Executive summary
What happened
On 8 March 2024, the pilot of an Aero Commander 500-S, registered VH-MEH and operated by GAM Air, was conducting a return cargo transport operation from Bankstown Airport to Parkes Regional Airport, New South Wales with one intermediate stop outbound, and 2 intermediate stops on return.
After landing on the first sector, the pilot found the fuel cap was off and secured only by a retention chain. The pilot re‑secured the cap but after landing at Parkes on the second sector, they again found the fuel cap off, and arranged an inspection by a maintenance engineer. The engineer found a fault that prevented the fuel cap from locking and rectified it.
Later that day, the pilot commenced the return sectors to Bankstown. Shortly after departing Bathurst for the final sector, both engines lost power, and the pilot conducted a forced landing in a field. The aircraft was undamaged and the pilot was uninjured.
What the ATSB found
The ATSB found that for the first 2 sectors, the fuel cap was incorrectly installed with the retention chain lodged in the fuel tank’s anti-siphon valve, resulting in the cap dislodging in‑flight and fuel being siphoned overboard. At Parkes Regional Airport, the pilot identified an unexplained discrepancy between expected fuel remaining and gauge quantity indication but did not refuel to a known quantity or amend the flight log. As a result, the aircraft departed Parkes with the pilot unaware there was insufficient fuel to complete the remaining flights.
After departing Parkes, the pilot likely did not monitor the fuel gauge, continued fuel calculations based on an incorrect fuel quantity, and did not refuel the aircraft to a known quantity at Bathurst Airport. This resulted in fuel exhaustion shortly after the aircraft departed from Bathurst.
The ATSB also found that GAM Air's Quick Turn Around – Pre-Start checklist did not include a fuel quantity check before start, contrary to the aircraft flight manual’s before-start checklist.
What has been done as a result
GAM Air published a pilot notice reinforcing fuel management procedures for Aero Commander 500 series aircraft. The notice highlighted the importance of fuel tank cap security, and the likelihood of fuel loss should a fuel cap become dislodged, despite the anti-siphon valve. The notice also provided instructions and guidance on fuel planning, in-flight fuel calculations and fuel log entries to expand on information in the standard operating procedures.
GAM Air also commenced periodic auditing of pilot fuel calculations and advised an intention to discontinue use of the Quick Turn Around – Pre-Start checklist. The fuel supplier at Bankstown was also reminded of the requirement to let fuel settle when refuelling.
Safety message
A missing or unsecured fuel cap can lead to rapid and substantial fuel loss in‑flight, even when the fuel tank is equipped with an anti-siphon valve. Loss of a fuel cap in‑flight should be considered as an emergency and, if detected, an immediate diversion to the nearest suitable aerodrome should be conducted. In addition, in aircraft with rubber fuel cells or bladders, fuel gauge readings should not be relied upon as siphoning of fuel can lead to collapse and distortion of the cells causing the fuel gauge to overread. Filling to an amount that can be visually confirmed is required to re‑establish an accurate measure of fuel on board.
The Civil Aviation Safety Authority’s Advisory Circular 91-15 – Guidelines for aircraft fuel requirements, stated:
It is of critical importance that the amount of usable fuel on board an aircraft at the commencement of and during a flight is known with the highest level of certainty.
Pre-flight fuel quantity checks should use at least 2 different verification methods to determine the amount of fuel on board. When using computed fuel on board and comparing against gauge readings, it is important that calculations are accurate. If any discrepancy is detected between the 2 methods, another method such as filling to a known quantity is required.
The investigation
Decisions regarding the scope of an investigation are based on many factors, including the level of safety benefit likely to be obtained from an investigation and the associated resources required. For this occurrence, a limited-scope investigation was conducted in order to produce a short investigation report, and allow for greater industry awareness of findings that affect safety and potential learning opportunities. |
The occurrence
On 8 March 2024, the pilot of an Aero Commander 500-S, registered VH-MEH and operated by GAM Air, was preparing to conduct a return cargo transport operation from Bankstown Airport to Parkes Regional Airport, New South Wales (NSW). The planned flight to Parkes included a stop at Orange Regional Airport to unload a portion of the cargo. The aircraft and pilot were to remain at Parkes for the day before the aircraft was reloaded to return to Bankstown in the afternoon with intermediate stops at Orange and Bathurst airports to load additional cargo (Figure 1). All operations were conducted under instrument flight rules (IFR).[1]
Figure 1: VH-MEH flights on day of incident
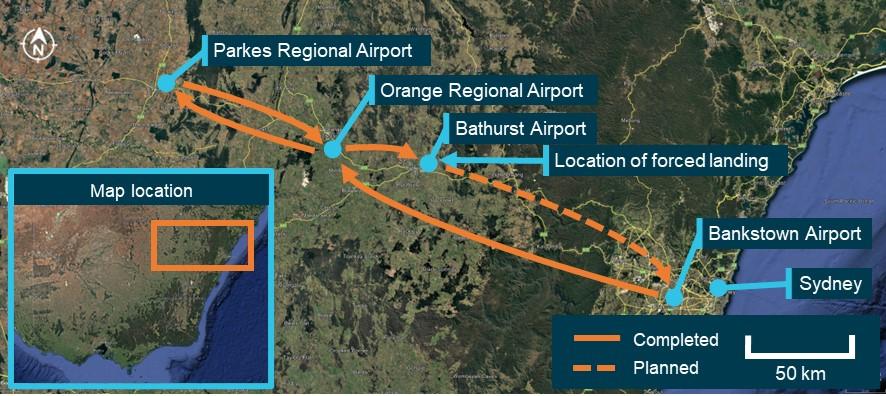
Source: Google Earth, annotated by the ATSB
The aircraft had been refuelled 5 days earlier by a contract refueller, with a written instruction to fully refuel the aircraft. Since refuelling, the aircraft had been repositioned on the ground but not flown.
VH-MEH had a single fuel tank that supplied fuel to both engines, accessed through a filler port on the top of the right wing. A spring-loaded anti-siphon valve was installed at the fuel tank opening to mitigate in-flight fuel siphoning.[2] The anti-siphon valve could be pushed open when refuelling or when visually observing the fuel level. The fuel cap was secured to the filler neck by a chain and interlocked with the top of the anti-siphon valve, securing both the fuel cap in place and the anti‑siphon valve in its closed position when the locking screw was turned (Figure 2). To ensure the locking mechanism engaged correctly, pilots were advised to tap the structure around the tank cap once closed. That action should cause the cap to pop open if it was loose or unsecured.
