What happened
On 16 August 2020, a Robinson R22 Beta II helicopter, registered VH-YMU, was mustering cattle on a property about 44 km south of McArthur River Mine Airport, Northern Territory. The helicopter was operated by ENJAY Services, and the pilot was the sole occupant.
While hovering at a height of about 60 ft, the helicopter experienced a sudden loss of rotor drive. The helicopter rapidly lost height and collided with terrain. The pilot sustained serious injuries and the helicopter was substantially damaged.
What the ATSB found
The ATSB found evidence of fatigue cracking in the fanwheel outer support ring and in the welded region of 2 vanes of the fanwheel assembly. These fatigue cracks probably weakened the fanwheel structure sufficiently to result in in-flight break‑up of the fanwheel.
During this investigation, it was also found that there had been other instances where cracking had been identified in the welded regions of fanwheels. However, a search of the CASA Defect Report Service for R22 and R44 models identified only a single reported occurrence in 2013 for vane weld cracking.
The imbalance caused by the fanwheel break-up, likely led to the forward drive belt migrating from the drive sheaves. The remaining rear drive belt likely failed under the load exerted on it, when the helicopter impacted the ground, and the downward motion of the engine overloaded the drive belt to failure.
Due to the helicopter being in a 60 ft hover at the time of the drive belt failure, the pilot had limited options to respond to the emergency, resulting in a heavy landing and serious injuries to the pilot.
It was also identified that the details for the emergency locator transmitter had not been updated after the helicopter had been recently purchased by the operator. This led to a delay in the Joint Rescue Coordination Centre (JRCC) being able to confirm the accident. Fortunately, prompt assistance was provided to the pilot by other personnel involved in the muster.
Safety message
Cracking of Robinson fanwheels in the vane weldment, has been identified to occur in a limited number of the R22 fleet, however this was the first instance where the cracking had progressed sufficiently to permit an in-flight failure to occur. The circumstances of this accident are an important reminder for pilots and maintainers to pay particular attention to the installation, maintenance, and ongoing inspection of critical components of the Robinson R22 (and R44 – being a similar system) helicopter drive system.
The non-reporting of defects prevents the sharing of knowledge to the wider aviation community and identification of emerging issues. Defect reporting allows CASA to create a database, which is used to identify trends in design and maintenance reliability of aircraft systems and components and is a publicly accessible service. Defect reporting benefits the aviation industry such that data may be utilised to develop or review an Airworthiness Directive or Airworthiness Bulletin, which leads to long term improvement in design, manufacturing, and maintenance standards.
The investigation
Decisions regarding whether to conduct an investigation, and the scope of an investigation, are based on many factors, including the level of safety benefit likely to be obtained from an investigation. For this occurrence, a limited-scope investigation was conducted in order to produce a short investigation report and allow for greater industry awareness of findings that affect safety and potential learning opportunities. |
The occurrence
On 16 August 2020, a Robinson R22 Beta II helicopter, registered VH-YMU (YMU) and operated by ENJAY Services, was being utilised for cattle mustering operations on McArthur River Station, about 44 km south‑west of the McArthur River Mine Airport, Northern Territory. At about 0700 local time, the pilot departed to begin the mustering operation. At about 0730, another pilot operating a Robinson R44 joined the mustering activities. Both then worked together to move the cattle into the yards.
Sometime later, both helicopters flew to a fuel point. A hot fuel[1] was performed to quickly return to the cattle. The R44 pilot assisted the other pilot by refuelling YMU. During the refuel, the R44 pilot reportedly noticed a drive belt misalignment on YMU. During a discussion, the pilot of YMU commented that drive belt engagement[2] on previous starts had been normal and that the clutch warning light in the cockpit had not flickered[3] during the previous flight. Both pilots considered that the misalignment did not warrant shutting down the helicopter for further investigation and decided to complete an inspection of the drive system at the conclusion of the day’s mustering.
Both helicopters returned to the mustering task and at about 1140, YMU was moving cattle toward the stockyard at low level in a valley. The pilot of the R44 was manoeuvring about 100 ft higher and about 200 m away to the left of YMU, looking for other cattle and observing YMU muster the cattle.
While YMU was being hovered at about 60 ft above ground level, the R44 pilot saw a large plume of blue smoke at the rear of YMU and, recognising a problem, quickly alerted the pilot of YMU by radio. The R44 pilot then observed fragments burst from the cooling shroud area at the rear of the helicopter before YMU rapidly descended and impacted terrain (Figure 1 and Figure 2).
Figure 1: Damage to cooling fanwheel and missing shroud
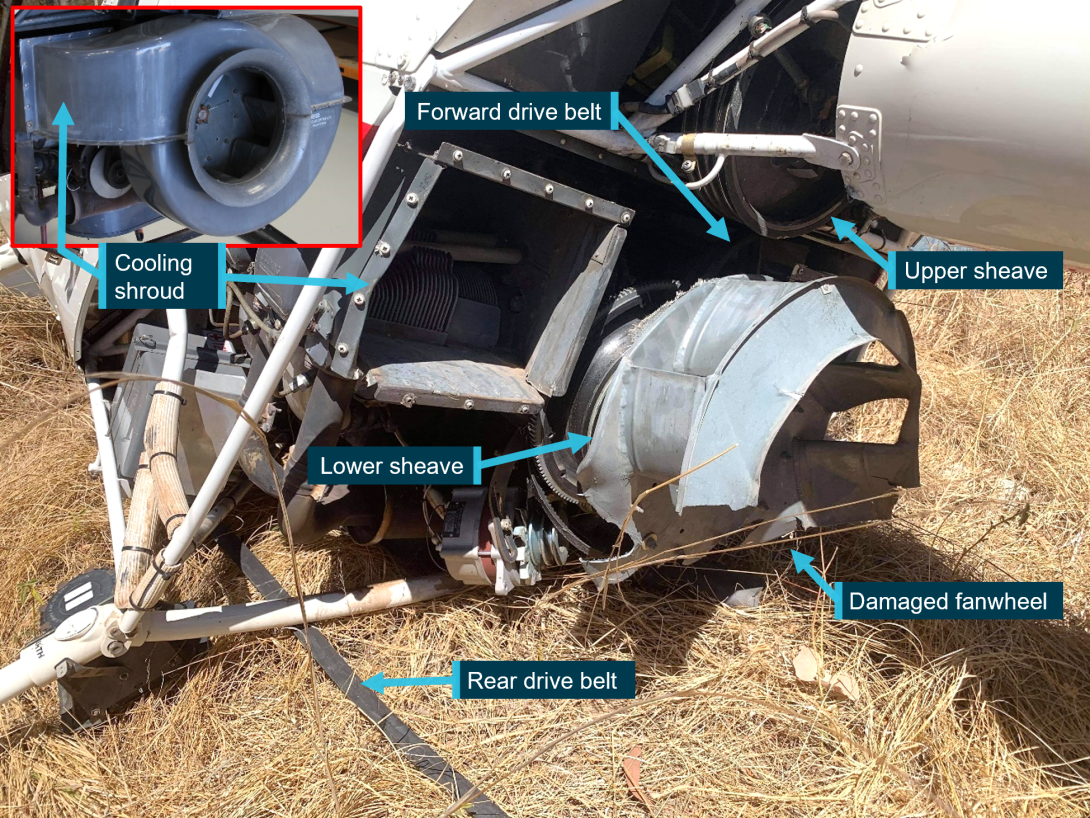
Source: ATSB and Operator, annotated by the ATSB
The pilot of YMU reported hearing a loud bang and loss of main rotor drive propulsion and recalled that there was limited time to react due to the low-level operations at the time. The pilot sustained serious back injuries and was heavily winded from the impact, however, was able to exit the helicopter unassisted. A station hand mustering on the ground, witnessed the accident and rendered first aid to the pilot.
