Executive summary
What happened
On 3 February 2021, a Robinson Helicopter Company R44 Clipper II helicopter, registered VH‑SXC, was operated by GSL Group Pty Ltd on a passenger charter flight from Proserpine Airport to Whitehaven Beach, Queensland. On board were the pilot and 2 passengers.
While cruising at 1,500 ft between Long Island and Hamilton Island, the pilot smelled burning rubber and saw the clutch warning light flicker briefly. The pilot then heard a bang from behind the cabin, and the clutch warning light illuminated and remained on. The pilot turned the helicopter back toward Long Island, declared an emergency to Hamilton Island air traffic control, and made a successful emergency landing on the beach on the western side of Long Island. The pilot and passengers were uninjured. There was minimal damage to the helicopter.
What the ATSB found
Of the 4 drive belts in the helicopter’s drive system, it was found that the forward 2 drive belts had dislodged and moved forward of the upper sheave. They then lodged against the sheave and clutch shaft, leading to damage to the drive belts and surrounding components.
The other 2 drive belts remained intact and shifted forward from their original sheave positions and were not effectively engaged within the grooves of the sheaves. Consequently, there was a complete loss of effective drive of the rotor system.
In consultation with the Robinson Helicopter Company (RHC), it was found that the previous procedure of extending the clutch actuator to stretch a new drive belt set, was no longer advised. This procedure, which had been carried out on VH-SXC, was performed with the engine stopped and the actuator extended, to hold the drive belts under tension for an unspecified time. RHC identified that if performed regularly, this may lead to overstretching and looseness in the drive belts during start-up. This in turn can result in the drive belts dropping below the lower sheave grooves and misaligning during start-up belt tensioning.
What has been done as a result
RHC has amended the Pilot’s Operating Handbook Safety Notice SN-33 ‘Drive Belt Slack’. This safety notice covers the pre-flight inspection requirements of the drive belts and the rotor turning time after clutch engagement.
RHC recognised that the practice of stretching the drive belts with the clutch actuator engaged was contributing to excessive slack in drive belts at start-up. The procedure of stretching new drive belts by extending the clutch actuator and leaving it engaged with the engine off, has been removed.
The helicopter maintenance organisation has raised awareness with their engineers and advised their customers and operators of the removal of the RHC drive belt stretching procedure. They have also reiterated the requirement for the main rotor blades to be turning within 5 seconds of clutch engagement, and to seek maintenance support if not within these limits.
Safety message
Following the helicopter manufacturer’s latest advice, operators should not stretch new drive belt sets using the clutch actuator. This will avoid overstretching and reduce instances of excessive slackness of the drive belts at start-up and the risk of misalignment.
The outcome highlights the importance of managing an in-flight emergency efficiently by following flight manual emergency procedures and having a pre-planned course of action. These fundamentals enabled the pilot to make a safe landing with no injuries or loss of the helicopter.
The investigation
Decisions regarding whether to conduct an investigation, and the scope of an investigation, are based on many factors, including the level of safety benefit likely to be obtained from an investigation. For this occurrence, a limited-scope investigation was conducted in order to produce a short investigation report, and allow for greater industry awareness of findings that affect safety and potential learning opportunities. |
The occurrence
On 3 February 2021 at about 1240 local time, a Robinson Helicopter Company (RHC) R44 Clipper II helicopter, registered VH‑SXC and operated by GSL Group Pty Ltd, departed Proserpine Airport, Queensland. On board were a pilot and 2 passengers. The passenger charter flight was to visit Whitehaven Beach located on the eastern side of Whitsunday Island (Figure 1). Weather conditions at the time were fine, with clear skies and a 10-15 kt wind from the south-east.
The helicopter departed Proserpine Airport and tracked east over Conway Beach, toward the southern end of Long Island. The flight was to continue to the north of Hamilton Island and then traverse the southern side of Whitsunday Island.
Figure 1: Area of operation
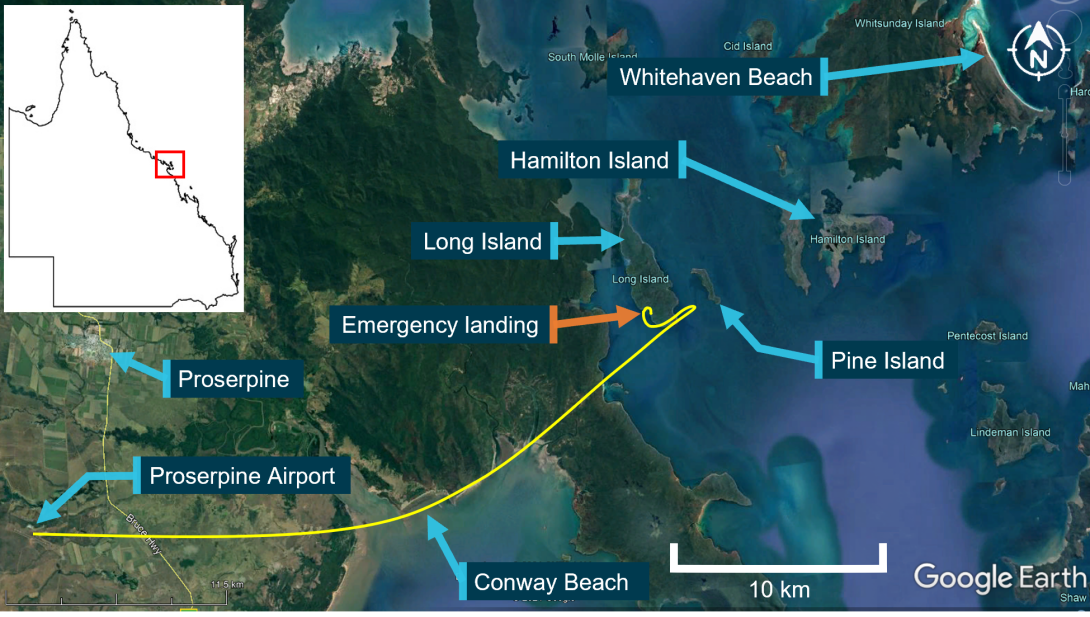
Source: Google Earth, annotated by the ATSB
At about 1255 (15 minutes after departure) while approaching Pine Island at an altitude of 1,500 ft, the pilot identified the smell of burning rubber and observed the clutch actuator light momentarily flicker[1]. The pilot then reported hearing what sounded like ‘a rubber band smacking against the cowling’ from the rear of the cabin and saw the clutch light illuminate and remain on. The pilot also identified a rise in engine RPM, which was controlled by manipulating the throttle, and a slow reduction in main rotor RPM.
