Executive summary
What happened
On 22 December 2020, the pilot of a Robinson R44 II helicopter was conducting aerial agricultural spray operations on a property about 13 km south-east of Clare Valley Aerodrome, South Australia. After completing numerous spraying runs throughout the morning, the pilot started a gentle descending turn to the landing site to replenish with chemical product when a loud bang emanated from the rear of the helicopter. The pilot reported that the helicopter descended rapidly, and the flight controls appeared to be jammed. The helicopter collided heavily with the loading vehicle, coming to rest on its side. The pilot and ground crewman were uninjured, and the helicopter was substantially damaged.
What the ATSB found
The ATSB found that the forward yoke of the helicopter’s clutch shaft had failed due to an undetected fatigue crack that originated from an indent in one of the arms of the yoke. This resulted in loss of drive to the main and tail rotor systems. The unrestrained clutch shaft caused the displacement of the hydraulic reservoir and the loss of fluid. The loss of hydraulic fluid removed hydraulic power assistance to the flight control servos leading to increased control stick forces to operate the helicopter.
The pilot experienced difficulties in controlling the helicopter and executed an emergency descent from a low height without hydraulic power assistance and no tail rotor control. The pilot was presented with a compound emergency for which no training had been provided and for which they had no prior experience.
The ATSB found that the helicopter manufacturer’s maintenance instructions requiring verification that no cracks, corrosion or fretting were present on the yoke, lacked specific instructions on the method to be employed. The visual inspection that was employed increased the risk that a crack in the yoke arm may not be detected.
What has been done as a result
The helicopter manufacturer, the Robinson Helicopter Company, introduced new maintenance inspection requirements for the clutch shaft forward yoke at the 2,200/2,400-hourly inspection for the R44 helicopter. This included replacement of yokes of earlier revision status (A through G) and for later revision (H and subsequent), the option of replacement, or a more detailed examination that included a magnetic particle inspection. This update was included in the R44 maintenance manual in August 2022. The manufacturer also changed the paint colour of the yokes at the forward flex coupling from dark grey to white. This was to enhance the visibility of fretting dust during inspections, in the event of loose hardware.
Following the accident, the ATSB issued a Safety Advisory Notice, AO-2020-064-SAN-014 advising operators of R44 helicopters that based on the preliminary finding of fatigue cracking, to look for the presence of corrosion, fretting or cracking, which may not be visually obvious during all inspections of the clutch shaft yoke.
The Civil Aviation Safety Authority issued an Airworthiness Bulletin, AWB 63-010 advising industry of the failure of the yoke based on the ATSB investigation preliminary finding. It advised pilots and maintenance personnel to exercise vigilance for any signs of deterioration in the helicopter drive train components. This was further supported by the release of similar bulletins by the European Union Aviation Safety Agency and the US Federal Aviation Administration.
Safety message
This occurrence highlighted how non-life limited components such as a drive train yoke may still develop defects and fail in-flight. Aircraft owners and maintenance personnel are reminded of the importance of applying inspection and maintenance criteria specified in the aircraft manufacturer’s publications. Should maintenance information be lacking or unclear, the manufacturer or authorised representative should be contacted for appropriate, additional information.
The occurrence also serves as a reminder to pilots and maintenance personnel that when conducting inspections to be prepared for the unexpected, and to remain vigilant for defects in parts with an established history of reliability.
The occurrence
On the morning of 22 December 2020, the pilot of a Robinson Helicopter Company R44 II, registered VH-HOB, prepared the helicopter for aerial agricultural spray operations to be conducted on a property located about 13 km to the south-east of Clare Valley Aerodrome, South Australia. The pilot completed the daily inspection and departed the Clare Valley hangar at 0652 Central Daylight-saving Time[1] for the short flight to the loading zone, from where operations would be based.
The pilot arrived at the loading zone at 0700 and departed at 0702 with the property owner on board to conduct a short survey flight of the area to be sprayed, returning to the loading zone at 0708. Following the arrival of the ground crewman, the helicopter was loaded with chemical product, and at 0728 the pilot departed and conducted a series of spraying runs.
Numerous spraying runs were completed during the morning between 0728 and 0920 with the pilot returning to the loading zone periodically to replenish with chemical product and to refuel the helicopter. The pilot reported that the operation proceeded smoothly, and the long spray runs with minimal obstacles made for ideal spraying conditions.
During the final descent to the loading zone at about 0926, the pilot momentarily increased altitude to gain a better view of a light shower approaching from the south-west, and to assess its potential impact on further spraying operations. The pilot slowed the helicopter, and once satisfied that the shower did not pose a threat, started a gentle, right descending turn at 0926:20 towards the ground loading vehicle with the intent to land alongside as on previous occasions (Figure 1).
Figure 1: VH-HOB flight path showing return to loading zone and descent and inset providing accident location
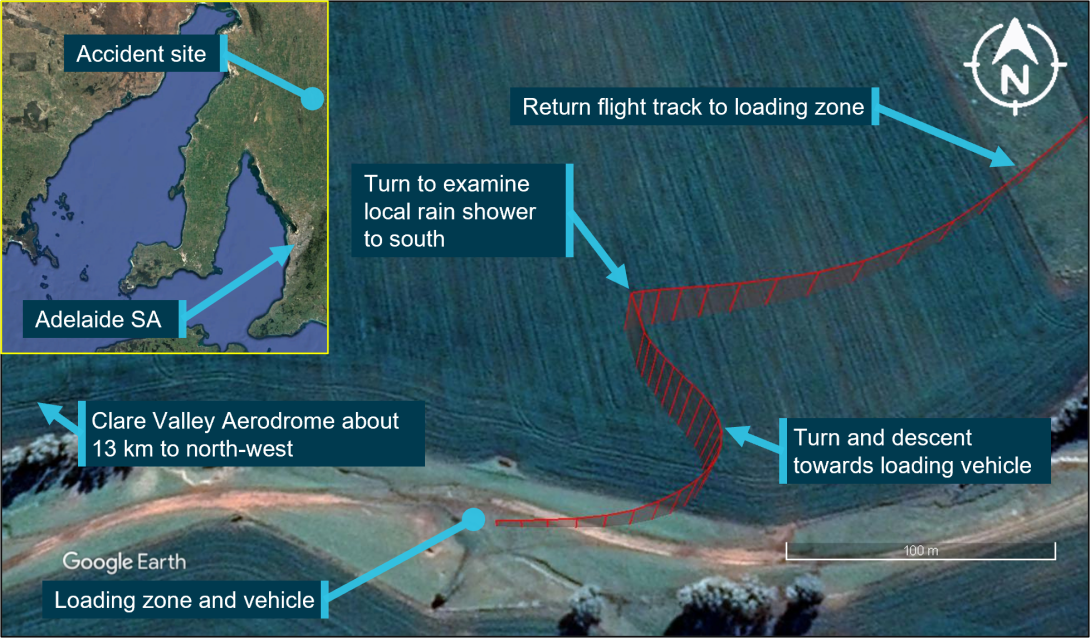
Source: Google and DGPS data, annotated by the ATSB
About 10 seconds into the turn, at 0926:30, a loud bang from the rear of the helicopter was heard, followed by vibrations from the rotor systems. The ground crewman recalled looking up and seeing that the tail rotor had stopped turning. The pilot reported that the cockpit flight controls appeared to have jammed and of not being able to move the tail rotor pedals. The helicopter’s rate of descent increased to 550 ft/min and as reported by the pilot, its movement towards the ground loading vehicle was generally unaffected by the pilot’s attempts at control inputs. The helicopter’s flight path continued until its landing gear impacted the vehicle’s roof, which resulted in it rolling onto its right side and colliding with terrain at 0926:46.
The pilot was not injured in the collision and was assisted from the helicopter wreckage by the ground crewman. There was no post-impact fire, and the helicopter was substantially damaged.