Figure 2: VH-YMU accident site
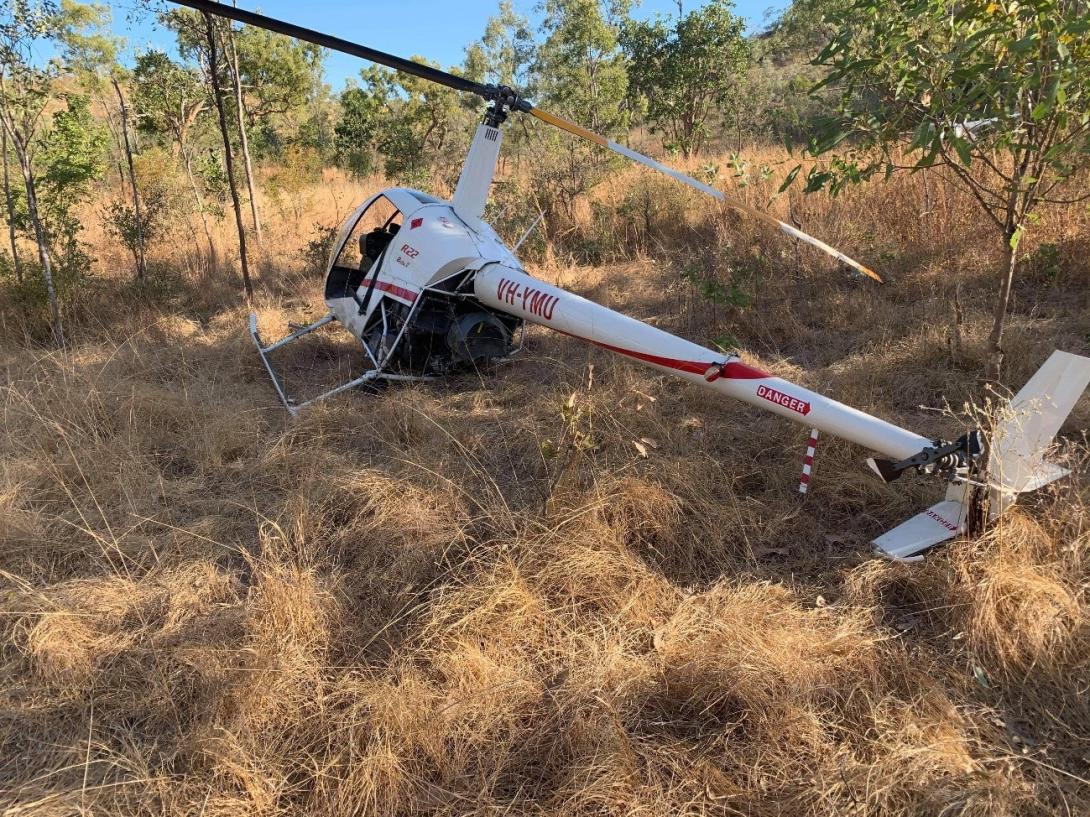
Source: Operator
Following the accident, the R44 pilot immediately diverted to pick up the station manager who was a short distance from the accident site, but unaware of the accident as they were on the other side of a hill with the main cattle herd. The R44 pilot returned to the accident site with the manager and first aid equipment. The pilot of YMU was transported in the R44 to the McArthur River Mine medical facility, and subsequently evacuated by aeroplane to Darwin.
The emergency locator transmitter activated during impact. The signal was detected by the Joint Rescue Coordination Centre (JRCC) in Canberra at 1209 Eastern Standard Time,[4] who then contacted the registered owner. However, due to a change of ownership, the registration details of YMU were not updated, which led to a delay in the accident confirmation and rescue effort by the JRCC.
Context
Pilot information
The pilot of VH-YMU (YMU) held a valid Commercial Pilot Licence (Helicopter) issued in May 2019, and a current Class 1 Aviation Medical Certificate. They held approvals for low-level operations and mustering and had about 300 hours flight time in helicopter mustering operations. They had worked for the operator for about 18 months.
Helicopter information
The Robinson R22 (R22) is a 2‑seat, single‑engine helicopter predominately used for pilot training, private use and in utility roles. It is primarily all‑metal construction with a 2-blade main and tail rotor system and is powered by a 4-cylinder Lycoming piston engine. YMU was manufactured in the United States in 2012 and registered in Australia in the same year. YMU changed ownership in February 2020, when it was acquired by the operator.
A routine 100-hour service was conducted about 42 hours prior to the accident, on 13 July 2020. Additional work also performed, included an adjustment of the engine height and sheave alignment. This involved shimming the engine due to engine mounts sagging. The shimming procedure raised the engine to obtain optimal alignment in the sheaves. The rotor drive belts were last replaced at 2,850.2 hours, about 275 hours prior to the accident. The maintenance release indicated that YMU had accumulated 3,125.2 hours in service on the morning of the accident.
Rotor drive system
The rotor drive system on the R22 helicopter uses two reinforced rubber drive belts. The drive belts are double-banded and fitted to multi-grooved sheaves. The upper sheave is mounted on a free‑wheel clutch shaft that drives the main rotor gearbox and the tail rotor driveshaft. The lower sheave is attached directly to the engine crankshaft.
The upper sheave is moved relative to the lower sheave by means of an electric clutch actuator, thereby controlling the tension on the drive belts. This allows the engine to be started unloaded (drive belts slack) without the drag of the rotor system, and then tensioned to allow engine power to be transmitted to the rotor drive (Figure 3).