Figure 2: Fuel cap and filling point components (not incident aircraft)
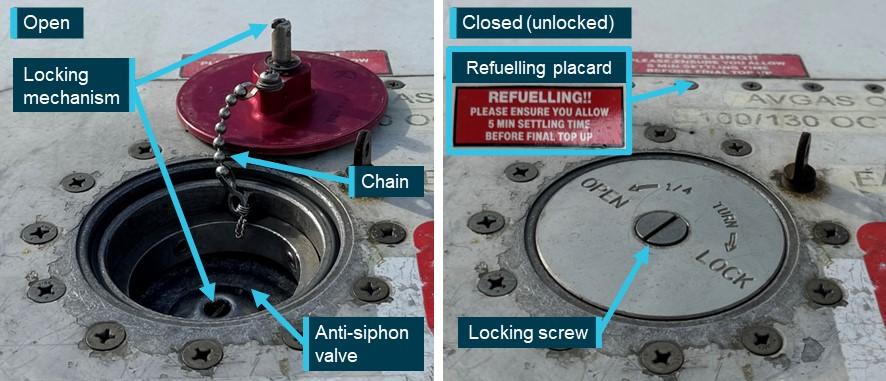
Source: GAM Air, annotated by the ATSB
At about 0610 local time, the pilot conducted a pre-flight inspection of the aircraft, during which they observed the fuel quantity to be 3–4 cm below the anti-siphon valve, which was below the level usually observed when the fuel tank was full. Based on that observation, the pilot estimated that they had 560 L of fuel on board of the total 590 L usable fuel[3] capacity. The pilot also received a weather briefing for the planned flights, which showed no significant wind effect en route (see the section titled Fuel planning).
The aircraft had fuel quantity, fuel pressure and fuel flow gauges in the cockpit (Figure 3). A printed calibration card that provided the conversion of fuel gauge readings in US gallons (USG) to usable fuel in litres was affixed adjacent to the fuel quantity gauge. Although full fuel was 159 USG (590 L), the gauge could not indicate a quantity of fuel above 135 USG (480 L). Therefore, prior to commencing the flight, the pilot was unable to confirm the fuel level using the gauge. Because of this gauge limitation, the operator required pilots to begin flights with a fuel quantity that had been visually confirmed.
Figure 3: Cockpit fuel system indicators
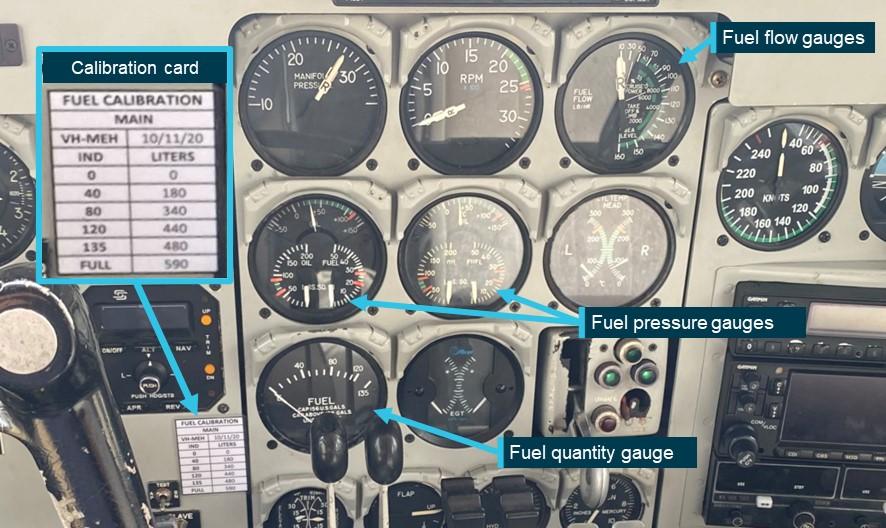
Source: GAM Air, annotated by the ATSB
In accordance with the operator’s procedures, the pilot planned to assess the aircraft’s fuel on board by maintaining a log of fuel usage for each sector using a prescribed calculation method (see the section titled Fuel management). The calculated fuel on board would then be regularly compared to the fuel quantity gauge in the cockpit. The pilot used the estimated 560 L of fuel on board as the starting point for their calculations.
The aircraft departed Bankstown at 0658 and landed at Orange Airport at 0735. Upon landing, the pilot calculated that 89 L of fuel had been used. After shutdown, the pilot conducted a post-flight inspection. During the inspection the pilot found that the fuel cap was off, attached only by the chain, which they re‑secured. The pilot reported that they compared the calculated fuel remaining with the fuel quantity gauge reading and determined that there was no discrepancy. Additionally, the pilot reported that they expected the anti-siphon valve would have prevented any fuel loss from the unsecured cap.
The aircraft departed Orange at 0802 and landed at Parkes at 0825. After landing, the pilot calculated that 63 L of fuel would have been used for the sector and calculated the fuel remaining. The pilot conducted a post-flight inspection and again found that the fuel cap was off. They advised the company operations team, who arranged for an aircraft maintenance engineer at Parkes to inspect the fuel cap.
The pilot then identified that the fuel gauge was showing approximately 35–40 L less than the calculated fuel remaining. Due to the discrepancy, the pilot reported recalculating the fuel required for the remaining sectors, based on the fuel gauge indication, and determined that there was adequate fuel on board for the return flight. Specifically, even taking into account the required fuel reserves, the pilot calculated there was almost 1.5 hours excess fuel endurance. However, the pilot did not reduce the calculated fuel remaining on the flight log to reflect the lower gauge quantity indication. The pilot then left the airport.
The maintenance engineer inspected the fuel cap and found that the chain securing the fuel cap to the inside of the filler neck had disconnected from its attachment point and lodged under the anti‑siphon valve, holding it slightly open. This also prevented the fuel cap locking mechanism from engaging. The engineer removed the chain from its lodged position, re‑attached it to the filler neck, and successfully closed and locked the fuel cap. They also observed minor blue fuel dye staining aft of the fuelling point, consistent with Avgas 100 low lead fuel. The engineer later reported that they informed the pilot and the operator’s engineering department of what was found with the fuel cap.
The pilot returned to the airport in the afternoon and the aircraft departed for Orange at 1622, landing at 1644. The pilot calculated that 59 L of fuel had been used for that sector. After loading additional cargo, the aircraft departed Orange at 1702 and landed at Bathurst Airport at 1719, using a calculated 38 L of fuel (see the section titled Fuel monitoring). At that point, the pilot’s calculations determined that 311 L of fuel remained on board. The pilot later reported that they did not recall specific gauge readings at those intermediate stops, but that there were no noted discrepancies.
The aircraft departed Bathurst Airport at 1730 for the planned 73 NM flight to Bankstown Airport. At that time, the automated weather observation at the airport indicated no cloud, and wind from the north-east at 10 kt. The aircraft initially tracked north before turning right to track east towards Bankstown (Figure 4).
