Executive summary
What happened
On 17 March 2023, the pilot of a Cirrus SR22, registered VH-XGR, was conducting a private flight under the instrument flight rules from Southport, Queensland to Bankstown, New South Wales.
During the landing, the aircraft sunk onto the runway and bounced along the runway for about 5 seconds, then rapidly entered a steep climbing turn to the left. Having reached a maximum height of about 40 ft, the bank angle exceeded 90° and the aircraft dropped onto the left wing and nose.
When emergency services arrived at the site, the aircraft was upside down on the grass between the runways. The left wing had detached, and fuel was leaking from the right side. The pilot was strapped in and conscious but confined in the aircraft.
Once the site had been blanketed with fire suppression foam and the aircraft stabilised with step blocks, ambulance personnel were able to attend to the pilot. Rescue personnel stabilised the wreckage and used a reciprocating saw to cut the left side of the inverted fuselage to extricate the pilot.
When the pilot was extricated, their condition suddenly deteriorated they were taken to hospital in a critical condition and later died from injuries sustained in the accident.
During the rescue process the site commander was advised that the aircraft was equipped with a ballistic parachute. A Cirrus-qualified maintenance engineer then attended to render the ballistic system safe from inadvertent activation.
What the ATSB found
In the early stages of a go-around from an unstable landing, the pilot was unable to counter the substantial torque effect associated with high engine power, low airspeed, and high pitch angle, resulting in loss of control and collision with terrain.
The emergency responders were initially unaware that the aircraft was equipped with a ballistic parachute (CAPS) and initiated the recovery of the pilot with the system still armed. By not securing the CAPS, the risk of inadvertent rocket activation and injury was increased.
Cirrus Aircraft provided training, education, and placards to reduce the risk of inadvertent post‑accident actuation of the ballistic parachute (CAPS) rocket and associated injury. However, the training and education had limited reach, and the placards did not clearly communicate the danger or provide access to safety information.
The ATSB also identified an opportunity for Cirrus to enhance the safety benefit of their go-around related training and educational products, especially in regard to the SR22 models that were equipped with relatively high-power engines.
What has been done as a result
Cirrus Aircraft advised that they had enhanced the external CAPS placarding on 2 new models of aircraft (the SF50, and another in development) to align with current American Society for Testing and Materials (ASTM) standards. The SR2X series of aircraft (the SR20, SR22, and SR22T) were certified prior to the implementation of ASTM standards. At the time of writing, Cirrus was reviewing the possibility of enhancing the placard that was certified with SR2X.
During the draft report review process the ATSB sought input from Cirrus as to whether there was an opportunity to enhance the safety benefit of their go‑around training and educational products, especially in regard to the SR22 models that are equipped with relatively high-power engines during the landing phase.
Cirrus did not advise of any associated safety action.
Safety message
A go-around to recover from an unstable landing is more dynamic and presents a greater challenge than a go-around on approach. Although the procedure for go-arounds generally applies to both scenarios, it requires careful application when implemented in the landing phase.
Pilots of single-engine aircraft with relatively high-power engines, such as the Cirrus SR22, need to be aware of the potential for significant torque effect and loss of control associated with high engine power, low airspeed, and high pitch attitude.
The Cirrus Airframe Parachute System (CAPS) is credited with saving a number of lives but also presents a serious post-accident hazard when it has not been deployed and the aircraft is damaged. If the rocket is inadvertently activated, anyone in its path would be seriously or fatally injured. Cirrus Aircraft advises first responders that it is imperative that the presence of an airframe parachute system be identified as early as possible, and the system disabled to make it safer to work around.
The ATSB directs first responders/emergency services and airport operators to the Advisory Guide For First Responders: Cirrus First Responders (cirrusaircraft.com) to provide awareness and reduce the risk of inadvertent post-accident activation of CAPS and to the ATSB webpage ‘Hazards at aviation accident sites’.
Additional safety information is available from the news item ‘Approach aviation accident sites with caution’ released in conjunction with the final report of ATSB investigation report AO-2018-038 and Flight Safety Australia article ‘Beware of the rocket in the wreckage’ published on 7 June 2019.
The investigation
Decisions regarding the scope of an investigation are based on many factors, including the level of safety benefit likely to be obtained from an investigation and the associated resources required. For this occurrence, a limited-scope investigation was conducted in order to produce a short investigation report and allow for greater industry awareness of findings that affect safety and potential learning opportunities. |
The occurrence
On 17 March 2023, the pilot of a Cirrus SR22, registered VH-XGR, was conducting a private flight under the instrument flight rules[1] from Southport, Queensland to Bankstown, New South Wales.
The aircraft departed Southport at 1211 Eastern Standard Time[2] and tracked initially to the south‑west. After a couple of minutes, the pilot turned the aircraft onto a southerly heading for the relatively direct track to Bankstown. The pilot initially climbed the aircraft to FL 180[3] for a couple of minutes then descended to FL 160 for the remainder of the cruise phase of the flight. All of the flight parameters—track, altitude and groundspeed—indicated normal operation.
At 1504 Eastern Daylight-saving Time,[4] the pilot commenced descent and altered track slightly. There were other minor track changes, consistent with air traffic control (ATC) or airspace requirements, as the flight progressed towards visual flight rules (VFR)[5] reporting point Prospect Reservoir (Figure 1).[6]
Figure 1: Sydney VTC extract showing Prospect Reservoir in top left corner and Bankstown Aerodrome in lower middle of image
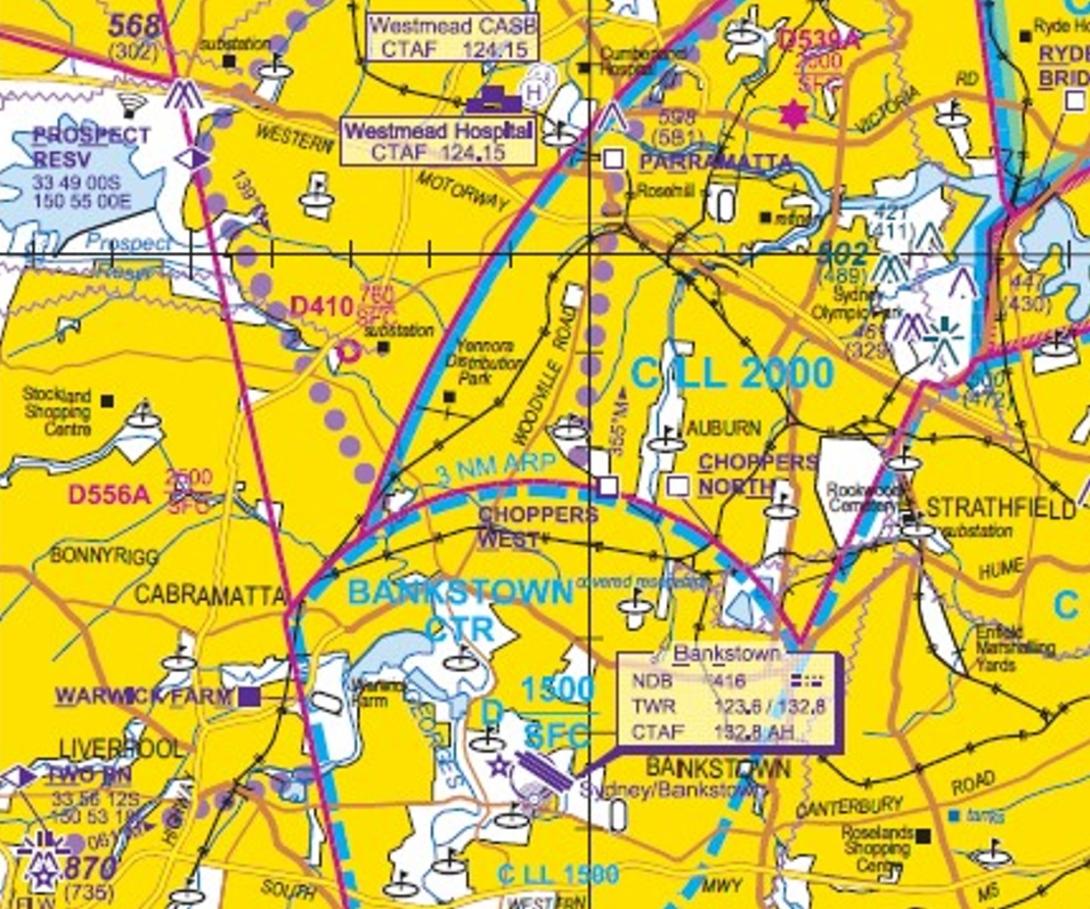
Source: Sydney VTC
At 1533, the aircraft was over Prospect Reservoir on descent through 1,900 ft and tracking towards Bankstown Airport (Figure 2). Shortly after, the pilot transmitted on the applicable Bankstown Tower frequency:
Bankstown Tower, Cirrus xray golf romeo (XGR), Prospect, 1,800, inbound with information November, and visual.
