Investigation summary
What happened
On 20 October 2023 the pilot of a Cessna 208 aircraft, registered VH‑UMV and operated by Experience Co, was conducting parachute operations at Barwon Heads Airport, Victoria with 16 parachutists on board. Passing about 500 ft on climb, the pilot detected a partial power loss consistent with a previously‑encountered transient power reduction.
Expecting the power to return immediately, the pilot did not lower the aircraft’s nose to maintain airspeed. The airspeed continued to reduce until the stall warning horn sounded and, due to the low height, low engine power and low airspeed, the pilot attempted to conduct a forced landing. However, the aircraft collided with water before continuing onto the riverbank and ground for approximately 50 m before coming to rest.
The aircraft was substantially damaged, 6 of the parachutists received serious injuries, 8 sustained minor injuries, and 2 were uninjured. The pilot also sustained minor injuries.
What the ATSB found
The ATSB found that passing about 500 ft on climb, the power reduced likely due to abnormal activation of an engine torque and temperature limiting system. Expecting the power to return quickly and surge, and in preparation for turning off the system, the pilot moved the power lever aft to reduce the power setting and delayed lowering the aircraft’s nose to maintain airspeed, resulting in a stall warning and subsequent collision with water.
The ATSB also found that Experience Co’s engine power loss checklist instructed pilots to significantly reduce power in preparation for deactivating the engine limiting system, but did not specify a minimum safe height at which to do so. This increased the risk of a loss of control and/or ground collision.
Further, the ATSB found that the operator's weight and balance calculation for the accident flight did not include the bench seating weight or moment, and the loadmaster did not load parachutists in positions used for the calculation of the centre of gravity, therefore, although it did not contribute to the accident, the weight and balance was inaccurate for the intended flight. Additionally, the software used to calculate aircraft weight and balance did not provide a warning if individual aircraft zones were overloaded.
Finally, the ATSB found that Experience Co did not ensure sport parachutists received essential safety information about emergency exits, restraints and brace position, prior to take-off.
What has been done as a result
At the time of writing, Experience Co was re‑developing its sport skydivers safety video to include emergency procedures. Additionally, the following proactive safety actions have been taken:
- A safety communique was developed and circulated at each drop zone reminding parachutists to be seated in accordance with their manifested location.
- Chief instructors, drop zone safety officers and loadmasters were reminded of the loadmasters’ responsibilities to ensure parachutists were seated in accordance with the weight and balance calculation.
- Skydive Operations Manual was amended to clarify the loadmasters’ responsibilities.
- Additional training was provided for manifest staff.
- A fleet-wide audit was undertaken to ensure all aircraft had accurate basic empty weight figures.
- A prompt was added to the internal reporting software to confirm an entry has been made to the aircraft’s maintenance release when submitting a maintenance‑related internal safety report.
- Briefings that cover essential safety information about emergency exits, restraints, and brace position, are now required annually by sport skydivers.
- Additional pilot training relating to the single red line/torque and temperature limiter malfunctions has been developed and was scheduled to be delivered to all pilots.
- Emergency exit signs in all aircraft were being assessed for compliance and effectiveness, and updated if necessary.
- Engineering personnel have undertaken specialised TPE331 Powerplant and Systems training.
- Information circulars were provided to company pilots about the proper defect reporting requirements using the aircraft maintenance release.
- Experience Co was updating advice as to the altitude at which seatbelts must be worn.
- Experience Co has developed Cessna 208 and Cessna 208B aircraft flight manual supplements, which outline the carriage of 17 parachutists and 21 parachutists respectively.
- An additional support bracket has been designed to be fitted to the end of the bench seats in aircraft and will be installed once formally approved.
- A new engine power loss checklist was developed in cooperation with the supplemental type certificate (STC) holder to be followed at or above 1,000 ft above ground level.
The Australian Parachute Federation (APF) has taken the following safety action:
- The APF will ensure skydivers and pilots review their aircraft emergency procedures on a regular basis. Recommended topics are likely to include:
- general safety around aircraft
- hot loading
- door activation
- achieving correct restraint fitment
- emergency landings
- brace position
- emergency exit altitudes and which parachute to use
- communication during an emergency
- for coastal operations, life jacket use in a ditching.
- Each parachuting aircraft operator will conduct a thorough assessment of its aircraft to ensure single point restraints are properly installed, to prevent parachutists from moving outside their designated seating positions and to maintain the aircraft’s weight and balance.
- The APF will review global data on the use of dual-point restraints to gather insights from other national parachuting organisations regarding their experiences with this system.
- The APF examined aircraft flight manual wording of all aircraft currently conducting parachute operations in Australia to identify which aircraft would require a short-term CASA exemption to permit operations with the number of passengers onboard in excess of those able to occupy the normal seats under the type design. They identified 22 aircraft requiring an exemption, spanning 5 operators.
- The APF added the following statement to the participant waiver form: ’parachuting aircraft are not operated to the same safety standards as a normal commercial passenger flight’.
Finally, the Civil Aviation Safety Authority advised that it is developing the following:
- An exemption, for pilots or operators of parachuting aircraft who may be unable to comply with elements of the aircraft flight manual, is expected to be completed by mid‑2025.
- CASA stated that it was satisfied that reasonable steps had been taken by the APF to ensure that a level of safety, commensurate with the risks involved in the parachuting activities in which participants engage, was provided to those participants in the interim while the exemption was being developed.
- An amendment to the Civil Aviation Safety Regulations Part 21 Manual of Standards to specify the standards required for the modifications made to parachuting aircraft. This proposed action is expected to be finalised by the end of 2025.
- Additional guidance to support aircraft owners and operators seeking to make an approved modification.
Safety message
The ATSB research report Avoidable Accidents No. 3 – Managing partial power loss after take-off in single-engine aircraft provides information to assist pilots to maintain aircraft control in the event of an emergency or abnormal situation after take-off. The report prescribed initial actions to be considered including:
- Lower the nose to maintain the glide speed of the aircraft. If turning is conducted, keep in mind an increased bank angle will increase the stall speed of the aircraft.
- Maintain glide speed and assess whether the aircraft is maintaining, gaining or losing height to gauge current aircraft performance.
- Fly the aircraft to make a landing, given the aircraft’s height and performance, and the pre-planned routes for the scenario.
If time permits, moving the power lever through the full range may result in increased power available to climb and/or create the time to diagnose the issue.
The ATSB SafetyWatch highlights the broad safety concerns that come out of our investigation findings and from the occurrence data reported to us by industry.
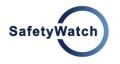
One of the safety concerns is reducing the severity of injuries in accidents involving small aircraft. This incident highlights the importance of passengers being appropriately briefed on the brace position and use of emergency exits. It also illustrates the higher injury risk associated with the carriage of parachutists, due to the increased number of occupants and inferior restraints compared to being secured in a certified seat.
The occurrence
Early on the morning of 20 October 2023, the pilot of a Cessna 208 aircraft, operated by Experience Co and registered VH-UMV, refuelled and inspected the aircraft in preparation for parachuting operations from Barwon Heads Airport, Victoria. No defects, including any fuel debris or contaminants, were identified.
The pilot’s first flight of the day was to carry 16 sport parachutists for a parachute jump from 15,000 ft. At about 0750 local time, the parachutists boarded the aircraft. The pilot recalled that the conditions were CAVOK,[1] with a light wind from the north. They taxied the aircraft to runway 36 for a northern departure.
A review of OzRunways[2] flight data, recorded at 5-second intervals, showed the aircraft commenced the take-off roll at 0757. The pilot reported moving the power lever forward until the engine reached 100% torque, and then reducing the power slightly during the take-off roll. Camera footage showed that the aircraft became airborne at 0757:22.
The pilot reported that, as the aircraft climbed and the airspeed increased, they retracted one stage of flap passing through 85 kt and another at about 95 kt. At 0757:47, climbing through about 400 ft, the aircraft reached its maximum recorded ground speed of 95 kt. The pilot reported that as the aircraft approached 500 ft above ground level and they reached for the flap lever to retract the last stage of flap, they heard a reduction in engine noise, and felt a deceleration.
The pilot initially associated the loss of power with activation of the torque and temperature limiter (TTL) (see the section titled Torque and temperature limiter), which they had previously experienced in that aircraft. Consistent with the previous TTL activation, the pilot expected the power to quickly return, and reported reducing power slightly to prevent the engine surging[3] as power was restored.
The reduction in engine power, combined with the climb pitch attitude, resulted in the airspeed reducing and activation of the stall warning horn. On hearing the stall warning, the pilot lowered the aircraft’s nose to reduce the angle of attack[4] and increase the airspeed.
At 0757:57 the aircraft reached the highest recorded altitude of about 700 ft at 88 kt ground speed and, 5 seconds later, had descended to 600 ft and the ground speed reduced to 71 kt, then to 69 kt 5 seconds later. This flight path was consistent with video camera footage of the aircraft’s flight path (Figure 1). At 0758:08 the ADS-B[5] data recorded a descent rate of 3,520 ft/m passing an altitude of approximately 400 ft.
Figure 1: VH-UMV flight path captured by the airport camera
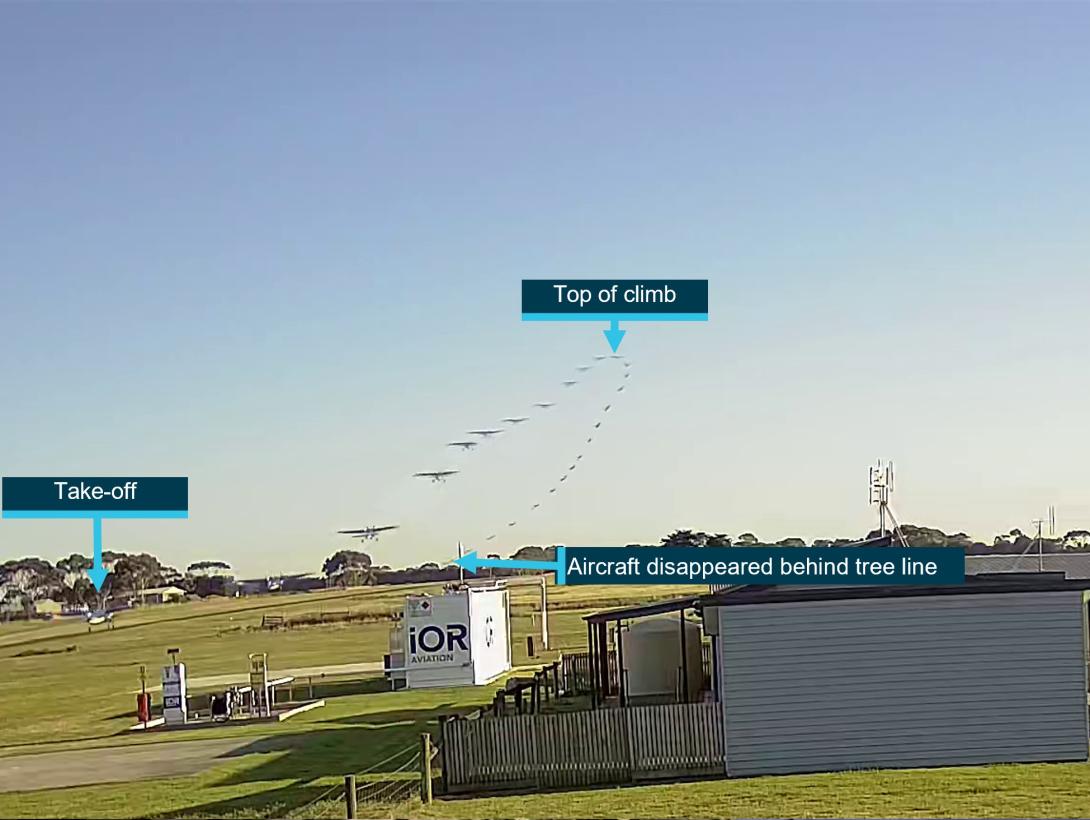
The ATSB combined multiple images together to show the flight path of the aircraft as captured by a local video camera. Source: Airport operator, annotated by the ATSB
The pilot reported that, as the aircraft descended, they observed the engine torque indication reducing through approximately 30% and attempted to switch off the TTL in accordance with the operator’s Engine Power Loss checklist. Due to the aircraft’s low height above the ground, and the pilot’s assessment that there was an engine issue, the pilot then selected a field in which to conduct a forced landing.
The pilot turned to the loadmaster[6] seated beside them and called out ‘gear-up’, to alert parachutists to be ready to exit the aircraft. In response, the loadmaster began directing parachutists to open the roller door, secure their harnesses, and brace for landing. The roller door was opened, but not secured in that position.
The pilot selected a forced landing location in a clearing beyond a river. However, less than 1 minute after becoming airborne and unable to maintain altitude, the aircraft impacted the water short of the clearing, resulting in water entering the cabin and forcing the unsecured roller door closed. The aircraft continued onto the riverbank where the main landing gear detached, then travelled along the ground for about 50 m before coming to rest (Figure 2).