Figure 3: Diagram of the Robinson R22 rotor drive system
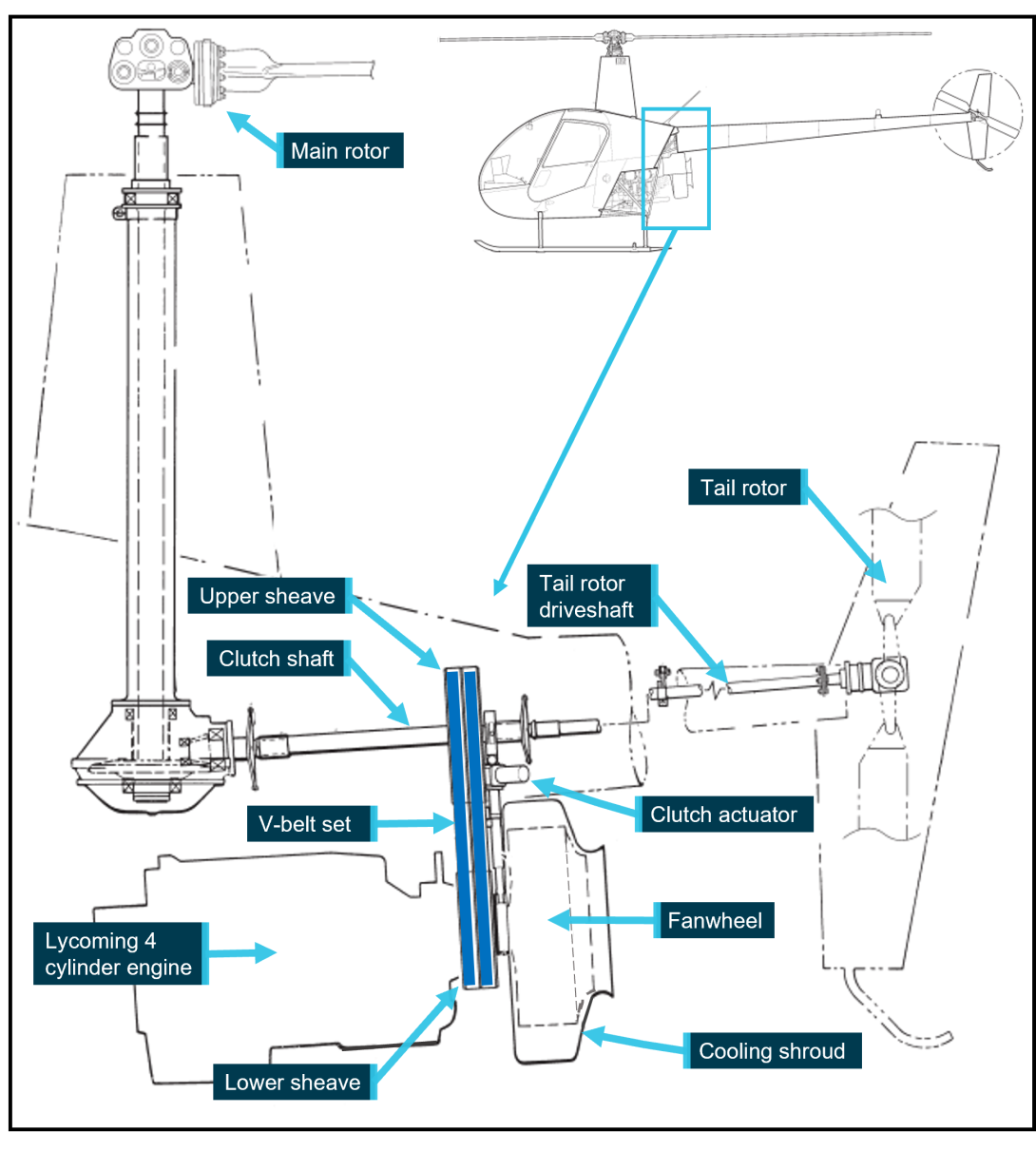
Source: Robinson Helicopter Company, annotated by the ATSB
Robinson Helicopter Company (RHC) stated in the pilot’s operating handbook that, after engaging the clutch actuator switch, the rotors should be turning within 5 seconds. RHC Safety Notice SN‑33 also stated that if the rotors turned during the start sequence, or the time was greater than 5 seconds, it indicated that the rotor drive belts adjustment was not correct. In both scenarios, maintenance action was required to rectify the problem.
The actuator may also operate momentarily during flight as the drive belts warm up or stretch slightly. A warning light illuminates on the instrument panel to indicate any movement of the actuator and a flicker of the light during operation is considered normal. On the day of the accident, the pilot did not recall any abnormal actuator operation for the engagement of the drive belts or of a light illuminating prior to the accident.
Fanwheel
The fanwheel utilised on the R22 is a commercial product, modified by RHC. Its purpose is to direct cooling air onto the engine. The fanwheel is constructed of steel, comprising 8 cooling vanes which are welded to the rear plate (on the engine side) and a support ring at the outer side. The assembly mounts onto the fan shaft, aft of the lower sheave, and is enclosed in a fibreglass cooling shroud.
There have been several reported cases of fanwheel cracking at the bolt holes at the central hub attaching hardware on the rear plate. The fanwheel on YMU did not have any evidence of cracking from these locations. A search of the CASA Defect Reporting Service did not reveal any reports of fatigue cracking or structural failures from the vane welds of Robinson R22 (or R44) fanwheels, despite evidence of several other fanwheels being removed from service due to cracking in the welded areas. Photos of these fanwheels were provided to the ATSB during this investigation. The manufacturer also stated that fanwheels containing cracks in the vane welds had been returned to the factory.
Although there was knowledge in the Robinson community (from maintainers and operators) that cracking does occur in the welded regions of fanwheel vanes, there has been no defect reports submitted to CASA which would raise awareness of this issue. Defect reporting is an essential of aircraft operation and maintenance and the requirement is covered in Part 4B of the Civil Aviation Regulations and Advisory Circular AC 20-06v1.1.
Robinson reported to the ATSB that about 2% of R22 (and 3% of R44) fanwheels returned to Robinson fail inspection due to fatigue cracking at the vane welds. These fanwheels are removed from service and scrapped. The rejected fanwheels were identified by Robinson as having been in service for at least 2 overhauls (at least 4,400 hours, time in service).
Robinson have changed the maintenance manual requirement, which now states that fanwheels are to be replaced at the 2,200-hour inspection.[5] These are supplied as a new or factory overhauled item and are part of the 2,200-hour overhaul kit supplied by Robinson. The fanwheel that was installed on YMU had been replaced at the 2,200-hour inspection and had accumulated about 1,000 hours since installation.
The R22 maintenance manual states that a dynamic balance must be performed each time the fanwheel is fitted to the helicopter. This ensures the balance is maintained within acceptable limits to prevent damage to the fanwheel and the helicopter drivetrain. The most recent fanwheel balance on YMU had been carried out 204.5 hours prior to the accident.
