Executive summary
What happened
On 3 November 2022, a Robinson Helicopter Company R44 Raven I helicopter, registered VH‑OCL was departing a cultural heritage site in the Collier Ranges, Western Australia, with 1‑pilot and 3 passengers on board. During the take-off, just above treetop height and at a speed of about 27 kt, the pilot experienced a severe drop in the helicopter’s performance and the low rotor RPM warning horn sounded.
The pilot conducted the low rotor RPM recovery actions but was unable to arrest the descent. The helicopter collided with terrain and rolled onto its left side about 150–200 m from its take-off point. The pilot and 2 passengers received minor injuries. One passenger received serious injuries and the helicopter was substantially damaged.
What the ATSB found
The helicopter was operating at a high density altitude and although the pilot had expected to be near to, but below, the maximum gross weight, the helicopter was likely to have exceeded the maximum gross weight. This was a result of the pilot not obtaining actual passenger weights, instead using estimated figures. These figures were not provided directly by the passengers.
The pilot had completed performance calculations prior to commencing the day’s flying, but they did not review or recalculate the helicopter’s performance using the actual conditions at the time of the accident flight.
Density altitude and weight are known factors which affect helicopter performance. In addition, the helicopter was operating from a relatively confined area which did not allow the pilot to maintain the recommended take-off profile. As there were no indications of an engine failure or malfunction, it is likely that the power required was more than the power available for the gross weight and conditions at the time. This was coincident with the pilot commencing the climb and transitioning out of ground effect. This likely led to rotor overpitching, where the rotor blade angle of attack is too high, creating so much drag that the available engine power is not sufficient to maintain the required rotor RPM.
The ATSB also identified that the flight should have been operated under the Part 133 air transport operations as it was a passenger carrying flight and not an aerial work operation. The operator was only authorised for aerial work operations.
What has been done as a result
The operator immediately paused all operations to undertake debriefing and discussions on the incident with all company pilots. They also engaged an independent auditor to review their operations.
Prior to commencing their following year’s operations, the operator conducted induction and familiarisation training, which included an independent examiner to conduct proficiency checks and flight reviews for all pilots to ensure competency on all operations and emergency procedures. Further, the operator reported that passenger carrying operations would require Head of operations clearance to proceed.
Safety message
Helicopter pilots should remain cognisant of the importance of accurate figures when calculating weight and balance and expected performance, especially when operating at full capacity and near the maximum gross weight. This, combined with local conditions including high density altitudes, affects helicopter performance and can result in reduced safety margins. This is critical for confined area operations where the physical characteristics of the landing site may limit the options available to the pilot in the event of an unanticipated loss of performance during critical phases of flight, such as the subsequent take-off.
Pilots should review their plans often and when necessary, amend those plans, including by reducing passenger numbers, to ensure that their proposed operations can be conducted safely.
The investigation
Decisions regarding the scope of an investigation are based on many factors, including the level of safety benefit likely to be obtained from an investigation and the associated resources required. For this occurrence, a limited-scope investigation was conducted in order to produce a short investigation report, and allow for greater industry awareness of findings that affect safety and potential learning opportunities. |
The occurrence
On 3 November 2022, a Robinson Helicopter Company R44 Raven I helicopter, registered VH‑OCL was operated by C.A. Helicopters from an airfield at Abra mine camp (Abra) to transport a survey team of 7 people to a cultural heritage site in the Collier Ranges, Western Australia (Figure 1). Commencing at about 0730 local time, the pilot transported 3 passengers at a time to a small clearing near the cultural site, which was about a 40 minute flight. The last flight with the final team member arrived at about 1300, after which the whole group remained at the site for lunch.
Figure 1: Accident site location
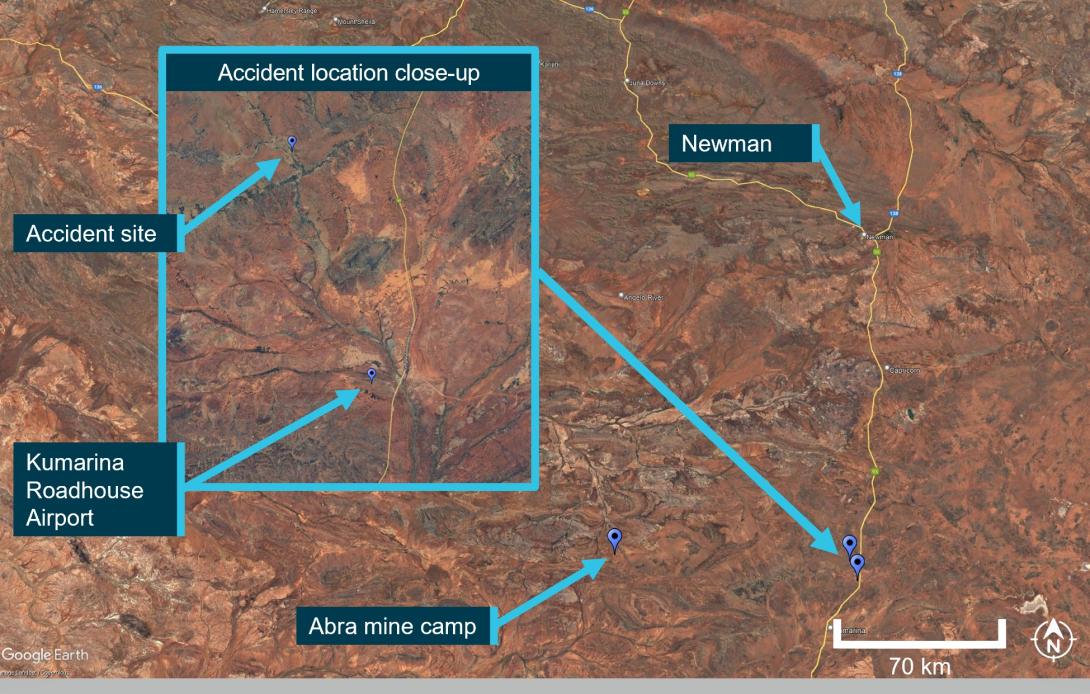
Source: Google Earth, annotated by the ATSB
At about 1340 the helicopter lifted from the site with the pilot and 3 passengers on board for the first return flight to Abra. After lift-off, the pilot was satisfied with the helicopter’s performance in the hover and continued the take-off in a north-easterly direction, towards a nearby gap in the tree line that was about 10 ft high and at least one helicopter’s length away from the take-off point. The pilot reported there was a short level segment before the climb commenced, and that just above the treetop height, at a speed of about 27 kt, the pilot experienced a ‘severe’ drop in the helicopter’s performance and the low rotor RPM warning horn sounded. The pilot did not recall any abnormal indications prior to the warning horn.
