Executive summary
What happened
On 7 April 2023, during a freight only charter flight from Bankstown Airport, New South Wales, to Archerfield Airport, Queensland, the pilot of a Piper PA-31-350, registered VH-HJE, reported a loss of power from the right engine followed soon after by the left engine. Unable to reach the destination aerodrome, the pilot conducted a gear up forced landing alongside a railway line. The aircraft struck multiple trees and was substantially damaged. The pilot, who was the sole occupant, sustained minor injuries.
What the ATSB found
Post accident inspections conducted by the operator’s engineers and an engine overhaul facility found no indication of a mechanical failure that would have caused the engines to fail.
Although the pilot reported changing from the auxiliary fuel tanks to main fuel tanks prior to descent, the quantity of fuel recovered from each tank after the accident, and fuel burn calculations, indicated that those selections had probably not been made and both engines lost power as a result of fuel starvation.
The loss of power from each engine was misdiagnosed by the pilot as a partial power loss and the engine failure procedures were not carried out. Following the first power loss on the right engine, the right propeller was not feathered. This configuration produced excessive drag, and the aircraft was unable to maintain altitude while the left engine was operating.
A review of the pilot’s sleep history found that it is likely that the pilot was experiencing a level of fatigue shown to have an effect on performance. In this case it is likely that fatigue impacted the pilot’s incorrect tank selection as well as their ability to troubleshoot the loss of power. The flight departed Bankstown at about 0350 and by the time of the accident, the pilot had been awake for almost 20 hours.
What has been done as a result
The operator issued a notice to aircrew and conducted a review of pilot training to include the recognition and management of fuel starvation. Company policy and flight planning software was reviewed to ensure consistency, and the Fatigue Management Manual was updated to include external employment and restrictions around hours of work and duty times.
Safety message
During a power loss event, pilots should take the time to determine whether a total failure has transpired or if the engine is still delivering some power. While this may not be clearly apparent in all configurations, the consequences of misdiagnosing a failed engine can be fatal. The Civil Aviation Safety Authority’s Civil Aviation Advisory Publication CAAP 5.23-1(2) Multi-engine aeroplane operations and training provides guidance on how to identify engine failures in multi‑engine aircraft.
Pilots are reminded of the importance of understanding an aircraft’s fuel supply system and being familiar and proficient in its use. Adhering to procedures, maintaining an accurate fuel record, and ensuring appropriate tank selections are made for the phase of flight will lessen the likelihood of fuel starvation.
Fuel management related accidents have been published by the ATSB in Avoidable Accidents No. 5 – Starved and exhausted: Fuel management aviation accidents (AR-2011-112) which outlines strategies and key messages for fuel management.
The management of fatigue is a joint responsibility between the operator and the pilot. This accident also reinforces the importance of obtaining some sleep during the day prior to commencing operations at night during normal periods of sleep.
The ATSB SafetyWatch highlights the broad safety concerns that come out of our investigation findings and from the occurrence data reported to us by industry. One of the safety concerns is improving the management of fatigue.
The investigation
Decisions regarding the scope of an investigation are based on many factors, including the level of safety benefit likely to be obtained from an investigation and the associated resources required. For this occurrence, a limited-scope investigation was conducted in order to produce a short investigation report, and allow for greater industry awareness of findings that affect safety and potential learning opportunities. |
The occurrence
On 7 April 2023, the pilot of a Piper Aircraft Corporation PA-31-350 Chieftain (PA-31), registered VH-HJE and operated by Air Link, was conducting a freight charter flight from Archerfield, Queensland. The planned flight included one intermediate stop at Bankstown, New South Wales before returning to Archerfield, and was conducted under the instrument flight rules at night.
The aircraft departed Archerfield at about 0024 local time and during the first leg to Bankstown, the pilot reported an intermittent fault with the autopilot, producing uncommanded pitch changes and associated rates of climb and descent of around 1,000 ft/min. As a result, much of the first leg was flown by hand. After landing at Bankstown at about 0248, a defect entry was made on the maintenance release; however, the pilot was confident that they would be able to hand fly the aircraft for the return leg and elected to continue with the planned flight.
The aircraft was refuelled to its maximum capacity for the return leg after which a small quantity of water was detected in the samples taken from both main fuel tanks. Additional fuel drains were conducted until the fuel sample was free of water. The manifested freight for the return leg was considered a light load and the aircraft was within weight and balance limitations.
After taking off at 0351, the pilot climbed to the flight planned altitude of 9,000 ft. Once established in cruise, the pilot changed the left and right fuel selectors from the respective main tank to the auxiliary tank. The pilot advised that, during cruise, they engaged the autopilot and the uncommanded pitch events continued. Consequently, the pilot did not use the autopilot for part of the flight.
Approaching top of descent, the pilot recalled conducting their normal flow[1] checks by memory before referring to the checklist. During this time, the pilot completed a number of other tasks not related to the fuel system, such as changing the radio frequency, checking the weather at the destination and briefing themselves on the expected arrival into Archerfield. Shortly after, the pilot remembered changing from the auxiliary fuel tanks back to the main fuel tanks and using the fuel quantity gauges to confirm tank selection. The pilot calculated that 11 minutes of fuel remained in the auxiliary tanks (with an estimated 177 L in each main tank).
Around eight minutes after commencing descent and 28 NM (52 km) south of Archerfield (at 0552), the pilot observed the right ‘low fuel flow’ warning light (or ‘low fuel pressure’) illuminate on the annunciator panel. This was followed soon after by a slight reduction in noise from the right engine. As the aircraft descended through approximately 4,700 ft, the ADS-B data showed a moderate deceleration with a gradual deviation right of track. While the power loss produced a minor yaw[2] to the right, the pilot recalled that only a small amount of rudder input was required to counter the adverse yaw once the autopilot was disconnected. Without any sign of rough running or engine surging, they advised that had they not seen the annunciator light, they would not have thought there was a problem. Over the next few minutes, the pilot attempted to troubleshoot and diagnose the problem with the right engine.
Immediately following power loss, the pilot reported they:
- switched on both emergency fuel boost pumps
- advanced both mixture levers to RICH
- cycled the throttle to full throttle and then returned it to its previous setting without fully closing the throttle
- moved the right fuel selector from main tank to auxiliary
- disconnected the autopilot and retrimmed the aircraft.
This did not alter the abnormal operation of the right engine, and the pilot conducted the engine roughness checklist from the aircraft pilot’s operating handbook noting the following:
- oil temperature, oil pressure, and cylinder head temperature indicated normally
- manifold absolute pressure (MAP) had decreased from 31 inHg to 27 inHg
- exhaust gas temperature (EGT) indicated in the green range[3]
- fuel flow indicated zero.
With no indication of mechanical failure, the pilot advised they could not rule out the possibility of fuel contamination and chose not to reselect the main tank for the remainder of the flight.
After considering the aircraft’s performance, handling characteristics and engine instrument indications, the pilot assessed that the right engine, while not able to generate normal power, was still producing some power and that this would assist in reaching Archerfield. Based on the partial power loss diagnosis, the pilot decided not to shut down and secure the engine which would have included feathering[4] the propeller.
