Investigation summary
What happened
On 26 April 2024, the pilot (who was the sole occupant) of a DHC‑1 MK 22 Chipmunk, registered VH‑POR, taxied for take‑off from Jandakot Airport, Western Australia for a private flight. A witness took photographs of the aircraft taxiing past, which showed the engine cowl latches on the left side had not been secured.
After the aircraft took off, another witness near the runway recalled seeing something ‘flapping’ on the aircraft. This witness, and witnesses in a nearby building looking through a window, observed the aircraft turn to the left at low height near the end of the runway. The pilot declared a MAYDAY, and camera footage showed the aircraft’s angle of bank increasing and the aircraft descending before colliding with terrain.
An instructor, with a student pilot who had just landed, taxied to a position adjacent to the accident site to provide assistance. The pilot was initially treated onsite by Royal Flying Doctor Service personnel before being transported to hospital. Later, the pilot succumbed to injuries.
What the ATSB found
Prior to commencing taxi, the pilot did not detect that the engine cowl latches on the left side had been left unfastened. After take-off, the cowl was free to open and close in flight. Witness reports and camera footage show the engine cowl was opening and closing until the aircraft collided with terrain.
While likely distracted by the flapping engine cowl and experiencing a high cognitive workload, the pilot made a MAYDAY call while commencing a low‑level turn, likely in an attempt to return to land. During the turn, the aircraft’s angle of bank increased, and the aircraft aerodynamically stalled and collided with terrain.
When the aircraft collided with terrain, the upper structure between the front and rear cockpits, corresponding to the attach point for the front cockpit shoulder harness, was torn away from its mountings. Most noteworthy, all 12 rivets (6 per side) that attached the structure to the mountings had sheared. ATSB examination of the rivets using metallurgical equipment found that all of the rivets were of a non-conforming type, and half were estimated to be about one-third of the specification strength. This compromised the crashworthiness of the aircraft, however, the effect on survivability in this accident could not be determined.
What has been done as a result
To advise DHC‑1 Chipmunk maintainers and owners of the importance of ensuring modifications are carried out to the required specification, the ATSB issued a safety advisory notice (AO‑2024‑013‑SAN‑01) on 11 September 2024.
The Portuguese Office for the Prevention and Investigation of Accidents in Civil Aviation and Rail (GPIAAF) published information from the ATSB’s safety advisory notice (AO-2024-013-SAN-01) in its Civil Aviation Quarterly Bulletin Publication (issue QB 03/2024) in October 2024.
Safety message
This accident illustrates the importance of pre-flight preparation to reduce the likelihood of an abnormal occurrence. In addition, pilots are reminded of the hazards that can lead to loss of control events, such as high angles of bank, especially at low heights, which should be avoided to reduce the risk of a stall/spin accident.
The modification carried out on the accident aircraft significantly compromised its crashworthiness. Maintainers and owners are reminded that when making modifications to any aircraft, that they are carried out to the required specification, or during maintenance returned to that specification.
The investigation
Decisions regarding the scope of an investigation are based on many factors, including the level of safety benefit likely to be obtained from an investigation and the associated resources required. For this occurrence, a limited-scope investigation was conducted in order to produce a short investigation report, and allow for greater industry awareness of findings that affect safety and potential learning opportunities. |
The occurrence
On the afternoon of 26 April 2024, the pilot (who was the sole occupant) of a DHC‑1 MK 22 ‘Chipmunk’, registered VH‑POR, commenced taxi for take-off at Jandakot Airport, Western Australia for a private flight. The weather was clear, with the wind about 10 kt from the north‑west.
