful attempt to extend the TOA did not result in any discussion between the PO and the NC about the reason for the extension, i.e., that the work was incomplete, and the track was not suitable for normal line speed. This conversation focused on the train running after the XPT trains, and on when another TOA was expected to be taken.
The NC asked the PO if the existing TOA would be handed back at the expected time and the PO answered that it would. There was no mention of any speed restriction or other condition. The reduced speed would have affected the train running time as any trains travelling through the section would have required a written CAN issued to the driver, and the train would have had to slow down over the worksite.
After the unsuccessful attempt to extend the TOA, the PO made arrangements to restore the line for rail traffic and fulfil the TOA.
The PO had arranged the TOA utilising the eTAP application on their mobile phone. They also used eTAP to fulfill the TOA when handing back the track. The PO selected ‘Yes’ in response to the question “Is the track suitable for line speed operations?” in the fulfillment assurance checks, instead of selecting ‘No’.
If No was selected, then the application would have directed the PO to call the NC and advise the details of the temporary speed restriction. The PO stated at interview that they had never used the eTAP application to impose a temporary speed restriction after fulfilling a TOA. This was the first time the PO had fulfilled a TOA that required a CAN warning for a speed restriction.
Operation of XPT train ST24
Shortly after fulfilling the TOA on eTAP, the PO realised their error and unsuccessfully attempted to contact the NC before the XPT arrived at the worksite. At this time, the NC was dealing with a report of children trespassing in the rail corridor and another request for work on track access from a different work group at Harefield using Absolute Signal Blocking. When the PO was unable to contact the NC on the regular phone line, they called the emergency Network Control number notifying the NC of the error. The NC answered the emergency call but by this time the train had already left Bomen.
By the time the NC was aware of the need for the CAN warning, ST24 had passed the PO at the Wagga Wagga end of the TOA and was travelling through the worksite.
ST 24 passed through the worksite at approximately 100 km/h, 60 km/h over the intended speed of 40 km/h. The driver reported seeing the workers beside the track and so sounded the train horn and received acknowledgement from the workers before passing through the site.
It was possible for the PO to stand to the side of the track and use the emergency stop handsignal to alert the driver to stop. The PO did not attempt to use handsignals to stop the train.
ARTC introduction of eTAP app-based solution
ARTC undertook a trial of the eTAP solution prior to full implementation.
Prior to initiating the trial, ARTC established the following criteria to determine the success or failure of the trial. These were:
- It had to be a functional electronic system
- It had to reduce the time it took to issue a TOA (with an aim of 50%)
- The trial had to contain zero safe working errors attributed to the application
- It had to be positively taken up by the workforce
- At least 200 TOA events needed for validity of trial.
Figure 4: eTAP screen shot for TOA fulfillment on PO device
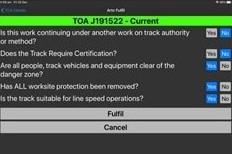
Source: Australian Rail Track Corporation
Using eTAP, a NC could issue TOA information electronically to a PO. The PO could then review and confirm the information and location on the device before verification and acceptance. This process replaced the previous paper form and verbal read out/read back communication.
At the time of fulfillment of a TOA, a PO checks off assurance questions in the eTAP application (figure 4). If there is no CAN identified (as indicated by the PO’s answers to the assurance questions) then the PO can complete the fulfilment of the TOA electronically. The NC then completes their work to fulfil the TOA by using the fields on their screen (figure 5). However, if any CAN are identified (as indicated by the PO’s answers to the assurance questions) then the application requires the PO to call the NC and verbally complete the fulfilment of the TOA.