At 0556, at about 20 NM south of Archerfield at approximately 3,300 ft, the pilot advised air traffic control (ATC) that they had experienced an engine malfunction and requested to maintain altitude. With maximum power being set on the fully operating left engine, the aircraft was unable to maintain height and was descending at about 100 ft/min. Even though the aircraft was unable to maintain height, the pilot calculated that the aircraft should have been able to make it to Archerfield and did not declare an emergency at that time.
At 0602, about 12 minutes after the power loss on the right engine, the left engine began to run rough and the pilot observed the left low fuel flow warning light illuminate on the annunciator panel. This was followed by severe rough running and surging from the left engine which produced a series of pronounced yawing movements. The pilot did not run through the checklist a second time for the left engine, reporting that they completed the remaining item on the checklist for the left engine by switching the left engine’s fuel supply to the auxiliary tank. The pilot once again elected not to change tank selections back to mains.
With both engines malfunctioning and both propellers unfeathered, the rate of descent increased to about 1,500 ft/min. The pilot advised that following the second power loss, it was clear that the aircraft would not be able to make it to Archerfield and their attention shifted from troubleshooting and performance management to finding somewhere to conduct a forced landing.
ADS-B data showed the aircraft was at about 1,600 ft when the left engine malfunctioned. The pilot stated that they aimed to stay above the minimum control speed, which for VH-HJE was 72 kt.[5] The aircraft was manoeuvred during the brief search (Figure 1), during which time the groundspeed fluctuated from 110 kt to a low of 75 kt. It was calculated that in the prevailing wind, this would have provided an approximate indicated airspeed of 71 kt; equal to the aircraft’s clean configuration stall speed.[6]
Figure 1: Flight profile showing recorded groundspeed
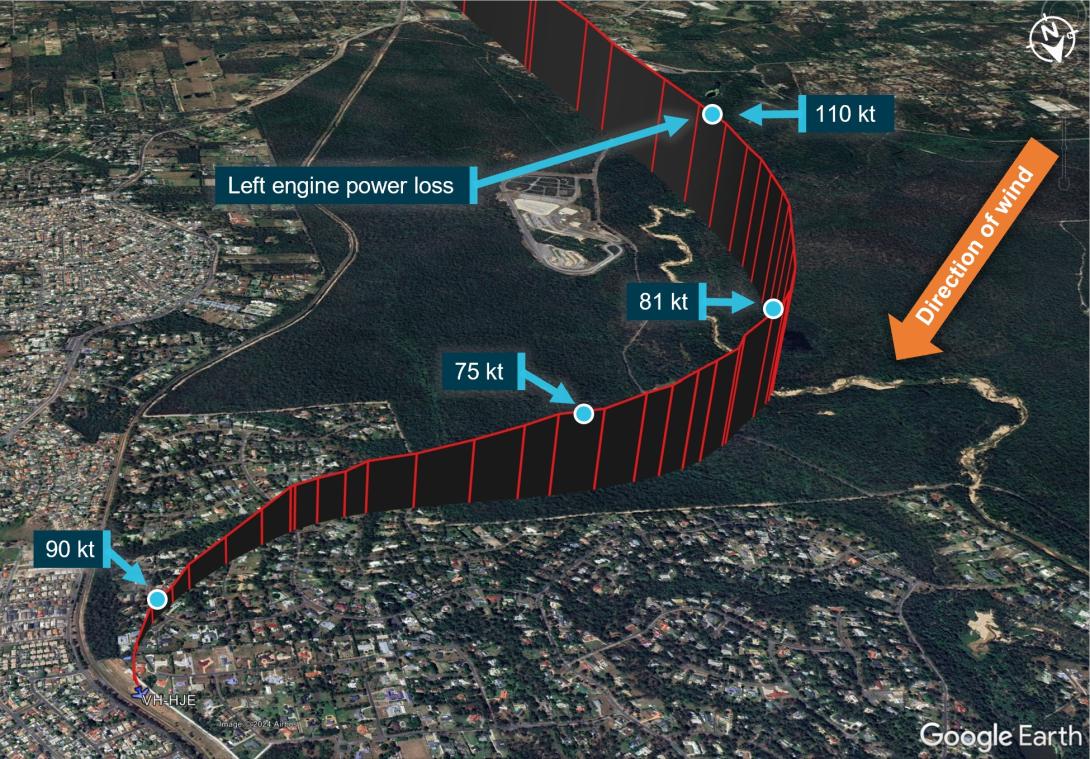
Source: Google Earth, annotated by the ATSB based on ADS-B data
The pilot declared an emergency and advised ATC that they were unable to make Archerfield Airport and would be conducting an off‑airport forced landing. With very limited suitable landing areas available (Figure 1), the pilot elected to leave the flaps and gear retracted to minimise drag to ensure they would be able to make the selected landing area.
At about 0605, the aircraft touched down in a rail corridor beside the railway line, and the aircraft’s left wing struck a wire fence. The aircraft hit several trees, sustaining substantial damage to the fuselage and wings (Figure 2). The pilot received only minor injuries in the accident and was able to exit through the rear door of the aircraft.
Figure 2: Accident site
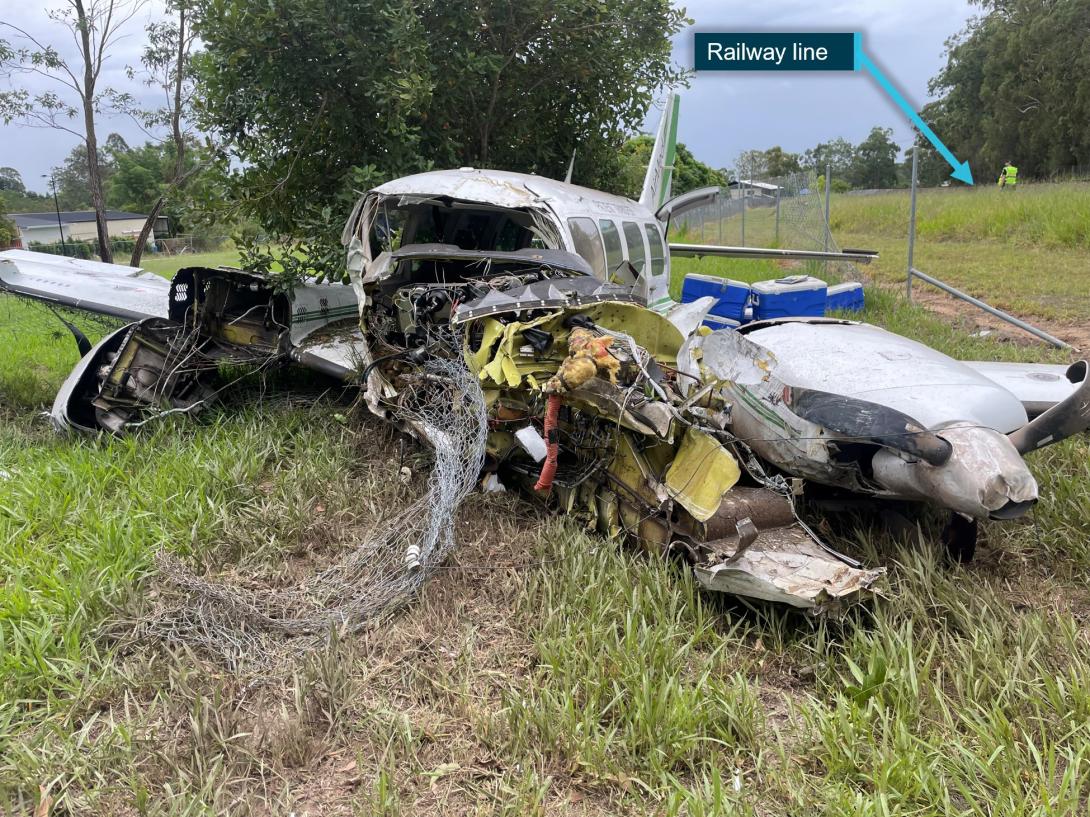
Source: Queensland Police Service, annotated by the ATSB
Context
Pilot qualifications and experience
The pilot attained their commercial pilot licence (aeroplane) in 2020 and completed an instrument proficiency check on a multi-engine aircraft in May 2022. Both a line check and a proficiency check were completed with the operator on 9 January 2023, where the pilot was assessed as competent, and approved to conduct charter flights.