Context
Pilot information
The pilot of VH-HOB held a Commercial Pilot Licence (Helicopter) and a Private Pilot Licence (Aeroplane), both issued in March 2015. The pilot held class ratings included single engine helicopters and helicopter low-level rating. From 2017, the pilot also held an aerial application rating for helicopter operations.
The pilot completed an aerial application proficiency check for single engine helicopters and a night Visual Flight Rules (Helicopter) flight review for Robinson R44 helicopters on 23 July 2020. Both were valid until 31 July 2021.
The pilot held a Class 2 Aviation Medical Certificate issued by the Civil Aviation Safety Authority (CASA), without medical restrictions, which was valid until 23 January 2023.
The pilot’s logbook indicated that at the time of the accident, the pilot had a total flying experience of about 6,521 hours. Of these, about 1,337 hours were in the Robinson R44 helicopter and 1,018 hours conducting aerial application work. The pilot had flown about 105 hours on type in the previous 90 days, and about 54 hours on type in the previous 30 days.
Aircraft information
VH-HOB was a Robinson Helicopter Company R44 II helicopter that was manufactured in the United States in 2005 with serial number 10801. It was first registered in Australia in 2005.
The R44 II is a single-engine, light utility and training helicopter with a semi-rigid, two-bladed main rotor, a two‑bladed tail rotor and skid type landing gear. It had an enclosed cabin with two rows of side‑by‑side seating for a pilot and three passengers.
The helicopter was powered by a Textron Lycoming IO-540-AE1A5, 6-cylinder, fuel-injected piston engine and was fitted with hydraulic servo-actuators providing hydraulic power assistance to the main rotor, flight control system.
VH-HOB was configured for aerial application work that included a belly-mounted storage tank and laterally mounted spray booms for chemical product dispersal.
The helicopter’s current maintenance release was issued on 20 October 2020, about 92 flight hours prior to the accident. It was valid for 12 months or 100 hours, whichever occurred sooner. At the time of the accident, VH-HOB had accumulated about 4,579 hours, total time-in-service. There were no open defects recorded on the maintenance release and no outstanding or overdue maintenance was noted.
Maintenance records also showed that about 188 flight hours prior to the accident, at an aircraft time-in-service of 4,391.0 hours, an airframe 2,200-hour/12-year inspection was completed.
Meteorological information
The forecast meteorological conditions for Clare Valley Aerodrome (13 km north-west of the accident site) area, indicated winds from the south-south-west at 19 kt and a temperature of 12 ⁰C. Visibility was forecast to be greater than 5 km with isolated showers of rain and broken cloud above 1,200 ft.
The METAR[2] for Clare Valley township issued at 0930 recorded wind from the south-west at 7 kt and a temperature of 14 ⁰C. This was consistent with witness in the accident area who reported that some cloud was present with isolated showers to the south.
Wreckage information
The ATSB did not attend the accident site and based assessment of the helicopter on imagery and reports supplied by the operator, maintenance personnel, interview records and witness account.
The helicopter presented as relatively intact with the tailboom broken aft of its forward mount point. The operator’s examination identified that one of the arms of the clutch shaft forward yoke had fractured resulting in loss of drive to the main and tail rotor systems. The tubular steel structure surrounding the shaft was damaged by the rotation of the unrestrained clutch shaft. The hydraulic reservoir was also found displaced from its mounting base and was located within the wreckage (Figure 2).
Figure 2: VH-HOB following the collision with inset showing clutch shaft with upper drive sheaves and displaced hydraulic reservoir
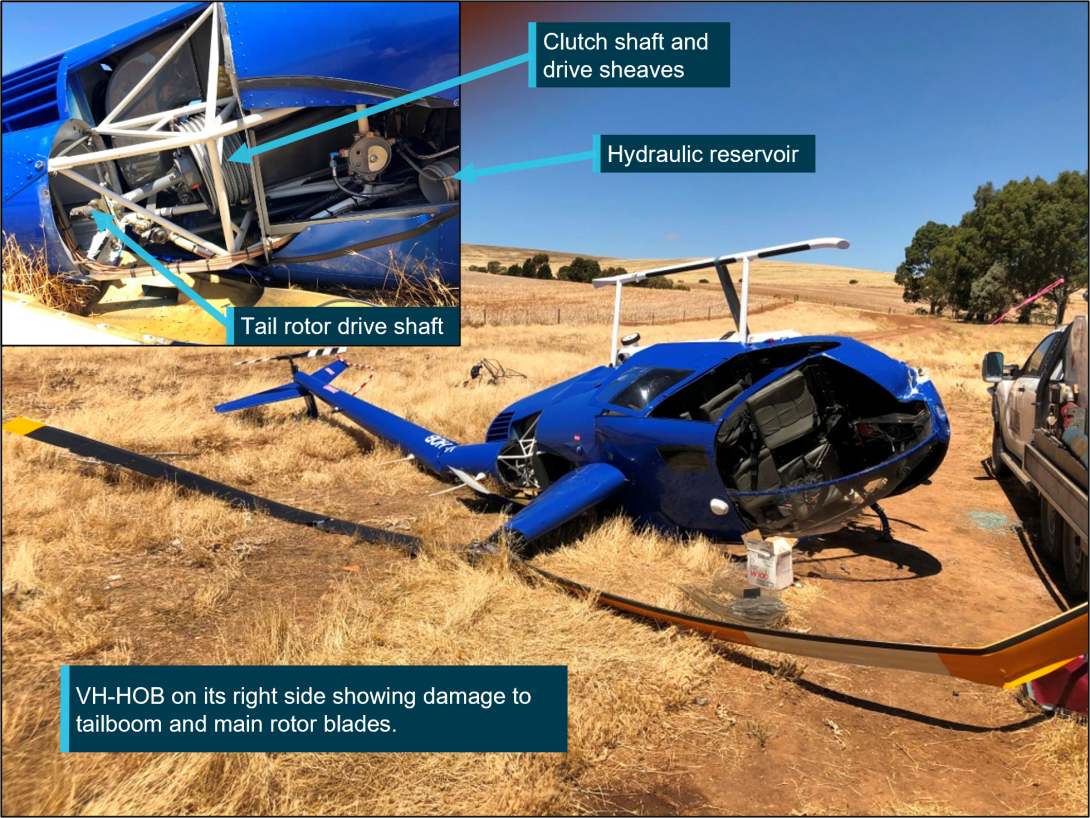
Source: Supplied, annotated by the ATSB
Following the accident, attending maintenance personnel reported they conducted a functional check of the flight control system and found the cyclic[3] and collective[4] controls had full and free movement. However, one of the tail rotor control tubes exhibited bending damage that was likely the result of contact with the unrestrained clutch shaft.
Both the pilot and the ground crewman reported that the engine stopped operating shortly before the collision. Images showed that a cutting action of the unrestrained clutch shaft forward yoke (see R44 rotor drive system below) penetrated the engine upper firewall and damaged the engine fuel system flow divider located on the engine below. The yoke perforated the flow divider top housing, which likely interrupted fuel flow to the engine, resulting in engine stoppage.
Both of the fuel tanks were found intact and there was little external distortion of the auxiliary tank following the impact with the ground.
At interview, the ground crewman commented that the helicopter was observed to approach at a low rate of descent, and had it not struck the vehicle, the landing would likely have resulted in significantly less damage to the helicopter.
R44 rotor drive system
The clutch shaft forward yoke assembly is part of the R44 rotor drive system. The R44 pilot’s operating handbook provided the following description of the main and tail rotor drive system and is illustrated in Figure 3.
A vee-belt sheave is bolted directly to the engine output shaft. Vee-belts transmit power to the upper sheave which has an overrunning clutch contained in its hub. The inner shaft of the clutch transmits power forward to the main rotor and aft to the tail rotor. Flexible couplings are located at the main gearbox input and at each end of the long tail rotor drive shaft.
