Executive summary
What happened
On 11 January 2022, a Robinson Helicopter Company R22 Beta helicopter with registration VH‑VHE, was participating in a mustering operation south-west of Mitchell, Queensland. At approximately 1015, 25 minutes into the second mustering flight of the day, the pilot heard a ‘pop’ and a ‘crack’ and experienced a significant uncommanded yaw and abnormal vibration. The pilot completed a forced landing from an altitude of approximately 3 to 5 metres, shut down the engine and inspected the helicopter; identifying that the tail rotor drive shaft had fractured.
What the ATSB found
The ATSB found that the intake valve in the engine’s number-four cylinder sustained thermal damage, which led to reduced engine performance and required the pilot to conduct a forced landing. During the forced landing, for reasons that could not be determined, the tail rotor drive shaft fractured as a result of torsional overstress.
In addition, an unapproved modification was present on the leading edge of the tail rotor blades, although this probably had no influence on the occurrence.
Safety message
This occurrence illustrates the potential seriousness of unexpected yaw and reduced engine performance during flight. These characteristics in piston engine helicopters may be symptomatic of developing engine intake valve damage. If this condition remains unattended it can lead to an increased risk of induction backfire events and significant loss of engine power.
When a loss of engine power or abnormal operation is encountered, an appropriately‑licensed maintenance engineer should complete an engine cylinder inspection in accordance with the helicopter and engine manufacturer’s requirements before further flight.
There is an opportunity to improve the understanding of engine intake valve issues with better quality data. Maintenance organisations are therefore encouraged to follow the Civil Aviation Safety Authority (CASA) recommendation for borescope inspections of valves and report any defects or nil-defect findings.
Decisions regarding whether to conduct an investigation, and the scope of an investigation, are based on many factors, including the level of safety benefit likely to be obtained from an investigation. For this occurrence, a limited-scope investigation was conducted in order to produce a short investigation report, and allow for greater industry awareness of findings that affect safety and potential learning opportunities. |
The occurrence
On 11 January 2022, a Robinson Helicopter Company (RHC) R22 Beta helicopter, registered VH‑VHE and operated by Diamond T Helicopters, was participating in a mustering operation south‑west of Mitchell, Queensland. The pilot was the only person on board.
Prior to the first flight of the day, the pilot prepared the helicopter for operation and completed pre‑flight checks, with no anomalies observed. The pilot then performed a stabilised hover check[1] and conducted a 1.1 hour positioning flight to the mustering location, departing at 0530 Eastern Standard Time.[2] After shutting down, the pilot then refuelled the helicopter and completed the first mustering flight, which took 2.5 hours. The pilot shut down the helicopter and again refuelled. Both flights were reported to be free from incident or abnormalities.
At about 0950, the pilot commenced a second mustering flight. About 25 minutes into the flight, the pilot heard a ‘pop’ and a ‘crack’, then experienced a significant uncommanded yaw[3] and abnormal vibration. The pilot conducted a forced landing, with a degree of pedal control, from height of 10 to 15 ft above ground level. As the skids touched the ground, the pilot heard another ‘crack’ and felt the helicopter go ‘into a spin’.
The pilot remained in the helicopter while completing shut down, including waiting for the cylinder head temperature to reduce. Inspection following shut down revealed that the tail rotor drive shaft was fractured.
Subsequent technical inspection by the maintenance organisation revealed that the number-four cylinder could not hold the required pressure and the intake valve had significant thermal damage and guttering[4] (see the section titled Context - Examination by maintenance organisation).
Context
Examination by maintenance organisation
The helicopter was examined by a maintenance organisation who initially identified the following:
- the tail rotor drive shaft had fractured approximately 5 mm forward of the rear flange weld (Figure 1 and Figure 2)
- rotational scoring was present on the internal surface of the tailcone adjacent to the fracture location
- the tail rotor blade surfaces were free from evidence of foreign object damage, and the skid tube (shown schematically in Figure 1) was free from contact indications
- there was erosion on the leading-edge of the main rotor blades and the tail rotor blades
- epoxy additions were present on the tip of the leading-edge of the tail rotor blades (Figure 3), which were reportedly applied to increase blade wear resistance.