A witness on the southern apron took photographs of the aircraft taxiing past, which show the engine cowl latches on the left side were oriented vertically[1] (Figure 1).
Figure 1: VH‑POR taxiing for take-off

The gap at the rear edge of the cowl is normally present when the cowl is closed fully. Image source: Witness, annotated by the ATSB
The pilot continued to taxi to the end of runway 24L and at 1313 was given clearance to take off. Camera footage recorded the aircraft commencing its take-off roll and becoming airborne about halfway along the runway’s length (Figure 2).
Figure 2: Approximate flight path
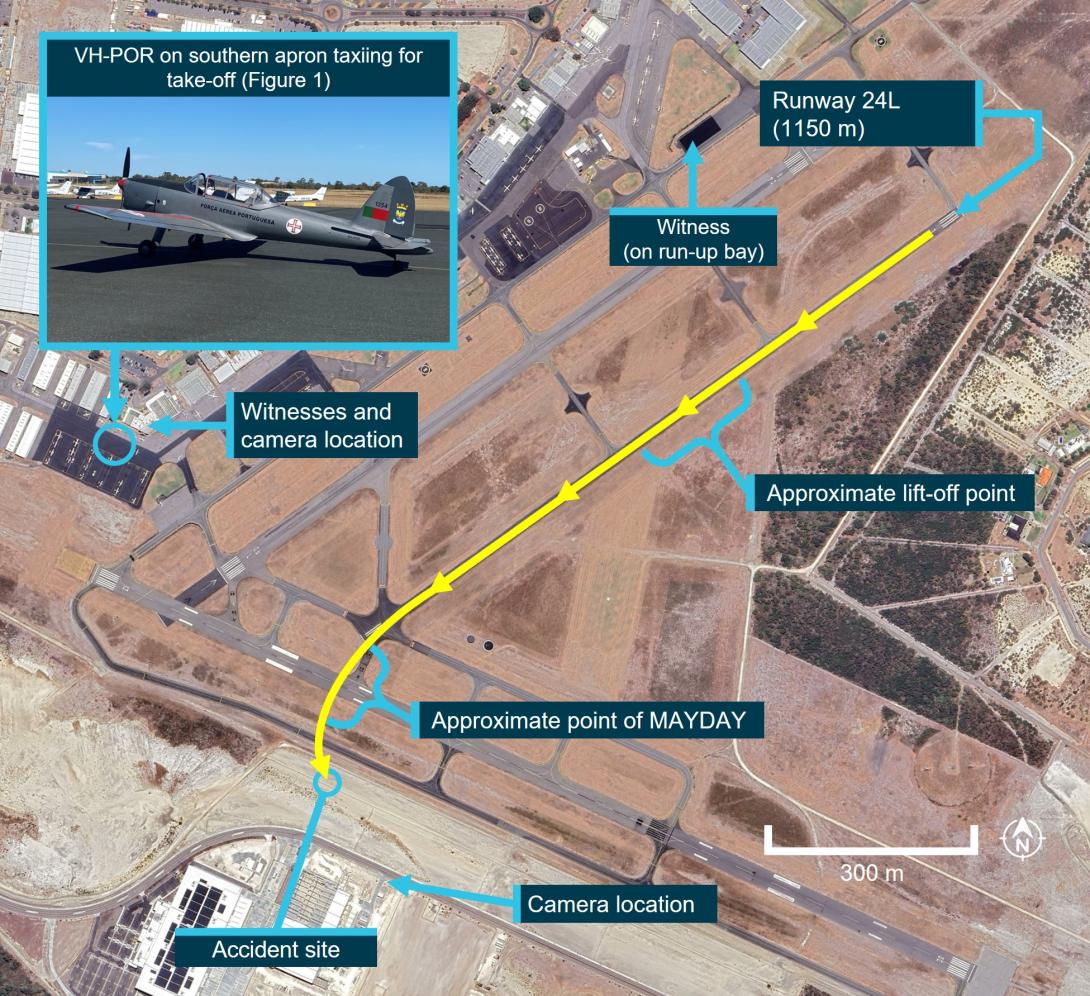
Image source: Google Earth, annotated by the ATSB
One witness, located at the run-up bay, recalled seeing something ‘flapping’ on the aircraft during the take-off. This witness, and witnesses in a nearby building looking through a window, observed the aircraft turn to the left at low height near the end of runway 24L. There were no reports of an abnormal engine sound. At 1314:24, the pilot made a radio call stating ‘papa oscar romeo papa oscar romeo MAYDAY MAYDAY MAYDAY’.[2]
The camera footage showed the aircraft’s angle of bank increasing and the aircraft descending before colliding with terrain.
A camera at a building about 180 m to the south‑east of the accident site recorded the engine cowling on the left side opening and closing in the seconds prior to the aircraft’s collision with terrain (Figure 3).
Figure 3: VH-POR showing engine cowl open
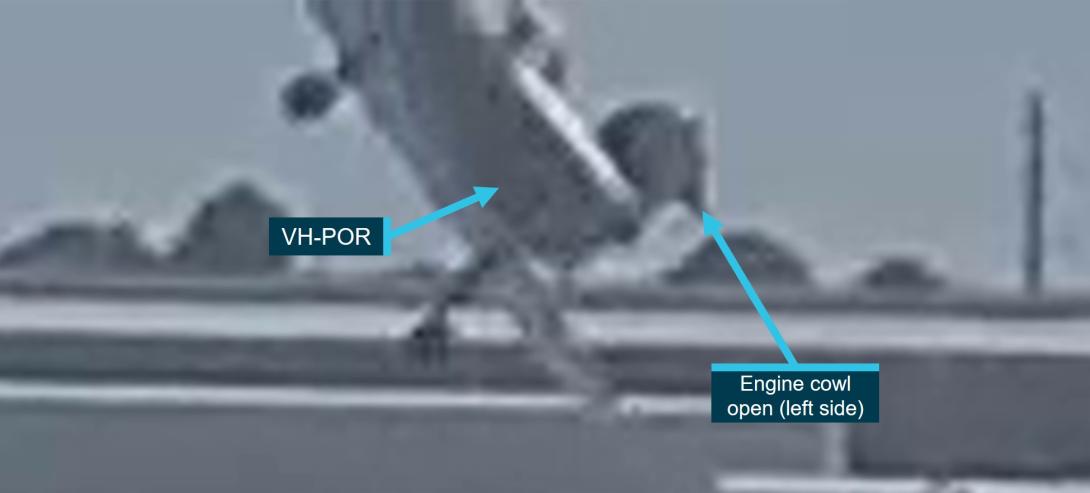
Image source: Supplied, annotated by the ATSB
An instructor with a student pilot who had just landed recalled seeing the aircraft’s engine cowl open and the collision with terrain. The instructor and student taxied to a position adjacent to the accident site to provide assistance. The pilot was initially treated onsite by Royal Flying Doctor Service personnel before being transported to hospital. The pilot succumbed to injuries 3 days later.
Context
Pilot information
The pilot was issued a private pilot licence (aeroplanes) by the United Kingdom Civil Aviation Authority in 1977. The pilot was issued with an Australian private pilot licence (aeroplanes) in 1978 and held a current Civil Aviation Safety Regulation Part 61 Private Pilot (Aeroplane) Licence. The pilot held a valid class 2 civil aviation medical certificate with no restrictions and was required to wear vision correction when flying.
The pilot had no reported significant medical conditions. Toxicology and post-mortem examination reports were not available at the time of publication.
At the time of the accident, the pilot had accumulated about 330 hours total aeronautical experience. In the 12 months prior to the accident, the pilot had flown about 5 hours, 3.5 hours of which was in VH‑POR. The pilot completed a flight review in December 2023, and their last flight prior to the accident was in January 2024. Both flights were in VH-POR.
Aircraft information
General information
The DHC-1 MK 22 Chipmunk is a 2 seat, low-wing aircraft constructed predominantly from light aluminium alloy with fabric covered wings and control surfaces. The aircraft was designed for ab initio military flight training. The Chipmunk was manufactured in Canada, the United Kingdom, and Portugal.
VH‑POR was manufactured in Portugal under licence by Oficinas Gerais de Material Aeronautico[3] (OGMA) in 1958 as a DHC-1 MK 20, and later modified to MK 22 specifications.[4] It was powered by a 4 cylinder de Havilland Gipsy Major 10 MK 2 engine driving a fixed-pitch wooden propeller. The aircraft operated in service with the Portuguese Air Force before being operated privately in the United States from 1979. It was first registered in Australia in 2010, and the accident pilot had been the registration holder since 2018.
A periodic inspection and minor maintenance tasks were carried out on 22 March 2024. At the time of the accident, the aircraft had accumulated 2,082 flying hours.