Figure 4: Incident flight path
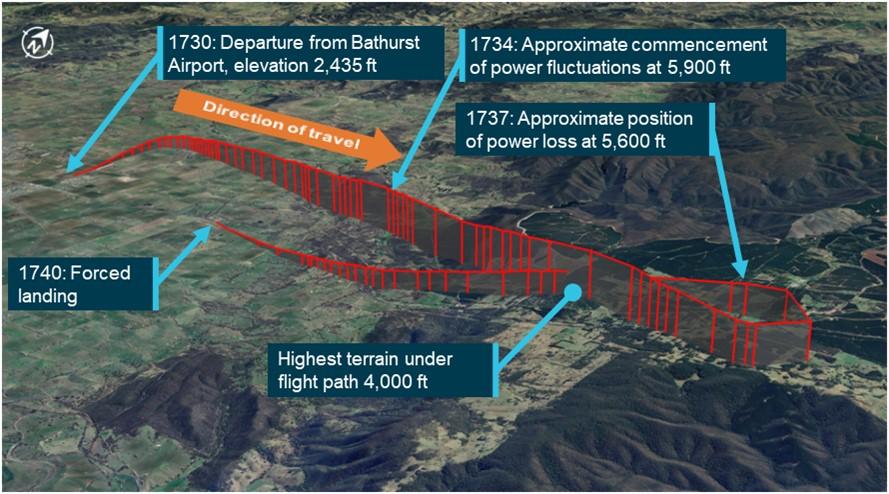
Source: FlightRadar24 flight data overlaid on Google Earth, annotated by the ATSB
The pilot reported that, approximately 4 minutes after departure, while climbing through 5,900 ft above mean sea level (AMSL), the aircraft yawed[4] significantly to one side, and then shortly afterwards, yawed to the other side. The pilot recalled performing initial engine failure actions, while using rudder to control the yaw as the engine noise and power fluctuated on both engines.
The pilot observed the fuel flow gauge readings increasing and decreasing in line with the fluctuating engine RPM indication and switched on the fuel boost pumps. The pilot was aware that the terrain below was at approximately 4,000 ft AMSL and the terrain ahead provided few options for a safe forced landing. The pilot advised air traffic control (ATC) of the situation before conducting a 210° left turn to track back towards Bathurst Airport, and towards flatter and lower terrain.
After completing the turn, both engines stopped making power, and the pilot prepared for a forced landing. The pilot selected a large field ahead as a suitable landing area. The pilot elected not to feather[5] the propellors in case partial power was restored and they could continue to the airport. As the aircraft approached the planned landing area, the pilot extended the landing gear prior to manoeuvring below power lines and over a fence. The aircraft landed in the field and came to a stop, after which the pilot advised ATC of their situation before securing the aircraft. The aircraft was undamaged and the pilot was uninjured.
Context
Pilot information
The pilot held a commercial pilot licence (aeroplane) issued in 2018 and completed an instrument proficiency check[6] in August 2023. A line check and a proficiency check were completed with the operator in September 2023, where the pilot was assessed as competent, and approved to conduct charter flights.
The ATSB obtained the pilot’s experience as of 2 months after the incident, by which time they had accumulated 1,745 total flight hours, 776 hours on multi-engine aircraft, of which 335 hours were logged on Aero Commander 500-type aircraft.
The pilot held a valid Class 1 aviation medical certificate with no restrictions and reported that they were well rested.
Aircraft information
VH-MEH was an Aero Commander 500-S aircraft fitted with 2 Lycoming IO-540-E1B5 290-hp piston engines driving Hartzell 3-bladed constant‑speed propellors. The aircraft was manufactured in the United States in 1975 and first registered in Australia in 1976.
The aircraft had an Australian Supplemental Type Certificate allowing an increased maximum take-off and landing weight of 3,243 kg for IFR operations.
The last periodic inspection was carried out on 13 December 2023, and there were no outstanding items recorded on the aircraft’s maintenance release.[7] At the time of the incident, the aircraft had accumulated 44,963.3 hours total time in service.
There were no onboard recording devices installed on the aircraft that recorded engine indications, gauge readings, fuel flow or fuel levels.
The aircraft’s fuel tank consisted of 5 interconnected synthetic rubber cells installed in the inboard and centre wing sections (Figure 5). A single fuel quantity transmitter was installed in the centre fuel cell and electrically connected to the fuel quantity gauge. Both the operator and the aircraft manufacturer reported that the distribution of the fuel throughout interconnected fuel cells made physical determination of the fuel level using a dipstick impractical. Therefore, the only way to confirm the fuel level was to observe the fuel at a level full or close to full. Additionally, during refuelling, the fuel could take time to settle and allow a reliable visual determination of the fuel level. A placard advising of this was placed adjacent to the filling point on the operator’s Aero Commander aircraft (Figure 2).
Figure 5: Fuel tank internal layout
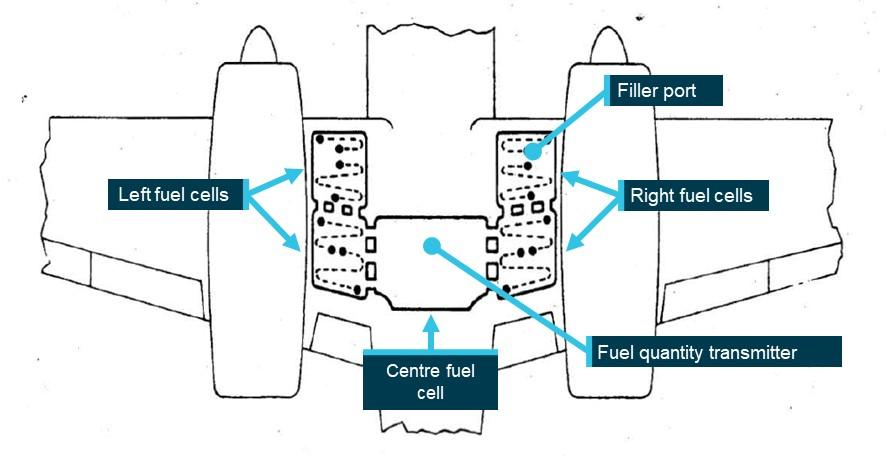
Source: Aero Commander 500-S maintenance manual, annotated by the ATSB
Post-incident inspection
The ATSB did not attend the incident site. Evidence from approximately 30 minutes after the incident showed the fuel gauge indicating empty when electrical power was turned on. The operator’s maintenance engineers conducted an on-site inspection of the aircraft 6 days later, at which point they reported that the fuel cap was found secured and locked, and the fuel drain points were in the closed position. A small amount of fuel discharged from them when opened, likely to be unusable fuel.[8]
The fuel cap was inspected and tested and was found to attach and remain on, with an observation that the retention spring in the locking screw was noted to be in weak condition, meaning that it could be turned by pressure from a finger or thumb rather than requiring a screwdriver. The fuel cap was replaced as a precautionary measure. Inspection and testing of fuel system components and a general inspection on the aircraft found no issues.
The aircraft was recovered 2 weeks later and taken to Bathurst Airport, where 180 L of fuel was added to the fuel tank, during which the fuel gauge was noted to read correctly and move as expected. Engine ground runs and propellor checks were conducted with all engine parameters observed as normal.
Fuel gauge calibration was required to be conducted every 4 years and prior to the incident was last conducted for VH-MEH on 10 November 2020. Before the aircraft was returned to service, the fuel gauge was recalibrated to verify the correct operation of the fuel indication system, and to fulfil the periodic recalibration requirement. The calibration was expanded to 10 increments from the initial 6. Additionally, a new visual fuel level, annotated as SIPHON, was added. Figure 6 shows how these 2 visible levels were observed and compares the re‑calibration with the calibration values available to the pilot during the incident flight.