Sheave alignment
In accordance with RHC maintenance requirements, sheave alignment was to be checked each 100 flight hours or 12-month period, and any time that the drive belts were replaced. The specific procedures were outlined in the R22 maintenance manual. The engine height, clutch shaft angle and throttle correlation rigging was also checked to ensure all elements of the drive system were in alignment. RHC released Service Letter SL-35 in 1990 highlighting the importance of ensuring that sheave alignment is maintained within acceptable limits. This was released to highlight the correct tooling and procedure to be used when carrying out sheave alignment.
The Civil Aviation Safety Authority (CASA) released Airworthiness Bulletin AWB 63-006 in 2009, which emphasised the need to adhere to all current RHC data. It noted that engine height and sheave alignment was a critical element of the drive system. RHC testing identified that most drive belt failures are caused by misalignment of the drive belts on the sheaves.
Damage to the helicopter
A post-accident inspection of the helicopter was completed by the operator and the R44 pilot at the accident site the following day. The operator reported that the:
- forward drive belt was displaced forward from its normal operating position on the sheaves, and was tangled around the lower sheave and ring gear, and the upper sheave on the clutch shaft
- rear drive belt had split and was laying on the ground under the helicopter
- clutch actuator and engine cooling shroud had broken free from the rear of the engine
- tail rotor control bell crank had fractured, and a segment was in the tail boom
- metal cooling fanwheel was damaged, with 2 vane segments found away from the main wreckage.
Additionally, the skid landing gear was splayed outward, and the pilot seat base had collapsed mainly on the right rear side. The forward tail rotor drive flex coupling was significantly damaged, most likely due to contact from the failing fanwheel or the tail cone attachment lower frame. The tail rotor blades had fractured, and the lower vertical stabiliser was bent to the left. Both main rotor blades had minor impact damage, most likely due to contact with the surrounding trees.
Operator-supplied images of the collapsed pilot seat structure of YMU also showed several items stored under the seat. While not evident that the equipment had filled the area, large amounts of equipment stored under the seat can lead to occupant injuries in the event of an accident, as the collapsible space may be compromised. In the case of this accident, there was sufficient collapsible space to prevent further injury to the pilot during the impact sequence.
Component examination
The drive belt set, fanwheel, tail rotor blades, clutch actuator and drive sheaves were examined at the ATSB’s technical facilities in Canberra (Appendix). The ATSB’s examination found that the forward drive belt had disengaged and become entangled in the rotating drive train components and the rear drive belt had stretched before failing in overload. The upper and lower sheaves had significant rubber deposits on the forward surfaces due to drive belt skidding. No indication of abnormal wear or damage was identified on the painted surfaces within the sheave grooves from a drive belt anomaly.
Measurements showed that the clutch actuator had not extended to is full travel limit. Additionally, the actuator had sustained impact damage and had fractured in overstress from its mount location.
The metallurgical examination of the fanwheel identified evidence of pre-existing fatigue cracks in the welded region of 2 vanes, and in the outer support ring structure. Two segments of fanwheel had liberated from the assembly. One segment had 1 vane with evidence of severe metal-to-metal contact during the rotation of the fanwheel, and a black witness mark, which was most likely rubber transfer due to contact with the drive belt/s. The other was a segment of 2 vanes with wood fibres entrapped in the structure.
The fibreglass cooling shroud showed evidence of slice and penetration damage and had been separated from the rear of the engine in flight. This damage was most likely a result of fanwheel segments separating from the cooling fan while the fanwheel was rotating.
Both tail rotor blades had fractured at the root with evidence of rotation at the time of impact.
Emergency locator transmitter
The helicopter was equipped with a Kannard 406 AF emergency locator transmitter (ELT). Impact forces automatically activated the ELT, which then transmitted a signal on the 406 MHz frequency. This transmission contains digital information, including a unique identifier, enabling the search and rescue authority to contact the registered owner of the beacon to determine whether the activation was a false alarm or genuine. At the time of writing, the 406 MHz ELT was required to be registered with the Australian Maritime Safety Authority.
The signal relating to this accident was received by the Joint Rescue Coordination Centre (JRCC) in Canberra, who then attempted to contact the registered owner. They advised that the aircraft had been sold and that the details had not been updated since the change of ownership in February 2020. After being provided contact details for the new owner, JRCC then attempted unsuccessfully to contact them. As such, the JRCC was unable to confirm the validity of the ELT activation.
JRCC then contacted the Northern Territory Police. The police point of contact in the area was, coincidentally, the R44 pilot who was able to confirm the accident occurrence to the police about one hour after the ELT was first detected. The aircraft operator switched the ELT off on the following day when they attended the site. While not affecting the response to this accident, more generally it is important that contact details of the registered owner are up to date to ensure a timely search and rescue.
Low-level operations
A successful forced landing following a complete drive train failure requires a sufficient combination of height (potential energy) and airspeed (kinetic energy). A description of sufficient available energy following a sudden loss of power is provided in the height/velocity (H/V) diagram (Figure 4). While most mustering operations take place at a height and airspeed suitable for forced landings, there is occasional need to operate within the shaded avoid area of the H/V diagram.
When operating within the shaded area, pilots are exposed to the risk of a high energy impact in the event of a sudden loss of power to the rotor system. However, in practice this risk must be balanced with other risks associated with low‑level operation such as obstacle collision (e.g., trees and wires) and brown out from dust. There is also the consideration of being able to complete a task efficiently. At the time of rotor drive belt failure, the pilot of VH-YMU was operating inside the avoid area of the H/V diagram.