Figure 1: Tail rotor drive shaft fracture location
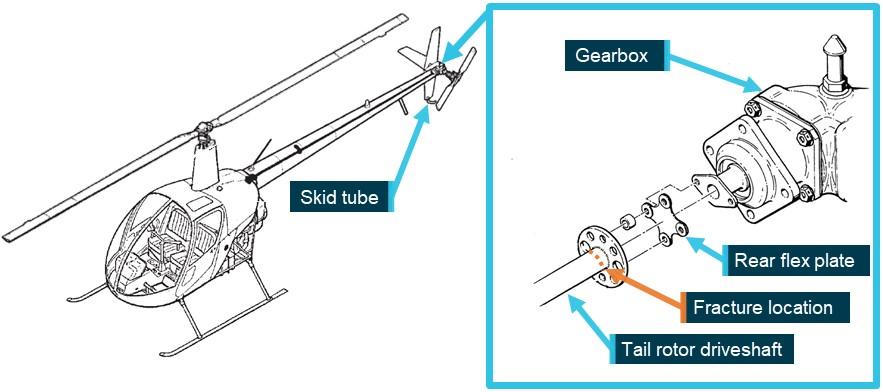
The fracture location is approximately 5mm forward of the rear flange weld.
Source: Robinson Helicopter Company, annotated by the ATSB
Figure 2: Fractured tail rotor drive shaft
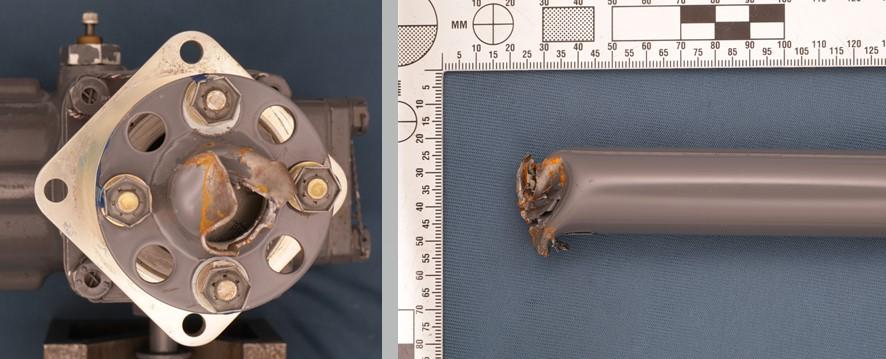
The fracture shows significant plastic deformation. The corrosion product was not present at time of the occurrence.
Source: ATSB
Figure 3: Tail rotor blade leading edge erosion and blade modification
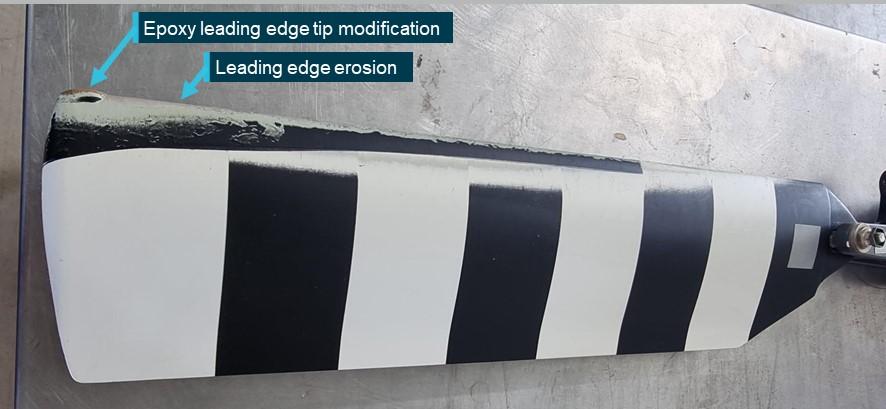
Both tail rotor blades exhibited erosion and a leading-edge tip modification. There was no indication consistent with a strike to either tail rotor blade.