The pilot reported lowering the collective[1] and attempting to increase airspeed and rotor RPM, which initially extinguished the low rotor RPM horn for a brief time before the horn reactivated. They continued the recovery actions but realised that the rotor RPM had decayed beyond recovery. At that point, the helicopter was over rough, rocky ground in a gorge and the pilot flew the helicopter towards some trees in an attempt to cushion the emergency landing.
The pilot was not able to arrest the descent and the helicopter collided with terrain and rolled onto its left side (Figure 2) about 150–200 m from its take-off point. The pilot received minor injuries but was able to exit the helicopter and assist the 2 rear seat passengers’ exit. The 2 rear seat passengers received minor injuries. The passenger in the front left seat was seriously injured and not able to exit the helicopter unassisted. The remaining 4 survey team members arrived at the helicopter and assisted the pilot to retrieve the trapped passenger. The helicopter was substantially damaged.
Figure 2: VH-OCL
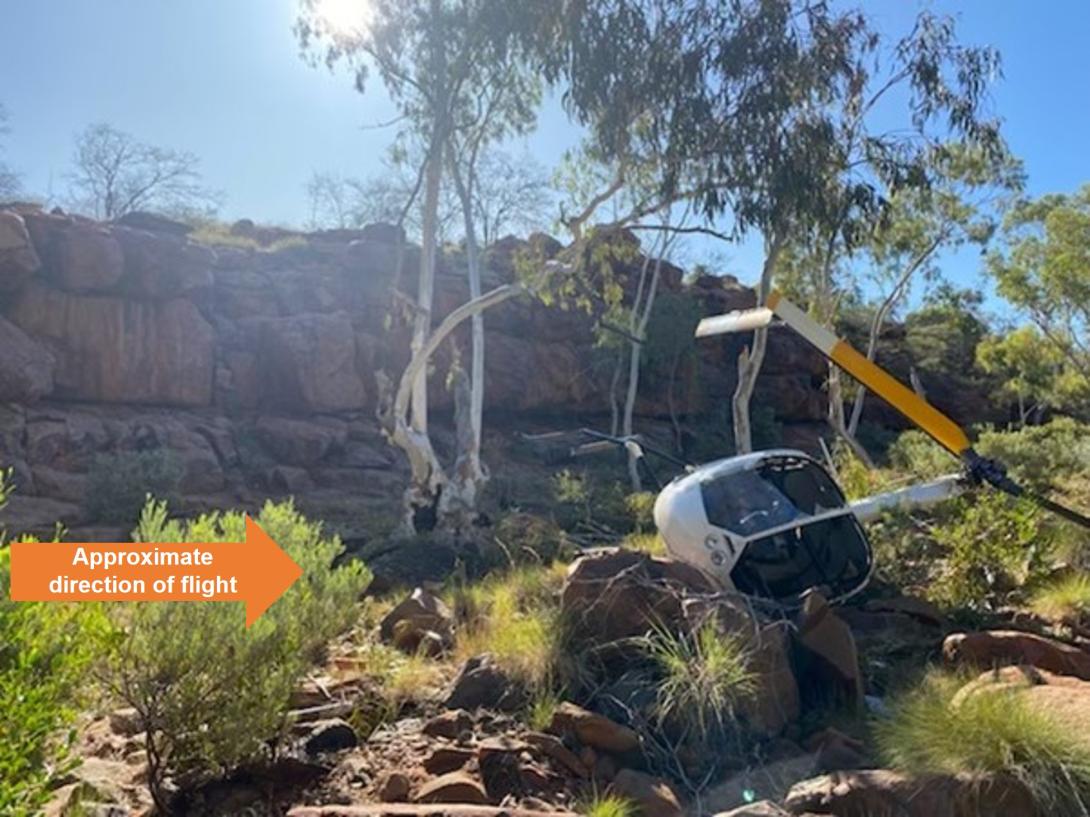
The helicopter approached the gorge from the left of the picture prior to the collision with terrain.
Source: Operator, annotated by the ATSB
Context
Pilot information
The pilot held a Commercial Pilot Licence (Helicopter) and a Class 1 Aviation Medical Certificate, valid until February 2023 with a requirement to wear distance vision correction while flying. Their last flight review was in an R44 in February 2021, and they had completed a proficiency check with the operator in an R22 in April 2022.
At the time of the accident the pilot had accumulated 1,824 hours aeronautical experience, of which 66.7 hours were on the R44 type helicopter, the remaining hours were on the R22. With the exception of the positioning flight the day prior and the flights on the morning of the accident, the pilot had not flown an R44 since March 2022 (about 8 months prior).
