Executive summary
What happened
On 27 May 2022, a Singapore Airlines Airbus A350-941, registered 9V-SHH, was being prepared for a regular public transport flight from Brisbane Airport, Queensland to Changi Airport, Singapore. Just prior to the aircraft being pushed back for departure, a refueller on an adjacent bay informed the licenced aircraft maintenance engineer responsible for the aircraft turnaround that the pitot probe covers were still fitted. Subsequently, the covers were removed just before pushback.
What the ATSB found
The ATSB found that the procedural risk controls for the removal of the pitot probe covers were circumvented when a licenced aircraft maintenance engineer certified for the removal of the covers in the technical log and removed a warning placard from the flight deck without visual or verbal confirmation that the covers had been removed.
Further, a final walk-around of the aircraft by maintenance personnel to ensure it was correctly configured for flight was also not conducted. This represented the last procedural opportunity to identify that the covers had not been removed. Similarly, it was established from closed-circuit television footage of Singapore Airlines turnarounds at Brisbane Airport that the majority of flight crew pre-flight inspections observed around the time of this occurrence were truncated and not undertaken in accordance with company procedures. This included the occurrence flight.
The ATSB also identified that Heston MRO had not yet implemented an acceptable method for accounting for tooling and equipment prior to aircraft pushback, although this had been identified as a safety issue in investigation AO-2018-053. Also, Heston MRO did not track the work hours of personnel who had dual roles within the company for fatigue management purposes, even though there was a requirement in the fatigue management policy to do so.
Lastly, the pitot probe covers fitted to the aircraft were about 3 m above eye height and had relatively short streamers, which were not conspicuous and limited the possibility of incidental identification.
What has been done as a result
Heston MRO no longer requires the Brisbane regional manager position to undertake dual responsibilities, which included aircraft maintenance certification requirements, Further, Heston MRO now tracks the work hours of all employees for fatigue management purposes.
Singapore Airlines has communicated with flight crew about the requirements of their pre-flight walk-around checks and why they are important. In addition, Singapore Airlines has also provided Heston MRO at Brisbane with pitot probe covers that have longer streamers to ensure better conspicuity.
Safety message
Airspeed is a critical flight parameter, which is particularly important to flight crew during take-off and initial climb. It is the basis for their awareness of flight conditions such as the approach of aerodynamic stall and determination of critical decision points. This occurrence demonstrates how assumptions and procedural omissions can lead to unsafe conditions. In this case, the potential for an aircraft to commence a take-off with erroneous or absent airspeed indications due to the pitot probe covers remaining fitted.
Fatigue is a known factor in maintenance errors and can have a range of adverse influences on human performance. Therefore, it is important that organisations appropriately track all hours worked by safety critical employees to ensure they are receiving adequate rest and safeguard against the effects of fatigue.
Finally, this investigation recognises the positive actions of the refueller, who was working on the adjacent bay and had identified that the pitot covers remained fitted. This serves as a reminder that all line personnel have a safety role and should always speak up if they see or feel that something is not right.
The occurrence
On 27 May 2022, a Singapore Airlines Airbus A350-941 aircraft, registered 9V-SHH, was being prepared by maintenance personnel on bay 81 for a regular public transport flight from Brisbane Airport, Queensland to Changi Airport, Singapore, as flight number SQ256.
The engineering maintenance contractor had provided a licenced aircraft maintenance engineer (LAME) and an aircraft maintenance engineer (AME) to conduct its regular receipt, dispatch, certification, and maintenance duties during the aircraft’s scheduled 2-hour turnaround. The LAME (who was also the regional manager) was supervising the AME and assisting with the turnarounds of SQ256 and another aircraft on an adjacent bay. The AME had started with the contractor 3 weeks prior and had not completed all their induction training. On the day, the AME was conducting headset (turnaround coordinator) duties.[1]
Closed-circuit television footage from bay 81 showed that, between 0705 and 0727 local time, the LAME instructed the AME through the external walk-around inspection of the transit check for the aircraft. At 0732, the AME utilised an elevated work platform to install covers on all 4 pitot probes[2] in accordance with airline and company procedures specifically for Brisbane Airport. At about the same time, the LAME entered the flight deck to check the technical log for defects. As part of the pitot cover installation and removal procedures, the LAME made an entry in the technical log that the covers had been fitted and then placed a warning placard on the flight deck engine control pedestal to also show that the pitot covers were fitted.
Between 0852:18 and 0854:03, the first officer conducted a pre-flight walk-around. The walk‑around was truncated from the nose of the aircraft to the right engine, across to the left engine and back to the airbridge. From the footage, the first officer looked up at and likely observed the fitted pitot covers, however, they were required to be fitted at that time as per the operator’s procedure.
At 0859, the LAME arrived back on bay 81 after tending to an aircraft on an adjacent bay. The LAME conferred with the AME about fuel figures and talked to the flight crew via headset to confirm the fuel upload.
About 5 minutes later, the LAME re-entered the flight deck, certified for the transit check in the technical log, cleared the technical log entry for the fitment of the pitot covers, and removed the pitot cover warning placard from the flight deck pedestal. The LAME then returned to the tarmac and placed the placard on the dashboard in their work vehicle.
At 0913, the LAME returned to the tarmac at the nose of the aircraft and conversed with the AME for about 3 minutes. With 4 minutes remaining until the expected pushback[3] time, the LAME told the AME that they were going to the adjacent bay to complete the refuelling of another aircraft. The AME remained at bay 81 to conduct the pushback headset duties (Figure 1).
Around this time, an aircraft refueller on an adjacent bay observed that SQ256 appeared ready to pushback, but the pitot covers were still fitted. When the LAME reached the aircraft at the adjacent bay, the refueller immediately pointed to SQ256 and informed the LAME that the covers were fitted (Figure 2).
