Investigation summary
What happened
On 3 March 2022, the pilot of a Cessna U206G, registered VH-JVR and operated by MAGSPEC Aviation Pty Ltd, was conducting a low-level geophysical survey, about 120 km west of Norseman, Western Australia. Recorded data showed the first survey line commenced at 1252 local time, and the aircraft’s last recorded position occurred at 1343, in the survey area.
At about 1430, the ground operator observed that the satellite tracking system was no longer reporting the aircraft’s position, and they were subsequently unable to contact the pilot. When the aircraft failed to return to Kalgoorlie by its estimated arrival time of 1630, a search was initiated. At about 1852, the wreckage was located 3.2 km west of the aircraft’s last recorded position. The injured pilot had extricated themselves from the wreckage but shortly after succumbed to their injuries. The aircraft was destroyed.
What the ATSB found
The ATSB found it was likely that, during a manoeuvre to intercept the next survey line, for undetermined reasons, control of the aircraft was lost at a height from which recovery was not possible. While an aerodynamic stall situation was a plausible explanation for the loss of control, this remained only a possibility due to the lack of recorded data beyond the last known position of the aircraft and no witness observations.
Although the aircraft’s satellite tracking system had stopped at 1343, an emergency response was not initiated until 1700. This was in accordance with the operator’s emergency response plan, in which a search and rescue response was to commence 30 minutes after the estimated time for arrival. However, an earlier response was very unlikely to have altered the outcome due to the extent of the pilot’s injuries. Minimising the time for a search and rescue is essential to increasing the chances of a successful outcome in the event of an accident.
In accordance with the operator’s training, its pilots routinely used high angle of bank (45–60°) turns at low level to manoeuvre between survey lines. Steep turns at low level increases the risk of an aerodynamic stall from which a recovery may not be possible. ATSB analysis of the available satellite tracking data identified that, although the pilot was conducting steep turns, they had flown the previous 24 turns without incident.
The pilot was not wearing any protective clothing or a helmet nor were they required to do so by the operator. Wearing of such items has been recommended by industry bodies, as they may offer some protection in the event of an accident, particularly from fire but also as environmental protection following an accident.
The ATSB identified that the operator’s risk management processes did not include a pre‑operational risk assessment that considered the generic risks and hazards common across their low‑level survey operations. Further, a risk register was not maintained, which limited the operator’s ability to track, monitor, and mitigate all known hazards, and assess the effectiveness of the existing risk controls.
Also, the operator trained its pilots to routinely fly survey patterns utilising steep turns at low level. However, the procedures or limitations specific to these manoeuvres were not included in the operations manual. It was also noted that, the operator’s aircraft were fitted with a satellite tracking system, but there was no requirement nor supporting procedures to confirm the set‑up and functionality of the system prior to flight.
Although not contributory, the ATSB identified that the regulatory oversight of the operator had not specifically examined the primary activity of low‑level geophysical survey flights or the processes and procedures designed to mitigate any associated risks.
What has been done as a result
MAGSPEC Aviation has consolidated its manuals, with its health, safety and environmental management system manual incorporated into its operations manual. In addition, it has implemented a range of measures regarding its low‑level survey operations including:
- an updated job safety analysis, which provides for the consideration of likelihood, consequence and details of any risk mitigations
- procedures for the use of satellite tracking including a requirement for a pre-flight check
- conduct of procedure turns including how the turns should be flown, with minimum speeds indicated and what to do if those speeds could not be achieved
- the requirement for fixed emergency locater transmitters on all aircraft, and limitations for flight if the unit is unserviceable or not present
- updating its low-level training syllabus to include specific parameters (which mimic its previous practical training), so that competency can be formally assessed against those parameters.
MAGSPEC Aviation has also advised it no longer operates at survey heights below 30 m above ground level and it provides its pilots with an individually registered portable locator beacon, which they are required to wear on their person. It is also progressing operational amendments to enable Flight Safety Foundation’s Basic Aviation Risk Standard accreditation.
Safety message
Geophysical survey operations are generally conducted at low level, necessitated by the requirement for high quality, accurate data acquisition. This creates a high‑risk operating environment that requires effective risk management.
Risk management should include a pre‑operational risk assessment to consider hazards and risks common to an operation. This can then be used to inform the management of risk for specific taskings and assist in developing appropriate mitigations. Tools such as a risk register can assist an organisation to effectively monitor its risk profile and continually improve its risk mitigation strategies.
Policy and procedures form part of effective risk mitigation strategies and will establish safety and the operating standards to be met and maintained. Documented policies and procedures can ensure the correct set‑up and functionality of operating equipment and systems. It can also minimise opportunities for deviation from an operator’s expectations and the erosion of safety margins.
This accident further highlighted that regulatory oversight activities should ensure that an operator’s primary activity is examined in sufficient detail. Not doing so potentially limits the opportunity to assess an operator’s ability to manage the risks associated with its proposed operations.
The occurrence
On 3 March 2022, a Cessna Aircraft Company U206G aircraft, registered VH-JVR, was being operated by MAGSPEC Aviation Pty Ltd for low-level, geophysical survey flights of an area about 120 km west of Norseman, Western Australia (Figure 1).
The aircraft was based at Kalgoorlie for this survey task along with 2 pilots and a ground operator. One pilot would operate the aircraft in the morning and the other in the afternoon. The ground operator was responsible for the technical and logistical aspects of the survey.
At about 1125 local time, at the completion of the morning survey flight, the aircraft was returned to Kalgoorlie. The second pilot commenced their pre‑flight preparations at about 1130 and discussed the morning survey flight with the returning pilot. That pilot advised of a minor concern about a fuel imbalance that developed during the approximate 4‑hour flight, however, they did not report any impact on aircraft handling or engine operation.
The ground operator prepared the survey equipment and assisted the pilot to fully fuel the tanks.
Figure 1: VH-JVR's operating area in proximity to Kalgoorlie and Norseman
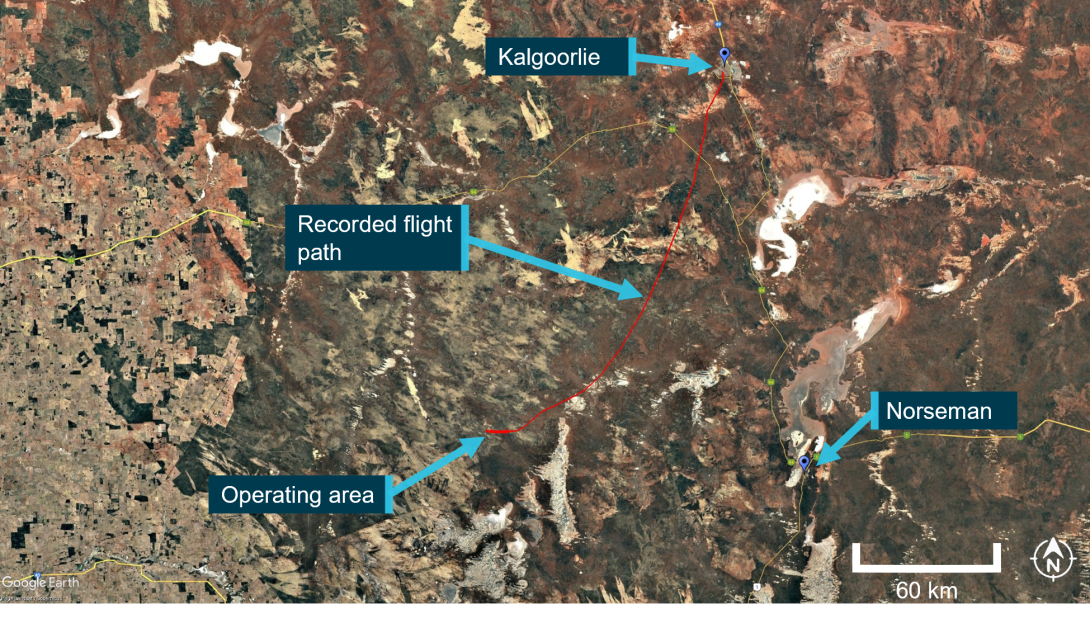
Source: Operator’s satellite tracking data, overlaid on Google Earth, annotated by the ATSB
At about 1200, the aircraft departed for the survey area with the pilot as the sole occupant. Recorded GPS data showed that the first survey line was commenced at about 1252, picking up where the morning survey flight had been completed. The last position uploaded to the tracking system was at 1343, which showed the aircraft was on a westerly heading at a ground speed of 116 kt and a GPS height of 1,398 ft above mean sea level in the target survey area.
At about 1430, the ground operator checked the satellite tracking system for VH‑JVR and noted that the aircraft’s position was no longer being reported on the system. The satellite tracking system had the ability to automatically alert the operator 15 minutes after tracking data was no longer being uploaded to the system’s servers. The operator reported they did not receive an automatic alert.
The ground operator then attempted unsuccessfully to call and text the pilot’s mobile phone. Although the aircraft carried a satellite phone as part of its survival kit, it was not routinely switched on during operations. The ground operator then advised the operations manager, who directed them to continue the attempts at making contact and prepare the ground vehicle for a potential response. Further attempts at contact were unsuccessful and the operations manager directed that no further action could be taken other than to monitor the situation and wait until the aircraft’s estimated time of arrival at Kalgoorlie.
The aircraft did not return to Kalgoorlie by the estimated time of arrival of 1630. At 1700, in accordance with its emergency response plan, the operator contacted the Australian Maritime Safety Authority’s Joint Rescue Coordination Centre (JRCC). Another company aircraft and pilot that was at Norseman was dispatched by the operator to VH-JVR’s last known position, however, the pilot was not able to locate the aircraft.
The JRCC initiated a search and rescue operation at 1739. The aircraft wreckage was located at 1852, approximately 3.2 km west of its last recorded position (Figure 2). The search aircraft’s crew were unable to establish communications with the pilot of VH‑JVR. The JRCC also deployed a rescue helicopter to the site, and at 0042, they found the pilot, fatally injured a short distance from the wreckage.
Figure 2: VH-JVR's accident site location and last recorded position
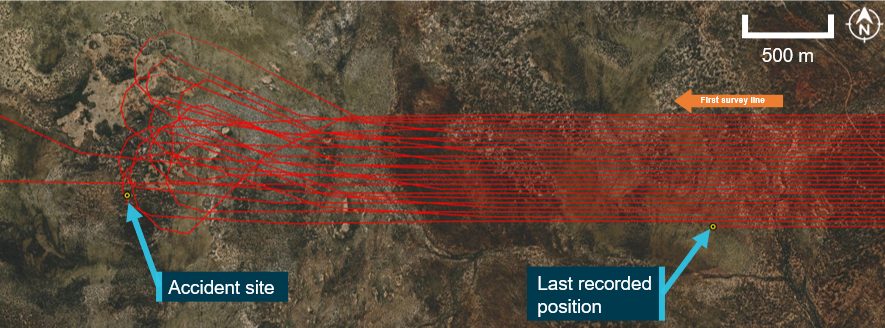
Source: Operator’s satellite tracking data, overlaid on Google Earth, annotated by the ATSB
Context
Pilot information
Qualifications and experience
The pilot held a commercial pilot licence (aeroplane) issued in 2014 and a valid class 1 aviation medical certificate. They held a multi‑engine aeroplane instrument rating and a grade 3 instructor rating, although neither were current, nor were they required to be.
At the time of the accident, the pilot had about 1,822 hours total aeronautical experience, of which about 570 hours were with the operator, primarily in Cessna 210 aircraft. The pilot had accrued over 350 hours on Cessna 206 aircraft prior to joining the operator and had about 12 hours on VH‑JVR.
The pilot commenced and completed a low‑level (aeroplane) rating in June 2021, which comprised 6.7 hours of dual training in a Cessna 152 aircraft, including a flight test. In July 2021, the pilot then commenced low‑level survey training with the operator in a Cessna 210 aircraft. The pilot’s logbook detailed 5 initial training survey flights totalling 18.6 hours. These were followed by about 21 hours of solo low‑level survey, culminating in a check flight of 5.6 hours.
The chief pilot (CP) conducted the pilot’s low‑level survey training and their geophysical survey operations check flight. The CP reported that the pilot ‘was one of those pilots who picked it up very quickly’ and was ‘very switched on’. In total, the pilot had conducted about 500 hours of low‑level survey operations.
Although the pilot had previously flown high‑level surveys, MAGSPEC Aviation was the first operator that the pilot had flown low‑level surveys for. The operator also reported that the pilot had been recently offered and had accepted the role of deputy chief pilot/deputy head of operations.
Recent history
The pilot had been on leave since 23 February 2022. The pilot’s partner reported that, on 1 March 2022, the pilot woke at about 0700, went to bed at about 1930–2000 and did not fly that day. On 2 March 2022, the day prior to the accident, the pilot woke at 0400 and arrived at Perth Airport at 0500 to take a scheduled passenger flight to Geraldton, where VH‑JVR had been undergoing scheduled maintenance. The pilot then ferried the aircraft about 700 km to Kalgoorlie, arriving around midday. Later that day, the pilot accompanied the second company pilot assigned to the survey area on a 30–40 minute local flight to familiarise the second pilot with VH‑JVR, as they had not previously flown that aircraft.
The pilot’s partner received a text message from the pilot at 1922, advising that they were cooking dinner in their accommodation and had no plans to go out that night. There was no further evidence of the pilot’s activities prior to the accident flight, but the pilot usually woke around 0600–0630, exercised and studied in the mornings before conducting the afternoon survey flight.
The day of accident was the first day of that survey task. Neither the other pilot nor the ground operator expressed any concern for the pilot. Based on the available recent history, there was no evidence the pilot was likely experiencing a level of fatigue at the time of the accident.
Aircraft information
General
The Cessna Aircraft Company U206G Stationair was a high‑wing, fixed tricycle undercarriage aircraft powered by a single Continental IO‑520‑F piston engine, with a 3‑bladed constant speed propeller. VH‑JVR was manufactured in 1978 in the United States and was first registered in Australia in 1998. The aircraft was acquired by the operator in 2021.
Factory fitted standard equipment included:
- a vane‑type aerodynamic stall[1] warning system in the leading edge of the left wing designed to activate the audible warning horn 5–10 kt above the stall speed in all configurations
- 2 vented fuel wing tanks, which were an integral part of the metal wing structure[2] and supplied fuel via gravity feed to 2 reservoir tanks, and a fuel selector valve with selections for LEFT, RIGHT and OFF
- 3-point safety harness restraints.
Modifications
In October 2021, VH‑JVR had been modified and equipped to conduct geophysical survey operations in accordance with engineering orders approved by a Civil Aviation Safety Authority (CASA) authorised aeronautical engineer and supplemental type certificates.[3] These modifications included:
- A magnetometer boom installed at the rear of the aircraft and associated survey equipment, with its own power supply, mounted in the rear cabin.
- A fuel selector valve, which enabled the selection of LEFT/BOTH/RIGHT with a pull‑out fuel shut off valve installed to cut off fuel flow.
- A survey data acquisition and navigation system, which included flight path guidance via a digital display mounted on top of the instrument panel, allowing the pilot to monitor aircraft position in relation to the pre-programmed survey lines.[4]
- A 4-point inertia safety restraint harness.
Maintenance
The aircraft was being maintained by an approved maintenance organisation in accordance with the CASA maintenance schedule 5 and regulatory requirements. The last periodic inspection was completed on 2 March 2022 at 7,982.4 hours total time‑in‑service. The current maintenance release was not recovered and likely destroyed in the post‑impact fire. A review of previous maintenance releases and maintenance records did not identify any major repairs or recurring airworthiness issues with the aircraft.