Source: Maintenance organisation, annotated by the ATSB
During the post-occurrence inspection of the engine, maintenance engineers identified that the number-four cylinder was unable to hold pressure when subjected to a hot-compression check. The maintenance organisation removed the cylinder and, on further inspection, identified thermal damage and guttering to the intake valve (Figure 4). The bottom of the valve exhibited an asymmetric burn pattern, which was evidence of severe and uneven heating. The guttering present on the valve face provided a gas leakage path between the cylinder and the intake manifold.
Figure 4: Damaged engine intake valve from number-four cylinder
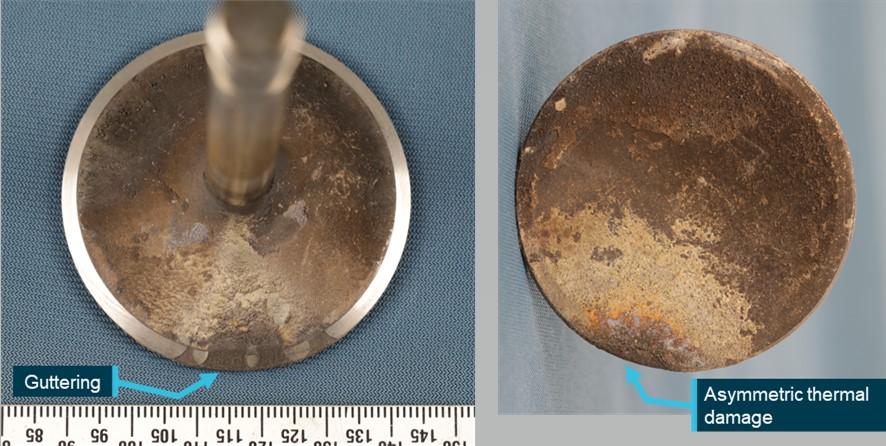
The asymmetric burn pattern on bottom on valve is evidence of severe and uneven heating. The valve face guttering is a leakage path between the cylinder and the intake manifold. The valve was ground by the maintenance organisation, following removal, to ‘clean’ the face to enhance the appearance of the thermal damage. The appearance of the face immediately following the occurrence was not recorded.
Source: ATSB
The maintenance organisation inspected the drive train components, and observed that:
- the intermediate flex plate was undamaged
- the tail rotor gearbox chip detector was free from debris and the gearbox oil was clear
- the clutch assembly operated without defect or roughness, and the lubricating fluid was free from contaminants or fragments.
ATSB technical examination
Additional examination of the damaged number-four cylinder intake valve, tail rotor gearbox, and the fractured tail rotor drive shaft was completed at the ATSB’s technical facilities.
The ATSB examination found:
- confirmation of the thermal damage and guttering on the intake valve[5]
- correct assembly of the tail rotor drive shaft to the gear box yoke connection
- no anomalies with the gearbox bevel gears and bearings that could have restricted movement of the drive shaft were identified
- the turning resistance of the tail rotor gear box was consistent with manufacturer's advice.
The direction of the torsional deformation of the driveshaft was indicative of either drag on the tail rotor assembly or over-torque from the driving side of the failure location.
Examination at high magnification, using both an optical and scanning electron microscope, of the mating fracture surfaces of the drive shaft revealed only gross ductile overstress features. A polished and etched cross section, and hardness measurements taken through the weld connecting the shaft to the flange, found the weld to be heat-relieved, which was consistent with the manufacture’s specifications. Energy dispersive spectroscopic analysis found the composition of the alloy to also be consistent with the manufacturer’s specifications.
