On 19 December 2004, a Boeing Company 737-86N aircraft, registered VH-VOH, was being operated on a scheduled passenger flight from Melbourne, Victoria to Canberra, ACT. At about 1655 Eastern Daylight-saving Time, while landing on runway 35, the right inboard main landing gear tyre failed.
In December 2004, the Australian Transport Safety Bureau (ATSB) noted an increase in the rate of tyre failures on Boeing 737 aircraft in Australia. It was noted that all of the failed tyres were at retread level (the number of times it had been retreaded) 4 and 5. The ATSB investigated the VH-VOH tyre failure in conjunction with these other recent failures.
Examination by the ATSB and the tyre manufacturer found that all the tyres had failed by fatigue in the sidewall. That fatigue was a result of cyclic flexing of the sidewall and was possibly present to some degree, but not detected, at the last retread.
Aircraft tyres of this type had several operational measures to prevent premature failure. Those included non-destructive inspection during the retread process, inflation pressure maintenance, and aircraft weight and speed limitations. The ATSB found that changes could be made by the aircraft operator and retread facility to improve the pressure maintenance and inspections during retread.
As a result of this investigation, safety improvements have been made by the aircraft manufacturer, aircraft operator and tyre retread facility to improve the life and reliability of the retreaded tyres. The United States Federal Aviation Administration is reviewing the certification requirements for the tyres and retread packages to include improved reliability programs.
History of the flight
On 19 December 2004, a Boeing Company 737-86N aircraft, registered VH-VOH, was being operated on a scheduled passenger flight from Melbourne, Victoria to Canberra, ACT. At about 1655 Eastern Daylight-saving Time, while landing on runway 35, the right inboard (No. 3) main landing gear tyre failed. The aerodrome controller reported hearing a loud bang, then a piece of rubber was seen 'flying from under the aircraft'. The controller advised the crew that the right inboard tyre had failed. The crew completed the landing roll and stopped the aircraft on the adjacent taxiway.
The airport Rescue and Fire Fighting Service (RFFS) attended the aircraft and confirmed that the other three tyres appeared to be undamaged. The crew then elected to taxi the aircraft to the terminal with the RFFS following. Approximately 20 pieces of rubber ranging in size from several centimetres to over a metre and a half in length were subsequently recovered from the runway.
The Australian Transport Safety Bureau (ATSB) attended the scene to inspect the damage to the tyre and aircraft. The ATSB retained the pieces of rubber for further examination. The operator's maintenance facility removed the tyre from the wheel rim for later examination by the ATSB.
Damage to aircraft
The aircraft structure sustained minor damage, which consisted of several dents in the lower surface of the right wing and flap, and deformation and cracking of a bracket in the right wheel well. A hydraulic line running through the wheel well also sustained a small dent.
The number 3 tyre had shed a significant portion of the tread and had a diagonal tear through the casing1 (Figure 1). The diagonal tear ran continuously from one sidewall to the other. There was also scuffing running circumferentially around the shoulders of the tyre.
Figure 1: Failed number 3 tyre
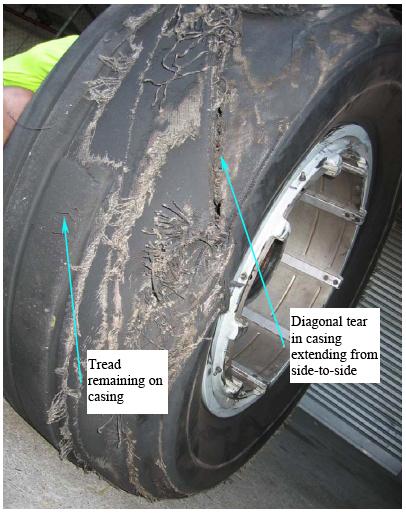
Aircraft operation
A review of the recorded data from the flight indicated that the landing was within the operating limitations. The take-off and landing weights were within the allowable limits, as was the aircraft's centre of gravity.
Examination of the taxi speed data recorded over a set of previous flights from VH-VOH and another 737-800 series aircraft in the operator's fleet (that also had a tyre failure), indicated that the straight-line taxi speeds were not exceeded, but a number of turns were recorded slightly above the manufacturer's recommended 10 kt maximum taxi speed whilst turning through 30º or more.
