Executive summary
What happened
On 17 October 2022, at about 1345 local the pilot of a Mooney Aircraft Corporation M20J aircraft, registered VH-UDQ, departed Maitland Airport, NSW for a local flight. The pilot flew to Cessnock Airport, NSW and completed an orbit, then continued to Luskintyre airfield, NSW. When overhead Luskintyre airfield, the pilot broadcast their intent to track to Maitland Airport.
Witnesses near Luskintyre airfield reported observing the aircraft in what appeared to be descending to land. They further reported that smoke and flames were seen trailing the aircraft. At about 1359 VH-UDQ collided with terrain about 330 metres short of runway 30 with witnesses describing an explosion and accompanying fireball.
The aircraft was destroyed by an intense post-impact fire. The pilot survived the collision but eventually succumbed to injuries sustained during the accident.
What the ATSB found
The ATSB determined that an O-ring seal fitted to the engine-driven fuel pump outlet fitting remained in service until it became age-affected and failed to provide an effective seal. The escaping fuel from the age-affected O-ring seal ignited and created an engine compartment fire. In response to the fire, the pilot initiated an emergency descent towards the runway but subsequently landed in a field resulting in the aircraft impacting trees. That led to a break-up of the aircraft and a severe post‑impact fire that consumed the aircraft.
The ATSB also established that the aircraft had been recently refurbished. The refurbishment included repainting the aircraft and replacing interior furnishings with alternate materials. Neither the refurbishment activity nor details of the flammability assessment of the substituted materials, were recorded in the aircraft log books. The effect this refurbishment had on the in-flight fire, or the survivability of the pilot could not be determined.
What has been done as a result
In response to this accident, the Civil Aviation Safety Authority proposed to review Airworthiness Bulletins AWB 02-001 relating to on-condition maintenance, and AWB 85-004 regarding aircraft piston engine calendar time overhaul and most likely update them. The review would serve to highlight that ‘on-condition’ was not a ‘fit and forget’ approach to preventative maintenance.
The ATSB has issued safety advisory notice SAN AO-2022-049-001 in conjunction with this investigation report. The SAN draws attention to the proactive replacement of O-ring seals fitted to engines and engine components, should inspection of aircraft records indicate they have been in service for a significant period.
Safety message
Piston engines, and the components necessary for their operation, installed in aircraft operating in the private or airwork category are permitted to remain in service beyond their recommended calendar time overhaul interval. As O-ring seals fitted to such engines are susceptible to deterioration due to age, being aware of their accumulated time-in-service may initiate replacement action before they fail.
Maintaining an aircraft’s internal appearance may require the introduction of alternate materials when original products may no longer be available. Aircraft owners are encouraged to document aircraft refurbishment action in the aircraft logbook and to include details of materials if substituted, and their suitability for use in aircraft interiors.
The investigation
Decisions regarding the scope of an investigation are based on many factors, including the level of safety benefit likely to be obtained from an investigation and the associated resources required. For this occurrence, a limited-scope investigation was conducted in order to produce a short investigation report, and allow for greater industry awareness of findings that affect safety and potential learning opportunities. |
The occurrence
On 17 October 2022, at about 1345 the pilot of a Mooney Aircraft Corporation M20J aircraft, registered VH‑UDQ, departed Maitland Airport, NSW for a local flight. The aircraft travelled to the south-east before turning west towards Cessnock Airport. The pilot conducted an orbit of Cessnock Airport and by about 1353, was headed north-east towards Luskintyre airfield (Figure 1). At 1357:29, when about 2,150 ft above ground level (AGL)[1] during an orbit of Luskintyre airfield, the pilot made a broadcast on the common traffic advisory frequency[2] alerting other pilots in the area that they were overhead Luskintyre airfield and intending to track to join crosswind for runway 23[3] at Maitland Airport.
Figure 1: VH-UDQ Maitland to Luskintyre flight with inset showing flight path north of Sydney, NSW
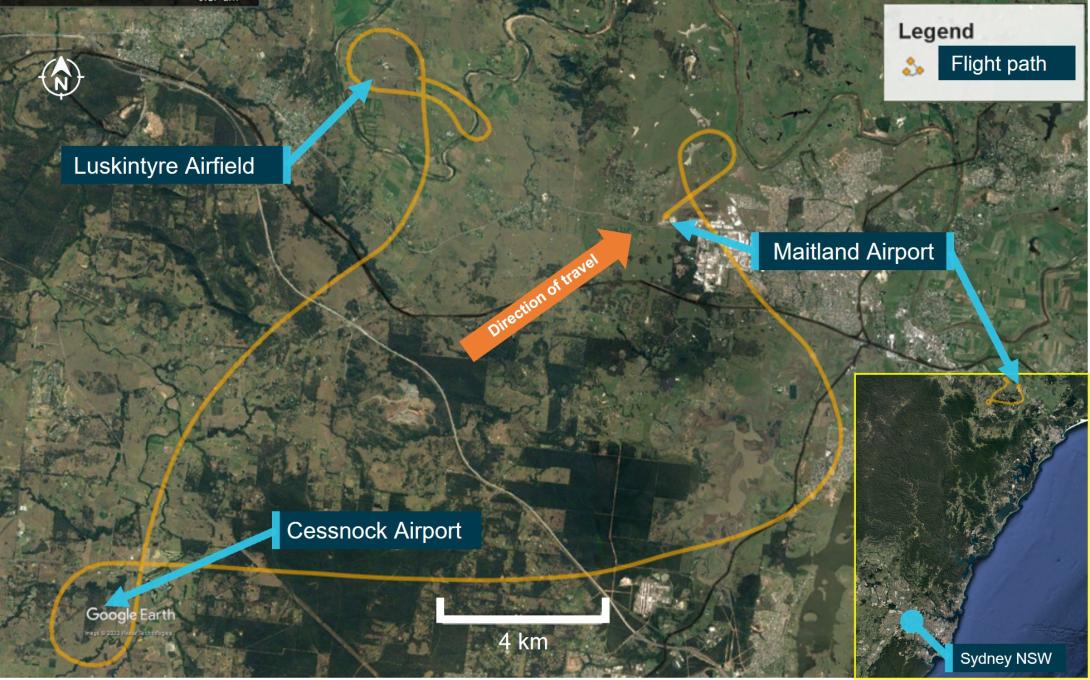
Source: Google and AvPlan flight data. Annotated by ATSB.
Witnesses reported observing a light aircraft near the airfield that appeared to be descending to land. As VH-UDQ descended towards a line of trees to the south of their position, one witness observed flames coming from the front of the aircraft. The other witnesses reported seeing the aircraft with smoke trailing behind. No distress or emergency calls from the pilot were recorded (Figure 2).