At the time of the accident, the pilot had 1,473 total flight hours, 233 hours on multi-engine aircraft, of which 204 hours were logged on Piper PA-31-350 type aircraft.
Aircraft information
Aircraft
VH-HJE was a Piper PA-31-350 ‘Chieftain’, light twin-engine aircraft, fitted with Textron Lycoming TIO-540 turbocharged piston engines. The aircraft was manufactured in the US in 1978 and was first registered in Australia in 1987. Air Link became the registered operator in July 2022.
The company operated 12 PA-31 aircraft. These aircraft all used the same operational data published in the operator’s piston engine aircraft flight crew operating manual. VH-HJE had been fitted with a Boundary Layers Research vortex generator kit. This kit increased the maximum permitted take-off weight, while lowering the minimum control speeds and stall speeds of the aircraft.
Operating instructions and performance figures were provided in a supplement to the aircraft’s pilot operating handbook. Discussion indicated the pilot was familiar with the supplement and its contents.
There were no on-board recording devices installed in VH-HJE that would have recorded engine indications or fuel system settings.
Fuel system
The aircraft contained 2 inboard main fuel tanks and 2 outboard auxiliary fuel tanks that provided a combined usable fuel quantity of 690 L of AVGAS. The fuel management controls were located on the fuel control panel between the front seats. The controls consisted of tank selectors, tank shutoffs and cross-feed controls.
The fuel controls in the cockpit controlled the left and right fuel tanks’ supply to their respective engines. Figure 3 shows the layout of the standard fuel system installed in the aircraft.
Figure 3: PA-31-350 Fuel system schematic

Source: Piper PA-31-350 pilot operating handbook, annotated by the ATSB
The pilot operating handbook contained operating instructions for the selection of tanks during various phases of flight. Due to the shape of the tanks and the location of the fuel outlet at the rear of the tanks, certain manoeuvres may cause the fuel to move away from the outlet increasing the likelihood of fuel flow interruption. To avoid this, the manufacturer published guidance around minimum quantities of fuel to be retained in each tank when manoeuvring. Further to this, inboard main tanks were required to be selected for take-off, climb and descent, with the auxiliary tanks only to be used during level co-ordinated flight in cruise. The operator adhered to the manufacturer’s guidance with the checklist in Figure 4 serving as a prompt to the pilot to ensure the inboard tanks were selected for descent.
Figure 4: PA-31-350 top of descent checklist
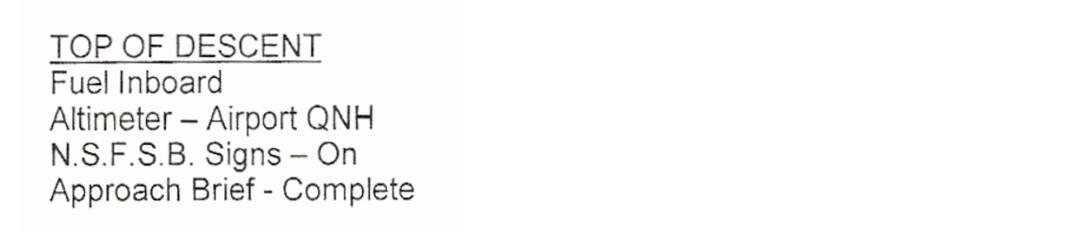
Source: Operator’s Flight Crew Operating Manual - Piston.
The PA-31-350 was equipped with 3 fuel pumps each for the left and right fuel systems:
- engine-driven fuel pump
- fuel boost pump that operated when the electric master switch was turned on
- emergency fuel pump that could be used in case of an engine‑driven fuel pump failure.
When fuel boost pressure was less than 3 psi, fuel boost pump warning lights located on the annunciator panel would illuminate.
Later build PA-31-350 aircraft are equipped with a left and right low fuel warning light that activates when the fuel level near the main tank outlet drops to a level where fuel flow interruption and power loss could occur. An engineering order had been obtained by a previous operator to modify the fuel system and remove these warning lights and associated hardware from VH-HJE due to the expense of replacing the fuel probes.
The engineering order included the following requirements:
- amendment of the aircraft minimum equipment list to alert pilots of the system’s removal
- the statement ‘Operating Procedures – During the flight, flight crew shall monitor the related fuel flow indicator’ shall remain in the minimum equipment list
- a placard alerting the crew of the system’s removal shall be installed in the cockpit
- this placard should be incorporated into the inspection schedule to ensure that it continues to remain legible.
At the time of the accident, the warning system had not been reinstalled and a worn placard was installed in the aircraft (Figure 5).
This unique configuration was not reflected in the operator’s PA-31 minimum equipment list[7] where aircraft were required to have at least one low fuel warning light serviceable for flight. The only warning lights related to the fuel system on the annunciator panel in VH-HJE were the fuel boost pump warning lights that activated in response to low fuel pressure.
A fuel-burning heater was installed as part of the cabin heating, ventilating, and defrosting system. Fuel was plumbed into the heater from the selected right fuel tank. Based on pilot experience, the average consumption rate was estimated at 6 L/hr.