In response, the pilot lowered the collective[2] to maintain adequate main rotor speed and turned back toward a resort on the south-west side of Long Island. The pilot also made an emergency radio call to Hamilton Island air traffic control (ATC) detailing the developing situation. Approaching a beach near the resort, the pilot armed the emergency float system in preparation for a potential water landing. In response to the warning light, the pilot pulled the clutch circuit breaker as required by the R44 Pilot’s Operating Handbook (POH) (See the section titled Clutch caution light). The pilot noted the alternator light had also illuminated during the incident.
After conducting an emergency autorotation and landing on the beach, the pilot shut down the helicopter and evacuated the passengers to the front of the helicopter. The pilot advised ATC of the safe landing, and then moved both passengers away to the nearby resort facilities. During the operator’s subsequent inspection of the helicopter, the drive system was found to be damaged.
Photographs taken onsite following the event, showed the forward 2 drive belts had dislodged and shifted out of position from the upper and lower sheaves during operation (Figure 2). There was substantial damage to those drive belts. The images also showed a large amount of rubber dust in the area of the upper sheave, indicating the system had continued to operate while abrading the drive belts after they had dislodged.
The other 2 drive belts remained intact and on the upper and lower sheaves but had shifted forward from their original positions. As that occurred, it led to a loss of effective drive to the rotor system, resulting in the observed rise in engine RPM and a reduction in main rotor RPM.
Several other components were also damaged, these included the:
- alternator belt, which was dislodged by the drive belts
- oil cooler and oil supply line
- lower sheave
- fan shaft and bearing
- clutch actuator.
Figure 2: Drive system of VH-SXC showing the rear two drive belts remaining on the upper and lower sheaves
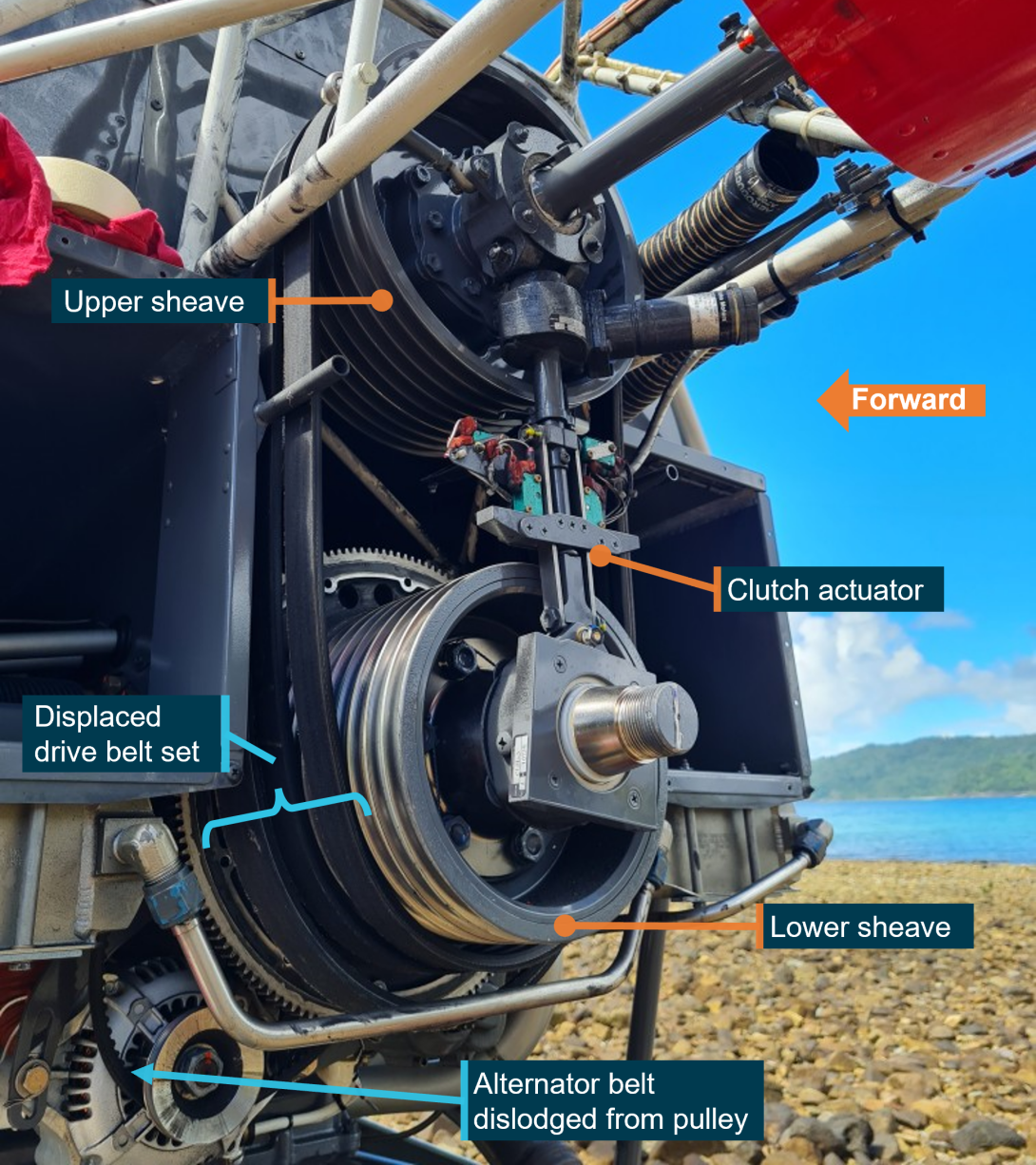
Source: Operator photo, annotated by the ATSB
Context
Pilot information
The pilot held a valid commercial pilot licence for both helicopters and aeroplanes, and a current Class 1 aviation medical certificate. They were endorsed on several single and twin-engine, piston and turbine helicopters, including the Robinson R44 (R44).