In response, the aerodrome controller (ADC) instructed XGR to:
Join final runway 11 Left[7] and report established at 3 miles. VFR traffic about 2 miles is a Tecnam. If you get a bit too close you can expect runway centre.
This was acknowledged by the pilot of XGR.
About 20 seconds later, the ADC advised XGR:
I’ll make that a plan now, join final for runway 11 Centre. Report established 3 miles. Traffic is that Tecnam ahead.
This was acknowledged by the pilot of XGR.
The ADC passed traffic information to the Tecnam with advice that the Cirrus would be overtaking to the right and to shift slightly to the left. This was followed by some traffic guidance to the pilot of XGR:
XGR suggest a slight right turn, the Tecnam is in about your one o’clock at 1 mile.
This was associated with a diversion of track slightly to the right for a minute and 15 seconds.
The pilot then turned left to align the aircraft for final approach to runway 11C. At this point (1535:19), the aircraft was 2.87 NM (5.3 km) from the runway threshold, slowing down through 106 kt groundspeed, and about to descend from 950 ft.
As XGR was being turned onto finals, the ADC advised:
XGR runway centre number 1. Additional traffic is a Diamond late right downwind in the training circuit [runway 11 Right].
This was acknowledged by the pilot of XGR.
At 1535:45, the ADC advised:
XGR runway centre cleared to land
This was promptly read back by the pilot of XGR:
Cleared to land on centre, XGR
That was the last communication with the pilot of XGR. At that point, XGR was 1.9 NM (3.5 km) from the threshold, on descent through 725 ft, and slowing down through 90 kt groundspeed.
As the approach continued, the groundspeed continued to slow until reaching a groundspeed of 60 kt while on descent through 350 ft. The groundspeed varied between 60 and 63 kts until the last data point recorded at 100 ft.
Figure 2: Track from Prospect reservoir to Bankstown Airport
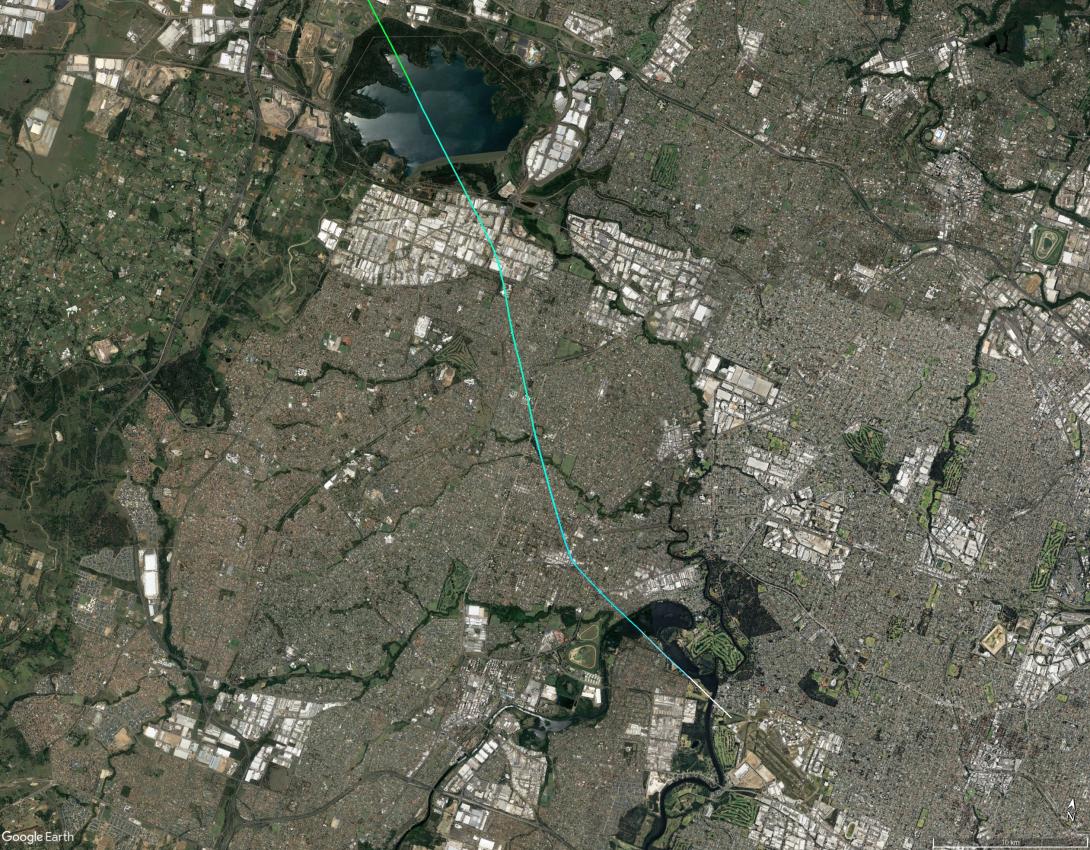
Source: Google Earth, annotated by the ATSB
Although some witnesses noted the speed of the Cirrus was relatively slow, there were no reports of anything abnormal until the landing. The landing was observed by pilots on concurrent approaches to the adjacent runways, and the aerodrome controller. A security camera recorded imagery of the accident sequence.
The instructor in the right seat of the Tecnam (at about 200 ft on final for runway 11 Left) observed the Cirrus touchdown on the runway and bounce into the air to a height of about 10–20 ft. They advised that the aircraft appeared to be very slow, and it bounced again with low energy, with white dust evident from the tail area. It then started to veer to the right, pitched up violently and started to bank steeply to the left (towards runway 11 Left). Concerned about separation, the instructor initiated a go-around. The Cirrus came down on one wing and tumbled onto the roof, stopping quickly.
The instructor in the right seat of the Diamond (on short final for runway 11 Right) observed the Cirrus over the runway in a very high nose attitude and veering right. They advised that it then rolled sharply to the left, dropped the nose, and tracked over the grass between runways 11 Centre and 11 Left. The left wing impacted the ground first, followed by the nose, then flipped over onto the canopy.
The ADC was observing the Cirrus as it was about to touch down. They advised that they saw the aircraft pitch up and reach about 30–40 ft then roll to the left. As the aircraft was crossing over towards runway 11 Left, the ADC issued a safety alert to the Tecnam (1537:38). It appeared to the ADC that the aircraft was accelerating as the left-wing tip impacted the ground followed by the nose.
A camera mounted on the Bankstown Airport passenger terminal[8] recorded low resolution imagery of the accident sequence (Figure 3). It showed the aircraft sinking onto the runway, proceeding along the runway for about 5 seconds, then rapidly entering a steep climbing turn to the left. Having turned through 90° and reached a maximum height of about 40 ft, the bank angle exceeded 90° and the aircraft dropped onto the left wing and nose. This was also recorded by a camera in a different location.
Figure 3: Bankstown Airport terminal CCTV showing sequence from initial touchdown to just before impact (right to left)
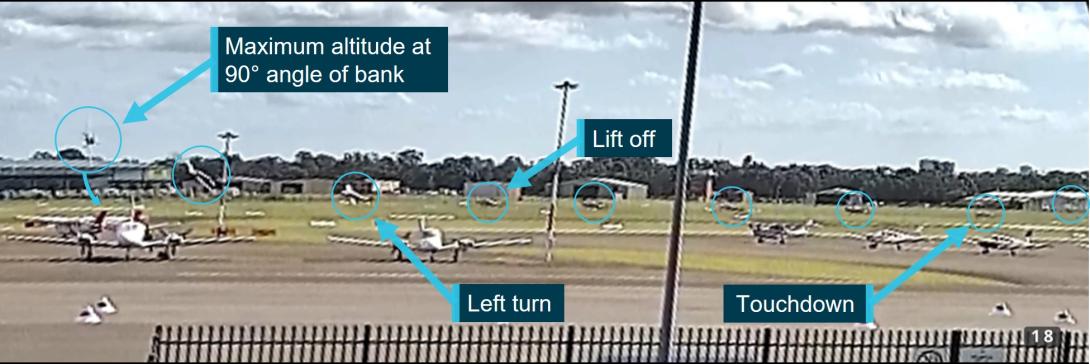
Source: Bankstown Airport edited and annotated by the ATSB
Bankstown Tower activated the aerodrome emergency plan, including notification to emergency services and the aerodrome reporting officer. The airport was subsequently closed, and traffic was processed out of the control zone.
New South Wales (NSW) Police Force personnel arrived within 5–8 minutes of the notification, followed by NSW Ambulance. Fire and Rescue NSW (FRNSW) crews arrived about 8.5 minutes from receiving the call. Bankstown Fire Station crews usually responded to incidents at the airport, but they were unavailable so crews from Revesby Fire Station attended.