Meteorological information
At the time of the occurrence, the Terminal Area Forecast (TAF) for Canberra indicated moderate to severe turbulence below 5000 ft AGL. The Canberra Automatic Terminal Information Service (ATIS) reported the wind as 280 degrees at 25 kts with turbulence over the runway. A maximum gust of 32 kts was reported 5 minutes prior to the landing. However, the approach and landing was within the allowable wind limits for the aircraft.
Similar occurrences
Between early October and late December 2004, the ATSB noted an increase in the number of tyre failures on Boeing 737 aircraft in Australia. In this 3-month period, the ATSB received seven reports from operators of Boeing 737 aircraft, as compared with four reports in the preceding 21 months.
Six of the seven failures had occurred on the High Gross Weight variant of the Boeing 737-800 series aircraft and with tyres on the fourth (R4) and fifth (R5) retread. As a result, the ATSB issued safety recommendation R20040093 on 23 December 2004, recommending that operators of Boeing 737-800 series aircraft review the practice of fitting retread tyres of R4 (fourth retread) or above, until their serviceability limitations could be identified.
There were two commercial operators of Boeing 737-800 aircraft in Australia. Of the six failures on these aircraft, five were from one operator.
The ATSB obtained five of the failed tyres for further examination. All tyres were tubeless H44.5x16.5-21 28 PR2 tyres, which were approved by the aircraft manufacturer for use on the aircraft type and met the applicable US Federal Aviation Administration (FAA) Technical Standard Order, TSO-C62d. All failed tyres were from the same original manufacturer (or brand) and retreaded by the same retread facility. Both operators had about 50% of this brand in their tyre pool. The other two brands used on this aircraft type making up about 30% and 20% of each pool. All brands had representative tyres at retread levels R4 and R5.
Each operator had separate tyre pools that had operated since new and were of about the same age and R-level distribution. All of the tyres in these pools had been retreaded by the one retread facility since new.
The failures were not common to any position on the main landing gear, phase of flight, location, or retread date.
Examination of failed tyres
Five of the failed tyres were examined by the ATSB and by the tyre manufacturer in the United Kingdom (UK). The ATSB performed a visual examination and took fibre samples for detailed laboratory examinations, prior to shipping the tyres to the manufacturer. The tyre manufacturer examined the tyres under the supervision of a representative from the UK Air Accidents Investigation Branch (AAIB). A description of the tyre section components is contained in Figure 2.
Figure 2: Tyre section components

Examination by the ATSB
All tyre failures were similar in respect to the manner of casing break-up, with all presenting transverse ruptures along the sidewall ply axes. The stripping and loss of the tread from the tyre crown was limited to the two tyres that had failed at higher rotational speeds (landing and take-off) and was attributable to the effects of centrifugal forces on the tread belts as fracture and tearing progressed across the tyre crown. Bulk tread separation was not evident on the three tyres that had failed at lower (taxi) speeds.
Examination of the sampled fibres showed a combination of failure modes, attributable to tensile overload and possible cyclic loads stemming from structural flexure.
The failures were all consistent with the effects of a progressive failure and breakdown within the sidewall structure of the tyres. There was no evidence of the involvement of individual events such as foreign object impact, wheel skidding, or similar damage.
Examination by the tyre manufacturer
The tyre manufacturer's examinations found that the five tyres had failed in a similar manner. The conclusion made for each of the items examined was:
Cyclic fatigue in the inner ply turn-ups 3, leading to casing break-up, fracturing of the inner liner construction, ply separation and a localised sidewall rupture along the bias angle of the cord layers.
The tyre manufacturer also indicated that the fatigue in the inner ply turn-ups was due to cyclic flexing of the inner plies, which created a local looseness and reduction in strength. This led to a small fracture in the inner liner, resulting in a slow loss of pressure. The rate of pressure loss increased as the fracture in the inner liner grew, until it reached a point where, when combined with the operational loads, exceeded the venting capacity 4 of the casing and a rupture occurred.
A review of the original manufacture records for each of the tyres indicated that all had been manufactured from the correct material that were checked and passed laboratory sample testing. The destructive examination confirmed that the tyres were constructed to the approved design and process specifications.
Due to the extent and severity of the fatigue damage in the sidewall, and the low number of landing cycles accumulated by some of the failed tyres since the last retread, the manufacturer considered that the damage was possibly present, to some degree, during the last retreading process.
Approved tyres
At the time of the failures there were three tyre manufacturers approved to produce H44.5x16.5-21 28 PR tyres for the Boeing 737-800 series aircraft. A review of the specifications found that all three complied with the requirements of FAA Technical Standard Order TSO-C62d. The only notable difference between the brands was the average weight. The average weight for the tyres was 85.7 kg, 90 kg and 93 kg. The failed tyres were from the brand having the higher average weight.
