What happened
On 15 July 2022, a Bell Textron 505 helicopter registered VH-VTB was conducting a scenic flight near Double Island, Queensland, with a pilot and 2 passengers on board. About 30 minutes into the flight, the pilot heard 2 brief, loud ‘grinding noises’ and elected to proceed to Cairns Airport.
While over the airfield, the grinding began again and did not stop. After 10-12 seconds, approximately 10 ft off the ground, the pilot heard 2 loud bangs, and the helicopter yawed to the right. In response, the pilot moved the throttle to idle, which stopped the yaw. A run-on landing was performed on the grass short of the assigned helipad. Subsequent inspection of the helicopter revealed that the tail rotor driveshaft had failed.
What the ATSB found
A section of the tail rotor driveshaft failed due to a bearing that seized and overheated in flight. The reason for the bearing seizure could not be determined. An examination of the bearings 2 days previously found no problems, and the adjacent bearing was well lubricated, with some very small points of damage on the bearing race indicating potential contaminants.
The pilot’s decision to adopt a shallow approach into Cairns, and to reduce throttle immediately following the tail rotor failure both assisted in controlling the helicopter following the uncommanded yaw, and allowed a safe landing.
Safety message
Unusual sounds and responses from an aircraft can be an indication of an imminent system failure. In this instance, the pilot’s decision to return to Cairns was probably influenced by the initial short duration of the unusual noises and overwater operation. While a safe landing on an airfield resulted, the occurrence also illustrates how quickly failures can occur.
Therefore, pilots experiencing any unusual vibration or noise should land as soon as possible and have the aircraft inspected prior to further flight. If an immediate landing is not possible then pilot should be prepared to conduct an emergency landing or ditching if the situation deteriorates.
The investigation
The occurrence
The pilot elected to perform a shallow return approach and, as the aircraft approached overhead the airfield, the grinding noise began again. The noise continued as the pilot neared the designated helipad. After 10-12 seconds, while approximately 10 ft above the ground, the pilot increased the power slightly to transition into a hover for landing and a ‘couple of big bangs’ were heard from the rear of the helicopter. It immediately yawed approximately 45° to the right, and the pilot responded by moving the throttle to idle. The uncommanded yaw stopped as a result, and the helicopter’s forward motion combined with a 10‑12 kt headwind aligned it with the direction of travel.
With the main rotor RPM decreasing, the pilot lowered the collective and executed a run-on[1] landing on a grass strip in the undershoot of the assigned helipad. The passengers disembarked and the helicopter was shut down normally. A subsequent inspection found that the tail rotor driveshaft had failed and separated at a bearing near the aft firewall.
Context
Managing tail rotor failures
The United States Federal Aviation Administration (FAA) recommends shallow approaches followed by a run-on landing in circumstances where there is insufficient power to hover.[2] This allows the helicopter to gain additional lift from its forward motion up until it touches down.
In the specific event of a tail rotor drive system failure the FAA notes that the severity of the resulting yaw is reduced by low power and high airspeed. Less power means a smaller reaction from the airframe due to main rotor torque, and more airspeed allows the aerodynamics of the fuselage and vertical stabiliser to mitigate the yaw effect. Following an in-flight tail rotor failure, the FAA recommends an immediate reduction of power and lowering of collective to land the helicopter (via an autorotation if necessary).[3]
Component examination
A section of the tail rotor driveshaft assembly known as the fan shaft was sent to the ATSB for detailed technical examination (Figure 1). This section of the driveshaft also drove the oil cooler fan, as well as cabin air-conditioning via a pulley and drive belt. In a functional fan shaft assembly, the engine drives the fan shaft which connects to the rest of the tail rotor driveshaft and ultimately, the tail rotor itself. The forward and aft hangers restrain the fan shaft via ball bearings that are clamped in each hanger using a nut.