Emergency locator transmitter
Civil Aviation Safety Regulations (CASR) 1998 Part 91 General operating and flight rules Manual of Standards (MOS) required that VH‑JVR carry an emergency locator transmitter (ELT) or a survival ELT for its intended operation. At the time of the accident, VH‑JVR was not fitted with an ELT but carried a survival ELT (refer to section titled Emergency beacons).
Weight and balance
The CP provided a recreated weight and balance sheet of the accident flight to the ATSB. The morning pilot witnessed the aircraft depart with full fuel in the survey configuration. The weight and balance sheet identified that VH‑JVR weighed about 1,488 kg on departure, about 150 kg below the maximum take‑off weight of 1,636 kg. The centre of gravity on take‑off was near the centre of the allowable range. Therefore, it was very likely that VH‑JVR was within the weight and balance limits at the time of take‑off.
Meteorological information
The pilot who flew the morning survey flight reported that the weather at that time was fine with good visibility, except for some light turbulence.
The Bureau of Meteorology forecast for the area, valid from 1300, was for visibility to be greater than 10 km and no significant weather for the time of the accident. Winds were forecast to be southerly at about 15 kt. Satellite imagery indicated no cloud cover over the survey area. The nearest weather stations to the accident site were at Norseman (124 km east) and Hyden (158 km west‑south‑west). There was no significant weather reported at either location. Recorded winds at 1330 were south‑westerly at about 14 kt at Norseman and south‑easterly at 10 kt gusting to 17 kt at Hyden.
According to Geoscience Australia’s geodetic calculator, the sun azimuth was north‑west at about 56° elevation about the time of the accident. This was relatively high in the sky and sun glare affecting the pilot was considered not likely.
Recorded data
Spidertracks data
A Spidertracks Spider X tracking system was installed on the aircraft, which provided near real‑time tracking via satellite and/or cellular networks, recording position, altitude, track heading and groundspeed at 15‑second intervals, increasing during aircraft manoeuvring. The data was transmitted to Spidertracks servers once every minute. The Spidertracks system also had an automatic watch function whereby an alert would be sent via text and email to a nominated person(s) in the event that the data transmissions from the device were not received for a period of 15 minutes.
Spidertracks data was able to be recovered for analysis due to its cloud‑based operation. The physical unit, and other possible data sources of recorded data identified in the wreckage, including personal electronic devices, the engine data monitoring device and the geophysical survey data equipment, were all damaged in the post‑impact fire, preventing data recovery.
The last known position transmitted by Spidertracks was about 3.2 km east, and approximately 1 minute away (at the last recorded speed) from the accident site (Figure 3). Position data was recorded by Spidertracks once every 15 seconds, increasing to about once every 3 seconds during a turn. However, as the data was only transmitted once every minute, it was likely that the accident occurred before Spidertracks was able to transmit the last data packet to the cloud storage.
The recovered data showed that the pilot had conducted procedure turns (refer to section titled Survey pattern) at the end of each of the completed 24 survey lines, over a period of about 50 minutes. Although all turns were observed to be conducted in a similar manner, one particular turn commenced at a greater distance away from the survey area. During interview, the CP suggested that the pilot may have done so in order to have a drink or attend to a flight‑related task. The ATSB noted no evidence to suggest any concern with this particular turn. The aircraft was on the 25th survey line when the data stopped, and the accident site was in the vicinity of the expected 25th procedure turn (Figure 3).
The recorded data showed the survey lines were being conducted in an east‑west orientation, with left turns conducted to the west and right turns to the east. The average survey line speed was 114 kt at an average height of about 78 ft above ground level (AGL).
Figure 3: Recorded flight path (excluding transit from Kalgoorlie)
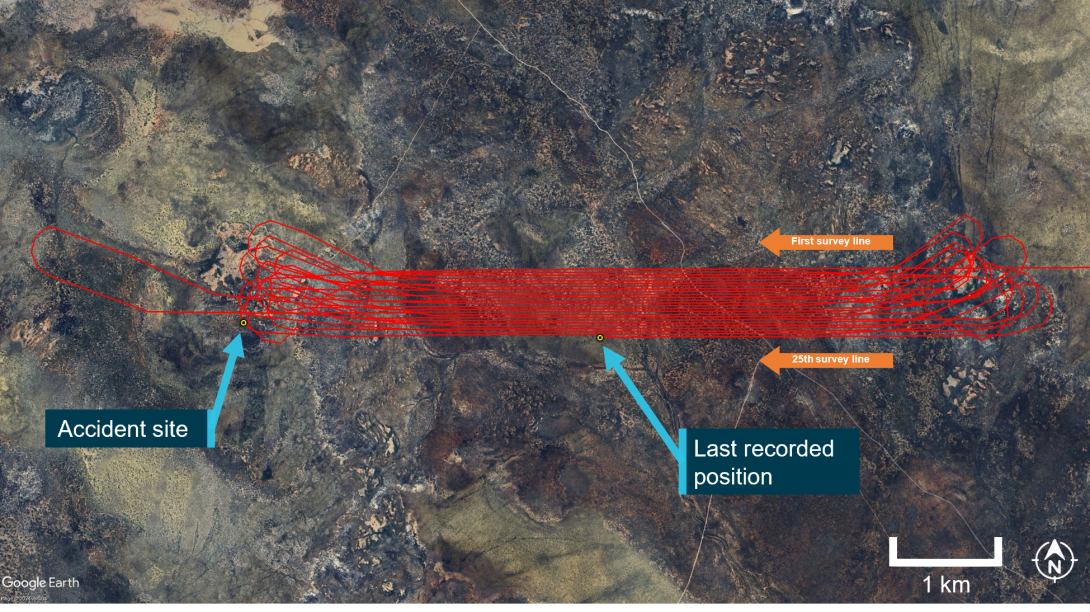
Source: Operator’s satellite tracking data, overlaid on Google Earth, annotated by the ATSB
Procedure turn analysis
The available Spidertracks data was analysed to assess the aircraft handling during the accident flight. The recorded ground speed data and forecast wind and direction were used to estimate the true airspeed during the survey flight. Based on the available atmospheric conditions, true airspeed was assumed equal to indicated airspeed and is used throughout the following analysis.[5]
Using the available recordings, the average bank angle, rate of turn and G load for each turn for the accident flight were calculated. These calculations assumed steady coordinated turns, at constant altitude and airspeed, with a constant wind speed and direction.
The ATSB’s analysis of the Spidertracks data from the aircraft identified that during the procedure turns:
- The angle of bank ranged from 43° to 60° and was typically between 50° to 60°.
- The rate of turn ranged from 10° to 18° per second and was typically between 14° to 18° per second.
- The G load[6] ranged from 1.3 G to 2 G and was typically about 1.7 G to 1.8 G.
- The indicated airspeed ranged from 89 kt to 109 kt and was typically between 94 kt to 104 kt.
- The altitude during turns were between 150 ft to 300 ft AGL, with the average being 200 ft.
Comparison flights
Spidertracks data from 2 previous flights for the accident pilot, which were in VH‑JVR, as well as the morning survey flight conducted in VH‑JVR by another pilot were made available to the ATSB. These were analysed for comparison to the accident flight.
Morning flight
The morning flight conducted by the other pilot consisted of 50 survey lines and 49 procedure turns. These survey lines were typically flown at 85 ft AGL and 120 kts. This set of survey lines were immediately adjacent to the accident flight survey, with the procedure turns occurring in a similar area. Analysis of these procedural turns identified:
- The angle of bank ranged from 24° to 56° and was typically between 40° and 50°.
- The rate of turn ranged from 4° to 16° per second and was typically between 10° and 13° per second.
- The G load ranged from 1.1 G to 1.8 G and was typically between 1.3 G and 1.5 G.
- The airspeed ranged from 92 kt to 109 kt and was typically between 95 kt and 104 kt.
- The altitude during the turns varied between 210 ft and 550 ft, with the average being 320 ft AGL.
These turns, while generally comparable with the accident pilot’s turns, and considered steep turns,[7] were typically flown at lower angle of banks, rates of turn and G load, and at higher heights above ground level. The ATSB noted that the morning pilot had recently completed their survey training with the accident pilot on the Cessna 210. This was their first low‑level survey flight in the Cessna 206.
Previous flights (accident pilot)
Spidertracks data from 2 prior survey flights in VH‑JVR for the accident pilot were available. These flights were conducted in a different location, over undulating terrain with dense vegetation, with a higher average survey height of about 140 ft AGL at about 113 kt. Each flight consisted of just over 50 procedure turns and survey lines. A summary of the analysis of these procedural turns is contained in Table 1 below (refer flights 2 and 3), with comparison to the accident flight, and the morning pilot (flight 1).
Table 1: Comparative turn analysis results
Accident flight | Flight 1 | Flight 2 | Flight 3 | |
Averaged turn radius (m) | 197 | 277 | 280 | 248 |
Averaged angle of bank (°) | 54 | 45 | 47 | 46 |
Averaged turn rate (°/s) | 15 | 11 | 11 | 12 |
Averaged G load (G) | 1.7 | 1.4 | 1.5 | 1.5 |
The ATSB’s analysis of the Spidertracks data from the pilot’s previous survey flights identified that those turns were flown at slightly lower angles of bank, rates of turn and G load when compared with the accident flight. While the pilot was operating at a different location, which may have influenced the way they conducted their turns, the reason for the differences was not able to be determined from the evidence available.
Wreckage and impact information
Wreckage distribution
The aircraft was located in moderately dense scrubland with small to medium trees. The terrain was relatively flat, with some low ridges in the surrounding area.
The distribution of the wreckage indicated that the aircraft initially struck trees in an upright orientation, with an approximate 20° left angle of bank, and a nose‑down attitude at about a 30° angle of impact. The initial tree strike resulted in the left wingtip and aileron separating from the aircraft. The aircraft then impacted the ground on its left side and continued through the bush in a southerly direction, coming to rest about 45 m from the initial point of impact, where it was consumed by a post‑impact fire.
The wreckage trail consisted of a number of felled trees and aircraft components, including the nose gear assembly, left main gear and fairing, left door, section of the left wing flap, windscreen and sections of the lower engine cowling and lower engine components. There was no indication of fire in the wreckage trail or detached aircraft components (Figure 4).
Figure 4: Wreckage trail looking north towards the impact area
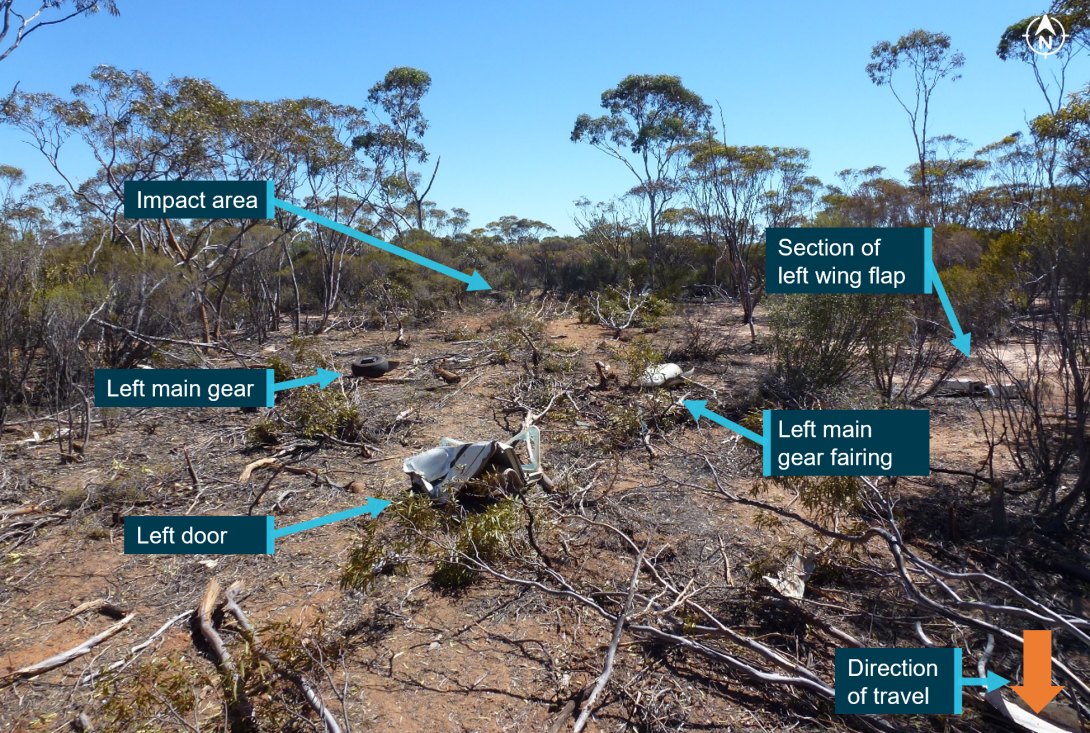
Source: ATSB
The propeller had separated from the engine and was located towards the rear of the wreckage and the engine was upside down and detached from its mounts. Although the left wing was significantly affected by fire, the wing spar was still distinguishable. The right wing was relatively intact as was the magnetometer boom, albeit damaged by fire (Figure 5).
Figure 5: Main wreckage
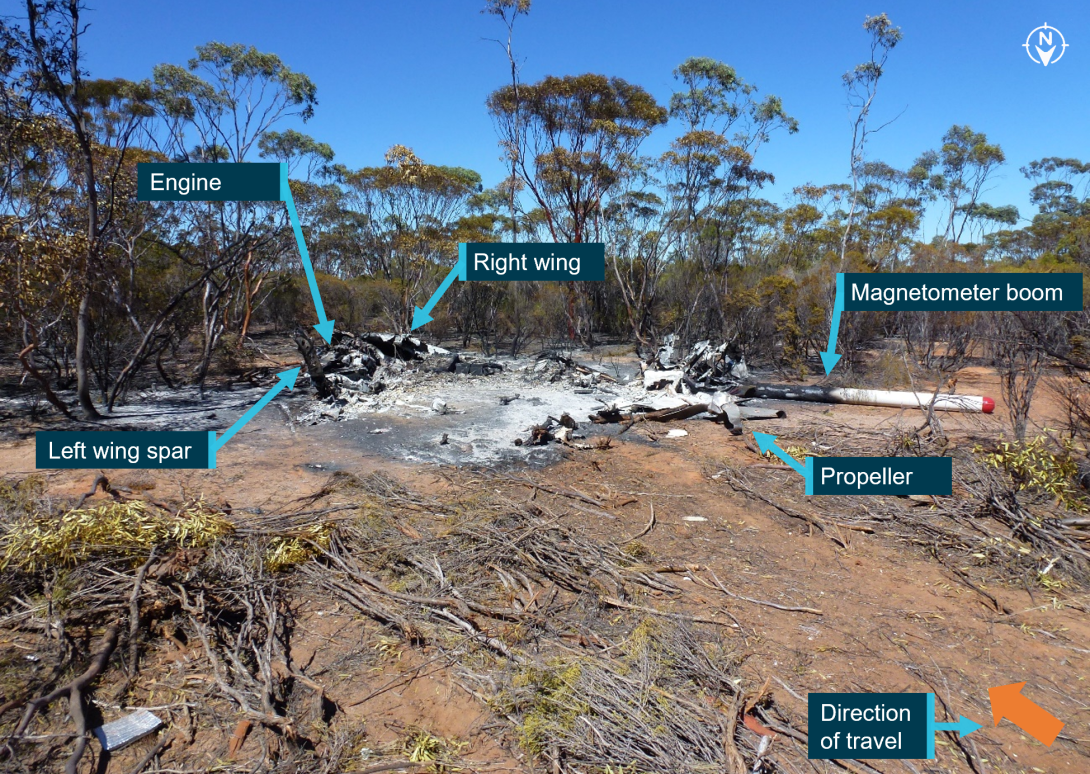
Source: ATSB
Wreckage examination
Although post‑impact fire damage precluded examination of a significant proportion of the aircraft, inspection of the site and wreckage found:
- no evidence of any pre‑existing structural, mechanical or flight control defects that would have prevented normal operation
- the wing flaps were in the fully up (retracted) position
- a small, yet intense fire zone indicative of a significant amount of fuel, with ignition occurring from the left‑wing integral fuel tank rupturing during the accident sequence
- the fuel selector was in the ‘BOTH’ orientation
- damage to the propeller indicated that the engine was producing power at the time of the impact.