The pilot sustained minor injuries, 6 parachutists sustained serious injuries, 8 sustained minor injuries and 2 were uninjured. The aircraft was substantially damaged.
Figure 2: VH-UMV flight path
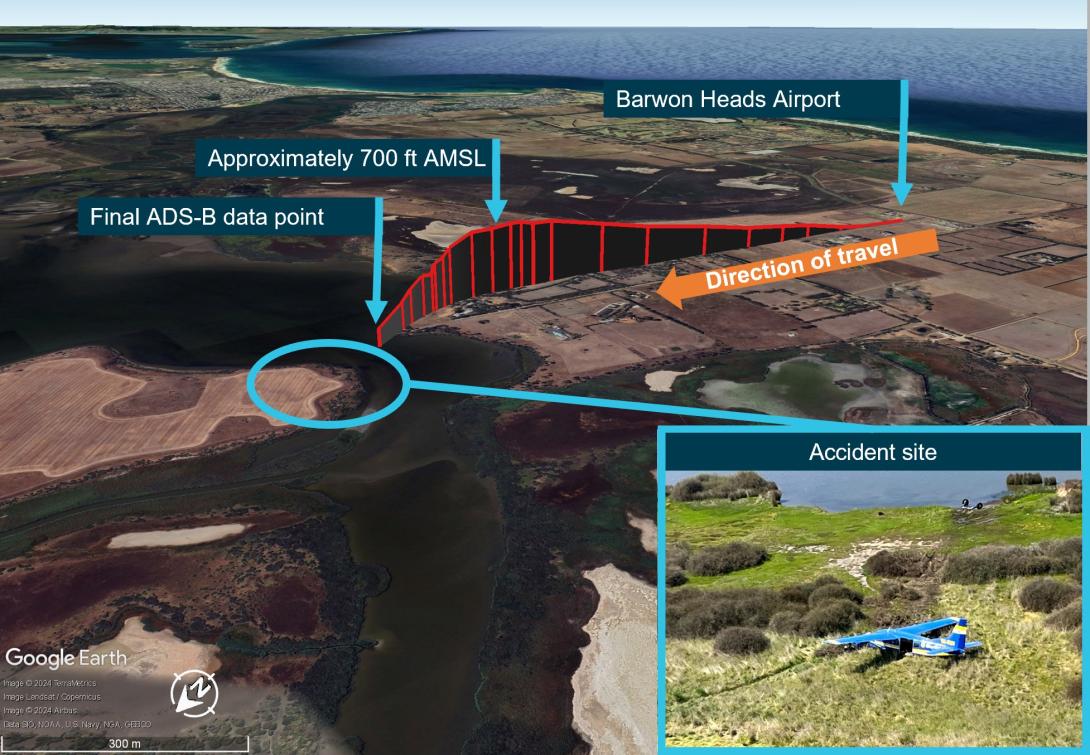
Source: ADS-B exchange flight data overlaid on Google Earth and image of accident site provided by operator, annotated by the ATSB
Context
Pilot information
The pilot held a commercial pilot licence (aeroplane) and a current class 2 aviation medical certificate. On 19 April 2023, the pilot completed their gas turbine engine design feature endorsement and single engine aircraft flight review in a Cessna 208 aircraft.
At the time of the accident, the pilot had accrued approximately 220 hours of total flight experience, which included 38 hours on the Cessna 208 aircraft type. Of those hours on type, 36 had been accrued in the previous 90 days.
The pilot reported that they were familiar with VH-UMV, having conducted multiple flights in it prior to the accident flight. The pilot was also aware of operator-specific engine operating limitations for VH-UMV, and reported having previously experienced an engine surge at 5,000 ft (see the section titled Engine surging).
Aircraft information
Certification details
The Cessna Aircraft Company 208 (C208) is an all-metal, high-wing aeroplane with tricycle landing gear and designed for general utility usage. The aircraft type certificate data sheet (TCDS) A37CE described the C208 as an ‘11-place closed land monoplane’, and under the heading ‘No. of seats’, provided a centre of gravity range for seating for one or 2 pilot seat locations and referenced the current Pilot’s Operating Handbook (POH) and United States (US) Federal Aviation Administration (FAA) Airplane Flight Manual (AFM) for passenger seat arrangements for seats 3 to 11.
The C208 POH Section 2 – Limitations – Maximum passenger seating limits stated that up to 11 seats, including the pilot’s seat/s, may be installed.
VH-UMV, serial number 20800077, was manufactured in 1986 and first registered in Australia in 2005. At that time, the aircraft was issued 2 certificates of airworthiness, one for normal category[7] operations and one for restricted category[8] operations for the purpose of carrying people for parachute jumping.
Operating in the restricted category required several conditions, including removal of the cabin seats, compliance with a specific engineering order and readily visible restricted category placards, none of which were in place on the accident flight. Additionally, under Civil Aviation Safety Regulations (CASR) current at the time of the accident (CASR 91.845, 91.025, 135.030), aircraft operating in the restricted category were not permitted to conduct air transport operations (carriage of passengers or cargo for hire or reward).
In 2017, the aircraft’s Pratt & Whitney PT6A-114 gas turbine engine was replaced with a Honeywell International Incorporated TPE331-12JR-704TT gas turbine engine that drove a 4‑bladed, constant‑speed, full‑feathering,[9] reversible[10] Hartzell HC-E4N-5KL propeller with hydraulically‑operated variable‑pitch control. The engine modification was completed under the Texas Turbine Conversions supplemental type certificate (STC) SA10841SC, with an associated AFM Supplement. Under the heading ‘Maximum passenger seating limits’, the AFM supplement stated ‘No changes’ (from the C208 AFM).
The aircraft was also modified in accordance with STC SA01180SE, which increased the original maximum take-off weight from 3,628 kg to 3,792 kg. Both STCs were approved by the US FAA and therefore accepted in Australia and taken as having been issued by CASA in accordance with CASR Part 21 regulation 21.114.
Three modifications made to VH-UMV and other aircraft in the operator’s fleet were completed under engineering orders in accordance with the CASR Part 21 regulation 21.437 Grant of modification/repair design approvals—grant by authorised person or approved design organisation:
- ESE-C208-25-001—Rework of interior for parachute operations
- ESE-C208-25-007—Installation of parachute bench seating
- ESE-C208-95-003—Installation of Go-Pro cameras.
Torque and temperature limiter
VH‑UMV was fitted with a switch‑activated torque and temperature limiter (TTL) system designed to prevent these parameters exceeding specified limits. Where an exceedance of the allowable torque or exhaust gas temperature (EGT) was detected, the TTL computer restricted fuel flow to the engine. The maximum allowable fuel reduction of a normally-functioning bypass was about 68 L/hour (125 lbs/hour), resulting in a reduction of the torque output from 100% to about 62% (due to the approximate 25% reduction in fuel flow).
Texas Turbine Conversions advised that, when functioning normally, the system would maintain the lower of the allowable torque or EGT limits and if the TTL bypassed the maximum allowable fuel, it would be felt immediately. In that case, the appropriate pilot response was to switch off the TTL.
The aircraft’s engine monitoring system included a single red line (SRL) controller, associated with the EGT limit. Like the TTL, the SRL was switch‑activated and deselection of the SRL also deactivated the TTL.
The allowable EGT limit was dependent on the phase of flight. Specifically, the operating margin from the EGT limit in the climb phase was reduced in the cruise phase. The phase was dependent on the position of the speed lever. Therefore, if the speed lever was moved aft during take-off or climb, the EGT limit also reduced and could result in activation of the TTL. The operator reported that the speed lever was fully forward throughout the short flight, and therefore the climb EGT limit applied.
Operating limits
The AFM supplement for the Honeywell engine specified operating limits. With the SRL and TTL on, those limits included a maximum EGT of 650 °C, maximum 100% torque and maximum of about 101% RPM during take-off and climb. The supplement also provided an EGT table with limits for operating with the SRL off or inoperative, or ‘manual mode’. The limits were provided for operating at 100% RPM or 96% RPM based on the outside air temperature in 5 °C increments from −60 to +60 °C.
The AFM defined take-off power as the lower of 100% torque or 650 ºC EGT (SRL ON), whichever is reached first at 100% engine RPM.
Engine surging
On 17 October 2023, the pilot submitted an internal safety report relating to an uncommanded engine surge, which they experienced at an altitude of approximately 5,000 ft. The pilot report stated:
Torque roll back for a split second, noticeable reduction in power and deceleration.
The pilot reported reducing the power then slowly increasing it while monitoring engine parameters in response to the event.
Although not recorded on the aircraft’s maintenance release (MR),[11] reportedly due to their transient nature, pilots submitted 7 other internal safety reports between July and October 2023 of engine surging in VH‑UMV, assessed as being due to the TTL.
A review of maintenance recorded in VH-UMV’s engine logbook for the previous 12 months showed that the TTL controller was replaced ‘for fault isolation’ following the first reported surging occurrence on 3 April 2023. A further logbook entry on 18 September 2023 recorded that the EGT harness was replaced in response to reported engine surging at take-off power.
The engine surging safety reports indicated troubleshooting test flights were also conducted. A series of test flights on 7 September 2023 was able to replicate the previously‑reported surging. In addition, a test flight following the EGT harness replacement noted that the surging was still present. One of the experienced surges resulted in a torque value of 62% and fuel flow reduced by approximately 72 L/hour (128 lbs/hour). The MR current at the time of the accident identified that the aircraft operated over 90 flights prior to the next reported surge event on 17 October 2023. On that day, the aircraft operated 6 flights, and one surge occurrence was reported. According to the MR, 12 flights were conducted over the next 2 days (18–19 October), with no reports of engine surging submitted. However, the ATSB was also advised of an engine surge on 18 October, which was not recorded.
The MR current at the time of the accident recorded 257 flights over 3 months, during which there were 6 reported surging events. That frequency illustrated the intermittent nature of the anomaly, which likely hindered troubleshooting.
As a result of the internal reports, on 21 July 2023, pilots were advised to operate VH-UMV under a set of unique operating conditions to avoid the TTL scheduling a significant bypass of fuel and subsequent notable drop in available power. These were limitations of 95% torque and 640 °C EGT.
A review of the operator’s safety reports also identified that surging events were reported on 3 other company aircraft. For those aircraft, maintenance actions rectified the cause of each event and there were no subsequent surging events reported.
Minimum equipment list
Experience Co’s minimum equipment list (MEL) specified permissible unserviceable items with which the aircraft was permitted to operate temporarily under the stated procedures, conditions and limitations. The MEL included that both the SRL computer system and TTL ‘may be inoperative provided inoperative SRL system procedures and limits are observed’. In that case, it was also required that an MEL placard be fitted adjacent to the TTL or SRL switch for the inoperative system/s. There was no MEL placard for the TTL nor was it listed as inoperative at the time of the accident.
Engine power loss checklist
The Texas Turbine Conversions AFM supplement provided checklists for engine failures, but not for partial engine power loss. The operator’s ‘Engine Power Loss’ checklist for the C208 with the Honeywell engine (Figure 3), required pilots to first control the aircraft by moving the elevator control forward to lower the aircraft’s nose if climbing. After completing initial checks, if the RPM was above 60% or the engine was surging, the pilot was to move the power lever to ½ inch (12.7 mm) forward of the flight idle position, in preparation for turning off the TTL, so as not to produce a transient exceedance of the EGT.
Figure 3: Engine power loss checklist
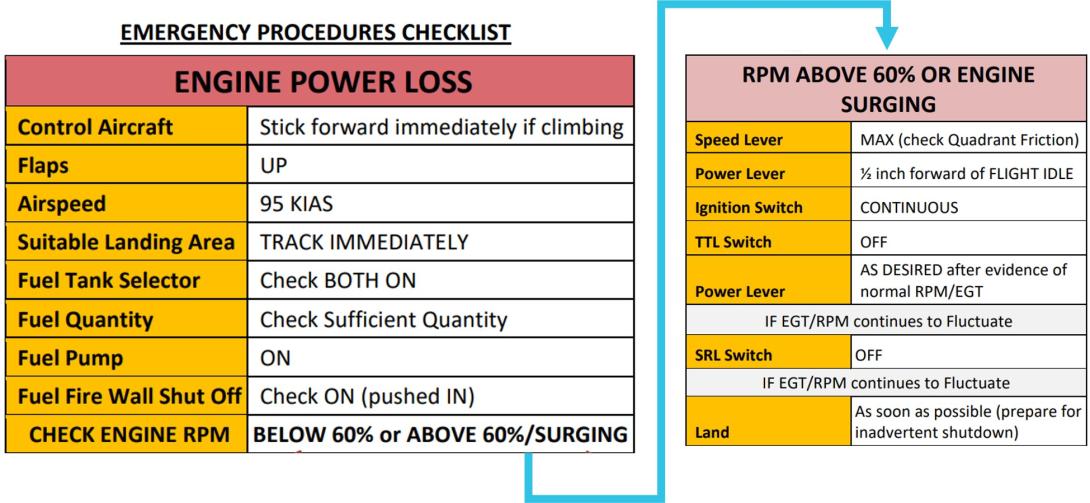
Source: Aircraft operator
Weight and balance
Aircraft moment arms
To enable calculation of the aircraft’s weight and balance, the C208 POH included a 2-place seating option, which divided the cabin into 7 zones (zones 0–6) (Figure 4). The flight manual supplement for the Texas Turbine Conversions STC did not include changes to the zones or seating configuration, therefore the POH applied.
