Safety summary
What happened
On 11 May 2020, a Fairchild SA227-DC Metro 23 (Metro) aircraft, registered VH-HPE and operated by Toll Aviation, was being loaded for its scheduled freight service from Townsville to Rockhampton then Brisbane, Queensland. The pilot was the only person on board.
The pilot completed a load and trim sheet, which indicated that the planned load was not within the allowable centre of gravity limits. It was agreed that 126 kg of freight would be moved from compartment three to the nose compartment. The revised load and trim sheet indicated the centre of gravity to be within the limits. During the flight to Rockhampton, the pilot observed that the aircraft felt tail heavy, but did not experience any controllability issues.
Due to the concern of an aft centre of gravity, the additional freight loaded at Rockhampton was limited, which was still within the calculated allowable centre of gravity limits. On take-off from Rockhampton, the pilot reported that the aircraft had a strong pitch-up tendency and that strong forward pressure on the flight controls was required to maintain the correct pitch attitude. During the cruise, the autopilot would not consistently maintain level flight. The pilot disconnected the autopilot and with full nose-down trim applied, the pilot had to maintain forward pressure to control the pitch attitude of the aircraft. The aircraft continued to Brisbane and the pilot reported that no problems were experienced during the approach and landing.
What the ATSB found
The ATSB found that, the ground handlers at Townsville did not accurately weigh the freight relocated into the nose compartment, but rather, it was estimated by feel. This resulted in an inaccurate load and trim sheet, and the centre of gravity being further aft than expected. Therefore, when additional freight was loaded in Rockhampton, this unknowingly moved the centre of gravity beyond the rear limit, leading to the pitch-up tendency experienced by the pilot.
Although not contributory, the operator’s paper-based load planning tool used by ground handlers for the Metro did not account for the centre of gravity position. Rather, this was later determined by the pilot on the load and trim sheet, which was potentially completed after loading had commenced. This increased the chance of freight having to be relocated and the potential for loading errors to occur.
It was also identified that the operator’s ground handling manual did not contain sufficient procedural detail to facilitate the accurate redistribution of freight. In particular, there was no guidance on conducting last-minute changes or taking into account the centre of gravity when preparing a load plan to ensure that an aircraft would be correctly loaded.
What has been done as a result
Following the incident, the operator amended their ground handling processes and included increased direction to ensure that freight would be accurately redistributed in the event of a last-minute change. The operator has since relinquished their Civil Aviation Safety Authority’s Air Operator’s Certificate and divested their flying operations to another operator. The new Metro aircraft operator also considered the findings of this investigation, reviewed their ground handling manual and incorporated amendments to ensure that an aircraft would be correctly loaded.
Safety message
This incident demonstrates the critical nature of load control and the requirement to ensure an aircraft is correctly loaded and the centre of gravity is within the allowable limits. It also emphasises the importance of providing ground handlers with sufficient and detailed procedures to allow them to accurately conduct load control duties and minimise the potential for error.
Townsville–Rockhampton
On 11 May 2020, a Fairchild SA227-DC Metro 23 (Metro) aircraft, registered VH-HPE and operated by Toll Aviation, was being loaded for its scheduled freight service from Townsville to Rockhampton then Brisbane, Queensland. The pilot was the only person on board.
The pilot signed on for duty at 1700 Eastern Standard Time[1] and shortly after commenced pre‑flight preparations of the aircraft. The loading process had already commenced by that time and was about half complete when the ground handlers provided the load plan to the pilot.
The pilot then completed a load and trim sheet and ascertained that the planned load was aft of the rear centre of gravity limit. The pilot advised the ground handlers that the load was too heavy in compartment (zone) three and that some of that freight be moved to the nose compartment.
A team of four ground handlers were loading the aircraft, none of which were designated as a supervisor. One ground handler suggested to the pilot that 126 kg could be moved from compartment three into the nose compartment, leaving 300 kg in zone three. The pilot agreed, provided this could be achieved, having noted that the nose compartment was much smaller than the remaining compartments in both size and weight limit (Figure 1).
The ground handler contacted their supervisor who was at the freight depot. The supervisor had completed and signed the load plan, and advised the ground handler to carry out the pilot’s request to move the load. The ground handler commenced loading freight into the nose compartment. The ground handler recalled that ‘the nose is small in space’ and that it will ‘only fit a certain amount of things in there’, so only loaded as many bags as they could, filling the nose to volume capacity. This freight was not weighed, but rather, estimated by feel as there were no scales available at the aircraft. The ground handler explained that the load change took place at about 1745 and that the aircraft was scheduled to depart at 1800.
The pilot asked the ground handler if the freight had been moved as requested and the ground handler confirmed it had been. Believing that the load distribution was correct as amended from the original plan, the pilot completed a new load and trim sheet, which indicated the centre of gravity to be within the limits.
Shortly after, the aircraft departed Townsville. During the flight to Rockhampton, the pilot indicated that the aircraft felt tail heavy, but did not experience any controllability issues.