Figure 5: Cockpit
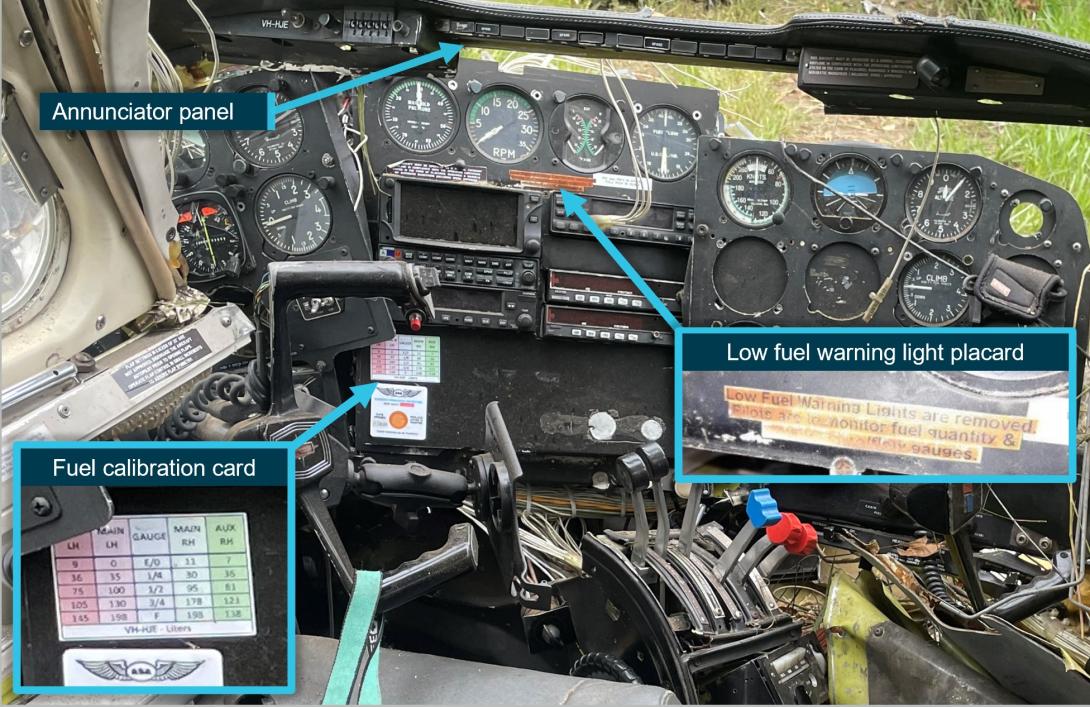
Image shows the low fuel warning light placard below the engine instruments, the annunciator panel that houses the light it refers to and the fuel calibration card on the instrument panel.
Source: Operator, annotated by the ATSB
Recent maintenance
VH-HJE was released from maintenance prior to the accident flight following work by engineers to rectify a defect with the autopilot. The intermittent defect produced uncommanded pitch events with significant nose-up and nose-down deviations while the autopilot was engaged in both pitch and altitude[8] modes. The autopilot received inputs from the aircraft’s attitude indicator, and during maintenance the attitude indicator was replaced. In addition to the requirements of the maintenance manual, the engineers also tested the autopilot’s response to in and out-of-level conditions prior to engine start to confirm it was performing as expected before the aircraft was returned to service.
Additionally, the right engine-driven fuel pump was adjusted following a report of the output pressure being at or near the minimum permitted for normal operations.
The operator advised that they had resting and maintenance facilities available at Bankstown airport. The pilot did not advise Bankstown engineering staff or the Archerfield base manager of the recurrence of the problem with the autopilot prior to the accident flight.
Engine-related procedures and guidance
The aircraft pilot’s operating handbook (POH) contained emergency checklists including those for engine roughness (Figure 6) and an engine failure during flight (Figure 7).
Figure 6: PA-31-350 engine roughness checklist
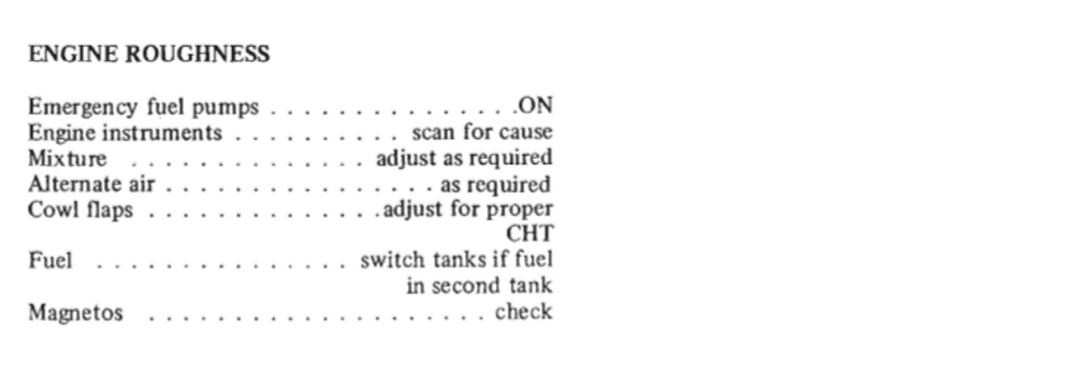
Source: Piper PA-31-350 pilot operating handbook.
Figure 7: PA-31-350 engine failure during flight
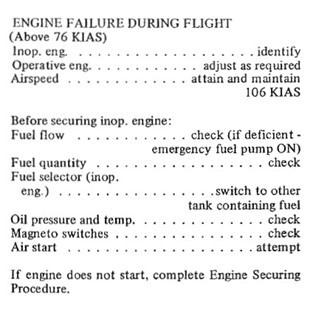
Source: Piper PA-31-350 pilot operating handbook
If a multi-engine aircraft experiences an engine failure when airborne, there are two immediate aerodynamic effects; the yawing that occurs due to the asymmetric thrust from the engines, and the drag effect of the windmilling[9] propeller. To maintain directional control with an inoperative engine, the rudder must be deflected to counteract the adverse yaw.
The speed at which full rudder deflection can maintain a constant heading in combination with a 5 degree bank angle is defined, by regulations, as the minimum control speed and is referred to as velocity of minimum control in the air (Vmca). Vmca will vary depending on aircraft configuration. These criteria combine to give the published Vmca, which is a conservative example of when directional control will be lost (not the lowest possible speed where directional control will be lost). When Vmca occurs close to the aircraft’s stall speed, there is a reduced margin over the stall speed at which a departure from controlled flight will occur.
Examples of criteria that affect the actual minimum speed that directional control can be maintained include:
- higher power settings (creates higher asymmetric forces)
- windmilling propeller (increases asymmetric drag)
- flap setting (likely configuration for phase of flight where potential Vmca issues are greatest and/or adds buffer over stall speed)
- landing gear retracted (asymmetric drag potentially the greatest, no drag added by landing gear in accelerated airflow on the live side); and
- centre of gravity (aft centre of gravity is the most unfavourable position).
The total yawing moment can be very large, particularly when the aeroplane is at high power and low speed such as during a take-off. For lower power settings and higher airspeeds, such as those used for descent, this aerodynamic effect will be less pronounced. While the drag from the failed engine remains, the thrust from the operating engine is less, and therefore the resulting yaw will be less noticeable and may reinforce the pilot’s perception of a partial power loss. Additionally, the increased airflow over the rudder surface during descent will make the rudder more effective and therefore easier to manage the adverse yaw from the failed engine.