At the time of the incident, they had about 3,600 flight hours experience, of which about 1,100 hours were in the R44. They completed their last flight review in December 2020, which included emergency autorotation procedures.
Helicopter information
The R44 is a 4-place helicopter that is primarily all metal construction with a 2-blade main and tail rotor system and powered by a 6-cylinder Lycoming piston engine. The Clipper II version of the R44 is fitted with an emergency pop-out float system.
VH-SXC was manufactured in the United States in 2019 and issued serial number 14285. It was initially imported to New Zealand in 2019, before being imported and registered in Australia, in the same year. The maintenance release indicated that VH-SXC had accumulated a total of 461.8 hours in service at the time of the occurrence.
Rotor drive system
The rotor drive on the Robinson R44 helicopter uses 4 reinforced rubber drive belts that engage with upper and lower multi-grooved sheaves. The lower sheave is mounted to the engine crankshaft and the upper sheave is mounted on a free-wheel clutch shaft that drives the main and tail rotor driveshafts.
When engaged, the clutch actuator extends and moves the upper sheave upwards a small amount, which applies tension to the drive belts, transmitting engine power to the rotors (Figure 3). When the drive belts are properly tensioned, the clutch actuator senses the compressive load (drive belt tension), and the clutch actuator switches off.
Figure 3: Robinson R44 rotor drive system
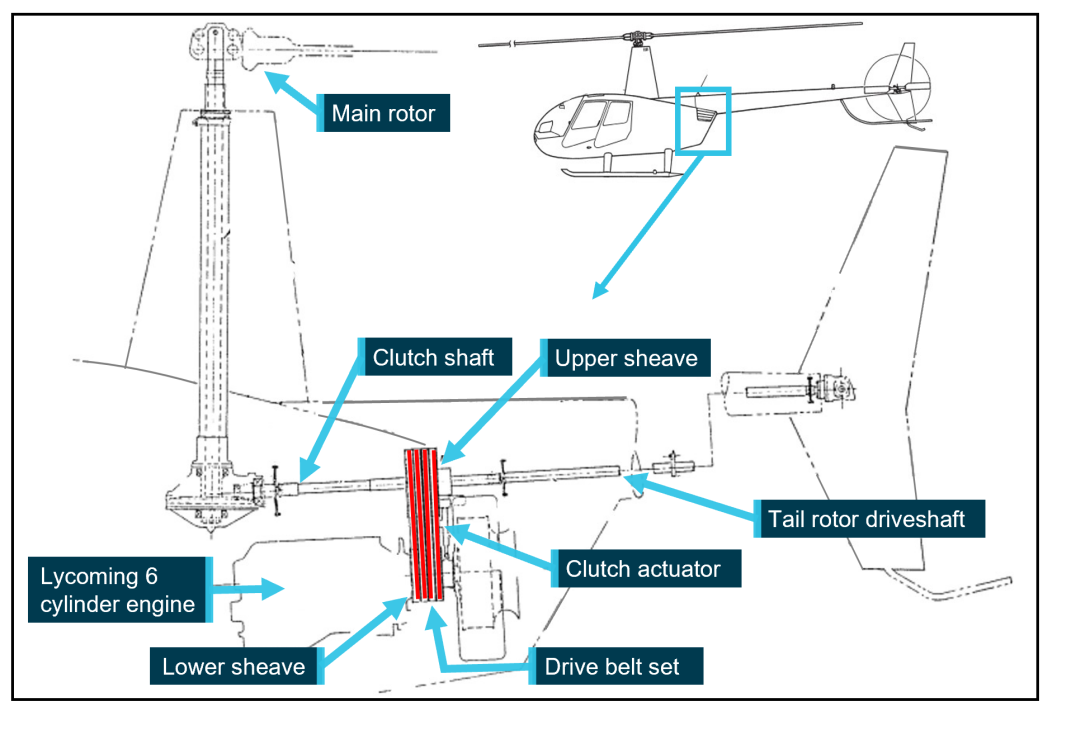
Source: Robinson Helicopter Company, annotated by the ATSB
During engine start, the drive belts are not under tension to reduce the load on the starter motor that would otherwise attempt to turn both the engine and the entire rotor system. After start, the pilot selects the clutch actuator to ENGAGE, tensioning the drive belts within the sheave grooves. The POH stated, that after engaging the clutch actuator switch, the rotors should be turning within 5 seconds. Also, Safety Notice SN-33, Drive Belt Slack states that if:
…rotor does not turn within 5 seconds, shut down and have actuator adjusted prior to flight.