Figure 4: Cessna 208 Pilot’s Operating Handbook seating configuration
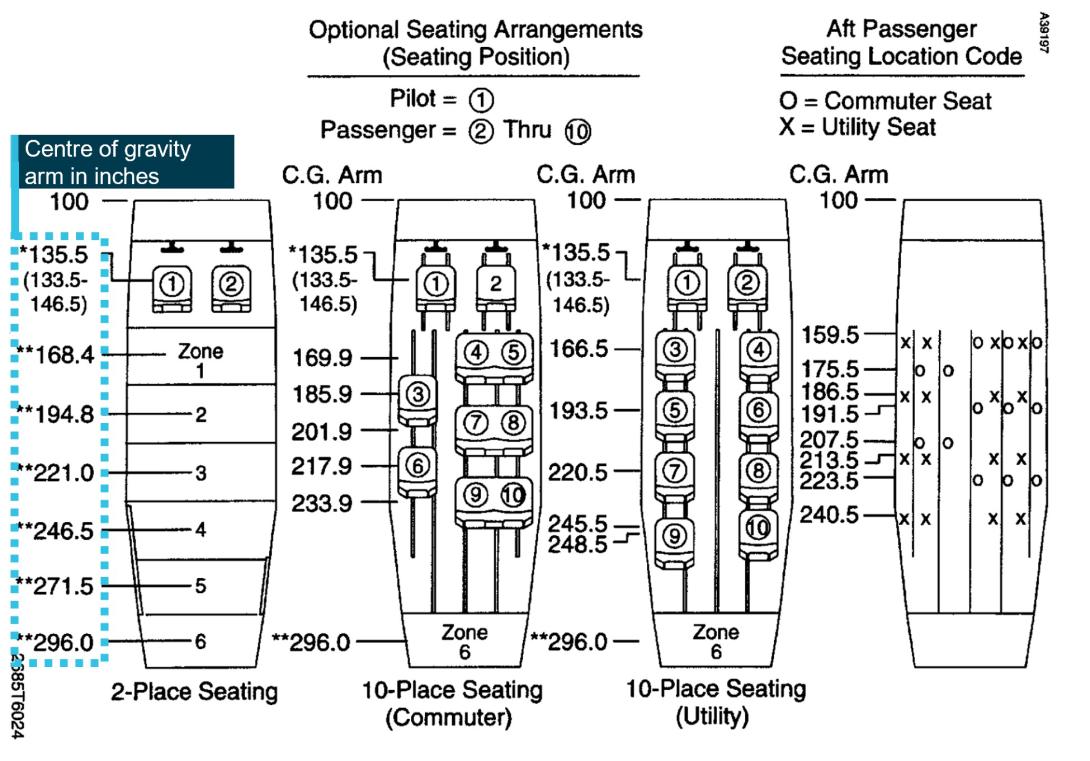
Source: Cessna 208 Pilot’s Operating Handbook, annotated by the ATSB
Accident flight weight and balance
Prior to departure, a member of the parachuting operations team calculated the weight and balance for the proposed flight using the IBIS Technology flight planning module software (Table 1).[12] The moment arms from the POH were used for the calculations. Zone 6 was not used.
Table 1: Planned weight and balance for accident flight
Item | Arm (mm) | Weight (kg) | Moment (kg-mm) |
Aircraft basic empty weight | 4,181 | 1,889 | 7,897.909 |
Fuel | 4,680 | 272.152 | 1,273.672 |
Zone 0 [1] | 3,442 | 272 | 936.142 |
Zone 1 | 4,277 | 218 | 932.386 |
Zone 2 | 4,948 | 318 | 1,573.464 |
Zone 3 | 5,613 | 173 | 971.049 |
Zone 4 | 6,261 | 404 | 2,529.444 |
Zone 5 | 6,896 | 173 | 1,193.008 |
Total | 3719.152 | 17,307.075 | |
Centre of gravity | 4,653 | ||
The calculated weight and balance resulted in a take-off weight of approximately 3,719 kg and the aircraft’s centre of gravity located at 4,653 mm aft of the datum. To remain inside the operating limitations, the maximum allowable weight was 3,792 kg. Additionally, the aircraft needed to remain within the centre of gravity envelope, which had an aft limit of 4,680 mm and the forward limit varied with the operating weight. Each zone had a maximum allowable weight limit, and the maximum for zone 0 was 159 kg. However, the calculation software did not provide a warning to notify the user a zonal limit had been exceeded.
Information provided by the parachutists included the position they were seated at the time of the accident. Those positions did not match the original seating positions on the planned weight and balance sheet provided to the pilot prior to departure. The operator calculated a revised weight and balance based on the probable parachutist seating positions, which moved the aircraft’s centre of gravity 5 mm aft, although still within the allowable envelope (Table 2). It also showed that zone 0 was under the allowable weight limit.
Table 2: Revised weight and balance for accident flight
Item | Arm (mm) | Weight (kg) | Moment (kg-mm) |
Aircraft basic empty weight | 4,181 | 1,889 | 7,897.909 |
Fuel | 4,680 | 272 | 1,272.960 |
Crew seat | 3,442 | 92 | 316.664 |
Zone 0 | 3,472 | 80 | 277.760 |
Zone 1 | 4,277 | 349.4 | 1,494.384 |
Zone 2 | 4,948 | 271.4 | 1,342.887 |
Zone 3 | 5,613 | 334.4 | 1,876.987 |
Zone 4 | 6,261 | 197 | 1,233.417 |
Zone 5 | 6,896 | 233 | 1,606.768 |
Total | 3,718.2 | 17,319.746 | |
Centre of gravity | 4,658 |
Aircraft basic empty weight
A weigh of VH‑UMV on 17 October 2017 identified that the aircraft’s basic empty weight was 1,889 kg in the single pilot seat configuration (Figure 5).
Figure 5: VH-UMV configuration on date of reweigh
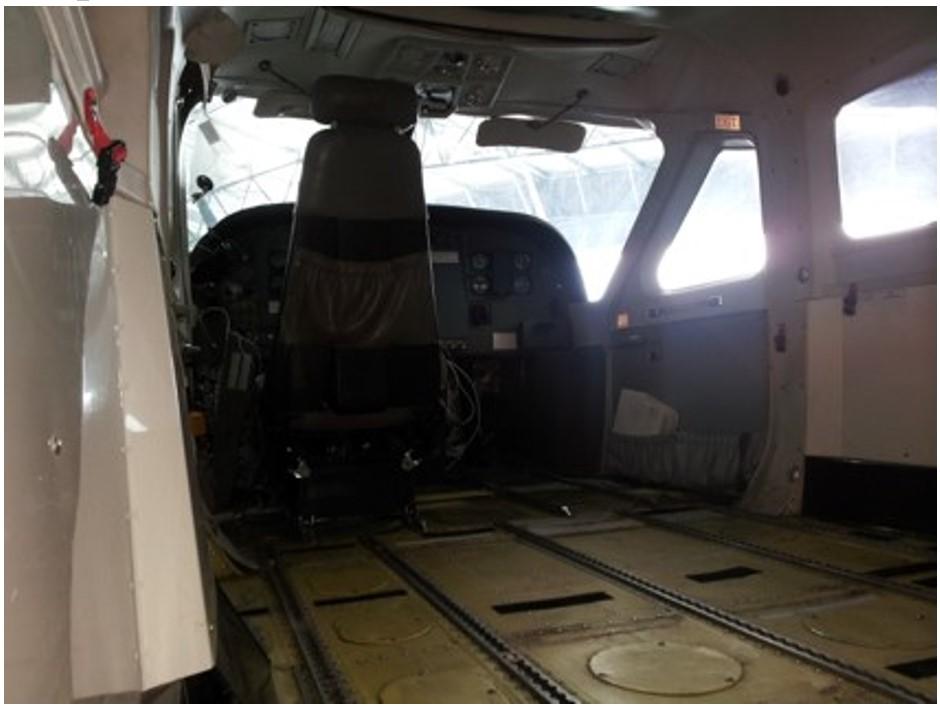
The image meta-data showed the image was taken on 17 October 2017 – the reweigh date. Source: AeroWeigh.
The aircraft seating configuration at the time of the accident is shown in Figure 6.
Figure 6: VH-UMV cabin seating arrangement
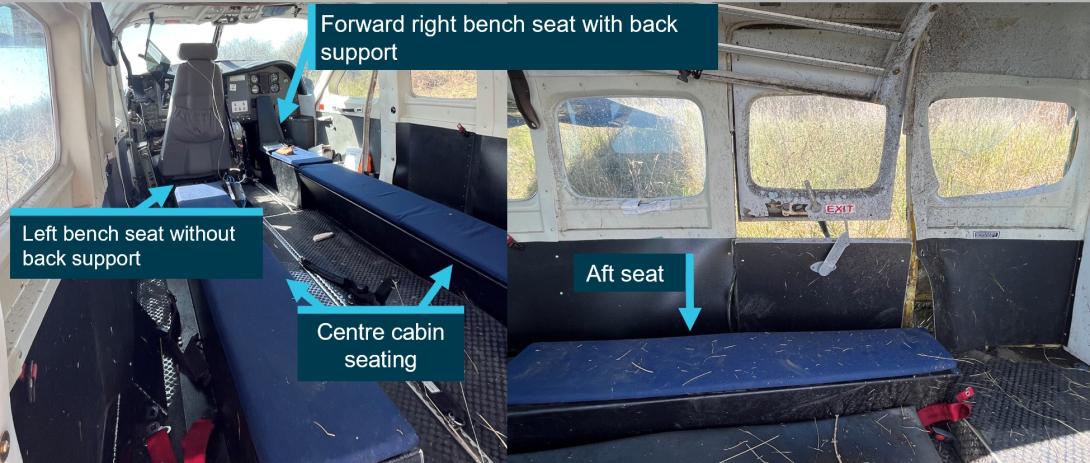
Source: Aircraft operator, annotated by the ATSB
The basic empty weight of the aircraft did not include the flooring, or the 36 kg bench seating installed under engineering order ESE-C208-25-007. The engineering order provided the moment arms and weights shown in Table 3.
Table 3: ESE-C208-25-007 Parachute bench seating options – bench seat weight and arm
Item | Arm (mm) | Weight (kg) |
Forward seat & backrest right-hand side only – option 2, without oxygen bottle mount. | 3,556 | 7.82 |
Centre cabin bench seats both left-hand and right-hand sides (2 x 10.92 kg) | 5,003 | 21.84 |
Aft bench seat right hand side only | 6,553 | 6.36 |
Total of unaccounted weight for bench seating | 36.02 |
Using the operator’s revised weight and balance calculation that reflected the likely positions of the parachutists, and the additional weight of the bench seating, the ATSB determined the probable take-off weight was 3,754 kg and the centre of gravity was 8 mm aft of the originally calculated centre of gravity (4,661 mm).
The operator subsequently weighed the aircraft’s jump mat, single point restraints, rubber matting, and portable oxygen tank. The total of these items was 30.2 kg, increasing the probable take-off weight to 3,784 kg.
Weight and balance implications
Regarding the importance of accurate weight and balance, the FAA Pilot’s handbook of aeronautical knowledge stated:
An overloaded aircraft may not be able to leave the ground, or if it does become airborne, it may exhibit unexpected and unusually poor flight characteristics.
Changes of fixed equipment have a major effect upon the weight of an aircraft. The installation of extra radios or instruments, as well as repairs or modifications, may also affect the weight of an aircraft.
Loading in a nose-heavy condition causes problems in controlling and raising the nose, especially during take-off and landing. Loading in a tail-heavy condition has a serious effect upon longitudinal stability and reduces the capability to recover from stalls and spins. Tail heavy loading also produces very light control forces, another undesirable characteristic. This makes it easy for the pilot to inadvertently overstress an aircraft.
Recorded data
The ATSB obtained OzRunways and third-party ADS-B recorded data for the accident flight. That data was compared with flight data for the flight conducted by the same pilot in the same aircraft on 17 October 2023, which was the day the pilot reported engine surging at about 5,000 ft. The comparison did not show significant performance difference from take-off to about 500 ft between the 2 flights.
Although the aircraft had an engineering order to fit GoPro cameras, they were not in place for the accident flight. The operator reported that these were only used during the creation of promotional footage and not during day-to-day operations. There was also no video footage from inside the aircraft, but the airport operator provided video footage from cameras located at the airport. One of those cameras recorded the accident flight footage (Figure 1) and provided audio for analysis.
The recorded audio included the aircraft noise and the nearby road and wind noise. The camera was stationary, therefore as the aircraft departed its sound signature reduced. Analysis of the audio conducted by Honeywell found that the engine RPM was approximately 99% throughout the take-off and initial climb. However, the engine noise was not discernible from the background sounds recorded at the time of the reported engine surge.
