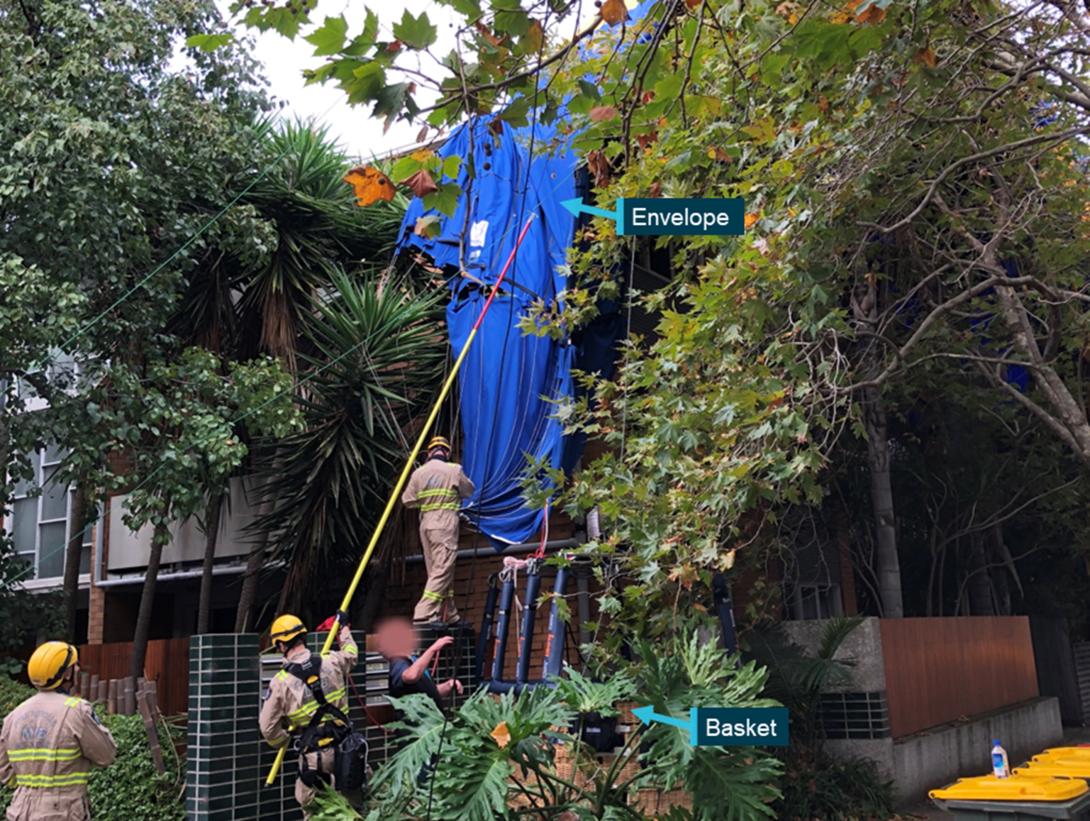
An ATSB investigation into a serious hot air balloon incident in a Melbourne bayside suburb last year highlights the importance of engineering rigour in analysis, design and testing.
On the morning of 20 April 2022, a sightseeing balloon took off from Royal Park, Melbourne, with 13 passengers and a pilot on board, with the intended destination of Moorabbin Airport. It was the first flight of the balloon since its manufacture.
Travelling south-east over the Melbourne CBD, the pilot observed gaps in the balloon’s circular top vent – a panel-covered opening designed to allow the pilot to let air out of the envelope. The gaps meant the balloon was leaking air without pilot input.
The pilot was unable to seal the vent as there was a fault with the balloon’s deflation system, and a large amount of fuel had to be burned to keep the balloon aloft.
Unable to conduct a more immediate landing at Fawkner Park, the pilot opted to attempt a landing at Elwood Beach.
During the approach to the beach, and without precise altitude control, the pilot struggled to keep the balloon clear of buildings, despite almost continually burning one or two of the balloon’s three burners.
The balloon’s basket collided with two rooftops, and liquid fuel for two of the balloon’s three burners was exhausted.
The pilot continued to activate the remaining burner as the balloon descended through trees, before coming to rest outside an apartment building.
The balloon and basket sustained minor damage, and three passengers sustained minor injuries.
“The balloon’s modified deflation system leaked air once internal pressure in the envelope reached a certain point during normal operation,” ATSB Director Transport Safety Stuart Macleod said.
“At the request of the operator, the balloon manufacturer developed and approved a modification to the balloon's deflation system.
“However, the manufacturer made incorrect assumptions about the modification and subsequently did not conduct the required tests or analysis during the design phase to ensure it was safe for use.”
After the balloon was manufactured with the modified deflation system, the fault went unnoticed during the manufacturer’s production testing process because the air temperature inside the envelope was below the minimum required value.
“For reasons that could not be determined, the actual internal envelope air temperature reached during the production test was lower than recorded, and below the minimum required value.”
This discrepancy meant envelope pressure did not get high enough during the test for the fault in the modified deflation system to manifest.
The manufacturer, Kubicek Balloons, implemented several safety actions in response to the accident.
These include annual calibration of temperature sensors, an update to the production inflation test procedure, and revisions to the production quality control checklist to verify whether any balloon modifications and required tests were completed.
“This investigation highlights the importance of engineering rigour in analysis, design, and testing,” Mr Macleod said.
“Any assumptions used in the engineering analysis and design of safety critical features on aircraft must be based on sound engineering logic, subject to rigorous review to assess their validity, and documented.
“This investigation also demonstrates that robust procedures and processes must be in place to ensure measurements taken during testing are valid, accurate and reliable.”
Read the final report: Collision with terrain involving Kubicek Balloons BB78Z, VH RJR, 15 km north-west of Moorabbin Airport, Victoria on 20 April 2022