When emergency services arrived at the site, the aircraft was upside down on the grass between the runways. The left wing had separated, and fuel was leaking from the right side. The pilot was strapped in and conscious but confined in the aircraft.
The responding FRNSW crews did not include technical rescue personnel, so the site commander arranged for that expertise to attend. Once the site had been blanketed with foam and the aircraft stabilised with step blocks, ambulance personnel were able to attend to the pilot.
Before starting the rescue, the crew strapped the rear fuselage to the ground. They then used a reciprocating saw to cut the left side of the inverted fuselage to extricate the pilot. The FRNSW personnel were unaware of any aircraft type-specific hazards and did not notice any no-cut labels on the aircraft.
When the pilot was extricated, their condition suddenly deteriorated, and they were taken to hospital in a critical condition.
About 15 minutes into the rescue process, the FRNSW site commander was advised that the aircraft was equipped with a ballistic parachute. The commander had a general awareness that a ballistic parachute was installed in the tail but found it difficult to get information about its operation. The airport owner arranged for a Cirrus-qualified maintenance engineer to render the ballistic parachute system, known as the Cirrus Airframe Parachute System (CAPS), safe from inadvertent activation.
The maintenance engineer advised that they inserted a pin into the CAPS activation handle located in the cabin ceiling and taped it into place. They inspected the activation mechanism in the rear cargo compartment and found that the activation cable was not under tension and the rocket igniter switch firing pin had not moved. The electrical wires were not disconnected because of concern about the fuel spillage. On the day after the accident, the engineer disconnected a battery in the tail but, due to aircraft damage, was unable to access an additional battery in the front of the aircraft.
Another Cirrus-qualified maintenance engineer who attended the aircraft the day after the accident advised that there was tension on the activation cable, and it was only marginally lower than the force required to move the pin. To render the CAPS safe for recovery of the wreckage, the engineer cut the activation cable and disconnected the electrical leads from the igniter switch.
The pilot died in hospital on 6 April 2023 from injuries sustained in the accident.
Context
Pilot information
The pilot held a private pilot licence (aeroplane), issued in 2011, with a single engine aeroplane rating. In addition, the pilot held a single engine aeroplane instrument rating and Night VFR rating.
In February 2023, the pilot had recorded total flying experience of 860 hours, including 47 hours in the previous 6 months. Almost all of the total experience and all of the recent experience was reported to be operating VH-XGR.
The last training or check completed by the pilot was an instrument proficiency check (IPC) in VH‑XGR. This was attempted on 8 February 2023 but was not successful. The flight examiner advised that during a hand-flown instrument approach the pilot had allowed the aircraft to descend below the glidepath indication and develop a high rate of descent.
As recommended by the flight examiner, the pilot then conducted some VFR flying (without an instructor) and a pre-IPC practice flight with the flight examiner. On 2 March 2023, the pilot attempted the IPC again with the flight examiner and was successful.
The flight examiner recalled that over the course of the 2 recent IPCs, and associated practice flights, the pilot’s general flying, including circuits and landings, was unproblematic. Although those flights included a number of go-arounds that were safely executed, the flight examiner had discussed with the pilot the need to be cautious when applying power during go-arounds to ensure the aircraft remained easy to control.
The flight examiner had completed the Cirrus Standardised Instructor Pilot training in 2020 and been involved in the pilot’s flying training and assessment during the previous 3 years.
The pilot’s last aviation medical examination, conducted on 28 February 2023, was for a Class 2 medical certificate. This was revalidated by the designated aviation medical examiner with continuation of the restrictions that distance vision correction must be worn and reading correction to be available while flying.
At the time of drafting the report, the postmortem report was not available. However, analysis of the radio transmissions made by the pilot to Bankstown Tower showed that these transmissions were appropriate and there were no indications of any abnormalities—slowed/slurred speech patterns or simple errors—which could indicate a medical issue.
Environmental conditions
The aerodrome forecast for Bankstown Airport issued at 1534 local time anticipated that between 1500 and 1700 the wind would be from 130 degrees (True) at 17 kt, visibility would be greater than 10 km with no cloud, temperature over the same time period was forecast to be 28°. At 1530, the wind was reported from 090 degrees (True) at 16 kts and the other conditions were consistent with the forecast.
Wind speed and direction were recorded at Bankstown airport every minute. Those observations in the 2 minutes before and after the accident are presented in Table 1.
Table 1: One-minute wind observations at Bankstown Airport on 17 March 2023
Local Time | Wind speed (kt) | Wind direction (Degrees True) |
1536 | 16 | 106 |
1537 | 15 | 106 |
1538* | 14 | 099 |
1539 | 17 | 104 |
1540 | 15 | 100 |
*The closest observation to the time of the accident was at 1538. At that time, the angle between runway 11 (111° magnetic) and the recorded wind from the left (086° magnetic) was 25°. That provided a crosswind component of 6 kt from the left and headwind component of 13 kt. There was no significant variation in the minute before or after that time.
Operational information for Bankstown Airport in the En Route Supplement Australia (ERSA) cautioned that:
During winds with a southerly direction, building induced mechanical turbulence may be experienced on final for RWY 11C and RWY 11R/29L.
Although the prevailing wind was not from a southerly direction, the ATSB considered the potential for mechanical turbulence. The closest buildings in line with the direction of the wind were no higher than 3 levels and located at least 900 m from the threshold of runway 11 Centre. Given the wind strength and the distance of the buildings, it is unlikely that the buildings had any significant effect on the conditions for landing on runway 11 Centre.
The instructor in the Tecnam advised that on approach and landing to runway 11 Left there was no significant crosswind or mechanical turbulence, and the conditions were relatively smooth. In addition, the ADC did not notice any disturbance to the flight path of aircraft on approach.
Operating procedures
The Cirrus SR22 Pilot’s Operating Handbook included a procedure for balked landing/go-around:
1. Autopilot .....................................................................DISENGAGE
2. Power Lever ........................................................FULL FORWARD
3. Flaps ........................................................................................50%
4. Airspeed........................................................................75-80 KIAS
After clear of obstacles:
5. Flaps .........................................................................................UP
Amplification
In a balked landing (go around) climb, disengage autopilot, apply full power, then reduce the flap setting to 50%. If obstacles must be cleared during the go around, climb at 80-85 KIAS with 50% flaps. After clearing any obstacles, retract the flaps and accelerate to the normal flaps up climb speed.
Pilot training and operational guidance
Pilot training and assessment
Pilot training and assessing in Australia was carried out in accordance with the CASR Part 61 manual of standards (MOS). The competency standards for the Land Aeroplane unit included elements and performance criteria for conduct of a missed approach and recovery from a missed landing.
For both sequences, the criteria was to make a smooth positively-controlled transition from approach or missed landing to a missed approach including selection of power, attitude and configuration to safely control the aeroplane. The causes of loss of control during landing and contents of the pilot’s operating handbook were part of the underpinning knowledge requirements.
The competency standards for night VFR and instrument approaches included the conduct of missed approaches.
To safely exercise the privileges of a rating, a pilot must have completed a flight review for the rating within the previous 2 years. Once the pilot demonstrated competency in accordance with the Part 61 MOS, the instructor was able to assess it as completed.
An instrument proficiency check (IPC) is an assessment of the pilot’s competency to conduct a flight in actual or simulated instrument meteorological conditions under the IFR to the standards specified in the Part 61 MOS. An IPC included missed approaches in the context of instrument approaches and was valid for 12 months.
Cirrus training and guidance material
Cirrus Aircraft provided an instructor pilot course intended to prepare qualified instructors with SR20/22 experience to provide high-quality standardised training to owner-pilots and students using Cirrus Aircraft-approved resources. The course included the demonstration, teaching, and assessment of landings and go-arounds with an emphasis on flight operations manual (FOM) procedures and use of the TOGA button, and memory items.
Online training and education for pilots was also available through the Cirrus Approach portal. This included the FOM for the SR series aircraft that addressed standard operating procedures applicable to the traffic pattern, stabilised approaches, landings, and go-arounds.
One of the specialty courses was ‘SR series Take-offs and Landings’ and 2 of the shorter presentations hosted on YouTube (Flight Fix) addressed go-arounds and stable approaches.
The following information, selected for relevance to the occurrence, has been adapted from the FOM and online training/education resources.
It was recommended that the autopilot was disconnected prior to entering the traffic pattern (circuit) and the yaw damper was off prior to landing.
For final approach, the target indicated airspeed (IAS) was 80 kt with full flap and engine power as required. One of the common errors on approach was not compensating for ballooning when deploying the flaps, resulting in excessive loss of airspeed and/or altitude gain.