Figure 2: Orbit and descent towards Luskintyre airfield
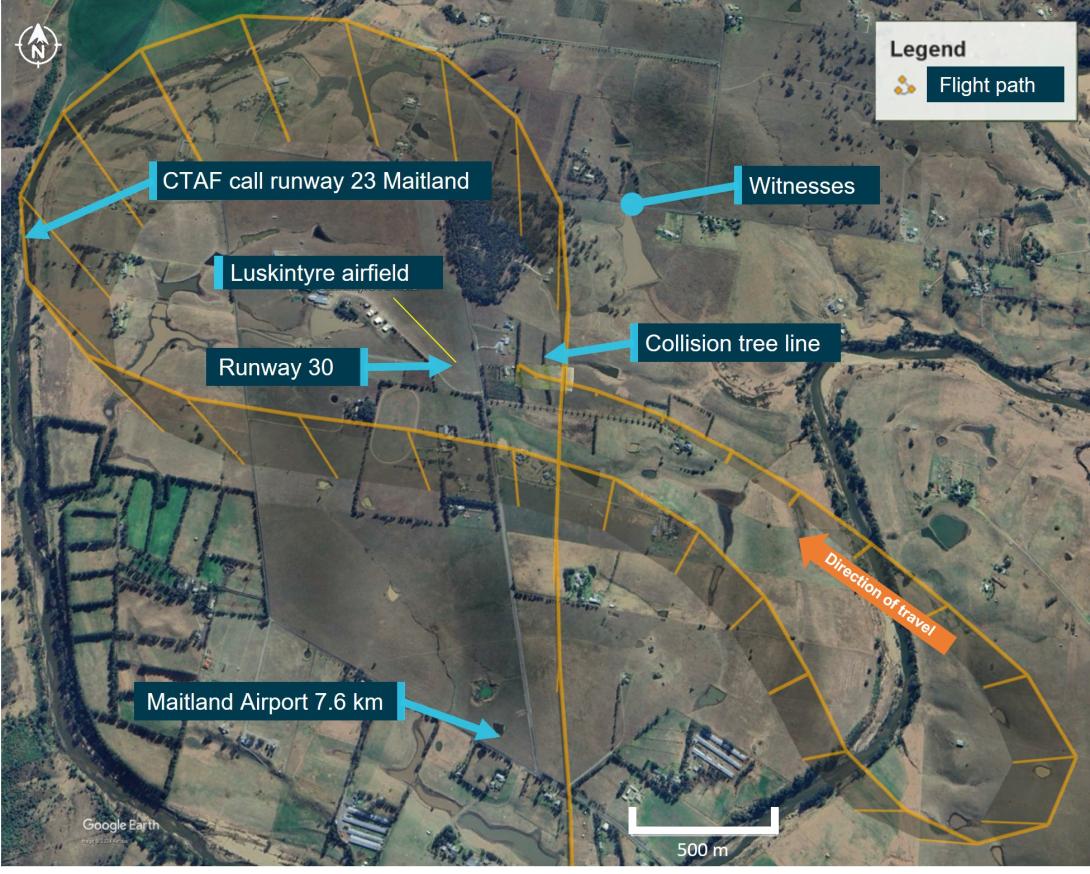
Source: Google and AvPlan flight data. Annotated by ATSB.
VH-UDQ continued its descent, and touched down in a grass field that was divided by a line of trees. At about 1359 VH-UDQ collided with the trees that were located about 330 metres short of runway 30 with witnesses describing an explosion and accompanying fireball. The collision with trees resulted in the break-up of the aircraft with the fuselage coming to rest about 70 m beyond the tree line.
The witnesses proceeded to the scene and on arrival, they located the pilot lying in the field about 10 m away from the burning aircraft. The pilot advised the witnesses that the aircraft engine had caught fire and that they had suffered smoke inhalation.
The aircraft was destroyed by an intense post-impact fire. Although the pilot survived the collision and escaped from the aircraft, the pilot sustained substantial burns. The pilot was taken to hospital but succumbed to these injuries about 10 weeks later.
Context
Pilot information
The pilot held a Commercial Pilot Licence (Aeroplane) and a valid Class 1 aviation medical certificate. The pilot was issued with a private pilot licence in 1998 and a commercial pilot licence in 2008. The pilot, who was an associate of the aircraft owner, held the required ratings and endorsements for the flight. According to the last medical examination report in October 2021, the pilot reported that they had accumulated about 990 flying hours experience.
Aircraft information
General
VH-UDQ was a Mooney Aircraft Corporation M20J, manufactured in the United States in 1978 and assigned serial number 24-0588. The aircraft Log Book Statement for maintenance direction specified that the airframe was to be periodically inspected in accordance with Civil Aviation Safety Authority (CASA) Schedule 5 and the engine per AD/ENG/4 as amended. For special inspections and lifed component changes, the aircraft maintenance manual was to be consulted.
Engine history
The aircraft was fitted with a 4-cylinder Lycoming engine, model IO‑360-A3B6D, serial number L‑22956-51A. Records show that the engine was last overhauled in May 1993 and had accumulated 1,806.3 hours, time-in-service since overhaul. At the time of the accident, the engine had been operating for 29.5 years since overhaul.
The engine manufacturer recommended that the engine type was to be overhauled on accumulating 2,000 hours, time-in-service or every 12 years. Continued operation in service beyond 12 years was permitted provided the continuing airworthiness requirements of CASA AD/ENG/4 Amendment 11 for ‘on-condition’[4] operation was met. Additional maintenance related information is addressed in Airworthiness directives and airworthiness bulletins.
This engine was installed in VH-UDQ in September 2021. The aircraft owner reported that the engine was replaced by the former owner prior to the sale of the aircraft. The engine had accumulated 27.4 hours since it was installed and the time of the accident.
A piston engine condition report conducted at the 100‑hour inspection addressed the continuing airworthiness requirements did not identify any faults with the engine. The available aircraft records did not contain maintenance activity related to engine‑driven fuel pump replacement or repair.
Airframe information
At the last 100-hour periodic inspection on 14 September 2022, a maintenance release was issued, permitting day VFR operations and showed that the airframe had accumulated 19,128.3 hours, time-in-service.
Refurbishment
Prior to the 100-hour inspection, the aircraft had been refurbished by the current owner. The refurbishment included new external livery and replacement of interior furnishings. The interior refurbishment included re-covering of the seats with leather and the renewal of cabin and baggage compartment linings and floor panels. The owner confirmed that the backing material used for some of the cabin and baggage compartment linings were of carbon fibre construction. Details of the specific furnishings used in the aircraft were not recorded in the aircraft maintenance log books.