Figure 1: VH-HPE freight compartment configuration and weight limits
Source: Toll Aviation, modified by the ATSB
Rockhampton–Brisbane
On arrival in Rockhampton, the pilot discussed the load with ground handlers. The ground handlers had already reviewed the load plan from Townsville and were aware that the aircraft was relatively heavy. As a result, they had transferred most of the freight to another carrier for transport.
The ground handler at Rockhampton noticed that the aircraft appeared to be sitting ‘tail heavy’, and due to the pilot’s concern regarding an aft centre of gravity, the aircraft was only loaded with 111 kg in compartment three and 3 kg in compartment five. While the pilot believed the aircraft could still be loaded with more, they both agreed to minimise additional load.
On take-off from Rockhampton, the pilot reported the aircraft had a strong pitch-up tendency and rotated without input. The pilot had to apply strong forward pressure on the flight controls to maintain the correct pitch attitude and the pressure required to do so increased with altitude. Concerned with maintaining sufficient air density[2] to maintain control effectiveness, the pilot reduced the planned cruising altitude to flight level (FL)[3] 130.
After establishing the aircraft in the cruise, the pilot observed that the autopilot would not consistently maintain level flight. The aircraft would ‘porpoise’ as the autopilot tried to correct the pitch-up tendency. The pilot disconnected the autopilot from controlling the pitch of the aircraft, keeping it in GPS steer mode (lateral guidance only). Full nose-down trim had already been applied and the pilot then manually controlled the pitch attitude of the aircraft.
The pilot found that constant application of forward pressure was required, though noted that the force needed was ‘only a couple of kilograms’. The pilot did not observe any other controllability issues and was satisfied that control of the aircraft could be maintained.
The aircraft continued to Brisbane and the pilot reported that no problems were experienced during the approach and landing. The pilot had contacted operations prior to arrival, explained their observations regarding pitch control, and was met on the ground by maintenance engineers.
__________
- Eastern Standard Time (EST): Coordinated Universal Time (UTC) + 11.0 hours.
- As altitude increases, air density decreases, which results in less air passing over the flight control surfaces reducing their ability to effect aircraft movement and therefore control.
- Flight level: at altitudes above 10,000 ft in Australia, an aircraft’s height above mean sea level is referred to as a flight level (FL). FL 130 equates to 13,000 ft.
Personnel information
Pilot
The pilot held a valid Commercial Pilot Licence (Aeroplane) and multi-engine command instrument rating. The pilot had over 3,000 hours in total, with about 2,500 hours in command and about 700 hours on the Metro 23 aircraft. The majority of their flying experience was in overnight freight (single pilot operations). The pilot had been flying for Toll Aviation (Toll) for about 1 year.
Ground handler 1 (Townsville)
Ground handler 1 had been a Toll employee for a combined total of 11 years. In addition to ground handling duties, they conducted other freight related duties including deliveries via motor vehicle.
Ground handler 2 (Townsville)
Ground handler 2 had been a Toll employee for almost 10 years in a variety of roles with the last six in operational roles. Their current position was supervisory in nature and oversaw freight related duties. Mostly located in the depot, they did not normally carry out actual loading duties, but were responsible for the preparation of, and signing of load plans.
Ground handler 3 (Rockhampton)
Ground handler 3 had 13 years at Toll and was in a supervisory role similar to ground handler 2. They had about 10 years’ experience with loading the Fairchild SA227 (Metro) aircraft, and often carried out both load planning and actual loading tasks.
Organisational information
Toll Aviation was part of the Toll group of companies and provided air freight capability to Toll Express Parcels. Toll Express Parcels provided ground handling services to Toll Aviation at some of its ports but was not a full-time aviation ground handling organisation. Ground handling in Townsville and Rockhampton was undertaken by Toll Express Parcels, but Brisbane was handled by Toll Aviation.
Ground handling staff explained that they were a mix of Toll employees and contract delivery drivers who were trained in aviation ground handling duties. When not conducting aircraft related duties, the ground handlers undertook road deliveries/pickup.
Aircraft information
VH-HPE was a Fairchild SA227-DC Metro 23, twin turboprop engine regional aircraft, which had been configured for freight operations. Freight could be loaded into the nose compartment, or the main fuselage compartment, which had been divided into five zones (compartments) (Figure 1). The zones had a webbing style net for segregation of freight between compartments. Heavy, bulkier freight could be physically restrained to the compartment floor.
Table 1: VH-HPE aircraft weight limits
Weight limit |
lb |
kg |
Maximum ramp weight |
16,566 |
7,530 |
Maximum take-off weight |
16,500 |
7,485 |
Maximum landing weight |
15,675 |
7,110 |
Maximum zero fuel weight |
14,500 |
6,580 |
An aircraft must be operated within prescribed weight and balance limits. That is, it should not be loaded above the maximum weight limitations (Table 1) and the position of the aircraft load (fuel, passengers, cargo etc.) should be such that the centre of gravity is within lateral and longitudinal limits (balance). Maintaining this balance is critical to stable, controllable flight. A pilot is to use the approved loading system for the aircraft to ensure that the weight and balance is within the approved envelope, either manually (graphical) or electronically.
