Safety summary
What happened
On 18 November 2016, at about 1244 Eastern Standard Time, a Robinson R44 II helicopter, registered VH-ZNZ, broke-up in the Mount Windsor National Park, about 41 km north-west of Mossman, Queensland. The helicopter was on a charter flight with one pilot and one passenger on board. Following impact with the ground, the passenger was fatally injured, and the pilot was seriously injured. The helicopter was destroyed.
What the ATSB found
The ATSB found that one of the main rotor blades struck and separated a section of the tailcone of the helicopter from the airframe, which resulted in a near vertical descent of the helicopter main body through the forest canopy. The wreckage indicated there was low engine power and rotor speed at the time of the strike, which was likely the result of a main rotor blade stall event. The ATSB was unable to determine what precipitated the blade stall event.
The ATSB also found that the helicopter was likely operating in at least moderate turbulent flight conditions, which were not forecast. The turbulence was associated with a wind strength of 15‑25 kt in undulating terrain at a high-density altitude (reduction in ambient air density). The Pilot Operating Handbook did not prohibit flight in either the forecast or actual conditions, but the presence of moderate turbulence potentially placed the helicopter in an environment for which it had not been flight tested.
Safety message
This accident highlighted the importance of impact-activated emergency locator transmitters. The activation of the transmitter on impact was the trigger to start the search and rescue operation, and recover the pilot, who may otherwise have not survived. ATSB research report AR-2012-128 provides guidance to owners and operators on how they can maximise the reliability and effectiveness of emergency locator transmitters.
Although it could not be determined if the wind and associated turbulence contributed to the accident, it is important for pilots to consider the effect of the terrain on the weather forecast, which could result in their helicopter not achieving its predicted performance.
On 18 November 2016, at about 1244 Eastern Standard Time,[1] a Robinson R44 II helicopter, registered VH-ZNZ, broke-up in the Mount Windsor National Park, about 41 km north-west of Mossman, Queensland. The helicopter was on a charter flight with one pilot and one passenger on board. Following impact with terrain, the passenger was fatally injured and the pilot was seriously injured. The helicopter was destroyed.
The passenger was a contractor providing maintenance services (gas and plumbing inspections) for the Queensland Park and Wildlife Service (QPWS) Northern Estate facilities. He contracted the pilot’s company to provide the transportation services for the site inspections and they were on their fourth day of flying together. The pilot provided the service for the first 2 days with a Bell 206 helicopter. The Bell 206 became unserviceable the day prior to the accident and was replaced with the R44 for 17 and 18 November.
On 18 November, the helicopter departed from Cardwell and stopped at Mareeba Airport, where it was refuelled with 140 L (100 kg) of aviation gasoline at about 1006. It then proceeded to Mossman, where the passenger met QPWS staff. The QPWS staff provided the passenger with the geographic coordinates to locate two facilities for gas appliance inspections in the Mount Windsor National Park. They were the forestry barracks facility and station house facility.
Recorded track data from OzRunways[2] showed that the helicopter departed from the vicinity of the QPWS Mossman facility at about 1134 and tracked towards the Mount Windsor National Park. The last recorded track was at about 1144, at which time the helicopter was about 18 km to the south-east of the barracks facility and on a direct track towards it.[3]
At about 1244, the Australian Maritime Safety Authority’s Joint Rescue Coordination Centre (JRCC) detected a signal from the helicopter’s emergency locator transmitter. At about 1432, the helicopter wreckage was located in the dense rainforest of Mount Windsor National Park, about 500–600 m south-east of the barracks facility (refer to Figure 4 in the section titled Wreckage and impact information).
The helicopter was found to have broken into multiple fragments and the main body was subject to a post-impact fire. The pilot required hospitalisation for a number of weeks, which included five days under an induced coma, and subsequently had no recollection of the events on the day of the accident.
Figure 1 depicts the known flight path from recorded track data and the location of the accident site with key event timings. The end of the recorded track is consistent with an expected loss of coverage in that area at low level.[4]
Figure 1: VH-ZNZ track and accident site
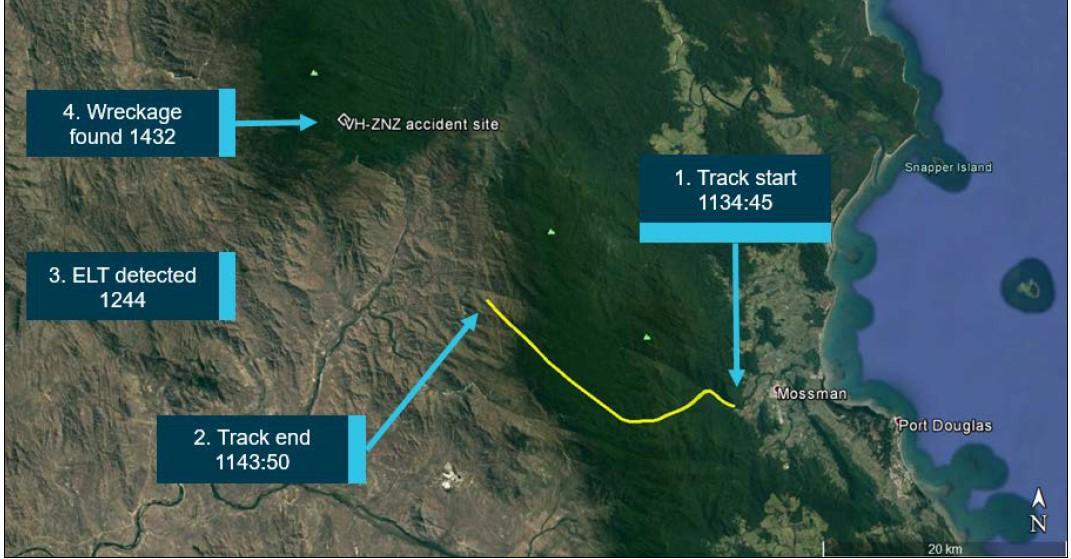
Recorded track data for the flight from Mossman to the Mount Windsor National Park, which is the forested area surrounding the accident site. The start of the track is in the vicinity of the Mossman QPWS office. Source: Google earth and OzRunways, annotated by ATSB.
__________
- Eastern Standard Time (EST): Coordinated Universal Time (UTC) + 10 hours.
- OzRunways is an approved data provider for Australian pilots for flight planning and in-flight navigation.
- The station house facility was located about 15 km north-west of the forestry barracks facility.
- Track data is transmitted to OzRunways server using the mobile phone network, which is affected by terrain shielding at lower levels in the area of the accident.
Pilot information
The pilot held a commercial helicopter pilot licence and had accumulated over 5,700 hours of flight time. His licence included the class rating for single-engine helicopters and the type rating for the Robinson R44.[5] The pilot initially qualified on the Robinson R22, R44 and Bell 206 helicopters in 2007. His last flight review was certified as taking place on 29 May 2016 in an R44. The pilot had flown VH-ZNZ on six occasions since the helicopter’s last periodic maintenance inspection on 7 September 2016, which included the day prior to the accident.
The pilot’s last aviation medical examination was on 19 January 2016. He was issued with a Class 1 Aviation Medical Certificate without restrictions. The pilot reported that prior to the accident flight he had slept about 18 hours in the last 48 hours. From the pilot’s logbook, there was no flying recorded for 12 and 13 November. The accident day, 18 November, was his fifth consecutive day of flying. He recorded 12 hours 20 minutes of flying for the previous four days. The time of the accident was not in the circadian low period and did not include an extended period of duty.
Helicopter information
General
VH-ZNZ was a Robinson Helicopter Company (RHC) R44 II helicopter, serial number 11954, powered by a 6-cylinder horizontally opposed Textron Lycoming IO-540-AE1A5 engine (Figure 2). It was a four-seat helicopter, certified by the United States (US) Federal Aviation Administration (FAA) and accepted by the Civil Aviation Safety Authority (CASA) in the normal category rotorcraft.[6] RHC manufactured the helicopter in 2007 and it was added to the CASA aircraft register in November of that year.