Meteorological information
The Maitland weather observation recorded at 1400 was wind from 160º at 12 kt, greater than 10 km visibility, cloud bases broken at 3,500 ft and 7,900 ft above airfield elevation, temperature and dew point of 21º and 14º respectively, and QNH 1019 hPa with no rainfall recorded since 0900. The ten‑minute weather observations for Maitland recorded the wind direction from 165º at 11 kt with a maximum gust of 14 kt in the period 1350-1400.
Luskintyre airfield
Luskintyre airfield is located about 8 km to the north-west of Maitland Airport. The airfield consists of a grass runway 12/30[5] which is 760 m long. The airfield has an elevation of about 35 m above mean sea level and is surrounded by fenced pastures containing dwellings and occasional stands of trees lining boundary fences.
Recorded data
Flight information sourced from AvPlan[6] indicated that at about 1358, VH-UDQ completed the orbit of Luskintyre airfield and commenced a descending turn to the right, reducing altitude from 1,863 ft AGL at 1358:02 to 1,597 ft at 1358:22. By 1358:32, VH-UDQ had begun a left turn and by 1358:42 was at 1,273 ft in an established turn and descending towards Luskintyre airfield. The final turn resulted in a tailwind component as the aircraft descended (Figure 3).
Figure 3: Aircraft flight - final turn towards Luskintyre airfield with time stamps
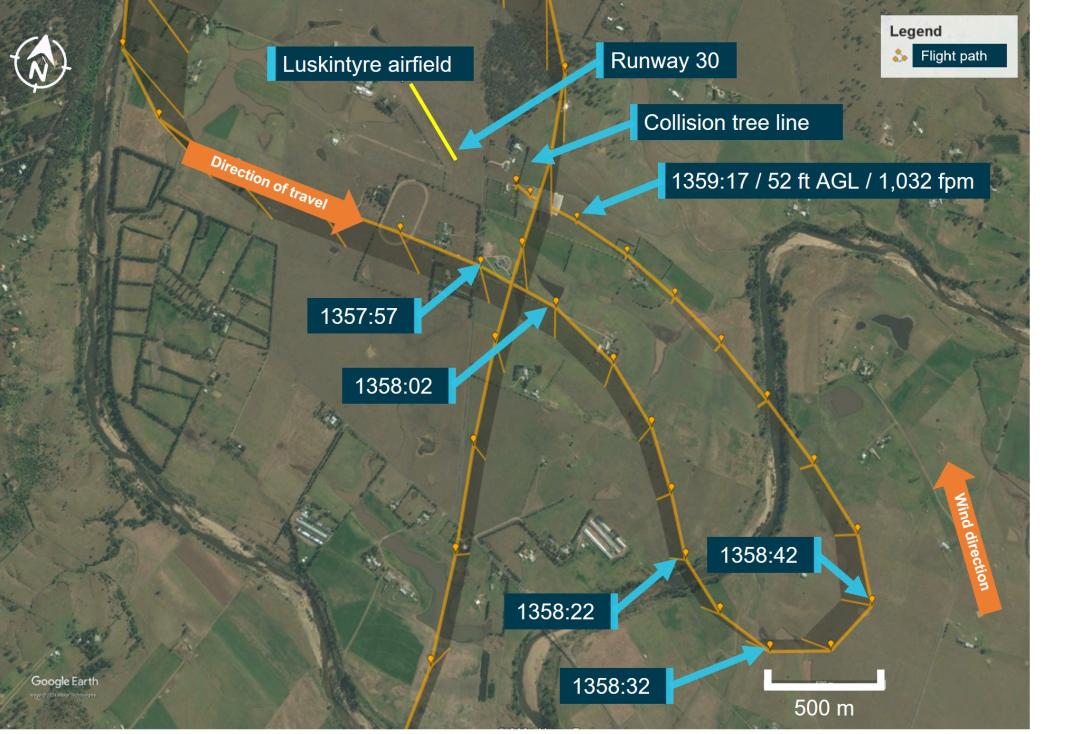
Image description: Overhead view of flight path with displayed height referenced to the elevation of Luskintyre airfield.
Source: AvPlan and Google, annotated by ATSB
Analysis of the data when VH-UDQ was established in the final turn and approach to the tree line, indicated that the aircraft rate of descent peaked at 3,504 feet per minute. Prior to initial ground contact, when at 52 ft AGL, the rate of descent was 1,032 feet per minute and a ground speed of 108 kt was recorded (Table 1).
Table 1: Aircraft performance during descent towards Luskintyre airfield
Time (local) |
Groundspeed (kt) |
Altitude (ft - AGL) |
Average rate of descent (ft/min) |
1358:27 |
91 |
1,522 |
- |
1358:42 |
94 |
1,273 |
996 |
1358:47 |
106 |
981 |
3,504 |
1358:57 |
124 |
551 |
2,580 |
1359:12 |
111 |
138 |
1,652 |
1359:17 |
108 |
52 |
1,032 |
Source: ATSB
Emergency procedures
The Mooney M20 pilot’s operating handbook (POH) advised pilots that in the event of an engine fire in‑flight, the emergency is to be treated in the following manner:
- Fuel Selector Valve – OFF
- Throttle and mixture – CLOSED and at IDLE CUTOFF
- Cabin ventilation and heating controls – CLOSED
- Landing gear – UP or DOWN, depending on terrain
- Flaps – Extend as necessary
The POH noted that if the fire is not extinguished, pilots should attempt to increase the airflow over the engine by increasing the glide speed and to attempt a power off landing. They should not attempt to restart the engine.
For a power off landing associated with an engine failure, the POH advised pilots to secure the engine by moving the mixture control to the idle cut-off position and to switch the magnetos off. Wing flaps were to be set to the full down position and undercarriage selected as necessary. Prior to landing, the master switch was to be in the off position and the aircraft approach speed to be 71 kts indicated airspeed.
Site and wreckage information
The initial ground contact points were tyre marks in a grass field ahead of a tree line that separated two grass fields and was located about 330 metres before the runway 30 threshold. The tyre marks began about 67 metres from the tree line and ended about 22 metres before the tree line, indicating that VH-UDQ had become airborne again before colliding with the trees in a near-level attitude. The collision with the closely spaced trees separated the wings from the fuselage and was followed by a progressive break-up of the rest of the aircraft. The resulting wreckage trail was spread over a distance of about 70 metres, on a heading of about 282 degrees (magnetic). Ignited fuel from the ruptured wing tanks created the initial fireball reported by witnesses and generated an intense post‑impact fire that consumed the cockpit and cabin area of the fuselage (Figure 4).