A stabilised approach was defined as constant angle and constant rate of descent approach profile ending near the touchdown point. If this was not achieved, a go-around must be carried out. In addition, a go-around was recommended in situations such as excessive ballooning during landing or excessive bouncing.
A go-around was presented as a 4-part flow comprising:
- Power Up – immediately but smoothly apply full power (as for take-off – typically 4–5 seconds), connected right rudder due to significant left turning tendencies (possible strong pitch up), and simultaneously;
- Pitch Up – smoothly and initially to level attitude and begin accelerating. If the aircraft has a TOGA button and it is pushed, it provides pitch guidance on the primary flight display (PFD)
- Clean Up – retract flaps to 50% then as the aircraft speed increases gently transition to Vx [speed for best angle of climb] or Vy [speed for best rate of climb]. When positive rate of climb and obstacles are cleared above flap retract speed of 80 KIAS, retract flaps to zero
- Call Up – communicate as required.
Common errors included not maintaining coordination during the go-around, and improper pitch control resulting in excessive loss of altitude, stall entry, or both. This could occur if the aircraft was climbed out of ground effect before a safe airspeed was reached.
Landing technique including in a crosswind was conventional. Common errors included the pilot flaring too high and creating a stall to hard landing situation.
Rejected landing and go-around aerodynamics
Engine power changes can affect stability. An increase of power may tend to make the nose rise (low thrust line tends to add to nose-up effect of horizontal tail surface). This effect can be exacerbated with full flap.
In a single-engine propeller-driven aircraft, application of engine power will produce ‘torque’ in the form of a twisting or rotating motion around at least one of the 3 axes. For an aircraft with a clockwise rotating propeller (viewed from the cabin) such as the Cirrus SR22, the overall result will be a left turning tendency. This is the combined effect of 4 elements, which are briefly explained in the context of a clockwise rotating propeller.
Torque reaction: as described by Newton’s Third Law of Physics, the revolution of the engine and propeller in one direction produces an equal force trying to rotate the aircraft in the opposite direction. As this induces a roll to the left when the aircraft is airborne, the design will generally compensate for this tendency in cruise (for example, by an offset engine and by provision of aileron trim). During the take-off roll, the increased loading on the left main wheel produces relatively higher drag and a turning moment to the left. The magnitude of the left roll and turn tendency is dependent on:
- size and power of the engine
- size of propeller and RPM
- size of the aircraft
- condition of the ground surface.
Corkscrew effect: At high propeller RPM and low forward speed, the spiral or corkscrew rotation of the slipstream exerts a sideways force on the vertical fin, which produces a yawing moment to the left. In addition, the corkscrew flow of the slipstream produces a rolling moment to the right around the longitudinal axis. Although these forces may be counteracting each other, they vary greatly and require the pilot to apply the necessary corrective action.
Gyroscopic action: as a spinning rotor, the propeller is subject to gyroscopic precession when a force is applied to the rim of the plane of rotation. In simple terms, any yawing about the vertical axis results in a pitching moment and any pitching around the lateral axis results in a yawing moment.
Asymmetric loading (P-factor): when an aircraft is flying with a high angle of attack, the effectiveness of the downward moving blade is greater than that of the upward moving blade. This moves the centre of thrust to the right, which results in a yawing moment towards the left around the vertical axis.
Aircraft information
General information
The aircraft was manufactured in 2009 by Cirrus Design Corporation in the United States to a GTS equipment specification and with G3 model features such as a redesigned carbon fibre wing. It was registered in Australia as VH-XGR in the same year.
Although produced as an SR22, which was certified with a normally aspirated Continental Motors Inc. IO-550-N engine, the aircraft engine had been modified during manufacture in accordance with a supplementary type certificate. This involved installation of a Tornado Alley Turbo Inc. Turbonormalizing System that was designed to maintain sea-level performance of 310 hp up to the maximum altitude of 25,000 ft. As such, it was referred to as an SR22TN.
One of the features of the aircraft was a single-lever power control that adjusted engine throttle with automatic adjustment of engine speed through a mechanical linkage to the propeller constant speed unit. The system was set to maintain approximately 2,500 RPM at cruise power settings and 2,700 RPM at full power.
The aircraft was also equipped with an oxygen system to allow the pilot to operate over 10,000 ft in the unpressurised cabin. A fingertip oximeter was located in the cabin after the accident.
Conventional flight controls are operated mechanically by a single-handed side control yoke and rudder pedals. Pitch and roll trim was provided through adjustment of the neutral position of a compression spring cartridge by means of an electric motor in each control system. These were intended to allow easy override of full trim or autopilot inputs by using normal control inputs. Pilot control was effected by movement of a conical trim button on the control yoke.
Yaw trim is provided by a spring cartridge in rudder control system that provided a centralising force, regardless of the direction of rudder deflection. This was not adjustable in flight.
Avionics and instrumentation
The aircraft was equipped with the Cirrus Perspective Integrated Avionics System developed by Garmin. Flight instrumentation, position, navigation, communication, and identification information were displayed through a primary flight display (PFD) and a multifunction display (MFD). An automatic flight control system (AFCS) provided flight director, autopilot, yaw damper, and manual electric trim functions.
Indicated airspeed is displayed on the PFD by a moving tape with a rolling number gauge. The colour-coded tape showed the low-speed range as a red strip up to the low-speed awareness velocity (VLSA). An airspeed trend vector in the form of a variable-length magenta vertical line showed the projected indicated airspeed in 6 seconds (for constant rate of acceleration or deceleration). When selected on, V speeds such as Vx (best angle of climb) and Vy (best rate of climb) were displayed next to the airspeed scale.
Key engine parameters are displayed on the left side of the MFD during normal operations, including analogue style power indication (percentage) and numeric values for power, RPM and manifold pressure.
A carbon monoxide detector generated a CO LVL HIGH annunciation when the carbon monoxide level was greater than 50 ppm.
The aircraft was equipped with an electro-pneumatic stall warning system to provide audible warning of an approach to an aerodynamic stall. At approximately 5 kt above the stall (full flaps, power off, level flight) and slightly higher in turning and accelerated flight, a warning horn will sound and a red stall warning annunciation will illuminate.
Electronic stability and protection is an optional feature to discourage exceedance of attitude, airspeed and angle of attack parameters through corrective control pressures. This will only function above 200 ft above ground level and when the autopilot is off.
An aircraft data logger system acquires serial information from the primary integrated avionics unit and transmits it to the recoverable data module located in the vertical stabiliser. The PFD and MFD had the capability to record flight and engine data on SD cards.
Occupant safety features
A composite roll cage within the fuselage structure provided roll protection for all occupants. The lower firewall was designed to improve crashworthiness. The seat bottoms have an integral aluminium honeycomb core designed to crush under impact to absorb downward loads. Integrated seat belt and shoulder harness assemblies with inertia reels were provided for each occupant. The front seats utilised a 4-point inflatable restraint system.
An inflatable shoulder harness is integral to each front seat harness. In the event of a collision, the sensor evaluates the force pulse and sends a signal to an inflator assembly mounted in the aft seat frame. This signal releases the gas in the inflator and rapidly inflates the airbag within the shoulder harness cover.
As is standard for SR series aircraft, the aircraft was equipped with a Cirrus Airframe Parachute System (CAPS). Cirrus Aircraft reported that there had been 124 CAPS Saves (deployments) that resulted in 254 lives saved. CAPS consisted of the following primary components:
- parachute
- solid-propellant rocket to deploy the parachute
- rocket activation handle and cable
- harness embedded in the fuselage structure.
The parachute and rocket were located in a compartment behind the rear baggage compartment. The rocket activation handle was mounted in a cabin ceiling enclosure between the 2 front seats and the cable was routed through the cabin ceiling and angled towards the left side of the CAPS compartment.
To initiate the CAPS, the pilot removes the access cover and pulls the rocket activation handle out and down. Movement of the cable compresses the igniter steel spring and cocks the plunger. When one half-inch of plunger travel is reached, the primary booster is ignited, which then ignites a secondary booster and the rocket motor. For aircraft with electronic ignition for the booster, both aircraft batteries are connected to the system and either can actuate the booster in response to cable movement.
Once ignited, the rocket impacts and dis-bonds the parachute compartment cover situated behind the rear cabin window and pulls the deployment bag from the enclosure. The deployment bag then stages the suspension line deployment and inflation of the parachute.
On the upper fuselage, either side of the CAPS rocket cover was a placard approximately 16.5 cm long (Figure 4).
