Executive summary
What happened
On 11 April 2024, a flight instructor and student pilot were conducting a dual training flight under the instrument flight rules in a Beechcraft E55 aircraft, registered VH-OMD and operated by Fly Oz. The aircraft departed from Cowra Airport, New South Wales, and conducted instrument approaches to Goulburn and Canberra Airports, before returning to Cowra.
As the aircraft tracked over the Cowra non-directional beacon (NDB) to conduct a practise instrument approach to runway 15, the instructor simulated a failure of the left engine by moving the mixture lever to the idle cut-off position. The student continued the approach with the left engine inoperative and the propeller windmilling, then joined the circuit for runway 33 on the crosswind leg.
During the landing flare, the instructor initiated a go-around. The aircraft rapidly yawed and rolled to the left and impacted the ground in an almost vertical nose-down attitude before coming to rest inverted. The flight crew sustained minor injuries and the aircraft was substantially damaged.
What the ATSB found
The ATSB found that the instructor moved the left engine mixture lever to idle cut-off to simulate an engine failure over the navigation aid, and it was likely that they unintentionally did not subsequently move the lever to rich and ensure the engine was restarted and available for instant use, when attempting to set zero thrust on the downwind leg of the circuit. As a result, the instructor initiated a go-around below the minimum control speed, unaware the left engine was inoperative, resulting in an asymmetric loss of control.
The ATSB also found that Fly Oz's asymmetric training procedure involved failing one engine using the mixture control without confirmation the engine was subsequently restarted, rather than reducing throttle to simulate zero thrust in accordance with the Beechcraft E55 Airplane Flight Manual. The use of the throttle to simulate an engine failure ensures the engine is available for immediate use, whereas using the mixture control increased the risk of an undetected inoperative engine during descent and landing, and the associated loss of control.
What has been done as a result
Fly Oz amended its multi-engine training to simulate engine failures only using throttle at any height. It has also taken the following proactive safety action:
- Following a simulated engine failure, zero thrust is to be set immediately after the student has completed the engine failure drills.
- The instructor standardisation manuals were being updated to include a requirement that both the student and instructor confirm that the pitch, power and mixture controls are set back to normal 2‑engine configuration during checks on final. This is now a call out item, ensuring that both pilots are satisfied with the correct settings.
Safety message
In conventional twin-engine aeroplanes, loss of power on one engine can lead to a loss of directional control and an accident if there is insufficient height above the ground to recover.
Aircraft manufacturers’ procedures for one engine inoperative training should be followed in the first instance. In this case, the manufacturer required the throttle be used to simulate an engine failure. In addition to the manufacturer’s procedures, Civil Aviation Safety Authority guidance recommended using the throttle rather than the mixture to simulate an engine failure when at low level – such as asymmetric instrument approaches. This ensures power can quickly be restored if needed.
Accidents as a result of engine malfunctions in twin-engine aeroplanes are rare, but often fatal. As such, training to manage one engine inoperative flight is important, but should not introduce unnecessary risks.
The occurrence
On 11 April 2024, a student pilot and flight instructor were conducting a dual instructional flight in a Beechcraft E55 aircraft, registered VH-OMD and operated by Fly Oz. The flight was the student’s third multi-engine aeroplane navigation exercise. The flight was to be conducted under the instrument flight rules,[1] from Cowra, New South Wales (NSW), to Canberra, Australian Capital Territory, and return. As the flight was conducted almost entirely in visual meteorological conditions,[2] the student wore a view limiting device or ‘hood’, to simulate flying in cloud or poor visibility.
OzRunways[3] flight path data showed that the aircraft departed Cowra Airport at 1156 local time. En route to Canberra, the student conducted an instrument approach[4] to Goulburn Airport, NSW, but did not land there. The student then conducted an instrument approach to Canberra, landed and taxied to the general aviation apron. After a short break, and without shutting down the engines, the aircraft departed Canberra Airport at 1323 via a standard instrument departure. The aircraft climbed to 10,000 ft above mean sea level (AMSL), tracked via waypoint AVBEG and commenced a descent when 35 NM from Cowra (Figure 1).
Figure 1: VH-OMD track from Cowra to Goulburn, Canberra and return via AVBEG
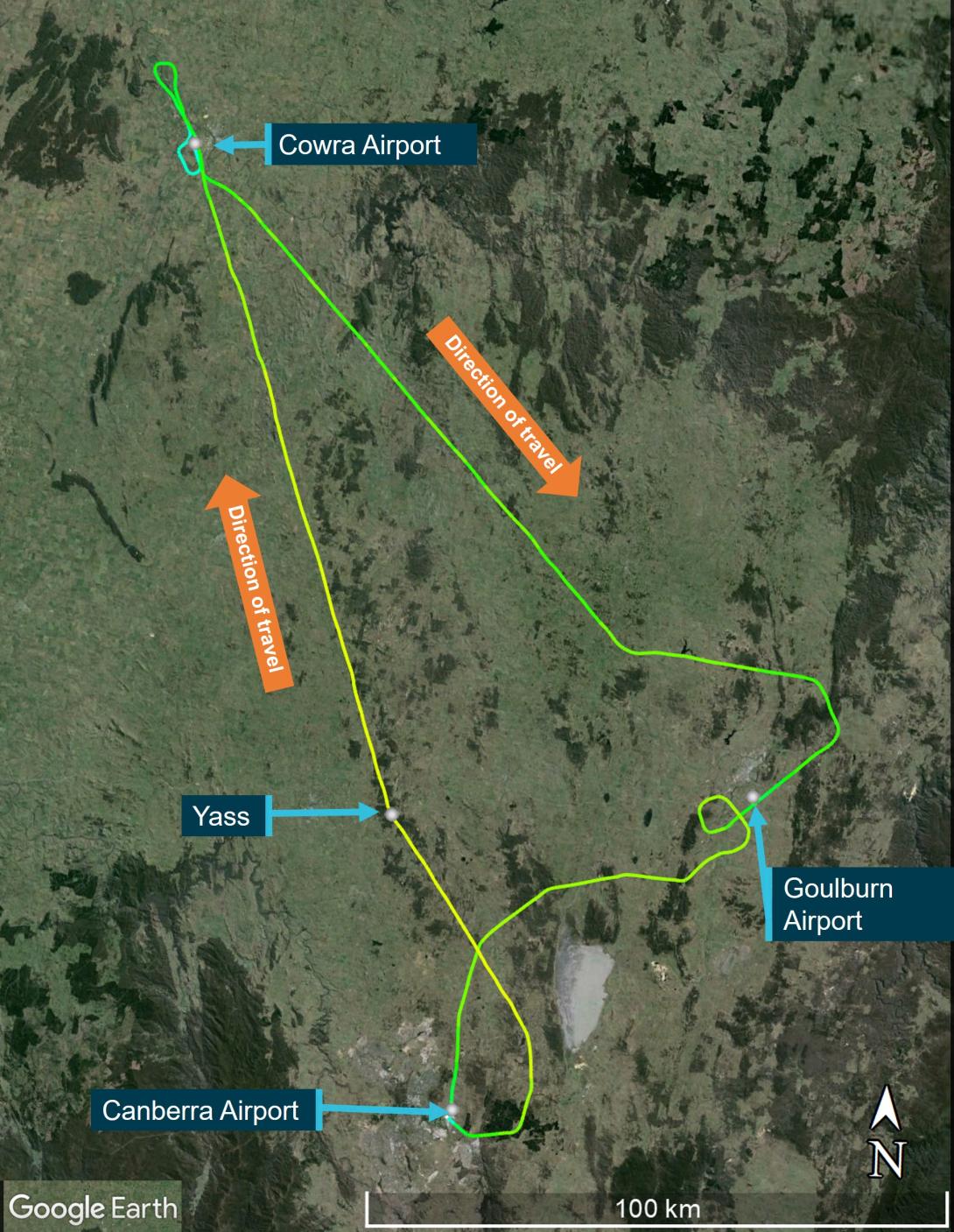
Source: OzRunways data overlaid on Google Earth, annotated by the ATSB
At 1404, the aircraft passed over the Cowra non-directional beacon (NDB)[5] at about 3,600 ft AMSL (2,600 ft above ground level) and commenced the NDB approach to runway 15. The instructor then simulated an engine failure, by pulling the left engine mixture control lever to the idle cut-off position. In that position, no fuel would flow from the injectors to the engine, but the magnetos would continue generating spark, and the propeller blades would windmill[6] unless feathered.[7]
In response, the student conducted initial engine failure checks and identified that the left engine was inoperative. At that time, the flight crew did not complete the operator’s one engine inoperative procedure to either feather the left propeller or set zero thrust to simulate a feathered propeller (see the section titled Simulated one engine inoperative – Fly Oz procedures). The flight path data showed that, consistent with the simulated left engine failure, the aircraft deviated left of the published outbound track, and tracked outbound on the published inbound track for about 2 minutes, before starting to correct to the right (Figure 2).
Figure 2: VH-OMD track overlaid on published Cowra NDB approach
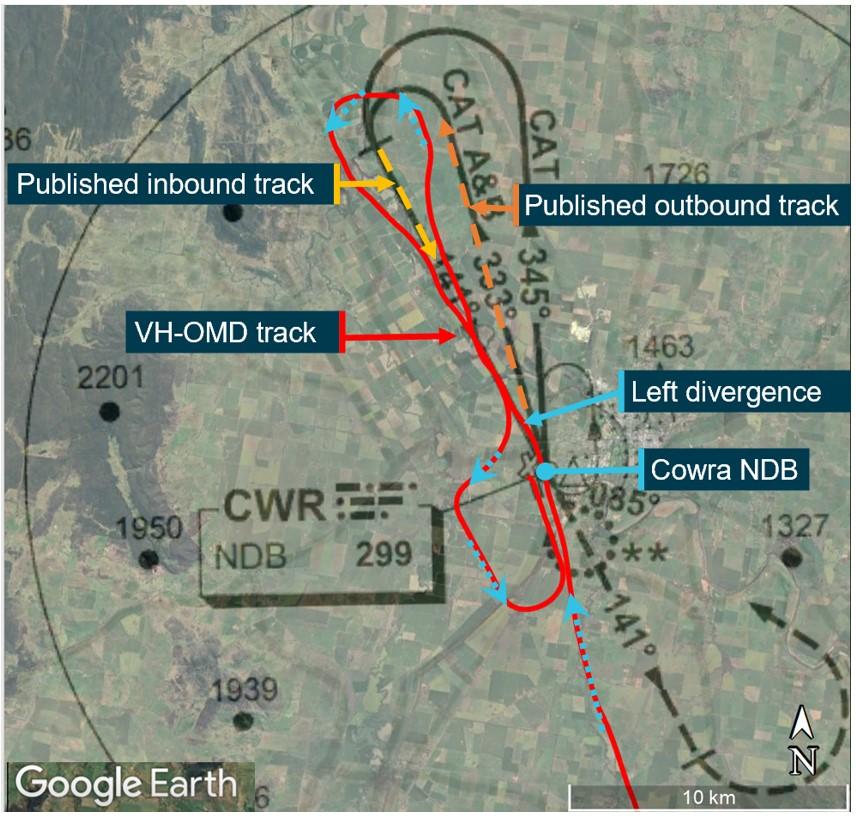
Source: OzRunways and Airservices Australia data overlaid on Google Earth, annotated by the ATSB
About 4 minutes after passing over the NDB, the aircraft commenced a left inbound turn and was established within the required 5° tolerance of the published inbound track about 5 NM from the threshold of runway 15.