The first item of the engine failure checklist in Figure 7 – identification of the inoperative engine – did not specify the method to identify an inoperative engine. In Civil Aviation Advisory Publication CAAP 5.23-1(2) Multi-engine aeroplane operations and training, the Civil Aviation Safety Authority (CASA) provided the following related guidance:
As a rule, unless a catastrophic engine failure occurs, an engine does not just fail without warning. It should be noted that the rpm and manifold pressure gauges of a piston engine are not reliable means of identifying a failed engine, as the instrument indications may appear normal. After identifying the failed engine through, for example, the ‘dead leg, dead engine’ method, the pilot should confirm that their identification is correct. This is done by closing the throttle of the failed engine - if no yaw develops as the throttle is eased back, and the serviceable engine operates normally it confirms the identification of the faulty engine.
During an actual failure, pilots should also take the time to determine whether a total failure has transpired or if the engine is still delivering some power. If it is delivering power, use the thrust to get to a safe height before shutting the engine down to avoid further damage, unless a greater risk exists in continuing to operate the engine, such as fire, oil/fuel leaks or significant mechanical damage.
The US Federal Aviation Administration FAA Airplane Flying Handbook Chapter 13: Transition to Multiengine Airplanes also provided guidance for the identification of an inoperative engine and advised the drag and adverse yaw produced by a windmilling propeller can be as much as the entire airframe.
According to the POH checklist, if engine power could not be restored, the pilot was directed to the engine securing procedure. The key part of this procedure was to close the throttle of the inoperative engine and feather the propeller. On a multi-engine aircraft, feathering the propeller of a failed engine results in both a reduction in drag and a reduction in adverse yaw, vastly improving the engine-out handling characteristics and the engine-out flight performance of the aircraft. For the aircraft weight and environmental conditions, the one-engine climb performance published in the POH was a positive rate of climb of about 300 ft/min.
The engine manufacturer advised that for a windmilling inoperative engine, any change in throttle position would have an effect on indicated manifold pressure.
Closing the throttle would increase a vacuum (less MP) in the system, whereas opening the throttle plate would allow the induction system to equalise with atmospheric pressure.
At an altitude of about 3,000 ft, an indication of 27 inHg of manifold pressure is consistent with ambient atmospheric air pressure and explains the indications observed by the pilot with full throttle set.
The manufacturer advised that they did not provide any guidance for scenarios resulting from multiple simultaneous failures. The assumption being that the engines operate independently of each other with their own independent fuel systems. Both engines failing would be the result of multiple unrelated failures or the mismanagement of a common system. As such, they did not, nor were they required to, specify a power-off or recommended glide speed for the aircraft. The POH referred to power-off landings as a basic emergency procedure covered in normal flight training and recommended that these procedures were reviewed periodically to maintain proficiency.
Engineering inspection
The ATSB did not attend the accident site. Photos supplied by the Queensland Police Service and reports obtained by engineers who inspected the wreckage revealed the following:
- both fuel selectors were found in the ‘auxiliary’ position
- fuel selector mechanisms were serviceable
- both emergency boost pumps were found in the ‘on’ position
- less than 600 ml of fuel was found in each auxiliary tank that were undamaged
- approximately 180 L of fuel was drained from right main tank
- the left main tank drain valve was sheared off and no fuel was recovered
- no residual fuel was found in the fuel system except for the airframe fuel filter
- no foreign objects or debris were found in any of the fuel tanks
- all fuel tanks were found to be intact with fuel tank flapper valves[10] operating freely.
Several engine components were sent away for independent testing. These included the engine‑driven fuel pumps, the emergency boost pumps, magnetos, and the fuel control units. The inspection found no evidence of a mechanical failure that would have precluded the normal operation of the engines at the time of the accident.
Additionally, engineers inspected various components with the following observations:
- oil filters contained normal deposits
- spark plugs were very clean indicating a potential lack of fuel
- a limited internal inspection of cylinders appeared normal
- right engine fuel control unit filter contained small non-magnetic slivers, possibly from one of the fuel pumps
- left engine fuel control unit filter was clean
- fuel nozzles were clear
- both engine‑driven fuel pump drive shafts were intact
- right engine turbo elbow was dislodged from the fuel control unit (suspected impact damage).
Operator’s fuel planning
The operator’s fuel policy conformed to the CASA guidance in Advisory Circular AC 91-15 v1.1 – Guidelines for aircraft fuel requirements.
The advisory circular specified that an accurate fuel consumption rate was to be used to calculate the required fuel quantity for a flight. Aircraft‑specific data should be derived from a fuel consumption monitoring (FCM) system or the aircraft manufacturer’s fuel consumption data. The operator had an FCM system in place and monitored the fuel burn figures from in-flight trend records and flight logs against historical fuel consumption rates for the PA-31.
The operator’s fuel policy provided a consumption of 160 L/h for use across the fleet of PA-31 aircraft. This figure was derived from operational experience and considered a conservative figure to account for the various fuel consumption rates during the climb, cruise and descent phases of flight.
The operator’s flight crew operating manual (FCOM) for piston aircraft provided fuel flow figures specific to the climb, cruise and descent phases of flight. These fuel figures were taken from the POH and provided in US gallons per hour, in the same units of measurement found on the aircraft fuel gauges.
The company utilised AvPlan flight planning software. In addition to generating the flight plan based on imported weather and route details, the program also generated the fuel calculations for the flight. The program required separate fuel consumption rates for the climb and the cruise phases of flight. The operator advised that the fuel consumption rates uploaded into AvPlan were derived from company data, aircraft manual figures and trend monitoring of the aircraft fuel use, and were calculated to provide the same overall figure that would be obtained by calculations using the fuel policy fuel flow of 160 L/h for the PA-31.
The AvPlan fuel calculations for the accident flight and flight prior are provided in Table 1.
Table 1: VH-HJE flight planned fuel calculations
FROM |
Archerfield |
Bankstown |
||
FUEL CALC. |
Minutes |
Litres |
Minutes |
Litres |
Climb |
17 |
62 |
15 |
55 |
Cruise |
126 |
285 |
131 |
297 |
Altn |
0 |
0 |
0 |
0 |
TRIP FUEL |
144 |
347 |
147 |
352 |
Contingency |
21 |
52 |
22 |
53 |
Final Reserve |
45 |
109 |
45 |
108 |
Holding |
0 |
0 |
0 |
0 |
Approach |
|
0 |
|
0 |
Taxi |
|
10 |
|
10 |
Fuel Required |
210 |
518 |
213 |
523 |
Margin |
81 |
172 |
77 |
167 |
ENDURANCE |
290 |
690 |
290 |
690 |
Source: Data reproduced by the ATSB from the operator’s flight plan
The operator advised that all company PA-31 were equipped with a GPS featuring an in‑built fuel calculator and that this was a company‑approved means of cross-checking the quantity of fuel on board when in-flight. The pilot also confirmed that they regularly used this GPS feature and the calculator was used on the flight. This required the fuel policy fuel flow figure to be entered into the GPS fuel calculator, which then provided an estimated fuel required and fuel remaining figure in litres based on the flight time. Other means of determining fuel quantity on board when in-flight included:
- calculated flight plan figures in litres
- checking fuel quantity gauges against the aircraft’s fuel calibration card in gallons (Figure 5)
- referencing the flight log against the aircraft fuel flow gauges presented in gallons.