Figure 1: The fan shaft and associated components removed from VH-VTB
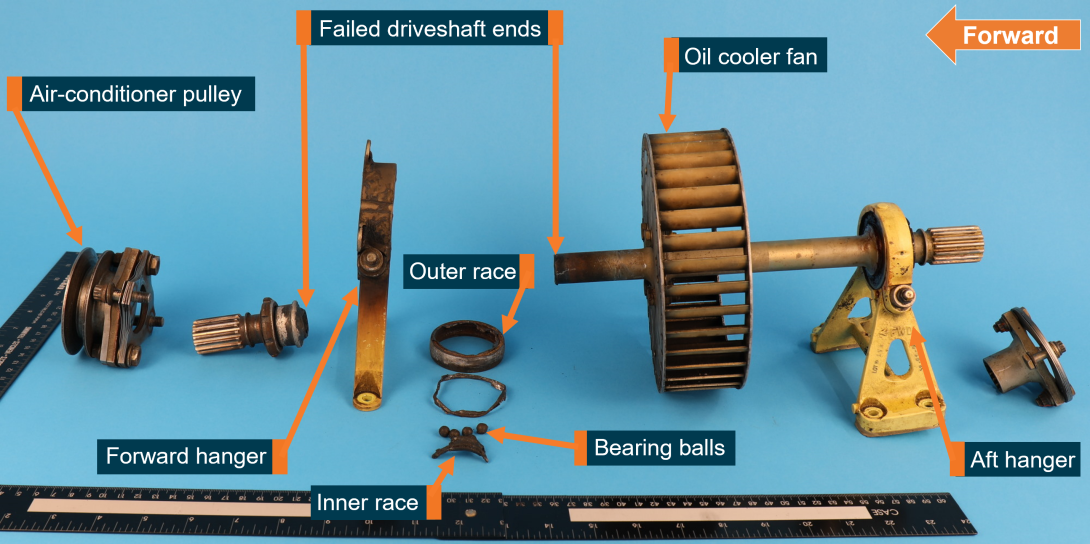
Source: ATSB
The driveshaft failed adjacent to the bearing seated inside the forward hanger. Blackening of the hanger, shaft and bearing components was present, indicative of exposure to high heat. The fracture surface closest to the bearing also appeared to be deformed due to heat exposure (Figure 2, D). Metal transfer on the bearing seat was likely from the adjacent inner race. No grease was observed in the bearing, though it might have been slung out or dissociated due to the high temperatures.
The outer race of the bearing was intact, but showed signs of corrosion (Figure 2, A). The inner race of the bearing had disintegrated, and only a small portion was found, along with only 5 bearing balls (Figure 2, B). Deep rotational scoring was observed on the inner face of the hanger and the outside of the outer race—normally clamped together during operation (Figure 2, C). The nut used to clamp the hanger to the bearing was still present, and a stripe of torque seal on the nut indicated that it had not backed off since it was last tightened. Metal was transferred onto the surface of the fan shaft, where the inner bearing sat during operation.
Figure 2: Damaged components of the failed bearing (A, B), hanger (C), and fan shaft (D)
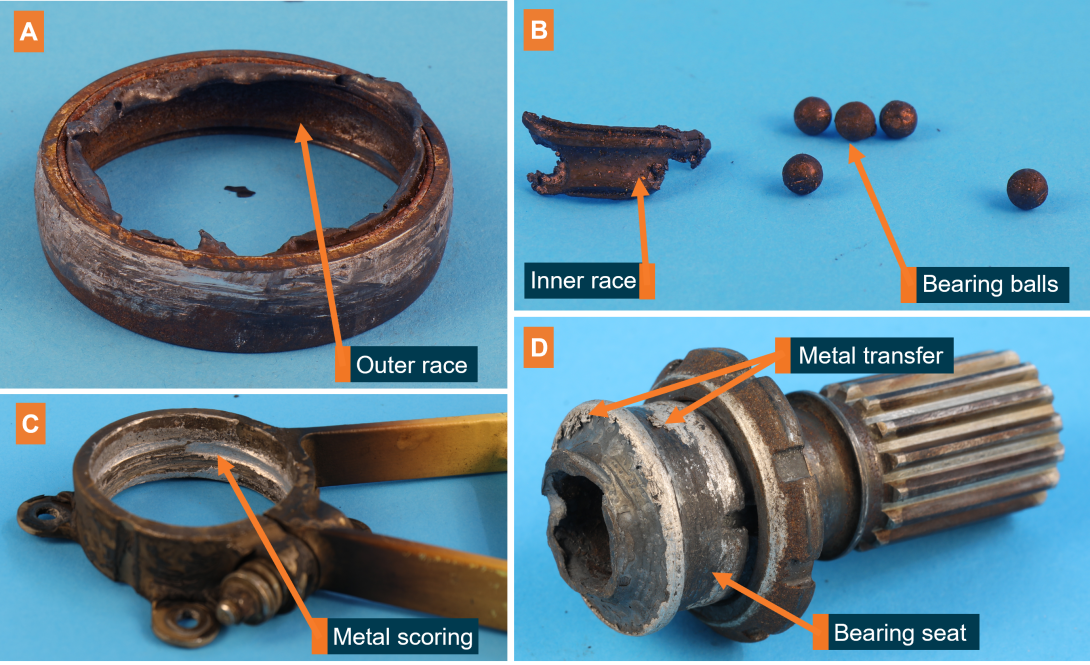
Source: ATSB
For comparison, the aft bearing was sectioned and examined for signs of damage (Figure 3). There were no signs of rotational scoring between the bearing and the aft hanger. The bearing contained sufficient grease, which had the same appearance as Mobilgrease 28. The grease showed no signs of contamination.
