Executive summary
What happened
On 11 April 2024, a Cessna 404 Titan was being operated on an aerial survey flight north of Emerald, Queensland, with 3 crew members onboard. During the survey run, the crew was affected by fumes inside the cabin and chose to return to Emerald. At 1538, the aircraft landed successfully at Emerald Airport, where all 3 crew members received medical treatment for impairment symptoms. The aircraft was temporarily withdrawn from service for examination.
What the ATSB found
The ATSB found that operating crew members were all affected by fumes in the cabin and, possibly due to the associated impairment, the pilot returned the aircraft to Emerald rather than diverting and landing at a closer alternate airport. Despite extensive ground and in‑flight examination after the occurrence, the source of the fumes could not be established.
What has been done as a result
On 30 April 2024, the operator issued a mandatory requirement for all pilots on all flights – including those below flight levels – to secure the onboard oxygen equipment within seated reach of the pilot-in-command. As an additional risk control, the operator also required photographic evidence of this to be forwarded to the Head of Flight Operations (HOFO) prior to departure.
On 2 May 2024, the operator issued guidance to all pilots via Notices to Aircrew (NOTACs) regarding the circumstances in which oxygen should be used in‑flight. The operator recommended that supplementary oxygen be used in the following circumstances:
- discharge of a fire extinguisher in aircraft cabin
- smoke or fumes in cabin
- suspected CO in cabin
- any other occasion where oxygen may assist the health or wellbeing of a crew member.
Pilots were also advised to follow existing standard operating procedures and conduct a precautionary landing as soon as possible in the event of smoke, fumes, or gas in the cabin. This guidance was also incorporated into the operator’s emergency training modules.
Safety message
Fumes and airborne contaminants can result in the rapid onset of incapacitation that significantly affects crew decision‑making, communication and aircraft handling ability. The degree of physical or cognitive incapacitation can also vary widely between individuals, which may make it difficult to detect and respond to fume events.
Operating crews should therefore be alert to the potential hazards posed by odours and fumes and not hesitate to use supplemental oxygen and all other available means to ventilate the cabin. It is also important to be aware of alternate airports en route, and consider diverting to reduce the airborne exposure time. Crews should also communicate the presence of fumes, and any symptoms being experienced, to air traffic control at the first available opportunity as this will maximise the assistance available to crews both in the air and on the ground.
The investigation
Decisions regarding the scope of an investigation are based on many factors, including the level of safety benefit likely to be obtained from an investigation and the associated resources required. For this occurrence, a limited-scope investigation was conducted in order to produce a short investigation report, and allow for greater industry awareness of findings that affect safety and potential learning opportunities. |
The occurrence
On 11 April 2024, a Cessna 404 Titan was being operated by Aero Logistics on an aerial survey flight north of Emerald, Queensland. The flight was being operated under visual flight rules,[1] with one pilot and 2 task specialists operating the survey equipment. At 1317 local time, the aircraft departed Emerald Airport to the north-east before turning towards Moranbah and climbing to an altitude of 5,000 ft (Figure 1).