The approved loading system for the Metro operated by Toll utilised a graphical method (load and trim sheet) for determining the centre of gravity position. The pilot was required to complete the load and trim sheet once all the weight information (freight, fuel, passengers) had been obtained. Freight loads were provided on the load plan (Appendix A). The operator had a load and trim sheet that was specific to VH-HPE (Appendix B).
The load and trim sheet considered weight and position when graphically determining centre of gravity. Load placed closer to the front (nose compartment) or rear (compartment five) of the aircraft would have greater effect on centre of gravity than load placed near the middle of the aircraft (compartment two). Load placed in compartment two had negligible effect on the aircraft’s centre of gravity. Load placed in the nose compartment and in compartment one shifted the centre of gravity towards the front of the aircraft. Load placed in compartments three‑five shifted the centre of gravity towards the rear of the aircraft.
Post-incident inspection/actions
Freight reweighed
Following arrival in Brisbane, the pilot discussed the incident with the maintenance engineers. This resulted in the freight being reweighed as it was unloaded from the aircraft. When compared to the load plan used to complete the load and trim sheet, there was a significant difference in the weight distribution. Notably, only 65 kg was in the nose compartment and an extra 64 kg was in compartment three. All other compartments had more weight than planned. However, the individual compartment weights were not exceeded. The planned and actual weights are shown in Table 2, representing the load for the flight from Rockhampton to Brisbane.
The pilot subsequently completed a new load and trim sheet using the actual weights and the centre of gravity was found to be aft of the rear limit (outside of the limits) (Appendix C).
Table 2: Aircraft load (reweighed) for Rockhampton to Brisbane
Compartment |
Load plan (kg) |
Actual weights (kg) |
Weight difference (kg) |
Nose |
126 |
65 |
-61 |
1 |
527 |
545 |
+18 |
2 |
582 |
606 |
+24 |
3 |
411 |
475 |
+64 |
4 |
219 |
225 |
+6 |
5 |
90 |
103 |
+13 |
The weight of the additional freight loaded at Rockhampton was subtracted to determine the actual weight and distribution of freight for the flight from Townsville to Rockhampton. The actual weights did not correspond to the load plan but did not exceed individual compartment limits. Table 3 shows the weights on the original load plan during aircraft loading and the revised plan after moving some freight from compartment three to the nose compartment, compared with the actual weights.
A load and trim sheet with the actual weights determined that the load from Townsville was still within limits but the centre of gravity was much further aft than originally calculated. The recalculated load and trim sheet also revealed that the aircraft departed Townsville about 6 kg above its maximum take-off weight (Appendix D). A lower fuel load on departure from Rockhampton meant that the aircraft was within the take-off weight limits. However, the additional freight loaded in Rockhampton shifted the centre of gravity position beyond the rear limit.
Table 3: Aircraft load for Townsville to Rockhampton
Compartment |
Original load plan (kg) |
Revised load plan (kg) |
Actual weights (kg) |
Nose |
0 |
126 |
65 |
1 |
527 |
527 |
545 |
2 |
582 |
582 |
606 |
3 |
426 |
300 |
364 |
4 |
219 |
219 |
225 |
5 |
87 |
87 |
100 |
Scales at Townsville
The operator’s internal investigation report stated that the scales used in Townsville were calibrated on 27 June 2019 and were due to be recalibrated in June 2020. They also verified that these scales were reporting an accurate weight.
Flight controls inspections
To confirm the serviceability of, and their potential to have contributed to the pitch control issues, the operator replaced the pitch servo and pitch flight guidance computer. Maintenance logs showed that replacement parts were fitted and tested serviceable. There was no evidence to suggest the components were malfunctioning or contributory.
Aircraft loading process
Townsville
On the day of the incident, items for air freight began arriving at the depot around 1600 and aircraft load preparations commenced at that time. Individual freight items were weighed with smaller envelope style parcels placed in consolidation bags, to a limit of 14 kg per bag. As each item was weighed, it was allocated to an aircraft compartment. The Townsville supervisor reported that, compartment allocation was based on the size or volume of the freight item and the experience of the ground handler to get an even distribution of freight. The supervisor said it was normal to prioritise freight to compartments one and two (toward the front of aircraft), to enable later ports to add freight to the rear.
Each aircraft compartment had its own ‘barrow’ (or area in a truck) to ensure segregation and facilitation of loading onto the aircraft. All weights were written on a load sheet, which upon completion, was presented to the supervisor.
Normally, consigned items already had a weight annotated on them. However, if found to be different when weighed prior to compartment allocation, it did not appear that these items were annotated with their correct weight. Consolidation bags did not have total weights annotated on the bag, nor was there a requirement to do so.
The supervisor stated that the load was driven to the aircraft as soon as preparations had completed.