The pilot reported they had 3 days off duty in the previous 4 days and felt well rested on the day of the accident. The pilot started work at 0700 and had flown 7 flights (approximately 3 hours 30 minutes in total) to transport the survey team and refuelling. The pilot reported that after completion of the 7 flights they were not feeling any effects of fatigue.
Aircraft information
VH-OCL was a 4-seat Robinson Helicopter Company R44 Raven I helicopter, serial number 2027, powered by a Textron Lycoming O-540-F1B5 6-cylinder piston engine. It was manufactured in 2009 and registered in Australia the same year. The helicopter was maintained in accordance with the manufacturer’s maintenance schedule, which required a periodic inspection every 100 hours or 12 months, whichever came first. The last periodic inspection had been completed on 23 October 2022 with the current maintenance release issued at that time. The helicopter had accrued about 5 hours since the periodic inspection and about 2,860 hours total time in service at the time of the accident. There were no outstanding defects noted in the maintenance release.
The helicopter was being operated with both forward doors removed at the time of the accident, as permitted by the R44 pilot’s operating handbook.
Meteorological conditions
The accident site and take-off point elevation was about 2,170 ft above mean sea level. Bureau of Meteorology (BOM) analysis concluded that winds in the area were likely to have been light, possibly moderate, and south-east to north-easterly. There were no significant weather phenomena forecasted or reported. However, the BOM analysis concluded that it was possible for moderate turbulence with thermals or dust devils to develop. At around the time of the accident, Newman Airport (approximately 145 km NNE of the accident site) recorded a temperature of 30 °C and south easterly winds at 8 kt. Degrussa Airport (approximately 105 km SSE of the accident site) recorded 29 °C with easterly winds at 5 kt.
The pilot said they had reviewed the weather via the BOM website prior to commencing the day’s flying and did not have any concerns with the forecasted weather. They recalled that temperatures were cooler during their first two departures from the survey site that morning, which they estimated were in the mid-twenties. At the time of the accident, the pilot recalled that the winds were easterly with a temperature of about 29 °C.
Using the forecast area QNH[2] of 1017 hPa, the ATSB determined the helicopter was operating at a pressure altitude of 2,050 ft and a density altitude of 4,210 ft.
Weight and balance
Prior to the accident flight, the pilot determined that their heaviest take-off weight would be 2,378 lb (1,078.6 kg), which was 22 lb (10 kg) under the maximum take-off weight for the R44 of 2,400 lb (1,088.6 kg). This included the pilot, 3 passengers and a maximum of 90 L of fuel which the pilot calculated was sufficient to fly one way with the required reserve fuel.[3]
The company operations manual required actual weights to be used in determining weight and balance. By weighing all occupants, equipment and baggage accurate weights could be used to determine performance. On the day of the accident, estimated weights of all the passengers provided by one of the survey team members was used by the pilot, with an additional total allowance of 22 lb (10 kg), per person for any personal items. These estimates were not directly obtained from each of the passengers, but rather derived by a description of each passenger by a survey team member and then conservatively adjusted by the pilot. The pilot recalled that their worst case weight and balance scenario would allow any combination of passengers that would be carried that day to remain within weight and balance limits.
While not able to recall the exact combination of passengers for the flights to the site, the pilot was certain that they had flown a combination of passengers that represented their planned worst case scenario. ATSB interview with the survey team member who provided the weights identified that the passengers on the accident flight had not flown together on the earlier flights.
The pilot believed that the survey team was required to be at the site as soon as possible and therefore maximised the passenger loads to reduce the number of flights to the site. For the flights returning the passengers, the pilot considered reducing the passenger load was not necessary believing that their initial plan was still valid. The pilot stated that for the accident flight, they had less than their planned maximum 90 L of fuel and also removed unnecessary baggage from the helicopter just prior to departure (see Helicopter performance below).
Table 1 shows the calculations for the pilot’s estimated take-off weight of 2,378 lb (1,078.6 kg) in column 2. This calculation used 3 of the estimated passenger weights assessed by the pilot as the worst-case scenario. The ATSB obtained passenger weight estimates directly from each of the passengers, and calculated the gross weight for the accident flight, which are in column 3 of Table 1. Noting the possible inaccuracies from the passengers estimating their own weights, the ATSB calculated that the helicopter’s take-off weight was likely about 2,467.2 lb (1,119 kg), which was about 67.2 lb (30 kg) above the helicopter’s maximum take-off weight.
Table 1: Comparative take-off weight figures (lb)
Item | Pilot’s calculated take-off weight for the day | ATSB calculated take-off weight on the accident flight |
Basic empty weight |
1,471.4 |
1,471.4 |
Remove forward right door |
-7.5 |
-7.5 |
Remove forward left door |
-7.5 |
-7.5 |
Remove aft right door |
- |
- |
Remove aft left door |
- |
- |
Remove cyclic |
-0.6 |
-0.6 |
Remove collective |
-0.8 |
-0.8 |
Remove pedals (both) |
-0.8 |
-0.8 |
Pilot (forward right seat) |
231.4 |
231.4 |
Left forward passenger |
143.3 |
160.6 |
Aft right passenger |
165.3 |
264.0 |
Aft left passenger |
220.4 |
215.6 |
Baggage under forward right seat |
5.5 |
- |
Baggage under forward left seat |
5.5 |
- |
Baggage under aft right seat |
- |
- |
Baggage under aft left seat |
11 |
- |
Zero usable fuel weight |
2,236.6 |
2,325.8 |
Usable main fuel |
91.0 |
91.0 |
Usable aux fuel |
50.4 |
50.4 |
Take-off gross weight |
(1,078.6 kg) 2,378.0 |
(1,119.1 kg) 2,467.2 |
Maximum gross weight |
2,400.0 |
2,400.0 |
Margin at take-off |
(+10.0 kg) +22.0 |
(-30.5 kg) -67.2 |
The Civil Aviation Safety Regulations (CASR) Part 91[4] plain English guide explains loading of aircraft required in subpart 91.805:
At all times you must ensure that the aircraft is loaded and operated within its weight and balance limits.
