Safety summary
What happened
On the night of 19 August 2021, the pilot of a Hawker Beechcraft King Air B200C aircraft, registered VH‑VAH and operated by Pel-Air, commenced the take-off from Essendon Fields Airport, Victoria on a medical retrieval flight to Albury, New South Wales. During the take-off, there was a reduction in power on the left engine and an uncommanded left yaw. The pilot initially managed the situation as an engine power loss and focused on maintaining directional control. However, when troubleshooting, the pilot identified that the left engine power lever had migrated rearwards to the idle position. In response, the pilot moved the power lever back to take‑off power and adjusted the friction lock to prevent further movement. The flight continued to Albury without further incident.
What the ATSB found
The ATSB found that the left engine power lever had migrated rearwards as the friction lock had not been sufficiently adjusted during the pre-flight checks. It was also established that power lever friction locks fitted to the Beechcraft King Air series aircraft required careful adjustment to prevent power lever migration, particularly during take-off. This was more prominent on the left engine, which was a characteristic generally known among King Air operators and pilots.
What has been done as a result
The operator provided additional training to all King Air pilots to demonstrate how the power lever system operated, when power lever migration could occur, and how to check that the friction locks were adequately adjusted to ensure the levers remain at take-off power. A component on friction locks was also included in the King Air pilot ground school training. In addition, the operator published a notice to air crew, which stipulated that all take-offs on sealed runways must be conducted using a standing start take-off. Further, the operator amended the take-off checklist for a standing start to include checking the friction locks to prevent a power lever migration during the take-off sequence.
The ATSB has released a safety advisory notice to all operators and pilots of King Air aircraft advising of power lever migration and the need to be aware of the careful adjustment required for the power lever friction lock.
Safety message
This incident highlights the importance of having a detailed understanding of the characteristics that may be specific to an aircraft type. In the case of the King Air series of aircraft, the design of the power lever system meant that the friction locks required careful adjustment to prevent power lever migration particularly during take-off.
Decisions regarding whether to conduct an investigation, and the scope of an investigation, are based on many factors, including the level of safety benefit likely to be obtained from an investigation. For this occurrence, a limited-scope investigation was conducted in order to produce a short investigation report and allow for greater industry awareness of findings that affect safety and potential learning opportunities. |
The occurrence
On 19 August 2021, a Hawker[1] Beechcraft B200C King Air aircraft, registered VH-VAH and operated by Pel‑Air, was scheduled to depart Essendon Fields Airport, Victoria on a medical retrieval flight to Albury, New South Wales. On board was a pilot, paramedic, and doctor.
At about 2300 Eastern Standard Time,[2] the pilot began to prepare the aircraft for departure as per the before engine starting checklist. One of the requirements was to set the power lever friction locks. The pilot recalled moving the power levers to the mid-range position to gauge their movement and adjusted the friction locks to establish adequate friction. They also recalled that their usual practice was to check the friction locks were correctly set before take-off.
Soon after, the aircraft was taxied to the runway and the pilot commenced a rolling take-off with their left hand on the control column and right hand on the power levers. When at about 94 kt, the pilot moved their right hand onto the control column and rotated the aircraft. When about 50 ft above ground level, the aircraft suddenly yawed left. Automatic dependent surveillance-broadcast data showed the aircraft tracking immediately left from the runway. The paramedic also recalled being pushed to the right and the aircraft not being aligned with the runway. The pilot looked at the engine instruments and observed that the left engine was showing a power loss, but the right engine appeared to be producing take-off power. Based on these indications, the pilot managed the situation as an engine power loss.