Figure 1: Survey area location and recorded flight path between Emerald and Moranbah
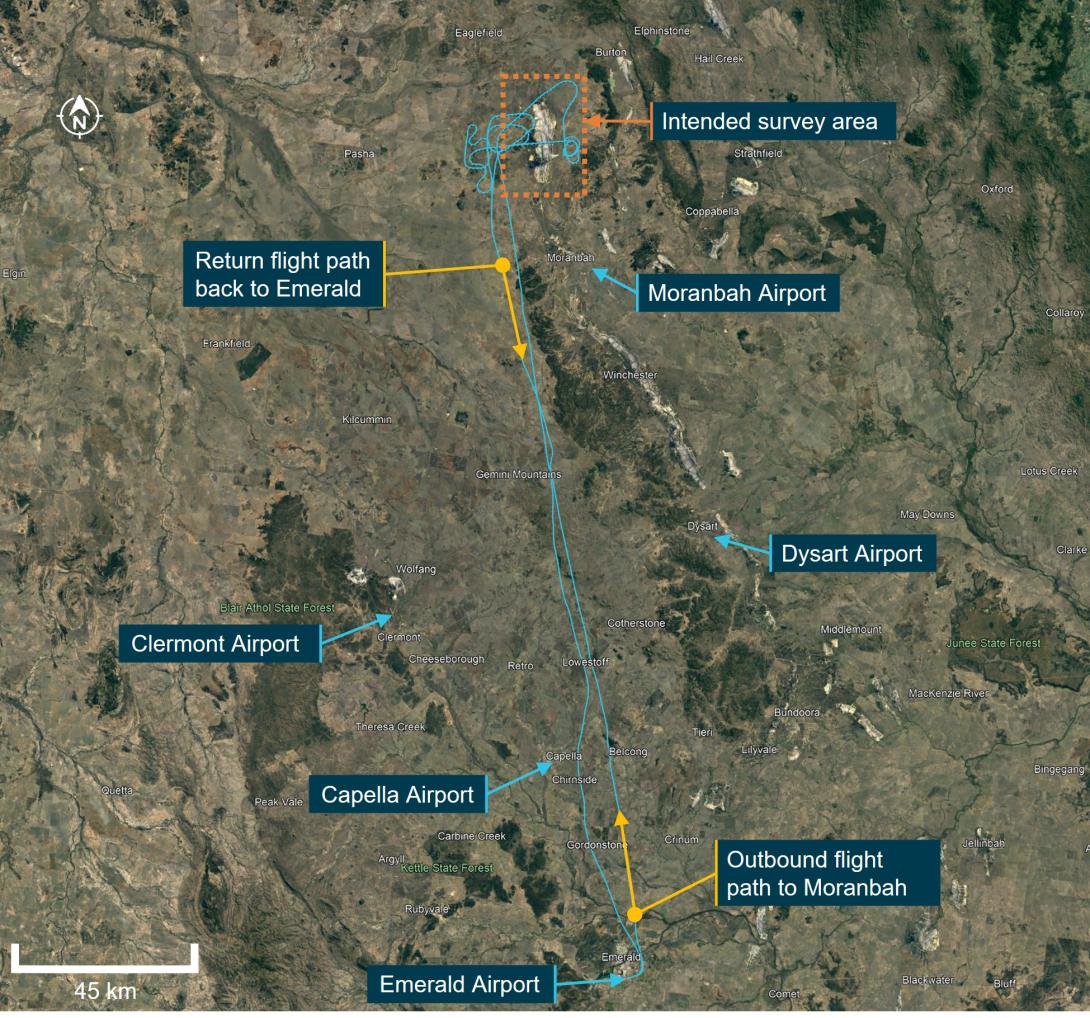
Source: Google Earth and operator ADS-B data, annotated by the ATSB.
At around 1349, the aircraft approached the Moranbah area and was descended to 4,000 ft to begin the first survey run. This required the aircraft to maintain a constant altitude and speed while travelling along specific parallel ‘lines’ overhead the target area as instructed by the task specialists. Approximately 20 minutes into this run, all 3 crew members started to notice a sporadic smell in the cabin, although their recollection of the smell differed.
The pilot advised that, as the flight progressed, they noticed that they had increasing difficulty setting the aircraft up and aligning it correctly. One of the task specialists also began to feel affected by the fumes, and at 1449 the pilot cancelled the survey and commenced a return to Emerald Airport. The first task specialist moved to the rear of the aircraft due to the extent of their respiratory symptoms. The second task specialist was not experiencing any symptoms at this stage, and repositioned to the cockpit to assist the pilot if needed.
Return to Emerald
During the return to Emerald, the crew opened the windows, vents, and cabin door to ventilate the cabin. They also disconnected the survey equipment and checked several aircraft systems, including ensuring that the autopilot was selected off, in an attempt to control or reduce the fumes. None of these measures resulted in any improvement, and the pilot and task specialists reported experiencing worsening symptoms as the flight progressed, but the nature and extent of these symptoms varied between each person. Although several diversionary airports were available en route, the pilot chose to continue to the base at Emerald.