The probability of overloading in small aircraft with less than 7 seats is high if standard passenger weights[5] are used. Therefore, it is recommended to use actual passenger weights.
Helicopter performance
Prior to the first flight of the day, the pilot checked the helicopter’s expected performance utilising the charts in the R44 Pilot’s operating handbook (POH). The charts indicated that they had sufficient performance for a hover in ground effect (IGE) but not for a hover out of ground effect (OGE).[6] The pilot reported that they did not consider this to be an issue because they did not plan to use OGE hover performance. Although the pilot did not have an exact location for the landing area at the heritage site, they recalled using either Abra or Kumarina airfields to determine performance, however the pilot could not recall which.
The pilot did not believe the lack of OGE performance would prevent the day’s flying from going ahead. They understood that they would not be able to conduct any ‘high power high performance’ techniques, and therefore OGE vertical manoeuvres would not be possible.
The ATSB calculated that the helicopter could hover IGE up to its maximum take-off weight at a temperature of 29 °C and a pressure altitude of 2,050 ft. However, the performance charts indicated that the helicopter would not be able to hover OGE (Figure 3). At the take‑off weight estimated by the pilot of 2,378 lb (1,079 kg), the maximum temperature for an OGE hover was calculated at 17 °C. At 29 °C, the maximum hover weight to conduct an OGE hover was 2,315 lb (1,052 kg).
The POH included a caution about performance data as follows:
Performance data presented in this section was obtained under ideal conditions. Performance under other conditions may be substantially less.
Figure 3: R44 out of ground effect hover ceiling
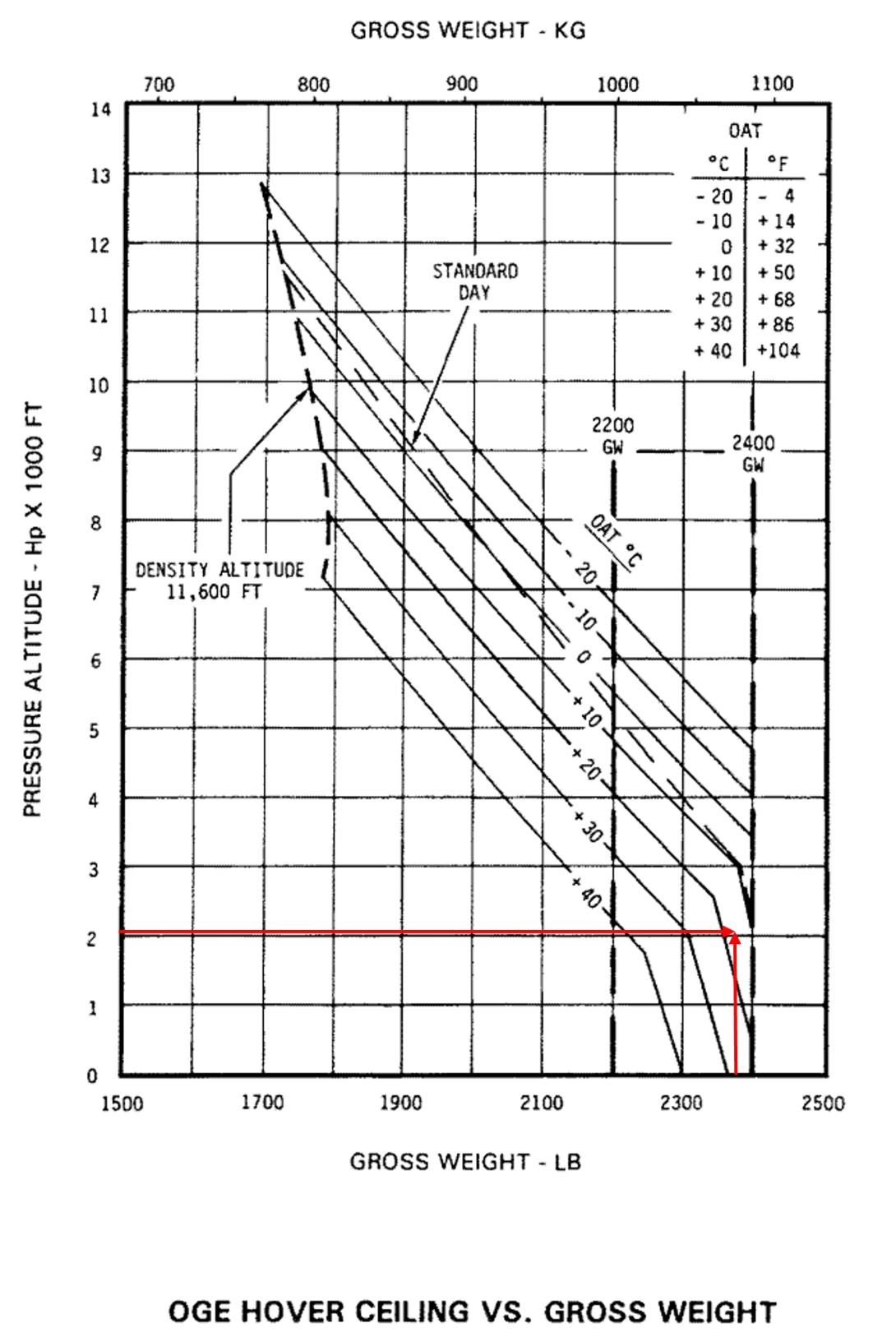
The OGE hover ceiling vs. gross weight chart is overlayed with red lines representing the pressure altitude of 2,050 ft and planned worst case gross weight of 2,378 lb, intersecting at a temperature of approximately 17 °C.