The pilot recalled focusing on maintaining directional control by applying right aileron and rudder. They then assessed the reason for the power loss and whether the propeller was feathered,[3] which they believed it was not. The pilot scanned the cockpit again and observed that the left power lever had migrated rearwards towards the idle position. While moving the left power lever back in-line with the right power lever, the aircraft yawed right as the pilot was still applying right rudder. The power increased on the left engine, the pilot reduced application of right rudder and retracted the landing gear. Immediately after, the left power lever started moving rearwards again. The pilot re‑tightened the friction lock on the left power lever, which resolved the issue. At that time, the aircraft was climbing through 200-300 ft. The paramedic reported that the pilot said the power lever had migrated as the friction lock had not been correctly set.
The flight continued to Albury without further incident. The pilot noted the power lever migration on the aircraft’s maintenance log as that they believed the friction lock was not adequately functioning. The subsequent engineering inspection did not find any technical issues with the power lever assemblies and friction locks.
Context
Pilot information
The pilot held a valid Air Transport Pilot Licence (Aeroplane), multi-engine command instrument rating, and a type rating for the B200C obtained in July 2021. At the time of the incident, the pilot had accrued about 16,000 hours of total aeronautical experience, of which 42 hours were in the B200C.
Engine controls
The aircraft’s engines were controlled using 3 sets of levers located on the centre pedestal.
- The 2 power levers controlled engine power from the idle position through to take-off power. When the levers were lifted and pulled aft over a gate, they controlled engine power for taxi operations, and over another gate for propeller reverse thrust to slow the aircraft after landing.
- The 2 propeller levers controlled propeller speed (rpm). The propellers could be feathered by moving the relevant lever past detents and back to the aft most position.
- Condition levers were used to select high or low idle, and to shut the engines down.
Friction locks
Four friction locks were located on the engine control pedestal. One each for the left and right power levers, one for the propeller levers, and one for the condition levers (Figure 1). The friction lock assemblies consisted of an adjustment mechanism, a phenolic drum, and a friction band. When the friction lock was rotated clockwise, the band around the phenolic drum tightened, which increased the friction between the 2 parts. The respective lever would become progressively resistant to movement, preventing the lever from moving out of position. When rotated counter‑clockwise, the lever moved freely. The design of the friction lock had been used since the 1965 model 88 Queen Air through to current production King Air aircraft.
Figure 1: Engine control levers and friction locks

Source: Pel-Air and Textron Aviation, annotated by the ATSB
A characteristic of the King Air friction locks was that they required careful setting as some aircraft had a narrow range between no friction and too much friction. The operator reported that there was no consistency in setting friction locks for a desired resistance between power levers in the same aircraft and other aircraft, and this changed over time due to wear. Worn friction locks were required to be replaced.
The maintenance log for the aircraft indicated that the left and right power lever assemblies, including both friction locks, were replaced in November 2020 after being observed to be worn, resulting in a reduced range of adjustment. Before the assemblies were replaced, pilots had reported to engineering staff that the friction locks were difficult to adjust.
The operator’s Flight Crew Operating Manual for the B200C aircraft included the following checklists where the friction locks were to be checked by the pilot prior to take-off:
- Internal daily inspection: This checklist was completed prior to the first flight of the day[4] and included checking the power levers friction lock settings in the idle position.
- Before engine starting: After the first flight of the day, the internal daily inspection was replaced by the ‘before engine starting’ checklist, which included a scan procedure beginning at the left side of the cockpit. This checklist required the power levers to be at idle and the friction lock setting checked. Further detail on how to adjust the friction locks was also included:
Place the power lever to the approximate position for take-off power and let go. If they roll back, set them again but tighten the friction.
The power levers have a spring retention configuration that increases resistance the more the levers are advanced. The result of this is the roll back of power levers if the friction lock is set too loose.
- Before take-off: In the before take-off checklist, the pilot would check the friction locks were set. After this, there was no further requirements to check the locks.
These checklists were consistent with the manufacturer’s Pilot Operating Handbook. The ATSB noted that the handbook did not contain further detail on how to adjust the friction lock and the potential for power lever migration.