Figure 4: Robinson R22 height/velocity diagram
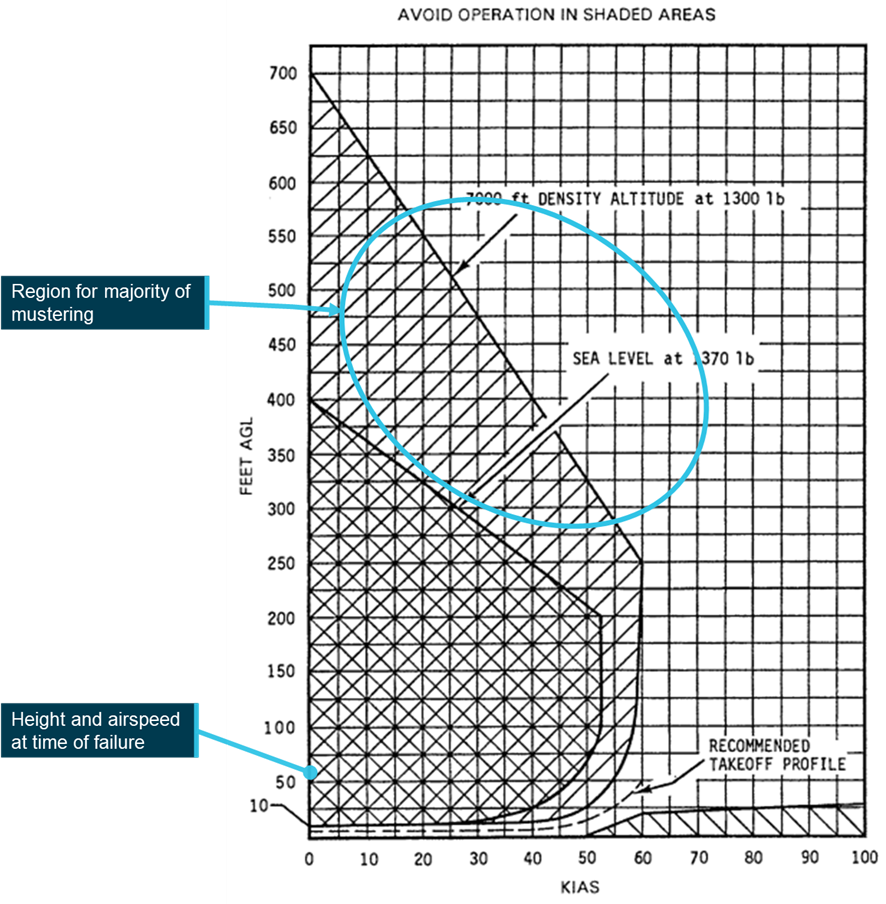
Source: Robinson Helicopter Company (annotated by the ATSB)
Hot fuelling
While there was no procedure for hot fuelling in the operators Operations Manual as required in Civil Aviation Order 20.10[6] (which was in force at the time of the accident), it is common in aerial mustering operations. In a single person operation, to hot fuel the aircraft, the pilot must leave the controls. This increases the risk of loss of control of the helicopter and has resulted in aircraft unintentionally becoming airborne, leading to injury of bystanders and damage to the helicopter. The Robinson R22 pilot’s operating handbook (POH) cautions against leaving flight controls unattended. Additionally, friction locks have been stated by CASA as unsuitable for use to secure unattended controls.
CAO 20.10 required hot fuelling be carried out safely and must have regard to the helicopter flight manual. Cautions written in a POH are binding requirements under Civil Aviation Safety Regulation (CASR) 138.210. This was also the case under subregulation 138 (1) of the Civil Aviation Regulations 1988. The Robinson POH caution would have prevented hot fuelling without the pilot on board the rotorcraft.
In addition, piston engine fuel possesses a higher flammability than turbine fuels, which can also contribute to a potential fire risk during hot fuelling operations, particularly when the fuel tanks are located above the engine.
Information relating to hot fuelling of an aircraft is contained in CASR 91.500 and 91.505 and the CASR Part 91 Plain English Guide. Further guidance can be found in the Visual Flight Rules Guide.
Safety analysis
Rotor drive system failure
Fanwheel failure
It could not be determined why the fanwheel assembly began to break up during the flight, mainly due to the limited amount of cracking evident within the fanwheel structure itself. The presence of fatigue cracking in the welded regions from the fanwheel vanes and on the outer support ring, were considered a pre-existing defect. There was no metallurgical evidence of continuous/intermittent crack growth from that region of damage to indicate that a period of progressive crack growth had occurred to the extent that the structural integrity of the fanwheel should have been affected.
Drive belt failure
Examination of the drive belts and photographs provided to the ATSB by the operator, established that the forward drive belt dislodged and moved forward, entangling in the rotating components of the engine and rotor drive. This was further supported by the witness account from the pilot of the R44, who observed smoke from the rear of VH-YMU moments before the accident. The forward drive belt showed signs of being heated and abraded by frictional contact with the upper sheave and clutch shaft. It is likely that the remaining rear drive belt failed in tensile overstress from the downward motion of the engine during the ground collision. This is supported by the short time from fanwheel failure to ground impact and the inability of the clutch actuator to have travelled to its full extension to cause the drive belt to fail through overstretching.
As the circumference and cross-sectional profile of the forward belt were consistent with a new Revision‑Z belt, dislodgement due to a belt defect was considered unlikely. The examination of the upper and lower sheaves showed that the sheave grooves did not exhibit any abnormal wear or damage to the painted surfaces, which also supported positive belt engagement.
Summary
The partial fragmentation of the fanwheel during flight resulted in a sudden load imbalance on the rotor drive system. Fragments from the fanwheel had evidence of contacting the rotor system drive belt/s, however it could not be determined if this affected the forward drive belt’s engagement. The more probable scenario was that the mass imbalance that resulted from the fanwheel fragmentation, probably led to the forward drive belt being disengaged from the drive sheaves. The subsequent load placed on the rear drive belt from the engine weight at ground impact likely led to it failing in overload.
Low-level operations
Mustering operations involve manoeuvring at low-level and at varying airspeeds. Such operations increase the risk associated with a loss of engine power. In this accident, the operational requirement to operate at about 60 ft above ground level did not allow sufficient time for the pilot to react to the drive belt failure or provide sufficient aircraft energy for an autorotation to cushion the landing.
The high hover provided limited opportunity to conduct a safe forced landing, however the pilot, with the remaining energy in the rotor system, was able to manoeuvre to a clear area and land the helicopter in an upright attitude, lessening the injuries sustained.
Emergency locator transmitter
Activation of the emergency locator transmitter (ELT) on impact and transmission of the 406 MHz signal was detected by the Joint Rescue Coordination Centre, although incorrect contact details delayed confirmation of the accident.
Fortunately, this accident was reacted to quickly, due to the mustering being performed by 2 helicopters operating in close proximity and nearby ground crew. In a circumstance where an aircraft may be operating alone, any delayed search and rescue (SAR) response has the potential to be a critical factor in occupant survival.
ELT registration is entered onto a database that is always accessible to SAR authorities. Up to date contact information is vital in deploying SAR resources and medical assistance effectively when an activation is detected.
Defect reporting
There is reportedly an awareness within operators of Robinson helicopters that cracking can occur at the welded regions of the cooling fanwheel, however this is not reflected in the CASA Defect Reporting Service data. Reporting of in-service defects, whether identified during operation or maintenance, must be reported to CASA via the online defect reporting service. This ensures a database can be maintained to assist in identifying reliability of aircraft components and systems which benefits the wider aviation community.
Additionally, feedback provided to the manufacturer permits awareness of defects to be identified and investigated, and system improvements to occur should it be required. This ensures that aircraft component reliability and safety are maintained at optimum levels.
Findings
ATSB investigation report findings focus on safety factors (that is, events and conditions that increase risk). Safety factors include ‘contributing factors’ and ‘other factors that increased risk’ (that is, factors that did not meet the definition of a contributing factor for this occurrence but were still considered important to include in the report for the purpose of increasing awareness and enhancing safety). In addition ‘other findings’ may be included to provide important information about topics other than safety factors. These findings should not be read as apportioning blame or liability to any particular organisation or individual. |
From the evidence available, the following findings are made with respect to the rotor drive system failure and collision with terrain, involving a Robinson R22 Beta II, VH-YMU, 44 km south of McArthur River Mine Airport, Northern Territory on 16 August 2020.