Figure 6: Fuel gauge recalibration and observations (photo not VH-MEH)
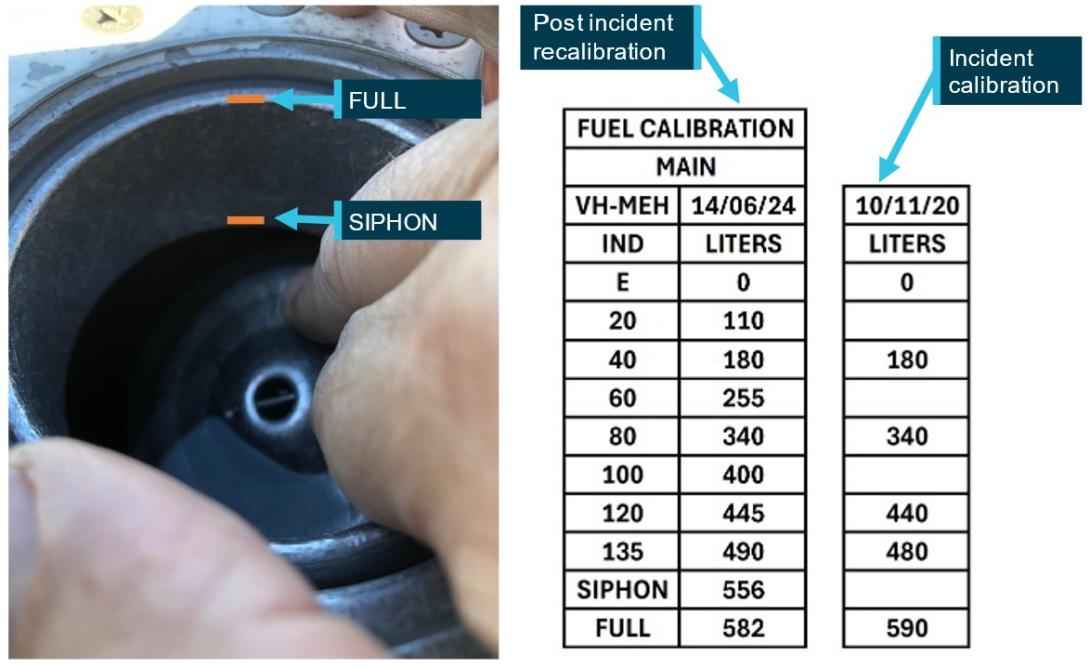
Source: Parkes Aviation and GAM Air, annotated by the ATSB
Fuel management
Determination of fuel on board
The operator’s fuel policy described the procedures to be conducted to determine fuel on board before each flight. Those procedures stated that fuel quantity gauge readings were required to be crosschecked against either a visual confirmation of the fuel on board, or against calculated fuel on board. This was in line with guidance provided in the Civil Aviation Safety Authority (CASA) Advisory Circular AC 91-15v1.1 Guidelines for aircraft fuel requirements:
Unless assured and verified by the PIC that the aircraft fuel tanks are completely full, or a totally reliable and accurately graduated dipstick, sight gauge, drip gauge or tank tab reading can be made, the PIC should endeavour to use the best available cross-check process before engine start. The cross-check should use at least two different verification methods to determine the amount of fuel on board.
As it was not possible to establish the quantity of fuel on board by visual inspection other than when full, a flight log was required to be maintained to calculate fuel usage. This calculated quantity, based on the flight time and maximum altitude of each flight leg, was then deducted from the starting fuel quantity to determine the fuel remaining on board prior to take-off of each flight and compared against the fuel gauge. Table 1 lists the components used in this calculation.
Table 1: Fuel calculation for VH-MEH
Calculation component | Fuel amount |
Start, taxi and run-up | 5 L |
Cruise and descent | 115 L/h |
Climb Allowance: | |
- To 3,000 ft | 10 L |
- 3,000 ft–6,000 ft | 15 L |
- Above 6,000 ft | 20 L |
Holding | 90 L/h |
Instrument approach allowance | 30 L |
Source: GAM Air
The operator’s fuel policy stated that when a significant or unexplained discrepancy was identified between fuel gauge readings and calculated fuel on board the only way to ensure a known quantity of fuel was to fill the tank to full and confirm visually.
Any significant fuel discrepancy or variation between gauge readings, actual fuel on board (visual) and/or calculated shall be reported to Operations Control.
Where a significant or unexplained discrepancy exists the only way to ensure a known quantity of fuel on board is to fill the tanks full and visually confirm. Should a visual confirmation of actual full tanks not be possible, a flight must not commence unless the Pilot in Command has ensured that the fuel quantity on board has been checked by two separate methods.
Fuel monitoring
The pilot maintained an aircraft flight log as required by the operator’s procedures to keep track of fuel usage. Table 2 compares the pilot’s calculations with the ATSB’s calculations based on the operator’s procedures detailed in Table 1, showing that the pilot underestimated the fuel used by 28 L (11%). The ATSB also reviewed flight log fuel calculations performed for flights on previous operating days of the incident aircraft. Those previous flights were operated by several different pilots, none by the incident pilot, and the calculations sometimes differed from the ATSB’s calculations based on the documented procedures, but to a lesser degree than the incident day flight log.
Table 2: Pilot calculations vs ATSB calculations – incident day
Route | Flight time |
Cruise altitude |
Pilot calculated fuel |
ATSB calculated fuel | Difference |
Bankstown – Orange |
37 min |
8,000 ft |
89 L |
96 L |
7 L |
Orange – Parkes |
24 min |
6,000 ft |
63 L |
66 L |
3 L |
Parkes – Orange |
22 min |
7,000 ft |
59 L |
68 L |
9 L |
Orange – Bathurst |
14 min |
5,000 ft |
38 L |
47 L |
9 L |
TOTAL |
|
|
249 L |
277 L |
28 L (11%) |
Fuel planning
The aircraft operator maintained and provided pro forma flight plans and fuel plans for pilots operating their standard routes. The fuel plans calculated fuel required using fuel flow rates applicable to the specific aircraft in the fleet. Pilots were required to adjust the standard flight times and fuel loads for forecast winds.
The pro forma fuel plan required that in nil wind, aircraft conducting the planned Bankstown–Parkes–Bankstown flights including intermediate stops, started with a minimum of 461 L, comprising 278 L of flight fuel, 40 L of taxi allowance, 112 L of mandatory reserves, and an allowance for 31 L for ATC delays. When aircraft conducting that route started the day with full fuel, they typically returned to Bankstown with more than an hour of fuel in addition to required reserves.
The ATSB obtained the weather forecast that would have been available to the pilot prior to departure from Bankstown to determine if forecast winds would have been expected to affect the fuel required. Table 3 shows that the total expected flight time for all sectors would have differed by 1 minute, resulting in an additional 2 L of fuel required.