Figure 4: CAPS Placard
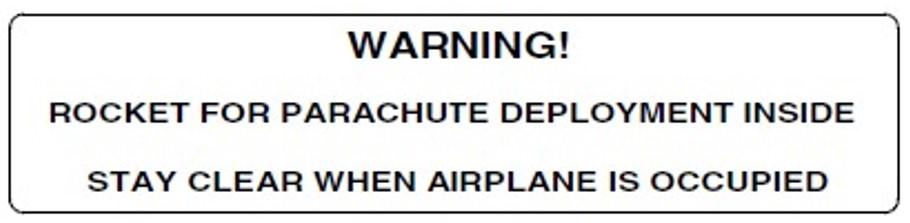
Source: Cirrus SR22 POH
Maintenance
The last 100-hour/annual inspection was completed on 13 January 2023 when the aircraft total time in service was 857.1 hours. According to the aircraft log book, the annual inspection was carried out in accordance with the Cirrus SR22 aircraft maintenance manual and included:
- scheduled inspection of the oxygen system
- scheduled inspection and check of the autopilot servos
- software update to Perspective Avionics
- MFD lower SD card slot and card contacts cleaned (due to supplemental data intermittently unavailable)
- scheduled check of the aircraft data logger system (RDM).
The scheduled check of the aircraft data logger system involved accessing the diagnostic LED and confirming that the rate and duration of the LED blinking indicated normal operation. According to the maintenance organisation, this was carried out with nil defects identified.
The only subsequent maintenance was carried out on 15 March 2023 at 887.1 hours total time in service. In response to pilot concern about uneven EGT burn at altitude, the maintenance organisation checked the magneto timing and found it within limits. And as engine data showed a spark plug irregularity, those plugs were cleaned, tested, and reinstalled.
Cirrus first responder information
The aircraft manufacturer produced a comprehensive Cirrus 1st Responder Information Manual to inform emergency services of the potential hazards they may encounter when working on or around a Cirrus aeroplane at an accident site. This focussed on CAPS and addressed other hazards such as oxygen bottles, airbag seatbelts, and composite materials. The manual and other safety information including a video was available at Cirrus First Responders (cirrusaircraft.com). In addition, Cirrus Aircraft advised that they had trained thousands of first responders in on-site and classroom contexts.
According to the manual, it is imperative that the presence of an airframe parachute system be identified as early as possible when responding to an aviation mishap and the system disabled to make it safer to work around. In certain circumstances it may be advisable to secure an accident site and have a Cirrus trained technician attend to disable or disarm the system prior to proceeding with recovery efforts.
Of particular concern is the activation cable routed through the cabin roof that can be altered or stretched during an accident sequence and/or rescue and recovery. This can occur with the activation handle safety pin inserted. On a diagram of the aircraft, the cable route and parachute compartment were identified as a do not cut zone (Figure 5).
Figure 5: Diagram extracted from Cirrus 1st Responder Information Manual - Activation handle and cable hazards
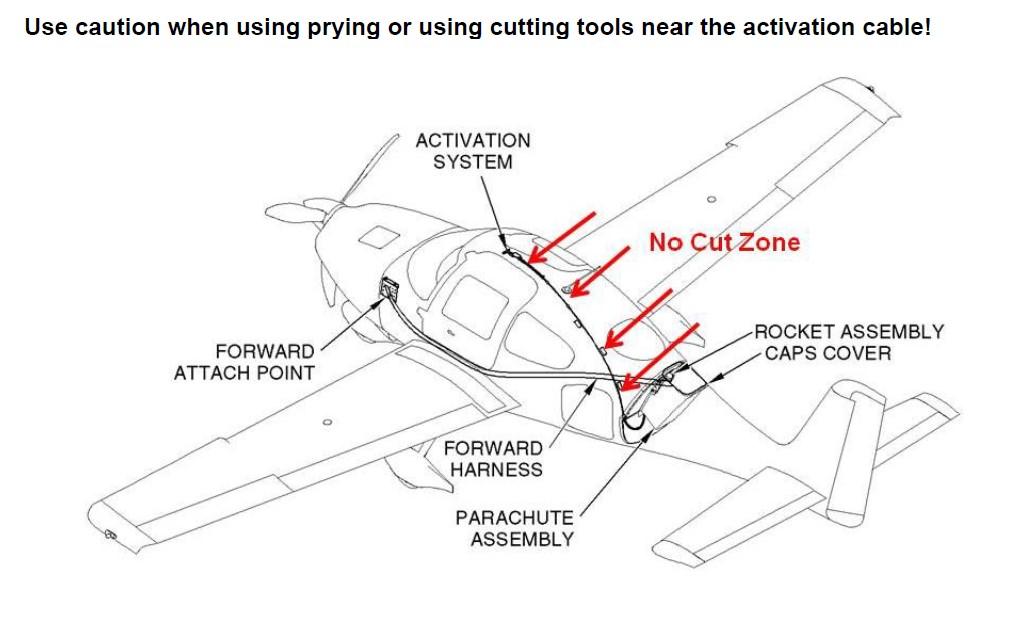
Source: Cirrus 1st Responder Information Manual, Date: July 23, 2018, Revision: 2
If the rocket is launched, it accelerates to over 100 mph (160 kmh) in the first tenth of a second, making it a projectile hazard to anyone in its path. Normal trajectory of the rocket is upward and rearward over the tail but damage to the aircraft and nearby obstacles in the flight path can render the trajectory unpredictable.
For an intact aircraft, CAPS can be secured by inserting a safety pin into the activation handle and handle holder. If an aircraft is not intact, CAPS should be disabled by cutting the activation cable as close to the igniter assembly as practicable (Figure 6). This is a temporary measure that decreases the risk of inadvertent ignition substantially enough to proceed with rescue efforts. Additionally, for an electrically fired system, aircraft batteries can be disconnected, and the igniter wires shunted.
CAPS can be disarmed by trained and authorised technicians, which renders the rocket, igniter, base, and reefing line cutters inert.
In response to ATSB request for data about unintentional post-impact rocket activations, Cirrus Aircraft advised that there was limited data as most of these events were not recorded. A few rocket activations had resulted from exposure to direct flame or heat soaking in post-impact fires.
Figure 6: Image extracted from Cirrus 1st Responder Information Manual showing rear cabin (looking rearward; carpeting and panels removed), warning placard, and cable cutting location
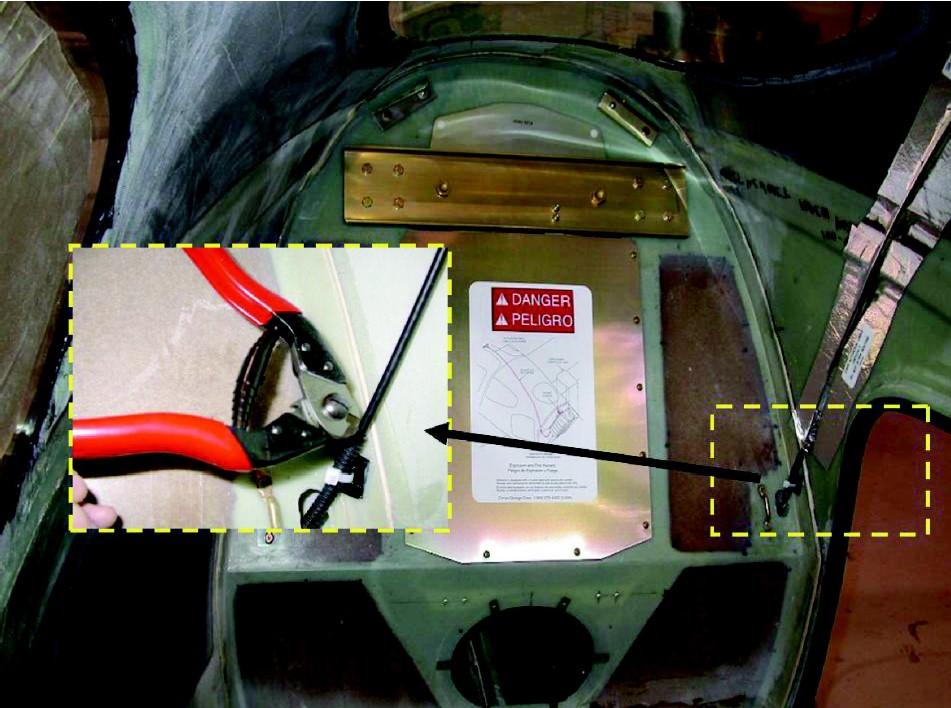
Source: Cirrus 1st Responder Information Manual, Date: July 23 2018, Revision: 2
Accident site and wreckage information
Images of the accident site and wreckage (after recovery of the pilot) were provided to the ATSB. Those images show that the aircraft came to rest on the grass about midway between runway 11 Centre and 11 Left. It was inverted and oriented on the same general heading as the runway.
About 100 m from the threshold of the runway was a white scrape mark on the centreline consistent with a tail strike. A further 230 m along the runway, a series of ground marks started from 30 m to the left of the runway centreline and extended 16 m away from the runway until the main wreckage site. These ground marks were consistent with left wing tip, left wing, and main nose down impact.