Figure 3: R44 drive train with inset showing clutch shaft forward yoke and flex plate providing input power to the main and tail rotor gearboxes
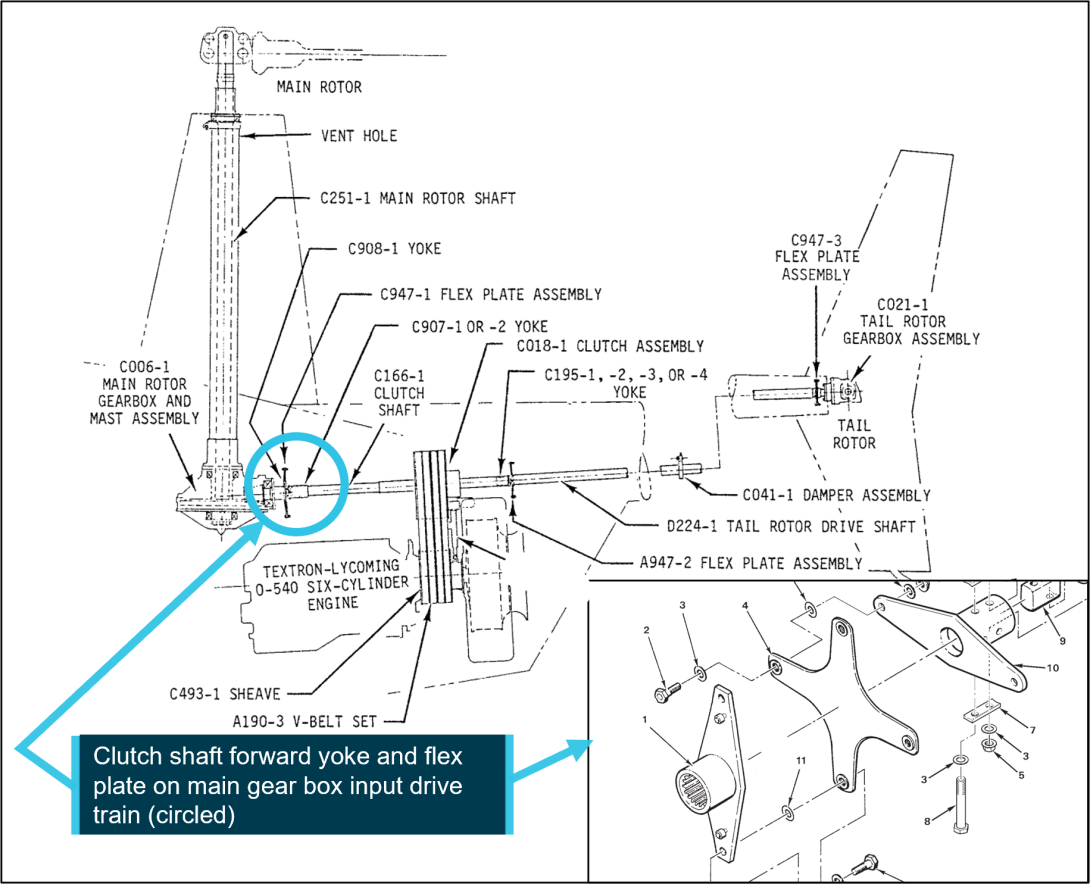
Source: Robinson Helicopter Company R44 maintenance manual, annotated by the ATSB
Images provided by maintenance personnel showed that during the accident sequence, the vee‑belts had dislodged from the upper sheave.
A manual, cable operated rotor brake was mounted on the aft end of the main gearbox and when applied via the pull handle in the cabin ceiling, friction pads of the braking mechanism would contact the main gearbox input yoke to stop the rotor system. Images showed that the actuating cable was displaced from its guide pulley and was disconnected from the braking mechanism (Figure 4).
Figure 4: Rotor brake mechanism minus actuating cable attached and trapped wire material around the main gearbox input yoke shaft
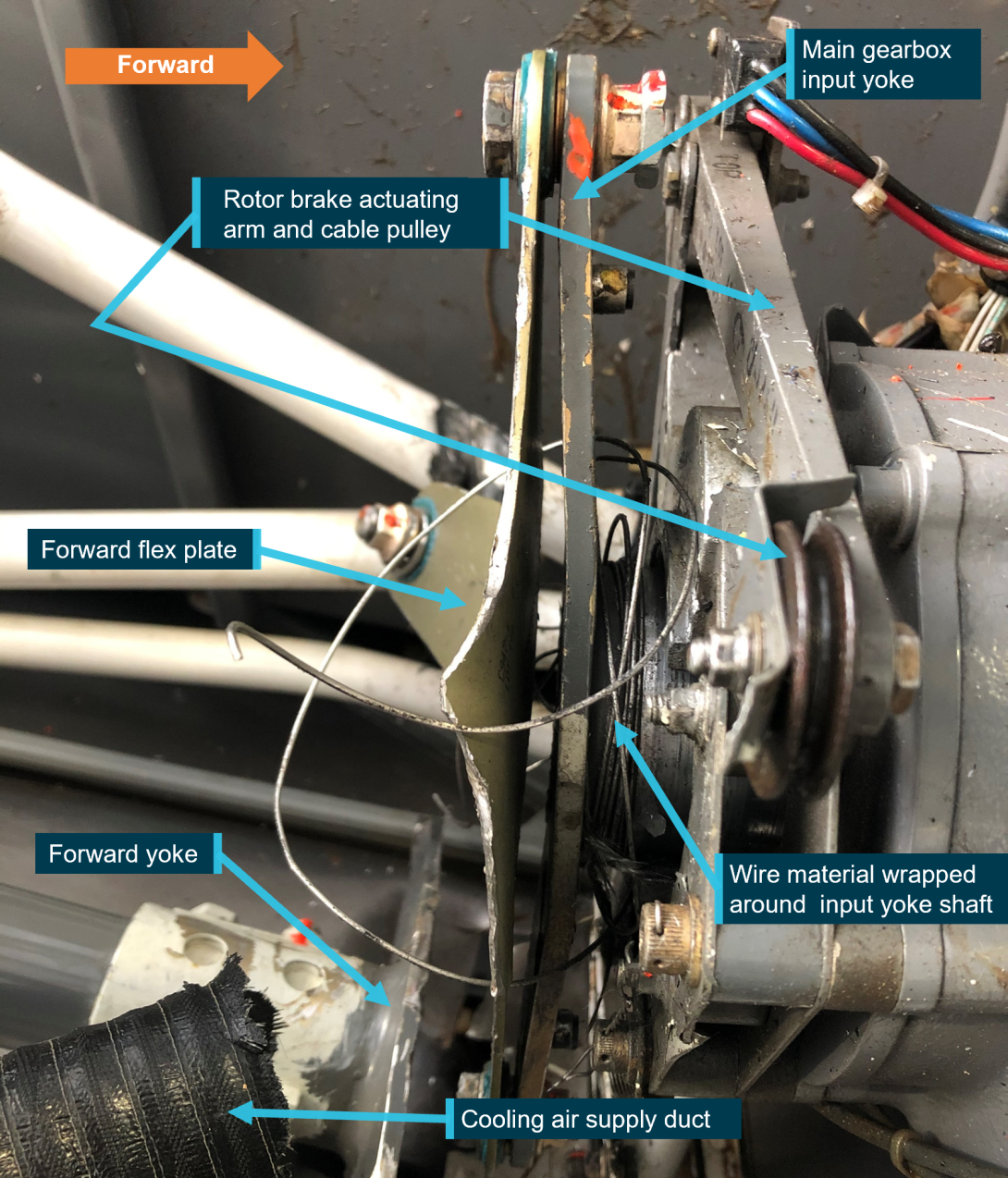
Source: Maintenance organisation, annotated by the ATSB
The action of separating the cable from the braking mechanism likely caused the rotor brake to be momentarily actuated, and while considered minimal, may have affected the speed of the main rotor system.
R44 II hydraulic system
The R44 II hydraulic system consists of a pump mounted to the main rotor gearbox, a servo at each of the control tubes connecting the cockpit controls to the swashplate, a reservoir assembly, hydraulic fluid and interconnecting flexible hoses (Figure 5). Should a loss of hydraulic pressure occur, the servos contain an irreversible feature to reduce main rotor feedback forces to the pilot’s controls. However, in the absence of hydraulic pressure, the manufacturer advised that the cyclic control system is harder to move in the fore-and-aft and lateral planes, while the collective control can be easily lowered, but becomes harder to raise.