Table 3: Forecast wind effect on expected flight times
Route |
Proforma plan flight time (nil wind) |
Forecast Wind |
Expected flight time |
Bankstown – Orange |
40 min |
14 kt tailwind |
37 min |
Orange – Parkes |
20 min |
8 kt tailwind |
19 min |
Parkes – Orange |
20 min |
7 kt headwind |
21 min |
Orange – Bathurst |
12 min |
14 kt headwind |
13 min |
Bathurst – Bankstown |
32 min |
13 kt headwind |
35 min |
TOTAL |
124 min |
|
125 min |
Initial fuel quantity
The pilot estimated the start fuel to be 560 L based on observing the fuel level 3–4 cm below the anti-siphon valve. Post-incident fuel calibration found the siphon level to be 556 L on VH-MEH and 490 L to be the maximum that could be shown on the fuel gauge. Based on that, the ATSB estimated that initial fuel was between 556 L and 490 L, as less than that would have indicated on the fuel gauge prior to departure. This indicated that the pilot overestimated the initial fuel by up to 70 L.
Unaccounted-for fuel
Applying the operator’s fuel calculation method, the ATSB calculated that 305 L of fuel would have been consumed by the engines for the flights conducted on the incident day until fuel exhaustion. Therefore, considering the above range of fuel onboard at the start of the flight, 185–251 L of fuel was unaccounted for (Table 4). The ATSB considered whether a higher rate of fuel consumption by the engines compared to that expected could account for that fuel. However, it was determined that the fuel flow required would have been at least 276 L/h, greater than the maximum continuous power specified in the aircraft flight manual (AFM) and more than the fuel flow gauges could indicate. Therefore, this was not considered to be a possibility. The flight times of each sector were also compared against the operator’s planned flight times and showed no significant differences, indicating that en route winds did not adversely affect fuel calculations.
Table 4: Fuel analysis
Route |
Flight time |
Start fuel |
Fuel used |
Unaccounted fuel |
End fuel |
Bankstown – Orange |
37 |
490–556 |
96 |
112–152 |
282–308 |
Orange – Parkes |
24 |
282–308 |
66 |
73–99 |
143 |
Parkes – Orange |
22 |
143 |
68 |
|
75 |
Orange – Bathurst |
14 |
75 |
47 |
|
28 |
Bathurst – [Exhaustion] |
4 |
28 |
28 |
|
0 |
TOTAL |
|
490–556 |
305 |
185–251 |
0 |
Based on the unaccounted-for fuel, for each of the return sectors, the fuel gauge reading that would have been showing according to the ATSB‑calculated start fuel was compared against the reading expected by the pilot based on their flight log (Figure 7).
Figure 7: Pre-departure fuel gauge indications
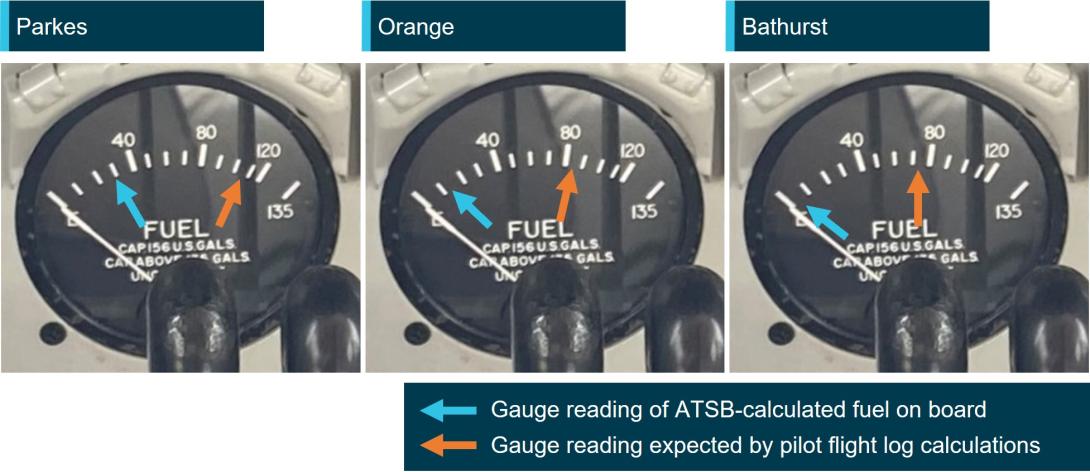
Source: GAM Air annotated by the ATSB
Fuel loss and anti-siphon valve
Because the fuel filling point of VH-MEH was located on the top surface of the wing (as on most light aircraft), the low-pressure area on the top surface of the wing created when the aircraft was in‑flight could draw fuel up and out of the fuel tank if the fuel cap become dislodged.
The anti-siphon valve (Figure 8) provided a secondary barrier to fuel venting. The relatively higher pressure inside the fuel tank would act to hold the valve closed and reduce the opportunity for fuel loss without the fuel cap in place.
Any obstruction preventing the anti-siphon valve from closing would provide an opening for fuel to vent should the fuel cap become dislodged. Additionally, the fuel cap locking mechanism would be unable to engage as the locking point of the anti-siphon value would be held away from the locking component of the fuel cap, making it more likely to dislodge.
Figure 8: Anti-siphon valve
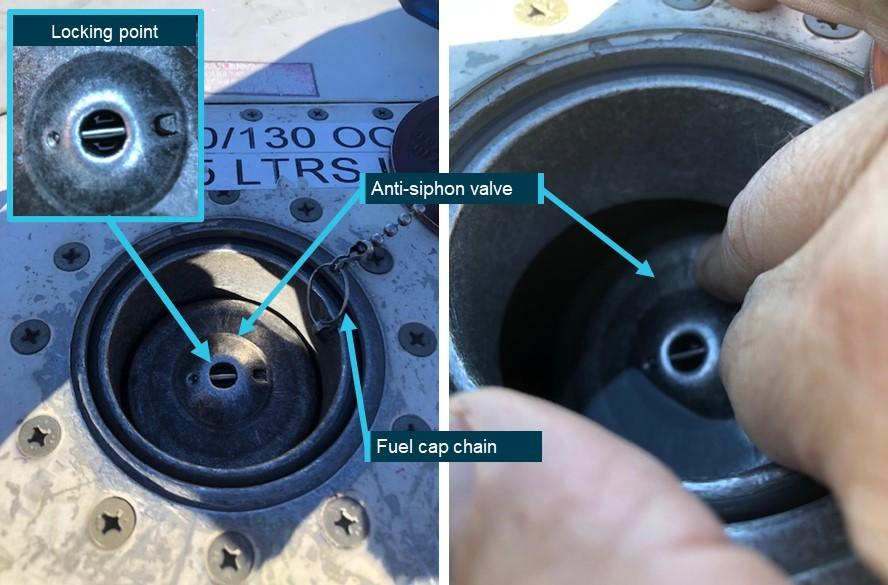
Source: Parkes Aviation, annotated by the ATSB
In 2018, the operator circulated a notice to pilots regarding fuel tank cap security in response to 2 incidents involving unsecured fuel caps. One of those incidents was an in-flight fuel siphoning event resulting in the loss of approximately 250 L of fuel. The notice was also issued to the incident pilot as part of their induction. The notice advised that significant fuel loss was possible from Aero Commander aircraft (turbine and piston engine) despite being fitted with an anti-siphon valve, and highlighted the pilot’s responsibility to ensure fuel tank caps were secured. It stated:
During the pre-flight inspection and after each refuelling all Aero Commander pilots will check tank cap security by:
- Ensuring the lock mechanism is secured by using a flat blade screw driver as found in the aircraft fuel drain tool (a 5 cent piece can be used only if no screw driver present)
- Firmly thump/bang the structure immediately around the fuel tank cap. A loose cap may ‘pop’ open if loose. Thumping the tank cap itself will not show if loose.