The Cowra Airport common traffic advisory frequency (CTAF) was not recorded. However, the student reported making the standard radio calls, including broadcasting when inbound and on downwind, and using the word ‘asymmetric’ in their calls to alert others that they were practising one engine inoperative procedures. The instructor reported communicating with the pilots of 2 other aircraft operating in the circuit at the time. Those 2 aircraft were operating on runway 33, which was the most into wind runway. To sequence with the circuit traffic, the instructor advised the student they were now ‘visual’ and could lift the hood and track to join the crosswind leg of the circuit for runway 33.
The instructor thought that they had set zero thrust either when inbound on the instrument approach or on the downwind leg of the circuit, and recalled first asking the student whether they wanted zero thrust set. However, the student recalled prompting the instructor to set zero thrust on downwind. The instructor reported that their normal procedure for setting zero thrust was to bring the propeller pitch lever to the feather detent, then push the mixture lever forward to rich and gradually move the left throttle lever forward until the manifold pressure gauge read about 10 inches Hg.[8] The instructor reported that, although they usually moved the engine/propeller controls slowly, there would be a detectable yaw[9] associated with returning power to the inoperative engine.
The student and instructor both reported that the student’s normal downwind checks included checking both mixture levers were in the fully rich position, but neither could recall when the checks were done. The student recalled extending the landing gear either just before, or when turning onto, the base leg of the circuit. Neither the instructor nor the student recalled when the student extended the approach (15°) stage of flaps. After turning onto final, the student reported completing their pre-landing checks by pushing both pitch levers forward to the full fine position, checking they had 3 green lights, which indicated the landing gear was down and locked, and electing not to extend full (30°) flap for landing.
A review of recorded flight data identified that the aircraft crossed the runway threshold at 1416:01 aligned with the runway centreline. The instructor reported that the student commenced the flare[10] a bit high and therefore directed them to add some power to cushion the landing. The instructor further reported that when the student added power, the aircraft immediately yawed significantly to the left such that it was no longer aligned with the runway. In response, the instructor called for a go-around. The student could not recall being asked to add power and reported that the main landing gear touched down on the runway before the instructor initiated the go-around. However, the instructor recalled that the wheels did not touch down and that the go-around commenced about 30–50 ft above the runway.
OzRunways data showed that the aircraft started to deviate left of the runway centreline at 1416:14 at 69 kt ground speed, but there was insufficient recorded information to determine whether or not it touched down prior to that occurring. The instructor reported taking control of the aircraft from the student and verifying that both throttle levers were fully forward. Assessing that the yaw was due to left rudder input by the student, the instructor called for the student to let go of the controls and applied right rudder, but was unsuccessful in regaining control of the aircraft. A witness facing away from the runway heard what they assessed as one engine power up and turned to see the aircraft 10–20 ft above the runway, pitched 10–12° nose-up, and in a rapid left roll (Figure 3).
Figure 3: VH-OMD track along the runway, accident site and witness location
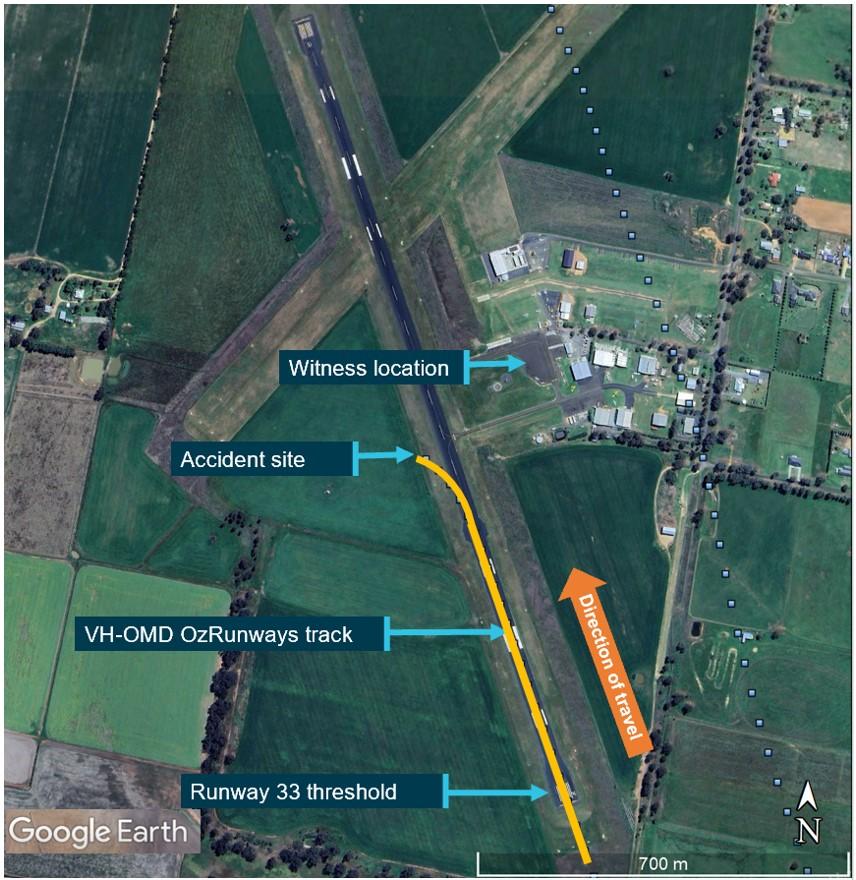
Source: OzRunways data overlaid on Google Earth, annotated by the ATSB
The aircraft collided with the ground in a nearly vertical nose-down attitude and came to rest inverted (Figure 4). The student and instructor sustained minor injuries and it is possible that their recollection of events may have been affected by trauma associated with the collision. The aircraft was substantially damaged.
Figure 4: VH-OMD accident site
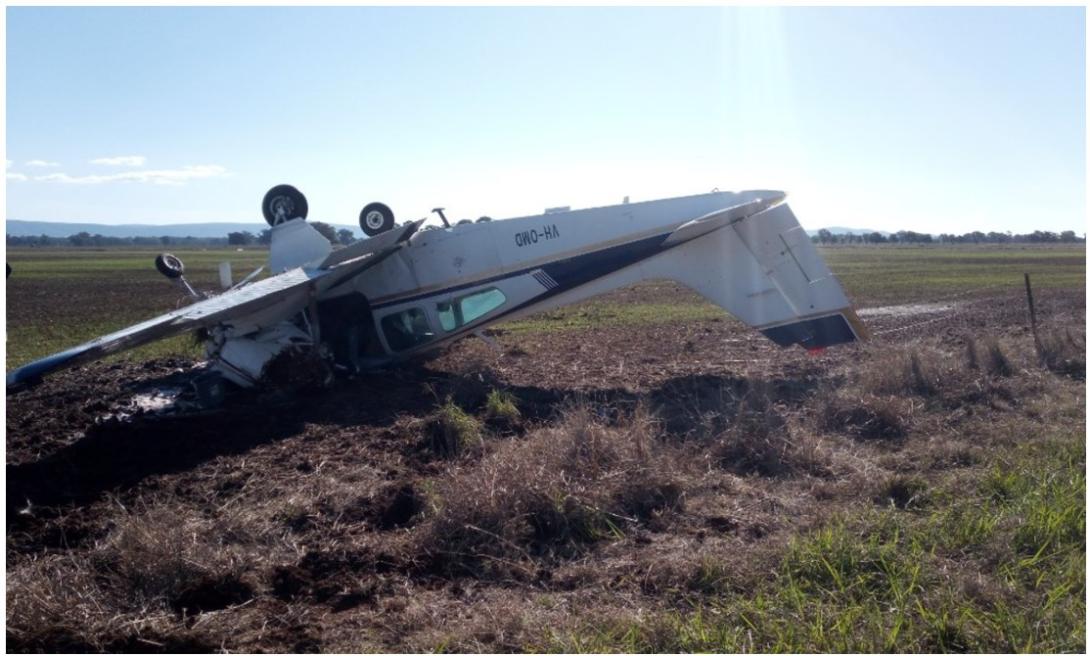
Source: Cowra Council
Context
Personnel information
The student was enrolled in Fly Oz’s commercial pilot licence (aeroplane), multi-engine aeroplane class and command instrument rating integrated flight training course. At the time of the accident, the student held a private pilot licence (aeroplane) and had accrued 247 hours of flying time, 11 of those in VH-OMD (all in the last 90 days), with 7 hours recorded as instrument flight time.
The instructor held a commercial pilot licence (aeroplane), with multi-engine aeroplane class and command instrument ratings, which they had attained at Fly Oz. The instructor had accrued 850 hours of flying time, of which 82.8 were in VH-OMD (70.3 of those in the last 90 days and 43.5 hours recorded as instrument flight time).
Aircraft information
General
VH-OMD was a Beechcraft E55 (serial number TE-970), manufactured in the United States (US) in 1974 and first registered in Australia in 1990. Fly Oz was not the registered operator[11] of VH‑OMD but hired the aircraft and had been using it for training and charter operations for about 6 months.
The aircraft was powered by 2 Continental IO-520-C 6-cylinder, horizontally‑opposed, fuel‑injected engines rated at 285 hp at 2,700 RPM and fitted with 2 Hartzell 3-bladed full‑feathering constant speed propellers (PHC-C3YF-2UF).
The maintenance release[12] current on the accident day showed that the aircraft was approved to operate under instrument flight rules and charter categories. The maintenance release was issued on 9 April 2024 with an aircraft total time in service of 4,622.1 hours. Since then, 2 flights totalling 8.8 hours flight time had been conducted prior to the accident day. There were no recorded defects or outstanding maintenance.
The aircraft departed with a take-off weight of 2,190 kg and operated within the approved weight and balance envelope during the flight, at mid-range centres of gravity.
Fuel system
The fuel system included multiple individual fuel cells with a total capacity of 651 L. The fuel cells had elastomeric liners capable of tolerating large deformation without rupture. In an impact, this reduced the likelihood of an explosive fuel-air mist compared with unlined metal tanks. The fuel selector was an OFF-ON-CROSSFEED arrangement for each engine with the selector panel located on the floor.