Figure 2: Robinson R44 II helicopter VH-ZNZ
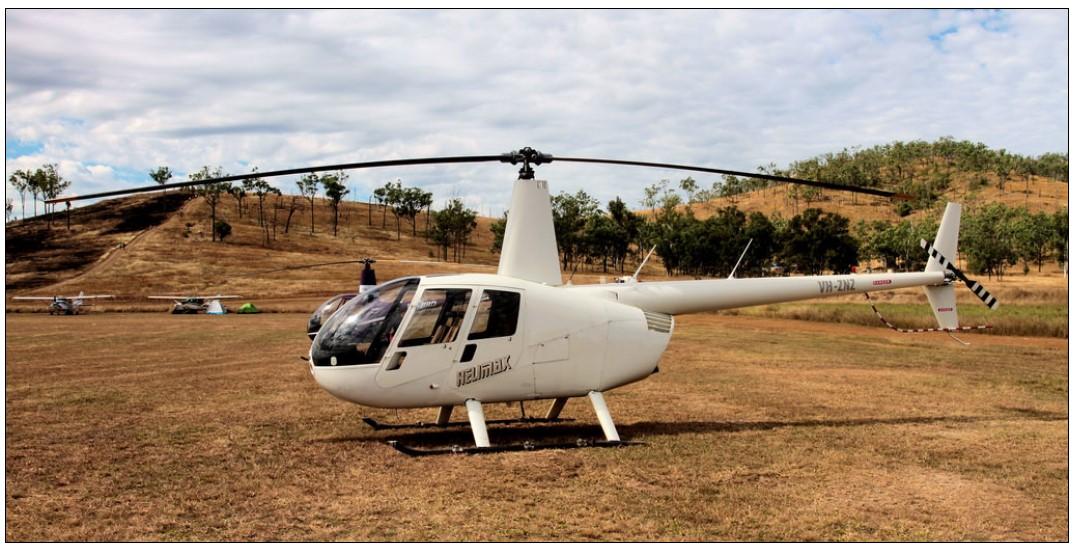
Source: Ian McDonell
Engine power is transmitted via four V-belts and a clutch to a shaft, which transmits power forward to the main rotor and aft to the tail rotor, via respective gearboxes. An engine governor senses changes in engine speed and applies corrective throttle inputs to maintain engine speed and therefore driveshaft and rotor speed within the normal operating limits. The throttle also opens or closes in response to the pilot raising or lowering the collective lever,[7] or if the pilot manually adjusts the throttle lever (located on the collective) to override the governor.
The main rotor consists of two all-metal blades mounted to the hub by coning hinges.[8] The hub is mounted to the main rotor shaft by a teeter hinge and the main rotor head is known as a teetering, or semi-rigid, rotor head. The three-hinged body teetering rotor head is a unique design feature to Robinson helicopters. The tail rotor has two all-metal blades mounted to a teetering hub. Pitch links transmit flight control movements to the rotor systems.
The flight control system operation is conventional and incorporates a centre-mounted[9] cyclic[10] stick to control the attitude[11] of the main rotor disc, and collective lever to control main rotor thrust. Tail rotor pitch and thrust is controlled by pilot movement of the tail rotor pedals. Tail rotor thrust is used to control the helicopter heading while in the hover, and balance while in forward flight.
Maintenance history
The helicopter log book statement indicated that the helicopter was to be maintained in accordance with the Robinson R44 maintenance manual, the pilots operating handbook (POH) for the daily/pre-flight inspection, Civil Aviation Safety Regulation 1998 Part 39 for airworthiness directives (ADs), and Civil Aviation Order 100.5 (general requirements in respect of maintenance of Australian aircraft). The logbook statement indicated the operational category of ‘charter’.
The last periodic maintenance inspection was completed on 7 September 2016, at 1,709 aircraft hours, in accordance with the Robinson R44 maintenance manual. Maintenance performed on the flight controls during the last periodic inspection was included in the wreckage examination and no anomalies were found. The current maintenance release[12] was not located and likely destroyed in the accident fire. Airworthiness directives were tracked and certified at the periodic inspections. The helicopter was modified with a bladder fuel tank in April 2013.
Weight and balance
The ATSB performed weight and balance calculations using the Robinson R44 II POH and estimated weights, provided by the pilot and the passenger’s next-of-kin. Calculations were made with full fuel (128.9 kg) and empty fuel. Both calculations were within the centre of gravity limits. The maximum gross weight limit for the R44 II is 1,134 kg. The estimated weight when it departed Mareeba with a full fuel load was about 1,075 kg. The helicopter would have consumed about 25 kg of fuel on arrival at the Mount Windsor National Park, providing an estimated operating weight of about 1,050 kg.
Performance
The helicopter performance for hovering in-ground effect and out-of-ground effect[13] was calculated using the environmental conditions reported by the rescue helicopter pilot (described below). This resulted in a density altitude equivalent to about 5,900 ft in a standard atmosphere. Using the estimated take-off weight from Mareeba Airport of about 1,075 kg, the in‑ground effect and out-of-ground effect performance figures were within limits. Maximum weight to hover out-of-ground effect at the accident site in nil wind was about 1,110 kg, which was slightly above the estimated operating weight of 1,050 kg on arrival at the park.
Meteorological information
Forecast conditions
The Bureau of Meteorology weather forecast for the area of operation, valid from 1100 until 2100 on 18 November, divided Area 45 into north-east and south-west subdivisions. The accident site was located in the north-east subdivision, where the wind was forecast as from 120 degrees at 25 kt at the altitudes of 2,000 ft and 5,000 ft above mean sea level. Moderate turbulence was also forecast below 8,000 ft on and about 30 NM lee of the eastern ranges north of Cooktown. The accident site in Mount Windsor National Park was about 50 NM south of Cooktown (outside of the forecast area for moderate turbulence), but located on the eastern ranges and in the same subdivision as the area to the north of Cooktown (refer to Appendix A).
Actual conditions
The rescue helicopter pilot reported the weather conditions on-site in the hover at the time of the search and rescue were a temperature of 26–28 °C at 3,500 ft, with gusting and varying wind at 15–25 kt and mostly clear. The rescue helicopter was a larger and more powerful helicopter than VH‑ZNZ and the rescue pilot reported that he had been ‘working hard’ to maintain a hover position over the accident site in ‘very turbulent’ conditions. When asked about the likely flying conditions for the accident helicopter, the rescue pilot commented that it ‘would have been working hard’.
One of the first responders to the report of the accident was from QPWS. He reported that the Mount Windsor National Park area is susceptible to strong and gusting wind conditions, and that those conditions were present on the day of the accident. Figure 3 depicts the local terrain about 500 ft below the elevation of the accident site with a view towards the south-east, the direction of the forecast wind.
Figure 3: Image of the local terrain with a view towards the south-east
View towards the south-east, the direction of the forecast wind, at about 3,000 ft elevation. The helicopter wreckage was located further inland behind the photographer at an elevation of about 3,500 ft, with surrounding peaks of about 4,500 ft. Source: ATSB
Table 1 lists the recorded wind conditions at 1230, about 14 minutes prior to the activation of the emergency locator beacon, from the surrounding Bureau of Meteorology observation sites.