Engine cowl
Access to the engine is via a cowling door on either side. The cowl doors are hinged at the top and fastened by 2 latches at the bottom of each cowl. The latches are attached to the lower engine cowl and when in the vertical position pass through holes on the cowling doors (Figure 4, left). To fasten the cowl, the latches are pulled outboard, further compressing a pre‑compressed spring, and turned aft (1/4 turn) to the horizontal position. Releasing the latch then fastens the cowl. The latches are held in place by the spring and prevented from unfastening by a tab (Figure 4, right). There was no evidence of pre‑impact damage to the engine cowl latches fitted to VH‑POR (see Wreckage and impact information).
Figure 4: DHC-1 Chipmunk cowl latch detail (exemplar aircraft, left side shown)
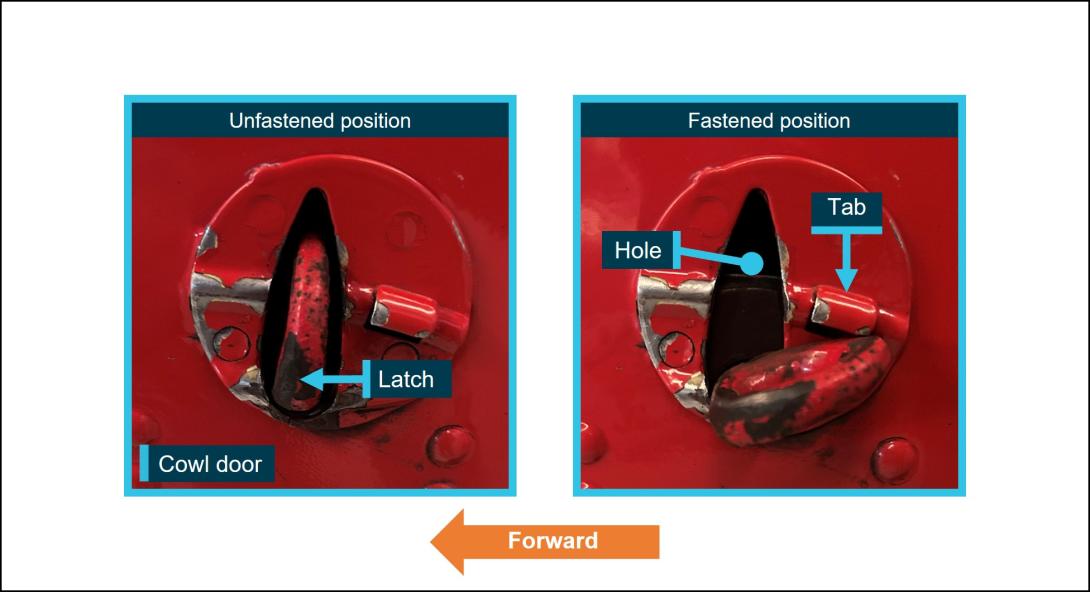
Image source: Supplied, annotated by the ATSB
Fuel line priming and carburettor flooding
A number of actions are required to start the engine of a DHC-1 Chipmunk, including to ensure the lines from the fuel pumps to the carburettor have been filled with fuel (primed). This is accomplished by the use of a hand lever on the rear fuel pump which is accessed via an opening on the left engine cowl. After this is accomplished, the carburettor is flooded[5] using a pull-wire that is accessed via another opening on the left engine cowl. The left engine cowl can be opened to allow direct access instead of using the access openings to perform these actions.
Crashworthiness modification
Modification H.268
The upper structure between the front and rear cockpits of the DHC-1 Chipmunk, corresponding to the attach point for the front cockpit shoulder harness, had 2 mountings, called gussets (Figure 5 and Figure 6).
Figure 5: DHC-1 Chipmunk cockpit showing gusset and shoulder harness locations (exemplar aircraft)
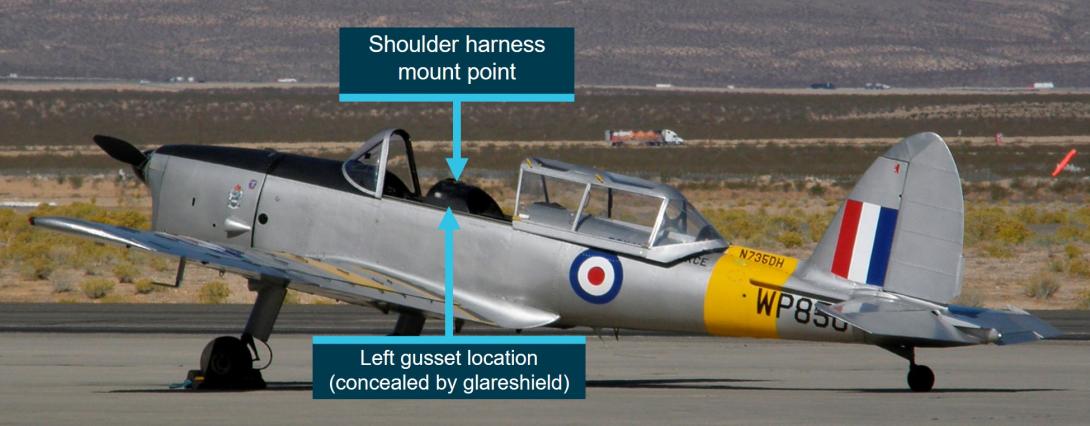
Image source: Alan K. Radecki, annotated by the ATSB
Figure 6: Modification H.268 gusset and rivet location (left side shown)
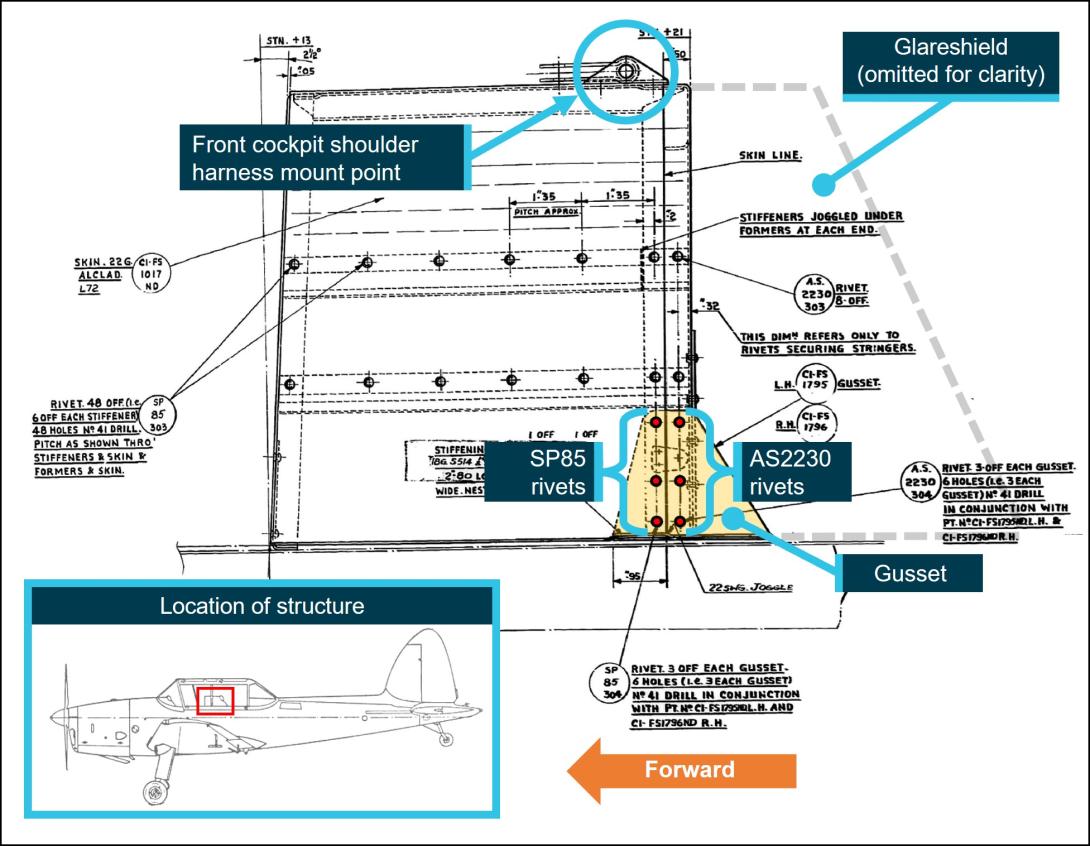
Image source: ATSB, de Havilland Support Ltd, annotated by the ATSB
In October 1966, modification H.268 was issued[6] to strengthen this structure. The modification was classified as ‘desirable’, and was applicable to DHC-1 Chipmunk marks 20 (which included Portuguese-manufactured aircraft), 21, 22, 22A and 23. The modification replaced the original aluminium alloy gussets with high-tensile steel. The modification required the forward row of rivets attaching the structure to the gussets to be part number SP85 mushroom head rivets, and the rear row to be part number AS2230 countersunk rivets. Later testing by the manufacturer subjected the front cockpit shoulder harness of a modified aircraft to a 22 G load, with no failures.
Information on the ATSB examination of relevant components of VH‑POR is presented in Wreckage and impact information.
Technical news sheet 154