Figure 3: The aft fan shaft bearing, sectioned and disassembled.
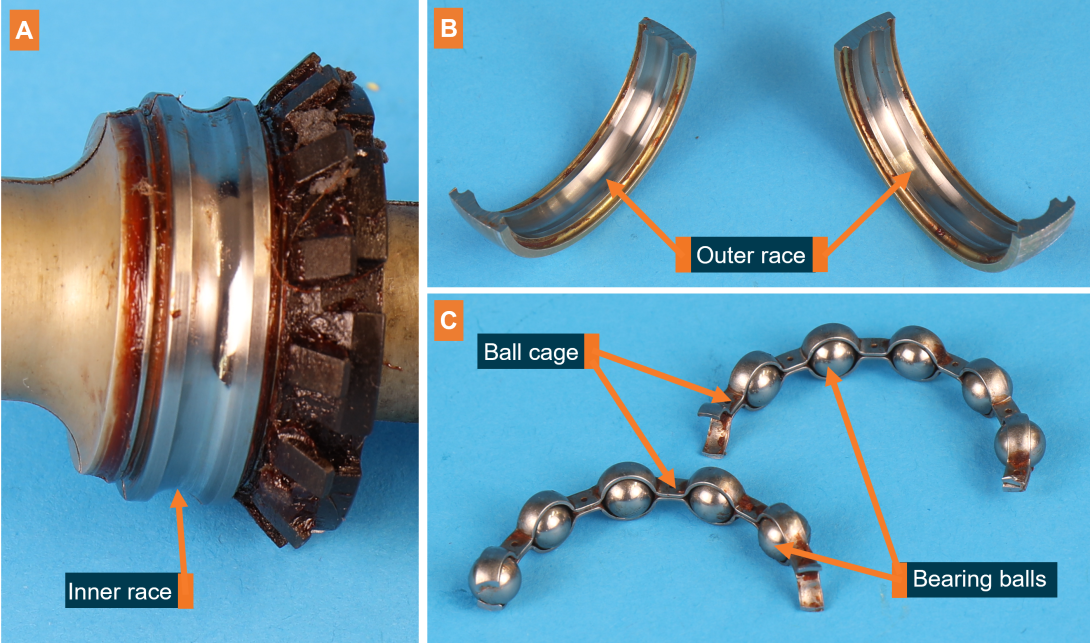
Source: ATSB
On the aft bearing, surfaces of the inner and outer bearing race were in good condition, with some very small points of spalling damage[4] on the inner race where contact would be made with the balls (Figure 4). No other mechanical damage associated with bearing degradation was observed (Figure 3, A and B). Likewise, there was no damage to the bearing balls or the ball cage retaining them (Figure 3, C).