Table 1: Surrounding weather observations
Location | Position from accident |
Elevation | Wind conditions |
Cooktown | 50 NM N | 60 ft | ESE 20 kt gusts to 29 kt |
Cairns | 55 NM SE | 6 ft | ESE 20 kt gusts to 25 kt |
Mareeba | 50 NM SSE | 1,330 ft | ESE 15 kt gusts to 20 kt |
Palmerville | 62 NM WNW | 807 ft | SE 6 kt gusts to 12 kt |
Mountain and lee wave activity
According to Underdown and Standen (2003), the following conditions are conducive to the formation of mountain and lee wave activity:
- Wind at right angles (or within +/- 30°) to a continuous mountain range
- Little change of wind direction with height
- Wind speed 15 kt[14] or more at the mountain summit and increasing with height
- Very stable layer several thousand feet thick just above the mountains, with less stable air above and below the stable layer.
Immediately downwind from the mountain, rotors form with strong downdraughts and updraughts. Rotor streaming, which differs from rotor zones under mountain waves, may occur when there is a deep layer of strong winds across high ground with lighter winds above. Here, the turbulence in the rotor streaming occurs downwind of and level with the top of the high ground and for a considerable height above.
Underdown and Standen (2003) and the Bureau of Meteorology Aviation weather services both report that aircraft may encounter severe turbulence in mountain wave systems. Moderate turbulence indicates aircraft G-load[15] variations of +/- 0.50–0.99 and severe turbulence indicates variations of +/- 1.0–1.99. The aircraft reaction to a moderate level of turbulence is described as: ‘Appreciable changes in attitude and/or altitude. Pilot remains in control at all times. Rapid bumps or jolts’. A severe level of turbulence is described as ‘Large abrupt changes in attitude and/or altitude. Momentary loss of control’.
Bureau of Meteorology comments
The Bureau of Meteorology reported that the winds on the area forecast are averaged over the 15-hour period of the forecast and over the subdivision area. They reported that ‘it is possible that there were other wind changes (direction and strength) not depicted in the forecast, which could have resulted in the forecast of turbulence north of Cooktown only’.
Wreckage and impact information
The ATSB did not conduct an initial on-site examination of the wreckage, but later conducted two targeted on-site visits following analysis of the evidence provided by the Queensland Police Service and QPWS staff. The first visit focused on examining the main rotor head, and the main and tail rotor systems. The second visit focused on the flight controls, engine and drive train.
Barracks facility
The accident pilot reported that he would not land the helicopter at the facility to be inspected if he assessed the location as unsuitable. In this situation, he would survey the local area for an alternative landing site nearby and the passenger would then hike to/from the facility to perform his inspections. The barracks facility was located a short walk east of a concrete causeway, which was large enough for an R44 to land on (Figure 4). The causeway was oriented east-west at a point where the river was oriented north-south. The accident site was in an upwind position relative to the barracks facility and causeway, consistent with the expected direction of travel if departing from the barracks.[16] The gas compliance plate at the barracks facility was not annotated for the visit, but the Queensland Petroleum and Gas Inspectorate reported that it was not required to be annotated for an inspection only. The compliance plate is only annotated for installation or modification to an existing installation.
Figure 4: Accident site relative to barracks facility and causeway
Forecast wind direction indicating the accident site was located about 500–600 m upwind of the barracks facility and causeway. Source: Google earth, annotated by ATSB
Site and distribution of wreckage
The accident site was at an elevation of about 3,500 ft and towards the south-east edge of a bowl with surrounding terrain up to about 4,500 ft. This placed it on the lee side of high terrain and 500‑600 m south-east of the Mount Windsor barracks facility. There was very dense vegetation with a forest canopy height of about 100 ft above ground level throughout the Mount Windsor National Park. The park is used for scientific research and closed to the public.
The helicopter was found to have broken into multiple fragments separated over an area of about 40 m x 50 m (refer to Appendix B). A separated section of tailcone, the empennage, tail rotor driveshaft sections and tail rotor blade debris were distributed to the west and south of the main wreckage. A post‑impact fire had consumed the main body of the helicopter, but the fragments separated from the main body were undamaged by fire. There were several tall trees surrounding the main wreckage, which had evidence of fire damage, but little impact damage. The damage to the forest canopy was concentrated directly above the main body of the helicopter, which indicated a near vertical final descent with little main rotor rotational energy (Figure 5).
Figure 5: Approach to canopy entry directly above wreckage site
Rescue helicopter view of the damaged canopy. Main body of the helicopter is located on the forest floor, about 100 ft directly below the canopy damage. Source: Search and rescue helicopter service (courtesy Queensland Police Service), annotated by ATSB
The main wreckage included the helicopter frame assembly, engine, main rotor drive train and the main rotor. The helicopter frame was oriented left nose down in a south-west direction with high ground on the port (left) side. It showed evidence of significant burning as a result of a post-impact fuel-fed fire (Figure 6). Immediately beyond the main wreckage site, helicopter debris and flora were unburnt. The fire destroyed the main body and forward section of the tailcone. The aluminium and bladder fuel tanks had perished in the fire. The left landing gear skid tube extender was located in a position consistent with a left nose down impact.
Figure 6: Main wreckage
Source: Queensland Police Service, annotated by ATSB
Engine
The engine was examined in the impact position and then the main frame section was rotated so that the engine could be examined from the underside. An external examination of the engine found no evidence of pre-existing mechanical defects. The throttle and mixture linkages were connected from the cockpit through to the engine controls. The fuel control unit was examined and the mixture noted to be in the full rich position and the throttle full open (full power position).
The ATSB inspected the engine’s external components for evidence of rotational impact damage to determine if the engine was operating when the helicopter impacted the ground. One area of identified contact was between the flywheel and port oil cooler. RHC reported that flexing of the airframe on impact with the ground may push the port or starboard oil cooler into the flywheel, and that such damage did not necessarily indicate the flywheel was rotating. The on-site examination could not determine if the damage was cutting from rotation and therefore this evidence was considered inconclusive.
The majority of the fuel system was consumed by fire. However, both fuel tank caps were identified in the wreckage. They were found secured to the top sections of their respective fuel tank inlets. The fuel shut-off valve was not found. Remnants of the bladder fuel cells were found throughout the wreckage.
Tailcone and tail rotor system
The rear half of the tailcone was found about 25 m south of the main wreckage with evidence of a main rotor blade strike mark and yellow paint transfer from the rotor (Figure 7). The forward separation point of the tailcone had a tension failure (pulled apart at the rivet joint). RHC reported that in power-on situations, the main rotor blades will cut through the tailcone and driveshaft. In power-off situations, and/or rotor speed reduced, it will ‘smash’ the tailcone, pulling the driveshaft out, which was consistent with the wreckage.
Figure 7: Separated tailcone (left) and empennage (right)
Left: the rear tailcone assembly with strike mark and yellow paint transfer in and around the strike was found to the south of the main wreckage. Right: the empennage was found adjacent to the main wreckage but outside the fire zone with both tail rotor blades separated. Source: Queensland Police Service, annotated by ATSB
An onsite representative from the Queensland Police Service crash forensics unit noted the site had a dense canopy with a lot of trees between the separated tailcone and main body of the helicopter. This suggested to him that the tailcone had fallen through the canopy after separation, rather than being liberated from the main body inside the canopy. The empennage assembly (tail rotor gearbox with vertical and horizontal stabiliser) had torn laterally from the tailcone and was found adjacent to the main wreckage, but outside the fire zone, with both tail rotor blades separated near the hub.