There were no pre-existing defects identified from manufacture, or operational damage such as surface scoring, fatigue cracking, denting, or corrosion that might have otherwise weakened the shaft and predisposed it to fracture.
Operational and maintenance history
VH-VHE was manufactured by the Robinson Helicopter Company (RHC) in 2010 and first registered in Australia in the same year. The helicopter was powered by a Lycoming Engines (Lycoming) four-cylinder O-360-J2A engine. The helicopter had accumulated 2,135.5 hours total time in service.
The helicopter was overhauled in August 2021 and new Lycoming engine cylinder kits[6] were fitted at that time. The pilot stated that the engine seemed underpowered, when compared with engine power prior to the overhaul. The tail rotor drive shaft was also replaced with a new item at the overhaul.[7]
The next 100-hourly scheduled inspection (75.7 hours following overhaul),[8] included compression checks[9], service limitations for valves checks,[10] and valve guide condition checks.[11] The compression checks found inadequate compression in the number-two and number-three cylinders, and the cylinders were reconditioned. At this inspection, the number‑four cylinder recorded adequate compression (78/80 pounds per square inch). The pilot stated that the power was improved following this inspection and cylinder reconditioning; however, was still underpowered compared with prior to the overhaul. The maintenance organisation did not perform, nor was there a requirement for them to perform, borescope inspection of the valve faces.
The helicopter accrued 93.3 hours in service from overhaul to the occurrence flight. The pilot reported that they did not observe any adverse indications or unusual behaviour of the engine, such as rough running, yawing, or backfiring during the numerous flights leading up to the occurrence.
The maintenance organisation had a practise of applying epoxy to the leading edge, adjacent to the tips, of the tail rotor blades to extend the interval between re-painting. The epoxy was applied to the blades at the first instance re-painting was required. The maintenance organisation described the modification as
- common practise in rural operations
- low mass
- inspected during scheduled maintenance
- checked for balance, as part of blade balancing, following their addition and/or repainting.
The maintenance organisation did not observe a change in the condition of the epoxy after the occurrence, except that the paint had eroded.
Manufacturers’ advice in response to the occurrence
The ATSB sought comment from Lycoming regarding the condition of the damaged intake valve and the acceptable compression check result for the number-four cylinder, which occurred 17.6 hours prior to the occurrence. However, no advice was received at the time of writing.
With regards to the subject occurrence, RHC advised that the VH-VHE tail rotor drive shaft fracture was consistent with a tail rotor strike, described as anything that creates a sudden resistance or drag to the tail rotor blade(s). They went on to state that a strike does not always result in damage to the blades, nor always leave an identifiable residue. The location of the tail rotor drive shaft fracture, in the event of a strike, can vary, but the fracture location in this occurrence would not be unusual for a strike.
ATSB investigation AO-2021-008 (see the section titled Other occurrences - Tail rotor drive shaft fracture) had similarities to this occurrence. Consequently, the ATSB asked RHC whether there could be causal link between the engine response to intake valve failure, the instinctive pilot control inputs, the landing, and fracture of the tail rotor drive shaft. RHC stated that in the event of a sudden power loss followed by an instant increase in power, the input spike could distort the tail rotor drive shaft, possibly to the extent of twisting the shaft, provided that the contributing circumstances were extreme.
RHC also advised that the epoxy blade modifications were unapproved and would prevent inspection of the blade surface for cracking or corrosion. In addition, RHC stated that a helicopter could experience a more catastrophic consequence of the blade modification if an out-of-balance condition developed, possibly resulting in the loss of the entire empennage.