Figure 4: VH-UDQ wreckage trail and location of major items
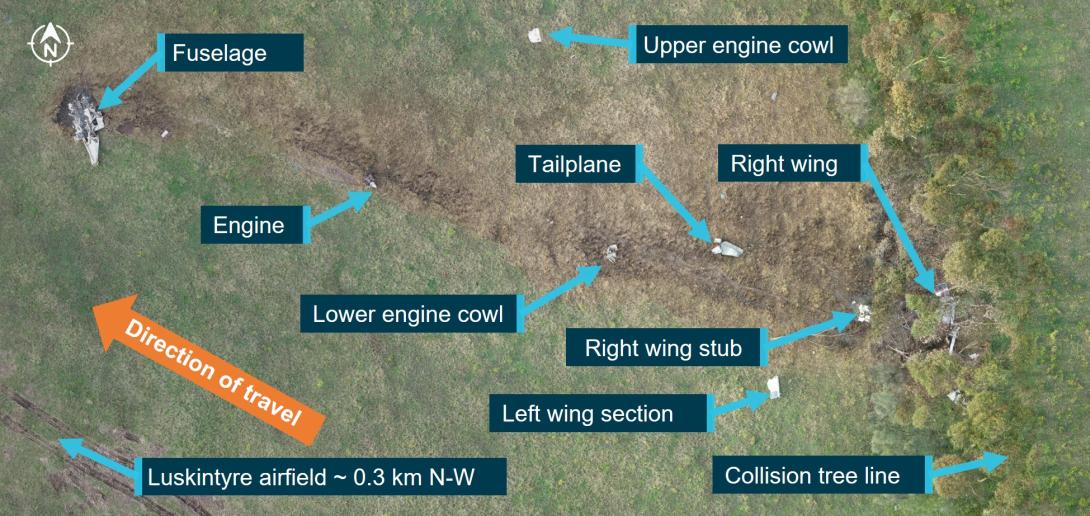
Source: ATSB
The complete aircraft was present at the accident site with all the flight control surfaces and major components accounted for. Examination of the aircraft control systems did not identify any defects that may have affected control of the aircraft. When examining the fuselage remains, the ATSB identified sections of carbon-fibre based products in the aircraft cabin and baggage compartment.
The nose undercarriage was noted to be in the down and locked position however the left and right main undercarriages were found housed in the wheel wells. The main undercarriage actuation and locking mechanism was found to be broken and the damage attributed to the wings separating from the fuselage.
The flap and tailplane trim actuators were retrieved from the accident site and details of their respective jack screw positions were provided to the aircraft manufacturer for comment. The aircraft manufacturer reported that in consideration of the position of the flap jack screw, the wing flaps were set in a slightly down position. The tailplane trim position could not be accurately determined.
Assessment of ground slash marks created by propeller rotation indicated that the propeller was operating between 1,590 and 1,150 revolutions per minute.[7] The engine manufacturer reported that the propeller speed was above that expected for an engine to be windmilling.
Due to the post-impact fire, the position prior to impact of cockpit switches and magneto selection, the fuel selector valve, the throttle and mixture controls, and the cabin ventilation and heating controls, could not be determined.
Engine examination
A detailed engine examination was undertaken at the ATSB technical facilities in Canberra, ACT. The following observations were noted:
- Evidence of scorching and soot residue on engine hoses and components, presented as a distinct flame path that commenced at the rear of the engine and progressed to the front (Figure 5).
- The origin of the engine fire was localised to the area surrounding the engine-driven fuel pump.
- Pressure testing of the engine fuel supply and distribution hoses did not reveal any fluid leak associated with a hose defect.
- Pressure testing of the engine-driven, mechanical fuel pump detected fluid leakage at the base of the fuel outlet fitting of the pump.
Figure 5: Underside of engine showing components and direction of flame travel
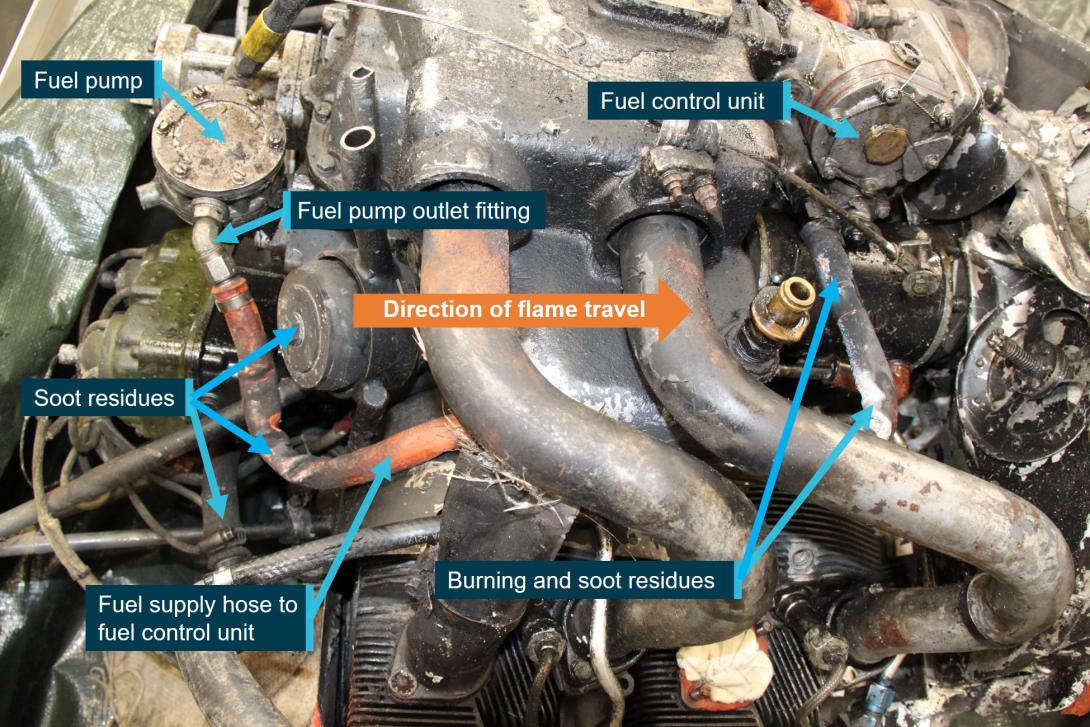
Source: ATSB
The fuel pump inlet and outlet fittings were removed to allow for examination of the O-ring seals installed between the fittings and the fuel pump body. Inspection of the outlet fitting seal revealed a deteriorated elastomer that had lost its pliability and its round, cross‑sectional shape. Further, the seal showed signs of permanent deformation and contained surface defects (Figure 6).