TSO-C62d prescribed the minimum performance standard that aircraft tyres must meet to be identified with the applicable TSO marking. This performance standard included an overpressure and a dynamometer test 5. The TSO also dealt with changes to the tyre design with the following statement:
7.0 Requalification tests. A tire shall be requalified unless it is shown that changes in materials, tire design, or manufacturing processes could not affect performance. Changes in material, tire design, or manufacture processes that affect performance or changes in number or location of tread ribs and grooves or increases in skid depth, made subsequent to the tire qualification, must be substantiated by dynamometer tests in accordance with paragraph 6.0.
Retreading of tyres
Operational experience has shown that the tread of an aircraft tyre wears away at a much higher rate than the basic casing of the tyre and can be safely replaced multiple times before the casing reaches its service limits. As with all aircraft components, a controlled and regulated process was required to retread tyres. The FAA required a retread facility to have an approved process to both qualify tyres for retread, and for physically performing the retread. In 1982, to assist retread facilities in producing a process specification, the FAA released guidance material in the form of Advisory Circular AC 145-4.
In 1985, the Australian Civil Aviation Authority (the predecessor to the Civil Aviation Safety Authority, CASA) mandated the use of the guidance material in FAA AC 145-4 for the retreading of aircraft tyres, through the release of Airworthiness Directive AD/WHE/3 Amendment 1. The Australian retread facility responsible for the retreading of the occurrence tyres had a process specification approved by CASA that corresponded to AC 145-4.
Retread qualification requirements
For the speed rating 6 of the occurrence tyres, AC 145-4 required that the retread process specification included overpressure and dynamometer testing 7. Although not clearly stated in AC 145-4, the FAA and CASA have accepted that the retread process for a tyre of a particular size, speed rating and load rating shall be qualified by overpressure and dynamometer testing to R1 (first retread) level. To qualify for higher R-levels, the retreader need only perform a set of ply adhesion tests to check the strength of the rubber bond.
For bias-ply tyres 8, the FAA and CASA have also accepted that the overpressure and dynamic testing need only be carried out on one brand representing the size, speed rating and load rating, as 'Many years of evolution have resulted in a nylon bias tire having a casing structure that is essentially the same, irrespective of the manufacturer'. The tyres that were the subject of this investigation had not come from the brand of tyre that had been used in the qualification testing for this tyre range. The ATSB has had no reports of the observed type of failure in the brand used to qualify the retread process for the H44.5x16.5-21 28 PR tyre on the 737-800 series aircraft.
The retread facility noted some small differences to the profile between the subject brand and the other brands approved for use on 737 series aircraft.
Retread process
During retreading, before any physical work was carried out, the casing was subjected to a non-destructive inspection (NDI) process to determine if it was suitable for retread. The NDI process consisted of visual, shearography, and casing leak inspections.
The visual inspection was a check by a trained technician to determine if there was any obvious damage in the surface of the tyre casing. The technician assessed any damage found to determine if it was within the limits allowed for the tyre, or if it was suitable for repair.
The shearography was a computer-based inspection system that compared the tyre under atmospheric pressure and a reduced pressure to determine if there were any separations within the ply structure. Tyres with separations exceeding preset limitations were rejected and destroyed. At the time the occurrence tyres were retreaded, only a shoulder-to-shoulder (crown area) shearography inspection was carried out. However, radial ply tyres 9 required a bead-to-bead (which included sidewalls) shearography inspection.
The final check was a casing leak check. Pressurised air was injected into the casing plies and soapy water sprayed over the tyre. Any leaks found were either accepted, or repaired if they were within the allowable limits, or the tyre was rejected and destroyed.
After successful completion of all tests, the facility carried out the physical retreading process. A visual and dimensional check completed the retread process. Since the facility had been operating the shearography equipment (early 2004), they have included an additional, post-retread, shearography.
A review of the process documentation for each of the tyres examined found that all applicable inspections had been certified as having been completed before the tyre was released for service.
The area of the sidewall where the fatigue occurred was not subject to the pre- or post-retread shearography inspection on any of the tyres examined, nor was it required by their approved process specification.
Aircraft tyre maintenance
A review of the tyre pressure maintenance practices found that once fitted to the aircraft, the tyres were subject to a condition and inflation pressure check as part of the daily inspection. However, except for a layover in excess of 4 hours, there was no requirement to examine the tyres in detail on a normal turn-around pre-flight check. In that instance, only a condition check was required.