Other occurrences
Cylinder head inlet valve distress
In 2019, prompted by increasing industry reports of engine issues involving RHC R22 and R44 helicopters, the Australian Helicopter Industry Association (AHIA) released an independent industry-supported investigation into durability issues affecting Lycoming O-320, O-360, and
O-540 engines, fitted to RHC R22 and R44 models.[12] The report identified that poor operational durability of intake valves was principally due to accelerated valve, valve guide, and/or valve seat wear. The investigation further stated that these durability issues lead to a loss of cylinder compression and the potential for partial power loss events. The valve damage could result in an induction backfire, engine power loss, and airframe yaw. No one factor was identified as the reason for the accelerated intake valve wear. The report recommended helicopter operators remain vigilant of the issues outlined within the AHIA report and ensure they continue to follow best-practice operation and maintenance protocols.
In October 2020, RHC issued a Safety Alert in response to reports of burned engine intake valves in their R44 model helicopters.[13], [14] The Safety Alert listed three precautions for pilots to follow:
- Perform a complete run up and stabilized hover check prior to every flight. Do not initiate flight if there is any indication of engine roughness or sudden yaw.
- If engine roughness or sudden yaw occurs in flight, land as soon as practical and be prepared to land immediately.
- Following any engine roughness or sudden yaw, have a mechanic check valve condition before further flight. The mechanic should listen for sound of leakage at each intake valve while performing a compression check. Any intake vale with audible leakage requires repair prior to further flight. Check may be done with engine hot or cold.
Subsequently, Lycoming released a service instruction to collect early-life intake valve in-service data for the same RHC R44 models covered in the RHC Safety Alert to further understand the engine durability issues.[15] The ATSB asked Lycoming whether the collected data had revealed any safety relevant information data. At the time of writing, no response had been received, although it was also noted that R22 models were not included in this safety instruction.
In July 2021, Lycoming published a service instruction allowing for the incorporation of rotator-type intake valves into O-360-J2A model engines[16] (the engine model fitted to VH-VHE) to improve valve seating and minimise compression loss at the intake valve seat. Valve rotation is known to improve face and seat wear distribution and cleaning. This optional modification had not been installed on VH-VHE.
The most recent issue of Civil Aviation Safety Authority (CASA) Airworthiness Bulletin 85-025 RHC R22/R44 Engine Intake Valve and Valve Seat Distress, published in August 2021, detailed many of the factors that may contribute to intake valve damage.[17] CASA made numerous recommendations to operators regarding operating procedures and limitations, which included:
- expanding the three recommendations made in the RHC Safety Alert to include all R22 and R44 models
- guidance for operating temperature limitations
- guidance for cool down and shut down procedures.
In addition, CASA strongly encouraged the implementation of regular borescope inspections and reporting of both defect and nil-defect findings to CASA. At the time of ATSB consultation, CASA had not received any borescope inspection results.
Tail rotor drive shaft fracture
A search of the Australian and United States aviation service difficulty reporting databases[18] identified two similar reported instances of a RHC R22 tail rotor drive shaft fracture events, both were Australian‑registered helicopters:
- A defect report, which noted that the failure of the tail rotor drive shaft occurred during take-off and that the helicopter may have experienced an overspeed event or have operated within a resonant speed range.[19]
- The ATSB investigated occurrence AO-2021-008, involving an R22 with registration VH-HCX. This investigation detailed notable similarities with this occurrence. In both occurrences the investigation found a thermally damaged intake valve, a fractured tail rotor drive shaft, no strike indications on the tail rotor blades or stinger, and both pilots stated they did not strike any object. A distinct difference between the two occurrences, however, was that the pilot of VH‑HCX had experienced reduced engine performance and associated momentary uncommanded yawing in the flight just prior to the occurrence, whereas the pilot of VH-VHE experienced no abnormal indications prior to the occurrence. The VH-HCX investigation also found that ‘the [intake] valve from the number-four cylinder of the engine sustained thermal damage, which led to reduced engine performance during the occurrence flight and the requirement for the pilot to perform a forced landing’. The ATSB concluded that the fracture of the tail rotor drive shaft occurred during the running landing; however, the investigation was unable to conclusively determine the reasons for the driveshaft fracture.