Figure 1: Security footage of bay 81 showing SQ256 4 minutes before pushback with the pitot covers fitted and the LAME moving towards the adjacent bay
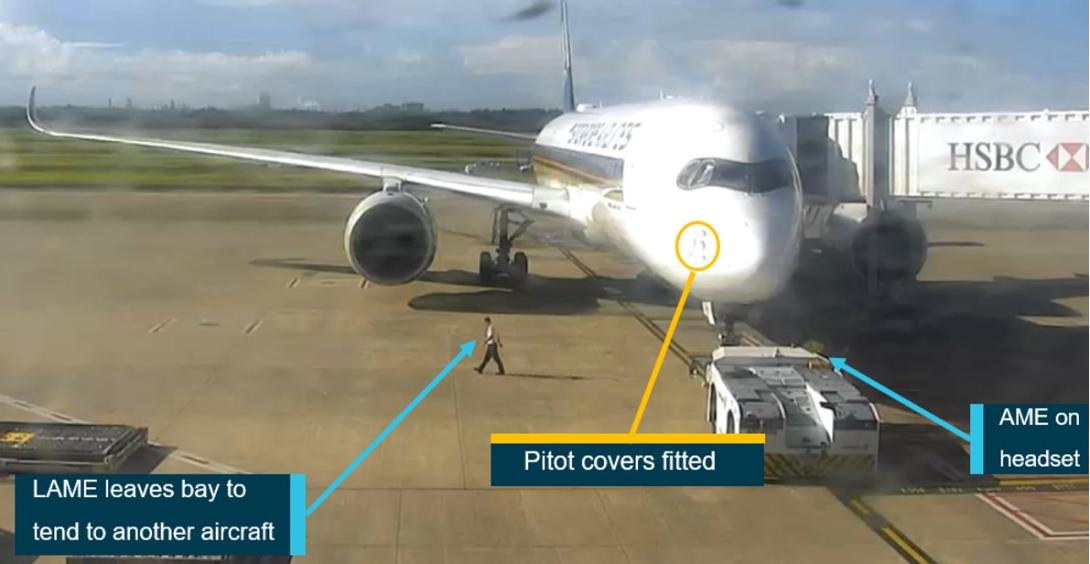
Source: Brisbane Airport Corporation, annotated by the ATSB
Figure 2: Security footage of the refueller pointing towards SQ256 and informing the LAME that the pitot covers were fitted
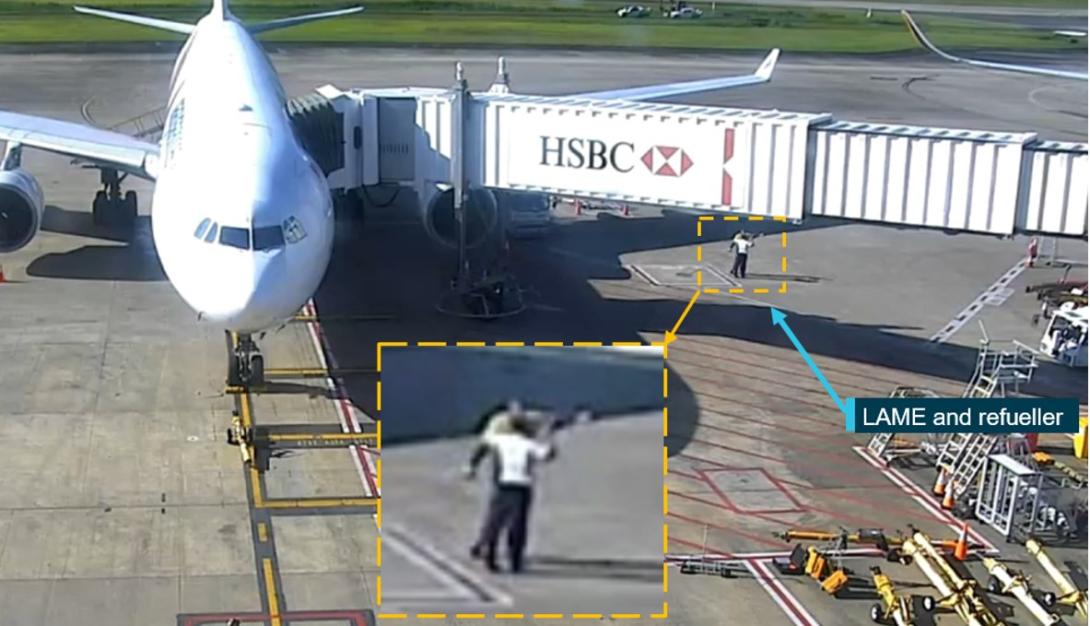
Source: Brisbane Airport Corporation, annotated by the ATSB
The LAME returned to SQ256 and alerted the AME that the pitot covers were still fitted. At about the same time, the flight crew requested pushback approval from air traffic control and turned on the aircraft beacons. The aerobridge began to retract away from the aircraft.
The flight crew then notified the AME on the headset that they were ready to pushback. The AME, having just been informed that the pitot covers were fitted, told the flight crew to standby as they were in the process of removing the pitot covers.
With 2 minutes remaining until the expected departure time, the LAME positioned an elevated work platform on each side of the nose and removed the pitot covers (Figure 3).
Figure 3: LAME removing the pitot covers
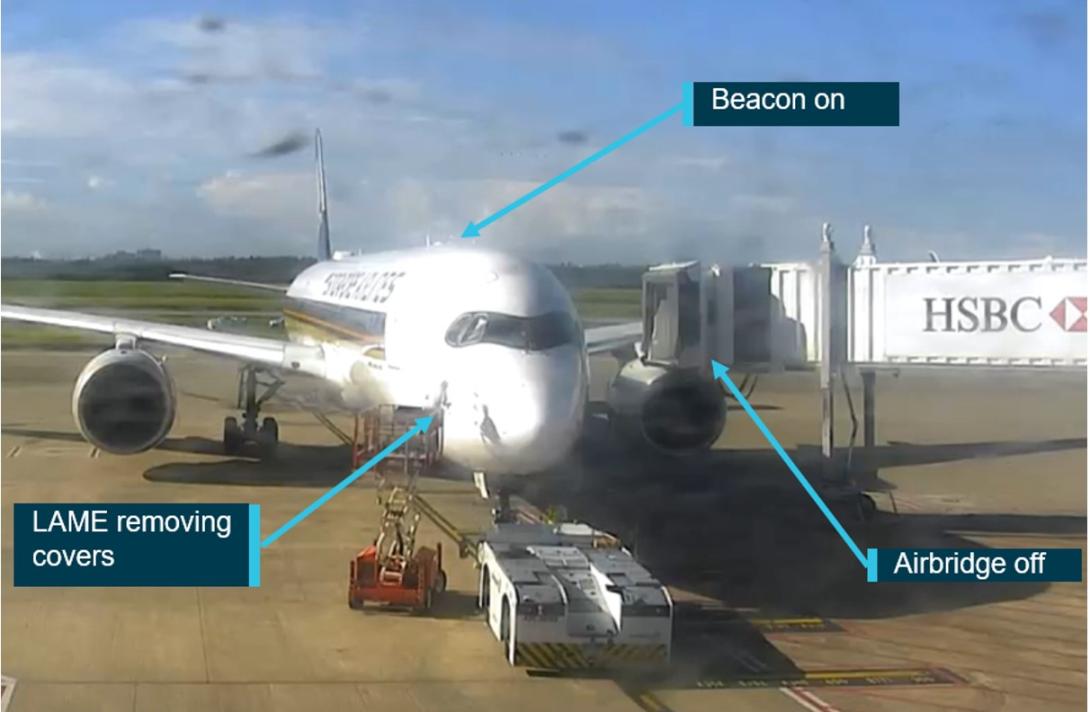
Source: Brisbane Airport Corporation, annotated by the ATSB
Context
Operator information
Operator arrangements for support services at Brisbane Airport
Much like other international airlines, Singapore Airlines had significantly scaled back services to Brisbane during the COVID-19 pandemic (2020 to 2021), halving its services from 28 to 14 flights per week. The airline had increased services to Brisbane to 21 flights from March 2022.
Singapore Airlines’ Brisbane Airport engineering services were contracted to Heston MRO. The requirements for the services of Heston MRO were also significantly reduced across all airlines it serviced during the pandemic. Therefore, its workforce was significantly reduced, and the remaining engineering staff had their hours decreased considerably. In 2022, when the Australian Government opened its borders to international travel, Heston MRO abruptly returned to normal operations, which equated to a significant increase in demand from airlines requiring their service.
Maintenance personnel information
Licenced aircraft maintenance engineer and regional manager
Qualifications and experience
The LAME joined Heston MRO in July 2021 and had licence coverage on several large aircraft and engine types, and extensive line maintenance experience over several years. The LAME’s main role was as the regional manager for south-east Queensland. In that role, the LAME was responsible for managing engineering operations for Heston MRO at Brisbane, Wellcamp and Gold Coast airports. The LAME also had responsibilities that included certification requirements at Brisbane Airport, storage and movement of aircraft at Wellcamp, and regular LAME functions when there were unscheduled LAME absences.
72-hour history
The LAME indicated that, in the 72-hours prior to the occurrence day (on Friday), they had:
- About 6 to 7 hours sleep on Tuesday after a workday average of 12 hours.
- On Wednesday, the LAME covered work spanning 2 shifts. One was conducting the return to service of an aircraft at Wellcamp with a commute starting at 0530 and a return to their residence at 1700. The second shift was line duties to cover another LAME’s absence starting at 1900 and working until midnight. Following those shifts, the LAME estimated that they had about 6 hours sleep.
- On Thursday, the LAME reported that they worked from home conducting administration duties and slept for about 7 hours before the occurrence shift.
- On Friday, the LAME commenced work at 0630.
During interview, the LAME was asked about their level of fatigue on the day of the occurrence utilising an alertness scale. The scale estimated alertness using descriptive anchors numbered from 1 to 7, with 1 being fully alert and 7 being completely exhausted. The LAME stated that they varied between 4 to 6 on the scale but seemed to be ‘moderately tired and let down’ on most days, which is 5 on the scale.
