Executive summary
What happened
On the morning of 27 June 2023, the pilot of a Robinson Helicopter R22 Beta II, registered VH‑PSC and operated by Top End Mustering, was conducting mustering operations in company with a second R22 registered VH-RCS, on Limbunya Station, Northern Territory.
After not hearing from the pilot of VH-PSC for some time, the pilot of VH-RCS attempted to contact VH-PSC with no response received, and the ground mustering crew stated that they had no recent communication either. Subsequently, the pilot of VH-RCS commenced a search and shortly after located the wreckage of VH-PSC. The helicopter was destroyed, and the pilot had sustained fatal injuries.
What the ATSB found
The ATSB found that, for reasons that could not be determined, VH-PSC collided with terrain in a nose and right-side down orientation. The site and wreckage examination identified signatures consistent with low rotor energy and low-to-nil engine power.
There was no evidence of any flight control or mechanical system abnormality that would have prevented the helicopter from operating normally. In addition, in the absence of an identified problem with the helicopter, the reason for the loss of control could not be determined.
The ATSB also identified that the maintenance release contained no endorsements for daily inspection certification, hours flown, total time‑in‑service or engine oil uplift. This was despite VH‑PSC being operated daily since its issue 13 days prior. A scheduled 25-hour engine oil and filter change had reportedly been conducted, however, had not been certified on the maintenance release. Further, the absence of recorded operating hours increased the risk of the helicopter having been operated beyond other scheduled maintenance requirements.
Safety message
Routine low-level flight brings several significant complexities to a helicopter operation including management of emergencies and the conduct of forced landings. Time to respond and the availability of suitable forced landing areas may also be significantly reduced. Main rotor energy management is an important element of maintaining control and safely landing a helicopter.
Aircraft owners and pilots should ensure that the maintenance release is updated at the end of each day’s flying. This will allow all pilots to be aware of the operational status of the aircraft and to avoid unintentional flight beyond scheduled maintenance. In addition, engine oil uplift records assist with trend monitoring of engine condition.
The investigation
Decisions regarding the scope of an investigation are based on many factors, including the level of safety benefit likely to be obtained from an investigation and the associated resources required. For this occurrence, a limited-scope investigation was conducted in order to produce a short investigation report, and allow for greater industry awareness of findings that affect safety and potential learning opportunities. |
The occurrence
On 27 June 2023, at about 0700 local time,[1] the pilot of a Robinson Helicopter R22 Beta II, registered VH‑PSC (PSC), and operated by Top End Mustering, departed Limbunya Station, Northern Territory, in company with a second R22 registered VH‑RCS (RCS). Their task was to muster stock in a small paddock to the north of ‘GB’ bore, about 29 km to the south-east of the station homestead. In addition, they were to assist the ground mustering crew (on horseback and motorcycles) to move stock that had been mustered the previous day from ‘no 22’ paddock into the GB bore holding yards, to the ‘no 18’ yards (Figure 1). RCS was working the western side of the paddock, with PSC working down the eastern side. The helicopter pilots could communicate with each other via very high frequency (VHF) or ultra high frequency (UHF) band radios, and with the ground mustering crew via UHF.
The helicopters arrived at the northern end of the paddock at about 0730 and began pushing cattle south towards the GB bore holding yards. The pilot of PSC then supported the ground mustering crew in moving stock from the yards into a fenced laneway. The laneway would guide the stock to the no 18 holding yards that were located about 8 km to the south‑west.
At about 0915, when the cattle were moving along the laneway under the control of the ground mustering crew, the pilot of PSC was released from that task, and returned to assist the pilot of RSC with completing the mustering task.
At about 0930, the pilot of RCS diverted to Manu bore to refuel the helicopter from drum stock. After refuelling, the pilot of RCS departed back to the small paddock, and at about 0945 acknowledged a departure call from the pilot of PSC, on VHF radio, who had also completed refuelling at Manu bore.
Following a period of radio silence, the pilot of RCS contacted the head musterer at about 1000, via UHF, to enquire if they had been in contact with the pilot of PSC. The head musterer advised that no contact had occurred since about 0915. Having received no replies from PSC to their radio calls, the pilot of RCS commenced searching the area around Manu bore, and then progressed the search towards GB bore.
After about 15 to 20 minutes, the pilot of RCS located the wreckage of PSC. The helicopter was destroyed, and the pilot had sustained fatal injuries. There were no witnesses to the accident.
Figure 1: Limbunya Station and operational area
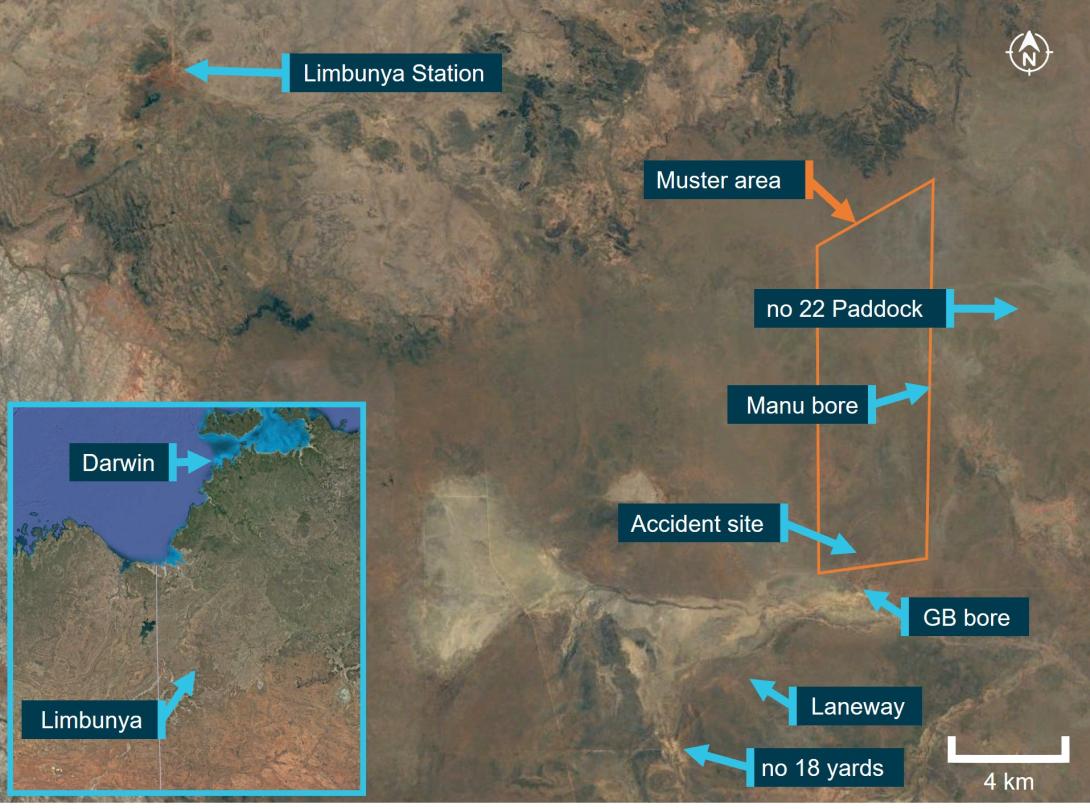
Source: Google Earth, annotated by the ATSB
Context
Pilot information
Qualifications and experience
The pilot held a Commercial Pilot Licence (Aeroplane) since 1985, a Commercial Pilot Licence (Helicopter) since 1986 and a valid Class 1 Aviation Medical Certificate. The pilot also held helicopter gas turbine engine and night visual flight rules ratings. Additionally, the pilot held a low‑level aerial mustering (aeroplane and helicopter) rating and helicopter sling operations, valid until 3 April 2025.
On 3 April 2023, the pilot underwent a flight review in an R22, with a helicopter low-level flight review and a company pilot proficiency check also conducted at the same time, at Kununurra, Western Australia. The pilot demonstrated proficiency with emergency procedures and the instructor’s handwritten flight review note stated, ‘all to a good standard. Placed a lot of emphasis on power management’.
The last entry in the pilot’s helicopter logbook was dated 10 July 2021, almost 2 years prior to the accident, with a total helicopter aeronautical experience of 12,288.1 hours. Using several sources of information, the ATSB calculated the pilot had about 14,000 flying hours on helicopters at the time of the accident, including over 3,000 hours on the R22 helicopter type.
Recent history
The pilot relocated to Kununurra and had been operating the R22, R44 and Bell 206-series helicopters across north-western Australia since 3 April 2023. The pilot had operated several helicopters most days from 5 June 2023, and VH-PSC (PSC) exclusively since 21 June 2023.
On 25 June, the pilot ferried PSC to Limbunya Station, arriving around 1800. On 26 June, the pilot conducted mustering operations at the station, with 2 other company R22 helicopters, from about 0630 until about 1300.