Site and aircraft examination
Site assessment
The ATSB did not attend the accident site, but the aircraft operator and Victoria Police attended shortly after the accident and provided the ATSB with photos of the aircraft and cockpit. A review of the images showed that the:
- flaps were fully retracted
- power lever was in the max reverse position
- speed lever was in the minimum position
- condition lever was in shutoff/feather position.
Those positions were consistent with the pilot’s reported actions to secure the engine after the impact. Additionally, one image appeared to show the TTL switch ON and the SRL switch OFF, indicating that the pilot may have inadvertently selected the SRL OFF instead of the TTL.
Engine and accessories assessment
The aircraft’s engine was recovered by the operator and sent to the Honeywell Investigation Laboratory in the US. On behalf of the ATSB, the US National Transportation Safety Board (NTSB) arranged independent oversight of the engine examination that was conducted between 3–5 January 2024.
Honeywell and the NTSB subsequently oversighted inspection and testing of removed components at various technical facilities. The Honeywell investigation report, provided to the ATSB and aircraft operator, detailed the observations and findings from the engine and associated component examinations, as follows.
The SRL and TTL were tested on 27 February 2024. Although some test points were not within the specified test tolerances, both units were found to be functional. However, further examination of the fuel bypass valve conducted by Woodward Inc. on 5 November 2024, resulted in a maximum bypass flow of 110 L/hour (194.5 lbs/hour), which exceeded the maximum flow test range of 68–74 L/hour (120–130 lbs/hour). At take-off power, a normal fuel flow was approximately 312 L/hour (550 lbs/hour). Therefore, if a bypass of 110 L/hour occurred during the accident flight with take‑off power set, the fuel flow would have reduced by about 35%.
Initial inspection of the fuel bypass valve’s outer casing revealed impact markings (Figure 7). When the protective cover plate was removed, the pole associated with the impact side was found in contact with the armature. When a 4.5 kg (10 lb) force was applied to each of the poles, there was no visible movement. The armature was cut away from the spade to determine if the armature screws were loose. The armature screws were found to be suitably tightened, and the armature was not bent.
The findings of the inspection showed the out‑of‑limit test results were due to impact damage resulting from the accident. As such, the higher fuel bypass identified in the test was not considered to be contributory.
Figure 7: Fuel bypass valve
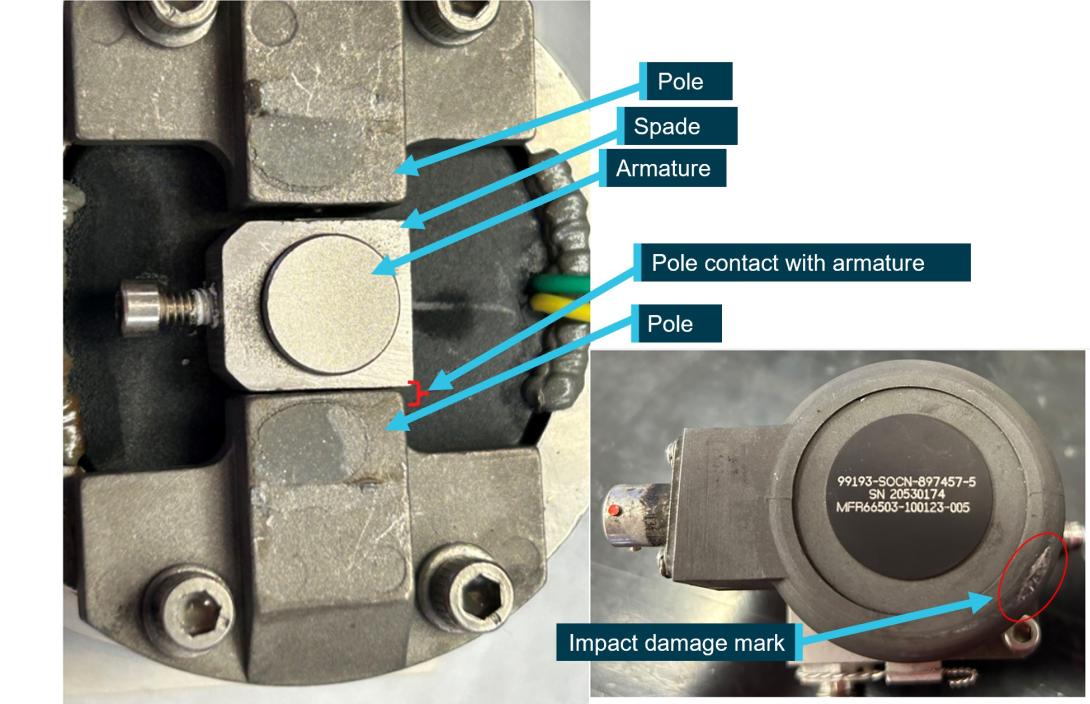
Source: Woodward Inc, annotated by the ATSB
The fuel control unit (FCU) was examined and tested between 26–27 March 2024. The FCU tested values were either within specified ranges or marginally outside of tolerance limits for new or overhauled components. The test results may have been affected by procedures for adjusting an in-service FCU defined in the engine maintenance manual.
On 11 January 2024, a computed tomography scan of the propeller governor was conducted by Honeywell. Between 26–27 March 2024, the propeller governor was subject to functional testing by the manufacturer. While there were abnormalities identified with the magnetic pickup voltage and RPM maximum/minimum speeds, no contributing anomalies were noted. It was then disassembled, inspected and reassembled, followed by an additional functional test. The results from both functional tests were consistent with expected parameters of various operational modes.
The fuel pump was functionally tested on 2 May 2024, and found to be operating within specifications.
The Honeywell investigation found that the damage was indicative of an engine that was rotating and operating at the time of impact. It found no pre-existing condition that would have prevented normal operation.
Photos of the propeller were provided to Hartzell for analysis. As the propeller was of composite material, on impact it fractured into parts rather than deforming the propeller shape. From the limited fragments that were retrieved, Hartzell concluded the blades were likely rotating under low power at the time of the accident.
The ATSB considered whether the pilot had moved the power lever to beta range, reversing the propeller, but Hartzell found it likely that the propeller was forced to a low pitch angle during the initial impact.
Carriage of parachutists
Cabin configuration
The aircraft was configured for skydiving such that:
- the cargo door was replaced with a vertical sliding door (made of nylon, polycarbonate and aluminium)
- the passenger seats and lap belts were removed
- bench seating and 17 single point restraints were installed.
The restraints attached to the parachute harness and parachutists could be seated either on the bench seating or floor, facing toward the aft of the aircraft.
The associated flight manual supplements for the parachute configuration were:
- cargo doors removed kit
- in-flight openable cargo door
- in-flight opening of doors
- oxygen system
- skydiving jump light
- external mounted GoPro cameras.
Aircraft modifications
Classification of design changes
CASA stipulated regulations for modification of an aircraft from the original manufacturer specifications. CASA Advisory Circular (AC) 21-12 Classification of design changes provided different processes for modifying aircraft, depending on the type of change being made. These changes were classified as either major or minor.
A minor modification was anything that was not considered to be a major modification and could be completed by a CASA-authorised person under CASR Part 21.M. Any modification with a significant effect on airworthiness – structural, weight and balance, systems, operational or other characteristics, were classified as major. Additionally, any alteration to the type certificate datasheet was classified as a major change.
A major modification was further classified into a substantial change or a significant change. A significant change required a supplemental type certificate application to be completed with CASA’s involvement. A substantial change required a new type certificate application, which also involved CASA. The AC provided the following example of a significant change to a small aircraft:
Changes in types and number of emergency exits or an increase in maximum certificated passenger capacity.
The notes associated with that example were:
Emergency egress certification specifications exceed those previously substantiated. Invalidates assumptions of certification.
CASA advised that the modifications would be considered a major change if the number of persons was increased above that permitted by the aircraft type certificate data sheet. This was consistent with the US FAA Advisory Circular 105-2E – Sport Parachuting, which included:
The approved number of skydivers that each aircraft can carry for parachute operations will most commonly be found on FAA Form 337, Major Repair and Alteration (Airframe, Powerplant, Propeller, or Appliance), used for field approvals, or an aircraft Supplemental Type Certificate (STC).
In its submission to the draft report, CASA advised that it considered that the legal basis for conducting parachuting flights with a greater number of passengers than the TCDS specified may be met if the aircraft was modified appropriately by a suitably authorised person and there was an associated aircraft flight manual supplement.
In determining whether the parachuting configuration modification was major or minor, the CASA‑authorised design engineer assessed that it was minor as it had no significant effect on:
- structure
- cabin safety
- flight
- performance or function of:
- systems
- propellers
- engines or powerplant installation
- environment.
The engineer also assessed that the design did not:
- alter airworthiness or operating limitations
- require an adjustment of the type-certification basis
Technical assessment of modifications
Aircraft modifications must meet the airworthiness requirements of the aircraft’s certification basis. According to the type certificate data sheet, VH-UMV was certified under FAR 23 amendments 23-1 through 23-28. Modifications were required to comply with standards from that or subsequent amendments. Technical assessments of the modifications detailed in the engineering orders nominated FAR 23 amendment 62 as the certification basis for the parachuting configuration modifications, including the roller door, bench seating and oxygen system.
The technical assessments included a design compliance matrix, with the following key comments by the design engineer of relevance.
Weight and balance
The engineering order was to include that:
It is the operator’s responsibility to accurately update the aircraft’s load data sheet to reflect the quantity and positioning of oxygen bottles as this may vary dependant on the number of parachutists on a given high altitude drop.
Structure
Standard aircraft hardware is used to secure items of mass installed as part of the parachute fit out modifications. This modification does not alter or effect the strength of the aircraft structure to support all normal aircraft loads. All materials & fasteners used as part of this design package have been selected to have adequate structural properties for their intended use.
Flight loads
The document package includes instructions to ensure the Cessna standard Flight Manual Supplement for operations with the cargo door open/removed is in the Flight Manual.
Oxygen
The engineer assessed the oxygen requirements for conducting flights above 14,000 ft in an unpressurised aircraft, stating:
…The operators (max) occupant capacity for the 208 & 208B model aircraft is x16 & x20 occupants respectively. As such these aircraft must be fitted with a minimum of 2x oxygen dispensing face masks if more than x15 occupants are carried…
Emergency landing conditions
Engineers assessed that the oxygen cylinder restraints were adequate in all load cases. They also rated the seats to at least 170 lb (77 kg) as required by FAR 23.785.
Regarding the installation of the oxygen bottle the engineers provided the following:
…the seat base and surrounding structure is adequate to support the small increase in weight due to the installation…there is no risk of the installation coming loose and inflicting serious injury on the cabin occupants.
Control systems
The design package included instructions for the removal of the copilot control wheel and column in accordance with the aircraft maintenance manual, to configure the aircraft for parachuting operations. There was no change to the design or functionality of the pilot's primary flight controls.
Doors
The number and arrangement of doors was not altered by the modifications. Regarding ‘vibration and buffeting’, the parachute door had a proven service history, with no reported issues since the design was originally implemented in June 2012. Further, the roller-style parachute door was commonly installed on parachuting aircraft and Cessna had an approved roll-up door as part of the production standard design.
Operation of the roller door was ‘simple and obvious’, easily operable from inside and outside the aircraft. The door was held in place by gravity and friction and could not be accidentally opened. Decals specific to the operation of the parachute roller door were installed.
Seats and restraints
The single point restraints for the parachutists were previously approved for use by ‘Air Safety Solutions’.
The aircraft certification did not require dynamic testing of the seats and, although the bench seating was not tested, the design engineer referenced FAA AC 105-2E Sport parachuting, which stated:
- Straddle benches can offer more occupant crash protection than floor seating since they can be designed to provide significant vertical energy absorption.
Emergency exits
For reference, FAR 23.807 required:
In addition to the passenger-entry door, for an airplane with a total passenger seating capacity of 16 through 19, three emergency exits, as defined in paragraph (b) of this section, are required with one on the same side as the passenger entry door and two on the side opposite the door.
(b) Emergency exits must be movable windows, panels, canopies, or external doors, openable from both inside and outside the airplane, that provide a clear and unobstructed opening large enough to admit a 19-by-26-inch ellipse. Auxiliary locking devices used to secure the airplane must be designed to be overridden by the normal internal opening means. The inside handles of emergency exits that open onward must be adequately protected against inadvertent operation. In addition each emergency exit must:
- be readily accessible, requiring no exceptional agility to be used in emergencies;
- have a method of opening that is simple and obvious;
- be arranged and marked for easy location and operation, even in darkness;
- have reasonable provision against jamming by fuselage deformation; …
(c) The proper functioning of each emergency exit must be shown by tests
The design engineer commented that there was no change to the number of emergency exits and that the ‘steps, handles, bench seats etc. installed for this modification met the requirements for egress in an emergency as specified by this regulation’. Additionally, as there was no change to the door functionality or positioning, no additional emergency testing was required.