Approximately 15 minutes from Emerald, the pilot considered conducting a precautionary landing in a field, due to worsening symptoms. They initiated a descent, and made a broadcast to Brisbane Centre, advising they were ‘landing somewhere in a field hopefully’.
Recorded flight data showed that, during this descent, the aircraft reached a maximum descent rate of 2,664 ft/minute. The pilot levelled the aircraft off at around 2,200 ft, approximately 14.5 km north‑east of Capella Airport. However, the pilot did not consider a diversion to Capella at that time. The pilot advised that they had managed to get some fresh air and decided to continue.
Several minutes later the pilot observed that the trim wheel started what they assessed as an uncommanded nose down input, and that ‘the autopilot was actually now trying to push us into the ground.’ In response, the pilot asked the task specialist seated beside them to hold the trim wheel, which rectified the issue. The task specialist confirmed that the trim wheel was moving but that they did not require significant force to stop it. They also advised that it was possible the pilot accidently activated the electric trim switch on the control column.
Landing
The pilot advised air traffic control that they were experiencing fumes in the cabin, but they did not mention any control issues with the aircraft. They declined an offer for emergency services on arrival, and no MAYDAY[2] or PAN PAN[3] calls were heard or recorded by air traffic controllers at any point during the flight. The pilot continued to Emerald where, after confirming the wind direction on their electronic flight bag, and informing other traffic of their intentions, tracked for a right base leg of the circuit for runway 24,[4] and landed at 1538.
Although the pilot had not requested emergency services, the Brisbane Centre controller called the aerodrome reporting officer (ARO) at Emerald Airport to advise them of the aircraft’s approach. The ARO then called emergency services at around 1530, and several Queensland Fire and Emergency Service (QFES) appliances were waiting at the parking bay when the aircraft landed. The crew was able to disembark unassisted, but one task specialist exited the aircraft and lay down on the grass next to the aircraft due to nausea. The second task specialist reported having a headache towards the end of the flight.
The ARO did not detect any fumes or smoke when they opened the rear door of the aircraft. The operator’s chief engineer entered the aircraft and similarly could not identify any smells, fumes, or smoke inside the aircraft. QFES crews then attended the aircraft, conducting a thermal scan and gas sampling of the interior with nil results. All of the internal panels and the flooring were removed for inspection and the QFES crews did not detect any fluid leaks internally or externally, but the aircraft was isolated overnight as a precaution.
The crew was attended to by paramedics at the scene before being transported to Emerald Hospital. They were given several hours of high-flow oxygen as a standard treatment and cleared to leave hospital later that evening. Blood samples were not taken from the crew as Emerald Hospital did not have the equipment required for blood gas testing. The aircraft was temporarily withdrawn from service for additional examination and testing.
Context
Crew information
Pilot
The pilot was experienced with piston and turboprop aircraft, and possessed the relevant qualifications and competencies for the work being conducted. The pilot had several decades of experience conducting freight, passenger, and recreational flights with a number of operators across Australia and overseas. The pilot had recently joined the operator to operate their piston aircraft. The pilot had passed their most recent aviation medical examination in July 2023.
Task Specialist 1
Task specialist 1 (TS1) was experienced with aerial survey work, having worked for a number of years with the owner/operator of the aerial survey equipment installed on the aircraft. Most of their experience had been in Cessna 404 and 406 series aircraft, and they had not previously experienced fumes or smells inside the cabins of these aircraft.
Task Specialist 2
Task specialist 2 (TS2) had limited experience on the Cessna 404 and had spent most of their time on Cessna 406 and 441 series aircraft. At the time of the occurrence, they were in the process of obtaining an aeroplane pilot licence, with several hours of flight time already logged. TS2 had experienced fumes in another aircraft several years earlier caused by a fault in the air conditioning system, but had not encountered anything similar in the Cessna 404.