The operator with the five failures had a fleet of 45 737-700 and -800 series aircraft, including low, medium and high gross weight variants of each model. Each of the variants in the fleet (five in total) had their own nominal pressure requirements of 190, 200 or 205 psig 10 and were all listed on the same daily check Task Card. The Boeing Maintenance Manual inflation pressure check required that 'all tyres on the same gear are inflated to the selected nominal service pressure +/-5 psig'. The operator's Task Card did not present this range, but did contain the statement 'NOTE: If any tyre is below the nominal pressure by more than 5%, review the Aircraft Maintenance Manual for further requirements.' The Aircraft Maintenance Manual required that if the tyre pressure was 5% to 10% below the nominal service pressure, the tyre was to be reinflated to the nominal service pressure then checked again 24 hours later. If the tyre pressure was again more than 5% below the nominal service pressure, it was to be removed. If the tyre was found at any stage to be more than 10% below the nominal service pressure, it was to be removed from the aircraft immediately.
A review of a small sample of the operator's Maintenance Discrepancy Reports indicated that some of the engineers that checked tyre pressures had reinflated the tyres to 200 psig (the lower limit for the aircraft model), rather than the nominal service pressure of 205 psig. On one occasion, a tyre was found to be 180 psig, which is 12% below the nominal service pressure of 205 psig, but was reinflated to 200 psig and rechecked 24 hours later. The operator provided a revision of the Task Card that was reported to be applicable at the time of these Maintenance Discrepancy Reports that indicated that the nominal service pressure for the tyres was 200 psig. A revision of the task card in 2004, prior to the tyre failures, increased the nominal service pressure to 205 psig.
The operator carried out a survey of tyre pressures on a portion of their fleet over an eleven-day period and found that about 1% of tyres were 5% or more below the nominal service pressure. Of these low-pressure events, about one third were recorded in accordance with the operator's procedures.
Although both operators selected the same nominal main landing gear tyre pressure (in accordance with the Boeing maintenance instructions), the operator with the low number of failures had opted to avoid the lower end of the normal service pressure range and utilised the upper end of the pressure range (205 to 210 psig) for inflation pressure servicing.
Factors affecting tyre fatigue life
The heat generated by operation of aircraft tyres is a well-documented factor affecting tyre life. The heat in the tyres may be from an external source, such as the brakes, however the heat generated from flexing of the tyres is generally considered the primary source of temperature rise in aircraft tyres.
Studies carried out by various tyre manufacturers (presented in their tyre care and maintenance documentation) show that the effects of taxi speed, taxi distance and inflation pressure on the internally generated heat can be quite dramatic. The general effects are:
- Increased taxi speed leads to increased tyre temperature
- Increased taxi distance leads to increased tyre temperature
- Decreased inflation pressure leads to increased tyre temperature.
The most significant increase in temperature was identified in the tyre bead/sidewall area.
The FAA provided guidance on the effects of turns on tyre temperature in AC 20-97B. The guidance to operators in this AC is:
Aircraft tires generate internal heating during normal operations. Under high aircraft loads (particularly under sideloading conditions), heat build-up is accelerated by excessive taxi speed and/or excessive taxi distances. Tire integrity and reliability may be compromised when a combination of these conditions occur.
Studies by tyre manufacturers have found that the performance of a tyre casing reduced by more than 50% when run continuously under-inflated by only 5%.
- The casing is the body of the tyre consisting of the nylon structural cords embedded in a rubber compound.
- H44.5x16.5-21 defines the size of the tyre. In this case, the tyre has an outer diameter of 44.5 inches, a width of 16.5 inches and fits on a 21-inch wheel rim. PR is the ply rating and is an indicator of the load capability of the tyre.
- The inner ply turn-ups are the tail ends of the plies after they have wrapped around the bead and are located in the mid-sidewall region.
- Tubeless aircraft tyres are designed with small vent holes in the outer sidewall. These vents release air pressure from the plies that has leaked or diffused through the inner liner.
- The dynamometer test is a dynamic test that cycles a tyre through a range of operational speeds and loads to simulate a series of take-off and taxi cycles.
- Because the tyres are designed to a performance specification for the tyre as a stand-alone item (TSO-C62d) and not to a particular aircraft, they are approved to a maximum speed and load. These limits are referred to as the 'speed rating' and 'load rating'.