The unmodified rear right passenger door met the requirements of the regulation in that a 19" x 26" (48 x 66 cm) ellipse may be passed through the door un-obstructed. However, the rear right bench seat extended across the door at a height of 10” (25.4 cm). The design engineer commented that access to the door handles/operation and decals was not obstructed, and no exceptional agility was required to exit through that door in an emergency.
The roller door was also required to meet the emergency exit criteria, including ‘reasonable provisions against jamming by fuselage deformation’, and that ‘proper functioning of each emergency exit must be shown by tests’. However, this was not documented.
The parachuting configuration detailed in the engineering orders enabled seating and single-point restraints for 17 parachutists, in addition to the fitted pilot seat and 5-point restraint. The design engineer had not intended to explicitly increase the seating capacity above the 11 specified in the TCDS, as the number of parachutists that could be carried was an operational consideration. The design engineer provided comment on a technical assessment provided to CASA in 2017 regarding maximum passenger seating configuration, that the aircraft operator’s understanding was:
it is the pilots [sic] responsibility to ensure the aircraft is loaded within the weight and balance and centre of gravity limitations of the aircraft at all times. From these calculations the maximum safe number of parachutists to carry on the Cessna 208 Caravan is 17...
Regulatory requirements
Part 105 of the CASR came into effect in December 2021 and set out the operational requirements for aircraft used to facilitate parachute descents. Civil Aviation Order (CAO) 20.16.3 paragraph 15 Carriage of parachutists was in force at the time of the accident, and the following regulations were relevant to the aircraft parachuting configuration:
- CASR 91.200 Persons not to be carried in certain parts of aircraft permitted a person to be carried in ‘a part of the aircraft that is not designed to carry crew members or passengers’, if the aircraft was being operated for a parachute descent and met the Part 105 MOS.
- CAO 20.16.3 required parachutists to wear a seatbelt, shoulder harness or approved single point restraint (except when about to jump). Similarly, CASR Part 105 section 105.105 required parachutists who were not flight crew to be provided with a seatbelt, shoulder harness or approved single-point or dual-point restraint.
The Part 105 Manual of Standards (MOS) came into effect on 2 December 2023, 44 days after the accident, and specified requirements in greater technical detail. CASA advised that the Part 91 Manual of Standards will be amended to remove ambiguity about approved passenger restraints being permitted in lieu of seatbelts.
Maximum passenger seating configuration
In drafting CASR Part 105, the number of parachutists that could be carried was a significant point of discussion between CASA and the parachuting industry.
In 2006, CASA proposed Civil Aviation Safety Regulation 105.140 paragraph 3.5.20 which stated:
Proposed CASR Part 105 seeks to provide clarity to the parachuting industry that operating a parachuting aircraft with more parachutists than the normal published aircraft seating capacity in passenger-carrying operations is acceptable, provided weight and balance and other manufacturer’s limitations for the aircraft are observed.
A subsequent notice of proposed rulemaking indicated that the following may be included in the proposed CASR Part 105.140 – Number of parachutists in aircraft:
(1) A parachuting aircraft may carry more occupants than the maximum number that is specified in the aircraft’s flight manual only if the aircraft is loaded in accordance with the following requirements and limitations set out in the flight manual or the certification data for the aircraft:
(a) the weight and balance requirements; and…
When the above proposed rule was not incorporated into draft CASR Part 105 or MOS, as detailed in meeting minutes of the technical working group that reviewed the 30 August 2022 draft Part 105 MOS, they proposed to meet with CASA’s Airworthiness and Engineering Branch to discuss:
possible options for parachuting aircraft to operate with seats removed, to carry more passengers than currently permitted by the aircraft’s type certificate or flight manual and regulatory support mechanisms for modifications (doors, handles etc.) that support safe parachuting operations.
The ATSB was unable to determine whether this discussion took place, however no related changes were incorporated into the regulations or MOS, noting that the MOS had not come into effect at the time of the accident.
In response to the ATSB’s request for clarification of CASA’s expectation for the number of parachutists that could be carried, CASA advised that:
- The legal basis for conducting parachuting flights with a greater number of passengers than the TCDS is met where the aircraft has been modified appropriately by a suitably authorised person and the aircraft’s flight manual has been modified accordingly.
- CASA has been aware for multiple decades that parachuting aircraft were carrying a maximum number of passengers greater than the TCDS maximum number of dedicated passengers.
- CASA understood that the increase in passenger capacity for parachuting aircraft was achieved by operators through legitimate aircraft modification processes that removed the normal passenger seats and modified the aircraft for parachute‑specific operations.
- CASA did not identify any immediate safety of flight issues.
In its submission to the draft report, CASA advised that it was ‘considering the issue of a legislative instrument to remove any doubt that an approved aircraft modification which replaces normal seating with appropriate alternative seating and restraint arrangements is explicitly permitted’.
Supplemental type certificate application
In April 2017, the design engineer applied to CASA on behalf of the aircraft operator for a supplemental type certificate based on the engineering order for the addition of bench seating. The STC application submitted to CASA included details and images of aircraft that already had modifications completed under an engineering order and did not include an increase in the seating capacity.
After several communications and iterations of the documents provided, in August 2017, CASA highlighted 2 areas directly related to safety of parachutists: the rear exit crashworthiness and the increase of maximum passenger capacity to 17.
In July 2020, the STC application was withdrawn by the applicant.
Other parachuting configuration supplemental type certificates
Cessna 182 models E to R
In 1996, CASA issued STC-214 to the APF. The STC background explained the application was the result of a CASA ramp check, which identified that there were 6 persons on board without single point restraints while conducting parachute operations, where the TCDS stated it was a 4‑seat aircraft.
The STC assessed the floor loading capacity of the aircraft to carry 6 persons (including the pilot) for the purpose of parachute operations. It concluded:
The floor was analysed and substantiated for parachutist loads. The hard points for the approved single point restraints were determined, analysed and substantiated for parachute loads... The aircraft loading is such that no special loading system needs to be devised as the aircraft will always be within the approved centre of gravity range.
The original C182 TCDS 3A13 showed ‘No. of seats 4’.
The amended TCDS for the STC showed ‘No. of seats 1, Parachutist 5’.
Cessna 208, 208B
In 2018, the US FAA issued supplemental type certificate SA04352CH, which incorporated many similar modifications made to model 208 and 208B aircraft certified under A37CE. The modifications included the installation of:
- wind deflector
- benches
- external assist handle
- internal assist handle
- jump exit control light
- external step
- wind block (sliding parachute door).
The STC limitations and conditions included:
(3) This modification does not install Title 14 [US Code of Federal Regulations] CFR part 23 compliant seating and is therefore zero occupancy.
(4) The left and right hand benches are compliant as monuments and are not certified to carry any items of mass. Testing performed during certification would be sufficient for gust loading or seven evenly distributed masses of 215 pounds (97.5 kg) each…
Australian Parachute Federation
The APF is the peak body for the administration and representation of Australian Sport Parachuting. With the approval of the Civil Aviation Safety Authority, the APF:
- applies the standards of operation
- conducts competitions
- issues parachuting licences, certifications and instructor ratings
- conducts exams
- distributes publications to keep its members informed of events and safety standards.
The APF organisation had over 55 group members also known as member organisations, 3,000 licenced members, and engaged with the operators of nearly 100 aircraft conducting parachute operations. As detailed above, the APF held an STC for parachuting operations in Cessna 182 models E through R for parachuting 6‑person operations. The associated supplemental type certificate data sheet amended the aircraft configuration to 1 seat and 5 parachutists from the 4‑seat configuration stated on the type certificate data sheet.
Aircraft operators that conducted parachuting operations as a member of the APF did so in accordance with the APF regulations. This included adhering to the APF Jump Pilot Manual. The Jump Pilot Manual Version 01-2023, in force at the time of the accident, stated:
5.3.3 Loading – Balance/C of G
A parachuting aircraft may carry more occupants than the maximum number that is specified in the aircraft’s flight manual only if the aircraft is loaded in accordance with the following requirements and limitations set out in the flight manual or the certification data for the aircraft:
(a) the weight and balance requirements; and
(b) any other limitations related to the provision of:
(i) adequate structural support for restraint of occupants; or
(ii) supplemental oxygen for the flight.
For paragraph 5.3.3 (b), the limitations do not include those that are solely related to the number of seats or seating positions that are, or are normally, fitted in the aircraft.
If an aircraft does not have a flight manual, then any information supplied by the manufacturer that relates to the matters mentioned above or is included in the aircraft’s airworthiness certificate, is taken to be the flight manual.
Balance must be a consideration for all aircraft involved in parachuting operations and can be especially critical during climb-out and exit, when changes occur. Know the operational limitations of your aircraft!
Under the Loadmaster’s supervision, the parachutists will normally load the aircraft in the reverse order of the exit.
The Jump Pilot Manual was accepted by CASA and CASA personnel reported having reviewed the manual. Regarding the wording that a parachuting aircraft could carry more occupants than the maximum specified in the AFM, CASA reported that they understood that only applied to Cessna 182 models E through R, for which the APF held a supplemental type certificate that permitted the carriage of 6 persons. CASA personnel also reported that the manual wording was ‘never intended to serve as a quasi-engineering approval’.
At the time of writing, CASA and the APF were engaged in ongoing discussions, including the carriage of occupants in excess of the number detailed in the TCDS without the necessary modification approvals.
Survivability
Passenger briefing requirements
The CASA Multi-Part Advisory Circular – Passenger safety information, stated:
2.1.1 In addition to certification standards for the crashworthiness of the aircraft and cabin crew evacuation procedures, well-informed and knowledgeable passengers contribute to survivability in an aircraft accident or incident. There are multiple factors that affect survivability. Physical factors include adopting the correct brace position for impact, the correct use of seatbelts, as well as the location and operation of all emergency exits.
2.1.2 Accident investigations have shown that survival rates are improved when passengers are provided with accurate and effective information about the correct use of equipment such as seatbelts, and the actions they should take in a life-threatening situation such as how to adopt the brace position.
A pilot in command was in contravention of regulation 91.565 if an aircraft commenced a flight and the passengers had not been given a safety briefing and instructions as prescribed by the Part 91 MOS, unless:
(a) the passenger has been previously carried on the aircraft; and
(b) the passenger has previously been given a safety briefing and instructions in accordance with this regulation; and
(c) in the circumstances it is not reasonably necessary to give the same safety briefing and instructions.
The CASR Part 91 MOS provided a list of items that must be covered in a passenger safety briefing and instructions before an aircraft takes off for a flight. Relevant to this occurrence, the list included:
(c) when seatbelts must be worn during the flight, and how to use them;
(f) how and when to adopt the brace position;
(g) where the emergency exits are, and how to use them;
(s) for a flight of a jump aircraft — the physical location(s) within, or on, the aircraft that the passenger must occupy during the flight in order to ensure the aircraft is operated within the aircraft’s weight and balance limits during the flight.
Operator’s safety briefing
The aircraft operator had 2 videos, one of which was shown to parachutists depending on whether they were conducting a tandem jump or a sport jump. The sport jump video was specific to the Barwon Heads operation and included:
- aircraft climb performance
- 17 single point restraints, which were to be worn up to 2,000 ft
- sport jumpers were to listen to the pilot in command in the event of an emergency
- location of the door securing clip (but not instructions for use).
The video shown to tandem jump parachutists provided specific aircraft safety information including:
- how to approach the aircraft
- the use of single point restraints
- the location of fire extinguishers
- how to brace
- how to egress
- the requirement not to smoke
- the use of life jackets where required.
For the accident flight, the pilot reported that they did not provide a safety briefing, and multiple parachutists reported not having received a safety briefing prior to flight. There was no procedure in the operations manual that waived the pilot’s responsibility to provide parachutists with a safety briefing. The pilot reported that they understood that the drop zone safety officer ensured everyone was briefed on emergency situations before jumping and a video briefing was provided to tandem parachutists.
The operations manual provided the following guidance for providing a safety briefing during an emergency landing with parachutists on board:
It will be the Load Masters responsibility to assist the pilot in ensuring;
1. Parachutists are briefed on and instructed to assume the BRACE position prior to touchdown.
2. Emergency Exits are opened and secured (where possible) prior to touch down.
3. Single point restraints are utilised by all occupants.
The aircraft also had a sign on the rear wall of the internal cabin, detailing the in-flight emergency plan (Figure 8). The sign stated that single point restraints were required as directed by the pilot and at all times below 1,500 ft, differing from the 2,000 ft stipulated in the sport jump video.
The APF Jump Pilot Manual required that restraints were utilised by all occupants below 1,000 ft, or as directed by the pilot.