Dual roles
In 2022, the LAME/regional manager's dual roles progressively became more demanding as turnaround services increased, and aircraft were being removed from storage post COVID-19. They were recorded in the roster as working 7.5 hours, Monday to Friday. However, they reported that their workdays were often up to 12 hours with work also being conducted on weekends. Further, in their capacity as a LAME, conducting turnarounds was often required to cover shifts for other LAMEs due to sickness. For example, they reported that they had recently covered a shift for another LAME, following their own long workday. That workday exceeded the maximum work hour requirement and prescribed rest period between shifts.
The LAME also described that they seemed to be constantly in the state of being ‘moderately tired and let down’ due to the demands of their dual roles. The LAME mentioned that family and friends had expressed concern about the LAME’s stress levels and the amount of work they were doing. An internal company report into the occurrence had also noted that the LAME stated:
They could not remember the last time they had a full day of rest. In their own words, ‘’even when at home, they were working to catch up with their duties’’.
The report concluded that:
Based on the statements provided, [the LAME] seemed distracted. It is not clear if this was due to the activities that he assisted the Malaysian Aircraft with or if [they] were struggling with fatigue.
As Heston MRO did not track the LAME’s work hours for fatigue monitoring purposes (as per Heston MRO fatigue management policy, refer to section titled Heston MRO fatigue management program) the ATSB was unable to fully ascertain the extent of the LAME’s level of fatigue and how it may have affected their performance.
Aircraft maintenance engineer
The aircraft maintenance engineer (AME) joined Heston MRO 3 weeks prior to the occurrence and had a total of 2 weeks line experience with the company. The AME had completed a partial induction program, and training that included coordination/headset duties. Prior to joining Heston MRO, the AME had experience working on defence and civilian aircraft (not including the Airbus A350) conducting heavy maintenance. Some turnaround functions were conducted for a period of 6 months, although this was 2 years prior to the occurrence.
An internal Heston MRO report post-occurrence identified that, while the AME had completed a partial induction program and other training, they should not have been undertaking tasks unsupervised.
The AME reported that, on the day of the occurrence, they had just returned from 2 days off, were alert and well rested.
Pitot probes and covers
Pitot probes
Pitot probes (or part of the multi-function probes) are components of the aircraft’s pitot-static system. The Airbus A350 has 4 probes, which are attached to the nose of the aircraft (Figure 4). The pitot probe consists of a tube pointing directly into the airflow, measuring the stagnation pressure called total pressure. This total pressure information and the static pressure delivered by static ports on the fuselage are used to compute the aircraft’s indicated airspeed and Mach number. If the tube is partially or completely blocked, airspeed indications will be inaccurate. Airspeed is a critical parameter for flight.
Figure 4: Airbus A350 aircraft showing left side probes with covers fitted
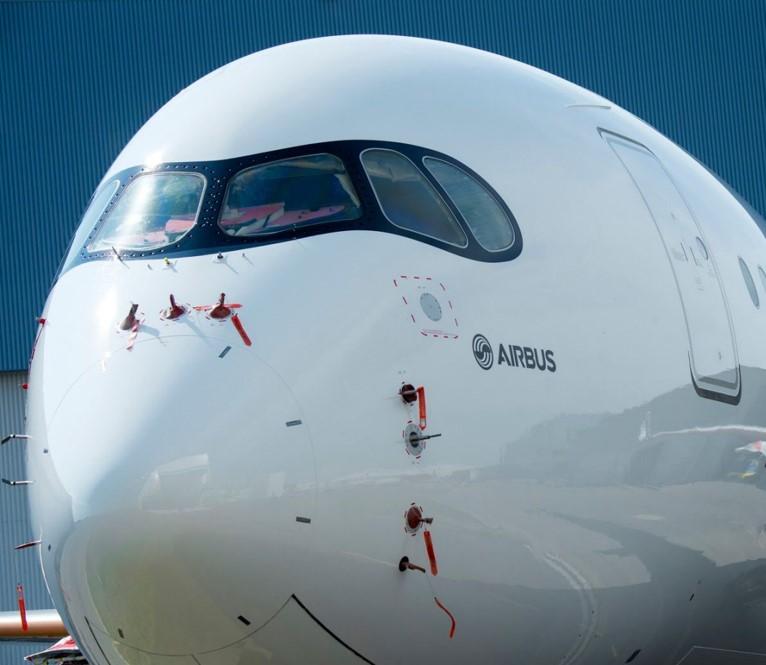
Source: Airbus
Contamination by mud wasps at Brisbane Airport
Historically, mud wasps have been known to build nests in aircraft pitot probes, entering through the forward-facing opening. Nesting and food material placed in the tube blocks the probe, to the point where it may no longer provide accurate airspeed information. A partial blockage, such as that resulting from the first addition of mud for a nest in the pitot, may be enough to cause anomalous airspeed readings as air flow is disturbed.
The Civil Aviation Safety Authority airworthiness bulletin 02-052 (Issue 6) Wasp Nest Infestation – Alert, stated that the potential for pitot probe contamination may arise within 20 minutes of availability. There may not be external signs of the presence of a nest or partial nest within the probe, and there have been numerous occurrences at Brisbane Airport where pitot probes were blocked during turnarounds. For that reason, the Brisbane Airport Corporation recommended the use of pitot probe covers during turnarounds.
Pitot probe covers
Pitot probe covers provide protection from foreign object obstruction when the aircraft is on the ground. The need for pitot probe covers is dependent on several factors, such as the duration the aircraft is on the ground, and local factors such as wildlife and weather. There may be a formal requirement by operators to fit pitot probe covers in these circumstances. As pitot probes are heated in-flight, maintainers need to wait 15-30 minutes for them to cool after landing before fitting covers (Airbus 2016).
Pitot probe covers typically incorporate a ‘remove before flight’ warning streamer (also known as a flag or ribbon) intended to alert relevant personnel of its presence. Several characteristics contribute to the conspicuity of the streamer. Red streamers can provide effective contrast against a white fuselage in good light but may not be as attention-attracting in poor lighting such as night, especially when they are dirty. Reflective materials may be helpful at night.
Another factor is length. Streamers come in various lengths, but its visibility may be improved by fitting an extended streamer or incorporating a lanyard between the cover and its streamer. Shorter streamers are less likely to draw a person’s attention when in their visual field even if they are not paying particular attention to that area. A longer streamer, or one with a lanyard, is more likely to move if wind is present. However, it has been reported that the greater force on longer streamers in strong winds can occasionally drag the covers off.
Figure 5 shows standard pitot probe covers fitted to the lower probes of an Airbus A350, which were estimated to be about 3 m above eye level. The Heston MRO internal report into this occurrence noted that:
The Pitot Cover streamers used at the station were short. They are not long enough to bring about attention to passers-by below the aircraft – refer photos [attached as Figure 5].