Extensive fire damage to all instruments and avionics resulted in no useful switch position information. The windscreen, located part way along the debris trail, did not exhibit signs of birdstrike, nor were feather or bird remains identified in the area. In addition, the morning pilot reported that, while they had observed bird activity on survey flights, none had been sighted that day.
The reason for the fuel imbalance noted by the morning pilot could not be determined from the wreckage examination.
Medical and pathological information
Post-mortem examination
A post-mortem examination of the pilot was undertaken by a qualified pathologist on behalf of the Western Australia Coroner. The pathologist determined that the pilot’s cause of death was a result of a combination of traumatic injuries (both soft tissue injuries and multiple fractures) and the effects of fire from significant thermal injury and smoke inhalation. There were multiple fractures to the nasal bones but none to the skull or pelvis.
The pathologist assessed that the traumatic injuries sustained were potentially survivable with immediate medical assistance, but those injuries were compounded by the thermal injury and smoke inhalation. The ATSB’s aviation medical specialist also advised that the impact injuries were likely not fatal, however, they would have been severely incapacitating. The extensive thermal injury and, in particular, the smoke inhalation was likely to have rendered the pilot unconscious within minutes. They also stated that immediate intervention would have been required but the sustained thermal injuries were likely not survivable.
The post-mortem report indicated that the pilot did not have any significant natural disease. Further, toxicological analysis did not detect the presence of alcohol or common drugs and carbon monoxide[8] levels were not significantly raised (at less than 5% saturation).
The pilot was reported by their partner to be fit and healthy with no known illnesses.
Survival aspects
Impact protection
Due to extensive fire damage to the fuselage, there was limited evidence available about the survivable space/intrusions, or seat and seatbelt condition. Therefore, the ATSB was not able to determine survivability with regard to the cabin area. The left (pilot) door indicated an intrusion/compression and the left main landing gear leg was detached, consistent with high impact forces and the injuries sustained to the pilot.
Post-impact fire
Metal fuel tanks are prone to rupturing during an accident impact, allowing fuel to escape and increasing the risk of a post‑impact fire. To improve crashworthiness, the addition of fuel bladders and fuel cells that have been constructed of flexible materials have proven less prone to rupturing during an impact. They are able to withstand greater deformation and puncture less readily and are less likely to expand or tear to form a larger opening from which fuel can escape. Such systems may provide occupants with more time to egress the aircraft and/or reduce the risk of any fire‑related injury.
ATSB investigation report AO‑2021‑052, extensively discussed post‑impact fire safety and referenced studies by the United States National Transportation Safety Board and Transport Safety Board of Canada. Those studies concluded that post‑impact fire had been shown to contribute significantly to injuries and fatalities in accidents that were otherwise potentially survivable. A potentially survivable accident is one in which the impact forces are within the limits of occupant tolerance, the aircraft structure preserves the required survival space, and the occupant restraint is adequate.
As a result of investigation AO‑2021‑052, the ATSB identified that the aircraft (an Air Tractor AT‑400) was not required to be fitted with a crash‑resistant fuel system under United States Federal Aviation Regulations. A safety issue was raised and the ATSB recommended that the United States Federal Aviation Administration take action to address certification requirements for crash‑resistant fuel systems for fixed‑wing aircraft, in an effort to reduce the risk of post‑impact fire. At the time of writing this report, the ATSB recommendation remained open and the Federal Aviation Administration had advised that the results of a study into post‑crash fire accidents was being reviewed to determine their next action (AO‑2021‑052‑SI‑01).
Protective clothing and helmets
For the accident flight, the pilot was reported to be wearing a t‑shirt, shorts and trainer type shoes and was not using a helmet. The operator did not require its pilots to wear protective clothing or helmets, nor were they required to do so by regulations. The CP explained that this decision took into account temperature, fatigue and pilot comfort balanced against mitigating the potential risks. In addition to comfort and fatigue factors, the bulk of a helmet may not be suitable to the smaller cockpit of the aircraft. However, the CP stated that no formal risk assessment had been completed to support this decision. The operator reported that it issued each pilot (including the accident pilot) with company polo shirts made of 100% cotton as a measure of fire protection and the use of other protective clothing and helmets was left to individual pilots’ discretion. The CP indicated that some of their pilots did wear such items. It could not be determined if the accident pilot was wearing the company polo shirt. The ATSB noted that the operator’s job safety analysis (refer to section titled Job safety analysis) included consideration of protective equipment and clothing as methods of reducing risk factors.
The ATSB’s aviation medical specialist advised that if protective clothing and an appropriate helmet was worn, in most general circumstances, this would have reduced the severity of injury in an accident. However, they were unable to comment on the effectiveness of these items for this accident and noted that protective clothing and a helmet would not have prevented any smoke inhalation injury.
The International Airborne Geophysics Safety Association (IAGSA – refer to section titled International Airborne Geophysics Safety Association) recommended that appropriate clothing should be worn by all flight crew involved in geophysical surveys to minimise the immediate risk of fire in the event of an accident and for protection from exposure in a survival situation. These include:
- cotton undergarments covered by long trousers and long‑sleeved shirt or an appropriate flying suit
- closed shoes
- have gloves available at all times
- layers of clothing appropriate for the conditions
- cold weather clothing should include felt lined boots, down parka with attached hood and large mittens.
IAGSA also recommended that for fixed‑wing operations, each individual operator should determine the appropriateness of the use of an industry approved helmet. A case by case, risk assessed approach should be adopted, taking into account the relevant variables for each specific survey task.
The Flight Safety Foundation’s Basic Aviation Risk Standard[9] is a set of risk‑based aviation industry standards. The standard covers a wide variety of aviation applications of which airborne geophysical survey operations were included. The standard implementation guidelines for survey operations also recommended appropriate clothing for crew such as non‑synthetic long trousers and pants or flying suit. It also recommended that helmets should be worn when operating below 500 ft AGL unless a risk assessment stated otherwise.
Flight following
Satellite tracking
Operator requirements
The operator had implemented flight following through use of the Spidertracks satellite tracking system installed on each of its aircraft. The company operations manual stated:
In addition to the required safety equipment the Company equips all aircraft with a real-time satellite monitoring system with a refresh rate of at least every 5 minutes and automatic alerting (to company mobile phone and email) in the event of an emergency.
Should the satellite monitoring system alert be inadvertently activated by the pilot an “ops normal” call should be made to the company as soon as practicable.
The ground operator assigned to each survey job was the primary person responsible for flight following. They were to monitor the aircraft’s location via the tracking system and initiate an emergency response, if required.
The morning pilot could not recall any specific pre‑flight requirements for the Spidertracks device and another company pilot reported that there were not any checks required, the device turned on once the aircraft’s electrical system was on.
The operations manual did not include flight following as a specific duty for the ground operator or any other staff member. Further, the manual did not detail procedures for the conduct of flight following, nor were there procedures or guidance to confirm that the tracking system was correctly configured and operating as expected prior to flight.
Automatic watch function
The operator was surprised that a Spidertracks automatic alert was not received during the accident and advised that, on a number of occasions, their satellite tracking had experienced dropouts. On some of those occasions, contact was made with the pilot and a system reset restored normal function. On other occasions, when contact with the pilot was not possible, the aircraft returned by the nominated estimated time of arrival (ETA). The operator had not contacted Spidertracks about the dropouts or conducted any other troubleshooting.
Spidertracks advised the ATSB that the automatic watch function on the aircraft’s device had not been activated on the accident flight, nor was it active for earlier flights on 2 and 3 March 2022. They further advised that there was no indication of any service‑related issues, confirming that up to the loss of data, the aircraft’s device was operating as expected. Diagnostic logs for the device were not available due to this data only being transmitted via mobile phone networks. Spidertracks confirmed that the length of time with no transmissions received, or a data loss or delay was not typical and could be indicative of a power or device failure, transmission interference or installation issue. Spidertracks found no recorded issues with the satellite service or their cloud platform at the time of, or leading up to, the accident.
Emergency response plan
The operator had a phased emergency response plan, predicated on an elapsed time since the aircraft’s ETA. Each phase was commensurate with an escalating level of concern. Satellite tracking was referred to in the plan, within the section Phase 1 - Uncertainty. Phase 1 commenced 0–15 minutes after the aircraft’s ETA had expired. The plan directed a check of the satellite tracking and if there was an abnormal or no indication in the system, the next step was to attempt contact with the crew. If contact with the crew was not possible and overall operations were assessed as not normal, the plan directed that the operations manager, as primary contact, to be notified, then the chief executive officer and CP as alternates.
The plan did not elaborate any further on required actions for an abnormal or no indication in the system prior to advancing to the next step, which was Phase 2 - Alert. Phase 2 commenced 15–30 minutes after the ETA had expired and directed the primary or alternate contacts to establish the final status of the aircraft via the tracking system. It included a note that, if there was no contact with company operations then the ground operator was to contact the Australian Maritime Safety Authority’s Joint Rescue Coordination Centre or local search and rescue services direct. Commencement of Phase 3 - Distress was at 30 minutes after ETA had expired or whenever the aircraft was confirmed as missing.
The operator commenced phase 3 at 1700, 30 minutes after the ETA for VH‑JVR had expired and then contacted the Joint Rescue Coordination Centre.
Emergency beacons
Emergency locator transmitter
The company operations manual stated that all company aircraft were to be fitted with an approved ELT or a portable ELT if the fixed device was inoperative or otherwise not serviceable. The operator was not able to determine why VH‑JVR was not fitted with an ELT.
The ATSB research report (AR‑2012‑128) discussed the potential safety benefits of an approved, fitted ELT, which were designed to automatically activate following an impact normally associated with a collision. While the research noted some limitations with the effectiveness of ELTs, the fitment of a crash‑activated ELT greatly increases the early notification for search and rescue efforts and arrival of potentially life‑saving medical treatment especially when occupants or crew are incapacitated.
Personal locator beacon
The CP and morning pilot stated that a personal locator beacon (PLB) was carried in the aircraft as part of a survival kit, which was secured to the passenger seat. The PLB was routinely carried in the aircraft, and not as an alternative to an ELT but as an additional item. In accordance with regulations, the PLB was classed as a survival ELT, and an alternative to a fixed ELT. However, the PLB was not identified in the wreckage and was likely consumed by fire.
The ATSB research report (AR‑2012‑128) suggested that carrying a PLB will most likely only be beneficial to safety if it is carried on the person, rather than being fixed or stowed elsewhere in the aircraft. The CASR Part 91 MOS stated that a survival ELT must be carried either on the person of a crew member, in or adjacent to a life raft, or adjacent to an emergency exit.
Operational information
Airborne geophysical survey flights
Airborne geophysical survey flights are conducted by a variety of rotary and fixed‑wing aircraft which have been specifically modified and equipped with geophysical sensors. Survey flights were normally flown below 500 ft AGL over the desired area via a pre‑determined pattern and at heights designed to maximise the quality of the data captured. The data provides a detailed below ground composition of the surveyed area, primarily to inform mining and resource industry activities.
Requirement for CASA low‑level rating
Operations requiring flight below 500 ft AGL, such as geophysical surveys, required a pilot to hold a CASA Part 61 low‑level rating. A low‑level rating is specific to various types of flying operations (such as aerial survey, firefighting or agricultural), however, the training and testing is not specific to any one type of operation. To obtain a low‑level rating a pilot must demonstrate competency in certain operational techniques, which included, but were not limited to, steep, maximum rate and minimum radius turns, procedure turns, recovery from approach to stalls (level and turning). In addition to holding a low‑level rating, MAGSPEC Aviation required prospective pilots to have a minimum of 500 hours as pilot in command. MAGSPEC Aviation then provides training specific to its operational requirements.
International Airborne Geophysics Safety Association (IAGSA)
The IAGSA is an international industry association comprised of airborne geophysical survey organisations with an overall objective to promote and enhance safety in the airborne geophysics survey industry. IAGSA publishes a safety manual for its member organisations, which details its standards and recommended safety practices.
IAGSA is a non-regulatory body and holds no authority to compel its members to follow its standards and recommended practices, which are not a replacement for the regulatory requirements that each individual organisation may operate under. However, members have agreed under the terms of membership to follow those standards and practices where they are more stringent or not covered by regulations, except where they have filed a notification of difference. Members are also required to complete an annual self‑audit. At the time of the accident, MAGSPEC Aviation’s most recent self‑audit outlined a number of differences to IAGSA standards and practices. Although IAGSA had requested it, it had not received a formal notification of differences from the operator.
Survey height
The operator was issued a CASA instrument in 2017, which allowed it to conduct operations at a height lower than that permitted by Civil Aviation Regulation (CAR) 157.[10] The instrument was last renewed in 2021 and was valid until 2024.
The instrument did not specify the lowest height that could be flown. The CP stated that survey flights would often be flown at 30 m (100 ft) AGL, although a standard or minimum height was not documented in the operations manual. Rather, the survey height would be requested by the client.
The CP explained that the requested survey height was assessed during the planning stage, through a review of maps of the survey area and the conduct of a reconnaissance flight. A detailed guide on how to conduct a reconnaissance flight was included as an appendix to the operations manual. This process would confirm if the survey could be flown at the requested height. The operator stated that, on numerous occasions this process resulted in the survey being flown at heights higher than requested.
The client for the accident survey specified a height of 25 m (82 ft) AGL.
The IAGSA safety manual acknowledged that there were increased risks associated with low flying and that operating at such heights can ‘aggravate the consequences of mechanical malfunctions or human error’. When discussing minimum safe survey heights, and while recognising that lower heights may improve the quality of survey data, they noted many differences of opinion among its members.
Having a predetermined height had been debated among the members, however, they concluded that ‘no single universal “minimum safe survey height” can be designated given the wide variety of survey conditions and aircraft characteristics’. As such, IAGSA indicated that the safety issue was not necessarily the survey height, but more importantly, could the survey be safely flown at the requested survey height. Consequently, IAGSA recommended that:
Clients specify the maximum clearance height possible, consistent with the objectives of the survey to be flown and that operators, prior to commencing a survey, conduct a detailed risk analysis in accordance with an internationally recognized procedure considering, but not limited to, the following factors and Appendix IV of this manual:
• terrain relief, elevation & vegetation canopy thickness
• aircraft type
• aircrew flight and duty times
• prevailing weather conditions
• anticipated density altitude
• pilot experience and recency
• planned flight speed.
Survey pattern
From the recorded data, the accident survey flight was flown in a back‑to‑back pattern, which was a series of consecutive parallel lines followed by a procedure turn used to establish the aircraft onto the next line in the reciprocal direction (Figure 6). This was the routine pattern used by the operator in its geophysical surveys. The client had specified 25 m spacing on east‑west survey lines.