Figure 8: In-flight emergency plan
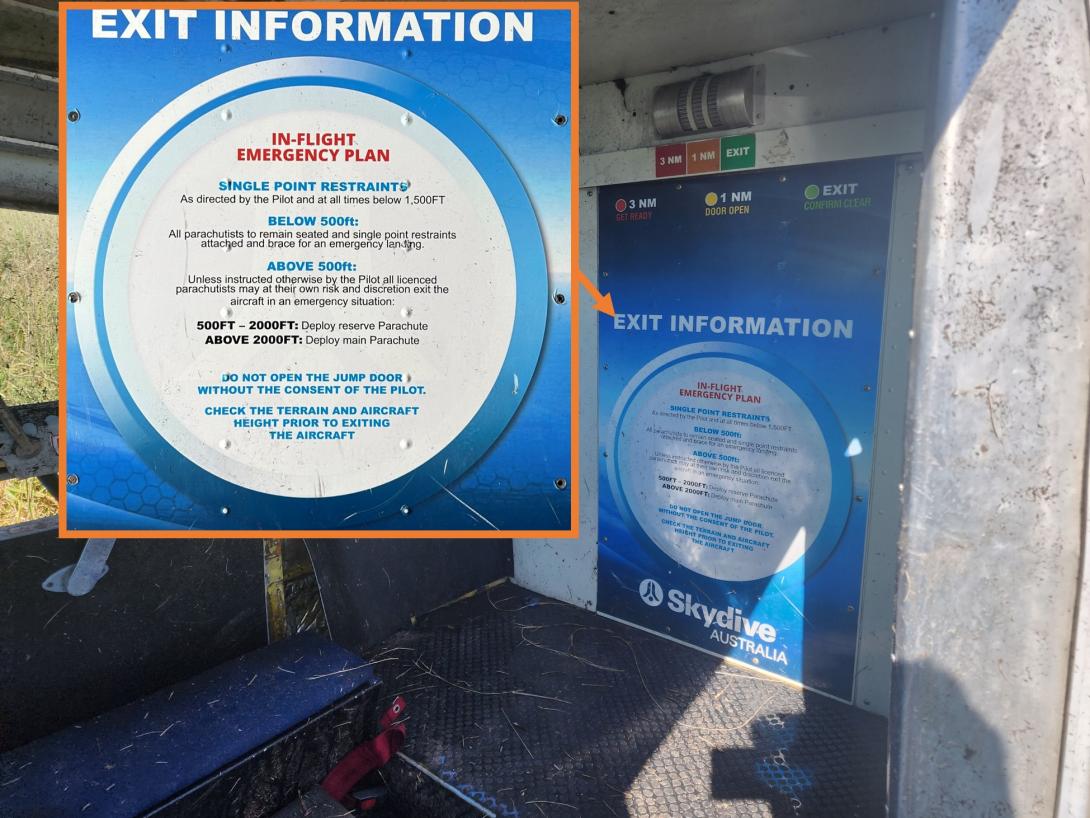
Source: Victoria Police and the aircraft operator
Parachutist preparedness
After the accident, in response to an ATSB survey, parachutists reported a lack of awareness of how to brace and the location of emergency exits that were available if the main roller door became damaged and unavailable for use in an evacuation. On this occasion the clip that secured the roller door in the open position was not used, which resulted in it closing on impact. Fortunately, the parachutists were still able to successfully evacuate the aircraft via that door. As detailed further below, several of the parachutists also reported that their restraints were not taut prior to the ground collision.
Some parachutists recalled receiving aircraft-specific emergency information during their initial parachuting training. However, in some cases, several years had passed without receiving a refresher. Furthermore, some had conducted their initial training on different aircraft types.
Injuries and seating positions
The pilot wore a 5-point restraint, and the 16 parachutists each had a single-point restraint attached to their parachute. The probable seating arrangement at the time of the accident was determined based on the recollections of parachutists who responded to ATSB’s request for information (Figure 9). There were 4 parachutists seated on the floor, 4 on the left bench seat and 8 on the right bench seat. The parachutists were facing aft and those on the bench seats were seated between each other’s legs.
Injury information was obtained for the pilot and 14 of the 16 parachutists, with the other 2 assumed to have no injuries (Table 4). The injury mechanisms included deceleration, flail and impact with the aircraft or other occupants.
Figure 9: Seating positions
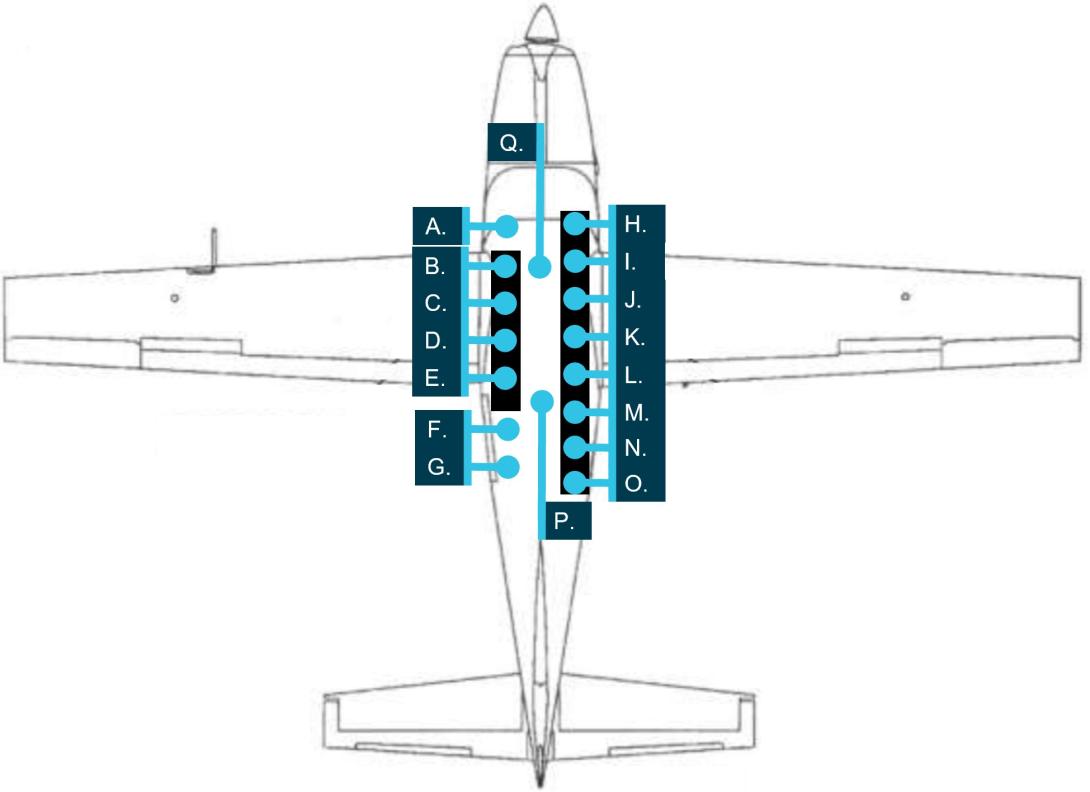
The seating positions in the image are referenced in Table 4: Injuries sustained. Source: Texas Turbines Cessna 208 pilot operating handbook, annotated by the ATSB
Table 4: Injuries sustained
Image reference | Injuries sustained | ATSB injury classification | Survivability Comments |
A. (Pilot) | Cut on forehead, bruising, whiplash, bruised sternum, and difficulty talking/breathing | Minor | 5-point safety harness; likely impact with control column/dash |
B. | Pulmonary contusion, fifth and sixth rib fractures, psychological trauma, and lower back pain | Serious | Slipped off the end of the bench seat and ended up squashed against the ladder or back of the pilot seat due to a loose restraint |
C. | No reported injuries | No injuries | |
D. | Tears to both rotator cuffs, tear to sternocleidomastoid muscle, and nerve damage to left arm and shoulder | Serious | |
E. | Broken ribs and internal bleeding to the chest. | Serious | Loose restraint |
F. | Whiplash, fractured L4 transverse process, and nerve pain in right shoulder and leg | Serious | Loose restraint, seated on floor; adjacent end of bench seat |
G. | Whiplash, bruising, and headaches | Minor | Seated on floor |
H. (Loadmaster) | Cut injury to right leg requiring stitches, and sore back | Minor | |
I. | Strained back, cuts, and bruising | Minor | |
J. | Whiplash, cuts, and bruising | Minor | Loose restraint |
K. | Whiplash, cuts, and bruising | Minor | Loose restraint |
L. | Cuts to head, face, internal chest cuts, and bruising | Minor | Tight restraint |
M. | Broken tailbone, bruising | Serious | Tight restraint |
N. | Concussion, and bruising | Minor | |
O. | Swollen knee, bruised kidney, bruised vertebrae, and strained neck ligaments | Minor | Loose restraint |
P. | Internal abdomen bleeding, Internal hematoma inner right leg, cuts, bruising, whiplash, and back pain. | Serious | Loose restraint; inappropriate structures around/in front |
Q. | No reported injuries | No injuries |
The single point restraints could not be adjusted, but an occupant could potentially position themselves such that the restraint was taut. Nine parachutists provided information about the tightness of their restraint; 7 reported their restraints were loose and 2 reported tight restraints. Of those with loose restraints, 3 sustained minor injuries and 4 sustained serious injuries. Of the 2 parachutists who reported having tight restraints, one sustained minor injuries and the other sustained serious injuries.
Of the 4 parachutists seated on the floor, 2 sustained serious injuries, one sustained minor injuries, and another was reported to have been uninjured. The other serious injuries were sustained by 2 parachutists on the left bench seat and one on the right bench seat.
The parachutist who sustained the most injuries of the highest severity was at the front of the left bench seat. As that bench seat did not have a seatback, the parachutist came off the forward end of the bench between the bench and pilot seat and contacted the back of the pilot’s seat and/or ladder adjacent to the seat. The injuries were likely also increased by the mass of the 3 other parachutists on that bench moving forward during the impact sequence.
The ATSB compared the injuries sustained by the pilot and parachutists of VH-UMV with those involved in 2 survivable accidents involving C208 aircraft, assessed as likely to have been subjected to similar impact forces (AO-2016-007 and AO-2024-001). In the 2 comparative accidents, some of the occupants sustained minor injuries while others were uninjured. The pilot and front seat passengers had 5-point restraints, and in the 2016 accident the other passengers wore lap belts. In the more recent accident, the other passengers wore 3-point restraints.
ATSB investigation AO-2014-053 found that single point restraints were less effective than dual restraints in mitigating injury for parachutists. This was consistent with the US FAA’s technical report – Evaluation of Improved Restraint Systems for Sport Parachutists, which found that dual straps attached to the parachute harness provided better restraint and produced less flailing and bending of the body than single point restraints (FAA 1988). The following loading of aft‑facing passengers was found to increase restraint effectiveness:
- the person most forward in the cabin should be leaning against a bulkhead or other substantial support to limit flailing and head impact.
- each parachutist’s restraint should be anchored to the floor aft of his/her pelvis (relative the aircraft’s orientation) at a point on the floor near the middle of the thigh. The restraint should be taut to reduce forward motion, and the loads transmitted to the person behind.
- the proper brace for impact position would be to lean toward the front of the aircraft onto the person or bulkhead behind them.
The US FAA AC 105-2E Sport parachuting also stated that single point restraints were ‘not very effective’, and that dual point restraints offered ‘superior restraint’.
The ATSB assessed that the increase in number and severity of injuries of the parachutists compared to passengers seated and restrained in seats, was probably a result of single-point restraints being less effective and less cushioning due to being seated on the floor or bench.
Related occurrences
National Transportation Safety Board Special investigation report
The US National Transportation Safety Board (NTSB), Special investigation report on the safety of parachute jump operations (2008), found that between 1980 and 2008 in the US, 32 accidents involving parachute aircraft resulted in fatal injuries of 172 people, most of whom were parachutists. Acknowledging risks associated with parachuting, the report stated:
Although parachutists, in general, may accept risks associated with their sport, these risks should not include exposure to the types of highly preventable hazards that were identified in these accidents and that the parachutists can do little or nothing to control. Passengers on parachute operations aircraft should be able to expect a reasonable level of safety that includes, at a minimum, an airworthy airplane, an adequately trained pilot, and adequate Federal oversight and surveillance to ensure the safety of the operation.
Of the 32 accidents, 8 involved exceedances of the aircraft’s weight and balance, and 21 resulted from inadequate airspeed or stall situations, and in 6 accidents, both were factors. There was one accident involving a Cessna 208, which resulted in 17 fatalities.
The report also acknowledged that parachuting is typically a revenue operation where a participant pays for a jump and receives the flight as part of that service, it stated:
Most parachute operations flights are operated under the provisions of 14 Code of Federal Regulations (CFR) Part 91 and are typically revenue operations; parachute jump operators provide the flights as part of their services to parachutists who pay to go skydiving, or parachutists pay dues for membership in parachuting clubs. The risks of parachuting are generally perceived to involve the acts of jumping from the aircraft, deploying the parachute, and landing; parachutists are aware of and manage these risks. However, a review of accident reports reveals that traveling on parachute operations flights can also present risks.
The report highlighted the potential for paying participants to be unaware of the risks they were accepting when they boarded a parachute aircraft.
The report identified the following recurring safety issues:
- inadequate aircraft inspection and maintenance;
- pilot performance deficiencies in basic airmanship tasks, such as preflight inspections, weight and balance calculations, and emergency and recovery procedures; and
- inadequate FAA oversight and direct surveillance of parachute operations.