Response to fumes and symptoms
When the crew decided to cancel the survey run, the aircraft was around 37 km north‑west of Moranbah Airport and Emerald was around 200 km south. The pilot advised that they would have had to declare an emergency to land at Moranbah Airport, as it was a private airport, and at that stage they did not consider there was an emergency. They had also experienced a flap issue the day before with resultant fumes in the cockpit and they considered this to be a similar event.
The pilot had completed emergency response and hypoxia awareness training in November 2023 and had been issued a pulse oximeter as part of the operator’s standard induction process. The aircraft had oxygen equipment onboard and the pilot and both task specialists were trained in how to use this equipment. The task specialists confirmed that the pilot had given an emergency briefing prior to departure. They could not recall whether the onboard oxygen equipment had been mentioned specifically, however there had been no plan to fly above 10,000 ft.
The crew confirmed that during the return to Emerald, they used a supplied pulse oximeter to assess the oxygen saturation levels in their blood several times – however, none of the crew considered using the onboard oxygen equipment.
Aircraft information
The aircraft was a Cessna Aircraft Company 404 Titan, manufactured in 1978 and equipped with 2 Teledyne Continental GTSIO-520-M engines. It was one of 7 such aircraft in the operator’s fleet. The operator told the ATSB that these aircraft were not modified from the original Cessna 404 design apart from the floor cutouts for the survey equipment unit. This unit was placed above the fuselage cutout at the rear of the cabin and secured to the floor with the cameras and sensors facing downwards.
The survey operators would usually place aluminium tape or cardboard around the unit to seal any gaps between the unit and the cutout in the floor. The operator also confirmed that the cable routing and electrical harnesses for the equipment and aircraft systems had been arranged and routed in a standard configuration around the cutouts in the fuselage.
Maintenance information
On 10 April, the day prior to the incident, the same aircraft with the same crew was conducting similar survey runs north of Emerald. The pilot said that during this flight they experienced an uncommanded extension of the flaps to the full-down position after the flaps were extended to Flap 10. The pilot attempted to troubleshoot the problem by moving the flap lever back and forth, but the flaps did not respond to movements of the flap lever. The pilot also began to notice a smell in the cabin when the flap issue commenced, and that their airspeed was lower than expected. The pilot decided to return to Emerald, but did not advise the maintenance personnel of the presence of fumes.
An engineering inspection found that the wires on the micro-switch had detached from the flap select lever. The operator said that this inspection also found that ‘the wire hadn't touched any surrounding areas, hadn't tripped, hadn't burned or anything like that’. The wires were checked and reconnected on the morning of 11 April, and the flap lever was tested before the aircraft was released back into service that day. No flap issues were detected after this repair was made.
Following the incident flight, the operator undertook flight tests, scheduled maintenance, and strip‑down examinations of aircraft wiring and componentry, including inspections and testing of:
- panels and flooring, which were removed to inspect for electrical wiring damage
- the autopilot and electrical trim systems
- around and underneath the cockpit dash and pilot side electrical panel and relay boxes
- the battery and lighting systems
- the heater and ventilation systems
- the engines, including alternators and electrical looms
- the hydraulic system
- the nose and main landing gear bays and wiring
- the tail interior and flight controls
- the left and right inner wings
- the flap coves and flight controls
- the nose locker and wing lockers including interior lighting.
No mechanical or wiring issues that could have been related to fumes were detected. The survey operator found no wiring defects or component faults in their survey equipment unit, which was then reassembled and installed on a different aircraft. The operator also confirmed that there was a card-based carbon monoxide and a digital aural CO detector on the aircraft, and that neither of these detectors had activated during the incident flight or the test flights conducted after the occurrence. Additionally, neither the pilot nor task specialists recalled either CO monitor activating during the occurrence flight.
Environmental
Weather
Weather data was requested from the Bureau of Meteorology (BOM) for winds aloft and automated METARs[5] in the area between Emerald and Mackay. This data confirmed that visual meteorological weather conditions[6] existed, with temperatures around 25 ˚C and cloud cover[7] ranging between few and scattered up to altitudes of around 5,000 ft. These conditions were consistent for the duration of the flight.