There were no indications of a failure of the tail rotor gearbox, gearbox mounts or pitch links. Fracture and separation of the tail rotor blades was by overstress. Tail rotor debris was distributed on an arc of a radius of about 15 m around the main wreckage in an anti-clockwise direction from west-north-west through to the south. One tail rotor blade exhibited impact damage consistent with a main rotor blade strike (Figure 8).[17] The other tail rotor blade tip cap was recovered and found to exhibit bending and yellow paint transfer that was consistent with main rotor blade contact (Figure 9). The outboard leading edges of the tail rotor blades were eroded and had split open. Wood fibres were found embedded within debris from both tail rotor blades.[18]
Figure 8: Tail rotor blade impact damage
Tail rotor blade 1 with strike damage consistent with the leading edge of a main rotor blade. Source: ATSB
Figure 9: Tail rotor blade tip
Tail rotor blade 2 tip cap with yellow paint transfer from the main rotor and bending deformation. Source: ATSB
Main rotor system
The main rotor and mast were inspected for evidence of in-flight damage, including mast bumping[19] and coning.[20] One of the teeter stops[21] was not present, likely to have been consumed in the post-accident fire. There was no evidence of damage to the mast where the teeter stop was previously located. The second teeter stop was in place, but exhibited fire damage. If mast bumping had occurred, it was not of a severity to result in visible mast damage. However, given the extent of the fire damage, the presence of mast bumping was inconclusive.
Some erosion of the main rotor blades leading edges was visible, but within limits. Both main rotor blades exhibited impact and fire damage. One main rotor blade and its associated pitch link assembly exhibited significant back-bending. RHC reported that deformation of the pitch link is typical following a main rotor blade strike. When a main rotor blade is bent and/or folded and still rotating, the loads on the pitch links and swashplate change dramatically, resulting in subsequent damage to main rotor head parts.
Neither of the main rotor blades exhibited coning (upward bending) damage, but both exhibited compression wrinkling of their upper surface. RHC reported that the angled creases from the leading edge to the trailing edge were indicative of backward bending of the rotor blades. The blade skin will retain the creases irrespective of whether the bending is elastic or plastic. Two marks on the upper surface of one of the main rotor blades indicated possible tail rotor blade strikes. Minor debonding of the main rotor blades was considered to be the result of the fire as there was no indication of associated bending from in-flight aerodynamic forces.
The main rotor blades, hub and shaft were found correctly assembled with no evidence of a pre‑existing defect.
Flight controls
The post-impact fire precluded examination and testing of the flight control system in its entirety. However, all of the flight control rod ends, attaching hardware and other steel components relating to the cyclic, collective and tail rotor controls were found intact and secure.
Most of the tail rotor pitch change controls were outside of the fire zone and were able to be examined. The tail rotor pitch link controls within the tailcone had fractured in overstress, likely as a result of the impact. The pitch links on the tail rotor itself moved freely and functioned as designed.
The dual controls for the cyclic, collective and tail rotor pedals, were not fitted at the time of the accident and were located in an area to the rear of the right rear passenger seat where they were likely to have been stored.[22]
A detailed inspection of the available flight control system components did not identify any defects that may have contributed to the accident.
Drive train
The engine to main rotor transmission drive shaft was examined and no pre-accident defects were identified. The main rotor gearbox casing was consumed by the fire, but the single-stage spiral‑bevel gear and mast roller bearings were visible and did not indicate any evidence of a catastrophic failure. The forward flex plate bolts exhibited minor bending on the main gearbox side, but not on the engine side (Figure 10). RHC reported that the deformation of the forward flex plate is consistent with damage from extreme angles between the yokes while being pulled apart. As the main rotor blades contact solid objects the mast will move fore, aft, left and right, which changes the angle of the input yoke of the gearbox. The entire airframe will flex, resulting in the yokes at all three flex couplings moving apart. They noted that in this case the forward flex plate bending was relatively minor.
Figure 10: Forward flex plate (left) and intermediate flex plate (right)
Left: forward flex plate with visible bending of bolts on the main gearbox side, but not on the engine side. Right: intermediate flex plate exhibited tension failure, but no significant torsion. The V-belt drive from the engine was located between the two flex plates. Source: ATSB
The tail rotor drive shaft had fractured into five sections between the intermediate and aft flex plate. Both flex plates had failed in tension (pulled apart) and the driveshaft pulled through the damper assembly. The separation points of the tail rotor drive shaft were reviewed and it was found that they displayed bending failures, with the exception of a section that was seized within the separated tailcone.
The section within the tailcone exhibited a torsional failure forward (facing towards engine drive) and a bending failure aft (facing towards the tail rotor gearbox). No paint transfer was found on any of the tail rotor driveshaft sections and the flex plates did not exhibit any significant torsional damage associated with their failure in tension. RHC reported there was very little indication of rotational scoring on the tail rotor driveshaft sections, which indicated to them that there was low drive speed at the time the flex plates were pulled apart.
Continuity of the drive train could not be established due to fire damage to the V-belts and clutch assembly. However, the material available did not exhibit any pre-existing defects that may have contributed to the accident.
Figure 11 depicts the approximate position of the separation points. Of note, the main rotor cyclic rigging setting is 13.5–14.25°. The blade strike mark was at an angle of about 17–18°.
Figure 11: Approximate positions of tailcone separation
Main rotor blade strike and associated tailcone separation points.
Source: Robinson Helicopter Company, annotated by ATSB
Survival aspects
The pilot was seated in the front right seat and the passenger in the front left seat. The orientation of the wreckage was left nose down with the left skid buried into the ground slightly aft of the airframe. This suggested a left nose down impact with sufficient force to separate the left skid from the airframe. The post-mortem results for the passenger determined that the likely cause of death was crash‑associated multiple injuries. The results of testing for drugs and poisons, including alcohol, were negative.
Crashworthiness
The certification standard for the R44 was based upon providing the occupant(s) with a reasonable chance of escaping serious injury in a minor crash based upon the rotorcraft absorbing the landing loads with an ultimate descent velocity of five feet per second. The following acceleration limits applied:
- upward – 1.5 G
- forward – 4.0 G
- sideward – 2.0 G
- downward – 4.0 G.[23]
The landing gear limit load drop test requirements for the helicopter landing gear were as follows:
(1) 13 inches from the lowest point of the landing gear to the ground; or
(2) Any lesser height, not less than eight inches, resulting in a drop contact velocity equal to the greatest probable sinking speed likely to occur at ground contact in normal power-off landings.[24]
The fuel tank drop test requirements were as for the occupant acceleration limits. The descent path of the helicopter and orientation of the wreckage indicated that the ground impact was likely outside the certification limits, which severely compromised the liveable volume[25] for the front left seat occupant and the integrity of the fuel tanks. The use of seat belts could not be determined from the fire damage, but are not considered likely to have influenced the outcome for the passenger.
Search and rescue
The ATSB found no evidence that a distress call was made by the pilot prior to the detection of the emergency locator transmitter (ELT). The JRCC first detected the helicopter’s ELT at 1244. Following detection of the ELT, search and rescue aircraft were directed to the vicinity of the signal. The last signal from the ELT was detected by the JRCC at 1351.[26] When the rescue helicopter arrived, the rescue helicopter pilot observed smoke, which was used to locate the main wreckage site. A rescue wire-person was winched down to the site and confirmed they had located the accident site. The confirmation was received by the JRCC at 1432.
The rescue wire-person found the pilot during a brief search of the area and confirmed his identification with his aviation security identification card. The pilot was initially conscious and reported that he was alone and had dropped his passenger off. However, his condition deteriorated and a doctor was winched down to the site to conduct an assessment. The pilot, wire‑person and doctor were recovered to the helicopter and the pilot was transferred to Cairns hospital. A search for the passenger in the surrounding area by air and ground continued until last light without success. The following day, 19 November, a police forensic team was winched down to the accident site to locate and retrieve the deceased passenger from within the main wreckage.
In-flight break-up research
There have been a number of main rotor divergence and in-flight break-up accidents involving the Robinson family of helicopters. This includes the R22, R44 and R66[27] helicopters. Previous R22 and R44 main rotor divergence accidents were examined by the United States National Transportation Safety Board in a 1996 special investigation report.[28] The ATSB reviewed their report and researched previous R44 and R66 main rotor divergence accidents, which resulted in an in-flight break-up with no evidence of a pre-existing defect.[29] This was for the purpose of a comparative analysis with the damage found to VH-ZNZ and resulted in a review of 12 historical accidents from Germany, the United States, France, Canada and New Zealand.