The operator advised the ATSB that in 2019, there were a number of reported rejected take-offs with serviceable aircraft with no faults found, which were assessed to be related to friction locks not being set correctly prior to take-off. As a result, the operator published an operations note to pilots about friction locks in the before take-off check for the King Air aircraft, with details about their proper adjustment. It was unknown if the incident pilot, who had commenced with the operator in 2021, was aware of this notice.
Power lever migration
Power lever migration on the King Air referred to an uncommanded spring back or migration of the lever towards the idle position. This was typically experienced when the pilot removed their hand from the levers during take-off. If unnoticed, this could result in the aircraft yawing towards the engine experiencing the power lever migration, a significant loss of propeller torque on that engine, and the auto-feather system disarming.[5]
This migration occurred when the friction locks were not appropriately set, and could affect King Air 90, 200 and 300 series aircraft. The propeller and condition levers were not susceptible to migration.
The cockpit to engine nacelle power lever control cables were connected to a cam assembly on the right side of each engine via a lever. This lever was spring loaded towards idle to prevent an uncommanded acceleration in the event of a power lever cable malfunction that could damage the engine when torque and temperature limits were exceeded. The springs also reduced the effect of hysteresis[6] when power was reduced, which could cause the rate one engine’s power reduced relative to the other to be different. An additional spring could be fitted during production or maintenance to further balance the rate of power reduction between both engines. This additional spring was not fitted to the incident aircraft. The effect of the springs migrating the power levers toward idle during normal operations was overcome by setting the friction locks.
In addition, as the power lever cables were connected to the right side of each engine, the cable for the left engine was shorter than the right, and therefore less affected by hysteresis. Due to this, if the friction locks were not correctly set, the left power lever could migrate further aft than the right, resulting in an uncommanded left yaw. The operator demonstrated this on the ground without the engines running. With both power lever friction locks loosened and the levers full forward, when they were released the left engine power lever migrated further aft than the right (Figure 2).
Figure 2: Power lever migration demonstration
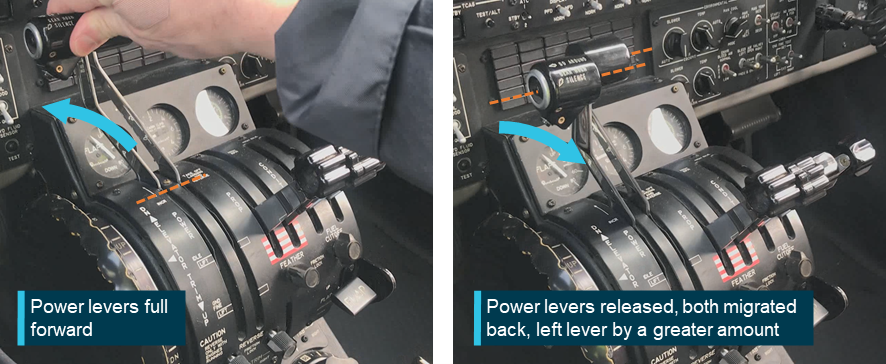
Source: Pel-Air, annotated by the ATSB
Prior to the incident, the operator’s training for pilots converting to the B200C was limited to the operation of the friction locks. At interview, the pilot reported that they were new to the B200C aircraft type and unaware that power lever migration could occur during take‑off. Another pilot from the operator noted that, until a pilot experienced a power lever migration, then it could be difficult to know how much to tighten the friction locks.
In addition, the King Air magazine included articles that emphasised the importance of adjusting the friction locks adequately to avoid power lever migration. The articles also described techniques to check that the friction locks were set sufficiently to prevent migration.
Similar occurrences
A review of the ATSB database did not find any reported occurrences involving power lever migration on the King Air series aircraft relating to the adjustment of the friction locks, but the manufacturer stated that they had received such reports. Likewise, the operator’s pilots interviewed recalled they had experienced or heard of others having a similar event. The operator’s senior base engineer also indicated that power lever migration was a known issue.
