What happened
At about 1109 Eastern Standard Time[1] on 20 April 2017, a Piper PA-28-161 aircraft, registered VH-SWV (SWV) taxied at Camden Airport, New South Wales for a private VFR[2] flight to the Blue Mountains. The pilot and a passenger were on board.
The pilot had conducted a pre-flight inspection of the aircraft and found everything to be serviceable. He had also flown the aircraft 2 days earlier and had not observed any problems with it.
Air traffic control (ATC) cleared SWV to taxi and informed the pilot that the wind was variable at about 5 kt and the QNH[3] was 1030 hPa. The pilot taxied SWV from the grass area where it was normally parked (Figure 1) to the engine run-up bay near the runway 06 threshold. The taxi time was about 1 minute and the taxi was conducted with the engine consuming fuel from the left-wing tank.
Figure 1: Aerial view of Camden Airport
Source: Google earth, annotated by the ATSB
At the run-up bay, the pilot conducted the engine run-up checks and found everything normal. He turned on the auxiliary fuel pump during the engine checks and, when ready to taxi, selected the right-wing fuel tank. The aircraft was then taxied to runway 06 holding point and the engine carburettor heat remained in the cold position. The pilot had previously been advised by ATC that there was another PA-28 aircraft in the circuit conducting a touch‑and‑go landing.[4]
At about 1114, when the pilot informed ATC that he was ready to take-off, he was issued a take-off clearance.
The pilot then lined up SWV on the runway 06 threshold and commenced the take-off. He noted that the engine indications were normal and the take-off was progressing normally. As the aircraft accelerated along the runway, it became airborne at the point the pilot expected (Figure 1).
When SWV was between 100‑200 ft above ground level (AGL), and not far past the runway 24 threshold, its engine ‘misfired’ and ‘coughed’ before an audible reduction in engine noise. The pilot recalled that the engine noise changed to a ‘humming’ but that the propeller continued rotating. He reported that he was using a passive noise reduction headset and was able to clearly hear the different aircraft and engine noises. The pilot saw that the vertical speed indicator (VSI) that had initially been indicating a positive climb of 400‑500 ft/min had decreased to 100‑200 ft/min.
The pilot assessed that the engine had experienced a partial power loss and adjusted the engine throttle in an attempt to restore full power. At the time, he believed there was enough engine power to remain in the circuit. At about 1115, he reported the engine problem to ATC and indicated that he would try to keep SWV in the circuit to land on runway 06.
The pilot noted the VSI was still positive and he started a slow turn to the left. Almost immediately, however, the engine began making a ‘coughing’ noise and stopped responding to throttle changes. A few seconds later, at about 160 ft AGL, the stall warning momentarily sounded. In response, the pilot lowered the aircraft’s nose to maintain airspeed and committed to a forced landing. At about 1116, another pilot broadcast ‘keep the nose down’ (about 25 seconds after SWV’s pilot had reported engine problems to ATC). A few months before the accident (late 2016), the pilot had conducted circuits and practiced forced landings during an aircraft flight review.
The pilot identified a small clearing between trees to the right and turned the aircraft toward that area. The aircraft continued to descend and about 8 seconds later, its right wing contacted the top of a tree. The aircraft then collided with the ground, spun around, and came to rest. The aircraft was substantially damaged (Figure 2) and fuel began leaking from its ruptured right fuel tank. The damaged right wing blocked the exit door; however, the front windscreen fractured on impact and provided an egress path for the occupants.