All historical cases reported evidence of mast bumping. Several cases included mast bending (3 of 12) and/or mast sheared (5 of 12).[30] The Transport Accident Investigation Commission of New Zealand’s report AO-2013-003 included comments from a metallurgical and fractographic[31] examination of the mast failure as follows:
Failure occurred by overload and the nature of the fracture indicates that significant bending and torsional loads were applied…The direction of torsional loading was consistent with power being applied to the rotor while the rotor was abruptly decelerated, perhaps through contact with the airframe or some other object.
The inspection of VH-ZNZ found no evidence of mast bending. Due to the fire damage to the teeter stops, evidence of mast bumping was inconclusive. There was no evidence of mast damage where the fire had consumed one teeter stop and therefore no evidence of excessive mast bumping.
Review of the rotor strikes to the airframes were limited by the amount of detail provided in the investigation reports and the various forms of description provided. Some reports included the description of tailcone ‘severed in-flight’, while others referred to it as ‘separated’. In some cases, the main rotors struck and cut through the cabin in addition to, or instead of the tailcone. While VH-ZNZ did exhibit a tailcone strike, the main rotors did not shear (cut through) the tailcone and there was no indication that the main rotors struck the cabin.
The historical cases were all fatal with no survivors. In several cases, the reports concluded that the accident was associated with pilot over-control in a low-G flight condition, which is described by RHC in their POH safety notice 11.[32] In other cases the reports concluded that the reason for the main rotor divergence could not be determined.
Additional information
Pilot operating handbook
The Robinson R44 II POH section 10: Safety tips and notices, included the following safety notice information of interest to the investigation:
Safety notice SN-10: Fatal accidents caused by low RPM rotor stall
Power available from the engine is directly proportional to RPM. If the RPM drops 10%, there is 10% less power. With less power, the helicopter will start to settle, and if the collective is raised to stop it from settling, the RPM will be pulled down even lower, causing the ship to settle even faster. If the pilot not only fails to lower collective, but instead pulls up on the collective to keep the ship from going down, the rotor will stall almost immediately. When it stalls, the blades will either “blow back” and cut off the tailcone or it will just stop flying, allowing the helicopter to fall at an extreme rate.
Safety notice SN-24: Low RPM rotor stall can be fatal
Rotor stall due to low RPM causes a very high percentage of helicopter accidents, both fatal and non-fatal… As the RPM of the rotor gets lower, the angle of attack[33] of the rotor blades must be higher to generate the lift required to support the weight of the helicopter. As with the airplane wing, the blade airfoil will stall at a critical angle, resulting in a sudden loss of lift and a large increase in drag.
When the rotor stalls, it does not do so symmetrically because any forward airspeed of the helicopter will produce a higher airflow on the advancing blade than on the retreating blade. This causes the retreating blade to stall first, allowing it to dive as it goes aft… Also, as the helicopter begins to fall, the upward flow of air under the tail surfaces tends to pitch the aircraft nose-down. These two effects, combined with aft cyclic by the pilot attempting to keep the nose from dropping, will frequently allow the rotor blades to blow back and chop off the tailboom as the stalled helicopter falls.
Safety notice SN-32: High winds or turbulence
Flying in high winds or turbulence should be avoided.
A pilot’s improper application of control inputs in response to turbulence can increase the likelihood of a mast bumping accident. If turbulence is encountered, the following procedures are recommended:
1. Reduce power and use a slower than normal cruise speed. Mast bumping is less likely at lower airspeeds.
2. For significant turbulence, reduce airspeed to 60–70 knots.
3. Tighten seat belt and rest right forearm on right leg to minimize unintentional control inputs. Some pilots may choose to apply a small amount of cyclic friction to further minimize unintentional inputs.
4. Do not overcontrol. Allow aircraft to go with turbulence, then restore level flight with smooth, gentle control inputs. Momentary airspeed, heading, altitude, and RPM excursions are to be expected.
5. Avoid flying on the downwind side of hills, ridges, or tall buildings where turbulence will likely be most severe.
The helicopter is more susceptible to turbulence at light weight. Reduce speed and use caution when flying solo or lightly loaded.
Safety notice 10 described the risk of a main rotor blade stall associated with an overpitching event, which is discussed further in the Over-pitching section of the report below. Safety notice 24 provided a more generic description of low rotor speed stall, which is discussed further under Loss of drive power below.
Safety notice 32 replaced an earlier airworthiness directive, issued by the FAA in 1995 for the R44 helicopter. The directive prohibited flight in surface winds greater than 25 kt, gusting winds greater than 15 kt, and in moderate, severe or extreme turbulence. These limitations have remained in place for low-experience R22 pilots (less than 200 flight hours in helicopters and less than 50 in the R22).
The ATSB enquired as to whether a handling assessment in moderate turbulence was ever conducted in the R44 and, if performed, what rating the helicopter received.[34] In reply, RHC reported that no additional assessment with quantitative scoring was performed besides the requirements for certification.
Over-pitching
The International Civil Aviation Organization (ICAO) manual of aircraft accident and incident investigation, chapter 15: Helicopter investigation, described over-pitching as a phenomena that happens when collective pitch is increased to a point where the main rotor blade angle of attack creates so much drag that all available engine power cannot maintain or restore normal operation rotor speed. At low rotor speed, the rotor blades bend upwards and drag increases. The high inflow angles and rotor drag quickly decay main rotor speed, which may decrease to the point where the main rotor blades stall as described in R44 safety notice 10.
The ICAO investigation manual noted that over-pitching could occur in any phase of powered flight and that high weight, high density altitude and high temperatures are contributing factors. The manual also noted that over-pitching to low rotor speed and blade stall is greatest in small piston engine helicopters with low rotor blade inertia, and that with a piston engine, the engine speed will also decrease and ‘may cease operation during over-pitching’.[35] RHC reported that they were aware that low rotor speed could result in the engine stalling. They reported it was more likely in the R22, but in the right conditions (high altitude, high temperature and high loading) the R44 can be over‑pitched enough to stall the engine.
Previous over-pitching events
ATSB investigation 200600979: Collision with terrain 10 km west of Gunpowder Mine, Qld, 21 February 2006, VH-HBS Robinson Helicopter Company R44, concluded that the accident was the result of insufficient main rotor thrust that was a consequence of low main rotor speed. The accident site was about 3,800 ft density altitude (assuming standard atmospheric pressure) with moderate thermal turbulence below 8,000 ft forecast.
ATSB investigation AO-2008-062: Collision with terrain – Robinson Helicopter R44 Raven, VH‑RIO, 6 km NE Purnululu ALA, Western Australia, 14 September 2008, concluded that the most likely scenario was that the engine power required exceeded the engine power available, resulting in main rotor speed decay. The helicopter was operating at about 3,500 ft density altitude and the investigation found that moderate thermal turbulence was likely present below 9,000 ft.
Loss of drive power
The ICAO investigation manual states that, in the event of a sudden engine stoppage, pilot reaction time is a significant factor to prevent a rapid decay of main rotor speed, and that a low inertia rotor system will decrease speed more rapidly than high inertia rotors. Lowering the collective lever enables the pilot to maintain rotor speed on entry to an autorotation,[36] but the last 100 ft are equally critical.
In the last 100 ft the pilot must reduce the forward speed and rate of descent to minimise the horizontal and vertical accelerations for landing. This manoeuvre is performed by the pilot flaring the helicopter (pitching the nose up) and raising the collective lever, which increases the rotor thrust to reduce the rate of descent and forward speed. Raising the collective lever without drive power will also rapidly decay the rotor speed. If it decays too low prior to landing, a low rotor speed blade stall as described in R44 safety notice 24 may occur. Drive power for the R44 is dependent on the performance of the engine and its governor system, and the continuity of the drive train, including the V-belts, clutch, gearboxes and driveshafts. The examination of the wreckage found no pre-existing defects with the gearboxes or driveshafts, but the impact and fire damage prevented examinations of the other components.