Safety analysis
Engine power loss
Approximately 25 minutes into a mustering flight VH-VHE experienced an engine power reduction, induction backfire(s), and yawing event resulting in a forced landing. The unusual engine behaviour was likely due to thermal damage to the intake valve from the number-four engine cylinder, which reduced the effectiveness of the seal between the valve face and the seat.
Neither the pilot nor the maintenance organisation observed any indications of the progressing damage to the intake valve. This included a successful compression test 17.6 flight hours prior to the occurrence. While not required, a borescope inspection may increase the likelihood of detecting valve damage that can lead to degraded engine performance. In this instance, the degradation in engine performance fortunately occurred where conditions were favourable for the forced landing.
Tail rotor drive shaft
The ATSB examination identified that the tail rotor drive shaft fractured in overstress from torsional loading. The reported pedal control, up until the skids touched the ground, suggested that the drive shaft fracture was concurrent with the helicopter touching the ground.
Noting the absence of identified mechanical or material issues with the tail rotor drive train, the ATSB considered two hypotheses to explain the fractured tail rotor drive shaft. These were:
- the tail rotor blades encountered a foreign object
- the altered engine performance, coupled with the pilot control inputs, and the ground contact led to fracturing of the tail rotor drive shaft.
However, there was insufficient evidence to support either of these hypotheses, with the reasons for the driveshaft fracture remaining unknown.
Blade modifications
The tail rotor blade modifications found on VH-VHE were unapproved and had the potential for significant consequences. Using approved and documented engineering processes to make changes to an aircraft system is important, as it ensures the design complies with applicable airworthiness standards or an equivalent level of safety.
Findings
ATSB investigation report findings focus on safety factors (that is, events and conditions that increase risk). Safety factors include ‘contributing factors’ and ‘other factors that increased risk’ (that is, factors that did not meet the definition of a contributing factor for this occurrence but were still considered important to include in the report for the purpose of increasing awareness and enhancing safety). In addition, ‘other findings’ may be included to provide important information about topics other than safety factors. These findings should not be read as apportioning blame or liability to any particular organisation or individual. |
From the evidence available, the following findings are made with respect to the engine failure and forced landing of a RHC R22 Beta helicopter that occurred 130 km south-west of Mitchell, Queensland, on 11 January 2022.
Contributing factors
- Damage to the number-four engine cylinder intake valve allowed the fuel and air mixture, and exhaust gases into the air induction system. This resulted in the degraded engine performance and the forced landing of the helicopter.
Other factors that increased risk
- For reasons that could not be determined, the tail rotor driveshaft failed through torsional overstress, likely during the forced landing.
- An epoxy addition present on the leading edge of the tail rotor blades was an unapproved modification.
Sources and submissions
Sources of information
The sources of information during the investigation included:
- the pilot of VH-VHE
- helicopter maintenance organisations
- Robinson Helicopter Company
- Helicopter Rebuilds Pty Ltd
- Lycoming Engines
Submissions
Under section 26 of the Transport Safety Investigation Act 2003, the ATSB may provide a draft report, on a confidential basis, to any person whom the ATSB considers appropriate. That section allows a person receiving a draft report to make submissions to the ATSB about the draft report.
A draft of this report was provided to the following directly involved parties:
- the pilot of VH-VHE
- Helismart Pty Ltd
- Approved Aircraft Maintenance Pty Ltd
- Lycoming Engines
- Robinson Helicopter Company
- Civil Aviation Safety Authority
- United States National Transportation Safety Board
A submission was received from:
- Robinson Helicopter Company
The submission was reviewed, however it did not result in any change to the report text.