The left wing had broken in 2 places and those pieces were detached from the main wreckage at the wing root. The nose of the aircraft was severely damaged, and 2 propeller blades had sheared off at the hub. Although the propeller blades were damaged, there was no plastic deformation that might indicate engine power at impact because the blades were composite material.
Some of the left fuselage was cut away and it is likely there was some alteration to the internal conditions around the pilot’s seat as part of the recovery of the pilot. There was significant intrusion of the instrument panel into the cabin. The cabin space was mostly intact, although there was apparent deformation and reduction of cabin height.
The pilot’s seat was in location but both outboard seat feet had torn the flanges from the outboard seat track at the mid‑seat position due to impact forces and track deformation. The pilot’s seat belt airbags had inflated.
Depending on observer perspective, the CAPS warning placard was visible on the left rear inverted fuselage (Figure 7). Because of the tilt of the wreckage, the right-side placard was not as visible.
Figure 7: Wreckage (inverted) at accident site showing CAPS warning placard on left rear fuselage
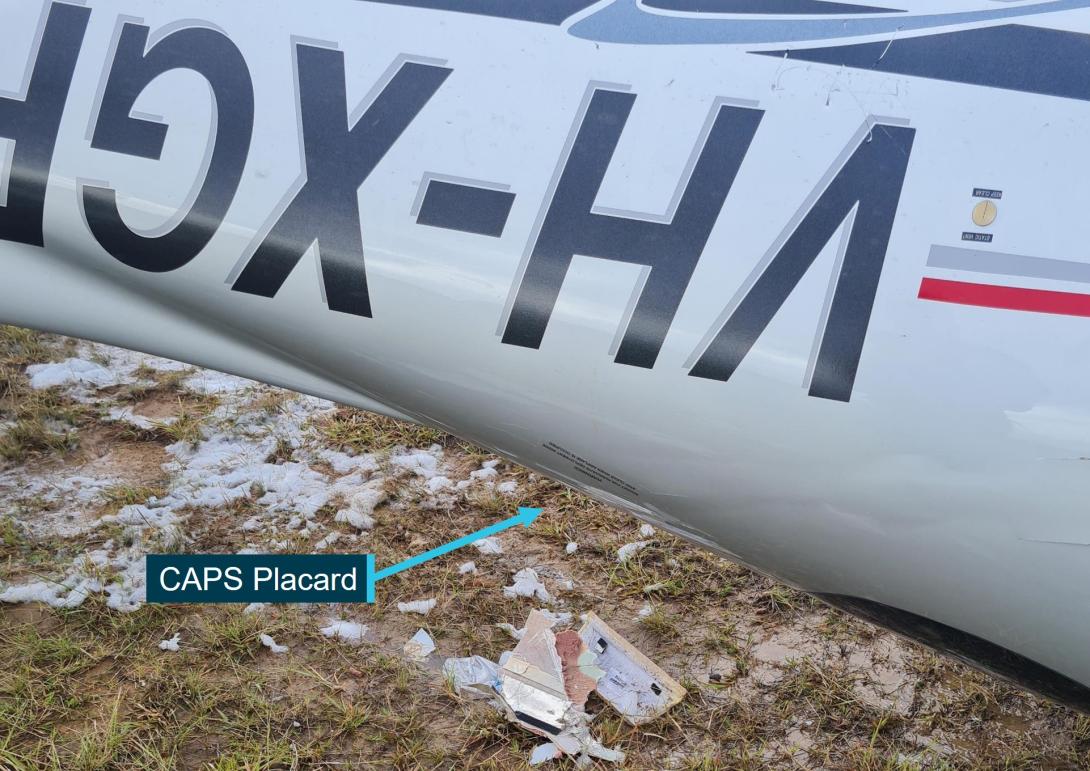
Source: NSW Police (annotated by ATSB)
The ATSB examined the wreckage after it was removed from the accident site and secured in a hangar. By that stage the CAPS rocket had been disarmed and removed.
A search for SD cards located 2 Garmin cards and an SD data card from the MFD. The PFD screen had detached from the instrument panel during the accident and no associated SD card was found. The Garmin cards were not designed to record data and the SD data card was not formatted properly to enable storage of information.
The recoverable data module (RDM) was intact and removed from the vertical fin for data recovery. The ATSB connected to the RDM but was unable to download any data. After consultation with Cirrus Aircraft and the National Transportation Safety Board (NTSB), the RDM was sent to the NTSB data recovery specialists. They confirmed the ATSB nil result then transferred the memory chips to a surrogate RDM. This allowed data to be downloaded but the RDM had not been recording data since at least 2012.
Examination of the aircraft identified that the:
- elevator trim setting was neutral
- wing flap selector was in the 100% down position
- oxygen controller was off but there were indications it had been used.
Fire and rescue
Bankstown Airport did not have an aviation rescue fire fighting facility and it was not a regulatory requirement for that airport. The emergency response to an aircraft accident on Bankstown Airport included Fire and Rescue NSW (FRNSW), which is the State Government agency responsible for the provision of fire, rescue and hazmat services in cities and towns across New South Wales. FRNSW advised that all fire and rescue personnel received the same training and had access to guideline support documents that addressed aircraft incidents including ballistic parachutes. In addition, firefighting crews with an aerodrome/airport as part of their risk profile would be familiar with that environment and take part in emergency exercises.
Flight path information
The ATSB obtained automatic dependent surveillance broadcast (ADS-B) data transmitted from the aircraft’s Mode S transponder during the flight. That data included altitude, indicated airspeed, and rate of descent, and the approximate distance to the runway threshold was derived from aircraft coordinates (Table 2).
Table 2: Selected ADS-B data for final approach
Altitude (ft) | Indicated airspeed (kt) | Rate of descent (ft/min) | Distance to runway (NM) |
500 | 98 | 416 | 1.51 |
400 | 87 | 448 | 1.23 |
300 | 80 | 416 | 0.93 |
200 | 83 | 448 | 0.71 |
100 | 79 | 352 | 0.37 |
50 | 74 | 224 | Not available |
25 | 73 | 384 | Not available |
0* | 71–61 | 416–224 | Not available |
* There were a number of data points around 0 ft altitude so the range of airspeed and rate of descent around the initial touchdown is provided. Cirrus noted that the last recorded airspeeds were low and may have been a factor in the bounced landing and aircraft response in the go‑around.
Based on the derived distance data, from 500 ft the aircraft was close to a 3° descent profile, which became about 2.5° after 300 ft.
In the landing configuration, the stall speed in steady flight was 62 kt (at unfavourable weight and balance conditions).
Other Cirrus SR22 go-around occurrences
AO-2015-110 Collision with terrain involving a Cirrus SR22, VH-OPX, near Moree, New South Wales, on 17 September 2015.
The pilot was landing at a private airstrip 10 km north of Moree. Based on observations at Moree and the runway direction, the wind was a quartering tailwind/crosswind from the right of up to 20 kt with small gusts up to 22 kt.
After a normal approach and extension of full flap, the pilot commenced the flare for landing at about 80–90 kt. To align the aircraft with the runway, the pilot reported applying almost full left rudder and right aileron due to the crosswind. The right main landing gear touched down first, and the aircraft bounced back into the air. The pilot immediately applied full power to initiate a go‑around. However, the left wing dropped and the aircraft yawed to the left. The aircraft’s left wing and propeller then collided with a dam wall. The aircraft stopped abruptly and spun around. The engine separated from the aircraft and came to rest about 20 m away, the tail broke off and the nose landing gear collapsed. The pilot suffered minor injuries, and the aircraft sustained substantial damage.
AO-2018-038 Loss of control and collision with terrain involving Cirrus SR22, VH-PDC, at Orange Airport, New South Wales, on 15 May 2018.
The pilot (aircraft owner) and flight instructor were conducting night circuits as the first part of training for a night endorsement. Wind conditions were reported as light and variable.
On the second approach, the pilot flared the aircraft a ‘little high’ for the touchdown, and the aircraft bounced twice. The pilot elected to go-around and applied full power before touching down again. The ATSB report identified that as the pilot applied full power to perform the go-around, the aircraft pitched nose-up and rolled to the left.
This report also identified 2 other accidents involving SR22 go-arounds in the United States where the aircraft nose pitched up and the aircraft veered left after full power was applied to the engine. (Report ERA12FA540, and Report NYC07CA010)
Previous CAPS hazard safety action
In the past, the ATSB produced a publication Hazards at Aviation Accident Sites: Guidance for Police and Emergency Personnel which was distributed as a booklet. The printed version is no longer available and at the time of writing the investigation report, a pdf copy was available while a digital version was under development.