Figure 5: Airbus A350 aircraft showing lower pitot probe covers fitted
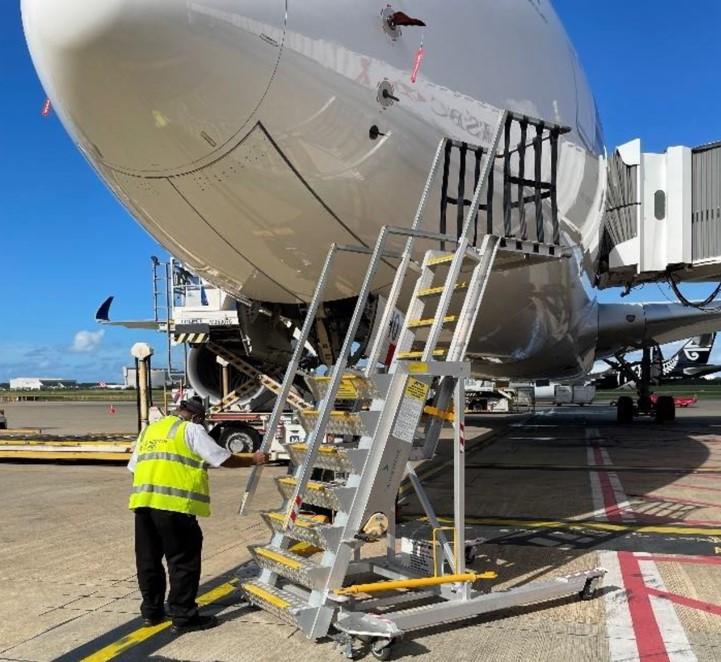
Source: Heston MRO, annotated by the ATSB
Pitot cover installation and removal procedures
Heston MRO and Singapore Airlines had a procedure for the installation and removal of the pitot covers at Brisbane Airport, which is summarised as follows:
- During the arrival procedures and after a short period of pitot cool down time, all pitot covers will be fitted.
- A warning placard will be placed on the flight deck pedestal stating that the pitot covers are fitted (Figure 6).
- An entry will be made in the aircraft technical log stating that the pitot covers have been fitted.
- The pitot covers are to be removed no earlier than 30 minutes prior to departure or as directed by the customer (Singapore Airlines is 20 minutes prior to departure).
- Following pitot cover removal, the entry in the aircraft technical log can then be closed and the placard removed from the flight deck and returned to the transit toolbox in accordance with Heston MRO’s transit toolbox procedure (below).
Figure 6: Flight deck warning placard
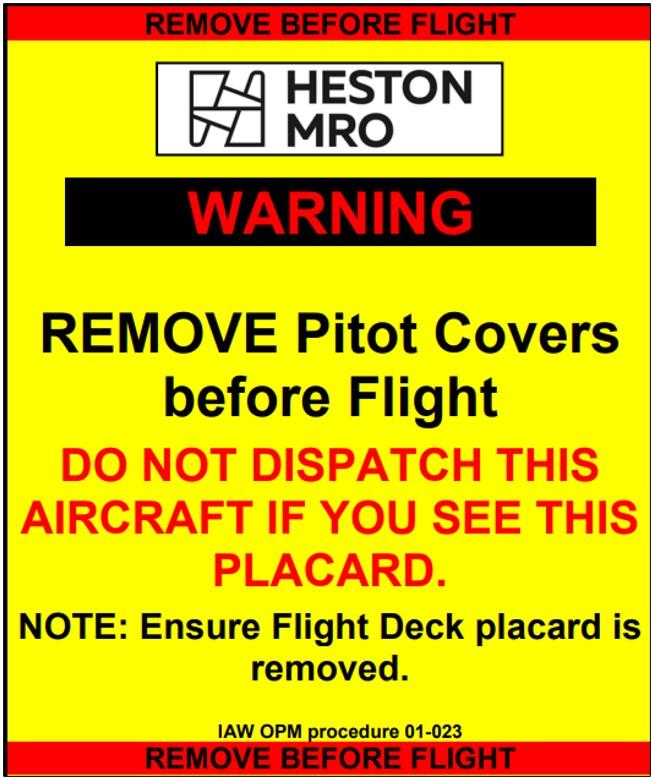
Source: Heston MRO
A review of the closed-circuit television (CCTV) footage for several Singapore Airlines turn arounds showed that the pitot covers were removed, on average about 30 minutes prior to departure, with the latest removal (other than the occurrence turnaround) being 15 minutes prior.
On the day of the occurrence, the LAME had placed the warning placard in the flight deck when the pitot covers were fitted. About 10 minutes prior to departure, CCTV footage showed that the LAME re-entered the aircraft. The LAME removed the warning placard and closed out the entry in the technical log. The CCTV footage also showed that, after leaving the aircraft, the LAME placed the placard on the dashboard of their vehicle rather than the tool control container.
The LAME stated that they had not verified that the pitot covers were removed or requested that the AME remove the covers. However, when the LAME closed out the technical log entry, they had assumed the AME had removed the covers by that time. The AME reported that they had previously been told by another LAME that they should not remove the pitot covers without being instructed to do so and therefore had not removed them.
Transit toolbox procedure
Heston MRO had a documented tool control procedure, which required maintenance personnel to:
- record the removal of company tooling from its storage location, and
- account for all tooling prior to certifying an aircraft for release to service and at the end of a shift.
It was the responsibility of the regional manager to review the movement of tooling and if any tooling was not returned to its storage location at the end of a shift it was to be recorded in a shift handover diary.
Heston MRO supplied basic tooling specific to aircraft turnarounds in a transit toolbox. This included a headset to communicate with the flight crew, marshalling wands, and a steering bypass pin[4] specific to an aircraft type. Additional items such as pitot probe covers and remove before flight placards could be added to the transit toolbox as required. The relevant procedure required the toolbox removal from its storage location be recorded, and for its return to be recorded along with a condition check of the items it contained. At the time of the occurrence, there was no requirement to check the toolbox for its contents (including pitot covers) before an aircraft was dispatched.
General tool control procedure
Heston MRO had a general tool control procedure in its operational procedures manual titled Maintenance Certifications and Certificate for Release to Service, which stated:
A certificate for release [CRS] to service will only be issued after all tooling and equipment used in the maintenance event has been accounted for and removed from the aircraft. The certifier is to ensure that the aircraft has been returned to its original airworthy state before issuing the CRS.
Turnaround inspection procedures
Introduction
There were 4 walk-around inspections required between the aircraft’s arrival and its dispatch. These were the:
- post arrival walk-around inspection conducted by maintenance personnel (sometimes incorporated into the transit check)
- external component of the transit check conducted by maintenance personnel
- external component of the pre-flight inspection conducted by one of the flight crew
- final walk-around inspection conducted by maintenance personnel (sometimes included as the final component of the transit check).
Post arrival check
The purpose of this inspection is to identify if there are any defects on the aircraft before or during the flight rather than during the post-flight ground handling functions.
Transit check
Singapore Airlines’ procedures dictated that the aircraft undergo a transit check (a type of engineering general inspection) while in Brisbane. This required certification in the technical log when completed.
The transit check procedure began with tasks mainly related to verifying the aircraft’s airworthiness, and later tasks were primarily concerned with verifying the aircraft’s general condition (that no damage had been incurred during the turnaround) and readiness for flight. The final components of that inspection included the below.
Following the aircraft refuelling, the transit check takes on a preparation for flight aspect to ensure that the aircraft is correctly configured for flight. The inspection titled Final included:
- Remove the protective covers from the aircraft (if installed).
- Record the Transit Check in the aircraft technical log. Make sure an authorized person releases the aircraft [This is the point where the LAME certifies that the transit check has been conducted].
- Ensure Technical Log, Cabin Defect Log, IFE Defect Log, all Deferred Defect Logs, Refuelling Log, Notes To Pilots and Engineers (NPE) and Maintenance Work Sheets are reviewed and completed as necessary. Ensure spare logs stowed on board [This is the point where the LAME certifies for the pitot cover removal].
- Perform final aircraft walk-around:
- Make sure that all crew doors, cargo compartment doors and service panel doors are correctly closed and secured.
- Make sure that no damage has been caused by ground equipment, during loading and/or servicing.
…
Flight crew pre-flight inspection
Singapore Airlines’ procedures stipulated that flight crew must conduct an exterior aircraft inspection (walk-around) about 30 minutes prior to departure. The procedure required that, during the walk-around, flight crew focus on safety critical areas of the aircraft to ensure:
…the general condition of the aircraft is satisfactory and that the visible aircraft components and equipment are safe for the flight…
Maintenance personnel usually inspect the aircraft before the flight. In the absence of maintenance personnel, a flight crewmember performs this walkaround before the flight. Items marked by (*) must be performed again by a flight crewmember before the flight.