Purpose of safety investigationsThe objective of a safety investigation is to enhance transport safety. This is done through:
It is not a function of the ATSB to apportion blame or provide a means for determining liability. At the same time, an investigation report must include factual material of sufficient weight to support the analysis and findings. At all times the ATSB endeavours to balance the use of material that could imply adverse comment with the need to properly explain what happened, and why, in a fair and unbiased manner. The ATSB does not investigate for the purpose of taking administrative, regulatory or criminal action. TerminologyAn explanation of terminology used in ATSB investigation reports is available here. This includes terms such as occurrence, contributing factor, other factor that increased risk, and safety issue. Publishing informationReleased in accordance with section 25 of the Transport Safety Investigation Act 2003 Published by: Australian Transport Safety Bureau © Commonwealth of Australia 2022 Ownership of intellectual property rights in this publication Unless otherwise noted, copyright (and any other intellectual property rights, if any) in this report publication is owned by the Commonwealth of Australia. Creative Commons licence With the exception of the Coat of Arms, ATSB logo, and photos and graphics in which a third party holds copyright, this publication is licensed under a Creative Commons Attribution 3.0 Australia licence. Creative Commons Attribution 3.0 Australia Licence is a standard form licence agreement that allows you to copy, distribute, transmit and adapt this publication provided that you attribute the work. The ATSB’s preference is that you attribute this publication (and any material sourced from it) using the following wording: Source: Australian Transport Safety Bureau Copyright in material obtained from other agencies, private individuals or organisations, belongs to those agencies, individuals or organisations. Where you wish to use their material, you will need to contact them directly. |
[1] Recommended by Civil Aviation Safety Authority (CASA) issued Airworthiness Bulletin 85‑025 RHC R22/R44 Engine Intake Valve and Valve Seat Distress
[2] Eastern Standard Time (EST): Coordinated Universal Time (UTC) + 10 hours
[3] The pilot was unable to recall the direction of the yaw with certainty.
[4] Guttering is damage caused by combustion extending across the valve sealing faces, progressively damaging the surfaces and further degrading the sealing efficacy in that area. Once valve sealing degrades, combustion gases may increasingly bypass the valve - leading to rapid failure.
[5] The ATSB was unable to assess the condition and appearance of the valve face immediately following the occurrence as the face had been ground.
[6] The installed cylinder kits were revision AJ and did not incorporate rotating intake valves. The most recent kits for this engine incorporate rotating intake valves.
[7] The tail rotor drive shaft was life-limited to 2,200 hours service, or 12 years of service, which ever came first.
[8] This inspection was performed early due to scheduling constraints around the Christmas and New Year period.
[9] Lycoming Service Instruction No. 1191 A, Cylinder Compression, 28 September 1998.
[10] Lycoming Service Bulletin No. 301 B, Maintenance Procedures and Service Limitations for Valves, 18 February 1977.
[11] Lycoming Service Bulletin No. 388 C, Procedure to Determine Exhaust Valve and Guide Condition, 22 November 2004.
[12] DURABILITY ISSUES - LYCOMING O-320, O-360 AND O-540 ENGINES FITTED TO ROBINSON HELICOPTER CO R22 AND R44 MODELS An independent industry-supported investigation, NR Blyth, Australian Helicopter Industry Association, 21 October 2019.
[13] Robinson Helicopter Company R44 I/R44 Cadet Safety Alert, 14 of October 2020
[14] Robinson R44 helicopters are fitted with Lycoming six-cylinder engines
[15] Lycoming Service Instruction No. 1577, Intake Valve In-Service Data, O-540-F1B5 engines with serial number ending with “-40E” installed in Robinson R44 Raven I and R44 Cadet helicopters, 10 November 2020.
[16] Lycoming Service Instruction No. 1280 D, Rotator Type Intake Valves, 20 July 2021.
[17] CASA Airworthiness Bulletin 85-025 Issue 5 Robinson R22/R44 Engine Intake Valve and Valve Seat Distress, 12 August 2021.
[18] Civil Aviation Safety Authority Defect Reporting Portal, United States Federal Aviation Administration Service Difficulty Reporting
[19] Civil Aviation Safety Authority, defect report number 611649334, dated 21 November 2016