Despite not taking part in the load preparation, the supervisor completed and signed the load plan in addition to other freight paperwork. The supervisor explained that the paperwork was then delivered to the pilot by one of their staff who was not on the load team. The supervisor stated they did not have an opportunity to verify if the load matched the plan or make changes prior to the load being delivered to the aircraft. They then forwarded a copy of the load plan to the Rockhampton supervisor to enable them to begin their load preparations.
The ground handler contacted the supervisor and was advised to amend the load as directed by the pilot.
The supervisor indicated that, on this particular night the freight allocation was much bigger than normal. Further, in general, it was a rare occasion in which the pilot requested freight to be moved once the load plan had been completed.
Rockhampton
The load process at Rockhampton was described as being similar to Townsville. Due to Rockhampton being a smaller depot, a distinct difference was the supervisor being more involved in the loading process and physically participated in all aspects. The supervisor at Rockhampton also stated that it was a rare occasion for a pilot to request changes to the load plan.
Load control policy and procedures
The operator’s load control policy and procedures were contained in numerous manuals within their operations manual suite. These are described in the following sections.
Flight operations
The flight operations manual stated that:
Responsibility for load control of Toll Aviation aircraft lies with the Pilot-in-Command for the particular flight.
The Pilot-in-Command shall ensure that a load sheet is completed prior to departure of the aircraft on each stage of every flight.
The Pilot-in-Command will advise Toll Aviation Operations or the Supervisor/Load Controller of the maximum payload for the particular flight as this will allow loading to commence. During the loading and unloading of freight on company aircraft, the Pilot-in-Command shall monitor the operation and location of loading vehicles and equipment by ground handling staff to ensure the aircraft is not damaged.
The Pilot-in-Command may delegate this duty to a person identified as an employee to a client freight organisation, trained in loading procedures for the aircraft.
Before each flight, the Pilot-in-Command shall ensure that the aeroplane is loaded within the prescribed centre of gravity limits as determined by the current approved loading system specified in the AFM for that aircraft.
As stated above, the pilot was ultimately responsible for load control, despite not physically undertaking load duties. Ground handlers carried out the bulk of load control duties on behalf of the pilot.
The pilot reported that it was not possible to physically confirm the load was accurate (for example, confirming correct weights). Similarly, although present at the aircraft for part of the loading, the pilot was not able to closely supervise the process. As these tasks were delegated to ground handlers, the pilot relied on the ground handlers providing an accurate load plan, so the pilot could complete the load and trim sheet and fulfil their requirement to ensure the aircraft was loaded within the prescribed centre of gravity limits.
Ground handling operations
The operator’s ground handling manual (GHM) covered the requirements for all organisations conducting ground handling for Toll Aviation. Section 2.4.4 was titled Ready reference and stated:
This manual is intended for use by Toll Aviation employees, contractors, freight forwarders and ground handlers involved in any way with the air transport process and specifically in relation to acceptance, handling, loading, carriage or consignment of cargo on Toll Aviation aircraft.
The ATSB’s review of the load control aspect of the GHM identified that it was focused on policy and procedural inclusions that were primarily related to load plan preparation. There was no other document or manual containing procedures or work instructions relating to load control.
Allocation of responsibilities
The GHM indicated that responsibility for load control was assigned to the pilot in command, reiterating the requirements of the flight operations manuals as:
2-4-6 Pilot-in-Command
…the Pilot-in-Command shall at all times:
b. take all reasonable steps to ensure that the:
1. load is properly distributed and safely secured
2. aircraft weight and balance is within the calculated limits for the operating conditions.
3-1-2 Pilot-in-Command responsibilities
Responsibility for Load Control of Toll Aviation aircraft lies with the Pilot-in-Command for the particular flight.
The Pilot-in-Command shall ensure that:
a. a Load and Trim Sheet is completed prior to departure of the aircraft for each stage of every flight
3-1-24 Pilot-in-Command approval
Prior to departure, a completed Loading Plan signed by the person responsible for loading the aircraft shall be provided to and shall be approved by the Pilot-in-Command
The GHM did not specify a similar assignment of responsibility for ground handlers undertaking load duties.
Supervision
The GHM did not specify a requirement for a supervisor to be included in the load team and none of the ground handlers in the load team at Townsville were assigned as a supervisor. The supervisor at Townsville said that, as the supervisor for all depot operations, they were not always able to attend the aircraft. Furthermore, there was not a leading hand position or similar that was part of the load team.
Weighing freight
The GHM directed that:
All freight loaded at any port shall be weighed and the weight shall be measured in kilograms to the nearest kilo using calibrated scales.
Ground handlers at both Townsville and Rockhampton confirmed that, upon arrival at the depot, all freight items were weighed. However, once weighed, items were not annotated with their verified weight, nor was there a requirement to do so.
Load plan preparation
The GHM included procedures for the preparation of a load plan and a generic load plan procedure.