Note: as the ATSB estimated weight of the accident flight was above the maximum gross take-off weight, it is not represented on the chart.
Source: Robinson Helicopter Company, annotated by the ATSB
The pilot reported that on the first arrival at the survey site that morning, they flew a couple of circuits of the area to locate a suitable landing site. The landing site selected was based on the need to be close to the survey site for the passengers and suitability due to surrounding trees. The pilot reported conducting a power check before landing at the site and recalled that the helicopter achieved the maximum power for the temperature (25 °C) and altitude conditions. They landed in the clearing on each occasion without experiencing any performance issues.
The POH provided the recommended take-off profile for the R44 helicopter, which starts with the helicopter accelerating forward from an IGE hover (2 ft skid height) to achieve an exit gate of 50 kt at 25 ft above ground level. While this profile was achievable at the Abra mine camp, it was not achievable at the landing site due to trees about 10 ft high and 1 helicopter’s length from the lift-off point. This required a steeper take-off profile but was considered by the pilot to be the most ideal direction, as it was into wind and there were higher trees and rising terrain in the other directions. The pilot also reported that the terrain was downhill in the take-off direction and descended into a gorge after the tree line, which may have increased the height above ground after the helicopter passed the tree line.
While the morning flights departed from the landing site without passengers, the afternoon return flights were planned to depart with a full load of passengers. However, no performance calculations were conducted for the afternoon return flights. Prior to the accident flight departure, 2 of the passengers recalled the pilot discussing that it would be harder for the helicopter with the increased temperature at the time of departure.
The pilot reported that they believed they would be within the weight limit but realised the take-off would require more power than the previous departures from the site in the morning and consequently they removed excess items from the helicopter to minimise the take-off weight.
The pilot reported that after engine start, they performed the ignition check and operational check of the governor with no observed faults. After lift-off, the pilot noted the hover power margin IGE was about 3–4 inches manifold pressure below the published maximum power for the temperature (29 °C) but could not recall the actual setting. There was no indication that the take-off could not continue. Prior to the low rotor RPM warning, the pilot did not recall any abnormal engine indications.
FAA Helicopter flying handbook
The US Federal Aviation Administration (FAA) Helicopter flying handbook explains:
A pilot’s ability to predict the performance of a helicopter is extremely important. It helps to determine how much weight the helicopter can carry before takeoff, if the helicopter can safely hover at a specific altitude and temperature, the distance required to climb above obstacles, and what the maximum climb rate will be.
A helicopter’s performance is dependent on the power output of the engine and the lift produced by the rotors, whether it is the main rotor(s) or tail rotor. Any factor that affects engine and rotor efficiency affects performance. The three major factors that affect performance are density altitude, weight, and wind.
As the air temperature increases, the density altitude increases, which reduces the power produced by the engine. As the helicopter weight increases, more rotor thrust is required, which demands more power from the engine to maintain rotor speed. Wind affects the aerodynamic performance of the main and tail rotors, and depending on the direction and strength it can either reduce or increase the power required for take-off (flying into wind reduces power required).
Civil Aviation Safety Authority advisory circular
Civil Aviation Safety Authority (CASA) initially released advisory circular 91-29 (AC 91-29): Guidelines for helicopters – suitable places to take-off and land, in October 2021. While the AC 91-29 definitions did not include ‘confined area’, section 11.1.1 provided the following description:
An unprepared landing site that has obstructions that require a steeper than normal approach, where the manoeuvring space in the ground cushion is limited, or whenever obstructions force a steeper than normal climb-out angle is often defined as ‘Confined Area’.
Section 8.1.3 and 8.1.4 provided the following information about take-off and landing from a confined area:
Before committing to a take-off or landing, particularly in a confined area, a power check to determine excess power should be conducted. This can be achieved by noting the power required to hover IGE. Confirm the maximum allowable power to be used for the ambient conditions from the placard or AFM [aircraft flight manual]. Slowly start a vertical climb until the maximum power is achieved. Note the corresponding MAP [manifold pressure] or torque reading. The difference represents the power margin available and indicates what type of take-off will be possible, i.e., cushion-creep or towering.
…a pilot should always plan an OGE hover when landing in an area that is uncertain or unverified.
Operations manual
The company operations manual did not include a definition for a confined area or prescribe when OGE should be planned and what engine performance margins were required for confined area operations. However, the manual did provide pilot responsibilities for the use of helicopter landing sites under section 2.4.4:
Before electing to use an area as a landing site, the pilot in command shall take all reasonable steps to ensure that:
1. For the intended operation, having regard to all the circumstances of the proposed landing or take-off including the prevailing weather conditions, the helicopter can land or take-off in safety;
2. The characteristics of the helicopter and the operating technique employed will permit safe operations under the ambient meteorological conditions;
Further information was under section 6.4.8.3 Landing sites detailed:
Power Available - pilots to ensure that there is sufficient power available at all times to safely approach and exit any chosen landing site. Temperature of the day and altitude will degrade the performance of the helicopter. Approach and departure paths, vertical and horizontal obstacle clearance must be carefully evaluated with regard to power available.
Robinson Helicopter Company Flight training guide
The Robinson Helicopter Company provided a 2019 Flight training guide on their website, which provided a training syllabus for R22, R44 and R66 helicopters. It included a section entitled R44 Maneuver guide that provided the techniques for the various manoeuvres flown in the training syllabus, which included Hover out-of-ground Effect (OGE), and Maximum performance takeoff and climb.
In the hover OGE section, the minimum power margin required from an IGE hover before attempting the manoeuvre was given as 2 inches manifold pressure below the maximum take-off power or full throttle position. The hover OGE section also recommended the ‘minimum OGE hover altitude for training is 50 feet.’