Figure 5: eTAP screen shot for TOA fulfillment on Network Controller workstation
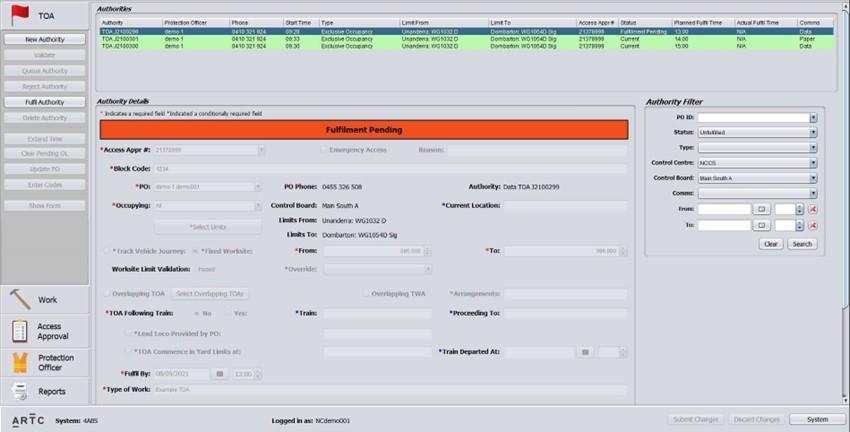
Source: Australian Rail Track Corporation
eTAP was designed to improve safety and efficiency outcomes for POs and NCs, by enhancing decision making through the provision of more information and electronic delivery.
Through a review into the establishment of worksite protection on its network, ARTC identified several common factors which had the potential to result in errors during the issue of a TOA. The most common factors identified were;
- Inadequate communication
- Incorrect planning
- Incorrect form compilation
- Incorrect graphing
- Incorrect location
- Lack of area knowledge
- Failure to identify the correct location of trains within the limits of a work authority
- Incorrect or inadequate use of blocking facilities.
The risks to track workers from one or more of these factors, led ARTC to explore controls to mitigate these errors. ARTC identified the 4Tel/John Holland Rail ETW System (eTAP) as a potential solution to trial. A trial was conducted in South Australia on the ARTC west network control centre between 9 May 2018 and 9 July 2018.
At the conclusion of the trial, ARTC determined that the eTAP electronic system had met the criteria successfully. In August 2018, ARTC recommended to continue utilising the eTAP electronic system in the trial location and to introduce its use throughout the entire ARTC interstate and Hunter Valley NSW networks.
ARTC risk assessment for the introduction of eTAP
ARTC conducted a risk assessment workshop on 28 March 2019 which explored potential risks involved with the introduction of the eTAP system into the NSW ARTC controlled network. The makeup of the risk assessment team included one operational infrastructure worker, a team leader from Coffs Harbour NSW.
The risks identified in the workshop included:
- System availability
- Confusion for the Network Controller using two systems
- Inadequate worksite protection
- Lack of interface between the eTAP app and the Phoenix signalling system
- IT security of devices
- Functionality of the eTAP application
- Failure of the device in the field.
The ARTC risk assessment did not contemplate a failure mode whereby the PO would return the track to service without imposing a temporary speed restriction to ensure safe operation of rail traffic. The potential for this human error was not identified by the risk assessment team. The composition of the risk assessment team did not include representation from people who could provide input on using the application from the PO perspective.
An ARTC Human Factors and Safety Risk Assessment was completed in November 2019 (prior to introduction of eTAP into the ARTC network) by an external organisation (RGB Assurance). The risk assessment included the risk of a PO answering the Assurance Questions incorrectly and this was identified including recognition of Current and Planned Controls to reduce the likelihood of that risk.
When the eTAP application is used to fulfil the TOA, it replaces with an electronic form, the use of a paper form and a conversation with the NC unless the PO ticks a box on the electronic form that indicates a conversation with the NC is required. The use of the eTAP electronic form replicates the conventional fulfilment process but uses a different media. It is arguable that removing the conversation between the PO and the NC at TOA fulfilment may reduce the safety performance of the rule. The conversation with the NC is an opportunity to confirm the situation during the fulfillment process and possibly address any risks during transition back to full operations.
The flow of information using the eTAP system follows the same path as conventional safeworking communication, but in this case, it has eliminated the explicit need to have a conversation and therefore the confirm and repeat back provision for safety critical messages under the ARTC Network Rule ANGE 204 Network Communication. The rule states:
Confirmation of communication
The receiver must confirm the content of a message by repeating the message back to the sender, if the communication is about:
• a Proceed Authority, or
• an instruction not to proceed, or
• a work on track authority, or
• a work on track method, or
• Train Running Information, or
• special working, or
• a Condition Affecting the Network (CAN).