3-1-22 Preparing the Loading Plan
The Departure Port Supervisor/Responsible person or PIC [pilot in command] shall be responsible for preparing the Loading Plan. He/she shall:
a. obtain the maximum payload figure from the Pilot-in-Command
b. using the excel Loading Plan spreadsheet, freight is allocated to particular zones on the aircraft (taking into account the maximum weight for floor loading limits for the zone). This information is then transferred to a Loading Plan form.
c. complete Loading Plan on the day departure including information at the end of the Loading Plan, REGO = Aircraft Rego, FROM = departing port, TO = NEXT port aircraft will land, DATE = Date of departure, Loaders name = Person responsible for completing Loading Plan on day of departure, Signature = of person responsible for Loading Plan
d. provide a copy of the Loading Plan to the Loader
e. transmit a copy of the Loading Plan to the Supervisor/responsible person at each transit port.
The load plan tool used by the operator for the Metro was a manual, paper-based tool. A diagram of each aircraft and their compartment layouts were annotated with the applicable weight limits. This tool did not account for how the position of freight may affect the resultant centre of gravity (Appendix A).
Load and trim sheet
The subsequent completion of the load and trim sheet was the only means to calculate the centre of gravity position. This was the responsibility of the pilot, since ground handlers were not required to undertake this task. To complete the load and trim sheet, the pilot was wholly reliant on the information provided on the load plan by ground handlers.
Freight loading and last-minute changes
The GHM did not provide guidance on how to distribute freight across the aircraft compartments. As previously discussed, the distribution of freight was highly dependent on the experience of the ground handler conducting the task. According to the pilot and the ground handlers, it appeared that, in most cases, the planned allocation rarely required changes to be made and the load plan was usually within the centre of gravity limits. The redistribution of freight requested by the pilot was considered a last-minute change (LMC). The GHM only referred to LMCs as follows:
Any last-minute change to the freight load shall be approved by the Pilot-in-Command
The operator stated that this scenario was trained for, and that in a situation like the incident, freight was to be returned to the depot to be reweighed before loading. This was not documented in any manual, nor was it included in the training presentations. Further, ground handlers were not able to weigh the freight at the aircraft as scales were not available to the load team at the aircraft.
Ground handler 1 at Townsville inferred that, if 10-20 kg needed to be moved then estimating the weight by feel would be sufficient. However, if 150 kg needed to be moved, this would require taking freight back to the depot to reweigh. The ground handler could not explain why the 126 kg LMC for this incident was any different.
Ground handler 3 at Rockhampton explained that, if freight needed to be moved, they would attempt to move an entire compartment allocation (a known weight) or only move items that had weights annotated. Although not explicitly stated, the ground handler inferred that, if either of those options were not feasible, then they would return to the depot to reweigh the freight.
A procedure or explanation regarding a LMC was not detailed in the GHM. However, ground handlers appeared to have been provided some training/guidance for handling an LMC. The operator advised that, returning to the depot to reweigh freight was taught but conceded this was not documented anywhere.
Ground handling training
The operator’s ground training program included several presentations covering all aspects of load control. This was supplemented by practical instruction and formal assessment. Recurrent training was required every 24 months.
Module 3 of the training covered load control and discussed its critical nature. It emphasised the requirement for accurate loading of the aircraft and that the pilot was reliant on ground handlers to provide accurate information to complete the load and trim sheet. The module provided examples of the consequences of incorrect loading to reinforce this message. The ATSB noted that this information was not explicitly included in the GHM.
The operator advised that ground handlers were taught that freight was to be returned to the depot to be reweighed in the event of LMCs such as this incident. They acknowledged that this was not documented in any manual (it was also not in module 3 of the training).
The operator also reported that, about 3 years prior, several issues covering the delivery of, and management of ground handling training had been identified. As a result, the operator received board approval for additional resources to revise their training structure and improve those issues. They advised that, at the time of this incident, remedial action was in progress to amend training documentation and provide greater scrutiny over training activity.
The supervisor at Townsville was the designated trainer, but had not completed recurrent training. The supervisor explained that, training had been deficient for about 4 years since the branch manager had left the organisation. The supervisor also reported that significant catch-up had been required to get all staff up-to-date. Rockhampton did not appear to have such training issues.
The ATSB reviewed training as a possible contributing factor to the incident. However, when considering the lack of procedural guidance for load control duties, the ATSB assessed that effective training could not take place without robust documented procedures to train for, therefore did not consider training aspects any further.
Similar occurrence
ATSB investigation (AO-2013-044)
On 30 January 2013, a Toll Fairchild SA-227AC Metro aircraft, registered VH-UUO, departed Melbourne Airport, Victoria for Launceston Airport, Tasmania on a scheduled freight flight. The pilot was the only person on board.
During the take-off, the pilot reported that they needed more forward elevator trim than usual to climb out at a 10° nose-up attitude. The pilot noticed that, in straight-and-level flight, the aircraft had full nose-down trim, but flying at a 5° nose-up attitude. When the autopilot was engaged, the pilot stated that the autopilot struggled to maintain straight-and-level flight, explaining that the aircraft ‘porpoised’. The pilot conducted a normal landing at Launceston.