The CP explained that procedure turns consisted of an initial climbing turn to establish the aircraft at about 300 ft AGL and about 400–500 m lateral offset from the next line. After this, a level turn would be commenced (into wind) at a 45–60° angle of bank (referred to as a steep turn) to intercept the next line. Descent to the survey height commenced once the aircraft wings were established straight-and-level.
Figure 6: Back-to-back pattern and procedure turns
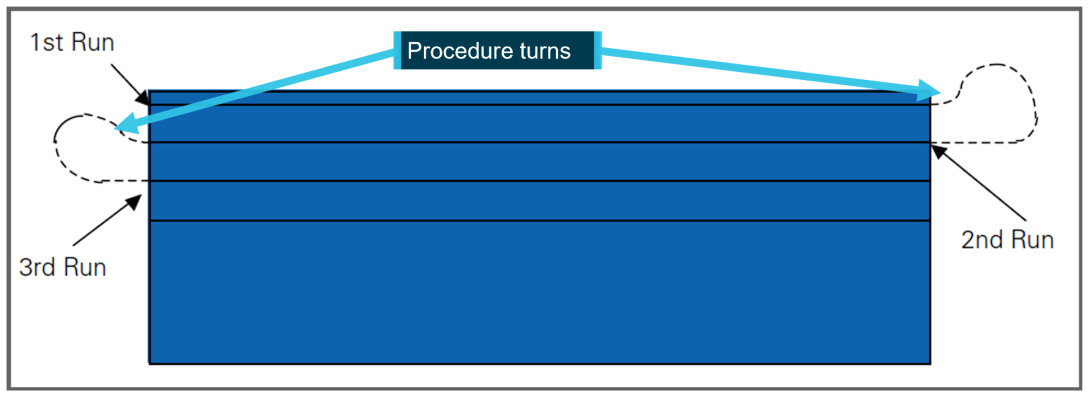
Source: Aerial Application Association of Australia, annotated by the ATSB
IAGSA highlighted the risks associated with turns at low level:
Turns at low level present a considerable hazard, particularly if the terrain presents visual illusions; the aircraft descends in the turn, airspeed is low, or the angle of bank is steep. An excessive angle of bank, often resulting from close line spacing or drifting in strong crosswind conditions, is insidious as the stall speed of the aircraft increases with the angle of bank (assuming a level turn) whilst at the same time the aircraft’s speed is reduced from increased drag.
During straight and level flight there may be a significant margin above the stall speed, however in a steep turn the stall speed may be reached quickly with little warning and a stall in the turn at low level will likely result in a fatal accident.
For manoeuvring at low level, IAGSA recommended:
All turns at low level should be limited to a maximum angle of bank of 30 degrees and be done at a constant altitude. No climbs or descents should be carried out during the turn. If the terrain dictates that a climb is necessary the aircraft should be climbed to the required height prior to commencing the turn and any descent back to survey height should only be done after established in a wings level attitude.
The CP explained that the back‑to‑back pattern with procedure turns was the most efficient method and enabled the capture of higher quality survey data. They reported that flying consecutive lines was less workload intensive for their pilots, especially regarding obstacle hazard avoidance. This allowed a pilot to deal with a particular hazard for a short period as they moved away from it.
Operations manual – Special operations
Volume 2 of the operations manual, valid at the time of the accident, discussed aircraft operations and included a section titled Part 2D Special Operations specific to survey operations. It included sub sections on low flying, survey tolerances and safety considerations during surveys. However, there was limited detail with regard to the process or procedures for the conduct of low‑level survey flights.
As previously discussed, a standard or minimum survey height was not included in the operations manual.
In Part 2D1.1 Low Flying, height was discussed in terms of a minimum height when overflying occupied structures, vehicles or livestock but it did not include reference to other obstacles such as terrain, vegetation canopy or masts/antennas.
Part 2D1.4 Survey Tolerances stated:
Track, height and groundspeed tolerances for the survey will be established by the client and should be adhered to as closely as possible. Significant deviations will require the line to be re-flown.
Client established survey tolerances, although important to data accuracy, remain secondary to safety and pilots should disregard them as necessary to ensure the safety of aircraft, personnel, equipment, and environment.
Part 2D1.5 Safety considerations during survey, required a minimum survey speed to be established for each aircraft type operated by MAGSPEC Aviation. This was to be the greater of the 130% of clean stall speed (wing flaps up and landing gear up if retractable), 110% of the best single‑engine climb speed or 110% of the take‑off safety speed.
Although procedure turns and a back‑to‑back survey pattern were taught to, and routinely flown by all company pilots, the special operations section did not refer to these manoeuvres. The CP stated that there was no other reference document that outlined how the operator expected its pilots to conduct the procedure turns, nor were there any documented limitations such as a maximum angle of bank or minimum height AGL prior to commencing the procedure turn.
Aerodynamic stall
A wing generates lift as a result of the pressure differential created by airflow over the wing’s surface. The angle between the incoming or relative air flow and wing chord is known as the angle of attack (AoA). As the AoA increases, lift increases up to a certain angle, known as the critical AoA. At this point, the airflow over the upper surface of the wing becomes separated. This condition is referred to as an aerodynamic stall (or simply a stall) and results in a significant loss of lift and an increase in drag. Due to the sudden reduction in lift from the wing and rearward movement of the centre of lift, typically an uncommanded aircraft nose‑down pitch results.
A loss of altitude also occurs during the recovery from a stall and it is possible to stall with insufficient height above the ground to recover. The pilot’s operating handbook (POH) for the U206G stated that the maximum altitude loss during a stall recovery may be as much as 240 ft in power off conditions and straight and level flight. The U206G has a stall warning vane[11] and warning horn to alert the pilot of an impending stall.
Most general aviation aircraft typically have a critical AoA of around 16°. This critical AoA can be exceeded at any airspeed, any (pitch) attitude and any power setting. However, as most small aircraft are not fitted with an AoA indicator, the AoA at which the stall occurs may be referenced to an airspeed.
When banking or turning an aircraft, it is necessary to increase the amount of lift generated to ensure that the aircraft does not descend. This increases the AoA resulting in lift and drag greater than normal straight and level flight. This increases the load factor on the aircraft above 1 G. As the angle of bank increases, the lift required to maintain a constant altitude also increases, requiring the pilot to apply back pressure on the control column. The effect is, as the angle of bank and load factor increases, the stall speed increases. At 45° angle of bank, the load factor is 1.41. This results in an almost 19% increase in the wings level stall speed. At 60° angle of bank, the load factor is 2, resulting in an increase in stall speed of 41%.
The U206G POH provided the stall speeds at maximum weight with power off, flaps up, various angles of bank (up to the POH limit of 60°) and centre of gravity (CoG) positions (Table 2Table 2).
Table 2: U206G stall speeds (extracted from the POH)
Angle of bank | 0° | 30° | 45° | 60° |
Stall speed (forward CoG) | 55 kt | 59 kt | 65 kt | 78 kt |
Stall speed (rear CoG) | 41 kt | 44 kt | 49 kt | 58 kt |
Recovery from a stall requires reducing the AoA by moving the control column forward, which normally means lowering the aircraft nose (pitching down).
Organisational and management information
MAGSPEC Aviation
MAGSPEC Aviation Pty Ltd commenced operations in 2017 to provide airborne geophysical survey services across Australia. It operated a fleet of 2 Cessna 206 and 2 Cessna 210 aircraft. At the time of the accident, they operated under a CASR Part 138 (aerial work) air operator’s certificate. Part 138 came into effect on 2 December 2021. Since commencing low‑level survey operations, the operator had experienced the following occurrences:
- In 2018, the engine of a Cessna 210 failed necessitating a forced landing. The pilot was uninjured, however, the aircraft was substantially damaged. It was identified that sufficient fuel had not been transferred from the aircraft’s tip tanks to the main fuel tanks. The operator undertook action to review training and to reinforce fuel management procedures.
- In 2019, a Cessna 210 struck a powerline and the aircraft sustained minor damage. The aircraft was safely flown back to its departure point. The operator reported that the aircraft had been flown on north‑south lines due to the sun’s position before transitioning to east‑west lines after the sun was no longer a factor. Following this, the pilot had flown 50 m from the powerline before making contact on the reciprocal heading. Subsequently, the operator incorporated a national database of powerlines into its pre‑survey assessment process.
- In 2020, the engine of a Cessna U206G lost partial power and the pilot conducted a forced landing, resulting in substantial damage to the aircraft. The pilot was uninjured. Fuel starvation was determined as the reason for the engine power loss. It was identified that the aircraft had been operated with only one fuel tank selected instead of both. The operator updated checklists to incorporate the requirement for fuel tank selection to BOTH and amended the survey data acquisition system to provide periodic fuel check messages as a reminder to pilots.
Following the 2018 occurrence, the ATSB completed an occurrence brief (AB-2018-058). This was a short summary report and not an investigation, to allow for greater industry awareness of potential safety issues and possible safety actions. The ATSB did not investigate the other occurrences. CASA conducted 2 surveillance events following the 2018 occurrence. In response to the draft report, on 28 January 2025, the operator reported that they had requested assistance from CASA after the other occurrences but reported no assistance was provided. The ATSB reviewed CASA records, which indicated no action had been taken following the 2019 or 2020 occurrences (refer to section titled Regulatory oversight activity.
Safety management system
Managing safety
According to the International Civil Aviation Organization (ICAO, 2018), a safety management system is a systematic approach to managing safety that seeks to proactively mitigate risks before they result in an accident or incident. This includes defining the necessary organisational structures, accountabilities, responsibilities, policies and procedures.
At the time of the accident, there was no CASA regulatory requirement for the operator to have a safety management system. However, the operator had implemented a Health, Safety and Environmental Management System (HSEMS), for the purpose of describing:
…the process by which MAGSPEC aviation manages risks has been developed to meet the Civil Aviation Safety Authority SMS requirements in addition to providing more generalized guidance on the management of risk within the organisation.
Specifically, one of the operator’s policy commitments was to:
…minimize the risks associated with operational activity to a point that is as low as reasonably practicable/achievable…
While the HSEMS was submitted to CASA, a review of CASA records found that it had not been assessed, nor was there a requirement to do so.
Safety risk management
Risk management is a key component of safety management and includes hazard identification, safety risk assessment, safety risk mitigation and risk acceptance. It is an ongoing process as the aviation system is constantly changing, with new hazards introduced, and some hazards and associated risks changing over time (ICAO, 2018).
CASR Part 138 required an operator conducting aerial work to undertake risk assessments of its operations. This was a new requirement introduced with Part 138. The Part 138 MOS detailed a layered approach to risk assessment and that before conducting an operation:
(a) the operator’s operations manual must contain:
(i) pre-operational risk procedures [refer below] for risk assessments and mitigation processes applicable to the operation; and
(ii) procedures for post-flight risk review; and
(b) the operator must have a flight risk management plan based on a pre-operational risk assessment in accordance with the procedures; and
(c) the operator must ensure that the operator and each crew member is satisfied, in a pre-flight risk review, that the flight risk management plan will eliminate, reduce or mitigate risks and hazards to the extent that it is safe to conduct, and continue, the operation without unacceptable risk to the crew members, any aerial work passengers, the aircraft or any other person or property.
The MOS further specified what was to be included in an operator’s pre‑operational risk procedures:
a. processes for identifying, reporting and recording hazards;
b. processes for analysing identified hazards and assessing the risks they may pose, including for pre-flight, in-flight and post-flight stages of operations;
c. processes to mitigate the risks or control the risks, including processes for the incorporation of risk controls into standard operating procedures;
d. the creation and management of:
i. a risk register; and
ii. records of dedicated risk assessments performed to address each type aerial work operation that is to be conducted, including details of the risk assessors;
e. procedures to ensure that the pilot in command and the other crew members are familiar with the pre-operational risk assessment and the associated standard operating procedures (SOP);
f. in-flight procedures for the pilot in command and the other crew members to consider and manage the risks associated with aerial work operations.
The operator’s HSEMS stated that safety risk management begins with hazard identification and then assessing the risks associated with the hazard in terms of likelihood and severity. The manual further stated that, once the level of risk was identified, appropriate remedial or mitigation measures could be implemented to reduce the risk to as low as reasonably practicable. The risk management process detailed in the HSEMS followed a 5‑stage process:
- Stage 1 - Identify the hazard and associated risks
- Stage 2 - Assess the risk in regard to severity and likelihood
- Stage 3 - Evaluate risk tolerability
- Stage 4 - Treat/mitigate the risk
- Stage 5 - Monitoring
Stage 1 of the process listed sources for hazard identification and stated that the safety manager was to use the Donesafe[12] system to manage and record these hazards. It also noted that:
Due to the varying nature of MAGSPEC Aviation’s operating environment a separate Operational Job Safety Analysis (JSA) (see appendix 3) was undertaken by the Chief Pilot or his designee to assess site-specific risks prior to each job provide an overall risk rating for the job.
Where non-site-specific items are identified as part the JSA or field crew safety meeting these will be reported to the HSEMS system via the DONESAFE “Hazards” report tab.
Each survey task, including the risks associated with that task, were assessed via the job safety analysis (JSA). Any risks identified in the JSA that were not specific to the survey tasking location were entered into the Donesafe system. The risks specific to the location were not captured in the system.
Pre-operational risk assessment
One of the key requirements for managing risk was that an operator should undertake an overarching assessment (pre‑operational risk assessment) to consider and evaluate the risks associated with its proposed operations, in this case, low‑level geophysical survey. This assessment recognised the underlying principles of CASR Part 138, where the risks and hazards associated with a type of aerial work operation are common to that type of operation. The matters to be considered in the assessment included, but were not limited to the (CASA, 2023):
− nature of the intended operation and its particular characteristics
− location (if known) of the intended operation and its particular characteristics
− aircraft to be used in the intended operation and their performance profile and impacts of serviceability status
− qualifications and experience of the FCMs [flight crew members] and support personnel to be used in the intended operation
− generic or known hazards particular to the type of aerial work operation, external to the aircraft, that may be met during the operation.
CASA advisory circular 138‑05 v2.1 Aerial work risk management, stated that an operator should use data from the risk register and dedicated risk assessments to inform the pre‑operational risk assessment. Once populated, the assessment should then be updated over time and from operational experience, to incorporate lessons learnt from previous operations. Further, to ensure it is readily available to all crew members, it should form part of the company’s operations manual.
The ATSB’s review of the HSEMS and operations manual did not identify any requirement for a pre‑operational risk assessment to be completed.The CP also confirmed that, at the time of the accident, such an assessment had not been conducted.
Risk register
Safety risk management activities should be documented, including any assumptions underlying a risk assessment, decisions made, and risk controls implemented. A risk register could be used to ensure identified hazards and risks that emerged during planning or day‑to‑day operations were tracked and mitigated as part of formal risk management processes. An operator’s risk register can also be incorporated into the pre‑operational risk assessment. The register could include the hazard, potential likelihood and consequences, assessment of the associated risks, when or where it applied, and any controls put in place to mitigate the risk. Notably, (ICAO, 2018):
Maintaining a register of identified hazards minimizes the likelihood that the organization will lose sight of its known hazards. When hazards are identified, they can be compared with the known hazards in the register to see if the hazard has already been registered, and what action(s) were taken to mitigate it.
The CP reported that a risk register was not maintained for the company’s operations. Although it was noted that the operator did retain a fatigue risk register.
Flight risk management plan
The results of the pre‑operational risk assessment were to be considered when preparing a flight risk management plan, which was specific to an individual flight or task within the type of operation. The plan should outline the specific mitigators or risk controls that were to be used during the flights. The flight crew should also have sufficient time to review and confirm the plan prior to the commencement of the operation.