Following the accident, the hydraulic system was provided to the ATSB for further examination. Without hydraulic pressure applied, examination of each servo showed that the irreversible feature was functional. The forces required to move each servo were noted to be slightly higher in comparison to new servos but were considered acceptable.
The hydraulic reservoir had separated from the hydraulic manifold mounted to the tubular frame likely from the clutch shaft striking the manifold (mounting location circled, Figure 5). This resulted in significant loss of hydraulic fluid. The ATSB’s examination of the hydraulic reservoir revealed multiple impact marks attributed to striking, or being struck repeatedly by a rotating component, likely the main gearbox input yoke.
Figure 5: Hydraulic system and main gearbox installation from VH-HOB
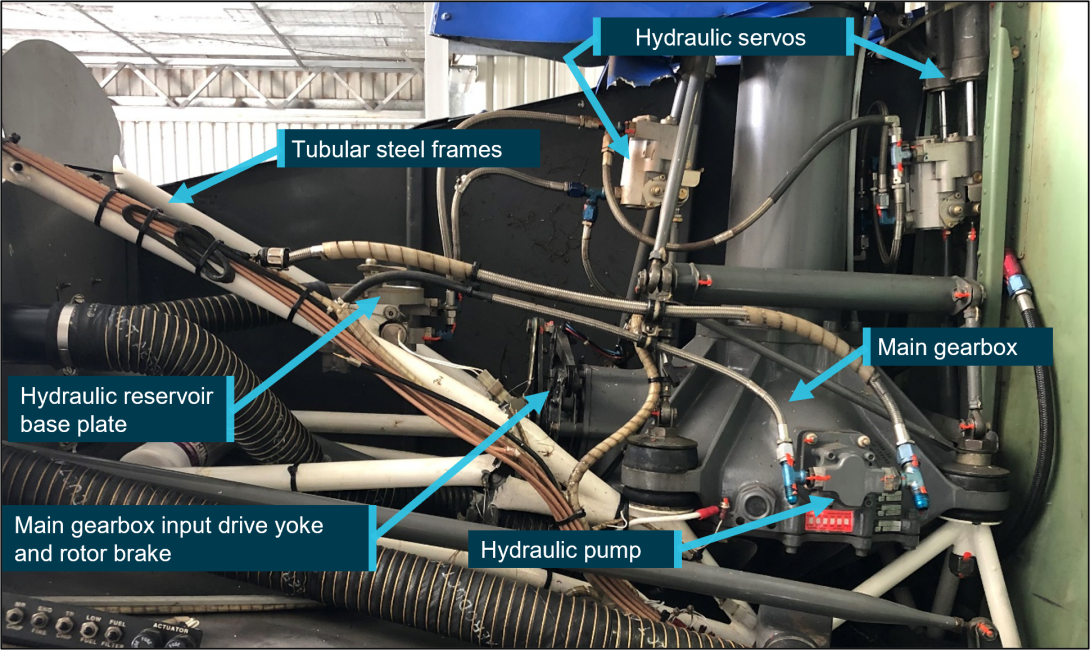
Source: Maintenance organisation, annotated by ATSB
Yoke examination
The clutch shaft with the fractured yoke arm, the forward flex plate and the attaching hardware were provided to the ATSB for detailed examination (Figure 6). A portion of the flex plate that remained connected to the yoke and the separated section of the arm was also provided for examination.
The yoke presented with one arm intact, to which a portion of the forward flex plate and its attaching hardware were present. The opposite arm had fractured at the bolt hole that secured the arm to flex plate.
The surfaces of the yoke presented with scoring marks and indentations to the painted surfaces. Mechanical impact damage and gouging was also present with smearing damage to the arm fracture surfaces obscuring some of the original fracture features.
Figure 6: Fractured forward yoke arm with inset showing clutch shaft assembly and flex plate
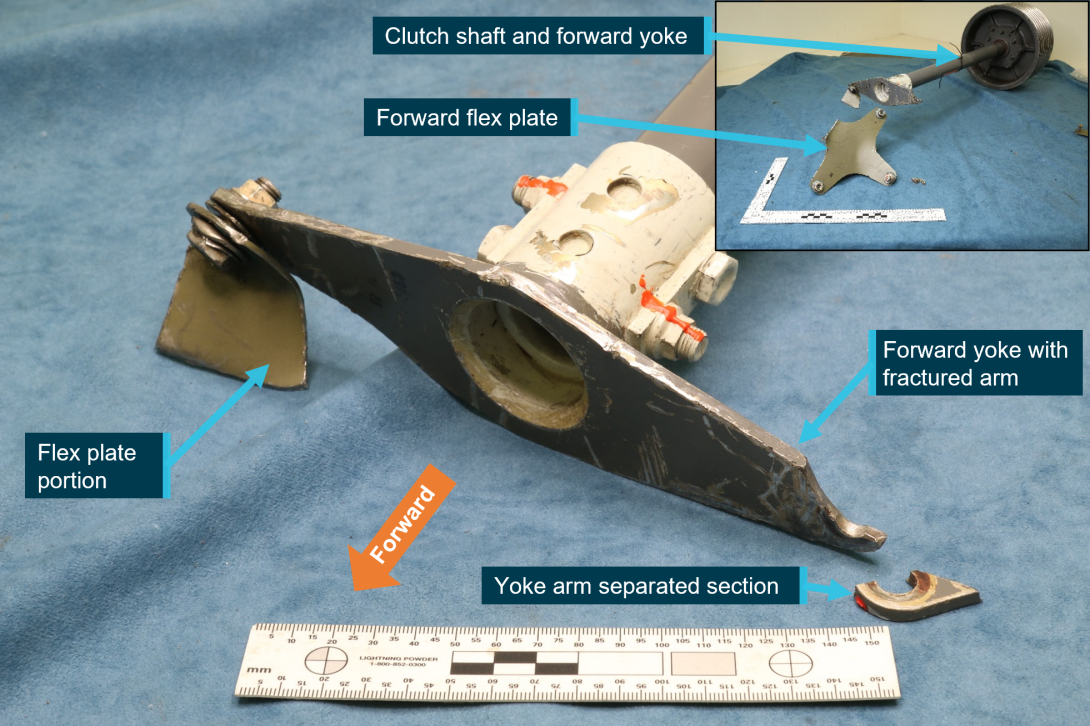
Source: ATSB
A detailed visual inspection of the yoke arms using an optical microscope and a magnetic particle inspection of the yoke surfaces and bolt hole regions, did not identify additional cracks.
Red-coloured corrosion products were observed on the forward face of the yoke where it contacted the bonded stainless-steel washer from of the forward flex plate (Figure 7). Fretting damage was present on the aft face that was in contact with the attaching hardware. Microscopic examination of the red-coloured product identified it to have been produced from general corrosion/oxidation of the underlying steel surface. There were no indications of pitting corrosion.
Figure 7: Fractured yoke arm and separated section front and rear surface condition

Source: ATSB
Visual examination of the fracture surfaces on either side of the bolt hole showed evidence of fatigue fracture. The fracture surface showed concentric beach marks indicative of a progressive crack mechanism, which radiated outwards from the likely origin at the inner bolt hole surface on the front face of the yoke (Figure 8). The fatigue crack had propagated from the front to the aft face, and initially obscured from view by the presence of the attaching hardware.
Crack propagation continued across a substantial portion of the cross section (about 98% of fracture # 1 and about 80% of fracture #2), with a visible portion on the rear face of about 6 mm before final overstress fracture and separation occurred.