- AC 145-4 had additional qualification requirements for tyres with a speed rating above 160 mph.
- Bias-ply tyres are also known as cross ply tyres. They are constructed from layers of rubber-coated nylon ply cords that extend around the beads and are oriented at alternating angles to the tread centreline.
- Radial ply tyres are constructed from nylon and rubber cords, however, the cords are oriented differently to bias ply tyres. A set of cords run from one bead, across the crown and to the opposite bead. Another set of cords lie around the circumference of the tyre under the tread area.
- The indicator reading, in pounds per square inch, showing the amount by which the tyre pressure exceeds atmospheric pressure.
ANALYSIS
Tyre failure mechanism and detection during maintenance and retread
Each of the tyres examined sustained a casing break-up event as a result of fatigue damage in the sidewall of the tyre. These failures occurred at a similar retread level (R4 and R5), but occurred well before the tread was due for replacement.
Aircraft tyres of this type had several operational measures to prevent premature failure. These included non-destructive inspection (NDI) during the retread process, inflation pressure maintenance, and aircraft weight and speed limitations.
Examination of the failed tyres found that the fatigue damage was quite extensive and was considered to be possibly present at the last retread. Because the shoulder-to-shoulder NDI used by the tyre retread facility was limited to the crown (tread area) of the tyre, it could not detect damage in the sidewall unless the extent of the damage breached the inner or outer surface of the tyre resulting in a leak. The NDI technique utilised by the retread facility was physically capable of inspecting the sidewall of the tyres, but neither the Civil Aviation Safety Authority (CASA) nor the Federal Aviation Administration (FAA) required sidewall inspection for bias-ply tyres.
Diffusion of the air through the inner liner of tubeless aircraft tyres resulted in the slow loss of pressure. Thus, it is vitally important to regularly check and maintain the tyre inflation pressures. The normal practice was a daily check on cold loaded tyres. This not only ensured that the tyres were operated in the correct pressure range but also allowed maintenance engineers to determine if a tyre was leaking at an abnormal rate.
An excessive leakage rate is a strong indication of imminent tyre failure and so it is critical that it is identified as soon as possible. The survey conducted by the operator indicated that only about one third of the low-pressure events were being recorded by the engineers. For those events that were not recorded, the only way to identify a 'leaker' (a tyre with pressure leakage in excess of the normal limits) was for a maintenance engineer to remember that the same tyre on the same aircraft was topped up on the previous day. As the operator had 45 aircraft, each with six tyres (four main and two nose) and operated from different ports around Australia, the detection of a 'leaker' was very unlikely.
The maintenance Task Card used by the operator during the daily check listed procedures for all of the 737 variants in their fleet. This was particularly evident for the tyre inflation checks where there were three possible nominal inflation pressures. This Task Card did not directly indicate the inflation pressure range for each aircraft variant but contained a note to refer to the Aircraft Maintenance Manual (AMM) if the pressure was below nominal by more than 5%. Although the abbreviated data on the Task Card provided the correct nominal pressure, it left the appropriate inflation pressure range open to some level of interpretation and possible confusion, as the limit for the inflation pressure in the AMM was the nominal ±5 psig, but the special maintenance procedures started at 5% (i.e. 10 psig) below the nominal pressure.
Until 2004, when the task card had the tyre nominal service pressure increased from 200 psig to 205 psig, the tyres had been operated at or below the lower limit of the normal service pressure range for extended periods. Under-inflation is a well-known factor in the development of fatigue in the sidewall of tyres resulting in reduced life performance.
The examination of the incident flight data did not show any single event that would have resulted in the failure. However, a review of the taxi speed data from two aircraft that had tyre failures, indicated that they were occasionally turned at speeds approaching, or exceeding, that recommended by the aircraft manufacturer. Considering the examination of the failed tyres and the analysis presented above, the damage to the tyres was not due to a single event, but an accumulation of damage during normal operations. The effect of turning at taxi speeds above that recommended by the manufacturer would further reduce the life expectancy of the tyre casing.
Certification of tyres and qualification for retread
The basic design standard for the tyres (FAA TSO-C62d) required requalification for a tread design change. This applied to each manufacturer. If a manufacturer changed their basic tread design, such that it was the same as a retread package, they would be required to retest to show compliance with the TSO. However, the practice for retread qualification accepted by both CASA and the FAA, required only one brand of tyre to be fully tested (overpressure and dynamometer). This testing may verify the retread package but does not capture the effect that the tread design, which may be different to the original tread design on the tyre, has on the performance of the casing of the non-tested brands.