Contributing factors
- It is likely that fatigue cracks in the vane welds and outer support ring of the fanwheel reduced its structural integrity, leading to an in-flight fracture and release of fanwheel segments.
- The forward drive belt migrated from the rotor system drive sheaves, probably due to the resulting drivetrain imbalance from the fanwheel failure. The loads exerted on the rear belt due to movement of the engine weight during impact likely led to its subsequent failure.
- While operating at low-level during mustering operations, the pilot had limited opportunity to arrest the descent before impacting terrain once rotor drive was lost.
Other factors that increased risk
- The helicopter had recently changed ownership, but the emergency locator transmitter registration had not been transferred to the new owner. This delayed confirmation of the accident by the Joint Rescue Coordination Centre.
- The apparent non-reporting of defects associated with the cooling fanwheel increased the risk that any associated safety issue would not be identified.
Sources and submissions
Sources of information
The sources of information during the investigation included the:
- pilot of VH-YMU
- operator/chief pilot
- maintenance organisation for VH-YMU
- accident witness
- Robinson Helicopter Company
- Australian Maritime Safety Authority
- Civil Aviation Safety Authority.
References
Australian Government 2013, AI-2009-038, Reliability of the Robinson R22 helicopter belt drive system, Australian Transport Safety Bureau, Canberra, ACT, viewed 8 November 2021, <Reliability of the Robinson R22 helicopter belt drive system (atsb.gov.au)>.
Australian Maritime Safety Authority [current], Beacons and MMSI Register, accessed 14 February 2023, <Public - Home - 406MHz Distress Beacon and MMSI Register (amsa.gov.au)>.
Civil Aviation Safety Authority Briefing 2020 Flight Safety Australia -The challenge for aerial mustering [Online video] Available at: https://www.youtube.com/watch?v=hiViOeqZO_o Accessed:[4 Nov 2021]
Civil Aviation Safety Authority 2015, Sector Risk Profile for the aerial mustering sector, accessed 8 November 2021, < Sector Risk Profile for the aerial mustering sector (casa.gov.au)>.
Civil Aviation Safety Authority 2021, CASR Part 91, General Operating and Flight Rules, Plain English Guide, accessed 14 February 2023. < Part 91 plain English guide version 2.0 (casa.gov.au)>.
Civil Aviation Safety Authority 2021, Part 4B of CAR Defect reporting, accessed 14 February 2023, < Part 4B of CAR Defect reporting | Civil Aviation Safety Authority (casa.gov.au)>.
Civil Aviation Safety Authority 2022, Advisory Circular AC 20-06 v1.1, accessed 14 February 2023, < AC 20-06 v1.1 - Defect reporting (casa.gov.au)>.
Robinson Helicopter Corporation 2020, R22 Pilot’s Operating Handbook, section 4, p.4-7 and section 10, p.27.
Robinson Helicopter Corporation 2020, R22 Pilot’s Operating Handbook, section 5, p.5-11.
Robinson Helicopter Corporation 2018, R22 Maintenance Manual, chapter 7, pp.7.20-7.22.
Submissions
Under section 26 of the Transport Safety Investigation Act 2003, the ATSB may provide a draft report, on a confidential basis, to any person whom the ATSB considers appropriate. That section allows a person receiving a draft report to make submissions to the ATSB about the draft report.
An initial draft of this report was provided to the following directly involved parties:
- the pilot of VH-YMU
- the pilot of the R44
- the operator
- the maintenance provider
- Robinson Helicopter Company
- the Civil Aviation Safety Authority.
Submissions on that draft were received from the:
- operator
- maintenance provider
- Robinson Helicopter Company
- Civil Aviation Safety Authority.
The submissions were reviewed and resulted in significant change to the initial draft report. As such, this second draft report was provided to the above directly involved parties. Submissions on the second draft report were received from the:
- operator
- Robinson Helicopter Company
- the Civil Aviation Safety Authority.
The submissions were reviewed and, where considered appropriate, the text of the report was amended accordingly.
Appendix
Component examination
The helicopter wreckage was transported to a maintenance facility where sections of the helicopter drive system were subsequently removed and sent to the ATSB’s technical facilities in Canberra for detailed examination.
Drive belts
That examination identified that the drive belts fitted to YMU were part number A190-2, Revision‑Z, and had been in service for about 275 hours. The examination and review of the on‑site imagery identified that during operation, the forward drive belt had dislodged and shifted out of position from the upper and lower sheaves.
The forward drive belt had sustained consequential damage from contact with the rotating drive system components, as evidenced by abraded rubber deposits on the forward face of the upper sheave and on the clutch shaft. Measurement of the rear drive belt identified that it had a 25 mm greater overall circumference than the forward drive belt, indicating that the rear drive belt had stretched during the ground impact and then failed in tensile overstress (Figure 5). The circumference of the forward drive belt was consistent with that of a new Revision‑Z belt and the cross-sectional profile of both belts did not show any evidence of excessive wear.
Figure 5: Drive belt damage
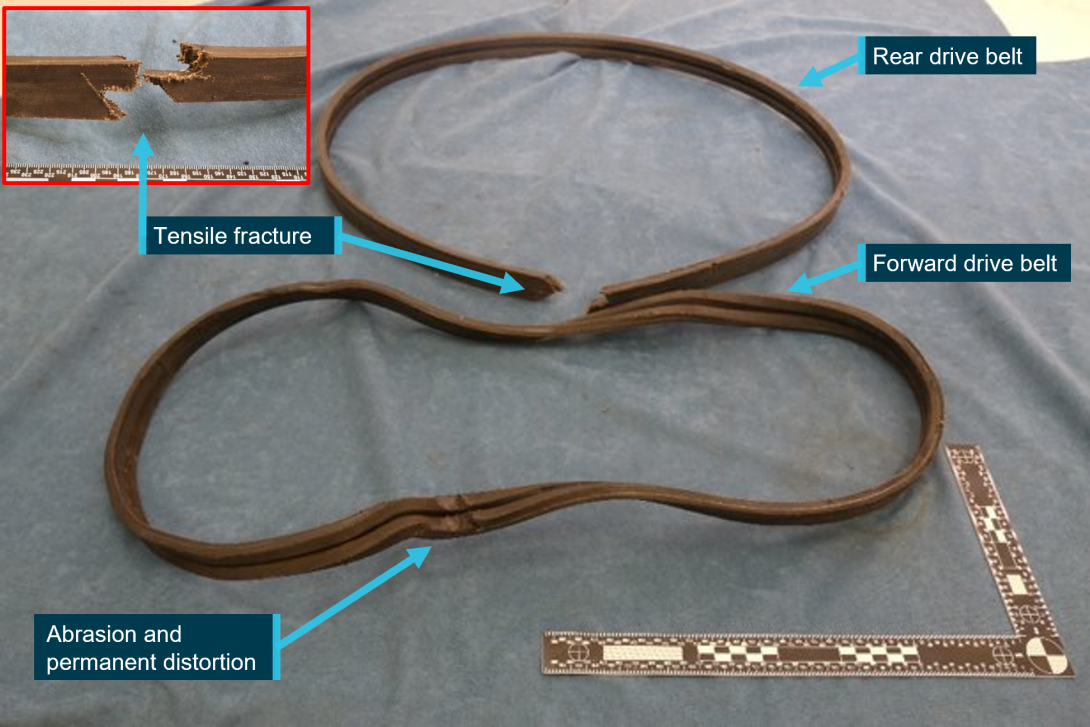
Source: ATSB
Measurement of the clutch actuator identified that it had not reached its full extension, indicating that the period from complete drive train failure to ground impact was likely to have been rapid. No abnormal wear to the paint within the sheave grooves had occurred. Some localised chipping of the aluminised coating had occurred, however that damage was likely produced during the accident sequence.