On 29 March 1966, in the United Kingdom there was a fatal accident involving a DHC-1 MK 22 Chipmunk, registered G‑ARME. Following the investigation into the accident, Hawker Siddeley[7] issued technical news sheet TNS 154 in May 1967. Compliance with TNS 154 was classified as ‘mandatory’, to be carried out prior to 31 July 1967. The heading indicated that it was applicable to ‘CT(C1)’ series aircraft, meaning those in civilian (non-military) service. TNS 154 also stated that it was for English production Chipmunk aircraft. The ATSB was advised by de Havilland Support Ltd (DHSL) that since the 1990s, the Portuguese Air Force and military operators of DHC-1 Chipmunks in the United Kingdom have been briefed when new technical news sheets were issued.
The procedure to fulfil TNS 154 is summarised as follows. After gaining access to the gussets securing the upper structure between the front and rear cockpits to the fuselage, dimensional checks (diameter and edge distance) were to be made on the 3 bolt holes in each gusset. If either criterion was not met, the aircraft was required to have modification H.268 embodied. Additionally, each gusset was to be inspected for the presence of the correct number of securing rivets.
Applicability to Portuguese manufactured DHC-1 Chipmunks
All Chipmunk aircraft manufactured in Portugal had been originally built to MK 20 specifications. When issued in 1966, modification H.268 was applicable to Portuguese manufactured MK 20 Chipmunks and remained applicable when those aircraft were converted to MK 22 (civilian) specifications. When issued in 1967, TNS 154 was not applicable for MK 20 (military) aircraft but became applicable to any aircraft modified to MK 22 (civilian) specifications.
The available Portuguese records for VH‑POR did not include entries for modification H.268 or TNS 154. The records did however show that various modifications and civilian TNS inspection requirements had been carried out when VH-POR was operating in Portuguese Air Force service.
The aircraft manufacturer (OGMA) advised that it had no record of being advised about modification H.268 by Hawker Siddeley, and that it had received technical news sheet TNS 154 in 1997.
Additionally, the ATSB were advised[8] that the Portuguese Air Force held no records for aircraft serial number OGMA 44 (VH‑POR). However, of the 6 remaining DHC-1 Chipmunk aircraft still operating in Portuguese Air Force service in 2025, records indicate that:
- no aircraft have records of modification H.268 being embodied
- records showed inspections in accordance with TNS 154, and that modification H.268 was not needed.
Australian airworthiness requirements
In 1966, the Australian Department of Civil Aviation (DCA) issued airworthiness advisory circular AAC 1‑3 Chipmunk aircraft – crashworthiness. This document outlined 3 modifications that were considered by the DCA as ‘highly desirable’. The modifications were for the installation of inertia reel shoulder harnesses, energy absorbing seat inserts, and for the modification of the front cockpit shoulder harness mount point structure. For the latter, AAC 1‑3 stated that:
The structural shell which carries the front shoulder harness attachment is in itself quite rigid, but fails by tearing at its attachment to the aircraft upper longerons when subjected to a high load applied through the shoulder harness. A sheet aluminium alloy doubler running from the shoulder harness attach point down to the longeron bolts and using existing rivets and bolts will provide the reinforcement desired.