Because the tyres were originally approved to Technical Standard Order TSO-C62d and had lasted for more than three retread lives, it was clear that there was no immediate weakness inherent in the original tyre design. As the aircraft type was fitted with several tyre brands, but only developed similar fatigue flaws in one brand, it appears that there were performance differences between the brands that the retread qualification testing of a single brand at R1 could not identify. There was no apparent compliance substantiation for the untested brands to the original design standard (i.e. TSO-C62), other than historical acceptance of similarities in the construction of bias-ply tyres.
SIGNIFICANT FACTORS
- Flexing of the tyre sidewalls in operation resulted in fatigue damage in the inner casing plies.
- The fatigue damage was possibly present at the last retread process but was not detected by the non-destructive inspection used in the process.
- The fatigue in the plies allowed cracks to develop and grow in the inner liner, allowing high-pressure air to leak into the casing.
- Maintenance crews did not detect an increase in the rate of pressure loss in the days leading up to the tyre failure.
- The pressure leakage into the casing increased to the point that exceeded the capacity of the in-built venting and combined with operational loads, resulted in the failure of the tyre structure.
SAFETY ACTION
Australian Transport Safety Bureau
On 23 December 2004 the Australian Transport Safety Bureau issued safety recommendation R20040093. That recommendation stated:
The Australian Transport Safety Bureau recommends that Australian operators of Boeing 737-800 series aircraft review the practice of fitting retread tyres of R4 (fourth retread) or above, until their serviceability limitations can be identified.
In response to the safety recommendation, the ATSB was advised that the following actions were taken:
- The operator of VH-VOH limited their in-service retread level to R3 on the 737-800 series fleet.
- The other operator with 737-800 series aircraft performed a visual inspection of all in-service tyres and instigated a more stringent inspection of the tyres by maintenance and flight crews as part of the pre-flight checks.
- The retread facility limited the maximum retread level for the H44.5x16.5-21 28 PR tyre to R3.
Aircraft manufacturer
The aircraft manufacturer noted a worldwide increase in 737 tyre failures, particularly in the 737NG (600, 700, 800, 900 and BBJ series). As a result, they conducted a study of the failures and released a Flight Team Digest in January 2005. Although their study found that no particular root cause for the failures was apparent, they were able to make some recommendations to improve the operation of the tyres. These recommendations included:
Inflate tires to the high end of the allowable ranges shown in AMM [Aircraft Maintenance Manual] 12-15-51. This reduces the sidewall deflection of the tire and therefore reduces the heat generated by the tire.
It is important to check inflation pressures frequently.
If a tire is identified as a leaker (as evidenced by two successive pressure checks where pressure is more than 5% low), it should be removed from the airplane immediately. Note that tires which are leaking gas through their inner-liner pose an imminent threat of a tread loss.
Operators should require that their retreaders perform the more complete bead-to-bead NDT checks (holography/shearography) on their tires as opposed to just checking the crown area. This appears to be especially important on 737NG tire sizes and is most critical when the tires reach high retread levels.
On 28 June 2005, the Boeing Commercial Airplane Company released Service Letter 737-SL-32-128-A 'Tire Retreading Recommendations' to 737-600/-700/-800/-900/BBJ operators. This Service Letter provided guidance on retreading NDI, retread limits and frequent and thorough pressure checks.
Operator of VH-VOH
On 1 June 2005, the aircraft operator released a General Engineering Notice (GEN) regarding tyre pressure checking and discrepancy recording. This GEN was associated with a change to the daily Task Card and provided more detailed guidance on the pressure maintenance of the tyres in the fleet and actions to be taken when a tyre pressure is found to be low. The GEN and daily Task Card included the following improvements:
- Tyres are to be maintained in the upper end of the pressure range (i.e. nominal pressure +5/-0 psi).
- Any tyre requiring a pressure top-up during the daily check is to be recorded in the Flight Technical Log (with pre- and post-inflation pressures) and the pressure re-checked on the next daily check.
- The allowable pressure range (+5/-0 psi) has been listed with the nominal pressure for each aircraft variant in the fleet.
- Expanded maintenance actions from the AMM for under-inflated tyres.
- A note to ensure that the gauge used to check pressures is within calibration prior to use.
Tyre retread facility
On 9 September 2005, the Australian tyre retread facility included in their CASA approved Process Specification, bead-to-bead shearography inspections on all 737NG main gear tyres of retread level R3, and above.