The receiver must not act on the communication until the sender confirms that the message has been repeated correctly.
The requirement to repeat back in the ARTC Network Rule for network communication regarding work on track authority is not obviated or overridden by the use of an electronic device to transmit and receive safety critical information. However, the adoption of this technology has led to a possible reduction in the performance of safeworking because it limits when a conversation with the NC is required. It relies on the correct completion of an e-form to identify when a conversation with the NC should take place.
The human factors aspects of using an electronic form to replace what was a verbal exchange between the NC and PO during the TOA fulfilment were not addressed in the design and implementation of the new eTap. For example, there is no repeat back or prompting involved in the eTAP application during the TOA fulfilment.
If an error is made during the TOA fulfillment process, it remains contained within the information transmitted electronically to the NC and acted upon without question or validation by the NC. That is what happened in this incident where a train was permitted to run in excess of the desired track speed because the e-form was incorrectly completed and there was no required conversation between the PO and the NC which might have detected the error.
Possible enhancements to the eTAP system such as, an additional prompt to confirm that the track is fit for normal speed prior to the completion of the fulfillment message to the NC, were not examined during the risk assessment process to overcome this issue.
ARTC did consider reverting to verbal communications for TOA fulfilment rather than relying on the eTAP system, but this was rejected by the ARTC risk assessment team as counter to the aims of the eTAP implementation.
Rollout of eTAP to the Wagga Wagga district
The PO involved in the incident identified at interview that the eTAP solution was implemented in their district some time before the incident, but they could not be sure when. Evidence provided by ARTC indicated the briefing associated with the roll out of eTAP took place in February 2020.
At this time the PO was a PO1 and was therefore not trained in the rules and procedures for TOA and unable to implement a TOA. The PO indicated that they may not have absorbed this element of the briefing, as it was not relevant to their level of certification at the time.
The PO stated that the briefing was a Power Point presentation only with no opportunity to try out the test device to become familiar with it and the process. According to the PO, the presentation consisted of 93 slides that were rushed through. They said that there was an exercise about TOA fulfilment at the end of the presentation, however that exercise was not applicable to them at the time, being only a PO1.
There was no record of any competence assessment of these exercises for the PO involved in this incident.
No additional training was offered for someone moving between the PO grades to provide assurance that they were competent in the use of the eTAP system. No other training took place with the PO prior to them becoming a PO2 and therefore able to use the eTAP system for TOA. Their knowledge was gained on the job not from a structured learning program.
The Robel clamp
The track was being held together by a Robel clamp while awaiting permanent joining via a weld. At interview, the ARTC work supervisor advised that a Robel clamp with a safety lock fitted and used, is safe for trains to travel up to 80km/h.
The 40 km/h temporary speed restriction was requested by the track certifier to protect the edge of the unwelded rail joint from wheel damage by passing trains. This speed reduction is consistent with the ARTC engineering standards for this type of join. Irrespective of the engineering performance of the Robel clamp, the speed restriction required for XPT train ST24 was 40km/h and the train travelled at 100km/h over the join, 60km/h above the required speed.
Findings
ATSB investigation report findings focus on safety factors (that is, events and conditions that increase risk). Safety factors include ‘contributing factors’ and ‘other factors that increased risk’ (that is, factors that did not meet the definition of a contributing factor for this occurrence but were still considered important to include in the report for the purpose of increasing awareness and enhancing safety). In addition ‘other findings’ may be included to provide important information about topics other than safety factors. Safety issues are highlighted in bold to emphasise their importance. A safety issue is a safety factor that (a) can reasonably be regarded as having the potential to adversely affect the safety of future operations, and (b) is a characteristic of an organisation or a system, rather than a characteristic of a specific individual, or characteristic of an operating environment at a specific point in time. These findings should not be read as apportioning blame or liability to any particular organisation or individual. |
From the evidence available, the following findings are made with respect to the overspeed of XPT train ST24 at Harefield on 29 June 2021.
Contributing factors
- The Protection Officer answered “no” to the assurance question on eTAP which asked whether there were any Conditions Affecting the Network (CAN). As a result, the Protection Officer fulfilled the Track Occupancy Authority (TOA) without initiating a temporary speed restriction.