Figure 2: Accident site of Piper PA-28-161, VH-SWV
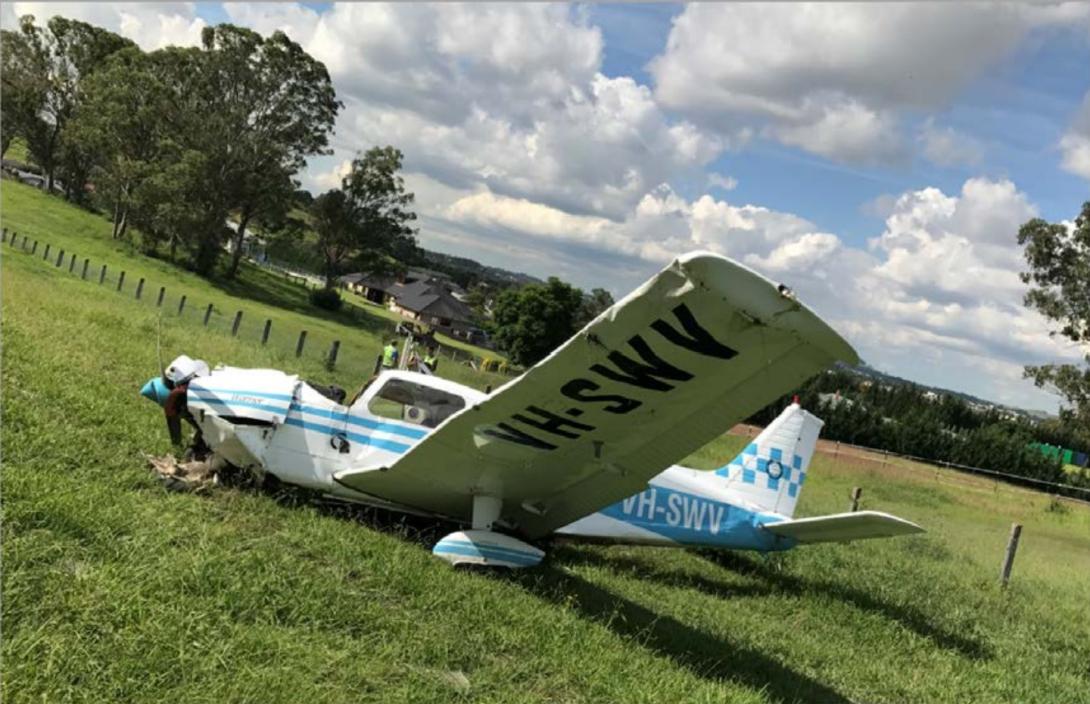
Source: NSW Police
At about 1119, a police helicopter that had been airborne in the area landed to assist. The helicopter crew helped the pilot and passenger to evacuate the aircraft and provided them with first aid. Both of them sustained serious injuries and were subsequently transported to hospital.
Post-accident inspection
The aircraft operator advised that an aircraft maintenance engineer conducted a post-accident inspection of the aircraft. The engineer found the fuel selector set to the right fuel tank and the electric boost pump switch in the ON position. About 25 L of fuel was drained from the damaged right fuel tank from which fuel had leaked after the accident. The pilot reported that a total of 120 L of fuel was on board the aircraft prior to the engine start – measured as 70 L in the right-wing tank and 50 L in the left tank.
Fuel was also found in the gascolator (main fuel strainer and drain for water and small particles) and the engine carburettor bowl. No water was evident in the fuel sample taken. The engine was removed from the aircraft and a complete test of its operation was carried out. That test did not identify any problem with the engine.
Aircraft maintenance
On 3 December 2016, a 100-hour/12-month periodic maintenance inspection of the aircraft was completed and a maintenance release was issued. An overhauled engine was installed at the time of that inspection. The engine carburettor was overhauled and two new magnetos were also installed at that time.
Since the December 2016 periodic inspection, the aircraft had flown a total of 6.7 hours before the accident. The maintenance release identified the next maintenance was due at 10 hours (change of engine oil and filter). In the time since the periodic inspection, the aircraft had not been flown for extended periods. These included a 29-day period over December/January and, more recently, a 91-day period until 2 days before the accident. Another pilot had flown SWV on the day before the accident and no defects were recorded on the aircraft’s maintenance release.
Carburettor icing
Induction icing, often referred to as carburettor icing, is the accumulation of ice within the induction system of an engine fitted with a carburettor. This ice forms as the decreasing air pressure and introduction of fuel reduces the temperature within the induction system. The temperature may reduce sufficiently for moisture within the air to freeze and accumulate. This build-up of ice restricts airflow to the engine, leading to a reduction in engine performance.