United States Federal Aviation Administration
On 9 March 2006, the United States Federal Aviation Administration advised the Australian Transport Safety Bureau that they are currently reviewing and revising Technical Standard Order TSO-C62 and Advisory Circular AC 145-4. The changes to AC 145-4 are to include the recommendation for a reliability program and the increased use of shearography at increasing retread levels.
Tyre failure mechanism and detection during maintenance and retread
Each of the tyres examined sustained a casing break-up event as a result of fatigue damage in the sidewall of the tyre. These failures occurred at a similar retread level (R4 and R5), but occurred well before the tread was due for replacement.
Aircraft tyres of this type had several operational measures to prevent premature failure. These included non-destructive inspection (NDI) during the retread process, inflation pressure maintenance, and aircraft weight and speed limitations.
Examination of the failed tyres found that the fatigue damage was quite extensive and was considered to be possibly present at the last retread. Because the shoulder-to-shoulder NDI used by the tyre retread facility was limited to the crown (tread area) of the tyre, it could not detect damage in the sidewall unless the extent of the damage breached the inner or outer surface of the tyre resulting in a leak. The NDI technique utilised by the retread facility was physically capable of inspecting the sidewall of the tyres, but neither the Civil Aviation Safety Authority (CASA) nor the Federal Aviation Administration (FAA) required sidewall inspection for bias-ply tyres.
Diffusion of the air through the inner liner of tubeless aircraft tyres resulted in the slow loss of pressure. Thus, it is vitally important to regularly check and maintain the tyre inflation pressures. The normal practice was a daily check on cold loaded tyres. This not only ensured that the tyres were operated in the correct pressure range but also allowed maintenance engineers to determine if a tyre was leaking at an abnormal rate.
An excessive leakage rate is a strong indication of imminent tyre failure and so it is critical that it is identified as soon as possible. The survey conducted by the operator indicated that only about one third of the low-pressure events were being recorded by the engineers. For those events that were not recorded, the only way to identify a 'leaker' (a tyre with pressure leakage in excess of the normal limits) was for a maintenance engineer to remember that the same tyre on the same aircraft was topped up on the previous day. As the operator had 45 aircraft, each with six tyres (four main and two nose) and operated from different ports around Australia, the detection of a 'leaker' was very unlikely.
The maintenance Task Card used by the operator during the daily check listed procedures for all of the 737 variants in their fleet. This was particularly evident for the tyre inflation checks where there were three possible nominal inflation pressures. This Task Card did not directly indicate the inflation pressure range for each aircraft variant but contained a note to refer to the Aircraft Maintenance Manual (AMM) if the pressure was below nominal by more than 5%. Although the abbreviated data on the Task Card provided the correct nominal pressure, it left the appropriate inflation pressure range open to some level of interpretation and possible confusion, as the limit for the inflation pressure in the AMM was the nominal ±5 psig, but the special maintenance procedures started at 5% (i.e. 10 psig) below the nominal pressure.
Until 2004, when the task card had the tyre nominal service pressure increased from 200 psig to 205 psig, the tyres had been operated at or below the lower limit of the normal service pressure range for extended periods. Under-inflation is a well-known factor in the development of fatigue in the sidewall of tyres resulting in reduced life performance.
The examination of the incident flight data did not show any single event that would have resulted in the failure. However, a review of the taxi speed data from two aircraft that had tyre failures, indicated that they were occasionally turned at speeds approaching, or exceeding, that recommended by the aircraft manufacturer. Considering the examination of the failed tyres and the analysis presented above, the damage to the tyres was not due to a single event, but an accumulation of damage during normal operations. The effect of turning at taxi speeds above that recommended by the manufacturer would further reduce the life expectancy of the tyre casing.
Certification of tyres and qualification for retread
The basic design standard for the tyres (FAA TSO-C62d) required requalification for a tread design change. This applied to each manufacturer. If a manufacturer changed their basic tread design, such that it was the same as a retread package, they would be required to retest to show compliance with the TSO. However, the practice for retread qualification accepted by both CASA and the FAA, required only one brand of tyre to be fully tested (overpressure and dynamometer). This testing may verify the retread package but does not capture the effect that the tread design, which may be different to the original tread design on the tyre, has on the performance of the casing of the non-tested brands.