The actuator may operate momentarily during flight as the drive belts warm up or stretch slightly. A caution light illuminates on the instrument panel to indicate any movement of the actuator and a momentary flicker during operation is considered normal.
Clutch caution light
The POH provided advice for the pilot with how to respond to a clutch caution light illumination which has occurred for greater than 10 seconds (clutch motor engaging or disengaging). The response requires the clutch circuit breaker to be pulled, therefore isolating power to the clutch motor. The advice notes:
Clutch light may come on momentarily during run-up or during flight to re-tension belts as they warm-up and stretch slightly. If, however, the light flickers or comes on in flight and does not go out within 10 seconds, pull CLUTCH circuit breaker and land as soon as practical. Reduce power and land immediately if there are other indications of drive system failure (be prepared to enter autorotation). Have drive system inspected for a possible malfunction.
VH-SXC operational and maintenance history
VH-SXC was previously utilised for flight training and, in April 2020 was involved in a dynamic rollover[3] accident which led to substantial damage of the helicopter[4]. The rebuild of the helicopter was consistent with the completion of the R44 2,200-hour overhaul[5] requirements and the 4,400‑hour component replacement schedules. The rebuild included the fitting of new drive belts, clutch shaft and actuator, tail cone and all drivetrain components.
Additionally, during the rebuild, repairs were carried out on the left and right lower frames in accordance with an approved engineering order[6]. Post-assembly alignment checks were performed on the airframe, engine, and drivetrain assemblies. These included adjustments of the sheaves, to ensure proper alignment of the drive belts from the engine lower sheave to the upper sheave. Post-rebuild rigging checks ensured there was no misalignment - a known contributor to drive belts disengaging during operation.
Since the rebuild, but prior to this occurrence, engineers had replaced the drive belts due to overstretching and looseness. Maintenance records showed that the sheave alignment was checked at that service. The drive belts fitted at that time are the subject of this report and failed after only 6.2 hours of flight. Table 1 details the history of drive belt replacement on VH-SXC.
While installing new drive belts following this occurrence, the sheave alignment was again checked, and maintenance records showed that the sheave alignment was stable, changing only 1 thousandth of an inch between drive belt sets. That replacement set of belts were themselves subsequently replaced on 15 February 2021, after only 8.6 flight hours due to overstretching.
Table 1: VH-SXC drive belt maintenance history
Date | Maintenance | Time in service | Notes |
23 Apr. 2020 | 379.5 | Dynamic rollover during hover taxi and collision with terrain. Helicopter was substantially damaged. | |
23 Nov. 2020 | Helicopter rebuild carried out | 379.5 | New drive components fitted include new drive belt set, clutch shaft, and upper and lower sheaves. Sheave alignment carried out. |
29 Jan. 2021 | 100-hour inspection carried out | 455.6 | Overstretched drive belt set replaced with a new drive belt set. Sheave alignment carried out. Drive belts flight time in service: 76.1 hours. |
3 Feb. 2021 | Incident flight | 461.8 | Drive belts disengaged from sheaves in flight leading to emergency landing. New drive belt set, lower sheave, clutch actuator, and alternator belt fitted. Sheave alignment carried out. Drive belts flight time in service: 6.2 hours. |
15 Feb. 2021 (post‑incident) | Drive belt set replaced | 470.4 | Stretched and disengaged drive belt set replaced with a new drive belt set. Sheave alignment carried out. Drive belts flight time in service: 8.6 hours. |
Source: VH-SXC maintenance logbook
Drive belt replacement and stretching
The maintenance manual task for the installation of a new drive belt set did not contain a procedure for drive belt stretching or checking drive belt tension. As the drive belts contain rubber, they warm and stretch during use. After shutting down, some drive belts shrink to a minimal slack condition as they cool. This can lead to increased drive belt tension and place additional load on the drive train during start-up.
To remedy this, the POH contained a procedure in Safety Notice SN‑33 (Appendix A) which specified a drive belt stretching procedure using the clutch actuator. The actuator would be engaged, with the engine stopped, and left in this condition for a period[7]. The clutch would then be disengaged during the next pre-flight. Robinson’s reason for this was to limit dimensional reductions that could occur as the drive belts cooled. Robinson further advised that this procedure was intended to be used as a one-off procedure, and then further adjustments to belt engagement time was to be done through adjustment of the clutch actuator down-limit switch. However, these details were not included in the safety notice.
The procedure for stretching the drive belts in service was listed only in the POH due to these characteristics of the drive belts. If the pilot determined that the drive belts were too tight, they could perform the stretching, without the need for maintenance personnel to be involved.