Figure 8: Separated yoke tip with fracture features identified

Source: ATSB
A scanning electron microscope (SEM) was used to further qualify the fracture surfaces at high magnifications. The SEM examination confirmed:
- many hundreds of crack progression bands were observed, which indicated crack growth occurred as a result of high-cycle fatigue[5]
- surface damage (an indent) approximately 0.10 mm in depth at the fatigue crack origin of fracture #1 had likely influenced the initiation of cracking within the yoke arm at the point of fracture
- a clear boundary on the fracture surface existed between the region of corrosion and the region that was not corroded (Figure 9).
Figure 9: Fracture surface of separated section showing corrosion boundary with inset showing crack surface discoloration
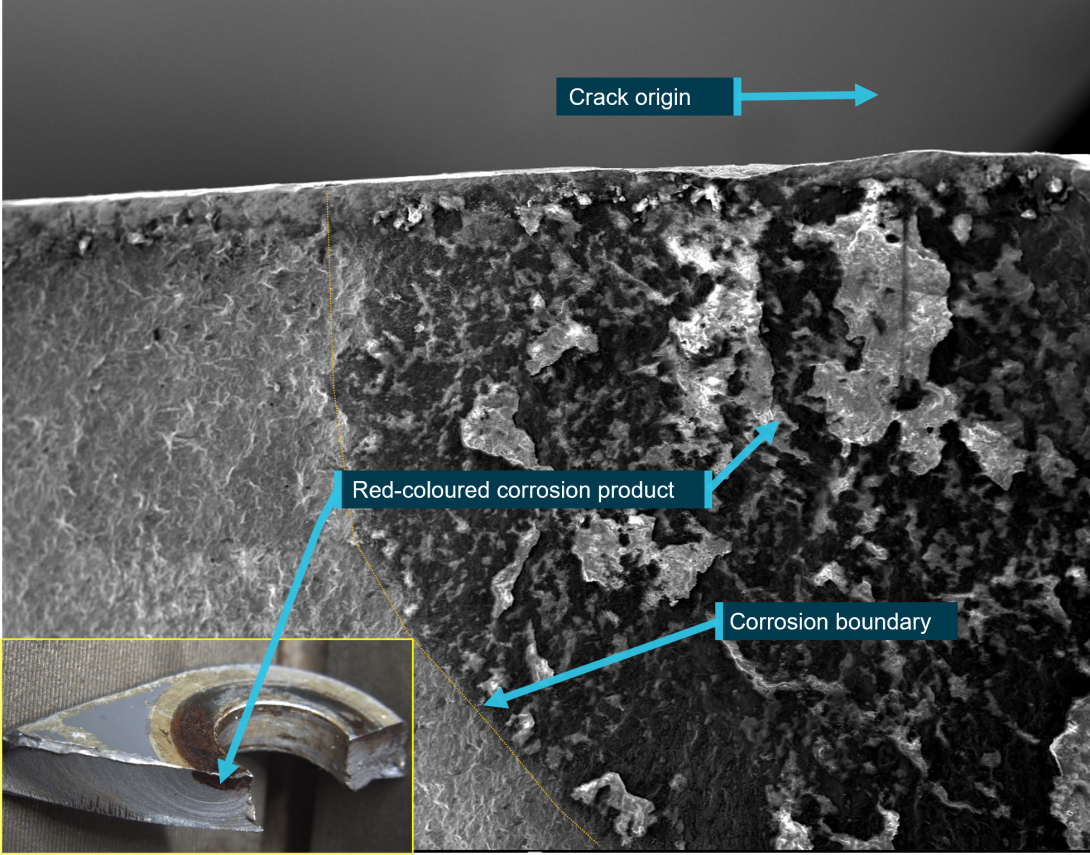
Source: ATSB
Metallurgical, chemical and dimensional analysis established that the yoke conformed to the manufacturer’s specification for material type, hardness, and physical dimensions.
Overall corrosion protection had been specified by the manufacturer that was for the yoke to be cadmium-plated, primed and then painted. These corrosion protection schemes were confirmed during metallurgical examination of the yoke.
Manufacturer’s clutch shaft forward yoke inspections
The manufacturer’s instructions for continuing airworthiness of the clutch shaft forward yoke (part number C907) were contained in the Robinson R44 II pilot’s operating handbook (POH) and the aircraft maintenance manual. The following was noted:
- At each daily or pre-flight inspection, the yoke flanges[6] (yoke arms) were to be checked. No cracks were permitted.
- At each 100-hour or annual airframe inspection, the yoke was to be checked for condition and to verify no cracks, corrosion or fretting was present. The yoke was also to be checked for security and operating clearance.
- At each 2,200-hour inspection, a 100-hour or annual inspection is also conducted, and the yoke was to be checked for condition. Additionally, the aircraft maintenance manual provided a list of components that were to be replaced with new or overhauled exchanged parts when they had accumulated 2,200/2,400-hours time‑in‑service. There was no requirement for the yoke to be replaced with a new or overhauled part once those hours had accumulated.
Other than for unscheduled maintenance, the yoke was only separated from the forward flex plate (see Figure 3 insert) when parts were replaced at their assigned 2,200/2,400-hour service interval. The yoke was treated as an ‘on-condition’ item and was not assigned an operating time‑in‑service, fatigue, or calendar life-limit.
Maintenance personnel reported that when installed, the yoke can be viewed on a daily inspection via an access panel located on the right side of the helicopter. During the 100-hour or annual inspection, the yoke can also be inspected from above when the upper panel between the fuel tanks was removed. It was noted that cracking on the front face of the yoke arm would not be visible during these inspections as there was no requirement to remove the yoke from the flex plate.
The aircraft maintenance manual specified a range of examination methods for the detection of defects and identified specific parts that warranted examination above that provided by visual inspection means. Higher levels of examination for nominated parts included the use of a suitably powered magnifying glass, and fluorescent penetrant and magnetic particle inspection processes. However, the yoke was not included in the nominated parts list.
Maintenance practices
The pilot reported that on the day of the accident, a pre-flight inspection was completed, and no defects were noted. Maintenance personnel also reported that no defects associated with the forward yoke were noted during the 100-hour inspection that was conducted 92 hours prior to the accident.
During the most recent 2,200-hour inspection, the helicopter’s main rotor gearbox was refitted, and the three flex plates of the rotor system drive train were replaced with new items.
Records showed that the engine-to-gearbox clutch shaft assembly had been replaced about 701 hours prior to the 2,200-hour inspection with the forward yoke transferred to the replacement shaft. This may have provided another opportunity for detailed inspection of all yoke surfaces.
Maintenance personnel involved in the 2,200-hour inspection reported that at the time of replacing the flex plates, following separation from the forward flex plate, the yoke surfaces were visually examined for defects and the yoke was determined to be serviceable.
The manufacturer advised that yokes were commonly removed from service due to the presence of corrosion or fretting damage, but not due to cracks. When forward yokes were returned to the manufacturer as part of the clutch shaft for overhaul, the surface finish was removed, and a magnetic particle inspection for defects would be completed prior to release to service.
Helicopter emergency procedures
Hydraulic system normal and emergency procedures
The R44 II POH advised pilots that for training purposes, a hydraulic system failure may be simulated by switching the hydraulic system off by using the cyclic-mounted hydraulic switch. With hydraulics switched off, controlling the helicopter in a hover may be difficult due to control system feedback forces.
The handbook also advised pilots to expect control stiffness and feedback when conducting hydraulic systems checks or pre-take off control checks with the hydraulic system switched off.
The handbook described the symptoms for a hydraulic system failure as indicated by heavy or stiff cyclic and collective controls, and loss of hydraulic fluid may cause intermittent and/or vibrating feedback in the controls. Should that occur, the POH stated that control of the helicopter would be normal except for the increase in stick forces. Additionally, if hydraulic power was not restored after verifying that the hydraulic switch is in the ‘ON’ position, the pilot is to switch hydraulics to ‘OFF’ and to land as soon as practical.
Engine power loss or loss of tail rotor function
In the event of an engine or drive system failure, the POH advised pilots to immediately lower the collective lever and enter autorotation[7] while observing airspeed requirements. Pilots were also instructed to enter an autorotation if loss of tail rotor thrust in forward flight occurs.