Figure 6: Fuel pump fittings and O-ring seals showing loss of natural shape and surface defects
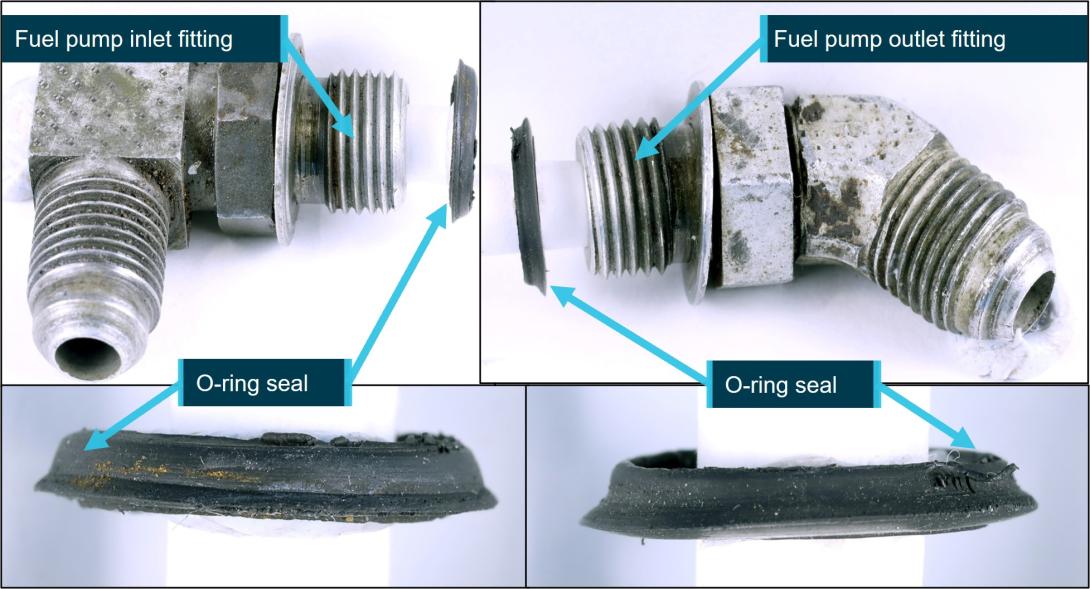
Source: ATSB
The inlet fitting seal exhibited similar in-service defects as the outlet fitting seal, however the deterioration had not progressed to failing to provide an effective seal. The examination indicated that fuel under pressure was leaking past the outlet fitting O-ring.
Maintenance records and requirements
Responsibility of registered operators – conduct and recording of maintenance
Section 3 of the Civil Aviation Act 1988, describes maintenance as:
Any task required to ensure, or that could affect, the continuing airworthiness of an aircraft or aeronautical product, including one or a combination of overhaul, repair, inspection, replacement of an aeronautical product, modification or defect rectification.
The owner or if appointed, the registered operator is responsible for the airworthiness and maintenance control of the aircraft to ensure its safe operation. Provision for the recording and certification of maintenance that is carried out are contained in the aircraft logbooks.
Maintenance activity or modifications which may include repainting of exterior surfaces or internal furnishings renewal, may change the aircraft’s empty weight and its centre of gravity position. If the change varies by more than the specified amount detailed in the aircraft’s weight and balance record, or the effect of the change is unknown, the aircraft may need to be re-weighed to determine its new empty weight and centre of gravity position. Maintaining the accuracy of the aircraft’s weight and balance information is necessary to ensure that changes do not adversely impact the performance of the aircraft as published in the aircraft flight manual.
To ensure that aircraft type certification standards are maintained and occupant survivability in the case of fire is not further degraded, modifications that include changes to materials used in interior furnishings are subject to approval by an authorised entity. The approval process will likely involve testing of the materials to evaluate their flash or flame resistance.
Airworthiness directives and airworthiness bulletins
An airworthiness directive (AD) is a document issued by the aircraft State of Design or CASA, if an unsafe condition exists in a kind of aircraft or aeronautical product. Registered operators are to comply with the requirements of an AD or an approved alternate means of compliance. CASA also issues Airworthiness Bulletins (AWBs) to inform the aviation public of essential information or make recommendations that are not considered mandatory.
Airworthiness directives – continuing airworthiness of aircraft and aeronautical products
CASA airworthiness directive AD/ENG/4, Piston engine continuing airworthiness requirements, was first issued in March 1995. Amendment 11 became effective on 15 January 2009 and specified the piston engine continuing airworthiness requirements. It required that registered operators of aircraft operated in either the private or airwork categories, in addition to scheduled engine maintenance, conduct additional maintenance actions to confirm the serviceability of the engine.
AD/ENG/04 also referenced CASA Airworthiness Bulletin AWB 85-004, Aircraft piston engine calendar time overhaul, that provided guidelines for additional inspections related to engine calendar time overhaul. The purpose of this AWB was specified as:
This AWB provides guidelines for procedures to be followed to ensure continued airworthiness of the engines that have exceeded the calendar time overhaul limits specified by the manufacturer. These guidelines are in addition to the recommendations by the manufacturers relating to inspections for corrosion.
The AWB highlights corrosion and degradation of elastomers as factors contributing to engine deterioration associated with calendar time. The AWB recommended inspecting elastomer components such as engine mounts, hoses and other elastomer related items for deterioration, however O-ring seals fitted to engine components were not specifically mentioned.
Airworthiness Bulletins
While airworthiness bulletins are for information only, they contain useful information concerned with the airworthiness of aircraft and aeronautical products. CASA recommends that all aircraft owners, and other key stakeholders involved in the operation or maintenance of aircraft, review AWBs for applicability and take any action they consider appropriate.
Airworthiness Bulletin AWB 02-1, On-condition maintenance, was issued on 27 November 2001, and provided information relating to ‘on-condition’ maintenance.
‘On-condition’ maintenance means that the condition of the item is monitored continuously or at specified intervals. When its performance or physical appearance is observed to no longer meet an appropriate standard, the resultant action is the removal of the item before it fails in service. Items in the engine may remain in service longer than the manufacturer recommended time‑in‑service, provided they continue to meet desired physical conditions and performance standards. The AWB identified that ‘on-condition’ is not an opportunity to fit and forget until a failure occurs. The AWB further advised that the condition of an item may require appropriate judgement to determine that failure of the item will not occur prior to the next scheduled inspection.
CASA recommended that where applicable, certificate of registration holders utilise the philosophy of ‘on condition’ maintenance to detect the potential for failures of critical items or products, especially when the time-in-service is approaching the manufacturer’s recommended overhaul period.