Each engine had a 2-speed electric (auxiliary) fuel boost pump, which could be selected at HIGH pressure, OFF or LOW pressure. High was used for providing fuel pressure to prime the engine before start and provided near maximum engine performance should the engine‑driven pump fail. The airplane flight manual (AFM) stated that the ‘high pressure position should not be selected while the engine is operating except in the event of engine driven pump failure since the high pressure mode supplies a greater pressure than can be accepted by the injector system for a reduced power condition’.
Front seats and restraints
The front seats were fitted with 4-point restraints, each consisting of 2 lap straps connected to the seat frame and 2 shoulder harness straps connected via a Y belt to an inertia reel attached to the upper cabin structure. The inertia reel was designed with a locking device that would secure the shoulder straps in the event of sudden forward movement or impact. The seats could be adjusted forward or aft, with the seat guides sliding along 3 seat rails: 2 main (aft) and 1 centre (forward) (Figure 5). The seat is retained at the desired adjustment by a spring-loaded locking pin engaging in one of the forward centre rail holes. Shims could be added to the inside of the guide to ensure locking pin alignment.
Figure 5: Seat rails
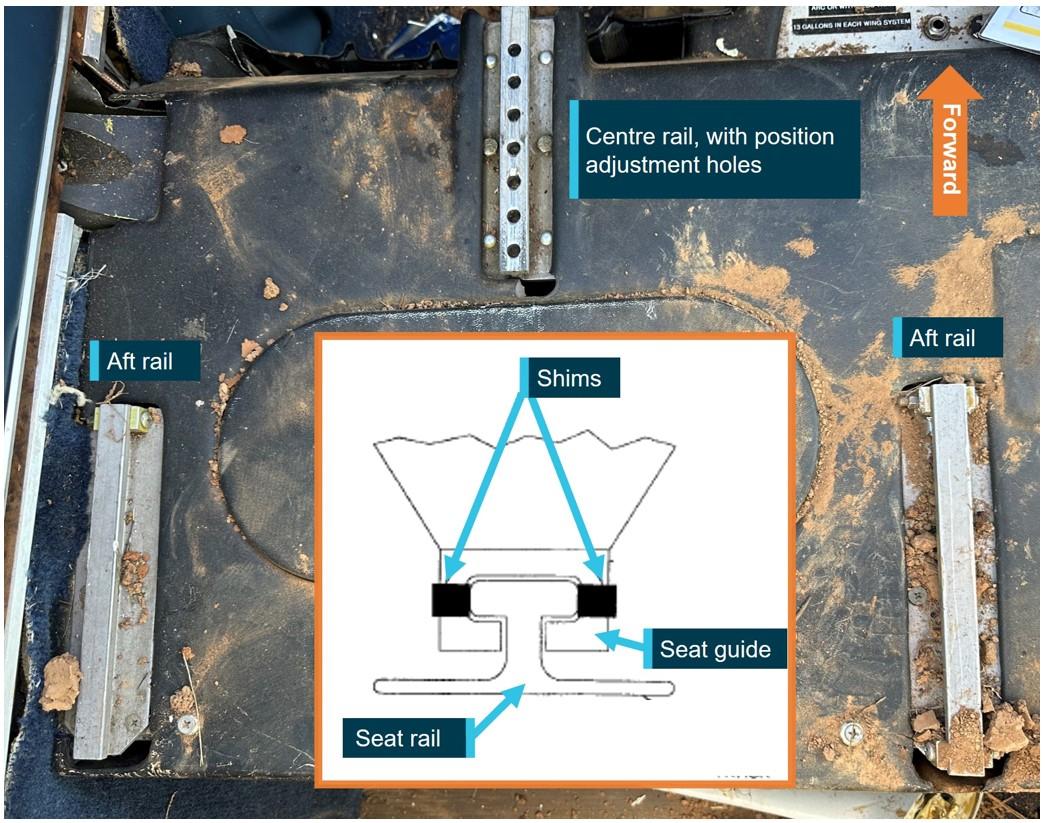
Left seat position depicted in image, right seat rails identical.
Source: ATSB and Beechcraft, annotated by ATSB
Meteorological information
The Bureau of Meteorology graphical area and grid point wind and temperature forecasts covering Cowra Airport for the accident time predicted primarily clear skies, visibility greater than 10 km and a light northerly wind.
Consistent with the forecasts, Cowra Airport’s recorded meteorological conditions[13] at 1400 included wind at 3 kt from 010°, and at 1430 the wind was 5 kt from 310°. At both those times, there was no cloud, the temperature was 21 °C and QNH 1019 hPa.[14]
Recorded data
OzRunways[15] data from the student’s electronic flight bag application contained aircraft track, altitude and ground speed. The ATSB also obtained flight data from the aircraft’s Garmin electronic flight instrument (EFI), which included 40 data parameters. Figure 6 shows key parameters from the EFI data, with the following observations.
From 1404:07, after passing over the NDB, there were heading changes, yaw (evident as lateral accelerations) and a sudden left roll[16] followed by a 10–15 kt reduction in airspeed, consistent with a left engine power loss.
Between about 1408:12 and 1409:27, during the turn from the outbound to the inbound tracks of the NDB instrument approach, the aircraft descended, climbed and descended again, at vertical speeds exceeding 1,000 fpm. During that period the airspeed varied between about 120–150 kt, with left roll angles up to 34°.
The aircraft was on the downwind circuit leg between about 1413:26 and 1414:14, during which time there were no significant changes in lateral acceleration, roll, heading or performance (speed or height).
The aircraft crossed the runway threshold at 1416:01 at 98 kt airspeed aligned with the runway centreline. The last position recorded by the EFI was at 1416:09, at which time the aircraft’s nose had pitched[17] up 6.5°, the airspeed had reduced to 79 kt and the ground speed was 77 kt, indicating a 2 kt headwind. The OzRunways recorded ground speed at the same time was 76 kt.
The OzRunways data showed the aircraft started to deviate left of the runway centreline at 1416:14 at 69 kt ground speed, which would equate to an airspeed of about 71 kt for the same headwind component. The final OzRunways data point recorded before the fence, where the impact with terrain occurred, was at 1416:18 at a ground speed of 65 kt.
Figure 6: Selected parameters from the Garmin electronic flight instrument
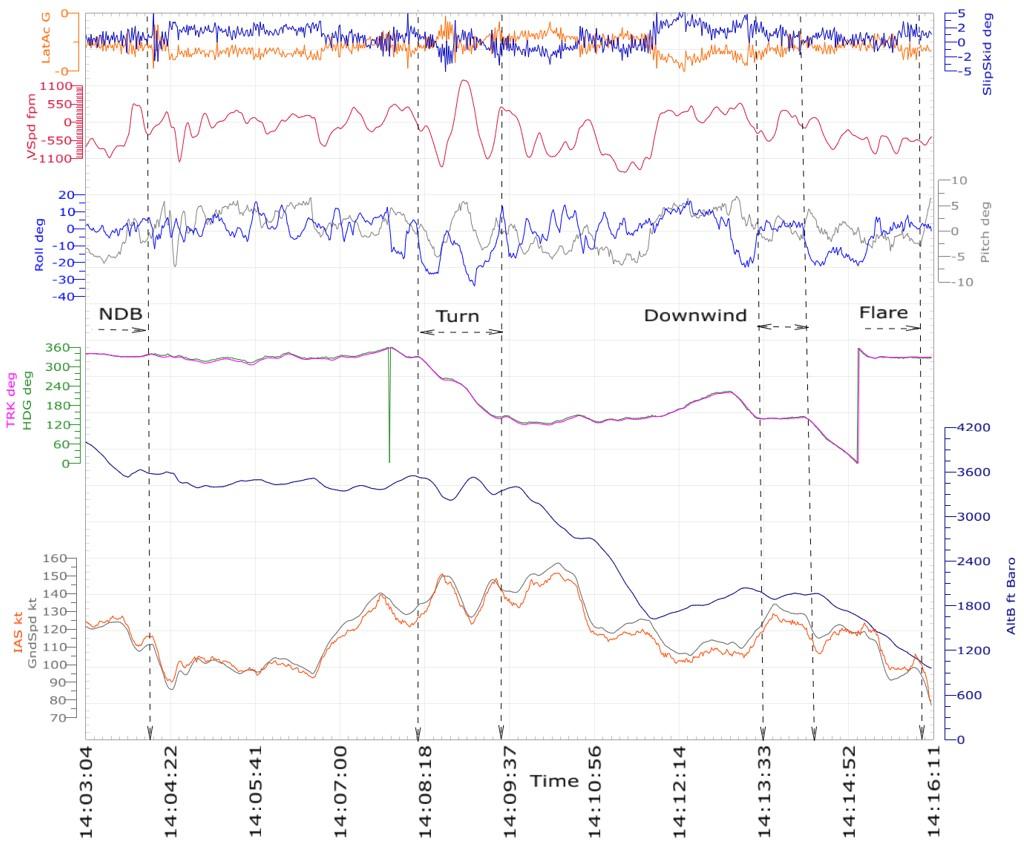
Source: ATSB analysis of Garmin data
Site and wreckage
The aircraft impacted the ground nose-down and inverted about 75° from the horizontal, resulting in crushing of the 2 m‑long nose structure (Figure 7). It collided with a fence and came to rest about 66 m left of the runway centreline and about 700 m beyond the runway threshold. The landing gear was extended, and the flaps were in the approach position.
Both engines had folded backwards around the wing leading edge, which pulled the engine control cables such that the engine control levers were no longer representative of the pre‑impact positions. Damage to the wing leading edge resulted in fuel leaking, but there was no post-impact fire. The aircraft departed with full fuel, and had approximately 400 L of fuel remaining on board at impact. Both fuel selectors were set to ON. Flight control continuity was established.