Table 2 is based on the accident flight from Bankstown to Archerfield for VH-HJE on 7 April 2023. It shows the different fuel requirements when using the fuel policy consumption rate compared to the pilot’s flight plan calculated using AvPlan.
Table 2: Fuel calculations
Time (minutes) | AvPlan (litres) | Fuel policy rate (litres) | |
Taxi |
- |
10 |
10 |
Climb |
15 |
55 |
40 |
Cruise/Descent |
131 |
297 |
349 |
Trip fuel + Taxi |
146 |
362 |
399 |
Contingency fuel |
15% trip fuel [11] |
53 |
58 |
Final reserve |
45 @ cruise flow |
102 |
120 |
Total required |
517 |
579 |
As part of the FCM system, any discrepancies greater than 3% of the planned fuel consumption were to be reported by pilots through the internal reporting system and investigated by the continuing airworthiness and maintenance manager. The operator advised that no fuel discrepancy reports had been made for this aircraft and the review process[12] had not identified any adjustment required to the PA-31 fuel consumption rate published in the fuel policy.
The ATSB conducted a review of the flights in VH-HJE between February 2023 and April 2023 for those flights where flight plans were provided by the operator. Analysis was limited to flights of the same route and of similar duration (+/- 0.1 hour flight time duration without evidence of a diversion). The AvPlan fuel calculations on the flight plans were compared to the recorded fuel burns in the company’s fuel log for VH-HJE. Of the 13 flight records of a similar duration, it was determined that 9 flights had fuel consumptions that were more than 103% of the AvPlan fuel calculation.
Fatigue
The pilot was employed by the operator on a casual basis and had recently commenced secondary ground-based employment with a different employer. The operator was aware of the secondary employment and advised this was very common, with the majority of casual pilots working a second non-aviation job. However, there was no requirement for casual aircrew to disclose secondary employment. As a result, there was no company oversight of hours worked outside rostered flight and duty times, and it was not considered when generating the pilot’s roster. The fatigue risk management manual outlined the operator’s expectation that pilots would notify the operator of a change in circumstances that may impact the pilot’s ability to meet the fatigue management obligations and that once provided with a roster, pilots would ensure they were fit for duty, making the necessary arrangements to facilitate the rostered shifts. Company pilots were provided with a roster a month in advance. A typical roster consisted of 2–4 flights per week with additional rostered duty periods for training.
Existing measures in place to ensure that fatigue was being managed included providing crew with appropriate rest opportunity prior to commencing a duty period and providing rest facilities at each base.
On the day of the occurrence the pilot reported waking at 1030 after obtaining 13 hours sleep. They worked a shift with their second employer from 1300 until 2130 before driving to the airport to prepare for the flight. The pilot advised that for the particular flight they were rostered to complete, they usually arrived at 2230 to allow time for planning and preparation. The duty period ran continuously from their arrival at 2230 until the accident at 0605 the following morning.
Using the information obtained at interview and the pilot’s roster, the ATSB conducted a fatigue analysis, including using biomathematical analysis software. From the fatigue analysis, the ATSB identified it was likely that the pilot was experiencing a level of fatigue shown to affect performance, predominately due to hours awake, sleep in the previous 24 hours and time of day. The additional employment shift was considered in the fatigue analysis to determine if it likely increased the estimated fatigue level of the pilot, and it was found to not have a significant influence.
Related occurrences
Fuel management and fuel starvation incidents and accidents continue to occur in twin engine aircraft. Examples of other ATSB investigations covering starvation related occurrences include:
- Fuel starvation and forced landing involving Piper PA-31, VH-IHR, 22 km N of Mount Isa Airport, Qld, on 17 July 2008 (AO-2008-048).
- Fuel starvation and forced landing involving Piper PA-28, VH-BDB, 15 km WSW of Bankstown Airport, NSW, on 19 September 2017 (AO-2017-094).
- Fuel starvation involving Cessna 206, 3.5 NM NE of Aldinga, SA, on 3 February 2019 (AB‑2019-004).
- Fuel starvation event involving Cessna 310, VH-JQK, near Sunshine Coast Airport, Queensland, on 18 August 2022 (AO-2022-040).
The 2013 ATSB publication, Avoidable Accidents No. 5: Starved and exhausted: Fuel management aviation accidents (AR-2011-112) focused on accidents involving fuel starvation due to fuel management, stating:
Keeping fuel supplied to the engines during flight relies on the pilot’s knowledge of the aircraft’s fuel supply system and being familiar and proficient in its use. Adhering to procedures, maintaining a record of the fuel selections during flight, and ensuring the appropriate tank selections are made before descending towards your destination will lessen the likelihood of fuel starvation at what may be a critical stage of the flight.
Safety analysis
As the aircraft was on descent into Archerfield the right engine failed. The pilot treated it as a partial power loss and continued without managing to restore power or secure the engine, and was unable to maintain altitude.
About 12 minutes later the left engine also lost power and the pilot was forced to make an off‑airport landing. Although the aircraft was seriously damaged during the landing, the pilot escaped with minor injuries.
The ATSB considered the factors that could have affected operation of both engines and pilot management of the emergency. Pilot fatigue and company procedures were also considered.
Engine power loss
In simple terms, engine power loss can occur in a PA-31-350 because of a mechanical defect, fuel contamination, or fuel exhaustion/starvation.
The operator examined the aircraft, and key engine and fuel system components were independently tested. As no defects were identified, the ATSB concluded that there was probably no mechanical factor in the loss of power to either engine.
With regard to the water identified after refuelling at Bankstown, given the fuel was drained until there was no water in the samples and the aircraft was operated on main tanks in the first part of the flight without incident, it is unlikely that fuel contamination was a factor.
Based on the fuel plan, fuel uplifted at Bankstown, and examination of the aircraft after the forced landing, there was sufficient fuel on board the aircraft for the planned flight from Bankstown to Archerfield. In that context, the ATSB considered fuel starvation.
The pilot reported operating on main tanks for take-off and climb, auxiliary tanks for cruise, then changing to the main tanks for descent. Based on the likely fuel consumed from each tank in this scenario using the company approved AvPlan generated fuel log that was available to the pilot, the ATSB calculated there would have been approximately 150 L of usable fuel in each main tank, and 15 L of usable fuel in each auxiliary tank when the engines lost power. In addition to this usable fuel, it would be expected that a quantity of unusable fuel would also be present, however, this was not consistent with the quantity of fuel recovered from the undamaged fuel tanks during the post-accident inspection. As such, if the pilot had moved the fuel tank selector back to the main tanks at the top of descent as was recalled, then there would have been sufficient fuel to complete the flight.