Figure 4: Inner race spalling damage seen through an optical microscope (left) and electron microscope (right)
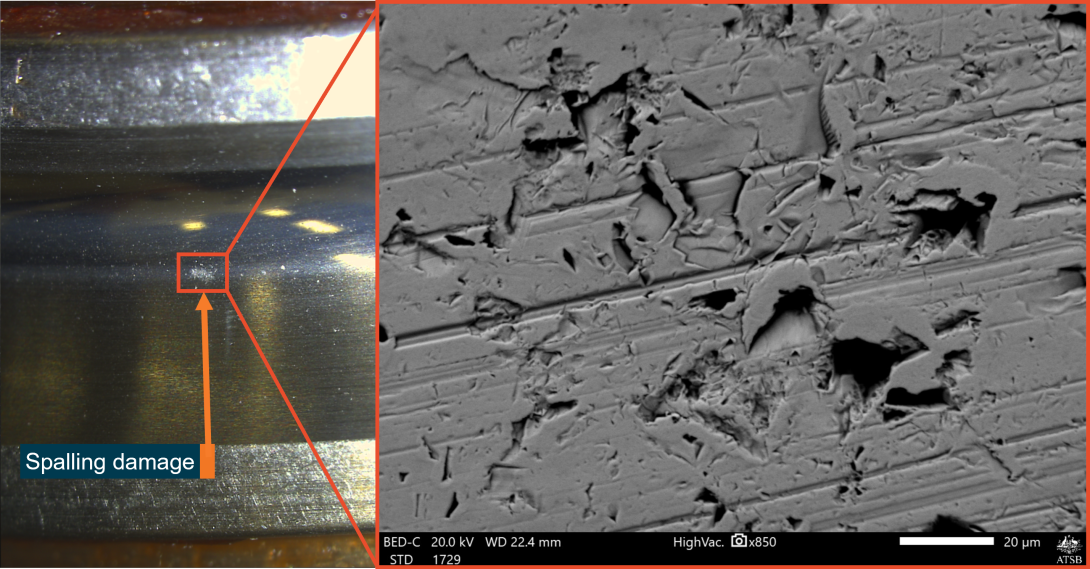
Source: ATSB
Aircraft maintenance
At the time of the incident, the helicopter had accrued 1,392.5 hours total time in service. The tail rotor driveshaft and associated bearings were the original parts installed when the operator received the new helicopter from Bell. The forward and aft fan shaft bearings were lubricated 246 flight hours previously using Mobilgrease 28, as part of the helicopters most recent 300-hourly inspection. This was done in accordance with Bell Textron’s maintenance schedule.
Two days before the incident, a different pilot heard a strange noise coming from what was thought to be the engine of VH-VTB. After an engine shutdown and restart the noise persisted. The helicopter was grounded for an inspection by maintenance personnel, but the noise could not be replicated. The helicopter was examined, including the tail rotor driveshaft. Bearings were inspected for signs of heat damage, excessive temperature, or noise, but no abnormalities were found and the helicopter returned to service. The pilot from the incident flight heard a recording of the initial noise, but did not believe it was the same ‘metal-on-metal’ sound heard during the incident, describing it as more of a vibration.
Comments from Bell Textron
Bell was not aware of any previous instances of bearing failure in 505 fan shaft bearings. Nor was it aware of any bearing failures in the 206 model helicopters, which use a similar drivetrain. Bell raised the possibility of air-conditioner belt tension or damage to the air-conditioner pulley splines as potential contributing factors. However, the splines were found to be in good condition and the operator reported that the belt had been installed in accordance with Bell’s maintenance schedule.
Other bearing issues
The failed bearing on VH-VTB associated with this incident was replaced with one from another 505, but after some time in service, maintenance personnel heard a ‘slight rumbling sound’ coming from the replacement bearing. It was subsequently sent to Bell for examination. The bearings and fan shaft assembly from the incident flight were also sent to Bell following the ATSB’s examination. At the time of writing the results of these examinations were not available.
The ATSB was also notified of another instance where an operator informed their maintainer of a strange and intermittent noise coming from one of the forward fan shaft bearings of a 505. Water was also found in the bearing when it was purged. The maintainer replaced the bearing in question, and there was no further examination of the removed bearing.
Safety analysis
During landing, a combination of heat and torque due to a seized forward fan shaft bearing resulted in failure of the fan shaft just aft of the bearing. The bearing seizure was evidenced by the disintegrated inner race, metal deposited on the bearing seat and signs of excessive heat around the bearing components and fan shaft. As a result of the bearing seizure, the fan shaft spun independently of the bearing, resulting in disintegration of the inner race. Scoring on the outer race and hanger indicated that at some stage, the bearing and fan shaft were also spinning together. It could not be determined when the bearing seized, but the noises heard by the pilot were likely either the fan shaft spinning on the bearing, or bearing spinning on the hanger. It could also not be determined whether the noise heard 2 days before the incident was related to the bearing failure.
Due to the amount of damage on the failed bearing, the reasons for its seizure could not be identified. The disintegrated inner race, corrosion within the outer race and damage to the hanger could all have been a result of the seizure, rather than factors contributing to it. No grease was observed following the failure, but it could have been slung out or dissociated due to the excessive heat. If the bearing was not properly greased, it would likely have resulted in abnormal noise or excessive heat when it was visually inspected 2 days previously, but neither were detected.