This modification could be seen in historical photographs of DHC-1 Chipmunk aircraft in Royal Aero Club service in Australia.
In response to TNS 154, an Australian airworthiness directive, AD/DHC-1/18, was issued in August 1967 and mandated that compliance to TNS 154 was required before 1 January 1968. In 2008, AD/DHC-1/18 was cancelled on the basis that ‘as all affected aircraft would have been inspected and modified by now, this AD is no longer required.’
VH-POR crashworthiness modification
No records from the aircraft’s time in the United States were available for examination. Maintenance records from the time the aircraft was registered in Australia were available to the investigation, along with incomplete records from the aircraft’s service in Portugal. There was no record available showing whether modification H.268 or the requirements of technical news sheet TNS 154 having been carried out on VH‑POR. Examination by the ATSB of the aircraft showed that modification H.268 had been embodied (the relevant mountings, or gussets, were steel as required by H.268) at an unknown time, and with non-conforming rivets (see Rivet examination).
Aerodrome information
Jandakot Airport is a certified, controlled airport. It had 3 asphalt runways:
- 06R/24L[9] (1,150-m long)
- 06L/24R (in parallel with 06R/24L and 1,392-m long)
- 12/30 (1,508-m long).
The accident flight took off from runway 24L, which was only available from sunrise to sunset, and at all times the circuit direction was left (turns made in the circuit were to the left).
Wreckage and impact information
General information
The wreckage had been relocated to a secure hangar on Jandakot Airport prior to the arrival of ATSB investigators. Further, the accident site had been decontaminated after the wreckage was relocated due to a significant fuel spill. Therefore, a detailed survey of the impact location was not possible. However, in addition to the 2 cameras showing the flight and accident, the ATSB obtained photographs of the site provided by first responders.
The ATSB examined the wreckage in the hangar. All major aircraft components were accounted for, and the propeller showed evidence that the engine was running at impact. The engine control pushrods in the engine compartment had been fractured by impact forces. Flight control continuity was established. The wing flaps were assessed to have likely been in the retracted position at the time of impact, which is a permissible setting for take-off.
Damage to the engine cowl latches was indicative of the latches being correctly fastened on the right side but unfastened on the left at the time of impact. The engine cowls and latches were otherwise undamaged.
Cockpit structure
The ATSB found that on impact the upper structure between the front and rear cockpits, corresponding to the attach point for the front cockpit shoulder harness, was torn away from its mountings (Figure 7). All 12 rivets (6 per side) that attached the structure to the mountings had sheared.
Figure 7: Detached upper structure showing harness attach point and location of sheared rivets
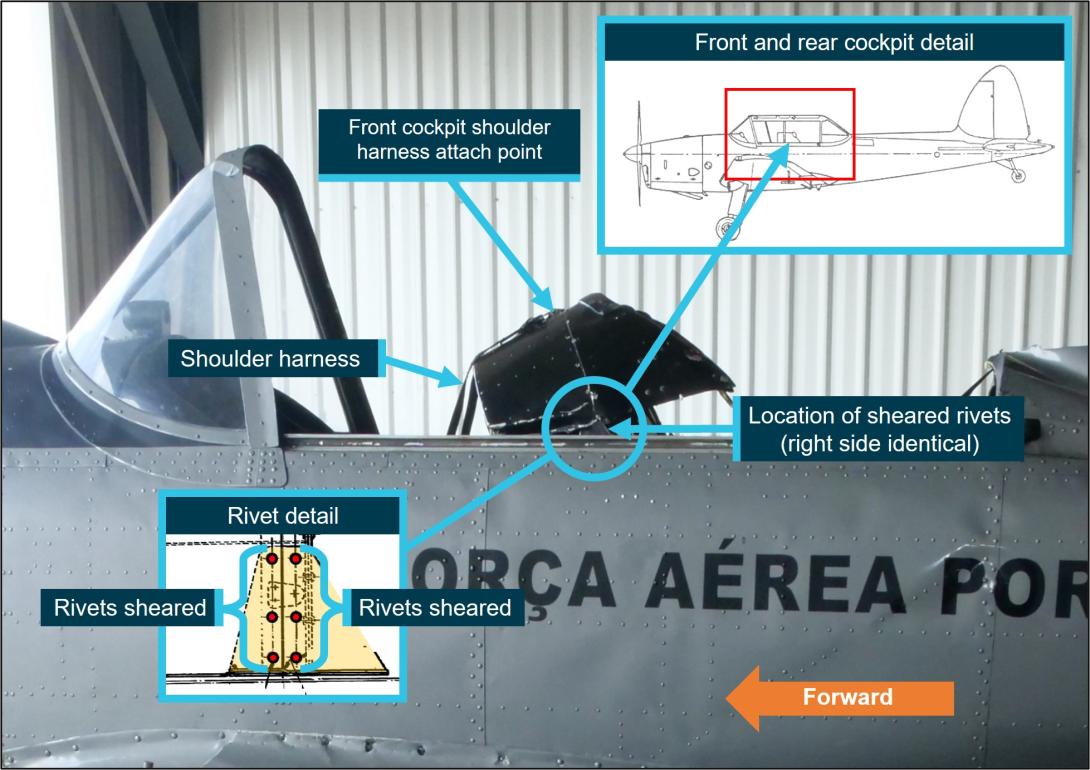
Upper structure has been placed in position for the photograph and is representative of its position immediately post-accident. Image source: ATSB, de Havilland Support Ltd (detail), annotated by the ATSB
Rivet examination
The gussets fitted to VH‑POR were steel, rather than aluminium alloy, which indicated that modification H.268 had been embodied. This modification also required the use of part number SP85 and AS2230 rivets. Both types were required to be manufactured to British standard L.86, which was an aluminium alloy that included copper and magnesium.[10] The standard also specified that the rivets were to be anodised (a surface treatment) and coloured violet.