An autorotation is typically conducted at a specified forward airspeed and rotor RPM at which a power-off glide is most efficient. Autorotation airspeed and RPM is different for each helicopter type and is characterised as a controlled descent. The flight controls are used to manoeuvre the helicopter during the autorotation, through to completion of the landing sequence.
Although the tail rotor is used to counteract the yawing effect of the main rotor at low speed, a loss of tail rotor control or drive to the tail rotor, is manageable provided adequate airspeed is maintained, as directional stability is provided by the helicopter’s vertical and/or dorsal fin.
Pilots are trained to perform autorotational descents, and autorotational capability is a certification requirement for helicopters.
At interview, the pilot reported that simulated engine failures, tail rotor system malfunctions and hydraulic failures were practised during training and flight reviews. However, they were trained and assessed as independent emergencies and were never conducted simultaneously as a compound emergency.
Recorded data
VH-HOB was not equipped with a flight data or cockpit voice recorder, nor was it required to be. Differential GPS[8] flight path data from the on-board SatLoc Bantam[9] aerial application tracking device was provided to the ATSB.
Speed and position data from the SatLoc device was used in the analysis of the helicopter’s movements in the final 3 minutes of flight (Table 1).
Table 1: Key events involving VH-HOB during the final minutes of flight with approximate values of flight behaviour
Time | VH-HOB movements | Height above ground level (ft) | Ground speed (kt) | Rate of descent (ROD) (fpm) |
Rate of track change (⁰ per minute) |
0924:06 | Pilot returning to loading zone, slows prior climbing flight from about 160 to 40 fpm. | 250 | 19 | ||
0924:08 | Pilot commences descent to loading zone | 20 | 60 | ||
0925:44 | Bottom of descent | 62 | 21 | 0 | |
0925:46 | Pilot initiates a climb, rate of climb about 60 fpm | 64 | 20 | ||
0926:18 | Approaching top of climb, pilot slows rate of climb to about 20 fpm | 124 | 5 | ||
0926:20 | Helicopter on descent | 122 | 5 | 60 | |
0926:28 | Bang heard (estimated time of noise) | 104 | 4 | 200 | 475 |
0926:30 | Descent | 94 | 5 | 335 | 416 |
0926:36 | Descent – maximum ROD | 43 | 8 | 550 | 207 |
0926:38 | Descent | 30 | 10 | 413 | 232 |
0926:40 | Descent | 18 | 10 | 314 | 133 |
0926:42 | Descent | 10 | 11 | 236 | 74 |
0926:44 | Descent | 5 | 10 | 160 | 11 |
0926:46 | Helicopter collides with vehicle/terrain | 9 | 160 |
From 09:26:40 to collision at 09:26:46, the aircraft track varied by about 4 degrees. In the last two seconds of flight, the track varied by less than one degree, and aligned the helicopter’s movement with the position of the stationary ground vehicle (Figure 10).
Figure 10: VH-HOB flight path showing landing approach with momentary climb and descent towards ground vehicle
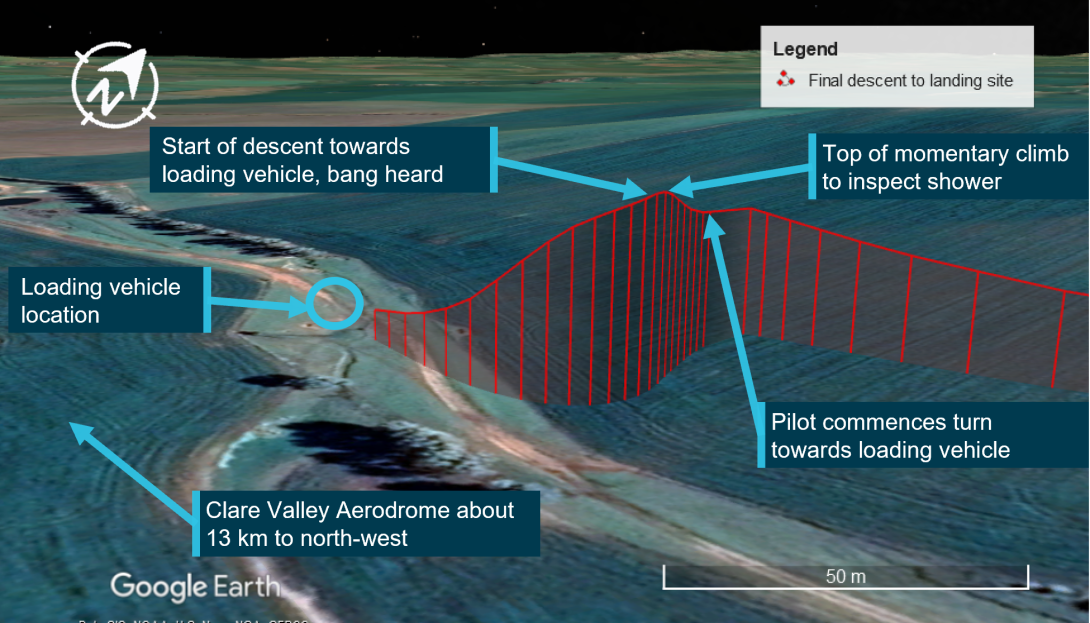
Source: Google, annotated by the ATSB
Related occurrences
This accident involving the clutch shaft forward yoke (part number C907) was the first occurrence to be investigated by the ATSB that involved an in-flight failure of a yoke on a helicopter model in the Robinson range.
Robinson advised of no other reports of fatigue cracks associated with forward yokes. Searches of the CASA, the US Federal Aviation Administration (FAA) and New Zealand Civil Aviation Authority (CAA) Service Difficulty Report databases did not reveal other documented cases of fatigue related cracking.
There was one similar R44 occurrence, involving loss of drive to the main and tail rotor due to weld failure of the forward yoke. The incident occurred during cruise flight in which the pilot heard a bang and experienced a loss of tail rotor effectiveness due to the failure of a weld joint in the forward yoke.
As a result of this incident, an airworthiness directive was issued by the FAA in August 1999 (FAA Priority Letter Airworthiness Directive AD 99-17-17), requiring the replacement of certain yoke assemblies in R44 helicopters before further flight. The manufacturer identified manufacturing lots associated with the failed yoke and retired the affected yokes from service. If uncorrected, the FAA advised that the condition could result in failure of the yoke assembly, loss of main and tail rotor drive, and subsequent loss of control of the helicopter. In October 1999, CASA issued AD/R44/13 in support of FAA action.
Safety analysis
The collision with terrain involving Robinson R44 II VH-HOB, about 13 km south-east of Clare Valley Aerodrome, South Australia, was the result of the loss of drive to the main and tail rotor systems due to fracture of the clutch shaft forward yoke. This analysis will focus on the failure of the yoke, the emergency descent, and the subsequent collision with terrain. The analysis will also consider maintenance information for the continued airworthiness of the yoke and management of in-flight emergencies.
Yoke failure and separation
The yoke failed as a result of fatigue crack propagation that initiated on the forward face of the yoke arm coincident with the bolt hole. On one side, the crack had initiated from a mechanical surface defect. The fatigue cracking was assessed to have propagated slowly as evidenced by the many hundreds of crack progression bands, with failure of the yoke arm occurring when minimal intact cross-sectional area remained.
A distinctly corroded region was identified on the forward-most surface of the yoke. A similarly corroded/stained region was identified on the fracture surface. The corroded regions were underneath where the bonded washer from the forward flex plate would normally be clamped. The varying nature of the corrosion within the fatigue crack and the demarcation between the various regions suggested that the crack had existed during an overhaul cycle of the component.
Following the fracture of the yoke, the clutch shaft became disconnected from the main gearbox creating misalignment of the upper and lower sheaves and displacement of the vee-belts. This resulted in a loss of drive from the engine to both the main and tail rotor systems. The loss of drive committed the pilot to find a suitable place to land the helicopter while conducting an emergency descent without tail rotor control.