The second helicopter pilot and several members of the ground mustering team reported the pilot was in good spirits at dinner the night before the accident and retired to their room about 2130.
The ATSB considered whether the pilot’s activity in the preceding days and months may have led to them being fatigued at the time of the accident. A review of the pilot’s diary indicated they had operated a helicopter for all but 19 days in the preceding 90 days, totalling over 340 hours of duty time.[2] The diary indicated over 170 hours in the preceding 30 days and about 47 hours in the 7 days prior to the accident. The accident occurred on the 14th consecutive day of duty. However, the ATSB noted a short ferry flight on 25 June, the pilot being relieved from duty about midday on 26 June and being on duty for less than 5 hours on the day of the accident. It was possible that the months of extensive work time coupled with high workload operations had the potential to produce cumulative fatigue. However, noting the workload and opportunity for rest in the preceding days, there was insufficient evidence to establish if the pilot was likely experiencing a level of acute fatigue known to affect performance at the time of the accident.
Helicopter information
General
VH-PSC was a Robinson Helicopter Company (RHC) R22 Beta II helicopter, serial number 4429, powered by a Textron Lycoming O-360-J2A, 4-cylinder carburetted piston engine (Figure 2). It was manufactured in the United States in December 2008 and first registered in Australia in January 2009.
The R22 has 2 seats, with the pilot flying from the right seat, and each seat was fitted with a seatbelt and inertia reel shoulder strap, similar to those used in motor vehicles. The helicopter was not fitted with an optional cabin heating system.[3] Typical for mustering activities, the helicopter was being operated with both doors removed.
Figure 2: VH-PSC
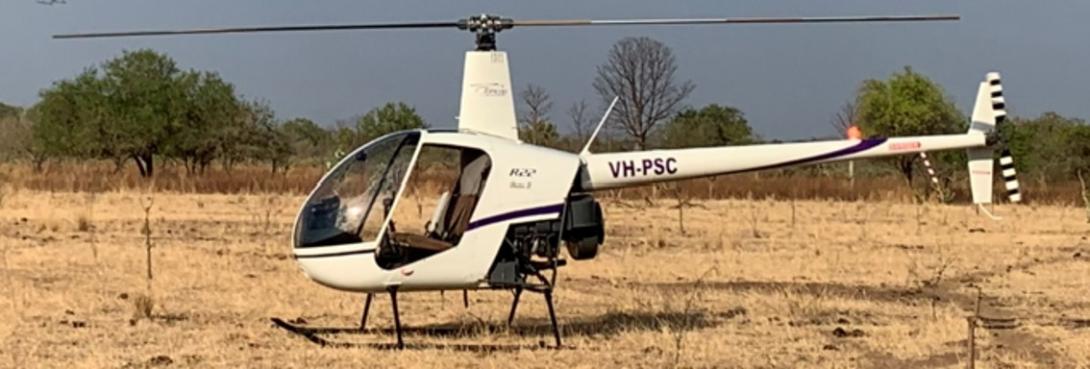
Source: Operator
Systems information
Rotor drive system
The rotor drive system on the R22 helicopter uses 2 reinforced rubber drive belts (V-belts). The drive belts are double-banded and fitted to upper and lower multi-grooved sheaves. The upper sheave has an overrunning sprag clutch (freewheeling unit)[4] in its hub, which the clutch shaft passes through. The clutch shaft transmits power forward to the main rotor gearbox and aft to the tail rotor driveshaft. The lower sheave is attached directly to the engine crankshaft.
The upper sheave is moved, relative to the lower sheave, by means of an electric clutch actuator, thereby controlling the tension on the drive belts. This allows the engine to be unloaded during startup (drive belts slack) without the rotor system engaged, and then tensioned to allow engine power to be transmitted to the rotor drive (Figure 3).
The fanwheel utilised on the R22 is a commercial product, modified by RHC. Its purpose is to direct cooling air onto the engine. It is constructed of steel, and is comprised of 8 cooling vanes welded to the rear plate (on the engine side) and a support ring on the outer side. The assembly mounts onto the fan shaft, behind the lower sheave, and is enclosed in a fibreglass shroud.
The tail rotor was fitted with a visual warning guard located on the underside of the tailcone, just forward of the tail rotor. Painted with red and white stripes, it provides a visual warning of the tail rotor disc, which can be difficult to see when operating.
Figure 3: Diagram of the R22 rotor drive system
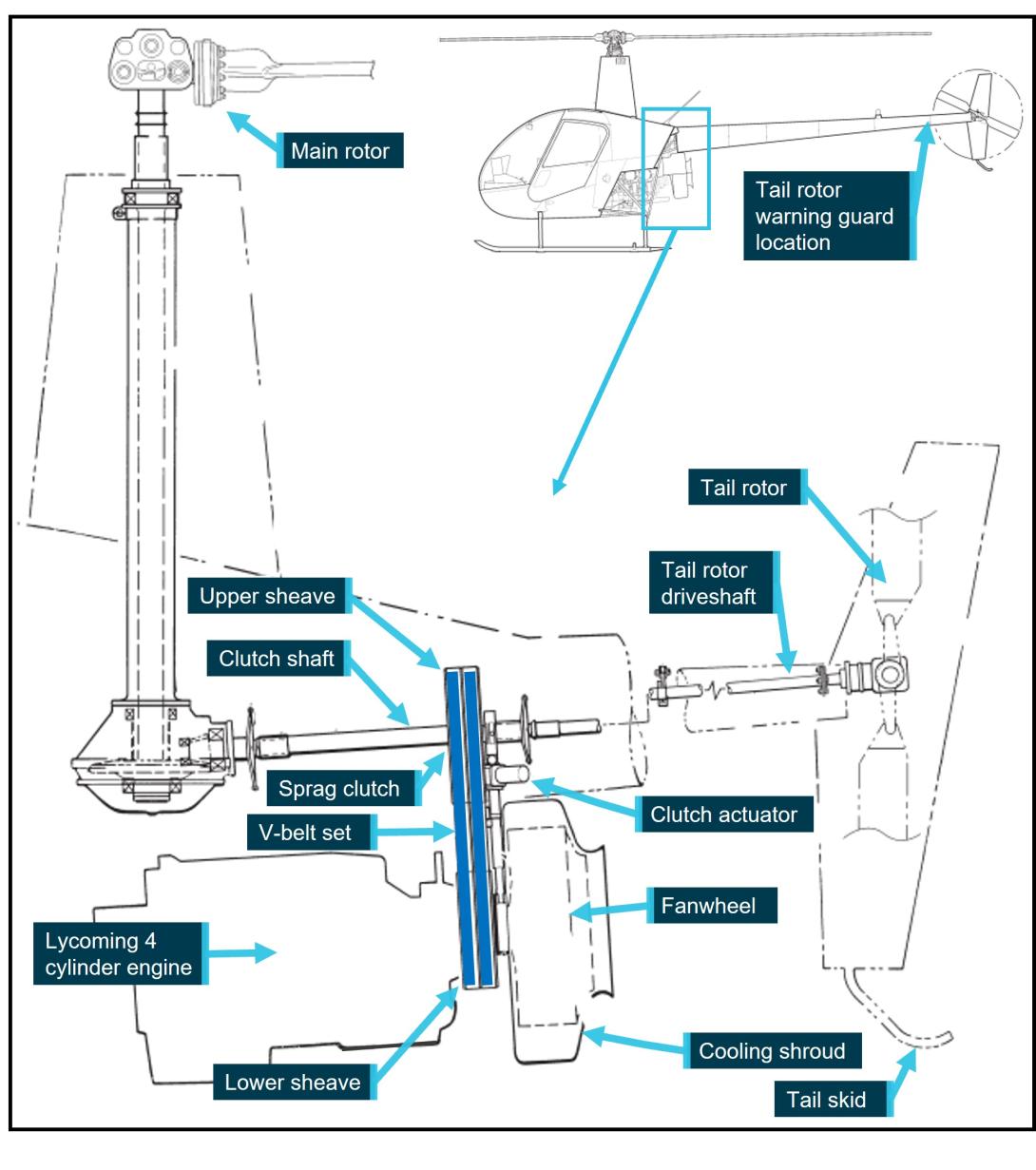
Source: Robinson Helicopter Company, annotated by the ATSB
Low rotor revolutions per minute (RPM) warning
A ‘low RPM’ warning light will illuminate, with an associated horn, when rotor RPM is at or below 97%, regardless of engine RPM.
Fuel system
The fuel system consists of a main tank (left side, when looking from the rear of the helicopter, 69 L) and an auxiliary tank (right side, 37 L). Fuel is gravity-fed via a gascolator to the carburettor.