Previous loss of drive power events (powerplant or drive train faults)
A search of the ATSB’s database for engine failure or malfunction occurrences involving the R44 II found 10 events between 2012 and 2017.[37] A similar search for transmission and gearbox issues identified three occurrences. The results from the two searches were mutually exclusive.
The reasons for the transmission faults included one undetermined (ATSB investigation AO-2016-172), one required a clutch unit replacement, and one revealed the V-belts were loose. For AO‑2016-172, the helicopter’s rotor speed decayed in-flight, but engine speed was maintained. Following recovery of the helicopter, no pre-existing defect was found and the fault could not be reproduced.
__________
- The R44 was a type rating in the initial introduction of Civil Aviation Safety Regulation 1998 Part 61, but was later moved to the single-engine class rating in January 2015.
- Normal category applies for rotorcraft with maximum weights of 7,000 pounds or less and nine or less passenger seats.
- Collective: a primary helicopter flight control that simultaneously affects the pitch of all blades of a lifting rotor. Collective input is the main control for vertical velocity.
- Coning of main rotor blades: the upwards movement of the main rotor blades while they are rotating. This is usually in response to an increase in aerodynamic force as a result of a control input from the pilot. It is more pronounced at high weights and/or low main rotor speed.
- The centre-mounted cyclic stick is a unique design feature to the Robinson helicopter family.
- Cyclic: a primary helicopter flight control that is similar to an aircraft control column. Cyclic input tilts the main rotor disc, varying the attitude of the helicopter and hence the lateral direction.
- Attitude refers to the comparison of the rotor disc or helicopter axes with the local horizon.
- Maintenance release: an official document, issued by an authorised person as described in Regulations, which is required to be carried on an aircraft as an ongoing record of its time in service (TIS) and airworthiness status. Subject to conditions, a maintenance release is valid for a set period, nominally 100 hours TIS or 12 months from issue.
- Helicopters require less power to hover when ‘in ground effect’ than when ‘out- of ground effect’ due to the cushioning effect created by the main rotor downwash striking the ground. The height of ‘ground effect’ is usually defined as less than one main rotor diameter above the surface, which is about 33 ft for the R44 helicopter.
- A higher value of 25 kt may be reported by other publications.
- G-load: the nominal value for acceleration. In flight, g load represent the combined effects of flight manoeuvring loads and turbulence and can have a positive or negative value.
- A departure into wind would improve the helicopter’s performance by reducing the power required and ground speed, and improving the climb performance, when compared with a tailwind. This is more critical as the environmental conditions become more adverse, such as stronger winds and higher density altitudes.
- RHC reported that the damage to the tail rotor blade in Figure 8 is more consistent with the tail rotor blade striking a tree than a main rotor blade striking the tail rotor blade. However, their response did not account for the tip bending and paint transfer evident in Figure 9, and the ATSB noted a scratch in the yellow paint of a main rotor blade, near the main rotor blade tip, consistent with contact with a tail rotor blade. Footnote 19 refers to an unsuccessful attempt to verify if the tail rotor blades did strike the same tree.
- The wood fibres were sent to the University of Adelaide, School of Biological Sciences, for genetic testing to determine if both tail rotor blades struck the same tree. However, there was insufficient material for a successful test. Therefore, no conclusion as to the nature of the break-up has been made from their presence.
- Mast bumping: contact between the main rotor hub and the rotor mast which, if excessive, could severely damage the mast, or result in the separation of the main rotor system from the helicopter. Damage from mast bumping is indicative of excessive blade flapping and/or excessive tilt of the main rotor disc relative to the mast.
- Coning damage may include upward bending of the main spar and/or compression wrinkling damage to the upper surface of the main rotor blade.
- Two elastomeric stops are fitted at the top of the main rotor mast to protect the mast from direct contact with the main rotor blades. Excessive teetering of the main rotor blades in-flight will result in the main rotor blades striking the teeter stops.
- In accordance with the R44 pilot operating handbook, the left seat controls must be removed if the person in that seat is not a rated helicopter pilot.
- US Code of Federal Regulations Part 27.561 (2 October 1964) – Emergency Landing Conditions.
- US Code of Federal Regulations Part 27.725 (2 October 1964) – Landing Gear.
- Flight Safety Foundation 1989, Helicopter Safety: Helicopter crashworthiness – part one, Vol. 15 No. 6.
- The emergency locator transmitter was installed in the main body of the helicopter, which was subject to the post-crash fire.
- The Robinson R66 is the five seat turbine-engine helicopter using the same T-bar cyclic and teetering main rotor hub design features as the R22 and R44, approved for normal category rotorcraft on 25 October 2010.
- United States National Transportation Safety Board 1996, Special investigation report: Robinson Helicopter Company R22 loss of main rotor control accidents, NTSB, Washington.
- These accidents were found to have occurred under normal power and rotor speed conditions.
- Results included both R44 and R66 helicopters.
- Fractography is the examination of the cause of a material failure by studying the characteristics of the fracture surface.
- R44 safety notice SN-11: Low-G pushovers – extremely dangerous: Pushing the cyclic forward following a pull-up or rapid climb, or even from level flight, produces a low-G (weightless) flight condition. If the helicopter is still pitching forward when the pilot applies aft cyclic to reload the rotor, the rotor disc may tilt aft relative to the fuselage before it is reloaded… With no lift from the main rotor…mast bumping can occur. Severe in-flight mast bumping usually results in main rotor shaft separation and/or main rotor contact with the fuselage… Always use great care to avoid any manoeuvre which could result in a low-G condition. Low-G mast bumping accidents are almost always fatal.
- The angular difference between the chord of the rotor blade and the relative airflow. The chord is the straight line between the rotor blade leading edge and trailing edge.
- Harper RP & Cooper GE 1984, Handling qualities and pilot evaluation, manuscript prepared for the 1984 Wright Brothers Lectureship in Aeronautics. The manuscript provided a recommended process for pilots to evaluate and rate aircraft handling qualities and was the reference source for the enquiry.
- As engine speed decreases at full throttle, a maximum torque value will be passed. The area below the maximum torque value is referred to as the ‘low end’ torque zone, or ‘unstable torque region’. An increase in resistance in this area will result in a drop in engine torque and engine stall.
- Descent with power-off. Air flowing in the reverse direction upwards through the rotors produces the driving force for the rotors.
- The results prior to 2012 were excluded as some did not differentiate between the different models of R44 helicopters.
Introduction
While operating in the Mount Windsor National Park on a charter flight to provide gas and plumbing inspection services, the Robinson R44 helicopter broke-up after the main rotor struck the helicopter’s tailcone. As a result of the in-flight break-up and impact, the passenger was fatally injured and the pilot sustained serious injuries.
No evidence was found of a pre-existing mechanical defect with the helicopter. However, no tests or internal inspections were performed on the engine or clutch, which were subject to impact and fire damage in a remote location. In addition, the drive train V-belts had perished, which prevented the verification of drive train continuity.
The accident flight was within the published weight and balance limits for the helicopter, which had sufficient power to hover out-of-ground effect, in nil wind. Turbulence may have reduced the power margin, which is discussed further under: Possible scenarios precipitating the in-flight break-up.
This analysis will discuss the weather conditions on the day, in particular, the possibility of turbulence, which was not forecast, and its potential effect on the flight. It also considers several scenarios for the in-flight break-up and highlights the benefits of having an emergency locator transmitter fitted for survivability.