Recent accidents
The following 3 more recent accidents involved aircraft conducting parachuting operations and resulted in injuries to the occupants.
- Loss of engine power after take-off involving Cessna 208B, PH-FST, West of International Airport Teuge, Netherlands, on 25 June 2021 (2021062)
On 25 June 2021 at 0932 local time, a Cessna 208B with a pilot and 17 parachutists on board departed from International Airport Teuge. During the initial climb, the aircraft suddenly lost engine power after which the pilot made an emergency landing in a field close to a motorway. The aircraft was substantially damaged, and one parachutist sustained minor injuries.
- Accident involving GA8-TC-320 Airvan, SE-MES, Storsandskär, Västerbotten, Sweden, on 14 July 2019 (RL 2020:08e).
The purpose of the flight was to drop 8 parachutists from an altitude of 13,000 ft. On the drop run, the pilot lost control of the aircraft. The parachutists were unable to evacuate the aircraft resulting in fatalities of the 9 persons on board.
The investigation found that control of the aeroplane was probably lost due to low airspeed. Other contributing factors were that the aeroplane was unstable as a result of a tail-heavy loading, weather conditions, and a high workload in relation to the pilot’s knowledge and experience.
- Loss of control involving Cessna U206G, VH-FRT, Caboolture Airfield, Queensland, on 22 March 2014 (AO-2014-053)
On 22 March 2014, a Cessna U206G aircraft was being used for tandem parachuting operations at Caboolture Airfield, Queensland. At about 1124 local time, the aircraft took off from runway 06 with the pilot, 2 parachuting instructors and 2 tandem parachutists on board. Shortly after take-off, witnesses at the airfield observed the aircraft climb to about 200 ft above ground level before it commenced a roll to the left. The left roll steepened, and the aircraft then adopted a nose‑down attitude until impacting the ground in an almost vertical, left-wing low attitude. All the occupants on board were fatally injured. A post-impact, fuel-fed fire destroyed the aircraft.
The ATSB identified that the aircraft aerodynamically stalled at a height from which it was too low to recover control prior to collision with terrain. The reason for the aerodynamic stall was unable to be determined. Extensive fire damage prevented examination and testing of most of the aircraft components. Consequently, a mechanical defect could not be ruled out as a contributor to the accident.
A number of safety issues were also identified by the ATSB. These included findings associated with occupant restraint, modification of parachuting aircraft and the regulatory classification of parachuting operations.
Safety analysis
Introduction
On the morning of 20 October 2023, the pilot of a Cessna 208, registered VH-UMV, commenced take-off for a planned climb to 15,000 ft to drop 16 parachutists. Passing about 500 ft on climb, the pilot detected a partial power loss, consistent with an abnormal activation of the torque and temperature limiter (TTL). The pilot reduced the power to prevent the engine surging, but the combination of low power and airspeed resulted in the aircraft colliding with water before continuing into a field.
Six of the parachutists sustained serious injuries and the pilot and 8 parachutists sustained minor injuries. The aircraft was substantially damaged.
This analysis will discuss the TTL activation and response actions. The aircraft’s seating configuration, weight and balance and occupant safety will also be examined. Additionally, the analysis will consider the number of parachutists on board, and operational guidance from the Australian Parachute Federation manual approved by the Civil Aviation Safety Authority (CASA).
Operator’s prescribed actions
Normal operation of the TTL permitted reduction in the fuel flow to the engine to maintain the lower of 100% torque or 650 °C nominal exhaust gas temperature (EGT). However, the TTL manufacturer advised that the limiter was capable of restricting fuel flow sufficiently to reduce the maximum power to about 62% torque. A noticeable power reduction, followed quickly by a power increase, had been reported by the operator’s pilots as engine surging events associated with the TTL. However, maintenance actions had been unable to identify or resolve the cause of 6 reported engine surging events in VH-UMV over a 5‑month period.
Unable to resolve the intermittent excessive TTL response, the aircraft operator had advised pilots to limit torque to 95% and EGT to 640°C to prevent TTL activation. Although well intentioned, that was contrary to the aircraft flight manual supplement, which defined take-off power as 100% RPM and 100% torque or 650°C EGT, whichever was reached first. The operator had not assessed the TTL and single red line (SRL) systems as inoperable, which would have required pilots to manually ensure torque and temperature limits were not exceeded. Power reductions resulting from TTL activations were reported to be momentary and power returned to the previous level after the torque or EGT limit reduced below the limit.
Additionally, in the absence of an aircraft manufacturer’s checklist for partial power loss, the operator had created an engine power loss checklist. The first item was to immediately move the elevator control forward if climbing to prevent airspeed decay. After other initial actions, the checklist then instructed pilots to significantly reduce power if the engine RPM was above 60% or surging, in preparation for switching off the TTL. While that was intended to ensure engine limits would not be exceeded when the pilot subsequently reintroduced power, the operator did not specify a minimum height at which it was appropriate for a power reduction to be made.
Such a significant power reduction close to the ground increased the risk of a loss of control and/or ground collision.
Contributing factor Experience Co’s engine power loss checklist instructed pilots to significantly reduce power in preparation for deactivating the TTL, but did not specify a minimum safe height at which to do so. This increased the risk of loss of control and/or ground collision. |
Pilot actions
At the commencement of the take-off roll, in accordance with normal and the manufacturer’s procedures, the pilot reported applying full power – initially reaching 100% torque for take-off, before reducing power slightly in an attempt to remain under the operator‑specific torque limit of 95%. Whether the torque or temperature limit were reached during the initial climb could not be determined as these parameters were not recorded. However, the pilot detected a power reduction consistent with an abnormal TTL activation.
As shown by previous safety reports, in the event of TTL activation, the maximum power available may have been approximately 62%. Such a significant power reduction would have required the pilot to lower the aircraft’s nose attitude to prevent an aerodynamic stall, consistent with the operator’s engine power loss checklist.
However, the pilot did not initially lower the aircraft’s nose, instead they moved the power lever aft, reducing the power setting. This was in accordance with the operator’s procedure in preparation for switching off the TTL. Although the as‑found switch positions indicated that the pilot may have inadvertently selected the SRL switch instead of the TTL, in either event the TTL would have been deactivated. However, as the pilot had not lowered the aircraft’s nose, the aircraft approached an aerodynamic stall, and the stall warning horn sounded.
In response, the pilot lowered the aircraft’s nose and, due to the low height above terrain, low airspeed and low power, searched for a suitable field for landing. Although the pilot only reported reducing the power slightly, as the post-accident inspections found the engine was capable of producing normal power, and there were no pre-existing conditions that would have prevented normal operation, the low power was likely a result of the pilot reducing power to a level insufficient to maintain height in the climb attitude, and not restoring it.
At the low height above the ground at which the power loss occurred, the above factors led to the collision with water.
Contributing factor Passing about 500 ft on climb, the power reduced likely due to abnormal activation of the torque and temperature limiter (TTL). Expecting the power to return quickly, and in preparation for deactivating the TTL, the pilot further reduced the power and delayed lowering the aircraft’s nose to maintain airspeed. This resulted in a stall warning and subsequent collision with water. |
Weight and balance
The aircraft had all the aircraft’s certified seating removed other than the pilot’s seat, following which the aircraft was weighed, and a basic empty weight established. However, that weight did not include the bench seating, parachute restraints, floor matting or oxygen bottles which were fitted to the aircraft at the time of the accident. Although the weight and moment arm of the bench seating had been provided with the engineering order, it was not accounted for in the IBIS Technologies weight and balance calculation software used by the operator.
As a result, the bench seating and other aircraft fixtures were not accounted for in the accident flight weight and balance calculation. Additionally, parachutists did not sit in the positions used for the weight and balance calculations for the accident flight. Therefore, the calculated weight and balance was inaccurate.
Although the operator’s post-accident calculations found that the aircraft was almost certainly operating within the weight and balance limitations throughout the flight, an accurate weight and balance assessment prior to take-off to ensure the flight will operate below the maximum take-off weight is essential for the structural integrity of the aircraft. Operating outside the centre of gravity limits increases the risk of a loss of control. Exceeding weight and balance limitations has previously resulted in fatal accidents involving aircraft conducting parachute operations.
Other factor that increased risk The operator's weight and balance calculation for the accident flight was inaccurate as it did not include the bench seating weight or moment, and the loadmaster did not load parachutists in positions used for the calculation of the centre of gravity. |
IBIS Technologies flight planning module
When conducting post-accident weight and balance calculations using the operator’s IBIS Technologies flight planning module, the ATSB identified that, while warnings were provided when the aircraft was outside the overall weight or centre of gravity limit, there was no warning when the weight for a zone within the cabin exceeded the limit. This increased the likelihood of an aircraft being loaded contrary to zone limitations.
The lack of an alert did not contribute to this accident and, as noted above, the aircraft was not loaded in accordance with the planned overall or zonal distributions. However, the software used to calculate the aircraft weight and balance was used by many operators and overloading a zone limit could result in damage to the aircraft.
Other factor that increased risk The IBIS technologies software used to calculate aircraft weight and balance did not provide a warning if individual zones were overloaded. |
Safety briefings
To maximise survivability in the event of an emergency, pilots are required to ensure aircraft occupants receive a safety briefing and instructions including in the correct use of restraints, emergency exits and adopting the brace position. However, a pilot is not required to brief passengers on every flight, if they have previously been on the aircraft and are likely to be familiar with safety information.
The pilot understood that this responsibility had been delegated to the drop zone officer and that the parachutists had received the required safety briefing and information. However, there was no record of which parachutists had been briefed or when. Additionally, as none of the parachutists on board were tandem jump parachutists, they were unlikely to have viewed the operator’s video that included use of single point restraints, how to brace or exit the aircraft in the event of an emergency.
Although some of the parachutists on board had previously received a safety briefing, it had not necessarily been in the accident aircraft type or recently. Additionally, an ‘in-flight emergency plan’ printed on the rear of the cabin advised parachutists to remain seated with single point restraints attached and brace for an emergency landing when below 500 ft, but did not specify how to brace or exit the aircraft. As a result, some of the occupants were unaware of essential safety information regarding brace position and emergency exits.
Although the aircraft’s roller door closed on impact and water entered the cabin, all 17 occupants evacuated with no difficulties reported. The ATSB was unable to determine whether the absence of a safety briefing increased the severity of the injuries sustained by parachutists. However, adopting the correct brace position for impact, the correct use of restraints, and knowledge of the location and operation of all emergency exits, are factors demonstrated to increase survivability.
Other factor that increased risk Experience Co did not ensure sport parachutists received essential safety information about emergency exits, restraints and brace position, prior to take-off. (Safety issue) |
Seating configuration
The operator routinely conducted parachuting operations in Cessna 208 aircraft with the pilot and up to 17 parachutists on board. This was based on the CASA-accepted Australian Parachute Federation Jump Pilot Manual, which stated that the aircraft could carry as many parachutists as there were restraints and provided the aircraft was operated within the weight and balance limitations.
The aircraft’s cabin was configured with a roller door, oxygen system, bench seating and single‑point restraints for parachuting operations under an engineering order by a CASA‑authorised person. Although the configuration nominally provided restraints and seating (including on the floor) for up to 17 parachutists, this was not formally documented in the aircraft flight manual or a supplement. The engineer also assessed and modified the aircraft to supply oxygen for 16 occupants to meet the operator’s requirements of their intended operation.
CASA assessed that increasing the number of persons carried above that stated on the type certificate data sheet (TCDS) required a supplemental type certificate (STC) as it was a major modification. In this case the TCDS stated that the aircraft had a maximum seating capacity of 11, but the aircraft was modified to supply oxygen for an intended 16 occupants. As such, the CASA‑authorised engineer incorrectly assessed that the modifications they were approving were minor and conducted them under engineering orders. The ATSB considered whether conducting the modifications in that manner increased safety risk.
As part of the assessment of an STC application for the same modifications submitted by the design engineer in 2017, CASA questioned the modified rear exit crashworthiness and increased number of occupants. Specifically, it was noted that the effect of increased occupancy on speed and ease of emergency egress had not been established, nor had it been demonstrated that the roller door would be unlikely to jam in the event of fuselage deformation.
As that STC application was never finalised, the safety of egress via the modified exit was not verified. However, in this accident, all the occupants evacuated the aircraft through the roller door after impact. As such, while the STC process was not followed when modifying the aircraft, there was no evidence that it increased the safety risk on this occasion. Additionally, CASA advised that the legislative requirements would likely be met if a modification conducted by an authorised person (under an engineering order) included an associated aircraft flight manual supplement.
The expectation for parachuting operations was that the parachutists would jump from a planned height, or be able to exit the aircraft in the event of an emergency when above a safe height. However, they would be inside the aircraft during take-off, at low level, and if unable to exit in the event of an emergency. In those phases of flight or conditions, increasing the number of occupants increased the number of people exposed to the risk of harm in the event of an accident. In this accident, as the aircraft was too low for parachutists to exit airborne, 15 of the 17 occupants sustained injuries, some of which probably occurred due to impact with each other.