When the final report for AO-2018-038 was released the ATSB released a news item with a safety message about the risks associated with post-impact deployment of the CAPS rocket. Flight Safety Australia magazine, produced by CASA, also published an article warning readers to beware of the rocket in the wreckage.
Safety analysis
Attempted landing and loss of control
En route, approach and landing
The flight path from Southport to final approach at Bankstown was steady with no indication of problems and there was no report of any anomalies regarding radio transmissions. Given the oxygen system was used, there is low risk that the pilot was exposed to hypoxia when operating above 10,000 ft.
After reporting inbound at Prospect Reservoir in accordance with standard procedures, the pilot responded appropriately to controller advisories. When the pilot acknowledged the clearance to land, which was the last transmission from the pilot, there was no discernible indication of any stress or impairment.
After joining final approach at 950 ft, the pilot maintained a direct, steady track to the runway and the descent profile was close to a standard 3° approach profile. Although some witnesses reported the aircraft speed was slower than expected on approach, the transmitted data indicated that the aircraft was at the Cirrus‑recommended approach speed of 80 kt (indicated airspeed) by 300 ft. Based on the flight data, the approach was consistent with the Cirrus stabilised approach criteria.
Below 100 ft, the airspeed reduced to between 71 and 61 kt but given the fidelity of the data it is not possible to establish the speed at the initial touchdown or subsequently. As Cirrus indicated, low airspeed just before landing may have been a factor in the occurrence.
In the CCTV imagery, the aircraft appeared to sink onto the runway and witnesses observed the aircraft bounce along the runway. After the initial bounce, the aircraft tail scraped on the runway, which was symptomatic of the unstable landing without any effect on the subsequent controllability of the aircraft.
Although there was a crosswind component, it was well within the capability of the aircraft and expected to be within the capability of the pilot. There was also no indication from the aerodrome forecast and observations, or from other pilots on approach to adjacent runways, of any significant wind gusts or turbulence affecting the landing.
Landings are dynamic, skill-based manoeuvres that rely on pilot judgement of existing and projected energy state with sensitive adjustment of aircraft attitude and engine power. The unstable landing was consistent with a misjudged flare. Pilots can recover by adjusting the aircraft energy and attitude for another attempt to land or by initiating a go-around.
Loss of control
About 5 seconds after the initial touchdown, the aircraft came off the ground and immediately rolled into a climbing steep left turn up to a height of about 40 ft then dropped and impacted the ground on the left wing and nose.
As there was no recorded flight or engine data, there was no direct information about the engine power settings during the accident sequence. The pilot did not transmit his intentions however, in the context of landing difficulties and trying to control the aircraft, a radio call would not be expected.
Based on the CCTV and witness information, the performance of the aircraft as it lifted off and entered the climbing turn was consistent with high engine power. It follows that the pilot had intentionally initiated a go-around as recovery from the unstable landing.
A mild pitch up would be expected in the early stages of go-around from a bounced landing to maintain ground clearance. However, the large pitch up that was observed was not consistent with the recommended go-around procedure to pitch up to a level attitude and begin accelerating to the speed consistent with either Vx (best angle of climb) or Vy (best rate of climb). It is likely that application of high engine power exacerbated the effects of nose-up control inputs. The Cirrus SR22 is equipped with a relatively high-power engine for a 4-place aircraft. Although turbo‑normalising the engine does not increase the maximum rated power of the engine, it was reported that there could be a noticeable ‘surge’ as the throttle was advanced on the ground.
Application of high engine power will produce ‘torque’ that will result in a strong left turning tendency. This effect is magnified by low airspeed and a high pitch angle. The rate of throttle control movement and engine response will also influence torque characteristics and associated controllability.
In normal operational contexts where high or full engine power is applied at the recommended rate, the pilot is able to counteract torque effect through coordinated use of steering (on the ground), and use of rudder and aileron once airborne. However, in this case, the torque effect was probably stronger than experienced during normal operation and the effectiveness of the flight controls was compromised by the low airspeed. Consequently, the pilot lost directional control of the aircraft early in the go-around sequence and was unable to recover.
As the angle of bank increased in the turn away from the runway, the stall speed increased, and the vertical component of lift generated by the wings decreased to zero as the aircraft reached a 90° angle of bank. Consequently, the aircraft dropped out of the turn.
The ATSB investigated 2 previous Cirrus SR22 go-around accidents at Moree in 2015 and Orange in 2018. Although the reports identified other factors that played a role in those occurrences, it is likely that torque effect played a key role in each loss of control.
To summarise: In the early stages of a go-around from an unstable landing, the pilot was unable to counter the substantial torque effect associated with high engine power, low airspeed, and high pitch angle. As a result, when the aircraft came off the ground, it rolled into a climbing steep left turn up to a height of about 40 ft then dropped and impacted the ground on the left wing and nose.
Go-around safety considerations
A go-around is a transition from a low-power condition while descending/landing to a high-power climb. When this occurs during an approach, the aircraft has potential and kinetic energy and in visual conditions there is generally no urgency to carry out the procedure. In contrast, when a pilot does a go-around from an attempted landing, the aircraft is in a low energy state and there is typically some urgency to initiate the procedure to recover from an unstable state on or close to the ground.
Flight training and reviews include go-arounds and the pilot had recently completed an instrument proficiency check that included missed approaches. As this check, and the preceding attempted check with associated training, was carried out by a Cirrus Standardised Instructor Pilot in the pilot’s SR22, the pilot was familiar with the type-specific characteristics of missed approaches. The instructor had also conducted practice go-around sequences at safe altitudes with the pilot.
This training and assessing is essential but has an inherent limitation because it is not feasible to simulate the conditions experienced during recovery from an unstable landing. It is possible that the pilot had not previously encountered a go-around from a rejected landing and was not prepared for the aircraft response to engine power in that context.
The balked landing/go-around procedure in the POH specified a sequence of 5 actions/parameters. Although this was applicable to all phases of flight, it did not provide any guidance for conduct of the procedure in different conditions.
To supplement the POH, Cirrus produced a flight operations manual and training videos that addressed approach, landing, and go‑arounds in SR20/22 aircraft. These resources provided useful guidance that was oriented to go‑arounds during final approach. It is not known if the pilot had referred to the guidance in the flight operations manual and there was no record of the pilot having directly accessed training videos for go-arounds, although some videos were freely available without a subscription.
The Cirrus procedure and the more detailed flow for go-arounds was conventional and applicable to the occurrence scenario with careful implementation from memory so control could be maintained during the recovery and transition into a climb. However, the ATSB noted that the material provided by Cirrus did not highlight the risk of loss of control associated with a go-around during the landing phase, where there was high engine power, low airspeed, and high pitch attitude.
CAPS hazard
Cirrus Aircraft advised that 254 lives have been saved due to the CAPS system. However, notwithstanding the benefits, CAPS also presents a serious post-accident hazard when it has not been deployed and the aircraft is damaged. If the rocket is inadvertently activated, anyone in its path would be seriously or fatally injured.
Cirrus Aircraft had been actively managing this risk by providing training to first responders (in the United States) and producing a detailed manual for first responders that is freely available on a dedicated website. In Australia, the ATSB has published and distributed a booklet for emergency services that addressed the risk of ballistic parachute systems in various aircraft types, including the Cirrus SR20/22. After the Cirrus SR22 accident at Orange in 2018 when the rocket was activated by the post-impact fire, the ATSB produced a video about the CAPS hazard and Flight Safety Australia magazine published a related article.
The only external indication of the CAPS hazard on the aircraft is a warning placard either side of the rocket exit point. These are not prominent and did not feature symbology or colour that are recognised indicators of danger. In addition, there are no markings to identify the no-cut area associated with the activation cable. On this occasion, the placards were not easy to identify or read because the aircraft was inverted.
Despite the availability of online guidance for first responders to a Cirrus aircraft accident, placards on the aircraft, and RFNSW training/education, the emergency services site commander was not aware of the presence of the airframe parachute system until advised after the rescue had started. At that point, while the site commander was aware of the rocket hazard, they did not know how to access information about the activation mechanism and method to secure the system. All first responders from FRNSW should have an awareness that aircraft might be equipped with a rocket propelled parachute system and the associated risks but it is not feasible for them to have type‑specific knowledge.
As the accident was at a major general aviation airport on a weekday and during standard working hours, there were aircraft maintenance personnel with knowledge of Cirrus aircraft that were available to assist with securing of the CAPS. They informed emergency personnel about the activation mechanism and secured the handle, which helped to reduce the risk of rocket activation. The risk could have been reduced further if the system had been secured by cutting the activation cable and, if the conditions had allowed, disconnection of the 2 batteries.
If the rocket had been inadvertently activated while the fuselage was inverted, the path of the rocket would have been uncertain and the release of heat and energy in the presence of fuel would have been a significant fire risk.