Yoke inspections
The manufacturer’s in-service requirements for yoke serviceability specified that the yoke be inspected for cracks, fretting or corrosion at specific intervals that included the daily inspection, at scheduled time in service intervals and during the 2,200-hour inspection.
The drive train was inspected on the morning of the accident flight and at the previous scheduled inspection, and no defects were found. However, with the yoke connected to the forward flex plate, there was no opportunity to visually detect the crack on the forward face during the daily and 100-hour inspections. Once the crack had progressed to the rear surface of the yoke arm, it would have been difficult to see, given that the crack was estimated to be about 6 mm in length, and the area would have needed to have been sufficiently clean.
The only opportunity for detecting a crack initiating on the front face of the yoke would be when all yoke surfaces were exposed and not obscured by the presence of the flex plate and attaching hardware. This would be at the 2,200‑hour inspections, or at unscheduled clutch shaft or flex plate removal. The last time the yoke was separated from the forward flex plate was at the recent 2,200-hour inspection, about two months and 188 flight hours prior to the accident.
The presence of corrosion deposits in part of the cracked region indicated that the crack was likely present at that inspection. Once the yoke arm was re-installed, the forward face was obscured by the flex plate and the crack would not have been visible during the subsequent routine inspections.
Maintenance instructions for critical item
The forward yoke was not assigned a service life by the manufacturer so its continuation in service was dependent on it meeting specific inspection criteria to determine on-going serviceability. The maintenance instructions for continued airworthiness specified that the yoke be inspected for condition, and maintenance personnel were required to verify that no cracks, corrosion or fretting was present. No specific method on how to accomplish this was provided in the manufacturer’s documentation, and as such, a visual inspection would be acceptable.
Defects related to corrosion and fretting damage are likely detected by the un-aided eye, but crack identification may be not as obvious. At the 2,200-hour inspection, the yoke was separated from the forward flex plate and the visual inspection method that was used to detect cracks that existed on the helicopter’s forward yoke, was unsuccessful.
The methods used to verify the absence of cracks varied between this maintenance organisation and the aircraft manufacturer. When yokes were returned to the manufacturer as part of the clutch shaft assembly, the yokes were subject to magnetic particle inspection, which would have a greater chance of identifying a crack than visual inspection alone. This suggested that the inspection instruction was open to interpretation and was not consistently applied.
On this occasion, the failure of the yoke led to a loss of drive to both the main and tail rotor systems. The failure of this critical item further resulted in a secondary failure of the hydraulic system under the action of the unrestrained clutch shaft. This presented the pilot with a compound emergency resulting in an emergency descent and subsequent collision with the ground vehicle and terrain.
The reliability of the yoke and lack of history of removal from service due to cracking, likely influenced the use of visual inspection methods and reduced the expectation for a crack to be present. However, that further reduced the probability of detecting the crack when all the yoke surfaces are available for inspection.
Helicopter control
The pilot reported that when the yoke fractured the helicopter was configured for a gentle descent and turn towards the loading vehicle. However, the consequential failures that followed the failure of the yoke, which included a loss of tail rotor drive, resulted in degraded directional control. The pilot also reported that the cyclic and collective controls felt like they were jammed.
The significant bending of the tail rotor pitch control tube following impact by the intermediate flex coupling/clutch shaft aft yoke, likely restricted the movement of the tail rotor pedals, adding to the sense of difficulty in controlling the helicopter.
Post-accident examination of the collective and cyclic control systems found that they moved freely within their travel range. The loss of hydraulic power assistance would have increased the cyclic and collective feedback forces required by the pilot to control the helicopter. An unexpected increase in the control forces while flying with a normal relaxed grip on the cyclic and collective might have led the pilot to perceive the controls were jammed.
The multiple impact marks that presented on the hydraulic reservoir body indicated that the reservoir had become dislodged in flight rather than when the helicopter collided with terrain. The ATSB considered the possibility that the displaced hydraulic reservoir impeded the movement of the hydraulic servos or their control system, or that in the attempt to position the helicopter away from the ground vehicle, the flight controls were moved to their mechanical stops, which prevented further movement. However, based on the evidence available, neither of these possibilities could be confirmed.
The pilot’s usual practice was to land beside the loading vehicle to enable replenishment of chemical product and had configured the helicopter accordingly. Analysis of the flight path following the initial turn towards the ground support vehicle, revealed that the helicopter’s rate of descent repeatedly changed, as did the rate of turn as it approached the vehicle. This suggested that the helicopter was likely responding to some pilot control inputs and therefore some control of the helicopter was likely available. However, it was insufficient for the pilot to avoid a collision with the loading vehicle.
Multiple emergencies
The pilot reported that during their initial training and subsequent flight reviews, there was a requirement to demonstrate competency in performing autorotational descents and flying and landing the helicopter without hydraulic power assistance. However, there was no requirement to conduct compound major emergencies, such as the loss of tail rotor control coupled with a loss of hydraulic power assistance.
The hydraulic pump is driven by the helicopter’s main gearbox, so the hydraulic system is expected to continue providing hydraulic power during autorotation training. Consequently, this accident presented the pilot with a scenario for which they had no prior experience. It also occurred at a low height and low forward speed, which provided the pilot with very little time to diagnose the situation and manage the emergency landing.
Findings
ATSB investigation report findings focus on safety factors (that is, events and conditions that increase risk). Safety factors include ‘contributing factors’ and ‘other factors that increased risk’ (that is, factors that did not meet the definition of a contributing factor for this occurrence but were still considered important to include in the report for the purpose of increasing awareness and enhancing safety). In addition, ‘other findings’ may be included to provide important information about topics other than safety factors. Safety issues are highlighted in bold to emphasise their importance. A safety issue is a safety factor that (a) can reasonably be regarded as having the potential to adversely affect the safety of future operations, and (b) is a characteristic of an organisation or a system, rather than a characteristic of a specific individual, or characteristic of an operating environment at a specific point in time. These findings should not be read as apportioning blame or liability to any particular organisation or individual. |
From the evidence available, the following findings are made with respect to the loss of control and collision with terrain involving Robinson R44, VH-HOB, near Clare, South Australia, on 22 December 2020.
Contributing factors
- Fatigue cracks in the clutch shaft forward yoke progressed until the yoke fractured during operation, which led to a loss of drive to the main rotor system that necessitated an emergency descent.
- During the emergency descent from a height of about 100 feet, the pilot experienced difficulties in controlling the helicopter and was unable to avoid colliding with the ground vehicle, which increased the severity of the collision with terrain.
- Although it was very likely that a crack was present when the clutch shaft yoke was last disassembled from the forward flex plate, it was not detected during inspection. Once assembled, the crack, which had formed on the forward face of the yoke arm, was obscured by the presence of the flex plate.
- Although the helicopter manufacturer’s instructions for continuation in service for the clutch shaft forward yoke specified that the condition of the yoke was to be inspected to verify that no cracks, corrosion, or fretting was present, it did not provide specific instructions for the method to be employed. The visual inspection that was employed increased the risk that a crack in that area may not be detected [Safety issue].
Other (key) finding
- The emergency descent was performed without hydraulic power assistance to the main rotor control systems and without drive to the tail rotor. That required the pilot to manage simultaneous emergencies that were not concurrently presented during training sessions and for which they had no prior experience.
Safety issues and actions
Central to the ATSB’s investigation of transport safety matters is the early identification of safety issues. The ATSB expects relevant organisations will address all safety issues an investigation identifies. Depending on the level of risk of a safety issue, the extent of corrective action taken by the relevant organisation(s), or the desirability of directing a broad safety message to the aviation industry, the ATSB may issue a formal safety recommendation or safety advisory notice as part of the final report. All of the directly involved parties are invited to provide submissions to this draft report. As part of that process, each organisation is asked to communicate what safety actions, if any, they have carried out or are planning to carry out in relation to each safety issue relevant to their organisation. Descriptions of each safety issue, and any associated safety recommendations, are detailed below. Click the link to read the full safety issue description, including the issue status and any safety action/s taken. Safety issues and actions are updated on this website when safety issue owners provide further information concerning the implementation of safety action. |
Critical item
Safety issue number: AO-2020-064-S1-01
Safety issue description: Although the helicopter manufacturer’s instructions for continuation in service for the clutch shaft forward yoke specified that the condition of the yoke was to be inspected to verify that no cracks, corrosion, or fretting was present, it did not provide specific instructions for the method to be employed. The visual inspection that was employed increased the risk that a crack in that area may not be detected.