Job safety analysis
Components
As required by the company operation’s manual, the JSA was the documented risk management process designed to address the safety concerns with each project the operator conducted, that is, for each specific survey task. The ATSB’s interpretation of the Part 138 risk assessment requirements was that the JSA was equivalent to the flight risk management plan, as discussed above. The JSA consisted of 5 parts:
- Part A - Pre-survey risk assessment: This assessment was to be completed by the operations manager at the time a tasking was quoted and included details on the activity, hazards, hazard effects, initial risk score, risk mitigators, residual risk, and a final risk score. This used a pre‑populated risk matrix with 14 hazard areas, each of which were assigned a descriptor and risk score of 1 (negligible) to 5 (unacceptable). The total risk score determined if any further action was required, such as a need for additional risk controls or stopping the tasking until the risk was reduced.
- Part B - Operational job safety analysis. This was to be completed by the CP or other suitable person prior to commencing the survey task. This considered any operational limitations relating to aircraft performance, obstacles and human performance, whether any hazards affected the safety or technical performance of the survey, and if any changes were required. The risk level for the task was assessed using a pre-populated matrix with 27 hazards, but with instructions to add more as appropriate. The final risk level determined if the survey could proceed as planned (low risk), or if the survey could proceed with approval from the CP and amendments to the plan or additional risk mitigators (medium risk), or if the survey was not to proceed as currently planned (high risk).
- Part C - Field crew safety meeting: The meeting was to be completed by operational personnel at the survey site, prior to commencing survey operations and every crew change. This section was a yes/no answer sheet covering a range of operational areas designed to assess any additional hazards and risks not identified in Parts A and B. At the direction of the CP, a reconnaissance flight could also be performed to assess the survey area for any additional risks or hazards not already identified in the original JSA.
- Part D - Post-survey field crew meeting: This meeting allowed the operator to better understand any issues faced on the job and if anything needed to be accounted for, either at that specific location or for an ongoing basis.
- Part E - Emergency response plan: This plan was to be reviewed during the field crew safety meeting and crew members were to ensure that the contact and procedure details were correct.
Neither Part A nor Part B referred to consideration of previous JSAs for any applicable risk information that may be relevant to the current JSA.
Survey task assessment
Parts A-C of the JSA completed for the accident flight survey task are discussed in the following paragraphs.
Part A was completed by the operations manager and listed hazards including the 25 m survey height, which was assessed with the highest risk score of 5. It did include mitigating factors of carrying a portable personal ELB and portable GPS, conducting operations with satellite flight following and a comprehensive pilot briefing including maps.
Several elevated risk areas were identified on the matrix, such as operations below 100 ft AGL and operating in hot conditions between 35–40 °C. Overall, the initial risk rating for the survey task was determined to be low, based on a score of 36 (Figure 7)Figure 8.
Figure 7: Part A – Initial pre-survey risk assessment for the accident task
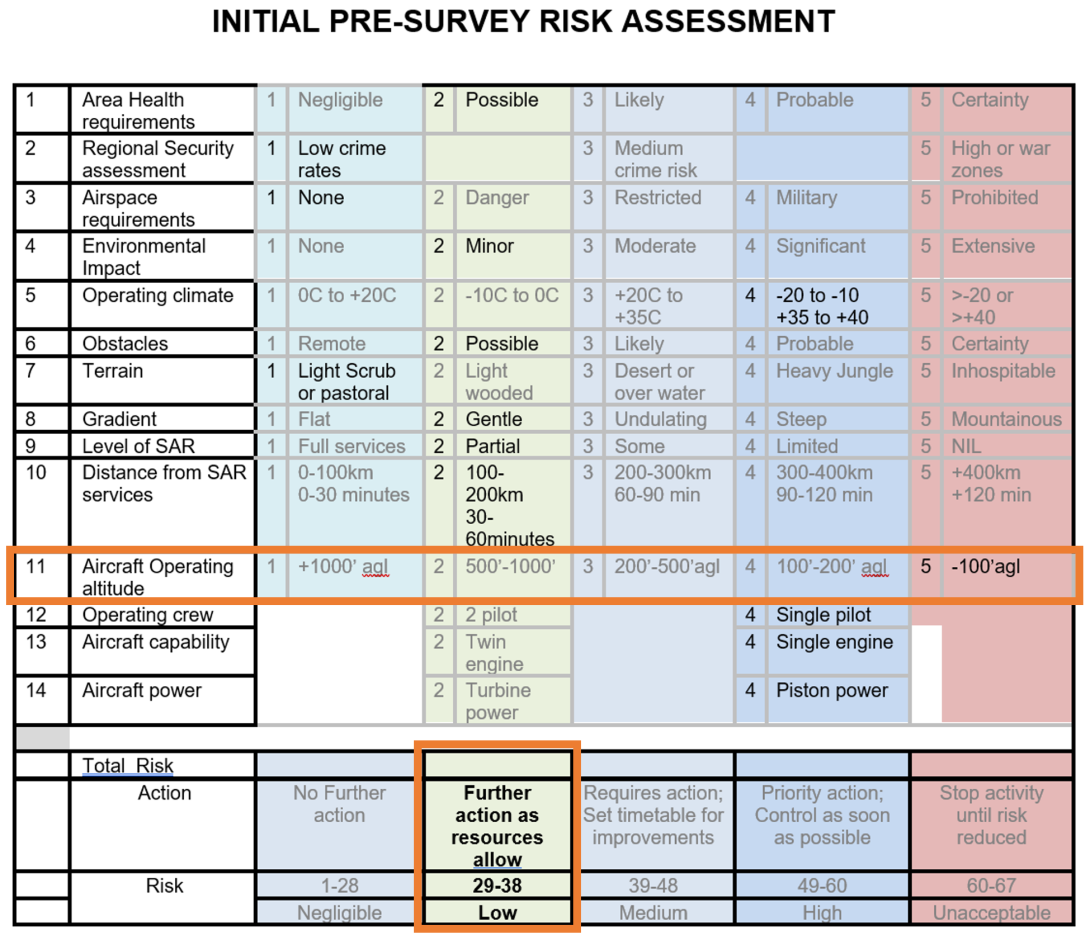
Source: MAGSPEC Aviation, annotated by the ATSB
The CP and operations manager approved Part B of the JSA, identifying that the survey height and antenna/masts, and the survey location with regard to other aircraft activity were concerns. When considering if there were any hazards that would affect safety or the technical performance of the survey, the survey height of 25 m was noted, and the possibility of trees, powerlines and masts in the area were low still but still a risk. As such, it was determined that a detailed reconnaissance flight was to be conducted.
The final risk level was assessed as low, with 4 hazards identified (Figure 8Figure 9). The ATSB noted that the hazard of ‘terrain clearance less than 30 metres’ had not been ticked. However, if it had been selected, the final risk level would have remained at low.
Figure 8: Part B – Hazards risk matrix for the accident tasking
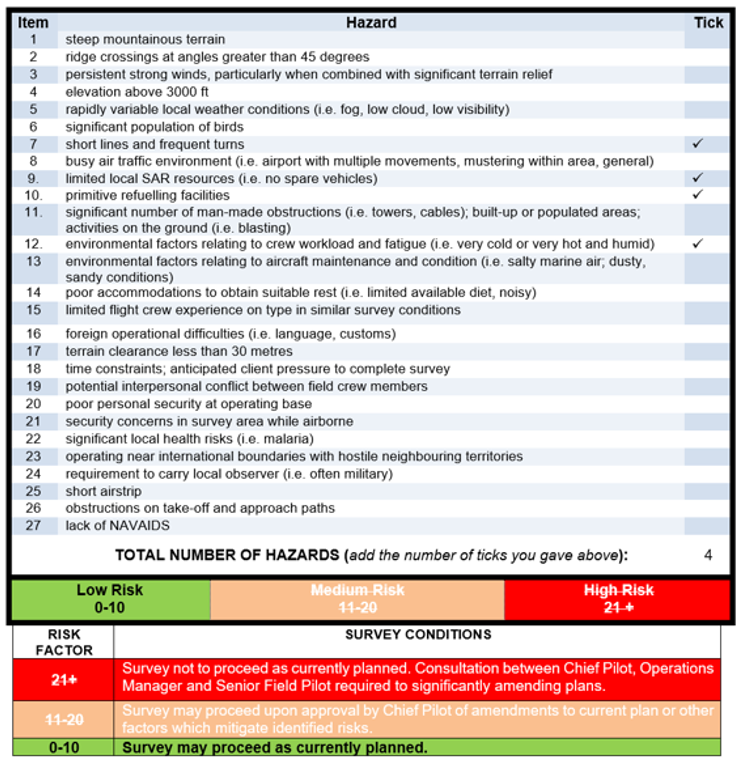
Source: MAGSPEC Aviation
Part C had been originally completed by another pilot and the ground operator. That pilot had conducted a reconnaissance flight of the survey area and signed part C noting that no additional risks had been identified. That pilot was subsequently assigned to another task.
The ATSB noted that the survey height was referred to in the question, Can the job be flown at the suggested survey height? and this was answered as yes with no amplifying comments.
The day prior to the accident, the ground operator met with the accident and morning pilot to conduct another field crew safety meeting. They discussed the JSA, and the ground operator reported that they advised the pilots about some taller trees in the area, which had been identified in the reconnaissance flight (but not noted in Part C).
Text messages between the accident pilot and CP showed that conducting another reconnaissance flight was discussed. The CP suggested that another could be done if the pilot felt it was required but there was no direction from the CP to do so. The morning pilot completed another reconnaissance of the survey area prior to commencing their survey.
In reference to the utility and sufficiency of the JSA, the operator advised on 28 January 2025 in response to the draft report that they considered the JSA to be their risk assessment process and was a combined risk register, pre‑operational risk assessment, flight risk management plan and record of the crew meeting. The operator further advised that the JSA was reviewed by CASA during the transition to Part 138 and:
This risk assessment was approved by CASA during the 2nd December 2021, Part 91 / 138 AWK [aerial work] changes. It has been accepted and approved by multiple third-parties, including those that represent BARS [Flight Safety Foundation’s Basic Aviation Risk Standard].
The ATSB sought clarification from CASA to determine if the JSA met the requirement of Part 138 and whether it had been approved by CASA. On 1 May 2025, CASA advised:
The JSA as described in the report does not meet the requirement of a pre-operational risk assessment.
The reasons for this advice are:
- The ATSB report outlined that Part A of the JSA had a pre-populated risk matrix with 14 hazard areas and Part B of the JAS had a pre‑populated matrix with 27 hazards and instructions to add more as necessary.
- CASA’s AC 138-05 identifies how a risk register is a critical component to the creation of a pre‑operational risk assessment and CASA notes that the ATSB report mentions that the operator’s Chief Pilot (CP) “reported that a risk register was not maintained for the company’s operations” which supports that a pre-operational risk assessment was not produced.
- CASA agrees with the ATSB that this activity is not specifically considering or evaluating the risks associated with the type of aerial work operation to be conducted, i.e. the JSA process is basically done on a per task basis, which is not the same as the pre-operational risk assessment as the pre‑operational risk assessment is intended to be an enduring document that is regularly updated from risk register updates and post-flight risk reviews (see the first sentence of CASA AC 138‑05 paragraph 4.2.5).
- Effectively, the JSA Part A is potentially covering elements of risk assessments that would support the updating of the pre-operational risk assessment but is not creating the pre-operational risk assessment itself.
- CASA further advised:
- The accident occurred 3 months after the commencement of the new flight operations regulations, of which Part 138 of CASR and its supporting Manual of Standards was one element.
- Under the transitional rules in Subpart 202.EAA of CASR, holders of AOCs authorising aerial work under the pre-2 December 2021 paragraph 206(1)(a) of CAR, where the AOC was in force immediately before 2 December 2021, had these AOCs recognised as legally being an aerial work certificate and such operators were required to ensure their operations manuals complied with Part 138 of CASR and contained all necessary content to enable that compliance.
- As the operator was the holder of an AOC authorising aerial work under the pre-2 December 2021 rules, the content of their operations manual would have been approved by CASA as part of them holding that AOC. Compliance with the new flight operations regulations for all such operators would be reviewed at the next appropriate CASA oversight event.
Regulatory oversight activity
Regulatory framework
CASA was responsible, under the provisions of Section 9 of the Civil Aviation Act 1988, for the safety regulation of civil aviation in Australia and of Australian aircraft outside of Australia. Section 9(1) stated the means of conducting the regulation included:
(c) developing and promulgating appropriate, clear and concise aviation safety standards;
(d) developing effective enforcement strategies to secure compliance with aviation safety standards…
(e) issuing certificates, licences, registrations and permits;
(f) conducting comprehensive aviation industry surveillance, including assessment of safety‑related decisions taken by industry management at all levels for their impact on aviation safety…
The 2 primary means of oversighting a specific operator’s aviation activities were:
- assessing applications for the issue of, or variations to its air operator’s certificate (AOC) and associated approvals (including approvals of key personnel)
- conducting surveillance of its activities.
CASA was required by Section 28 of the Civil Aviation Act 1988 to satisfy itself about various matters when processing an application for the issue of, or variation to, an AOC. The matters included whether the organisation was suitable and whether it had suitable procedures and practices to ensure that AOC operations were conducted safely.
CASA provided records related to their assessment of MAGSPEC Aviation’s initial AOC and low flying applications.
Initial issue of air operator’s certificate
The CASA entry control process involved assessing an application for the issue of a new AOC or a variation to an existing AOC. The worksheet used by CASA for an AOC assessment was intended to be used in conjunction with the AOC Process Manual, AOC Handbook, other relevant technical assessor handbooks and applicable legislation. This worksheet contained the criteria required for an assessor to undertake a technical assessment. It focused on generic regulatory requirements applicable to most operators and there was no specific criteria that referred to assessing an operator’s primary activity, in this case, low‑level survey operations. Although the assessment process confirmed that the operator had processes and procedures to support its operations, there was no evidence that these were examined in any detail for their suitability for the proposed operations.
However, the CASA officer processing the AOC application acknowledged that, while it was a new operation, the organisation included personnel from a previous operator, and that these personnel had experience and exposure to low‑level survey operations. The officer further stated that this experience was evident during the assessment, interview, and inspection phases of the assessment.
As part of the AOC application, CASA was to also approve the appointment of the CP. The CP’s records included an assessment paper, interview record, and notes from an assessment flight. The assessment focused on the CP’s ability to manage the regulatory requirements of an AOC holder, yet did not indicate how the operator would conduct its low‑level survey operations. The assessment flight did not include any low‑level flying as CASA did not permit its officers to undertake low flying.
The AOC was issued to the operator on 3 October 2017.
In December 2021, CASA amended its AOC entry control procedures to include more emphasis on assessing the proposed primary activity. A specific worksheet was introduced for assessing a Part 138 application and included reviewing the processes that allow an operator to safely conduct and manage its aerial work operation in compliance with the regulations.
Low flying approval
The AOC Handbook acknowledged that low flying was an operational requirement and that an application for low flying under CAR 157(4)(b) was required. This assessment was conducted at the same time as the initial AOC application.
The worksheet for the AOC application did not record any assessment undertaken by CASA to approve the operator to undertake low flying below the levels permitted in CAR 157. However, the assessing officer indicated that a key component of issuing the low flying approval was that the operator had a legitimate requirement and that its CP and line pilots held the required low‑level rating. There was no record of any in depth assessment of how the operator would address the risks associated with low flying. Further, the AOC Handbook did not provide any guidance or instruction on how such an application should be assessed.
The low flying instrument was issued to the operator on 22 September 2017.