The maximum performance take-off and climb technique, which is used to simulate clearing an obstruction during take-off, was described as follows:
While on the ground at a reduced RPM, check the manifold pressure limit chart to determine the maximum takeoff power. Clear the aircraft left, right and overhead, then complete a before takeoff check (RPM 102%, Warning Lights, Instruments, and Carb Heat). Select a reference point(s) along the takeoff path to maintain ground track.
Begin the takeoff slowly by getting the helicopter light on the skids. Pause and neutralize all aircraft movement. Slowly increase the collective and position the cyclic so as to break ground and maintain a 40 KT attitude (approximately the same attitude as when the helicopter is light on the skids). Continue to slowly increase the collective until the maximum takeoff power is reached. This large collective movement will require a substantial increase in left pedal to maintain heading. The governor will maintain the RPM.
At 50 feet of altitude, slowly lower the nose to a normal 60 KT climb attitude. As the airspeed passes 55 KTS, reduce the collective to normal climb power.
Low rotor RPM recovery
Overpitching can occur when the rotor blade angle of attack[7] is too high, creating so much drag that the available engine power cannot maintain the required rotor RPM. According to the FAA Helicopter flying handbook, overpitching is where the pilot demands more power than the engine is able to provide, normally as a result of pulling up too much on the collective. This can occur at higher density altitudes where the engine is already producing its maximum power and the pilot raises the collective. The increased angle of attack of the rotor blades will require more engine power, but as the engine is already producing its maximum, the rotor RPM will decrease.
The operational range of rotor RPM for the R44 is 90–108% with the rotor RPM normally operating at 101–102%. An aural (warning horn) and visual alert will be triggered once the rotor RPM drops below 97%. The pilot could not recall any RPM figures during the accident.
The R44 POH procedure for restoring RPM after a low rotor RPM warning states:
To restore RPM, lower collective, roll on throttle and, in forward flight, apply aft cyclic.
Robinson Helicopter Company issued safety notice SN-10 reinforced this procedure, stating:
No matter what causes the low rotor RPM, the pilot must first roll on throttle and lower the collective simultaneously to recover RPM before investigating the problem. It must be a conditioned reflex. In forward flight, applying aft cyclic to bleed off airspeed will also help recover lost RPM.
During the first interview, the pilot described immediately lowering the collective and then attempting to increase airspeed to fly out of the situation. Later in that interview they added that they did roll on throttle while lowering the collective. The pilot reported that the low RPM horn stopped for a brief time then came on again.
In a follow up interview, the pilot explained that they did perform the standard recovery of lowering the collective and rolling on throttle and that the horn stopped. The pilot reported that they then applied forward cyclic to increase airspeed and the low RPM horn sounded again. The pilot then repeated the recovery actions until realising that recovery was not possible.
In response to the draft report, the pilot clarified that when conducting the low rotor RPM recovery technique, the actions of lowering the collective and rolling on throttle were taught and drilled as simultaneous actions, and that while they only stated lowering the collective, they would have carried out both actions together. The pilot also reported that aft cyclic was not applied in an attempt to maintain speed and retain translational lift.
Passenger carriage under CASR Part 138
The operator held a Civil Aviation Safety Regulation 1998 (CASR) Part 138 (aerial work operations) Air Operator’s Certificate (AOC). The company operations manual indicated that they were not authorised for air transport operations and that when carrying out aerial work operations, only aerial work passengers[8] and task specialists[9] may be carried.
Part 138 aerial work operations generally undertake higher risk activities such as dispensing operations (dropping or releasing any substance or object from the aircraft), external load operations (carrying or towing an object outside the aircraft) or task specialist operations (such as low-level aerial survey, inspection or stock mustering). As such, only aerial work passengers or task specialists may be carried as they are exposed to and accept a higher level of risk during an operational task.
In this case, passengers were being transported from the mine camp to the cultural site, and no aerial work activities as defined in CASR Part 138 were being undertaken. Surveillance undertaken by CASA following the accident determined that the operator had mistakenly believed the transport of the passengers to conduct a survey of the cultural site after deboarding the helicopter to fall within their Part 138 authorisation. CASA stated that the passengers should have been classified as air transport passengers and that the flight should have been conducted under a CASR Part 133 (Australian air transport operations rotorcraft) AOC. CASA issued a safety finding to the operator.
CASR Part 133 governs passenger air transport operations in rotorcraft and provides a higher standard of safety for the carriage of passengers. As the operator did not hold a CASR Part 133 AOC, it was not subject to the standards of CASR Part 133, nor had they been assessed for suitability to conduct Part 133 air transport operations by CASA.
Safety analysis
Weight and balance
The pilot used estimated passenger weights based on their physical description rather than weighing them or asking the passengers to each provide their own weight. This approach was very likely to produce an incorrect gross weight calculation of the helicopter. The ATSB analysis found that the take-off weight for the accident flight was likely about 30 kg more than the pilot had calculated. This was above the out of ground effect (OGE) hover performance weight and the maximum gross weight for the helicopter.
Due to the helicopter having exceeded its maximum gross weight, there was no assurance that it could achieve the required take-off performance in accordance with the R44 Pilot operating handbook. Operations above maximum gross weight will negate the safety margins that are available to minimise the risk of performance-limited conditions during critical phases of flight.
Helicopter performance
The pilot believed that not having OGE performance would prevent them from attempting high power, high performance take-offs and landings. As the landing site was not previously known to the pilot, they could not be sure if the helicopter would require OGE performance at the site. CASA AC 91-29 advised pilots to always plan to hover OGE for unverified or uncertain landing areas.