Figure 7: Impact damage to VH-OMD
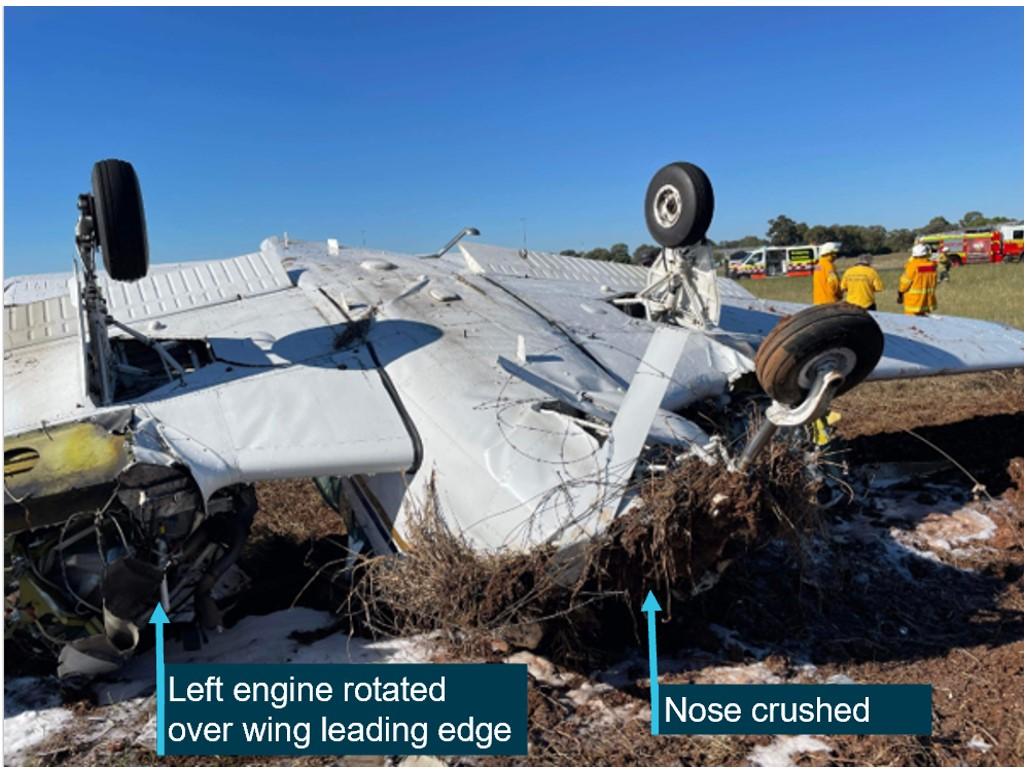
Source: Supplied, annotated by the ATSB
The left propeller flange fractured resulting in the propeller assembly detaching from the engine crankshaft and coming to rest spinner-down embedded in the dirt. The propeller manufacturer advised that the damage to the blades was consistent with the propeller either windmilling or not rotating at impact. The left spinner was indented with the counterweight, showing that the propeller was in fine pitch and not feathered.
The right propeller remained attached to the right engine with evidence of being driven by significant engine power. Fence wire was wrapped around the engine and propeller, which had dug into the ground and first responders reported evidence of dirt having been flung from the hole by the rotating blades.
Examination of the left engine found no evidence of mechanical failure or any pre‑existing fault. The fuel filters and air induction system were clear. The spark plugs were removed with no evidence of fouling from oil or carbon deposits and there were no visible defects with the ignition leads. Borescope examination of the cylinders found no damage or abnormal appearance of the internal surfaces. The fuel distributor manifold was empty of fuel and the diaphragm was undamaged. When electrical power was applied to the starter motor, the engine turned over normally with no evidence of loss of compression in the cylinders.
The 2 front (crew) seats had separated from their track assemblies, although the shoulder harness inertia reels of both seats remained attached to the upper cabin structure. The instructor and student remained partially secured in their seats via the lap straps attached to the seat frame, The instructor came to rest in their seat outside the aircraft cabin following the opening of the cabin door during the accident sequence.
Damage and distortion to the seat rails and seat guides was consistent with forward and right forces sustained during the impact sequence. Both seats’ centre rails exhibited distortion and smearing on the forward edge from the locking pins being forced from their rail holes. The left seat locking pin was bent rearward, and the right seat alignment pin had sheared. Figure 8 shows spreading of one of the seat guides and the associated damage to the seat rails.
Figure 8: Spreading of one seat guide (left) and associated damage to the rails (right)
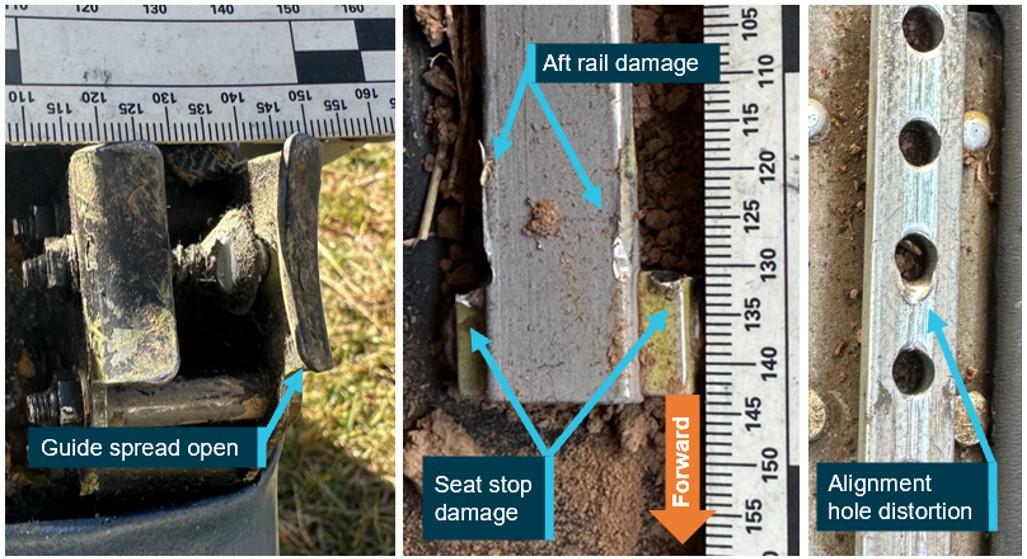
Source: ATSB
A post-impact photograph showed the left engine auxiliary pump in the high position (Figure 9). However, as the entire panel had come adrift, there was dirt adjacent to the switch, and most of the switches in the row beneath it had broken off, its post-impact position was not considered reliable evidence of its position at the time of the accident. The switch panel location was also consistent with injury to the student’s knee. Additionally, the student reported that the pump had been used only for priming prior to engine start then confirmed to be off and not used again during the flight. The metal fuel pump switches were also by design unlikely to be confused with the smaller plastic light switches in the row below and inadvertently selected. It was therefore unlikely to have been on prior to the accident.
Figure 9: Panel showing post-impact switch positions and disruption

Source: Fly Oz, annotated by the ATSB
Asymmetric flight
Asymmetric control
In conventional light twin-engine aeroplanes with one engine inoperative, asymmetric thrust will cause the aeroplane to yaw (rotate about its vertical axis) towards the inoperative engine. As a secondary effect of yaw, it will also roll. The yawing needs to be countered by deflection of the rudder and a small aileron deflection to raise the inoperative engine’s wing, in order to maintain balanced flight. At maximum power on the operative engine, the amount of rudder deflection needed increases as airspeed reduces, to a minimum control speed, below which the rudder is unable to maintain directional control.
Below the minimum control speed, the pilot must reduce power on the operative engine to reduce the asymmetric force, and/or lower the aircraft nose to increase airspeed, to prevent a loss of control. If directional control is lost, the aircraft will yaw and then roll and descend rapidly. Controlled flight may be recovered if enough height is available, by reducing power and lowering the nose.
Minimum control speed
The Civil Aviation Safety Authority’s (CASA) Civil Aviation Advisory Publication (CAAP) 5.23‑1(2) Multi-engine aeroplane operations and training, defined minimum control speed (VMC) as:
a speed that is associated with the maintenance of directional control during asymmetric flight. If the pilot flies below this speed the tail fin and rudder are unable to generate enough lift to prevent the aircraft from yawing. If uncorrected, the yaw causes roll, the nose drops, the aircraft rapidly assumes a spiral descent or even dive, and if the aircraft is at low altitude, it will impact steeply into the ground. This type of accident is not uncommon in a multi-engine aircraft during training or actual engine failure.
There is both a ground value (VMCG) and an airborne value (VMCA), but for simplicity, VMC usually refers to VMCA. The VMC is designated by the red radial on the airspeed indicator. The AFM specified VH-OMD’s VMCA as 79 kt indicated airspeed. That value is determined by US Federal Aviation Regulations (FAR) as the minimum airspeed at which it is possible to recover directional control of the aircraft within 20° heading change, and thereafter maintain straight flight, with no more than 5° of bank toward the operating engine following the sudden failure of one engine with:
- take-off power on both engines
- rearmost allowable centre of gravity
- flaps in the take-off position
- propeller windmilling in take-off pitch configuration.
However, the actual VMC will vary depending on the configuration, conditions and pilot technique (FAA, 2021). The CASA CAAP 5.23-1(2) stated that flight tests conducted in a Cessna Conquest aircraft, which had a published VMC of 91 kt, found that if the wings were held level instead of the inoperative engine wing raised 5°, the actual minimum control speed was 115 kt – an increase of 24 kt. Other light twin-engine aeroplanes would similarly show an increase in actual minimum control speed without bank towards the operative engine. The American Bonanza Society Air Safety Foundation advised that in Baron aircraft types (including the E55), actual VMC is about 15 kt higher than the published VMC if the wings are held level instead of the inoperative engine wing raised, and the slip/skid ball remains centred instead of deflected towards the operative engine.
At speeds below the actual VMC, with one engine inoperative and the other at take-off power, the aircraft will lose directional control – yaw, roll towards the inoperative engine and descend steeply.
Best rate of climb one engine inoperative airspeed
The best rate of climb speed with one engine inoperative (single-engine) (VYSE) is denoted by a blue line on the airspeed indicator and therefore also known as ‘blue-line speed’. It represents the single-engine best rate of climb speed at maximum weight. The AFM for VH-OMD specified the VYSE was 99 kt. Pilots often use blue-line speed as a safety margin above VMC for initiating a simulated engine failure and assume that if blue-line speed is maintained, there is sufficient margin above VMC to prevent an asymmetric loss of control.
Simulated one engine inoperative
Aircraft manufacturer’s procedures
The AFM emergency procedures section included the following procedure titled Determining inoperative engine:
The following checks will help determine which engine has failed.
1. DEAD FOOT – DEAD ENGINE. The rudder pressure required to maintain directional control will be on the side of the good engine.
2. THROTTLE. Partially retard the throttle for the engine that is believed to be inoperative; there should be no change in control pressures or in the sound of the engine if the correct throttle has been selected. AT LOW ALTITUDE AND AIRSPEED THIS CHECK MUST BE ACCOMPLISHED WITH EXTREME CAUTION.
Do not attempt to determine the inoperative engine by means of the tachometers or the manifold pressure gages. These instruments often indicate near normal readings.
The AFM further described the following procedure titled Simulated one engine inoperative:
Zero thrust (simulated feather)
Use the following power setting (only one engine at a time) to establish zero thrust. Use of this power setting avoids the difficulties of restarting an engine and preserves the availability of engine power.