Engine governor system
Under normal conditions, the governor senses engine RPM and makes adjustments to the throttle control to maintain a constant engine RPM, which leads to a constant rotor RPM in flight. The governor can be selected on or off using the toggle switch on the right seat’s collective.[5] The R22 pilot’s operating handbook (POH) stated that the governor may not prevent over- or under-speed conditions generated by aggressive flight manoeuvres. In the event of malfunction, the pilot can override the governor and manipulate the throttle to maintain engine RPM, until the governor can be selected off, or rendered inoperative by pulling the circuit breaker.
Given the dynamic nature of mustering operations, when compared to flying in cruise (normal flight conditions), the pilot was likely not relying on the governor.
Carburettor heat system
The helicopter was fitted with a carburettor heat system, which directed hot air collected from a scoop installed on the engine exhaust system, via a duct, to the engine induction air box. Within the air box was a sliding guillotine-type valve to proportion the mix of cool and heated air. The pilot could monitor the temperature of the carburettor air using the carburettor air temperature gauge on the instrument panel console.[6] The carburettor heat control knob was situated aft and rear of the cyclic,[7] with ‘down’ being no heat and ‘up’ providing full heat, or anywhere in between as selected by the pilot. This heated air prevented the temperature within the carburettor from dropping to, or below, the freezing point of water.
The helicopter also had a carburettor heat assist system, which automatically applied carburettor heat when lowering the collective, generally for descent, to reduce pilot workload. The pilot could override the heat assist. In addition, a latch was provided at the carburettor heat control knob to lock the heat assist off when not required.
Fuel rotary pump
The operator reported that each helicopter would carry a drum fuel pump, which could be broken down into components with the suction tube (standpipe) capable of being separated into 3 sections. The operator advised the fuel pump components could be stored under the left (passenger) seat or optionally store some, or all, of the pump components in the left seat footwell.
The pilot of RCS used their pump for refuelling from the drum stock at Manu bore.
Airworthiness and maintenance
General
A periodic inspection of the helicopter was to be conducted every 100 hours or 12 months, whichever came first. In addition, the helicopter was subject to an overhaul every 2,200 hours or 12 years. On 15 June 2023, the helicopter underwent a 100-hourly/annual inspection, during which the engine was replaced with a newly overhauled unit.[8] As part of the periodic inspection, the exhaust system was certified as being visually inspected and pressure tested. A new maintenance release was issued at this time, which stated that the helicopter had accrued 6,300.2 hours total time‑in‑service.
Maintenance release
The maintenance release (MR) is a legal document that is part of the ongoing airworthiness requirements of an aircraft and is divided into several parts. Part 1 details any scheduled maintenance that will be required to be completed during the MR period of validity. When a maintenance task has been completed it can be certified for in Part 2 of the MR, or in the aircraft maintenance logbook. The person who performed the maintenance, or the certificate of registration holder is then required to clear the entry in Part 1, making note if the certification was logged in Part 2 or the aircraft logbook. Part 3 of the MR is used to certify for the daily inspection of the aircraft, for recording the daily total flight time, calculating the total time-in-service at the end of each day’s flying and for tracking other events, such as engine oil uplift. The regulations state that, if the certificate of registration holder, the pilot in command or the operator becomes aware the aircraft may be operated beyond any maintenance requirement noted in Part 1, then they must make ‘an endorsement signed by him or her setting out the facts of the situation and stating that the aircraft is unairworthy, and thereupon the maintenance release ceases to be in force’.
The current MR was located at the accident site. An endorsement, in Part 1 of the MR, included that an engine oil and filter change was required at 25, 50 and 75 hours post engine change. Since its issue on 15 June 2023, there were no endorsements for daily inspection certification, hours flown, total time-in-service or engine oil uplift.
Pilot approved maintenance
The civil aviation regulations permitted the pilot to perform some maintenance including changing oil filters and changing or replenishing engine oil. Further, the regulations required that ‘a person who carries out maintenance … must ensure that completion of the maintenance is certified in accordance with … the CASA [Civil Aviation Safety Authority] system of certification of completion of maintenance’.
Engine oil and filter maintenance
Following fitment of any new, rebuilt or overhauled engine, RHC required Lycoming service bulletin 480 be complied with. The bulletin required an oil and filter change after the first 25 hours of engine operation and then an oil and filter change, along with suction screen inspection and cleaning, every 50 hours of operation, or 4 months, whichever came first.[9] In addition, the filter was to be cut open and the filter element carefully inspected for metal contamination. Further, oil uplift was to be recorded to enable monitoring of oil consumption.[10]
A text message from the pilot to the operator on 19 June 2023 stated that the 25-hour oil change on PSC had been conducted. The pilot also commented that the filter looked ‘pretty clean’ and that they had bagged the element (filter) with the intent to provide it to the operator the next day. The MR had not been endorsed to show this inspection had been completed. Neither the operator, or the maintainer, could locate the filter element to verify whether the maintenance had taken place. Text messages to the operator, which aligned with the pilot’s diary, indicated the helicopter may have accumulated an additional 25 hours following the first oil and filter change, prior to 27 June 2023. However, there were no records indicating the 50-hour oil and filter change had become due, nor if it was completed.
Weight and balance
There were no records to indicate fuel quantity onboard PSC following the refuel. The ATSB calculated the helicopter weight for ‘full fuel’ and for the quantity of fuel drained from PSC at the accident site. Both calculations determined that the helicopter was being operated within the approved weight and balance envelope.
Meteorological information
Witnesses in the area and the pilot of RCS reported that the weather conditions at the time of the accident consisted of overcast[11] cloud well above their operating height with no precipitation, a temperature of about 20–25 °C, and a slight breeze.
The weather station at Limbunya recorded precipitation only. The nearest Bureau of Meteorology station was located at Victoria River Downs, about 144 km to the north-east. At about the time of the accident, the temperature recorded was 27 °C and the dewpoint[12] was 15 °C. The wind was about 5 kt, variable between north and east-north-east. The graphical area forecast showed the accident site shared similar conditions with Victoria River Downs. The forecast grid point temperature was 2 °C lower. The actual temperature and dew point data was not available for the accident site.
According to the Civil Aviation Safety Authority Carburettor icing probability chart, the temperature and dewpoint at Victoria River Downs were on the edge of the ‘serious icing – descent power’ and ‘moderate icing – cruise power’ envelopes. Carburettor ice is formed when the normal process of vaporising fuel in a carburettor cools the carburettor throat so much that ice forms from the moisture in the airflow, which can restrict airflow to the engine. This is more likely to occur at low engine power settings, and may result in reduced power output, rough running and in some cases engine failure. The pilot of RCS advised the ATSB that their assessment of the local conditions was they were not conducive to carburettor icing. Therefore, they did not use carburettor heat and did not encounter any adverse effects to engine operation.
Recorded information
Flight data
The helicopter was not fitted with a flight data recorder or cockpit voice recorder, nor was it required to be. In addition, the operator did not utilise electronic tracking of the helicopter.
The ATSB obtained flight tracking data from the OzRunways application installed on the pilot’s mobile phone. The application was using the mobile telephone network to transmit data to the OzRunways[13] servers every 5 seconds, which included the current position, track, groundspeed and truncated altitude in increments of 100 ft.
The recorded data showed PSC being operated in a manner consistent with the other pilot’s description of the mustering activities that day. Following the departure from the station homestead, the helicopter was flown direct to the northern end of the paddock and then systematically flown back and forth within the operational area, while gradually heading south to the designated holding area (Figure 4).
The flight profile data showed PSC was operated generally about 300 ft (100 m) above the ground, with extremities between 80 and 800 ft above terrain. Following the refuel, the data showed the helicopter being operated slightly higher than before the refuel. However, this was consistent with the bulk of the cattle having been mustered and the requirement to go to a higher altitude to identify isolated cattle through the timber. The final data points showed a descent of about 750 ft (230 m), followed by about 30 seconds of relatively level flight between 180–345 ft (55–105 m), before the data ceased.
There were several periods of no data being recorded during the day, of between 5 and 10 minutes.[14] The tracking data stopped short of the accident site,[15] at 1011, which prevented analysis of the final stages of flight. It could not be determined if this lack of recorded data was consistent with earlier dropouts, or due to the collision with terrain interrupting normal function.