Flammability resistance
CASA (2011) AWB 25-016 Cabin interior and cargo compartment flammability provided guidance regarding flammability requirements for aircraft material and advised that when repairing or replacing interior material in an existing aircraft, the applicable flammability requirements are to be understood, and compliance with, is shown.
Factors to consider are the minimum flammability requirements for the aircraft, which is dependent on the aircraft category and the standard applicable at the time that the aircraft was first certificated. Certification information is contained in a document usually referred to as the Type Certificate Data Sheet.
The Type Certificate Data Sheet for the Mooney M20 showed that the aircraft was certified under Part 3 of the United States Civil Air Regulations as amended in 1956, which required that materials making up the cabin interior be ‘flash resistant’, or ‘flame resistant’ if the compartment could be used for (cigarette) smoking.
For a material to be flash resistant, AWB 25-016 notes that the material is to be of a type that is not susceptible to burning violently when ignited. To be flame resistant, it is not to be susceptible to combustion to the point of propagating a flame beyond a limit when the ignition source is removed.
Elastomer type products used in aircraft systems
Aircraft and engine systems carrying petroleum-based products use fluid carrying hoses, seals and gaskets that commonly involve nitrile rubber in the manufacturing process (Brink, Czernik and Horve, 1993). Nitrile rubber is a widely used, synthetic elastomer that is resistant to oil, fuel and chemicals with inherent properties that include tear and abrasion resistance, tensile strength, resilience,[8] and compression set.[9] Distinguishing characteristics of elastomer type products are their ability to be stretched up to several hundred percent and given their ability to store energy, to return to their near original shape when significantly compressed (Brady and Clauser,1991). Hoses, seals and gaskets are normally subject to handling, inspection and replacement requirements while in service.
Following installation, standard aviation maintenance practices described in US Advisory Circular AC-43-13, Acceptable methods, techniques and practices-aircraft inspection and repair (FAA, 1998), require that O-ring seals should not be re-used if disturbed during maintenance or disassembly of the part to which they are fitted. The O-ring seal may have swelled from exposure to fluid, hardened over time, or gained a permanent set. When installed as a gasket within a recessed area to seal a fluid carrying fitting, leaks are not normally acceptable. However, opportunities to replace or physically examine O-ring seals are reliant on scheduled maintenance where the component to which they are fitted is targeted for attention, or unscheduled maintenance in response to the component developing a defect when in service.
As specified by the Logbook Statement,[10] contained in VH-UDQ’s logbook, when considering aircraft components, reference is to be made to the overhaul and replacement schedule provided in the Mooney M20J aircraft maintenance manual. The schedule specifies that fuel and oil system flexible hoses containing elastomer type material are replaced every two to seven years, or at engine overhaul, whichever occurs first. The schedule also specifies that all other fuel and oil system components such as an engine‑driven fuel pump are treated as on-condition items and may remain in service until an inspection, or their performance reveals an unserviceable condition.
Additional information
Annex 13 to the convention on international civil aviation is published by the International Civil Aviation Organization and details the standards and recommended practices for aircraft accident and incident investigation. For statistical purposes, an injury is classified as a fatal injury when death results within thirty days of the date of the accident. The pilot involved in this accident did not succumb to injuries until after the 30-day period, and therefore, the accident is not registered as a fatal collision, despite the outcome.
Related occurrences
Between 2014 and 2023, the ATSB investigated two accidents (described below) involving aircraft in-flight fires that resulted in a fatality or serious injuries. In one accident, the origin of the fire was attributed to burning oil due to engine failure while the other was attributed to a fuel-fed cabin fire.
ATSB investigation AO-2014-059
On 28 March 2014, the pilot of a Cessna Aircraft Company 210L aircraft departed Numbulwar, Northern Territory, on a charter flight with one passenger on board for a return flight to Tindal, Northern Territory.
When about 22 NM west of Numbulwar, smoke was detected in the cabin and following a ‘MAYDAY’ call advising of an engine failure, the pilot applied the cabin fire extinguisher which quickly stopped the smoke. The aircraft landed heavily and collided with trees. The pilot and passenger suffered serious injuries and the aircraft was destroyed.
The ATSB determined that a piston connecting rod broke resulting in a catastrophic engine failure. The smoke entering the cockpit was likely from burning oil.
ATSB investigation AO-2022-026
On 16 April 2022, the pilot of a Beechcraft B58 Baron aircraft, on a charter flight with one passenger on board from Broome Western Australia, commenced a straight in approach to runway 12 at the East Kimberley Regional Airport, Western Australia.
When attempting to extend the landing gear, smoke emerged from forward of the pilot’s circuit breaker panel. The pilot made a PAN-PAN call, by which time flames were observed to be coming from the area of the source of the smoke. Attempts to extinguish the fire were unsuccessful with flames and thick smoke filling the cockpit.
The aircraft collided with terrain about 800 m from the threshold of runway 12 and was consumed by the post-impact fire. The passenger succumbed to their injuries and the pilot received serious injuries.
The ATSB determined that a fault associated with the landing gear electrical system likely ignited fuel from the cabin heater supply line, resulting in a significant and sustained cockpit fire.
NTSB investigation
A similar occurrence in the United States was investigated by the National Transportation Safety Board. The accident was attributed to an engine compartment fuel leak and described in NTSB report, ERA17LA284 as summarised below.
On August 20, 2017, the pilot of a Mooney M20C aircraft registered N6833N departed Palm Coast, Florida on a private flight with one passenger on board to Fort Lauderdale, Florida.
During take‑off and climb the pilot noticed that the engine was losing power. Upon reaching 400 ft above ground level the engine lost total power. During touchdown for the subsequent forced landing to a road, the pilot noticed flames coming into the cabin near the passenger’s feet. The pilot was able to stop the aircraft and both occupants were able to egress quickly after landing.
The pilot and passenger were not injured however the aircraft was substantially damaged.
The NTSB investigation found that a crack in the engine’s No. 4 cylinder resulted in a rough running engine and a subsequent loss of power. The increased vibration loosened a fuel line fitting that generated a fuel leak and was the source of the in-flight fire.
Safety analysis
Introduction
On 17 October 2022, at about 1345 the pilot of a Mooney Aircraft Corporation M20J aircraft, registered VH-UDQ, departed Maitland Airport, NSW for a flight in the local area. While overhead Luskintyre airfield the pilot broadcast an intent to track to Maitland Airport. However, witnesses nearby saw the aircraft descending towards Luskintyre airfield while trailing smoke and flames. Following an initial touch-down in a grass field, VH-UDQ collided with a line of trees. The witnesses described an explosion and accompanying fireball. The pilot was seriously injured but subsequently succumbed to injuries after 10 weeks. The aircraft was destroyed.