Bushfires and mining activity
The crew did not observe any blast fumes or mining activity in the Moranbah area during the incident flight. BOM data also confirmed no known plumes and smoke in the area. Queensland government data on mining activity and blast fumes was requested but this was not provided. The pilot did not indicate the presence of any bushfires or smoke that could have generated fumes, and TS2 stated that there were some minor grass fires in the area, but these were not in the immediate vicinity of the flight path.
The operator confirmed through post-flight testing that ground-based fumes and smells could ‘be picked up within the cabin with the environmental settings open in the venting configuration’. The operator also described a smoke smell in the cabin during the post-incident test flight when the aircraft flew directly overhead a local grass fire. However, this smell was only temporary and limited to the specific fire area and was markedly different to the smell described by the crew.
Safety analysis
During the return flight to Emerald following the onset of impairment symptoms, the crew could not identify the source of the fumes inside the cabin. Based on the available evidence, no definitive cause or source for the fumes could be established. There were no visible signs of smoke or leaks, and there were no environmental conditions that could have consistently generated fumes inside the cabin. The onboard CO detectors did not activate, and post-incident testing by QFES did not identify noxious gases or thermal hotspots. The operator was also unable to identify any faults or defects in the wiring or componentry of the onboard systems and could not replicate the fumes in test flights.
Although the decision to cancel the survey run was prudent, flying back to Emerald, rather than diverting to closer suitable airports exposed the crew to the fumes for longer than necessary and may have worsened the impact. However, this decision may have been influenced by the flap‑related incident on the previous day. In addition, although the crew was trained to use the supplemental oxygen equipment onboard, and repeatedly used the pulse oximeters, the crew did not consider using the available oxygen.
It is probable that all the crew members were affected by the fumes, although these symptoms presented differently in each crew member. TS1, sitting at the rear of the aircraft, reported nausea and respiratory symptoms. TS2 reported experiencing a headache. The pilot did not experience any physical symptoms but may have been experiencing cognitive impairment in terms of their decision-making and aircraft handling, even though the pilot navigated and controlled the aircraft as per the established procedures and communicated effectively on the radio.
The pilot’s decision not to declare a MAYDAY or PAN PAN, or to have emergency services in attendance for the landing, may have been a result of their impaired decision‑making. Fortunately, the controller proactively initiated the emergency response by alerting the ARO.
Findings
ATSB investigation report findings focus on safety factors (that is, events and conditions that increase risk). Safety factors include ‘contributing factors’ and ‘other factors that increased risk’ (that is, factors that did not meet the definition of a contributing factor for this occurrence but were still considered important to include in the report for the purpose of increasing awareness and enhancing safety). In addition, ‘other findings’ may be included to provide important information about topics other than safety factors. These findings should not be read as apportioning blame or liability to any particular organisation or individual. |
From the evidence available, the following findings are made with respect to the fumes event involving Cessna 404, VH-LAD, near Moranbah, Queensland on 11 April 2024.
Contributing factors
- The operating crew was affected by fumes in the cabin and the pilot returned the aircraft to Emerald rather than landing at a closer suitable alternate airport.
Other findings
- Despite extensive post‑occurrence ground and in‑flight examination, the source of the fumes could not be established.
Safety actions
Whether or not the ATSB identifies safety issues in the course of an investigation, relevant organisations may proactively initiate safety action in order to reduce their safety risk. The ATSB has been advised of the following proactive safety action in response to this occurrence. |
Safety action by Aero Logistics
Prior to the commencement of the ATSB investigation, the operator proactively took several steps in response to the incident.
Placement of oxygen equipment
On 30 April 2024, the operator issued a mandatory requirement for all pilots on all flights – including those below flight levels – to secure the onboard oxygen equipment within seated reach of the pilot-in-command. As an additional risk control, the operator also required photographic evidence of this to be forwarded to the Head of Flight Operations (HOFO) prior to departure.