Figure 4: VH-PSC track data
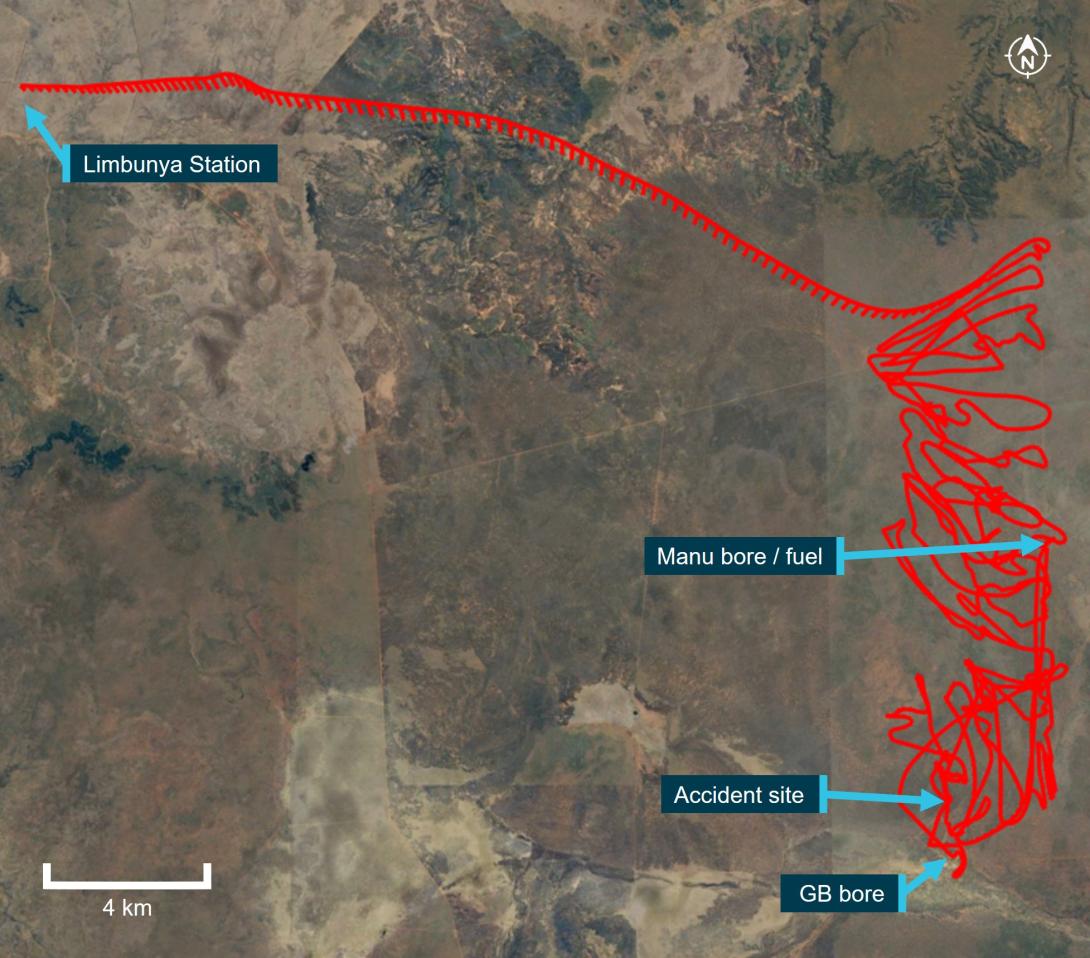
Image source: OzRunways and Google Earth, annotated by the ATSB
Helicopter recording devices
RHC introduced cockpit video cameras and engine monitoring units/governor (EMU), which are standard on new R22, R44 and R66 helicopters. The forward-facing camera records video (encompassing a view through the windshield, pilot controls and the instrument panel), intercom audio, radio transmission and GPS data. The cameras are an optional retrofit to most in-service helicopters.
The EMU monitors engine speed, rotor speed, engine oil temperature, cylinder head temperature, manifold pressure, ambient pressure, and outside air temperature. If the EMU detects an engine or rotor parameter outside of operating limits, an exceedance record is created and the data is stored.
These recording devices could assist with occurrence investigations by allowing investigators to understand the circumstance/s that precede an accident, particularly when there are no survivors or witnesses. In turn, this aids the identification of important safety issues. VH-PSC was not equipped with a cockpit camera nor EMU, nor was it required.
Wreckage and impact information
Wreckage distribution
The accident site was located in an area that was flat and moderately wooded (Figure 5). There were no power lines or wires in the surrounding area. The helicopter collided with several branches of a tree (Tree 1) about mid height (5.7 m above the ground). The forward fuselage then impacted terrain in a nose-down, right side low attitude at the base of the second tree (Tree 2). The descent angle through the trees was calculated to be 45–48°. There was a short wreckage trail of about 18 m, on an approximate north-west heading. All helicopter parts were present at the accident site and there was no evidence of an in-flight break-up or a post-impact fire.
Figure 5: Site location, showing surrounding vegetation
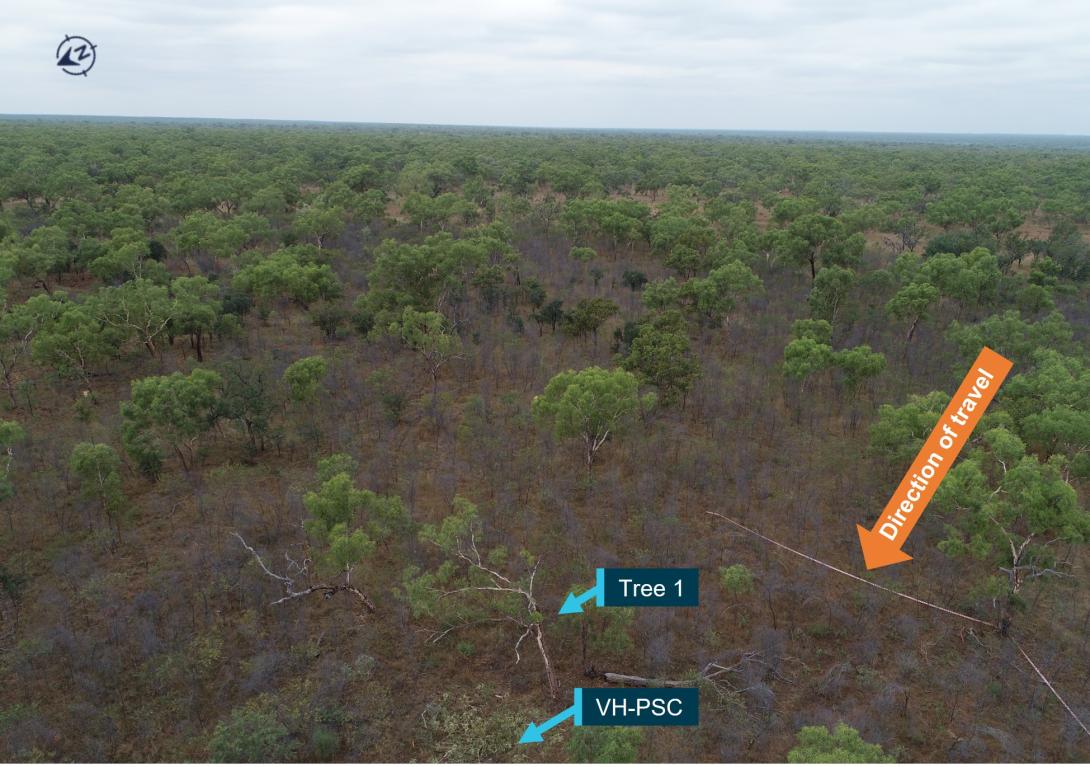
Source: ATSB
The stabiliser assembly, with branch impact damage, was located just prior to Tree 2, the base of which exhibited impact damage and black paint transfer consistent with the landing gear. Pieces of windshield, the instrument panel and other forward fuselage components were located in the impact zone at the base of Tree 2. Fallen foliage was cleared from around Tree 2, and a distinct main rotor blade (MRB) ground scar was identified, with tip components embedded at the start. The fuselage came to rest, upright and to the right of a small tree, with the detached tailcone assembly nearby (Figure 6). The outboard section of the other MRB (MRB tip) had liberated during the tree strikes and was located about 40 m to the left of the debris trail. Rotary fuel hand pump components were located in the vicinity of the fuselage.