The maintenance organisation advised that the procedure for static stretching of the drive belt set as described in SN-33 was used for each set of new drive belts fitted to VH-SXC at the initial installation. Additional stretching of the drive belts was then performed by the operator, for a further 5 flight hours. This was conducted in accordance with SN-33, under the guidance from the maintenance organisation, with the clutch remaining engaged overnight.
Drive belt examination
The drive belt set was examined at the ATSB’s technical facilities in Canberra (Appendix B). The examination found that the 2 forward drive belts had dislodged, leading to substantial damage to the drive belts. The drive belts had also been damaged by the rotating drive system components, causing rubber to be abraded from the drive belts and a vee section of each drive belt to be torn free.
Both rear drive belts had remained on the upper and lower sheaves but had moved forward from their original locations and not engaged in the sheave grooves. The drive belt set was measured, and the rear drive belts had stretched about 40 mm greater in diameter when compared with the forward drive belts. This indicated that the rear drive belts had continued to operate after the forward drive belts had dislodged and were stretched by the extension of the clutch actuator.
Safety analysis
Repeated drive belt loss
Repairs to the helicopter had been performed according to applicable manufacturer’s instructions and engineering orders. The stability of the sheave alignment from rebuild, and between drive belt sets replacements, indicate that this was not the source of drive system failure.
The drive belt stretching procedure, which was current at the time and recommended by the manufacturer, was used on each set of drive belts, and for an additional 5 flight hours thereafter to remedy the tight drive belts. However, the procedure of engaging the clutch actuator as a means of stretching tight drive belt sets was later recognised by Robinson Helicopter Company as a contributing factor to excessive slack in the drive belts at start-up.
Robinson’s intent of the procedure in SN-33 was that the stretching of the drive belts was to be a once only application. However, this was not detailed in the safety notice and in-service feedback from operators showed it was being performed multiple times. It is likely that the multiple use of the stretching process contributed to the repositioning of the drive belts in operation.
Pilot response
In dealing with emergencies pilots follow a basic set of priorities: aviate, navigate, and communicate. Once the pilot of VH-SXC diagnosed a problem within the drive train, they reacted to the increasing engine speed and decreasing rotor speed by following the POH procedure and maintained control of the helicopter.
The pilot also followed the POH procedure for isolating power to the clutch by pulling the clutch circuit breaker following the steady illumination of the clutch warning light. On this occasion, had the circuit breaker for the clutch not been pulled, the remaining two rotor drive belts may have tensioned and restored drive to the rotor system. However, faced with the burning rubber smell, clutch light illumination and banging sound and no way to visually assess the drive belt condition, the pilot’s actions were prudent.
They then conducted an immediate return and navigated toward Long Island to a suitable landing location, before communicating their situation and intentions to Hamilton Island control tower.
Observing this fundamental approach and using the POH procedures allowed the pilot to have a clear decision-making process and procedure to achieve a safe outcome.
Findings
ATSB investigation report findings focus on safety factors (that is, events and conditions that increase risk). Safety factors include ‘contributing factors’ and ‘other factors that increased risk’ (that is, factors that did not meet the definition of a contributing factor for this occurrence but were still considered important to include in the report for the purpose of increasing awareness and enhancing safety). In addition ‘other findings’ may be included to provide important information about topics other than safety factors. These findings should not be read as apportioning blame or liability to any particular organisation or individual. |
From the evidence available, the following findings are made with respect to the drive system failure and forced landing, involving a Robinson Helicopter Company R44 II, VH-SXC 11 km west of Hamilton Island, Queensland on 3 February 2021.
Contributing factors
- The drive belt stretching procedure current at the time of the occurrence was used, and likely overstretched the drive belts, permitting the drive belt set to become misaligned upon tensioning of the system.
- The 2 forward drive belts displaced from the upper and lower sheaves and became entrapped against the rotating components, leading to abrading of the drive belts. The load on the remaining rear 2 drive belts led to them moving forward and disrupting the rotor system drive, necessitating a forced landing.
Other findings
- In responding to the situation, the pilot carried out an emergency landing on a nearby island resulting in minimal damage to the helicopter and no injuries to the pilot or passengers.
Safety actions
Whether or not the ATSB identifies safety issues in the course of an investigation, relevant organisations may proactively initiate safety action in order to reduce their safety risk. All of the directly involved parties are invited to provide submissions to this draft report. As part of that process, each organisation is asked to communicate what safety actions, if any, they have carried out to reduce the risk associated with this type of occurrences in the future. The ATSB has so far been advised of the following proactive safety action in response to this occurrence. |
Safety action by Robinson Helicopter Company
Robinson Helicopter Company (RHC) identified that the procedure utilising the clutch actuator to statically stretch the drive belts was a likely cause of excessive slack in the drive belts at start-up.
In July 2021, 5 months after this event, RHC proactively removed the drive belt stretching procedure from the safety notice contained in the pilot’s operating handbook, The amended page was published on the Robinson Helicopter Company website, and has likewise been updated for the R22.
Sources and submissions
Sources of information
The sources of information during the investigation included the:
- pilot of VH-SXC
- operator
- maintenance provider
- Robinson Helicopter Company
Submissions
Under section 26 of the Transport Safety Investigation Act 2003, the ATSB may provide a draft report, on a confidential basis, to any person whom the ATSB considers appropriate. That section allows a person receiving a draft report to make submissions to the ATSB about the draft report.
A draft of this report was provided to the following directly involved parties:
- the pilot of VH-SXC
- the operator
- the maintenance provider
- the Civil Aviation Safety Authority
- Robinson Helicopter Company.