Because the tyres were originally approved to Technical Standard Order TSO-C62d and had lasted for more than three retread lives, it was clear that there was no immediate weakness inherent in the original tyre design. As the aircraft type was fitted with several tyre brands, but only developed similar fatigue flaws in one brand, it appears that there were performance differences between the brands that the retread qualification testing of a single brand at R1 could not identify. There was no apparent compliance substantiation for the untested brands to the original design standard (i.e. TSO-C62), other than historical acceptance of similarities in the construction of bias-ply tyres.
- Flexing of the tyre sidewalls in operation resulted in fatigue damage in the inner casing plies.
- The fatigue damage was possibly present at the last retread process, but was not detected by the non-destructive inspection used in the process.
- The fatigue in the plies allowed cracks to develop and grow in the inner liner, allowing high-pressure air to leak into the casing.
- Maintenance crews did not detect an increase in the rate of pressure loss in the days leading up to the tyre failure.
- The pressure leakage into the casing increased to the point that exceeded the capacity of the in-built venting and, combined with operational loads, resulted in the failure of the tyre structure.
Australian Transport Safety Bureau
On 23 December 2004 the Australian Transport Safety Bureau issued safety recommendation R20040093. That recommendation stated:
The Australian Transport Safety Bureau recommends that Australian operators of Boeing 737-800 series aircraft review the practice of fitting retread tyres of R4 (fourth retread) or above, until their serviceability limitations can be identified.
In response to the safety recommendation, the ATSB was advised that the following actions were taken:
- The operator of VH-VOH limited their in-service retread level to R3 on the 737-800 series fleet.
- The other operator with 737-800 series aircraft performed a visual inspection of all in-service tyres and instigated a more stringent inspection of the tyres by maintenance and flight crews as part of the pre-flight checks.
- The retread facility limited the maximum retread level for the H44.5x16.5-21 28 PR tyre to R3.
Aircraft manufacturer
The aircraft manufacturer noted a worldwide increase in 737 tyre failures, particularly in the 737NG (600, 700, 800, 900 and BBJ series). As a result, they conducted a study of the failures and released a Flight Team Digest in January 2005. Although their study found that no particular root cause for the failures was apparent, they were able to make some recommendations to improve the operation of the tyres. These recommendations included:
Inflate tires to the high end of the allowable ranges shown in AMM [Aircraft Maintenance Manual] 12-15-51. This reduces the sidewall deflection of the tire and therefore reduces the heat generated by the tire.
It is important to check inflation pressures frequently.
If a tire is identified as a leaker (as evidenced by two successive pressure checks where pressure is more than 5% low), it should be removed from the airplane immediately. Note that tires which are leaking gas through their inner-liner pose an imminent threat of a tread loss.
Operators should require that their retreaders perform the more complete bead-to-bead NDT checks (holography/shearography) on their tires as opposed to just checking the crown area. This appears to be especially important on 737NG tire sizes and is most critical when the tires reach high retread levels.
On 28 June 2005, the Boeing Commercial Airplane Company released Service Letter 737-SL-32-128-A 'Tire Retreading Recommendations' to 737-600/-700/-800/-900/BBJ operators. This Service Letter provided guidance on retreading NDI, retread limits and frequent and thorough pressure checks.
Operator of VH-VOH
On 1 June 2005, the aircraft operator released a General Engineering Notice (GEN) regarding tyre pressure checking and discrepancy recording. This GEN was associated with a change to the daily Task Card and provided more detailed guidance on the pressure maintenance of the tyres in the fleet and actions to be taken when a tyre pressure is found to be low. The GEN and daily Task Card included the following improvements:
- Tyres are to be maintained in the upper end of the pressure range (i.e. nominal pressure +5/-0 psi).
- Any tyre requiring a pressure top-up during the daily check is to be recorded in the Flight Technical Log (with pre- and post-inflation pressures) and the pressure re-checked on the next daily check.
- The allowable pressure range (+5/-0 psi) has been listed with the nominal pressure for each aircraft variant in the fleet.
- Expanded maintenance actions from the AMM for under-inflated tyres.
- A note to ensure that the gauge used to check pressures is within calibration prior to use.
Tyre retread facility
On 9 September 2005, the Australian tyre retread facility included in their CASA approved Process Specification, bead-to-bead shearography inspections on all 737NG main gear tyres of retread level R3, and above.
United States Federal Aviation Administration
On 9 March 2006, the United States Federal Aviation Administration advised the Australian Transport Safety Bureau that they are currently reviewing and revising Technical Standard Order TSO-C62 and Advisory Circular AC 145-4. The changes to AC 145-4 are to include the recommendation for a reliability program and the increased use of shearography at increasing retread levels.