Figure 6: Site overview
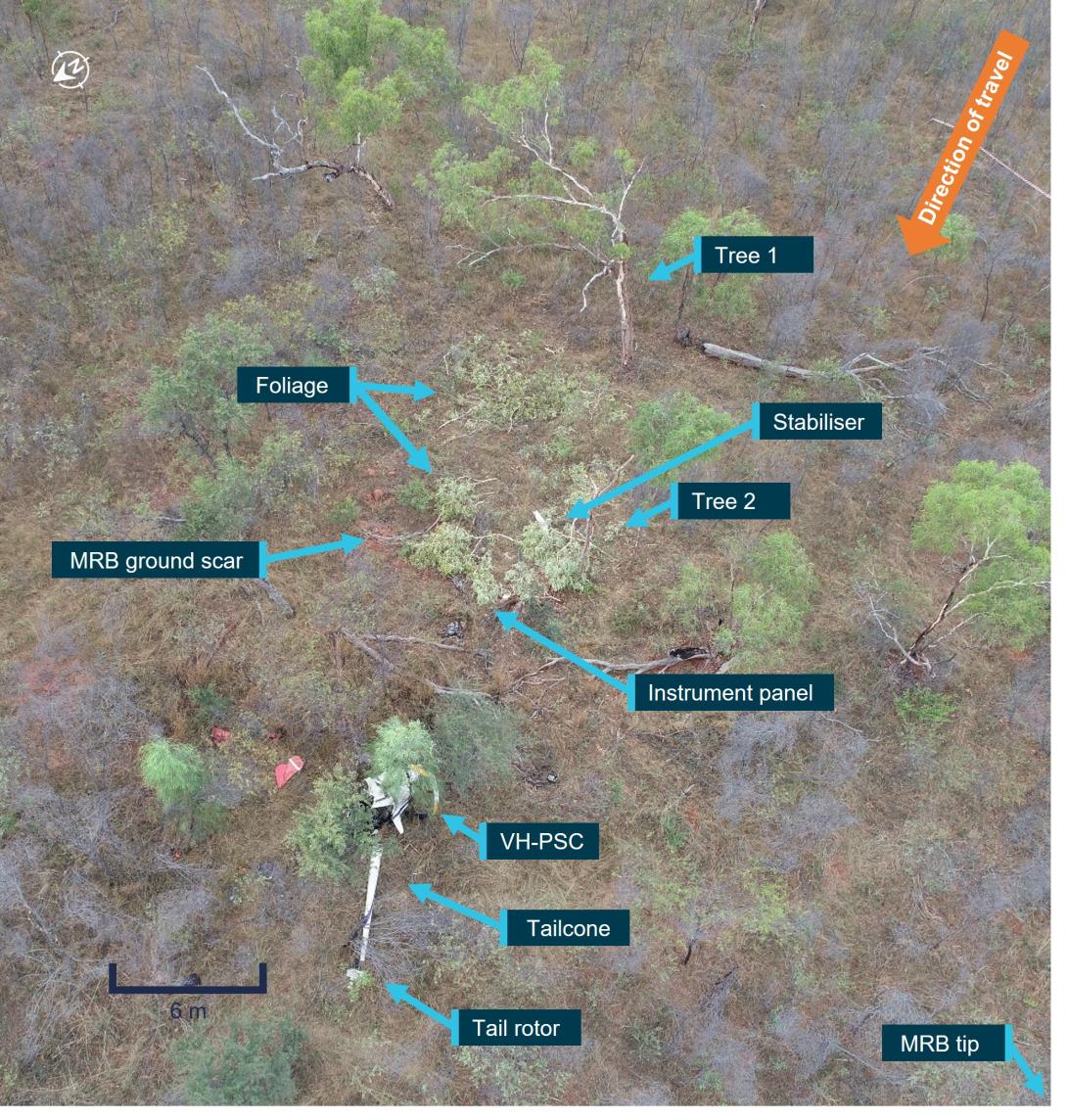
Source: ATSB
Wreckage examination
Detailed examination of the wreckage identified continuity of the flight and engine controls, with all fractures consistent with overstress failure. However, distortion to the fuselage precluded determining engine control position prior to impact. There was nil evidence of birdstrike found in the wreckage or the surrounding area. The examination further identified the following.
Fuselage/cabin area
The collision with terrain compressed the cabin section, resulting in significant disruption of the cockpit area, the cabin structure, and the underfloor flight control mechanism. Police site images showed that the pilot was found to be wearing their seat belt at the time of the accident. Further, tearing of the seat belt webbing was very likely a result of the forces generated by the pilot restrained by the seat belt and being propelled in the direction of impact. The quick-disconnect dual flight controls[16] were not installed for left seat operation. The copilot’s seatbelt was found to be latched with the tongue locked in the buckle.
The mixture knob was in the ‘full-rich’ position with distortion to the fuselage preventing determination of the throttle selection. The throttle and mixture controls were securely connected to the carburettor, however, both linkages had failed in overstress. There was no evidence of a restriction or blockage to any part of the air induction system. Notably, the air intake hose was in good condition and the air box filter was clear.
Main rotor assembly
The main rotor blades had not contacted the cabin or tailcone and there was no evidence of extreme teeter or mast bump.[17] Both main rotor blades remained connected to the rotor head and exhibited rearward bending distortion. All hardware associated with the rotor head, blades and flight controls was secure and both pitch links were measured and found to be within service adjustment limits.[18] The pitch links were secured to the swashplate and main rotor pitch horns, with one pitch horn exhibiting distortion consistent with the main rotor blade ground strike. Overall, the damage to the main rotor blades and head assembly was indicative of low rotational energy at impact with the ground and simultaneous strike to the upper sections of Tree 2.
Landing gear
Vegetation debris on the upper surface of the left skid, forward of the strut, along with distortion to the forward strut was consistent with impact with the base of Tree 2. Fracture of the right skid and distortion to the right side of the landing gear was consistent with the nose and right-side low, impact with the ground.
Drivetrain
Both drive belts were intact, however, the rear belt had dislodged entirely from the upper sheave and the forward belt had jumped one groove forward (with one ‘v’ still engaged) during the accident sequence. There was no evidence of rubbing on either belt or sheave outer rim.[19]
The belt-tensioning clutch actuator extension was consistent with a properly functioning actuator and a relatively new belt set.[20] There was evidence of minor rotational scoring to the actuator body. The upper sheave rear face exhibited some minor surface corrosion of about a quarter to a third of the circumference, consistent with actuator body contact during the accident sequence.
Continuity of the drive train was established, except where the tail rotor drive shaft had fractured and there was tailcone separation. The main and tail gearboxes contained sufficient oil, could be rotated and the respective chip detectors were free of contamination. The freewheeling sprag clutch engaged/disengaged as expected.
Tailcone
The tailcone was securely mounted to the fuselage but had separated where the outer skin had fractured at the forward-most frame rivet line. Distortion to the tailcone just aft of the fractured rivet line was consistent with dynamic deflection occurring at fuselage impact with terrain. This corresponded to the upper left bolt, that secures the tailcone to the upper frame, being sheared. Momentum carried the tailcone forward and it came to rest in front of the fuselage, 180° opposite normal orientation.
The horizontal stabiliser and lower vertical fin exhibited damage consistent with tree branch impact and the mount to the tailcone had fractured in overstress. There was no damage or distortion to the upper vertical fin nor tail skid.[21] The tail rotor assembly was secured to the tailcone and both tail rotor blades exhibited low-energy tree strike damage. There was a small amount of dirt on the end of the tail rotor visual warning guard, consistent with coming into contact with the ground following tailcone separation from the fuselage.
Fuel system
The fuel system was selected to ‘ON’ and the bladder-type fuel tanks contained sufficient fuel for engine operation. The fuel supply from the tanks to the carburettor was intact and no signs of obstructions were noted. In addition, fuel quality was established through testing of fuel stocks at Manu bore and the homestead, and no contamination was found.
Carburettor
The carburettor heat knob was fully down (nil heat) and the heat assist was locked out (not functioning). The carburettor heat slider was in the HEAT selection, however, disruption to the airframe resulted in the control cable pulling the slider before the cable fractured in overstress.
Governor
The governor switch was oriented toward ON, however, impact damage and distortion meant the selection prior to impact could not be determined. The governor control unit was examined and tested by RHC, while being observed by a member of the United States National Transportation Safety Board (on behalf of the ATSB). The governor was within limits for all but one parameter, the ‘duty cycle’, which recorded an exceedance of 0.89%. RHC noted:
Duty cycle is the percentage of power sent to the motor to effect required throttle response. Under normal flight conditions this slight reduction in response speed would not be observable by the pilot.
Engine and fanwheel
The onsite examination identified the engine was intact and securely attached to its mount with all engine accessories securely attached. The engine sump casing had been perforated at impact, with a loss of oil contents.
Examination of the fanwheel identified the ring aft face was perforated between 2 vanes, with the edges of the break displaced aft, and curling of the edges. There was no paint transfer nor vegetation deposits, which may have identified if the damage was from a helicopter component, or tree branch. The dimension of the peeled skin was similar to the diameter of a rotary fuel pump standpipe section.
There was no circumferential scoring or damage to the other vane segments nor the aft face of the fan ring, as would be expected with a rotating fan. Damage to the fan shroud was consistent with ground impact with a stationary fan. Therefore, damage to the fan and shroud indicated that the engine was likely not operating at the time the damage to the fanwheel occurred.