Cirrus advised first responders that it is imperative that the presence of an airframe parachute system be identified as early as possible, and the system disabled to make it safer to work around. In support of these imperatives, Cirrus provided training, education, and aircraft placards. However, the ATSB considered that the training and education had limited reach, and the placards did not effectively communicate the danger or provide access to safety information.
The ATSB considered that these limitations increased the risk of injury during the recovery of the pilot in this occurrence. Given no recorded incidents of post-impact rocket activations unrelated to fire, and the variability of aircraft accidents and associated damage, the ATSB did not identify this as a safety issue. Nevertheless, the ATSB supports any enhancement to the post-accident identification of CAPS and disabling of the system to reduce the risk of injury.
Findings
ATSB investigation report findings focus on safety factors (that is, events and conditions that increase risk). Safety factors include ‘contributing factors’ and ‘other factors that increased risk’ (that is, factors that did not meet the definition of a contributing factor for this occurrence but were still considered important to include in the report for the purpose of increasing awareness and enhancing safety). In addition, ‘other findings’ may be included to provide important information about topics other than safety factors. These findings should not be read as apportioning blame or liability to any particular organisation or individual. |
From the evidence available, the following findings are made with respect to the loss of control and collision with terrain involving Cirrus Design Corporation S22 at Bankstown Airport, New South Wales on 17 March 2023.
Contributing factor
- In the early stages of a go-around from an unstable landing, the pilot was unable to counter the substantial torque effect associated with high engine power, low airspeed, and high pitch angle. As a result, when the aircraft came off the ground, it rolled into a climbing steep left turn up to a height of about 40 ft then dropped and impacted the ground on the left wing and nose.
Other factors that increased risk
- The first responders were initially unaware that the aircraft was equipped with a ballistic parachute (CAPS) and initiated the recovery of the pilot with the system still armed. By not securing the CAPS, the risk of inadvertent rocket activation and injury was increased.
- Cirrus Aircraft provided training, education, and placards to reduce the risk of inadvertent post‑accident actuation of the ballistic parachute (CAPS) rocket and associated injury. However, the training and education had limited reach, and the placards did not clearly communicate the danger or provide access to safety information.
Safety actions
Whether or not the ATSB identifies safety issues in the course of an investigation, relevant organisations may proactively initiate safety action in order to reduce their safety risk. The ATSB has been advised of the following proactive safety action in response to this occurrence. |
Safety action by Cirrus Aircraft
Cirrus Aircraft advised that they have enhanced the external CAPS placarding on 2 new models of aircraft (the SF50, and another in development) to align with current American Society for Testing and Materials (ASTM) standards (Figure 8). The SR2X series of aircraft (the SR20, SR22, and SR22T) were certified prior to the implementation of ASTM standards. At the time of writing, Cirrus was reviewing the possibility to enhance the placard that was certified with SR2X.
Figure 8: Example of an ASTM Standard CAPS Placard used on the SF50 Vision Jet
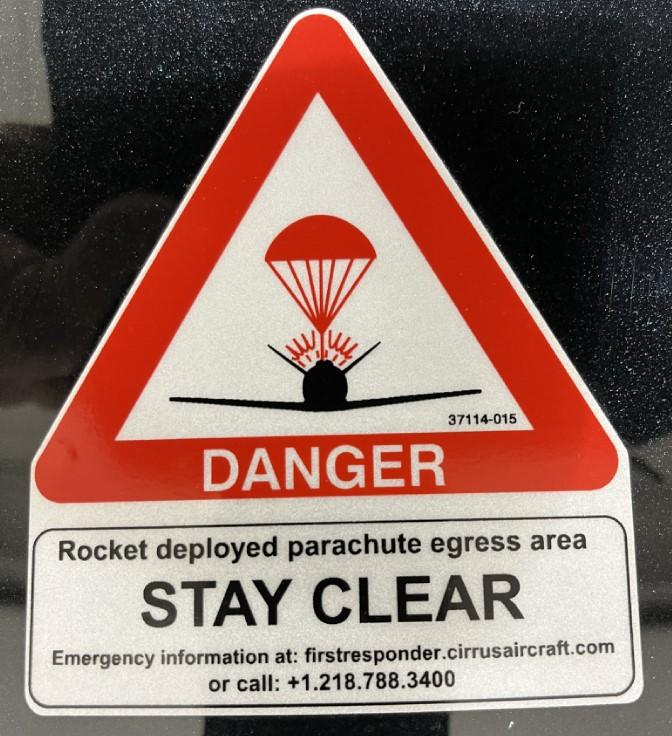
Source: Cirrus Aircraft
During the draft report review process the ATSB sought input from Cirrus as to whether there was an opportunity to enhance the safety benefit of their go‑around training and educational products, especially in regard to the SR22 models that are equipped with relatively high-power engines during the landing phase.
Cirrus did not advise of any associated safety action.
Sources and submissions
Sources of information
The sources of information during the investigation included:
- the aerodrome controller
- accident witnesses
- the New South Wales (NSW) Police Force
- the Fire and Rescue NSW onsite commander
- Aeria Management Group (Bankstown Airport)
- Airservices Australia
- Civil Aviation Safety Authority
- the flight examiner
- Cirrus Aircraft
- the maintenance organisation for VH-XGR
References
Pilot’s Handbook of Aeronautical Knowledge FAA-H-8083-25C
Submissions
Under section 26 of the Transport Safety Investigation Act 2003, the ATSB may provide a draft report, on a confidential basis, to any person whom the ATSB considers appropriate. That section allows a person receiving a draft report to make submissions to the ATSB about the draft report.
A draft of this report was provided to the following directly involved parties:
- aerodrome controller
- Fire and Rescue NSW onsite commander
- Aeria Management Group (Bankstown Airport)
- Civil Aviation Safety Authority
- Flight examiner
- Cirrus Aircraft
- maintenance organisation for VH-XGR
Submissions were received from:
- Civil Aviation Safety Authority
- Cirrus Aircraft
The submissions were reviewed and, where considered appropriate, the text of the report was amended accordingly.
Purpose of safety investigationsThe objective of a safety investigation is to enhance transport safety. This is done through:
It is not a function of the ATSB to apportion blame or provide a means for determining liability. At the same time, an investigation report must include factual material of sufficient weight to support the analysis and findings. At all times the ATSB endeavours to balance the use of material that could imply adverse comment with the need to properly explain what happened, and why, in a fair and unbiased manner. The ATSB does not investigate for the purpose of taking administrative, regulatory or criminal action. TerminologyAn explanation of terminology used in ATSB investigation reports is available here. This includes terms such as occurrence, contributing factor, other factor that increased risk, and safety issue. Publishing informationReleased in accordance with section 25 of the Transport Safety Investigation Act 2003 Published by: Australian Transport Safety Bureau © Commonwealth of Australia 2024 ![]() Ownership of intellectual property rights in this publication Unless otherwise noted, copyright (and any other intellectual property rights, if any) in this report publication is owned by the Commonwealth of Australia. Creative Commons licence With the exception of the Coat of Arms, ATSB logo, and photos and graphics in which a third party holds copyright, this publication is licensed under a Creative Commons Attribution 3.0 Australia licence. Creative Commons Attribution 3.0 Australia Licence is a standard form licence agreement that allows you to copy, distribute, transmit and adapt this publication provided that you attribute the work. The ATSB’s preference is that you attribute this publication (and any material sourced from it) using the following wording: Source: Australian Transport Safety Bureau Copyright in material obtained from other agencies, private individuals or organisations, belongs to those agencies, individuals or organisations. Where you wish to use their material, you will need to contact them directly. |
[1] Instrument flight rules (IFR): a set of regulations that permit a pilot to operate an aircraft in instrument meteorological conditions (IMC), which have much lower weather minimums than visual flight rules (VFR).
[2] Eastern Standard Time (EST): Coordinated Universal Time (UTC) + 10 hours.
[3] Flight level: at altitudes above 10,000 ft in Australia, an aircraft’s height above mean sea level is referred to as a flight level (FL). FL 180 equates to 18,000 ft.
[4] Eastern Daylight-saving Time (EDT): Coordinated Universal Time (UTC) + 11 hours.
[5] Visual flight rules (VFR): a set of regulations that permit a pilot to operate an aircraft only in weather conditions generally clear enough to allow the pilot to see where the aircraft is going.
[6] An IFR flight can change to a VFR flight for the arrival to Bankstown Airport to enable sequencing with VFR traffic operating in the airspace.
[7] Runway number: the number represents the magnetic heading of the runway. The runway identification may include L, R or C as required for left, right or centre.
[8] The distance from the airport terminal to the threshold of runway 11 Centre was 600 m and the distance to the accident site was 350 m.