The following analysis will consider the cause of the in-flight engine compartment fire, the O‑ring seals of the engine fuel pump, and the recording of maintenance activity in the aircraft logbook. The risk to occupant safety when substituting materials used for interior furnishings is also discussed.
Fire and emergency descent
Witnesses in the area reported flames and smoke coming from the aircraft, and the pilot reported to first responders that the engine was on fire and that they had inhaled smoke. In consideration of the leak found with the engine-driven fuel pump outlet O‑ring seal (see O‑ring seal replacement below), it was likely that fuel leaking from the pump outlet fitting produced a vapor that was ignited by heat in the lower engine compartment.
Given that the pilot made a normal, inbound call for a landing at Maitland Airport, it is likely the pilot only became aware of the presence and/or extent of the engine compartment fire after the orbit of Luskintyre airfield and after the inbound call. However, once the pilot became aware of the fire, they abandoned their intention to land at Maitland Airport and the flight path suggests they instead intended to land at Luskintyre airfield due to its proximity.
The approach towards runway 30 at Luskintyre airfield was at a very high rate of descent, which was consistent with an emergency reaction to a fire that the pilot perceived as high risk to their safety. The available recorded data shows that the descent from 1,522 ft to 52 ft occurred in 50 seconds. From the available evidence it was not clear if, during that time, all of the pilot operating handbook checklist items for an in-flight fire were conducted. One item included cutting off fuel to reduce the source of fire, but the calculated propeller speed at collision suggested that the engine was rotating at well above windmilling speed and was not consistent with configuring the aircraft for a power off landing.
While a landing on a runway is generally safer than in a field, the high descent rate close to the ground may have limited the pilot’s ability to reach runway 30. However, it is also possible that the pilot was becoming more affected by heat, fire and/or smoke as the aircraft descended, and made a decision to land in the paddock to expedite the landing.
The relatively wings-level attitude when the aircraft touched down and then collided with the tree line indicates the aircraft was in an attitude appropriate for landing, albeit at a high ground speed and descent rate. The high speed at which the aircraft’s wheels first contacted the ground and the proximity of the tree line from the initial ground contact point indicated that the collision with trees and subsequent break-up of the aircraft was unavoidable. The release and atomisation of fuel as the wings separated from the fuselage was likely ignited by the pre-existing fire within the engine compartment and the generated heat ignited combustible materials of the aircraft.
As the fuselage was subsequently consumed by the post-impact fire, it was not possible to determine whether cockpit furnishings had started to burn in-flight due to radiant heat from the engine compartment fire, or that cockpit related smoke in-flight, contributed to the reported smoke inhalation.
O-ring seal replacement
An engine compartment fuel leak during the accident flight originated from the engine‑driven, mechanical fuel pump outlet fitting due to an O‑ring seal that had deteriorated with age and had lost the ability to provide an adequate seal. Maintenance related standard practices specify that O‑ring seals are not reused, and they should be replaced when disturbed during maintenance or when a leak is detected.
Unlike the engine fluid carrying hoses that were periodically replaced per the aircraft’s maintenance schedule, the fuel pump and the O-ring seals were on condition and had not required replacement while the engine was in service. Additionally, the maintenance records did not contain evidence of other opportunities to access and physically examine the condition of the O-ring seals that are normally hidden from view when installed on the fuel pump fittings.
O-ring seals were not specifically identified in the broad classification of elastomer type products described in CASA airworthiness bulletin AWB 85-004. Since the O-ring seals were not specifically targeted for attention, this may have resulted in them being overlooked for proactive replacement of easily accessible seals.
In the absence of physical examination or replacement opportunity, assurance that the O‑ring seals were functional, was reliant on checking for fluid leaks at specific intervals. When last inspected it was likely that no discernible leak was detected at the fuel pump outlet fitting. However, the engine was about 17.5 years past its normal overhaul calendar life and the potential for a leak to develop between scheduled inspection intervals was increasingly likely as the O‑ring seals continued to age. A review of the records may have identified the prolonged time-in-service of O‑ring seals, and if documented, the modifications that may have affected the weight of the aircraft, or the flammability attributes of materials used during interior refurbishment.
Flammability assessment
The interest in giving the aircraft a renewed look may have influenced the selection of products as interior furnishings. The use of alternate products was not prohibited. However, to understand the risk associated with substituting materials, an assessment of the substituted materials’ flammability was required. When conducted, the assessment would have indicated the suitability of the material in terms of potential impact on occupant safety in the case of a fire.
Regarding material type, those having flame or flash resistant attributes were permitted for use as cabin furnishings and was dependent on whether smoking was permitted in the aircraft. Considering the common practice of not permitting smoking in aircraft interiors, assurance that occupant safety was not compromised could have been achieved by using products that at a minimum, were determined to be flash resistant. However, a record of their use and their suitability needed to be included in the aircraft records.
Due to the intensity of the post-impact fire, and the lack of records, the ATSB was unable to determine the full extent of product or material substitution, or whether the replacement materials had fed or suppressed the fire.
Findings
ATSB investigation report findings focus on safety factors (that is, events and conditions that increase risk). Safety factors include ‘contributing factors’ and ‘other factors that increased risk’ (that is, factors that did not meet the definition of a contributing factor for this occurrence but were still considered important to include in the report for the purpose of increasing awareness and enhancing safety). In addition, ‘other findings’ may be included to provide important information about topics other than safety factors. These findings should not be read as apportioning blame or liability to any particular organisation or individual. |
From the evidence available, the following findings are made with respect to the collision with terrain involving Mooney Aircraft Corporation M20J, registration VH-UDQ, near Luskintyre airfield, NSW on 17 October 2022.
Contributing factors
- In response to an engine compartment fire, the pilot initiated an emergency descent towards the runway but subsequently landed in a field resulting in the aircraft impacting trees. That led to a break-up of the aircraft and a severe post‑impact fire that consumed the aircraft.
- An O-ring seal fitted to the engine-driven fuel pump outlet fitting remained in service until it became age-affected and failed to provide an effective seal. The escaping fuel ignited and created an engine compartment fire.
Other factors that increased risk
- The aircraft had recently been refurbished and changes included new external livery and replacement of interior furnishings. The aircraft records did not indicate that the refurbishment had been conducted, and consequently, there was no evidence of a flammability assessment for the materials used.