Submissions on that draft report were received from the:
- operator
- maintenance provider
- Robinson Helicopter Company
- Civil Aviation Safety Authority.
The submissions were reviewed and, where considered appropriate, the text of the report was amended accordingly. Given the nature of the amendments, a second draft was provided to the following directly involved parties:
- the pilot of VH-SXC
- the operator
- the maintenance provider
- Robinson Helicopter Company.
Submissions on the second draft report were received from the:
- operator
- Robinson Helicopter Company
The submissions were reviewed and, where considered appropriate, the text of the report was amended accordingly.
References
Australian Transport Safety Bureau, 2013, Reliability of the Robinson R22 helicopter belt drive system, AI-2009-038, Canberra, ACT
Robinson Helicopter Company 2020, R44 Pilot’s Operating Handbook, section 4, p.4-3 and section 10, p.26 Safety Notice SN-33.
Robinson Helicopter Company 2020, R44 Pilot’s Operating Handbook, section 3, p.3.1 - 3.3.
Robinson Helicopter Company 2018, R44 Maintenance Manual, chapter 7, pp.7.27 - 7.30.
Appendices
Appendix A – Safety Notice SN-33
Figure 4: Robinson Safety Notice SN-33 current at the time of the incident
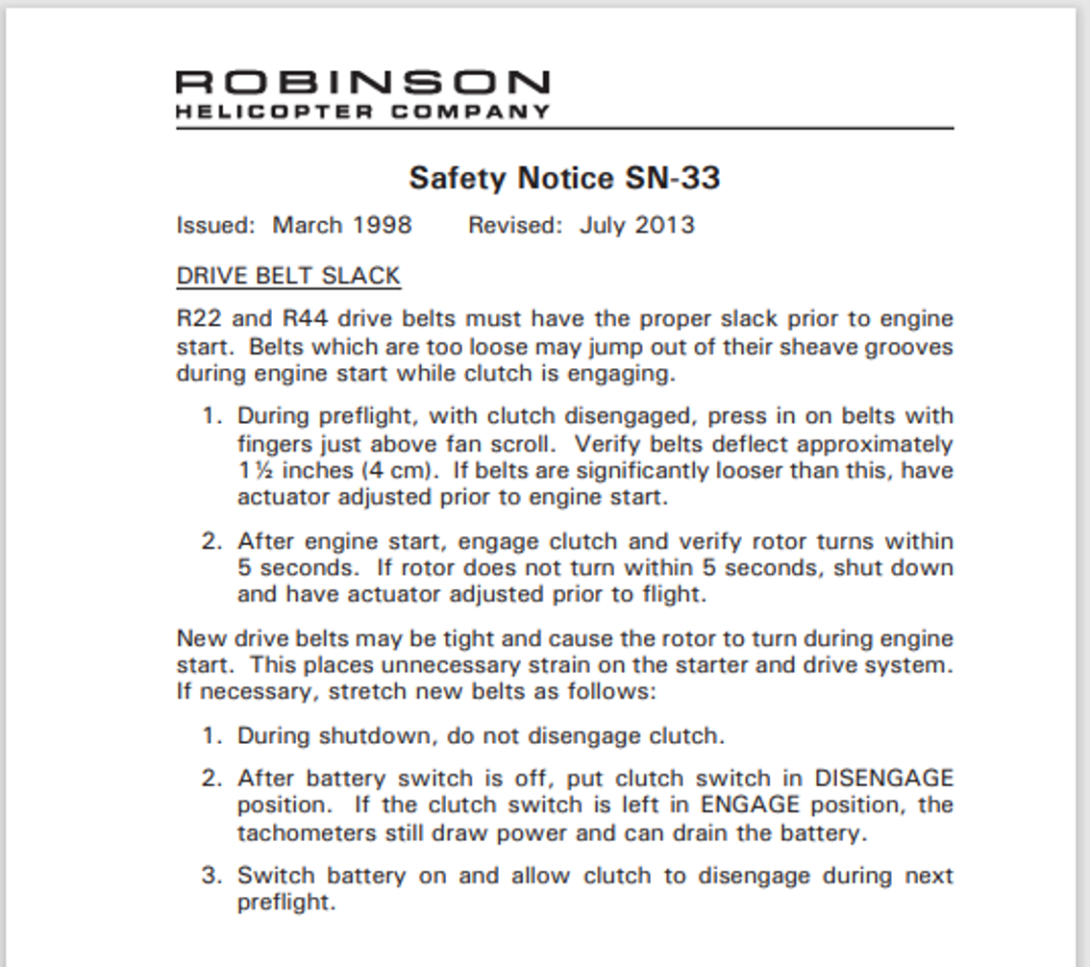
Source: Robinson Helicopter Company, annotated by the ATSB
Figure 5: Robinson Safety Notice SN-33 updated with stretching procedure removed

Source: Robinson Helicopter Company
Appendix B – Drive belt examination
The drive belt set from VH-SXC was sent to the ATSB’s technical facilities in Canberra for examination. For reference purposes, the drive belts were marked by the Robinson Helicopter Company (RHC) A through D. Belt A is the forward drive belt and belt D is at the rear of the drive belt set. The set is also marked by RHC with a painted arrow marking, which ensures that the drive belt set is installed in the same order each time they are removed.
The ATSB examination found that the drive belts contained 2 differing part numbers (PN). The forward drive belt was PN A190-3, while the rear 3 drive belts were identified as PN A190-2. All 4 drive belts were Revision (Rev) AB. Although the drive belts were marked with part numbers that applied to both the R44 and R22 helicopter type, the markings from manufacture indicated they were supplied as a matched set from the RHC factory (Figure 4).