The procedure required the extremities of the wings, airframe, and tail section to be inspected. Figure 7 shows the path that flight crew should take when conducting the pre-flight walk-around inspection. The numbers represent pause points to inspect a particular section of the aircraft, and each are associated with certain check items. One of the items to be checked was the condition of the pitot probes. As per the procedure, some of the items did not require checking if they were already inspected by maintenance personnel. However, the inspection path to be followed remained the same.
Figure 7: Schematic showing pre-flight walk-around path in blue with pause inspection points numbered
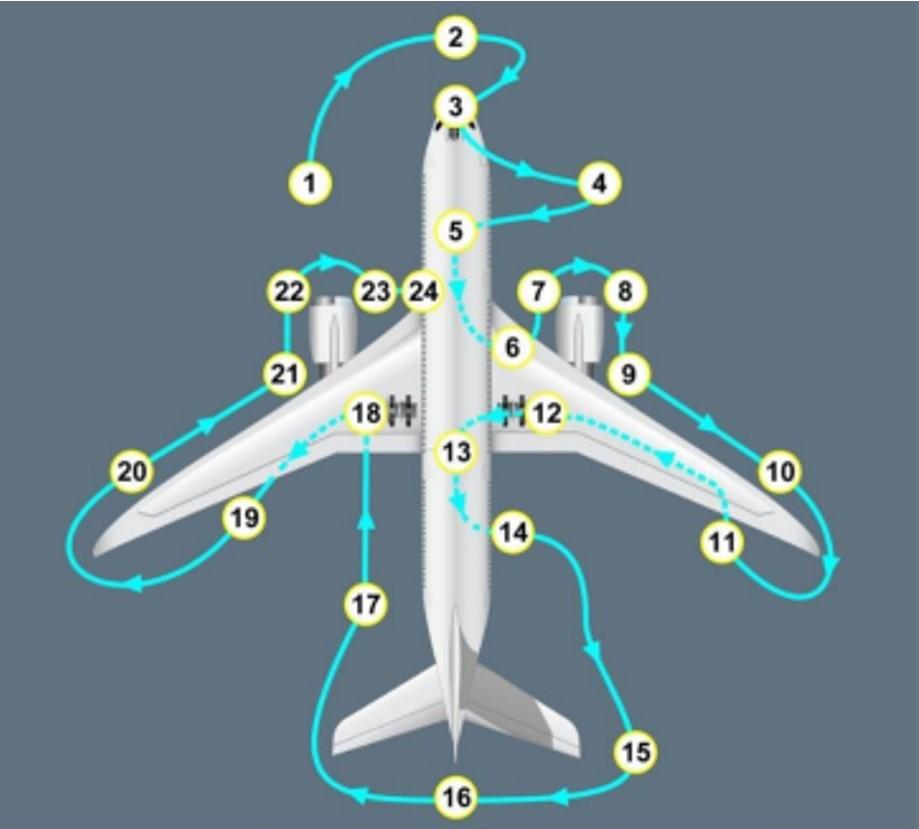
Source: Singapore Airlines
Maintenance final inspection
A final walk-around inspection of the aircraft was required by Singapore Airlines and Heston MRO procedures. The final walk-around was the responsibility of the headset/turnaround coordinator (the AME) or the turnaround supervisor (the LAME) after all the passenger and cargo doors were closed. It can be combined as part of the final transit check inspection, which was certified by the LAME. The final walk-around inspection was the last opportunity to ensure:
- there were no aircraft defects or damage
- foreign objects were not located near, in or on the aircraft
- doors and panels were secure
- all covers and pins were removed.
There was also a reference to check for pitot cover removal in the Heston MRO departure procedures for Brisbane Airport, and the training and testing documentation for dispatching an aircraft.
The AME reported that they completed the final walk-around inspection. However, a review of CCTV footage showed that, while the AME had removed the aircraft chocks, they did not complete the inspection as per the procedure. Likewise, the LAME was not observed conducting the inspection.
Review of other walk-around inspections
A review of the CCTV footage of 5 Singapore Airlines turnarounds at Brisbane Airport around the time of the occurrence showed that none of the pre-flight inspections conducted by flight crew (including the occurrence flight) followed the complete path in accordance with the above procedure. As per Table 1, some of the inspections were substantially truncated and conducted with reduced diligence. For the final engineering walk-around, the day of the occurrence was the only time observed where the inspection was not conducted by maintenance personnel.
Table 1: CCTV footage assessment for flight crew pre-flight inspections and final engineering walk-around
Flight number/date | Flight crew pre-flight walk-around | Final engineering walk-around |
SQ256 23-05-22 | Partial – Duration 3 minutes 5 seconds. On phone during part of the inspection and did not look in left engine intake. | Completed in full. |
SQ256 24-05-22 | Partial – Duration 1 minute 45 seconds. Did not inspect the outer wings, empennage or tail. | Completed in full. |
SQ256 25-05-22 | Partial – Duration 2 minutes 2 seconds. Did not inspect the left side fuselage, left outer wing or engine intake. | Completed in full. |
SQ256 26-05-22 | Partial – Duration 3 minutes 11 seconds. Did not inspect the left outer wing. | Completed in full. |
SQ256 27-05-22 (incident flight) | Partial – Duration 1 minute 45 seconds. Did not inspect the outer wings, empennage or tail. | Not carried out. |
Fatigue management
Heston MRO fatigue management program
The Heston MRO safety management system included a section on fatigue management, which stated that:
The Fatigue Management program aims to identify and assess fatigue related risks and issues within the workplace and aid in the implementation of process and procedure to manage and control fatigue.
The Fatigue Management program applies to all HESTON MRO staff and specialist maintenance providers. Fatigue is generally associated with tiredness after work or effort, either physical or mental.
Symptoms of fatigue include weakness, stress, depression, health problems and the tendency to make mistakes or errors.
Excessive hours of work, poor planning, insufficient staff, bad shift scheduling and a work environment without proper control of temperature, humidity or noise are all known to contribute to fatigue.
The Heston MRO process for the management of fatigue was divided into key areas such as:
- roster design
- hours of work
- detection and monitoring fatigue in the workplace
- identification of fatigue risks and control measures
- fatigue risks strategies
- fatigue investigation
- training.
Heston MRO utilised a web-based program to manage maximum hours per period worked and the maximum hours per day worked through the establishment of rostered cyclic rules. The rules for the design of rosters included:
- no planned shift to exceed 12 hours
- no actual (worked) shift to extend beyond 14 hours unless a risk assessment had been performed
- the hours of planned work are based on 38 hours per week, 76 hours per fortnight and/or 152 hours per month
- shift start times to move forward from one day to the next, that is, early starts and then progress through to starting in afternoons
- a requirement for a 10-hour minimum stand-down period between shifts.
The requirements above were incorporated into the design of rosters with the aim of an equal distribution of work hours among employees and the tracking of hours worked for fatigue management purposes.
Heston MRO management responsibilities and accountabilities
In accordance with the Heston MRO fatigue management program, the person in the role of regional manager was responsible for ensuring:
- All employees were provided with rostered shifts within the fatigue risk management guidelines.
- Employees were aware of the fatigue management procedures and familiar with their responsibilities and accountabilities. In addition, if an employee was required to work beyond the fatigue management guidelines an appropriate risk assessment was performed, with mitigation strategies implemented.
- That the hours of work were monitored to include overtime, shift allocation and shift changes with the aim of preventing unacceptable levels of fatigue accrual.
- Where there was an operational need to extend shift hours or alter personnel shift patterns, the regional manager was required to perform a risk assessment, implement mitigating strategies in consultation with the human resources manager. The human resources manager provided oversight governance to ensure compliance with legislative requirements.
Noting that the LAME/regional manager was conducting dual roles, the ATSB asked Heston MRO if their total work hours were monitored in accordance with the fatigue management policy. They stated:
[The LAME] is hired as and has the position of [Regional] Manager. As the manager, [the LAME] is required to manage the fatigue levels of all [their] subordinates, and this includes [themselves].