The sheared rivets and coatings from VH‑POR were examined and tested by the ATSB using metallurgical equipment. It was determined that:
- The material composition of the rear row of rivets (countersunk) was consistent with pure or near-pure aluminium[11] and therefore a non-conforming specification. Testing indicated a significant reduction in strength, estimated to be about one-third of the strength of the specification rivets.
- The material composition of the forward row of rivets (mushroom head) was consistent with an alloy consistent with L.86. The rivets were coated with a gold-coloured chromate conversion coating instead of violet anodising. ATSB testing indicated that the strength of the rivets met or exceeded literature values for L.86 alloy.
The presence of the non-conforming rivets significantly reduced the integrity of the structure retaining the front cockpit restraint, and thereby compromised the crashworthiness of the aircraft. This non-conforming modification may be present in other Chipmunk aircraft, in which case it would likely affect survivability in an accident.
To advise DHC‑1 Chipmunk maintainers and owners of the importance of carrying out this modification to the required specification, the ATSB issued a safety advisory notice (AO‑2024‑013‑SAN‑01) on 11 September 2024.
Survival aspects
The ATSB attempted to determine the impact velocity and deceleration imparted on the aircraft’s structure during the accident. As there was no recorded data[12], calculations of deceleration during the impact were made using estimates of the aircraft’s velocity and angle of impact. Additionally, assumptions were required in the analysis resulting in a wide range of possible outcomes across the established threshold for human tolerance. As a result, the ATSB was unable to definitively determine whether the impact accelerations were within or exceeded the levels considered tolerable for human survival.
Similarly, it was not possible to determine whether the longitudinal force was greater than the force that the restraints were known to withstand in testing (22 G) and therefore not possible to determine whether the correct rivets would also have failed had they been fitted.
Flight path analysis
The pilot’s handbook and pilot’s notes for the Chipmunk state that normal take-off speed is 45 kt, climb speed is 70 kt, and stall speed is 47 kt with the wing flaps up. The ATSB estimated from camera footage of the accident flight that the aircraft’s angle of bank increased to about 55° during its turn while maintaining about 130 ft, immediately prior to the descent (Figure 8). It was not possible to accurately estimate its airspeed at this time.
Figure 8: VH-POR angle of bank during left turn after take-off
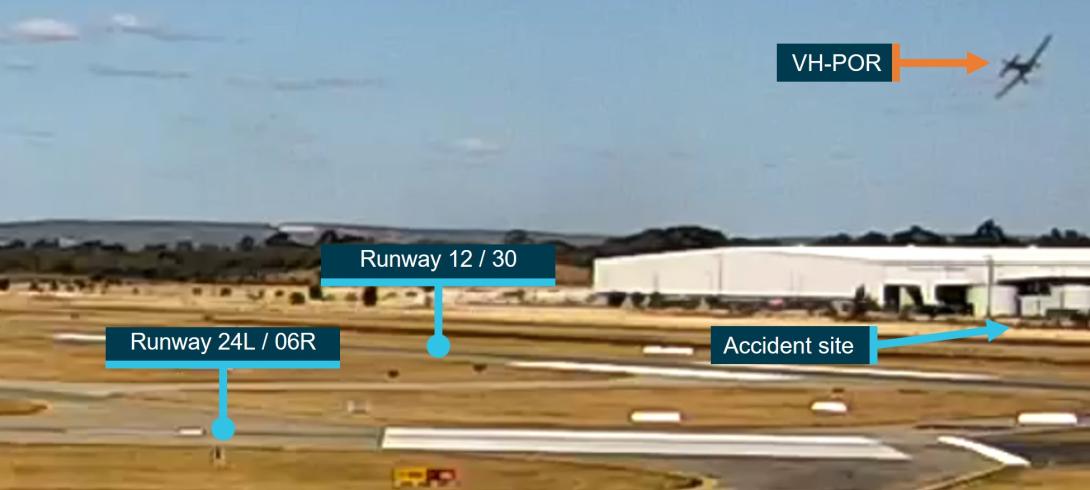
Image source: Supplied, annotated by the ATSB
The aerodynamic stall[13] speed of aircraft in a steady turn increases appreciably with an angle of bank greater than 30°, and at angles greater than 45° there is a rapid increase in stall speed. At 55° angle of bank, stall speed is increased by about 32%. The Chipmunk’s stall speed in a 55° steady turn while maintaining level flight would have therefore been about 62 kt.
Guidance on manoeuvring at low level
The 2024 Civil Aviation Safety Authority information card Preventing a stall at low level (2405.4903) provided tips for pilots including:
Manoeuvring at low level increases the chances of a low-level stall.
…
Remember that turns and any application of ‘G’ will increase the stall speed – sometimes dramatically.
…
Try to avoid using more than 30 degrees of bank in the circuit. Use coordinated controls.
The 2010 ATSB educational publication Avoidable Accidents No. 3 - Managing partial power loss after take-off in single-engine aircraft (AR-2010-055) noted that:
A turnback requires accurate flying during a period of high stress to prevent a stall and possibly a spin occurring. If an aerodynamic stall and or spin occurs, given that these circumstances are likely to be at low level, there is little likelihood of a successful recovery. With careful management and by being aware of the hazards that can lead to loss of control events, the risk of being involved in a stall/spin accident can be reduced.
During a non-normal or emergency event in-flight, and particularly in a critical phase of flight such as initial climb and final approach, there can be a high cognitive workload placed on the pilot. In such a situation, a pilot’s hierarchical priorities are to ensure the aircraft remains in controlled flight, navigate (such as to a suitable landing area) and, if time permits, communicate the nature of the emergency to air traffic control enabling them to respond appropriately. These hierarchical priorities are colloquially known as ‘aviate, navigate, communicate’.
Related occurrences
The ATSB was advised by DHSL of an occurrence in the United Kingdom where the left engine cowl of a DHC-1 Chipmunk opened in flight. The pilot of that aircraft reported that by sideslipping[14] the aircraft, the cowling slammed shut until the aircraft was straightened for touchdown when it opened again. The aircraft landed safely, and there was no reported damage to the cowling.