The landing area selected was confined, with a tree line of about 10 ft high obstructing the most into wind take-off direction. The pilot successfully departed twice from the site that morning with lower temperatures and at significantly reduced weights (no passengers). The accident flight was the first departure from the site with a full passenger load and occurred later in the day with a higher outside air temperature. The pilot was aware that the helicopter was heavy, and that the helicopter’s performance may be limited as a result. Although removing unnecessary items from helicopter, this did not significantly reduce weight and therefore was not sufficient to markedly improve helicopter performance.
The pilot did not follow the Robinson Helicopter Company (RHC) guidance for clearing an obstruction during take-off. The pilot assessed the negligible OGE performance and did not want to conduct high power/high performance manoeuvres. The RHC maximum performance take-off procedure calls for applying maximum power, climbing vertically and achieving obstacle clearance height prior to commencing forward flight. This would have given the pilot an accurate assessment of the power available at the treetop height. If maximum power could not be achieved at a height sufficient to clear the trees, the pilot would then be able to land immediately and reassess their planned departure.
The pilot commenced a normal take-off, but with a significantly reduced time IGE prior to commencing a climb above the treetops. The pilot did not report any abnormal engine indications and the ATSB did not consider that an engine failure or malfunction had occurred. However, due to the heavy weight and high density altitude, it is likely that the power required was in excess of the power available and helicopter blade overpitching developed.
The pilot initially did not mention increasing the throttle when attempting to recover from the low rotor RPM, later clarifying that they had simultaneously lowered the collective and rolled on throttle. They reported they had attempted to increase airspeed (which requires forward cyclic) and that aft cyclic would slow the aircraft, causing a loss of translational lift. This was not in accordance with the POH which states ‘lower collective, roll throttle on and, in forward flight, apply aft cyclic.’
The ATSB found that there was insufficient evidence to ascertain the effect of the emergency technique, however not applying the correct recovery technique for low rotor RPM, may have inhibited the recovery.
Given the low height, low airspeed and low rotor rpm, the helicopter did not have sufficient energy for the pilot to arrest the descent to avoid a collision with terrain.
Reviewing and amending the helicopter weight and balance and the required performance was especially important given the confined area that the helicopter had landed in. However, the pilot did not review or recalculate the weight and balance, nor did they review predicted helicopter performance for the actual conditions at the time of the accident flight to confirm if their initial plan remained valid.
The overweight helicopter condition, combined with the confined take-off area and high density altitude, required more power than was available to safely conduct the take-off. The pilot’s assumptions about helicopter performance could not be expected to be correct.
Passenger carriage under CASR Part 138
The Civil Aviation Safety Regulations 1998 (CASR) specify the requirements which an operator must be assessed against by the Civil Aviation Safety Authority (CASA) in order to conduct their approved operations. Given the wide variety of aviation activities, there are numerous CASR parts to govern particular operations and compliance; compliance with one part does not ensure compliance with others.
CASR Part 133 regulations are generally accepted as providing higher levels of assurance that the risks to passengers have been reduced to a reasonably acceptable level. This is in contrast to CASR Part 138 operations which may involve higher risk operations and acceptance of that risk by the crew and aerial work passengers or task specialists engaged in the aerial work task.
As there was no aerial work operation being conducted the passengers should have been classed as CASR Part 133 air transport passengers. CASA viewed this as a genuine mistake by the operator, who believed the tasking they were undertaking to be a survey operations flight.
The operator was not authorised under CASR Part 133 and had not been assessed against the higher regulatory requirements. This resulted in reduced safety assurance that the risks to the passengers had been reduced to an acceptable level of safety under Part 133.
While CASR Part 133 included more prescriptive requirements for the calculation of weight and balance and take-off performance, CASR Part 138 required similar outcomes relating to helicopter operations within the manufacturer’s weight and balance limits and performance calculations to ensure sufficient safety for the proposed take-off considering the ambient conditions. Elements of these were reflected in the company operations manual, however non-compliance with these procedures under CASR Part 138 suggests the same outcome could have occurred under Part 133. Therefore, the ATSB considered that the operations under CASR Part 138 instead of Part 133 did not contribute to the accident outcome.
Findings
ATSB investigation report findings focus on safety factors (that is, events and conditions that increase risk). Safety factors include ‘contributing factors’ and ‘other factors that increased risk’ (that is, factors that did not meet the definition of a contributing factor for this occurrence but were still considered important to include in the report for the purpose of increasing awareness and enhancing safety). In addition ‘other findings’ may be included to provide important information about topics other than safety factors. These findings should not be read as apportioning blame or liability to any particular organisation or individual. |
From the evidence available, the following findings are made with respect to the collision with terrain involving Robinson R44, registered VH-OCL, 8.1 km north-north-west of Kumarina Roadhouse Airport, Western Australia on 3 November 2022.
Contributing factors
- The pilot did not calculate the weight and balance for the accident flight, instead relying upon a worst case, heaviest load scenario which used estimated rather than actual passenger weights. As a result, it was likely that the helicopter was in excess of its maximum gross weight at take-off.
- Prior to take-off, the helicopter performance was not re-evaluated using the actual conditions. The manufacturer's recommended normal take-off profile was not able to be flown due to obstacles and the manufacturer's guidance for a maximum performance take-off and climb was not followed. This increased the risk of insufficient performance for take-off.
- During take-off, the helicopter rotor RPM began to decay, triggering the low RPM warning. The pilot was not able to recover the rotor RPM and attempted an emergency landing.
- The low rotor RPM during take-off was likely to be the result of an overpitching situation, where the power required was more than the power available. This was due to the heavy take-off weight, high density altitude, and steep take-off profile.
- While attempting an emergency landing, the pilot was not able to arrest the rate of descent resulting in a collision with terrain, injuring all 4 people on board.