[They] do not sign in/out of work and there is no time monitoring.
[They] are asked regularly about ensuring [they] are receiving sufficient rest – and if [they] are not – to ensure that [they] gets some.
The ATSB further asked if other personnel had dual roles and if all their hours were tracked for fatigue monitoring purposes. Heston MRO indicated that, at the time of the occurrence they had a total of 4 employees who had dual management and aircraft operational roles whose total hours were not monitored for fatigue management purposes. However, all other LAMEs and AMEs not undertaking dual roles had their hours tracked.
During the week of the incident, the LAME/regional manager conducted 2 shifts amounting to about 17 hours on the same day to cover for a LAME who was absent from work. While the LAME/regional manager notified the Quality and Safety manager about the extra shift, a risk assessment was not conducted as per the company’s fatigue management program.
ATSB SafetyWatch - Fatigue management
The SafetyWatch is a set of broad safety concerns that the ATSB has identified through investigation findings and from occurrence data reported by industry. At the time of this report, the ATSB had identified fatigue management as a safety concern and stated:
Despite increased awareness across the transport sector, fatigue remains one of the most relevant ongoing concerns for safe transport. Fatigue impairment has been identified as a contributory factor in numerous aviation, maritime and rail accidents.
Human fatigue is a condition primarily caused by inadequate or bad sleep, or by staying awake for too long. Things like underlying health conditions, medication, and stress can amplify the likelihood and effects of fatigue.
Fatigue can have a range of adverse effects on human performance, including:
- decreased short-term memory
- slowed reaction time
- decreased work efficiency
- reduced motivational drive
- increased variability in work performance
- increased errors of omission
- increased risk tolerance.
These symptoms can occur before an individual experiences the “feeling” of fatigue.
Related occurrence
ATSB investigation (AO-2018-053)
On 18 July 2018, a Malaysia Airlines Airbus A330, registered 9M-MTK, took off on a regular public transport flight from Brisbane, Queensland to Kuala Lumpur, Malaysia. As the covers had been left on the aircraft’s 3 pitot probe’s, the instruments showed a red speed flag in place of the airspeed indication from early in the take‑off, and unrealistically low airspeeds afterwards. The flight crew did not respond to the speed flags until the aircraft’s speed was too high for a safe rejection of the take-off, and the take‑off was continued.
The ATSB investigation subsequently identified safety factors across a range of subjects including flight deck and ground operations, aircraft warning systems, air traffic control, aerodrome charts, and risk and change management. The report safety message stated:
The loss of airspeed data due to mud wasp ingress can occur even after brief periods, and the use of pitot probe covers for aircraft turnarounds at Brisbane is largely an effective defence. However, it introduces another risk, which is the potential for aircraft to commence a take-off with pitot probe covers still fitted…
As a result of the investigation, a safety issue for Aircraft Maintenance Services Australia (rebranded to Heston MRO in 2019) was identified:
Aircraft Maintenance Services Australia did not have a reliable method to account for tooling and equipment (such as pitot probe covers) prior to aircraft dispatch when providing non-certifying engineering support.
In February 2022, in response to the safety issue, Heston MRO advised that it had implemented a procedure for all toolboxes taken to aircraft. Based on the below, the ATSB closed this safety issue. The procedure required that:
All toolboxes (including the transit toolboxes) will carry a notebook inside the box.
The above notebook will have the below drawn table.
An audit of the contents of the toolbox will be carried out and signed for prior to the use of any of the contents from the toolbox.
After all work on the aircraft and prior to pushback – the contents of the toolbox will be re-audited and signed for to ensure all contents have been returned to the box.
It should be noted that, at the time of this occurrence in May 2022, the procedure described above was not utilised or implemented as advised.
In addition to the above, the ATSB’s investigation also identified the following findings regarding the conspicuity of the pitot probe covers and inspections:
Although suitable for use in most situations, the streamers attached to the pitot probe covers supplied and used for A330 operations by Aircraft Maintenance Services Australia provided limited conspicuity due to their overall length, position above eye height, and limited movement in wind. This reduced the likelihood of incidental detection of the covers, which is important during turnarounds.
Malaysia Airlines flight crew and engineers did not fully complete the required aircraft inspections.
The Malaysia Airlines engineer did not perform a final walk-around inspection of the aircraft, including a check for pitot probe covers, as required by the transit check that the engineer had certified as complete. The engineer assumed that the walk-around would be completed by the support engineer and/or ground handlers.
Safety analysis
Introduction
A Singapore Airlines Airbus A350-941 aircraft was being prepared for a regular public transport flight from Brisbane Airport, Queensland to Changi Airport, Singapore. Just prior to the aircraft being pushed back for departure, a refueller on an adjacent bay noticed that the pitot probe covers were still fitted. The refueller informed the licenced aircraft maintenance engineer (LAME) responsible for the aircraft turnaround and the covers were subsequently removed just before pushback.
This analysis will discuss the actions of maintenance personnel regarding the removal of the pitot probe covers prior to pushback and incomplete walk-around inspections by both maintenance and flight crew. It will also consider tooling control procedures and the conspicuity of the pitot probe covers used. The LAME’s workload and fatigue management of personnel with dual roles will also be examined.
Pitot cover installation and removal procedures
As per the procedure, on arrival of the aircraft at Brisbane, a warning placard was placed on the flight deck and a corresponding entry made in the technical log indicating that the pitot probe covers had been fitted. Prior to departure, the placard was to be removed and the log entry was to be closed once the pitot covers had been taken off. While there was a procedure in place that was designed to ensure that pitot cover removal had occurred, on this occasion, the LAME reported that they had assumed rather than verifying that the covers were removed by the AME. However, the AME, who was new to the organisation, had been told that they were not to remove the covers without instruction from a LAME. While there was no communication from the LAME either to instruct the AME to remove the covers or to visually check that they had been removed, the LAME certified the log entry as completed. Likewise, the closed-circuit television (CCTV) footage showed that the LAME had removed the placard and placed it in their work vehicle, although the covers remained fitted to the aircraft.
Transit toolbox procedure
The primary function of tool control is to prevent tooling remaining on board (or fitted to) an aircraft prior to its departure. Its secondary function is to account for tooling as an asset. The Heston MRO tool control requirements at the time of the occurrence for the transit toolbox were not a reliable means to account for tooling (such as pitot probe covers) prior to aircraft dispatch. This was due to the procedural checks for toolbox contents (including pitot covers and the warning placard) being carried out when returning the tooling at the end of a shift, rather than prior to aircraft dispatch. Therefore, the transit toolbox procedure was not an effective method of tool control, but rather, a check for inventory at the end of a shift.
Tool control was highlighted as a safety issue following a previous incident investigated by the ATSB (AO-2018-053). At the time of drafting the final report into that incident (March 2022) Heston MRO (previously AMSA) advised the ATSB that the tool control procedure had been changed to incorporate a requirement to check for the contents of the transit toolbox before pushback. That safety enhancement was accepted by the ATSB, and the safety issue was closed. However, at the time of this occurrence (May 2022), the ATSB identified that the tool control procedure remained unchanged. Therefore, the same safety issue has been identified as a result of this investigation.
There was a company requirement for a general post‑maintenance tool control check. However, tools used for line maintenance, turnaround and ground handling of aircraft require specific controls to ensure they have been accounted for prior to flight. Had there been a robust tool control procedure in place for the transit toolbox contents, such as the one previously identified by Heston MRO, then it was likely that the pitot covers would have been identified as missing from the transit toolbox and removed in a timely manner, prior to pushback.
Maintenance personnel final walk-around
The LAME left the bay to refuel another aircraft, leaving the relatively inexperienced AME (on aircraft type and at Heston MRO) to dispatch the aircraft by themselves. The AME reported that they completed the final walk-around, however, the closed-circuit television footage showed that they had removed the aircraft chocks but had not completed the inspection as per the procedure. Likewise, and consistent with the footage, the LAME reported that they did not conduct the inspection as they had assumed this had been completed by the AME as part of their headset coordinator responsibilities.