Tail rotor blades
Examination of the tail rotor blades showed that each had fractured in a uniform, almost identical manner, close to the blade attachment to the hub. Bending and deformation of the skin surfaces surrounding the fracture points was against the direction of rotation. This indicated that the tail rotor had been rotating at the time of the failure, most likely while being driven by the residual rotational force of the rotor system.
Fanwheel
Examination of the fanwheel identified that it had sustained significant disruption with 3 of the cooling vanes and associated rear support ring separated from the main structure. The liberated sections of fanwheel were comprised of a single vane ring and another comprising two vane rings. The fanwheel had sustained overall deformation, off axis bending with twisting and buckling evident throughout the structure. Notably, one of the liberated vane segments displayed considerable sliding contact damage.
The ATSBs metallurgical examination identified the presence of discrete pre-existing fatigue cracks on the fracture surfaces of the fanwheel where the cooling vanes had been welded. The formation of corrosion product on some of those crack surfaces indicated that those fatigue cracks had been present for a significant period. The fanwheel fracture surfaces, beyond the regions of fatigue, showed evidence of gross tearing that was consistent with overstress of the structure.
A detailed examination of the fanwheel fracture surfaces identified regions of fatigue cracking located on the weldment of the fan vanes. These were located at the rear of one vane (Region 5) and forward of the next vane (Region 3), where the vane was welded to the fanwheel rear plate. The fatigue cracks were measured at approximately 8 and 12 mm, respectively. The vane section containing the 12 mm crack had separated from the fanwheel along with another vane and displayed rapid ductile tensile tearing of the fracture surface (Figure 6).
Figure 6: Fanwheel fatigue cracking
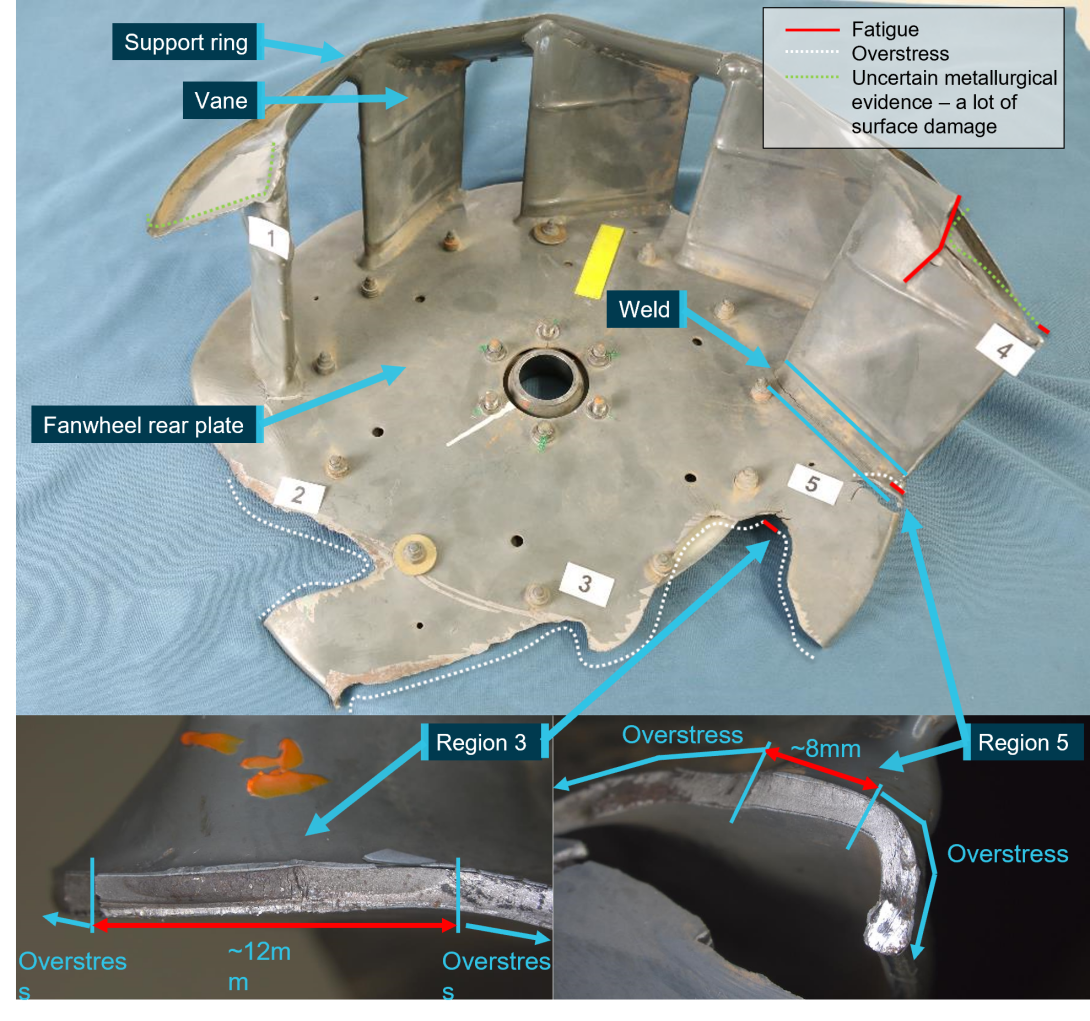
Source: ATSB
The vane support ring also had an area of fatigue cracking (Region 4) measuring approximately 45 mm. There was a degree of corrosion formation on the surfaces that suggested the cracking had been there for a significant period. There was insufficient metallurgical evidence on the fracture surfaces of the vane support ring to conclude definitively whether this region was damaged by fatigue that then could have led to a structural weakening of the fanwheel.