Safety action not associated with an identified safety issue
Whether or not the ATSB identifies safety issues in the course of an investigation, relevant organisations may proactively initiate safety action in order to reduce their safety risk. All of the directly involved parties are invited to provide submissions to this draft report. As part of that process, each organisation is asked to communicate what safety actions, if any, they have carried out to reduce the risk associated with this type of occurrences in the future. The ATSB has so far been advised of the following proactive safety action in response to this occurrence |
Safety advisory notice to operators of R44 helicopters
The ATSB advises operators of R44 helicopters to note the preliminary finding of this accident and to look for the presence of corrosion, fretting or cracking, which may not be visually obvious, during all inspections of the clutch shaft yoke. Any identified defects should be notified to both the ATSB and the Civil Aviation Safety Authority.
Additional safety action taken by CASA
CASA issued Airworthiness Bulletin AWB 63-010 Issue 1 to inform owners, registered operators, maintenance organisations and Licensed Aircraft Maintenance Engineers of a failure in a Robinson R44 drive train component (the yoke) that was found by the ATSB during investigation AO-2020-064 and that the ATSB has issued a Safety Notice AO-2020-064-SAN-014 to highlight the component failure.
A revision to the AWB (Issue 2) was issued by the CASA on 23 September 2021. Further to original references that signs of loose fasteners, corrosion or discolouration warrant further investigation, Issue 2 advised that further investigation may require the use of specialised inspection methods such as non-destructive testing (NDT). The manufacturer's maintenance data should be consulted and if lacking sufficient detail for the required inspection or method/s, then the manufacturer is to be contacted for the appropriate inspection data, or if a specialised inspection is required, then the inspection data will need to be generated and approved under civil aviation legislation. Further, any specialised inspections will need to be conducted using approved data by an appropriately authorised person.
Additional safety action taken by European Union Aviation Safety Agency (EASA)
Following the release of CASA AWB 63-010 Issue 1 dated 21 June 2021, EASA issued Safety Information Bulletin No. 2021-13 on 29 June 2021 advising owners and operators that EASA concurs with the AWB's recommendations and to ensure that owners and operators are aware of the recommendations.
Additional safety action taken by Federal Aviation Administration (FAA)
Following receipt of a report of a failed C907 yoke in the R44 main rotor drive system, the FAA issued a Special Airworthiness Information Bulletin (SAIB: AIR-22-08) to remind owners and operators of any Robinson R44 rotorcraft of the importance of adhering to existing inspection procedures in the applicable operating handbooks and maintenance manuals.
The SAIB advised of the presence of a fatigue crack near the bolt hole of the arm of the C907 yoke, and that an initial metallurgical examination found corrosion products and fretting damage on the surface near the fatigue crack. The yoke failure may have been caused by corrosion and/or improper hardware torque. Further, inadequate inspection and maintenance of all driveshaft yokes may result in undetected wear and/or corrosion that could lead to yoke failure and loss of main and tail rotor drive.
The FAA recommended that owners and operators of R22 and R44 series rotorcraft follow Robinson's published pre-flight inspection and periodic maintenance criteria regarding main and tail rotor driveshaft yokes in order to prevent future failures.
Glossary
FAA Federal Aviation Administration
CAA Civil Aviation Authority
GPS Global Positioning System
METAR Meteorological Terminal Air Report
POH Pilot Operating Handbook
RHC Robinson Helicopter Company
SAN Safety Advisory Notice
SDR Service Difficulty Report
TAF Terminal Aerodrome Forecast
Sources and submissions
Sources of information
The sources of information during the investigation included the:
- accident witnesses
- aircraft manufacturer
- Bureau of Meteorology
- Civil Aviation Safety Authority
- maintenance organisations for VH-HOB
- County Helicopters Pty Ltd
- photographs and videos taken on the day of the accident
- pilot of the accident flight
- recorded data from the DGPS unit on the aircraft.
References
Federal Aviation Administration (2019), Helicopter Flying Handbook, U.S. Department of Transportation, FAA-H-8083-21B
Under section 26 of the Transport Safety Investigation Act 2003, the ATSB may provide a draft report, on a confidential basis, to any person whom the ATSB considers appropriate. That section allows a person receiving a draft report to make submissions to the ATSB about the draft report.
A draft of this report was provided to the following directly involved parties:
- aircraft manufacturer
- Civil Aviation Safety Authority
- County Helicopters Pty Ltd
- pilot of the accident flight
- maintenance organisations for VH-HOB.
Submissions were received from:
- aircraft manufacturer
- Civil Aviation Safety Authority
The submissions were reviewed and, where considered appropriate, the text of the report was amended accordingly.
Purpose of safety investigationsThe objective of a safety investigation is to enhance transport safety. This is done through:
It is not a function of the ATSB to apportion blame or provide a means for determining liability. At the same time, an investigation report must include factual material of sufficient weight to support the analysis and findings. At all times the ATSB endeavours to balance the use of material that could imply adverse comment with the need to properly explain what happened, and why, in a fair and unbiased manner. The ATSB does not investigate for the purpose of taking administrative, regulatory or criminal action. TerminologyAn explanation of terminology used in ATSB investigation reports is available here. This includes terms such as occurrence, contributing factor, other factor that increased risk, and safety issue. Publishing informationReleased in accordance with section 25 of the Transport Safety Investigation Act 2003 Published by: Australian Transport Safety Bureau © Commonwealth of Australia 2022 Ownership of intellectual property rights in this publication Unless otherwise noted, copyright (and any other intellectual property rights, if any) in this report publication is owned by the Commonwealth of Australia. Creative Commons licence With the exception of the Coat of Arms, ATSB logo, and photos and graphics in which a third party holds copyright, this publication is licensed under a Creative Commons Attribution 3.0 Australia licence. Creative Commons Attribution 3.0 Australia Licence is a standard form licence agreement that allows you to copy, distribute, transmit and adapt this publication provided that you attribute the work. The ATSB’s preference is that you attribute this publication (and any material sourced from it) using the following wording: Source: Australian Transport Safety Bureau Copyright in material obtained from other agencies, private individuals or organisations, belongs to those agencies, individuals or organisations. Where you wish to use their material, you will need to contact them directly. |
[1] Central Daylight Time (CDT): Coordinated Universal Time (UTC) +10.5 hours
[2] METAR: a routine aerodrome weather report issued at routine times, hourly or half-hourly
[3] Cyclic: a primary helicopter flight control that is similar to an aircraft control column. Cyclic input tilts the main rotor disc, varying the attitude of the helicopter and hence the lateral direction.
[4] Collective: a primary helicopter flight control that simultaneously affects the pitch of all blades of a lifting rotor. Collective input is the main control for vertical velocity.
[5] Failure mechanism associated with high frequency vibration, flexing or rotation of machinery, typically at a rate of many times per second.
[6] Yoke flanges or arms: interchangeable terms used by the manufacturer to describe the connecting surfaces of the yoke
[7] Autorotation, also known as an autorotational descent, is a power off manoeuvre in which the engine is disengaged from the main rotor system and the rotor blades are driven solely by the upward flow of air through the main rotor.
[8] Differential GPS: an enhancement to global navigation satellite system (GNSS) systems. A differential GPS base station broadcasts a correction signal that allows differential GPS devices to provide sub-metre positional accuracy relative to the base. If the position of the base is precisely known, this allows for high absolute positional accuracy.
[9] SatLoc Bantam: a proprietary aerial application guidance system utilising differential GPS signals.