Additionally, a DHC-1 Chipmunk subject matter expert advised the ATSB of 3 other occurrences in Australia involving a Chipmunk where the left cowl opened in flight. The ATSB was able to obtain formal investigation records about one of these accidents (described below). On the other 2 occasions there were no reported issues with performance or controllability, and both aircraft landed safely. There was minor damage to the left cowl on one aircraft.
Accident involving DHC-1 MK 10 Chipmunk, VH-RFW at Bull Creek, Western Australia on 19 September 1959
On 19 September 1959, the pilot of a DHC‑1 MK 10 Chipmunk, registered VH‑RFW, had difficulty recovering from a spin during aerobatic manoeuvres and entered a dive, during which the left engine cowl opened then slammed shut. The investigation report did not state whether the cowl stayed shut or opened again. When the pilot applied power to return to Perth Airport, the engine did not respond, and the throttle lever was reportedly loose. The pilot elected to land at an emergency airstrip at Bull Creek. During landing the pilot inadvertently approached downwind and the aircraft overshot the runway, collided with trees and caught fire. The pilot survived and was treated for burns in hospital. The investigation found that the left engine cowl had been unfastened, and had damaged the throttle linkage as it slammed closed in flight.
Safety analysis
Engine cowl latches
In preparing the aircraft for flight, it is possible that the fuel line priming and carburettor flooding functions were carried out by opening the left engine cowl, rather than via the openings on it, and that the cowl was then left unsecured. Alternatively, the cowl might have been opened for another reason or left unfastened from previous activities. In any case, the pilot did not detect that the engine cowl latches on the left side had been left unfastened prior to boarding the aircraft and commencing taxi. After take-off, the cowl was free to open and close in flight.
Left turn after take-off
This accident, and the 1959 accident involving VH‑RFW, demonstrate that the engine cowl being free to open and close in‑flight can be hazardous. However, while by no means a benign event, there were 2 anecdotally reported occasions involving DHC-1 Chipmunks where the left engine cowl was not secured. With these, there were no reported performance or controllability issues, and the aircraft were able to be recovered safely. Nevertheless, in this case the engine cowl began flapping after take-off, and the pilot would have been likely distracted and experiencing a high cognitive workload while managing the in-flight emergency.
From the available evidence, there were no indications of pre-impact defects, configuration issues (other than the cowl being unfastened), or controllability issues. There were no engine issues, and it is very likely the aircraft’s engine controls had not been damaged in a similar way to the accident involving VH‑RFW. The reason for the pilot commencing a left turn after take-off could not be determined, though it is possible that the pilot was attempting to recover by conducting a circuit and returning to Jandakot Airport.
During the turn the pilot made a MAYDAY call, and the aircraft’s angle of bank then increased until reaching about 55°. The rapid increase in stall speed associated with higher angles of bank resulted in the aircraft aerodynamically stalling at a height where recovery was not possible.
While the pilot was appropriately licenced and had completed a flight review using VH‑POR about 4 months prior to the accident, the extent to which the pilot’s limited recent experience influenced their actions could not be established.
Non-conforming rivets and survivability
On an unknown date, potentially many years previously, rivets that did not conform to the design specification had been fitted to the mountings between the front and rear cockpits. Importantly, the attach point for the front cockpit shoulder harness was attached to this structure. Testing indicated a significant reduction in strength in half of the rivets (the aft 3 rivets on both sides), estimated to be about one-third of the strength of the specification rivets.
During the accident, all of the rivets securing the structure failed. However, it was not possible to establish whether the correct rivets would also have failed, and the impact deceleration alone may have been above expected human tolerance. Therefore, it was not possible to establish whether the presence of non-conforming rivets affected survivability in this instance. Regardless, the presence of non-conforming rivets was a latent threat to the aircraft’s crashworthiness and reduced the likelihood of an accident being survivable.
As complete records for the aircraft were not available, it was not possible to determine where or when the rivets had been installed. The 6 DHC-1 Chipmunk aircraft still operating in Portuguese Air Force service had been inspected but not modified, and this likely occurred after the aircraft manufacturer (OGMA) received TNS 154 in 1997. It is therefore likely that VH‑POR had not been inspected under TNS 154 in Portugal prior to 1979 when the aircraft was privately registered in the United States, and modification H.268 was likely carried out some time later. While the existing rivets would have been replaced when the H.268 modification was made, some or all may have been replaced again later.
This non-conforming modification may be present in other Chipmunk aircraft, in which case it would likely affect survivability in an accident.
Australian airworthiness directive
The Australian airworthiness directive relating to TNS 154, AD/DHC-1/18, was issued when the aircraft operating in Australia had been manufactured in England, and therefore meeting the stipulated applicability for TNS 154. The airworthiness directive was cancelled in 2008 (before VH‑POR was first registered in Australia) on the expectation that all aircraft by that time had been inspected and modified. Read strictly, the cancellation did not account for the possibility that an aircraft could have been inspected, met the dimensional criterion, and therefore not modified in accordance with H.268.
Findings
ATSB investigation report findings focus on safety factors (that is, events and conditions that increase risk). Safety factors include ‘contributing factors’ and ‘other factors that increased risk’ (that is, factors that did not meet the definition of a contributing factor for this occurrence but were still considered important to include in the report for the purpose of increasing awareness and enhancing safety). In addition ‘other findings’ may be included to provide important information about topics other than safety factors. These findings should not be read as apportioning blame or liability to any particular organisation or individual. |
From the evidence available, the following findings are made with respect to the collision with terrain involving Oficinas Gerais de Material Aeronautico DHC-1 MK 22 Chipmunk, VH‑POR at Jandakot Airport, Western Australia on 26 April 2024.
Contributing factors
- The pilot did not detect that the engine cowl latches on the left side had been left unfastened prior to commencing taxi. After take-off, the cowl was free to open and close in flight.
- During a low level, high angle of bank turn, and while the pilot was likely distracted by the flapping engine cowl and experiencing a high cognitive workload, the aircraft aerodynamically stalled and collided with terrain.
Other factors that increased risk
- Rivets that did not conform to the design specification had been fitted to mountings between the front and rear cockpits and significantly reduced the integrity of the structure retaining the front cockpit restraint. This compromised the crashworthiness of the aircraft; however, the effect on survivability in this accident could not be determined.