Surveillance post‑AOC issue (pre‑accident)
Post‑authorisation review
As at 2017, following the issue of an initial AOC, CASA was to conduct a post‑authorisation review (PAR) of the operator to ensure that all the entry control requirements were being met. This surveillance activity was to be conducted within 6–15 months following the initial issue.[13] As described in the CASA Surveillance Manual, a PAR was a type of level 1 surveillance, which was a structured, forward planned larger surveillance event.
The CASA records showed that a PAR, as defined in its surveillance manual, had not been undertaken on the operator.
In response to the draft report on 3 February 2025, CASA advised the ATSB that:
At the time of the accident CASA conducted its surveillance planning under the National Surveillance Selection Process (NSSP), which was a risk-based methodology for the selection and prioritisation of surveillance events. Under the NSSP an operator such as this did not require a post authorisation review. CASA has since implemented a multi-year surveillance approach whereby all Aerial Work Operators undergo surveillance on a regular basis, irrespective of the degree of risk that CASA has assessed. This multi-year surveillance approach is one of many core elements of CASA’s National Oversight Plan.
On 3 April 2025, the ATSB and CASA had a follow‑up briefing to seek clarification on its responses to the draft report. CASA advised that the obligation for a PAR could also be achieved through an alternative activity, and in this case had been accomplished through the conduct of a level 2 surveillance event. CASA indicated that the level 2 surveillance, conducted in July 2018 (discussed below), was noted in its surveillance system as ‘post authorisation’ and would likely have been similarly scoped to a PAR. Therefore, this was considered an equivalent activity at the time. CASA had not provided the ATSB any supporting documentation indicating that an equivalent activity was permitted, or what should have been considered if this was to be undertaken.
Surveillance in 2018
A level 2 surveillance event was a less formal interaction with an operator and could be in the form of checklist-based compliance and product checks of a specific section of its systems. A level 2 surveillance event took place in July 2018, after the operator’s first occurrence. The planned scope included airworthiness assurance, fuel load control, operational standards, and safety assurance. Nil findings were issued, and the CASA surveillance team noted that the operator was still in the process of reviewing its operating procedures with changes to be reviewed at the next surveillance event scheduled for later in 2018. It was not evident to what extent that low‑level survey operations were examined.
A second level 2 surveillance took place in October–November 2018. The planned scope included the same areas as the previous surveillance with the additional items of:
- airworthiness control
- implementation of the drug and alcohol management plan
- crew scheduling
- flight systems
- safety risk management
- assessments
- training infrastructure
- training management.
Three safety findings and 7 safety observations were issued as a result of that surveillance. The surveillance team noted that the operator was actively trying to mitigate some of the operational risks, but the operations manual was lacking some of the procedures followed by the operator. The findings related to non‑conformance with operations manual procedures, uncontrolled documents, and aircraft defect management.
Observations were not required to be actioned by the operator, although CASA did encourage them to do so. One observation related to fuel load control and procedures for addressing discrepancies in fuel quantity. Another observation related to limited procedures for the completion of the JSA. The surveillance report did not make any findings or observations on overall processes or procedures for low‑level survey operations.
Periodic assessment tool
The authorisation holder performance indicator (AHPI) was a questionnaire‑based tool used by CASA to assess ‘the apparent risk to safety presented by an authorisation holder [operator]’. The AHPI tool consisted of a number of factors and sub‑factors associated with organisational characteristics and performance, commonly thought to affect or relate to safety performance behaviour. This was used by CASA to assist with determining whether any risk‑based surveillance of an organisation was required, and to scope the areas for that assessment.
A number of AHPI assessments had been completed by CASA and 5 out of the 6 AHPIs did not trigger any higher priority for surveillance. The last AHPI prior to the accident was completed in February 2022. CASA noted that there was no record in its system of a formal PAR being conducted, and there was no record of action following the 2019 and 2020 occurrences. The CASA officer recommended surveillance take place at the earliest possible convenience.
Transition to Part 138 regulations
In response to the draft report, on 1 May 2025, CASA advised the ATSB that the accident occurred about 3 months after the commencement of the new flight operations regulations, which included Part 138. Under the transitional arrangements to the new regulations, current holders of an AOC authorising aerial work before 2 December 2021 had this certificate legally recognised as being an ‘aerial work certificate’. These operators were required to ensure that the operations manual complied with Part 138 and contained all the necessary content to enable that compliance.
In this case, as the operator held an AOC prior to 2 December 2021, the content of its operations manual would have been approved by CASA. The operator’s compliance with Part 138 was to be reviewed at the next appropriate CASA oversight event.
While operators were not required to submit their entire operations manual for assessment prior to 2 December 2021, as part of the transition, CASA required operators (no later than 60 days prior) to submit extracts from their operations manual covering 2 key measures. These included change management and procedures for the carriage of aerial work passengers required under Part 138. CASA only required operators to submit their entire updated operations manual immediately before the commencement date of the new regulations.
On 27 September 2021, MAGSPEC provided CASA with its complete operations manual, the HSEMS, including the change management and carriage of aerial work passenger procedures. CASA notified MAGSPEC via email in April 2022 that its initial submissions related to these 2 aspects were not yet compliant. Following a further submission by the operator, on 18 August 2022 CASA advised via email that these areas were ‘compliant’. CASA did not provide any advice related to an assessment of any other parts of the operations manual including those related to operational risk management.
Surveillance post-accident
Shortly after the accident, CASA conducted an initial review to determine if further surveillance of the operator was required. The CASA officer noted that the operator had never undergone a level 1 surveillance event or had a PAR conducted. The officer recommended that a response surveillance event should be scheduled.
On 31 August 2023, the ATSB briefed CASA on the draft investigation findings, which included discussion on the operator’s risk management processes in place at the time of the accident. A similar briefing had also been provided to the operator on 19 July 2023. CASA completed a level 1 systems audit of the operator in September 2023. This level of surveillance is a structured, larger-type event that considers the specific activities conducted by the operator. The audit included a review and follow-up of this accident. The scope included:
- airworthiness and maintenance aspects
- aircraft and passenger loading control
- crew scheduling and fatigue management
- operational standards, and data and documentation
- authorised activities
- flight systems and operational support systems
- safety assurance and safety risk management.
The audit identified 6 safety findings and one observation for the operator related to maintenance documentation, fatigue management, and operations manual compliance. Specifically, one finding regarding the operations manual noted that it did not include all the content as required by the regulations. This included limited detail regarding:
- processes and procedures relating to low‑level operations and manoeuvring and role specific equipment usage (data acquisition system)
- processes and procedures relating to the training of operational and handling procedures with regards to low‑level operations and manoeuvring and role specific equipment usage (data acquisition system).
There were no other findings or observations made regarding the operational risk management processes and procedures.
At the time of the audit, the operator advised CASA that it was waiting for the completion of the ATSB’s investigation prior to initiating any changes to its processes or procedures. However, it was noted that, while the audit was not an investigation, a number of potential latent issues existed, including:
- No active or consistent fatigue monitoring of flight crew during operations other than the required recording of flight and duty records.
- Limited detail in operational risk assessments pertaining to operations in general and the additional fatigue obligations as required by legislation.
- Limited documented operational procedures and associated training relating to low level flight techniques and procedures including the use of operational equipment utilised during survey operations [as detailed above].
- Limited documented process and procedure, and subsequent detail established when conducting internal investigation following operational incidents.
Similar occurrences
Regulatory oversight
Regulatory oversight of air operations has been discussed in detail in previous ATSB investigation reports. These included a fatal Cessna 172 accident at Agnes Waters, Queensland in 2017 (AO‑2017‑005), a fatal Eurocopter EC120B helicopter accident at Hardy Reef, Queensland in 2018 (AO‑2018‑026), and a fatal Eurocopter EC135 helicopter accident at Port Hedland, Western Australia in 2018 (AO‑2018‑022).
These investigations identified that CASA’s regulatory oversight activities had not specifically examined the nature of the operator’s primary activities. The findings were as follows:
The Civil Aviation Safety Authority’s procedures and guidance for scoping a surveillance event included several important aspects, but it did not formally include the nature of the operator’s activities, the inherent threats or hazards associated with those activities, and the risk controls that were important for managing those threats or hazards. (safety issue AO-2017-005-SI-08)
Although the operator’s primary helicopter activity was conducting charter flights to pontoons at Hardy Reef, regulatory oversight activity by the Civil Aviation Safety Authority had not specifically examined the operator’s procedures and practices for conducting operations to these helicopter landing sites.
Although the operator’s primary helicopter activity was conducting marine pilot transfers, regulatory oversight activity by the Civil Aviation Safety Authority had not specifically examined the operator’s procedures and practices for conducting approaches and landings to ships at night in degraded visual cueing environments.
In response to safety issue AO-2017-005-SI-08, CASA amended its surveillance and scoping form to require consideration of current activities. Further, it proposed the addition of an operator profile report to provide current, contextual information on an operator with a view to provide a more effective audit scoping process in which consideration and documentation of an operator’s activities was mandatory.
In response to the draft report, on 3 February 2025, CASA advised the ATSB that:
CASA’s Surveillance activities do not include specific checks of the suitability or effectiveness of the processes and procedures in these specific areas. However, under CASR [Civil Aviation Safety Regulation] Part 138.370, the operator is required to conduct risk assessments and mitigation processes before conducting any particular aerial work operation (that is, they must consider the risk of the specific operation and introduce appropriate mitigants). Surveillance is carried out under set scope of 138 operators under this regulation to ensure the operations are suitably risk assessed.
Based on the actions in response to AO-2017-005-SI-08, the ATSB was of the understanding that an operator’s primary activity was considered in entry control processes and surveillance scope. As such, the above comment was also discussed at the ATSB‑CASA meeting on 3 April 2025. CASA advised that an operator’s primary activity is considered, and when assessing a Part 138 operator it uses a standardised worksheet to ensure there is a consistent approach to that assessment and to maintain a record of the decision‑making process.
Low-level accidents
There has been a number of ATSB investigations into fatal accidents that resulted from a loss of control at low altitude, from which a recovery was not possible.
ATSB investigation AO-2012-059
On 29 April 2012, the owner-pilot of a Cessna 150 aircraft, registered VH‑UWR, was aerial stock mustering on a cattle station about 55 km north‑east of Bourke, New South Wales. The aircraft was observed circling over an area (where cattle were not moving), then entered a steep descent followed by the sound of an impact. The aircraft was substantially damaged, and the pilot sustained fatal injuries.
The ATSB found that, while manoeuvring at low level, the pilot inadvertently allowed the aircraft to aerodynamically stall, resulting in a high rate of descent and collision with terrain. There was insufficient information about pilot control inputs to establish the factors that precipitated the stall.
ATSB investigation AO-2014-192
On 29 December 2014, a Cessna 172S aircraft, registered VH‑PFT, departed Cambridge Airport, Tasmania to photograph yachts participating in the 2014 Sydney Hobart race. On board the aircraft were the pilot and a photographer.
At about 1815 local time, the aircraft commenced low-level photographic runs on yachts to the east of Cape Raoul. Shortly after completing a run on one yacht at a height of about 50 ft, the aircraft entered a steep climbing turn. The aircraft had almost completed a 180° turn when the upper (right) wing dropped sharply while the aircraft’s nose pitched down to almost vertical. The aircraft impacted the water’s surface in an almost vertical nose‑down attitude with wings about level. Both aircraft occupants were fatally injured, and the aircraft was substantially damaged.
As a result of the steep climbing turn, the aircraft’s upper wing aerodynamically stalled, resulting in a rapid rotation out of the turn. The steep pitch attitude indicated that, due to the stalled upper wing, the aircraft entered a spin. There was insufficient height for the pilot to recover the aircraft.
ATSB investigation AO-2021-016
On 13 April 2021, a Cessna R172K aircraft, registered VH-DLA, departed Canberra Airport, Australian Capital Territory, with a pilot and an observer on board to conduct powerline survey work to the north of Sutton township, New South Wales.
About 3 hours into the flight, while conducting a powerline inspection in the vicinity of Tallagandra Lane, nearby witnesses observed the aircraft flying low above the trees before commencing a left turn that continued into a steep descent and collision with terrain. The pilot and observer were fatally injured, and the aircraft was destroyed.
The ATSB found that, while manoeuvring to align the aircraft to inspect a powerline, the aircraft aerodynamically stalled and entered a spin at a height that was insufficient for recovery prior to the collision with terrain.
ATSB investigation AO-2021-052
On 4 December 2021, the pilot of an Air Tractor AT‑400 aircraft, registered VH‑ACQ, was conducting aerial spraying operations on a property 75 km west‑south‑west of Moree, New South Wales.
At 0632 local time, the aircraft took off from the property’s airstrip with the first spray load. The pilot then completed 10 spray loads, each time returning to the airstrip to replenish its load.
Prior to departing with the 11th load, the aircraft was refuelled to full and its spray load refilled. The aircraft then returned to the western side of the target block, but after descending to recommence spraying towards the south, the aircraft climbed and turned away to track north and overfly a flood-affected area. The pilot radioed the company operations manager expressing concern about the weather conditions and the potential for chemical to drift onto a neighbouring property. About 5 minutes later, the aircraft returned to the target block, this time on the eastern boundary.
The pilot then conducted 2 ‘smoker’ runs to assess the drift, followed by 5 back‑to‑back (parallel) spray runs. At the end of the 5th spray run, the aircraft was observed to climb then enter a right procedure turn. During the turn, the aircraft descended rapidly, collided with terrain, and was subsequently destroyed by fire. The pilot sustained fatal injuries.
The ATSB found that the aircraft was too close to the start of the spray run during the turn, which probably resulted in the pilot tightening the turn. This almost certainly resulted in an aerodynamic stall at a height too low to recover before colliding with the ground.
Safety analysis
Introduction
In the afternoon of 3 March 2022, a Cessna U206G, registered VH‑JVR, was being operated on a low‑level geophysical survey flight. When on the 25th survey line, the aircraft collided with terrain and was destroyed in the post‑impact fire. The pilot was fatally injured.
This analysis will discuss the potential reasons for the loss of control and the initiation of the emergency response. The angle of bank regularly used for procedure turns, and the benefits of protective clothing and helmets are also examined. It will also consider the operator’s risk management processes and supporting procedures for low‑level geophysical survey flights, and regulatory oversight of these activities.
Loss of control
The last recorded position of the aircraft was on a survey line consistent with the planned survey parameters. Likewise, a comparison of the available flight data indicated that the aircraft’s location was in a similar position to that of previous procedure turns. Therefore, it was likely that the aircraft was being manoeuvred onto the next survey line at the time of the accident.
The wreckage examination determined that the aircraft impacted the trees in a left angle of bank, with a steep angle of impact and a nose‑down attitude, indicative of a loss of control. The ATSB considered several reasons for the loss of control. There was no evidence to suggest any airborne impact with a bird nor that the weather conditions affected the pilot’s ability to maintain control of the aircraft. To the extent possible, the ATSB determined that the aircraft was structurally intact, there was no flight control malfunction, and the engine was producing power at the time of impact. Further, the pilot did not have any reported health issues, and the post‑mortem and toxicology examinations did not identify the presence of any natural disease or substances. While some causes of incapacitation may not always be identified post‑mortem, there was no evidence to suggest that the pilot had become incapacitated during flight.
The pilot had previously conducted 24 survey lines with no apparent issues identified from the recorded data. Based on the ATSB’s analysis, the aircraft’s airspeed had remained above the aerodynamic stall speed during the procedure turns. Therefore, there was no indication of a near or actual stall on the previous turns. Although, the data identified that the procedure turns were consistently conducted at heights below which a recovery from a stall and loss of control may not be possible. A stall situation was a plausible explanation, as found in previous ATSB investigations into low‑level accidents. However, in this case, this remained only a possibility due to the lack of recorded data beyond the last known position and no witness observations, making it difficult to determine the precise circumstances that led to the loss of control and collision with terrain.