If there is any doubt about the fuel tank security or integrity pilots will advise Operations Control.
CASA’s Fuel and Oil Safety Advisory Circular (AC) 91-25v1.1 described the importance of maintaining the integrity of fuel caps in preventing in-flight fuel loss including the impact of a trapped fuel cap chain:
In-flight fuel loss by siphoning overboard is primarily attributed to poor maintenance and service practices. Siphoning overboard can be traced to problems such as fuel filler caps incorrectly installed and/or worn fuel filler caps and gaskets. Always check the condition of fuel filler cap O-rings, gaskets, pawls, and springs for evidence of wear and/or deterioration. Deformed or worn pawls may affect the sealing effectiveness of the O-rings or gasket. Similarly, a tank-cap attachment chain or lanyard can be trapped across the seal and defeat its purpose.
In addition to fuel loss, in aircraft where the fuel tanks were comprised of flexible rubber cells, the suction effect created by the low pressure above the wing could cause the fuel cells to collapse upwards from the bottom as fuel is siphoned out. The collapse and deformation of the cells could increase the level of the fuel as the volume of the fuel cells decreased causing the fuel quantity gauge to overread. AC 91-25v1.1 described the potential effect of fuel cell collapse and distortion on fuel quantity indication:
If the fuel gauge apparatus is in the vicinity of the pump and surrounded by relatively solid structure it may not be immediately affected by a tank collapse and could continue to give readings that may at first appear to be credible. It is possible for the indications to temporarily suggest a very low rate of usage or even show a transitory increase in the quantity of fuel in the tank. Whatever the cause or manner of fuel bladder collapse, a dangerous situation will result.
CAUTION: Fuel bladder collapse may exaggerate indications of fuel in the tank.
The Flight Safety Australia article Caps tanks and drains: a three pronged attack (CASA, 2016), described the potential consequences of in-flight fuel siphoning due to a loose fuel cap, including the possibility of fuel cell deformation and its effect on fuel gauge readings.
The loose cap exposes the fuel to the low-pressure area over the wing; the fuel then obeys the laws of physics and finds its way out.
If the tank is a rubber fuel cell it will collapse upwards from the bottom, because the top of the rubber fuel cell is secured more firmly to the top wing-tank cavity. This can have at least three effects, all of them bad:
- The bottom of the tank keeps rising. Fuel is thus kept at or near the top of the tank near the cap hole, so that siphoning continues until most or all of the fuel is lost overboard.
- The float of the fuel tank quantity gauge can come into contact with and be supported, or even raised, by the rising of the tank liner bottom. As a result, the cockpit fuel quantity indicator may continue to show full or nearly full, despite the loss of fuel.
- The tank becomes distorted and wrinkled. The tank may not re-shape itself and volume is reduced for the next fill. The valleys now hold lakes and rivers that cannot be drained, until the aircraft is climbing.
Recognising the hazard posed by fuel cell distortion, the aircraft operator and maintainer advised that this was not possible in Aero Commander aircraft as the fuel tanks are interconnected via feed tubes and vent tubes. Additionally, the fuel sender unit is at the bottom of the main tank, and both the sender and the tank are held at the bottom via a large panel and a series of retaining bolts. It would therefore be impossible for the bottom part of the tank to suck up and affect the sender arm to give an erroneous high reading.
The aircraft manufacturer also advised that they would not expect fuel siphoning to lead to fuel gauge overreading.
Aircraft checklists
The operator’s checklists (Figure 9) to be used when operating VH-MEH provided points at which the fuel quantity was required to be checked.
Before the aircraft was started, the pilot was required to conduct the INTERIOR checklist, followed by the BEFORE START checklist. This second checklist contained an item to check that the fuel quantity was sufficient, and the gauge was indicating correctly.
To enable expediency during multiple sectors such as cargo operations, the operator provided a QUICK TURN AROUND – PRE-START (QTA) checklist as an alternative to those 2 checklists. The QTA checklist did not include a fuel quantity check. However, regardless of whether the standard or QTA checklists were used before aircraft start, a subsequent fuel quantity check was required to be conducted in the BEFORE TAKE-OFF checklist before the aircraft departed.
Figure 9: GAM Air Aero Commander 500 checklists
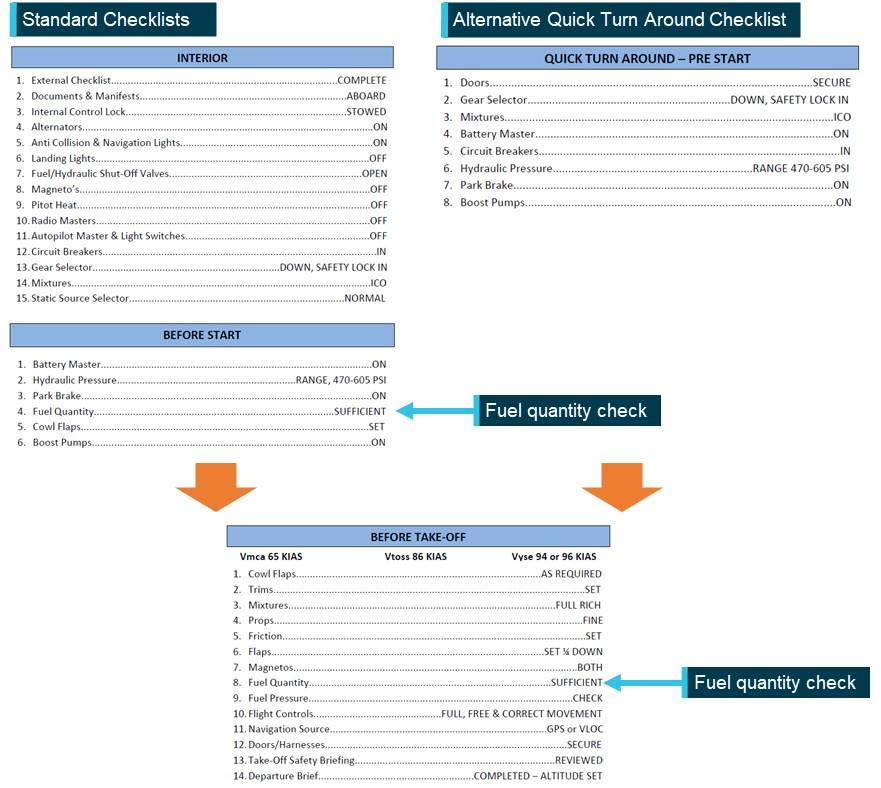
Source: GAM Air, annotated by the ATSB
The ATSB compared the operator’s checklists with equivalent checklists in the manufacturer’s aircraft flight manual (AFM) (Figure 10). While standard checklists closely followed the checks included in the AFM, several checks were excluded when a pilot conducted the operator’s QTA Checklist.