Use of oxygen equipment
On 2 May 2024, the operator issued guidance to all pilots via Notices to Aircrew (NOTACs) regarding the circumstances in which oxygen should be used in‑flight. The operator recommended that supplementary oxygen be used in the following circumstances:
- discharge of a fire extinguisher in aircraft cabin
- smoke or fumes in cabin
- suspected CO in cabin
- any other occasion where oxygen may assist the health or wellbeing of a crew member.
Pilots were also advised to follow existing standard operating procedures and conduct a precautionary landing as soon as possible in the event of smoke, fumes, or gases in the cabin. This guidance was also incorporated into the operator’s emergency training modules.
Sources and submissions
Sources of information
The sources of information during the investigation included:
- the operating crew
- Aero Logistics
- Airservices Australia
- Bureau of Meteorology
- recorded data from the ADS-B unit on the aircraft.
Submissions
Under section 26 of the Transport Safety Investigation Act 2003, the ATSB may provide a draft report, on a confidential basis, to any person whom the ATSB considers appropriate. That section allows a person receiving a draft report to make submissions to the ATSB about the draft report.
A draft of this report was provided to the following directly involved parties:
- the operating crew
- Aero Logistics
- the Civil Aviation Safety Authority.
No submissions were received.
Purpose of safety investigationsThe objective of a safety investigation is to enhance transport safety. This is done through:
It is not a function of the ATSB to apportion blame or provide a means for determining liability. At the same time, an investigation report must include factual material of sufficient weight to support the analysis and findings. At all times the ATSB endeavours to balance the use of material that could imply adverse comment with the need to properly explain what happened, and why, in a fair and unbiased manner. The ATSB does not investigate for the purpose of taking administrative, regulatory or criminal action. TerminologyAn explanation of terminology used in ATSB investigation reports is available here. This includes terms such as occurrence, contributing factor, other factor that increased risk, and safety issue. Publishing informationReleased in accordance with section 25 of the Transport Safety Investigation Act 2003 Published by: Australian Transport Safety Bureau © Commonwealth of Australia 2024 Ownership of intellectual property rights in this publication Unless otherwise noted, copyright (and any other intellectual property rights, if any) in this report publication is owned by the Commonwealth of Australia. Creative Commons licence With the exception of the Coat of Arms, ATSB logo, and photos and graphics in which a third party holds copyright, this publication is licensed under a Creative Commons Attribution 3.0 Australia licence. Creative Commons Attribution 3.0 Australia Licence is a standard form licence agreement that allows you to copy, distribute, transmit and adapt this publication provided that you attribute the work. The ATSB’s preference is that you attribute this publication (and any material sourced from it) using the following wording: Source: Australian Transport Safety Bureau Copyright in material obtained from other agencies, private individuals or organisations, belongs to those agencies, individuals or organisations. Where you wish to use their material, you will need to contact them directly. |
[1] Visual flight rules (VFR): a set of regulations that permit a pilot to operate an aircraft only in weather conditions generally clear enough to allow the pilot to see where the aircraft is going.
[2] MAYDAY: an internationally recognised radio call announcing a distress condition where an aircraft or its occupants are being threatened by serious and/or imminent danger and the flight crew require immediate assistance.
[3] PAN PAN: an internationally recognised radio call announcing an urgency condition which concerns the safety of an aircraft or its occupants but where the flight crew does not require immediate assistance.
[4] Runway number: the number represents the magnetic heading of the runway.
[5] METAR: a routine report of meteorological conditions at an aerodrome. METAR are normally issued on the hour and half hour.
[6] Visual Meteorological Conditions (VMC): an aviation flight category in which visual flight rules (VFR) flight is permitted – that is, conditions in which pilots have sufficient visibility to fly the aircraft while maintaining visual separation from terrain and other aircraft.
[7] Cloud cover: in aviation, cloud cover is reported using words that denote the extent of the cover – ‘few’ indicates that up to a quarter of the sky is covered, ‘scattered’ indicates that cloud is covering between a quarter and a half of the sky.