Safety actions
Whether or not the ATSB identifies safety issues in the course of an investigation, relevant organisations may proactively initiate safety action in order to reduce their safety risk. All of the directly involved parties are invited to provide submissions to this draft report. As part of that process, each organisation is asked to communicate what safety actions, if any, they have carried out to reduce the risk associated with this type of occurrences in the future. The ATSB has so far been advised of the following proactive safety action in response to this occurrence. |
Safety action by the ATSB
In response to this accident, the ATSB has issued safety advisory notice SAN AO‑2022‑049‑001 in conjunction with this investigation report. The safety advisory notice draws attention to the management of O-ring seals in engine components and their pro‑active removal from service, should inspection of aircraft records indicate a significant time‑in‑service.
Safety Action by the Civil Aviation Safety Authority
In response to the investigation finding related to deteriorated O-ring seals, the Civil Aviation Safety Authority proposed to review Airworthiness Bulletins AWB 02-001 and AWB 85-004 and most likely update them. The update would serve as a reminder to industry of some of the concepts and philosophy related to ‘on-condition’, which is not a ‘fit and forget’ approach to preventative maintenance.
Sources and submissions
Sources of information
The sources of information during the investigation included the:
- Civil Aviation Safety Authority
- aircraft manufacturer
- registered operator
- maintenance organisation for VH-UDQ
- accident witnesses
- recorded data from AvPlan.
References
Brady, G.S. and Clauser, H. R. (1991), Materials Handbook: An Encyclopaedia for Managers, Technical Professionals, Purchasing and Production Managers, Technicians, Supervisors, and Foremen, McGraw-Hill, Inc. New York, NY, USA
Brink, R.V., Czernik, D.E., and Horve, L.A. (1993), Handbook of fluid sealing, McGraw-Hill, Inc. New York, NY, USA.
Civil Aviation Safety Authority (2001), Airworthiness Bulletin AWB 02-1 Issue 1, On-condition maintenance, Civil Aviation Safety Authority, Canberra, ACT, Australia.
Civil Aviation Safety Authority (2005), Airworthiness Bulletin AWB 85-004 Issue 1, Aircraft Piston Engine Calendar Time Overhaul, Civil Aviation Safety Authority, Canberra, ACT, Australia.
Civil Aviation Safety Authority (2009), Airworthiness Directive, AD/ENG/4 Amendment 11, Piston Engine Continuing Airworthiness Requirements, Civil Aviation Safety Authority, Canberra, ACT, Australia.
Civil Aviation Safety Authority (2016), Airworthiness Bulletin AWB 25-016 Issue 2, Cabin Interior and Cargo Compartment Flammability, Civil Aviation Safety Authority, Canberra, ACT, Australia.
Civil Aviation Safety Authority (2017), Airworthiness Bulletin AWB 00-001 Issue 3, Airworthiness Bulletins, Civil Aviation Safety Authority, Canberra, ACT, Australia.
Federal Aviation Administration (1998), Advisory Circular 43.13-1B, Acceptable methods, techniques and practices-aircraft inspection and repair, U.S. Department of Transportation, Oklahoma City, OK, USA.
Submissions
Under section 26 of the Transport Safety Investigation Act 2003, the ATSB may provide a draft report, on a confidential basis, to any person whom the ATSB considers appropriate. That section allows a person receiving a draft report to make submissions to the ATSB about the draft report.
A draft of this report was provided to the following directly involved parties:
- aircraft manufacturer
- Civil Aviation Safety Authority
- engine manufacturer
- National Transportation Safety Board
- registered operator/owner.
Submissions were received from the Civil Aviation Safety Authority.
The submissions were reviewed and, where considered appropriate, the text of the report was amended accordingly.
Purpose of safety investigationsThe objective of a safety investigation is to enhance transport safety. This is done through:
It is not a function of the ATSB to apportion blame or provide a means for determining liability. At the same time, an investigation report must include factual material of sufficient weight to support the analysis and findings. At all times the ATSB endeavours to balance the use of material that could imply adverse comment with the need to properly explain what happened, and why, in a fair and unbiased manner. The ATSB does not investigate for the purpose of taking administrative, regulatory or criminal action. TerminologyAn explanation of terminology used in ATSB investigation reports is available here. This includes terms such as occurrence, contributing factor, other factor that increased risk, and safety issue. Publishing informationReleased in accordance with section 25 of the Transport Safety Investigation Act 2003 Published by: Australian Transport Safety Bureau © Commonwealth of Australia 2024 Ownership of intellectual property rights in this publication Unless otherwise noted, copyright (and any other intellectual property rights, if any) in this report publication is owned by the Commonwealth of Australia. Creative Commons licence With the exception of the Coat of Arms, ATSB logo, and photos and graphics in which a third party holds copyright, this publication is licensed under a Creative Commons Attribution 3.0 Australia licence. Creative Commons Attribution 3.0 Australia Licence is a standard form licence agreement that allows you to copy, distribute, transmit and adapt this publication provided that you attribute the work. The ATSB’s preference is that you attribute this publication (and any material sourced from it) using the following wording: Source: Australian Transport Safety Bureau Copyright in material obtained from other agencies, private individuals or organisations, belongs to those agencies, individuals or organisations. Where you wish to use their material, you will need to contact them directly. |
[1] All heights in this report are referenced to the Luskintyre airfield elevation of 35 m (115 ft)
[2] Common traffic advisory frequency (CTAF): a local VHF radio frequency used for air‑to‑air communication at non‑towered airports. The frequency was shared between airfields in the local area that included Maitland and Cessnock Airports and Luskintyre airfield.
[3] Runway number: the number represents the magnetic heading of the runway.
[4] On-condition: A type of aircraft maintenance in which parts are replaced only when their condition appears no longer airworthy, instead of at pre-determined intervals of operation.
[5] Runway numbers: the number and its reciprocal represent the magnetic headings of the runways.
[6] AvPlan: the AvPlan EFB application allows users, with appropriate setting selected, to track and record flight path information based on the position of the device. This data can then be downloaded either from the device or from the application servers.
[7] RPM: Revolutions per minute – a measure of the speed of a rotating unit.
[8] Resilience: In material science, resilience is the ability of a material to absorb energy when it is deformed elastically and release that energy upon unloading. An ability to return to its original size and shape after deformation.
[9] The decrease in thickness of a rubber specimen which has been deformed under specific conditions of load, time and temperature.
[10] Log Book Statement: a document forming part of the log book that specifies an aircraft’s maintenance needs that includes CASA and the aircraft manufacturer’s requirements, any special conditions, and the validity period of the maintenance release.
[11] For statistical purposes, an injury is classified by the International Civil Aviation Organization as a fatal injury when death results within thirty days of the date of the accident.