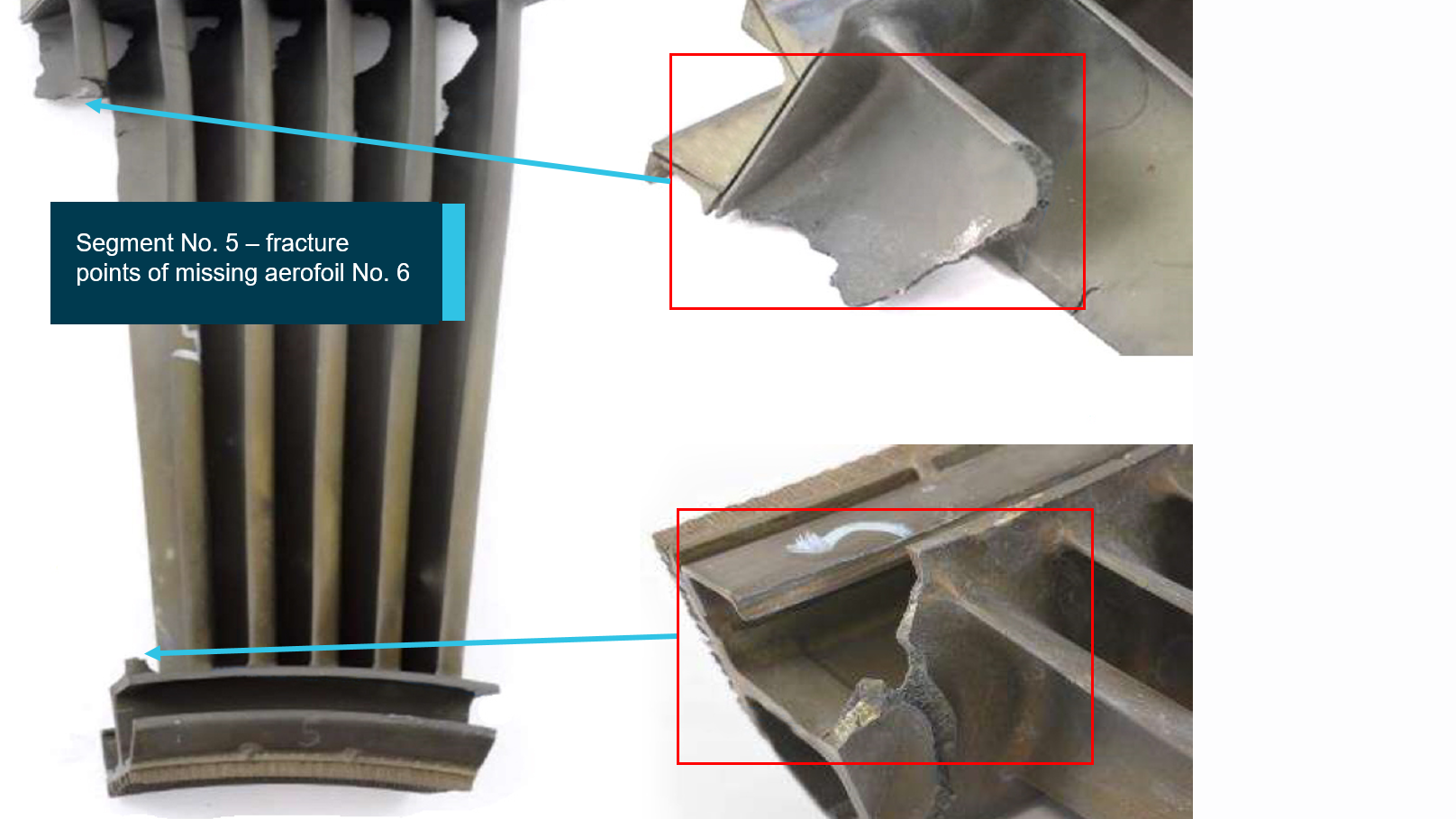
Key points:
|
The flight crew of an Airbus A330 shut down one of the aircraft’s two General Electric CF6 engines and turned back to their departure airport after the engine experienced a nozzle guide vane aerofoil failure.
The Qantas A330-300, registered VH-QPI, had departed Sydney Airport on 1 June 2018 bound for Bangkok, Thailand, operating a scheduled passenger flight with 13 crewmembers and 297 passengers on board.
As the engine thrust was being reduced from the take‑off setting at an altitude of about 1,700 feet, the first officer (the pilot monitoring) heard a sound described as a ‘pop’. The flight crew also received an ECAM (electronic centralised aircraft monitor) advisory message relating to the right engine’s vibration level, and observed light airframe vibration.
The flight crew discontinued the climb and consulted the ‘High Engine Vibration’ checklist, which directed them to reduce the right engine’s thrust to idle. With the reduction in thrust, the vibration on the right engine reduced but remained relatively high. To prevent further engine damage, the crew shut down the engine, with the vibration ceasing as a consequence.
The flight crew then initiated a holding pattern, and while holding they decided to return to Sydney and perform an overweight landing, in line with company procedures. The descent and return to Sydney Airport was uneventful, with the aircraft landing safely.
“Initial inspection by engineering staff found visible damage to the right engine low-pressure turbine, and damage to the aircraft’s wing flap lower surfaces and body fairings due to engine debris impact,” noted ATSB Director Transport Safety Stuart Macleod.
The engine was removed and sent to engine manufacturer General Electric’s overhaul facility in Taiwan for detailed examination and repair, where it was identified that oxidation and deterioration of the protective coating of the low-pressure turbine stage 4 nozzle guide vane (NGV) segments had led to intergranular oxidation, crack development and loss of an aerofoil from the number 5 segment.
“The liberated aerofoil impacted downstream rotating components, resulting in a loss of turbine blade material, a rotor imbalance and the subsequent airframe vibration,” said Mr Macleod.
“Despite the high reliability of modern turbine engines, this incident illustrates that flight crews can still be faced with malfunctions that require their combined judgement and expertise to manage the situation safely.”
Following this occurrence, General Electric changed the protective coating on NGVs from chromide to vapour-phased aluminide, citing better resistance to oxidation.
Qantas, meanwhile, proactively worked to ensure stage four low-pressure turbine NGV segments that exhibited cracking of the aerofoil leading edge were removed from service, and that only new – and not overhauled segments – were fitted to its CF6-80E1 engines. It also introduced a borescope inspection program that was successful in identifying other engines with aerofoil cracking and removed those affected engines from service.
Read the report: Engine vibrations and in-flight shutdown involving Airbus A330, VH-QPI, near Sydney Airport, New South Wales, on 1 June 2018