Summary
Typical signatures of high energy (the engine driving the rotor) at the time of a collision with terrain include liberation and/or fragmentation of main rotor blades, fragmentation of the fanwheel and/or shroud, fracture of the main rotor pitch links and severe deformation of driveshaft flex couplings. However, in this instance, both main rotor blades remained connected to the rotor head and only exhibited rearward bending distortion. All hardware associated with the rotor head, blades and flight controls was secure. The pitch links were secured to the swashplate and main rotor pitch horns, with one pitch horn exhibiting distortion consistent with the main rotor blade ground strike. These, and other signatures, were indicative of a collision with terrain in a low rotor energy state (engine not driving the rotor system), where the energy diminishes with main rotor contact with the trees, followed by rotor sudden stoppage at ground strike.
Post onsite examination
The magneto switch was found selected to the BOTH position with the key in the barrel. The switch was examined and tested at the ATSB’s technical facility in Canberra, Australian Capital Territory. The results of the testing indicated that the ignition switch was fully functional and other than some external, physical damage attributed to impact forces, no internal defects that may have affected magneto selection operation were identified.
In January 2024, the engine was disassembled and examined at a CASA‑authorised engine overhaul facility under the supervision of the ATSB. The engine condition was consistent with the engine’s recorded time-in-service since overhaul. No internal or external damage was identified that may have prevented the engine from operating normally prior to the accident. No defects were identified in the induction system components, core engine, or cylinder assemblies that may have affected its pre-accident operation. Both magnetos were operationally tested and returned positive results and then internally examined and resistance tested with nil defects identified.
The carburettor was bench tested and internally examined, with no issues identified.
Medical and pathological information
Medical history
The pilot was known to be health conscious, fit, did not drink alcohol or smoke (cigarettes or vapes) and did not use recreational drugs. A review of the pilot’s medical records noted no medications were prescribed between 27 June 2021 and 27 June 2023.
Due to the pilot’s age, they were required to undergo an electrocardiogram (ECG),[22] and serum lipids (cholesterol) and blood glucose testing for each Class 1 medical certificate renewal. At the pilot’s most recent medical examination (November 2022) it was identified that their cholesterol level had increased. Due to the heightened cholesterol level, the pilot underwent an ECG, a treadmill stress echocardiogram,[23] and a computed tomography (CT) coronary angiogram. Following a review by a consultant cardiologist and the CASA‑designated aviation medical examiner, the pilot’s Class 1 medical certificate was renewed.
Post-mortem and toxicology
A post-mortem examination of the pilot was conducted by a qualified pathologist, on behalf of the Northern Territory Coroner. The pathologist’s report indicated that their examination was impeded due to the elapsed time between the accident and the recovery of the pilot’s body to a suitable mortuary facility. With consideration to these limitations, the report concluded that:
- the pilot succumbed to multiple blunt force injuries sustained during the accident sequence
- there was no evidence of any natural disease that have may resulted in death or impaired the pilot’s ability to control the aircraft.
Toxicological testing conducted as part of the pilot’s post-mortem examination identified concentrations of alcohol at 0.078% and carboxyhaemoglobin (COHb) at 11%.
The pathologist concluded that the alcohol concentration, while higher than that permitted to operate a vehicle in Australia, was ‘not relevant to death by means of interfering with mood, judgement or coordination’. In addition, the pathologist also noted that the sample location and post‑mortem changes likely affected the alcohol concentration in this instance.
The ATSB engaged an aviation medical specialist to review the pilot’s post-mortem and toxicology examinations (discussed below). Acknowledging the limitations reported by the pathologist due to decomposition, the ATSB’s aviation medical specialist also advised that some causes of death or incapacitation were not always able to be identified post-mortem.
Carboxyhaemoglobin
Carbon monoxide is an odourless, colourless and tasteless gas formed by the incomplete combustion of carbon-containing materials. When inhaled, it preferentially binds to haemoglobin, the oxygen carrying molecule in red blood cells. This creates COHb compounds and prevents oxygen from binding to the molecule and being transported, resulting in oxygen starvation.
ATSB investigation AO-2017-118 found that the physical symptoms of carbon monoxide exposure generally start to occur at COHb levels of around 10%. However, adverse neurobehavioural and cognitive effects can occur at lower levels. These symptoms and effects can include headaches, nausea, dizziness, confusion, and disorientation. These will become more severe with increasing COHb levels and duration.
The toxicology report noted:
Samples other than unpreserved peripheral blood may be unsuitable for accurate carboxyhaemoglobin determination. Results must be interpreted with caution in instances of aged or putrefied blood samples.
Correspondence with the pathologist and the ATSB’s aviation medical specialist determined that, given the time elapsed before sample collection, the sample location, and absence of an accurate determination of fluid versus blood ratio of the sample, resulted in uncertainty as to the accuracy of the COHb concentration level at the time of the accident.
A review of the ATSB aviation occurrence database identified about 60 carbon monoxide occurrences involving aeroplanes between 2010 and 2024. In contrast, only one occurrence was recorded for helicopters between 1991 and 2023:
In 2018, during take-off, the wind blew the exhaust fumes into the cockpit of an R44 resulting in the crew receiving a carbon monoxide warning. The crew returned the helicopter to the aerodrome.[24]
In addition, no accident reports (worldwide) were identified, which discussed elevated COHb levels involving R22 helicopters.
Based on the configuration of the helicopter, with the engine below and behind the cabin, it was considered unlikely for significant exhaust gases to enter the cabin, even with both doors removed.
Pilot injury assessment
According to Campman and Luzi (2007), identifying who was in control of the aircraft at the time of impact may provide valuable insight into the events leading up to the accident. The presence or absence of certain occupant injuries could assist with this determination. In particular, those relating to the upper and lower extremities from manipulating the flight controls and by the forces transmitted through the extremities at the time of impact.
Gradwell and Rainford (2016) stated that although ‘Unequivocal control-type injuries indicate that the pilot was conscious at the time of the crash’, they also highlighted that:
…caution must be exercised in their interpretation as they are neither particularly sensitive nor specific findings. Similar injuries may be seen in passengers if they grasp a solid structure at the time of impact, and if the pilot lets go of the controls in the instant before impact, then control-type injuries will not be seen.
The ATSB’s aviation medical specialist indicated that they would have expected more bone fractures if the pilot had been manipulating the controls at the time of impact. However, it was not possible to determine if the absence of typical control-related injuries identified on the pilot were suggestive of incapacitation prior to impact or rather, letting go of the flight controls during the accident sequence.
Operational information
Mustering operations
The operator’s staff described that the helicopters were typically operated ‘at height’ so that the helicopter ‘noise’ was used to move the cattle, rather than flying low and ‘upsetting’ the cattle. In this method, the helicopters were operated about 700–900 ft above the ground, which allowed the pilots to have a good overview of the area and see down through the timber to locate cattle. They would then gradually descend the helicopter, using the noise to get the cattle moving in the desired direction, before climbing to locate other cattle. The accident pilot was described as ‘careful’ and ‘calm’, when compared with some other pilots.
Quick descent
Where a quick descent is desired, the pilot will lower the collective while simultaneously rolling off throttle, to avoid main rotor overspeed. The descent will typically be steep and in a right turn, to allow the right-seated pilot to maintain forward airspeed and visual contact with their target. The throttle will then be rolled on prior to raising the collective to arrest the descent. This technique is similar to that when practicing an autorotation. The normal procedures section of the R22 POH Practice autorotation – power recovery includes the following caution:
To avoid inadvertent engine stoppage, do not chop throttle to simulate a power failure. Always roll throttle off smoothly. Recover immediately if engine is rough or engine RPM continues to drop.
Autorotation
The R22 POH detailed that a power failure may result from either an engine or drive system failure and will usually be indicated by the low rotor RPM horn. An engine failure may be indicated by a change in noise level, nose left yaw, an oil pressure light, or decreasing engine RPM. A drive system failure may be indicated by an unusual noise or vibration, nose right or left yaw, or decreasing rotor RPM while engine RPM is increasing.
The energy to successfully land (autorotation)[25] a helicopter in an engine off condition, such as an engine failure, comes from a combination of available potential and kinetic energy in the form of height, forward speed and rotor RPM. A pilot can utilise that energy to maintain drive to the main rotor and create lift.
The R22 POH explained the steps to take to enter an autorotation when between 8–500 ft.[26] The procedure stated to lower the collective immediately to maintain rotor RPM. While in a steady descent, adjust the collective to maintain rotor RPM between 97 and 110%. If time permitted, and when an engine restart is not possible, turn off unnecessary switches and close the fuel valve. Prior to landing from an autorotation, at about 40 ft above the ground, the pilot must flare the helicopter in order to reduce forward speed and increase rotor RPM before cushioning the landing.