A review of the operator’s safety management system database found 10 reports from the previous 5 years, 6 of which involved VH-VAH. For example, on 18 August 2021 (the day prior to the incident), VH-VAH was being operated on a patient transfer flight. During take-off, the aircraft lost partial engine power and yawed left. This occurred due to the left power lever migrating aft when the pilot under check moved their hand to the control column to rotate the aircraft. Both the check captain and the pilot under check immediately identified the reason for the loss of power. The check captain moved the power lever forward to full power while the pilot under check applied right rudder to maintain control, retracted the landing gear, and adjusted the friction lock when the aircraft was at safe height. The flight continued without further incident.
In addition, the operator advised the ATSB of another power lever migration occurrence involving a B200 aircraft after the occurrence that was the subject of this investigation. On 31 September 2022, the aircraft was being operated on a patient retrieval flight. During the take-off roll, the pilot detected a migration of the left power lever, resulting in an uncommanded yaw left. This occurred at about the time when the pilot removed their hand from the control column. The pilot rejected the take-off and the aircraft subsequently impacted the runway edge lights. Engineers replaced the throttle quadrant and the throttle friction assembly. Based on this event, the operator is conducting a review of their take-off procedure including simulator testing and research.
The ATSB also contacted another B200 operator who recorded 4 reports of power lever migration over the previous 5 years.
A review of the United States Aviation Safety Reporting System database found 3 reported power lever migration occurrences due to friction lock adjustment since 1988. In addition, there have been 2 notable international investigations where this was identified as a potential factor that contributed to the accident involving a King Air (detailed below).
UK Air Accidents Investigation Branch investigation (7/2003)
On 23 December 2000, a Beechcraft B200 aircraft departed Blackbushe, United Kingdom to Palma, Spain on a private flight. Shortly after take‑off, the aircraft was observed to bank left before colliding into a factory complex 13 seconds later, resulting in a fire. All on board were fatally injured.
An examination of the aircraft did not identify any technical issues that would have contributed to the accident. However, analysis of the cockpit voice recorder showed a reduction in one of the propeller’s rpm as the aircraft rotated, which would have led to thrust asymmetry. The investigation concluded that, it was probable a migration of a power lever due to insufficient friction being set had occurred. It was also noted that the friction control had been slackened during recent maintenance and it was possible that it was not adjusted adequately by the pilot when doing their checks prior to take-off. As a result of the investigation, a safety recommendation was made to Raytheon Aircraft Company:
The Raytheon Aircraft Company should ensure that reference to the correct adjustment of power lever friction is suitably emphasised in the Beech 200 Aircraft Operating Manual (AOM) and the consequences of insufficient adjustment are not only highlighted in the AOM but also included in the recommended Beech 200 type training syllabus.
The ATSB was unable to find any follow-up action on this recommendation recorded in the investigation site.
US National Transportation Safety Board investigation (CEN19MA190)
On 30 June 2019, a Beechcraft King Air 300 departed Addison, Texas, United States, on a private flight. During take-off, the aircraft was observed to roll left before reaching a maximum altitude of 100 ft above ground level. It then descended and collided with a hangar in an inverted attitude about 17 seconds after take-off. All on board were fatally injured.
Analysis of the cockpit voice recorder showed that 7 seconds after take-off, the propeller speeds diverged, with the left propeller speed decreased to 1,688 rpm and the right propeller speed decreased to 1,707 rpm. An engineering examination did not identify any technical issues with the aircraft, but other evidence suggested a loss of thrust in the left engine was most likely experienced shortly after take-off.
While the reason for the reduction in thrust could not be conclusively determined, the investigation considered inadequate friction setting the most likely cause. It was noted that other circumstances, such as a malfunction within the power control system could have also resulted in a loss of engine thrust. However, the extent of damage to the power control system precluded determining the position of the power levers at the time of the loss of thrust or the friction setting during the flight.