The aircraft engine manufacturer, Lycoming, issued a service instruction, No. 1148C Use of Carburetor Heat Control[5], that applied to all its engines fitted with a float type carburettors, including SWV. The service instruction indicated that for take-off at full throttle, the carburettor heat should be selected to the full cold position. The service instruction also noted that the possibility of throttle icing at wide throttle openings, such as during take‑off, was very remote (may be dependent on the individual engine installation).
By its nature, any evidence of carburettor icing will rapidly dissipate at an accident site. However, the Civil Aviation Safety Authority’s Carburettor icing probability chart[6] (Figure 3) provided a guide to the likelihood of carburettor ice forming based on environmental conditions.
Figure 3: Carburettor icing probability chart (prevailing conditions shown in orange)
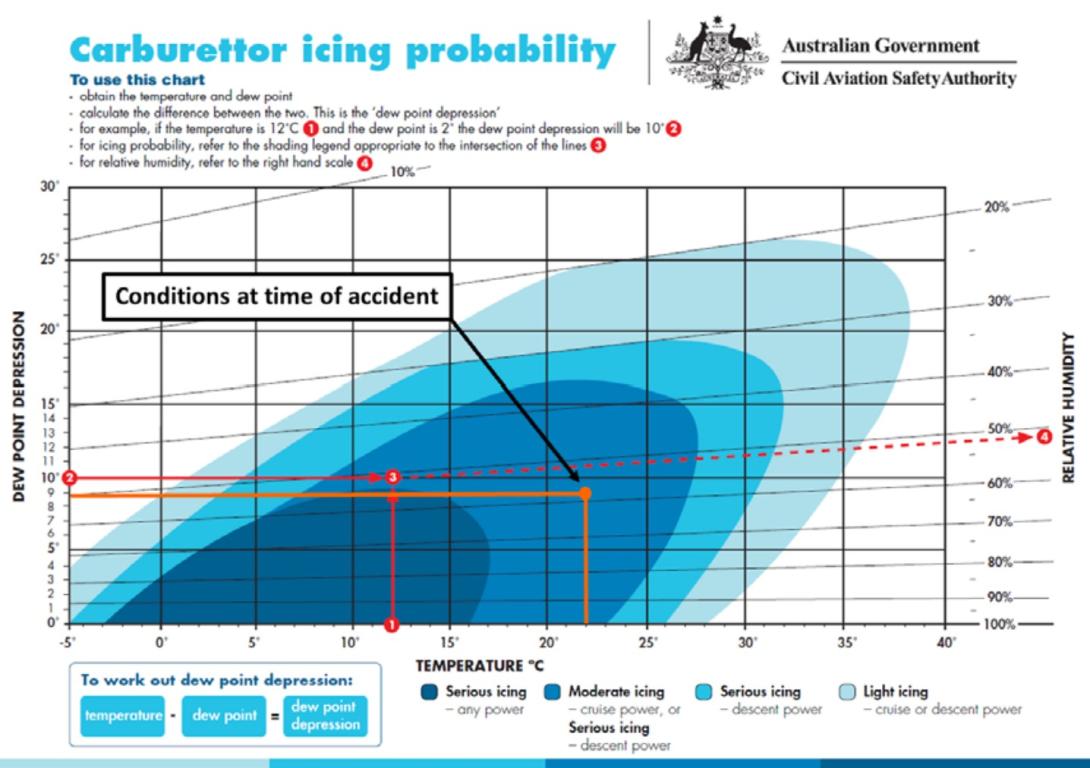
Source: CASA, annotated by ATSB
Safety analysis
Examination of the aircraft by the operator did not identify anything that may have contributed to the engine power loss. The potential for induction icing to have led to the power reduction was considered.
The relevant temperatures recorded by the Camden Airport automatic weather station at the time of the accident are shown below (Table 1).
Table 1: Weather conditions at Camden Airport
Time | Temperature (°C) | Dew point Temperature (°C) |
1109 | 23.0 | 13.5 |
1110 | 22.8 | 13.5 |
1111 | 23.0 | 13.5 |
1112 | 22.6 | 12.8 |
1113 | 22.4 | 13.2 |
1114 | 22.2 | 12.7 |
1115 | 22.0 | 13.1 |
The carburettor icing probability chart indicated that the probability of icing in the weather conditions at the time of accident was in the shaded royal blue area (orange dot in Figure 3). Therefore, moderate icing could be expected at cruise power setting and serious icing at descent power. The chart does not show icing probability at the higher take-off power setting at the time of the accident. However, based on the advice in the Lycoming service letter, the short period of operation at low power following the engine run-up and the icing probability chart, significant carburettor icing was considered unlikely.