Contributing factor It was likely that, during a manoeuvre to intercept the next survey line, for undetermined reasons, control of the aircraft was lost at a height from which recovery was not possible, resulting in a collision with terrain. |
Delayed emergency response
The operator had a phased emergency response plan, predicated on an elapsed time since the aircraft’s estimated time of arrival (ETA). Each phase was commensurate with an escalating level of concern. Unless there was a notification of an accident by other means, the distress phase would commence at 30 minutes past the ETA, at which point the Joint Rescue Coordination Centre (JRCC) would be contacted to initiate search and rescue activity. Each phase of the plan required accessing the satellite tracking system to ascertain the location of the aircraft.
When the satellite tracking data stopped at 1343, the automatic watch function did not send an alert to the operator after 15 minutes had elapsed, as this function had not been activated. This was not noticed until 1430 when the ground operator conducted a periodic check. While the operator reported previously experiencing dropouts of the satellite tracking system, Spidertracks confirmed that up to the loss of data, the device was functioning as expected and that there were no recorded system outages.
The ground operator was not able to contact the pilot via mobile phone and there was no emergency beacon activation. The ATSB noted that, while the aircraft was not fitted with an emergency locator transmitter, a personal locator beacon was carried in the aircraft. However, as this was not worn by the pilot, this was not readily accessible following the accident.
As such, the status of the pilot and aircraft could not be established. The operations manager then advised the ground operator to follow the emergency response plan and wait until the ETA. When the aircraft did not arrive at the ETA of 1630, about 3 hours after the accident, in accordance with the plan the operator contacted the JRCC at 1701.
The JRCC promptly initiated search and rescue procedures, and an aircraft departed at 1739 and located the aircraft wreckage at 1852. A search and rescue helicopter crew physically located the pilot at 0042. With the time taken to access the pilot, whose injuries required immediate medical care, it was very likely that even if the search and rescue activities had commenced when the satellite tracking data was lost, the pilot would have succumbed to the injuries received.
When an accident occurs and any injuries that result are potentially survivable, a timely response is essential. Minimising the time for search and rescue and enabling emergency services to respond as quickly as possible may increase the chances of a successful outcome.
Other factor that increased risk An emergency response was not initiated until 30 minutes after the aircraft's estimated time of arrival, which was 3 hours after satellite tracking had stopped and attempts to contact the pilot had been unsuccessful. Although an earlier response was very unlikely to have altered the outcome in this case, minimising the time for search and rescue and enabling emergency services to respond as quickly as possible may increase the chances of a successful outcome. |
Low-level manoeuvring
The operator’s pilots routinely used high angle of bank procedure turns to manoeuvre between consecutive survey lines. This back‑to‑back pattern was described by the chief pilot (CP) as the most efficient method and it also reduced pilot workload, especially for obstacle and hazard avoidance.
The CP stated that procedure turns were trained to be at about 300 ft above ground level and a 45–60° angle of bank (known as a steep turn). Analysis of the accident flight indicated that the pilot was flying high angle of bank procedure turns consistent with the operator’s training. However, they were turning at an average of about 200 ft, lower than what was explained by the CP.
The ATSB noted that, during the preceding 24 turns, the pilot had maintained sufficient margin above the stall speeds listed in the pilot’s operating handbook. However, as aircraft data was not available up to the loss of control it was not possible to determine if the aircraft stalled nor the exact circumstances that existed.
The similar occurrences discussed involved a loss of control that was preceded by a stall at very low heights. The U206G pilot’s operating handbook stated that up to 240 ft may be required to recover from a stall, but this height was based on flight testing in controlled conditions and that significantly more height may be required.
High angle of bank turns at low level present a significant risk and International Airborne Geophysics Safety Association (IAGSA) recommended that the angle of bank should be limited due to the stall speed increasing with increasing angles of bank, thus reducing the safety margins available. These margins can be quickly eroded if a pilot tightens the turn to ensure they intercept the survey line, which can increase the load factor further, resulting in reaching the stall speed quicker.
Other factor that increased risk In accordance with the operator’s training, pilots routinely used increased angle of bank (45–60°) turns at low altitude to position the aircraft onto survey lines. This increased the risk of an aerodynamic stall at altitudes from which recovery may not be possible. |
Protective clothing and helmets
At the time of the accident, the pilot was not wearing any protective clothing or a helmet. The use of such equipment was not required by the regulator, or the operator having considered environmental, comfort, and cockpit space aspects. Instead, it was left to the individual pilot’s discretion.
The ATSB’s aviation medical specialist indicated that protective clothing and helmets may reduce the magnitude of injuries in an accident. While they were unable to comment on the effectiveness of these items for this accident, it was acknowledged that these items would not have protected the pilot from smoke inhalation.
In some cases, occupants survive an accident only to succumb to hazards such as fire, drowning or environmental elements such as heat and cold (Shanahan, 2004). IAGSA recommended that survey pilots/crew wear protective clothing, not just as fire protection in the event of an accident but to also provide coverage from the elements while waiting for rescue or in a survival situation. Similarly, the Basic Aviation Risk Standard also recommended that all flight and aircrew wear protective clothing during operations. It is therefore important that these hazards have been considered to enable the best opportunity for survival in the event of an accident.
Other factor that increased risk The operator did not require its pilots to wear protective clothing or helmets during low‑level survey operations, nor were they required to do so by regulations. However, the use of such has been recommended by industry to improve survivability in the event of an accident. |
Risk management
In August 2019, MAGSPEC Aviation implemented a health, safety and environmental management system (HSEMS), which was intended to meet the Civil Aviation Safety Authority (CASA) safety management system (SMS) requirements. It also provided more generalised guidance on the management of risk within the organisation. However, as an SMS was not required by regulation, it was not assessed by CASA. The ATSB acknowledges that an operator’s SMS, in this case HSEMS, will evolve and mature with time. Significant events like accidents provide an opportunity to assess if the system is operating in a way that assures the highest level of safety given the nature of their operations.
Acknowledging the CASR Part 138 requirements for aerial work operators to undertake risk assessments, which came into effect about 3 months prior to the accident, the ATSB reviewed the safety risk management component of the HSEMS. The HSEMS manual had detailed the 5‑stage process for risk management. However, there was no requirement in the operator’s manuals, as required by Part 138, to conduct a pre‑operational risk assessment nor had one been completed, as confirmed by the CP.
The absence of a pre‑operational risk assessment did not allow formal mitigation strategies, nor provide assurance that the risk level associated with low‑level survey operations was as low as reasonably practical. For example, the operator reported that the survey flights were often flown at about 30 m (100 ft) above ground level. While low operating heights were specified in the job safety analysis (JSA), there was no formalised risk controls referred to in the JSA. The accident survey flight had been flown at 25 m (85 ft) and this had been accepted on the basis of the reconnaissance flight, without any formal identification and implementation of supporting risk controls. While IAGSA acknowledged that stipulating a fixed minimum safe survey height was not practical given differences in survey conditions and aircraft characteristics, a pre‑operational risk assessment for operations at a reasonably anticipated operating height may have provided a foundation from which to adequately assess any variations to this height.
Further, the operator routinely flew consecutive survey lines, which used increased (steep) angle of bank procedure turns (45–60°) to manoeuvre between the lines. There was no assessment to identify any risks associated with conducting higher angle of bank turns at low-level to ensure that reasonable mitigations were implemented, and appropriate safety margins were applied.
The HSEMS further outlined that non‑site‑specific hazards were reported in their online SMS program, but due to the varying nature of operations, a separate site‑specific assessment of each survey job would be completed using the JSA. With the JSA, each survey task was assessed in isolation, with no reference to previous JSAs to ensure that applicable risk controls continued to be applied and/or were appropriate. Also, the JSA did not benefit from being informed by an overarching pre‑operational risk assessment. Therefore, as the predominant method for assessing operational risk, the JSA did not provide assurance that all hazards would be identified, and the associated risks would be assessed and mitigated.
As noted by the International Civil Aviation Organization (2018), safety risk management activities should be documented and the Part 138 Manual of Standards stipulated that the operator’s pre‑operational risk procedures were to include the use of a risk register. The CP reported that an operational risk register was not being maintained as part of their HSEMS at the time of the accident. While non‑site‑specific hazards would be recorded and assessed in the online SMS program, there was a missed opportunity to record the site‑specific hazards identified from the individual JSAs. Therefore, without a risk register, the operator’s ability to track, monitor, and mitigate all known hazards, and assess the effectiveness of existing risk controls was limited.
In interactions with CASA during the transition phase to Part 138 and the level 1 surveillance event post‑accident, there was no commentary related to the adequacy of the operator’s operational risk management processes. On that basis, the operator was of the understanding that the JSA met the risk assessment requirements of Part 138 inclusive of a pre‑operational risk assessment. However, CASA has since advised the ATSB that the JSA did not meet the requirements of a pre‑operational risk assessment.
Other factor that increased risk MAGSPEC Aviation's safety risk management processes did not include a pre‑operational risk assessment that recognised the generic risks and hazards common across that type of operation nor was a risk register maintained. Consequently, there was limited assurance that all the risks had been identified and that all reasonable mitigations had been applied. (Safety issue) |
Survey manoeuvres
As emphasised by IAGSA, conducting steep turns at low level can present challenges for fixed‑wing aircraft as any margin above the stall speed can quickly diminish and there may be limited height within which to respond to an unexpected situation. The ATSB’s analysis of the flight data showed there was some variation in the angle of bank used during the procedure turns on the accident flight, ranging from 43° up to the Cessna U206G angle of bank limit of 60°. At this limit, the stall speed increases by about 40%. The data also indicated that the procedure turns were conducted at an average of about 200 ft above ground level, which was lower than what was explained by the CP.
Similarly, a review of the morning pilot’s flight and discussions with other company pilots identified that there were differences in the individual turn techniques, demonstrating variations of the procedure turns.
While 45–60° angle of bank procedure turns were being taught, the operations manual did not include any policy or procedure for this manoeuvre. Further, there were no specific limits identified, such as a minimum turn height or maximum angle of bank, to establish appropriate safety margins such as that recommended by IAGSA.
ATSB research investigation report B2004/0337 discussed the importance of operational procedures:
The absence, deficiency or inappropriateness of operating procedures for operators may increase the risk to aviation safety.
The absence of standardised procedures means there may be considerable differences in the techniques used by different operators and contracting organisation staff to conduct tasks. Processes that are used to accomplish a particular task will evolve through a process of experience and passing on this information, often by word of mouth. There will be inconsistencies in how the task is accomplished, as different staff and operators will have differing levels of competence and experience, and different solutions to the same problem will have naturally evolved. The organisation that is managing the operation in such an uncontrolled environment will not be in full control or fully aware of how its tasks are being accomplished and therefore will have less control over the safety of the operation.
While the ATSB was unable to determine the circumstances that led to the loss of control, an operator’s expectations and desired safety margins should be documented to minimise variation and ensure operations are performed safely. Otherwise, without formal procedures, pilots are required to exercise judgement based on their experience, skills and knowledge.
Other factor that increased risk The operator’s pilots were trained to, and routinely flew survey patterns utilising steep turns at low level. However, procedures or limitations specific to these manoeuvres were not included in the operations manual, which increased the risk of inconsistencies in the application of those manoeuvres and reducing the safety margins available. |
Flight following
Survey flights are often conducted over remote, inhospitable terrain where regular communication services may not be available. Therefore, the use of satellite‑based flight following services are essential for providing real‑time monitoring of an aircraft’s location and for an efficient search and rescue response.
The operator had installed Spidertracks to all its aircraft and there was an expectation that an automatic alert would be received from the system in the event of emergency. However, there was no requirement and supporting procedure to check the functionality of the system prior to each flight. In this case, the alert function had not been activated for multiple flights, including the accident flight, which potentially influenced the delayed emergency response. Also, while the ground operator assigned to each tasking was responsible for providing flight following services, there was no expected schedule for checking the satellite tracking nor any procedure detailing the expectations of this role. Despite this, given the severity of the pilot’s injuries, it was very unlikely that a prompt emergency response would have changed the outcome.
It is important that an emergency response plan clearly identifies the notification and escalation triggers to avoid delays. Satellite tracking systems are useful in their ability to provide early notification of an emergency, especially in cases where the occupants have been incapacitated or otherwise unable to raise an alarm. However, their usefulness can only be realised if, when installed, they are correctly configured and operating as expected, otherwise increasing the risk of a delayed response.
Other factor that increased risk While the operator’s aircraft were fitted with a satellite‑based flight following system, there was no requirement nor were there supporting procedures to confirm the set‑up and functionality of the system prior to flight or to monitor the system during flight. This increased the risk of the system not operating as expected and not providing early notification of an emergency. |
Regulatory oversight activity
Since 2019, 3 ATSB investigations have been published identifying that regulatory oversight did not formally include the nature of the operator’s primary activities, the inherent threats or hazards associated with those activities, and the risk controls for managing those threats or hazards.
The ATSB acknowledges that CASA’s regulatory oversight activities were subject to normal constraints of time and resources, which may limit an ability to identify issues. Therefore, regulatory surveillance cannot examine every aspect of an operator’s activities, nor identify all the limitations associated with these activities.
The initial air operator’s certificate assessment of the operator and CP focused on the generic regulatory requirements and there were no criteria to evaluate their primary activity of low‑level survey operations. Although CASA had considered the operator and its key personnel as being suitable to conduct the proposed operations, there was no evidence that the processes and procedures for the primary activity had been specifically examined. Likewise, while the operator’s pilots held the appropriate low-level rating, there were no records to indicate that a detailed assessment of how the operator would address the risks associated with low flying had been conducted as part of the low flying approval.
Prior to this accident, the operator had undergone surveillance twice in 2018, following the first occurrence. Operational standards were included in the scope for both surveillance events but there were no related findings made by CASA nor was there any indication to what extent the operator’s low-level survey operations were examined.
The last AHPI review in early 2022 also noted that no post‑authorisation review (PAR) had been conducted following the initial issue of the air operator’s certificate (AOC) and there were no CASA records of action following the 2019 and 2020 occurrences. Consequently, it was recommended that a surveillance activity take place. The same recommendation was also made following this accident. The subsequent surveillance event in 2023 identified that the operator had limited documented operational procedures and training related to low‑level flight techniques.
CASA advised that a PAR (a type of level 1 surveillance) was likely to have been covered by an alternative level 2 surveillance event. The ATSB noted that a level 1 event was more comprehensive than a level 2, and for a PAR, was intended to ensure that the entry control requirements were being met following the initial issue of an AOC. As the CASA officers had made comments about a PAR having never been conducted, it was unclear whether the level 2 was sufficient to have been considered as having met the requirement of a PAR.
While none of CASA’s activities specifically focused on topics related to low‑level survey operations, for example survey patterns and heights, it was difficult to determine whether additional focus, through the conduct of a level 1 PAR for example, would have identified the specific aspects as found in the post‑accident surveillance event. However, CASA has since strengthened its AOC entry control procedures and surveillance planning and scoping to include more emphasis on assessing the primary activity including the use of a specific worksheet that highlights areas specific to Part 138 operators. Consideration of the primary activity provides a level of assurance that operators continue to meet the established requirements and function at the level of competency and safety required to undertake the activity for which they have been approved to perform.