Safety analysis
Uncommanded left yaw
Just after take-off at night, the pilot reported that the aircraft suddenly yawed left. This was consistent with the recorded flight path and the paramedic’s observations. When the yaw occurred, the pilot’s immediate response was to manage the situation as a left engine failure by applying right rudder and aileron to maintain directional control. The pilot then noticed the left power lever had migrated to the idle position and responded by pushing the power lever forward. After resetting the power lever friction lock, the flight continued without incident.
Insufficient friction applied
The friction locks were adjusted by the pilot to a level they believed to be sufficient prior to take-off. However, as the post-flight engineering inspection did not find any technical issues with the power lever and friction lock assemblies, and the left power lever had migrated twice during the take-off sequence, it was likely that the friction lock had not been sufficiently set during pre-flight checks. This was consistent with the paramedic’s recollection of the pilot indicating that the friction lock had to be re-set.
King Air friction lock characteristics
Due to the spring loading of the power levers on the King Air series aircraft, there was a tendency for the levers to migrate towards the idle position, particularly during take-off, if the friction locks were not appropriately set. This was more prevalent on the left power lever due to the shorter length of its cable. There was also an awareness of the possibility of a narrow range of adjustment, inconsistency in friction lock settings between the left and right engines, and from aircraft to aircraft, which could change due to wear.
While the incident pilot was not aware of the possibility of power lever migration, the need to carefully adjust the friction locks to prevent migration was more broadly known by B200C pilots and operators. This characteristic had been experienced among different operators and pilots as demonstrated in the reported occurrences and had also been considered as a potential factor in two fatal accidents.
Findings
ATSB investigation report findings focus on safety factors (that is, events and conditions that increase risk). Safety factors include ‘contributing factors’ and ‘other factors that increased risk’ (that is, factors that did not meet the definition of a contributing factor for this occurrence but were still considered important to include in the report for the purpose of increasing awareness and enhancing safety). In addition ‘other findings’ may be included to provide important information about topics other than safety factors. These findings should not be read as apportioning blame or liability to any particular organisation or individual. |
From the evidence available, the following findings are made with respect to the uncommanded power reduction involving Hawker Beechcraft King Air B200C, VH-VAH, Essendon Fields Airport, Victoria, on 19 August 2021.
Contributing factors
- During a night take-off from Essendon Fields Airport, the left-engine power lever migrated to idle, which resulted in an uncommanded left yaw.
- During the pre-flight checks, it was likely that the pilot applied insufficient friction to prevent the left power lever migrating.
- The power lever friction locks fitted to the Beechcraft King Air series aircraft required careful adjustment to prevent power lever migration during take-off, particularly on the left engine. This characteristic was broadly known among operators and pilots.
Safety actions
Whether or not the ATSB identifies safety issues in the course of an investigation, relevant organisations may proactively initiate safety action in order to reduce their safety risk. All of the directly involved parties are invited to provide submissions to this draft report. As part of that process, each organisation is asked to communicate what safety actions, if any, they have carried out to reduce the risk associated with this type of occurrences in the future. The ATSB has so far been advised of the following proactive safety action in response to this occurrence. |
Safety action by the Pel-Air
As a result of the incident, Pel-Air undertook the following safety actions.
Training
The engineering department and flight operations manager provided additional training to all King Air pilots demonstrating how the friction lock system worked, how power lever migration could occur, and how to check the friction locks were adequately adjusted. In addition, a course on power lever migration has now been included as part of the ground school pilot training for the King Air aircraft.
Revised take-off procedure
The day after the incident, the operator published a notice to air crew, which stipulated that all take-offs on sealed runways must be conducted using a standing start take-off. Further, the take‑off checklist for a standing start in the Flight Crew Operations Manual was amended to include a requirement for pilots to check that the friction locks were set to prevent power lever migration when take-off power had been set.