Irrespective of the cause of the power loss, this occurrence highlights the short period of time available to the pilot to respond and manage the situation. The ATSB has produced a booklet, Avoidable Accidents No. 3 - Managing partial power loss after take-off in single-engine aircraft,[7] aimed at increasing awareness among flying instructors and pilots of the issues relating to partial power loss after take-off in single-engine aircraft. The key messages from the booklet emphasise the following strategies to minimise the risk of harm following a partial or complete power loss:
- pre-flight decision making and planning for emergencies and abnormal situations for the particular aerodrome
- conducting a thorough pre-flight and engine ground run to reduce the risk of a partial power loss occurring
- taking positive action and maintaining aircraft control either when turning back to the aerodrome or conducting a forced landing until on the ground, while being aware of flare energy and aircraft stall speeds.
On this occasion, the pilot maintained control of the aircraft throughout the emergency and acted decisively when it became apparent that there was insufficient engine power to return to the runway.
Findings
These findings should not be read as apportioning blame or liability to any particular organisation or individual.
- Following an engine power loss shortly after becoming airborne, the pilot conducted a forced landing having assessed that there was insufficient engine power to return to the runway.
- Post-accident tests of the engine and fuel did not identify a cause for the loss of engine power. Carburettor icing at take-off power in the environmental conditions at the time was unlikely to have resulted in the loss of power.
Safety message
The accident highlights the value of practicing emergency procedures as time, and the options available in an emergency, can be minimal. In this case, the pilot had practiced forced landings in his last flight review. That may have assisted his decisive action and maintenance of aircraft control when faced with the engine power loss at low altitude.
Purpose of safety investigationsThe objective of a safety investigation is to enhance transport safety. This is done through:
It is not a function of the ATSB to apportion blame or provide a means for determining liability. At the same time, an investigation report must include factual material of sufficient weight to support the analysis and findings. At all times the ATSB endeavours to balance the use of material that could imply adverse comment with the need to properly explain what happened, and why, in a fair and unbiased manner. The ATSB does not investigate for the purpose of taking administrative, regulatory or criminal action. TerminologyAn explanation of terminology used in ATSB investigation reports is available here. This includes terms such as occurrence, contributing factor, other factor that increased risk, and safety issue. Publishing informationReleased in accordance with section 25 of the Transport Safety Investigation Act 2003 Published by: Australian Transport Safety Bureau © Commonwealth of Australia 2018 Ownership of intellectual property rights in this publication Unless otherwise noted, copyright (and any other intellectual property rights, if any) in this report publication is owned by the Commonwealth of Australia. Creative Commons licence With the exception of the Coat of Arms, ATSB logo, and photos and graphics in which a third party holds copyright, this publication is licensed under a Creative Commons Attribution 3.0 Australia licence. Creative Commons Attribution 3.0 Australia Licence is a standard form licence agreement that allows you to copy, distribute, transmit and adapt this publication provided that you attribute the work. The ATSB’s preference is that you attribute this publication (and any material sourced from it) using the following wording: Source: Australian Transport Safety Bureau Copyright in material obtained from other agencies, private individuals or organisations, belongs to those agencies, individuals or organisations. Where you wish to use their material, you will need to contact them directly. |
- Eastern Standard Time was Universal Coordinated Time (UTC) + 10 hours.
- Visual flight rules (VFR): a set of regulations that permit a pilot to operate an aircraft only in weather conditions generally clear enough to allow the pilot to see where the aircraft is going.
- QNH: the altimeter barometric pressure subscale setting used to indicate the height above mean seal level.
- Touch-and-Go Landing: A procedure whereby an aircraft lands and takes off without coming to a stop.
- Available at www.lycoming.com/content/service-instruction-no-1148c
- Available at www.casa.gov.au
- Available at www.atsb.gov.au/publications/2010/avoidable-3-ar-2010-055/