Figure 10: AFM checklists
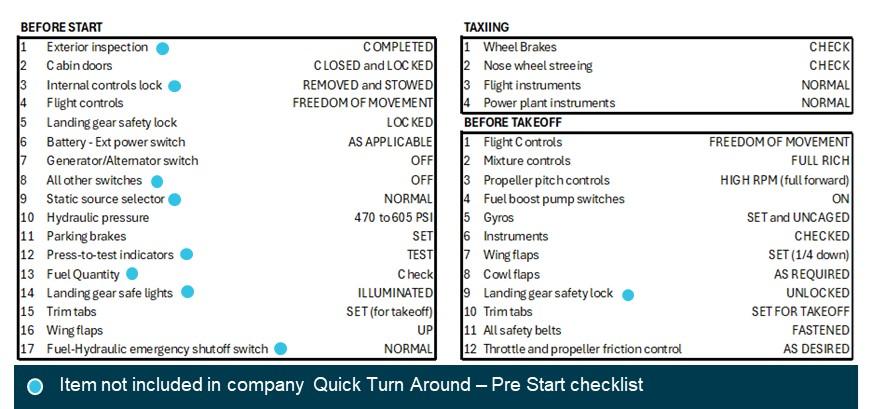
Source: Aero Commander 500-S aircraft flight manual, annotated by the ATSB
Emergency procedures
The operator’s checklists and the AFM did not contain checklists specific to simultaneous power loss from both engines. However, having identified that an engine was inoperative, the checklists instructed the pilot to feather the propellor of the inoperative engine. Feathering the propellor of a failed engine reduces drag and adverse yaw (when only one engine has failed).
In the case of both engines failing, feathering both propellors significantly reduces drag, improves the handling characteristics and flight performance of the aircraft and, by increasing the glide distance, potentially expands options for a forced landing site.
Related occurrences
Australia
Excluding the incident flight, the ATSB occurrence database contained 97 reported occurrences of fuel leaking or venting from non-jet aircraft between 2014 and 2024. Of those occurrences, 7 resulted in fuel starvation or fuel exhaustion. Additionally, in 17 of those occurrences, the fuel cap was incorrectly installed or not secured prior to flight. Those numbers likely under‑represent the total number of incidents of this type, as the ATSB only requires instances of fuel leaking/venting or missing/insecure fuel caps to be reported for commercial passenger transport operations.
The database also contained one occurrence of fuel venting leading to starvation immediately after landing of an Aero Commander 500-S in 1995. Although the ATSB did not investigate the incident, it was reported that a post-landing inspection revealed the main fuel tank filler cap was defective and would not remain locked, allowing fuel to vent overboard in‑flight.
International
The ATSB identified the following occurrences of fuel exhaustion of an Aero Commander 500 aircraft:
Fuel exhaustion of Aero Commander 500 N107DF on 28 January 2023 (NTSB ERA23LA122)
The aircraft lost power to both engines and landed in a field, sustaining substantial damage and seriously injuring the pilot. It was determined that it was likely that the pilot did not visually confirm the aircraft’s initial fuel quantity prior to departing and that the available fuel was exhausted.
Fuel exhaustion of Rockwell 500 N900DT on 28 August 2020 (NTSB ERA20LA297)
The aircraft impacted a building and terrain about 10 minutes after take-off and was destroyed, fatally injuring both pilots. It was determined that this was due to a total loss of engine power due to fuel exhaustion. Contributing to the fuel exhaustion was the fatigue fracture of an electrical wire in the tank unit or fuel transmitter, which likely resulted in an inaccurate fuel quantity indication. It was also determined that the initial fuel quantity on board was not able to be confirmed visually.
Safety analysis
Prior to the day’s flights, the pilot estimated the fuel on board based on a visual assessment of fuel below the anti-siphon valve level. The fuel quantity was less than full due to either the refueller not allowing the fuel to settle during refuelling, ground running to reposition the aircraft, or a combination of both. Although the pilot likely overestimated the fuel quantity by up to 70 L, the aircraft departed Bankstown with enough fuel to complete the planned sectors and return to Bankstown with the required reserves intact, given the forecast winds.
As the pilot found the fuel cap off and replaced it after landing at both Orange and Parkes airports, it was likely that the fuel cap was also unsecured in‑flight during those sectors. The maintenance engineer in Parkes found that the fuel cap chain had been holding the anti‑siphon valve slightly open, preventing the fuel cap locking mechanism from engaging, and reported advising the pilot of that. Significantly, the engineer also detected evidence of fuel dye staining, indicating fuel had leaked from the tank.
After rectification by the maintenance engineer, the fuel cap remained secured including after the forced landing. ATSB analysis indicated that it was very likely that about 200 L of fuel siphoned overboard in‑flight during one or both sectors to Parkes. The loss of fuel en route to Parkes left the aircraft with about 143 L of fuel upon landing at Parkes, which was insufficient for the return sectors to Bankstown.
At Parkes, aware that the fuel cap had been unsecured on the 2 previous sectors, but unable to physically confirm the quantity of fuel in the tank, the pilot identified an unexplained discrepancy between their calculated fuel remaining and the fuel quantity gauge reading.
Due to the discrepancy, the operator’s procedures required the pilot to refuel the tank to full, to visually confirm the quantity of fuel onboard. However, instead of refuelling, the pilot reported recalculating the aircraft’s fuel state based on the gauge reading, although they did not update the flight log, and incorrectly determined that they had sufficient fuel for the remaining flights. Despite being informed of issues found with the fuel cap, the pilot’s decision not to refuel may have been influenced by their expectation that the anti-siphon valve would prevent fuel siphoning overboard and the typical excess of remaining fuel on board when completing the same route.
The ATSB assessed whether the fuel quantity gauge was likely to have been providing erroneous indications to the pilot. This was based on CASA guidance that during in-flight siphoning events in aircraft with rubber fuel cells, it was possible for the rubber to deform and move upwards away from the base of the tank, resulting in overreading of the fuel quantity sender. However, the aircraft operator/maintainer and manufacturer advised that this was not possible in Aero Commander aircraft due to the construction of the fuel cells and sender. There were also no reported issues or defects with the fuel gauge prior to the incident flight.
The fuel gauge was determined to be working correctly after the incident and 2 minor adjustments were made to fuller fuel quantities in the calibration conducted post‑incident. Therefore, the fuel quantity gauge was likely indicating correctly at Parkes and would have shown a significant discrepancy with the pilot’s assessed fuel quantity.