Safety advisory notice to King Air series aircraft operators
SAN number: | AO-2021-034-SAN-01 |
The Australian Transport Safety Bureau advises pilots and operators of the King Air series aircraft (90, 200, and 300) that the power lever friction locks require careful adjustment to prevent power lever migration towards the idle position, particularly during take-off. Inadvertent migration of one power lever towards idle can result in power reduction and yaw that, when occurring at low height, can result in catastrophic outcomes. Operators should ensure pre-flight checks provide opportunities to confirm friction lock settings before the take-off run, and ensure pilots have adequate knowledge of friction lock sensitivity to help prevent and recover from inadvertent power lever migration.
Sources and submissions
Sources of information
The sources of information during the investigation included:
- the pilot
- the paramedic
- Pel-Air
- Textron Aviation (type certificate holder)
- United States National Transportation Safety Board.
Submissions
Under section 26 of the Transport Safety Investigation Act 2003, the ATSB may provide a draft report, on a confidential basis, to any person whom the ATSB considers appropriate. That section allows a person receiving a draft report to make submissions to the ATSB about the draft report.
A draft of this report was provided to the following directly involved parties:
- the pilot
- the paramedic
- Pel-Air
- Textron Aviation
- United States National Transportation Safety Board.
A submission was received from Pel-Air. The submission was reviewed and, where considered appropriate, the text of the report was amended accordingly.
Purpose of safety investigationsThe objective of a safety investigation is to enhance transport safety. This is done through:
It is not a function of the ATSB to apportion blame or provide a means for determining liability. At the same time, an investigation report must include factual material of sufficient weight to support the analysis and findings. At all times the ATSB endeavours to balance the use of material that could imply adverse comment with the need to properly explain what happened, and why, in a fair and unbiased manner. The ATSB does not investigate for the purpose of taking administrative, regulatory or criminal action. TerminologyAn explanation of terminology used in ATSB investigation reports is available here. This includes terms such as occurrence, contributing factor, other factor that increased risk, and safety issue. Publishing informationReleased in accordance with section 25 of the Transport Safety Investigation Act 2003 Published by: Australian Transport Safety Bureau © Commonwealth of Australia 2022 Ownership of intellectual property rights in this publication Unless otherwise noted, copyright (and any other intellectual property rights, if any) in this report publication is owned by the Commonwealth of Australia. Creative Commons licence With the exception of the Coat of Arms, ATSB logo, and photos and graphics in which a third party holds copyright, this publication is licensed under a Creative Commons Attribution 3.0 Australia licence. Creative Commons Attribution 3.0 Australia Licence is a standard form licence agreement that allows you to copy, distribute, transmit and adapt this publication provided that you attribute the work. The ATSB’s preference is that you attribute this publication (and any material sourced from it) using the following wording: Source: Australian Transport Safety Bureau Copyright in material obtained from other agencies, private individuals or organisations, belongs to those agencies, individuals or organisations. Where you wish to use their material, you will need to contact them directly. |
[1] At the time of VH-VAH’s manufacture in 2010, the type certificate holder for the Beechcraft King Air series was Raytheon Aircraft Company, operating under the Hawker Beechcraft brand name. Textron Aviation has been the type certificate holder for the Beechcraft King Air series since 2014.
[2] Eastern Standard Time (EST): Coordinated Universal Time (UTC) + 10 hours.
[3] Feathering reduces drag following an in-flight engine failure or shutdown by increasing the angle of the propeller blades until they are parallel with the aircraft’s line of flight.
[4] The incident flight was the tenth flight of the day.
[5] The auto-feather system automatically feathered the propellers in the event of an engine failure. If the power lever moved back past the 90% engine speed position, the auto-feather system would disarm.
[6] In this context, hysteresis is the lost motion (or backlash) in the cables used in the power control system. For a given input by the pilot, the cable’s movement may be impeded mechanically by friction and/or non-linear movement of the cable within its housing.