Weather conditions
Moderate turbulence was forecast to the north of the Mount Windsor National Park for the time of the accident flight, but not for the park area. However, the park was subject to the same forecast wind strength of 25 kt as the area to the north. Given the wind direction and strength on the day, combined with the undulating terrain and tree canopy, the conditions in the area were conducive to terrain‑induced turbulence. This was consistent with the reports from personnel who responded to the accident. While the degree of turbulence could not be determined, in consideration of the reports provided and the Bureau of Meteorology’s turbulence intensity descriptions, it was likely to have been at least moderate.
In the absence of a forecast for turbulence the pilot may not have had a complete appreciation of how the weather would affect flying conditions in an R44 in the national park environment. However, as the pilot could not recall the events on the day of the accident, his understanding of the conditions could not be established.
The Robinson R44 safety notice SN-32 advised pilots to avoid flying in high winds or turbulence, which could result in fluctuating G-conditions and mast bumping, as described in safety notice SN‑11. This notice, SN-32, replaced an earlier airworthiness directive, which prohibited flight under such conditions. Those conditions were likely present at the time of the accident. Although the airworthiness directive had been cancelled, RHC reported that they had no handling qualities assessment for the helicopter in conditions of moderate turbulence (nor were they required to for certification). Therefore, the likely presence of at least moderate turbulence potentially placed the helicopter in an environment for which it had not been flight tested. Despite this, the ATSB could not determine if the weather contributed to the accident.
In-flight break-up sequence
The break-up of the helicopter likely started with a main rotor blade striking and liberating the tailcone from the airframe. This likely occurred above the forest canopy due to the separation of the tailcone from the main body wreckage on the forest floor and the density of the forest between them. The strike occurred while the tail rotor driveshaft was rotating, as indicated by a section of driveshaft with a torsional failure. The bending failures of the tail rotor driveshaft in lieu of shearing, and absence of torsional damage to the flex plates and rotational scoring to the driveshaft, indicated there was likely low engine power and rotor speed at the time of the tailcone strike.
Following the tailcone strike, the tail rotor driveshaft was pulled apart at the intermediate and aft flex plates and the empennage was torn laterally from the aft portion of tailcone due to its own inertia. This presented the tail rotor blades within striking distance of the main rotor disc path, which struck and liberated both tail rotor blades. The helicopter then descended on a near vertical trajectory through the forest canopy and impacted the forest floor left nose down relative to the ground.
The distribution of the tail fragments to the west and south of the main body was consistent with the helicopter moving on an easterly track at the time of the break-up. The elapsed time between the helicopter’s track towards the park and activation of the emergency locator beacon, in association with the location of the accident site and distribution of wreckage, indicated the accident more likely than not occurred during an upwind departure from the barracks facility. The relatively small distribution area of the wreckage and survival of the pilot indicated that the break‑up likely occurred close to the forest canopy without a high rate of descent.
A review of previous R44 and R66 helicopter in-flight break-ups at normal operating rotor speeds and powers revealed notable differences with this accident. Specifically, the tailcone strike damage and absence of any significant mast damage did not support a mast bumping scenario from the pilot overcontrolling the cyclic at normal engine power and rotor speed. Historically, these accidents have resulted in significant damage to the main rotor mast, including bending and fracture, which was not exhibited by this accident. The low engine power and rotor speed, and absence of any significant mast damage, indicated the strike was likely the result of a low rotor speed blade stall, which is discussed below.
Possible scenarios precipitating the in-flight break-up
In consideration of the environmental conditions and helicopter damage, the ATSB considered two possible scenarios, which could result in a low rotor speed blade stall.
Loss of drive power (powerplant or drive train fault)
As the helicopter climbed from near sea level into the Mount Windsor National Park it was exposed to an increasing density altitude (reduction in ambient air density). As a result of the increasing density altitude the margin between the power available and power required would have reduced with high rotor drag. The R44 pilot operating handbook indicated that the throttle is frequently wide open when operating at altitudes above 3,000‑4,000 ft. This would result in a rapid reduction of rotor speed in the event of a loss of drive power.
A loss of drive power at high power, low height and low speed, such as on take-off and initial climb, would result in very little energy available to trade-off, in order to recover from a loss of rotor speed. A significant loss of rotor speed while attempting to arrest the rate of descent before entering the forest canopy could lead to a main rotor blade stall and tailcone strike as described in the R44 pilot operating handbook safety notice 24. Of note, a loss of rotor speed due to a drive train fault with the V-belts or clutch could result in a low power tailcone strike in-flight followed by flywheel rotational damage to the port oil cooler on impact with the ground.
Overpitching
The accident site was located on the lee side of a bowl surrounded by higher terrain. The lee side of terrain is the highest risk area for encountering a downdraught in strong wind conditions as described in R44 safety notice 32. If mountain or lee wave activity was present, then tracking into wind towards rising terrain at a high-density altitude could potentially result in the helicopter flying into a downdraught, which exceeds the power available. This can result in an overpitching event followed by a blade stall and tailcone strike as described in the R44 pilot operating handbook safety notice 10.
A blade stall and tailcone strike while overpitching is expected to exhibit significant engine power at the time of the strike. However, if the engine stalled while overpitching before a main rotor blade stalled, then this would result in a tailcone strike, which exhibited low power and low rotor speed.
There was no evidence of upward bending (coning) of the main rotor blades indicative of overpitching. Further, the compression wrinkling present on the main rotor blades exhibited backward bending from a strike, rather than upward bending from coning. Therefore, although the reported environmental conditions of high-density altitude combined with turbulence indicated that the helicopter was susceptible to overpitching, the damage found to the helicopter did not provide conclusive support for this scenario.
Summary
The absence of any significant mast bumping damage combined with the apparent low power tailcone strike indicated a likely main rotor blade stall strike. This would be consistent with the pilot attempting to arrest the helicopter’s rate of descent before entering the forest canopy, which is itself consistent with the pilot surviving the accident.
A loss of rotor speed presents several scenarios, including overpitching, a loss of engine power (including an engine stall), or a loss of drive continuity. None of these scenarios could be verified. Therefore, the scenario, which resulted in the main rotor blade stall, could not be determined.
Emergency locator transmitter
Historical accidents of this nature, involving an in-flight break-up, generally result in fatal injuries for all occupants on board. The survival of the pilot in this accident was a rare occurrence and was likely due to the reduced rate of descent as the helicopter entered the canopy combined with the orientation of the airframe at impact. However, for the passenger in the front left seat, the orientation of the airframe at impact resulted in high energy attenuation in this location and was therefore considered not to be survivable.
The three key elements for the rescue of the pilot were the automatic activation of the emergency locator transmitter, the response of the Australian Maritime Safety Authority’s Joint Rescue Coordination Centre and the availability of the search and rescue helicopter. The activation of the emergency locator transmitter on impact was the trigger to start the search and rescue. This resulted in the discovery of the accident site by the search and rescue helicopter about 1 hour and 48 minutes after the initial detection of the emergency locator transmitter. The pilot may otherwise have not survived.
ATSB investigation AO-2017-033: Collision with terrain involving Agusta AB206, VH-DPU, found that the rescue of the occupants took about 39 hours. They were carrying a manually activated emergency position indicating radio beacon, which they were physically unable to retrieve and activate after the accident. They were eventually located with the assistance of OzRunways recorded track data.
Limitations on the effectiveness of emergency locator transmitters in aviation accidents were reviewed by the ATSB in research report AR-2012-128. The report identified several performance issues, which could affect their operational reliability, but still credited them for saving an average of four lives per year. While some of the reliability issues were considered beyond the control of the individual pilot, such as damage during impact, the report identified several measures within the control of the individual to improve their performance. In this accident, smoke emitted from the post-accident fire enabled the rescue helicopter to locate the accident site. However, according to the report (AR-2012-128), a global positioning system enabled transmitter can improve the accuracy of detection from about 5 km to 120 m.