An alternative scenario is that the pilot overlooked changing the fuel tanks from auxiliary to main tanks at top of descent. In that case, the calculated total fuel remaining in each main tank would be approximately 175 L and there would be no usable fuel remaining in the auxiliary tanks. This is consistent with the quantity of fuel recovered from the undamaged fuel tanks. It is also consistent with the fuel system warnings and indications associated with each engine power loss.
The pilot recalled conducting the checks initially by memory and later by reference to the on-board checklist. Considering the time that passed between the check, actioning of the checklist item (fuel selectors), and the number of other tasks the pilot had to attend to, it is possible that the pilot became distracted and either missed the tank change or reversed a selection from the initial flow check.
Based on the determination that there was no fault found with the engines or fuel system that would have precluded the normal operation of both engines, it was determined to be likely that the pilot did not action the checklist items relating to the selection of main fuel tanks for descent, resulting in the change of tanks being missed and the engines being starved of fuel.
Diagnosis and management of the first engine power loss
In a fuel-injected piston engine, the key instrument indications of an engine failure are fuel pressure (if available), fuel flow, and EGT. Despite other indications that may be consistent with an operative engine, if fuel pressure, fuel flow and EGT are significantly low or zero, the engine will not be developing power. The pilot was aware that a fuel flow warning light had activated at the time of each engine power loss, and noted that fuel pressure and flow were zero, but did not appreciate the implications. Although the pilot assessed that the right engine was still producing some power, with zero fuel flow, it is almost certain that the right engine was no longer producing any power and the windmilling propeller produced significant drag for the remainder of the flight.
By continuing with an inoperative unfeathered engine, the pilot was not able to extract the maximum possible performance from the aircraft with the operative engine. Had the propeller been feathered, the aircraft would have been able to maintain height or even climb. While it could not be determined if this would have guaranteed the aircraft would reach Archerfield in the context of the impending left engine failure, it would have provided additional options to the pilot.
Having assessed that the right engine was operating at reduced power, the pilot was not prompted to conduct the engine failure checklist and instead conducted the rough running checklist. That checklist was not applicable and did not assist the pilot to identify and address the engine failure. Nevertheless, the rough running checklist prompted the pilot to scan the instruments and consider switching fuel tanks if there was fuel in the other tank. The pilot was aware there was a substantial amount of fuel in the main tanks and could have confirmed that the auxiliary fuel tank was essentially empty by reference to the fuel quantity indicating system. Because of the water that needed to be drained from the main tanks before flight, and in the absence of mechanical failure, the engine power loss resulted in the pilot hypothesising that the quality of fuel in the main tanks was the cause. This also resulted in the pilot not re-selecting the main tanks at this point. Without using the correct (engine failure) checklist, and with the suspicion about fuel quality, the pilot did not identify the fuel quantities available in each tank.
The ATSB noted that the low fuel warning light system had been removed from the aircraft. This system is essentially a low fuel quantity indication for each main tank and would not have provided a warning for low fuel flow from the auxiliary tanks. Given the substantial quantity of fuel found in the main tanks, the absence of this system was not a factor in this occurrence.
Diagnosis and management of the second engine power loss
The symptoms of the second engine power loss were consistent with fluctuating fuel pressure and flow. As was the case for the right engine, the pilot could have confirmed that the auxiliary fuel tank was essentially empty by reference to the fuel quantity indicating system.
Although continuous engine power was not restored, it is not clear if the left engine failed completely. If that had occurred, feathering the propeller as part of securing the engine would have had a significant benefit to the glide performance of the aircraft.
Fatigue
The International Civil Aviation Organization (ICAO) (2016)[13] defines fatigue as:
… a physiological state of reduced mental or physical performance capability resulting from sleep loss or extended wakefulness, circadian phase, or workload (mental and/or physical activity) that can impair a person’s alertness and ability to perform safety related duties.
At the time of the accident, the pilot had obtained 5 hours sleep in the prior 24 hours and was in a period of high workload. The pilot’s workload likely unexpectedly increased due to the need to manually fly the aircraft for extended periods during the flight, and therefore this would have likely increased the level of fatigue experienced by the pilot. The pilot was also making tank selection decisions during the window of circadian low (a period of maximum sleepiness between 0300–0500).
While the pilot had obtained 13 hours sleep in the night preceding the accident shift, that sleep period ended almost 20 hours earlier with no additional rest obtained prior to commencing the overnight shift. Although the additional employment shift was found to not have had a significant influence on the pilot’s fatigue, completing this shift removed the opportunity for the pilot to obtain additional sleep (through an afternoon nap) prior to commencing their night shift.
Fatigue can affect a variety of performance factors including problem‑solving and decision‑making. In this case it is likely that fatigue impacted the pilot’s incorrect tank selection as well as their ability to troubleshoot the loss of power.
Forced landing manoeuvring speed
Following the second unresolved power loss, it was apparent that a forced landing would be required. The aircraft manufacturer did not provide a glide speed for the PA-31 and the pilot was not aware of an airspeed that would have provided the best glide range. In this case, the airspeed did not have as much effect on performance as the drag produced by the windmilling propellers.
The ADS-B data showed that the aircraft speed reduced during manoeuvring and at times provided a small margin over the stall speed. Although the pilot considered that the aircraft speed could safely be reduced to Vmca, this should be considered in conjunction with the stall speed, especially while turning.
The pilot was able to maintain control of the aircraft and decided to limit drag by not extending flap and landing gear, to maximise the options available to them. The site selected minimised the risk of damage and injury to those on the ground and the controlled touchdown maximised the chances of survivability.
Company fuel documentation
The operator’s fuel policy and flight crew operating manual provided different sources of information relating to fuel flow in the PA-31 and presented these figures in both US gallons and in litres. While intended to be consistent, calculations using the 2 different fuel consumption figures did not always yield the same results.
Due to the requirement to depart with full fuel on flights between Bankstown and Archerfield, the difference in the fuel policy and flight crew operating manual fuel consumption rates was found to be inconsequential and therefore not a contributing factor to this occurrence. Despite this, the provision of fuel‑related data that may not be consistent with established consumption rates, or that increases the likelihood of conversion errors between units of measurement, increases the risk of a fuel related calculation error.
The operator’s fuel consumption monitoring system required company pilots to monitor the fuel consumed on flights and compare these quantities to the fuel plan, reporting discrepancies in excess of 3% of the flight planned figure. However, it was found that the operator was using the block fuel figure of 160 L/h in the fuel policy as the base rate for comparison. The fuel plan generated by the AvPlan software was found to generally provide lower total consumption figures than the fuel policy block figure. As the operator was using a higher consumption rate as the reference figure, fuel monitoring practices did not detect higher fuel burns than what was specified in fuel planning data.
The requirement to depart Bankstown with full tanks ensured an excess of fuel was carried. As a result, the fuel burn for the accident flight, while outside the permitted 3% discrepancy, was determined not to be a contributing factor to this occurrence. Of importance though, operating to a consumption higher than calculated may be significant when the AvPlan software is used to determine the operational limits for the aircraft.