The following procedure should be accomplished by alternating small reductions of propeller and then throttle, until the desired setting has been reached.
Propeller lever – RETARD TO FEATHER DETENT
Throttle lever – SET 12 in. Hg MANIFOLD PRESSURE
NOTE: This setting will approximate zero thrust using recommended one-engine inoperative climb speeds.
Fly Oz procedures
Fly Oz provided a document detailing its simulated engine failure procedure for the Beechcraft E55 aircraft. The procedure was for the instructor to reduce the mixture on one engine to idle cut‑off when above 1,000 ft. Once a student completed the initial checks, identified and verified the inoperative engine, the flight crew must decide whether to ‘fix’ the engine (if en route), or ‘feather’ the engine (‘at critical stages of flight’). If they elect to feather the engine:
… the student will articulate to the instructor which engine they determine has failed and the instructor will set zero thrust.
Fly Oz also provided a copy of their Multi Engine Training Approval Standardisation Manual, which it advised was written for operating Beechcraft Model 76 Duchess aircraft, but was also applicable to the Beechcraft E55. The manual included an Engine failure recovery sequence, describing the 3 stages of a student’s mastery in handling an engine failure. For that sequence, the instructor was to ‘fail an engine by closing the mixture’ [their emphasis]. This was followed by completing the ‘engine out checks’, identifying and verifying the failed engine, then either feathering or troubleshooting to ‘fix’ the failed engine. That procedure did not mention its applicability to asymmetric instrument approaches.
The standardisation manual also had an Asymmetric circuits one engine inoperative procedure, which included 2 notes:
- Never fail an engine below 500 ft AGL.
- Always use the throttle to fail engines in the circuit so you can immediately add power if required.
For that procedure, the instructor was to set zero thrust once the student had identified the correct engine to feather by touching the corresponding pitch lever. The asymmetric circuit procedure also mentioned conduct of an instrument approach and stated:
During an instrument approach a power setting of 20”MP [manifold pressure] with gear down should provide similar performance to the standard 15”MP with both engines operating. Gear should remain down if performance can be adequately maintained.
Additionally, the student or instructor was to include in the radio transmissions that they were ‘asymmetric’ to ‘allow other pilots to keep a safe distance and not try and push in on you in the circuit’.
Fly Oz also provided the ATSB with a copy of the Beechcraft Pilot Proficiency Program Instructor Standards Manual (American Bonanza Society, 2020), which it reported provided best practice guidance for operating the aircraft. The manual stated not to use the mixture to simulate an engine failure in single engine aircraft types. However, it did not stipulate how to simulate an engine failure in multi-engine aeroplanes, and included the following guidance on simulating zero thrust:
set the throttle to 10-12” MP, minimum governing RPM and mixture for ~ 6-7 GPH.
Fly Oz advised the ATSB that it was common industry practice in both flight training and CASA flight testing to use the mixture to shut down an engine particularly when above circuit height. They further advised that their interpretation of the Beechcraft E55 AFM was that it did not specify how a simulated engine failure should be initiated.
Guidance material
The US Federal Aviation Administration (FAA) publication Flying light twins safely (P-8740-066) advised pilots to ‘become thoroughly familiar with the AFM/POH recommended procedures’. Further, it recommended that simulated engine failures below 3,000 ft above ground level (AGL) should be accomplished by smoothly retarding the throttle (FAA, 2008). This was reiterated in the FAA’s Airplane Flying Handbook (FAA-H-8083-3C), Chapter 13: Transition to multiengine airplanes, which stated:
The FAA recommends that all in-flight simulated engine failures below 3,000 feet AGL, be introduced with a smooth reduction of the throttle. Thus, the engine is kept running and is available for instant use, if necessary. Smooth throttle reduction avoids abusing the engine and possibly causing damage.
The handbook also advised that the AFM/POH takes precedence, and that for engines equipped with dynamic crankshaft counterweights, it was essential to make throttle reductions smoothly.
The United Kingdom Civil Aviation Authority’s Aeronautical Information Circular (Pink) 2008-P-064 also advised pilots to refer to the engine manufacturer’s recommendations for simulating engine failures. It recommended that engine failures after take-off ‘should be simulated only by reducing power and never by complete shutdown of the engine until recommended minimum heights at paragraph 9.4 have been achieved’. The referenced paragraph 9.4 recommended minimum safe heights for complete shutdown of power plants for training purposes of 3,000 ft AGL for twin engine piston and turboprop aeroplanes with a maximum take-off weight not exceeding 5,700 kg.
Transport Canada’s Instructor Guide – Multi-engine class rating (TC, 2010), stated:
Actual engine shutdowns for training purposes are not recommended, as the training value is not worth the added safety risk and abuse of engines and airframe…
Simulate the engine failure by reducing the throttle to idle, while calling out "simulated". Complete the engine failure drill in accordance with the [pilot’s operating handbook] POH or the procedures outlined on the previous page.
When these checks have been completed, and you are ready to simulate feathering the propeller, adjust the manifold pressure and rpm to simulate by setting zero thrust. Consult the POH for zero thrust power settings prior to flight. Complete the engine securing items by referring to the appropriate emergency checklist.
The CASA CAAP 5-23-1(2) Multi-engine aeroplane operations and training advised instructors to consult the aircraft flight manual or pilot’s operating handbook for the recommended method of simulating an engine failure. It recommended:
Do not simulate an engine failure using procedures that may jeopardise the restoration of power. It is not recommended to simulate an engine failure at low level by selecting the mixture to idle cut-off or turn the fuel selector off. These procedures would be more appropriate at higher altitude.
Further, the CAAP stated:
6.5.4 Slowly closing the throttle is one of the methods used to simulate an engine failure. Although selecting idle cut-off may be kinder to an engine, the engine or aircraft manufacturer may not permit it. So slowly closing the throttle to idle or zero thrust is unlikely to harm the engine and allows for immediate restoration of power.
…
6.8.1 Flight instructors often simulate an engine failure by rapidly closing the throttle or moving the mixture control to idle cut-off. The latter method should never be used at low altitude.
American Bonanza Society Air Safety Foundation recommendation
The American Bonanza Society Air Safety Foundation recommended multi-engine instructors simulate an engine failure by smoothly reducing the throttle to idle, then block throttle movement on the simulated inoperative engine while the pilot receiving instruction (PRI) completes actions from the POH Engine failure in flight checklist. When the PRI gets to the checklist item ‘Propeller – Feather’, the instructor takes over the power controls and sets zero thrust in accordance with the BE55 POH/AFM.
The American Bonanza Society Air Safety Foundation recommended not simulating engine failure by turning off the fuel selector or pulling the mixture control to cutoff, consistent with FAA guidance.
Lycoming service bulletin
In April 1987, engine manufacturer Lycoming issued Service Bulletin No. 245D, Dynamic counterweight system detuning, which affected 9 Lycoming 6-cylinder engine models. The service bulletin explained that when the inertia force on an engine (which increases with engine speed), or the expansion force (manifold pressure), is suddenly changed, the engine counterweight system can ‘detune’. Damage to the counterweights, rollers and bushings could result, culminating in engine failure.
The service bulletin listed 4 operating conditions that could cause the counterweight system to detune: rapid throttle operation, high engine speed and low manifold pressure, excessive speed and power, and propeller feathering. The bulletin stated:
To avoid detuning during simulated engine failure, use the mixture control to shut off the engine and leave the throttle in normal open position until the engine has slowed down because of lack of fuel.
Fly Oz reported being unaware of the bulletin at the time of the accident. Additionally, Fly Oz reported that its procedures had been written for the Beechcraft 76 (Duchess) aircraft type, which were fitted with 4-cylinder Lycoming O-360 engines, and therefore not affected by the service bulletin. Finally, VH-OMD was not fitted with Lycoming engines and there was no comparable service bulletin or known issue associated with Continental engines.
Checklists
The student’s normal checklists are listed in the following tables.
Table 1: Downwind checklist
Item | Action |
Brakes | Pressure and off |
Undercarriage | Down |
Mixture | Rich |
Fuel | On and sufficient |
Instruments | Indicating normally |
Switches | As required |
Hatches and harnesses | Secure |
Table 2: Final checklist
Item | Action |
Pitch | Full fine |
Undercarriage | Down and 3 greens |
Flap | As required |
Fuel | Sufficient for a go-around |
Workload
The student described the flight as ‘quite busy’, that they were ‘learning a lot of things’, and ‘a little overwhelming but normal for that stage of flying’. The student rated their workload on final as moderate (about 6/10).
The instructor described that the student had been performing really well that day, asymmetric work and checks were good, and overall the student was a good pilot. The instructor also assessed that the student ‘got a bit distracted on the outbound’ leg of the approach, was a ‘little slow’ getting established on the inbound track, and there was some distraction due to circuit traffic operating on the opposite runway. The instructor reported that the student was ‘wrestling’ the aircraft on inbound or downwind, which prompted the instructor to ask whether the student wanted zero thrust set.
The instructor rated their workload as moderate (5/10) and reported that for every landing, they had their seat fully forward, feet on the pedals and was alert and ready to intervene if necessary.
Survivability
The student sustained a cut under the chin, a small fracture in the right hand, and lacerations to the left knee. The instructor had a deep laceration to the chin and one arm and bruising to the knees. Both sustained additional cuts and bruises, including bruising from the lap belt and shoulder harnesses.
The certification basis of the aircraft was US Civil Air Regulation 3. The certification standards required that for a standard weight person (77 kg), the seat must withstand flight, ground, and emergency load conditions. For the seats, the critical conditions were 9 G forward, 3 G upwards and 1.5 G sideways, with the seat attachments to withstand 133% of those requirements.
ATSB analysis of the wreckage and accident site found that the impact deceleration likely exceeded 30 G in a principally forward direction. This significantly exceeded the 9 G forward requirement and the 12 G requirement for the seat attachments. The stable collapse of the airframe structure forward of the occupants aided their survivability.
Similar occurrences
ATSB occurrences
The ATSB occurrence database contained 16 twin-engine aeroplane loss of control occurrences during simulated engine failures since 1978. Two of those occurred in the last 10 years and resulted in fatal accidents in which the loss of control resulted from a simulated engine failure using a method and/or height contrary to manufacturers’ guidance. Key findings of these 2 investigations are as follows.
Loss of control and collision with terrain involving Cessna 441, VH-XMJ, 4 km west of Renmark Airport, South Australia on 30 May 2017 (AO-2017-057)
The flight departed Adelaide, South Australia, at about 1524 local time and flew to the Renmark area for exercises related to the check flight, followed by a landing at Renmark Airport. After a short period of time running on the ground, the aircraft departed from runway 25 at about 1614.