Figure 6: Drive belt set removed from VH-SXC
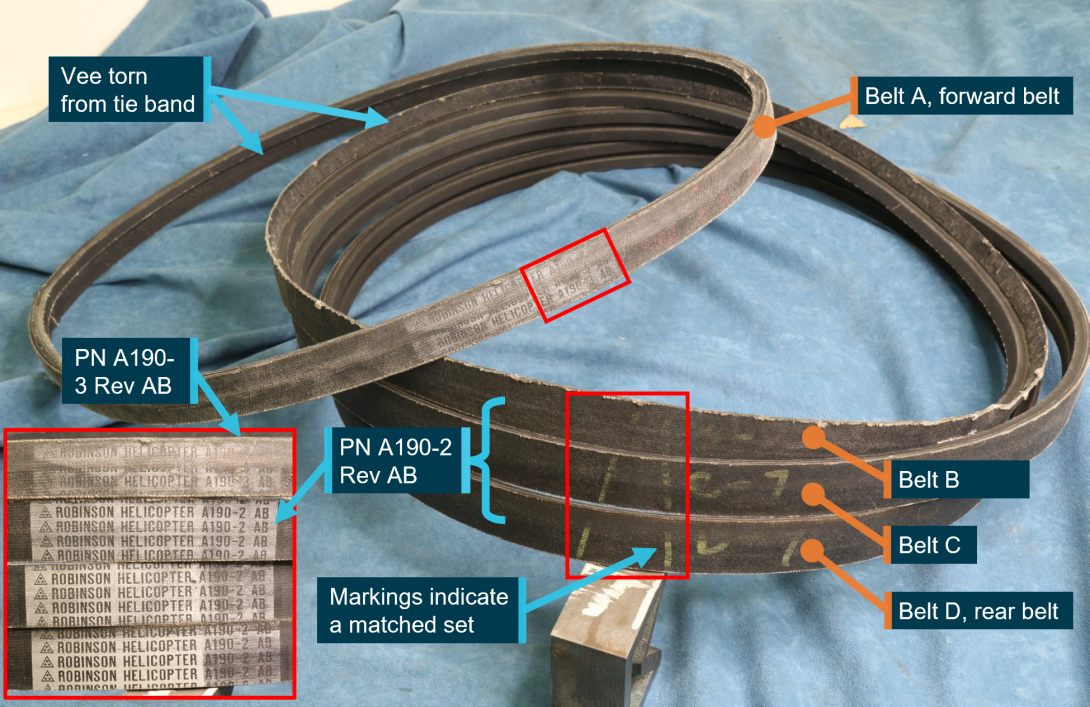
Source: ATSB
RHC reported that the A190-2 Rev AB drive belts possess the same dimensions and characteristics as the A190-3 Rev AB drive belt. When the R22 reverted to the Rev Z drive belt, a significant number of A190‑2 Rev AB drive belts were re-measured, matched as a set and re‑identified as A190-3 Rev AB and categorised as an R44 drive belt set. The drive belt set removed from VH-SXC had the additional markings of a part numbered set of A190-3 AB, consistent with the information supplied by the manufacturer, confirming the correct part was fitted to the helicopter (Figure 5).
Figure 7: Drive belt set part number
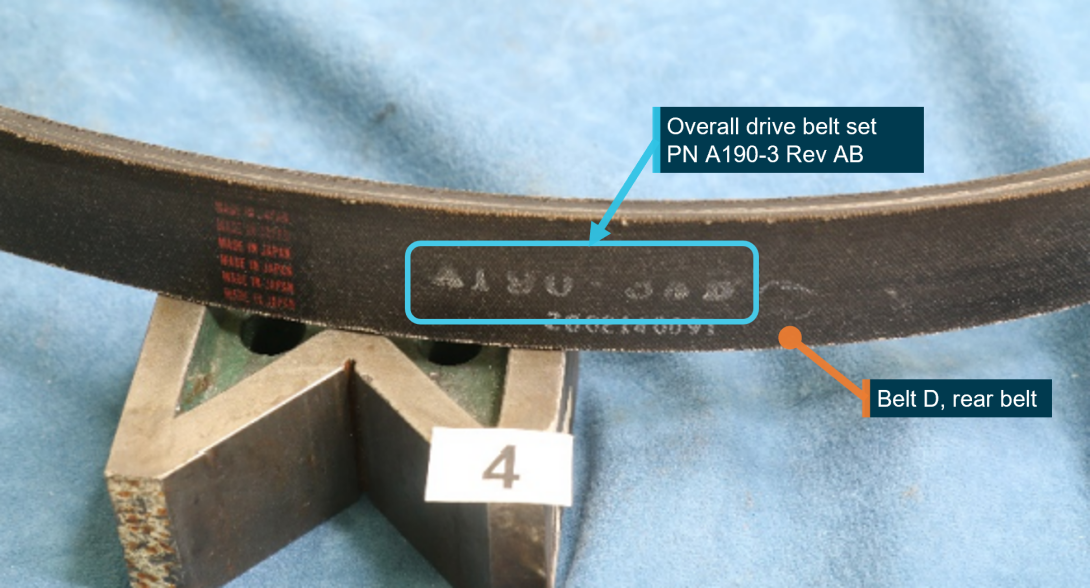
Source: ATSB
All 4 drive belts appeared to be of a similar construction with 11 tensile cords contained within each ‘vee’. Figure 6 shows drive belt A, which had sustained significant loss in overall width and the rear part of the vee torn from the tie band. Belt B was similarly damaged, having the forward vee torn form the tie band. The intact drive belts, C and D, were of larger overall diameter, 40 mm, and 45 mm respectively, than the severely damaged drive belts, A and B.