In addition to the above, and as previously discussed, the ATSB identified deficiencies with the operator’s risk management processes. As the requirement for risk assessments only came into effect about 3 months prior to the accident, with the introduction of Part 138, there was limited opportunity for CASA to review these processes within that period. It was also noted that CASA had intended to look at the operator’s Part 138 compliance at the next scheduled surveillance event.
The 2023 surveillance event, which was also a review and follow-up to the accident, was a level 1 surveillance and included risk management within the scope of that activity. However, there were nil findings or observations identifying that there was no pre‑operational risk assessment and risk register, although required under Part 138. As an unintended consequence of this and the transition process to Part 138, the operator was of the understanding that the JSA satisfied this requirement. However, CASA has since indicated to the ATSB that the JSA did not meet the requirement of a pre‑operational risk assessment. While post‑accident, the 2023 surveillance event was a missed opportunity for CASA to identify the deficiencies in processes and inform the operator’s understanding of their risk assessment obligations under Part 138.
Other factor that increased risk The Civil Aviation Safety Authority regulatory oversight of the operator had not specifically included the primary activity of low‑level survey flights, or the processes and procedures designed to reduce the risks associated with that activity. |
Findings
ATSB investigation report findings focus on safety factors (that is, events and conditions that increase risk). Safety factors include ‘contributing factors’ and ‘other factors that increased risk’ (that is, factors that did not meet the definition of a contributing factor for this occurrence but were still considered important to include in the report for the purpose of increasing awareness and enhancing safety). In addition ‘other findings’ may be included to provide important information about topics other than safety factors. Safety issues are highlighted in bold to emphasise their importance. A safety issue is a safety factor that (a) can reasonably be regarded as having the potential to adversely affect the safety of future operations, and (b) is a characteristic of an organisation or a system, rather than a characteristic of a specific individual, or characteristic of an operating environment at a specific point in time. These findings should not be read as apportioning blame or liability to any particular organisation or individual. |
From the evidence available, the following findings are made with respect to the collision with terrain, involving a Cessna U206G registered VH-JVR, 124 km west of Norseman, Western Australia, on 3 March 2022.
Contributing factors
- It was likely that, during a manoeuvre to intercept the next survey line, for undetermined reasons, control of the aircraft was lost at a height from which recovery was not possible, resulting in a collision with terrain.
Other factors that increased risk
- An emergency response was not initiated until 30 minutes after the aircraft's estimated time of arrival, which was 3 hours after satellite tracking had stopped and attempts to contact the pilot had been unsuccessful. Although an earlier response was very unlikely to have altered the outcome in this case, minimising the time for search and rescue and enabling emergency services to respond as quickly as possible may increase the chances of a successful outcome.
- In accordance with the operator’s training, pilots routinely used increased angle of bank (45–60°) turns at low altitude to position the aircraft onto survey lines. This increased the risk of an aerodynamic stall at altitudes from which recovery may not be possible.
- The operator did not require its pilots to wear protective clothing or helmets during low‑level survey operations, nor were they required to do so by regulations. However, the use of such has been recommended by industry to improve survivability in the event of an accident.
- MAGSPEC Aviation's safety risk management processes did not include a pre‑operational risk assessment that recognised the generic risks and hazards common across that type of operation nor was a risk register maintained. Consequently, there was limited assurance that all the risks had been identified and that all reasonable mitigations had been applied. (Safety issue)
- The operator’s pilots were trained to, and routinely flew survey patterns utilising steep turns at low level. However, procedures or limitations specific to these manoeuvres were not included in the operations manual, which increased the risk of inconsistencies in the application of those manoeuvres and reducing the safety margins available.
- While the operator’s aircraft were fitted with a satellite-based flight following system, there was no requirement nor were there supporting procedures to confirm the set‑up and functionality of the system prior to flight or to monitor the system during flight. This increased the risk the system not operating as expected and not providing early notification of an emergency.
- The Civil Aviation Safety Authority regulatory oversight of the operator had not specifically included the primary activity of low-level survey flights, or the processes and procedures designed to reduce the risks associated with that activity.
Safety issues and actions
Central to the ATSB’s investigation of transport safety matters is the early identification of safety issues. The ATSB expects relevant organisations will address all safety issues an investigation identifies. Depending on the level of risk of a safety issue, the extent of corrective action taken by the relevant organisation(s), or the desirability of directing a broad safety message to the aviation industry, the ATSB may issue a formal safety recommendation or safety advisory notice as part of the final report. All of the directly involved parties are invited to provide submissions to this draft report. As part of that process, each organisation is asked to communicate what safety actions, if any, they have carried out or are planning to carry out in relation to each safety issue relevant to their organisation. Descriptions of each safety issue, and any associated safety recommendations, are detailed below. Click the link to read the full safety issue description, including the issue status and any safety action/s taken. Safety issues and actions are updated on this website when safety issue owners provide further information concerning the implementation of safety action. |
Risk management framework
Safety issue number: AO-2020-011-SI-01
Safety issue description: MAGSPEC Aviation's safety risk management processes did not include a pre‑operational risk assessment that recognised the generic risks and hazards common across that type of operation nor was a risk register maintained. Consequently, there was limited assurance that all the risks had been identified and that all reasonable mitigations had been applied.
Safety recommendation to MAGSPEC Aviation Pty Ltd
The ATSB makes a formal safety recommendation, either during or at the end of an investigation, based on the level of risk associated with a safety issue and the extent of corrective action already undertaken. Rather than being prescriptive about the form of corrective action to be taken, the recommendation focuses on the safety issue of concern. It is a matter for the responsible organisation to assess the costs and benefits of any particular method of addressing a safety issue. |
Safety recommendation number: AO-2022-011-SR-01
Safety recommendation description: The Australian Transport Safety Bureau recommends that MAGSPEC Aviation Pty Ltd develops and maintains a pre-operational risk assessment and risk register that is separate to its existing job safety analysis process. This should encompass the generic risks and hazards common across its operations and allow it to fully consider operational risks beyond individual survey tasks.
Safety action not associated with an identified safety issue
Whether or not the ATSB identifies safety issues in the course of an investigation, relevant organisations may proactively initiate safety action in order to reduce their safety risk. The ATSB has been advised of the following proactive safety action in response to this occurrence. |
Additional safety action by MAGSPEC Aviation Pty Ltd
In response to this accident, MAGSPEC Aviation has taken the following safety action:
- The JSA has been revised to include the selection of consequence and likelihood to determine a risk for each identified hazard. It also recorded mitigations that would be applied. The operator advised the overall and highest risk scores determined whether the survey could proceed and/or if it was likely to increase the fatigue and safety of the operation to unacceptable levels.
- The health, safety and environmental management system has been incorporated into the operations manual as an appendix.
- The emergency response plan was revised to clarify initiation triggers and accounted for a satellite tracking system failure. The operator has also equipped its operations room with 2 dedicated monitors for the sole purpose of tracking aircraft.
- The operations manual now includes a minimum speed versus angle of bank section and pilot actions if an aircraft cannot achieve or maintain the required speed.
- Guidance on procedural turns has been formalised in the operations manual. Although there is a description of how to conduct the turn, the manual also explains that this was the desired turn method and may not always be possible (due to terrain, obstacles, block shape et cetera).
- The operations manual has been amended to clearly state that an aircraft was required to have a fixed emergency locator transmitter. If this becomes unserviceable or has to be removed, the aircraft can only be flown for the purpose of having the issue rectified.
- Each pilot has been issued with a personal locator beacon, individually registered with the Australian Maritime Safety Authority. Pilots are required to keep the device on their person while operating company aircraft. The operations manual also states that the personal locator beacon cannot be carried/used if not tested.
- Follow-up with Spidertracks is to be made on each occurrence of dropout, service interruption or delay in tracking updates and numerous improvements made to the interface. The operator advised that the SOS automatic watch function and alert has been investigated and rectified. A checklist item has been added to ensure Spidertracks is correctly functioning prior to departure.
- They no longer operate at survey heights below 30 m.
- The operator identified that its low‑level training syllabus was lacking parameters to mark a pilot as competent, especially in critical phases of flight. This has been formalised to match what had been done practically.
- Its operations manual is currently under review by CASA. This includes items to enable Flight Safety Foundation’s Basic Aviation Risk Standard accreditation. Just prior to final publication of this report, the operator advised that it had been awarded the Basic Aviation Risk Standard accreditation.
Glossary
AGL | Above ground level |
AHPI | Authorisation holder performance indicator |
AoA | Angle of attack |
AOC | Air operator’s certificate |
CAR | Civil Aviation Act |
CASA | Civil Aviation Safety Authority |
CASR | Civil Aviation Safety Regulations |
CoG | Centre of gravity |
CP | Chief pilot |
ETA | Estimated time of arrival |
ELT | Emergency locator transmitter |
G | Gravity |
GPS | Global positioning system |
HSEMS | Health, safety and environmental management system |
IAGSA | International Airborne Geophysics Safety Association |
JRCC | Joint Rescue Coordination Centre |
JSA | Job safety analysis |
MOS | Manual of Standards |
PLB | Personal locator beacon |
POH | Pilot’s operating handbook |
SMS | Safety management system |
Sources and submissions
Sources of information
The sources of information during the investigation included:
- MAGSPEC Aviation Pty Ltd
- other pilots who conducted flights for the operator
- recorded data from the satellite tracking device
- the maintenance organisation
- aviation medical specialist
- Pathwest Laboratory Medicine WA
- Civil Aviation Safety Authority
- Bureau of Meteorology
- Western Australia Police Force
- Australian Maritime Safety Authority Joint Rescue Coordination Centre
- Spidertracks Ltd.
References
Australian Transport Safety Bureau. (2005). Aviation Research Investigation Report B2004/0337 Risks associated with aerial campaign management: Lessons from a case study of aerial locust control. Retrieved from https://www.atsb.gov.au/publications/2005/aerial_locust_control/
Australian Transport Safety Bureau. (2013). ATSB Research Investigation AR-2012-128 A review of effectiveness of emergency locator transmitters in aviation accidents. Retrieved from https://www.atsb.gov.au/publications/2012/ar-2012-128
Civil Aviation Safety Authority, (2021). Civil Aviation Safety Regulations 1998 Part 138 - Aerial work Operations. Retrieved from https://www.legislation.gov.au/F1998B00220/2021-12-02/text
Civil Aviation Safety Authority, (2021). Part 138 (Aerial Work Operations) Manual of Standards 2020 Retrieved from https://www.legislation.gov.au/F2020L01402/2021-12-02/text
Civil Aviation Safety Authority, (2022). Aerial work risk management (advisory circular AC138-05 v2.0) Retrieved from https://www.casa.gov.au/aerial-work-risk-management
Federal Aviation Administration, (2021). Airplane Flying Handbook, FAA-H-8083-3C. US: FAA. Retrieved from Airplane Flying Handbook | Federal Aviation Administration (faa.gov)
Flight Safety Foundation, (2022). Basic Aviation Risk Standard Implementation Guidelines. (Version 9 2022). Retrieved from https://flightsafety.org/bars/the-bar-standards-and-manuals/
International Airborne Geophysics Safety Association. (2017). Safety Policy Manual (v2017-1201). Retrieved from https://iagsa.ca/
International Civil Aviation Organization. (2018). Safety Management Manual, fourth edition, Montréal: International Civil Aviation Organization.
Shanahan, D.F. (2004). Human tolerance and crash survivability. RTO HFM Lecture Series on ‘Pathological Aspects and Associated Biodynamics in Aircraft Accident Investigation’. Madrid, Spain.
Submissions
Under section 26 of the Transport Safety Investigation Act 2003, the ATSB may provide a draft report, on a confidential basis, to any person whom the ATSB considers appropriate. That section allows a person receiving a draft report to make submissions to the ATSB about the draft report.
A draft of this report was provided to the following directly involved parties:
- MAGSPEC Aviation Pty Ltd
- other pilots who conducted flights for the operator
- Civil Aviation Safety Authority.
Submissions were received from:
- MAGSPEC Aviation Pty Ltd
- Civil Aviation Safety Authority.
The submissions were reviewed and, where considered appropriate, the text of the report was amended accordingly.
Purpose of safety investigationsThe objective of a safety investigation is to enhance transport safety. This is done through:
It is not a function of the ATSB to apportion blame or provide a means for determining liability. At the same time, an investigation report must include factual material of sufficient weight to support the analysis and findings. At all times the ATSB endeavours to balance the use of material that could imply adverse comment with the need to properly explain what happened, and why, in a fair and unbiased manner. The ATSB does not investigate for the purpose of taking administrative, regulatory or criminal action. TerminologyAn explanation of terminology used in ATSB investigation reports is available here. This includes terms such as occurrence, contributing factor, other factor that increased risk, and safety issue. Publishing informationReleased in accordance with section 25 of the Transport Safety Investigation Act 2003 Published by: Australian Transport Safety Bureau © Commonwealth of Australia 2025
Ownership of intellectual property rights in this publication Unless otherwise noted, copyright (and any other intellectual property rights, if any) in this report publication is owned by the Commonwealth of Australia. Creative Commons licence With the exception of the Commonwealth Coat of Arms, ATSB logo, and photos and graphics in which a third party holds copyright, this report is licensed under a Creative Commons Attribution 4.0 International licence. The CC BY 4.0 licence enables you to distribute, remix, adapt, and build upon our material in any medium or format, so long as attribution is given to the Australian Transport Safety Bureau. Copyright in material obtained from other agencies, private individuals or organisations, belongs to those agencies, individuals or organisations. Where you wish to use their material, you will need to contact them directly. |
[1] Aerodynamic stall: occurs when airflow separates from the wing’s upper surface and becomes turbulent. A stall occurs at high angles of attack, typically 16˚ to 18˚, and results in reduced lift.
[2] Integral fuel tanks are part of the aircraft structure. They are manufactured by assembling parts of the aircraft structure with sealant to form a fuel-tight compartment, most commonly in the wings.
[3] A supplemental type certificate is a type certificate issued when an applicant has received regulatory approval to modify an aeronautical product from its original design. The supplemental type certificate, which incorporates by reference the related type certificate, approves not only the modification but also how that modification affects the original design.
[4] The system was pre-programmed by the ground operator prior to departure, minimising any manipulation required by the pilot during flight.
[5] From the pilot’s operating handbook, the calibrated airspeed and indicated airspeed in the range of interest were within 1 kt, so for the purposes of the analysis were considered equivalent. The term indicated airspeed is used throughout the analysis.
[6] G load: the nominal value for acceleration. In flight, G load represents the combined effects of flight manoeuvring loads and turbulence and can have a positive or negative value.
[7] A steep turn is one greater than a 45° bank angle.
[8] Carbon monoxide is a colourless, odourless, tasteless, and poisonous gas that is produced as a by-product of burnt fuel. Exposure to a leak from the exhaust of an aircraft engine into the cabin can lead to elevated levels of carbon monoxide, which can impair cognitive function.
[10] CAR 157 (2) requires that an aircraft shall not fly over a populous area at a lower height than 1,500 ft or any other area at a lower height than 500 ft. CAR 157 (4)(b) states that the provisions of CAR 157 (2) shall not apply if the aircraft is engaged in aerial work operations and the operator has a permit from the authority (CASA) to do so.
[11] As the wing to which the stall warning vane is mounted approaches the critical AoA, the relative air flow changes direction and will push the vane up, closing a switch in the device. This will activate a warning horn.
[12] Donesafe is a web and application‑based safety management system tool.
[13] This timeframe has since changed with the most recent being 12-18 monthsfollowing the initial issue, depending on the type of authorisation issued (CASA Surveillance Manual version 5.2 ‑ May 2024).