The operator determined that, although the loading plan for the aircraft indicated 100 kg of freight in the nose locker, one of the loaders had removed about 70 kg of freight from the nose locker and moved it to the rear of the aircraft. The operator identified that there was no formalised approach to the loading and unloading of the aircraft.
In addition, as the freight for the aircraft was not reweighed at Launceston, it was not possible to determine the exact centre of gravity that existed at the time of take-off from Melbourne. However, the flight characteristics of the aircraft suggested that it was either at the most rearward centre of gravity position, or just outside the rear centre of gravity limit.
The operator identified a lack of formal training for ground handlers and a lack of general procedures for them to follow. They also noted that there was insufficient oversight of the loading process and that the load plan for the Metro did not take centre of gravity position into account. Actions proposed by the operator included a review of, and publishing revisions to the GHM and the development of a ground handling training manual.
Operator comments
The operator’s investigation for this incident also identified that there was a lack of procedural guidance in the ground handling manual to support ground handlers in their duties. They stated that:
The Ground Handling Manual provides limited information on practical application of safe loading procedures for the Metro Aircraft and instead relies on input from the Pilot in Command.
The ATSB noted similarities between the two occurrences (albeit 8 years apart) and sought additional information regarding the status of safety actions from the 2013 incident. The operator’s safety manager was not able to provide any additional information relating to the previous occurrence as it was before their tenure and there was no record within their safety management system. Therefore, the ATSB was unable to explore any potential links between the two occurrences.
Introduction
During the dedicated freight flight from Townsville to Rockhampton, Queensland, the pilot of VH‑HPE noted that the aircraft felt tail heavy, but did not experience any controllability issues. On the subsequent flight from Rockhampton to Brisbane, the aircraft had a strong pitch-up tendency, and the pilot was required to apply strong forward pressure on the flight controls to maintain the correct pitch attitude. The aircraft continued to Brisbane and the pilot reported that no problems were experienced during the approach and landing.
This analysis will examine the planned and actual load distribution and corresponding centre of gravity position for the flights from Townsville to Rockhampton and then to Brisbane. It will further discuss the operator’s load planning tool and ground handling procedures regarding the redistribution of freight.
Inaccurate load
After receiving the load plan from the ground handlers at Townsville, the pilot completed the load and trim sheet, and identified that the aircraft’s centre of gravity was aft of the rear limit. Consequently, it was agreed that 126 kg of freight was to be relocated to the nose compartment.
As there were no scales available at the aircraft, the ground handler estimated the amount of freight to be moved based on feel. However, the reweigh of the load post-incident established that the aircraft was not loaded in accordance with the revised load plan. Therefore, the completed load and trim sheet did not reflect the actual load distribution. Although the load distribution was not as planned, it was still within centre of gravity limits, albeit more toward the rear than expected. As this was not known, any additional load would not have been accurately reflected on the load and trim sheet and was potentially out of limits.
Centre of gravity out of limits
At Rockhampton, additional freight was loaded based on the load and trim sheet prepared at Townsville. However, since the load and trim sheet did not accurately reflect the actual load distribution, the additional freight moved the centre of gravity rearward, beyond the rear limit. As a result, the aircraft was operated outside of its centre of gravity limitations.
The centre of gravity envelope is established to provide a pilot with the allowable distribution of weight, within which the aircraft will have longitudinal stability and allow the pilot to have full control of the aircraft. Although the aircraft was still controllable in this case, the pilot had used full nose‑down trim and the auto pilot was not able to maintain level flight. This required the pilot to apply constant forward pressure to manually control pitch and reduced the options available to the pilot to maintain full control of the aircraft.
Load plan did not account for centre of gravity position
The paper-based load planning tool utilised by Toll Aviation (Toll) for its Metro aircraft only accounted for compartment weight limits and did not provide information on the resultant centre of gravity position. This was later determined on completion of the load and trim sheet, which was a pilot responsibility. Ground handlers were not trained to, nor were they required to, complete the load and trim sheet. Further, there was no documented guidance for the distribution of freight within the aircraft and it was dependent upon an individual ground handler and/or supervisor’s training, experience and knowledge of the aircraft.
Loading was often commenced prior to the pilot being able to complete the load and trim sheet. Consequently, loading may be quite advanced if not already completed by the time the pilot has determined that the load plan was not within limits. While in this case and for the 2013 incident, the loading error occurred due to the freight not being weighed, this could necessitate additional workload and delay. As there was no ability to weigh freight at the aircraft and no documented procedure to guide such a reasonably foreseeable situation, this increased the chance of freight having to be relocated, thereby creating opportunities for errors to occur.
Ground handling procedures
According to the operator’s flight operations and ground handling manuals (GHM), the pilot was ultimately responsible for load control. However, practically, a significant portion of the load process was delegated to the ground handlers. The GHM detailed the requirements for conducting ground handling operations, including the loading of freight. However, the procedures were primarily related to the preparation of a load plan, with no other routine tasks or reasonably expected contingency tasks included. Further, there was no other documents or manuals that contained work instructions for ground handling operations.