Findings
ATSB investigation report findings focus on safety factors (that is, events and conditions that increase risk). Safety factors include ‘contributing factors’ and ‘other factors that increased risk’ (that is, factors that did not meet the definition of a contributing factor for this occurrence but were still considered important to include in the report for the purpose of increasing awareness and enhancing safety). In addition ‘other findings’ may be included to provide important information about topics other than safety factors. These findings should not be read as apportioning blame or liability to any particular organisation or individual. |
From the evidence available, the following findings are made with respect to the fuel starvation and forced landing involving Piper PA-31-350, VH-HJE, 11 km south of Archerfield Airport, Queensland, on 7 April 2023.
Contributing factors
- It is likely that the pilot did not action the checklist items relating to the selection of main fuel tanks for descent. The fuel supply in the auxiliary tanks was subsequently consumed resulting in fuel starvation and loss of power from the right then left engine.
- Following the loss of power to the right engine, the pilot misinterpreted the engine instrument indications as a partial power loss and carried out the rough running checklist but did not select the main tanks that contained substantial fuel to restore engine power, or feather the propeller. This reduced the available performance resulting in the aircraft being unable to maintain altitude.
- When the left engine started to surge and run rough, the pilot did not switch to the main tank that contained substantial fuel, necessitating an off‑airport forced landing.
- It is likely that the pilot was experiencing a level of fatigue shown to have an effect on performance.
Other factors that increased risk
- As the pilot was manoeuvring for the forced landing there was a significant reduction of airspeed. This reduced the margin over the stall speed and increased the risk of loss of control.
- Operator guidance material provided different fuel flow figures in the fuel policy and flight crew operating manual for the PA-31 aircraft type.
- The operator’s fuel monitoring practices did not detect higher fuel burns than what was specified in fuel planning data.
Other findings
- The forced landing site selected minimised the risk of damage and injury to those on the ground and the controlled touchdown maximised the chances of survivability.
Safety actions
Whether or not the ATSB identifies safety issues in the course of an investigation, relevant organisations may proactively initiate safety action in order to reduce their safety risk. The ATSB has been advised of the following proactive safety action in response to this occurrence. |
Safety action by Air Link
Following this occurrence, the operator issued a notice to aircrew and conducted a review of pilot training to include the recognition and management of fuel starvation. Company policy and flight planning software was reviewed to ensure consistency, and the Fatigue Management Manual was updated to include external employment and restrictions around hours of work and duty times.
Sources and submissions
Sources of information
The sources of information during the investigation included:
- the pilot of the accident flight
- Air Link
- the maintenance organisation for VH-HJE
- the Queensland Police Service
- the Civil Aviation Safety Authority
- the Bureau of Meteorology
- the aircraft and engine manufacturers.
Submissions
Under section 26 of the Transport Safety Investigation Act 2003, the ATSB may provide a draft report, on a confidential basis, to any person whom the ATSB considers appropriate. That section allows a person receiving a draft report to make submissions to the ATSB about the draft report.
A draft of this report was provided to the following directly involved parties:
- the pilot of the accident flight
- Air Link
- the Civil Aviation Safety Authority
- the Bureau of Meteorology
- the aircraft and engine manufacturers.
Submissions were received from:
- Air Link
- the Civil Aviation Safety Authority.
The submissions were reviewed and, where considered appropriate, the text of the report was amended accordingly.
Purpose of safety investigationsThe objective of a safety investigation is to enhance transport safety. This is done through:
It is not a function of the ATSB to apportion blame or provide a means for determining liability. At the same time, an investigation report must include factual material of sufficient weight to support the analysis and findings. At all times the ATSB endeavours to balance the use of material that could imply adverse comment with the need to properly explain what happened, and why, in a fair and unbiased manner. The ATSB does not investigate for the purpose of taking administrative, regulatory or criminal action. TerminologyAn explanation of terminology used in ATSB investigation reports is available here. This includes terms such as occurrence, contributing factor, other factor that increased risk, and safety issue. Publishing informationReleased in accordance with section 25 of the Transport Safety Investigation Act 2003 Published by: Australian Transport Safety Bureau © Commonwealth of Australia 2024 Ownership of intellectual property rights in this publication Unless otherwise noted, copyright (and any other intellectual property rights, if any) in this report publication is owned by the Commonwealth of Australia. Creative Commons licence With the exception of the Coat of Arms, ATSB logo, and photos and graphics in which a third party holds copyright, this publication is licensed under a Creative Commons Attribution 3.0 Australia licence. Creative Commons Attribution 3.0 Australia Licence is a standard form licence agreement that allows you to copy, distribute, transmit and adapt this publication provided that you attribute the work. The ATSB’s preference is that you attribute this publication (and any material sourced from it) using the following wording: Source: Australian Transport Safety Bureau Copyright in material obtained from other agencies, private individuals or organisations, belongs to those agencies, individuals or organisations. Where you wish to use their material, you will need to contact them directly. |
[1] Flow checks: Flight-phase related actions are performed from memory following a cockpit flow pattern. Specific critical items are checked /cross-checked using a challenge-and-response checklist, whereby the pilot reads the items to be checked and confirms the proper status/configuration of the appropriate items.
[2] Yaw: the motion of an aircraft about its vertical or normal axis.
[3] All of the indicating range below the red line was colour coded green.
[4] Feathering: the rotation of propeller blades to an edge-on angle to the airflow to minimise aircraft drag following an in‑flight engine failure or shutdown.
[5] HJE was fitted with a vortex generator kit which lowered the minimum control speed in the air from 76 kt to 72 kt, and the clean configuration stall speed from 77 kt to 71 kt.
[6] Winds obtained from the aerodrome weather information service at 0551 local time indicated winds from 280 at 5 kt. The Meteorological Aerodrome Report (METAR) at the time of the accident indicated winds of 240 at 5 kt. Following the first turn to the right, this placed the wind behind the aircraft with about 4 kt of tailwind. For the ADS-B groundspeed of 75 kt, this meant the indicated airspeed would have been approximately 71 kt.
[7] A copy of this minimum equipment list was carried in VH-HJE.
[8] Pitch and altitude modes: Both are vertical navigation modes of an automatic flight control system, also known as an autopilot. Pitch mode maintains a constant attitude where altitude mode maintains a preset altitude.
[9] Windmilling: a rotating propeller being driven by the airflow rather than by engine power, and results in increased drag at normal propeller blade angles.
[10] Flapper valves are one-way valves installed in the fuel tanks that prevent backflow in the system.
[11] AC 91-15 does not require contingency fuel for IFR below 5,700 kg. Operator fuel policy includes a 15% contingency fuel.
[12] The operator’s review process involved calculations made by the Chief Pilot where monthly total fuel usage was divided by monthly total tacho time to arrive at an average fuel consumption rate per aircraft. This was then compared to previous figures to determine if the planned fuel rate needed to be adjusted.
[13] International Civil Aviation Organization, 2016, Manual for the oversight of fatigue management approaches, 2nd Edition.