The final walk-around represented the last procedural opportunity to identify that the aircraft was correctly configured for flight with all panels and doors closed, pins and covers removed. Given the AME’s limited experience, direct supervision would have been prudent until such time as the LAME was satisfied that the AME could conduct the turnaround functions effectively. Irrespective, had a final inspection been conducted, it was likely that the pitot covers would have been identified as it was one of the check items in the final walk-around procedure.
Flight crew pre-flight walk-around inspection
Much like final walk-around inspections, flight crew pre-flight inspections are an important risk control to ensure that the aircraft is prepared and configured for flight. If inspections are not done correctly, it increases the risk of defects not being identified and/or the aircraft not being correctly configured for flight.
The closed-circuit television footage of 5 Singapore Airlines turnarounds showed that none of the pre‑flight inspections were completed in full by flight crew in accordance with the company procedure. The pre-flight walk-around inspection was generally conducted about 30 minutes prior to departure. As the pitot probe covers were not required to be removed until 20 minutes prior, the flight crew could expect to see the covers fitted during their inspection. Despite this, pre-flight inspections need to be completed in full and with careful diligence. Each one needs to be conducted with the mindset that it may be the sole opportunity to detect damage or other irregularities and confirm the aircraft’s readiness for flight.
Licenced aircraft maintenance engineer workload and Heston MRO fatigue management
The LAME reported that the workload associated with the dual role of LAME/regional manager had become considerably more demanding post the COVID-19 pandemic This was consistent with observations made by their family and friends, and from their 72-hour work history, which showed some long days including a double shift. Consequently, they were constantly moderately tired.
In addition, while Heston MRO had a fatigue management policy in place, 4 employees who had combined management and operational duties (including the LAME) did not have all their work hours tracked and assessed for fatigue calculation purposes. Therefore, aside from an individual self-reporting, Heston MRO could not assess or assure that those employees were not experiencing the negative effects of elevated fatigue levels. Fatigue has been shown to significantly raise the likelihood of errors and omissions and increase the risk of an incident involving those personnel. While the LAME worked significant hours outside the normal roster periods, the ATSB was unable to accurately determine if they were experiencing a level of fatigue that may have contributed to the occurrence. Regardless, without appropriate tracking of their hours, Heston MRO had no way of knowing if the LAME (and others) were experiencing high levels of fatigue.
Pitot probe cover characteristics
The purpose of a ‘remove before flight’ streamer, attached to an item of ground support equipment such as a pitot probe cover, is to gain the attention of someone who is not primarily looking for the equipment. Several characteristics contribute to the conspicuity of streamers including the colour and length. The streamers attached to the pitot probe covers provided by maintenance personnel were relatively short, and when fitted, were about 3 m above eye height, which may be difficult to detect.
As highlighted in the ATSB’s previous investigation, a human’s perceptual system is sensitive to motion, particularly in their peripheral vision (McKee and Nakayama 1984; Wickens and others 2013). A shorter streamer may not necessarily attract a person’s attention, particularly if they are not focussed on that area, but strong winds may occasionally drag the covers off with a longer stream. Operators need to balance the likelihood of this occurring against the need to ensure their removal before flight through the use of longer streamers.
While the maintenance personnel responsible for the aircraft departure did not conduct a final aircraft walk-around inspection, the limited conspicuity of the pitot probe covers used reduced the likelihood of incidental detection of the covers. There are incidental opportunities that arise for ground crews to notice pitot probe covers while conducting unrelated tasks such as attaching a tug and pushing the aircraft back, or in this case, the refueller working on an adjacent bay. The likelihood of this incidental detection is increased with the use of larger or brighter streamers that hang into the view of ground staff, particularly in positions that are closer to the aircraft. This is especially important when there are increased time pressures and fewer opportunities for their removal during turnarounds.
Refueller identification of pitot probe covers
For this occurrence, it was an incidental detection made with a wider view of the aircraft by a refueller working on an adjacent bay that led to the identification of the covers. The immediate action of the refueller by advising the LAME ensured that the covers were removed prior to pushback, thereby preventing the flight crew commencing a take-off with erroneous or absent airspeed indications.
Findings
ATSB investigation report findings focus on safety factors (that is, events and conditions that increase risk). Safety factors include ‘contributing factors’ and ‘other factors that increased risk’ (that is, factors that did not meet the definition of a contributing factor for this occurrence but were still considered important to include in the report for the purpose of increasing awareness and enhancing safety). In addition ‘other findings’ may be included to provide important information about topics other than safety factors. Safety issues are highlighted in bold to emphasise their importance. A safety issue is a safety factor that (a) can reasonably be regarded as having the potential to adversely affect the safety of future operations, and (b) is a characteristic of an organisation or a system, rather than a characteristic of a specific individual, or characteristic of an operating environment at a specific point in time. These findings should not be read as apportioning blame or liability to any particular organisation or individual. |
From the evidence available, the following findings are made with respect to the flight preparation event involving Airbus A350-941 registered 9V-SHH at Brisbane Airport, Queensland, on 27 May 2022.
Contributing factors
- The licenced aircraft maintenance engineer certified for the removal of the pitot covers in the technical log and removed a warning placard from the flight deck without visual or verbal confirmation that the pitot covers had been removed.
- Heston MRO had not yet implemented a previously proposed and accepted method to account for tooling and equipment (such as pitot probe covers) prior to aircraft pushback. (Safety issue)
- Maintenance personnel responsible for the aircraft departure did not conduct a final aircraft walk-around inspection. That inspection was the last procedural opportunity to identify that the pitot covers had not been removed.
Other factors that increased risk
- The licenced aircraft maintenance engineer was undertaking dual roles as both regional manager and engineer. This increased the risk of a fatigue-related maintenance error occurring as a result of a significantly expanded workload in the months that preceded this incident.
- Heston MRO did not track the work-related hours of personnel with dual management and operational roles (including the licenced aircraft maintenance engineer) for fatigue calculation purposes. Therefore, there was an increased risk of a fatigue‑related incident involving those personnel. (Safety issue)
- The majority of Singapore Airlines flight crews (observed around the time of the incident) did not fully complete the required pre-flight walk-around inspections. (Safety issue)
- Although suitable for use in most situations, the streamers attached to the pitot probe covers used for the Airbus A350 operations at Brisbane Airport provided limited conspicuity due to their overall length, position above eye height, and limited movement in wind. This reduced the likelihood of incidental detection of the covers, which is important during turnarounds. (Safety issue)
Other findings
- The refueller on an adjacent bay identified that the pitot covers were still fitted and advised maintenance personnel to ensure that they were removed prior to pushback.
Safety issues and actions
Central to the ATSB’s investigation of transport safety matters is the early identification of safety issues. The ATSB expects relevant organisations will address all safety issues an investigation identifies. Depending on the level of risk of a safety issue, the extent of corrective action taken by the relevant organisation(s), or the desirability of directing a broad safety message to the aviation industry, the ATSB may issue a formal safety recommendation or safety advisory notice as part of the final report. All of the directly involved parties were provided with a draft report and invited to provide submissions. As part of that process, each organisation was asked to communicate what safety actions, if any, they had carried out or were planning to carry out in relation to each safety issue relevant to their organisation. The initial public version of these safety issues and actions are provided separately on the ATSB website, to facilitate monitoring by interested parties. Where relevant, the safety issues and actions will be updated on the ATSB website as further information about safety action comes to hand. |
Tool control issues
Safety issue number: AO-2022-032-SI-01
Safety issue description: Heston MRO had not yet implemented a previously proposed and accepted method to account for tooling and equipment (such as pitot probe covers) prior to aircraft pushback.