As a result of the pilot’s misunderstanding of the fuel quantity, the aircraft departed Parkes with significantly less fuel than determined by the pilot, and insufficient for the remaining flights. The pilot did not then effectively monitor the fuel state or refuel after landing at Bathurst. Consequently, fuel exhaustion occurred shortly after the aircraft departed from Bathurst.
Although not considered to have contributed to this occurrence, the operator’s Quick Turn Around – Pre-Start checklist was an abbreviated version of the before-start checklist specified in the aircraft flight manual and did not include a fuel quantity check. As there was a fuel quantity check in the operator’s and manufacturer’s before-take-off checklist, the pilot was required to verify the fuel quantity before departure. However, a fuel quantity check before start in accordance with the manufacturer’s procedures would have prompted the pilot to crosscheck the fuel state when workload was lower, and any discrepancy could have been more easily identified and addressed.
Findings
ATSB investigation report findings focus on safety factors (that is, events and conditions that increase risk). Safety factors include ‘contributing factors’ and ‘other factors that increased risk’ (that is, factors that did not meet the definition of a contributing factor for this occurrence but were still considered important to include in the report for the purpose of increasing awareness and enhancing safety). In addition ‘other findings’ may be included to provide important information about topics other than safety factors. These findings should not be read as apportioning blame or liability to any particular organisation or individual. |
From the evidence available, the following findings are made with respect to the fuel exhaustion involving Aero Commander 500-S, VH-MEH, 6 km east of Bathurst Airport, New South Wales on 8 March 2024.
Contributing factors
- For the first 2 sectors, the fuel cap was incorrectly installed with the chain lodged in the fuel tank’s anti‑siphon valve, resulting in the cap dislodging in‑flight and a significant quantity of fuel being siphoned overboard.
- At Parkes Regional Airport, the pilot identified an unexplained discrepancy between their calculated fuel remaining and the fuel quantity gauge indication but did not refuel to a known quantity. As a result, the aircraft departed Parkes with the pilot unaware that there was insufficient fuel to complete the remaining flights.
- After departing Parkes, the pilot likely did not monitor the fuel gauge, continued fuel calculations based on an incorrect fuel quantity, and did not refuel the aircraft to a known quantity at Bathurst Airport. This resulted in fuel exhaustion shortly after the aircraft departed from Bathurst.
Other factors that increased risk
- GAM Air's Quick Turn Around – Pre-Start checklist did not include a fuel quantity check before start, contrary to the aircraft flight manual’s before-start checklist.
Safety actions
Whether or not the ATSB identifies safety issues in the course of an investigation, relevant organisations may proactively initiate safety action in order to reduce their safety risk. The ATSB has been advised of the following proactive safety action in response to this occurrence. |
Safety action by GAM Air
GAM Air published a pilot notice reinforcing fuel management procedures for Aero Commander 500 series aircraft. The notice highlighted the importance of fuel tank cap security, and the likelihood of fuel loss should a fuel cap become dislodged, despite the anti-siphon valve. The notice also provided instructions and guidance on fuel planning, in-flight fuel calculations and fuel log entries to expand on information in the standard operating procedures.
GAM Air also commenced periodic auditing of pilot fuel calculations and advised an intention to discontinue use of the Quick Turn Around – Pre-Start checklist. The fuel supplier at Bankstown was also reminded of the requirement to let fuel settle when refuelling.
Sources and submissions
Sources of information
The sources of information during the investigation included the:
- pilot
- aircraft operator and maintainer
- Civil Aviation Safety Authority
- Parkes maintenance engineer
- aircraft manufacturer
- recorded flight data.
Submissions
Under section 26 of the Transport Safety Investigation Act 2003, the ATSB may provide a draft report, on a confidential basis, to any person whom the ATSB considers appropriate. That section allows a person receiving a draft report to make submissions to the ATSB about the draft report.
A draft of this report was provided to directly involved parties including the:
- pilot
- aircraft operator and maintainer
- Civil Aviation Safety Authority
- Parkes maintenance engineer
- aircraft manufacturer.
Submissions were received from the:
- aircraft operator and maintainer
- Civil Aviation Safety Authority
The submissions were reviewed and, where considered appropriate, the text of the report was amended accordingly.
Purpose of safety investigationsThe objective of a safety investigation is to enhance transport safety. This is done through:
It is not a function of the ATSB to apportion blame or provide a means for determining liability. At the same time, an investigation report must include factual material of sufficient weight to support the analysis and findings. At all times the ATSB endeavours to balance the use of material that could imply adverse comment with the need to properly explain what happened, and why, in a fair and unbiased manner. The ATSB does not investigate for the purpose of taking administrative, regulatory or criminal action. TerminologyAn explanation of terminology used in ATSB investigation reports is available here. This includes terms such as occurrence, contributing factor, other factor that increased risk, and safety issue. Publishing informationReleased in accordance with section 25 of the Transport Safety Investigation Act 2003 Published by: Australian Transport Safety Bureau © Commonwealth of Australia 2024
Ownership of intellectual property rights in this publication Unless otherwise noted, copyright (and any other intellectual property rights, if any) in this report publication is owned by the Commonwealth of Australia. Creative Commons licence With the exception of the Commonwealth Coat of Arms, ATSB logo, and photos and graphics in which a third party holds copyright, this report is licensed under a Creative Commons Attribution 4.0 International licence. The CC BY 4.0 licence enables you to distribute, remix, adapt, and build upon our material in any medium or format, so long as attribution is given to the Australian Transport Safety Bureau. Copyright in material obtained from other agencies, private individuals or organisations, belongs to those agencies, individuals or organisations. Where you wish to use their material, you will need to contact them directly. |
[1] Instrument flight rules (IFR): a set of regulations that permit the pilot to operate an aircraft in instrument meteorological conditions (IMC), which have much lower weather minimums than visual flight rules (VFR). Procedures and training are significantly more complex as a pilot must demonstrate competency in IMC conditions while controlling the aircraft solely by reference to instruments. IFR-capable aircraft have greater equipment and maintenance requirements.
[2] In-flight fuel siphoning: a phenomenon where fuel escapes from the fuel tank of an aircraft in-flight. On aircraft where the fuel filler point is on top of the wing, the low-pressure area above the wing created when an aircraft is in‑flight can draw the fuel up and out of the fuel tank if it is not sufficiently sealed.
[3] Usable fuel: The amount of fuel which is available in the fuel tanks for supply to the engines.
[4] Yawing: the motion of an aircraft about its vertical or normal axis.
[5] Feathering: the rotation of propeller blades to an edge-on angle to the airflow to minimise aircraft drag following an in‑flight engine failure or shutdown.
[6] Instrument Proficiency Check: A 12-monthly assessment with a flight examiner to assess the flying skills and operational knowledge required to conduct flights under the IFR.
[7] Maintenance release: an official document, issued by an authorised person as described in Regulations, which is required to be carried on an aircraft as an ongoing record of its time in service (TIS) and airworthiness status. Subject to conditions, a maintenance release is valid for a set period, nominally 100 hours TIS or 12 months from issue.
[8] Unusable fuel is the amount of fuel in the tank below which continued running of the engine while performing the most adverse manoeuvre cannot be assured.