The ATSB determined that, following a simulated failure of one of the aircraft’s engines at about 400 ft above the ground during the take‑off from Renmark, the aircraft did not achieve the expected single engine climb performance or target airspeed. As there were no technical defects identified, it is likely that the reduced aircraft performance was due to the method of simulating the engine failure, pilot control inputs or a combination of both.
It was also identified that normal power on both engines was not restored when the expected single engine performance and target airspeed were not attained. That was probably because the degraded aircraft performance, or the associated risk, were not recognised by the pilots occupying the control seats. Consequently, about 40 seconds after initiation of the simulated engine failure, the aircraft experienced an asymmetric loss of control.
The single engine failure after take‑off exercise was conducted at a significantly lower height above the ground than the 5,000 ft recommended in the Cessna 441 pilot’s operating handbook. This meant that there was insufficient height to recover from the loss of control before the aircraft impacted the ground. The 3 occupants were fatally injured.
The operator’s training and checking manual procedure for simulating an engine failure in a turboprop aircraft was inappropriate and increased the risk of asymmetric control loss.
Loss of control and collision with terrain involving Angel Aircraft Corporation 44, VH-IAZ, near Mareeba Airport, Queensland, on 14 December 2019 (AO-2019-072)
On 14 December 2019, 2 pilots were conducting a private flight in an Angel Aircraft Corporation Model 44 aircraft, registered VH-IAZ, at Mareeba, Queensland. An instructor seated in the right pilot seat was conducting a flight review of the pilot (and aircraft owner) in the left seat.
After the aircraft took off from Mareeba Airport, witnesses reported hearing one of the engines hesitating and backfiring, accompanied by a sooty smoke trail from the right engine. The aircraft operated in the training area until returning to the airport circuit area. Witnesses observed the aircraft touch down on the runway, accelerate and take off again. After take-off, the aircraft climbed to about 100–150 ft above ground level before entering a right descending turn. The aircraft was airborne for about 20 seconds before witnesses observed it rolling rapidly to the right and impacting terrain in a cornfield 475 m north of the runway. The pilots sustained fatal injuries and the aircraft was destroyed.
The ATSB found that shortly after take-off, the flight instructor very likely conducted a simulated failure of the right engine in environmental conditions and a configuration in which the aircraft was unable to maintain altitude with one engine inoperative. Power was not immediately restored to the right engine to discontinue the exercise and the pilots were unable to maintain altitude or heading, particularly with the aircraft banked towards the inoperative engine. The pilots did not reduce power and land ahead, as required by the Airplane Flight Manual, resulting in a loss of directional control and roll. The loss of control occurred at a height too low to recover and the aircraft impacted terrain.
United States occurrences
A search of the US National Transportation Safety Board’s (NTSB) database for investigations involving twin engine aeroplanes, with the words ‘engine’ and ‘simulated’ in the probable cause text, yielded 37 investigations since February 1989,13 of which occurred in the last 10 years. Two of those provide some context relevant to this occurrence:
Piper PA-34, N88AG, Miami, Florida, US on 11 September 2018
The flight instructor in the multi-engine aeroplane reported that the pilot under instruction was conducting a simulated instrument approach in visual flight rules conditions. The instructor placed the left engine fuel selector in the ‘off’ position to simulate an engine out, and the pilot under instruction initiated the left engine failure procedure by placing the engine and propeller levers in a simulated feathered zero-thrust configuration. The instructor became distracted by traffic and failed to place the left engine fuel selector back to the ‘on’ position.
With full flaps and the landing gear extended and while about 250 ft above ground level, the instructor terminated the simulated instrument approach and instructed the pilot to land visually; however, the airspeed decreased below safe limits, and the instructor directed the pilot to increase the airspeed. The pilot increased power on both engines; however, the left engine power did not increase, and the aeroplane rolled to the left about 45°. The instructor took the controls and applied right aileron and rudder, but the aeroplane settled down in a level attitude in a shallow lagoon on the left side of the runway.
Probable cause: The pilot under instruction’s failure to maintain the twin-engine airplane’s minimum control airspeed with one engine inoperative and the flight instructor’s distraction when reconfiguring the airplane following the simulated engine failure, which resulted in no power being available to the left engine and a loss of control during landing when the throttles were advanced to increase airspeed.
Cessna 402C, N2714B, Hyannis, Massachusetts, US on 26 April 2021
A flight instructor and a new-hire trainee pilot were practising instrument approach procedures in the multi-engine aeroplane. On climb-out, the flight instructor reduced power on the left engine to simulate an engine failure on take-off. The pilot then ran the memory items for an engine failure, which included turning the left engine auxiliary fuel boost pump to high. They then conducted an instrument approach. When the aircraft was about 50 ft above the runway, the flight instructor called for a 2-engine go-around. The pilot brought both throttles to full power and retracted the flaps and gear. The flight instructor reported that the aircraft yawed left, and the airspeed was about 80 kt, well under the aircraft’s best single engine rate of climb speed of 95 kt. The flight instructor took control of the aircraft and called for the gear to be extended. The aircraft landed hard and the nose and left main landing gear collapsed, resulting in substantial damage to the left engine and wing. Prior to exiting the aircraft, the pilot turned the left engine auxiliary boost pump from the high position to the off position.
The flight instructor reported that turning the boost pump to high while the engine was still operating could flood the engine with excess fuel and cause it to lose power. The instructor reported that they normally reminded pilots not to turn the pump to high during a simulated engine failure in flight, but neither flight crewmember recalled it being mentioned during the accident flight. Post-accident examination of the left engine revealed no mechanical discrepancies that would have precluded normal operation. As a result, it was most likely that when the boost pump was turned to high, it flooded the engine with excess fuel, resulting in loss of engine power while attempting to go around.
Probable cause: The flight instructor’s failure to confirm the position of the left engine’s auxiliary fuel boost pump switch during a simulated engine out procedure, which resulted in an excess amount of fuel in the engine and subsequent partial loss of power during a go-around/rejected landing. Contributing to the accident was the flight instructor’s failure to maintain control of the airplane, which resulted in a hard landing.
Engine control standardisation
VH-OMD was certified to the 1956 US Civil Air Regulations. The NTSB special study General Aviation Accidents involving fuel starvation 1970–1972 identified design-associated and pilot‑associated factors that influenced or caused ‘operational problems’ in fuel starvation accidents. As a result, the NTSB issued several recommendations. One was for the FAA to issue an advisory circular including ‘to warn certificated flight instructors of the danger associated with simulation of emergency engine failure by positioning the fuel selector valve to “off” or the mixture control to “idle cutoff”’. Another recommendation, A-74-38, was for the FAA ‘to amend the regulations to include specifications for standardizing powerplant control location, visual and tactile appearance, and mode of actuation’.
In 1976, in response to NTSB recommendation A-74-38 regarding fuel control standardization, the US General Aviation Manufacturers Association (GAMA) proposed to the FAA changes to FAR 23.777 through 23.781. It prescribed left to right throttle, propeller and mixture controls, landing gear to the left of the throttle or pedestal centreline, and flap to the right, and included recommended shapes and colours (Figure 10). The FAA’s General aviation (FAR 23) cockpit standardization analysis (FAA-NA-77-38) recognised that ‘increased standardization of cockpit systems can reduce cockpit workload, reduce the potential for habit interference when transitioning to another type aircraft, and provide for application of the best and most error‑resistant designs’ (FAA, 1978).
However, regarding the subsequent FAR amendment 23–33 1986, the FAA stated, ‘that color of control knobs is not a safety issue and will not adopt the proposed color requirement’. As a result, the recommended black throttle control knob and blue propeller control knob standard was not incorporated into FAR 23. A mixture lever was considered an ‘emergency control’ and therefore under FAR 23.1555(e)(2) must be red. The landing gear lever (left) and flap lever (right) requirement was incorporated in FAR 23.777 (f) and (g)).
Figure 10: Recommended control standardisation shapes and colours
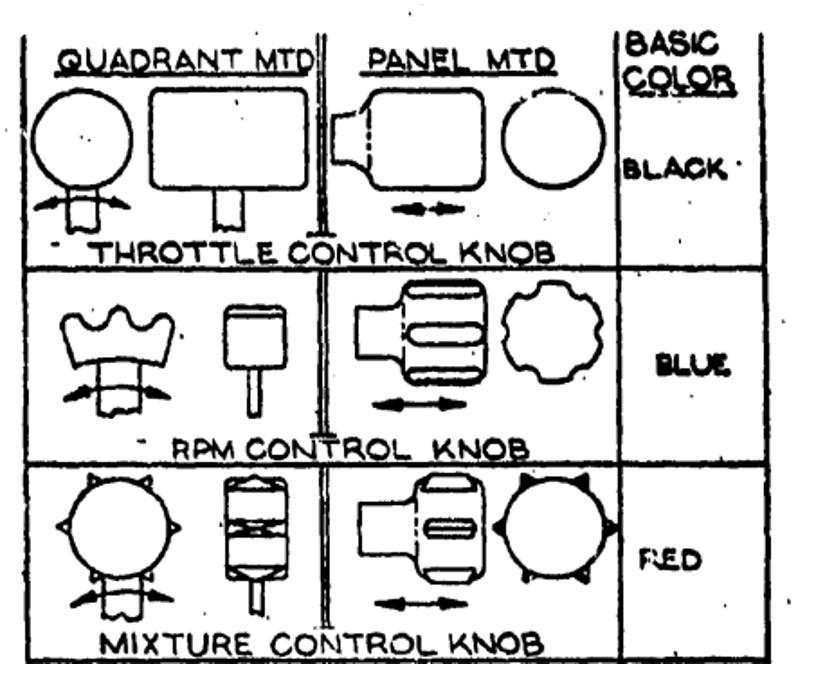
Source: US Federal Aviation Administration
Figure 11 is a post-accident photo of VH-OMD’s engine control levers, which are all black, the throttle pair is in the middle and each pair has different shaped knobs. Additionally, the landing gear selector was to the right of the centre console and the flaps to the left. As VH-OMD was certified prior to the standardisation requirements, it was not required to comply with subsequent FARs.
In this case, as the instructor primarily flew VH-OMD, and it was the only twin engine aeroplane the student had flown (other than a simulator), habit interference was unlikely. However, the lack of colour differentiation in the levers, and particularly not having red mixture control levers, may have reduced the opportunity for rapid visual identification of the mixture lever position.