Although the parachuting configuration was assessed as compliant with the required airworthiness standards, parachutists were exposed to greater risk of harm than if they were passengers in certified seats with adequate restraints. Those seated on the floor did not have the benefit of a seat to absorb impact forces and the bench seating had not been shown to optimally absorb impact forces. Additionally, the lack of a seatback on the left bench seat likely increased the injuries sustained by the forward-most parachutist seated on that side. The parachutists were also using single-point restraints, demonstrated to be less effective than dual restraints.
Findings
ATSB investigation report findings focus on safety factors (that is, events and conditions that increase risk). Safety factors include ‘contributing factors’ and ‘other factors that increased risk’ (that is, factors that did not meet the definition of a contributing factor for this occurrence but were still considered important to include in the report for the purpose of increasing awareness and enhancing safety). In addition ‘other findings’ may be included to provide important information about topics other than safety factors. Safety issues are highlighted in bold to emphasise their importance. A safety issue is a safety factor that (a) can reasonably be regarded as having the potential to adversely affect the safety of future operations, and (b) is a characteristic of an organisation or a system, rather than a characteristic of a specific individual, or characteristic of an operating environment at a specific point in time. These findings should not be read as apportioning blame or liability to any particular organisation or individual. |
From the evidence available, the following findings are made with respect to the partial power loss and collision with terrain involving Cessna 208, VH-UMV near Barwon Heads Airport, Victoria on 20 October 2023.
Contributing factors
- Experience Co’s engine power loss checklist instructed pilots to significantly reduce power in preparation for deactivating the TTL, but did not specify a minimum safe height at which to do so. This increased the risk of loss of control and/or ground collision.
- Passing about 500 ft on climb, the power reduced likely due to abnormal activation of the torque and temperature limiter (TTL). Expecting the power to return quickly, and in preparation for deactivating the TTL, the pilot further reduced the power and delayed lowering the aircraft’s nose to maintain airspeed. This resulted in a stall warning and subsequent collision with water.
Other factors that increased risk
- The operator's weight and balance calculation for the accident flight was inaccurate as it did not include the bench seating weight or moment, and the loadmaster did not load parachutists in positions used for the calculation of the centre of gravity.
- The IBIS technologies software used to calculate aircraft weight and balance did not provide a warning if individual zones were overloaded.
- Experience Co did not ensure sport parachutists received essential safety information about emergency exits, restraints and brace position, prior to take-off. (Safety issue)
Safety issues and actions
Central to the ATSB’s investigation of transport safety matters is the early identification of safety issues. The ATSB expects relevant organisations will address all safety issues an investigation identifies. Depending on the level of risk of a safety issue, the extent of corrective action taken by the relevant organisation(s), or the desirability of directing a broad safety message to the aviation industry, the ATSB may issue a formal safety recommendation or safety advisory notice as part of the final report. All of the directly involved parties were provided with a draft report and invited to provide submissions. As part of that process, each organisation was asked to communicate what safety actions, if any, they had carried out or were planning to carry out in relation to each safety issue relevant to their organisation. The initial public version of these safety issues and actions are provided separately on the ATSB website, to facilitate monitoring by interested parties. Where relevant, the safety issues and actions will be updated on the ATSB website as further information about safety action comes to hand. |
Safety issue information
Safety issue number: AO-2023-049-SI-01
Safety issue description: Experience Co did not ensure sport parachutists received essential safety information about emergency exits, restraints and brace position, prior to take-off.
Safety action not associated with an identified safety issue
Whether or not the ATSB identifies safety issues in the course of an investigation, relevant organisations may proactively initiate safety action in order to reduce their safety risk. The ATSB has been advised of the following proactive safety action in response to this occurrence. |
Proactive safety action taken by Experience Co
Experience Co has taken the following proactive safety actions:
- A safety communique was developed and circulated at each drop zone reminding parachutists to be seated in accordance with their manifested location.
- Chief instructors, drop zone safety officers and loadmasters were reminded of the loadmasters’ responsibilities to ensure parachutists were seated in accordance with the weight and balance calculation.
- Skydive Operations Manual was amended to clarify the loadmasters’ responsibilities.
- Additional training was provided for manifest staff.
- A fleet‑wide audit was undertaken to ensure all aircraft had accurate basic empty weight figures.
- A prompt was added to the internal reporting software to confirm an entry has been made to the aircraft’s maintenance release when submitting a maintenance‑related internal safety report.
- Briefings that cover essential safety information about emergency exits, restraints, and brace position, are now required annually by sport skydivers.
- Additional pilot training relating to the SRL/TTL malfunctions has been developed and was scheduled to be delivered to all pilots.
- Emergency exit signs in all aircraft were being assessed for compliance and effectiveness, and updated if necessary.
- Engineering personnel have undertaken specialised TPE331 Powerplant and Systems training.
- Information circulars were provided to company pilots about the proper defect reporting requirements using the aircraft maintenance release.
- Experience Co was updating advice as to the altitude at which seatbelts must be worn.
- Experience Co has developed C208 and C208B aircraft flight manual supplements, which outline the carriage of 17 parachutists and 21 parachutists respectively.
- An additional support bracket has been designed to be fitted to the end of the bench seats in aircraft and will be installed once formally approved.
- A new engine power loss checklist was developed in cooperation with the STC holder to be followed at or above 1,000 ft above ground level.
Proactive safety action taken by IBIS Technologies
IBIS Technologies amended its software to include an alert that will be flagged to the staff member in charge of manifesting the flight load if a zone exceeds zonal weight limits.
Proactive safety action taken by the Australian Parachute Federation
The Australian Parachute Federation (APF) has taken the following safety action:
- The APF will ensure skydivers and pilots review their aircraft emergency procedures on a regular basis. Recommended topics are likely to include:
- general safety around aircraft
- hot loading
- door activation
- achieving correct restraint fitment
- emergency landings
- brace position
- emergency exit altitudes and which parachute to use
- communication during an emergency
- for coastal operations, life jacket use in a ditching.
- Each parachuting aircraft operator will conduct a thorough assessment of their aircraft to ensure single point restraints are properly installed, to prevent parachutists from moving outside their designated seating positions and to maintain the aircraft’s weight and balance.
- The APF will review global data on the use of dual-point restraints to gather insights from other national parachuting organisations regarding their experiences with this system.
- The APF examined aircraft flight manual wording of all aircraft currently conducting parachute operations in Australia to identify which aircraft would require a short-term CASA exemption to permit operations with the number of passengers onboard in excess of those able to occupy the normal seats under the type design. They identified 22 aircraft requiring an exemption, spanning 5 operators.
- The APF added the following statement to the participant waiver form: ’parachuting aircraft are not operated to the same safety standards as a normal commercial passenger flight’.
Proposed safety action by the Civil Aviation Safety Authority
The Civil Aviation Safety Authority advised that it is developing the following:
- An exemption, for pilots or operators of parachuting aircraft who may be unable to comply with elements of the aircraft flight manual, is expected to be completed by mid‑2025.
- CASA stated that it was satisfied that reasonable steps had been taken by the APF to ensure that a level of safety, commensurate with the risks involved in the parachuting activities in which participants engage, was provided to those participants in the interim while the exemption was being developed.
- An amendment to the Civil Aviation Safety Regulations Part 21 Manual of Standards to specify the standards required for the modifications made to parachuting aircraft. This proposed action is expected to be finalised by the end of 2025.
- Additional guidance to support aircraft owners and operators seeking to make an approved modification.
Glossary
AC | Advisory circular |
ADS-B | Automatic dependent surveillance broadcast |
AFM | Airplane Flight Manual |
APF | Australian Parachute Federation |
CASA | Civil Aviation Safety Authority |
CASR | Civil Aviation Safety Regulations |
CAVOK | Conditions and visibility okay |
EGT | Exhaust gas temperature |
FAA | (United States) Federal Aviation Administration |
FCU | Fuel control unit |
MEL | Minimum equipment list |
NTSB | (United States) National Transportation Safety Board |
POH | Pilot’s Operating Handbook |
RPM | Revolutions per minute |
SRL | Single red line |
TCDS | Type certificate data sheet |
TTL | Torque and temperature limiter |
US | United States |
Sources and submissions
Sources of information
The sources of information during the investigation included:
- the pilot and sports jump parachutists
- Experience Co
- Civil Aviation Safety Authority
- Australian Parachute Federation
- Victoria Police
- Textron Aviation
- Honeywell International Inc
- OzRunways
- Barwon Heads Airport
- Texas Turbine Conversions
References
Federal Aviation Administration (2023). Pilot’s handbook of aeronautical knowledge. FAA-H-8083-25C.
Civil Aviation Safety Authority (2022). Classification of design changes (advisory circular AC 21-12 v1.1), https://www.casa.gov.au/classification-design-changes, CASA, accessed 23 September 2024.
Federal Aviation Administration (1998). Evaluation of improved restraint systems for sport parachutists, https://libraryonline.erau.edu/online-full-text/faa-aviation-medicine-reports/AM98-11.pdf.
National Transport Safety Board (2008). Special investigation report on the safety of parachute operations, https://www.ntsb.gov/safety/safety-studies/Documents/SIR0801.pdf, NTSB/SIR-08/01.
Submissions
Under section 26 of the Transport Safety Investigation Act 2003, the ATSB may provide a draft report, on a confidential basis, to any person whom the ATSB considers appropriate. That section allows a person receiving a draft report to make submissions to the ATSB about the draft report.
A draft of this report was provided to the following directly involved parties:
- the pilot and aircraft operator
- Australian Parachute Federation
- Civil Aviation Safety Authority
- Textron Aviation
- Honeywell International Inc
- Texas Turbine Conversions
- Bowden Engineering solutions.
Submissions were received from:
- the pilot and aircraft operator
- Australian Parachute Federation
- Civil Aviation Safety Authority
- Honeywell International Inc.
The submissions were reviewed and, where considered appropriate, the text of the report was amended accordingly.
Purpose of safety investigationsThe objective of a safety investigation is to enhance transport safety. This is done through:
It is not a function of the ATSB to apportion blame or provide a means for determining liability. At the same time, an investigation report must include factual material of sufficient weight to support the analysis and findings. At all times the ATSB endeavours to balance the use of material that could imply adverse comment with the need to properly explain what happened, and why, in a fair and unbiased manner. The ATSB does not investigate for the purpose of taking administrative, regulatory or criminal action. TerminologyAn explanation of terminology used in ATSB investigation reports is available here. This includes terms such as occurrence, contributing factor, other factor that increased risk, and safety issue. Publishing informationReleased in accordance with section 25 of the Transport Safety Investigation Act 2003 Published by: Australian Transport Safety Bureau © Commonwealth of Australia 2025
Ownership of intellectual property rights in this publication Unless otherwise noted, copyright (and any other intellectual property rights, if any) in this report publication is owned by the Commonwealth of Australia. Creative Commons licence With the exception of the Commonwealth Coat of Arms, ATSB logo, and photos and graphics in which a third party holds copyright, this report is licensed under a Creative Commons Attribution 4.0 International licence. The CC BY 4.0 licence enables you to distribute, remix, adapt, and build upon our material in any medium or format, so long as attribution is given to the Australian Transport Safety Bureau. Copyright in material obtained from other agencies, private individuals or organisations, belongs to those agencies, individuals or organisations. Where you wish to use their material, you will need to contact them directly. |
[1] Ceiling and visibility okay (CAVOK): visibility, cloud and present weather are better than prescribed conditions. For an aerodrome weather report, those conditions are visibility 10 km or more, no significant cloud below 5,000 ft, no cumulonimbus cloud and no other significant weather (Source: Airservices Australia).
[2] OzRunways is an electronic flight bag application that provides navigation, weather, area briefings and other flight information. It provides the option for live flight tracking by transmitting the device’s position and altitude.
[3] Engine surging as reported by the pilots of VH-UMV was a power reduction followed quickly by an increase in the power level.
[4] Angle of attack: the relative angle between the chord line of the wing and the relative airflow.
[5] Automatic dependent surveillance-broadcast (ADS-B) is a surveillance system that broadcasts the precise location of an aircraft through a digital data link.
[6] Loadmaster: a person nominated by the drop zone safety officer who is performing duties for a parachute descent.
[7] Normal category applies to aircraft which are intended for non-acrobatic operation, having a seating configuration (excluding pilot seats) of 9 seats or less, and a maximum take-off weight of 5,700 kg or less.
[8] Restricted category applies to aircraft which may carry out certain special purpose operations, but may not carry passengers or cargo for hire or reward.
[9] Feathering: the rotation of propeller blades to an edge-on angle to the airflow to minimise aircraft drag following an in‑flight engine failure or shutdown.
[10] The propeller can move to reverse when the engine is operating in beta mode, which results in thrust acting in the opposite direction of the aircraft. In beta mode, the propeller blade pitch is controlled by the power lever.
[11] Maintenance release: an official document, issued by an authorised person as described in Regulations, which is required to be carried on an aircraft as an ongoing record of its time in service (TIS) and airworthiness status. Subject to conditions, a maintenance release is valid for a set period, nominally 100 hours TIS or 12 months from issue.
[12] The parachutist’s names, weights, and seating locations removed.