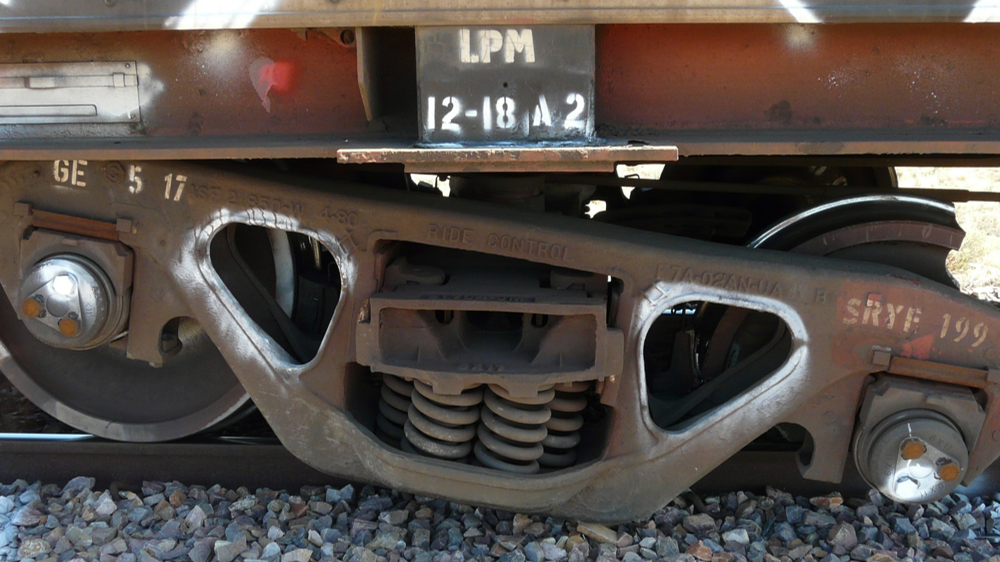
The derailment of a freight train wagon following a ruptured wheel in the wagon’s ‘B’ end wheelset highlights potential limitations of field inspections for the detection and monitoring of fatigue cracks, a new ATSB investigation says.
SCT Logistics freight train 6MP9 was travelling from Melbourne to Perth early on the morning of 4 January 2019. While on the Fisher-Thomair section of track near Cook, South Australia, a single wagon derailed due to a ruptured wheel. While no other wagons derailed, damage to sleepers and clips was found in the area of the derailment
Prior to the derailment, the train had passed over two wayside detectors designed to alert the operator of abnormalities that might indicate wheel or bearing damage. However, there was no record of any alerts received from these detectors.
While vigilant field inspections are a useful tool for the detection and monitoring of fatigue cracks, they are not infallible and should be used with an understanding of their limitations.
ATSB Director Transport Safety, Stuart MacLeod said the derailment was due to fatigue cracking in the ruptured wheel.
“Metallurgical examination found a fatigue crack had initiated in the wheel flange and then propagated into and around the wheel plate and rim, causing the wheel to fail and break into multiple pieces,” Mr Macleod said.
“The fatigue crack was found to have initiated in an area of the wheel that showed signs of sliding contact with the rails. Sliding contact can cause thermal damage to the wheel leaving a white etching layer that is brittle and more susceptible to cracking.”
Mr Macleod noted that at the last inspection, the flange fatigue crack was likely observable but was either not detected, or was deemed acceptable under the work instruction provided. This work instruction provided guidance that was less conservative than the Australian Standard, but it was not possible to establish whether compliance with the standard would have prevented the occurrence.
“This incident demonstrates that while vigilant field inspections are a useful tool for the detection and monitoring of fatigue cracks, they are not infallible and should be used with an understanding of their limitations,” Mr Macleod said.
“Further, selection of the appropriate materials for wheels can also assist in reducing the occurrence of fatigue cracks and subsequent failures.”
Since the incident the operator has worked with its maintenance provider to develop an improved inspection process for wheels exhibiting brakes issues, particularly sticking brakes, an issue known to lead to the development of thermal cracking.
The operator is also phasing out the ruptured wheel class type from its fleet.
Read the report: Derailment of SCT Logistics freight train 6MP9, near Cook, South Australia, on 6 January 2019