The conditions from which a safe autorotation could be made were specified in the height-velocity diagram in the POH. A notation on the diagram encouraged pilots to avoid operation in the shaded area. When operating in this area, a pilot may be unable to complete an autorotation landing without damage. The unshaded region of the diagram shows the combinations of airspeed and height above the ground that allows a pilot to successfully complete a landing in a full autorotation without requiring exceptional skill. Recorded data showed that, over the course of the morning, PSC had been operated both in the shaded ‘avoid’ area, as well as in the non-shaded area.
Low rotor RPM and stall
The R22, with its low rotor system mass and relatively high RPM, is described as ‘low inertia’ helicopter. In low inertia systems, rotor RPM is gained and lost very easily. Low rotor RPM occurs when drag on the rotor system exceeds the power available to drive it. Without quick and effective intervention, the rotor RPM decays, it produces less lift, and the helicopter will start to descend. Airflow over the blade changes and the condition deteriorates until one or both of the main rotor blades stall.[27] According to RHC safety notice SN-24 Low RPM rotor stall can be fatal, recovery from rotor stall is ‘virtually impossible’.
Low-rotor RPM can occur at almost any time during power-on and power-off operations and is usually the result of improperly coordinating the collective and throttle, including overpitching or a failure to quickly lower the collective in an emergency such as engine failure or power reduction.
RHC safety notice SN-10 Fatal accidents caused by low rotor RPM rotor stall included:
A primary cause of fatal accidents in light helicopters is failure to maintain rotor RPM. To avoid this, every pilot must have his reflexes conditioned so he will instantly add throttle and lower collective to maintain RPM in any emergency.
The low rotor RPM warning lamp and horn will activate when the rotor RPM reduces to 97% or below. The warning lamp is located on the top of the instrument panel and the horn can be heard in the cabin and through the headset. The POH stated that ‘catastrophic rotor stall could occur if the rotor RPM ever drops below 80% plus 1% per 1,000 ft of altitude’. Further, the United States Federal Aviation Administration Helicopter Flying Handbook stated that ‘low inertia rotor systems can become unrecoverable in 2 seconds or less if the RPM is not regained immediately’.
Partial power loss
As discussed in ATSB investigation AO-2022-009, RHC previously advised that a main rotor strike to the ground, a significant tree or structure, could stall (stop) an engine when operating at low power or idle, prior to an impact with the terrain.
Safety analysis
Introduction
On the morning of 27 June 2023, 2 Robinson Helicopter Company R22 helicopters were conducting mustering operations near Limbunya Station, Northern Territory, in conjunction with a ground team on horseback and motorcycles. When the pilot of the second helicopter (VH-RCS) had not heard from the pilot of VH-PSC for some time, they commenced a search and located the accident site after about 15–20 minutes. The helicopter was destroyed, and the pilot was fatally injured.
There were no witnesses and no recorded data to accurately determine the accident sequence, including the time of the accident.
This analysis will discuss the potential reasons for engine power reduction and loss of control. It also considers some aspects associated with the maintenance release.
Occurrence events
Engine power reduction
The wreckage signatures were consistent with the main rotor being in a low energy state. Given this, the ATSB considered how much engine power was being produced at the time of the accident.
Examination of components identified some minor scoring to the drive train belt-tensioning clutch actuator body, consistent with contact with the upper sheave. The corresponding location on the sheave exhibited some minor discolouration from actuator body material deposits that had begun to corrode. While scoring would normally indicate engine rotation at impact, in this instance, the sheave discolouration extended only a quarter to one third of the circumference. This limited scoring may be more representative of a low‑energy main rotor blade being forced backward to the direction of rotation at impact with the ground, rather than engine rotation. However, the non‑rotational damage to the fanwheel was consistent with the engine not operating at the time of impact.
The ATSB considered the potential reasons for the reduction in engine power, which can be broadly categorised as:
- engine and associated systems defect
- fuel contamination or starvation
- carburettor ice
- pilot-induced (intentional).
Examination of the engine and associated systems did not identify a fault or condition, which would have prevented normal operation. Nor was any issue found with the fuel quantity or quality. While an intermittent interruption to normal operation could not be completely discounted, there was no observable evidence to indicate this may have occurred.
The meteorological conditions at the nearest Bureau of Meteorology weather station,144 km away, were on the edge of the ‘serious icing – descent power’ and ‘moderate icing – cruise power’ envelopes for carburettor icing. However, the pilot of the other R22 operating in the accident area, reported that local conditions did not require the use of carburettor heat and they did not observe any indications of the formation of carburettor ice.
The ATSB considered the possibility that the pilot intentionally reduced the throttle as part of a quick descent. Inadvertent engine stoppage could occur from the throttle being reduced too quickly, which may have occurred at a height too low to perform a successful engine off landing (autorotation) to clear ground. In addition, the collision with terrain in a nose and right-side low orientation could also be indicative of a quick descent manoeuvre, from which recovery did not occur. Alternatively, as noted by the manufacturer, if the engine was in a low-power state when the main rotor blades impacted the tree and ground, it was possible that this impact stopped the engine.
Loss of control
The ATSB considered other loss of control events that may have preceded the nose and right-side down trajectory through a tree and then the subsequent collision with terrain.
There were no indications of a collision with a bird or other object, such as a wirestrike. Based on the witness observations, there was no evidence to suggest that the weather conditions affected the pilot’s ability to maintain control of the helicopter. As discussed above, there was no observable issue identified with the helicopter nor was there any indication of mast bumping. While it was possible that a loose object in the cabin interfered with the pilot’s flight controls, the disruption to the cabin area precluded identifying any evidence of this. Regardless, this scenario did not account for the low rotor energy (engine not driving the rotor system).
While distractions can occur unexpectedly, the other R22 was not operating in the immediate area to distract the pilot. The engine reduction (if not intentional) could have potentially been a distraction and required the pilot to conduct an autorotation. However, ATSB research has shown that distraction events most often result in an incident rather than accident (ATSB, 2006).
A reduction in engine power, whether operating at low or idle power, or in the event of a complete engine stoppage, requires prompt and effective management of main rotor RPM, above 97%, in order to conduct a successful autorotation. In this instance, the trajectory and orientation of the helicopter was not consistent with what would be expected if the helicopter was being flared, to reduce the rate of descent prior to touching down during a controlled autorotation.
Conclusions
The site and wreckage signatures were consistent with an engine power reduction and loss of control. Further, it could not be determined if the engine was producing low power, or was stopped, and if this was due to an engine issue (unobserved from the wreckage examination) or pilot induced. The pilot was highly experienced in low-level helicopter operations and demonstrated their capability to an instructor during simulated emergency procedures about 3 months prior. However, as there was no recorded data available or witnesses to the final stages of the flight, the pilot’s actions leading up to the accident were unknown.
Without conclusive reasons to explain the accident sequence, the ATSB also considered if it was possible that the pilot experienced some level of incapacitation before (resulting in inadvertent throttle manipulation), or after the reduction in engine power. Incapacitation could also explain the low rotor energy and/or helicopter trajectory into terrain. The absence of a radio transmission, in the event of an autorotation, could be suggestive of an incapacitation event, but could also indicate a sudden event that the pilot did not have time to transmit.
Despite this, a comprehensive review of the pilot’s medical history and general health did not identify any pre‑existing or other condition that could have adversely affected their performance. The post‑mortem did not identify the presence of any natural disease, however, the pathologist reported limitations due to decomposition, including the elevated carboxyhaemoglobin results. Further, analysis of the flight control injuries was inconclusive. Although the ATSB’s aviation medical specialist advised that some causes of death or incapacitation were not always able to be identified post-mortem, incapacitation remained only a possibility as there was insufficient evidence to conclude probability.
Therefore, due to the limited evidence available, the ATSB was unable to determine the reason for the engine power reduction and loss of control, nor the sequence of these events.
Maintenance release no longer in force
The current maintenance release, located at the accident site, had no endorsements showing daily inspections, hours flown each day, calculation of accumulated time-in-service or certification for completion of scheduled maintenance.
The pilot’s diary indicated they had operated VH-PSC every day since the maintenance release was issued (13 days prior to the accident). Text messages between the pilot and operator indicated that the required 25-hour engine oil and filter change had been completed, despite not being certified for on the maintenance release. Without a record of the accumulated total time‑in‑service, the ATSB could not determine if the 50-hour oil and filter change had come due, nor if it had been completed.
In this instance, as the pilot was the sole operator of the helicopter, the absence of endorsements did not hinder other pilots from being aware of the serviceability status. However, the maintenance release is a legal document that is part of the ongoing airworthiness requirements for the helicopter. The lack of certification for the completion of maintenance did not contribute to the accident, however, the helicopter was being operated with a maintenance release that had ceased to be in force and was therefore considered unairworthy.