To maintain the pre-set factory tension settings during the occurrence flight, the clutch actuator is likely to have applied additional load to the rear 2 intact drive belts (C and D). The observed stretching of drive belts C and D may be an indicator that the helicopter had operated with just those 2 drive belts for an extended period during the occurrence flight, after A and B had dislodged from the fitted position and become damaged.
Figure 8: Damage to forward drive belt (Belt A)
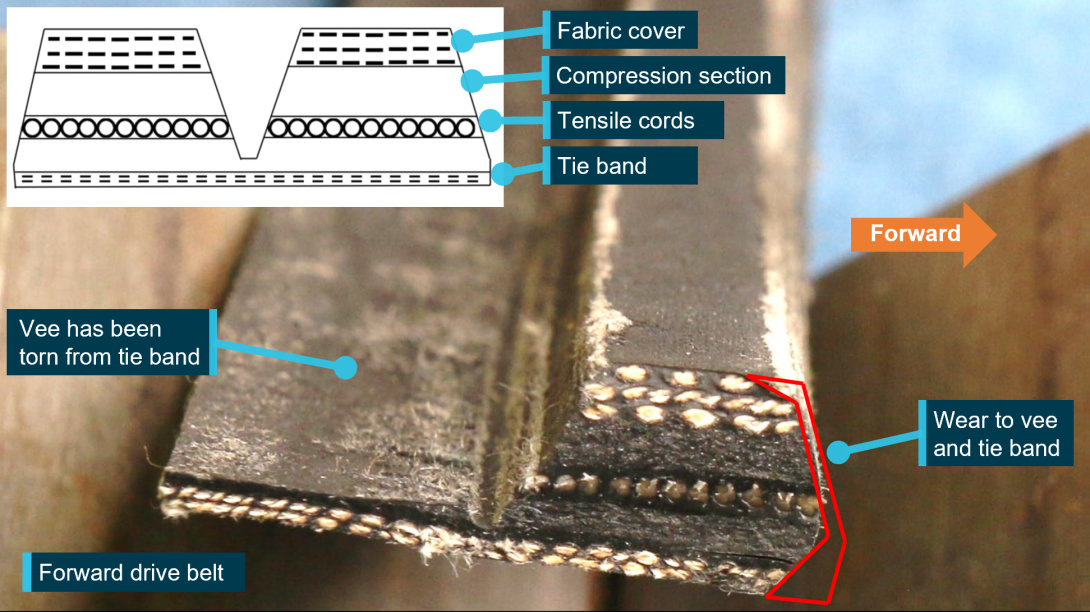
Source: ATSB
Purpose of safety investigationsThe objective of a safety investigation is to enhance transport safety. This is done through:
It is not a function of the ATSB to apportion blame or provide a means for determining liability. At the same time, an investigation report must include factual material of sufficient weight to support the analysis and findings. At all times the ATSB endeavours to balance the use of material that could imply adverse comment with the need to properly explain what happened, and why, in a fair and unbiased manner. The ATSB does not investigate for the purpose of taking administrative, regulatory or criminal action. TerminologyAn explanation of terminology used in ATSB investigation reports is available here. This includes terms such as occurrence, contributing factor, other factor that increased risk, and safety issue. Publishing informationReleased in accordance with section 25 of the Transport Safety Investigation Act 2003 Published by: Australian Transport Safety Bureau © Commonwealth of Australia 2023 Ownership of intellectual property rights in this publication Unless otherwise noted, copyright (and any other intellectual property rights, if any) in this report publication is owned by the Commonwealth of Australia. Creative Commons licence With the exception of the Coat of Arms, ATSB logo, and photos and graphics in which a third party holds copyright, this publication is licensed under a Creative Commons Attribution 3.0 Australia licence. Creative Commons Attribution 3.0 Australia Licence is a standard form licence agreement that allows you to copy, distribute, transmit and adapt this publication provided that you attribute the work. The ATSB’s preference is that you attribute this publication (and any material sourced from it) using the following wording: Source: Australian Transport Safety Bureau Copyright in material obtained from other agencies, private individuals or organisations, belongs to those agencies, individuals or organisations. Where you wish to use their material, you will need to contact them directly. |
[1] The presence of the clutch light flickering indicates the clutch is moving to take up normal drive belt looseness in operation.
[2] Collective: a primary helicopter flight control that simultaneously affects the pitch of all blades of a lifting rotor. Collective input is the main control for vertical velocity.
[3] Dynamic rollover: The helicopter rolls or pivots around a skid, or landing gear wheel, until a critical rollover angle is reached. The main rotor thrust then continues the roll and the helicopter rolls onto its side, regardless of cyclic control correction inputs.
[4] A report for this incident was released by the ATSB as occurrence brief AB-2020-015.
[5] The overhaul of the complete helicopter is carried out each 2,200 hours or 12 years, time-in-service of the helicopter.
[6] An engineering order is an approved modification, repair or alteration to an aircraft or system.
[7] There was no published limit to the amount of time that the drive belts could remain in a stretched condition between starts