From the evidence available, the following findings are made with respect to the in-flight break-up involving a Robinson R44, registered VH-ZNZ, 41 km north-west of Mossman, Queensland, on 18 November 2016. These findings should not be read as apportioning blame or liability to any particular organisation or individual.
Contributing factors
- The helicopter main rotor diverged from the normal plane of rotation and struck the tailcone, which resulted in the in-flight break-up of the helicopter.
- The main rotor strike to the tailcone was likely the result of a low main rotor speed blade stall for reasons undetermined.
Other safety factors
- The helicopter likely encountered at least moderate turbulence, which was not forecast. It was approved to operate in the prevailing weather, but was not flight tested for those conditions.
Other findings
- The fitment and registration of the emergency locator transmitter to the helicopter assisted the search and rescue of the pilot.
- The helicopter was within the weight and balance, and performance limits for the planned flight.
- Although the post-impact fire precluded examination of the helicopter in its entirety, a detailed inspection did not identify any pre-existing defects that may have contributed to the accident.
Sources of information
The sources of information during the investigation included the:
- Australian Maritime Safety Authority (JRCC)
- Bureau of Meteorology
- Civil Aviation Safety Authority
- OzRunways
- Pilot (also the operator)
- Queensland Parks and Wildlife Service
- Queensland Petroleum and Gas Inspectorate
- Queensland Police Service
- Rescue helicopter pilot
- Robinson Helicopter Company
- University of Adelaide (School of Biological Sciences).
References
Australian Transport Safety Bureau 2013, AR-2012-128: A review of the effectiveness of emergency locator transmitters in aviation accidents, ATSB, Canberra.
Bureau of Meteorology aviation weather services. Hazardous weather phenomena: Turbulence; retrieved from www.bom.gov.au on 3 August 2017.
Flight Safety Foundation 1989, Helicopter Safety: Helicopter crashworthiness – part one, Vol. 15 No. 6.
Harper RP & Cooper GE 1984, Handling qualities and pilot evaluation, manuscript prepared for the 1984 Wright Brothers Lectureship in Aeronautics.
International Civil Aviation Organization 2011, Manual of aircraft accident and incident investigation Part III: Investigation, Doc 9756, ICAO, Montréal.
Underdown RB & Standen J 2003, Meteorology (3rd Ed.), Blackwell Publishing, Oxford.
United States National Transportation Safety Board 1996, Special investigation report: Robinson Helicopter Company R22 loss of main rotor control accidents, NTSB, Washington.
Transport Accident Investigation Commission (New Zealand) 2016, Aviation inquiry AO-2013-003: Robinson R66, ZK-IHU, Mast bump and in-flight break-up, Kaweka Range, 9 March 2013, TAIC, Wellington.
Submissions
Under Part 4, Division 2 (Investigation Reports), Section 26 of the Transport Safety Investigation Act 2003 (the Act), the Australian Transport Safety Bureau (ATSB) may provide a draft report, on a confidential basis, to any person whom the ATSB considers appropriate. Section 26 (1) (a) of the Act allows a person receiving a draft report to make submissions to the ATSB about the draft report.
A draft of this report was provided to the Australian Maritime Safety Authority, Bureau of Meteorology, Civil Aviation Safety Authority, the pilot, Queensland Parks and Wildlife Service, Queensland Petroleum and Gas Inspectorate, Queensland Police Service, rescue helicopter pilot, Robinson Helicopter Company, and the United States National Transportation Safety Board.
The submissions from those parties were reviewed and where considered appropriate, the text of the draft report was amended accordingly.
Appendix A – Planning chart with weather subdivisions
Appendix B – Distribution of the helicopter wreckage (North-Up)
Purpose of safety investigationsThe objective of a safety investigation is to enhance transport safety. This is done through:
It is not a function of the ATSB to apportion blame or provide a means for determining liability. At the same time, an investigation report must include factual material of sufficient weight to support the analysis and findings. At all times the ATSB endeavours to balance the use of material that could imply adverse comment with the need to properly explain what happened, and why, in a fair and unbiased manner. The ATSB does not investigate for the purpose of taking administrative, regulatory or criminal action. TerminologyAn explanation of terminology used in ATSB investigation reports is available here. This includes terms such as occurrence, contributing factor, other factor that increased risk, and safety issue. Publishing informationReleased in accordance with section 25 of the Transport Safety Investigation Act 2003 Published by: Australian Transport Safety Bureau © Commonwealth of Australia 2019 Ownership of intellectual property rights in this publication Unless otherwise noted, copyright (and any other intellectual property rights, if any) in this report publication is owned by the Commonwealth of Australia. Creative Commons licence With the exception of the Coat of Arms, ATSB logo, and photos and graphics in which a third party holds copyright, this publication is licensed under a Creative Commons Attribution 3.0 Australia licence. Creative Commons Attribution 3.0 Australia Licence is a standard form licence agreement that allows you to copy, distribute, transmit and adapt this publication provided that you attribute the work. The ATSB’s preference is that you attribute this publication (and any material sourced from it) using the following wording: Source: Australian Transport Safety Bureau Copyright in material obtained from other agencies, private individuals or organisations, belongs to those agencies, individuals or organisations. Where you wish to use their material, you will need to contact them directly. |
Occurrence: accident or incident.
Safety factor: an event or condition that increases safety risk. In other words, it is something that, if it occurred in the future, would increase the likelihood of an occurrence, and/or the severity of the adverse consequences associated with an occurrence. Safety factors include the occurrence events (e.g. engine failure, signal passed at danger, grounding), individual actions (e.g. errors and violations), local conditions, current risk controls and organisational influences.
Contributing factor: a safety factor that, had it not occurred or existed at the time of an occurrence, then either: (a) the occurrence would probably not have occurred; or (b) the adverse consequences associated with the occurrence would probably not have occurred or have been as serious, or (c) another contributing factor would probably not have occurred or existed.
Other factors that increased risk: a safety factor identified during an occurrence investigation, which did not meet the definition of contributing factor but was still considered to be important to communicate in an investigation report in the interests of improved transport safety.
Other findings: any finding, other than that associated with safety factors, considered important to include in an investigation report. Such findings may resolve ambiguity or controversy, describe possible scenarios or safety factors when firm safety factor findings were not able to be made, or note events or conditions which ‘saved the day’ or played an important role in reducing the risk associated with an occurrence.
Safety issue: a safety factor that (a) can reasonably be regarded as having the potential to adversely affect the safety of future operations, and (b) is a characteristic of an organisation or a system, rather than a characteristic of a specific individual, or characteristic of an operational environment at a specific point in time.
Safety action: the steps taken or proposed to be taken by a person, organisation or agency in response to a safety issue.
Pilot details
Licence details: | Commercial Pilot (Helicopter) Licence, issued December 2014 |
Endorsements: | Gas turbine engine (GTE) |
Ratings: | Single-engine helicopter (SEH), R44, R22; Low level – Aerial mustering helicopter, Sling operations |
Medical certificate: | Class 1, valid to February 2017 |
Aeronautical experience: | Approximately 5,715 hours |
Last flight review: | 29 May 2016 |
Aircraft details
Manufacturer and model: | Robinson Helicopter Company R44 II | |
Year of manufacture: | 2007 | |
Registration: | VH-ZNZ | |
Operator: | Stock-Air Heliworks | |
Serial number: | 11954 | |
Total Time In Service | 1,713.3 (as of last recorded maintenance on 15 Sept 2016) | |
Type of operation: | Charter - Passenger | |
Persons on board: | Crew – 1 | Passengers – 1 |
Injuries: | Crew – 1 (serious) | Passengers – 1 (fatal) |
Damage: | Destroyed |