Specifically, the GHM did not provide details on how to take centre of gravity into account when preparing a load plan, to minimise the potential for last-minutes changes. Also, the GHM did not include any instructions for the conduct of last-minute changes to ensure the aircraft was loaded correctly. For such situations, ground handlers were taught that the freight was to be returned to the depot to be reweighed, however, this instruction was not documented. The operator also identified that there was limited information in the manual regarding safe loading procedures.
In this incident, the ground handlers involved had different views on what was required when faced with a similar situation. Ground handler 1 at Townsville displayed an understanding of what should have occurred with regard to moving the freight, specifically mentioning that an amount of 150 kg would require return to the depot for reweigh, although they could not answer why 126 kg was different. Ground handler 3 at Rockhampton displayed a higher understanding and had numerous options available to consider when redistributing freight, none of which were documented in the GHM.
In the absence of clear, documented procedures, ground handlers were effectively put into situations where they had to rely on their own judgement and experience, and possibly utilise other procedures, which may not necessarily be appropriate for the task. Robust documented procedures create predictable standards and expectations and provide a solid foundation for training. This will enable staff to undertake tasks, identify errors and ensure consistent, safe outcomes.
Load awareness
The ground handler’s recognition that the aircraft was relatively heavy on arrival at Rockhampton and the decision to make alternative arrangements for freight to minimise the additional load demonstrated a high level of situational awareness. While they were not to know that the aircraft was incorrectly loaded and that additional load would result in the centre of gravity being out of limits, their actions limited the potential severity of the situation.
ATSB investigation report findings focus on safety factors (that is, events and conditions that increase risk). Safety factors include ‘contributing factors’ and ‘other factors that increased risk’ (that is, factors that did not meet the definition of a contributing factor for this occurrence but were still considered important to include in the report for the purpose of increasing awareness and enhancing safety). In addition, ‘other findings’ may be included to provide important information about topics other than safety factors. Safety issues are highlighted in bold to emphasise their importance. A safety issue is a safety factor that (a) can reasonably be regarded as having the potential to adversely affect the safety of future operations, and (b) is a characteristic of an organisation or a system, rather than a characteristic of a specific individual, or characteristic of an operating environment at a specific point in time. These findings should not be read as apportioning blame or liability to any particular organisation or individual. |
From the evidence available, the following findings are made with respect to the aircraft loading and in-flight controllability issue involving Fairchild SA227, VH-HPE, Rockhampton Airport, Queensland, on 11 May 2020.
Contributing factors
- Ground handlers did not accurately weigh the freight relocated to the nose compartment at Townsville. This resulted in an inaccurate load record on the load and trim sheet, with the centre for gravity further aft, though still within limits.
- Additional freight was loaded in Rockhampton as per the load and trim sheet. However, due to inaccuracies in the load and trim sheet (ex. Townsville), the additional load unknowingly moved the centre of gravity aft of the rear limit (out of limits). This resulted in the aircraft exhibiting a strong pitch-up tendency, requiring the pilot to apply constant forward pressure to maintain aircraft control.
Other factors that increased risk
- The load planning tool used by the operator for the SA227-DC Metro 23 aircraft did not account for the centre of gravity position. This increased the chance of freight having to be relocated once the pilot completed the load and trim sheet and increased the potential for loading errors to occur.
- The operator's ground handling manual did not contain detailed procedural guidance for facilitating accurate redistribution of freight to ensure that an aircraft would be correctly loaded. (Safety Issue)
Other findings
- Ground handlers at Rockhampton assessed the aircraft as relatively heavy and took action to minimise additional load. On arrival, it was agreed with the pilot to limit the additional freight. These actions reduced the severity of the centre of gravity being out of limits.
Central to the ATSB’s investigation of transport safety matters is the early identification of safety issues. The ATSB expects relevant organisations will address all safety issues an investigation identifies. Depending on the level of risk of a safety issue, the extent of corrective action taken by the relevant organisation(s), or the desirability of directing a broad safety message to the aviation industry, the ATSB may issue a formal safety recommendation or safety advisory notice as part of the final report. All of the directly involved parties were provided with a draft report and invited to provide submissions. As part of that process, each organisation was asked to communicate what safety actions, if any, they had carried out or were planning to carry out in relation to each safety issue relevant to their organisation. Descriptions of each safety issue, and any associated safety recommendations, are detailed below. Click the link to read the full safety issue description, including the issue status and any safety action/s taken. Safety issues and actions are updated on this website when safety issue owners provide further information concerning the implementation of safety action. |
Guidance in the ground handling manual
Safety issue number: AO-2020-027-SI-02
Safety issue description: The operator's ground handling manual did not contain detailed procedural guidance for facilitating accurate redistribution of freight and ensure that an aircraft would be correctly loaded.