Figure 11: VH-OMD engine control levers
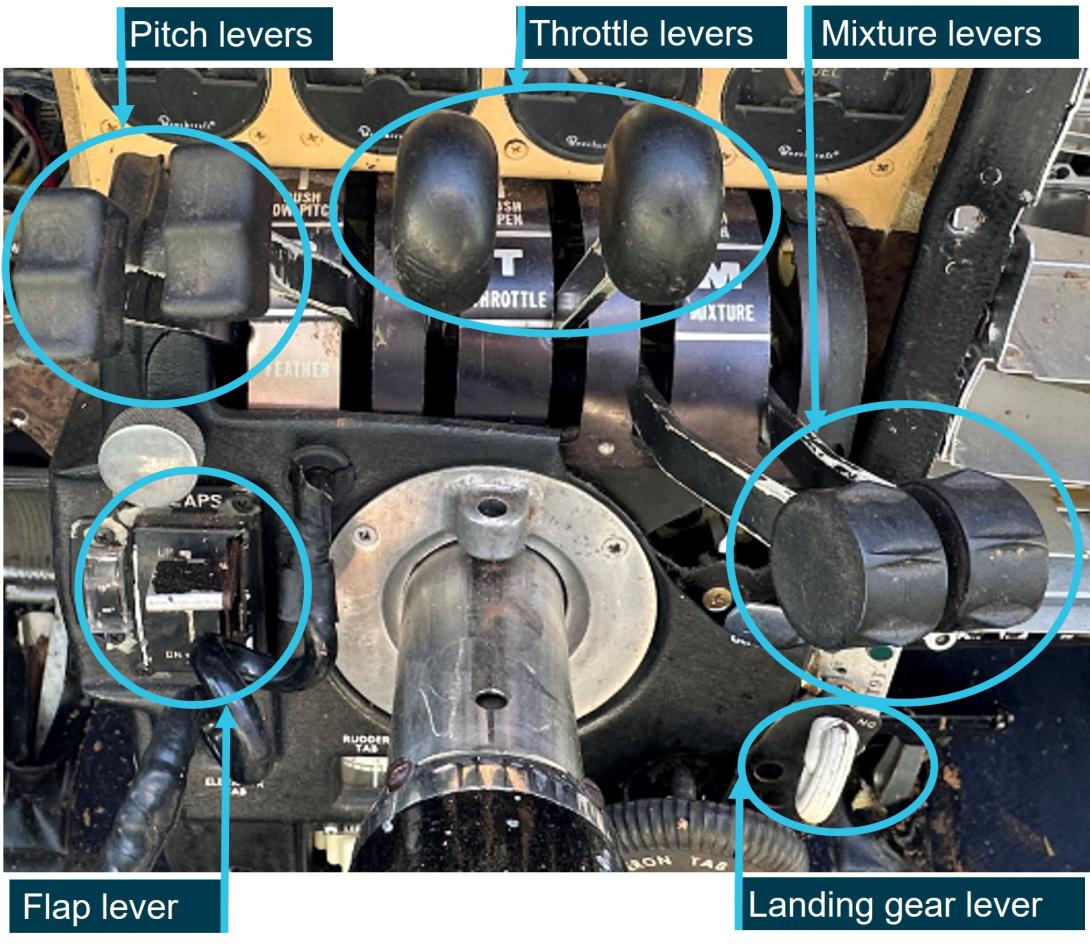
Source: Fly Oz, annotated by the ATSB
Safety analysis
Introduction
When overhead the Cowra Airport navigation aid at the commencement of an instrument approach, at about 2,600 ft above ground level, the instructor simulated a failure of the left engine. After the student conducted the instrument approach and had visually established the aircraft on final approach to the runway, the instructor initiated a go-around at a low height above the runway. Control of the aircraft was lost as it rapidly yawed and rolled left and impacted the ground in an almost vertical nose-down attitude, before coming to rest inverted.
Wreckage examination determined that the left engine was not producing power and the right engine was making significant power at impact. Additionally, there was no evidence of any defect in the left engine or airframe that could have contributed to the accident.
The following analysis will consider why the left engine was not operating at impact and why the go‑around was attempted with one engine inoperative. Additionally, operational procedures associated with simulated engine failures and related risk controls, including their potential to influence future operations will be discussed.
Left engine not restarted
The instructor followed their normal method of simulating an engine failure in accordance with the operator’s stated procedure for the aircraft type by moving the left engine mixture control lever to the idle cut-off position, thereby rendering the engine inoperative.
The required response was for the student to maintain directional control of the aircraft and complete the engine failure checks. Once the student had identified which engine was inoperative, they were to either complete troubleshooting checks to ‘fix’ the failed engine when en route or feather the propeller at a critical stage of flight.
In a training scenario, once the student had identified the inoperative engine correctly, the instructor would normally set zero thrust to simulate a feathered propeller. Their process for setting zero thrust included returning the mixture control to full rich, thereby restarting the engine. However, for reasons that could not be determined, zero thrust was not set at that stage, the mixture remained at idle cut-off with the left propeller windmilling.
The windmilling propeller increased drag and the likelihood of a loss of control, particularly during the left turn towards the inoperative engine. Although the student did not report experiencing a high workload, the approach was not flown within prescribed tolerances and included significant changes in airspeed and altitude. Given the benign weather and light winds at the time, these deviations were likely a result of pilot handling, not environmentally induced. The subsequent improvement in tracking accuracy evident when the aircraft turned to join the circuit, was consistent with the student lifting the hood and resuming flight with external visual reference.
Whether the instructor or student prompted the setting of zero thrust could not be resolved. Given that the instructor recalled setting zero thrust either on inbound or downwind and the student recalled this occurred on downwind, downwind was considered more likely as it was consistent with both recollections. There was no change in heading or increase in performance evident in the recorded data to indicate power was restored to the left engine on downwind, although any such change may have been negligible at the relatively low power settings.
As the manifold pressure would essentially read normally with the propeller windmilling, the stated practice of the instructor of moving the throttle lever forward to achieve the target manifold pressure for setting zero thrust would not confirm the engine was operating. It was for this reason that the Beechcraft E55 Airplane Flight Manual (AFM) cautioned against using manifold pressure indications to assess engine power. In the context of this accident, the observed (and expected) variation of manifold pressure with throttle movement supported an assessment that the engine had been restarted and was capable of normal operation.
Prompting and attempting to set zero thrust on downwind may have interrupted the student’s completion of the downwind checks, which should have included moving both mixture levers to the full rich position. Additionally, the student did not complete the previous checklist item of extending the landing gear, electing to defer doing so until turning onto the base leg and potentially interrupting the checklist flow. As the student had broadcast that they were operating in asymmetric configuration, they were not anticipating the conduct of a go-around. There was no check conducted by either crewmember, or required by procedure, that would verify the engine had restarted and was making power.
The initial small increase in power to the right engine and associated yaw prior to the go-around, as reported by the instructor, was not evident in the data. However, the recorded data showed the aircraft veered off the runway within 3 seconds of the initial deviation from the runway centreline, and the yaw and roll continued to impact. This was consistent with significant asymmetric thrust due to the left engine being inoperative, as evidenced by the absence of rotation when the propeller blades subsequently impacted the ground.
As there was also no evidence of any engine failure mechanism and although the mixture lever position prior to impact could not be determined, the ATSB found that the left mixture lever likely remained in the idle cut-off position from shortly after commencing the instrument approach and the engine was unintentionally not restarted.
Go-around and loss of control
The instructor was unaware they had not returned power to the left engine, and therefore when they instructed the student to commence a go-around, it was based on a belief that symmetrical power was available. This misunderstanding meant the instructor's initial actions in response to the left yaw were to verify the throttle levers were fully forward and to call for the student to let go of the controls, while attempting to correct with rudder. At that stage the only way to avoid the loss of control would have been to reduce power on the right engine and land.
The last recorded airspeed from the electronic flight instrument data, prior to the yaw was 79 kt, which was the published minimum control speed (VMC). The OzRunways data showed the ground speed reduced another 7 kt before the yaw commenced, and the airspeed likely similarly reduced. Additionally, the actual VMC may have been higher, as the wings were probably levelled for landing, rather than having the inoperative engine wing raised 5°, as required to achieve the optimum published VMC. As the aircraft was almost certainly below actual VMC when the go-around commenced, there was insufficient rudder authority to maintain control, and the loss of control occurred at a height too low to recover.
The low height at which the loss of control commenced, estimated to be about 20 ft above the runway, and the crushing of the aircraft’s structure on impact, contributed to the accident’s survivability. The impact forces exceeded the certification requirements of the seats, which detached from their rails, but the flight crew were initially restrained by 4-point harnesses. Significantly, as the aircraft was fitted with fuel cells, despite disruption to the wing leading edge and fuel slowly leaking post impact, there was no explosive fuel-air misting or post-impact fire.
Fly Oz simulated engine failure procedure
The Beechcraft E55 AFM included a procedure for simulating one engine inoperative. The procedure was to set zero thrust, which involved retarding the propeller lever to the feather detent and the throttle lever to set 12 inches of manifold pressure. The flight manual stated that the purpose of the procedure was to ‘avoid difficulties of restarting an engine and preserve the availability of engine power', which would be associated with cutting off the mixture and/or selecting the fuel off.
Fly Oz’s procedure for simulating an engine failure in the Beechcraft E55 aircraft was to move the mixture to idle cut-off to simulate an engine failure, when above 1,000 ft, which was contrary to the AFM procedure to use throttle. It was also contrary to guidance not to use mixture to simulate engine failures when below 3,000 ft above ground level from the aviation regulators in the United States, United Kingdom, and Canada. The Australian Civil Aviation Safety Authority’s guidance did not specify a height below which mixture cut-off should not be used. However, it advised not to simulate an engine failure ‘using procedures that may jeopardise the restoration of power’. Further, that slowly closing the throttle allows for immediate restoration of power.
As the conduct of an asymmetric instrument approach may include one or more legs of a circuit and end in a landing, there is a potential need for immediate restoration of power close to the ground. Therefore, the use of throttle to simulate an engine failure for conduct of an instrument approach could be inferred from the CASA guidance. The guidance also included the need to consult the aircraft flight manual for the manufacturer’s recommended method of simulating an engine failure.
Fly Oz’s Multi Engine Training Approval Standardisation Manual also included a procedure to simulate an engine failure that involved moving the mixture to idle cutoff. However, consistent with the AFM, it also contained a procedure that stipulated the use of throttle to simulate engine failures in the circuit (under which it included the conduct of asymmetric instrument approaches). Fly Oz stated that, while the manual had been written for a different aircraft type, it provided a description of the procedure applicable to VH-OMD. Despite that, on the day of the accident the instructor used the Fly Oz Beechcraft E55 specific procedure in use at the time and simulated the engine failure using the mixture control. That procedure did not contain a requirement or process to verify the engine was subsequently restarted and available for instant use.
This likely resulted in the inoperative engine being undetected by the flight crew, while operating at low power during the approach and landing. Ultimately this resulted in the loss of control during initiation of a go-around.
The ATSB occurrence database held 2 fatal accidents in the last 10 years that resulted from a loss of control following a simulated engine failure using a method and/or height contrary to guidance. Although there was no data available for the number of simulated engine failures conducted and by what method, the frequency of loss of control accident types and likelihood of fatality indicated that these posed a significant risk.