Findings
ATSB investigation report findings focus on safety factors (that is, events and conditions that increase risk). Safety factors include ‘contributing factors’ and ‘other factors that increased risk’ (that is, factors that did not meet the definition of a contributing factor for this occurrence but were still considered important to include in the report for the purpose of increasing awareness and enhancing safety). In addition ‘other findings’ may be included to provide important information about topics other than safety factors. These findings should not be read as apportioning blame or liability to any particular organisation or individual. |
From the evidence available, the following findings are made with respect to the collision with terrain involving a Robinson R22 Beta II, VH-PSC, near Limbunya Station, Northern Territory, on 27 June 2023.
Contributing factors
- While conducting mustering operations, for reasons that could not be determined, there was a reduction in engine power and a loss of control.
Other findings
- While not contributory to the accident, the absence of endorsements for daily inspections and nil certification for the completion of scheduled maintenance resulted in VH-PSC being operated with a maintenance release that had ceased to be in force.
Sources and submissions
Sources of information
The sources of information during the investigation included:
- the other pilot and members of the ground muster team
- the operator and maintainer
- Civil Aviation Safety Authority
- Northern Territory Office of the Coroner
- Northern Territory Police
- Western Australia Police
- forensic and aviation pathology specialist
- Robinson Helicopter Company
- Airservices Australia
- Bureau of Meteorology
- OzRunways data from the pilot’s phone
- next of kin and friends of the pilot.
References
Gradwell, D. & Rainford, D.J. (Eds.). (2016). Ernsting’s Aviation and Space Medicine (5th ed). Boca Raton, FL: CRC Press.
Submissions
Under section 26 of the Transport Safety Investigation Act 2003, the ATSB may provide a draft report, on a confidential basis, to any person whom the ATSB considers appropriate. That section allows a person receiving a draft report to make submissions to the ATSB about the draft report.
A draft of this report was provided to the following directly involved parties:
- the operator
- pilot of VH-RCS
- the maintenance organisation that conducted the engine overhaul
- Civil Aviation Safety Authority
- United States National Transportation Safety Board
- Robinson Helicopter Company
- Bureau of Meteorology
- the pathologist and medical subject matter expert.
Submissions were received from:
- Robinson Helicopter Company
- the operator.
The submissions were reviewed and, where considered appropriate, the text of the report was amended accordingly.
Purpose of safety investigationsThe objective of a safety investigation is to enhance transport safety. This is done through:
It is not a function of the ATSB to apportion blame or provide a means for determining liability. At the same time, an investigation report must include factual material of sufficient weight to support the analysis and findings. At all times the ATSB endeavours to balance the use of material that could imply adverse comment with the need to properly explain what happened, and why, in a fair and unbiased manner. The ATSB does not investigate for the purpose of taking administrative, regulatory or criminal action. TerminologyAn explanation of terminology used in ATSB investigation reports is available here. This includes terms such as occurrence, contributing factor, other factor that increased risk, and safety issue. Publishing informationReleased in accordance with section 25 of the Transport Safety Investigation Act 2003 Published by: Australian Transport Safety Bureau © Commonwealth of Australia 2024
Ownership of intellectual property rights in this publication Unless otherwise noted, copyright (and any other intellectual property rights, if any) in this report publication is owned by the Commonwealth of Australia. Creative Commons licence With the exception of the Commonwealth Coat of Arms, ATSB logo, and photos and graphics in which a third party holds copyright, this report is licensed under a Creative Commons Attribution 4.0 International licence. The CC BY 4.0 licence enables you to distribute, remix, adapt, and build upon our material in any medium or format, so long as attribution is given to the Australian Transport Safety Bureau. Copyright in material obtained from other agencies, private individuals or organisations, belongs to those agencies, individuals or organisations. Where you wish to use their material, you will need to contact them directly. |
[1] All times provided by the pilot of RCS and members of the ground muster team were estimated (give or take 10-15 minutes each side), however, were sufficiently consistent to develop the timeline of events.
[2] The hours noted in the diary were likely a combination of flight time and duty (or on ground) time.
[3] When installed, the cabin heat system uses air warmed by a shroud surrounding the muffler, which is then directed via ducting to the cabin.
[4] The freewheeling unit automatically disengages any time the engine revolutions per minute become less than rotor revolutions per minute, allowing the rotor system to rotate free of the engine drive system.
[5] Collective: a primary helicopter flight control that simultaneously affects the pitch of all blades of a lifting rotor. Collective input is the main control for vertical velocity.
[6] When conditions were conducive to carburettor ice, the POH required the pilot to use carburettor heat as required to keep the needle on the carburettor air temperature gauge out of the yellow arc (-15 to 5 °C). In addition, carburettor heat was to be used with power settings below 18” mercury, regardless of the indicated carburettor air temperature.
[7] Cyclic: a primary helicopter flight control that is similar to an aircraft control column. Cyclic input tilts the main rotor disc, varying the attitude of the helicopter and hence the lateral direction.
[8] As the engine had been fitted to other aircraft, its overhaul cycle did not align with PSC.
[9] Service bulletin SB 480 also noted that ‘in special circumstances’ the oil and filter change ‘can be extended not more than 5 hours while en route to a place where the oil change can be done’.
[10] High oil consumption and/or a change in oil consumption can be indicative of a developing engine issue.
[11] Cloud cover: in aviation, cloud cover is reported using words that denote the extent of the cover – ‘overcast’ indicates that all the sky is covered.
[12] Dewpoint: the temperature at which water vapour in the air starts to condense as the air cools. It is used, among other things, to predict the probability of aircraft carburettor icing or the likelihood of fog.
[13] OzRunways is an electronic flight bag application that provides navigation, weather, area briefings and other flight information. It provides the option for live flight tracking by transmitting the device’s position and altitude.
[14] OzRunways distinguishes one flight from another by identifying that the aircraft is conducting a flight when it is above a threshold speed. Therefore, a ‘flight’ is considered to be when the aircraft is above the threshold speed to when it drops below the threshold speed. Data may not be recorded when the aircraft is below the speed threshold. PSC likely regularly dropped below the threshold speed, probably while at low altitude moving the stock. As such, the OzRunways system thought this was the end of a flight and did not record the data. Data acquisition recommenced when the helicopter was operated above the ‘flight’ thresholds.
[15] The ATSB examined the pilot’s mobile phone in case data had been collected but not yet transmitted, however, no additional information was available.
[16] Quick-disconnect flight controls do not require use of tooling to fit and remove and can therefore be accomplished by the pilot, without the requirement for a licenced aircraft maintenance engineer.
[17] Mast bumping: contact between the main rotor hub/spindle and the rotor mast which, if excessive, could severely damage the mast, or result in the separation of the main rotor system from the helicopter. Damage from mast bumping is indicative of excessive blade flapping and/or excessive tilt of the main rotor disc relative to the mast. As documented in many investigation reports worldwide, scenarios that have been linked to mast bumping include low-g and/or low rotor revolutions per minute/rotor stall, in conjunction with delayed and/or inappropriate flight control inputs.
[18] Main rotor pitch links can be lengthened (to decrease RPM) or shortened (to increase RPM) to obtain optimum autorotation rotor RPM.
[19] Rubbing from contact between a belt and the sheave can be an indication of engine providing power to the drivetrain, however, it is also possible that a dislodged belt may not make contact with the sheave under certain circumstances.
[20] A new drive belt set had been installed during the last periodic inspection.
[21] Tail skid: A guard device attached below the lower vertical fin to protect the tail rotor blades from ground strike.
[22] An ECG detects heart problems by measuring the electrical activity generated by the heart as it contracts. ECGs from healthy hearts have a characteristic shape. If the ECG shows a different shape it could suggest a heart problem.
[23] Stress echocardiogram (stress echo) is a test to assess heart function under physical stress. It uses ultrasound waves (inaudible sound waves) to image the heart and assess its function before and immediately after the exercise to see how the heart muscle pump is working, and sometimes to measure other parameters.
[24] Effects to the flight crew, if any, were not provided to the ATSB in the occurrence notification.
[25] Autorotation is a condition of descending flight where, following engine failure or deliberate disengagement, the rotor blades are driven solely by aerodynamic forces resulting from rate of descent airflow through the rotor. The rate of descent is determined mainly by airspeed.
[26] For power failure below 8 ft, the pilot was to apply right tail rotor pedal input as required to prevent yaw, allow the helicopter to settle and raise the collective just before touchdown to cushion landing.
[27] Rotor stall, similar to aerodynamic stall in aeroplanes, occurs when increasing rotor blade angle, relative to airflow (angle of attack), reaches a point where airflow separates from the rotor upper surface and becomes turbulent, reducing lift. As the helicopter descends, the upward flow of air further increases the angle of attack until the critical angle of stall in reached, resulting sudden loss of lift and a large increase in drag. The increased drag acts like a rotor brake causing the rotor RPM to rapidly decrease, further increasing the rotor stall.