Safety action not associated with an identified safety issue
Whether or not the ATSB identifies safety issues in the course of an investigation, relevant organisations may proactively initiate safety action in order to reduce their safety risk. The ATSB has been advised of the following proactive safety action in response to this occurrence. |
Additional safety action Toll Aviation
Soon after the incident, Toll Aviation advised that:
- An outcome discussion was conducted with all ground handlers regarding the actions taken on the day of the incident and their responsibilities under the ground handling manual.
- Human Factors for Ground Handlers training had been finalised and was being implemented in stages across Toll Air Express.
- An electronic load tool (Excel) had been devised for the Metro aircraft, to provide the ground handlers with a guide for the position of the index units when determining freights loaded into each compartment. This tool was in the stage of testing and quality review prior to formal change management process and implementation.
- A weight and balance review of VH-HPE was conducted by the weight control officer. The load and trim sheet has been revised and was undergoing testing and quality review prior to formal change management process and implementation.
EST Eastern standard time
FL Flight level
GHM Ground handling manual
GPS Global positioning system
LMC Last-minute change
Sources of information
The sources of information during the investigation included the:
- the pilot
- the ground handlers (Toll Express Parcels)
- the operator (Toll Aviation).
Submissions
Under section 26 of the Transport Safety Investigation Act 2003, the ATSB may provide a draft report, on a confidential basis, to any person whom the ATSB considers appropriate. That section allows a person receiving a draft report to make submissions to the ATSB about the draft report.
A draft of this report was provided to the following directly involved parties:
- the pilot
- the ground handlers (Toll Express Parcels)
- the operator (Toll Aviation)
- the Civil Aviation Safety Authority.
Submissions were received from:
- the pilot
- the ground handlers (Toll Express Parcels)
- the operator (Toll Aviation)
- the Civil Aviation Safety Authority.
The submissions were reviewed and, where considered appropriate, the text of the report was amended accordingly.
Appendix A – Metro 3/23 load plan
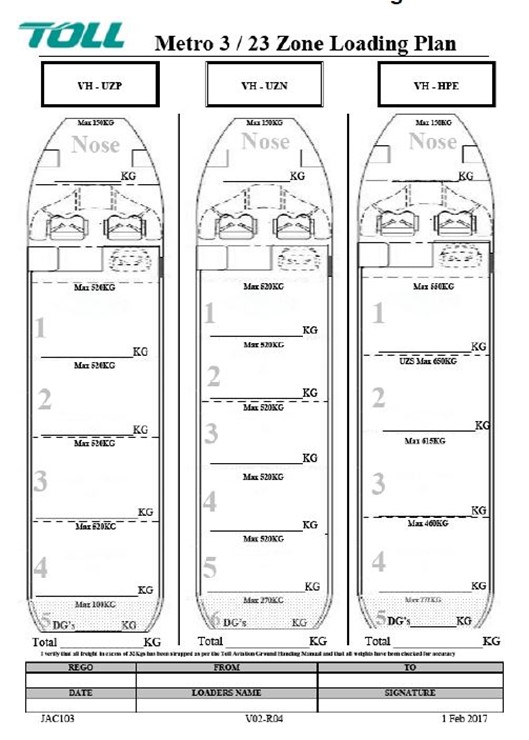
Source: Toll Aviation
Appendix B – VH-HPE load and trim sheet
Source: Toll Aviation
Appendix C – Centre of gravity (CoG) position (Rockhampton to Brisbane)
Source: Toll Aviation, annotated by the ATSB
Appendix D – Centre of gravity (CoG) position (Townsville to Rockhampton)
Source: Toll Aviation, annotated by the ATSB
Purpose of safety investigationsThe objective of a safety investigation is to enhance transport safety. This is done through:
It is not a function of the ATSB to apportion blame or provide a means for determining liability. At the same time, an investigation report must include factual material of sufficient weight to support the analysis and findings. At all times the ATSB endeavours to balance the use of material that could imply adverse comment with the need to properly explain what happened, and why, in a fair and unbiased manner. The ATSB does not investigate for the purpose of taking administrative, regulatory or criminal action. TerminologyAn explanation of terminology used in ATSB investigation reports is available here. This includes terms such as occurrence, contributing factor, other factor that increased risk, and safety issue. Publishing informationReleased in accordance with section 25 of the Transport Safety Investigation Act 2003 Published by: Australian Transport Safety Bureau © Commonwealth of Australia 2021 Ownership of intellectual property rights in this publication Unless otherwise noted, copyright (and any other intellectual property rights, if any) in this report publication is owned by the Commonwealth of Australia. Creative Commons licence With the exception of the Coat of Arms, ATSB logo, and photos and graphics in which a third party holds copyright, this publication is licensed under a Creative Commons Attribution 3.0 Australia licence. Creative Commons Attribution 3.0 Australia Licence is a standard form licence agreement that allows you to copy, distribute, transmit and adapt this publication provided that you attribute the work. The ATSB’s preference is that you attribute this publication (and any material sourced from it) using the following wording: Source: Australian Transport Safety Bureau Copyright in material obtained from other agencies, private individuals or organisations, belongs to those agencies, individuals or organisations. Where you wish to use their material, you will need to contact them directly. |