- The work group task allocation meant the Protection Officer had to leave the worksite, to remove protection while also completing actions to fulfill the Track Occupancy Authority (TOA). It is likely the Protection Officer was distracted while performing these competing tasks.
- A further delay in communicating the Condition Affecting the Network (CAN) occurred when the Protection Officer’s call to the Network Controller on the regular phone went unanswered, and a follow up call was required on the emergency phone line to try and stop the train after the Protection Officer realised the error.
- The Protection Officer did not attempt to use hand signals to stop the train when it approached the worksite.
- The eTAP system, used at Track Occupancy Authority (TOA) fulfilment, did not include a key safeworking requirement contained in the ARTC Network Rule ANGE 204 for confirming and repeating back safety critical information. (Safety issue)
- The eTAP roll out did not include an effective training regime, as the briefing was not targeted to the appropriate level of competence of the trainees. The Protection Officer involved was not trained or competent in the rules and procedures for Track Occupancy Authority (TOA) at the time of the eTAP briefing. There was no competence assessment for the use of the application for the Protection Officer involved. (Safety issue)
Glossary
ARTC Australian Rail Track Corporation
CAN Condition Affecting the Network
DIP Directly Interested Party
JHR John Holland Rail
NC Network Controller
PO Protection Officer
RIM Rail Infrastructure Manager
TOA Track Occupancy Authority
XPT Express Passenger Train
Sources and submissions
Sources of information
The sources of information during the investigation included the:
- Interview with the ARTC Protection Officer
- Interview with the ARTC Civil team leader
- Interview with the ARTC Network Controller
- Audio recordings from ARTC Junee control centre
- eTAP implementation presentation
- ARTC Risk assessment report for implementation for eTAP.
Submissions
Under section 26 of the Transport Safety Investigation Act 2003, the ATSB may provide a draft report, on a confidential basis, to any person whom the ATSB considers appropriate. That section allows a person receiving a draft report to make submissions to the ATSB about the draft report.
A draft of this report was provided to the following directly involved parties:
- Australian Rail Track Corporation
- Office of the National Rail Safety Regulator
- NSW Trains
Any submissions from those parties will be reviewed and, where considered appropriate, the text of the draft report will be amended accordingly.
Submissions were received from:
- Australian Rail Track Corporation
- Office of the National Rail Safety Regulator
The submissions were reviewed and, where considered appropriate, the text of the report was amended accordingly.
Purpose of safety investigationsThe objective of a safety investigation is to enhance transport safety. This is done through:
It is not a function of the ATSB to apportion blame or provide a means for determining liability. At the same time, an investigation report must include factual material of sufficient weight to support the analysis and findings. At all times the ATSB endeavours to balance the use of material that could imply adverse comment with the need to properly explain what happened, and why, in a fair and unbiased manner. The ATSB does not investigate for the purpose of taking administrative, regulatory or criminal action. TerminologyAn explanation of terminology used in ATSB investigation reports is available here. This includes terms such as occurrence, contributing factor, other factor that increased risk, and safety issue. Publishing informationReleased in accordance with section 25 of the Transport Safety Investigation Act 2003 Published by: Australian Transport Safety Bureau © Commonwealth of Australia 2023 Ownership of intellectual property rights in this publication Unless otherwise noted, copyright (and any other intellectual property rights, if any) in this report publication is owned by the Commonwealth of Australia. Creative Commons licence With the exception of the Coat of Arms, ATSB logo, and photos and graphics in which a third party holds copyright, this publication is licensed under a Creative Commons Attribution 3.0 Australia licence. Creative Commons Attribution 3.0 Australia Licence is a standard form licence agreement that allows you to copy, distribute, transmit and adapt this publication provided that you attribute the work. The ATSB’s preference is that you attribute this publication (and any material sourced from it) using the following wording: Source: Australian Transport Safety Bureau Copyright in material obtained from other agencies, private individuals or organisations, belongs to those agencies, individuals or organisations. Where you wish to use their material, you will need to contact them directly. |
[1] A NSW Government agency constituted by the Transport Administration Act 1988 1A Section 3C.