Findings
ATSB investigation report findings focus on safety factors (that is, events and conditions that increase risk). Safety factors include ‘contributing factors’ and ‘other factors that increased risk’ (that is, factors that did not meet the definition of a contributing factor for this occurrence but were still considered important to include in the report for the purpose of increasing awareness and enhancing safety). In addition ‘other findings’ may be included to provide important information about topics other than safety factors. Safety issues are highlighted in bold to emphasise their importance. A safety issue is a safety factor that (a) can reasonably be regarded as having the potential to adversely affect the safety of future operations, and (b) is a characteristic of an organisation or a system, rather than a characteristic of a specific individual, or characteristic of an operating environment at a specific point in time. These findings should not be read as apportioning blame or liability to any particular organisation or individual. |
From the evidence available, the following findings are made with respect to the loss of control and collision with terrain involving Beech E55, VH-OMD, at Cowra Airport, New South Wales on 11 April 2024.
Contributing factors
- The instructor moved the left engine mixture lever to idle cut-off to simulate an engine failure overhead the navigation aid, and it was likely that they unintentionally did not subsequently move the lever to rich and ensure the engine was restarted and available for instant use.
- The instructor initiated a go-around below the air minimum control speed unaware the left engine was inoperative, resulting in an asymmetric loss of control.
- Fly Oz's asymmetric training procedure involved failing one engine using the mixture control without confirmation the engine was subsequently restarted, rather than reducing throttle to simulate zero thrust in accordance with the Beechcraft E55 Airplane Flight Manual. This increased the risk of undetected asymmetric operation during descent and landing and the associated loss of control. (Safety issue)
Safety issues and actions
Central to the ATSB’s investigation of transport safety matters is the early identification of safety issues. The ATSB expects relevant organisations will address all safety issues an investigation identifies. Depending on the level of risk of a safety issue, the extent of corrective action taken by the relevant organisation(s), or the desirability of directing a broad safety message to the aviation, industry, the ATSB may issue a formal safety recommendation or safety advisory notice as part of the final report. All of the directly involved parties were provided with a draft report and invited to provide submissions. As part of that process, each organisation was asked to communicate what safety actions, if any, they had carried out or were planning to carry out in relation to each safety issue relevant to their organisation. Descriptions of each safety issue, and any associated safety recommendations, are detailed below. Click the link to read the full safety issue description, including the issue status and any safety action/s taken. Safety issues and actions are updated on this website when safety issue owners provide further information concerning the implementation of safety action. |
Operator’s procedure to use mixture to simulate engine failure
Safety issue number: AO-2024-011-SI-01
Safety issue description: Fly Oz's asymmetric training procedure involved failing one engine using the mixture control without confirmation the engine was subsequently restarted, rather than reducing throttle to simulate zero thrust in accordance with the Beechcraft E55 Airplane Flight Manual. This increased the risk of undetected asymmetric operation during descent and landing and the associated loss of control.
Safety action not associated with an identified safety issue
Whether or not the ATSB identifies safety issues in the course of an investigation, relevant organisations may proactively initiate safety action in order to reduce their safety risk. The ATSB has been advised of the following proactive safety action in response to this occurrence. |
Additional safety action by Fly Oz
Fly Oz has taken the following proactive safety action:
- Following a simulated engine failure, zero thrust is to be set immediately after the student has completed the engine failure drills.
- The instructor standardisation manuals were being updated to include a requirement that both the student and instructor confirm that the pitch, power and mixture controls are set back to normal 2‑engine configuration during checks on final. This is now a call out item, ensuring that both pilots are satisfied with the correct settings.
Glossary
AFM | Airplane Flight Manual |
AGL | Above ground level |
AIP | Aeronautical information publication |
AMSL | Above mean sea level |
CAAP | Civil Aviation Advisory Publication |
CASA | Civil Aviation Safety Authority |
CTAF | Common traffic advisory frequency |
EFI | Electronic flight instrument |
FAA | (US) Federal Aviation Administration |
FAR | Federal Aviation Regulations |
METAR | Meteorological conditions at an aerodrome |
NDB | Non-directional beacon |
NSW | New South Wales |
NTSB | (US) National Transportation Safety Board |
QNH | The altimeter barometric pressure subscale setting used to indicate the height above mean seal level |
TIS | Time in service |
US | United States |
Sources and submissions
Sources of information
The sources of information during the investigation included:
- the flight instructor and student pilot
- the maintainer of VH-OMD
- Fly Oz
- Civil Aviation Safety Authority
- New South Wales Police Force
- the aircraft, propeller and engine manufacturers
- Bureau of Meteorology
- OzRunways
- accident witnesses
- photographs and videos taken on the day of the accident and for subsequent examination
- recorded data from the GPS unit on the aircraft.
References
American Bonanza Society, BPPP Instructor Standards Manual, Revision 10, July 2020.
Civil Aviation Safety Authority, Civil Aviation Advisory Publication 5.23-1(2) Multi-engine aeroplane operations and training, September 2015.
Federal Aviation Administration, Airplane Flying Handbook, FAA-H-8083-3C, 2021. Accessed 10 May 2024: Airplane Flying Handbook | Federal Aviation Administration (faa.gov)
Federal Aviation Administration, Flying light twins safely, FAA-P-8740-66 (2008). Accessed 19 May 2024: FAA_P-8740-66.pdf (faasafety.gov)
Lycoming Service Bulletin No. 245 D Dynamic Counterweight System Detuning, 10 April 1987. Accessed 10 May 2024: Service Bulletin No. 245 D | Lycoming
Transport Canada, Instructor Guide: Multi-engine class rating, Second edition, October 2010. Accessed 19 May 2024: Microsoft Word - TP11575E.doc (canada.ca)
United Kingdom Civil Aviation Authority, Aeronautical Information Circular, 64/2008 (Pink 142) 17 July 2008. Accessed 10 May 2024: Pink 142.qxp (ead-it.com)
Submissions
Under section 26 of the Transport Safety Investigation Act 2003, the ATSB may provide a draft report, on a confidential basis, to any person whom the ATSB considers appropriate. That section allows a person receiving a draft report to make submissions to the ATSB about the draft report.
A draft of this report was provided to the following directly involved parties:
- the flight instructor and student pilot
- Fly Oz
- Civil Aviation Safety Authority
- the maintainer of VH‑OMD
- American Bonanza Society Air Safety Foundation
- the aircraft, engine and propeller manufacturers.
Submissions were received from:
- the flight instructor and student pilot
- Fly Oz
- Civil Aviation Safety Authority
- American Bonanza Society Air Safety Foundation.
The submissions were reviewed and, where considered appropriate, the text of the report was amended accordingly.
Purpose of safety investigationsThe objective of a safety investigation is to enhance transport safety. This is done through:
It is not a function of the ATSB to apportion blame or provide a means for determining liability. At the same time, an investigation report must include factual material of sufficient weight to support the analysis and findings. At all times the ATSB endeavours to balance the use of material that could imply adverse comment with the need to properly explain what happened, and why, in a fair and unbiased manner. The ATSB does not investigate for the purpose of taking administrative, regulatory or criminal action. TerminologyAn explanation of terminology used in ATSB investigation reports is available here. This includes terms such as occurrence, contributing factor, other factor that increased risk, and safety issue. Publishing informationReleased in accordance with section 25 of the Transport Safety Investigation Act 2003 Published by: Australian Transport Safety Bureau © Commonwealth of Australia 2024
Ownership of intellectual property rights in this publication Unless otherwise noted, copyright (and any other intellectual property rights, if any) in this report publication is owned by the Commonwealth of Australia. Creative Commons licence With the exception of the Commonwealth Coat of Arms, ATSB logo, and photos and graphics in which a third party holds copyright, this report is licensed under a Creative Commons Attribution 4.0 International licence. The CC BY 4.0 licence enables you to distribute, remix, adapt, and build upon our material in any medium or format, so long as attribution is given to the Australian Transport Safety Bureau. Copyright in material obtained from other agencies, private individuals or organisations, belongs to those agencies, individuals or organisations. Where you wish to use their material, you will need to contact them directly. |
[1] Instrument flight rules (IFR): a set of regulations that permit the pilot to operate an aircraft in instrument meteorological conditions (IMC), which have much lower weather minimums than visual flight rules (VFR). Procedures and training are significantly more complex as a pilot must demonstrate competency in IMC conditions while controlling the aircraft solely by reference to instruments. IFR-capable aircraft have greater equipment and maintenance requirements.
[2] Visual Meteorological Conditions (VMC): an aviation flight category in which visual flight rules (VFR) flight is permitted – that is, conditions in which pilots have sufficient visibility to fly the aircraft while maintaining visual separation from terrain and other aircraft.
[3] OzRunways is an electronic flight bag application that provides navigation, weather, area briefings and other flight information. It provides the option for live flight tracking by transmitting the device’s position and altitude.
[4] Instrument approach procedure: A series of predetermined manoeuvres by reference to flight instruments that provides specified protection from obstacles.
[5] NDB: a ground-based radio transmitter that provides a reference point to navigate by.
[6] Windmilling: a rotating propeller being driven by the airflow rather than by engine power, and results in increased drag at normal propeller blade angles.
[7] Feathering: the rotation of propeller blades to an edge-on angle to the airflow to minimise aircraft drag following an in‑flight engine failure or shutdown.
[8] Manifold pressure gauge measures the absolute pressure in the intake manifold of an engine, expressed in inches of mercury (in. Hg). Normal operating range (green arc) was 15 to 29.6 in. Hg.
[9] Yawing: the motion of an aircraft about its vertical or normal axis.
[10] Flare: the final nose-up pitch of a landing aeroplane used to reduce the rate of descent to about zero at touchdown.
[11] A registered operator is responsible for airworthiness and maintenance control of the aircraft (CASA).
[12] Maintenance release: an official document, issued by an authorised person as described in Regulations, which is required to be carried on an aircraft as an ongoing record of its time in service (TIS) and airworthiness status. Subject to conditions, a maintenance release is valid for a set period, nominally 100 hours TIS or 12 months from issue.
[13] METAR: a routine report of meteorological conditions at an aerodrome. METAR are normally issued on the hour and half hour. Winds use true north as the reference.
[14] QNH: the altimeter barometric pressure subscale setting used to indicate the height above mean seal level.
[15] OzRunways is an electronic flight bag application that provides navigation, weather, area briefings and other flight information. It also provides the option for live flight tracking by transmitting the device’s position and altitude.
[16] Rolling: the movement of an aircraft about its longitudinal axis.
[17] Pitching: the motion of an aircraft about its lateral (wingtip-to-wingtip) axis.