Safety actions
Safety advisory notice to DHC-1 Chipmunk maintainers and owners
SAN number: | AO-2024-013-SAN-01 |
SAN release date: | 11 September 2024 |
The ATSB advises DHC-1 Chipmunk maintainers and owners to be aware that fitment of non‑conforming rivets where the upper structure between the front and rear cockpits attaches to the gussets on either side could significantly compromise the crashworthiness of the aircraft.
Those conducting work on aircraft must ensure modifications are carried out to the required specification, or during maintenance returned to that specification.
Proactive safety action taken by the GPIAAF
Action number: | AO-2024-013-PSA-01 |
Action organisation: | Gabinete de Prevenção e Investigação de Acidentes com Aeronaves e de Acidentes Ferroviários (GPIAAF) |
Action status: | Closed |
The Portuguese Office for the Prevention and Investigation of Accidents in Civil Aviation and Rail (GPIAAF) published information from the ATSB’s safety advisory notice (AO-2024-013-SAN-01) in its Civil Aviation Quarterly Bulletin Publication (issue QB 03/2024) in October 2024.
Sources and submissions
Sources of information
The sources of information during the investigation included:
- Air Accidents Investigation Branch (United Kingdom)
- Airservices Australia
- Civil Aviation Safety Authority
- de Havilland Support Ltd
- Gabinete de Prevenção e Investigação de Acidentes com Aeronaves e de Acidentes Ferroviários (Portugal)
- National Archives of Australia
- OGMA Indústria Aeronáutica de Portugal
- Portuguese Air Force
- Royal Aero Club of Western Australia
- Western Australia Police Force
- accident witnesses
- camera footage of the accident flight and other photographs taken on the day of the accident
- subject matter experts.
Acknowledgement
The ATSB would like to acknowledge the significant assistance provided by multiple DHC-1 Chipmunk subject matter experts during the onsite investigation phase and evidence collection activities.
References
National Archives of Australia B638, 6/659/133 - Accident at Bulls [sic] Creek on 19/9/1959: DHC‑1 A/C: VH‑RFW [includes photographs and plans], 1959 - 1960.
Submissions
Under section 26 of the Transport Safety Investigation Act 2003, the ATSB may provide a draft report, on a confidential basis, to any person whom the ATSB considers appropriate. That section allows a person receiving a draft report to make submissions to the ATSB about the draft report.
A draft of this report was provided to the following directly involved parties:
- Air Accidents Investigation Branch (United Kingdom)
- Civil Aviation Safety Authority
- De Havilland Aircraft of Canada Limited
- de Havilland Support Ltd
- Gabinete de Prevenção e Investigação de Acidentes com Aeronaves e de Acidentes Ferroviários (Portugal)
- Royal Aero Club of Western Australia
- Transport Safety Board of Canada.
The submissions were reviewed and, where considered appropriate, the text of the report was amended accordingly.
Purpose of safety investigationsThe objective of a safety investigation is to enhance transport safety. This is done through:
It is not a function of the ATSB to apportion blame or provide a means for determining liability. At the same time, an investigation report must include factual material of sufficient weight to support the analysis and findings. At all times the ATSB endeavours to balance the use of material that could imply adverse comment with the need to properly explain what happened, and why, in a fair and unbiased manner. The ATSB does not investigate for the purpose of taking administrative, regulatory or criminal action. TerminologyAn explanation of terminology used in ATSB investigation reports is available here. This includes terms such as occurrence, contributing factor, other factor that increased risk, and safety issue. Publishing informationReleased in accordance with section 25 of the Transport Safety Investigation Act 2003 Published by: Australian Transport Safety Bureau © Commonwealth of Australia 2025
Ownership of intellectual property rights in this publication Unless otherwise noted, copyright (and any other intellectual property rights, if any) in this report publication is owned by the Commonwealth of Australia. Creative Commons licence With the exception of the Commonwealth Coat of Arms, ATSB logo, and photos and graphics in which a third party holds copyright, this report is licensed under a Creative Commons Attribution 4.0 International licence. The CC BY 4.0 licence enables you to distribute, remix, adapt, and build upon our material in any medium or format, so long as attribution is given to the Australian Transport Safety Bureau. Copyright in material obtained from other agencies, private individuals or organisations, belongs to those agencies, individuals or organisations. Where you wish to use their material, you will need to contact them directly. |
[1] See Engine cowl.
[2] MAYDAY: an internationally recognised radio call announcing a distress condition where an aircraft or its occupants are being threatened by serious and/or imminent danger and the flight crew require immediate assistance.
[3] Currently known as OGMA Indústria Aeronáutica de Portugal.
[4] The DHC-1 MK 20 was the export version of the original MK 10 manufactured for military service in the United Kingdom. For civilian use, aircraft were modified to MK 22 and other specifications.
[5] Flooding fills the carburettor float bowl by depressing its float and overriding the float’s normal function which is to shut off fuel flow to the carburettor bowl when it reaches a set level.
[6] Modification H.268 was amended in March 1967.
[7] Hawker Siddeley was the type certificate holder at the time.
[8] The Portuguese Office for the Prevention and Investigation of Accidents in Civil Aviation and Rail (GPIAAF) established contact with the Portuguese Air Force on the ATSB’s behalf and provided a response.
[9] Runway numbering: represents the magnetic heading closest to the runway orientation (for example, runway 24L is oriented 236º magnetic).
[10] International equivalences were Alloy Designation 2117, US specification AMS7222, and European specification ENAW-AlCu2.5Mg).
[11] The composition was not determined exactly; there was >99% aluminium with some alloying iron and silicon, consistent with 1000-series aluminium, although the specific alloy could not be determined.
[12] The aircraft was not fitted with flight or engine recording devices, and there was no requirement to do so.
[13] Aerodynamic stall occurs when airflow separates from the wing’s upper surface and becomes turbulent. A stall occurs at high angles of attack, typically 16˚ to 18˚, and results in reduced lift.
[14] Sideslipping is a manoeuvre in which controls are deliberately crossed, for example to sideslip to the left, the aircraft is banked to left while right rudder is applied.