Fatigue levels not monitored
Safety issue number: AO-2022-032-SI-02
Safety issue description: Heston MRO did not track the work-related hours of personnel with dual management and operational roles (including the licenced aircraft maintenance engineer) for fatigue calculation purposes. Therefore, there was an increased risk of a fatigue related incident involving those personnel.
Ineffective pre-flight inspections
Safety issue number: AO-2022-032-SI-03
Safety issue description: The majority of Singapore Airlines flight crews (observed around the time of the incident) did not fully complete the required pre-flight walk-around inspections.
Pitot probe cover streamers
Safety issue number: AO-2022-032-SI-04
Safety issue description: Although suitable for use in most situations, the streamers attached to the pitot probe covers supplied and used for A350 operations by Heston MRO at Brisbane Airport provided limited conspicuity due to their overall length, position above eye height, and limited movement in wind. This reduced the likelihood of incidental detection of the covers, which is important during turnarounds.
Safety action not associated with an identified safety issue
Whether or not the ATSB identifies safety issues in the course of an investigation, relevant organisations may proactively initiate safety action in order to reduce their safety risk. All of the directly involved parties are invited to provide submissions to this draft report. As part of that process, each organisation is asked to communicate what safety actions, if any, they have carried out to reduce the risk associated with this type of occurrences in the future. The ATSB has so far been advised of the following proactive safety action in response to this occurrence. |
Additional safety action Heston MRO
Heston MRO has advised the ATSB that they have implemented an additional procedure, which required the placement of a warning placard on the communications panel where the ground headset connects to (Figure 8).
Figure 8: Warning placard fitted to the ground communication panel
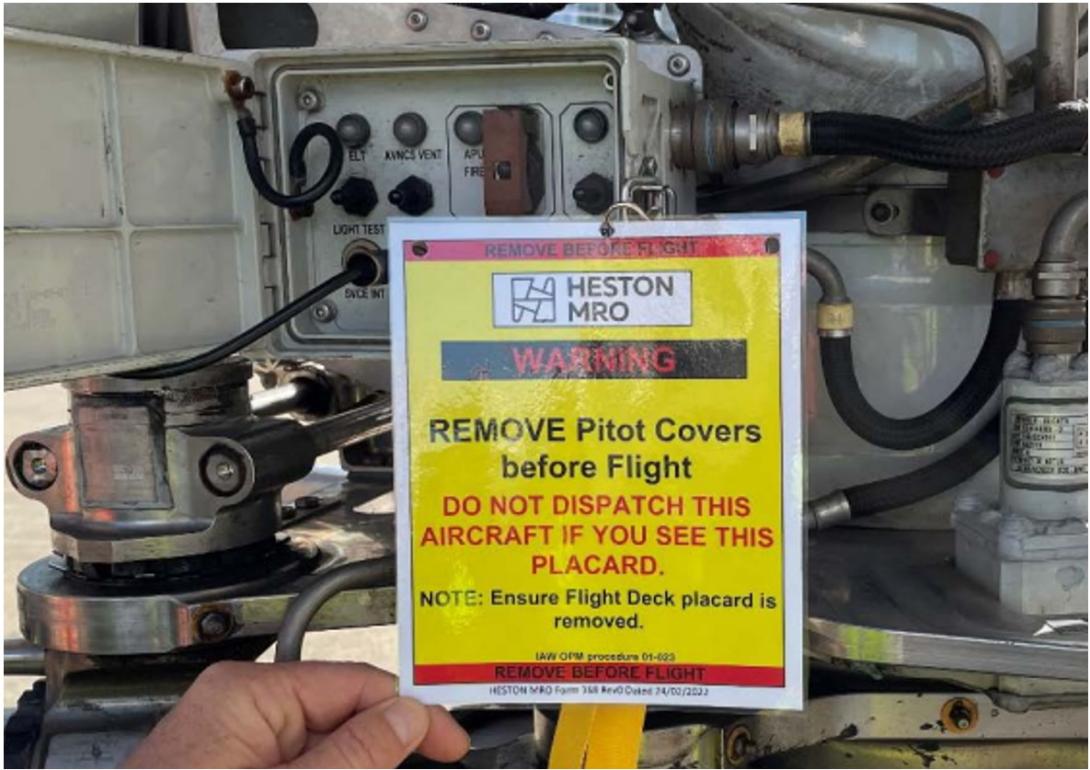
Source: Heston MRO
Glossary
AME | Aircraft maintenance engineer |
CCTV | Closed-circuit television |
LAME | Licenced aircraft maintenance engineer |
Sources and submissions
Sources of information
The sources of information during the investigation included:
- the aircraft refueller
- the licenced aircraft maintenance engineer
- the aircraft maintenance engineer
- Heston MRO
- Singapore Airlines
- Brisbane Airport Corporation
- Closed-circuit television footage.
References
Airbus (2016) ‘Pitot probe performance covered on the ground’, Safety First, July, 22: 6–13.
McKee, S. P., & Nakayama, K. (1984). The detection of motion in the peripheral visual field. Vision Research, 24(1), 25–32.
Wickens, CD, Hollands, JG, Banbury, S and Parasuraman, R (2013) Engineering psychology and human performance, 4th Ed. Pearson, United States.
Submissions
Under section 26 of the Transport Safety Investigation Act 2003, the ATSB may provide a draft report, on a confidential basis, to any person whom the ATSB considers appropriate. That section allows a person receiving a draft report to make submissions to the ATSB about the draft report.
A draft of this report was provided to the following directly involved parties:
- aircraft refueller
- licenced aircraft maintenance engineer
- aircraft maintenance engineer
- Heston MRO
- Singapore Airlines
- Brisbane Airport Corporation
- Civil Aviation Safety Authority.
Submissions were received from:
- Heston MRO
- Singapore Airlines.
The submissions were reviewed and, where considered appropriate, the text of the report was amended accordingly.
Purpose of safety investigationsThe objective of a safety investigation is to enhance transport safety. This is done through:
It is not a function of the ATSB to apportion blame or provide a means for determining liability. At the same time, an investigation report must include factual material of sufficient weight to support the analysis and findings. At all times the ATSB endeavours to balance the use of material that could imply adverse comment with the need to properly explain what happened, and why, in a fair and unbiased manner. The ATSB does not investigate for the purpose of taking administrative, regulatory or criminal action. TerminologyAn explanation of terminology used in ATSB investigation reports is available here. This includes terms such as occurrence, contributing factor, other factor that increased risk, and safety issue. Publishing informationReleased in accordance with section 25 of the Transport Safety Investigation Act 2003 Published by: Australian Transport Safety Bureau © Commonwealth of Australia 2024 ![]() Ownership of intellectual property rights in this publication Unless otherwise noted, copyright (and any other intellectual property rights, if any) in this report publication is owned by the Commonwealth of Australia. Creative Commons licence With the exception of the Coat of Arms, ATSB logo, and photos and graphics in which a third party holds copyright, this publication is licensed under a Creative Commons Attribution 3.0 Australia licence. Creative Commons Attribution 3.0 Australia Licence is a standard form licence agreement that allows you to copy, distribute, transmit and adapt this publication provided that you attribute the work. The ATSB’s preference is that you attribute this publication (and any material sourced from it) using the following wording: Source: Australian Transport Safety Bureau Copyright in material obtained from other agencies, private individuals or organisations, belongs to those agencies, individuals or organisations. Where you wish to use their material, you will need to contact them directly. |
[1] Headset duties, also called turn around coordination, involved communicating between the ground and flight deck via a headset connected in the nose area of the aircraft.
[2] Pitot probes provide air data computers and flight instruments with airspeed information and are ineffective if covered or blocked. The term pitot probes also include the multi-function probes fitted to the Airbus A350, which measure total pressure, total air temperature and angle of attack measurements.
[3] Pushback: using a tug to push an aircraft backwards from the terminal so that it can then taxi under its own power.
[4] A steering bypass pin when fitted to an aircraft allows it to be manoeuvred on the ground.