When considering the hypothesis for an in-flight break-up of the fanwheel to have occurred, ATSB’s examination of the single vane that had released from the fanwheel showed extensive rotational contact and scoring damage from metal-to-metal contact. That damage conflicted with the metallurgical evidence and was an indicator of a potential in-flight release and subsequent contact of that part with nearby rotating drivetrain componentry.
The larger segment of the fanwheel that had also released (containing the two vanes) was extensively deformed and contained entrapped wood fibres that was consistent with that portion striking a tree. There was an absence of wood fibres on all other parts of the fanwheel. It is likely that this section of fanwheel contacted a tree after it had broken from the fanwheel, prior to ground impact (Figure 7).
Figure 7: Fragmented cooling fanwheel and liberated fragments: a vane section sustained severe metal-to-metal contact and a lager section contained entrapped wood fibres
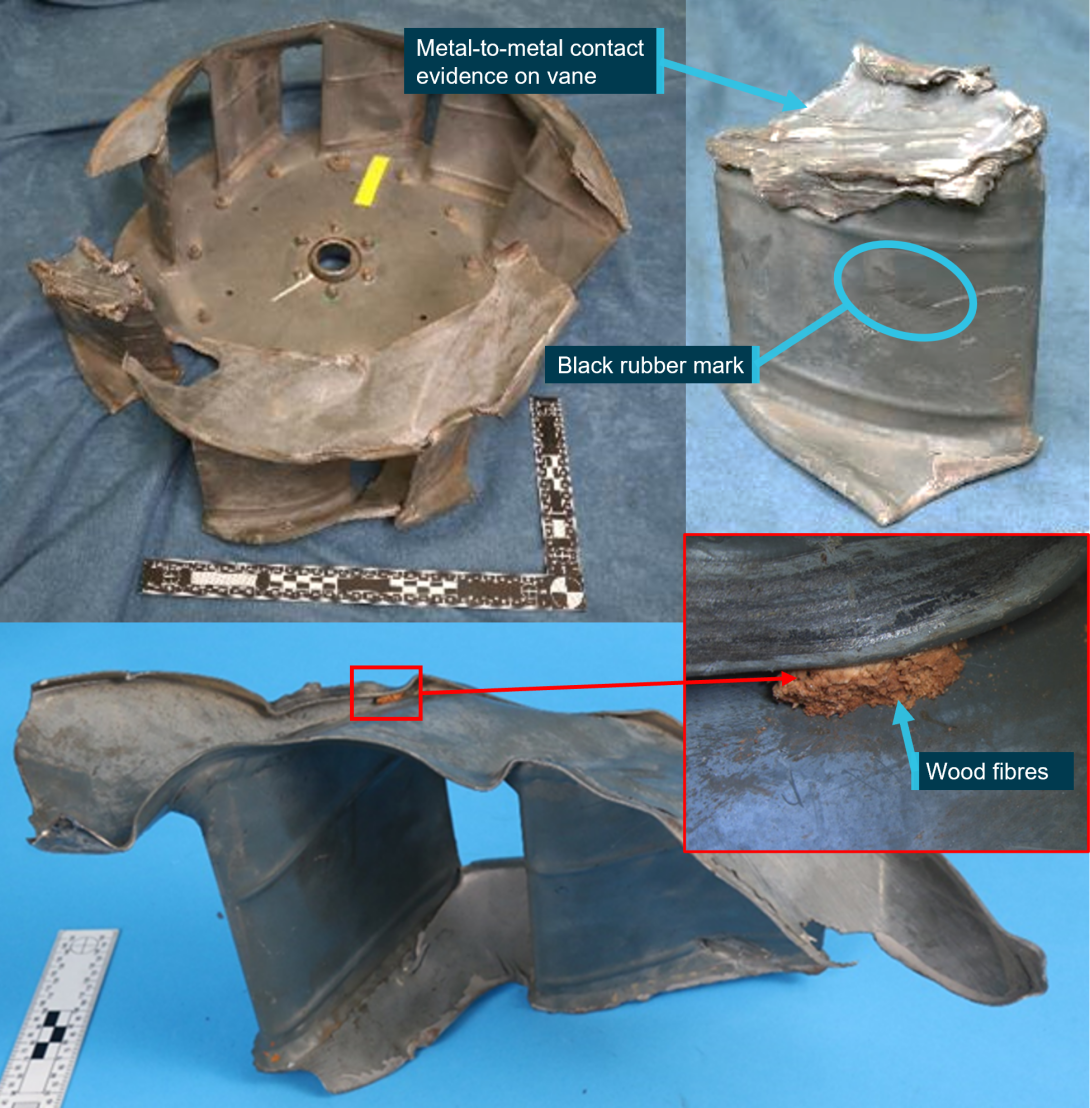
Source: ATSB
Purpose of safety investigationsThe objective of a safety investigation is to enhance transport safety. This is done through:
It is not a function of the ATSB to apportion blame or provide a means for determining liability. At the same time, an investigation report must include factual material of sufficient weight to support the analysis and findings. At all times the ATSB endeavours to balance the use of material that could imply adverse comment with the need to properly explain what happened, and why, in a fair and unbiased manner. The ATSB does not investigate for the purpose of taking administrative, regulatory or criminal action. TerminologyAn explanation of terminology used in ATSB investigation reports is available here. This includes terms such as occurrence, contributing factor, other factor that increased risk, and safety issue. Publishing informationReleased in accordance with section 25 of the Transport Safety Investigation Act 2003 Published by: Australian Transport Safety Bureau © Commonwealth of Australia 2023 Ownership of intellectual property rights in this publication Unless otherwise noted, copyright (and any other intellectual property rights, if any) in this report publication is owned by the Commonwealth of Australia. Creative Commons licence With the exception of the Coat of Arms, ATSB logo, and photos and graphics in which a third party holds copyright, this publication is licensed under a Creative Commons Attribution 3.0 Australia licence. Creative Commons Attribution 3.0 Australia Licence is a standard form licence agreement that allows you to copy, distribute, transmit and adapt this publication provided that you attribute the work. The ATSB’s preference is that you attribute this publication (and any material sourced from it) using the following wording: Source: Australian Transport Safety Bureau Copyright in material obtained from other agencies, private individuals or organisations, belongs to those agencies, individuals or organisations. Where you wish to use their material, you will need to contact them directly. |
[1] Hot fuelling means the refuelling of a helicopter with its engine or engines running.
[2] After engagement of the clutch actuator, the pilot must ensure the rotors turn within 5 seconds, ensuring correct system adjustment and drive belt stretch is not excessive.
[3] The presence of the clutch light flickering indicates the clutch is moving to take up drive belt looseness in operation.
[4] Eastern Standard Time: Coordinated Universal Time (UTC) + 10 hours.
[5] The overhaul of the complete helicopter is carried out each 2,200 hours or 12 years, time-in-service of the helicopter.
[6] Legislation for hot fuelling changed on 2 December 2021, now covered under Civil Aviation Safety Regulation CASR 138.300.