Other factors that increased risk
- The operator believed that the passengers were aerial work passengers in accordance with their Part 138 Air Operator's Certificate. However, the passengers were not involved with any aerial work purpose, nor was an aerial work purpose being conducted. The passengers should have been classified as air transport passengers under Part 133, for which the operator was not authorised. This resulted in a lower level of safety assurance for the flights.
Safety actions
Whether or not the ATSB identifies safety issues in the course of an investigation, relevant organisations may proactively initiate safety action in order to reduce their safety risk. The ATSB has been advised of the following proactive safety action in response to this occurrence. |
Safety action by C.A. Helicopters
The operator immediately paused all operations to undertake debriefing and discussions on the incident with all company pilots. They also engaged an independent auditor to review their operations.
Prior to commencing their following year’s operations, the operator conducted induction and familiarisation training, which included an independent examiner to conduct proficiency checks and flight reviews for all pilots to ensure competency on all operations and emergency procedures. Further, the operator reported that passenger carrying operations would require Head of operations clearance to proceed.
Sources and submissions
Sources of information
The sources of information during the investigation included the:
- pilot of the accident flight
- operator and the chief pilot of C.A. Helicopters
- Civil Aviation Safety Authority
- Bureau of Meteorology
- accident witnesses and passengers.
References
Civil Aviation Safety Authority. (2019). Civil Aviation Safety Regulations 1998 – Part 91 (General operating and flight rules). Commonwealth of Australia
Civil Aviation Safety Authority. (2023). CASR Part 91 Plain English guide.
Civil Aviation Safety Authority. CASA multi-part advisory circular AC 121-05, AC 133-04 and AC 135-08 Version 1.1 Passenger, crew and baggage weights
Federal Aviation Administration. (2019). Helicopter flying handbook. U.S Department of Transportation.
Robinson Helicopter Company. (2021). R44 Pilot’s Operating Handbook. Robinson Helicopter Company.
Robinson Helicopter Company. (2020). Flight Training Guide.
Submissions
Under section 26 of the Transport Safety Investigation Act 2003, the ATSB may provide a draft report, on a confidential basis, to any person whom the ATSB considers appropriate. That section allows a person receiving a draft report to make submissions to the ATSB about the draft report.
A draft of this report was provided to the following directly involved parties:
- pilot of the accident flight
- operator and the chief pilot of C.A. Helicopters
- Civil Aviation Safety Authority
Submissions were received from the:
- pilot of the accident flight
- operator and the chief pilot of C.A. Helicopters
- Civil Aviation Safety Authority.
The submissions were reviewed and, where considered appropriate, the text of the report was amended accordingly.
Purpose of safety investigationsThe objective of a safety investigation is to enhance transport safety. This is done through:
It is not a function of the ATSB to apportion blame or provide a means for determining liability. At the same time, an investigation report must include factual material of sufficient weight to support the analysis and findings. At all times the ATSB endeavours to balance the use of material that could imply adverse comment with the need to properly explain what happened, and why, in a fair and unbiased manner. The ATSB does not investigate for the purpose of taking administrative, regulatory or criminal action. TerminologyAn explanation of terminology used in ATSB investigation reports is available here. This includes terms such as occurrence, contributing factor, other factor that increased risk, and safety issue. Publishing informationReleased in accordance with section 25 of the Transport Safety Investigation Act 2003 Published by: Australian Transport Safety Bureau © Commonwealth of Australia 2024 Ownership of intellectual property rights in this publication Unless otherwise noted, copyright (and any other intellectual property rights, if any) in this report publication is owned by the Commonwealth of Australia. Creative Commons licence With the exception of the Coat of Arms, ATSB logo, and photos and graphics in which a third party holds copyright, this publication is licensed under a Creative Commons Attribution 3.0 Australia licence. Creative Commons Attribution 3.0 Australia Licence is a standard form licence agreement that allows you to copy, distribute, transmit and adapt this publication provided that you attribute the work. The ATSB’s preference is that you attribute this publication (and any material sourced from it) using the following wording: Source: Australian Transport Safety Bureau Copyright in material obtained from other agencies, private individuals or organisations, belongs to those agencies, individuals or organisations. Where you wish to use their material, you will need to contact them directly. |
[1] Collective: a primary helicopter flight control that simultaneously affects the pitch of all blades of a lifting rotor. Collective input is the main control for vertical velocity.
[2] QNH: the altimeter barometric pressure subscale setting used to indicate the height above mean seal level.
[3] The pilot had arranged for fuel drums to be prepositioned at both Abra mine camp and Kumarina Roadhouse Airport, allowing them to refuel when necessary.
[4] CASR Part 91 General operating and Flight Rules Subpart 91.J Weight and Balance
[5] Part 121 Manual of Standards sets out the standard passenger weights for use in Australian Air Transport Operations—Larger Aeroplanes. The weights are based on gender and age of each passenger carried on an aircraft with a seat capacity of 7 seats or more.
[6] When hovering within about one rotor diameter of the ground, the performance of the main rotor is affected by ground effect. A helicopter hovering in-ground-effect (IGE) requires less engine power to hover than a helicopter hovering out‑of-ground-effect (OGE). That is, when hovering close to the ground, the air being drawn down through the rotor collects under the helicopter and provides a ‘cushion’ of air, requiring slightly less power than would otherwise be required.
[7] Angle of attack (AoA) is the angle the rotor blade and the resultant relative wind as the rotor blade rotates.
[8] An aerial work passenger is a person who is closely associated with the aerial work operation and not present in the aircraft for convenience or enjoyment.
[9] A task specialist is a crew member (but not a flight crew or air crew member) who undertakes a specialist function for the flight relating to the aerial work operation.