The aft fan shaft bearing showed no signs of corrosion or damage associated with improper lubrication. The only damage observed were small regions of spalling. Such localised damage was most likely due to a foreign contaminant within the bearing, since other possibilities such as poor tolerances, misalignment or manufacturing defects would have resulted in more widespread damage within the bearing. The forward bearing failure could have resulted from exposure to similar contaminants, but the faces of the inner and outer race were too damaged to permit an assessment of the failure mechanism.
Findings
ATSB investigation report findings focus on safety factors (that is, events and conditions that increase risk). Safety factors include ‘contributing factors’ and ‘other factors that increased risk’ (that is, factors that did not meet the definition of a contributing factor for this occurrence but were still considered important to include in the report for the purpose of increasing awareness and enhancing safety). In addition ‘other findings’ may be included to provide important information about topics other than safety factors. These findings should not be read as apportioning blame or liability to any particular organisation or individual. |
From the evidence available, the following findings are made with respect to the control issues involving Bell Textron 505, registration VH-VTB at Double Island, Queensland on 15 July 2022.
Contributing factor
Other (key) finding
- A shallow approach combined with timely and appropriate control inputs enabled the pilot to safely perform a run-on landing following the shaft failure.
Sources and submissions
Sources of information
The sources of information during the investigation included:
- the pilot and operator
- Bell Textron Inc.
- United States Federal Aviation Administration
Submissions
Under section 26 of the Transport Safety Investigation Act 2003, the ATSB may provide a draft report, on a confidential basis, to any person whom the ATSB considers appropriate. That section allows a person receiving a draft report to make submissions to the ATSB about the draft report.
A draft of this report was provided to the following directly involved parties:
- the pilot and operator
- Bell Textron Inc.
- Civil Aviation Safety Authority
- Transportation Safety Board of Canada
Submissions were received from:
- Bell Textron Inc.
- Transportation Safety Board of Canada
The submissions were reviewed and, where considered appropriate, the text of the report was amended accordingly.
Purpose of safety investigationsThe objective of a safety investigation is to enhance transport safety. This is done through:
It is not a function of the ATSB to apportion blame or provide a means for determining liability. At the same time, an investigation report must include factual material of sufficient weight to support the analysis and findings. At all times the ATSB endeavours to balance the use of material that could imply adverse comment with the need to properly explain what happened, and why, in a fair and unbiased manner. The ATSB does not investigate for the purpose of taking administrative, regulatory or criminal action. TerminologyAn explanation of terminology used in ATSB investigation reports is available here. This includes terms such as occurrence, contributing factor, other factor that increased risk, and safety issue. Publishing informationReleased in accordance with section 25 of the Transport Safety Investigation Act 2003 Published by: Australian Transport Safety Bureau © Commonwealth of Australia 2023 Ownership of intellectual property rights in this publication Unless otherwise noted, copyright (and any other intellectual property rights, if any) in this report publication is owned by the Commonwealth of Australia. Creative Commons licence With the exception of the Coat of Arms, ATSB logo, and photos and graphics in which a third party holds copyright, this publication is licensed under a Creative Commons Attribution 3.0 Australia licence. Creative Commons Attribution 3.0 Australia Licence is a standard form licence agreement that allows you to copy, distribute, transmit and adapt this publication provided that you attribute the work. The ATSB’s preference is that you attribute this publication (and any material sourced from it) using the following wording: Source: Australian Transport Safety Bureau Copyright in material obtained from other agencies, private individuals or organisations, belongs to those agencies, individuals or organisations. Where you wish to use their material, you will need to contact them directly. |
[1] A run-on/running landing is one in which a helicopter lands with significant forward motion, as opposed to landing from a hover, and maintains some forward motion after touching down. It is generally used when there is insufficient power to sustain a hover.
[2] FAA Helicopter Flying Handbook, Chapter 10: Advanced Flight Maneuvers, p. 6
[3] FAA Helicopter Flying Handbook, Chapter 11: Helicopter Emergencies and Hazards, pp. 16-17
[4] Spalling is the shedding of material, or ‘spall’ from a surface, In a bearing, spalling at a single point is typically due to nicks, dents, or hard-particle contaminants.